石灰石-石膏湿法烟气脱硫系统

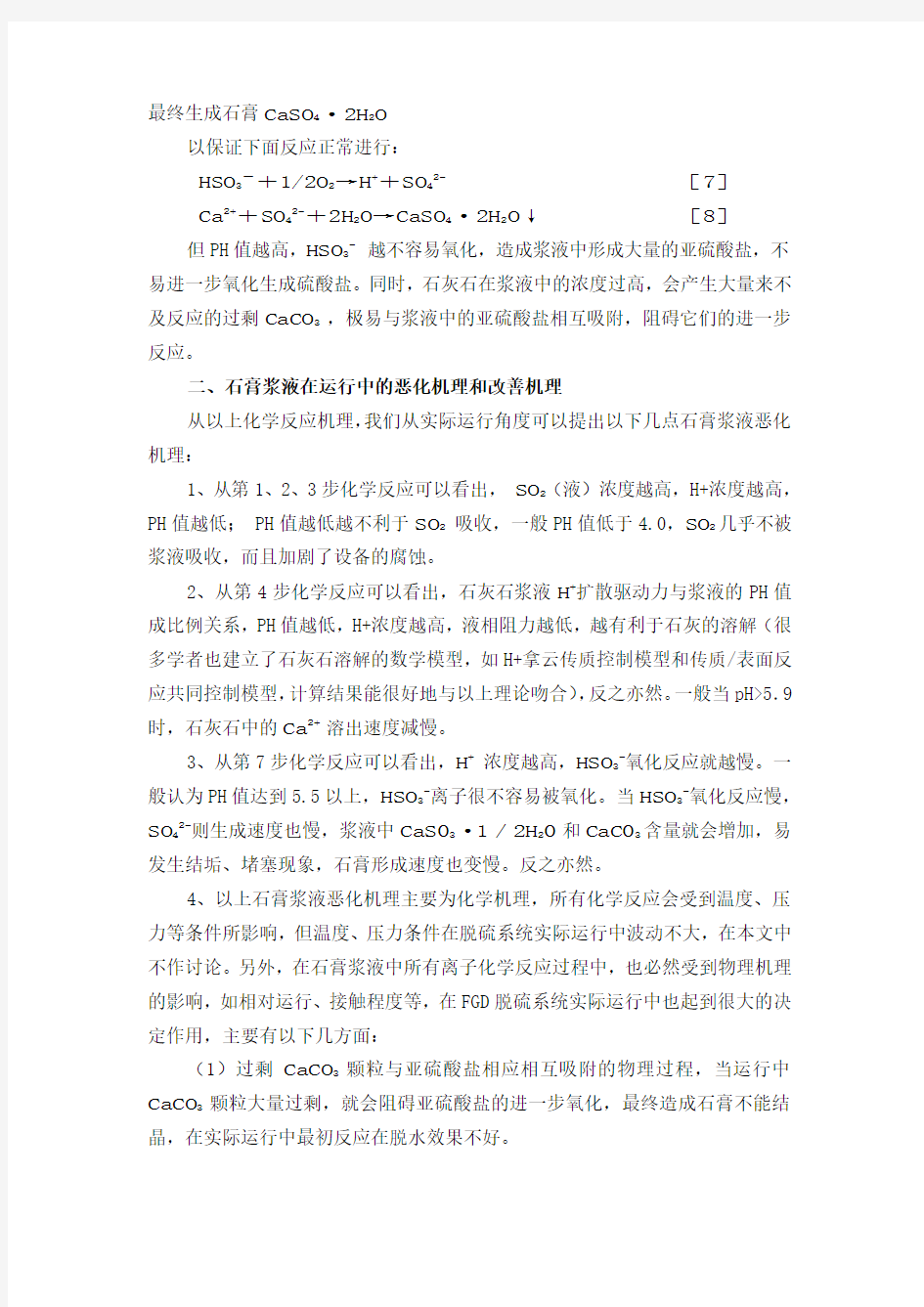
石灰石-石膏湿法烟气脱硫系统
运行中石膏浆液品质控制综论
引言
在石灰石-石膏湿法烟气脱硫系统(FGD)主要是利用石膏浆液来脱除烟气中的SO2,石膏浆液是通过循环泵从吸收塔浆液池抽出,打入喷淋层,形成石膏浆液雾化层,与烟气中SO2接触反应后,再回落到吸收塔浆液池中,进行二次反应,如此反复,形成石膏浆液在FGD 系统中的循环利用。由此可见,石膏浆液就像人体的血液一样重要,其品质的好坏,对FGD 系统的的性能有着重要影响。石膏浆液品质变差,会导致脱硫系统结垢、堵塞、电耗增加等现象,严重时会出现“石灰石盲区”现象,进一步造成系统效率降低、设备损坏,甚至影响系统不能正常运行。
本文结合江苏省射阳港发电有限责任公司二期FGD系统的实际运行数据,着重从石膏浆液的恶化机理和改善机理来阐述FGD系统在实际运行中石膏浆液品质好差的判断和控制,提前作出合理的运方调整,防止石膏浆液出现“石灰石盲区”现象的发生。
一、脱硫系统运行中石膏浆液化学反应机理
1、SO2的吸收机理
在脱硫系统吸收塔上部喷淋层,烟气中的S02首先被浆液中的水吸收,形成亚硫酸,并部分电离,产生H+、HSO3-、SO32-等离子:
SO2(气)+ H2O → SO2(液)+H2O [1]
SO2(液)+H2O → H++HSO3-[2]
H++HSO3-→2H++SO32-[3]
2、石灰石的溶解机理。
石膏浆液的PH值不仅影响SO2的吸收和亚硫酸钙的氧化,同时也会影响石灰石的溶解,因此对石灰石在脱硫系统中的反应活性有极重要的影响。
下面是石灰石溶解化学反应式:
CaCO3+H+→Ca2++HCO3-[4]
HCO3-+H+→H2CO3→H2O+CO2(气)[5]
3、石膏结晶机理
第一步,亚硫酸与吸收塔浆液中的CaCO3细颗粒反应生成CaSO3·1/2H2O细颗粒:
Ca2++SO32-→CaSO3·1/2H2O↓+H+[6]
第二步,通常在FGD工艺上会采用氧化风机向吸收塔石膏浆液中鼓入空气的方法,加强氧化HSO3-离子,CaSO3·1/2H2O被鼓入的空气中的氧气所氧化,
最终生成石膏CaSO4·2H2O
以保证下面反应正常进行:
HSO3-+1/2O2→H++SO42-[7]
Ca2++SO42-+2H2O→CaSO4·2H2O↓[8]
但PH值越高,HSO3-越不容易氧化,造成浆液中形成大量的亚硫酸盐,不易进一步氧化生成硫酸盐。同时,石灰石在浆液中的浓度过高,会产生大量来不及反应的过剩CaCO3 ,极易与浆液中的亚硫酸盐相互吸附,阻碍它们的进一步反应。
二、石膏浆液在运行中的恶化机理和改善机理
从以上化学反应机理,我们从实际运行角度可以提出以下几点石膏浆液恶化机理:
1、从第1、
2、3步化学反应可以看出,SO2(液)浓度越高,H+浓度越高,PH值越低; PH值越低越不利于SO2吸收,一般PH值低于4.0,SO2几乎不被浆液吸收,而且加剧了设备的腐蚀。
2、从第4步化学反应可以看出,石灰石浆液H+扩散驱动力与浆液的PH值成比例关系,PH值越低,H+浓度越高,液相阻力越低,越有利于石灰的溶解(很多学者也建立了石灰石溶解的数学模型,如H+拿云传质控制模型和传质/表面反应共同控制模型,计算结果能很好地与以上理论吻合),反之亦然。一般当pH>5.9时,石灰石中的Ca2+ 溶出速度减慢。
3、从第7步化学反应可以看出,H+浓度越高,HSO3-氧化反应就越慢。一般认为PH值达到5.5以上,HSO3-离子很不容易被氧化。当HSO3-氧化反应慢,SO42-则生成速度也慢,浆液中CaS03·1/2H20和CaC03含量就会增加,易发生结垢、堵塞现象,石膏形成速度也变慢。反之亦然。
4、以上石膏浆液恶化机理主要为化学机理,所有化学反应会受到温度、压力等条件所影响,但温度、压力条件在脱硫系统实际运行中波动不大,在本文中不作讨论。另外,在石膏浆液中所有离子化学反应过程中,也必然受到物理机理的影响,如相对运行、接触程度等,在FGD脱硫系统实际运行中也起到很大的决定作用,主要有以下几方面:
(1)过剩CaCO3 颗粒与亚硫酸盐相应相互吸附的物理过程,当运行中CaCO3 颗粒大量过剩,就会阻碍亚硫酸盐的进一步氧化,最终造成石膏不能结晶,在实际运行中最初反应在脱水效果不好。
(2)烟尘和石膏浆液中其他盐类和杂质,也会阻碍石膏浆液中的离子之间的充分反应。在实际运行中,控制烟尘含量和石膏浆液的杂质含量,也是非常必要的。
(3)石膏浆液中的各种成份如果不能充分接触,化学反应也会受到影响。如吸收塔搅拌器不能正常工作、石膏浆液池底有沉积等。
5、从以上机理分析,我们从实际运行角度可以提出以下几点石膏浆液改善机理:
(1)通过恶化机理第1、2条,我们可以通过降低PH值(一般降至4.1),并根据浆液的具体情况,保持相应时间,在浆液中产生大量H+离子,以使过剩CaCO3充分反应。
(2)通过恶化机理3,在低PH值条件下,一般在4.2以下,加大氧量,以促进亚硫酸根离子充分氧化,进而形成硫酸根离子。
(3)进一步减少过剩CaCO3 ,增加石灰石粉的细度,以使进入浆液的石灰石能够充分溶解和反应。
(4)控制原烟气烟尘含量和石膏浆液中的杂质含量。
三、FGD脱硫系统在实际运行中如何判断石膏浆液品质好与差
脱硫系统(FGD)运行时吸收塔浆液pH值控制在5.2~5.6,以确保CaC03石灰石的溶解平衡和SO2的吸收平衡,并按照脱硫效率90%~95%的要求设计,吸收塔系统的钙硫比保持在1.03左右,这是一个十分理想的性能指标。此时,从理论引来说,浆液中的硫主要是以HSO3-或SO3-的形态存在,而未与石灰石反应的H2S03或SO2数量极低,可以认为SO2的吸收和石灰石的溶解达到了动态平衡,CaC03的溶解速率等于SO2的吸收速率。
此时,我们可以按照各火电厂的脱硫系统运行规程对各运行参数进行正常的调整控制。但在实际运行中,脱硫的化学反应过程是一个动态过程,石膏浆液的品质也不能保始终保持稳定,影响因素很多,如何准确地判断与分析石膏浆液品质好与差,应紧密结合以上机理,并在实际运行中进行参数对比,以能够及时地调控石膏浆液品质,保证系统稳定运行。
根据射阳港发电厂二期脱硫系统实际运行数据,结合以上机理,我们来谈谈在实际运行中,如何有效、及时地判断石膏浆液品质变差。
1、PH值与脱硫效率的对应关系
实际运行描述:PH值能够正常调整,但脱硫效率与PH值不能很好对应,脱硫效率随PH上升而上升较慢,随着PH值降低而降低较慢。
在石膏浆液品质良好的状态下,PH值与脱硫效率有很好的对应关系,如图1。
当PH值升高时,脱硫效率亦同步升高,反之,亦然。当石膏浆液品质变差,与正常运行时的数值相比,随着PH值的升高,脱硫效率上升趋缓,PH值与脱硫效率对应关系不好,如图2,这需要运行人员在平时运行中注意对运行参数的分析对比。
出现上述情况后,我们认为此时石膏浆液活性已经开始变差,应及时分析存在的原因,调控石膏浆液品质,否则,石膏浆液品质会进一步恶化。
一般情况下,造成石膏浆液此种现象的主要原因有:第一,前期运行时间内石灰石供给量偏大,造成石膏浆液内碳酸盐含量长高,就会因4.1所述的恶化机理而造成石膏浆液品质变化;第二,石膏浆液中杂质较多,阻碍有益离子的正常接触反应;第三,PH值一直运行在较高水平,一般指5.8以上,此时供给大量的石灰石浆液,虽短时间内PH会升高,但HSO3-离子却不容易被氧化, SO42-则生成速度也会减慢,最终会打破整个SO2的吸收反应的整体平衡,脱硫效率下降;第四,其他的运行参数原因,如原烟气SO2含量偏高、烟气量偏大等,这是可明显控制的参数,这里不再累述。
2、石灰石浆液的供给量与PH值的变化关系
正常情况下,在脱硫系统外部数据变动不大的条件下,如机组负荷、原烟气SO2含量等,当石灰石供浆量变大时,PH值应相应升高,当减少石灰石供浆量时,PH应相应降低。而当外数据不变,石灰石供浆量不变时,PH值也不应有大的波动。但如果石膏浆液品质发生变化后,以上正常情况会发生改变,如图3中,是两组实际运行的数据,大家可以看到两条曲线1曲线2,是在相同条件、相同石灰石供浆量的情况下,PH值上升速度和幅度都不一样,当发生曲线2的情况,可以认为石膏浆液品质变差了。
造成石灰石供给量增大,而PH值上升缓慢的主要原因为供浆量增加情况下,
-+H+,使石灰石在低pH值时发生石灰石溶解过程中产生的H2CO3电离产生HCO
3
的反应为:
CaC03+2H+→Ca2++H2C03
而不是石灰石溶解平衡时的化学反应:
CaC03+H2O→Ca2++HC03+OH-,
石灰石的溶解并没有提高pH值,也不能提高浆液中的硫酸钙含量,结果是阻碍了石灰石的溶解。
为此时,在实际运行中,不能有两条曲线同时让运行人员对比,PH值上升速率应该保持多少为正常,这与脱硫系统的石灰石的品质、系统设计、测点位置等客观因素有关,不同类型、不同容量的脱硫系统应该不尽相同,运行人员应在平时运行中积累经验,在运行调整中进行对比分析。
3、烟尘含量超标对石膏浆液PH值的影响
在这里有一种特殊情况应特别注意,因国内燃煤资源越来越紧张,价格不断上涨,火力发电厂对煤碳品种的选择余地越来越小,有些煤种偏离锅炉设计煤种,指标差别较大,当燃煤中灰份含量较大时,有些火力发电厂为了保证脱硫系统的投运率,而将脱硫系统烟尘含量(一般不超过300mg/Nm3)保护退出,只设报警。运行中,当脱硫系统原烟气烟尘量较大时,且运行一段时间后,当不管石灰石供浆量提高多少,PH值升到某一数值后,不再发生变化,如图4。
根据相关文献资料,这种现象主要是由于电除尘后粉尘含量高或重金属成份高,在吸收塔浆液内形成一个稳定的化合物ALFn(其中n一般为2~4),附着在石灰石颗粒表面,影响石灰石颗粒的溶解和反应,导致石灰石供浆对pH值的调
节无效,这是石膏浆液产生氟化铝致盲的前兆。一般这种情况下PH值很难达到5.0,可以明显判断石膏浆液品质变差。此时,脱硫效率不会明显受到影响,但实际运行中如果不注意,为了提高PH值而大量提高石灰石浆液的供给量,会造成石膏浆液中碳酸盐含量大幅增加,出现亚硫酸盐含量超标,
3、石膏的化验数据与眼睛观察
以上石膏化验数据中,特别是对亚硫酸盐含量要特别注意,当亚硫酸盐含量大于标准值,或有增大趋势时,说明石膏浆液因某种原因,对亚硫酸盐氧化生成硫酸盐的过程起到了阻碍作用,应增加化验分析的次数,加强对比,注意在运行中进行调整,防止石膏浆液品质进一步恶化。
也可以在运行中,通过眼睛来观察石膏的品质,从而判断石膏浆液的总体状况。如石膏颜色变深、石膏中肉眼可见细小的杂质等,这都能说明石膏浆液的品质有所下降。
4、石膏浆液中的CL-含量
石膏浆液中的CL-、F-等主要来源为煤碳燃烧后析出和工艺水、石灰石带入系统内部,在火电厂的生产过程中,进入脱硫系统的CL-含量占主要比例。CL-含量增加,会与石膏浆液中的其他碱性离子反应生成难溶解的固体杂质,阻碍石膏浆液中离子间的正常化学反应。在运行中很难从运行参数中看出,需要通过石膏浆液的化验报告看出。
5、废水化验指标
三、FGD脱硫系统在实际运行中保证石膏浆液品质始终维持良好的状态
以上几种情况在脱硫系统运行中较常见,对石膏浆液品质的影响较为缓慢,也很隐蔽,但对系统稳定运行的危害较大,故以明确表述。那么在脱硫系统运行中如何进行及时调控,以避免上述情况发生呢?
1、pH值在实际运行中,采取高低值间断运行方式。
各火力发电厂脱硫运行规程一般规定pH值为5.0~5.8之间,在运行中pH 值具体控制在多少,一般都是根据机组负荷、原烟气SO2含量等决定。当机组负荷高、原烟气SO2含量也高时,此时石灰石供浆量会增加,pH值会运行在高值,才能满足SO2排放指标的要求。就是在正常运行工况下,维持石灰石浆液供给量的稳定,但因脱硫系统外部参数的小幅度变化,也会影响石膏浆液内部各种离子浓度的变化,特别是在机组负荷增加速度较快时,短时间内大幅度供给石灰石浆液,CaC03来不及溶解,Ca2+来不及被吸收,在石膏浆液中会残留CaC03细颗粒,根据恶化机理的2、3两条,此时,HSO3-、SO32-的含量也会增加,长时间运行必然造成石膏浆液内化学反应不平衡。
在实际运行中,可以采取pH值高、低间断运行方式。当机组负荷较高、原烟气SO2含量较高,可以提高pH值,运行一段时间后,如果SO2排放指标允许,应降低pH值至规程允许的低值运行。这样的运行方式,可以有效地减少石膏浆液中的CaC03、HSO3-、SO32-的含量,使石膏浆液内部的离子间在化学平衡不被有效打破前,保持一种动态的化学反应平衡,对石膏浆液品质是有力的保证。根据运行数据,一般每次pH值在5.1~5.2之间连续运行30分钟,即能有效降低石膏浆液中CaC03、HSO3-、SO32-的含量,使石膏浆液中的各化学反应趋于良好状态。如果运行工况许可,SO32-氧化和石膏结晶的最佳pH值在4.5 ~4.7,此环境下只要鼓入足够的空气,HSO3-、SO32-几乎可以全部氧化,保证石膏的结晶。
当机组负荷变动较大时,应立即切除供浆自动,采取手动控制石灰石浆液供给量,但也不能瞬间大幅度提高供给量。这要求在运行中,每次机组负荷、锅炉燃煤大幅度变动时,值长应提前通知脱硫运行人员,运行人员提前做出调控,这样能避免因石灰石供给量大幅变化而造成石膏浆液品质变化。
2、增开氧化风机
增开氧化风机,补充石膏浆液内的氧量,是改善石膏浆液品质的较好手段。在上一条已提到,石膏浆液内的化学反应是一个动态平衡过程,根据恶化机理第3条,强制氧化亚硫酸盐,是结晶生成硫酸盐的必要条件。那么在运行中什么情况下需要增开氧化风机来提高石膏浆液内的氧量呢?
根据运行经验,可以从以下几方面判断:
(1)比较脱硫系统进出口烟气氧量
当脱硫系统正常运行时,一般情况下净烟气有效氧量(是指减去脱硫系统漏风产生的氧量)比原烟气氧量高0.2~0.4为最适合氧量。当净烟气氧量等于或小于原烟气氧量时,应及时增开一台氧化风机,以保证石膏浆液中有足够的氧量。
脱硫系统漏风率,我们无需去进行测量,但在运行中掌握系统因漏风而造成的烟气氧量的增加值,应有可靠的数据。这是一项较为细致的工作,因为不同的烟气压力、不同的主机运行工况都会造成不一样的烟气漏风率,作为脱硫系统运行工程师是必然要掌握的。
(2)石膏的颜色
根据恶化机理,当石膏浆液中氧量不足,亚硫酸盐被强制氧化的过程就会减弱,浆液中亚硫酸盐含量超标。当亚硫酸盐含量超过一定数值后,脱出的石膏颜色就会比正常石膏颜色深,呈淡灰色或深灰色。此时,应立即增开氧化风机。
以颜色来判断石膏浆液中亚硫酸盐含量超标,还应排除其他两个原因,一是脱硫剂石灰石本来的颜色是否是清灰色;二是原烟气烟尘含量是否超标。因为这两点也会造成石膏颜色加深。
(3)脱水效果
亚硫酸盐的水溶性很好,较石膏晶体来说,脱水性能不强。当石膏浆液中亚硫酸盐含量超标更多时,直接会导致脱水系统不能正常脱水,脱出的“石膏”为半固体状,俗称“稀泥”。此时,应立即增开氧化风机,否则会对脱硫系统中其他设备造成严重危害,如结垢、堵塞、电耗增加等。
4、脱水系统运行时,废水系统一定要投入运行。
废水,固名思义,就是不能再用的水。在脱硫系统中,经过石膏浆液一级分享后的水经过高效旋流器再分离后,水内含有大量的氯酸盐、氟化铝等固体杂质,以及烟气、石灰石带入系统内的难溶性杂质,大部分被分享出来,此时的水是不能再作为滤液水的一部分打入吸收塔浆液池中的,否则,脱硫系统长期运行,石膏浆液品质必然变差。
所以,在脱水系统运行时,废水系统一定要正常投入运行。在运行中,可以根据废水的化验报告,来调整实际运行中的废水排出量。
5、当烟尘量大时,最有效的手段为:吸收塔溢流、废水排放。
6、当石膏浆液品质综合变差,运行中又不能大量转换浆液时,且吸收塔溢流堵塞、废水系统不能正常投运时,可以采取非正常手段来改善石膏浆液品质,但不影响系统安全运行。如:除雾器补水、滤液水系统补水
石灰石石膏湿法脱硫原理
石灰石-石膏湿法烟气脱硫工艺 石灰石(石灰)-石膏湿法脱硫工艺是湿法脱硫的一种,是目 前世界上应用范围最广、工艺技术最成熟的标准脱硫工艺技术。是当 前国际上通行的大机组火电厂烟气脱硫的基本工艺。它采用价廉易得 的石灰石或石灰作脱硫吸收剂,石灰石经破碎磨细成粉状与水混合搅 拌成吸收浆液,当采用石灰为吸收剂时,石灰粉经消化处理后加水制 成吸收剂浆液。在吸收塔内,吸收浆液与烟气接触混合,烟气中的二 氧化硫与浆液中的碳酸钙以及鼓入的氧化空气进行化学反应被脱除, 最终反应产物为石膏。脱硫后的烟气经除雾器除去带出的细小液滴, 经换热器加热升温后排入烟囱。脱硫石膏浆经脱水装置脱水后回收。 由于吸收浆液循环利用,脱硫吸收剂的利用率很高。最初这一技术是 为发电容量在100MW以上、要求脱硫效率较高的矿物燃料发电设备配 套的,但近几年来,这一脱硫工艺也在工业锅炉和垃圾电站上得到了 应用. 根据美国EPRI统计,目前已经开发的脱硫工艺大约有近百种,但真正实现工业应用的仅10多种。已经投运或正在计划建设的脱硫系统中,湿法烟气脱硫技术占80%左右。在湿法烟气脱硫技术中,石灰石/石灰—石膏湿法烟气脱流技术是最主要的技术,其优点是: 1、技术成熟,脱硫效率高,可达95%以上。 2、原料来源广泛、易取得、价格优惠 3、大型化技术成熟,容量可大可小,应用范围广
4、系统运行稳定,变负荷运行特性优良 5、副产品可充分利用,是良好的建筑材料 6、只有少量的废物排放,并且可实现无废物排放 7、技术进步快。 石灰石/石灰—石膏湿法烟气脱硫工艺,一般布置在锅炉除尘器后尾部烟道,主要有:工艺系统、DCS控制系统、电气系统三个分统。 基本工艺过程 在石灰石一石膏湿法烟气脱硫工艺中,俘获二氧化硫(SO2)的基本工艺过程:烟气进入吸收塔后,与吸收剂浆液接触、进行物理、化学反应,最后产生固化二氧化硫的石膏副产品。基本工艺过程为:(1)气态SO2与吸收浆液混合、溶解 (2) SO2进行反应生成亚硫根 (3)亚硫根氧化生成硫酸根 (4)硫酸根与吸收剂反应生成硫酸盐 (5)硫酸盐从吸收剂中分离 用石灰石作吸收剂时,SO2在吸收塔中转化,其反应简式式如下: CaCO3+2 SO2+H2O ←→Ca(HSO3)2+CO2 在此,含CaCO3的浆液被称为洗涤悬浮液,它从吸收塔的上部喷
石灰石-石膏湿法脱硫系统的设计计算解析
石灰石 - 石膏湿法脱硫系统 设计 (内部资料) 编制: x xxxx 环境保护有限公司 2014年 8 月 1.石灰石 - 石膏法主要特点 ( 1)脱硫效率高,脱硫后烟气中二氧化硫、烟尘大大减少,脱硫效率高达 95%以上。(2)技术成熟,运行可靠性高。国外火电厂湿法脱硫装置的投资效率一般可达98%以上,特别是新建的大机组采用湿法脱硫工艺,使用寿命长,可取得良好的投资效益。
(3)对燃料变化的适应范围宽,煤种适应性强。无论是含硫量大于 3%的高硫燃料,还是含 硫量小于 1%的低硫燃料,湿法脱硫工艺都能适应。 (4)吸收剂资源丰富,价格便宜。石灰石资源丰富,分布很广,价格也比其它吸收剂便宜。(5)脱硫副产物便于综合利用。副产物石膏的纯度可达到 90%,是很好的建材原料。 (6)技术进步快。近年来国外对石灰石 - 石膏湿法工艺进行了深入的研究与不断改进,可望使该工艺占地面积较大、造价较高的问题逐步得到妥善解决。 (7)占地面积大,一次性建设投资相对较大。 2.反应原理 (1)吸收剂的反应 购买回来石灰石粉(CaCO3)由石灰石粉仓投加到制浆池,石灰石粉与水结合生成脱硫浆液。 (2)吸收反应 烟气与喷嘴喷出的循环浆液在吸收塔内有效接触 ,循环浆液吸收大部分 SO2,反应如下: SO2(气)+H2O→H2SO3(吸收) H2SO3→ H+ +HSO3- H+ +CaCO3→ Ca2+ +HCO3-(溶解) Ca2+ +HSO3- +2H2O→ CaSO3·2H2O+H+(结晶) H+ +HCO3-→ H2CO3(中和) H2CO3→ CO 2+H2O 总反应式: SO2+ CaCO3+2H2O→CaSO3·2H2O+CO2 (3)氧化反应 一部分 HSO3-在吸收塔喷淋区被烟气中的氧所氧化,其它的 HSO3-在反应池中被氧化空气完全氧化并结晶,反应如下: CaSO3+1/2O2→ CaSO4(氧化) CaSO4+2H2O→CaSO4·2H2O(结晶) 4)其他污染物
石灰石石膏法脱硫方案
.. . . . .. xxxx有限公司 锅炉房扩建工程 2×75t/h锅炉烟气脱硫工程 技术方案 xxxx集团有限公司 2013年10月
目录 1 总述 (1) 1.1 项目概况 (1) 1.2基本设计条件 (1) 1.3 标准和规范 (1) 1.4性能保证 (2) 1.5总的技术要求 (3) 2 工艺描述 (5) 2.1 FGD系统及工艺描述 (5) 2.2 吸收塔中SO2,SO3,HF和HCl去除 (6) 2.3 SO2,SO3和HCl的吸收 (7) 2.4 与石灰石反应 (7) 2.5 氧化反应 (8) 2.6 吸收塔安装和设计 (8) 2.7 石灰石浆液制备系统 (9) 2.8 烟道系统 (9) 2.9 石膏的浓缩、净化和脱水 (9) 2.10 石灰石浆液制备系统 (10) 2.11 工艺水和石膏冲洗水供应 (10) 2.12 排放系统 (10) 3 机械部分 (11) 3.1总述 (11) 3.2 石灰石浆液制备系统 (12) 3.3 烟气系统 (13) 3.4 SO2吸收系统 (16) 3.5 排空及浆液抛弃系统 (20) 3.6 石膏脱水系统 (20) 3.7 工艺水 (22) 3.8 杂用气和仪用压缩空气系统 (22) 3.9 管道和阀门 (23) 3.10 箱罐和容器 (25) 3.11 泵 (25) 3.12 搅拌设备 (28) 3.13 检修起吊设施 (29) 3.14 钢结构,平台和扶梯 (29) 3.15 保温、油漆和隔音 (30) 3.16 防腐内衬及玻璃钢(FRP) (31) 3.17 材料、铸件和锻件 (37) 3.18 润滑 (37) 3.19 电动机 (37) 4 仪表及控制 (41) 4.1 总则 (41) 4.2系统设计要求及工作范围 (42) 4.3 供货范围 (44)
石灰石膏法脱硫运行规程
XXXX公司 脱硫运行规程 二零一五年五月
目录 第一篇脱硫系统运行规范 (1) 第一章脱硫系统主要特性 (1) 第一节石灰-石膏湿法脱硫工艺过程简介 (1) 第二节脱硫系统概述 (3) 第三节脱硫系统基本流程及简介 (3) 第二章检修后的试运 (6) 第一节脱硫装置大修后的检查 (6) 第二节转动机械的检查 (8) 第三节脱硫系统启动前的准备投运前的准备工作 (9) 第三章脱硫系统的启动、停止操作...................................................9第一节脱硫系统的启动 (9) 第二节脱硫系统的停
止 (11) 第四章脱硫系统运行中的控制与调整 (13) 第一节脱硫系统工艺控制的基本方法 (13) 第二节脱硫系统运行的检查维护 (15) 第五章事故处理 (19) 第一节总则 (19) 第二节紧急停止脱硫运行的规定 (20) 第三节转动机械故障 (20) 第四节10k V电源中断的处理 (21) 第五节380V电源中断的处理 (22) 第六节脱硫塔循环泵全停的处理 (22) 第七节工艺水中断的处理 (23) 第八节脱硫效率低的处
理 (24) 第九节其它故障及其处理 (25) 第二篇石膏脱水系统运行规程 (29) 第一章真空皮带机运行原理 (29) 第二章真空皮带机设备 (29) 第三章脱水系统运行操作 (30) 第一节石膏脱水系统启动前的检查与准备 (30) 第二节脱水皮带机的启动 (32) 第三节脱水系统的停止 (32) 第四节运行操作注意事项 (32) 第五节脱水系统运行中监视的内容 (33) 第三篇石灰浆液制备系统运行规程 (33) 第一章石灰浆液制备系统概
石灰石石膏湿法脱硫原理
深度脱硫工艺流程简介 班级:应化141 :段小龙寇润宋蒙蒙 王春维贺学磊
石灰石-石膏湿法烟气脱硫工艺 石灰石(石灰)-石膏湿法脱硫工艺是湿法脱硫的一种,是目前世界上应用围最广、工艺技术最成熟的标准脱硫工艺技术。是当前国际上通行的大机组火电厂烟 气脱硫的基本工艺。它采用价廉易得的石灰石或石灰作脱硫吸收剂,石灰石经破 碎磨细成粉状与水混合搅拌成吸收浆液,当采用石灰为吸收剂时,石灰粉经消化 处理后加水制成吸收剂浆液。在吸收塔,吸收浆液与烟气接触混合,烟气中的二 氧化硫与浆液中的碳酸钙以及鼓入的氧化空气进行化学反应被脱除,最终反应产 物为石膏。脱硫后的烟气经除雾器除去带出的细小液滴,经换热器加热升温后排 入烟囱。脱硫石膏浆经脱水装置脱水后回收。由于吸收浆液循环利用,脱硫吸收 剂的利用率很高。最初这一技术是为发电容量在100MW以上、要求脱硫效率较 高的矿物燃料发电设备配套的,但近几年来,这一脱硫工艺也在工业锅炉和垃圾 电站上得到了应用. 根据美国EPRI统计,目前已经开发的脱硫工艺大约有近百种,但真正实现工业应用的仅10多种。已经投运或正在计划建设的脱硫系统中,湿法烟气脱硫技术占80%左右。在湿法烟气脱硫技术中,石灰石/石灰—石膏湿法烟气脱流技术是最主要的技术,其优点是: 1、技术成熟,脱硫效率高,可达95%以上。 2、原料来源广泛、易取得、价格优惠 3、大型化技术成熟,容量可大可小,应用围广 4、系统运行稳定,变负荷运行特性优良 5、副产品可充分利用,是良好的建筑材料
6、只有少量的废物排放,并且可实现无废物排放 7、技术进步快。 石灰石/石灰—石膏湿法烟气脱硫工艺,一般布置在锅炉除尘器后尾部烟道,主要有:工艺系统、DCS控制系统、电气系统三个分统。 基本工艺过程 在石灰石一石膏湿法烟气脱硫工艺中,俘获二氧化硫(SO 2 )的基本工艺过程:烟气进入吸收塔后,与吸收剂浆液接触、进行物理、化学反应,最后产生固化二氧化硫的石膏副产品。基本工艺过程为: (1)气态SO 2 与吸收浆液混合、溶解 (2)SO 2 进行反应生成亚硫根 (3)亚硫根氧化生成硫酸根 (4)硫酸根与吸收剂反应生成硫酸盐 (5)硫酸盐从吸收剂中分离 用石灰石作吸收剂时,SO 2 在吸收塔中转化,其反应简式式如下: CaCO 3+2 SO 2 +H 2 O=Ca(HSO 3 ) 2 +CO 2 在此,含CaCO 3 的浆液被称为洗涤悬浮液,它从吸收塔的上部喷入到烟气 中。在吸收塔中SO 2被吸收,生成Ca(HSO 3 ) 2 ,并落入吸收塔浆池中。 当pH值基本上在5和6之间时,SO 2 去除率最高。因此,为了确保持续高 效地俘获二氧化硫(SO 2 )必须采取措施将PH值控制在5和6之间;为了确保要 将PH值控制在5和6之间和促使反应向有利于生成2H+和SO 3 2-的方向发展,持 续高效地俘获二氧化硫(SO 2 ),必须采取措施至少从上面方程式中去掉一项反应
4x150万吨锅炉石灰石膏法脱硫方案
第一章,概述 项目背景 工程概况 西安西联热电有限公司现有4台150t/h循环流化床锅炉投入使用,根据环保要求,需要配套建设相应的脱硫除尘设施,将排放烟气中的二氧化硫浓度控制在150mg/ m3以下。烟尘排放浓度:≤50mg/Nm3。 第二章,设计依据 设计标准 (1)《工业锅炉及炉窑湿法烟气脱硫工程技术规范》HJ462-2009(2)《中华人民共和国环境保护法》(1989年12月26日通过)(3)《中华人民共和国大气染污防治法》(2004年4月29通过)(4)《大气污染物综合排放标准》GB16297-1996 (5)《火电厂大气污染排放标准》GB13223-2003 (6)《锅炉大气污染物排放标准》GB13271-2001 (7)《环境空气质量标准》GB3095-2012 (8)《工业企业厂界噪声标准》GB12348-90 (9)《污水综合排放标准》GB8978-1996 (10)《建筑给排水设计规范》GB50015-2003
(11)《建筑地基基础设计规范》GB50007-2002 (12)《混凝土结构设计规范》GB50010-2002 (13)《花岗岩类湿式烟气脱硫除尘装置》HJT319-2006 (14)《花岗岩建材检验标准》JC204-205-1996 (15)《脱硫除尘专用建材检验标准》GB/ (16)《湿式烟气脱硫除尘装置技术要求》HJ/T288-2006 (17)《压力容器技术管理规定》YB9070—92 (18)《钢制压力容器》GBl50—98 设计原则 (1)贯彻执行国家经济建设和新、改、扩建项目的一系列方针政策 和规范,在工程设计中贯彻切合实际、技术先进、经济合理、安全适 用原则,确保排放烟气达标并最大限度地提高工程的经济效益。 (2)选用先进可靠的脱硫技术工艺,确保脱硫效率高的前提下,强 调系统的安全、稳定性能,并减少系统运行费用。 (3)充分结合厂方现有的客观条件,因地制宜,制定具有针对性的 技术方案。 (4)系统平面布置要求紧凑、合理、美观,实现功能分区,方便运行管理。 (5)操作简单、维护方便、可靠性高、噪音小、运行稳定,无二次 污染。
石灰石石膏湿法脱硫原理
石灰石石膏湿法脱硫原理
深度脱硫工艺流程简介 班级:应化 141 姓名:段小龙寇润宋蒙蒙 王春维贺学磊 石灰石- 石膏湿法烟气脱硫工艺 石灰石(石灰)-石膏湿法脱硫工艺是湿法脱硫的一种,是目前世界上应用范围最广、工艺技术最成熟的标准脱硫工艺技术。是当前国际上通行的大机组火电厂烟气脱硫的基本工艺。它采用价廉易得的石灰石或石灰作脱硫吸收剂,石灰石经破碎磨细成粉状与水混合搅拌成吸收浆
液,当采用石灰为吸收剂时,石灰粉经消化处理后加水制成吸收剂浆液。在吸收塔内,吸收浆液与烟气接触混合,烟气中的二氧化硫与浆液中的碳酸钙以及鼓入的氧化空气进行化学反应被脱除,最终反应产物为石膏。脱硫后的烟气经除雾器除去带出的细小液滴,经换热器加热升温后排入烟囱。脱硫石膏浆经脱水装置脱水后回收。由于吸收浆液循环利用,脱硫吸收剂的利用率很高。最初这一技术是为发电容量在100MW 以上、要求脱硫效率较高的矿物燃料发电设备配套的,但近几年来,这一脱硫工艺也在工业锅炉和垃圾电站上得到了应用. 根据美国EPRI统计,目前已经开发的脱硫工艺大约有近百种,但真正实现工业应用的仅10 多种。已经投运或正在计划建设的脱硫系统中,湿法烟气脱硫技术占80% 左右。在湿法烟气脱硫技术中,石灰石/ 石灰—石膏湿法烟气脱流技术是最主要的技术,其优点是: 1、技术成熟,脱硫效率高,可达95%以上。 2、原料来源广泛、易取得、价格优惠 3、大型化技术成熟,容量可大可小,应用范围广 4、系统运行稳定,变负荷运行特性优良 5、副产品可充分利用,是良好的建筑材料 6、只有少量的废物排放,并且可实现无废物排放 7、技术进步快。 石灰石/ 石灰—石膏湿法烟气脱硫工艺,一般布置在锅炉除尘器后尾部烟道, 主要有:工艺系统、DCS控制系统、电气系统三个分统。 基本工艺过程 在石灰石一石膏湿法烟气脱硫工艺中,俘获二氧化硫(SO)的基本工艺 过程:烟气进入吸收塔后,与吸收剂浆液接触、进行物理、化学反应,最后产生固化二氧化硫的石膏副产品。基本工艺过程为: (1) 气态SO2 与吸收浆液混合、溶解 (2)SO2进行反应生成亚硫根 (3)亚硫根氧化生成硫酸根 (4)硫酸根与吸收剂反应生成硫酸盐 (5)硫酸盐从吸收剂中分离 用石灰石作吸收剂时,SQ在吸收塔中转化,其反应简式式如下:
石灰石石膏法
石灰石石膏法
石灰/石灰石-石膏法脱硫 石灰/石灰石一石膏法烟气脱硫技术最早是由英国皇家化学工业公司提出的,该方法脱硫的基本原理是用石灰或石灰石浆液吸收烟气中的SO2,先生成亚硫酸钙,然后将亚硫酸钙氧化为硫酸钙。副产品石膏可抛弃也可以回收利用。 (1)反应原理 用石灰石或石灰浆液吸收烟气中的二氧化硫分为吸收和氧化两个工序,先吸收生成亚硫酸钙,然后再氧化为硫酸钙,因而分为吸收和氧化两个过程。 1)吸收过程在吸收塔内进行,主要反应如下。 石灰浆液作吸收剂:Ca(OH)2+SO2一CaSO3.1/2H2O 石灰石浆液吸收剂:Ca(OH)2+1/2SO2一CaSO3.1/2H2O+CO2 CaSO3.1/2H2O+SO2+1/2H2O一Ca(HSO3)2 由于烟道气中含有氧,还会发生如下副反应。 2CaSO3.1/2Hz0+O2+3 H2O一2CaSO4.2H20 ②氧化过程在氧化塔内进行,主要反应如下。 2 CaSO3·1/2H20+O2+3H2O一2CaSO4·2H20 Ca(HSO3)2+1/2O2+H2O一CaSO4·H2O+SO2
传统的石灰/石灰石一石膏法的工艺流程如图所示。将配好的石灰浆液用泵送人吸收塔顶部,经过冷却塔冷却并除去90%以上的烟尘的含Sq烟气从塔底进人吸收塔,在吸收塔内部烟气与来自循环槽的浆液逆向流动,经洗涤净化后的烟气经过再加热装置通过烟囱排空。石灰浆液在吸收so:后,成为含有亚硫酸钙和亚硫酸氢钙的棍合液,将此混合液在母液槽中用硫酸调整pH值至4左右,送人氧化塔,并向塔内送人490kPa的压缩空气进行氧化,生成的石膏经稠厚器使其沉积,上层清液返回循环槽,石膏浆经离心机分离得成品石膏。 现代石灰/石灰石一石膏法工艺流程主要有原料运输系统、石灰石浆液制备系统、烟气脱硫系统、石膏制备系统和污水处理系统。 ①原料运输系统烟气脱硫所需的石灰石粉(粒度为250目,筛余量为5%),采用自卸封罐车运输,并卸人石灰石料仓。每个料仓可有多个进料口,能同时进行多台运料车卸料作业。在每个仓底设有粉碎装置,仓顶安装布袋除尘器。 ②浆液制备系统石灰石粉料从料仓下部出来,经给料机及输送机送人石灰石浆液槽。 石灰石浆液槽为混凝土结构,内衬树脂防腐,容积为l00m3”左右。浆液浓度约为30%,用调节给水量来控制浆液浓度。 ③烟气脱硫系统烟气脱硫系统主要由吸收塔、烟气再加热装置、旁路系统、有机剂 添加装置及烟囱组成。 吸收塔是脱硫装置的核心设备,现普遍采用的集冷却、再除尘、吸收和氧化为一体的新型吸收塔。常见的有喷淋空塔、
氨法、石灰石石膏法、干法脱硫方案比选
氨法脱硫、半干法、石灰石石膏法方案 比选 工艺流程比较 半干法烟气脱硫 半干法以生石灰(CaO)为吸收剂,将生石灰制备成Ca(OH) 2 浆 液,或消化制成干式Ca(OH) 2 粉(也可以直接使用电石渣),然后将 Ca(OH) 2浆液或Ca(OH) 2 粉喷入吸收塔,同时喷入调温增湿水,在反应 塔内吸收剂与烟气混合接触,发生强烈的物理化学反应,一方面与烟 气中SO 2 反应生成亚硫酸钙;另一方面烟气冷却,吸收剂水分蒸发干 燥,达到脱除SO 2 的目的,同时获得固体分装脱硫副产物。原则性的工艺流程见下图。 半干法烟气脱硫工艺示意图 整套脱硫系统包含:预除尘系统,脱硫系统,脱硫后除尘系统,
吸收剂供应系统,灰再循环系统,灰外排系统,工艺水系统及其他公用系统。 目前半干法应用案例较成功的主要是福建龙净环保公司研发的DSC-M干式超净工艺,在广州石化有应用业绩。主要烟气脱硫机理为:锅炉烟气从竖井烟道出来后,先进入预电除尘器进行除灰,将大颗粒的飞灰收集、循环送回炉膛。经预电除尘器之后,烟气从半干法脱硫塔底部进入,与加入的吸收剂、循环灰及水发生反应,除去烟气中的SO 2 等气体。烟气中夹带的吸收剂和脱硫灰,在通过脱硫吸收塔下部的文丘里管时,受到气流的加速而悬浮起来,形成激烈的湍动状态,使颗粒与烟气之间具有很大的相对滑落速度,颗粒反应界面不断摩擦、碰撞更新,从而极大地强化了气固间的传热、传质。同时为了达到最佳的反应温度,通过向脱硫塔内喷水,使烟气温度冷却到高于烟气露点温度15℃以上。主要化学反应式为: Ca(OH) 2+SO 2 =CaSO 3 ·1/2 H 2 O+1/2H 2 O Ca(OH) 2+SO 3 =CaSO 4 ·1/2H 2 O+1/2H 2 O CaSO 3·1/2H 2 O+1/2O 2 =CaSO 4 ·1/2H 2 O 2Ca(OH) 2+2HCl=CaCl 2 ·Ca(OH) 2 ·2H 2 O 半干法脱硫技术特点:一是烟囱不需防腐、排放透明,无视觉污染。二是无废水产生,半干法脱硫技术采用干态的生石灰作为吸收剂,在岛内直接消化成消石灰,脱硫副产物为干态的,整个系统无废水产生,不必配套污水处理设施。缺点是脱硫剂成本高、脱硫效率较低等。 石灰石-石膏法烟气脱硫 石灰石(石灰)-石膏湿法脱硫工艺(简称钙法)采用石灰石或石灰作脱硫吸收剂,石灰石经破碎磨细成粉状与水混合搅拌制成吸收浆液。当采用石灰为吸收剂时,石灰粉经消化处理后加水搅拌制成吸收浆。在吸收塔内,吸收浆液与烟气接触混合,烟气中的SO2与浆液中的碳酸钙以及鼓入的氧化空气进行化学反应而被脱除,最终反应产物为石膏。脱硫后的烟气经除雾器除去带出的细小液滴,
脱硫工艺-强制氧化石灰石石膏法计算步骤
脱硫工艺-强制氧化石灰石石膏法计算步骤2008-06-17 17:51:25) 由于本人并非工艺设计人员,所以这个计算步骤有可能存在不足之处;但应该是脱硫工艺入门同行有的参考价值的计算向导。 首先,根据所给的烟气成分,计算烟气的分子量,烟气的湿度等。 其次,要先行计算出吸收塔的进口及出口烟气的状况。 1 假定吸收塔出口的温度T1(如果有GGH,则需要先行假定两个温度,即吸收塔进口T0及出口温度。) 2 利用假定的出口温度,查表可以知道对应改温度的饱和蒸汽压P as。 3 由H as=0.622P as/(P-Pas)可以求出改温度下的饱和水湿度 4 由已知的进口温度T0、r0、C H(C H= 1.01+1.88H0)、H0,可以求出 T as=T0-(r0*(H as-H0)/(1.01+1.88 H0))(H0:初始烟气的湿度,r0=2490) 5 如果T as接近于 T1,那么这个假定温度可以接受,若果与假定温度相距太远,则该温度不能接受,需要重新假定。 (上述为使用试差法的绝热饱和计算过程,对于技术上涉外的项目,一般外方公司会提供,上面一部分的计算软件无须人工手算的) 6 有GGH时,假定吸收塔出口温度经已确定后,判断该温升是否符合GGH出口与入口的烟温差,假如烟温差同样适合的话,再校验GGH的释放热量问题。 再次,在确定好吸收塔出口气体的流量后,利用除雾器的最大流速限值,计算出吸收塔的直径。再根据进口烟气限速,计算出烟气进口的截面积。 7 由提供的液气比L/G可以计算出,喷淋所需的吸收液流量。由这个吸收液流量,再按照经验停留时间,可以计算出循环水箱的容积。同样根据经验需要的氧化时间及设计的氧气上升速度,可以计算出循环水箱的液位高度。那么就可以计算出整个吸收塔基循环水箱的截面积。 8 计算消耗的石灰石用量 由入口的二氧化硫浓度以及设计的二氧化硫脱除率可以知道脱除的二氧化硫。 对于烟气的三氧化硫而言,其脱除率达100%,所以多氧化硫物质的脱除量可以计算出来。
石灰石石膏湿法脱硫培训教材
灰-膏湿法烟气脱硫工艺 灰(灰)-膏湿法脱硫工艺是湿法脱硫的一种,是目前世界上 应用围最广、工艺技术最成熟的标准脱硫工艺技术。是当前国际上通 行的大机组火电厂烟气脱硫的基本工艺。它采用价廉易得的灰或灰作 脱硫吸收剂,灰经破碎磨细成粉状与水混合搅拌成吸收浆液,当采用 灰为吸收剂时,灰粉经消化处理后加水制成吸收剂浆液。在吸收塔, 吸收浆液与烟气接触混合,烟气中的二氧化硫与浆液中的碳酸钙以及 鼓入的氧化空气进行化学反应被脱除,最终反应产物为膏。脱硫后的 烟气经除雾器除去带出的细小液滴,经换热器加热升温后排入烟囱。 脱硫膏浆经脱水装置脱水后回收。由于吸收浆液循环利用,脱硫吸收 剂的利用率很高。最初这一技术是为发电容量在100MW以上、要 求脱硫效率较高的矿物燃料发电设备配套的,但近几年来,这一脱硫 工艺也在工业锅炉和垃圾电站上得到了应用. 根据美国EPRI统计,目前已经开发的脱硫工艺大约有近百种,但真正实现工业应用的仅10多种。已经投运或正在计划建设的脱硫系统中,湿法烟气脱硫技术占80%左右。在湿法烟气脱硫技术中,灰/灰—膏湿法烟气脱流技术是最主要的技术,其优点是: 1、技术成熟,脱硫效率高,可达95%以上。 2、原料来源广泛、易取得、价格优惠 3、大型化技术成熟,容量可大可小,应用围广 4、系统运行稳定,变负荷运行特性优良
5、副产品可充分利用,是良好的建筑材料 6、只有少量的废物排放,并且可实现无废物排放 7、技术进步快。 灰/灰—膏湿法烟气脱硫工艺,一般布置在锅炉除尘器后尾部烟道,主要有:工艺系统、DCS控制系统、电气系统三个分统。 基本工艺过程 在灰一膏湿法烟气脱硫工艺中,俘获二氧化硫(SO2)的基本工艺过程:烟气进入吸收塔后,与吸收剂浆液接触、进行物理、化学反应,最后产生固化二氧化硫的膏副产品。基本工艺过程为: (1)气态SO2与吸收浆液混合、溶解 (2)SO2进行反应生成亚硫根 (3)亚硫根氧化生成硫酸根 (4)硫酸根与吸收剂反应生成硫酸盐 (5)硫酸盐从吸收剂中分离 用灰作吸收剂时,SO2在吸收塔中转化,其反应简式式如下: CaCO3+2 SO2+H2O ←→Ca(HSO3)2+CO2在此,含CaCO3的浆液被称为洗涤悬浮液,它从吸收塔的上部喷入到烟气中。在吸收塔中SO2被吸收,生成Ca(HSO3)2 ,并落入
石灰石-石膏湿法脱硫系统的设计计算解析
石灰石-石膏湿法脱硫系统 设计 (内部资料) 编制:xxxxx环境保护有限公司 2014年8月
1.石灰石-石膏法主要特点 (1)脱硫效率高,脱硫后烟气中二氧化硫、烟尘大大减少,脱硫效率高达95%以上。 (2)技术成熟,运行可靠性高。国外火电厂湿法脱硫装置的投资效率一般可达98%以上,特别是新建的大机组采用湿法脱硫工艺,使用寿命长,可取得良好的投资效益。 (3)对燃料变化的适应范围宽,煤种适应性强。无论是含硫量大于3%的高硫燃料,还是含硫量小于1%的低硫燃料,湿法脱硫工艺都能适应。 (4)吸收剂资源丰富,价格便宜。石灰石资源丰富,分布很广,价格也比其它吸收剂便宜。(5)脱硫副产物便于综合利用。副产物石膏的纯度可达到90%,是很好的建材原料。 (6)技术进步快。近年来国外对石灰石-石膏湿法工艺进行了深入的研究与不断改进,可望使该工艺占地面积较大、造价较高的问题逐步得到妥善解决。 (7)占地面积大,一次性建设投资相对较大。 2.反应原理 (1)吸收剂的反应 购买回来石灰石粉(CaCO3)由石灰石粉仓投加到制浆池,石灰石粉与水结合生成脱硫浆液。(2)吸收反应 烟气与喷嘴喷出的循环浆液在吸收塔内有效接触,循环浆液吸收大部分SO2,反应如下: SO2(气)+H2O→H2SO3(吸收) H2SO3→H+ +HSO3- H+ +CaCO3→ Ca2+ +HCO3-(溶解) Ca2+ +HSO3-+2H2O→ CaSO3·2H2O+H+ (结晶) H+ +HCO3-→H2CO3(中和) H2CO3→CO2+H2O 总反应式:SO2+CaCO3+2H2O→CaSO3·2H2O+CO2 (3)氧化反应 一部分HSO3-在吸收塔喷淋区被烟气中的氧所氧化,其它的HSO3-在反应池中被氧化空气完全氧化并结晶,反应如下: CaSO3+1/2O2→CaSO4(氧化) CaSO4+2H2O→CaSO4·2H2O(结晶) (4)其他污染物
石灰石-石膏湿法烟气脱硫工艺的化学原理
石灰石-石膏湿法烟气脱硫工艺的化学原理 一、概述:脱硫过程就是吸收,吸附,催化氧化和催化还原,石灰石浆液洗涤含SO烟气,产生化学反应分离出脱硫副产物,化学吸收速率较快与扩散速率有关, 2又与化学反应速度有关,在吸收过程中被吸收组分的气液平衡关系,既服从于相平衡(液气比L/G,烟气和石灰石浆液的比),又服从于化学平衡(钙硫比Ca/S,二氧化硫与炭酸钙的化学反应)。 1、气相:烟气压力,烟气浊度,烟气中的二氧化硫含量,烟尘含量,烟气中的氧含量,烟气温度,烟气总量 2、液相:石灰石粉粒度,炭酸钙含量,黏土含量,与水的排比密度, -,它们与溶解了的CaCO和SOHSO的反应3、气液界面处:参加反应的主要是323是瞬间进行的。 二、脱硫系统整个化学反应的过程简述: 1、 SO在气流中的扩散,2 2、扩散通过气膜 3、 SO被水吸收,由气态转入溶液态,生成水化合物2 4、 SO水化合物和离子在液膜中扩散2 5、石灰石的颗粒表面溶解,由固相转入液相 6、中和(SO水化合物与溶解的石灰石粉发生反应)2 7、氧化反应 8、结晶分离,沉淀析出石膏, 三、烟气的成份:火力发电厂煤燃烧产生的污染物主要是飞灰、氮氧化物和二氧化硫,使用静电除尘器可控制99%的飞灰污染。 四、二氧化硫的物理、化学性质: ①. 二氧化硫SO的物理、化学性质:无色有刺激性气味的有毒气体。密度比2 空气大,易液化(沸点-10℃),易溶于水,在常温、常压下,1体积水大约能溶解40体积的二氧化硫,成弱酸性。SO为酸性氧化物,具有酸性氧化物的通性、2 还原性、氧化性、漂白性。还原性更为突出,在潮湿的环境中对金属材料有腐蚀性,液体SO无色透明,是良好的制冷剂和溶剂,还可作防腐剂和消毒剂及还原2剂。 ②. 三氧化硫SO的物理、化学性质:由二氧化硫SO催化氧化而得,无色易挥23发晶体,熔点16.8℃,沸点44.8℃。SO为酸性氧化物,SO极易溶于水,溶于33水生成硫酸HSO,同时放出大量的热,42③. 硫酸HSO的物理、化学性质:二元强酸,纯硫酸为无色油状液体,凝固点423,浓硫酸溶于水会放出大量的热,密度为1.84g/cm具有10.4℃,沸点338℃,为强氧化性(是强氧化剂)和吸水性,具有很强的腐蚀性和破坏性, 五、石灰石湿-石膏法脱硫化学反应的主要动力过程: 1、气相SO被液相吸收的反应:SO经扩散作用从气相溶入液相中与水生成亚硫 22-+,当PHH 亚硫酸迅速离解成亚硫酸氢根离子HSO值较高时,和氢离子酸HSO3232-,要使SO吸收不断进行下去,必须中和HSO二级电离才会生成较高浓度的SO233++当,即降低吸收剂的酸度,碱性吸收剂的作用就是中和氢离子电离产生的HH 吸收液中的吸收剂反应完后,如果不添加新的吸收剂或添加量不足,吸收液的酸度迅速提高,PH值迅速下降,当SO溶解达到饱和后,SO的吸收就告停止,脱22硫效率迅速下降
石灰石 石膏湿法脱硫技术的工艺流程 反应原理及主要系统
石灰石-石膏湿法脱硫技术的工艺流程 如下图的石灰石-石膏湿法烟气脱硫技术的工艺流程图。 图一常见的脱硫系统工艺流程 图二无增压风机的脱硫系统 如上图所示引风机将除尘后的锅炉烟气送至脱硫系统,烟气经增压风机增压后(有的系统在增压风机后设有GGH换热器,我们一、二期均取消了增压风机,和旁路挡板,图二),进入脱硫塔,浆液循环泵将吸收塔的浆液通过喷淋层的喷嘴喷出,与从底部上升的烟气发生接触,烟气中SO2的与浆液中的石灰石发生反应,生成CaSO3,从而除去烟气中的SO2。经过净化后的烟气在流经除雾器后被除去烟气中携带的液滴,最后从烟囱排出。反应生成物CaSO3进入吸收塔底部的浆液池,被氧化风机送入的空气强制氧化生成CaSO4,结晶生成石膏。石灰石浆液泵为系统补充反应消耗掉的石灰石,同时石膏浆液输送泵将吸收塔产生的石
膏外排至石膏脱水系统将石膏脱水或直接抛弃。同时为了防止吸收塔内浆液沉淀在底部设有浆液搅拌系统,一期采用扰动泵,二期采用搅拌器。 石灰石-石膏湿法脱硫反应原理 在烟气脱硫过程中,物理反应和化学反应的过程相对复杂,吸收塔由吸收区、氧化区和结晶区三部分组成,在吸收塔浆池(氧化区和结晶区组成)和吸收区,不同的层存在不同的边界条件,现将最重要的物理和化学过程原理描述如下:(1)SO2溶于液体 在吸收区,烟气和液体强烈接触,传质在接触面发生,烟气中的SO2溶解并转化成亚硫酸。 SO2+H2O<===>H2SO3 除了SO2外烟气中的其他酸性成份,如HCL和HF也被喷入烟气中的浆液脱除。装置脱硫效率受如下因素影响,烟气与液体接触程度,液气比、雾滴大小、SO2含量、PH值、在吸收区的相对速度和接触时间。 (2)酸的离解 当SO2溶解时,产生亚硫酸,同时根据PH值离解: H2SO3<===>H++HSO3-对低pH值 HSO3-<===>H++SO32-对高pH值 从烟气中洗涤下来的HCL和HF,也同时离解: HCl<===>H++Cl-F<===>H++F- 根据上面反应,在离解过程中,H+离子成为游离态,导致PH值降低。浆液中H+离子的增加,导致SO2在浆液中的溶解量减少。因此,为使浆液能够再吸收SO2,必须清除H+离子。H+离子的清除采用中和的方式。
石灰石石膏法湿法脱硫技术操作规程
第一部分石灰石—石膏法湿法脱硫装置的运行 第一章脱硫系统概述 第一节安全规程 第1条本运行规程必须与国家有关部门与行业、主管部门及本企业颁布实行的通用安全规程、安全指南、国家学会指南、工人自身安全规程与通用事故预防法规结合起来使用。 第2条必须遵守有关防止空气污染的各项法律、法令与技术说明、以及防止噪音与保护水质的各项措施。 第3条一旦出现本运行规程始料不及的运行故障与装置故障时,运行人员必须像专家一样熟练的采取行动,以防止可能出现的损坏。 第4条在装置运行期间要遵守装置专用运行说明,同时必须遵守运行说明中包含的各种规则。 第5条本运行规程要求运行人员认真仔细地观察烟气脱硫装置的各个程序,以便识别发生的各种异变并做出正确的判断,必要时排除异常情况。 第6条新运行人员通过本运行规程的学习,力争尽快精通本脱硫装置的运行、维护等工作。通过充分地与协调一致的应用本运行规程中的信息,应当达到以下几点: 1装置达到最大的可能利用率; 2不延迟验收烟气; 3最大限度地减少烟囱上游已处理烟气中的污染物; 4由于对装置进行预防性巡回检察,因而能确定在最佳时间进行维修工作; 5能确保对人员与装置的保护。 第7条启动调试已排空的系统(系统排空等)期间需要特别熟练的动作,以避免由于干运行,气穴现象与水锤而可能造成的损坏。在装置或其部件按计划长期停止运行时,尤其就是浆液输送管路,必须特别注意要完全排空并进行充分的冲洗。 第8条在检修关闭的槽罐与烟道之前与期间,必须检查防漏烟气的密封件;并要保证能充分的排空。要严格遵守有关的槽灌与狭小室内工作的指南(有中毒危险!!)。 第9条遵守意外事故预防规则;熟练操作装置;在处理化学物质时遵守涉及有损健康的运行说明;一旦发生火灾时的行为准则与灭火器的使用。 第10条安排与维持好各项设施,满足现有的各项规定,并尽可能地消除与/或防止可
石灰石石膏湿法脱硫技术原理简介
石灰石-石膏湿法脱硫技术原理简介 技术特点 1. 高速气流设计增强了物质传递能力,降低了系统的成本,标准设计烟气流速达到 4.0m/s。 2?技术成熟可靠,多用于55,000MWe的湿法脱硫安装业绩。 3 ?最优的塔体尺寸,系统采用最优尺寸,平衡了SO2去除与压降的关系,使得资金投入和 运行成本最低。 4 ?吸收塔液体再分配装置,有效避免烟气爬壁现象的产生,提高经济性,降低能耗。从而达到: a. 脱硫效率高达95%以上,有利于地区和电厂实行总量控制; b. 技术成熟,设备运行可靠性高(系统可利用率达98%以上); c. 单塔处理烟气量大,SO2脱除量大; d. 适用于任何含硫量的煤种的烟气脱硫; e对锅炉负荷变化的适应性强(30%~100%BMCR ); f. 设备布置紧凑减少了场地需求; g. 处理后的烟气含尘量大大减少; h. 吸收剂(石灰石)资源丰富,价廉易得; i. 脱硫副产物(石膏)便于综合利用,经济效益显著。 工艺流程 石灰石(石灰)——石膏湿法脱硫工艺系统主要有:烟气系统、吸收氧化系统、浆液制备系统、石膏脱水系统、排放系统组成。其基本工艺流程如下: 锅炉烟气经电除尘器除尘后,通过增压风机、GGH(可选)降温后进入吸收塔。在吸收塔内烟气向上流动且被向下流动的循环浆液以逆流方式洗涤。循环浆液则通过喷浆层内设置的 喷嘴喷射到吸收塔中,以便脱除S02、S03、HCL和HF,与此同时在强制氧化工艺”的处 理下反应的副产物被导入的空气氧化为石膏(CaSO4?2H2O),并消耗作为吸收剂的石灰石。循环浆液通过浆液循环泵向上输送到喷淋层中,通过喷嘴进行雾化,可使气体和液体得以充 分接触。每个泵通常与其各自的喷淋层相连接,即通常采用单元制。 在吸收塔中,石灰石与二氧化硫反应生成石膏,这部分石膏浆液通过石膏浆液泵排出,进入石膏脱水系统。脱水系统主要包括石膏水力旋流器(作为一级脱水设备)、浆液分配器和真空皮带脱水机。 经过净化处理的烟气流经两级除雾器除雾,在此处将清洁烟气中所携带的浆液雾滴去除。同时按特定程序不时地用工艺水对除雾器进行冲洗。进行除雾器冲洗有两个目的,一是防止除 雾器堵塞,二是冲洗水同时作为补充水,稳定吸收塔液位。 在吸收塔出口,烟气一般被冷却到46~55 C左右,且为水蒸气所饱和。通过GGH将烟气加热到80C以上,以提高烟气的抬升高度和扩散能力。 最后,洁净的烟气通过烟道进入烟囱排向大气。 脱硫过程主反应 1. SO2 + H2O T H2SO3 吸收 2. CaCO3 + H2SO3 T CaSO3 + CO2 + H2O 中和 3. CaSO3 + 1/2 O2 T CaSO氧化 4. CaSO3 + 1/2 H2O T CaSO3?1/2H2黠晶 5. CaSO4 + 2H2O T CaSO4?2H2O结晶
石灰石石膏法
石灰/石灰石-石膏法脱硫 石灰/石灰石一石膏法烟气脱硫技术最早是由英国皇家化学工业公司提出的,该方法脱硫的基本原理是用石灰或石灰石浆液吸收烟气中的SO2,先生成亚硫酸钙,然后将亚硫酸钙氧化为硫酸钙。副产品石膏可抛弃也可以回收利用。 (1)反应原理 用石灰石或石灰浆液吸收烟气中的二氧化硫分为吸收和氧化两个工序,先吸收生成亚硫酸钙,然后再氧化为硫酸钙,因而分为吸收和氧化两个过程。 1)吸收过程在吸收塔内进行,主要反应如下。 石灰浆液作吸收剂:Ca(OH)2+SO2一CaSO3.1/2H2O 石灰石浆液吸收剂:Ca(OH)2+1/2SO2一CaSO3.1/2H2O+CO2 CaSO3.1/2H2O+SO2+1/2H2O一Ca(HSO3)2 由于烟道气中含有氧,还会发生如下副反应。 2CaSO3.1/2Hz0+O2+3 H2O一2CaSO4.2H20 ②氧化过程在氧化塔内进行,主要反应如下。 2 CaSO3·1/2H20+O2+3H2O一2CaSO4·2H20 Ca(HSO3)2+1/2O2+H2O一CaSO4·H2O+SO2
传统的石灰/石灰石一石膏法的工艺流程如图所示。将配好的石灰浆液用泵送人吸收塔顶部,经过冷却塔冷却并除去90%以上的烟尘的含Sq烟气从塔底进人吸收塔,在吸收塔内部烟气与来自循环槽的浆液逆向流动,经洗涤净化后的烟气经过再加热装置通过烟囱排空。石灰浆液在吸收so:后,成为含有亚硫酸钙和亚硫酸氢钙的棍合液,将此混合液在母液槽中用硫酸调整pH值至4左右,送人氧化塔,并向塔内送人490kPa的压缩空气进行氧化,生成的石膏经稠厚器使其沉积,上层清液返回循环槽,石膏浆经离心机分离得成品石膏。 现代石灰/石灰石一石膏法工艺流程主要有原料运输系统、石灰石浆液制备系统、烟气脱硫系统、石膏制备系统和污水处理系统。 ①原料运输系统烟气脱硫所需的石灰石粉(粒度为250目,筛余量为5%),采用自卸封罐车运输,并卸人石灰石料仓。每个料仓可有多个进料口,能同时进行多台运料车卸料作业。在每个仓底设有粉碎装置,仓顶安装布袋除尘器。 ②浆液制备系统石灰石粉料从料仓下部出来,经给料机及输送机送人石灰石浆液槽。 石灰石浆液槽为混凝土结构,内衬树脂防腐,容积为l00m3”左右。浆液浓度约为30%,用调节给水量来控制浆液浓度。 ③烟气脱硫系统烟气脱硫系统主要由吸收塔、烟气再加热装置、旁路系统、有机剂 添加装置及烟囱组成。 吸收塔是脱硫装置的核心设备,现普遍采用的集冷却、再除尘、吸收和氧化为一体的新型吸收塔。常见的有喷淋空塔、
石灰石石膏湿法脱硫物料衡算(简单步骤)
石灰石石膏湿法脱硫物料衡算 首先,根据所给的烟气成分,计算烟气的分子量,烟气的湿度等。 其次,要先行计算出吸收塔的进口及出口烟气的状况。 1 假定吸收塔出口的温度T1(如果有GGH,则需要先行假定两个温度,即吸收塔进口T0及出口温度。) 2 利用假定的出口温度,查表可以知道对应改温度的饱和蒸汽压P as。 3 由H as=0.622P as/(P-Pas)可以求出改温度下的饱和水湿度 4 由已知的进口温度T0、r0、C H(C H= 1.01+1.88H0)、H0,可以求出 T as=T0-(r0*(H as-H0)/(1.01+1.88 H0))(H0:初始烟气的湿度,r0 =2490) 5 如果T as接近于T1,那么这个假定温度可以接受,若果与假定温度相距太远,则该温度不能接受,需要重新假定。 (上述为使用试差法的绝热饱和计算过程,对于技术上涉外的项目,一般外方公司会提供,上面一部分的计算软件无须人工手算的) 6 有GGH时,假定吸收塔出口温度经已确定后,判断该温升是否符合GGH 出口与入口的烟温差,假如烟温差同样适合的话,再校验GGH的释放热量问题。 再次,在确定好吸收塔出口气体的流量后,利用除雾器的最大流速限值,计算出吸收塔的直径。再根据进口烟气限速,计算出烟气进口的截面积。 7 由提供的液气比L/G可以计算出,喷淋所需的吸收液流量。由这个吸收液流量,再按照经验停留时间,可以计算出循环水箱的容积。同样根据经验需要的氧化时间及设计的氧气上升速度,可以计算出循环水箱的液位高度。那么就可以计算出整个吸收塔基循环水箱的截面积。 8 计算消耗的石灰石用量 由入口的二氧化硫浓度以及设计的二氧化硫脱除率可以知道脱除的二氧化硫。 对于烟气的三氧化硫而言,其脱除率达100%,所以多氧化硫物质的脱除量可以计算出来。
石灰石-石膏湿法脱硫系统简介
0.1 Plant description 脱硫岛介绍 The FGD plant consists of flue gas path, which includes the absorber vessel, booster fan, GGH and bypass dampers, which ensure the operation of the boiler in two modes – FGD operation and a bypass operation. Limestone slurry preparation system gets ready the absorbent needed in the process. The only by-product is gypsum slurry, which is transported to the dewatering system consisting primary and secondary dewatering stages. Gypsum, as a byproduct of dewatering is temporary storied for further use and water is partly led back to the process, partly to the waste water treatment. 脱硫岛包括烟气系统、石灰浆液制备系统、石膏浆液脱水系统、石膏库和废水处理等。在烟气系统中包括吸收塔、升压风机和旁路档板,旁路 档板的作用是它能够满足锅炉在两种模式下运行,一是在脱硫岛在线,二 是脱硫岛旁路。石灰浆液制备系统的功能是准备工艺流程中所需的吸收 剂。反应后生成的唯一的辅产品是石膏浆液,石膏浆液分别经过一级脱水 和二级脱水,经过脱水产生的辅产品是石膏被临时储存起来为以后用,脱 出的水一部分返回系统中,而另一部分被送到废水处理站。 0.1.1 Absorber system 吸收塔系统 A wet limestone process with forced oxidation with the SO2 absorber system is used to remove flue gas SO2 and to produce a gypsum by-product. SO2 removal efficiency of 96% is reached for all specified boiler loads and scope of the fuels. The absorber utilizes a perforated scrubber tray and four absorber spray levels for SO2removal, which are above the absorber tray. The absorber recirculation pumps feed separately each header when operating.