永磁铁氧体粘结磁粉生产的新进展
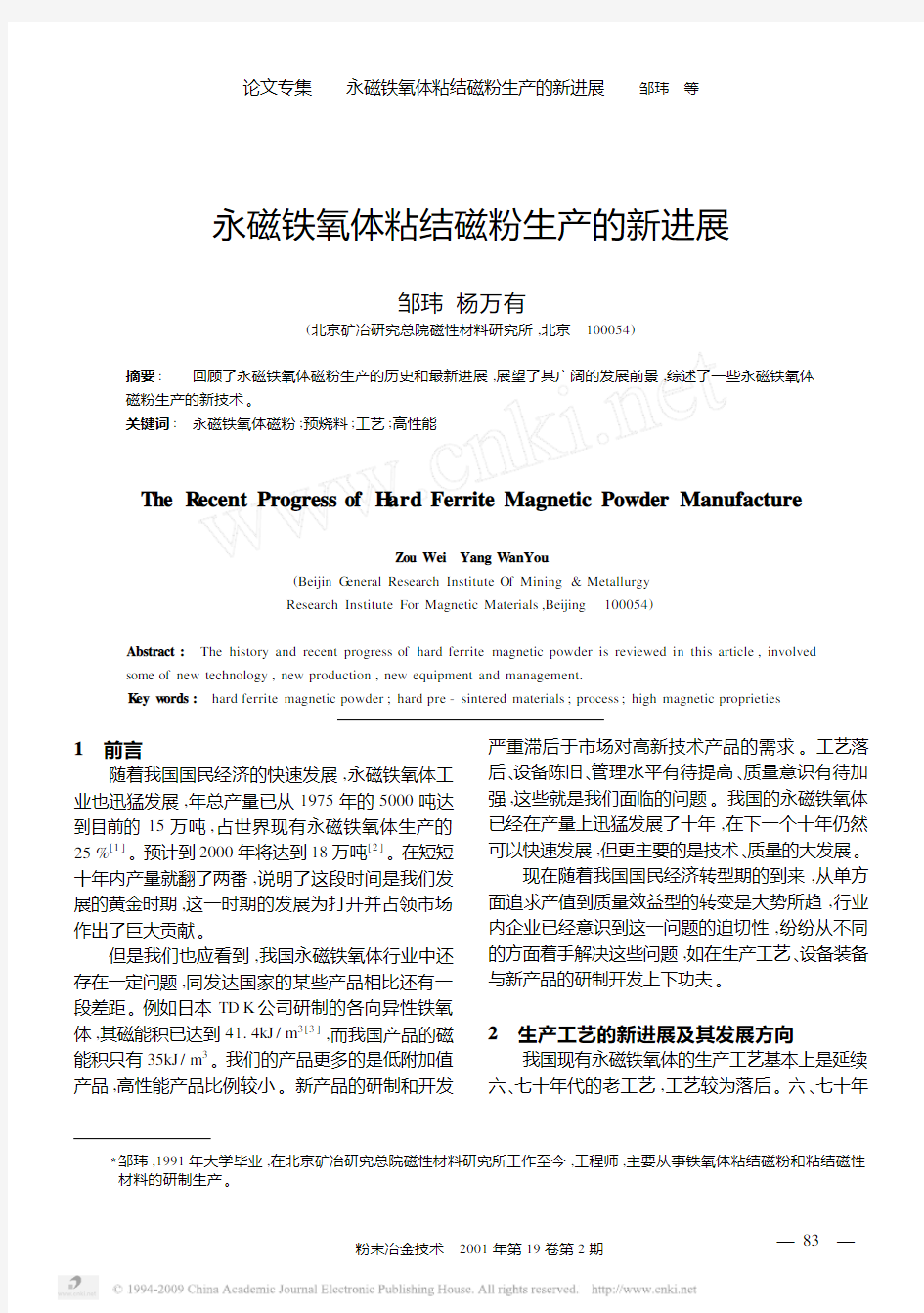
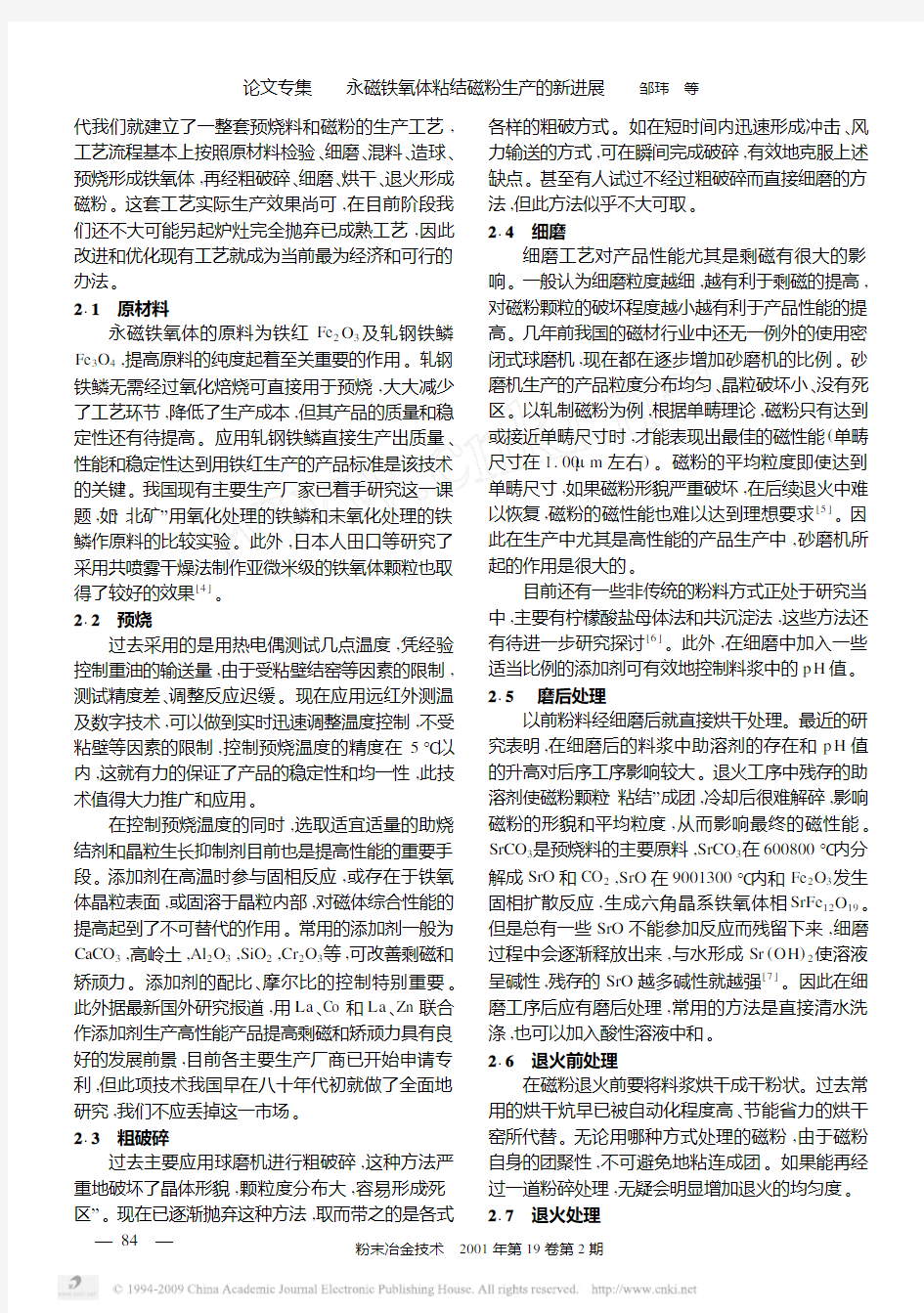
3邹玮,1991年大学毕业,在北京矿冶研究总院磁性材料研究所工作至今,工程师,主要从事铁氧体粘结磁粉和粘结磁性
材料的研制生产。
永磁铁氧体粘结磁粉生产的新进展
邹玮 杨万有
(北京矿冶研究总院磁性材料研究所,北京 100054)
摘要: 回顾了永磁铁氧体磁粉生产的历史和最新进展,展望了其广阔的发展前景,综述了一些永磁铁氧体磁粉生产的新技术。
关键词: 永磁铁氧体磁粉;预烧料;工艺;高性能
The R ecent Progress of H ard Ferrite Magnetic Powder Manufacture
Zou Wei Yang W anYou
(Beijin G eneral Research Institute Of Mining &Metallurgy Research Institute For Magnetic Materials ,Beijing
100054)
Abstract : The history and recent progress of hard ferrite magnetic powder is reviewed in this article ,involved some of new technology ,new production ,new equipment and management.
K ey w ords : hard ferrite magnetic powder ;hard pre -sintered materials ;process ;high magnetic proprieties
1 前言
随着我国国民经济的快速发展,永磁铁氧体工
业也迅猛发展,年总产量已从1975年的5000吨达到目前的15万吨,占世界现有永磁铁氧体生产的25%[1]。预计到2000年将达到18万吨[2]。在短短十年内产量就翻了两番,说明了这段时间是我们发展的黄金时期,这一时期的发展为打开并占领市场作出了巨大贡献。
但是我们也应看到,我国永磁铁氧体行业中还存在一定问题,同发达国家的某些产品相比还有一段差距。例如日本TD K 公司研制的各向异性铁氧体,其磁能积已达到41.4kJ /m 3[3],而我国产品的磁能积只有35kJ /m 3。我们的产品更多的是低附加值产品,高性能产品比例较小。新产品的研制和开发
严重滞后于市场对高新技术产品的需求。工艺落后、设备陈旧、管理水平有待提高、质量意识有待加强,这些就是我们面临的问题。我国的永磁铁氧体已经在产量上迅猛发展了十年,在下一个十年仍然可以快速发展,但更主要的是技术、质量的大发展。
现在随着我国国民经济转型期的到来,从单方面追求产值到质量效益型的转变是大势所趋,行业内企业已经意识到这一问题的迫切性,纷纷从不同的方面着手解决这些问题,如在生产工艺、设备装备与新产品的研制开发上下功夫。
2 生产工艺的新进展及其发展方向
我国现有永磁铁氧体的生产工艺基本上是延续六、七十年代的老工艺,工艺较为落后。六、七十年
—
38—
粉末冶金技术 2001年第19卷第2期
代我们就建立了一整套预烧料和磁粉的生产工艺,
工艺流程基本上按照原材料检验、细磨、混料、造球、预烧形成铁氧体,再经粗破碎、细磨、烘干、退火形成磁粉。这套工艺实际生产效果尚可,在目前阶段我们还不大可能另起炉灶完全抛弃已成熟工艺,因此改进和优化现有工艺就成为当前最为经济和可行的办法。2.1 原材料
永磁铁氧体的原料为铁红Fe 2O 3及轧钢铁鳞Fe 3O 4,提高原料的纯度起着至关重要的作用。轧钢铁鳞无需经过氧化焙烧可直接用于预烧,大大减少了工艺环节,降低了生产成本,但其产品的质量和稳定性还有待提高。应用轧钢铁鳞直接生产出质量、性能和稳定性达到用铁红生产的产品标准是该技术的关键。我国现有主要生产厂家已着手研究这一课题,如“北矿”用氧化处理的铁鳞和未氧化处理的铁鳞作原料的比较实验。此外,日本人田口等研究了得了较好的效果[4]。2.2 预烧
过去采用的是用热电偶测试几点温度,凭经验控制重油的输送量,由于受粘壁结窑等因素的限制,测试精度差、调整反应迟缓。现在应用远红外测温及数字技术,可以做到实时迅速调整温度控制,不受粘壁等因素的限制,控制预烧温度的精度在5℃以内,这就有力的保证了产品的稳定性和均一性,此技术值得大力推广和应用。
在控制预烧温度的同时,选取适宜适量的助烧结剂和晶粒生长抑制剂目前也是提高性能的重要手段。添加剂在高温时参与固相反应,或存在于铁氧体晶粒表面,或固溶于晶粒内部,对磁体综合性能的提高起到了不可替代的作用。常用的添加剂一般为CaCO 3,高岭土,Al 2O 3,SiO 2,Cr 2O 3等,可改善剩磁和矫顽力。添加剂的配比、摩尔比的控制特别重要。此外据最新国外研究报道,用La 、Co 和La 、Zn 联合作添加剂生产高性能产品提高剩磁和矫顽力具有良好的发展前景,目前各主要生产厂商已开始申请专利,但此项技术我国早在八十年代初就做了全面地研究,我们不应丢掉这一市场。2.3 粗破碎
过去主要应用球磨机进行粗破碎,这种方法严重地破坏了晶体形貌,颗粒度分布大,容易形成“死区”。现在已逐渐抛弃这种方法,取而带之的是各式各样的粗破方式。如在短时间内迅速形成冲击、风
力输送的方式,可在瞬间完成破碎,有效地克服上述缺点。甚至有人试过不经过粗破碎而直接细磨的方法,但此方法似乎不大可取。2.4 细磨
细磨工艺对产品性能尤其是剩磁有很大的影响。一般认为细磨粒度越细,越有利于剩磁的提高,对磁粉颗粒的破坏程度越小越有利于产品性能的提高。几年前我国的磁材行业中还无一例外的使用密闭式球磨机,现在都在逐步增加砂磨机的比例。砂磨机生产的产品粒度分布均匀、晶粒破坏小、没有死区。以轧制磁粉为例,根据单畴理论,磁粉只有达到或接近单畴尺寸时,才能表现出最佳的磁性能(单畴
尺寸在1.00
μm 左右)。磁粉的平均粒度即使达到单畴尺寸,如果磁粉形貌严重破坏,在后续退火中难
以恢复,磁粉的磁性能也难以达到理想要求[5]。因此在生产中尤其是高性能的产品生产中,砂磨机所起的作用是很大的。
目前还有一些非传统的粉料方式正处于研究当中,主要有柠檬酸盐母体法和共沉淀法,这些方法还有待进一步研究探讨[6]。此外,在细磨中加入一些适当比例的添加剂可有效地控制料浆中的p H 值。2.5 磨后处理
以前粉料经细磨后就直接烘干处理。最近的研究表明,在细磨后的料浆中助溶剂的存在和p H 值的升高对后序工序影响较大。退火工序中残存的助溶剂使磁粉颗粒“粘结”成团,冷却后很难解碎,影响磁粉的形貌和平均粒度,从而影响最终的磁性能。SrCO 3是预烧料的主要原料,SrCO 3在600800℃内分解成SrO 和CO 2,SrO 在9001300℃内和Fe 2O 3发生固相扩散反应,生成六角晶系铁氧体相SrFe 12O 19。但是总有一些SrO 不能参加反应而残留下来,细磨过程中会逐渐释放出来,与水形成Sr (OH )2使溶液呈碱性,残存的SrO 越多碱性就越强[7]。因此在细磨工序后应有磨后处理,常用的方法是直接清水洗涤,也可以加入酸性溶液中和。2.6 退火前处理
在磁粉退火前要将料浆烘干成干粉状。过去常用的烘干炕早已被自动化程度高、节能省力的烘干窑所代替。无论用哪种方式处理的磁粉,由于磁粉自身的团聚性,不可避免地粘连成团。如果能再经过一道粉碎处理,无疑会明显增加退火的均匀度。2.7 退火处理
—
4
8—
粉末冶金技术 2001年第19卷第2期
在细磨过程中,晶体的形貌和内部结构受到破坏,残余应力和晶格崎变增加,这些缺陷都可以通过退火进行修正。研究表明退火温度不是越高越好,温度升高带来的负面影响是使磁粉平均粒度增大,从而降低磁性能。
由于退火一般采用回转式电窑,在退火过程中又产生了新的粘连和团聚,这又需要重新粉碎。但通常的机械方法又会破坏磁粉的形貌,这样就会抵消退火的作用。因此选择一种粉碎方式代替机械破碎就显得尤为突出。据悉已有几家企业(如北矿)很好地解决了此问题。
3 生产设备与管理
近年来,整个磁性材料行业在设备改造与更新上所取得的成绩是大家有目共睹的。大量的新技术、新产品被广泛应用于各个工艺环节中,其中比较有影响的有回转窑温度实现计算机控制、砂磨机的逐渐普及推广、回转式干燥窑和回转式退火窑的使用。此外,大量地增加了新近研制的辅助设备,如各式粉碎、筛分、分级处理设备,越来越复杂、先进的分析、检验仪器,产品质量即时控制手段等被大量的应用于实践当中。例如,“北矿”的风式粉碎机和激光扫描粒度测量仪都在生产实践中起到了重要的作用。
在今后的设备发展中,大型设备由于投资大、寿命长,其发展更新换代必然受到限制,而小型设备的改造投入少、见效快、效果明显,是大有前途的。有资料表明,国产设备与国外的差距是整体性的,但更重要的是辅助设备的差别。国外磁粉的生产线大多是封闭式的,保证产品内部不搀杂任何杂质;工人少,避免了人为的波动因素,从而确保磁粉的外观质量。由此看来,辅助设备的研制、改进与管理是大有潜力可挖的。
十分喜人的是我国企业近年来的管理水平都有了大幅度的提高,已有多家企业相继取得了ISO9000系列证书,这无疑提高了企业的知名度和产品质量。今后我们应在生产效率的提高上再多下功夫,使我们的管理水平达到并超过世界先进水平。
参考文献
1 第一届海峡两岸磁性技术交流会文集:28.
2 第一届海峡两岸磁性技术交流会文集:28.
3 田口仁等.[日]粉体和粉末冶金,1997,44(1):310.
4 吴安国.磁性材料及器件,1999,30(3):18.
5 许有义等.磁性材料及器件,1998,29,(6):50.
6 吴安国.磁性材料及器件,1999,30(3):18.
7 贾成科.磁性材料及器件,1998,29,(5):5759.
—
5
8
—
粉末冶金技术 2001年第19卷第2期
永磁铁氧体粘结磁粉生产的新进展
3邹玮,1991年大学毕业,在北京矿冶研究总院磁性材料研究所工作至今,工程师,主要从事铁氧体粘结磁粉和粘结磁性 材料的研制生产。 永磁铁氧体粘结磁粉生产的新进展 邹玮 杨万有 (北京矿冶研究总院磁性材料研究所,北京 100054) 摘要: 回顾了永磁铁氧体磁粉生产的历史和最新进展,展望了其广阔的发展前景,综述了一些永磁铁氧体磁粉生产的新技术。 关键词: 永磁铁氧体磁粉;预烧料;工艺;高性能 The R ecent Progress of H ard Ferrite Magnetic Powder Manufacture Zou Wei Yang W anYou (Beijin G eneral Research Institute Of Mining &Metallurgy Research Institute For Magnetic Materials ,Beijing 100054) Abstract : The history and recent progress of hard ferrite magnetic powder is reviewed in this article ,involved some of new technology ,new production ,new equipment and management. K ey w ords : hard ferrite magnetic powder ;hard pre -sintered materials ;process ;high magnetic proprieties 1 前言 随着我国国民经济的快速发展,永磁铁氧体工 业也迅猛发展,年总产量已从1975年的5000吨达到目前的15万吨,占世界现有永磁铁氧体生产的25%[1]。预计到2000年将达到18万吨[2]。在短短十年内产量就翻了两番,说明了这段时间是我们发展的黄金时期,这一时期的发展为打开并占领市场作出了巨大贡献。 但是我们也应看到,我国永磁铁氧体行业中还存在一定问题,同发达国家的某些产品相比还有一段差距。例如日本TD K 公司研制的各向异性铁氧体,其磁能积已达到41.4kJ /m 3[3],而我国产品的磁能积只有35kJ /m 3。我们的产品更多的是低附加值产品,高性能产品比例较小。新产品的研制和开发 严重滞后于市场对高新技术产品的需求。工艺落后、设备陈旧、管理水平有待提高、质量意识有待加强,这些就是我们面临的问题。我国的永磁铁氧体已经在产量上迅猛发展了十年,在下一个十年仍然可以快速发展,但更主要的是技术、质量的大发展。 现在随着我国国民经济转型期的到来,从单方面追求产值到质量效益型的转变是大势所趋,行业内企业已经意识到这一问题的迫切性,纷纷从不同的方面着手解决这些问题,如在生产工艺、设备装备与新产品的研制开发上下功夫。 2 生产工艺的新进展及其发展方向 我国现有永磁铁氧体的生产工艺基本上是延续六、七十年代的老工艺,工艺较为落后。六、七十年 — 38— 粉末冶金技术 2001年第19卷第2期
生产工艺流程图及说明
(1)电解 本项目电解铝生产采用熔盐电解法:其主要生产设备为预焙阳极电解槽,项目设计采用大面六点进电SY350型预焙阳极电解槽。铝电解生产所需的主要原材料为氧化铝、氟化铝和冰晶石,原料按工艺配料比例加入350KA 预焙阳极电解槽中,通入强大的直流电,在945-955℃温度下,将一定量砂状氧化铝及吸附了电解烟气中氟化物的载氟氧化铝原料溶解于电解质中,通过炭素材料电极导入直流电,使熔融状态的电解质中呈离子状态的冰晶石和氧化铝在两极上发生电化学反应,氧化铝不断分解还原出金属铝——在阴极(电解槽的底部)析出液态的金属铝。 电解槽中发生的电化学反应式如下: 2323497094032CO Al C O Al +?-+℃ ℃直流电 在阴极(电解槽的底部)析出液态的金属铝定期用真空抬包抽出送往铸造车间经混合炉除渣后由铸造机浇铸成铝锭。电解过程中析出的O 2同阳极炭素发生反应生成以CO 2为主的阳极气体,这些阳极气体与氟化盐水解产生的含氟废气、粉尘等含氟烟气经电解槽顶部的密闭集气罩收集后送到以Al 2O 3为吸附剂的干法净化系统处理,净化后烟气排入大气。被消耗的阳极定期进行更换,并将残极运回生产厂家进行回收处置。吸附了含氟气体的截氟氧化铝返回电解槽进行电解。 电解槽是在高温、强磁场条件下连续生产作业,项目设计采用大面六点进电SY350型预焙阳极电解槽,是目前我国较先进的生产设备。电解槽为6点下料,交叉工作,整个工艺过程均自动控制。电解槽阳极作业均由电解多功能机组完成。多功能机组的主要功能为更换阳极、吊运出铝抬包出铝、定期提升阳极母线、打壳加覆盖料等其它作业。 (2)氧化铝及氟化盐贮运供料系统 氧化铝及氟化盐贮运系统的主要任务是贮存由外购到厂的氧化铝和氟化盐 ,并按需要及时将其送到电解车间的电解槽上料箱内。
永磁铁氧体材料项目可行性研究报告
永磁铁氧体材料项目可行性研究报告 项目可行性报告 中金企信国际咨询公司拥有10余年项目可行性报告撰写经验,拥有一批高素质编写团队,卓立打造一流的可行性研究报告服务平台为各界提供专业可行的报告。 项目可行性报告用途 1、企业投融资 此类研究报告通常要求市场分析准确、投资方案合理、并提供竞争分析、营销计划、管理方案、技术研发等实际运作方案。 2、项目立项 此文件是根据《中华人民某某国行政许可法》和《国务院对确需保留的行政审批项目设定行政许可的决定》而编写,是大型基础设施项目立项的基础文件,国家发改委根据可行性研究报告进行核准、备案或批复,决定某个项目是否实施。另外医药企业在申请相关证书时也需要编写可行性研究报告。 3、银行贷款申请 商业银行在贷款前进行风险评估时,需要项目方出具详细的可行性研究报告,对于国内银行,该报告由甲级资格单位出具,通常不需要再组织专家评审,部分银行的贷款可行性研究报告不需要资格,但要求融资方案合理,分析正确,信息全面。另外在申请国家的相关政策支持资金、工商注册时往往也需要编写可行性研究报告,该文件类似用于银行贷款的可研报告。 4、申请进口设备免税
主要用于进口设备免税用的可行性研究报告,申请办理中外合资企业、外资企业项目确认书的项目需要提供项目可行性研究报告。 5、境外投资项目核准 企业在实施走出去战略,对国外矿产资源和其他产业投资时,需要编写可行性研究报告报给国家发展和改革委或省发改委,需要申请中国进出口银行境外投资重点项目信贷支持时,也需要可行性研究报告。 6、政府资金项目申报 企业为获得政府的无偿资助,需要对公司项目进行策划、设计、技术创新、技术规划等,编写的可行性研究报告包含管理团队、技术路线、方案、财务预测等,是政府无偿资助的项目申报的主要依据。 项目可行性报告分类 可行性研究报告分为:政府审批核准用可行性研究报告和融资用可行性研究报告。 (1)审批核准用的可行性研究报告侧重关注项目的社会经济效益和影响;具体概括为:政府立项审批,产业扶持,中外合作、股份合作、组建公司、征用土地。 (2)融资用报告侧重关注项目在经济上是否可行。具体概括为:银行贷款,融资投资、投资建设、境外投资、上市融资、申请高新技术企业等各类可行性报告。 国统调查报告网(即中金企信国际咨询公司)以专业的服务理念、完善的售后服务体系为各界提供精准、权威的项目可行报告。 【报告说明】 可行性研究报告,简称可研,是在制订生产、基建、科研计划的前期,通过全面的调查研究,分析论证某个建设或改造工程、某种科学研究、某项商务活动切实可行而提出的一种书面材料。
1.铁氧体材料发展及分类
铁氧体 中文名称:铁氧体 英文名称:ferrite 定义:由以三价铁离子作为主要正离子成分的若干种氧化物 组成,并呈现亚铁磁性或反铁磁性的材料。 铁氧体是一种具有铁磁性的金属氧化物。就电特性来说,铁氧体的电阻率比金属、合金磁性材料大得多,而且还有较高的介电性能。铁氧体的磁性能还表现在高频时具有较高的磁导率。因而,铁氧体已成为高频弱电领域用途广泛的非金属磁性材料。由于铁氧体单位体积中储存的磁能较低,饱合磁化强度也较低(通常只有纯铁的1/3~1/5),因而限制了它在要求较高磁能密度的低频强电和大功率领域的应用。 简介 铁氧体(ferrites)是一种非金属磁性材料,它是由三氧化二铁和一种或几种其他金属氧化物(例如:氧化镍、氧化锌、氧化锰、氧化镁、氧化钡、氧化锶等)配制烧结而成。它的相对磁导率可高达几千,电阻率是金属的1011倍,涡流损耗小,适合于制作高频电磁器件。铁氧体有硬磁、软磁、矩磁、旋磁和压磁五类。 旧称铁淦氧磁物或铁淦氧,其生产过程和外观类似陶瓷,因而也称为磁性瓷。铁氧体是铁和其他一种或多种适当的金属元素的复合氧化物。性质属于半导体,通常作为磁性介质应用,铁
氧体磁性材料与金属或合金磁性材料之间最重要的区别在于导 电性。通常前者的电阻率为102~108Ω·cm,而后者只有10-6~10-4Ω·cm。 发展历史 中国最早接触到的铁氧体是公元前 4世纪发现的天然铁氧体,即磁铁矿(Fe3O4),中国所发明的指南针就是利用这种天然磁铁矿制成的。到20世纪30年代无线电技术的发展,迫切地要求高频损耗小的铁磁性材料。而四氧化三铁的电阻率很低,不能满足这一要求。1933年日本东京工业大学首先创制出含钴铁氧体的永磁材料,当时被称为OP磁石。30~40年代,法国、 日本、德国、荷兰等国相继开展了铁氧体的研究工作,其中荷兰菲利浦实验室物理学家J.L.斯诺克于1935年研究出各种具有优良性能尖晶石结构的含锌软磁铁氧体,于1946年实现工业化生产。1952年,该室J.J.文特等人曾经研制成了以 BaFe12O19为主要成分的永磁性铁氧体。这种铁氧体与1956年该室的G.H.永克尔等人所研究的四种甚高频磁性铁氧体具有类似的六角结构。1956年E.F.贝尔托和 F.福拉又报道了亚铁磁性的Y3Fe5O12的研究结果。其中代换离子Y有Pm、Sm、Eu、Gd、Tb、Dy、Ho、Er、 Tm、Yb和Lu等稀土离子。由于这类磁性化合物的晶体结构与天然矿物石榴石相同,故将其称之为石榴石结构铁氧体。迄今为止,除了1981年日本杉本光男采用超急冷法制得的非晶结构的铁氧体
电机磁铁粘接胶
电机磁铁粘接胶 【电机磁铁粘接胶产品特性】 ★研泰牌电机磁铁粘接胶,磁钢胶是用进口原料生产的高分子聚合物产品,用于平面刚性材料的粘接,是一种高性能多用途的单组分丙烯酸酯胶粘 剂。尤其适用于各类电机磁钢、磁瓦、金属材料等的结构性粘接。 ★耐溶剂性好、高强度、快固化,对刚性材料粘接效果好,如将铁氧体粘到电机的电镀金属件或扬声器零件上,能达到环氧树脂胶的强度、瞬干胶固化速度的高强度结构胶。 ★粘接强度高,耐冲击、抗振动,耐高低温性能优越,可耐温-55℃—180℃。 快速固化,使用方便。 ★电机磁铁粘接胶,电机磁铁粘接胶具有较强的拉伸、剪切与剥离强度,耐冲击、耐压、抗振动,环保无毒,已通过欧盟ROHS检测。 【电机磁铁粘接胶产品用途】 ★适用平面、套接或槽接结构的粘接,对钢、铁、铜、铝等粘接效果好,用于电机磁片、磁瓦与外壳间的粘接及其它金属材料间的结构性粘接。尤其适用于稀土永磁材料与金属底材的粘接。 ★适用于铁氧体粘电机的电镀金属件或扬声器零配件,也适用于粘接金属和玻璃及某些硬质塑料。 ★广泛应用于:五金灯饰、机械、电子、电机、汽车、船舶、金属加工等制造和维修中的各种金属、磁铁、硬质塑料的粘接及密封。 ★也可用于螺纹的锁固和密封,零件固持及微孔微缝的密封及平面密封结构粘接,封闭机件组合,管路密封,轴承固定等,可延长机械寿命,增加操 作安全,提高产品品质等,其耐老化性能极强。 【电机磁铁粘接胶技术参数】 ★外观:琥珀色液体 ★技术咨询:1392,9479,317;4006,5858,46 ★电机磁铁粘接胶,电机磁铁粘接胶详细技术参数请咨询研泰客服人员。 【电机磁铁粘接胶使用方法】 ★先将待粘接部位用丙酮或三氯乙烯清洗去污,彻底除去油污和锈渍,待溶剂挥发后备用。 ★均匀涂胶,涂胶量应确保涂满粘接件表面,不漏胶。 ★将待粘接零件(如铁氧体等)安装好,并调整好角度和位置,然后在结合处涂足够的TY5319胶液,使其自然渗入,静置几分钟,待初步定位方可移动,待24小时完全固化后进行检测程序。 ★将TY5324或TY5326胶涂于待粘接零件产品一面(整个接触面均需涂胶),再将另一面结合(填充间隙较大或环境温度过低时,将另一面涂促进剂加速固化)。适当磨动几下,使胶液均匀,静置几分钟,待初步定位方可移动,待24小时完全固化后进行检测程序。
生产工艺流程简述
生产工艺流程简述 清棉工序 1.主要任务:(1)将紧压的原纤维松解成较小的纤维块或纤维束,以利混合、除杂作用的顺利进行;(2)清除原纤维中的大部分杂质、疵点及不宜纺纱的短纤维。(3)将不同批次的纤维进行充分而均匀地混和,以利棉纱质量的稳定。(4)成卷:制成一定重量、长度、厚薄均匀、外形良好的棉纤维卷。 梳棉工序 1.主要任务 (1)分梳:将纤维分解成单纤维状态,改善纤维伸直平行状态。(2)混合:使纤维进一步充分均匀混合。(4)成条:制成符合要求的棉条。 精梳工序 主要任务: 1.除杂:清除纤维中细小的纤维疵点。 2.梳理:进一步分离纤维,排除一定长度以下的短纤维,提高纤维的长度整齐度和伸直度。 3.牵伸:将棉条拉细到一定粗细,并提高纤维平行伸直度。 4.成条:制成符合要求的棉条。
并条工序 主要任务 1.并合:一般用6-8根纤维条进行并合,改善棉条长片段不匀。2.牵伸:把纤维条拉长抽细到规定重量,并进一步提高纤维的伸直平行程度。3.混合:利用并合与牵扯伸,使纤维进一步均匀混合,不同唛头、不同工艺处理的纤维条,在并条机上进行混和。4.成条:做成圈条成型良好的熟条,有规则地盘放在棉条桶内,供后工序使用。 粗纱工序 主要任务: 1.牵伸:将熟条均匀地拉长抽细,并使纤维进一步伸直平行。2.加捻:将牵伸后的须条加以适当的捻回,使纱条具有一定的强力,以利粗纱卷绕和细纱机上的退绕。 细纱工序 主要任务: 1.牵伸:将粗纱拉细到所需细度,使纤维伸直平行。 2.加捻:将须条加以捻回,成为具有一定捻度、一定强力的细纱。3.卷绕:将加捻后的细纱卷绕在筒管上。4.成型:制成一定大小和形状的管纱,便于搬运及后工序加工。
注塑铁氧体
1.4 注射成型粘结磁体概况 注射成型是一种注射兼模塑的成型方法,又称注塑成型[36],是将聚合物组分的粒料或粉料放入注射机的料筒中,经过加热、压缩、剪切、混合和输送作用,使物料均匀化和熔融,然后借助于柱塞或螺杆向熔化好的聚合物熔体施加压力,将高温熔体通过喷嘴和模具的浇道系统射入预先闭合好的低温模腔中,最后冷却定型、开启模具就得到具有一定几何形状和精度的制品。 随着工业化进程的加快,注射成型技术已经应用到各个领域。 1980年诞生的第一块注射成型铁氧体磁体[37],掀开了磁体的注射成型技术的新纪元。随后铁氧体的注射技术迅速发展,现已经大规模产业化。 60年代开发出了第一代稀土磁性材料SmCo5合金,人们将该磁性材料用于注射成型,制备出比铁氧体磁性能优异得多的注射成型稀土SmCo5磁体,其最大磁能积达到10MGOe,但热稳定性能差[38];随后人们将第二代稀土永磁材料Sm2Co17类磁粉与注射成型技术结合,制备出的粘结磁体的热稳定性和磁性能均有较大的提高,其最大磁能积达到11MGOe[39]。但是,由于它们的主要成分是Sm和Co,这两种材料的价格昂贵,且又是战略物资,因此,注射成型的第一和二代稀土永磁的工业化大生产和市场开发受到了限制。 80年代人们结合美国GM公司研究开发的MQ快淬NdFeB磁粉研制了各向同性的注射粘结NdFeB磁体[40],特别是1999年日本Mate Co.Ltd用MQ等快淬NdFeB磁粉制成了各向同性的注射成型RIN-90的粘结钕铁硼磁体,其磁能积(BH)m达到72.5KJ/m3[41];日本爱知制钢公司采用d-HDDR工艺生产出不含Co,价格低廉的HDDR-NdFeB磁粉,其典型的磁性能:Br=13.8kG,Hcj=14.0kOe, (BH)m=38~42MGOe[42],采用这种高度各向异性HDDR钕铁硼粉,获得了(BH)m 达130KJ/m3的注射成型各向异性磁体[43]。 1987年,Sm2Fe17N3磁性材料被人们发现后[44],日本住友金属矿山公司用还原扩散法批量生产出了平均粒径2~3μm的Sm2Fe17N x磁粉,其磁特性为Br=1.35T,Hc=850kA/m,(BH)m=290kJ/m3;采用这种磁粉与PA12树脂混合料,已批量生产出磁能积为111kJ/m3的各向异性注射成型磁体Wellmax-S3A,而实验室样品的磁性能为141kJ/m3,是当今注射磁体的最高水平。 1999年,S Y oshizawa et al.采用Sm2Fe17Nx同不饱和聚酯系树脂混合制得了磁能
生产工艺流程图和工艺描述
生产工艺流程图和工艺描述 香肠工艺流程图 辅料验收原料肉验收 原料暂存肥膘解冻 精肉解冻水切丁辅料暂存分割热水漂洗1 漂洗2 加水绞肉 肠衣验收、暂存(处理)灌装、结扎 (包括猪原肠衣和蛋白肠衣) 咸水草、麻绳验收、暂存浸泡漂洗3 冷却 内包装 装箱、入库 出货
香肠加工工艺说明 加工步骤使用设备操作区域加工工艺的描述与说明 原料肉验收、暂存化验室、仓库 按照原料肉验收程序进行,并要求供应商 提供兽药残留达标保证函及兽医检疫检 验证明 辅料验收、暂 存 化验室、仓库按验收规程进行验收肥膘验收、暂 存 化验室、仓库按验收规程进行验收肠衣验收化验室按验收规程进行验收 肠衣处理腊味加工间天然猪肠衣加工前需用洁净加工用水冲洗,人造肠衣灌装前需用洁净加工用水润湿 咸水草、麻绳 验收 化验室按验收规程进行验收暂存仓库 浸泡腊味加工间咸水草、麻绳加工前需用洁净加工用水浸泡使之变软 解冻解冻间肉类解冻分 割间 ≤18℃、18~20h恒温解冻间空气解冻 分割分割台、刀具肉类解冻分 割间 将原料肉筋键、淋巴、脂肪剔除、并分割 成约3cm小肉块 加工步骤使用设备操作区域加工工艺的描述与说明 漂洗2 水池肉类解冻分 割间 加工用水漂洗,将肉的污血冲洗干净 绞肉绞肉机肉类解冻分 割间 12℃以下,采用Φ5mm孔板 肥膘切丁切丁机肉类解冻分 割间 切成0.5cm长的立方
漂洗1 水池肉类解冻分 割间 水温45-60℃,洗去表面游离油脂、碎肉 粒 灌装、结扎灌肠机香肠加工间按产品的不同规格调节肠体长度,处理量800~1200kg/h ,温度≦12℃ 漂洗3 水池香肠加工间水温45~60℃,清洗肠体表面油脂、肉碎 冷却挂肠杆预冷车间12℃下冷却0.5~1小时,中心温度≦25℃ 内包装真空机、电子 秤、热封口机 内包装间 将待包装腊肠去绳后按不同规格称重,装 塑料袋、真空包装封口 装箱、入库扣扎机、电子 秤 外包装间、成 品仓库 将真空包装的产品装彩袋封口,按不同规 格装箱、核重、扣扎放入成品库并挂牌标 识。
永磁材料的种类及发展
永磁材料的种类及发展 永磁材料种类多,用途广。现在所应用的永磁材料主要经历了金属永磁材料、铁氧体永磁材料和稀土永磁材料三个阶段。 第一阶段:金属永磁材料,是一大类发展和应用都较早的以铁和铁族元素为重要组元的合金型永磁材料,又称永磁合金。主要包括铝镍钴(Al-Ni-Co)和铁铬钴(Fe-Cr-Co)系两类永磁合金。这类材料的研发和生产始于20世纪初期,通过铸造工艺制备而成,因此,也被称为铸造永磁材料。1880年左右,人们首先采用碳钢制成了永磁材料,其最大磁能积(BH)max约为1.6 kJ/m3。紧接着,人们又发现了钨钢、钴钢等金属永磁材料。1931年以来,人们通过在Fe中加入Al、Ni、Co三种元素,经过浇注和热处理得到了铝镍钴系磁钢。最初,铝镍钴磁钢的(BH)max仅为14.3 kJ/m3,人们对合金成分和工艺进行调整后,(BH)max跃升到39.8 kJ/m3。从此,铝镍钴磁钢在永磁材料中占据了主导地位,一直到60年代。目前国际先进水平已经可以批量身材磁性能为(BH)max=13MGOe,Br>10.8 kGs,Hcb>1550Oe,Tc<550 ℃的铝镍钴磁体。这类材料的磁能积较低,但其居里温度很高(可高达890 ℃),温度稳定性很好,磁感温度系数低,因此,在某些特殊器件上的使用无法取代,至今依然有着稳定的市场需求。 第二阶段:铁氧体永磁材料,又称永磁铁氧体,是由Fe2O3和锶(或钡等)的化合物按一定比例混合,经预烧、破碎、制粉、压制成型、烧结和磨加工而成。当前应用的永磁铁氧体主要为六角晶系的磁铅石型铁氧体,其化学式为MO·6Fe2O3,其中M为Ba、Pb、Sr等元素。20世纪30年代发现了铁氧体永磁材料,这类永磁体的矫顽力一般只有0.5 T,剩磁在0.4 T左右,磁能积较低(25~36kJ/m3),其原材料便宜,工艺简单,价格低廉,因此在70年代得到迅速发展,其产量越居第一位。此外,其电阻率高,特别适合在高频和微波领域应用。 第三阶段:稀土永磁材料,是以稀土元素RE(Sm,Nd,Pr等)与过渡族金属元素TM(Fe,Co等)所形成的金属间化合物为基体的一类高性能永磁材料。从20世纪60年代开始,稀土永磁材料开始发展起来。稀土永磁材料的发展又经历了三代,第一代SmCo5、第二代Sm2Co17稀土永磁,和第三代的NdFeB稀土永磁。下面将三代稀土永磁材料分别介绍如下: 第一代稀土永磁SmCo5合金具有CaCu5型晶体结构,这是一种六角结构,这
永磁铁氧体预烧料的加工工艺及方法
永磁铁氧体预烧料的加工工艺及方法 永磁铁氧体预烧料的加工过程实际上是碳酸钡(BaCO3)或碳酸锶(SrCO3)与铁红(Fe2O3)经过高温下的固相反应充分生成六角形的铁氧体晶粒的过程。固相反应是否完善、充分,晶粒形状是否完整,对材料的质量有很大影响。同时预烧料的优劣在铁氧体磁铁的生产中至关重要,质量差的预烧料是无法生产出高性能铁氧体磁铁。 目前我们公司生产的铁氧体预烧料有:异方性锶料、等方性普通粒料、自动车料三种。决定永磁铁氧体预烧料性能优劣主要有以下几个方面: ○1材料○2配方○3工艺手段及控制方法 一、材料 在永磁铁氧体预烧料生产中首先要选择合适的原材料,选择时主要考虑:原料纯度、含杂质情况、原料化学活动性、颗粒度等几个方面。 1、铁红(Fe2O3):永磁铁氧体预烧料的主料,应选择纯度>97%以上,最好在98%以上。目 前我公司使用印度铁红有98.5%、98%、97.5%、96%四种,用量最大为 97.5%铁红。台湾铁红纯度98.5%、比利时铁红纯度99%。 2、碳酸钡(BaCO3)或碳酸锶(SrCO3):永磁铁氧体预烧料的主料,纯度应大于96%。最 好大于98%以上。目前我公司使用为纯度97%。 3、添加剂:在预烧时增加添加剂主要目的是为了改善材料的结构灵敏度,弥补某一特性。永 磁铁氧体常用的添加剂有:SiO2、CaCO3、SrSO4等,具体作用在配方中再 做介绍。 4、含杂质情况:杂质含量中二氧化硅(SiO2)含量应该在0.5%以下,最好在0.1%以下。 氯离子含量最好在0.15%以下(此杂质对铁氧体性能影响很大,直接影响产 品收缩率、反应气氛,应在烧结低温部分将其挥发排除)。 5、化学活动性:就铁红、铁磷、铁矿砂三种生产永磁铁氧体原料而言,铁红的化学活动性 优于其他两种。我公司目前全部使用铁红生产,另外纯度大的铁红化学活 动性优于纯度小的铁红。 4、颗粒度:原料的粒度最好在1um以下,颗粒度太大往往影响固相反应的充分发生。 5、原料密度:原料的压密程度(密度)同样对预烧料的烧结有较大影响,密度大的铁红在 混料过程中更加容易混料均匀、铁红与碳酸锶能充分接触;预烧过程中会增 加铁氧体的生成比例。 二、原料配方
注塑磁学-粘结永磁体的制造工艺类别
粘结永磁体的制造工艺类别 编辑删除 来源:磁性中国日期:2011-11-24 浏览次数275次 粘结永磁体是指用永磁粉末混入一定比例的粘结剂,按一定的工艺制成的一种磁体。按其最终的形态可分为柔性磁体和刚性磁体,按其生产工艺可分为4种:压延成型(又称辊轧成型)、注射成型、挤压成型和模压成型。 (1) 压延成型(Calendering) 压延成型是出现较早的一种粘结方法,其工艺过程大致为:将磁粉和粘结剂按大约7:3(体积比)的比例混合均匀,在柔软状态下通过两个对轧的轧辊轧制成所需的厚度,然后经过固化处理制成产品。所使用的粘结剂为丁氰橡胶和乙烯类树脂,制成的产品是柔性的磁板,厚度为0.3~6mm,宽度约lm,长度几十米,一般使用铁氧体磁粉,为了提高磁性能,可加人少量的钕铁硼磁粉。磁板表面不需要涂层保护,一般进行表面贴膜作为装饰。 (2) 注射成型(Injection Moulding) 注射成型是从制造注射塑料制品演变而来的。首先将磁粉和粘结剂混合均匀,经过混炼和造粒,制成干燥的粒料,然后把粒料用螺旋式导料杆送到加热室加热,注射进模具成型,冷却后即得产品。所用粘结剂一般为尼龙6、聚酞胺、聚脂和PVC等,加人量为20%~30%(体积百分数)。这种工艺可制成各种复杂形状的粘结磁体,且磁体是刚性的。所用磁粉一般为铁氧体,钕铁硼及钐钴磁粉,用后两种磁粉由于硬度较大,对导料杆和模腔磨损严重,是目前较为关注的问题之一。由于磁体表面已有一层粘结剂薄膜,不需进行表面涂层保护。 (3) 挤压成型(Extrusion) 其工艺过程和注射成型基本相同,唯一区别是这种工艺是将加热后的粒料通过一个孔洞挤入模具中成型,所得产品也是刚性的,所用粘结剂与注射成型相同,加入量为20%(体积)左右。这种工艺一般用来生产其它粘结工艺较难实现的薄片状或薄壁环状磁体。 (4) 模压成型(Compression) 模压成型是借鉴粉末冶金工艺的一种粘结方法,首先将磁粉和粘结剂按比例混合,使得粘结剂均匀地涂覆在每一个磁粉颗粒表面,经过简单造粒并加入一定量的添加剂,把混合粉放入模具中在压机上成型,成型压力一般为7~10t/cm2,最后将压坯放入烘箱中在120~150℃下固化得到最终产品。所用粘结剂一般是热固型环氧类树脂或酚醛类树脂,加入量为10%~20%(体积)。由于加入的粘结剂量少,这种工艺制成的粘结磁体的磁性能最好,是目前发展最快的一种工艺。特别是钕铁硼永磁材料出现以后,粘结钕铁硼永磁体几乎全部采用这种工艺,已逐渐形成了产业化。粘结磁体表面需进行涂层保护,一般采用阴极电泳、喷涂或其它表面防护方法。
铁氧体磁性材料
第一节铁氧体磁性材料概述 铁氧体磁性材料可用化学分子式MFe 2O 4表示。式中M 代表锰、镍、锌、铜等二价金属离子。铁氧体磁性是通过烧结这些金属化合物的混合物而制造出来的。铁氧体磁性的主要特点是电阻率远大于金属磁性材料,这抑制了涡流的产生,使铁氧体磁性能应用于高频领域。 首先,按照预定的配方比重,把高纯、粉状的氧化物(如Fe 2O 4、Mn 3O 4、ZnO 、NiO 等)混合均匀,再经过煅烧、粉碎、造粒和模压成型,在高温(1000~1400℃)下进行烧结。烧结出的铁氧体制品通过机械加工获得成品尺寸。上述各道工序均受到严格的控制,以使产品的所有特性符合规定的指标。 不同的用途要选择不同的铁氧体材料。有适用于低损耗、高频特性好的系列,有磁导率的线性材料。按照不同的适用频率范围分为:中低频段(20~150kHz )、中高频段(100~500kHz )、超高频段(500~1MHz )。 第二节铁氧体磁性材料的各项物理特性定义与计算公式 01) 初始磁导率μi 初始磁导率是磁性材料的磁导率(B/H )在磁性曲线始端的极限值,即 H B H i 00lim 1→μ=μ 式中 μ0:真空磁导率(4π×10-7H/m ); H : 交流磁场强度(A/m ); B : 交流磁通密度(T )。 02) 有效磁导率μe 在闭合磁路中(漏磁可以忽略),磁芯的有效磁导率可表示为: μe 72104××= e e A l N L π 式中 L :装有磁芯的线圈的自感量; N :线圈匝数; e e A l =C 1=磁芯常数(mm -1) 03) 饱和磁通密度B s
磁化到饱和状态的磁通密度。 04) 剩余磁通密度B r 从磁饱和状态去处磁场后,剩余的 磁通密度。 05) 矫顽力H c 从饱和状态去处磁场后,磁芯继续被反向的磁场磁化,直至磁通密度减小到零,此时的磁场强度称为矫顽力, 06) 损耗因素tan δ 损耗因数是磁滞损耗、涡流损耗和剩余损耗三者之和: tan δ=r e δδδtan tan tan h ++ =111r f e i V L h ++ 损耗因数也可用电阻和电抗之比来表示: L R R L R w eff m ωωδ?==tan 式中:tan δe :涡流损耗因数; tan δr :剩余损耗因数; h1:磁滞损耗因数; L :装有磁芯的线圈的自感量(H ); V :磁芯体积(m 3); i :电流(A ); e 1:涡流损耗系数; f :频率(Hz ); r 1:剩余损耗系数; R m :磁芯损耗的等效电阻(Ω); 0HH
永磁铁氧体预烧料的生产工艺是怎样的审批稿
永磁铁氧体预烧料的生产工艺是怎样的 YKK standardization office【 YKK5AB- YKK08- YKK2C- YKK18】
永磁铁氧体预烧料的生产工艺是怎样的 以优质铁鳞为原料,采用链篦机——回转窑干法生产工艺,生产Y30H-1型锶永磁铁氧体预烧料。 经过烘干、球磨后的铁鳞,与一定配比的碳酸锶、高岭土进行配料、强混、造球后,送入链篦机进行烘干、氧化处理。链篦机采用回转窑的尾气对物料进行烘干,以及将物料中的FeO氧化为Fe2O3,将物料中三氧化二铁的成份进行大比例的提高。 完成链篦机烘干、氧化后的球状物料,送入回转窑经过1200℃进行高温煅烧处理。在回转窑中,物料中的碳酸锶和碳酸钙会在高温中发生分解反应,然后再与Fe2O3生成产品——SrO(Fe2O3)6。 项目生产过程中发生的化学反应如下: 链篦机中的氧化反应: 4FeO +O2 = 2Fe2O3? 回转窑中的分解反应: SrCO3 =(高温) SrO+CO2↑ 回转窑中产品的生成反应: SrO+ 6Fe2O3=(高温) SrO(Fe2O3) 6 1、原料来源 铁鳞由汽车运输至本项目厂区铁鳞堆场进行散放堆存。项目外购的袋装碳酸锶、高岭土全部在车间内暂存库房内堆存。 2、原料处理
项目需要对铁鳞进行初步筛分、烘干、冷却、球磨机初磨、配料、配料后强混球磨等工段,为项目三条生产线提供合格的原材料。 具体处理步骤如下: (1)铁鳞筛分 项目铁鳞堆场内设置了一台孔径为75px的粗筛,除去铁鳞中较大的杂质。根据现场勘查,筛除的杂质主要为热轧厂铁鳞沉淀池中混杂的砖头、废弃角钢等固废。 (2)铁鳞烘干窑烘干 经过筛分后的合格铁鳞经3m高的斗提机输送至烘干窑中,通入煤气燃耗后进行烘干处理,将含水率为10%的铁鳞烘干到含水1%左右。 斗提机进料口,会产生车间粉尘(G1),采用集气罩收集后送入SMC4-30型布袋除尘器处理,除尘系统回收的粉尘送强混球磨机进行研磨。 烘干过程中将产生烘干烟气(G2),主要污染物为粉尘。烘干烟气经烟气管道收集送旋风除尘系统处理,除尘系统回收的粉尘送强混球磨机进行研磨。 (3)铁鳞烘干窑后冷却筒 烘干窑后冷却筒与项目烘干窑对接,烘干后的铁鳞直接进入冷却筒进行冷却处理。冷却筒通过对筒体喷淋水进行间接冷却,冷却废水(W1)经冷却水收集槽、收集管道收集后,送循环水处理站处理后循环使用。
永磁电机中常用的磁铁材质有哪些
永磁电机中常用的磁铁材质有哪些 永磁电机中常用的磁铁材质有哪些?电机磁铁全面解析:电机中常用的永磁材料包括烧结磁体跟粘结磁体,主要种类有铝镍钴、铁氧体、钐钴、钕铁硼等。 铝镍钴:铝镍钴永磁材料是最早广泛使用的一种永磁材料,其制备工艺和技术比较成熟。目前日本、美国、欧洲、俄罗斯、中国都有工厂生产。在大规模的生产企业当中,杭州永磁的产量目前在国内数第一,年产能力达3000吨。 永磁铁氧体材料:进入50年代,铁氧体开始蓬勃发展起来,尤其是70年代,在矫顽力、磁能机方面性能较好的锶铁氧体大量投入生产,迅速扩大了永磁铁氧体的用途。作为一款非金属磁性材料,铁氧体没有金属永磁材料易氧化、居里温度低、成本高的弊端,因此大受欢迎。 钐钴材料:20世纪60年代中期兴起的磁性能优异的永磁材料,且性能非常稳定。钐钴从磁性能方面来说特别适合于制造电机,但由于其价格昂贵,主要用于研究开发航空、航天、
武器等军用电机和高性能而价格不是主要因素的高科技领域的电机中。 钕铁硼材料:钕铁硼磁性材料是钕,氧化铁等的合金,又称磁钢。具有极高的磁能积和矫力,同时高能量密度的优点使钕铁硼永磁材料在现代工业和电子技术中获得了广泛应用,从而使仪器仪表、电声电机、磁选磁化等设备的小型化、轻量化、薄型化成为可能。由于含有大量的钕和铁,容易锈蚀。表面化学钝化是目前很好的解决方法之一。 电机常用永磁材料抗腐蚀性能、最高工作温度、加工性能、退磁曲线形状、价格对比(图) 安徽沃弗电力科技有限公司是一家集科研、设计、生产、销售服务为一体的高新技术企业,凭借在永磁传动领域的专业水平和成熟的技术,在工业领域迅速崛起。安徽沃弗电力科技有限公司奉行“进取、求实、严谨、团结”的方针,不断开拓创新,以技术为核心,视质量为生命,奉用户为上帝,竭诚为您提供性价比最高的永磁产品,高质量的工程改造设计及无微不至的售后服务。
永磁铁氧体预烧料的生产工艺是怎样的
永磁铁氧体预烧料的生产工艺是怎样的 以优质铁鳞为原料,采用链篦机——回转窑干法生产工艺,生产Y30H-1型锶永磁铁氧体预烧料。 经过烘干、球磨后的铁鳞,与一定配比的碳酸锶、高岭土进行配料、强混、造球后,送入链篦机进行烘干、氧化处理。链篦机采用回转窑的尾气对物料进行烘干,以及将物料中的FeO氧化为Fe2O3,将物料中三氧化二铁的成份进行大比例的提高。 完成链篦机烘干、氧化后的球状物料,送入回转窑经过1200℃进行高温煅烧处理。在回转窑中,物料中的碳酸锶和碳酸钙会在高温中发生分解反应,然后再与Fe2O3生成产品——SrO(Fe2O3)6。 项目生产过程中发生的化学反应如下: 链篦机中的氧化反应:4FeO +O2 = 2Fe2O3? 回转窑中的分解反应:SrCO3 =(高温)SrO+CO2↑ 回转窑中产品的生成反应:SrO+ 6Fe2O3=(高温)SrO(Fe2O3) 6 1、原料来源 铁鳞由汽车运输至本项目厂区铁鳞堆场进行散放堆存。项目外购的袋装碳酸锶、高岭土全部在车间内暂存库房内堆存。 2、原料处理
项目需要对铁鳞进行初步筛分、烘干、冷却、球磨机初磨、配料、配料后强混球磨等工段,为项目三条生产线提供合格的原材料。 具体处理步骤如下: (1)铁鳞筛分 项目铁鳞堆场内设置了一台孔径为75px的粗筛,除去铁鳞中较大的杂质。根据现场勘查,筛除的杂质主要为热轧厂铁鳞沉淀池中混杂的砖头、废弃角钢等固废。 (2)铁鳞烘干窑烘干 经过筛分后的合格铁鳞经3m高的斗提机输送至烘干窑中,通入煤气燃耗后进行烘干处理,将含水率为10%的铁鳞烘干到含水1%左右。 斗提机进料口,会产生车间粉尘(G1),采用集气罩收集后送入SMC4-30型布袋除尘器处理,除尘系统回收的粉尘送强混球磨机进行研磨。 烘干过程中将产生烘干烟气(G2),主要污染物为粉尘。烘干烟气经烟气管道收集送旋风除尘系统处理,除尘系统回收的粉尘送强混球磨机进行研磨。 (3)铁鳞烘干窑后冷却筒 烘干窑后冷却筒与项目烘干窑对接,烘干后的铁鳞直接进入冷却筒进行冷却处理。冷却筒通过对筒体喷淋水进行间接冷却,冷却废水(W1)经冷却水收集槽、收集管道收集后,送循环水处理站处理后循环使用。
磁性材料的研究进展汇总
《磁性材料的研究进展》 学院:物理与材料科学学院 班级:13级材料物理 姓名: 王郁 学号:B51314019 指导老师:李秋菊 完成日期:2016年5月11日
摘要: 目前,磁性材料蓬勃发展,磁性材料的应用已渗透到国防、工业、信息等各个领域,对我们的生活产生了巨大的影响。同时,各种新磁性材料的诞生,也不断推动着现代材料科学的进展。本文对磁性材料进行了概述,并简介了其最新研究进展,尤其是对稀土磁性材料、巨磁电阻材料、纳米微晶磁性材料的研究进展进行了详细论述。 关键词: 磁性材料铁氧体稀土磁性材料巨磁电阻材料 前言 磁性材料广义上分为两大类:软磁材料和硬磁材料。软磁材料能够用相对低的磁场强度磁化,当外磁场移走后保持相对低的剩磁。软磁材料的矫顽力为400~0116A?m-1 ,主要应用于任何包括磁感应变化的场合。硬磁材料是在经受外磁场后能保持大量剩磁的磁性材料,这类磁性材料的典型矫顽力值,Hc为10~1000kA?m-1 ,具有高Hc值的硬磁材料称为永磁材料,主要用于提供磁场。磁性材料的磁导率、矫顽力、磁致损失、剩磁和磁稳定性是结构敏感性的,这些性能可以通过加工(包括机械加工和热处理)来控制。目前,磁性材料的研究方向主要有软磁材料、硬磁材料、磁力学材料、磁电子材料。磁性材料的进展大致上分几个历史阶段:当人类进入铁器时代时,标志着金属磁性材料的开端。直到18世纪,金属镍、钴相继被提炼成功,这一漫长的历史时期是3d过渡族金属磁性材料生产与原始应用的阶段;20世纪初期,FeSi、FeNi、FeCoNi磁性合金人工制备成功,并广泛地应用于电力工业、电机工业等行业,成为3d过渡族金属磁性材料的鼎盛时期;从20世纪50年代开始,3d过渡族的磁性氧化物(铁氧体)逐步进入生产旺期,由于铁氧体具有高电阻率,高频损耗低等优点,从而为当时兴起的无线电、雷达等工业的发展提供了所必需的磁性材料,标志着磁性材料进入到铁氧体的历史阶段;1967年,SmCo合金问世,这是磁性材料进入稀土-3d化合物领域的历史性开端。巨磁致收缩材料与稀土磁光材料的问世更丰富了稀土-3d化合物磁性材料的内涵。1972年的非晶磁性材料与1988年的纳米微晶材料的呈现,更添磁性材料新风采。1988年,磁电阻效应的发现揭开了自旋电子学的序幕.因此从20世纪后期延续至今,磁性材料进入了前所未有的兴旺发达时期,并融入到信息行业,成为信息时代重要的基础性材料之一。 1、磁性材料的分类 磁性材料从材质和结构上讲,可分为金属及合金磁性材料和“铁氧体磁性材料两大类,铁氧体磁性材料又分为多晶结构和单晶结构材料[1]。从应用功能上讲,磁性材料分为:软磁材料、永磁材料、磁记录-矩磁材料、旋磁材料等种类。软磁材料、永磁材料、磁记录-矩磁材料中既有金属材料又有铁氧体材料;而旋磁材料和高频软磁材料就只能是铁氧体材料了,因为金属在高频和微波频率下将产生巨大的涡流效应,导致金属磁性材料无法使用,而铁氧体的电阻率非常高,将有效的克服这一问题、得到广泛应用。磁性材料从形态上讲。包括粉体材料、液
永磁材料的最常用的有 铁氧体永磁材料 和 稀土永磁材料 两种
永磁材料的最常用的有铁氧体永磁材料和稀土永磁材料两种。 1.永磁材料的主要技术参数有剩磁强度和矫顽力两项。 7.永磁材料 答:又叫硬磁材料,其主要特征是剩磁感应和矫顽力高。 1.试论述永磁电机常用哪几种永磁材料,主要性能和特点如何? 答:永磁材料主要有铝镍钴系列、硬磁铁氧体系列、稀土钴永磁系列、稀土钕铁硼永磁系列等。 铝镍钴系列永磁材料包括铸造和粉末冶金加工两种。剩磁较大,最大磁能积在永磁材料中处于中上水平,居里点高,磁感应温度系数小,组织结构稳定,是较早应用的一种材料。现有比较成熟的产品品种。但是这个系列中性能较好的材料内,镍和钴的成份比重较大,而镍和钴同为稀有金属,产量少铝镍钴材料的矫顽值相对较低,抗去磁能力差,应用受到了一定限制。 铁氧体永磁材料特点是矫顽力较高,回复磁导率较小。密度小,电阻率大,最大磁能积较小,如果合理应用,可以得到较大的回复磁能积,比较适合在动态磁路中工作。这种材料价格最便宜,在微电机中应用广泛。 稀土永磁材料包括稀土钴和稀土钕铁硼系列。这类材料磁性能最好,材料的剩磁、矫顽磁力与磁能积都较大,使电机磁系统体积、重量大大减速轻,出力增大。是目前最有发展前途的磁性材料。缺点是居里点偏低,使用温度不高,温度系数偏高。钕铁硼材料易氧化和锈蚀,使用时需注意表面防护。 2.试论述一下微特电机装配工艺特点 答:微特电机装配的特点主要由使用要求和结构特征决定,主要有下列几个方面: ①所有零件都应具有互换性.每个零件都应有明确的尺寸、形位公差及表面粗糙度要求。 ②保证轴类装配质量。轴类装配对电机寿命、噪声、静摩擦、温升等影响极大。各类电机对轴类精度与安装要求各不相同,应有明确的规定。 ③保证转子的静平衡和动平衡要求。因为静不平衡和动不平衡使电机工作时产生附加力矩,轻都有振动、噪声,重者可能出现扫膛、共振等。 ④保证滑动接触和导电接触的可靠性。换向器、滑环与电刷的滑动接触,稳速机构的触点接触,必须安装调整得位置正确、压力适中,表面粗糙度达到预定要求。 ⑤应特别注意轻小、薄壁零件的不变形,不受损伤。加工和装配时必须采用专门的工具传送、转运和保存。 (每答出一个要点给2分)
生 产 工 艺 流 程
适用产品:大班台、会议台、书柜类 一、主要用材要求: 1.贴面用材:胡桃木、柚木、花梨木、榉 木等高级进口木皮,厚度0.6mm。 2.封边用材:与贴面种类相同或由客户指 定的,与之相搭配的实木木材。 3.基材:优等品级中密度纤维板MDF。 4.油漆:易涂宝“IDOPA”牌雅光聚脂油漆。 5.五金配件:德国产海蒂斯“HETTICH” 海福乐“HEFELE”。 二、主要生产工艺流程: 1.木皮贴面加工 ○1、木皮拼缝(见图○1) 使用机械:拼缝机。 质量要求:拼缝齐整,无断线,脱线、漏拼等现象 ○2、木皮贴面(见图○2) 使用机械:热压机。 质量要求:基材平整,涂胶均匀,成品无起泡
适用产品:办公沙发类 一、主要用材要求: 1.软包饰面用材 ○1、意大利进口牛皮 ○2、进口麻绒或布艺布 2.海绵:高密度海绵 3.弹簧:¢5mm高强度蛇形弹簧 4.木架用材:含水率低于9%的硬木木方及5mm以上多层夹板 二、主要生产工艺流程: 1.选料(皮制品)见图○1) 使用设备:手工操作 质量要求:标明烙印、穿孔、 折痕等天然瑕疵以便将其别 除出裁剪范围 2.车缝(见图○2) 使用设备:工业用重型缝纫机 质量要求:线路均匀,顺畅, 针距均匀 3.扪面料(见图○3) 使用设备:气动钉枪 质量要求:整体感观流畅、外型 符合要求,左右对齐 4.组装后全面测试(见图○4)
生产工艺流程适用产品:各类高低间隔用屏风 一、主要用材要求: 1.框架用材: ○1、热拉伸铝材,厚度1.5mm以 上(厚度视品种设计而定) ○2、冷轨钢板1.5mm以上 2.基材:优等品级中密度纤维板 MDF 3.饰边用材:进口绒布或布艺布 料等,视客户要求而定。 二、主要生产工艺流程(以铝制屏风 为例) 1.开料(见图○1) 使用设备:开料锯 质量要求:切口直角成90° 斜口成45°,规格符合图 纸要求。 2.冲孔(见图○2) 使用设备:冲床 质量要求:冲口齐整,位置 符 合图纸要求。 3.制框架(见图○3) 使用设备:手提气动工具 质量要求:锣丝紧固,框架 牢固 4.贴面料—绒布或布艺(见图○4) 使用设备:喷枪及手工操作 质量要求:胶水分布均匀,无 漏胶、渗胶、印绒布松驰等现象。 5.组装 使用设备:手工操作 质量要求:成品规格符合图纸 要求,产品无碰伤起泡等瑕疵