精益六西格玛在铣床工序生产效率提升中的应用
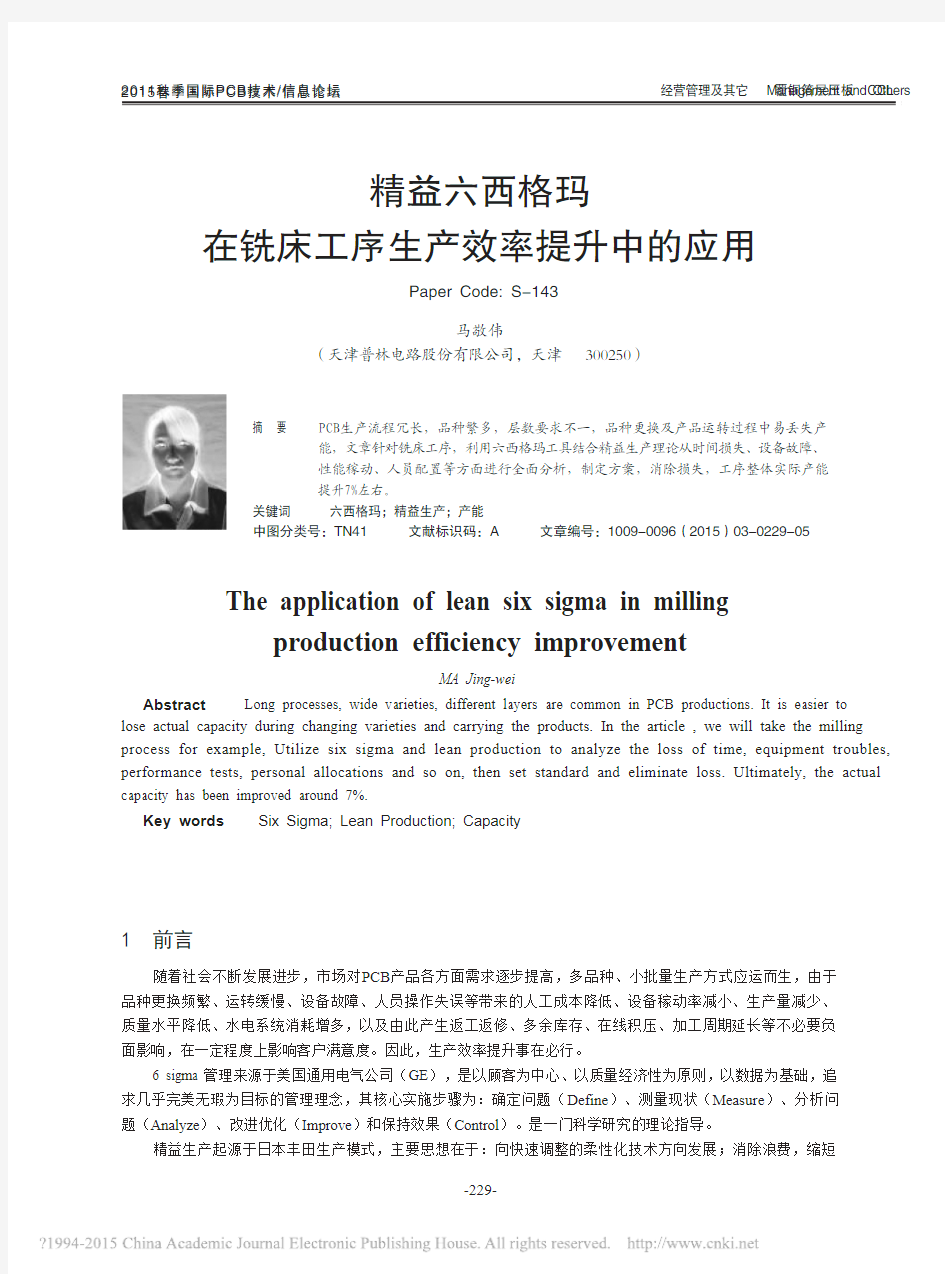

精益六西格玛
在铣床工序生产效率提升中的应用
Paper Code: S-143
马敬伟
(天津普林电路股份有限公司,天津 300250)
摘 要 PCB生产流程冗长,品种繁多,层数要求不一,品种更换及产品运转过程中易丢失产
能,文章针对铣床工序,利用六西格玛工具结合精益生产理论从时间损失、设备故障、
性能稼动、人员配置等方面进行全面分析,制定方案,消除损失,工序整体实际产能
提升7%左右。
关键词 六西格玛;精益生产;产能
中图分类号:TN41 文献标识码:A 文章编号:1009-0096(2015)03-0229-05
The application of lean six sigma in milling
production efficiency improvement
MA Jing-wei
Abstract Long processes, wide varieties, different layers are common in PCB productions. It is easier to lose actual capacity during changing varieties and carrying the products. In the article , we will take the milling process for example, Utilize six sigma and lean production to analyze the loss of time, equipment troubles, performance tests, personal allocations and so on, then set standard and eliminate loss. Ultimately, the actual capacity has been improved around 7%.
Key words Six Sigma; Lean Production; Capacity
1 前言
随着社会不断发展进步,市场对PCB产品各方面需求逐步提高,多品种、小批量生产方式应运而生,由于品种更换频繁、运转缓慢、设备故障、人员操作失误等带来的人工成本降低、设备稼动率减小、生产量减少、质量水平降低、水电系统消耗增多,以及由此产生返工返修、多余库存、在线积压、加工周期延长等不必要负面影响,在一定程度上影响客户满意度。因此,生产效率提升事在必行。
6 sig m a 管理来源于美国通用电气公司(GE),是以顾客为中心、以质量经济性为原则,以数据为基础,追求几乎完美无瑕为目标的管理理念,其核心实施步骤为:确定问题(Define)、测量现状(Meas u re)、分析问题(Analy z e)、改进优化(I mp ro v e)和保持效果(C on t rol)。是一门科学研究的理论指导。
精益生产起源于日本丰田生产模式,主要思想在于:向快速调整的柔性化技术方向发展;消除浪费,缩短
换型时间,提高效率。
精益六西格玛整合两种方法的优点,是以科学研究与现场操作深层结合为基础的一套新的系统的分析方法。本文以六西格玛D .M .A .I .C.解决问题的方法论为主,结合精益生产综合设备效率(OEE )的计算方式实施快速改善。
2 确定铣床产能问题(Define)
本阶段寻找系统中需要解决的项目。
由于市场需求,机加工工艺产品不断增加,在工厂产能达到32000 ㎡的愿景下,更多产品已由冲成型工艺改为铣成型工艺,铣床产量需求不断增加,已成为系统瓶颈。
3 测量铣床产能现状(Measure)
本阶段针对目标项目全面收集数据,确认问题和机会并量化。
以铣床标准产能为目标改善实际产能,利用时间损失分析表统计方式测量操作时间,如表1。
表1 铣床工序时间损失分析表
(1)根据工厂开班/停产工作计划将总体时间划分为计划时间和非计划时间;(2)根据设备是否运转将计划时间划分为停产时间和运转时间:
①设备停止运转:按照计划进行的设备停产,如:设备保养、维护,更换不同工号时相关准备工作,在计划范围内造成的停产称为计划停产;设备/配件突然故障造成的停产,如:吸尘故障,探测故障以及断刀等,在未计划时间内造成的停产称为未计划停产。
②设备正常运转:批量出产前,为其所做的各项准备工作,如:产品尺寸测量,加工实验板,新程式铣模板以及铣首枚等,称为技术性时间;批量出产时,为更换品种、更换同一品种的不同工单等做的准备工作,如:换活,上下活,程式更改及等待刀具图纸等,没有停机造成的设备等待称为等待时间,也包括用餐和宽放时间;除去时间损失分析表统计时间和用于实际出产时间以外的无法统计时间称为技术性损失时间。
(3)工厂停产放假时间称为非计划时间;
(4)根据时间损失分析表对铣床标准产能分析统计,如图1。
标准产能=未计划停产时间产能+计划停产时间产能+技术性时间产能+等待时间产能+纯生产时间产能+实际
?
? ? ? ?
?? ?
? ?
?? ?
?? ?
? ?
? ?
41.?佀 ?
出产+技术损失产能,共计45614m 2。
4 分析问题(Analyze)及相应问题的改善优化(Improve)
问题分析阶段对目标项目全面分析数据。本项目针对铣床工序总体时间损失分别进行时间稼动率损失、设备稼动率损失及性能稼动率损失分析,确定关键要因。
改善优化阶段是显示效果的关键步骤,针对关键要因提出相应建议和对策,制定改进方案,付出实践并验证效果。
4.1 时间稼动改善4.1.1 分析问题
时间稼动率是运转时间占总时间比率,基于以上测量阶段时间损失分析表数据得出以下时间稼动率损失帕累托图,如图1,换活和探测异常损失时间较长,需要重点改善。
图1 时间稼动率损失帕累托图
4.1.2 改善措施
(1)换活即品种更换,指铣不同工号产品时需更换不同程序、刀具,重新打底板、首枚,此换型过程耗费时间较长,改善空间很大。现针对铣床工序所有员工班次、换活时间及换活次数进行统计,利用Mini t a b 软件画出以下白夜班操作员换活时间长短的多变异图,如图4,对白夜班换活时间差距较大人员进行跟踪、调查、改善。
观察分析换活时间长的操作人员的操作动作,从中找到问题点:①外准备配错钻头,造成重复打底(打底前操作员复合钻头);②打底前未核对产品数量,打底后发现数量不符(加工前过数);③打底后找不到孔(贴胶带);
④用小刀加工的产品,3叠板加工时未调整Z 值,上电后销钉露出板,而大于2 mm 时需要重新打底;⑤打底时未调整Z 值,将定位孔打坏,需要重新打底;⑥打底时(4个头)未调整H 值,造成纸隔板跑电或主轴过载;⑦编辑程序错误,造成打底后,铣位置与定位间的位置错误(培训);
⑧由铣床工艺保证技师按照标准操作流程,对换活时间长的操作人员进行一对一讲解和训练;⑨完成培训的效果。(2)探测异常损失时间改善:
①对线体所有铣床进行刀具长度进行测试,铣刀长度设定20±0.3 mm ;②与设备人员合作共同将机床探测范围设定统一;
③与二厂人员沟通保证刀尖到刀环距离在20±0.2 mm 范围内。
5325
4575
900
450
300
75
75
5475
28200
43050
48.7%
80.6%
86.8%
92.8%
98.0%99.0%99.5%99.8%99.9%100.0%
?
?
?
?
?
?
オ
?
オ
?
?
4.1.3 改善结果
换活时间减少2870分钟/月,产能提升152 m2/月。如图2。探测异常损失时间减少5325分钟/月,产能提升282 m2/月,如图3。
图2 换活时间改善示意图 图3 探测异常改善示意图
4.2 设备稼动改善
4.2.1 分析问题
设备稼动率是设备故障时间占总时间比率,如图6,设备主轴故障、伺服器故障、压脚故障、电磁阀故障等诸多方面损失时间较长,需全面改善。
图4 设备故障损失帕累托图
4.2.2 改善措施
(1)对设备管理区域进行重新分配,由专职主管管理铣床设备。
(2)培训设备值班人员熟悉铣床主轴更换的要点,实现损坏即更换,降低主轴损坏维修时间;
(3)创新维修方式:原有冷却站损坏后设备停机待修复后设备恢复运转,现有方式为1台冷却站损坏后采取1托2的方式保证机台运转。
4.2.3 改善结果
设备故障减少7545分/月,降幅近70%,产能提升398 m2/月。
4.3 性能运转改善
4.3.1 分析问题
性能运转率是生产时间占总体时间比率,上下活等人时间、铣首枚时间、换活等人时间较长,需要重点改善。
4.3.2 改善措施(表2)
表2 性能运转率损失时间改善措施
4.3.3 改善结果
结合以上3种方法,将换活损失时间和首枚损失时间消除,降幅达30%左右,产能提升764 m2/月。
5 保持效果(Control)
此阶段是避免突然回到旧的习惯和程序上来而进行效果的跟踪改进,验证其是否长期有效,巩固改进结果,完成新过程的标准化、文件化。由以上改善结果制定标准方案,有效指导工序出产,总体产能提升2698 m2/月;OEE水平提升7%。
6 结语
运用六西格玛与精益生产的理论知识,结合铣床车间的生产情况,逐步分析影响生产产能的各项因素,推进各项提升产能措施的实施,最终有效提升铣床工序产能7%。
通过参与铣床产能提升项目,收获颇多:
(1)改善过程要不断持续进行,每个目标工序改善后制定的方案可能会成为其他工序制约因素,需要再次运用制约理论寻找新的制约点,立项改善。
(2)高效执行力是保持效果的关键因素之一,实施方案时要充分沟通,保质保量执行。
(3)正在结合六西格玛与精益生产的知识,参与到解决其他工序的产能等项目中。
参考文献
[1]唐晓芬.六西格玛核心教程—黑带读本中国标准出版社,2006年.
作者简介
马敬伟,生产部岗位管理专管职位,负责工序产能核算及效率提升工作。