水轮机主轴密封结构的优化改造
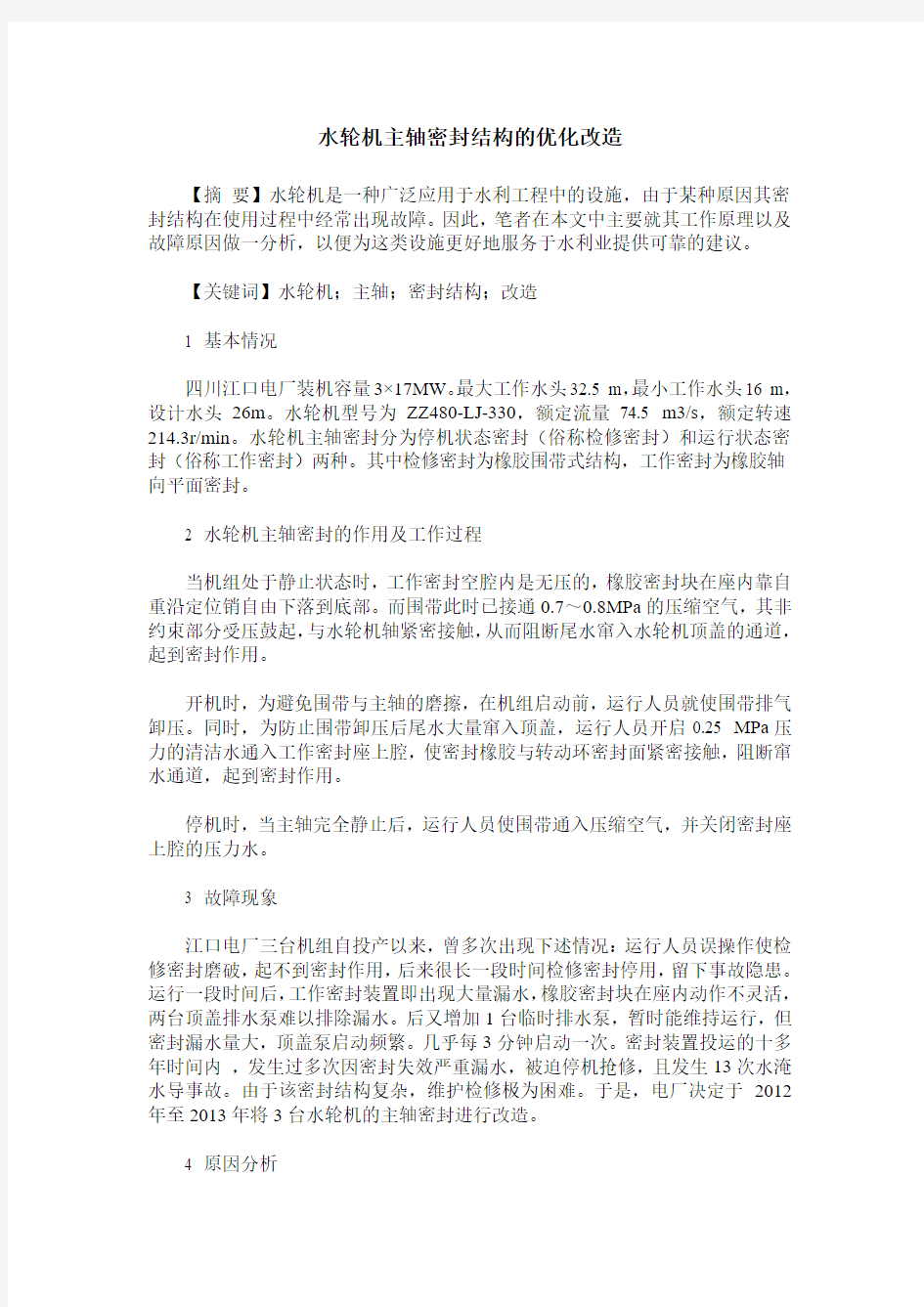

水轮机主轴密封结构的优化改造
【摘要】水轮机是一种广泛应用于水利工程中的设施,由于某种原因其密封结构在使用过程中经常出现故障。因此,笔者在本文中主要就其工作原理以及故障原因做一分析,以便为这类设施更好地服务于水利业提供可靠的建议。
【关键词】水轮机;主轴;密封结构;改造
1 基本情况
四川江口电厂装机容量3×17MW。最大工作水头32.5 m,最小工作水头16 m,设计水头26m。水轮机型号为ZZ480-LJ-330,额定流量74.5 m3/s,额定转速214.3r/min。水轮机主轴密封分为停机状态密封(俗称检修密封)和运行状态密封(俗称工作密封)两种。其中检修密封为橡胶围带式结构,工作密封为橡胶轴向平面密封。
2 水轮机主轴密封的作用及工作过程
当机组处于静止状态时,工作密封空腔内是无压的,橡胶密封块在座内靠自重沿定位销自由下落到底部。而围带此时已接通0.7~0.8MPa的压缩空气,其非约束部分受压鼓起,与水轮机轴紧密接触,从而阻断尾水窜入水轮机顶盖的通道,起到密封作用。
开机时,为避免围带与主轴的磨擦,在机组启动前,运行人员就使围带排气卸压。同时,为防止围带卸压后尾水大量窜入顶盖,运行人员开启0.25 MPa压力的清洁水通入工作密封座上腔,使密封橡胶与转动环密封面紧密接触,阻断窜水通道,起到密封作用。
停机时,当主轴完全静止后,运行人员使围带通入压缩空气,并关闭密封座上腔的压力水。
3 故障现象
江口电厂三台机组自投产以来,曾多次出现下述情况:运行人员误操作使检修密封磨破,起不到密封作用,后来很长一段时间检修密封停用,留下事故隐患。运行一段时间后,工作密封装置即出现大量漏水,橡胶密封块在座内动作不灵活,两台顶盖排水泵难以排除漏水。后又增加1台临时排水泵,暂时能维持运行,但密封漏水量大,顶盖泵启动频繁。几乎每3分钟启动一次。密封装置投运的十多年时间内,发生过多次因密封失效严重漏水,被迫停机抢修,且发生13次水淹水导事故。由于该密封结构复杂,维护检修极为困难。于是,电厂决定于2012年至2013年将3台水轮机的主轴密封进行改造。
4 原因分析
浅析数控铣床的主轴结构设计
浅析数控铣床的主轴结构设计 摘要自从我国改革开放之后,我国的工业领域发展就十分迅速,工业化水平不断提高,促进了国民经济的迅速发展,尤其是近几年自动化技术在工业领域中的普遍应用,极大提高了工业生产的质量和效率,其中各种工业生产设备的应用,极大的便利了工业生产活动,数控铣床作为工业生产中的常见设备,在工业生产中的高速度,高精度以及高效率等优势,使其在工业领域中发挥的作用越来越大。在数控铣床结构中,主轴结构无疑是十分关键的,直接影响着数控铣床的应用,所以本文就针对数控铣床的主轴结构设计进行分析,促进数控铣床在工业领域中的应用。 关键词数控铣床;主轴;结构设计 在我国的工业生产领域中,数控铣床作为高速切削技术的主要应用设备,在我国应用十分广泛,有效提高了切削工作的效率和质量,提高了工业生产中的产品加工精度,在高速切削的过程中主轴是极为核心的部件,主轴的结构和质量会直接影响工业生产的质量和效率,所以在现代数控铣床的应用过程中,需要加强对主轴结构的设计,提高主轴的质量,从而促进数控铣床的广泛应用。 1 數控铣床主轴结构特点 主轴是数控铣床结构中最为关键和核心的部件,其主要作用是带动刀具高速旋转,从而实现高速切削,完成加工任务,而在切削工作中,主轴的作用也就具体表现为切削力的承受和为机床提供驱动力。由于主轴在数控铣床的工作中发挥着重要的作用,承受了巨大的压力,所以数控铣床的工作过程中,主轴想要实现高速旋转,保证加工的质量和效率就必须对自身的结构进行优化,保证自身的可靠性,也就是说,需要有良好的静动态特性。 数控铣床的主轴具有一定的结构特点,主要包括: (1)主轴的中心为空心,在其中会装弹簧等装置来固定和使用铣刀,方便铣刀的使用; (2)在主轴的前端会设置一个7:24比例的锥形空洞,在断面上会设置用于将主轴转矩数据传输给铣刀的主轴转矩检测装置; (3)在主轴的后部会设置用于铣刀放松的液压缸,在日常为铣刀进行保护; (4)主轴的运转主要依靠齿轮进行,用齿轮进行变速传动; 2 数控铣床主轴结构的设计优化 2.1 进行设计控制
机械优化设计大作业2011 - 副本
宁波工程学院机械工程学院 机械优化设计大作业 班级 姓名 学号 教师
机械优化设计大作业 1.题目 行星减速器结构优化设计 NGW型行星减速器应用非常广泛。 1.1结构特点 (1)体积小、重量轻、结构紧凑、传递功率大、承载能力高; (2)传动效率高,工作高; (3)传动比大。 1.2用途和使用条件 某行星齿轮减速器主要用于石油钻采设备的减速,其高速轴转速为1300r/min;工作环境温度为-20℃~60℃,可正、反两向运转。 按该减速器最小体积准则,确定行星减速器的主要参数。 2.已知条件 传动比u=4.64,输入扭矩T=1175.4N.m,齿轮材料均选用38SiMnMo钢,表面淬火硬度HRC 45~55,行星轮个数为3。要求传动比相对误差02 ?u。 .0 ≤ 弹性影响系数Z E=189.8MPa1/2;载荷系数k=1.05; 齿轮接触疲劳强度极限[σ]H=1250MPa; 齿轮弯曲疲劳强度极限[σ]F=1000MPa; =2.97;应力校正系数Y Sa=1.52; 齿轮的齿形系数Y Fa 小齿轮齿数z取值范围17--25;模数m取值范围2—6。 注: 优化目标为太阳轮齿数、齿宽和模数,初始点[24,52,5]T
3.数学模型的建立 建立数学模型见图1,即用数学语言来描述最优化问题,模型中的数学关系式反映了最优化问题所要达到的目标和各种约 束条件。 3.1设计变量的确定 影响行星齿轮减速器体积的独立参数为中心轮齿数、齿宽、模数及行星齿轮的个数,将他们列为设计变量,即: x=[x 1 x 2 x 3 x 4 ]T=[z 1 b m c]T [1] 式中:z 1ˉ ̄ 太阳轮齿数;b―齿宽(mm);m—模数(mm);行星轮的个数。通常情况下,行星轮个数根据机构类型以事先选定,由已知条件c=3。这样,设计变量为: x=[x 1 x 2 x 3 ]T=[z 1 b m]T [1] 3.2目标函数的确定 为了方便,行星齿轮减速器的重量可取太阳轮和3个行星轮体积之和来代替,即: V=π/4(d 12+Cd 2 2)b 式中:d 1--太阳轮1的分度圆直径,mm;d 2 --行星轮2的分度圆 直径,mm。 将d 1=mz 1, d 2 =mz 2 ,z 2 =z 1 (u-2)/2代入(3)式整理,目标函数 则为: F(x)=0.19635m2z 1 2b[4+(u-2)2c][1] 式中u--减速器传动比;c--行星轮个数 由已知条件c=3,u=4.64,因此目标函数可简化为: F(x)=4.891x 32x 1 2x 2
主轴密封方式
水轮机主轴密封的几种形式 水轮机主轴密封是水轮机的一项重要保护,它装在水导轴承的下面,以防止压力水从主轴和顶盖(或支持盖)之间渗漏机坑内,淹没水导轴承,破坏水导轴承的工作,影响机组的运行。按水轮机主轴密封的工作性质可以分为检修密封和工作密封。 一、水轮机主轴检修密封。 检修密封是水轮机检修时候工作的一种密封,它是在停机或检修水轮机工作密封和水导轴承时需要的一种轴承密封,它防止在尾水位较高时倒灌进入机坑内。检修密封按其结构型式可以分为空气围带式、机械式和抬机式检修密封。但在实际中大多数运用空气围带检修密封。它主要由固定环和橡胶空气围带组成,在工作时,向空气围带充入0.4~0.7Mpa的空气压力,使空气围带橡皮膨胀,报紧主轴,防止水进入;当开机时,将空气围带里的压缩气体排除,使其收缩,让空气围带与主轴之间保持1.5~2mm的间隙。该检修密封结构简单,操作容易,密封效果好,大多数机组检修密封都用此种结构。 二、水轮机主轴密封工作密封。 工作密封按照密封结构型式可以分为: (一)平板密封。平板密封有单层平板密封和双层平板密封,单层平板密封主要是利用单层橡胶板与固定在主轴上的不锈钢转环端面形成密封,靠水压力进行密封,其结构简单,但密封效果没有双平板密封效果好,使用寿命也没有双平板密封长。双层平板密封效果好,但其结构复杂,抬机时漏水,目前在中小型轴流机组中还应用。 (二)径向密封。径向密封它是由若干块扇形碳精块在钢扇形块内靠弹簧紧压在主轴上,形成一层层的密封,在密封圈内开有小排水孔,将漏出的水由此排出,它主要是在清洁水中密封,在含泥沙水中其耐磨性较差。这种密封结构复杂,安装检修困难,弹簧性能不易保证,磨擦后径向自调量小,所以现在已经基本淘汰被端面密封所代替。 (三)盘根密封。盘根密封是由底封环、盘根、水封环、水封管和压盖等部件组成,它主要是靠底封环和压盖压紧套在中间的盘根,起到密封作用。该密封在小型卧式机组中使用比较普遍。 (四)端面密封。端面密封有机械式和水压式两种。机械端面密封它是依靠弹簧将装有圆形橡胶块的圆盘拖起,使圆形橡胶块和固定在主轴上的不锈刚圆环紧贴起到密封作用。橡胶密封环固定在水轮机的顶盖(或支持盖)上,该种密封结构简单,好调整,但弹簧受力不均匀,容易发生偏卡,磨损,密封性能不稳定。 (五)迷宫环密封。迷宫环密封是近年来出现的一种新型密封。其工作原理是在在水轮机转轮顶部设有泵板装置,由于泵板的吸出作用,主轴法兰始终处于大气之中,轴与轴封间不接触并只有一层空气,
结构优化设计是在满足规范要求
结构优化设计是在满足规范要求、保证结构安全和建筑产品品质的前提下,通过合理的结构布置、科学的计算论证、适度的构造措施,充分发挥材料性能、合理节约造价的设计方法。结构优化设计在当前竞争日益激烈的建筑设计市场成为大势所趋。如何在满足建筑功能的前提下,保证结构安全并控制含钢量成为摆在结构设计工程师面前的现实课题。本文总结了以往的设计经验,参考了相关文献,给出了结构优化设计的步骤和一些具体措施,供设计人员参考。 1结构优化设计的步骤 笔者认为,结构优化设计的合理步骤应该是:①在方案阶段,通过与建筑专业的充分沟通,对建筑的平面布置、立面造型、柱网布置等提出合理的建议和要求,使结构的高度、复杂程度、不规则程度均控制在合理范围内,避免抗震审查,为降低含钢量争取主动权;②在初步设计阶段,通过对结构体系、结构布置、建筑材料、设计参数、基础型式等内容的多方案技术经济性比较,选出最优方案,整体控制含钢量;③在具体计算过程中,通过精确的荷载计算、细致的模型调整,使结构达到最优受力状态,进一步降低用钢量;④在施工图阶段通过精细的配筋设计抠出多余钢筋,彻底降低含钢量。 在进行多方案的技术经济性比较时,应综合考虑材料费、模板费、基坑开挖降水支护费用、措施费、施工难易、工期长短等因素,与甲方协商后择优选用。 2结构体系与布置优化 结构体系和布置对造价影响很大,应予重视。 1)应根据建筑布置、高度和使用功能要求选择经济合理的结构体系。比如,异形柱框架比普通框架用钢量大,在可能的情况下尽量采用前者;短肢剪力墙比普通剪力墙含钢量高,在可能的情况下尽量采用后者。 2)应选择比较规则的平面方案和立面方案。尽量避免平面凸凹不规则或楼板开大洞,控制平面长宽比,合理设缝,使结构刚度中心与质量中心尽量靠近。竖向应避免有过大的外挑或内收,同时注意限制薄弱层、跃层、转换层等不利因素,使侧向刚度和水平承载力沿高度尽量均匀平缓变化。 3)应选择合理、均匀的柱网尺寸,使板、梁、柱、墙的受力合理,从而降低构件的用钢量。柱网大则楼盖用钢量大,柱网小则柱子用钢量增大,应根据建筑实际情况和经验合理布置。例如,住宅中小开间结构中墙柱的作用不能得到充分发挥,过多的墙柱还会导致较大的地震作用,可考虑采用大开间结构体系,既节约造价,又便于建筑灵活布置。 4)应选择经济合理的楼盖体系。楼盖质量大,层数多,占整体造价比重高,对楼盖的类型、构件的尺寸、数量、间距等应进行对比分析,选择最优的方案。一般住宅宜采用现浇梁板楼盖,预应力楼盖的预应力钢筋容易被二次装修破坏,井字梁楼盖影响室内美观,均不推荐。办公楼等大空间结构宜采用十字梁、井字梁、预应力梁板方案。双向板比单向板经济,应多做双向板。板的厚度,双向板宜控制在短跨的1/35,单向板宜控制在短跨的1/30,此时板易满足强度和变形要求,经济性好。 5)剪力墙结构的优化空间很大,应下大力气优化。剪力墙的布置宜规则、均匀、对称,以控制结构扭转变形。在满足规范和计算的前提下应尽量减少墙的数量,限制墙肢长度,控制连梁刚度,剪力墙能落地的就全部落地不做框支转换层,平面能布置成大开问的尽量布置成大开间,墙体的厚度满足构造要求和轴压比的要求即可。连梁刚度太大时可通过梁中开水平缝变成双梁、增大跨高比等措施降低连梁刚度。尽量少用短肢剪力墙,限制“一”字墙,少做转换。 6)降低含钢量的小技巧:①楼电梯间不宣布置在房屋端部或转角处。因其空间刚度较小,设在端部对抗扭不利,设在转角处应力集中。②框架结构层刚度较弱时,加大柱尺寸或梁高都可显著增大层刚度,而提高混凝土强度效果不明显。③柱的截面尺寸,多层宜2层~3层
机床主轴的动力学建模及优化设计
前言 机床主轴的性能正在向高转速、高精 度、高刚度方向发展,通过对机床主轴动 态特性的有限元分析,为改善机床主轴的 静动态特性提供必要的理论依据和数据, 不仅能在产品设计阶段就能对主轴部件动 机床主轴的 动力学建模及优化设计 吴化勇 山东理工大学工程技术学院 255012 态特性作出符合实际的预测并提出改进方 向,还可以在短时间内作出多种方案比 较,使机床主轴实现优化设计,进而提高 产品一次设计成功率、缩短产品开发周 期,提高加工中心产品的设计水平。 1 主轴部件的有限元建模 CA6140机床主轴为阶梯轴,可以简 化为一个线弹性系统,其运动微分方程可 以写为: (1) 图1 力学模型 图1(a) 有限元模型 图2(e) 五阶模态的振型图 最大变形位于主轴后端位置,最大位移量0.793619mm。 图2(d) 四阶模态的振型图 最大变形位于主轴前端位置,最大位移量0.326109 mm。 图2(c) 三阶模态的振型图 最大变形位于主轴中间位置,但与二阶模态变形的方向不 同,最大位移量0.291149 mm。 图2(b) 二阶模态的振型图 最大变形位于主轴中间位置,最大位移量为0.280559mm。 图2(a) 一阶模态的振型图 最大变形遍布于整个主轴,最大位移量为0.39574mm。 图2 五阶模态的列表显示
式中,[M]、[C]、[K]分别为系统的总体质量、阻尼和刚度矩阵;{δ(t)}、{R(t)}分别为节点的位移和外力矢量。 简化后的力学模型如图1所示。 其中Fr, Ft分别表示主轴上大齿轮所 受轴向力和切向力。F2表示刀具对工件的 主切削力。T1表示由Ft产生的扭矩,T2 表示F3产生的扭矩。应用体单元建立其结构有限元模型,如图1(a)所示。根据力学模型对其施加约束与载荷,模态提取方法选用子空间方法。根据力学模型对其施加约束与载荷,模态提取方法选用子空间方法。其前三阶固有频率分别为:f1=52.75Hz;f2=84.37Hz;f3=117.00Hz。前三阶固有频率的振型分别对应于图2(a)、(b)、(c)。五阶模态的列表显示如图2。五阶模态的振型图如图2(a)(b)(c) (d) (e)。由上述结果明显看出,各阶振型的分布状况及位移大小,高阶模态的位移量变化较大,前五阶最大值为0.793619mm,模态分析结果为改进主轴动态特性提供了理论依据。2 主轴部件的优化设计 优化设计问题描述:材料的弹性模量:E=2.1×108 MPa材料的许用应力:σ=200 MPa 需要简化有限元分析模型,因为主轴左端没有载荷作用,所以为了方便建模和减少设计变量,只对主轴中间支撑和右端支撑之间的部分进行优化设计。长度固定不变,只优化横截面,因为密度一定,所 以求体积最小转化为求质量最小。 有限元优化分析模型如图3。建立结构优化设计的模型:Min f﹙x﹚ X=〔X1,X2,X3,X4,X5,X6〕=〔A1,A2,A3,A4,A5,A6〕 s.t. σ≤〔σ〕0.020≤A1≤0.0260.035≤A2≤0.0450.035≤A3≤0.0500.035≤A4≤0.0530.035≤A5≤0.058 0.035≤A6≤0.100注:横截面积的单位为m。 其中,f﹙x﹚表示主轴的重量,A1、A2、A3、A4、A5、A6分别代表图3中所表明的变量。优化后的结果与优化前进行比较,如表1。 从表1中可以明确看出,在满足设计要求的情况下,能够减小横截面积,从而减轻主轴的重量(优化后的重量为14.436千克),实现对主轴结构的优化,可以节省材料。但是受到结构方面的限制,A6的值仍为100mm。 3 优化后的主轴动态分析 (1)使用相同的方法对优化后的主轴进行动态分析,得出5阶模态的频率及 表1 优化结果比较 (单位:mm) 表2 优化前后模态分析结果比较 (单位:Hz) 图4 五阶模态的列表显示 图3 优化分析模型 其它信息,如图4。 (2)对原主轴与优化后主轴的模态分析结果比较,如表2。 机床的转速范围为10~1400r/min,都不会发生共振,优化后的主轴在工作过程更远离共振发生的区域,满足要求。 4 结论 通过对机床主轴的动态模型建立并对其进行优化分析,在主轴设计阶段即得出相关结论。
数控机床主轴结构的改进和优化设计
数控机床主轴结构的改进和优化设计 严鹤飞 (天水星火机床有限责任公司技术中心 甘肃 天水 741024) 摘 要: 掌握机床主轴的关键部件,安装方式,轴承的调制环节以及材料、操作维护等,并且各种原因中又包含着多种影响因素互相交叉,因此必须对每个影响因素作具体分析。而对于优化设计理论的基本思想及其求解方法,将其应用于机床主轴的结构设计,建立了机床主轴结构优化设计的数学模型,并用内点惩罚函数法求解模型,得到了整体最优的结构设计方案,使机床主轴在满足各种约束要求条件下,刚度最好,材料最省。 关键词:机床主轴;轴承;调整;优化设计;数学模型 在数控机床中,主轴是最关键的部件,对机床起着至关重要的作用,主轴结构的设计首先考虑的是其需实现的功能,当然加工及装配的工艺性也是考虑的因素。 1. 数控机床主轴结构改进: 目前机床主轴设计普遍采用的结构如图1所示。图中主轴1支承在轴承4、5、8上,轴承的轴向定位通过主轴上的三个压块紧锁螺母3、7、9来实现。主轴系统的精度取决于主轴及相关零件的加工精度、轴承的精度等级和主轴的装配质量。在图1中主轴双列圆锥滚子轴承4的内锥孔与主轴1:12外锥配合的好坏将直接影响株洲的工作精度,一般要求其配合接触面积大于75%,为了达到这一要求,除了在购买轴承时注意品牌和等级外,通常在设计时对主轴的要求较高,两端的同轴度为0.005mm,对其相关零件,如螺母3、7、9和隔套6的端面对主轴轴线的跳动要求也较高,其跳动值一般要求在0.008mm以内。对一般压块螺母的加工是很难保证这么高的精度的,因而经常出现主轴精度在装配时超差,最终不得不反复调整圆螺母的松紧,而勉强达到要求,但这样的结果往往是轴承偏紧,精度稳定性差,安装位置不精确,游隙不均匀,造成工作时温升较高,噪音大,震动厉害,影响工件的加工质量和轴承的寿命。但对于重型数控机床用圆锥滚子轴承其承载负荷大,运转平稳,精度调整好时,其对机床的精度保持性较好,可对与轻型及高速机床就不十分有力了。 图1 通用机床主轴结构图 1— 主轴;2—法兰盘;3—圆螺母;4—双列圆柱滚子轴承;5—球轴承 6— 调整垫;7—圆螺母;8—双列圆柱滚子轴承;9-螺母
数控机床主轴部件结构
数控机床主轴部件结构 主轴部件是数控机床的核心部件,其运转精确度、耐磨性能、防震性能、机械强度等都会影响到工件加工的质量,再加上操作过程中还会有环境的影响以及人为因素的影响,工件加工的质量就更难得到保证。所以要从可控的方面着手,将一切可控因素都调整到位,比如数控机床的主轴结构设计以及主轴结构的日常维护等。 目前所使用的数控机床类型主要包括数控车床、数控铣床以及工件加工中心。 1.数控车床主轴部件结构特点 (1)主轴的主体结构是一个空心阶梯轴。 (2)主轴的前面部分主要由法兰盘和专门的卡盘结构组成。 (3)主轴的后面部分放置回转油缸。 (4)主轴空心部分用于设置油缸的活塞杆。 (5)车床的传动装置主要有齿轮传动、传送带传送以及齿轮-传送带组合传动等方式。 (6)驱动器主要作用是连接电动机,驱动数控车床的运转。 (7)光电脉冲编码器,用于测量主轴的转动速度,并
及时反馈信息至数控系统。 (8)回转油缸的主要作用是通过调整液压来控制卡盘装置与法兰盘的结合与分离。 2.数控铣床主轴部件结构特点 (1)同数控车床一样,主轴的中心是空心的。 (2)主轴的前面部分是一个比例为7:24的锥型孔洞,并且在端面上设有一对专门的主轴转矩检测装置将主轴转矩数据传输给铣刀。 (3)主轴的后面部分设有液压缸装置用于放松铣刀。 (4)主轴中间的空心部分用于弹簧的安装、以及铣刀固定刀爪的安装等。 (5)主轴的传动装置主要是齿轮传动,而且是变速传动。 (6)电气结构与数控车床相似,驱动器用于连接电动机,驱动数控铣床的运转;光电脉冲编码器,用于测量主轴的转动速度,并及时反馈信息至数控系统;液压缸的主要作用是通过调整液压来控制回路。 3.工件加工中心主轴部件结构特点 工件加工中心主轴部件的大致结构与数控铣床相类似,唯一不同的地方在于工件加工中心自带刀库和自动换刀的装置,自动化程度相对较高,在控制结构上与数控铣刀会有所不同,具体表现在:
浅谈水轮机主轴密封的几种形式
浅谈水轮机主轴密封的几种形式 [作者] 黔南州水利水电勘测设计研究院徐玲 [摘要] 水轮机主轴密封是水轮机的一项重要保护,它装在水导轴承的下面,以防止压力水从主轴和顶盖(或支持盖)之间渗漏机坑内,淹没水导轴承,破坏水导轴承的工作,影响机组的运行。按水轮机主轴密封的工作性质可以分为检修密封和工作密封。 一、检修密封。检修密封是水轮机检修时候工作的一种密封,它是在停机或检修水轮机工作密封和水导轴承时需要的一种轴承密封,它防止在尾水位较高时倒灌进入机坑内。检修密封按其结构型式可以分为空气围带式、机械式和抬机式检修密封。但在实际中大多数运用空气围带检修密封。它主要由固定环和橡胶空气围带组成,在工作时,向空气围带充入0.4~0.7Mpa的空气压力,使空气围带橡皮膨胀,报紧主轴,防止水进入;当开机时,将空气围带里的压缩气体排除,使其收缩,让空气围带与主轴之间保持1.5~2mm的间隙。该检修密封结构简单,操作容易,密封效果好,大多数机组检修密封都用此种结构。 二、工作密封。工作密封按照密封结构型式可以分为: (一)平板密封。平板密封有单层平板密封和双层平板密封,单层平板密封主要是利用单层橡胶板与固定在主轴上的不锈钢转环端面形成密封,靠水压力进行密封,其结构简单,但密封效果没有双平板密封效果好,使用寿命也没有双平板密封长。双层平板密封效果好,但其结构复杂,抬机时漏水,目前在中小型轴流机组中还应用。 (二)径向密封。径向密封它是由若干块扇形碳精块在钢扇形块内靠弹簧紧压在主轴上,形成一层层的密封,在密封圈内开有小排水孔,将漏出的水由此排出,它主要是在清洁水中密封,在含泥沙水中其耐磨性较差。这种密封结构复杂,安装检修困难,弹簧性能不易保证,磨擦后径向自调量小,所以现在已经基本淘汰被端面密封所代替。 (三)盘根密封。盘根密封是由底封环、盘根、水封环、水封管和压盖等部件组成,它主要是靠底封环和压盖压紧套在中间的盘根,起到密封作用。该密封在小型卧式机组中使用比较普遍。 (四)端面密封。端面密封有机械式和水压式两种。机械端面密封它是依靠弹簧将装有圆形橡胶块的圆盘拖起,使圆形橡胶块和固定在主轴上的不锈刚圆环紧贴起到密封作用。橡胶密封环固定在水轮机的顶盖(或支持盖)上,该种密封结构简单,好调整,但弹簧受力不均匀,容易发生偏卡,磨损,密封性能不稳定。 (五)迷宫环密封。迷宫环密封是近年来出现的一种新型密封。其工作原理是在在水轮机转轮顶部设有泵板装置,由于泵板的吸出作用,主轴法兰始终处于大气之中,轴与轴封间不接触并只有一层空气,该密封有极长的寿命。该主轴密封为不接触迷宫型,由紧靠着轴上的转动套、密封箱和主轴密封排水管等部件组成。在水轮机正常运行情况下,整个负荷范围内密封盒上无水压。转轮上的泵板随转轮一起旋转防止水和固体进入主轴密封,同时泵板排水管防止沙或固体物质积在水机顶盖下,并将透过上止漏环的少量漏水通过泵板排水管排至尾水。在起动和关闭速度降低情况下,水压可能达到轴封,此时由于迷宫环状密封箱的扩散作用使漏水压力大幅度下降,同时位于每个迷宫环之间的主轴密封排水管可有效地防止水漏在封密箱上,并将渗漏水排至电站集水井。该种新型密封已逐步被推广,在多个电站中被应用,且运行效果较好。
机械结构优化设计
机械结构优化设计 ——周江琛2013301390008 摘要:机械优化设计是一门综合性的学科,非常有发展潜力的研究方向,是解决复杂设计问题的一种有效工具。本文重点介绍机械优化设计方法的同时,对其原理、优缺点及适用范围进行了总结,并分析了优化方法的最新研究进展。关键词:优化方法约束特点函数 优化设计是一门新兴学科,它建立在数学规划理论和计算机程序设计基础上,通过计算机的数值计算,能从众多的设计方案中寻到尽可能完善的或最适宜的设计方案,使期望的经济指标达到最优,它可以成功地解决解析等其它方法难以解决的复杂问题,优化设计为工程设计提供了一种重要的科学设计方法,因而采用这种设计方法能大大提高设计效率和设计质量。优化设计主要包括两个方面:一是如何将设计问题转化为确切反映问题实质并适合于优化计算的数学模型,建立数学模型包括:选取适当的设计变量,建立优化问题的目标函数和约束条件。目标函数是设计问题所要求的最优指标与设计变量之间的函数关系式,约束条件反映的是设计变量取得范围和相互之间的关系;二是如何求得该数学模型的最优解:可归结为在给定的条件下求目标函数的极值或最优值的问题。机械优化设计就是在给定的载荷或环境条件下,在机械产品的形态、几何尺寸关系或其它因素的限制范围内,以机械系统的功能、强度和经济性等为优化对象,选取设计变量,建立
目标函数和约束条件,并使目标函数获得最优值一种现代设计方法,目前机械优化设计已广泛应用于航天、航空和国防等各部门。优化设计是20世纪60年代初发展起来的,它是将最优化原理和计算机技术应用于设计领域,为工程设计提供一种重要的科学设计方法。利用这种新方法,就可以寻找出最佳设计方案,从而大大提高设计效率和质量。因此优化设计是现代设计理论和方法的一个重要领域,它已广泛应用于各个工业部门。优化方法的发展经历了数值法、数值分析法和非数值分析法三个阶段。20世纪50年代发展起来的数学规划理论形成了应用数学的一个分支,为优化设计奠定了理论基础。20世纪60年代电子计算机和计算机技术的发展为优化设计提供了强有力的手段,使工程技术人员把主要精力转到优化方案的选择上。最优化技术成功地运用于机械设计还是在20世纪60年代后期开始,近年来发展起来的计算机辅助设计(CAD),在引入优化设计方法后,使得在设计工程中既能够不断选择设计参数并评选出最优设计方案,又可加快设计速度,缩短设计周期。在科学技术发展要求机械产品更新日益所以今天,把优化设计方法与计算机辅助设计结合起来,使设计工程完全自动化,已成为设计方法的一个重要发展趋势。 优化设计方法多种多样,主要有以下几种:1无约束优化设计法;无约束优化设计是没有约束函数的优化设计,无约束可以分为两类,一类是利用目标函数的一阶或二阶导数的无约束优化方法,如最速下降法、共轭梯度法、牛顿法及变尺度法等。另一类是只利用目标函数值的无约束优化方法,如坐标轮换法、单形替换法及鲍威尔法等。此法具有计算
机械结构优化设计
机械结构优化设计 ——周江琛 2013301390008 摘要:机械优化设计是一门综合性的学科,非常有发展潜力的研究方向,是解决复杂设计问题的一种有效工具。本文重点介绍机械优化设计方法的同时,对其原理、优缺点及适用范围进行了总结,并分析了优化方法的最新研究进展。关键词:优化方法约束特点函数 优化设计是一门新兴学科,它建立在数学规划理论和计算机程序设计基础上,通过计算机的数值计算,能从众多的设计方案中寻到尽可能完善的或最适宜的设计方案,使期望的经济指标达到最优,它可以成功地解决解析等其它方法难以解决的复杂问题,优化设计为工程设计提供了一种重要的科学设计方法,因而采用这种设计方法能大大提高设计效率和设计质量。优化设计主要包括两个方面:一是如何将设计问题转化为确切反映问题实质并适合于优化计算的数学模型,建立数学模型包括:选取适当的设计变量,建立优化问题的目标函数和约束条件。目标函数是设计问题所要求的最优指标与设计变量之间的函数关系式,约束条件反映的是设计变量取得范围和相互之间的关系;二是如何求得该数学模型的最优解:可归结为在给定的条件下求目标函数的极值或最优值的问题。机械优化设计就是在给定的载荷或环境条件下,在机械产品的形态、几何尺寸关系或其它因素的限制范围内,以机械系统的功能、强度和经济性等为优化对象,选取设计变量,建立
目标函数和约束条件,并使目标函数获得最优值一种现代设计方法,目前机械优化设计已广泛应用于航天、航空和国防等各部门。优化设计是20世纪60年代初发展起来的,它是将最优化原理和计算机技术应用于设计领域,为工程设计提供一种重要的科学设计方法。利用这种新方法,就可以寻找出最佳设计方案,从而大大提高设计效率和质量。因此优化设计是现代设计理论和方法的一个重要领域,它已广泛应用于各个工业部门。优化方法的发展经历了数值法、数值分析法和非数值分析法三个阶段。20世纪50年代发展起来的数学规划理论形成了应用数学的一个分支,为优化设计奠定了理论基础。20世纪60年代电子计算机和计算机技术的发展为优化设计提供了强有力的手段,使工程技术人员把主要精力转到优化方案的选择上。最优化技术成功地运用于机械设计还是在20世纪60年代后期开始,近年来发展起来的计算机辅助设计(CAD),在引入优化设计方法后,使得在设计工程中既能够不断选择设计参数并评选出最优设计方案,又可加快设计速度,缩短设计周期。在科学技术发展要求机械产品更新日益所以今天,把优化设计方法与计算机辅助设计结合起来,使设计工程完全自动化,已成为设计方法的一个重要发展趋势。 优化设计方法多种多样,主要有以下几种:1无约束优化设计法;无约束优化设计是没有约束函数的优化设计,无约束可以分为两类,一类是利用目标函数的一阶或二阶导数的无约束优化方法,如最速下降法、共轭梯度法、牛顿法及变尺度法等。另一类是只利用目标函数值的无约束优化方法,如坐标轮换法、单形替换法及鲍威尔法等。此法具有计算
机械结构优化设计分析
机械结构优化设计分析 摘要:机械结构优化设计具有综合性和专业性的特点,在设计过程中涉及方面很多,对设计人员的综合素质很高。因此,本文就结合实际情况,如何做好机械结构优化设计展开论述。 关键词:机械结构;设计流程;优化设计 一、机械设计的流程 机械的设计是开发和研究重要组成部分。设计人员在设计过程中,要提高自身设计水平,加快技术创新,为社会发展设计出质量优良的生产和机械。第一,要确立良好的设计目标。机械设计与开发要满足实际需要,能够发挥其自身的功能。第二,要严格遵守设计标准和要求,对具体的内容进行提炼,从而有效的设计任务和目标。第三,在承接设计任务书以后,要坚持合适的原则,明确设计责任;还要组织设计方案,对设计方案进行讨论,重视设计样品机械的关键环节和重要步骤,从而形成最初的设计。第四,要组建优秀的项目团队,对方案进行深入讨论,不断优化设计方案,控制方案变更。第五,要组织专家对设计图纸进行严格的审核,保证设计质量,在图纸完成交付以后,要针对存在的问题做好记录,为以后设计提供借鉴和帮助。第六,在机械创建完成后,要做好机械的验收,设计师要对机械进行检查,保证在发现问题能够及时有效的解决,只有在质量验收合格后,才能进行最后的交付使用。第七,在进行机械安装过程中,设计人员要在安装现场进行全程的监督和控制,做好技术指导。第八,为了保证机电和安装质量,要进行生产鉴定和调试,根据机械使用的效果进行合理的评价和鉴定。在以上设计流程中,缺一不可,需要设计人员不断提高自身设计水平,采用先进的设计理念,保证设计质量。 二、机械设计过程中需要注意的问题 为了保证机械设计质量,设计人员要不断总结经验教训,根据实际情况,树立质量第一的理念,实现机械结构的优化设计。 (一)在机械制造阶段,设计水平直接影响到预期的效果,甚至导致机械不能正常投入使用。因此,在设计过程中,设计人员要与制造人员进行协调,多深入生产现场,认真听取制造工人和设计人员的意见、建议,不断优化机械结构,提高机械的精密度。
水轮机主轴密封冒烟原因分析及对策
水轮机主轴密封冒烟原因分析及对策 1 基本情况 青溪水电厂是低水头径流式水电厂,装机容量4×36 MW。最大工作水头25 m,最小工作水头10 m,设计水头20.5 m。水轮机型号为ZZ500-LH-500,额定流量209.1 m3/s,额定转速125 r/min。水轮机安装高程45.00 m,下游最低发电水位48.51 m。水轮机主轴密封分为停机状态密封(俗称检修密封)和运行状态密封(俗称工作密封)两种。其中检修密封为橡胶围带式结构,工作密封为橡胶活塞式结构。工作密封面高程46.867 m。其结构如图1所示。 图1 水轮机主轴密封结构 2 水轮机主轴密封的作用及工作过程 当机组处于静止状态时,工作密封活塞下腔是无压的,活塞在活塞座内靠自重沿定位销自由下落到底部。而围带此时已接通0.6~0.7 MPa的压缩空气,其非约束部分受压鼓起,与密封环紧密接触,从而阻断尾水窜入水轮机顶盖的通道,起到密封作用。 开机时,为避免围带与主轴的磨擦,在机组启动前,开机继电器就使围带排气卸压。同时,为防止围带卸压后尾水大量窜入顶盖,开机继电器还使0.059 MPa压力的清洁水通入密封活塞下腔,使密封活塞克服重力上升到顶端,阻断窜水通道,起到密封作用。 停机时,当主轴完全静止后,停机继电器使围带通入压缩空气,并关闭密封活塞下腔的压力水,密封活塞自由落下。 3 故障现象 青溪水电厂3号机组自投产以来,已累计运行了28 000多小时。但在2000年9月下旬以来,曾多次出现下述情况:机组开机时,水轮机在开始运转的几分钟内,水车室内浓烟滚滚,且橡胶焦臭味非常浓烈,待机组运转一段时间后,浓烟才被机组旋转的气流渐渐吹散,一切又都恢复正常。
浅谈水轮机主轴密封的几种形式
浅谈水轮机主轴密封的几种形式 水轮机主轴密封是水轮机的一项重要保护,它装在水导轴承的下面,以防止压力水从主轴和顶盖(或支持盖)之间渗漏机坑内,淹没水导轴承,破坏水导轴承的工作,影响机组的运行。按水轮机主轴密封的工作性质可以分为检修密封和工作密封。 检修密封: 检修密封是水轮机检修时候工作的一种密封,它是在停机或检修水轮机工作密封和水导轴承时需要的一种轴承密封,它防止在尾水位较高时倒灌进入机坑内。检修密封按其结构型式可以分为空气围带式、机械式和抬机式检修密封。但在实际中大多数运用空气围带检修密封。它主要由固定环和橡胶空气围带组成,在工作时,向空气围带充入0.4~0.7Mpa的空气压力,使空气围带橡皮膨胀,报紧主轴,防止水进入;当开机时,将空气围带里的压缩气体排除,使其收缩,让空气围带与主轴之间保持 1.5~2mm的间隙。该检修密封结构简单,操作容易,密封效果好,大多数机组检修密封都用此种结构。 工作密封,工作密封按照密封结构型式可以分为: 一、平板密封。平板密封有单层平板密封和双层平板密封,单层平板密封主要是利用单层橡胶板与固定在主轴上的不锈钢转环端面形成密封,靠水压力进行密封,其结构简单,但密封效果没有双平板密封效果好,使用寿命也没有双平板密封长。双层平板密封效果好,但其结构复杂,抬机时漏水,目前在中小型轴流机组中还应用。 二、径向密封。径向密封它是由若干块扇形碳精块在钢扇形块内靠弹簧紧压在主轴上,形成一层层的密封,在密封圈内开有小排水孔,将漏出的水由此排出,它主要是在清洁水中密封,在含泥沙水中其耐磨性较差。这种密封结构复杂,安装检修困难,弹簧性能不易保证,磨擦后径向自调量小,所以现在已经基本淘汰被端面密封所代替。 三、盘根密封。盘根密封是由底封环、盘根、水封环、水封管和压盖等部件组成,它主要是靠底封环和压盖压紧套在中间的盘根,起到密封作用。该密封在小型卧式机组中使用比较普遍。 四、端面密封。端面密封有机械式和水压式两种。机械端面密封它是依靠弹簧将装有圆形橡胶块的圆盘拖起,使圆形橡胶块和固定在主轴上的不锈刚圆环紧贴起到密封作用。橡胶密封环固定在水轮机的顶盖(或支持盖)上,该种密封结构简单,好调整,但弹簧受力不均匀,容易发生偏卡,磨损,密封性能不稳定。 五、迷宫环密封。迷宫环密封是近年来出现的一种新型密封。其工作原理是在在水轮机
机床主轴结构优化设计
机床主轴结构优化设计【教学目标】 1.掌握优化设计方法与传统设计方法在轴设计上的异同 2.学会分析问题 3.掌握确定目标函数、设计变量、约束条件的方法 4.掌握计算方法的选择 【教学重点】 1.学会分析问题 2.掌握确定目标函数、设计变量、约束条件的方法【教学难点】 1.掌握确定目标函数、设计变量、约束条件的方法【教学过程】 一、以工程实际案例引入课题 【比较】轴的传统设计方法 经验法类比法设计更改繁琐且修改量较大 1、按扭转强度条件初步估算轴的直径
2、按弯扭合成强度计算轴的直径 3、按疲劳强度精确校核 4、按静强度条件进行校核 一、数学模型的建立 在设计这根主轴时,有两个重要因素需要考虑。一是主轴的自重;一是主轴伸出端c 点的挠度。 对于普通机床,不要求过高的加工精度,对机床主轴的优化设计,以选取主轴的自重最轻为目标,外伸端的挠度为约束条件。 当主轴的材料选定时,其设计方案由四个设计变量决定。孔径d 、外径D 、跨距l 及外伸端长度a 。由于机床主轴内孔用于通过待加工的棒料,其大小由机床型号决定。不作为设计变量。故设计变量取为 [][]123T T x x x x l da == 机床主轴优化设计的目标函数为 ()()()2213214f x x x x d πρ=+- 再确定约束条件 ()00 g x y y =-≤ 在外力F 给定的情况下,y 是设计变量x 的函数,其值按下式计算 ()23Fa l a y I π+=
()4464I D d π=- ()() ()23130442640 3Fx x x g x y E x d π+=-≤- 刚度满足条件,强度尚有富裕,因此应力约束条件可不考虑。边界约束条件为设计变量的取值范围,即 min max min max min max l l l D D D a a a ≤≤≤≤≤≤ 将所有的约束函数规格化,主轴优化设计的数学模型可表示为: ()()()()()() ()()()()2213223131044221min 32min 42max 53min 14 64/1031/0 1/0 /10 1/0 f x x x x d Fx x x g x y E x d g x x l g x x D g x x D g x x a πρπ=+-+=-≤-=-≤=-≤=-≤=-≤ 二、计算实例。 如图所示的主轴进行优化设计,已知主轴内径d=30mm,外力F=15000N, 许用挠度=0.05mm 。设计变量数n=3, 约束函数个数m=5, 收敛精度
基于ANSYS的机床主轴结构优化设计_杜官将
第12期2011年12月 组合机床与自动化加工技术 Modular Machine Tool &Automatic Manufacturing Technique No.12Dec.2011 文章编号:1001-2265(2011)12-0022-03 收稿日期:2011-05-25 *基金项目:南京工程学院科研基金项目(KXJ08024) 作者简介:杜官将(1967—),男,江苏盐城人,南京工程学院讲师,南京理工大学在读硕士研究生,研究方向为先进制造技术, (E -mail )gujidu@126.com 。 基于ANSYS 的机床主轴结构优化设计 * 杜官将1,2,李东波 2 (1.南京工程学院机械工程学院,南京211167;2.南京理工大学机械学院,南京210094)摘要:运用APDL 建立机床主轴的参数化有限元模型,应用ANSYS 优化设计功能,以主轴的重量为优 化目标,对主轴的支承跨距、外径、悬伸长度和传动件安装位置进行了优化计算,并对优化结果进行了分析。结果表明:主轴结构优化后,在保证机床各种性能的前提下,主轴重量得到有效的减小。关键词:机床主轴;优化设计;ANSYS ;APDL 中图分类号:TH16;TG65 文献标识码:A Optimization Design of the Structure of Machine Tool Spindle Based on ANSYS DU Guan-jiang 1,2 ,LI Dong-bo 2 (1.School of Mechanical Engineering ,Nanjing Institute of Technology ,Nanjing 211167,China ;2.School of Mechanical Engineering ,Nanjing University of Science and Technology ,Nanjing 210094,China )Abstract :A parameterized FEA model of machine tool spindle was established using APDL in ANSYS.Choosing the weight of spindle as the optimizing target ,its bearings distance and the outer diameter and overhang distance between the front spindle and the front bearing and the location of transmission parts were calculated by using the optimized function integrated in ANSYS ,and analysis on the optimized data was made.The result reveals its weight has significantly reduction in meeting various performance of the machine tool. Key words :machine tool spindle ;optimization design ;ANSYS ;APDL 0问题的提出 机床主轴部件是机床实现旋转运动的执行件, 是机床中的一个非常重要的零件,它关系到整个机床的使用性能,机床设计成功与否在一定程度上取决于主轴系统设计的优劣。机床主轴一般为多支撑空心阶梯轴,通常采用二支承或三支承,在主轴上安装有传动件,传递动力和运动,在主轴前轴通常装有刀具或工件,在切削加工过程中,有切削力作用于主轴。因此,机床主轴的优化设计始终是机床设计的一项重要内容。截至目前为止,关于主轴结构的优 化设计,国内外学者已经提出了不少方法[1] 。于国 平利用惩罚函数法对机床主轴结构进行了优化[2] ,沈浩等利用MATLAB 对机床主轴结构进行了优化设计[3],裴大明等采用有限元法对主轴进行了优化[4],宋春明等应用有限元方法对电主轴结构进行了优化[5] 。上述方法中,有的忽略了主轴轴承的特性,把其 看作刚性支承,有的未考虑主轴上传动件的位置、作用 力对主轴的影响,使建立的主轴模型不够准确,对主轴的优化结果产生了一定的影响。本文以普通机床的主轴为研究对象,在考虑主轴传动件位置、作用力及轴承刚度的基础上,利用ANSYS 的APDL 对机床主轴进行参数化建模,利用ANSYS 软件对其进行优化设计,使优化设计结果更接近实际情况。 1 ANSYS 优化设计原理与步骤 1.1 ANSYS 的优化设计原理 机床主轴的优化大多以在一定的约束条件下主轴刚度最好或质量最轻为目标,对轴承的支承跨度、轴径、悬伸长度等进行优化。由于主轴部件结构的复杂性及对主轴性能的更高要求,传统的材料力学分析方法已显得无能为力。有限元法是一种数值计算方法,它能够精确地对大多数机械结构进行结构
机械结构优化设计作业
甘蔗收获机机械台架虚拟样机 结构优化设计 摘要:结构优化设计就是寻求满足约束条件下的最佳构建尺寸、结构形式以及材料配置方式。利用有限元方法对虚拟样机台架结构进行分析,并采用一阶方法对台架进行优化,预估出经验设计结构上的最危险点,并对结构进行改造和优化,可以保证结构综合应力在材料的许用应力范围内,对结构轻量化,合理分配材料,大大缩短研制周期,降低设计成本,为虚拟样机的创新设计可以提供一种新的设计及优化设计方法。 关键词:甘蔗收获机;优化设计;模态分析;一阶方法 引言:甘蔗作为重要经济作物在全世界范围内广泛种植,中国的种植面积在世界位居第三位,成为我国制糖,轻工,化工和能源的重要原料,对整个国民经济的发展都有重要的地位和作用。甘蔗收获包括切梢、切割、清理和装运等工序,为甘蔗生产过程中劳动强度最大,费工费时,成本最高的一个环节。在我国,甘蔗成产机械化程度低,随着人工收获成本的逐年增加,我国糖业面临着巨大的竞争压力,实现甘蔗收获机械化的要求愈加迫切。随着设计理论与设计理念的发展,对虚拟样机进行优化设计能改进凭经验设计出现的缺陷以及预估结构或机构的最危险点,从而对其进行改造和优化,对设计结果及时进行审查,并及时反馈给设计人员,实现了设计过程中的快速反馈,按照优化后的设计方案进行物理样机研制,可以避开预估的缺陷和危险点,从而使结构更趋于合理,降低了制造成本,大大缩短了设计和产品研制周期,还可以保证将错误消灭在萌芽状态。 虚拟样机技术[ 1]为这类创新产品的开发提供了强有力的手段。甘蔗收割机在工作过程中, 要经历扶蔗、砍蔗、输送、断尾以及剥叶等动作, 承受的都是动态载荷, 而结构的固有频率和振型是承受动态载荷结构设计中的重要参数, 因此本文采用通用有限元分析软件ANSYS对甘蔗收割机机架结构部件进行模态分析, 根据机架结构的低阶模态和振型, 确定对机架结构是进行动力刚度优化还是静力强度优化。 1.机架结构模型建立