铅冶炼技术现状及我国第一台铅闪速熔炼炉试产情况
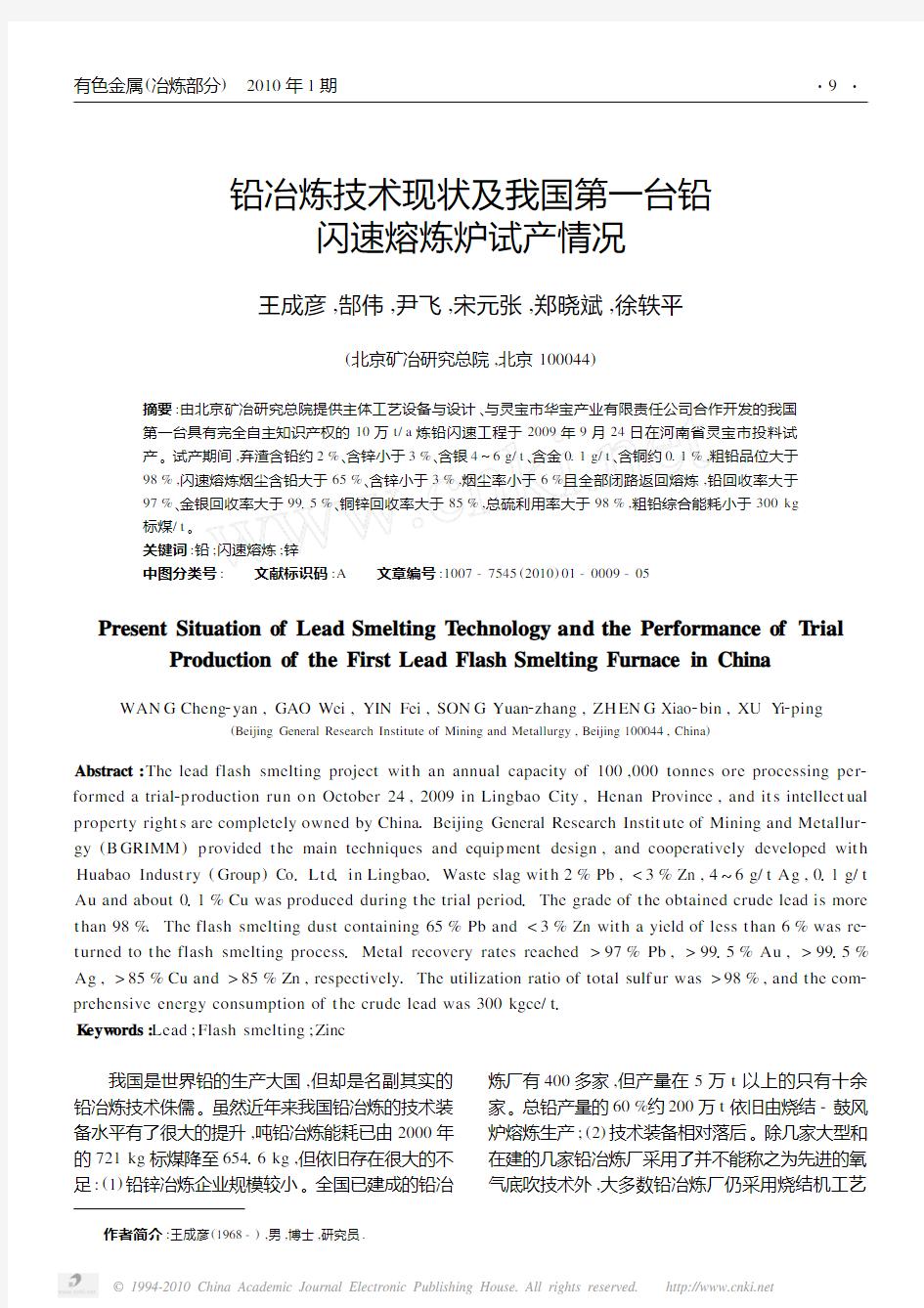
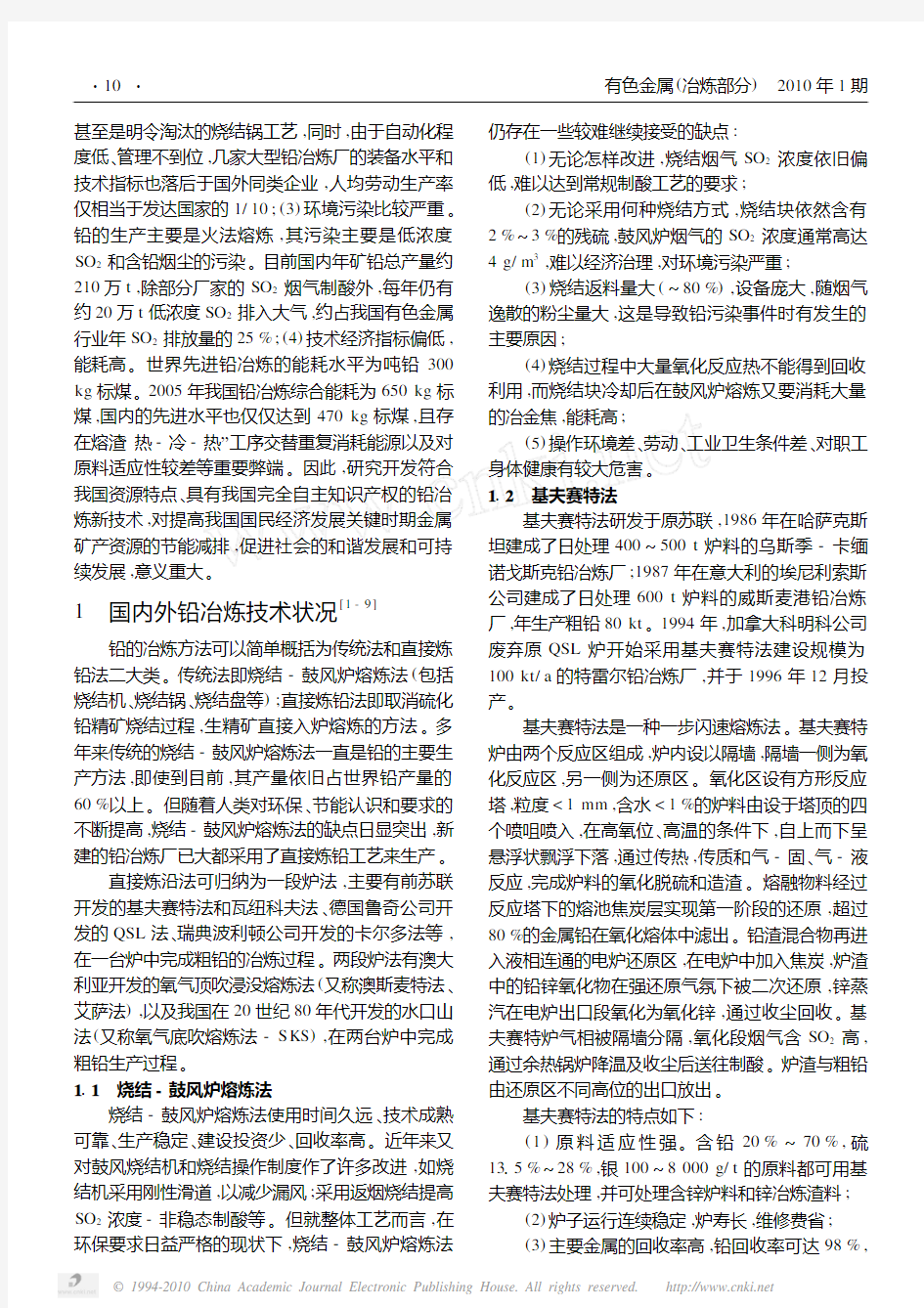
铅冶炼技术现状及我国第一台铅
闪速熔炼炉试产情况
王成彦,郜伟,尹飞,宋元张,郑晓斌,徐轶平
(北京矿冶研究总院,北京100044)
摘要:由北京矿冶研究总院提供主体工艺设备与设计、与灵宝市华宝产业有限责任公司合作开发的我国第一台具有完全自主知识产权的10万t/a 炼铅闪速工程于2009年9月24日在河南省灵宝市投料试产。试产期间,弃渣含铅约2%、含锌小于3%、含银4~6g/t 、含金011g/t 、含铜约011%,粗铅品位大于
98%,闪速熔炼烟尘含铅大于65%、含锌小于3%,烟尘率小于6%且全部闭路返回熔炼,铅回收率大于97%、金银回收率大于9915%、铜锌回收率大于85%,总硫利用率大于98%,粗铅综合能耗小于300kg
标煤/t 。
关键词:铅;闪速熔炼;锌
中图分类号:文献标识码:A 文章编号:1007-7545(2010)01-0009-05
Present Situation of Lead Smelting T echnology and the Performance of T rial Production of the First Lead Flash Smelting Furnace in China
WAN G Cheng 2yan ,GAO Wei ,YIN Fei ,SON G Yuan 2zhang ,ZH EN G Xiao 2bin ,XU Y i 2ping
(Beijing General Research Institute of Mining and Metallurgy ,Beijing 100044,China )
Abstract :The lead flash smelting project wit h an annual capacity of 100,000tonnes ore processing per 2formed a trial 2p roduction run o n October 24,2009in Lingbao City ,Henan Province ,and it s intellect ual p roperty right s are completely owned by China 1Beijing General Research Instit ute of Mining and Metallur 2gy (B GRIMM )p rovided t he main techniques and equip ment design ,and cooperatively developed wit h Huabao Indust ry (Group )Co 1Lt d 1in Lingbao 1Waste slag wit h 2%Pb ,<3%Zn ,4~6g/t Ag ,011g/t Au and about 011%Cu was produced during t he trial period 1The grade of t he obtained crude lead is more t han 98%1The flash smelting dust containing 65%Pb and <3%Zn wit h a yield of less t han 6%was re 2t urned to t he flash smelting process 1Metal recovery rates reached >97%Pb ,>9915%Au ,>9915%Ag ,>85%Cu and >85%Zn ,respectively 1The utilization ratio of total sulf ur was >98%,and t he com 2prehensive energy consumption of t he crude lead was 300kgce/t 1K eyw ords :Lead ;Flash smelting ;Zinc
作者简介:王成彦(1968-),男,博士,研究员1
我国是世界铅的生产大国,但却是名副其实的铅冶炼技术侏儒。虽然近年来我国铅冶炼的技术装备水平有了很大的提升,吨铅冶炼能耗已由2000年的721kg 标煤降至65416kg ,但依旧存在很大的不足:(1)铅锌冶炼企业规模较小。全国已建成的铅冶
炼厂有400多家,但产量在5万t 以上的只有十余家。总铅产量的60%约200万t 依旧由烧结-鼓风炉熔炼生产;(2)技术装备相对落后。除几家大型和在建的几家铅冶炼厂采用了并不能称之为先进的氧气底吹技术外,大多数铅冶炼厂仍采用烧结机工艺
甚至是明令淘汰的烧结锅工艺,同时,由于自动化程度低、管理不到位,几家大型铅冶炼厂的装备水平和技术指标也落后于国外同类企业,人均劳动生产率仅相当于发达国家的1/10;(3)环境污染比较严重。铅的生产主要是火法熔炼,其污染主要是低浓度SO2和含铅烟尘的污染。目前国内年矿铅总产量约210万t,除部分厂家的SO2烟气制酸外,每年仍有约20万t低浓度SO2排入大气,约占我国有色金属行业年SO2排放量的25%;(4)技术经济指标偏低,能耗高。世界先进铅冶炼的能耗水平为吨铅300 kg标煤。2005年我国铅冶炼综合能耗为650kg标煤,国内的先进水平也仅仅达到470kg标煤,且存在熔渣“热-冷-热”工序交替重复消耗能源以及对原料适应性较差等重要弊端。因此,研究开发符合我国资源特点、具有我国完全自主知识产权的铅冶炼新技术,对提高我国国民经济发展关键时期金属矿产资源的节能减排,促进社会的和谐发展和可持续发展,意义重大。
1 国内外铅冶炼技术状况[1-9]
铅的冶炼方法可以简单概括为传统法和直接炼铅法二大类。传统法即烧结-鼓风炉熔炼法(包括烧结机、烧结锅、烧结盘等);直接炼铅法即取消硫化铅精矿烧结过程,生精矿直接入炉熔炼的方法。多年来传统的烧结-鼓风炉熔炼法一直是铅的主要生产方法,即使到目前,其产量依旧占世界铅产量的60%以上。但随着人类对环保、节能认识和要求的不断提高,烧结-鼓风炉熔炼法的缺点日显突出,新建的铅冶炼厂已大都采用了直接炼铅工艺来生产。
直接炼沿法可归纳为一段炉法,主要有前苏联开发的基夫赛特法和瓦纽科夫法、德国鲁奇公司开发的QSL法、瑞典波利顿公司开发的卡尔多法等,在一台炉中完成粗铅的冶炼过程。两段炉法有澳大利亚开发的氧气顶吹浸没熔炼法(又称澳斯麦特法、艾萨法),以及我国在20世纪80年代开发的水口山法(又称氧气底吹熔炼法-S KS),在两台炉中完成粗铅生产过程。
111 烧结-鼓风炉熔炼法
烧结-鼓风炉熔炼法使用时间久远、技术成熟可靠、生产稳定、建设投资少、回收率高。近年来又对鼓风烧结机和烧结操作制度作了许多改进,如烧结机采用刚性滑道,以减少漏风;采用返烟烧结提高SO2浓度-非稳态制酸等。但就整体工艺而言,在环保要求日益严格的现状下,烧结-鼓风炉熔炼法仍存在一些较难继续接受的缺点:
(1)无论怎样改进,烧结烟气SO2浓度依旧偏低,难以达到常规制酸工艺的要求;
(2)无论采用何种烧结方式,烧结块依然含有2%~3%的残硫,鼓风炉烟气的SO2浓度通常高达4g/m3,难以经济治理,对环境污染严重;
(3)烧结返料量大(~80%),设备庞大,随烟气逸散的粉尘量大,这是导致铅污染事件时有发生的主要原因;
(4)烧结过程中大量氧化反应热不能得到回收利用,而烧结块冷却后在鼓风炉熔炼又要消耗大量的冶金焦,能耗高;
(5)操作环境差、劳动、工业卫生条件差、对职工身体健康有较大危害。
112 基夫赛特法
基夫赛特法研发于原苏联,1986年在哈萨克斯坦建成了日处理400~500t炉料的乌斯季-卡缅诺戈斯克铅冶炼厂;1987年在意大利的埃尼利索斯公司建成了日处理600t炉料的威斯麦港铅冶炼厂,年生产粗铅80kt。1994年,加拿大科明科公司废弃原QSL炉开始采用基夫赛特法建设规模为100kt/a的特雷尔铅冶炼厂,并于1996年12月投产。
基夫赛特法是一种一步闪速熔炼法。基夫赛特炉由两个反应区组成,炉内设以隔墙,隔墙一侧为氧化反应区,另一侧为还原区。氧化区设有方形反应塔,粒度<1mm,含水<1%的炉料由设于塔顶的四个喷咀喷入,在高氧位、高温的条件下,自上而下呈悬浮状飘浮下落,通过传热,传质和气-固、气-液反应,完成炉料的氧化脱硫和造渣。熔融物料经过反应塔下的熔池焦炭层实现第一阶段的还原,超过80%的金属铅在氧化熔体中滤出。铅渣混合物再进入液相连通的电炉还原区,在电炉中加入焦炭,炉渣中的铅锌氧化物在强还原气氛下被二次还原,锌蒸汽在电炉出口段氧化为氧化锌,通过收尘回收。基夫赛特炉气相被隔墙分隔,氧化段烟气含SO2高,通过余热锅炉降温及收尘后送往制酸。炉渣与粗铅由还原区不同高位的出口放出。
基夫赛特法的特点如下:
(1)原料适应性强。含铅20%~70%,硫1315%~28%,银100~8000g/t的原料都可用基夫赛特法处理,并可处理含锌炉料和锌冶炼渣料;
(2)炉子运行连续稳定,炉寿长,维修费省;
(3)主要金属的回收率高,铅回收率可达98%,
金银可达99%,原料中的锌回收率可达60%以上;
(4)烟气量小,烟气SO 2浓度高(30%~40%),余热锅炉和电收尘小、热量损失少;
(5)烟尘率低,仅为5%~6%;
(6)氧化还原在一台炉中完成,反应热利用充分,加之热量损失少,因而能耗很低;
(7)炉体密闭,易于实现自动化、机械化,炉体烟尘烟气逸散少、操作条件好、劳动安全、工业卫生条件好;
(8)基夫赛特炉可以处理湿法炼锌渣,回收铅锌、银、铟。基夫赛特炉产出的氧化锌可送炼锌系统处理作到铅锌互补,对铅锌联合企业更具优势。
基夫赛特法有诸多优点,但基夫赛特炉的隔墙由于二面受热,炉衬腐蚀比较快,并常常导致事故的发生。另外,在处理高锌物料时,由于氧化锌烟尘的堆积,常导致烟道的堵塞。113 Q SL 法
QSL 法为富氧底吹熔池熔炼,其QSL 炉为可
转动的卧式长圆筒型炉,并向放铅口方向倾斜015%,并分为氧化区和还原区。在氧化和还原两个区域,分别配有浸没式氧气喷嘴和粉煤喷嘴。铅精矿经制粒后由顶部加入氧化区,与氧枪喷入的氧气在熔池中反应生成氧化铅和SO 2,实现自热熔炼;氧化铅与硫化铅在氧化区发生交互反应生成一次粗铅由底部放出。炉渣由氧化区进入还原区,其中的PbO 被粉煤喷嘴喷入的粉煤还原,渣含铅逐渐降低,同时还产出铅锌氧化物烟尘和二次粗铅。二次粗铅和一次粗铅合并一起放出,炉渣逆向运动由反应器的另一端放出。为解决铅渣混流,在氧化段与还原段之间增设一道隔墙,耐火材料采用熔铸铬镁砖。
QSL 法曾在德国斯托尔伯格、韩国温山、中国
西北冶炼厂、加拿大特雷尔建厂使用,由于一个炉内氧化、还原气氛控制困难,加之操作难度大,炉衬冲刷侵蚀快,氧枪寿命短,结渣堵塞,烟尘率高(约25%)等问题,中国西北冶炼厂1992年投产,十多年间试车3次合计运行不足12个月而停产至今。特雷尔冶炼厂1989年建成,投产后出现了一系列的工艺和设备问题,喷枪寿命仅2~4天,内衬腐蚀严重,投产3个月就被迫停产,后改造为基夫赛特法。韩国温山经过试车改造,将氧化与还原分开为双室,至今生产正常。德国斯托尔伯格10年来历经多次技术改造,正常至今生产。韩国和德国的生产实践证明,QSL 仍是一种成功的直接炼铅方法。特点如
下:
(1)设备简单,粗铅生产在一台设备内完成;(2)原料适应性较好,可搭配处理电池糊、铅银
渣等含铅较高的二次物料。114 卡尔多炼铅法
卡尔多炼铅法是瑞典波利顿公司开发一项铅冶炼技术。1979年用来处理含铅烟尘的首台有色金属卡尔多熔炼炉在瑞典的隆斯卡尔冶炼厂诞生。1992年伊朗曾姜铅锌总公司用卡尔多炉处理氧化铅精矿生产铅,年生产能力411万t 。到目前为止,世界上已有12台卡尔多炉投产。我国西部矿业公司引进的卡尔多炉于2006年在青海建成投产,设计能力60kt/a 粗铅。
卡尔多炉有多种类型,但基本结构类似,其炉子本体与炼钢氧气顶吹转炉的形状相似,由圆桶形的下部炉缸和喇叭形的炉口两部分组成,内衬为铬镁砖。炉子本体在电机、减速传动机的驱动下,可沿炉缸轴作回转运动。在正常作业的倾角部位,设有烟罩和烟道,将炉气引入收尘系统,输送燃油和氧气的燃烧喷枪以及输送精矿的加料喷枪通过烟罩从炉口插入炉内。
卡尔多炉是一台倾斜氧气顶吹转炉,加料、氧化、还原、放渣/放铅四个冶炼步骤在一台炉内完成,周期性作业。还原期炉烟气SO 2很少,不得不在氧化期吸收、压缩冷凝一部分SO 2为液体,在还原期再气化后补充到烟气中以维持烟气制酸系统的连续运行,操作麻烦。115 氧气顶吹浸没熔炼法(澳斯麦特法、艾萨法)
氧气顶吹浸没熔炼法是20世纪70年代澳大利亚开发成功的铜冶炼技术,后移植于铅的冶炼。该熔炼技术是在一个圆桶形的炉内,通过炉子顶端斜烟道的开孔,插入一支由空气冷却的钢制喷枪。喷枪位于内衬耐火材料的炉膛中央,头部埋于熔体中,燃料和空气通过喷枪直接喷射到高温熔融渣层中,产生燃烧反应并造成熔体的剧烈搅动,进行物料的氧化脱硫,产出部分粗铅和富铅渣。这样,在一个小空间内加入的炉料被迅速加热熔化并完成化学反应。调整喷枪的插入深度可以控制熔体搅拌强度,操作灵活,炉子能在较长时间内保持热稳定。熔炼产出的富铅渣经铸渣机浇注成渣块,再送入鼓风炉还原熔炼,生产粗铅和炉渣。
喷枪是该炉子的核心部件,它为双层套管结构,上段材质为45#钢,下段喷口为不锈钢。内管通过燃料即油或用定量空气携带的煤粉。内外管间设有
螺旋形导流片,助燃空气(或富氧空气)从此通道中以大于两倍音速呈旋涡状流出,加大了枪体与气体间的传热,从而在喷枪外表面形成一层冷却的渣壳,此渣壳保护喷枪,延长了喷枪的使用寿命。顶吹熔池熔炼炉对入炉物料要求不高,不论是粒状物料还是粉状精矿、烟尘返料等,只要水分小于10%,均可直接入炉。若为粉状物料,经配料、制粒后入炉有利于降低烟尘率。该法由于主体设备结构简单,辅助、附属设备不复杂,与基夫赛特法、QSL法相比,基建投资较低。
氧气顶吹浸没熔炼法属于二段炉炼铅法,用氧化炉熔炼取代了传统炼铅工艺的烧结,氧化炉烟气量小、烟气SO2浓度高,解决了烧结过程低浓度SO2的污染问题,90%以上的硫得到回收利用,对环境污染小,且劳动卫生条件比传统法有很大改善。但由于氧化段只有约40%的铅以粗铅形式产出,富铅渣不能直接还原而必须浇注成渣块,高温富铅渣的大量显热无法利用,而在鼓风炉还原熔炼又需要配入大量的焦炭,因此其能耗很高。
氧气顶吹浸没熔炼法基本上属于熔池熔炼法,熔池气、固、液搅动激烈,对炉体冲刷严重,炉寿较短。另外,艾萨炉喷枪造价很高。
两段炉直接炼铅不是彻底、完善的直接炼铅工艺,如果澳斯麦特法进一步改进实现熔融物料转移在第2台竖炉中还原,不用鼓风炉还原,则可进一步改善劳动条件,减轻污染,节约能耗,但直至现在一些澳斯麦特法炼铅厂家对竖炉还原未予认同,仍然采用鼓风炉还原。所以从炉寿命、能耗、生产操作条件方面考虑,现阶段的氧气顶吹浸没熔炼法还不是理想的直接炼铅方案。
值得关注的是,澳斯麦特公司在印度锌公司已用1台澳斯麦特炉进行氧化熔炼、还原熔炼、炉渣烟化处理,1炉3用,粗铅生产能力达50kt/a,取得工业化成功,已开始实践原研发宗旨。这种1炉多用的澳斯麦特炉,原料适应性广、备料简单、工序少,投资省,是一种较好的工艺技术,但还原期、烟化期烟气要配入SO2方能连续制酸是其美中不足的地方。116 水口山炼铅法
水口山炼铅法又称氧气底吹熔炼法,是我国20世纪80年代在借鉴QSL法的基础上开发出来的。使用的反应器保留了QSL法的氧化段,而取消了还原段,氧气由熔池底部吹入,产出富铅渣和部分粗铅,富铅渣同样需要经铸渣机浇注成渣块,再送入鼓风炉还原熔炼,产出粗铅和炉渣。
但和氧气顶吹浸没熔炼法不同,氧气底吹熔炼法的炉体结构简单,建设投资较小。
和烧结-鼓风炉还原熔炼工艺相比,氧气底吹熔炼虽然较好地解决了氧化段烟气SO2的污染问题,但由于氧气底吹熔炼技术本身的缺陷,大部分铅只能以铅的氧化物形态和石英、石灰石等熔剂一起造渣,铅一次还原率不到40%。由于高铅液态渣直接还原技术目前尚不成熟,从而不得不把约1200℃的高温熔融渣冷却成熔渣块后,再送鼓风炉内用焦炭加热至约1250℃进行高温还原熔炼,热能利用极不合理。同时,氧气底吹熔炼只适用于含铅大于50%的高铅精矿的处理,而对于含铅40%左右或以下的低品位铅精矿,由于不能自热熔炼和无法在氧气底吹炉直接生产出粗铅,导致炉衬腐蚀严重,使炉体使用寿命大为缩短。另外,和QSL相类似,氧气底吹熔炼的烟尘率同样较高,通常为25%。
2 HUAS闪速炼铅法
2009年9月24日,由北京矿冶研究总院提供主体工艺设备与设计、与灵宝市华宝产业有限责任公司合作开发的10万t/a铅富氧闪速熔炼项目投料试产,25日闪速熔炼炉开始出铅,满负荷连续运行6天后进行了第一次点检,标志着我国第一台具有完全自主知识产权的铅富氧闪速熔炼项目-HUAS闪速炼铅法取得了圆满的成功。
HUAS闪速炼铅法是在借鉴现代铜闪速熔炼并充分吸纳基夫赛特炼铅工艺优点基础上研发的新型闪速炼铅炉,主体设备由一座闪速熔炼炉和一座矿热贫化电炉组成。闪速熔炼炉由三部分组成:圆形的反应塔、设有热焦滤层的矩形沉淀池和直形上升烟道。圆形的反应塔顶设有保温用燃油烧嘴、焦炭管,塔顶中央设有一个中央扩散型精矿喷咀,粉状炉料通过下料管从喷枪咽喉口处给出,氧气在咽喉口成高速射流,将炉料引入并经喇叭口分散成雾状送入反应塔。5~20mm的碎焦经焦炭管加入反应塔。炉料和氧气混合后呈悬浮状在约1450℃的高温下进行氧化反应,约10%的焦炭参与燃烧反应补充反应热。反应后的融熔物料先降落到焦炭层, 80%~90%的PbO与炽热焦炭层产生的CO及C 发生反应被还原成金属铅从沉淀池放铅口虹吸放出,少部分铅进入炉渣,经流槽自流至矿热贫化电炉进行深度还原。反应塔烟气进入沉淀池,以5~7 m/s速度流向直升烟道。为减轻融熔烟尘粘结,上升烟道垂直向上,直接与余热锅炉辐射冷却段相连。
流入贫化电炉、温度约1200℃的闪速炉渣在自焙电极的加热下维持约1250℃以上的还原温度,在炉渣进口处加入碎焦炭并通入压缩空气搅动熔体,通过控制适宜的还原强度,使大部分铅、锌还原,还原产生的锌蒸气和电炉烟气一起经水冷烟道降温、二次吸风燃烧、表冷降温后经布袋除尘器回收,保证外排的电炉渣含铅、锌小于3%。贫化电炉的粗铅从放铅口虹吸放出。
与炼铜闪速炉不同,HUAS闪速炼铅炉在熔池上保持150~200mm厚的焦炭层,熔融物先经焦炭层过滤,PbO与C反应后才进入沉淀池,其次HUAS闪速炼铅炉的上升烟道为直立式,垂直向上与锅炉辐射区连接,与炼铜闪速炉斜升烟道连接辐射冷却室也不相同。与基夫赛特炉不同,HUAS闪速炼铅炉只有反应塔、沉淀池、一个上升烟道,反应塔设有一个中央扩散型精矿喷咀;基夫赛特炉的反应塔、沉淀池与电炉互为一体,有2个上升烟道,其
,反应塔顶设有4个精矿喷嘴,炉体结构复杂。
在操作和控制条件上,HUAS闪速炼铅法也和基夫赛特有本质的区别,如氧势控制、渣型控制、脱硫率控制、冰铜层控制、底铅温度控制等等,正是由于上述操作和控制条件的改变,才确保了铅精矿中伴生铜的高效回收(在原料含铜014%的条件下,可以生产出含铜约8%的冰铜,铜回收率大于85%)。
由上述说明可以看出,HUAS闪速炼铅法在保留基夫赛特炼铅法优点的基础上,具有如下的特点:
(1)炉体结构简单,投资省。同等生产规模下,投资较基夫赛特节省30%以上,且HUAS闪速炼铅的操作和运行条件更稳定;
(2)物料适应性更强。不仅适用于铅精矿的处理,还可以处理湿法炼锌渣、湿法炼铜渣和铅贵金属系统渣,作到铅、锌、铜互补,对铅、锌、铜联合企业更具优势;
(3)铅及伴生有价金属铜锌和贵金属的回收率更高。渣含铅可以降至2%以下,渣含锌可以降至3%以下;渣含铜可以降至011%以下;约9915%的金银在粗铅中得到富集;闪速炉烟灰含锌约2%,含铅大于65%,从而避免了锌在物料中的无效循环。;
(4)烟气量小,烟尘率低,热量损失小,烟气SO2浓度高(>20%),配套电收尘小;
(5)炉体密闭性好,负压下操作烟气逸散少、操作条件好;
(6)和氧气底吹熔炼法相比较,不仅物料的适应性好,而且由于实现了高温熔融炉渣的直接还原,反应热利用充分,能耗很低,热能利用效率高,弃渣无需再经烟化炉处理回收锌、铅。
(7)可以使用廉价的兰碳代替冶金焦做焦炭过滤层,生产费用低。
试生产期间处理的是含铅40%、含锌6%、含铜014%的低品位杂矿(由4种杂料配制而成)。为降低油耗,额外配入3%~5%的碎煤。闪速熔炼日处理炉料600~720t。闪速熔炼渣含铅通常保持在10%~15%(最低降至6%)。经电炉贫化还原,电炉弃渣含铅115%~3%、含锌小于3%、含银4~6 g/t、含金011g/t、含铜小于011%;冰铜含铜8%、含铅32%、含硫16%;粗铅品位大于98%;闪速熔炼烟尘含铅大于65%、含锌小于3%,烟尘率小于6%且全部闭路返回熔炼;电炉烟尘含锌大于45%、含铅小于30%。
正常生产情况下,闪速熔炼可以不消耗柴油,但为了保证生产的稳定运行,塔顶油枪保持30L/h的给油量。
由于建设资金比较紧张,灵宝10万t/a铅富氧闪速熔炼项目余热锅炉产生的蒸汽除部分供物料干燥使用外,大部分直接排空,热能浪费较大。能耗方面,如果不考虑余热锅炉的蒸汽利用,按目前日处理600t含铅约40%的物料计算,吨粗铅综合能耗按老标准(1kW?h电=01404kg标煤)计算约443 kg标煤/t,按新标准(1kW?h电=011229kg标煤)计算约317kg标煤。如果考虑蒸汽的利用,按老标准约362kg标煤,按新标准约236kg标煤。
3 结语
经北京矿冶研究总院冶金研究设计所和灵宝市华宝产业有限责任公司2年多的努力,我国第一台具有完全自主知识产权的铅富氧闪速熔炼项目-HUAS闪速炼铅法最终取得了圆满的成功,试生产期间取得的多项技术经济指标表明,我国铅冶炼技术已跨入了世界先进水平行列。
参考文献
[1]何蔼平.面向二十一世纪我国铅冶炼技术的改造和发展
思考[J].有色金属(冶炼部分),2000(6):2-6.
[2]徐培伦.西北铅锌冶炼厂QSL反应器开炉实践[J].有
色冶炼,1998(7):17-19.
(下转第17页)
能源公司测试提供。
5 结论
经过分离的废锌极板进行连续循环的浸出-电积锌粉-制作锌阳极板的工艺是可行的。与树脂分离的废锌渣溶解浸出-还原电解的条件为:浸出介质为氢氧化钾溶液,浓度6~8mol/L,电解电流密度1800~2000A/m2左右,电解液循环量800 mL/min,溶液中Zn2+浓度20~25g/L,电解温度35℃,刮粉间隔时间1~2h。所得锌粉放电活性较好,适合作为锌-空气电池用锌粉。
参考文献
[1]叶红齐,李艳红,赖延清.碱性锌—空气电池的研究现状
[J].电源技术,2003,27(2):108-112.
[2]褚有群,马淳安,张文魁.碱性锌空气电池的研究进展
[J].电池,2002,32(5):294-297.
[3]马文保.可再充锌空气电池的发展[J].电源技术,2002,
26(6):448-451.
[4]徐采栋,林蓉,汪大成.锌冶金物理化学[M].上海:上海
科学技术出版社,1979:16-22.
[5]彭容秋.锌冶金[M].长沙:中南大学出版社,2005:103
-106.
(上接第13页)
[3]林廷芳.水口山炼铅法(SKS炼铅法)的新进展[A].//
全国重冶新技术新工艺成果交流大会文集[C].北京, 1998:144-149.
[4]郭森魁.火法炼铅新工艺和设备[J].上海有色金属,
2002,23(1):20-23.
[5]李东波.氧气底吹熔炼-鼓风炉还原炼铅新技术及应用
[J].有色金属(冶炼部分),2003(5):13-14,17.[6]游力挥.科明科公司特累尔冶炼厂新的铅冶炼系统[J].
中国有色冶金,2004(6):40-46.
[7]李东波.论我国中型炼铅厂的技改途径[J].有色金属
(冶炼部分),1997(4):12-15.
[8]叶国萍.基夫赛特炼铅法[J].有色金属(冶炼部分),
2000(4):20-24.
[9]A Perllo.维斯麦港基夫塞特炼铅厂的投产与生产指标
[J].有色冶炼,1989(4):1-7,48.