旋风分离器文献综述
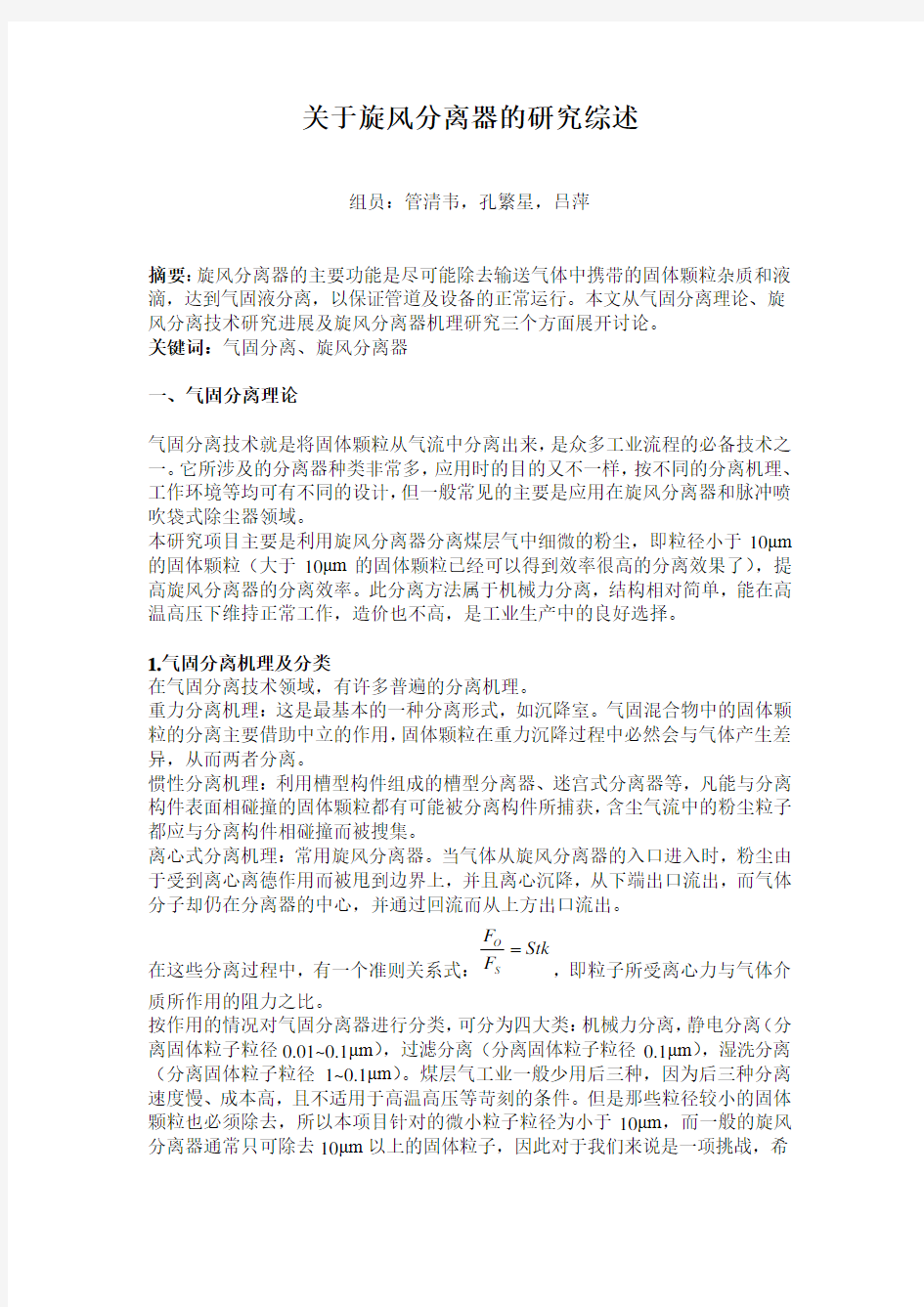
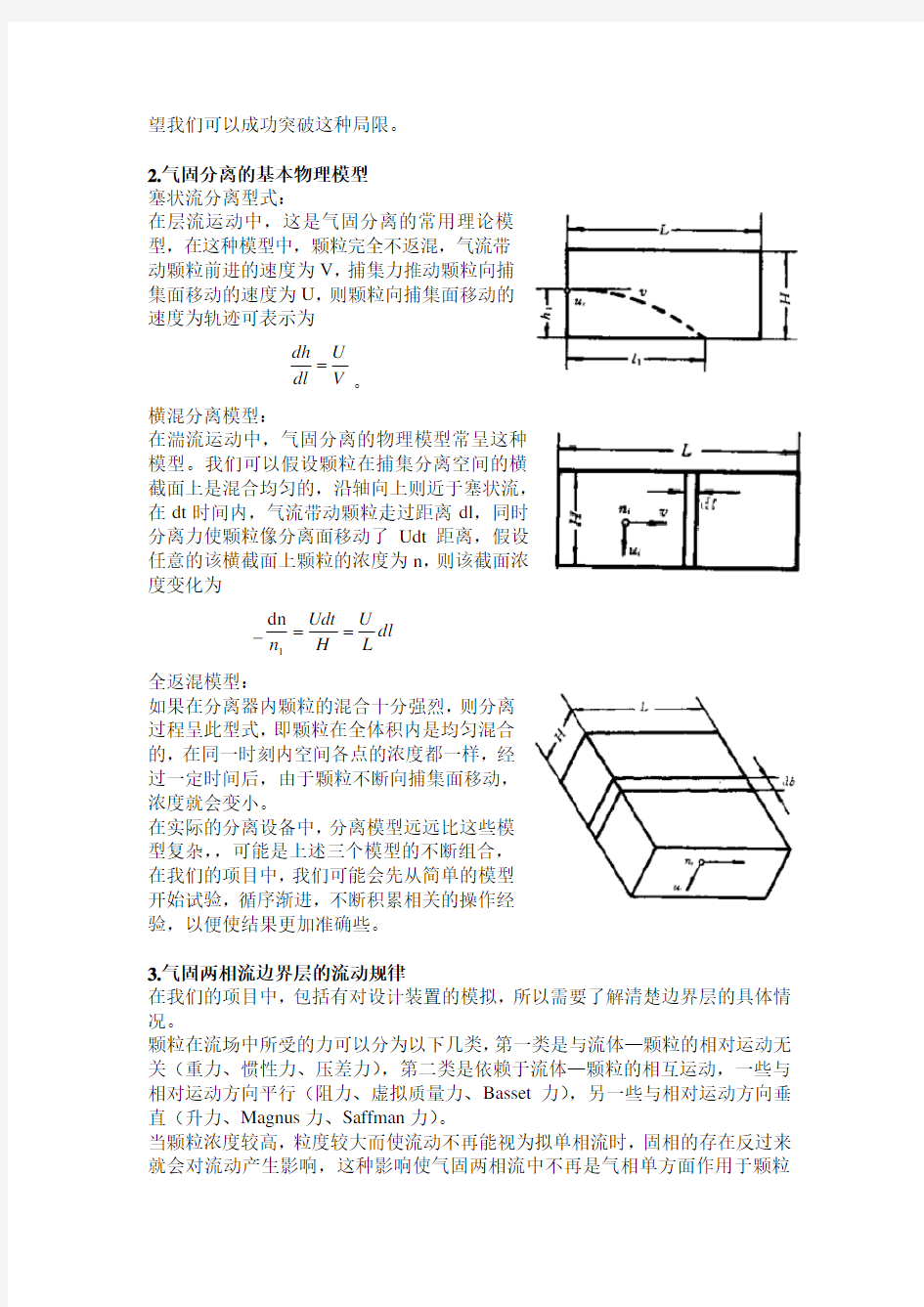
关于旋风分离器的研究综述
组员:管清韦,孔繁星,吕萍
摘要:旋风分离器的主要功能是尽可能除去输送气体中携带的固体颗粒杂质和液滴,达到气固液分离,以保证管道及设备的正常运行。本文从气固分离理论、旋风分离技术研究进展及旋风分离器机理研究三个方面展开讨论。
关键词:气固分离、旋风分离器
一、气固分离理论
气固分离技术就是将固体颗粒从气流中分离出来,是众多工业流程的必备技术之一。它所涉及的分离器种类非常多,应用时的目的又不一样,按不同的分离机理、工作环境等均可有不同的设计,但一般常见的主要是应用在旋风分离器和脉冲喷吹袋式除尘器领域。
本研究项目主要是利用旋风分离器分离煤层气中细微的粉尘,即粒径小于10μm 的固体颗粒(大于10μm的固体颗粒已经可以得到效率很高的分离效果了),提高旋风分离器的分离效率。此分离方法属于机械力分离,结构相对简单,能在高温高压下维持正常工作,造价也不高,是工业生产中的良好选择。
1.气固分离机理及分类
在气固分离技术领域,有许多普遍的分离机理。
重力分离机理:这是最基本的一种分离形式,如沉降室。气固混合物中的固体颗粒的分离主要借助中立的作用,固体颗粒在重力沉降过程中必然会与气体产生差异,从而两者分离。
惯性分离机理:利用槽型构件组成的槽型分离器、迷宫式分离器等,凡能与分离构件表面相碰撞的固体颗粒都有可能被分离构件所捕获,含尘气流中的粉尘粒子都应与分离构件相碰撞而被搜集。
离心式分离机理:常用旋风分离器。当气体从旋风分离器的入口进入时,粉尘由于受到离心离德作用而被甩到边界上,并且离心沉降,从下端出口流出,而气体分子却仍在分离器的中心,并通过回流而从上方出口流出。
在这些分离过程中,有一个准则关系式:
Stk
F
F
S
O
,即粒子所受离心力与气体介
质所作用的阻力之比。
按作用的情况对气固分离器进行分类,可分为四大类:机械力分离,静电分离(分离固体粒子粒径0.01~0.1μm),过滤分离(分离固体粒子粒径0.1μm),湿洗分离(分离固体粒子粒径1~0.1μm)。煤层气工业一般少用后三种,因为后三种分离速度慢、成本高,且不适用于高温高压等苛刻的条件。但是那些粒径较小的固体颗粒也必须除去,所以本项目针对的微小粒子粒径为小于10μm,而一般的旋风分离器通常只可除去10μm以上的固体粒子,因此对于我们来说是一项挑战,希
望我们可以成功突破这种局限。
2.气固分离的基本物理模型
塞状流分离型式:
在层流运动中,这是气固分离的常用理论模
型,在这种模型中,颗粒完全不返混,气流带
动颗粒前进的速度为V ,捕集力推动颗粒向捕
集面移动的速度为U ,则颗粒向捕集面移动的
速度为轨迹可表示为
V U dl dh =。
横混分离模型:
在湍流运动中,气固分离的物理模型常呈这种
模型。我们可以假设颗粒在捕集分离空间的横
截面上是混合均匀的,沿轴向上则近于塞状流,
在dt 时间内,气流带动颗粒走过距离dl ,同时
分离力使颗粒像分离面移动了Udt 距离,假设
任意的该横截面上颗粒的浓度为n ,则该截面浓
度变化为
dl L U H Udt n ==1dn _
全返混模型:
如果在分离器内颗粒的混合十分强烈,则分离
过程呈此型式,即颗粒在全体积内是均匀混合
的,在同一时刻内空间各点的浓度都一样,经
过一定时间后,由于颗粒不断向捕集面移动,
浓度就会变小。
在实际的分离设备中,分离模型远远比这些模
型复杂,,可能是上述三个模型的不断组合,
在我们的项目中,我们可能会先从简单的模型
开始试验,循序渐进,不断积累相关的操作经
验,以便使结果更加准确些。
3.气固两相流边界层的流动规律
在我们的项目中,包括有对设计装置的模拟,所以需要了解清楚边界层的具体情况。
颗粒在流场中所受的力可以分为以下几类,第一类是与流体—颗粒的相对运动无关(重力、惯性力、压差力),第二类是依赖于流体—颗粒的相互运动,一些与相对运动方向平行(阻力、虚拟质量力、Basset 力),另一些与相对运动方向垂直(升力、Magnus 力、Saffman 力)。
当颗粒浓度较高,粒度较大而使流动不再能视为拟单相流时,固相的存在反过来就会对流动产生影响,这种影响使气固两相流中不再是气相单方面作用于颗粒
相,而是双向耦合的。小颗粒的加入会抑制湍流,大颗粒则会增强湍流。当旋风分离器用来分离小颗粒时,增加入口颗粒浓度时分离器的压降不仅没有增加,反而有所减小。这对于我们来说是一个重要的信息,因为我们研究的微小固体粒子正是会对分离效果产生这种影响,所以我们需要进一步研究压降与入口颗粒浓度的关系。
对小颗粒,其运动基本上是由流体运动和湍流扩散控制的。这时,颗粒碰击壁面后,马上又跟随气流运动,因此壁面反弹的影响不大;对较大的颗粒,由于惯性,反弹变得更加重要。由于我们所研究的煤层气中包括有大颗粒与小颗粒,所以我们必须弄清楚这些影响,这将是一个重要工作。
层流边界层:边界条件可写为
?????∞======>=====∞∞y T T T U u u x y T T v v u p p p g p g w g p g g ,,0
,0,0ρρ;
这只是简单的边界条件,如果加入颗粒扩散项对求解结果的影响,需建立一种新的模型,颗粒相连续方程中引入了扩散项。事实上,颗粒在平板上的切向速度会受到诸如平板表面粗糙度、滑动摩擦系数和颗粒—壁面碰撞等因素的影响,所以,又引入了滑动系数。
湍流边界层:
气流速度分布与距壁高度呈幂次关系,即
)/lg(10y y K u u =*
在湍流边界层中,剪切应力增加时,会交替出现高速区和低速区,从而形成漩涡。即便加入的颗粒浓度很低,也会显著改变颗粒特性。颗粒与湍流的相互作用时间就是漩涡的生存时间。
4.气固分离理论与旋风分离
在边界层上,设边界层的边缘处的速度为B v ,则边界层内的气体速度分布可写
为 22)(δR R v v w B -=
排气管以下任一截面切向速度u 的关系式为 5.015.2???? ??=D d F u u e i i
——i u 为含尘气体进入旋风分离器的入口速度;i F 为旋风分离器进口截面积;D 为旋风分离器筒体直径;e d 为旋风分离器排气管直径。
李杨新提出的径向速度计算式:
???????????≥>≥>+-≥-=012
51212510
122
r R R r R r R R r R r v c c c c c
c 如右图,进入旋风分离器的含尘气流沿桶壁
边旋转边下降,也同时有少量气体沿径向运
动到中心区域,当旋转气流的大部分到达锥
体顶部附近时,则开始转为向上流动(具体
工作原理会在后文具体描述),在回流区内大
部分外涡旋转变成为内涡旋。
对上排气旋风分离器,旋风分离器内的速度
分布明显地由中心区的准强制涡和外部的准
自由涡组成;由于边界层效应引起的中心筒
表面附近的短路二次流是很重要的,它使分
离效率降低。
由于流场内的速度梯度而使颗粒受到的Saffman 升力对颗粒的分离有着很大影响,极细(<5μm )的颗粒受其影响不大,因为它们通常跟随主流运动而很少进入边界层中;较大的颗粒在壁面附近跳跃,反复的向壁面靠近,又离开,直到被分离下来,因为升力帮助颗粒从核心区向壁面靠近,在壁面附近时方向逆转,阻使颗粒减速接近壁面,而一旦颗粒撞击壁面,它又促使颗粒离开壁面。而当颗粒以很小的横向速度碰撞时,则无法反弹而被分离下来。
在分离器的每一截面上径向速度V 取得最大值的位置是逐渐的由接近中心向器壁转移,而后又向中心移动,在接近出口区域,由于叶片旋转产生的离心力的影响以及顶壁的阻挡作用,径向速度有一相对峰值出现,在叶片内部由于落煤管的阻挡作用,也存在一峰值。且前者的值大于后者。由于出现漩涡与回流,分离器内由上而下流动特性不断变化。
由于工作环境的苛刻,旋风分离器存在一些很难改进的缺陷。对煤层气的分离所需的分离器与一般的分离器结构有所改变,导致效率有所下降,迫使提高分离器入口速度来弥补,从而加重了对分离器内壁的磨损,阻力损失增加等一些较为严重的问题。而且旋风分离器体型庞大,会制约系统的大型化发展。
二、旋风分离技术研究进展
1.环流式旋风分离器
据了解,工业生产排放的大量亚微米粉尘较其他粒径粉尘对人类及环境的危害更大,却难以脱除。在目前工业上常用的除尘方法中,重力沉降法只能分离100μm 以上粗颗粒;常规的旋风除尘器可分离10μm 左右的细颗粒,高效的多管旋风除尘器还可将5μm 以上的细粉尘捕集下来;湿洗分离法是通过液层、液滴和液膜来捕集粉尘的,它可分离1~5μm 的粉尘,效率高而可靠,但气体内易夹带液雾,而且只能在较低温度下使用,还具有设备较大易产生二次污染的问题;过滤分离可
将1~0.1μm的粉尘有效捕集下来,但设备庞大,造价和运行费用高,且不能处理有结露或粉尘吸潮性强的物系;静电除尘器对0.01~1μm的粉尘有较好的分离效率,但设备造价过高,操作和管理的要求也比较高。由青岛科技大学经过十年研究和开发的环流式旋风除尘器和环流循环除尘系统,有效地克服了上述除尘装置的不足。
鉴定专家组认为,该系列技术以多相流体湍流流动的理论研究成果为基础,所开发的环流式旋风除尘器的各项性能指标,均处于同类设备的领先水平。所开发的8项专利技术为企业解决了四十余项工程技术难题,并拓展了旋风技术的应用领域。该系统的除尘颗粒半径最小可达到1μm,达到了静电除尘级的水平;比传统的旋风除尘器的气体处理量提高10倍以上;同时具有压降低、放大效应小、占地省、投资少、运行费用低等优点。
工作原理及特点
如附图所示,环流式旋风除尘器的外形为圆
柱圆锥形,但直筒段内设有由李建隆等人开发的
与直筒同轴的内件。启用时,气体从直筒段下部
以切向方式进入器内内件,在内件中螺旋上升进
行一次分离,达到净化要求的大部分气体直接从
顶部排出,少部分气体连同被分离下来的粉尘由
顶部特设旁路引入锥体,在锥体内进行二次分
离,分离后的流体在锥体下部沿轴心返回一次分
离区,少量气体将粉尘送入灰仓后返回器内。[1]
此新型旋风除尘器的特点在于:
(1)压降低。流体由直筒段底部旋转而上,直接从
顶部出气口排出,流体流动路线短,且内件中只
有一个向上的旋涡,流体沿径向、轴向速度梯度
小,流体剪应力小,故压降和能耗低(压降仅为
常规型旋风除尘器的二分之一左右)。
(2)放大效应小。由于器内剪应力小、能耗低,在
大直径设备中仍能保证多相流分离所需要的旋转速度,器内流体不易发生湍动,故放大效应小。克服了常规型设备放大效应显著,在大处理量时需多台并联操作的弊病。
(3)分离效率高。特殊的流路设计,防止了流体的短路及锥体和灰仓内颗粒的卷扬,使分离效率大幅度提高,且具有操作弹性大、操作稳定性好等特点。
大量工业应用的结果表明,大型环流式旋风除尘器(直径在1.2m以上)的分割粒径可达1.2μm左右,压降仅为500~1000Pa,且直径放大后,不会产生分离效率的显著下降,并具有操作稳定性强,操作弹性大的优点。该系列专利成果分别于2004年12月、2010年12月通过了由山东省科技厅组织、中国科学院余国琮院士和李洪钟院士、工程院金涌院士主持的项目鉴定,其鉴定意见为:达到了同类技术和设备的国际领先水平。并于2005年获山东省技术发明二等奖,2011年获山东省技术发明一等奖。
推广业绩
由青岛科技大学化学工程研究所自主开发的环流式旋风除尘器在1997年获国家发明专利(专利号:ZL 92106712.7),环流循环除尘系统、直流降膜式旋风除雾器等获5项国家实用新型专利(专利号:01243742.5;01243741.7;
ZL92219769.5;ZL 02270076.5;ZL 01243740.9),2006年环流循环除尘系统的导流整流器获国家发明专利(专利号:031350585)。近年来,我公司利用环流式旋风分离系列专利技术的优越性能,针对工业生产过程逐一进行流场模拟,并依据过程的耐磨损、耐高温、防堵塞等要求调整结构和内构件。累计推广应用600余台套,攻克了四十余项工程技术难题,企业应用后的经济、社会效益显著。现列举部分应用实例如下:
(1)、由大连理工大学开发的褐煤干馏工艺,其中因烟气温度高(550℃以上)、粉尘含量高等因素,采用常规旋风分离器难以满足分离要求,采用我单位开发的环流式旋风分离器两级串联除尘分离效率可达99.5%以上。已成功应用于陕西神木富油能源科技有限公司褐煤干馏工艺。目前环流式旋风分离器已顺利投入使用(2)、多晶硅、有机硅单体生产多采用流化床反应器,催化剂为硅铜粉,因涉及军工,多年来国外一直对中国进行技术封锁。该系统除尘的难度在于,硅粉硬度极高,对器壁冲刷严重;要求一级除尘器具有颗粒分级功能,只回收5~10μm 以上的粉尘,二级对5μm以下粉尘应彻底去除;一级分离下来的粉尘在不影响反应器内取热构件的前提下,顺利回床。针对上述要求,我公司采用特殊材料制成衬里以提高设备的耐磨性能。由于采用衬里,内构件壁厚大为提高,需对除尘器流场逐一模拟以调整结构尺寸。现已在多晶硅,有机硅行业应用二百余台,为企业创造了良好的经济效益,且使用周期从过去使用E—Ⅱ型高效旋风除尘器仅3个月延长至5年以上。
(3)、国内由乙炔和醋酸生产醋酸乙烯时,大多数采用流化床反应器,催化剂为椰壳活性炭浸渍醋酸锌经干燥而成。流化床出气的除尘器原采用DⅢ型,存在活性炭对器壁冲刷严重,设备使用周期仅半年,而且因除尘效率不高,催化剂损失严重,并造成后续工段堵塞问题。针对上述工况,采用导流形式降低活性炭对器壁的冲刷。因活性炭为多孔介质,表观密度小,经反复使用后粒度极细,湍流旋涡对颗粒的运动行为影响大,故设计时,在流场模拟的基础上,对整流构件结构进行了反复调整。自2001年始,环流式旋风除尘器已在该行业推广应用40余台,为企业创造了良好的经济效益。在山西三维集团运行的除尘器,一年可为厂家节省催化剂二十余吨,年节约和增收资金壹仟叁百余万元。且设备的使用周期提高到了5年以上,消除了生产中的安全隐患。
(4)、安徽安庆曙光化工有限公司为我国最大的氰化钠生产基地,年产固体氰化钠4万吨,干燥过程采用从美国引进的高温闪蒸成套技术与装备。生产中发现干燥系统所用旋风分离器效率低、易堵塞、物料损耗高。虽后设洗涤塔进一步净化排气,因氰化钠为剧毒物料,对排气含尘的要求非常高,环评不达标。针对上述工况,我公司在设计时首先通过流场模拟加长了一次分离区高度,调整了导流整流器结构,以提高除尘效率。然后对易积存物料的区域加设导流输送板,利用气体对易积存物料区域的冲击,防止堵塞;同时,依据工况下气体的含水蒸汽量计算出了水分凝析温度,通过调整操作条件与壁面伴管加热,防止水分析出;由此设计的环流式旋风除尘器于2003年5月投入工业使用。经用户测算,环流式旋风除尘器的收率达到了99%以上,解决了设备易堵塞的工程难题,洗涤塔更换循环液的时间从8小时延长至96小时,并于2004年12月顺利通过了“环境管理体系”认证,并为企业年创经济效益近500万元。因环流式旋风除尘器使用效果好,安庆曙光化工集团有限公司已将原美国进口的干燥生产线上的旋风除尘器拆除,更换了环流式旋风除尘器。
(5)、环流循环除尘系统在超细粉体气流干燥中的应用。环流循环除尘系统于
2002年用于广西瑞泉公司超细膨润土气流干燥的除尘。二级旋风除尘器除下的粉尘粒度在2mm以下的达到了75%,应用效果良好。
(6)、北京矿冶研究总院在浙江、江苏、大连、吉林、内蒙、甘肃等地建立的24条粉末炸药生产线中全部采用环流式旋风除尘器进行炸药收集。使炸药收率从90%提高到98%以上。每年多回收的炸药价值近4千万元。由于压降低,全年可节省电费114万元。
(7)、同时环流式旋风除尘器还分别用于中国石化齐鲁分公司的高压聚乙烯装置和热电厂硫氨净化装置、北京利德恒环保公司的供热锅炉排烟脱硫除尘、石家庄以岭药业的原料回收等工程。
2.回流型动态旋风分离器
旋风分离器设计研究至今已有一百多年历史,然而旋风分离器的结构设计与性能计算仍不能完全摆脱经验,多年来对旋风分离器的基础研究和技术改进从未间断,内容涉及许多方面,包括分离机理探究、内部流场描述、分离性能计算模型建立、结构设计开发等,所有研究的目的最终是为了提高细粉分离能力、降低阻力、减小设备尺寸。到目前,各国学者、科研机构和生产企业都为此做了各种改进的措施,现就几个典型方法做以介绍。
(1)改变入口形式:进气口对分离性能有着重要的影响,选择合理的进口形式具有可使内部流场对称、稳定,避免形成上灰环,减小压损等许多优点。关于进气口形式,前面已经做了大量叙述,在此不再赘述。
(2)改变筒体结构:对于旋风分离器筒体,较常采用的是直筒单锥式结构,如前面介绍过,筒体直径以及筒体高度对分离性能都有一定的影响。对这方面的研究已经很成熟普遍,除了通过确定最优的直径尺寸、筒体高度来提高分离性能外,还可以改变传统的筒体结构来优化分离器的性能。
(3)为了消除“上灰环”的影响,Buell公司、上海化工研究院等单位设计开发了旁路式旋风分离器。这种分离器是在主体外部、距顶部一定距离处开设一个螺旋面式的旁路分离室,用来将上灰环中的颗粒引出返送回分离室,改善分离性能,将筒锥式旋风分离器圆锥段倒置改装成扩散式旋风分离器,气流在筒体内向下旋转过程巾,流通面积逐渐变大,减小了颗粒向中心运动从排气管排出的可能性,并且反射屏也有效减弱了微细粉尘的返混,提高了分离效率。另外提高分离效率,增大处理量,多管式分离器结构也进行了大量的研究,并取得了很好的效果。
3.国外研究进展
国外关于旋风器分离模型的研究始于20世纪60年代,并分别基于上述分离理论从不同的角度采用不同的方法进行研究,较为全面、系统和详细。代表性的研究有:综述2003年第6期46中国粉体技术臼井于1969年假设旋风器内气固两相的分离过程是一次分离、二次分离及过渡区域内分离过程的综合值,进而给出了效率分离模型的综合表达式。Sproull于1970年采用与电除尘器相类似的方法,给出了旋风器效率的分离模型计算公式,该式的表达形式与Deutsch公式一致。
D. Leith和W. Licht于1972年考虑湍流扩散对固相颗粒分离的影响,基于边界层分析理论,把气流中悬浮颗粒的横向混合理论与旋风器内气流的平均停留时间相结合,从理论上严格推导出了分级效率模型,该模型把旋风器的分级效率表示为由旋风器结构参数确定的无因次特性系数C、由运行参数确定的修正惯性系数7以及切向速度分布指数n的函数。水田和木村典夫于1974年结合实验数据,给出了
旋风器分级效率的计算式,该式把分级效率表示为固相颗粒粒径与分割粒径dc50的指数函数形式。Dietz于1981年基于ter Linden的实验结果,将旋风器内的气固两相分离区域划分为3个区域即:入口分离区域、下降流分离区域和上升流分离区域,并根据D. Leith和W. Licht的横向混合模型的思想,推导出了旋风器内气固两相分离模型。在筒径为200 mm的旋风器上,采用燃煤飞灰作为固相颗粒进行分离实验时,模型的预测结果与实测结果比较吻合。Mothes和Loffler[9,10]于1988年将Dietz三分离区域的假设扩展为四分离区域,即在原有基础上增加了排气芯管分离区域,从而修正了Dietz模型对于分离过程预测的不连续性,引入粒子沉降系数修正了旋风器内、外涡固相的浓度扩散效应,并考虑了排尘口底部的返混现象和浓度的径向梯度变化,提出了另一分离模型,模型的假设条件比较接近旋风器内实际的分离状况且考虑较为全面。在筒径为190 mm的旋风器上,该模型的预测结果与实测结果相吻合。Clift[11 ]等于1991年根据已有的实验数据比较了以上3种旋风器内气固两相分离模型。结果表明,D. Leith和W. Licht模型在计算气流在旋风器内的平均停留时上有一定的局限性,并在其假设条件下重新推导了 D. Leith和W. Licht模型,计算结果表明分级效率图为S形曲线;Dietz模型亦存在同样的问题,但在小直径旋风器的固相颗粒物分级效率预测上, Dietz模型仍具有一定的准确性;而Mothes和Loffler模型总体上优于其它两个模型。Li. E和Y. Wang[12]于1989年假设在外涡内固相颗粒的沉降可被忽略,且壁面上固相颗粒的浓度梯度为0,仅存在有限的湍流扩散,并考虑了固相颗粒的径向浓度分布并在不同的分离区域做出不同的假设,推导了新的分离模型,尽管该模型在理论上与Dirgo和Leith[13]于1985年的实验数据较为吻合,但其边界条件的假定在一定程度上仍值得商榷。
R. L. Salcedo[14]1993年从理论上分析了L-L模型、Dietz模型、M-L模型和L-W模型4种旋风器气固分离模型的优缺点,并在筒径为305 mm的旋风器上实验加以比较验证,结果表明,Mothes和Loffler模型在理论考虑的相对完备性和估算结果的准确性使它的描述与旋风器内部的气固两相流动较为接近并优于其它几种模型。
ZhaoZhong-ming和R.Pfeffer[15]于1997年以D. Leith和W. Licht分离模型为基础,按照旋风器分离模型与重力沉降室的横向混合分离模型表达形式的相似性,将L-L模型中的参数7运用固相颗粒服从对数正态分布的规律进行积分简化,推导出了以750为参数的旋风器总分离效率简化模型,与经典研究结果的对比表明,结果比较一致,但该模型仅能在一定程度上反映旋风器的总体分离能力。
W. S. Kim和J. W. Lee[16]于1989年同时考虑湍流扩散和边界层固相颗粒的沉降作用,将旋风器内部分为两个主要的分离区域即湍流核心区和近壁边界层区,根据Mothes和Loffler以及Enliang和Yingmin分离模型,推导出了基于边界层特性的旋风器气固两相分离模型,并于2001年在此基础上进行了改进[17]。与实验对比的结果表明该模型的实用性较好,但其边界层条件的简化仍需进一步探讨。
4.国内研究进展
国内关于旋风器分离模型的研究较晚,大都始于20世纪90年代,并有相当一部分借鉴了国外旋风器分离模型的研究思想,代表性的研究有:
向晓东[18]于1990年考虑固相颗粒在旋风除尘器内的输运过程,引入了分离空间的概念。通过建立气体流动和颗粒运动的数学模型,得出在适当边界条件下
的旋风器分离效率计算公式,并与国内外典型的实验结果比较验证,结果较为一致。
张吉光等[19]于1991年根据旋风器内气流的轴向速度分布规律确定尘粒在旋风器内的平均停留时间,分析了旋风器内气体的三维速度分布规律对固相颗粒分离的影响及旋风器各主要结构参数和运行参数的影响,并考虑筒体与锥体边界层内颗粒的分离效应,建立了旋风器分级效率的数学模型,通过实验表明,该模型综述2003年第6期47中国粉体技术
估算旋风器的分离性能计算值与实测值符合较好。陈建义、时铭显[20]于1993年认为Leith和W. Licht以及Mothes和Loffler模型对于尺寸较大、流量也较大的旋风器计算结果误差较大,并在PV型高效旋风分离器旋风器内部流场及浓度场测定的基础上,考虑了旋风器的短路流、颗粒间的相互碰撞、返混等对分离性能的影响,建立了旋风器分级效率的多区计算模型,该模型在PV型旋风器上与实测结果较为一致,但在其他类型旋风器上的适用性仍需进一步探讨。
张从智等[21 ]于1996年在边界层分离理论的基础上,考虑了旋风器内部主要结构参数以及固相颗粒的特性和运行参数的影响,以及旋风器内的三维速度(尤其是轴向速度和径向速度)分布规律,建立了旋风器分级效率的数学模型。该模型计算结果与在长锥型和直锥型旋风器的实验结果符合较好,而且与D型、B型旋风器的实验结果也符合较好。
杨兴森等[22 ]于1997年根据Dietz的假设条件,在实验研究的基础上,建立了火力发电厂制粉系统中细粉分离器分离效率的理论模型,并以不同工况下的分离效率进行了比较。该模型基本承袭了Dietz模型的思想。
沈恒根等[23 ]于1998年应用平衡尘粒模型分析给出了旋风器分割粒径dc50,并对木村典夫模型为基础,给出了旋风器分级效率的计算方法,对反应分级效率分布的参数切割粒径dc50和切向速度分布指数n进行了讨论,并以筒径为203 mm 的Stairmand旋风器为例,与D. Leith和W. Licht、向晓东、张吉光和张从智的分离效率模型进行了对比,结果表明该模型更接近于实测值。
刁永发等[24 ]于2000年以平衡尘粒模型以及相似理论原理分析为基础,根据木村典夫分离模型,给出了该分离器高温旋风分离的分级效率的计算方法,对反映其在高温状态下分离特性的参数分割粒径dc50和分布指数n进行了分析,并以Stairmand高效旋风器试验对照。
王政和周学林[25 ]针对环流式旋风器的特点,推导出了其内筒分级效率的数学模型,并与L-L横混模型相结合,把环流式旋风除尘器看作部分环流的两个常规旋风除尘器的串联,进行其分离效率的研究。分析比较结果表明,该数学模型基本反映了环流式旋风器内固相颗粒的流动、分布以及分离的实际情况,但模型仅局限于环流式旋风器的预测。
王广军、陈红[26 ]于2001年考虑了径向浓度梯度以及重力沉降和径向加速过程对固相颗粒分离的影响,建立了锅炉细粉分离器分离效率的计算模型。该模型认为,当分离器进口风速较低及固相颗粒粒径较大时,重力沉降及径向加速过程对分离效果的影响不容忽视,并对已有的分离模型中有关简化条件的适用范围进行了分析。
三、旋风分离器机理研究
1.旋风分离器的简要介绍
(1)工作原理:净化天然气通过设备入口进入设备内旋风分离区,当含杂质气体沿轴向进入旋风分离管后,气流受导向叶片的导流
作用而产生强烈旋转,气流沿筒体呈螺旋形向下进入
旋风筒体,密度大的液滴和尘粒在离心力作用下被甩
向器壁,并在重力作用下,沿筒壁下落流出旋风管排
尘口至设备底部储液区,从设备底部的出液口流出。
旋转的气流在筒体内收缩向中心流动,向上形成二次
涡流经导气管流至净化天然气室,再经设备顶部出口
流出。
(2)性能指标
分离精度:旋风分离器的分离效果:在设计压力和气
量条件下,均可除去≥10μm的固体颗粒。在工况点,
分离效率为99%,在工况点±15%范围内,分离效率为97%。
压力降:正常工作条件下,单台旋风分离器在工况点压降不大于0.05MPa。
设计使用寿命:旋风分离器的设计使用寿命不少于20年。
(3)结构设计
旋风分离器采用立式圆筒结构,内部沿轴向分为集液区、旋风分离区、净化室区等。内装旋风子构件,按圆周方向均匀排布亦通过上下管板固定;设备采用裙座支撑,封头采用耐高压椭圆型封头。
设备管口提供配对的法兰、螺栓、垫片等。
通常,气体入口设计分三种形式:
a) 上部进气
b) 中部进气
c) 下部进气
对于湿气来说,我们常采用下部进气方案,因为下部进气可以利用设备下部空间,对直径大于300μm或500μm的液滴进行预分离以减轻旋风部分的负荷。而对于干气常采用中部进气或上部进气。上部进气配气均匀,但设备直径和设备高度都将增大,投资较高;而中部进气可以降低设备高度和降低造价。
(4)应用范围
旋风分离器适用于净化大于1-3微米的非粘性、非纤维的干燥粉尘。它是一种结构简单、操作方便、耐高温、设备费用和阻力较高(80~160毫米水柱)的净化设备,旋风除尘器在净化设备中应用得最为广泛。改进型的旋风分离器在部分装置中可以取代尾气过滤设备。
2.旋风分离器的工作原理及气流流动
(1)离心式气体净化设备简介
在离心分离设备内,通过让含尘气体产生旋转运动,将粉料颗粒甩向边壁然后通过边壁附近向下的气流,将已分离的颗粒带到排尘口。旋风分离器本体段由筒体和锥体组合而成。对于标准的逆流旋风分离器(具有通常所说的槽形或管形入口),通过人口结构的设计迫使气流切向进人旋风分离器内产生旋转运动。人口一般为如图所示的矩形截面。气流在作旋转运动的同时沿分离器的外侧空间向下运动。在分离器锥体段,迫使气流缓慢进人分离器内部区域,然后气体沿轴向向上运动。通常将分离器的流型划分为“双旋涡”,即轴向向下运动的外旋涡和向上运动的内旋涡。净化气体经过升气管排出,升气管为分离器顶板中心向下延伸
部分。除了将排气管称为升气管外,还有其他一些叫法,有时还常称为芯管。人口气体中的含尘颗粒在分离器内离心力场作用下向边壁运动,同时由边壁附近向下运动的气体将其带到分离器排尘口在后面章节里,将详细介绍分离空间内的气体流动。
具有切向人口的逆流式筒锥型旋风分离器示意切流式旋风分离器的几何尺寸主要有以下八个尺寸:
①旋风分离器本体直径(指分离器筒体截面的直径),D;
②旋风分离器总高(从分离器顶板到排尘口),H;
③升气管直径,Dx
④升气管插人探度(从分离空间顶板算起),S;
⑤入口截面的高度和宽度,分别为a和b;
⑥锥体段高度,Hc;
⑦排尘口直径,Dd;
所有尺寸皆被视为内部尺寸,即与气流接触面尺寸。
离心式分离器的种类
离心分离器依据以下特征分为:①人口结构型式;②分离器本体形状;③气流进出方向。
主要使用的有以下四种类型的人口结构。
①最简单的一种是圆形或管形人口。这种人口结构形式的旋风分离器常用金属板材制作、价格便宜,适用于分离性能要求不高的场合,许多木制品厂和造粒装置常选用这种人口结构的分离器。与后面所要介绍的槽型人口不同.圆管人口不需要安装圆形变矩形的过渡段。这种人口结构在化工和石油加工行业应用最为广泛。
②除了下面介绍的轴流式以外,用“切流式”来表示所有具有切向人口的旋风分离器。除了有时需要增加刚度或特定补强外,切向人口结构旋风分离器制造并不困难,而且分离性能好。由于一般采用圆形管道将来流输送到分离器,这种旋风分离器需要圆形变矩形的过渡段,使得其结构比简单的圆管形入口复杂一些。从制造或强度观点来看,人口顶板常略低于分离器顶板,而不是采用图中所示的平齐设计。这可能导致分离器顶板下面存在上灰环现象。但顶灰环存在一般不会显著影响分离性能。
③环绕式又称为螺旋或蜗壳式。对这种入口结构来说,由于气体进人蜗壳后的过流面积减少,使得气体在进人主要分离空间前已逐渐加速。因为这种蜗壳人口半径大于其他人口结构,导致气流人口环量大,内旋涡涡核的旋转速度也相应增高。这种入口结构可以实现在筒体和锥体段尺寸不变的情况下,增加处理气量。因为来流气体和粉料不会冲击升气管外壁,常选用直径较大的升气管。气体进人主要分离空间前,在蜗壳人口段已首先分离大部分颗粒,因此广泛使用于高浓度条件。蜗壳入口结构常用于处理大流量、高固料浓度的工况。
④导向旋流叶片人口〔导向叶片的作用是使气体沿轴向进人分离器。叶片位于升气管和分离器内壁之间的环形空间(或者,对于直流式分离器,中心部分为实体)。这种人口结构的分离器本体常采用直筒型。而不是筒体和锥体组合或单独锥体。有时,将这种分离器称之为旋风管或涡管分离器。旋风管一般尺寸小,常并联安装在承压容器内部的管板上。这些旋风管共用一个迸气室和一个排气室,进排气室由管板隔开。轴向入口的一个优点就是能保证内部气流流动的轴对称性,这样会给分离器的操作带来方便。例如,它可以消除一般切向人口分离器内与人口背
对着的升气管外侧的粉料层。气流的轴对称性也可以通过采用双切向人口来保证。轴向人口也省去了圆形变矩形的过渡段及在筒体段开缝这一工序。由于常将叶片铸造成一体,这样使得导流叶片型旋风分离器比其他分离器安装方便。
本体形状分离器有筒锥组合型和直筒型。
离心分离器的最后一种分类是依据气体进出分离器的方向来分。净化气体从分离器顶板排出的称为“逆流式”;气体与颗粒都从分离器底部方向排出的称为“直流式”。直流式旋风分离器常采用直筒型结构。
旋风分离器和旋风管
上述各种结构形式的旋风分离器有些在实际工程上很少使用,工业上最常用的两种结构旋风分离器,它们都为逆流式:
①切向人口(矩形和环绕式)和本体为筒锥体型的,称之为旋风分离器;
②具有轴向导流叶片人口和本体为直筒型的,这样就区分清楚了导向叶片和切向入口结构。对切向人口。除非特别加以说明,通常指槽型和环绕式人口。称之为旋风管。
为了解旋风分离器的实际工作原理,其中所谈论的论题必然涉及到不同的学科。尤其是与旋转流动有关的流体力学、流体中颗粒的流动、颗粒特性(例如尺寸和尺寸分布、形状、密度)等知识。
(2)气体流动
旋转流动
旋转流动,或者旋涡流动,经常存在于各种不同的设备中.例如旋风分离器、水力旋流器、喷射烘干机和旋涡燃烧室。旋流也在流体控制技术和过程强化研究领域中起着主要作用。它也是近年来在工业领域有重大应用的破沫旋风分离器的理论基础。
根据以下两类理想的旋流运动。叮得其对应的切向速度分布的表达式。
①强制涡即涡流内各点有相同的旋转角速度,就像旋转的刚体一样口
②自由涡即无摩擦流体的旋转运动.其涡流运动中的切向速度,使得流体微元在所有径向位置上的动量矩相同。而实际流体中的切向速度分布则介于以上二者之间。
为了得到这些速度分布式。首先来分析一下作用在旋转流体微元上的受力。采用柱坐标(r, θ, z) 来表示,其中,二轴是旋转轴,方向指向纸外。由于微元体是旋转的.因此,它将向中心作加速运动。如果它不作加速运动,那么它将沿与圆形运动轨迹相切的直线继续向中心运动。这个加速度就是向心加速度。对于一个微元体,如果用一个绕它旋转的坐标系来观察,则观察不到向心加速度,但它将以方向背对旋转轴的惯性力来出现,即离心力。这个力从性质上讲与重力相似,其大小等于质量与向心加速度的乘积。对于一个流体微元(不同于固体或液体颗粒),离心力是由静压梯度所产生的一个力来平衡的,后者的方向指向旋转轴,并维持流体微元作圆周运动。因此,也可以说这个压力产生了向心加速度,在旋转流动中的这个压力将随着与旋转轴距离的增加而增大。
假设旋流流体的黏性(表现为一个刚体)为无穷大,那么.在不同径向位置的各层流体之间没有剪切运动。此时,就使得所有径向位置上的流体微元具有相同的角速度口角速度s2的量纲是用单位时间的弧度大小来表示的。时间通常用秒来表示,因此,角速度的量纲为$-V,它等于}6}Y,其中v是切向速度。.单位为mls口S2为常数的旋转流动流叫做“强制涡流”或者“刚体转动”。旋风分离器的工作原理旋风分离器的工作原理是靠作用在旋转流场内颗粒上的离心力,使密度比
空气大的颗粒向外运动至旋风分离器器壁,然后再沿器壁向下运动到排料口口在逆流式旋风分离器中,净化气体大多沿中心轴线由旋风分离器顶部排出。
(3)旋风分离器中的流动
从几十年来所积累的实验结果可以看出,对旋风分离器内的气体流态已研究得相当清楚。然而,借助于计算流体动力学有关流场中的颗粒轨迹,却很少有实验数据。为此,可(CFD)方法来分析颗粒运动的轨迹。
气体流态:旋风分离器内速度场一般用热线风速仪、皮托管以及近年来常用的激光多普勒测速仪(LIIA )来测量。气体切向进人分离器后在分离空间产生旋流运动。在旋流的外部(外旋涡),气体向下运动,并在中心处向上运动(内旋涡)。这里,旋风分离器外部区域气体的向下运动是至关重要的。因为,它把所分离到器壁的颗粒带到旋风分离器底部,这主要依靠气体的向下运动,而不是靠重力的作用.在垂直放置的旋风分离器中,重力只起辅助作用。只有当旋风分离器内含尘浓度较高时,重力才对粉料排出具有显著的影响。因为,含尘浓度高时的“质量浓度”影响将很明显,以后将予以详细介绍。与此同时,气体还存在一个由外旋涡到内旋涡的径向流动,这个径向流动在沿升气管下面的分离器高度方向的分布并不是完全均匀的。
气体在外部区域沿轴向向下运动,在内部区域向上运动。如前面所提到的,器壁附近向下的轴向速度对将颗粒传输到排料口起重要作用。轴向速度在中心线附近常常存在一个滞留区域。有时甚至出现气体轴向速度是向下的口切向速度分布类似于兰金涡:外部的准自由涡和内部的准强制涡。
旋风分离器凹壁附近的旋流本身是不稳定的流动。因此旋流运动引起的压力梯度将在旋风分离器内壁产生“二次流”.,知道了静态压力沿旋流的外部区域是增加的。从顶板一直到下部的锥体的整个壁面的边界层内都存在压力梯度。另一方面,由于该边界层内的切向速度较低,其结果是在器壁附近区域的气团内存在向心的合力,于是沿旋风分离器顶板到锥体壁面出现方向向内的流动。因此,这个向心的合力,是由器壁和气团之间的摩擦阻力来平衡。
强烈的压力梯度除了产生上面提及的二次流动外,也会产生其他一些影响。含尘气体有一个离开器壁并作径向流动的强烈趋势,在器壁流动遇到扰动时,这种情况极有可能发生。这包含如下的情况:焊接裂缝、器壁的翘曲或变形、颗粒沉积、耐火或陶瓷衬里的损坏、器壁受到磨蚀、玻璃视窗、热电偶导管、观察孔、人孔或者人孔/窗(它们与旋风分离器的内表面不光滑或者形状不一致)、压力传感器、表面硬化或者“堆焊”的区域、法兰连接处、垫片伸人到流场内.以及大多数以前被维修过的地方(但“不像新的”旋风分离器那样有光滑的表面)。这甚至还包含器壁的不圆度或者器壁是用平板金属材料经过简单压制而成的,而不是经过滚压加工来保证内表面的光滑。实际上,这样的非理想情况是不可能用现有的模型进行精确地模拟。只有在已知壁面粗糙度的时候,模型才可用于具有均匀粗糙度的器壁。但是,这不能用来处理上面所列的非理想器壁情况。同时,这些情况还将严重影响分离性能。正因如此,这就特别需要现场工程师、维护人员以及设计者协调处理壁面情况,如果有流体扰动发生,则必须采取必要的、切实可行的措施,使得壁面平滑,以防止扰动现象的发生。
提及的二次流现象也会导致其他问题出现。例如,顶板附近的流动会使得流体沿升气管外壁向下流动。这就造成了升气管下口末端的径向速度增加,这就是前面所提到的常称之为“升气管末端短路流”。
实验研究表明,除了以上边界层内的二次流动外、在旋风分离器的涡核处还存在类似“面包卷”形状的二次流态。这种流态会使颗粒在旋风分离器内做循环运动。一般说来,通过考虑旋流对轴向和径向流动的影响,可以认识旋风分离器内的许多流动特征。
旋风分离器内的气流和颗粒运动是非常复杂,还没有能准确地反映各种影响因素的分离理论,于是,各国研究人员不得不作出各种简化假设,先后提出了不同的假说,比较有影响的主要有以下几种:
a.平衡轨道模型
将升气管向下延伸到旋风分离器的底部形成一个假想的圆柱面CS,假设所有气体速度分量沿整个圆柱面CS为常量,平衡轨道模型是对处于CS面上的旋转颗粒建立力的平衡得到的,即在此圆柱面上的旋转颗粒同时受到向外的离心力与向内流动的气流阻力,两力之间形成平衡。粒径较大的颗粒在离心力的作用下向旋风分离器壁运动被捕集;粒径较小的颗粒则被带入升气管而逃逸,处于平衡位置的颗粒的粒径就是旋风分离器的切割粒径。Barth在1956年提出的模型是最早的平衡轨道模型,他在实验的基础上提出了一个“通用曲线方程”,并用图形来表示。后来Dirgo和Leith用函数拟合了这个曲线。Licht认为如果旋风分离器中所有未被捕集的颗粒均趋于全返混,则可以用这个函数式来计算分级效率。b.停留时间模型
该模型主要考虑颗粒向器壁的移动,而忽略向内流动气体速度的影响。停留时间模型假设颗粒在旋风分离器内部又足够的停留时间使颗粒径向运动到器壁,并在旋风分离器的底部被捕集。最初的停留时间模型使由Rosin等人在1932年提出来的。他们将从旋风分离器入口的某一径向位置进入的颗粒径向到达器壁所需要的有效时间和实际的有效时间进行对比,把颗粒到达分离器底部之前径向运动的距离等于整个入口宽度的最小颗粒粒径称为临界粒径。停留时间模型的机理在本质上与平衡轨道模型的机理是不同的,但在很宽的旋风分离器设计合运行条件下,这两个完全不一样的模型计算的效率结果,在数值上以及变化趋势上吻合得非常好。
c.混合模型
混合模型综合了平衡轨道模型和停留时间模型的特点,它同时考虑了内外旋涡之间的颗粒交换和颗粒向器壁的移动这两个过程。最早在这方面研究的是Dietz,他的研究具有开创作用。后来Mothes和Loeffler在Dietz的研究基础上,建立了更为完善的模型。
旋风分离器内气固两相数值模拟研究
由于旋风分离器内内部的流动非常复杂,所以用试验或者解析的方法来得出分离器内部的流动状况比较困难。单纯地通过实验来研究旋风分离器,由于受到条件的限制,耗费大量的人力、物力和财力,而且周期通常都比较长。由于计算机的飞速发展,人们已经可以借助于计算机模拟技术来对旋风分离器的流场和颗粒运动进行数值模拟。数值模拟方法具有模拟能力强、计算速度快、资金投入少、等优点。通过对旋风分离器的气固两相进行模拟,可以揭示分离器内部的流动规律,从而能优化分离器的结构,缩短分离器的开发周期,具有重要的工程意义。由于旋风分离器内内部的流动非常复杂,所以用试验或者解析的方法来得出分离器内部的流动状况比较困难。单纯地通过实验来研究旋风分离器,由于受到条件的限制,耗费大量的人力、物力和财力,而且周期通常都比较长。由于计算机的飞速发展,人们已经可以借助于计算机模拟技术来对旋风分离器的流场和颗粒运
动进行数值模拟。数值模拟方法具有模拟能力强、计算速度快、资金投入少、等优点。通过对旋风分离器的气固两相进行模拟,可以揭示分离器内部的流动规律,从而能优化分离器的结构,缩短分离器的开发周期,具有重要的工程意义。
旋风分离器内气相数值模拟研究
旋风分离器内气相数值模拟的最重要的一个方面是对流场湍流的模拟。因为旋风分离器内的湍流为强旋转湍流,同时存在流体旋转和流线弯曲,还有回流现象,内部湍流具有强烈的非均匀性和各向异性的特点,流动比较复杂,因此旋风分离器内流场的模拟较为困难。数值计算结果的好坏很大程度上取决于湍流模型,因此,湍流模型是旋风分离器气相研究的主要研究对象。
在最初的发展时期,对湍流最根本的模拟方法是直接模拟,就是在湍流尺度的网格内求解三维N-S方程,在这种情况下没有采用任何湍流模型。但是这种方法的应用非常的局限,只能应用于某些简单运动,对实际工程中的大多数湍流流动,各国的学者还是倾向于采用各种湍流模型来进行模拟。
本世纪七十年代,计算流体力学和数值传热学取得了前所未有的发展。Boysan等人在1982年首次把CFD技术应用于模拟旋风分离器的气相流场。
旋风分离器内固相数值模拟研究
当利用数值计算方法研究旋风分离器内颗粒的运动情况时,由于气固两相流动气体单相流动要复杂得多,所以必须要引入多相流模型。求解气固两相流动的主要问题在于模拟颗粒相,而在解决问题时由于采用了各种近似或者简化,从而形成了不同得颗粒相模型。这些模型主要有:
a.SPD模型(单颗粒动力学模型)
它是最早期也是最简单得模型,该模型建立在拉格朗日坐标系中,认为颗粒相为离散体系,不考虑颗粒存在对流体运动的影响,相间有滑移,颗粒相无输运性质。因此可先求出流场后,再考虑颗粒再其中地受力和运动。然而在实际情况中,颗粒在流体中运动除受阻力和重力作用外,还受虚假质量力、压强梯度力以及非定常流场产生的力的影响。近来实验表明,颗粒的脉动不仅仅是因流场中流体的湍流脉动而产生的扩散,颗粒脉动有时反而大于流体的脉动,大颗粒的扩散有可能比小颗粒还要强,这些现象反映了该模型的局限性,所以在工程应用中受到了很大的限制。
b.SS模型(小滑移模型)
该模型采用欧拉坐标系,认为颗粒相为连续介质,不考虑颗粒对流体的影响。这一模型的基本点是认为颗粒与流体间的时均运动滑移就是颗粒相对于流体或相对于混合物扩散的体现,即认为颗粒的滑移及其扩散是同一现象的两个方面,颗粒的运动纯属受流体的夹带而引起的。小滑移模型把速度滑移和扩散漂移联系起来,是对问题的一种简化。该模型是建立较完整的两项流模型的开端,但又认为有颗粒时的流体流场与单相时相同,所以相对滑移较大的流动情况,特别时边界层或近壁层附近的应用中,SS模型的计算值与实测值有较大的差异。
c.NS模型(无滑移模型)
这个模型建立在欧拉坐标系中,认为颗粒相对流体流动有一定影响,但相间无滑移,颗粒有输运性质。该模型假设:各种粒度的颗粒时均速度等于当地流体速度;颗粒温度或保持为常数,或等于流体的温度;颗粒犹如流体中某一组分,其扩散与流体组分的扩散相同;颗粒按固定的尺寸或当地尺寸分组。由于无滑移的基本假设,NS模型的颗粒相方程组中不存在栋梁方程和能量方程,所以只须给出各尺寸颗粒组的质量守恒连续性方程或扩散方程,该方程可以由颗粒统计守
恒定律导出。由于不考虑颗粒相对于流体的速度滑移,利用该模型得出的结果与实际相差很大,所以很少用来解决工程实际问题。
d.PT模型(颗粒轨道模型)
颗粒轨道模型认为颗粒相是离散体系,并在拉格朗日坐标系中处理颗粒相问题。此模型与单颗粒模型的不同之处在于完整地考虑了颗粒与流体间的相互作用;与小滑移模型和无滑移模型地不同之处是考虑了相间有大滑移,且这些滑移与扩散漂移无关。PT模型又可分为颗粒具有输运性质的随机轨道模型和无输运性质的确定轨道模型两种。随机轨道模型属于一种较为完全的拉格朗日处理法,它之间由轨道形式的颗粒瞬时方程组出发,考虑流体湍流对颗粒的作用,计算颗粒的随机轨道及沿轨道的变化经历,其特点是,既考虑了颗粒的湍流扩散作用,又不需采用颗粒湍流扩散系数的概念;确定轨道模型忽略了颗粒相自身各变量的脉动和流体相密度的脉动及变质量源的脉动,与单流体模型方程相比,确定轨道模型的颗粒相方程组中除有颗粒相连续方程外,还增加了动量及能量方程,单单流体模型中存在的颗粒扩散相,去定轨道模型中却没有,与小滑移模型相比,确定轨道模型中的滑移和扩散无直接联系;而在小滑移模型中,认为相间的滑移就等于颗粒的扩散。颗粒轨道模型由于很直观地描述颗粒与颗粒、颗粒与气体、颗粒与固体边界之间相互作用,所以被很多研究两相流的人采用。
e.MF模型(拟流体或多流体模型)
该模型的本质是把颗粒群作为与流体相互渗透的拟流体或者拟连续介质,其质量、动量、能量守恒方程与气相方程一致,模型建立在欧拉坐标系上。与前面4种模型相比,MF模型更完整地考虑了颗粒相和流体相之间地滑移、相间耦合和湍流扩散效应。此模型与小滑移和无滑移模型地差别在于,认为相间存在大滑移,扩散与滑移不能等同,并认为颗粒地扩散也不同于流体地扩散。多流体模型与轨道模型相比,除描述颗粒相地坐标系不同外,前者还引入了颗粒粘性、导热及扩散系数等拟流体特性,故能完整地考虑颗粒相对流体流动的影响以及颗粒相的各种输运特征。多流体模型直接从湍流两相流时均守恒方程组出发,按颗粒拟流体连续介质模型或多流体模型概念使方程组封闭,是较为完整和严格的两相湍流的数学模拟方法。但此方法计算出的结果反映的是固体颗粒的浓度、压力、速度等的平均值,不能反映单个颗粒的运动规律,而且这种模型在处理固相边界时也不能真实反映颗粒的流动状况,并且对固相粘性系数也很难定义和确定,很多是通过经验得来的。
这些模型是从不同得角度对气固两相流得近似,它们各自得应用范围可以参照文献。在壁面边界处,粒径较小的颗粒主要受气体流动和湍流的影响,而对于粒径较大的颗粒,主要受惯性和与壁面的碰撞的影响。在壁面边界处,气体的速度梯度变化很大,因此要对颗粒与壁面的碰撞和反弹过程有一个清楚的了解。Grant,Tabakoff,Hamed等人给出了纯经验公式,计算颗粒与壁面的碰撞过程;Tsuji,Morikawa等人根据碰撞原理给出了颗粒与壁面碰撞过程的计算公式,他在模拟过程中引入了一个虚拟碰撞壁面,与真实壁面之间有一夹角α,颗粒与真实壁面碰撞角度为η,然后根据两者之间的关系计算颗粒碰撞后的速度。Sommerfeld在Tsuji模型的基础上,引入了一个随机分布函数作为壁面粗糙度对颗粒运动的影响,计算结果与实验吻合较好。Fletcher,Nguyen等人在边界层理论的基础上,分析了直径较小的颗粒在弧形壁面的运动,根据颗粒斯托克数的大小,确定了固体颗粒在边界的碰撞反射规律,并与数值计算结果进行了比较。
一般来说,对于固体浓度比较小的气固两相流,可以不用考虑颗粒间的相互
碰撞;但对于颗粒浓度较大的气固两相流,比如气力输送,必须考虑颗粒间的相互碰撞,因为颗粒间的相互碰撞对颗粒的运动影响很大。Cundall和Strack给出了颗粒之间碰撞的冲撞一滑移模型,并将其用于模拟计算准平衡粒状流中。Tsuji,Gera等采用了以上模型,并对其进行了修正,用于模拟水平和垂直管道流及循环流化床中的气泡。Tsuji、Tanaka等采用蒙特卡罗法模拟计算了循环流化床中颗粒团的絮状结构,在计算过程中,他们将流化床中的大量颗粒用少数具有代表性的颗粒团代替,每一颗粒团具有相同的速度,颗粒团之间的碰撞通过动量守恒定律来计算。Jie Ouyang和Jinghai Liu先根据动量守恒原理计算颗粒之间的碰撞,然后计算颗粒与流体之间的相互作用,对循环流化床内的颗粒运动了模拟,计算出了流化床内气泡变化过程。从这些研究可以看出,在很多情况下,必须要考虑颗粒间的碰撞,否则数值计算得出得结果与实验结果会有很大得偏差。
参考文献
【1】《旋风分离器——原理、设计和工程应用》 A.C.霍夫曼,L.E.斯坦因著,彭维明,姬忠礼译
【2】《气固分离技术及理论》岑可法等著
【3】《旋风分离器的螺旋导流和防返混》潘传九,靳兆文,冯秀(南京化工职业技术学院,江苏南京210048)
【4】《旋风分离器内部气-固两相流场研究与发展》李敏,贲伟(大庆石油学院) 任志民(大庆油田第七采油厂南垣机加修理厂) 李盼(大庆油田工程有限公司)
【5】《旋风分离器内气固分离模型的研究进展》赵兵涛、沈恒根、许文元、陈东武
100万吨催化裂化装置反应-再生系统工艺设计
兰州理工大学 毕业设计 设计题目:100万吨催化裂化装置反应-再生 系统工艺设计 院系:石油化工学院 专业班级:化学工程与工艺 学生姓名:王晶 指导教师:赵秋萍 2010年1 月14 日
毕业设计任务书 一、设计题目: 100万吨催化裂化装置反应-再生系统工艺设计 二、设计内容 以某炼油厂的直馏馏分油为原料,建一个年产100万吨的催化裂化装置。主要生产稳定汽油、轻柴油。年开工按330天计算。 三、基本数据 1、处理量:100万吨/年 2、开工时:8000 小时/年 3、原始数据及再生-反应及分馏操作条件 原料油及产品性质分别见表1、表2 产品的收率及性质见表3 再生器操作及反应条件见表4、 提升管反应器操作条件表5 催化裂化分馏塔回流取热分配见表6 分馏塔板形式及层数见表7 分馏塔操作条件表见8 表1 原料油及产品性质 物料,性质稳定汽油轻柴油回炼油回炼油浆原料油密度0.7423 0.8707 0.8800 0.9985 0.8995 恩氏蒸馏℃初馏点54 199 288 224 10% 78 221 347 380 377 30% 106 257 360 425 438 50% 123 268 399 450 510 70% 137 300 431 470 550 90% 163 324 440 490 700 终馏点183 339 465 平均相对分子量 表2 原料油的主要性质 项目数据项目数据 密度0.8995 族组成分析/W% 馏程℃饱和烃62.27 初馏点224 芳烃25 10% 377 胶质11.88 30% 438 沥青质0.85 350℃馏出率/v% 7.5 重金属含量/μg×g-1 500℃馏出率/v% 49 Ni 5.99 元素组成/w% V 4.77
旋风分离器计算
作成 作成::时间时间::2009.5.14 一、問題提出 PHLIPS FC9262/01 這款吸塵器不是旋風除塵式的,現在要用這款吸塵器測參數選擇旋風分離裝置。二、計算過程 1.選擇工作狀況選擇工作狀況:: 根據空氣曲線選擇吸入效率最高點的真空度和流量作為旋風分離器的工作狀態。 吸塵器旋風分離器選擇 Bryan_Wang
已知最大真空度h和最大流量Q,則H-Q曲線的兩個軸截距已知,可確H-Q直線的方程。 再在這個直線上求得吸入功率H*Q最高點(求導數得)。求解過程不再詳述。求得最大吸入功率時真空度H=16.5kPa;流量Q=18.5L/s;吸入功率P2=305.25w 現將真空度及流量按照吸入功率計算值與實際值的比例放大,得真空度H=18.3kPa;流量Q=20.5L/s;2.選擇旋風分離器 為使旋風分離裝置體積最小,選擇允許的最小旋風分離器尺寸。一般旋風分離器筒體直徑不小于50mm,故選擇筒體直徑為50mm。按照標準旋風分離器的尺寸比例,確定旋風除塵器的結構尺寸。 D0=50mm b=12.5mm a=25mm de=25mm h0=20mm h=75mm H-h=100mm D2=12.5mm 計算α約為11度 發現計算得到的吸入功率最大值與產品標稱值375W相差一些,可能是由于測量誤差存在以及壓力損失的原因。
一般要求旋風分離器進氣速度不超過25m/s,這里取旋風分離器進氣速度為22m/s. 計算入口面積為S=3.125e-4平方米。 則單個旋風除塵器流量為Q=6.9e-3平方米/秒則所需旋風除塵器個數為3個計算分級效率 根據GB/T 20291-2006吸塵器標準,這里使用標準礦物灰塵,為大理石沙。进气粒径分布 103058 10019037575015002010 10102016113 顆粒密度ρp=2700kg/m3 進口含塵濃度取為10g/Nm3,大致選取空氣粘度μ=1.8e-6Pa*s 按照以下公式計算顆粒分級效率: 平均粒徑(μm)比重(%)
氧化铝催化尿素水解
氧化铝催化尿素水解合成氨使其安全使用于电厂烟道气的处理 摘要 背景:氨气可以提高静电除尘器除去锅炉中由于燃料的燃烧而产生的粉煤灰的效率。目前,氧化铝催化尿素水解制氨用于烟道气的处理已经处于研究阶段。 结果:研究了温度、催化剂和初始浓度对转化率的影响,结果表明转化率随着温度的上升呈指数增长,催化剂的添加和氨初始浓度的增加促进了转化率的增大。实验在不同的催化剂用量下进行,找到了在特定的原料浓度下最适宜的催化剂用量。 结果:对反应动力学的研究表明了反应时间对尿素制氨效率的影响。使用氧化铝时,催化尿素水解反应可以作为一级反应,同时测定了不同温度下反应的反应常数和活化能。 关键字:氨;尿素;尿素水解;催化剂;氧化铝;处理烟道气 引言 人口的增长和工业的发展都需要可持续的电力,当今社会主要依靠热发电站的煤燃烧来生成电。然而,煤的燃烧导致大量灰烬、粉煤灰的生成。粉煤灰微粒在烟道气中以悬浮体的形式存在,导致周围环境中浮游粒子状物质(SPM)的增长。因此,为保护环境,减少SPM 的排放变得十分必要。为了达到这个目的,使用了几个污染控制装置例如旋风分离器、袋式过滤器和静电除尘器(ESPs)。然而旋风分离器和袋式过滤器都有它们各自的缺点,ESPs是最广泛应用于热发电站来降低SPM排放的装置,主要是由于(1)它可以以较高的效率除去粒子(<0.01 m)。(2)可以在大范围的温度内操作。(3)对腐蚀性的周围环境具有一定的适应性。 在早些时候就证明出可以通过以下方法来提高ESPs的效率:(1)改变原料煤的特性。(2)增加收集版的面积。(3)使用湿的ESPs来减少二次夹带。(4)增加或减小气体温度。(5)添加化学物质来改变烟道气或ESP中的电气条件。然而大多数方法在热发电站中是很难实行的,主要由于:(1)原料煤的约束条件(进口、洗煤、环境问题的花费)。(2)添加较大面积的收集板要求更多的空间和花费。(3)安装和操作湿的EPS的费用太高,更不用说考虑在灰中形成的块状物和建筑材料的老化问题。 在这种情况下,烟道气的处理变得不可避免,包括在烟道气中添加化学添加剂来提高ESPs收集灰烬的效率。基于对关键文献的回顾,已经发现了FGC的几个优点:(1)和ESPs 相比花费更少(2)需要更少的时间(3)可以更灵活多变的使用,可以改变一些反应参数(例如煤的特性、锅炉负荷、ESP的电压和电流),SPM可以很容易地通过改变FGC催化剂的用量从而达到要求的水平。这些催化剂对于提高烟道灰/粉煤灰粒子的表面导电特性非常有帮助,有助于提高ESP灰烬收集效率。 氨气和SO3是使用最广泛的烟道气处理剂,一个特定的处理剂的效果取决于粉煤灰的组成。对于氨气有利于火力发电厂中烟道气的处理这一结论,人们已经知道很长时间了。一个廉价的替代物-氨的添加不仅仅可以提高沉淀器的性能,而且可以使反应迅速发生。氨可以以无水液体或水溶液的形式获得,但是无论哪种方法安全问题都非常重要。日常供应大型工业设备的氨用量是非常大的,而且现场需要大容量储存器。氨气属于危险气体,在很多地方大量的储存氨气,例如靠近城市人口中心,是非常不受欢迎的。在氨气运输和操作过程发生过数起导致死亡的事故,在很多地方也规定了关于氨气的限制条件。 有几个用来生产氨气的化学方法,其中三个最常用的是Haber-Bosch方法,间接电化学分离方法,尿素分解方法。Haber-Bosch方法是在高温(475℃)高压(20Mpa)催化剂条件下使用气态的氢气和氮气合成氨,这是大规模的工业生产方法。然而,它需要严格的条件而且尚未证实当流量低于1t/h时在技术上或者经济上是可行的;电化学分离已经被提议在半导
简述旋风分离器性能的优化
简述旋风分离器性能的优 化 摘要:综合了国内众多优秀论文的观点,从旋风分离器的结构设计、故障排除等角度讲述了提高旋风分离器工作效率,减少压降、阻力(延长使用寿命)的优化措施。阐述了工艺优化后旋风分离器性能上的改善,为进一步扩展其应用领域提供了必要的依据。 关键词:旋风分离器:分离效率;压降;使用寿命;性能优化 0 引言 旋风分离器作为一种重要的除尘设备,在石油化工、燃煤发电等许多行业都得到广泛应用。但是,由于其除尘效率一般多在90%左右,同时对粉尘粒径较小的粉尘除去效果一般,故对于除尘要求较高的生产场合,它一般只作为多级除尘中的一级除尘使用。这就使得旋风除尘器的使用条件受到了很大的限制。本文综合了国内众多优秀论文的观点,从旋风分离器的结构设计、故障排除等角度论述其性能优化的方法措施,使旋风分离器能适用于更广阔的应用领域。 1 旋风分离器结构设计对其性能优化的影响 1.1 旋风分离器与多孔材料的组合 人们为提高旋风分离器的效率,做了许多努力:将金属多孔材料安置于旋风分离器中,组合成的旋风—过滤复合式除尘器就是其中之一。这种结构设计在锥筒底部加了一段直管,机器到了增加分离的目的,又起到减缓旋流的目的,以避免二次扬尘的产生。 为此,实验人员做了相关的测定实验,选取了铁合金冶炼粉尘等4种直径大小从0.05μm~10μm的不等的颗粒(基本上涵盖了所有常见粉尘的粒径范围),让实验更具有广泛的实用性,分离效率可大幅提高至近100%。实验结束后,用氮气反吹滤管后,得到的结果非常理想,可进行再次实验,即实验的再生效果好。 1.2 改变入口切入角及外筒直径对旋风分离器性能的影响
影响旋风分离器性能的因素有很多,可以从改变其入口切入角和外筒直径这两个方面考虑工艺的优化。根据模拟结果显示,r=6000mm、θ=7.5°构造的旋风分离器效率接近95%,分离效果较好。现实验人员研究的就是在此基础上的设计优化。 首先,把入口切入角θ改为θ=9°及θ=6°两组,发现θ=9°比θ=6°入口速度高,但速度衰减慢,速度场分布均匀,速度偏差小,减少了对颗粒的二次卷吸,在外筒壁面处速度高,分离效率提高了。 其次,实验人员将外筒直径由6000mm变更为5600mm、5800mm、6200mm、6400mm,发现当直径增大,离心力作用小,分离效率降低;直径减少后,分离效果好,但由于在下部形成内旋涡卷吸了一些下沉颗粒,分离效果下降。故可利用此外筒直径与分离效率的变化关系,寻找最合适的外筒直径大小,以达到最佳的分离效率。 1.3加装循环管和防液罩对旋风分离器性能的影响 对旋风分离器加装循环管前后进行实验对比分析可知,加装循环管的旋风分离器压降小于不带循环管的分离器,这就是说,带循环管的旋风分离器在入口摩擦损失、器内气流旋转的动能损失等方面均要小于不带循环管的分离器。 防液罩的存在对分离器压降影响不大,但带防液罩的分离器在不同高度剖面上的切向速度明显大于不带防液罩的分离器,那么他的分离效率就会相应提高。因此,防液罩可以在不增加压降损失的同时,进一步提高切向速度,从而提高气、液相的分离效率。 1.4新设计样式的旋风分离器与旋风分离器性能的影响 已有许多研究人员着手于新型旋风分离器的设计与研究,新型双蜗壳旋风分离器就是新设计出的一种新型旋风分离器。他的上行流区的静压变化为顺压梯度,有利于气体的顺利排出,减少旋风分离器的压力损失。 另外,循环式旋风分离器也有着提高分离效率,降低系统能耗的作用。 2 排除故障以优化旋风分离器的效率 2.1 消除三旋单管堵塞 笔者以比较常见的三级旋风分离器为例,简述通过工艺手段,消除由于
废物处理方式(绿色化工)
废物处理方式简述 绿色化工 化学工程具有巨大的生产力,它紧握能源这一国家发展的命脉,它曾经为人民的生活带来了巨大的财富,它创造的的材料应用于人民生活的方方面面。但生产过程中的一些废弃物排入环境中,造成水体、大气和土壤的污染,这些污染物在水环境、大气环境和土壤环境之间不断地时行互相迁移、循环给人类的生活环境带来严重的危害。为了保护人类的生存环境,人类也逐渐意识到破坏环境的严重性,逐渐找到了许多对化工生产中产生的废物进行处理的方式。本文就当前对化工废物的处理方法进行简述。 化工生产过程的废物来源有以下两种: ⑴化工生产原料、中间体、半成品及成品。①化学反应不完全。未反应的原料,因回收不完全或不可回收而被排放掉。②原料不纯。原料本身纯度不够,其中杂志不需要参加反应而被排放掉。③跑、冒、滴、漏。由于生产设备、管道等封闭不严密或由于管理操作不善而造成的现象。它不仅造成经济损失,也造成环境污染。 ⑵化工生产过程中排放出的废弃物。①燃料燃烧。化工供热和化工路在燃烧的过程中不可避免的要有大量烟气排出。烟气中除含有粉尘外,还含有其他有害物质,对环境危害极大。 ②冷却水。化工生产需要大量冷却水。当采用直冷时,直接与被冷却的物料接触,很容易使水含有化工原料,而成为污染物质。同时,大量热废水排入水域,导致水体温度上升,造成水中溶解氧减少,降低水体自净能力,使得水体中的毒性物质毒性加剧并加速细菌的繁殖。 ③副反应。在化工生产中,还常常伴随一些人们所不需要的副反应。往往由于副产物数量不大,成分复杂,回收困难,因而在分离过程中被排弃,引起环境污染。④反应的转化物和添加剂。⑤分离过程。分离过程是化工生产中几乎必不可少的过程,如精馏塔釜下脚料过滤器的残渣、旋风分离器的尾气等等。 化工生产产生的废物分为三类:⑴固体废物:指那些成粉末状、灰块、块状或凝固状的废物。如残渣、烟灰、废橡胶,选矿后留下的含金属的矿渣等。⑵液体废弃物:指那些被污染的水体或其它废溶液,其中溶有盐类、碱类、酸和有机物,也包括分散的油液和含有悬浮的颗粒状杂志。如生产中出的废水或用过的有机溶剂和有机液体。⑶气体形式废物:指一些工业锅炉、干燥设备、通风设备所排出的气体以及化学生产过程中分离出来的气体等。如各种烟,各种气味气体及含有毒性物质、液体弥散颗粒、蒸汽空气混合的烟雾和气体。对化工废物的处理方式也分为三类:物理方法、化学方法和生物方法。 第一,废气处理。 化学工业所排放的大气污染物主要有:二氧化硫、氮氧化物、氟化氢、氯气、氯化氢、碳氢化合物,各种有机的和无机的气体、粉尘等。分为气溶胶污染物和气体污染物。气溶胶有粉尘、烟尘、液滴、雾和烟雾。对气体污染物的物理处理方法是分离法,利用外力等物理方法将废物从气体中提取出来。对于气固分离有机械力除尘、湿式除尘、过滤除尘、静电除尘,对于气液分离有机械力除雾、静电除雾,对于气气分离有冷凝法、吸收法和吸附法。对气体污染物的化学处理方法是转化法,使废气中的污染物发生某些化学反应,然后分离或转化为其它物质,再用其它方法进行净化。对于气象反应有直接燃烧法(苯、沥青烟等)和其它气相反应法(NOx等),对于气液反应有吸收氧化法(H2S等)、吸收还
旋风分离器工作原理
旋风分离器的作用 旋风分离器设备的主要功能是尽可能除去输送介质气体中携带的固体颗粒杂质和液滴,达到气固液分离,以保证管道及设备的正常运行。 工作原理 净化天然气通过设备入口进入设备内旋风分离区,当含杂质气体沿轴向进入旋风分离管后,气流受导向叶片的导流作用而产生强烈旋转,气流沿筒体呈螺旋形向下进入旋风筒体,密度大的液滴和尘粒在离心力作用下被甩向器壁,并在重力作用下,沿筒壁下落流出旋风管排尘口至设备底部储液区,从设备底部的出液口流出。旋转的气流在筒体内收缩向中心流动,向上形成二次涡流经导气管流至净化天然气室,再经设备顶部出口流出。 性能指标 分离精度旋风分离器的分离效果:在设计压力和气量条件下,均可除去≥10μm的固体颗粒。在工况点,分离效率为99%,在工况点±15%范围内,分离效率为97%。压力降正常工作条件下,单台旋风分离器在工况点压降不大于0.05MPa。设计使用寿命旋风分离器的设计使用寿命不少于20年。 结构设计 旋风分离器采用立式圆筒结构,内部沿轴向分为集液区、旋风分离区、净化室区等。内装旋风子构件,按圆周方向均匀排布亦通过上下管板固定;设备采用裙座支撑,封头采用耐高压椭圆型封头。设备管口提供配对的法兰、螺栓、垫片等。通常,气体入口设计分三种形式:a) 上部进气b) 中部进气c) 下部进气对于湿气来说,我们常采用下部进气方案,因为下部进气可以利用设备下部空间,对直径大于300μm或500μm 的液滴进行预分离以减轻旋风部分的负荷。而对于干气常采用中部进气或上部进气。上部进气配气均匀,但设备直径和设备高度都将增大,投资较高;而中部进气可以降低设备高度和降低造价。 应用范围及特点
旋风分离器
过去(04-05年间)我们曾经对国内的几家锅炉厂做过调研(济南、上海、杭州),重点考察旋风分离器技术,回厂后对几种分离器做过比较,今天得知您们想了解这方面情况,特介绍如下: 几种旋风分离器性能比较 项目高温绝热旋风分离器高温汽冷旋风分离器高温水冷旋风分离器 结构结构简单,金属外壳内衬耐火防磨材料,外敷保温材料。结构较复杂,壳体由汽(水)冷管子弯制、手工焊装而成,壳外敷保温、壳内衬25mm厚耐磨料。壳体采用膜式壁制作,紧贴炉膛布置,为方型水冷。 适应煤种适应于烟煤,另可掺烧优质褐煤或炉渣。适应各种煤种,包括矸石。煤种适应性差。 可维修性砌筑要求较高,壳体维修容易。更换管子难,恢复耐磨层也有一定难度。汽(水)冷旋风分离器 事故几率低汽水系统,事故频率高。 热惰性大旋风分离器筒体部分小,料褪部分大。 冷却效果无,可降50℃ 运行控制汽(水)系统简单起停炉凝结水不易带出,造成积盐、腐蚀。 后燃结焦烧无烟煤易出现后燃结焦。不易出现。不易出现。 分离效果在符合粒径要求的条件下可达99.5% 在符合粒径要求的条件下可达99.5% 飞灰含碳较低较低较高 起炉时间 7小时 3小时 3小时 造价低高较高
选择循环流化床锅炉不可避免地会提到效率和防磨问题。 高效的旋风分离器是提高锅炉运行效率的基础保证(虽然有电除尘灰返料等手段,但非主流)。“哪一种更适合于化工生产用锅炉?”你能稳定采购到什么样的煤种?(必须满足企业的运行成本控制要求)你的用气制度怎样?旋风分离器当然是锅炉选型的重要依据,但其也只是锅炉的一个部件。煤耗的高低和使用燃煤的关系很大,旋风分离器没有绝对的好,只有适合自己的。建议楼主综合考虑。 PS:锅炉项目投资很大,原煤参数必须要给锅炉厂家提供准确,尽可能满足今后使用供煤的需要。(前年对几家锅炉厂家进行过考察,收集到一些信息。结合其他渠道收集整理的资料如下) 目前我国循环流化床锅炉使用的高效分离器主要有三种: 1、上排气高温旋风分离器(有绝热式和汽冷式)。PS:水冷式的川锅也在做,俗称“四川独眼龙”,比较有特点。 2、下排气中温绝热旋风分离器。 3、水冷方形分离器。 优缺点: 一、上排气高温旋风分离器 (1)绝热式旋风分离器:耐火防磨保温层内衬厚、热惯性大,冷态点火启动时间长达12~16h;体积大、重量重、支撑困难;维修费用高;散热损失大。优点是分离效率高。PS:旋风分离器是循环流化床锅炉烟气流速最高的位置,这种结构的分离器有钢制外壳、绝热块、保温耐火砖、防磨衬里、紧固砖多层组成,对施工质量、耐火材料选择要求很高! (2)汽冷旋风分离器:风筒内只附设一层40~50mm厚的薄耐火材料层,缩短启停时间和承担一定的热负荷,大大降低了耐火材料重量和维护费用;减少了高温管道和膨胀节,从而降低维护费用;可采用标准保温,使外表温度下降,减少散热损失,可节约燃料费用 0.25%~0.5%;重量和尺寸均有所减小;能在制造车间装配好,整体或分片出厂,减少了现场工作量。 缺点:制造复杂,工艺要求高,因此成本较高。 PS:上排气旋风分离器阻力大,但分离效率高,是国内外主要锅炉公司首选的循环流化床锅炉主导分离器。但对使用易燃燃料或发热值十分低、灰含量特高(60~80%)的劣质煤,选用分离效率低一些的分离器(如下排气中温旋风分离器,方型水冷旋风分离器是最适宜的。即能降耗又能达到飞灰再循环要求。 二、下排气中温绝热旋风分离器 华中科技大学研究开发,克服了常规排气旋风分离器的一些缺点。 特点是:向下排气以及特殊结构的导流体。属于中温旋风分离器,顺应了“Ⅱ”型锅炉的整体布局,保持了“Ⅱ”型锅炉布置的结构特性,与上排器旋风分离器相比,总体尺寸明显减小(可减小占地面积30%左右)。与高温旋风分离器相比耐温耐磨材料易于解决,成本降低,
动力工程及工程热物理进展
浙江工业大学 攻读硕士学位研究生课程 文献综述 专业动力工程及工程热物理 课程名称动力工程及工程热物理进展 任课教师包士毅等 姓名赵李盼 2016年1月10日
多相流技术在泵研究发展中的应用分析 概述 两相流动主要分为气液和固液的混合运动。两相流广泛应用于能源、化工、冶金,核能、冶金等领域。早在年,两相流就被用来减少波浪对建筑物的破坏作用。此后,在工程中也得到越来越广泛的应用,如在河口用气泡幕防止盐水入侵控制水库和湖泊中的分层结构以及改善水质加速反应装置中的物质混合、热量交换、以及化学反应过程在城市河流污染治理中,用纯氧曝气复氧来治理污染河流、消除黑臭。在电力行业中的应用主要体现在火力发电厂的水力除灰系统中,和火力发电厂湿式石灰石洗涤法脱硫系统中。气液两相流动很大程度上取决于气泡运动形态以及分散相和连续相之间的相互作用。然而,在气液两相流动中,气液两相的流速是不同的。在流动时,气液两相的流动结构又是多样的,而且,带有随机性。有关固液两相流的问题很早就己经提出。早在年就己经较系统地研究过明渠水流中泥沙的沉降和输运。于年研究过声波在泡沫液体中传播时强度的衰减。但是许多经验和研究成果分散在各个不同领域,交流不多。直至上世纪四十年代,刁`开始有意识地总结归纳所遇到的各种现象,用两相流的统一观点系统地加以分析和研究。五十年代以后相关的论文数量显著增加,内容包括两相流边界层,空化理论,流态化技术,喷管流动等。六十年代以后,越来越多的学者开始探索描述两相流运动规律的基本方程。两相流作为一门独立的学科形成,并有了迅猛阶段,但迄今为止还没有非常成熟的体系,尚处于发展初期,很多方面都要依赖于经验数据,而且数据
旋风分离器设计
旋风分离器设计中应该注意的问题 旋风分离器被广泛的使用已经有一百多年的历史。它是利用旋转气流产生的离心力将尘粒从气流中分离出来。旋风分离器结构简单,没有转动部分。但人们还是对旋风分离器有一些误解。主要是认为它效率不高。还有一个误解就是认为所有的旋风分离器造出来都是一样的,那就是把一个直筒和一个锥筒组合起来,它就可以工作。旋风分离器经常被当作粗分离器使用,比如被当做造价更高的布袋除尘器和湿式除尘器之前的预分离器。 事实上,需要对旋风分离器进行详细的计算和科学的设计,让它符合各种工艺条件的要求,从而获得最优的分离效率。例如,当在设定的使用范围内,一个精心设计的旋风分离器可以达到超过99.9%的分离效率。和布袋除尘器和湿式除尘器相比,旋风分离器有明显的优点。比如,爆炸和着火始终威胁着布袋除尘器的使用,但旋风分离器要安全的多。旋风分离器可以在1093 摄氏度和500 ATM的工艺条件下使用。另外旋风分离器的维护费用很低,它没有布袋需要更换,也不会因为喷水而造成被收集粉尘的二次处理。 在实践中,旋风分离器可以在产品回收和污染控制上被高效地使用,甚至做为污染控制的终端除尘器。 在对旋风分离器进行计算和设计时,必须考虑到尘粒受到的各种力的相互作用。基于这些作用,人们归纳总结出了很多公式指导旋风分离器的设计。通常,这些公式对具有一致的空气动力学形状的大粒径尘粒应用的很好。在最近的二十年中,高效的旋风分离器技术有了很大的发展。这种技术可以对粒径小到5微米,比重小于1.0的粒子达到超过99%的分离效率。这种高效旋风分离器的设计和使用很大程度上是由被处
理气体和尘粒的特性以及旋风分离器的形状决定的。同时,对进入和离开旋风分离器的管道和粉尘排放系统都必须进行正确的设计。工艺过程中气体和尘粒的特性的变化也必须在收集过程中被考虑。当然,使用过程中的维护也是不能忽略的。 1、进入旋风分离器的气体 必须确保用于计算和设计的气体特性是从进入旋风分离器的气体中测量得到的,这包括它的密度,粘度,温度,压力,腐蚀性,和实际的气体流量。我们知道气体的这些特性会随着工艺压力,地理位置,湿度,和温度的变化而变化。 2、进入旋风分离器的尘粒 和气体特性一样,我们也必须确保尘粒的特性参数就是从进入旋风分离器的尘粒中测量获得的。很多时候,在想用高效旋风分离器更换低效旋风分离器时,人们习惯测量排放气流中的尘粒或已收集的尘粒。这种做法值得商榷,有时候是不对的。 获得正确的尘粒信息的过程应该是这样的。首先从进入旋风分离器的气流中获得尘粒样品,送到专业实验室决定它的空气动力学粒径分布。有了这个粒径分布就可以计算旋风分离器总的分离效率。 实际生产中,进入旋风分离器的尘粒不是单一品种。不同种类的尘粒比重和物理粒径分布都不相同。但空气动力学粒径分布实验有机地将它们统一到空气动力学粒径分布中。 3、另外影响旋风分离器的设计的因素包括场地限制和允许的压降。例如,效率和场地限制可能会决定是否选用并联旋风分离器,或是否需要加大压降,或两者同时采用。 4、旋风分离器的形状 旋风分离器的形状是影响分离效率的重要因素。例如,如果入口
旋风分离器参考文献
参考文献 [1]金国淼等.除尘设备[M].北京:化学工业出版社,2002:1-300 [2]Louis E. Stein, Alex. C. Hoffmann.旋风分离器-原理、设计和工程应用 [M].北京,化学工业出版社,2004:1-78 [3]国家环保局标准处.中华人民共和国国家标准环境空气质量标准[J],油气田环境保护,1996(04 ) [4]姚玉英,黄凤廉,陈常贵等.化工原理[M].天津:天津大学出版社,1999:138 [5]舒帆.影响旋风除尘器除尘效率的因素分析[J],粮食加工.2008, 33 (3):73-75 [6]韩占忠,王敬,兰小平.FLUENT流体工程仿真计算实例与应用[M].北京:北京理工大学出版社,2004:20 [7]魏志军,张平.旋风分离器气相流场的数值模拟[J].北京理工大学学报.2000, 20 (5):19-21 [8]嵇鹰,张红波,田耀鹏等.进口位置对旋风分离器特性影响的数值模拟[J].金属矿山,2008, 387 (3):127-129 [9]岑可法,倪明江,骆仲泱等.循环流化床锅炉理论设计与运行[M].北京:中国电力出版社, 2002:511-540 [10]陈明绍,吴光兴,张大中等.除尘技术的基本原理与应用[M].北京:中国建筑工业出版社,1981:333-518 [11]钱付平,章名耀.基于边界层理论旋风分离器分离效率的改进模型[J],中国电机工程学报.2007, 27 (5):71-74 [12]Hoffmann A C, Stein L E. Gas cyclones and twirl tubes:principles,design and operation [M]. Springer-Verlag,Berlin,Heidelberg,2002,169. [13]Leith D, Licth W. The collection efficiency of cyclone type particle collector. A new theoretical approach[J]. AIChE Symp Series,1972,126 (68):196-206. [14]Obermair S,Woisetschlager J,Staudinger G.Investigation of the flow pattern in different dust outlet geometries of a gas cyclone by laser Doppler anemometry[J].Powder Technology,2003,2-3 (138):239-251 [15]Zhao Bingtao.Development of a new method for evaluating cyclone
旋风分离器设计计算的研究.
文章编号:1OO8-7524C 2OO3D O8-OO21-O3 IMS P 旋风分离器设计计算的研究 蔡安江 C 西安建筑科技大学机电工程学院, 陕西西安 摘要:在理论研究和设计实践的基础上, 提出了旋风分离器的设计计算方法O 关键词:旋风分离器9压力损失9分级粒径9计算中图分类号:TD 922+-5 文献标识码:A 71OO55D O 引言 旋风分离器在工业上的应用已有百余年历 离器性能的关键指标压力损失AP 作为设计其筒体直径D O 的基础, 用表征旋风分离器使用性能的关键指标分级粒径dc 作为其筒体直径D O 的修正依据, 来高效~准确~低成本地完成旋风分离器的设计工作O 1 压力损失AP 的计算方法 压力损失AP 是设计旋风分离器时需考虑的关键因素, 对低压操作的旋风分离器尤其重要O 旋风分离器压力损失的计算式多是用实验数据关联成的经验公式, 实用范围较窄O 由于产生压力损失的因素很多, 要详尽计算旋风分离器各部分的压力损失, 我们认为没有必要O 通常, 压力损失的表达式用进口速度头N H 表示较为方便O 进口速度头N H 的数值对任何旋风分离器将是常数O 目前, 使用的旋风分离器为减少压
力损失和入口气流对筒体内气流的撞击~干扰以及其内旋转气流的涡流, 进口形式大多从切向进口直入式改为18O ~36O 的蜗壳式, 但现有文献上的压力损失计算式均只适用于切向进口, 不具有通用性, 因此, 在参考大量实验数据的基础上, 我们提出了压力损失计算的修正公式, 即考虑入口阻力系数, 使其能适用于各种入口型式下的压力损失计算O 修正的压力损失计算式是: 史O 由于它具有价格低廉~结构简单~无相对运动部件~操作方便~性能稳定~压力损耗小~分离效率高~维护方便~占地面积小, 且可满足不同生产特殊要求的特点, 至今仍被广泛应用于化工~矿山~机械~食品~纺织~建材等各种工业部门, 成为最常用的一种分离~除尘装置O 旋风分离器的分离是一种极为复杂的三维~二相湍流运动, 涉及许多现代流体力学中尚未解决的难题, 理论研究还很不完善O 各种旋风分离器的设计工作不得不依赖于经验设计和大量的工业试验, 因此, 进行提高旋风分离器设计计算精度~提高设计效率, 降低设计成本的研究工作就显得十分重要O 科学合理地设计旋风分离器的关键是在设计过程中充分考虑其所分离颗粒的特性~流场参数和运行参数等因素O 一般旋风分离器常规设计的关键是确定旋风分离器的筒体直径D O , 只要准确设计计算出筒体直径D O , 就可以依据设计手册完成其它结构参数的标准化设计O 鉴于此, 我们在理论研究和设计实践的基础上, 提出了分级用旋风分离器筒体直径D O 的计算方法O 即用表征旋风分 收稿日期:2OO3-O3-O3 -21- AP = CjPV j 7N H 2
参考文献
参考文献 姓名:林诗远 学号:20100410208 班级:10级车辆二班 第九章机械制造业的环境保护 第一节机械工业的环境污染 机械工业是为国民经济各部门制造各种装备的部门,在机械工业的生产过程中不论是铸造、锻压、焊接等材料成型加工,还是车、铣、镗、刨、磨、钻等切削加工都会排出大量污染大气的废气、污染土壤的废水和固体废物,如金属离子、油、漆、酸、碱和有机物,带悬浮物的废水,含铬、汞、铅、铜、氰化物、硫化物、粉尘、有机溶剂的废气,金属屑、熔炼渣、炉渣等固体废物,同时在加工过程中还伴随着噪音和振动。 熔炼金属时会产生相应的冶炼炉渣和含有重金属的蒸气和粉尘。 在材料的铸造成形加工过程中会出现粉尘、烟尘、噪音、多种有害气体和各类辐射;在材料的塑性加工过程中锻锤和冲床在工作中会产生噪音和振动,加热炉烟尘,清理锻件时会产生粉尘、高温锻件还会带来热辐射;在材料的焊接加工中会产生电弧辐射、高频电磁波、放射线、噪音等,电焊时焊条的外部药皮和焊剂在高温下分解而产生含较多Fe2O3和锰、氟、铜、铝的有害粉尘和气体,还会出现因电弧的紫外线辐射作用于环境空气中的氧和氮而产生O3、NO、NO2等;气焊时会因用电石制取乙炔气体而产生大量电渣。 在金属热处理中,高温炉与高温工件会产生热辐射、烟尘和炉渣、油烟,还会因为防止金属氧化而在盐浴炉中加入二氧化钛、硅胶和硅钙铁等脱氧剂而产生废渣盐,在盐浴炉及化学热处理中产生各种酸、碱、盐等及有害气体和高频电场辐射等;表面渗氮时,用电炉加热,并通入氨气,存在氨气的泄露;表面氰化时,将金属放入加热的含有氰化钠的渗氰槽中,氰化钠有剧毒,产生含氰气体和废水;表面(氧化)发黑处理时,碱洗在氢氧化钠、碳酸和磷酸
旋风分离器的建模及fluent模拟
旋风分离器的建模及 f l u e n t模拟 公司标准化编码 [QQX96QT-XQQB89Q8-NQQJ6Q8-MQM9N]
Gambit建模部分 本次模拟为一旋风分离器,具体设置尺寸见建模过程,用空气作为材料模拟流 场。为方便图形截取,开始先设置界面为白色窗体,依次点击“Edit”,“Defaults”,“GRAPHICS”,选择“WINDOWS_BACKGROUND_COLOR”设置为“White”,点击Modify。关闭对话框。 一.利用Gambit建立几何模型 1.双击打开, 2.先创建椭圆柱 依次点击“Operation”下的“Geometry”创建体“Volume”,点击“Create Real Frustum”,输入数据基于Z轴正方向创建“height 475;radius1 ; radius3 95”,点击Apply,生产椭圆柱体。如图1-1,图1-2。 3.创建圆柱体 再次利用创建椭圆柱按钮,输入数据基于Z轴正方向创建“height 285; radius1 95;radius3 95”,点击Apply。 移动刚刚创建的圆柱体,依次点击“Geometry”,“Volume”,点击“Move/copy”,选择刚刚创建的圆柱体,点击“Move——>Translate”,输入移动的数据“X=0,Y=0,Z=475”,并选择Connected Geometry,点击Apply。如图1-3,1-4所示。 图1-1椭圆柱设置对话框图1-2椭圆柱生成图
同样的方法创建小圆柱体,输入数据基于Z轴正方向创建“height 150;radius1 32;radius3 32”,点击Apply。 同样的方式移动小圆柱体,点击“Move——>Translate”,输入移动的数据“X=0,Y=0,Z=665”,不选择Connected Geometry,点击Apply。如图1-5,图 1-6,图1-7所示。 显示实体图,如图1-8。 4.将小圆柱体进行分割,分成上下两个圆柱面,点击“Split Volume”,选择被分割的圆柱体Volume2,选择下部组合体为分割体,点击“Bidirectional 和connected”,点击Apply。删除Volume3。如图1-9,图1-10所示。 5.创建旋风分离器进风口,点击依次点击“Geometry”,“Volume”,“create real brick”,基于中心,输入数据“width 140 ,depth 38,height 95”,点击Apply。如图1-11,图1-12所示。 图1-6小圆柱体移动命令对话框 图1-3圆柱体移动设置对话框图1-4圆柱体生成图图1-5生成小圆柱体 图1-7小圆柱体移动生成图图1-8实体图图1-9实体分割命令对话框图1-10生成实体图
旋风分离器文献综述(DOC)
关于旋风分离器的研究综述 组员:管清韦,孔繁星,吕萍 摘要:旋风分离器的主要功能是尽可能除去输送气体中携带的固体颗粒杂质和液滴,达到气固液分离,以保证管道及设备的正常运行。本文从气固分离理论、旋风分离技术研究进展及旋风分离器机理研究三个方面展开讨论。 关键词:气固分离、旋风分离器 一、气固分离理论 气固分离技术就是将固体颗粒从气流中分离出来,是众多工业流程的必备技术之一。它所涉及的分离器种类非常多,应用时的目的又不一样,按不同的分离机理、工作环境等均可有不同的设计,但一般常见的主要是应用在旋风分离器和脉冲喷吹袋式除尘器领域。 本研究项目主要是利用旋风分离器分离煤层气中细微的粉尘,即粒径小于10μm 的固体颗粒(大于10μm的固体颗粒已经可以得到效率很高的分离效果了),提高旋风分离器的分离效率。此分离方法属于机械力分离,结构相对简单,能在高温高压下维持正常工作,造价也不高,是工业生产中的良好选择。 1.气固分离机理及分类 在气固分离技术领域,有许多普遍的分离机理。 重力分离机理:这是最基本的一种分离形式,如沉降室。气固混合物中的固体颗粒的分离主要借助中立的作用,固体颗粒在重力沉降过程中必然会与气体产生差异,从而两者分离。 惯性分离机理:利用槽型构件组成的槽型分离器、迷宫式分离器等,凡能与分离构件表面相碰撞的固体颗粒都有可能被分离构件所捕获,含尘气流中的粉尘粒子都应与分离构件相碰撞而被搜集。 离心式分离机理:常用旋风分离器。当气体从旋风分离器的入口进入时,粉尘由于受到离心离德作用而被甩到边界上,并且离心沉降,从下端出口流出,而气体分子却仍在分离器的中心,并通过回流而从上方出口流出。 在这些分离过程中,有一个准则关系式: Stk F F S O ,即粒子所受离心力与气体介 质所作用的阻力之比。 按作用的情况对气固分离器进行分类,可分为四大类:机械力分离,静电分离(分离固体粒子粒径0.01~0.1μm),过滤分离(分离固体粒子粒径0.1μm),湿洗分离(分离固体粒子粒径1~0.1μm)。煤层气工业一般少用后三种,因为后三种分离速度慢、成本高,且不适用于高温高压等苛刻的条件。但是那些粒径较小的固体颗粒也必须除去,所以本项目针对的微小粒子粒径为小于10μm,而一般的旋风分离器通常只可除去10μm以上的固体粒子,因此对于我们来说是一项挑战,希
旋风分离器的设计
旋风分离器的设计 姓名:顾一苇 班级:食工0801 指导老师:刘茹 设计成绩: 华中农业大学食品科学与技术学院 食品科学与工程专业 2011年1月14日 目录 第一章、设计任务要求与设计条件 (3) 第二章、旋风分离器的结构和操作 (4) 第三章、旋风分离器的性能参数 (6) 第四章、影响旋风分离器性能的因素 (8) 第五章、最优类型的计算 (11) 第六章、旋风分离器尺寸说明 (19) 附录 1、参考文献 (20) 任务要求 1.除尘器外筒体直径、进口风速及阻力的计算 2.旋风分离器的选型 3.旋风分离器设计说明书的编写
4.旋风分离器三视图的绘制 5.时间安排:2周 6.提交材料含纸质版和电子版 设计条件 风量:900m3/h ; 允许压强降:1460Pa 旋风分离器类型:标准型 (XLT型、XLP型、扩散式) 含尘气体的参数: 气体密度:kg/m3 粘度:x 10-5Pa?s 颗粒密度:1200 kg/m3 颗粒直径:6 [1 m 旋风分离器的结构和操作 原理: 含尘气体从圆筒上部长方形切线进口进入,沿圆筒内壁作旋转流动。颗粒的离心力较大,被甩向外层,气流在内层。气固得以分离。 在圆锥部分,旋转半径缩小而切向速度增大,气流与颗粒作下螺旋运动。在圆锥的底部附近,气流转为上升旋转运动,最后由上部出口管排出;固相沿内壁落入灰斗。 旋风分离器不适用于处理粘度较大,湿含量较高及腐蚀性较大的粉尘,气量的波动对除尘效果及设备阻力影响较大。 旋风分离器结构简单,造价低廉,无运动部件,操作范围广,不受温度、
压力限制,分离效率高。一般用于除去直径5um以上的尘粒,也可分离雾沫。
旋风分离器的工艺计算
旋风分离器的工艺计算 》 : *
目录 一.前言 (3) 应用范围及特点 (3) 分离原理 (3) 分离方法 (4) ) 性能指标 (4) 二.旋风分离器的工艺计算 (4) 旋风分离器直径的计算 (5) 由已知求出的直径做验算 (5) 计算气体流速 (5) < 计算旋风分离器的压力损失 (5) 旋风分离器的工作范围 (6) 进出气管径计算 (6) 三.旋风分离器的性能参数 (6) 分离性能 (6) ~ 临界粒径d pc (7) 分离效率 (8) 旋风分离器的压强降 (8) 四.旋风分离器的形状设计 (9) 五.入口管道设计 (10) $ 六.尘粒排出设计 (10) 七.算例(以天然气作为需要分离气体) (11) 工作原理 (11) 基本计算公式 (12) 算例 (13) ( 八.影响旋风分离器效率的因素 (14) 气体进口速度 (14) 气液密度差 (14) 旋转半径 (14) 参考文献 (15) …
' 旋风分离器的工艺计算 摘要:分离器已经使用十分广泛无论在家庭生活中还是工业生产,而且种类繁多每种都有各自的优缺点。现阶段旋风分离器运用比较广泛,它的性能的好坏主要决定于旋风分离器性能的强弱。这篇文章主要是讨论旋风分离器工艺计算。旋风分离器是利用离心力作用净制气体,主要功能是尽可能除去输送介质气体中携带的固体颗粒杂质和液滴,以达到气固液分离,以保证管道及设备的正常运行。在本篇文章中,主要是对旋风分离器进行工艺计算。 [ 关键字:旋风分离器、工艺计算 一.前言 旋风分离器设备的主要功能是尽可能除去输送介质气体中携带的固体颗粒杂质和液滴,达到气固液分离,以保证管道及设备的正常运行。它是利用旋转气流产生的离心力将尘粒从气流中分离出来。旋风分离器结构简单,没有转动部分制造方便、分离效率高,并可用于高温含尘气体的分离,而得到广泛运用。 ' 旋风分离器采用立式圆筒结构,内部沿轴向分为集液区、旋风分离区、净化室区等。内装旋风子构件,按圆周方向均匀排布亦通过上下管板固定;设备采用裙座支撑,封头采用耐高压椭圆型封头。设备管口提供配对的法兰、螺栓、垫片等。 通常,气体入口设计分三种形式: a) 上部进气 b) 中部进气 c) 下部进气 对于湿气来说,我们常采用下部进气方案,因为下部进气可以利用设备下部空间,对直径大于300μm或500μm的液滴进行预分离以减轻旋风部分的负荷。而对于干气常采用中部进气或上部进气。上部进气配气均匀,但设备直径和设备高度都将增大,投资较高;而中部进气可以降低设备高度和降低造价。 应用范围及特点 旋风分离器适用于净化大于1-3微米的非粘性、非纤维的干燥粉尘。它是一种结构简单、
旋风分离器的设计
旋风分离器的设计公司内部编号:(GOOD-TMMT-MMUT-UUPTY-UUYY-DTTI-
旋风分离器的设计 姓名:顾一苇 班级:食工0801 指导老师:刘茹 设计成绩: 华中农业大学食品科学与技术学院 食品科学与工程专业 2011年1月14日 目录 第一章、设计任务要求与设计条件 (3) 第二章、旋风分离器的结构和操作 (4) 第三章、旋风分离器的性能参数 (6) 第四章、影响旋风分离器性能的因素 (8) 第五章、最优类型的计算 (11) 第六章、旋风分离器尺寸说明 (19) 附录 1、参考文献 (20) 任务要求 1.除尘器外筒体直径、进口风速及阻力的计算 2.旋风分离器的选型 3.旋风分离器设计说明书的编写 4.旋风分离器三视图的绘制
5.时间安排:2周 6.提交材料含纸质版和电子版 设计条件 风量:900m3/h ; 允许压强降:1460Pa 旋风分离器类型:标准型 (XLT型、XLP型、扩散式) 含尘气体的参数: 气体密度: kg/m3 粘度:×10-5Pa·s 颗粒密度:1200 kg/m3 颗粒直径:6μm 旋风分离器的结构和操作 原理: 含尘气体从圆筒上部长方形切线进口进入,沿圆筒内壁作旋转流动。 颗粒的离心力较大,被甩向外层,气流在内层。气固得以分离。 在圆锥部分,旋转半径缩小而切向速度增大,气流与颗粒作下螺旋运动。 在圆锥的底部附近,气流转为上升旋转运动,最后由上部出口管排出; 固相沿内壁落入灰斗。 旋风分离器不适用于处理粘度较大,湿含量较高及腐蚀性较大的粉尘,气量的波动对除尘效果及设备阻力影响较大。 旋风分离器结构简单,造价低廉,无运动部件,操作范围广,不受温度、压力限制,分离效率高。一般用于除去直径5um以上的尘粒,也可分离雾沫。对于