大位移井技术报告1
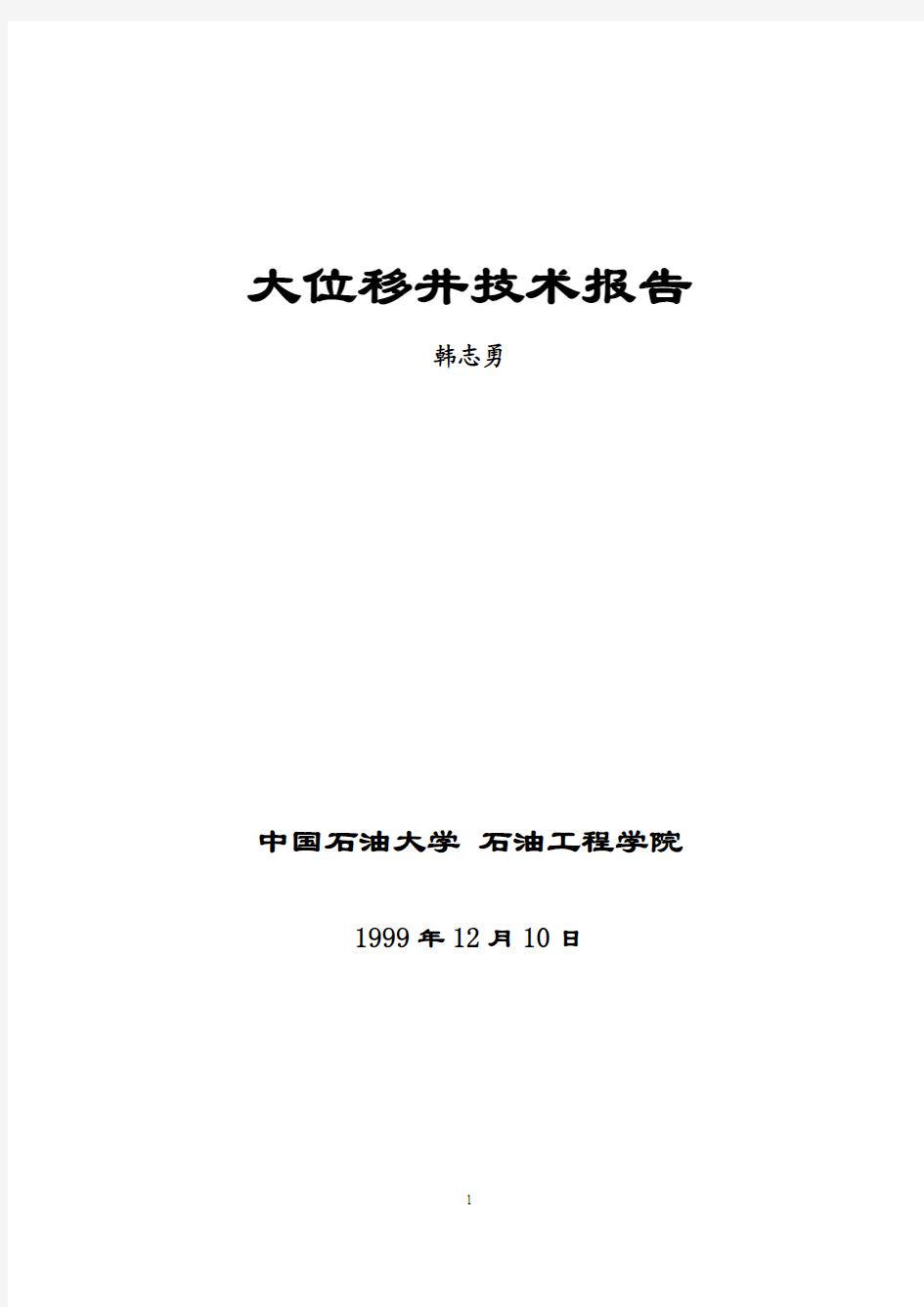

大位移井技术报告
韩志勇
中国石油大学石油工程学院
1999年12月10日
大位移井钻井技术基本问题
韩志勇
这份资料是根据1996年12月在我国大港油田举行的“大位移井技术座谈会”的资料和个人的理解整理而成。由于资料很不全,个人水平所限,所以难免有看法片面和观点错误之处。敬希各位专家批评指正。
一. 定义:
什么是大位移井?目前尚无统一的定义。初期,认为水平位移超过3000米就是大位移井,或认为KP>=1 就是大位移井。我国前几年水平位移超过1000米的井,就认为是大位移井。所以关于大位移井的定义,实际上是个发展过程。目前有两种定义法:
一种为“KC=测量井深与垂直井深之比>=2称为大位移井,KC>=3为特大位移井”。这是第14届石油大会上有人提出的。此定义目前主要用于挪威。
一种为“KP=水平位移与垂直井深之比>=2 ”。这种定义目前主要用于英国的BP公司和美国的ARCO公司。这种定义法在垂直剖面图上看起来比较直观。
现在这两种定义法各持己见。
二. 大位移井的主要用途:
大位移井的主要用途是油藏所在的地球表面(主要是水面)难以建立钻井井场的条件下,或者建立井场需要花费很大代价的条件下,从距离较远的已有的钻井井场上向该油藏钻探井或开发井。
三. 大位移井发展情况:
大约从30年代初,在美国加利福尼亚海岸上向海里钻定向井时,就可以认为这种思想就是钻大位移井的思想。但由于当时技术的限制,实际只能钻小位移的定向井。
现代大位移井大约从80年代末、90年代初开始。
1. 1989年开始,美国Pedernal油田(是距离加利福尼亚海岸6.?5 公里的海上油田)在原钻井平台上钻大位移井,少建了一个平台,省了1 亿美元。至1993年,共钻了6 口大位移井,水平位移为2500~4473米。
2. 1990年开始,美国Dos Cuadras 油田( 是距离加利福尼亚海岸9 ?公里的海上油田 )在原海上C 平台和B 平台上钻了9 口垂深非常浅相对水平位移非常大的大位移井。其中,C —29 井垂深293 米水平位移1156米,KP=
3.95;C—30 井垂深294 米,水平位移1485米,KP=5.05;都创造了当时的世界记录。
3. 1990年开始,挪威的海上油田Statfjord油田从原来的?C 钻井平台上连续钻了4口大位移井。其中C—10井水平位移5006米,创造了1990年的世界记录。1991年钻的C—3井水平位移达到6086米,1993年钻的C—2井水平位移达到7290米,创当年世界记录。
4. 1992年开始,挪威的?Oseberg海上油田用水平井和大位移井开发两个平台之间(两个平台相距15公里)的油,共钻了17口水平井。其中1995年完钻的C—26A?井水平位移达到7853米,在油层内延伸2100米。
5. 1991年开始,英国的海上油田Wytch Farm油田钻大位移井。原计划建立40?个人工岛,后改为从陆上钻14口大位移井,开发该油藏,可节约1.5亿美元,?而且采油期提前了三年。目前已经钻了9 口大位移井。其中LM-05SP 井,垂深1605米,测量井深8700米,水
平位移达到8035米,创造了大位移井的新的世界记录。
预计到2000年,大位移井的最大位移可达到10000米。
我国目前的大位移井距离世界水平相差很大。大港油田1991年完成的张17—1井,测量井深3919.82 米,垂直井深3000米,水平位移2279.83 米,这是我国大位移井的水平位移最高记录。从1991年以来至今没有新的进展。胜利油田也钻过6 口大位移井,其中桩310井水平位移达到1914.52 米。胜利油田钻的郭斜11井,测量井深2342米,垂深1400.60 米,水平位移达到1626.22 米,KP=1.161,是我国目前大位移井KP值的最高记录。还有一种看法,张17—1井造斜点在2000多米,若从造斜点算起,KP值将大于1了。
四. 大位移井的关键技术
(1).摩阻摩扭问题:
这是大位移井面临的首要问题。井斜角大,井眼特长,钻柱在井眼内起下或旋转将要遇到很大的阻力。此阻力大到一定值时,钻柱将无法运动。解决此问题需从以下几个方面着手。
1.优化井眼轨道设计:
开始也有使用双增剖面的。目前用得最多的是“悬链线剖面”或“准(视,假,类)悬链线剖面”。增斜率从1.0°~1.5°/30m逐渐增加到2.5°/30M,每400m增加0.5°/30m。此种剖面可以显著减小钻柱摩阻,并使套管的可下重量增加20~25%。
剖面的最大井斜角,一般不超过临界井斜角αK。αK的计算如下式:
αK =ATN( 1
)
式中:μ——钻柱与井壁的摩阻系数
大位移井的剖面设计必须依靠摩阻摩扭软件进行优化,而且要权衡各种工况。例如:起钻,下钻,钻进,正划眼,倒划眼等,工况不同,钻柱的受力情况就不一样,要求的悬链线形状也就不同。还要权衡不同井段的需要。同一钻柱结构,钻头所在的位置不同,则形成的悬链线形状也就不同。过去的定向井悬链线轨道都是根据起钻解卡的需要设计的。究竟应该选择哪一条悬链线作为大位移井的井身轨道,需要根据最困难的井段、最困难的工况下的悬链线来选择。
2.改善泥浆润滑性:
用得最多的是油基泥浆。也有在泥浆中加入“润滑珠”的。
3.采用扭矩减小护箍:
这是一种被称为“不旋转的钻杆护箍(Non-rotating drillpipe protector)”,该护箍由橡胶或塑料作成,装在钻杆的管体上,可以相对钻杆转动。在钻进中,钻杆旋转而该护箍不旋转。该护箍的两端有限制箍(STOP COLLAR)固定。?每隔一根钻杆装一个这种护箍,可使摩扭减小25%。
4.关于摩阻模型问题:
大位移井必须有摩阻摩扭的计算机模拟软件,否则就不指知道能不能起下钻柱。由于悬链线剖面的增斜率很小,所以摩阻模型可以使用“软绳模型”。关键在于较准确地求得摩阻系数μ。
摩阻摩扭软件中,最难确定的因素是:摩阻系数、钻头轴向力和钻头扭矩。钻头轴向力即钻压,但在大位移井中,地面的指重表难以反映出真实的钻压大小。钻头扭矩问题,最近已经有人在建立钻头扭矩的计算模型。?最好的办法是进行实测。?利用紧装在MWD 下面的接头测得井下靠近钻头处的轴向力和扭矩,再通过MWD 传输到地面上来,与地面上测得的钻压和扭矩值进行比较,计算出摩阻力和摩扭矩,从而反算出摩阻系数。
(2).钻柱设计问题:
大位移井钻进的突出问题是扭矩的传递。顶驱可以提供45000~60000 ft-lbs (62~82千牛米)的扭矩,但实际上能否用到这么大扭矩则取决于钻杆钻杆是否与此扭矩相匹配。钻柱设计的关键,是如何使钻柱能承受更大的扭矩,而不是承受更大的轴向力,因为实际的轴向力并不大。解决的方法是:增大接头的抗扭能力;减轻钻柱重量,减小摩阻扭矩,使钻头得到足够的扭矩破碎岩石。
1.接头的应力平衡:
以常用的S-135 钻杆为例,其接头抗扭强度小于管体的抗扭强度。应用应力平衡法可以提高接头的抗扭强度,但要牺牲接头丝扣的抗拉强度。其方法是在上扣时增大台肩的上扣压力,则丝扣的轴向拉力增大。这样,在工作中,接头丝扣可承受更大的扭矩,但可承受的轴向力则减小了。
2.使用高扭矩的丝扣油( High Torque Thread Compounds ):
使用这种高扭矩的丝扣油,可使上扣扭矩相对提高27%。而这并不需要增大台肩的压力和丝扣的轴向拉力。
3.使用高扭矩的丝扣连接( High Torque Connection ):
使用多级丝扣或多台肩丝扣,可以增大扭矩。现在常用的是双级双台肩丝扣。这是美国 Hydrill 公司研制出来的。这种丝扣也用在套管连接上。
4.高强度钻杆材料的选择:
现在已经生产出了ND-165高强度钻杆,在相同拉力下,比G-105钻杆重量减小25%。另外,铝合金钻杆和钛合金钻杆也是将来钻近更大位移井时可以应用的。例如,钛合金钻杆的屈服强度比S-135 高25%,而密度只有S-135 的50%。
(3).钻柱振动问题:
1.周向粘滑振动(Torsional Stick/Slip Vibrations):
钻柱的周向振动在我国现场被称为“蹩钻”。通常认为,蹩钻与钻头破碎岩石的扭矩变化有关。实际上,在大位移井中,尽管钻头会影响周向振动的存在和振幅,但周向振动主要是由整个钻柱的摩阻效应引起的。在大位移井中,当井斜很大时,绝大多数情况下是与井壁或套管壁的下侧接触,其结果导致很大的正压力并使摩阻力增大。所以,在大位移井中,??周向或粘滑振动总是存在。??这种振动导致钻头和钻柱的无序运动,大打不利于钻头寿命,机械钻速(ROP),?并使崐旋转钻井的长度受到限制。在Wytch Farm 油田这些影响都观察到了。?该油田得到的数据表明,周向振动决定了旋转钻井的极限能力。由于摩阻摩扭模型中没有考虑振动因素,所以,这些数据非常重要,不仅用于预测振动,而且用于钻进过程中减小振动。使用“旋转回馈系统”(Rotary Feedback System)可使周向振动减小到最低限度。调整通常的钻进参数,也可使周向振动减到较小程度。
2.旋转回馈系统:
该系统的原理是,先用传感器测得钻柱振动的振幅和频率,然后产生一个可以阻止振动的变化转速模型。?实现的方法是:当周向振动自井下传递到达地面时,该系统自动减小转速;当周向振动离开地面时,自动增加转速。这个速度的改变,阻尼了钻柱周向振动的能量,其结果奇迹般的减小了周向振动的振幅。为了监测周向振动,用很高的检测速率监测典型的振动频率。在Wytch Farm油田上,顶驱的电流和电压分别指示扭矩和速度。?第一代旋转回馈系统用于WF油田的前三口井,第二代用于F21井及以后的井。据说,?周向振动将使钻井能力的减小20%。关于旋转回馈系统,在研讨会上很多人询问其原理,但未能得到满意答复。
3.钻头和BHA 引起的横向振动(Lateral Vibration):
虽然旋转回馈系统成功地用于减小周向振动,但对钻头、钻柱和MWD/LWD 非常有害的横向振动还会发生。在设计时模拟此横向振动是很困难的。解决此问题的有效方法是在井下用加速度计监测钻进时的实时振动和冲击。MWD/LWD 的仪器即可测得各个方向的加速度。WF油田在81/2"井眼中曾有两个螺杆钻具(PDM) ?由于严重的横向振动而断掉。从而引起了对横向振动的重视,并将MWD 中通常用的单轴加速度计改为三轴加速度计。
(4).井眼清洁问题:
大斜度、长位移的井内,岩屑床是必然会有的。怎么清除岩屑床,保证井内清洁,是保证井眼畅通的重要问题。
1.排量问题( Flowrate ):
和其他井眼一样,首要的是提高泥浆排量。在Wytch Farm油田,在12-1/4"井眼钻达5200米时,使用3000米6-5/8"钻杆和2200米5-1/2"钻杆,一直保持1000gpm排量,对重要井段1100gpm(70l/s)。17-1/2"钻头,6-5/8"钻杆,70l/s的排量,则环空平均返速也仅有0.53米/秒。在挪威的statfjoid油田对17- 1/2"钻头,6 -5/8"钻杆,72l/s的排量,环空平均返速可达到0.54米/秒,这样的返速,在大位移井中,井眼仍然不能很好地清洁。
Wytch Farm 油田推荐的排量为:
12 -1/4"井眼,6 -5/8"钻杆, 950~1050gpm(60~66l/s)
8 -1/2" 井眼,5"钻杆, 450~500 gpm(28~32l/s)
挪威的statfjoid油田推荐的排量为:
26" 63~65l/s
17- 1/2" 50~55l/s
12- 1/4" 46~49l/s
8 -1/2" 20~30l/s
2.泥浆流变性问题( Thology ):
保持好的泥浆流变性是一切大斜度井的重要措施。动切力值应该保持在大于25,或小于12 lb/100ft2,前者保持流动是层流,后者保持流动为紊流,以便有效地携带岩屑。使用高流变性的油基泥浆,成功地钻过了12-1/4"井眼,特别注意保持泥浆的6转和3 转的读数在20左右,并保持PV/YP=60/30。
3.关于钻杆旋转问题:
从清除岩屑床,保持井眼清洁的观点出发,提高转数显然是应该的。但在大排量的情况下,高转数似乎意义不大。同时,在高转数下,钻柱的振动加剧了,弯外壳马达的疲劳加剧了,也增大了周围敏感地区的噪声水平。
4.起钻前的循环:
起钻前要进行较长时间的循环,直到井下的岩屑都返出来。否则,在起钻的过程中将会出现各种复杂问题。“短起下钻”( Wiper Trips ) 也是很有必要的。
5.摩阻软件监测井眼清洁状况:
井眼不清洁时必然出现摩阻增大。所以利用摩阻软件可以监测井眼是否清洁。当然关键在于摩阻软件计算的准确性。最重要的是要有准确的摩阻系数。利用紧装在MWD 下面的接头测得井下的轴向力和扭矩,再通过MWD 传输到地面上来,与地面上的测值进行比较,计算出摩阻力和摩扭矩,以及摩阻系数,这样可以检查短起下钻、划眼、循环和泵驱( Pumping Sweeps )等的效果。
(5).套管问题:
1.套管磨损问题:在已经下入的套管内,钻柱将长期躺在套管的下侧,在转动时对套管将造成巨大的磨损。一种方法是在钻杆上加胶皮护箍;另一种是改变钻杆接头表面上的加硬材料,既有足够的硬度,又可减小对套管的磨损。
2.套管下入问题
大位移井中下套管的困难,是很容易理解的。美国Unocal公司提出了一个新概念,即“负重量”(“负重量”的概念是指轴向受力是向上的,即轴向的重量是负值)。大位移井的套管下入优化问题牵扯到三个数值:最大下入重量;下入重量的摩阻损失;下入重量的机械损失。这三个数值决定了套管的下入限制。最大下入重量,取决于临界井深以前的井眼。临界井深是井斜角达到临界摩擦角的井深。钻井液的润滑性对临界摩擦角有重大影响。临界摩擦角取决于岩性、泥浆、以及其他因素。常见的临界摩擦角为70°~72°(摩擦系数为0.36~0.32)。在Wytch Farm ,油基泥浆的润滑性很好,在12-1/4"的裸眼内摩阻系数为0.21,临界摩擦角为78°。超过此角后,要把套管下入到大于此角的井眼内,需要上部套管的重力去推动,这就是下入重量的摩擦损失。与摩擦损失不同,机械损失是机械方式减少了套管的重量。机械损失是由岩屑,洞穴,台肩,粘卡,扶正器嵌入地层等因素造成。
解决下套管难的一个办法是采用部分浮力法(Partial Flotation)。?给下部套管内充气或充满低密度的液体(油),可以增大浮力,减小套管压在井壁上的正压力,从而减小摩擦阻力。在工艺上要有所讲究,在浮力部分的管内顶部有一个由销钉控制的塞子,当套管下到一定深度时,该塞子上面的液柱压力使销钉剪断,液体自动进入浮力部分的管内。
顶部驱动对大位移井是非常必要的。顶部驱动在下套管过程中的作用包括:循环,提放,转动,还可给套管施加压力。实现这些作用需要的基本设备有:一套顶驱系统以及与套管之间的转换器( Crossover),高扭矩套管联接(High-torque Caing Connections ),表面强化的扶正器(Rugged Solid-body Centralizers)。用顶驱旋转崐套管,可以破坏岩屑床和其他井下障碍,减小阻碍套管下入的摩阻。但是用顶部驱动旋转套管,仅是在不得已的情况下才用的,不轻易采用。用顶驱可以给套管提供94kips的下入重力,几乎是Wytch Farm 下入9-5/8"套管最大重量的两倍。现在9-5/8"套管只要每750~1000米循环一次就可以顺利下入井底。观察9-5/8"套管下入过程,发现在裸眼井段随处都可能发生机械损失。例如,在F19和F20井中,曾遇到过76和92kips的机械损失,而9-5/8",40lb/ft的套管在3300米长,82°井斜的井眼内,摩擦阻力损失仅仅24kips。
旋转尾管是大位移井提高尾管固井质量的重要措施。利用计算机软件模拟尾管固井过程中的摩阻,结果表明,尾管扭矩的变化主要是取决于浮力的变化。在注水泥过程中管内外流体的变化( 泥浆,隔离液,水泥浆) ,必然引起浮力的变化。这需要精心地模拟计算。
(6).定向井轨迹控制:
1.防碰要求:
大位移井往往要穿过很长的区域,就有可能与该区域的已钻井或设计井相碰。在设计大位移井时要特别注意防碰设计。
2.误差椭球问题:
由于井眼很长,所以积累的测量误差就很大,误差椭球很大,必然影响中靶精度。例如,Wytch Farm油田上地质部门给定的进入点(Entry Point) 是处在垂直井眼方向的200米×300米的靶区中心。考虑到测量的不确定性,对典型的水平位移4500米的井,取90%的可信度,则相当于靶区缩小为80米×170米。测量不确定性引起的垂深误差可达-11~+17米。
3.导向钻井系统:
目前设计的剖面形状主要是悬链线(或准悬链线)剖面。悬链线剖面的造斜率是不断变化的,要钻出悬链线轨道的形状,最好是使用导向钻井系统。但目前的导向钻井系统,是采用弯外壳螺杆马达,造斜时是滑动钻进,容易发生粘卡。所以大位移井希望尽可能多地使用转盘钻,以便防止粘卡。而目前的转盘钻还不能有效地控制井斜和方位。这是一个矛盾。解决的办法是开发“旋转导向钻井系统”。据说,这种新的导向钻井系统已经有几家公司在研究,预计在1997年可以进入商业使用。
(7).测斜问题
Wytch Farm 油田使用磁性MWD 和陀螺仪进行测斜。对24"和17-1/2"井眼采用地面直读单点陀螺,对17-1/2"井眼一直测到没有磁性干扰的深度。从该深度往下,在钻13-3/8"和9-5/8"套管井段,以及8-1/2" 裸眼井段,均使用MWD 进行测量。但在钻完12-1/4"和8-1/2"井眼之后,要将陀螺仪从钻杆内下入各复测一遍,并依陀螺数据为准。
多数大位移井都是从钻井平台上钻起,钻直井段时要受到已钻的邻井套管磁干扰。Wytch Farm油田的邻井磁性扫描表明,在深度接近550 米时,已经没有磁性干扰了。所以在此深度之前使用陀螺单点测斜是必要的。尽管测一个单点只需30分钟,但毕竟耽误时间。为提高上部井段的钻进效率,认为应该开发陀螺MWD。
为了减小轨迹控制的横向误差,BP公司提出了称作“ MWD井内参照法”,而不是用过去的在裸眼内下陀螺测量的办法。其方法是:当12-1/4"井眼钻达预计深度时,将陀螺仪穿过13-3/8"套管,停在裸眼井段的某个深度,通常是大约井深1050~1150米井斜65~70°处;然后上提测斜,每15米一个点;从中选100米长的一个井段作标志,?要求该井段的方位变
化小于0.5°/30米;随后下入MWD 并在此井段内作四个象限测量拍照,然后平均其方位测值,用陀螺测值进行校正,深度不附时可根据陀螺测值进行内插。此校正值将用于以后所有的MWD 测斜。每当更换MWD及其组合时,都要重新作“井内参照”。应用此管内参照技术,在钻达靶点时方位测量引起的横向误差可以减小65%。
当钻完9-5/8"套管鞋之后,用泵送法将陀螺从钻杆内送入直达BHA。为了作电缆深度检查在工具串中下入CCL(测套管接箍仪)。这样将消除由于大位移井段中电缆受力引起的深度误差。
(8).固相控制问题:
在大位移井眼内,岩屑在井眼内的时间远远大于在其他井眼内的时间,所以岩屑经过长时间的磨擦,变得更细。所以需要比普通井眼更强的固相控制系统。
(9).井眼稳定问题:
大斜度、长裸眼的井内,井壁稳定是个非常重要的问题。
解决井壁稳定问题的方法主要有三个方面:合理的井身结构,封住复杂地层;合理的泥浆性能,包括合理的泥浆密度和与地层的化学作用;沿最小水平地应力方向钻进;
(10).井身结构:
常用的井身结构为:
钻头套管
30"(导管)
22~26" 18-5/8"~20"(表套)
17-1/2" 13-3/8"(技套)
12-1/4" 9-5/8"(技套)
8-1/2" 7"(尾管)
6" 5-1/2"(尾管)
17 -1/2"和12-1/4"井眼是造斜、增斜井段。17-1/2"的井眼也是先钻12-1/4"井眼,然后再进行扩眼。
(11).钻机选择及设备:
一般情况下,应该有顶部驱动,顶驱可以提供的扭矩应在70~80千牛米以上。钻机应该有足够大的起升能力。一般应该有三台泥浆泵,可提供6000psi(41.37Mpa)?的循环泵压。钻杆的应用也有所不同,要使用6-5/8",5-1/2"还有5"钻杆进行组合成复合钻柱。
(12) .优化定向钻井作业
1.螺杆马达(PDMs):几乎是唯一地使用弯外壳螺杆马达进行钻进,可以在保持钻井效益的同时很好地控制轨迹;
2.水力学方案;
3.定子设计方案;
4.BHA性能;
5.BHA选择;
6.扭曲考虑;
7.已有的技术。
1997年4月
我国南海东部创世界纪录的
大位移井技术简介
韩志勇
我国南海东部石油公司,1997年钻成了一口创世界纪录的大位移井,XJ24-3-A14井。本人参加了该井技术总结的评审工作,了解一些情况。下面对该井的有关问题作以介绍。
一.钻该井的目的和意义
1.南海东部石油公司的位置
现已开发的油田共有四个:流花;陆丰;惠州;西江。
2.西江油田的位置及组成
三个区块:XJ24-3 ,XJ30-2 ,XJ24-1 。前两个是主力区块。
两个钻采平台,每个平台可钻16口井。生产出来的油,通过输油管线,送到“南海开拓号”油轮上。
3.XJ24-1区块的情况:位于XJ24-3区块的钻采平台东南(116°)约8公里
处。油藏圈闭面积不到2平方公里,是一个小油田,或称为XJ24-3油田的卫星油田。该海域水深100米左右。该区块是美国PHILIPS公司的风险勘探区,1986年1月8日钻完第一口探井XJ24-1X,发现了11个油层。主力油层分为两组。上组是边水,下组是底水。
地质储量465万方(400万吨)。
4.如何开采XJ24-1区块?太小了。如果在陆上,很好开采,而且很肥。但在
海上,困难大得多。如果建立一个卫星钻采平台(无人操作)要花7000万美元,加上钻井费用和按照7年开采期计算的作业费,加起来的投资将超过一亿美元。按采收率25%计算,可采出100万吨油。按120美元一吨算,可得1.2亿美元。基本上没有开采价值。所以,从1986年到1996年,10年时间,该区块没有开采。
90年代以来,大位移井技术的出现和发展,很自然提出用大位移井来开发这个油田。1995年,大位移纪录是8035米。经过论证,该井于1996年11月22日开钻,1997年5月19日完钻,6月10日完井。全井钻进时间85天,完井周期仅仅101天。
该井原计划投资2400万美元。实际打井费用1800万美元,加上论证及各项行政开支,共花钱2000万美元。
5.效益:6月23日交井投产,初产为1672桶(
6.29桶等于1方)约265方,
含水63%。以后产量逐日增加,直到7000桶(1000吨)稳住;含水逐日减少,减到2.2%稳住。到1997年底已经生产了16万多吨,价值约2000万美元。已将投入的全部成本收回。
而且,这口井在钻井中,还有大的发现,新发现5个油层,最厚的一个是
15.4米。地质储量翻了一番。
二.该井的主要钻井成果
1.三项世界纪录:
★水平位移,8062.7米;(原纪录为1995年BP公司在Wytch Farm 油
田创造的8035米)
★12-1/4”裸眼井段长度:5032米;也是任何尺寸井眼的裸眼井段长度纪录;
★MWD信号传输井深:9106米;(原纪录为7338米)
2.两个世界第二:
★ERD井完钻井深:9238米;(第一是9327米)
★9-5/8”套管下深:6752米;(第一是7132米)
3.钻达主力油层的靶心距为45米。(原设计为152米)
4.采用多项世界最先进的技术,为我国钻井技术的发展作出贡献。
三.该井采用的新技术情况
这样一口大位移井,肯定将遇到大量的难题。一开始就有一个明确的指导思想,就是尽可能采用最先进的技术。在全世界范围内选择最先进技术。
1.先进的设计技术:
首先进行了极其认真、极其细致的可行性研究。中外人员合作进行论证。
特别是细致的油藏工程工作。利用先进的模型对油藏进行模拟,进行敏感性分析。作各种完井方案比较。
●关于设计问题,一个很重要的问题是设计思想。这口井的设计充分体现
了各行业、各学科之间的协作和配合。钻井的本事应该是“指到那里,打到那里”。关键在于要指得正确。给出准确的靶点。所以要地质、物探、测井、油藏等学科的人,与钻井相配合。物探资料的处理,开始用平均速度法作图,误差较大,后来用横向速度梯度法作图,表明构造的高点向北移动了500米。于是修正了设计方位(原116.3°,改为114.9°)。实钻结果证明,修改是很准的。
●当井眼轨道初步设计出来以后,地质和物探工作人员,对井眼轨道所
经过的地层进行了尽可能深入的研究,提出可能穿过断裂破碎带。于是,将造斜点提高,重新设计,避开断裂破碎带,为顺利钻进创造了条件。
充分体现了“团队精神”。
●钻井计划作得非常详细。包括钻机改造,井身结构,完井方法,钻进措
施,固井完井,进度计划,生产预测,费用预算,经济评价,风险分析,安全环保,等等方面。基本上都是输入条件,利用计算机软件进行设计。
2.先进的钻井设备:
利用原来XJ24-3平台上的6000米钻机。这口井预计井深要达到9400米左右,显然是不够的。论证时,对钻机的动力和各部分设备都进行了校核,提出了钻机升级改造方案。
3.先进的导向钻井系统和轨迹控制技术:
井眼轨迹控制,是大位移井钻井技术的最重要的技术。先进的导向钻井系统,是轨迹控制的物质基础。
★导向钻井系统的组成:高效能的钻头+ 可调弯角的弯外壳螺杆钻具+ MWD/LWD + 遥控可变径扶正器。不起钻,连续进行轨迹控制。
●高效能的钻头:全井仅仅用了12只钻头,包括一只钻13-3/8”套管的
水泥塞的钻头,一只是用于冲洗7”尾管内部的6”钻头。实际钻进的钻头只有10只。我国“川石-CHRISTENSON”公司提供的特制PDC钻头从设计到送到平台上,仅用了不到一个星期。
●可调弯角的弯外壳螺杆钻具:这次使用的是美国Baker Hughes公司的
导向马达,在井下工作时间可达300小时以上。可提供PDC钻头破岩需要的高扭矩。弯角可调。
●MWD/LWD:随钻测量和随钻测井。这次使用的是Anadrill
Schlunmberger 公司的最新产品,M10型的MWD。连续波传送,比正脉冲,负脉冲要快得多。LWD包括浅电阻率和深电阻率,自然γ,地层密度测井,等。LWD完全代替了电缆测井,但未达到地质导向的水平。
●遥控可变径扶正器:商品名称,TRACS,哈里伯顿公司的最新产品。
这种可变径扶正器在前几年也有,但调了直径之后,地面上看不见,不知道调的结果。TRACS的优点是与MWD相联系,调之后的直径可通过MWD的传输系统传上来。
★有了这样的导向钻井系统,就可进行轨迹控制。MWD的信号一直到9100多米仍可传输。所以这口井的轨迹控制是很好的。两个靶心距分别为60米和45米。而设计给出的靶区半径是152米。
4.先进的测量仪器
★这口井的井眼测量问题,一直用MWD测量。用高精度的陀螺系统对MWD的精度进行校核。
★使用高精度速率陀螺仪,对MWD校核的结果表明,MWD的精度是足够的。
5.先进的泥浆和固控技术
采用一种低毒油基泥浆,称为VersaClean。基本上没有失水。非常有利于泥页岩的井壁稳定;而且润滑性很好,非常有利于减小摩阻系数。
6. 套管磨损问题的解决
大位移井套管磨损一个极其严重的问题。特别是在弯曲井段,弯曲钻柱以很大的正压力作用于套管壁,在旋转时引起套管磨损。这口井采用了一种“非旋转钻杆保护器”(NRDPP – Non-Rotating Drill Pipe Protector)。在套管保护段,每根钻杆单根加一个。
7. 套管下入问题的解决
钻柱如果下不去,还可以用顶部驱动旋转起来下入。套管由于丝扣问题,不能承受大的扭矩。所以下套管是大位移井最大的难题。这口井采取了两个主要技术。
★带轴向滚柱的套管扶正器。将套管与井壁之间的轴向滑动摩擦,变成了轴向滚动摩擦。
★使用漂浮技术。一个漂浮接箍可使一段套管中空。从而减小对井壁的正压力。
四.出现的问题
1.7”尾管没有下到预定井深。
2.18-5/8 表层套管被挤扁。
3.在12-1/4”井眼内卡了一次钻
总而言之,这口井打得是成功的。取得的成果是巨大的。一口井开发一个小油田,而且还发现了新的油层,使油田扩大,储量增加了一倍。
1998年5月17日
大位移井技术的新进展
韩志勇
一.新的世界记录,新的发展速度,新的更大挑战
1.新的世界记录:35186英尺(10725米)水平位移。
2.新的发展速度:1995-1997年水平位移由8035米增大到8062米;
1997-1999年水平位移有8062米增大到10725米。
3.新的更大挑战:澳大利亚正在计划大15000米的水平位移井;
英国正在计划大于16000米的水平位移井。
二 .大位移井的轨迹控制技术
1999年11月大位移井技术国际研讨会的重点内容。这些新技术的出现,标志着钻井技术的具有划时代意义的重大进展。
1.斯仑贝谢的PawerDrive(旋转导向钻井系统)
2.贝克休斯的AUTO-TRACK (井下闭环自动跟踪控制系统)
3.埃尼—阿吉普和贝克休斯共同研究的SDD系统(垂直钻井装置)
三.大位移井的测量技术
英国Wytch Farm油田的大位移井,为了解决MWD、LWD以及其他井下信息的长距离传输中信号受干扰而减弱的问题,斯仑贝谢公司开发了泥浆泵压力反馈系统,可以较好地消除泵压波动,保证信号传输。
四.大位移井的井眼清洁问题
麦克巴泥浆公司开发了一套实时检测井眼清洁状况的软件系统。在井下MWD上装有一个环空压力测量仪器,测得的环空压力可实时传输到地面。经过软件处理,计算出环空当量循环密度ECD,环空静液密度ESD比较,实时给出井眼清洁情况的报告。
1999年12月1日
我国的大位移井技术状况
韩志勇
一.我国的大位移井纪录
1.我国位移超过2000米的大位移井5口。其中大港油田钻4口,胜利油田1口。
2.我国位移超过1500米的大位移井11口。其中大港油田5口,胜利油田6口。
3.我国最大水平位移井是大港油田钻的F1井,达到2624.7米。
4.我国平垂比最大的位移超过1500米的井是红9-1井,达到1.45。
5.新疆克拉玛依油田的浅层大位移井,也有一定的水平。水平位移最大达到546米,平垂比达到2.76。
在大位移技术研究方面,在水平井技术的基础上,主要是进行了一些关于轨道设计和摩阻摩扭的研究。
二.大位移井轨道设计技术
1. 石油大学(华东)的研究成果。
① 提出了9种曲线,可作为增斜段的轨道形状。针对每一口井的具体设计参数,钻柱
条件,钻进参数,用摩阻软件进行优选,最后选出最佳轨道。
② 提出了轨道优选的三原则:长半径范围内的低造斜率;全井井深最小;最困难工况
的摩阻摩扭最小;
③.结论:没有那一种曲线在任何情况下都是最优。
2. 轨道设计的“可视化”。
三.摩阻摩扭问题的研究
西南石油学院的研究成果
① .摩阻系数的研究方面,有新做法:设计了一个新的泥饼摩擦系数的仪器。
认为摩阻系数与摩擦面积、摩擦速度、正压力大小、接触时间有关。
② .提出p a F F F +=。前者为剪切阻力,可用试验求得;但后者为犁沟阻力, 仍没有好的模型表达。
四.我国大位移井与世界的差距
我国的大位移井技术距离世界水平,有太大的距离。且有距离越来越大的趋势。 我们的主要差距在于:
①首先是钻井设备的差距,缺少顶部驱动;
②井下测量仪器差距;
③轨迹控制工具的差距;
④泥浆,水力学,井眼稳定等工艺技术的差距;
⑤设计思想及软件技术的差距;
1999年12月9日
渤海地区垦利油田大位移井固井实践
渤海地区垦利油田大位移井固井实践 发表时间:2019-01-02T17:28:21.263Z 来源:《基层建设》2018年第32期作者:隋赛 [导读] 摘要:2018年初渤海地区垦利油田刚完成的一口大位移井固井作业,该井完钻井深4566m,最大井斜60.12°,井斜大、稳斜段长,钻遇三处断层及多个煤层段,钻井期间还发生断层漏失情况。 中海油田服务股份有限公司油田化学事业部天津 300459 摘要:2018年初渤海地区垦利油田刚完成的一口大位移井固井作业,该井完钻井深4566m,最大井斜60.12°,井斜大、稳斜段长,钻遇三处断层及多个煤层段,钻井期间还发生断层漏失情况。本文分析了该井固井技术难点及相应固井现场实践,包括水泥浆体系、前置液优化,套管扶正器加放,防漏压稳、可划眼高抗扭尾管附件选取,机械式可旋转尾管悬挂器送钻等技术分析及总结成功经验,可供此类具有复杂井况大位移井固井作业作为参考。 关键词:大位移井;技术难点;现场实践 引言: 垦利区块油田位于渤海南部海域莱州湾内,为复杂断块油田,沙河街组地面原油为轻~中质常规原油。此次完钻的这口井,目的是揭开主力含油层位沙三段设计完钻井深超过4500m,最大井斜60.12°,井斜大、稳斜段长,井底温度达到90℃以上。 其中,12-1/4”井眼从1498m开始钻进,中完井深3699m,段长超过2000m,井底井斜58.33°,最大井斜60.12°。钻遇2处断层:断层1位于2226m,断距约20m;断层2位于2745m,断距约25m。其中断层2处钻进期间发生漏失后成功堵漏。9-1/2”井眼完钻井深4566m,3700m钻遇断层3,本井段含煤层较多,分别位于3889m~3890m、3891m~3892m、3918m~3919m、3965m~3966m、4192m~4193m、4221m~4222m、4232m~4233m、4249m~4250m、4262m~4263、4271m~4272m。 一、固井难点 1本井为大位移井,稳斜段比较长,循环过程中难以保证井眼清洁,易形成岩屑床,存在发生环空桥堵风险; 2本井斜度大,稳斜段比较长,存在下套管遇阻风险,尤其是7”尾管下放过程,避免出现提前做挂风险; 3本井存在3处断层以及大量煤层,12-1/4”井段还发生了漏失,因此要控制固井作业期间环空返速及井底当量,避免固井作业期间发生漏失。 4套管居中难。通常情况下为了减少摩阻,便于套管下入,一般会控制套管扶正器数量以降低风险,使套管居中度无法保证。 5水泥浆性能要求高,如密度、流变性能、自由水、失水等;水泥浆的稠化时间、井底循环温度需精准确认。 二、相应措施 1技术套管首重安全 本井12-1/4”井段段长超过2000m,中完钻井液密度均为1.40sg,因此在确保油气层段均达到有效封固的同时,降低井底当量密度,避免压漏地层。 ①前置液设计: 优选前置液体系,使用“双作用隔离液”代替传统“隔离液+冲洗液”模式,降低冲洗液对井壁的冲刷。由于该井段发生漏失,采用“堵漏+双作用隔离液”体系,确保作业期间施工安全。同时,调整隔离液密度及粘度,密度1.4sg与泥浆保持一致,粘度大于泥浆粘度20s。 ②循环过程优化: 因本井段钻井期间发生漏失,根据完钻后通井期间井底最大循环排量,反推标准井眼(12-1/2”)与钻杆(5-1/2〞)环空返速是0.95m/s,循环期间先小排量打通,之后逐级提高排量循环,每次提排量幅度不超过0.4 m3/min,最大排量为1.60m3/min(标准环空返速 0.92m/s)。循环结束时控制气全量在5%以下; ③优选水泥浆体系,优化配方性能: 在设计初期采用“膨润土+防窜聚合物”水泥浆体系三段浆柱结构。然而,经化验室对其所备添加剂样品进行化验时,发现前置浆与后置领浆相容性存在问题。 根据化验结果,以及现场实际情况,决定采用防窜胶乳聚合物水泥浆体系采用两段式浆柱结构,即:尾浆1.90sg、封固井底以上500m,领浆1.70sg,封固至上层管鞋以上100m。同时,根据现场投电石结果,计算井眼扩大率,合理优化水泥浆附加量,避免水泥浆泵入过量,导致井底压力过大,压漏地层。附表为化验室两种水泥浆相容性实验结果,图为垦利区块地层坍塌破裂压力系数
大位移延伸井钻井技术
石油钻井行业大位移延伸井钻井技术 近几年来,随着钻井工艺技术及钻井装备、工具、软件等技术的发展,诞生了大位移定向井,它的出现,为海洋平台钻井及在陆上开发滩海油气资源开辟了一条新途径,与其他井型相比,这项技术在油气勘探开发中起到了投资少、见效快和其它钻井方法无法替代的作用。 第一节国内外大位移井发展及技术现状 所谓大位移井世界上并无确切的定义,最初认为水平位移超过3000米或水平位移与垂深之比大于1的井即为大位移井,随着钻井及相关技术的发展,目前比较通用的概念是位移于垂深之比大于或等于2的井称为大位移井。井斜大于或等于86度的大位移井称为大位移水平井。由于各种原因使得方位发生变化的大位移井,称为三维大位移井。 大位移井始于20年代,随着科学技术和水平井钻井技术的不断发展,80年代大位移井才得到快速发展,九十年代以来,大位移井已经在油气勘探和开发中显示出其巨大的潜力。美国、挪威、澳大利亚、英国等几个国家先后钻成了一批有代表性的大位移井,位移与垂深之比大多都大于2,有的大于5,并取得了很好的经济效益。 Unocal公司在美国加利福尼压近海Dos Cuadras油田C平台上成功地钻了9口非常浅的水平位移很长的油井。其中C-29井和C-30井创造了当时的最高纪录。C-29井高峰日产量113吨/天,储层内长度942米,总垂深层93米,水平位移1156米,位移、垂深比3.95C-30井储层内长度1348米,垂深与位移之比达到了5.05。 英国BP石油公司和斯伦贝谢公司在北海Wytch Farm油田成功地钻了数口大位移水平井,开创了利用大位移井技术开发整装油田的范例。其中1992年完成的F19井水平位移5001米,总井深5757米,水平位移、垂深比创当时欧洲纪录。 BP石油公司于1998年1月在英国南部的Wytch Farm油田完成的M11井是目前世界上水平位移最大的大位移井,其水平位移达10100米,日产量高达20,000b/d 1997年6月,中国海洋石油总公司与美国菲理普石油公司合作在南海东部完成了一口当时世界上水平位移最长的水平井西江24-3-A14井,完钻井深9238米,垂深2985米水平位移8062.7米。大港油田利用国内技术于1991年独立完成了国内第一口大位移定向井张17-1井,测量井深3919.82米,垂深3000米,水平位移2279.83米。1996年完成的QK18-1井,该井井深4408米,位移2666米,是目前国内独立完成的水平位移最大的井。 胜利油田共钻过六口大位移井,其中1997年完成的郭斜11井,测量井深2342米,垂深1400.6米,水平位移达到1626.22米,水平位移与垂深之比达到1.161,创我国目前水平位移垂深比最高纪录。 第二节大位移井的井身轨迹设计 大位移井井身轨迹剖面主要采用悬链线或准悬链线剖面。悬链线剖面是由Edward
丛式井技术要点及措施分析
第四部分丛式井技术要点及措施 4.1 总体原则 4.1.1 采用交叉钻表层,减少水泥窜槽;最浅造斜点的外排井出套管鞋,待MWD无磁干扰就提前造斜,有利于防碰及防磁干扰。 4.1.2造斜点的选择: 根据甲方提供的原始数据计算出位移和方位,按照定向井原则,井网布置避免交叉,位移大的安排在边缘槽口,造斜点的选择原则是在地层均一、可钻性好的地层,但密集型丛式井为降低稳斜段的井斜角,造斜点尽量浅,相邻井的造斜点相互错开50米,平台从外到里造斜点依次加深,边缘造斜点最浅的井为220米至平台中心最深的KOP为420米,避免来自横向的磁干扰及井眼碰撞。 4.1.3 QHD32-6地区已完成了十几口的探井,油层位置已经清楚,对于如此小的井距密集型平台,钻井顺序必须按照定向井施工原则,即采用先浅后深(造斜点)、先外(边缘大位移、大斜度)后里,否则会后患无穷。如果采用定向井钻井原则,还避免不了,就要用陀螺定向. 要避免磁干扰、碰撞,除按以上原则外,必须保证一次造斜的成功,否则就会打乱整个钻井顺序,给下步作业带来困难。 4.2 大平台小井距最难解决的问题是井眼防碰 随着快速定向钻井大规模的展开,其浅层造斜技术、井眼控制技术和解决大斜度井滑动摩阻技术都有成熟的经验。但由于单平台井
口密度的逐渐增加,井眼相碰矛盾日趋尖锐,表层碰撞的可能性越来越大,锦州地区和绥中地区都有过惨痛教训的例子,小井眼的防碰必须按照定向井防碰预案实施,并且从上到下必须重视,相互让路,加强合作,避免该类事故的产生。以下是影响井眼发生碰撞的主要因素:: 4.2.1. 单平台井数的增加、井距的减小:97年前渤海单平台井数为4~16口,井距2~3米。由于井眼密度小,其防碰问题不突出。随着上千万吨的开始,为降低建平台的投入、增加平台的利用率,于97年底开始大平台小井距的作业,QHD32-6油田的井距缩小到1.5x1.7米,其井眼交叉的可能性越来越大,井眼防碰问题迫在眉睫。 4.2.2. 直井段偏斜:现有的钻井技术不可能将所有的直井段吊直为零,其原因是地层的不均一、邻井水泥环的影响等因素,使井眼产生偏斜。 4.2.3.钻井顺序不符合井眼防碰原则:定向钻井原则是“先外后里,先浅后深”---即先钻造斜点浅的定向井、依次钻造斜点深的井、最后钻直井;也就是说先钻位移大的边缘井、依次向平台中心钻。如果违背上原则,易产生碰撞。 4.2.4.直井段没有数据的丛式钻井:数据反映井眼的走向,没有数据就谈不上井眼防碰,有碰撞潜在的危险。 4.2.5小井距仪器的精度误差:我们知道所有的测量工具都有系统误差,随着井深的增加,其误差椭圆越来越大。 4.2.6.邻井套管对MWD磁干扰,产生测量偏差。
浅谈对大位移钻井技术的认识
浅谈对大位移井钻井技术的认识 张瑞平 摘要:近几年随着定向井、水平井钻井技术的日趋成熟,大位移钻井技术在国内已有了很大的发展和应用。利用大位移井技术勘探开发近海油田,断块油气田、边际油田、稠油油藏及沙漠等复杂地面条件油田是一种经济而有效的先进技术。本文简单分析了大位移井钻井技术的关键问题。 关键词:大位移井、水平井、旋转导向钻井 1、大位移井概况 20世纪90年代出现的大位移井(Extended Reach Drilling)是在水平井钻井技术和深井钻井技术基础上发展起来的一种新型钻井方式,它集中了水平井和深井的所有技术难点。代表了当今世界最先进的钻井技术。 图1 大位移井示图 目前,国际上较为普遍采用的大位移井基本定义为,水平位移与井的垂深之比等于或大于2的定向井。航行角大于60°的井,称为大位移井(注:航行角是指钻大位移井稳斜段的井斜角)。国内定义为:垂直井深2000m以上,水平位移与垂直井深之比为2以上的井称为大位移井。 2、大位移井的优势 大位移井技术迅速发展的原因是它具有重要的经济价值。目前世界上许多国家利用这项技术来勘探开发海上、槟海、岛屿和地面条件恶劣地区的油气田,减
少建造平台人工岛和减少钻油气井数。老油气田可利用原有的基础设施钻大位移井,加速油田探边和开发,缩短产油周期,扩大泄油半径,提高单井产量和延长井的寿命;增加整个油田的产量和最终采收率,大大节约投资。因此,虽然这项技术还正在发展和完善之中,但已在世界各地取得了重大成效。 由此可见,大位移井有以下优势:(1)用大位移井开发海上油气田,可大量节省费用。(2)靠近海岸的近海油田,可钻大位移井进行勘探、开发。(3)不同类型油气田钻大位移井可提高经济效益:小断块的油气田,或几个不相连的小断块油气田,可钻1口或2口大位移井开发;若几个油气田或油气层不在同一深度,方位也不一样,可钻多目标三维大位移井开发,节省投资,也便于管理。(4)使用大位移井可以代替复杂的海底井口开发油田,既可节省海底设备,又可节省大量投资。(5)利用大位移井可以在环保要求高的地区钻井,以满足环保要求。 图2 用大位移井实现海油陆采(探) 目前,大港油田、胜利油田均已钻过超过3000m水平位移的大位移井,具有一定的钻大位移井经验。对加快对边际油田的开发,以及提高油田的整体经济
复杂井固井新技术与发展
复杂井固井新技术与发展 一、中国石油集团工程技术研究院固井专业概况 中国石油集团工程技术研究院从1980年开始致力于固井技术研究,是国内最早从事固井材料研究的单位。 在集团公司的支持下,经过20多年的研究和积累,中国石油集团工程技术研究院固井专业已成为国内以固井外加剂为主导,集科研、开发、生产、技术服务于一体的技术力量雄厚的研发机构。现拥有高、中级科研人员35人,实验室面积2000m2,符合API规范的实验检测仪器设备160台套,并建成了年产万吨的外加剂生产线。拥有国家技术监督局认证和API 认定的集团公司油井水泥及外加剂产品质量监督检测中心。 工程技术研究院已先后完成国家和集团公司级固井科研项目77项,其研究成果先后获国家科技进步三等奖2项,集团公司科技进步一等奖3项,二等奖4项,三等奖3项。获国家级重点新产品5项,联合国技术信息系统发明创新科技之星奖1项并入选世界优秀专利。在世界石油大会及SPE和美国Oil&Gas上宣读和发表论文5篇,先后有2名科技人员成为美国石油协会勘探开发标准化委员会油井水泥分会投票委员。 在固井技术方面已形成十大系列、五十多个品种完备的油井水泥外加剂产品,为长庆油田、辽河油田、大港油田、吐哈油田及海洋石油、石化系统等二十多个油田固各种复杂疑难井3560井次。为集团公司海外(伊朗、厄瓜多尔、乌兹别克、苏丹、哈萨克斯坦等)勘探开发项目提供了8个品种、813吨固井外加剂和技术服务。 目前,国内固井水泥浆外加剂的年使用量约为1.8亿元,工程技术研究院约占12—15%,而在高端产品的市场份额超过70%,尤其在复杂疑难井固井方面形成了较强的技术优势和综合服务优势,在欠平衡井固井技术、低压易漏井固井技术、深井超深井固井技术、长封固段井固井技术、高压气井固井技术、岩盐层固井技术等方面形成了七大特色固井技术。 二、工程院特色固井技术 1、欠平衡钻井配套的高强低密度水泥浆固井技术 二十一世纪油气资源勘探开发,面临着复杂储层物性和复杂地质条件油气资源的开发;面临着低压、低渗、低产能油气资源的开发;面临着走出去战略的实施和激烈的世界石油市场的竞争。欠平衡钻井的兴起,为低压、易漏复杂地层的开发,有效提高钻速,提供了有力的技术保证。 同时,欠平衡钻井也对固井提出了更高的要求。欠平衡钻井配套固井技术的实质就是要解决欠平衡钻井后的近平衡固井问题,这就意味着要特别关注选择合理的固井压差,适宜的固井水泥浆密度以及合理的施工工艺,以防止固井漏失和对储层的污染,保证固井质量,为后续的油层改造、增产措施及采油作业提供良好的井筒条件。国内外固井实践证明,选用合适的低密度水泥浆,既可以有效地分隔低压油、气、水层,同时也是封堵低压漏失层较为成功的方法。 对水泥浆体系来说,低密度、高强度、低失水、好的流变性是其关键,但一般低密度水泥浆水灰比、外掺料较大,一般作为充填水泥用于非目的层封固,水泥浆密度的降低和水泥浆性能之间存在矛盾,突出表现在: ①水泥浆体系稳定性差,体系分层离析; ②水泥浆失水量难以控制; ③水泥浆流变性差,泵送困难; ④水泥石强度发展慢,强度低; ⑤水泥浆石渗透性高,易引起腐蚀性介质的腐蚀。 随着对微观力学和微观材料的认识逐渐深化,工程技术研究院利用紧密堆积理论对低密度固井水泥浆优化设计,在国内率先研制开发成功了以PZW系列增强材料为主体的新一代低密
大位移井
大位移井: 大位移井的定义是测量深度与垂深之比(也有用水平位移与垂深之比)大于或者等于2,大位移井综合体现了当今最先进的钻井技术,它对于利用现有平台开发老油田的剩余油、开发滩海和极浅海油田实现海油陆等采具有巨大的经济价值。该项技术自20世纪90年代开始得到发展,目前国外已经钻成数百口大位移井。最大水平位移已经超过10000m。 大位移井分为浅层大位移井和深层大位移井,浅层大位移井是指垂深只有100~500m,水平位移与垂深之比较大的井,使用斜井钻机和修井机即可施工。美国和加拿大这种井较多。其中美国的B21井垂深只有206m,井深1353m,钻穿油层段1084m,水平位移970m,水平位移与垂深只比是5.66。 深层大位移井早期是指水平位移超过3000m,水平位移与垂深之比大于1;后来定义为水平位移超过3000m,水平位移与垂深之比大于2的井。1982~1990年水平位移由4473m增大到7290m,1990~1999年水平位移增大到10728m。它是由英国BPAmoco公司在英国Wytch Farm油田钻成的M-16Z井,水平位移10728m,井深11278m,钻井及固井时间共123天。1998年创记录的M11井打了两个井眼:M-11Z,井深9688m,然后侧钻打了M-11Y,井深10658m,水平位移10114m,其中水平段的长度达4900m。 一、大位移井的概念(Extended Reach Well ) (1)国际上普遍采用的定义:井的水平位移与垂深之比等于2 或大于2的井称为大位移井。 (2)另外的定义:水平位移等于3000米或大于3000米的井。 二、大位移井的特点及用途 1、大位移井的主要特点 ?一是水平位移大,能较大范围地控制含油面积,开发相同面积的油田可以大量减少陆地及海上钻井的平台数量; 二是钻穿油层的井段长,可以使油藏的泄油面积增大,可以大幅度提高单井产量。 2、大位移井的用途 (1)用大位移井开发海上油气田从钻井平台上钻大位移井,可减少布 井数量,减少井投资。 (B)用大位移井开发近海油气田 以前开发近海油气田要求建人工岛或固定式钻井平台,现在凡距海岸10公里左右油气田均可从陆地钻大位移井进行开发。 (C)开发不同类型的油气田 几个互不连通的小断块油气田; 几个油气田不在同一深度,方位也不一样,可采用多目标三维大位移井开发。 (D)保护环境 可在环境保护要求低的地区用大位移井开发环境保护要求高的地区的油气田。
大位移井钻井技术
大位移井钻井技术 所谓大位移井钻井技术,是一种高精尖的钻井工艺,是当今定向井、水平井技术的综合系统工程,可广泛地应用于滩海油田、海上油田和地面条件极其复杂的油气藏的勘探开发。尤其位于我国南海西江和渤海湾的近海地区的浅海区域有许多油田,可以利用大位移井钻井技术进行海油陆采,可节约大量的修建海堤或人工造岛等投资费用。 我国引进应用和研究大位移井钻井技术,是从1997年开始的。应用大位移井,不仅使西江24-1边际油田得以成功开发,而且极大地推动了国外先进的大位移井技术在国内的研究与应用。近年来,专家针对大位移井的六大技术难点,对大位移井钻井的优化设计理论、国产化配套技术、计算机应用软件技术等进行研究摸索,形成了正确的理论研究方法。在先导性实验井埕北21-平1井的施工中,首次在我国使用变曲率悬链线井身轨迹剖面设计方法,首次引进具有世界先进水平的调式AGS稳定器和FEWD无线随钻测量仪等组成带地质导向的先进钻井技术,并配合使用新型黑色正电胶硅聚钻井液,有效地解决了摩阻、扭矩等技术难题,这口井创出目前国内陆上大位移延伸井水平位移最长全国新纪录,并在大位移井优化设计、井眼轨迹控制、井下工具应用和研制以及钻井液、完井液等方面,取得了7项突破性的研究成果,形成了钻3000m以上大位移井的配套技术,开展了水平位移4000m以上大位移井的钻井工程设计及井眼轨迹控制技术模拟实验,具备了5000m以内大位移的施工能力。 与此同时,在塔里木酸盐岩地层中,打出一口超深水平井———解放128井,填补了国内钻井施工运用6in钻头水平段和采用世界先进的换压钻进技术边喷、边钻两项钻井技术空白,创出了水平井施工垂深最深的亚洲记录;并在渤海湾附近的桩西古潜山地层中,钻出一口水平位移超2000m的高难度海油陆探大位移延伸定向井---桩斜314井,均见到良好油气显示。
大位移井钻井液关键技术问题
大位移井钻井液关键技术问题 摘要:文章以大位移井钻井液关键技术问题为研究对象,分别对其关键技术问 题如钻具磨阻与扭矩控制技术问题、井壁稳定技术问题、井眼净化技术问题进行 了研究分析,并提出了一些相应改进措施以供参考。 关键词:大位移井;钻井液;关键技术 1 降阻与降扭矩技术 1.1 科学选定钻井液体系 在大位移井作业中较为常用的钻井液主要有三种,分别为合成基钻井液、油 基钻井液与水基钻井液,在具体的钻井作业中,需要紧紧围绕设计情况选定最为 适宜的钻井液类型。为有效降低摩阻与扭矩,大位移井通常要运用具有良好润滑 能力的钻井液,如油基钻井液与合成基钻井液。近几年通过调查发现,世界范围 内约有七成左右的大位移井都采用油基/合成基钻井液。然而,传统意义上的钻井液主要将原油作为基础油,无法满足环保需求,而且造价很高。目前,很多专业 公司都开发出低毒性油基钻井液,改用基础油为白油,同时形成稳定的钻井液体系,如Vert-oil体系等。 1.2 钻井液性能调整 对于大位移井的钻井液而言,其流动摩擦主要和黏度、流速、管壁平滑度等 因素有关。在加入适宜的润滑材料以后,可借助钻井液管道管壁进行吸附,因此 提升管壁平滑度,达到降低摩阻的作用,同时也可采取性能调整策略类减少摩阻。对钻井液的黏土实际含量进行有效控制,同时运用固控装置,减少劣质固相的含量,缩减泥饼厚度,减小钻具和泥饼之间的接触面积;合理应用调节剂,对钻井 液粘滞性与流变性进行调整,进而达到提升润滑能力的目的。 1.3 润滑防卡技术 大斜度大位移井由于井斜大、水平位移长,在钻井及其它作业中,钻具、测 井仪器等与井壁的接触面积大,使得摩阻和扭矩增大,因此钻井液必须具有良好 的润滑性能,防止托压现象和粘附卡钻事故的发生,确保钻井和完井作业的顺利 进行。 2 大位移井钻井液关键技术问题 2.1 钻具磨阻与扭矩控制技术问题 对于大位移井来说,由于其具有井斜大,裸眼段长等特点,因此在具体进行 钻井过程中,会出现钻井管柱在井眼中出现偏心问题,在较长的裸眼井段中,钻 具与井壁解接触面积会更大,从而导致正常作业的钻井管柱会承受更大的摩擦阻 力与扭矩,进而对大位移井延伸造成了严重的限制问题,同时对井壁稳定性也造 成了不利影响。基于此,通过进一步改良钻井液体系,提升钻井液的润滑性,可 以有效减少钻具磨阻与扭矩,提高大位移井的延伸性能。因此需要选择合适的钻 井液体系。当前大位移钻井在作业过程中常用到三种钻井液体系,第一种是油基 钻井液体系,其以油作为连续相的油包水乳化钻井液,具有抗污染能力强,更加 有利于井壁的稳定、对油气层损害程度更小等优点,但这一类钻井液体系使用成 本较高,并且不利于环境保护;第二种是合成基钻井液体系,其在保留油基钻井 液优点的基础之上开发而来,其中应用最为广泛的为第二代合成基钻井液,其由 线性α烯烃、线性烷基苯、内烯烃、线性石蜡构成,相对于油基钻井液体系更为 环保。最后一种是水基钻井液体系,目前常见的水基钻井液体系有PEC钻井液、PEM钻井液、小阳离子钻井液等,其中PEM钻井液在我国海域应用较为广泛,