气缸和转子的相对膨胀
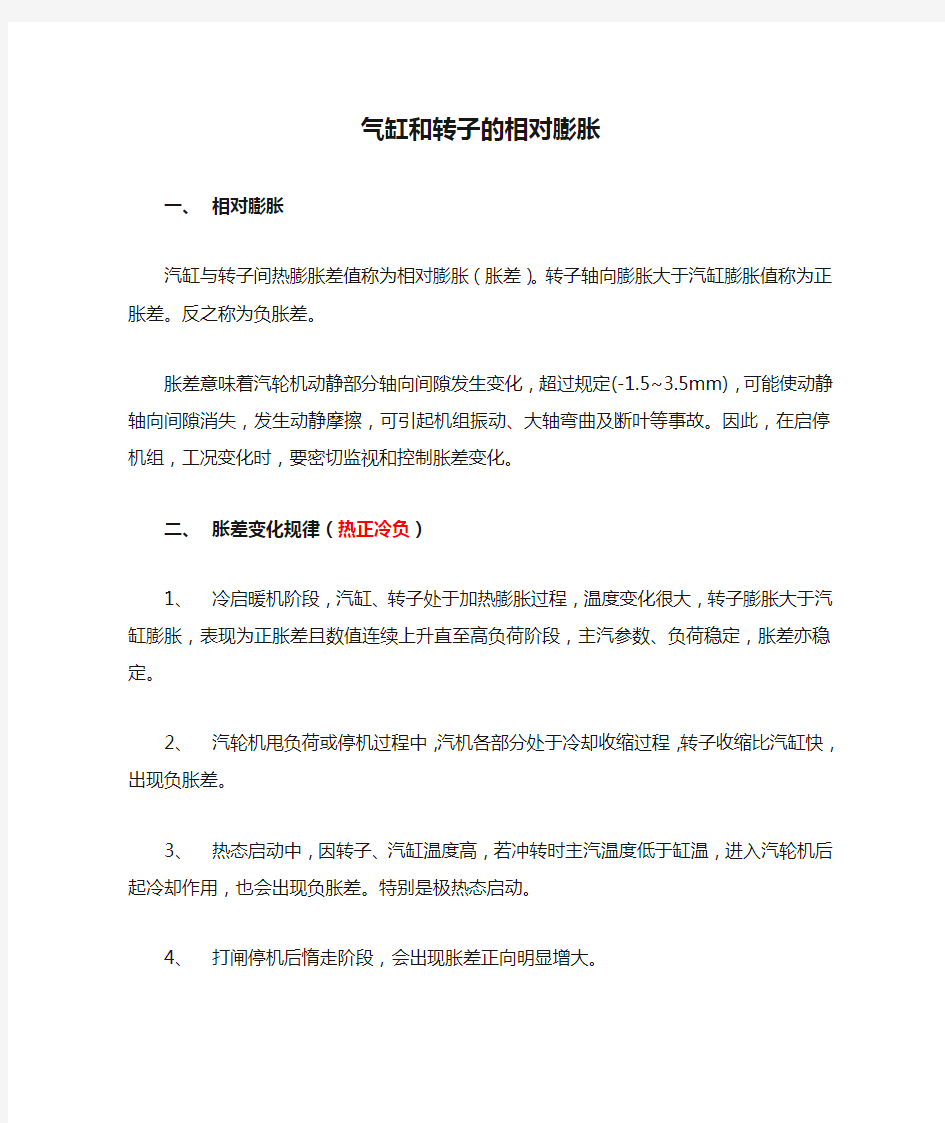

气缸和转子的相对膨胀
一、相对膨胀
汽缸与转子间热膨胀差值称为相对膨胀(胀差)。转子轴向膨胀大于汽缸膨胀值称为正胀差。反之称为负胀差。
胀差意味着汽轮机动静部分轴向间隙发生变化,超过规定(-1.5~3.5mm),可能使动静轴向间隙消失,发生动静摩擦,可引起机组振动、大轴弯曲及断叶等事故。因此,在启停机组,工况变化时,要密切监视和控制胀差变化。
二、胀差变化规律(热正冷负)
1、冷启暖机阶段,汽缸、转子处于加热膨胀过程,温度变化很大,转子膨胀大于汽缸
膨胀,表现为正胀差且数值连续上升直至高负荷阶段,主汽参数、负荷稳定,胀差
亦稳定。
2、汽轮机甩负荷或停机过程中,汽机各部分处于冷却收缩过程,转子收缩比汽缸快,
出现负胀差。
3、热态启动中,因转子、汽缸温度高,若冲转时主汽温度低于缸温,进入汽轮机后起
冷却作用,也会出现负胀差。特别是极热态启动。
4、打闸停机后惰走阶段,会出现胀差正向明显增大。
转子回转效应(泊桑效应):转子高速旋转时,受离心力作用,转子会在径向、轴
向变形,会变粗变短。当转速降低时,离心力变小,大轴又回到原本状态,即变细
变长,体现为胀差正方向突增。
三、影响胀差主要因素(冷态启动过程中)及控制
1、胀差产生的根本原因是汽缸转子存在温差。控制主蒸汽温度及温升速度,是启动中
控制胀差的根本。(主蒸汽升速率1~2.5℃/min,升压率0.2~0.3mpa/min)出现胀差
上涨过快,应联系锅炉停止升温升压保持稳定,一般情况不采取降主汽温度来减小
正胀差。
2、合理的暖机时间。在规程规定的暖机各阶段时间完成后,应综合汽缸绝对膨胀值、
胀差、缸温、振动等情况决定是否升速,升负荷。
3、轴封供汽温度影响
轴封供汽直接与大轴接触,其温度直接影响大轴伸缩。因此,可通过调整轴封供汽温度来控制胀差变化。
特别注意:轴封供汽应充分疏水
轴封供汽温度高于轴温会使大轴局部受热伸长,胀差正向增大。
轴封供汽温度低于轴温会使大轴局部冷却收缩,胀差负向增大,在极热态启动中,如果轴封供汽温度过低,会造成高压轴封处轴颈急剧冷却收缩,将导致此处局
部摩擦。
4、轴封漏汽影响
轴封漏汽应通畅,如漏汽未及时排走,会增大大轴轴封段的加热程度,造成胀差正向增大。
5、凝汽器真空影响。是启动中调整胀差的重要手段。
当真空降低时,(转速或负荷稳定情况)进汽量增大,加快汽缸膨胀;真空下降,低压缸排汽温度升高。均会明显减小正胀差。
6、冲转参数的选择:
原则范围内,冷态启动保证主蒸汽大流量是控制正胀差最好的方法。
如降低主汽压力,降低真空等都能使暖机汽量增大,使汽缸膨胀更充分,可明显减
小冷态启动中正胀差,明显缩短启动时间。
7、汽机滑销系统卡涩,体现为汽缸绝对膨胀值跳跃,正胀差过大及跳跃。
8、极热态启动
极热态启动中很难将主蒸汽参数提高至正温差,事实上基本都会是负温差启动。(一般规定主蒸汽应高于调节级上缸内壁温度50~100℃,过热度不低于50℃),具体体现为冲转后负胀差急速上升。
a)尽量提高主蒸汽温度,减小热冲击和负胀差程度
b)在冲转前,提前送入经过充分疏水的高温轴封气源,加热大轴轴封段,使转子
正向膨胀,留出冲转后的冷却收缩空间,防止负胀差大停机。切记充分疏水,
否则会加速负胀差增大。(温态0.12mpa、280~350度)
c)冲转前提高真空。减少冲转时进冷汽量,防止汽缸、转子收缩过快。
其他参照冷态启动。
系统投入时,泵的启动检查事项。
1、系统无影响投运的检修工作,工作票全部收回。所有电动门、转动机械送电,各表计信号投入。
2、检查补充进水侧容器水位至高位,检查高低水位报警。
3、检查进、出水侧管路畅通。
4、所有相关容器、管道放水阀、排空气阀关闭。(在启泵后逐一排空气至连续出水后关严排空气阀)
5、泵启动后重点检查法兰、焊口、测点等处有无泄漏,检查管道及附件情况,检查支、吊架。
6、检查系统内所有仪表报警工作情况。
7、在泵送电后,不要盘转动部分。
8、其他泵检查按常规。
图解常见汽车发动机结构图
发动机作为汽车的动力源泉,就像人的心脏一样。不过不同人的心脏大小和构造差别不大,但是不同汽车的发动机的内部结构就有着千差万别,那不同的发动机的构造都有哪些不同?下面我们一起了解一下。 ●汽车动力的来源 汽车的动力源泉就是发动机,而发动机的动力则来源于气缸内部。发动机气缸就是一个把燃料的内能转化为动能的场所,可以简单理解为,燃料在汽缸内燃烧,产生巨大压力推动活塞上下运动,通过连杆把力传给曲轴,最终转化为旋转运动,再通过变速器和传动轴,把动力传递到驱动车轮上,从而推动汽车前进。 ●气缸数不能过多
一般的汽车都是以四缸和六缸发动机居多,既然发动机的动力主要是来源于气缸,那是不是气缸越多就越好呢?其实不然,随着汽缸数的增加,发动机的零部件也相应的增加,发动机的结构会更为复杂,这也降低发动机的可靠性,另外也会提高发动机制造成本和后期的维护费用。所以,汽车发动机的汽缸数都是根据发动机的用途和性能要求进行综合权衡后做出的选择。像V12型发动机、W12型发动机和W16型发动机只运用于少数的高性能汽车上。 ●V型发动机结构 其实V型发动机,简单理解就是将相邻气缸以一定的角度组合在一起,从侧面看像V字型,就是V型发动机。V型发动机相对于直列发动机而言,它的高度和长度有所减少,这样可以使得发动机盖更低一些,满足空气动力学的要求。而V型发动机的气缸是成一个角度对向布置的,可以抵消一部分的震动,但是不
好的是必须要使用两个气缸盖,结构相对复杂。虽然发动机的高度减低了,但是它的宽度也相应增加,这样对于固定空间的发动机舱,安装其他装置就不容易了。 ●W型发动机结构 将V型发动机两侧的气缸再进行小角度的错开,就是W型发动机了。W型发动机相对于V型发动机,优点是曲轴可更短一些,重量也可轻化些,但是宽度也相应增大,发动机舱也会被塞得更满。缺点是W型发动机结构上被分割成两个部分,结构更为复杂,在运作时会产生很大的震动,所以只有在少数的车上应用。 ●水平对置发动机结构
热处理工艺规范(最新)
华尔泰经贸有限公司铸钢件产品热处理艺规范 随着铸造件产品种类增多,对外业务增大,方便更好的管理铸造件产品,特制定本规定,要求各部门严格按照规定执行。 1目的: 为确保铸钢产品的热处理质量,使其达到国家标准规定的力学性能指标,以满足顾客的使用要求,特制定本热处理工艺规范。 2范围 3术语 经保温一段时间后, 经保温一段时间后, 3.3淬火:指将铸钢产品加热到规定的温度范围,经保温一段时间后, 快速冷却的操作工艺。 3.4回火:指将淬火后的铸钢产品加热到规定的温度范围,经保温一 段时间后出炉,冷却到室温的操作工艺。 3.5调质:淬火+回火 4 职责
4.1热处理操作工艺由公司技术部门负责制订。 4.2热处理操作工艺由生产部门负责实施。 4.3热处理操作者负责教填写热处理记录,并将自动记录曲线转换到 热处理记录上。 4.4检验员负责热处理试样的力学性能检测工作,负责力学性能检测 结论的记录以及其它待检试样的管理。 5 工作程序 5.1 错位炉底板应将其复位后再装, 5.2 对特别 淬铸件应控制入水时间,水池应有足够水量,以保证淬火质量。 5.5作业计划应填写同炉热处理铸件产品的材质、名称、规格、数量、 时间等要素,热处理园盘记录纸可多次使用,但每处理一次都必须与热处理工艺卡上的记录曲线保持一致。 6 不合格品的处置 6.1热处理试样检验不合格,应及时通知相关部门。
6.2技术部门负责对不合格品的处置。 7 附表 7.1碳钢及低合金钢铸件正火、退火加热温度表7.2碳钢及低合金钢铸件退火工艺 7.3铸钢件直接调质工艺 7.4铸钢件经预备热处理后的调质工艺 7.5低合金铸钢件正火、回火工艺
汽轮机高压缸外缸跑偏的分析与处理
汽轮机高压外缸跑偏分析与处理措施 广东拓奇电力技术发展公司技术部周伟光 一、前言 滑销系统是在启动受热膨胀、停机冷却收缩及运行工况变化情况下,保证汽缸、轴承箱能自由滑动并保持与轴承箱、汽缸与转子的相对中心位置不变的重要部件。定中工字梁是汽轮机滑销系统的重要组成部分,其工作状况好坏直接影响到机组安全运行。 二、高压外缸跑偏的现象与原因 1、高压外缸跑偏的现象 某电厂5号600MW机组是上海汽轮机有限公司引进美国西屋公司技术生产的亚临界、一次中间再热、四缸四排汽、单轴、凝汽式汽轮机,型号N600-16.7/537/537。2008年2月广东拓奇电力技术发展有限公司承接某电厂5号汽轮机组大修项目,本次机组大修是安装该机投入商业运行以来的首次整体大修。在高压缸解体检查发现,汽轮机轴系中心不变的情况下,高压缸前轴封左右汽封间隙偏差较大:A排 1.40~2.00㎜之间炉侧 0.10~0.20㎜之间,高压外缸调端洼窝中心偏差1.10㎜的不正常现象。 高压外轴封调端A排侧汽封间隙1.40~2.00㎜之间
高压外调端轴封炉侧汽封间隙0.10~0.20㎜之间 从高压缸猫爪与高压外下缸支撑垫块有明显移动痕迹看,初步判断分析高压缸定中工字梁(调端)发生位移。 高压炉侧前猫爪位移印痕高压A排侧前猫爪位移印痕 2、高压外缸跑偏的原因 1)经初步判断分析有以下几种原因可能造成缸体跑偏: 1.1、定中工字梁螺栓松动或偏心定位销松动或材质不对; 1.2、汽缸有热变形; 1.3、与汽缸相联的管道存在应力。 2)检查结果 2.1、发现高压外缸与定中H梁偏心定位销与偏心套未点焊,用手可拔出,销子外径有手工严重打磨痕迹,销与孔配合间隙过大;缸体定中H梁螺栓垫片厚20mm;上偏心套只有11mm厚度而且未装进梁孔上,销子实际未起到作用;安装后上部偏心销也未点焊牢固的安装工艺。实际偏心套总长需55mm才能使销套完全装配到位及便于点焊。
热处理工艺规程(工艺参数)
热处理工艺规程(工艺参数) 编制: 审核: 批准: 生效日期: 受控标识处:
分发号: 目录 1.主题内容与适用范围 (1) 2.常用钢淬火、回火温度 (1) 要求综合性能的钢种 (1) 要求淬硬的钢种 (4) 要求渗碳的钢种 (6) 几点说明 (6) 3.常用钢正火、回火及退火温度 (7) 要求综合性能的钢种 (7) 其它钢种 (8) 几点说明 (8) 4.常用钢去应力温度 (10) 5.各种热处理工序加热、冷却范围 (12) 淬火………………………………………………………………………………………………1 2 正火及退火 (14) 回火、时效及去应力 (15) 工艺规范的几点说明 (16) 6.化学热处理工艺规范 (17) 氮化 (17) 渗碳 (20) 7.锻模热处理工艺规范 (22) 锻模及胎模 (22) 切边模 (24) 锻模热处理注意事项 (25) 8.有色金属热处理工艺规范 (26) 铝合金的热处理 (26) 铜及铜合金 (26)
9.几种钢锻后防白点工艺规范 (27) 第Ⅰ组钢 (27) 第Ⅱ组钢 (28) 1.主题内容与适用范围 本标准为“热处理工艺规程”(工艺参数),它主要以企业标准《金属材料技术条件》B/HJ-93年版所涉及的金属材料和技术要求为依据(不包括高温合金),并收集了我公司生产常用的工具、模具及工艺装备用的金属材料。 本标准适用于汽轮机、燃气轮机产品零件的热处理生产。 2.常用钢淬火、回火温度 要求综合性能的钢种:
注:①采用日本材料时,淬火温度为960~980℃,回火温度允许比表中温度高10~30℃。 ②有效截面小于20mm者可采用空冷。 要求淬硬的钢种(新HRC>30)
汽轮机的热应力、热变形、热膨胀分析
汽轮机的热应力、热变形、热膨胀 主要内容:主要介绍汽轮机的热应力、热膨胀和热变形;汽轮机寿命及如何进行汽轮机的寿命管理。 Ⅰ汽轮机的受热特点 一、汽缸壁的受热特点 汽轮机启停过程是运行中最复杂的工况。在启停过程中,由于温度剧烈变化,各零部件中及它们之间形成较大的温差。导致零部件产生较大的热应力,同时还引起热膨胀和热变形。当应力达到一定水平时,会使高温部件遭受损伤,最终导致部件损坏。 1.汽缸的受热特点 (1)启动时,蒸汽的热量以对流方式传给汽缸内壁,再以导热方式传向外壁,最后经保温层散向大气,汽缸内外壁存在温差,内壁温度高于外壁温度,停机过程则产生相反温差。 (2)影响内外壁温差的主要因素: ①汽缸壁厚度δ,汽缸壁越厚,内外温差越大。 ②材料的导热性能; ③蒸汽对内壁的加热强弱。 加热急剧:温度分布为双曲线型,温差大部分集中在内壁一侧,热冲击时; 加热稳定:温度分布为直线型,温差分布均匀,汽轮机稳定运行工况; 缓慢加热:温度分布为抛物线型,内壁温差较大,实际启动过程中; 2.转子的受热特点 蒸汽的热量以对流方式传给转子外表面,再以导热方式传到中心孔,通过中心孔散给周围环境,在转子外表面和中心孔产生温差,温差取决于转子的结构、材料的特性及蒸汽对转子的加热程度。 Ⅱ汽轮机的热应力 一、热应力
热应力概念:当物体温度变化时,热变形受到其它物体约束或物体内部各部分之间的相互约束所产生的应力。 ①温度变化时,物体内部各点温度均匀,变形不受约束,则物体产生热变形而没有热应力。当变形受到约束时,则在内部产生热应力。 ②物体各处温度不均匀时,即使没有外界约束条件,也将产生热应力;在温度高的一侧产生热压应力,在温度低的一侧产生热拉应力。 二、汽缸壁的热应力 1.启动时,汽缸内壁为热压应力,外壁为热拉应力,且内外壁表面的热压和热拉应力均大于沿壁厚其他各处的热应力。 内壁;t E i ??-?-=μ ασ132 外壁:t E ??-? -=μασ1310 在停机过程中,内壁表面热拉应力,外壁表面热压应力。
GB3801-83汽车发动机气缸体与气缸盖修理技术条件
GB3801-83汽车发动机气缸体与气缸盖修理技术条件 中华人民共和国国家标准GB3801-83 UDC621.431.72.222.004.124 本标准适用于国产往复活塞式汽车发动机铸铁及铝合金气缸体与气缸盖的修理。其他汽车发动机气缸体与气缸盖可参照执行。通过修理的气缸体与气缸盖应符合本标准的要求。 1技术要求 1.1气缸体与气缸盖不应有油污、积炭、水垢及杂物。 1.2水冷式气缸体与气缸盖用3.5-4.5kgf/cm2的压力作连续5min水压试验,不得渗漏。 1.3汽油发动机气缸体上平面到曲轴轴承承孔轴线的距离,不小于原设计差不多尺寸0.40mm。 注:原设计是指制造厂和按规定程序批准的技术文件(下同〉。 1.4所有结合平面不应有明显的凸出、凹陷、划痕或缺损。气缸体上平面和气缸盖下平面的平面度公差应符合表1的规定。 1.5气缸体曲轴、凸轮轴轴承承孔的同轴度公差应符合原设计规定。凡能用减磨合金补偿同轴度误差的,以气缸体两端曲轴轴承承孔公共轴线为基准,所有曲轴轴承承孔的同轴度公差为0.15mm,以气缸体两端凸轮轴轴承承孔公共轴线为基准,所有凸轮轴轴承承孔的同轴度公差为ф0.15mm。
1.6气缸体后端面对曲轴两端轴承承孔公共轴线的端面全跳动不大于0.20mm。 1.7燃烧室容积不小于原设计最小极限值的95%。同一台发动机的气缸盖燃烧室容积之差应符合原设计规定。 1.8气缸体、气缸盖各结合面经加工后的表面光洁度应不低于▽6。 1.9气缸盖上装火花塞或喷油嘴和预热塞的螺孔螺纹损害不多于一牙,气缸体与气缸盖上其他螺孔螺纹损害不多于两牙。修复后的螺孔螺纹应符合装配要求。各定位销、环孔及装配基准面的尺寸和形位公差应符合原设计规定。 1.10选用的气缸套、气门导管、气门座圈及密封件应符合相应的技术条件,并应满足本标准的有关装配要求。 1.11气门导管承孔内径应符合原设计尺寸或分级修理尺寸(见表2)。气门导管与承孔的配合过盈一样为0.02-0.06mm。 1.12进、排气门座圈承孔内径应符合原设计尺寸或修理尺寸(见表2)。气门座圈承孔的表面光洁度不低于▽5,圆度公差为0.0125mm,与座圆的配合过盈一样为0.07-0.17mm。 1.13镶装干式气缸套的承孔内径应为原设计尺寸或同一级修理尺寸(如表2)。承孔表面光洁度不低于▽6,圆柱度公差为0.0lmm。气缸套与承孔的配合过盈应符合原设计规定;无规定者,一样为0.05-0.10mm。有突缘的气缸套配合过盈可采纳0.05-0.07mm;无突缘的气缸套可采纳0.07-0.l0mm。气缸套上端面应不低于气缸体上平面,亦不得高出0.l0mm。 1.14湿式气缸套承孔的内径应为原设计尺寸或同一级修理尺寸(见表2)。湿式气缸套与承孔的配合间隙为0.05-0.15mm,安装后气缸套上端面应高出气缸体上平面,并应符合原设计规定。 1.15同一气缸体各气缸或气缸套的内径应为原设计尺寸或同一级修理尺寸(见表2),缸壁表面光洁度不低于气78。干式气缸套的气缸圆度公差为0.005mm,圆柱度公差为0.0075mm;湿式气缸套的气缸圆柱度公差为0.0125mm。
大型汽轮机汽缸膨胀不畅的分析及改进
大型汽轮机汽缸膨胀不畅的分析及改进 摘要:针对国产改进型300MW汽轮机因缸体膨胀不畅导致轴瓦冷态负荷分配不均,汽封磨损、延长暖机时间等缺陷;分析产生缸体膨胀不畅的原因;对消除滑销系统卡涩、改进推拉结构、管道与缸体的连接方式、基础台板的材质及润滑系统的改进等方面提出相应的措施 关键词:膨胀不畅滑销系统材质推拉结构一.概述 国产改进型300MW汽轮机系上海汽轮机厂生产的N300-16.5/535/535中间再热凝汽式、单轴四缸四排汽汽轮机组,其滑销系统及膨胀方向如图1所示 汽轮机高中压静止部分的死点在汽轮机纵向轴线与中
低压轴承座(#3)底部横向键中心线的交点上,高、中压静止部件以死点向前膨胀,前轴承座(#1)在高压外缸猫爪的推动下将向前移动约32mm,中轴承座(#2)在中压外缸猫爪的推动下将向前移动约17mm。 推力轴承装于中轴承座(#2)内,运行时,推力轴承带动整个轴系随中轴承座(#2)向前移动,这时高压转子以推力轴承为死点向前膨胀,中压转子以推力轴承为相对死点向与高压转子相反的方向膨胀。 在启动、运行期间,动静部分分别以各自死点为中心定向膨胀。高压缸为正差胀,中压缸启动时为正差胀,低压Ⅰ缸、低压Ⅱ缸为负差胀。 该类型机组自投产以来,均发生了高压、中压缸缸体膨胀不畅的现象,并且随着运行时间的推移、机组启停次数的增加,越来越严重,造成了各种缺陷:轴瓦冷态负荷分配不均,联轴器不能按正常中心值联结;缸体变形;启、停机过程低压缸差胀大;动静碰磨;延长暖机时间等缺陷,二.原因分析 缸体膨胀不畅既有滑销系统结构设计失误、管道与缸体连接方式不正确的原因,又与滑销系统的运行方式、检修工艺等方面有关。 1.轴承座无润滑膨胀 1)由于制造厂原设计的台板油路弯多线长,注油阻力大,
常见零件的热处理方式
一、齿轮 1.渗碳及碳氮共渗齿轮的工艺流程 毛坯成型→预备热处理→切削加工→渗碳(碳、氮共渗)、淬火及回火→(喷丸)→精加工2.感应加热和火焰加热淬火齿轮用钢及制造工艺流程 配料→锻造→正火→粗加工→精加工→感应或火焰加热淬火→回火→珩磨或直接使用调质 3.高频预热和随后的高频淬火工艺流程 锻坯→正火→粗车→高频预热→精车(内孔、端面、外圆)滚齿、剃齿→高频淬火→回火→珩齿 二、滚动轴承 1.套圈工艺流程 棒料→锻制→正火→球化退火 棒料→钢管退火磨→补加回火→精磨→成品 2.滚动体工艺流程 (1)冷冲及半热冲钢球 钢丝或条钢退火→冷冲或半热冲→低温退火→锉削加工→软磨→淬火→冷处理→低温回火→粗磨→补加回火→精磨→成品 (2)热冲及模锻钢球 棒料→热冲或模锻→球化退火→锉削加工→软磨→淬火→冷处理→低温回火→粗磨→补加回火→精磨→成品 (3)滚子滚针 钢丝或条钢(退火)→冷冲、冷轧或车削→淬火→冷处理→低温回火→粗磨→附加回火→精磨→成品 三、弹簧 1.板簧的工艺流程
切割→弯制主片卷耳→加热→弯曲→余热淬火→回火→喷丸→检查→装配→试验验收 2.热卷螺旋弹簧工艺流程 下料→锻尖→加热→卷簧及校正→淬火→回火→喷丸→磨端面→试验验收 3.冷卷螺旋弹簧工艺流程 下料→锻尖→加热→卷簧及校正→去应力回火→淬火→回火→喷丸→磨端面→试验验收 四、汽车、拖拉机零件的热处理 1.铸铁活塞环的工艺流程 (1)单体铸造→机加工→消除应力退火→半精加工→表面处理→精加工→成品 (2)简体铸造→机加工→热定型→内外圆加工→表面处理→精加工→成品 2.活塞销的工艺流程 棒料→粗车外圆→渗碳→钻内孔→淬火、回火→精加工→成品 棒料→退火→冷挤压→渗碳→淬火、回火→精加工→成品 热轧管→粗车外圆→渗碳→淬火、回火→精加工→成品 冷拔管→下料→渗碳→淬火、回火→精加工→成品 3.连杆的工艺流程 锻造→调质→酸洗→硬度和表面检验→探伤→校正→精压→机加工→成品 4.渗碳钢气门挺杆的工艺流程 棒料→热镦→机加工成型→渗碳→淬火、回火→精加工→磷化→成品 5.合金铸铁气门挺杆的工艺流程 合金铸铁整体铸造(间接端部冷激)→机械加工→淬火、回火→精加工→表面处理→成品合金铸铁整体铸造(端部冷激)→机械加工→消除应力退火→精加工→表面处理→成品钢制杆体→堆焊端部(冷激)→回火→精加工→成品 钢制杆体→对焊→热处理→精加工→表面处理→成品 6.马氏体型耐热钢排气阀的工艺流程 马氏体耐热钢棒料→锻造成型→调质→校直→机加工→尾部淬火→抛光→成品 7.半马氏体半奥氏体型耐热钢(Gr13Ni7Si2)排气阀的工艺流程
汽轮机膨胀不畅的原因汽轮机膨胀不畅的原因及一次中间再热、两缸两排汽机型滑参数停机
汽轮机膨胀不畅的原因汽轮机膨胀不畅的原因魏欣 摘要:根据汽轮机的结构和运行状况,分析汽轮机膨胀不畅的原因,并采取有效的措施进行改造。 关键词:汽轮机;膨胀不畅;诊断分析;处理方法 我厂N220-130/535/535型三缸三排汽凝汽式汽轮机配有五个轴承箱,其中1, 2号轴承箱座落在独立的机架上,3,4,5号轴承箱分别座落在三个排汽缸扩压管洼窝中。高压缸和中压缸前部通过猫爪搭座在1、2号轴承箱上,当高、中压缸膨胀或收缩时,1、2号轴承箱能在汽缸的推动下在机架的滑块上自由滑动(见图1),确保汽缸正常膨胀。2003年大修后,机组启动时出现中压缸膨胀不畅的问题,致使冷态启动时间延长,耗费了大量的锅炉燃油,造成巨大的经济损失,严重影响机组安全稳定生产。 一、原因分析 中压缸前部座落在2号轴承箱上,中压缸膨胀不畅最终是因2号轴承箱在机架的滑块上滑动受阻所至。分析汽轮机的结构知,为保证汽轮机高速运行时转子中心和汽缸中心保持一致,在汽缸的轴承座与基础台板之间装有滑销系统(见图2)。在机组启动过程中,汽缸与轴承座在滑销系统的引导下按一定的方向进行膨胀,使汽缸与轴承座在热状态下仍然保持中心一致。若滑销系统工作失常,会引起汽缸热膨胀不良,从而引起机组不能正常运行。由此得出2号轴承箱滑动受阻是由于底部滑销系统工作失常所致。 2号轴承箱与机架滑块间的相对滑动以润滑脂润滑,润滑脂被注到滑块上的润滑脂槽道内。这种设计形式导致2号轴承箱在运行中容易出现如下弊端。 1.轴承箱与滑块间润滑不良。润滑脂槽道面积相对于整个滑块滑动面较小,
不到滑动面的1/5,不能有效地润滑整个滑块表面(见图3)。 2.轴承箱与滑块间形成油泥。轴承箱与滑块接触处封闭不好,易使润滑脂形成油泥,影响轴承箱滑动。 3.轴封漏气进人轴承箱与滑块的接触面。2号轴承箱工作环境较差,位于高压进汽侧轴封和中压进汽侧轴封间,轴封漏汽容易进入机架与轴承箱底部之间的间隙内,造成机架、机架上滑块及机架与轴承箱间纵向键锈蚀、卡涩,并加剧了油泥的形成,导致轴承箱滑动受阻,引起机组膨胀不畅。 4.润滑脂高温碳化。2号轴承箱所处位置温度较高,润滑脂易出现高温碳化,增加了滑动阻力,也会引起机组膨胀不畅。 因此,中压缸膨胀不畅问题可通过改造轴承箱下部机架上的滑块得到解决。 二、处理方法 根据分析,决定将1、2号轴承箱下部滑块改为自润滑滑块。 改造前,先对滑块与机架、滑块与轴承箱底部进行对研,检查确认接触面积大于70%,再进行滑块自润滑改造。改造时在滑块上钻上按一定规则均匀排列的孔,在每个孔内镶石墨柱,再用石墨条将润滑脂槽填满,最后将石墨柱铲平并在整个滑块面刷上石墨层,增大润滑面积,保证润滑效果。同时,为了避免轴封漏气和杂质进人滑动面,此次检修还在轴承箱下部前后两端加装了遮板。 三、效果 滑块改造后,2#机组启动时汽缸膨胀良好,从开始进汽到中压缸膨胀达到5mm 仅用了6h,冲转时2#轴瓦温度低于80℃,问题彻底解决,节约了启动费用。 东方汽轮机厂制造的300 MW亚临界凝汽式汽轮机,型号为N300-16.7/537/537.4,一次中间再热、两缸两排汽机型滑参数停机 1主要结构 汽轮机高中压缸合缸,为双层缸结构,设有高压缸预暖系统和汽缸夹层加热系统。投入汽缸加热系统时,从外下缸左右两侧通过加热进汽管口送入加热蒸汽,然后经1段抽汽口进入3号高压加热器。高压内缸相
热处理综合实验方案
汽车变速箱齿轮固体渗碳工艺设计的实验方案 (2) 1 变速箱齿轮的材料选择 (2) 1.1 汽车变速齿轮的服役条件 (2) 1.2 汽车变速齿轮常见的失效形式 (2) 1.3 汽车变速齿轮的性能要求 (2) 1.4 汽车变速齿轮的材料的选择 (3) 2 渗碳工艺的确定 (4) 2.2 渗碳温度 (4) 2.3 渗碳保温时间 (5) 2.4 渗碳过程 (5) 2.5 渗碳后的淬火、回火处理 (6) 3 渗碳热处理后的检测 (6)
汽车变速箱齿轮固体渗碳工艺设计的实验方案 1 变速箱齿轮的材料选择 1.1 汽车变速齿轮的服役条件 齿轮是机械工业中应用最广泛的重要零件之一。其主要作用是传递动力,改变运动速度和方向。其服役条件如下: 1)齿轮工作时,通过齿面的接触来传递动力。两齿轮在相对运动过程中,既有滚动,又有滑动。因此,齿轮表面受到很大的接触疲劳应力和摩擦力的作用。在齿根部位受到很大的弯曲应力作用; 2)在运转过程中的过载产生振动,承受一定的冲击力或过载; 3)变速齿轮在换档时,端部受冲击,承受一定冲击力; 4)在一些特殊环境下,受介质环境的影响而承受其它特殊的力的作用。 1.2 汽车变速齿轮常见的失效形式 根据其服役条件,常见的失效形式为: 1)疲劳断裂:齿轮在交变应力和摩擦力的长期作用下,导致齿轮点面接疲劳断裂。其产生是由于当齿轮受到弯曲应力超过其持久极限就出现疲劳破坏而超过材料抗弯强度时,就造成断裂失效; 2)表面损伤 a 点蚀:是闭式齿轮传动中最常见的损坏形式,点蚀进一步发展,表现为蚀坑至断裂 b 硬化层剥落:由于硬化层以下的过渡区金属在高接触应力作用下产生塑性变形,使表 面压应力降低,形成裂纹造成碳化层剥落; 3)磨损失效 a摩擦磨损:汽车、拖拉机上变速齿轮属于主载荷齿轮,受力比较大,摩擦产生热量较大,齿面因软化而造成塑性变形,在齿轮运转时粘结而后又被撕裂,造成齿面摩擦磨损失效。 b 磨粒磨损:外来质点进入相互啮合的齿面间,使齿面产生机械擦伤和磨损,比正常磨 损的速度来得更快。另外,齿轮除上述失效形式外,还有在换档时,齿端相互撞击,而造成的齿端磨损,或因换档过猛或过载造成断裂以及齿面塑性变形,崩角等失效形式。 1.3 汽车变速齿轮的性能要求 根据变速齿轮服役条件及失效形式,对齿轮的性能作如下要求: 1 ) 有较高的弯曲疲劳强度;
汽车的排量指的是发动机所有汽缸的容量之和
汽车的排量指的是发动机所有汽缸的容量之和。比如说,某汽车发动机有4个汽缸,每个汽缸的容量是0.5L,那么该发动机的排量就是0.5L*4=2.0L。又或者是某汽车发动机有6个汽缸,每个汽缸容量0.6L,那么该发动机排量为0.6L*6=3.6L。 我们经常看到的车的发动机排量大概有以下几款:0.8 1.1 1.3 1.4 1.5 1.6 1.7 1.8 2.0 2.3 2.4 2.5 2.7 2.8 3.0 3.5 4.0 4.2 4.5 5.0 6.0等等。 一般来说,小轿车发动机单个汽缸的容量大概是0.5L左右,换句话说,一般1.6-2.0的发动机有4个汽缸,3.0左右的就有6个汽缸,4.0左右的就有8个汽缸,而5.0就有10汽缸,6.0就有12汽缸(但并非一定)。 理论上,发动机排量越大,功率和扭距都会越大。但也不一定,关键是看生产厂商对发动机的调校。比如说,在一些高性能跑车身上,它需要功率大的发动机,功率大就是说它能跑得快,所以车厂会把发动机调校得功率很大,而扭距则会有所损失。而如果是越野车,它不需要跑得多快,而是需要有很大的力(扭距)来牵引车子,所以车厂会把发动机调校得扭距很大,但会损失一些功率。举个例子说,某款发动机排量是4.0L,用在高性能跑车身上,他的功率有350KW,扭距为300NM,但如果用在越野车上,他可能会被调校成功率为280KW,而扭距变成450NM。 汽车排量的大小关系到车的加速性能以及极速。也关系到车的油耗问题。
一般来说,同一种车,排量越大,油耗就越大。但事实上不是一定成正比的。关键是要搭载合理。比如说某车,最合理的是搭载2.0的发动机,那么你搭载1.6的发动机,则会比2.0的耗油,搭载3.0的也会比2.0的耗油。 发动机的汽缸排列大概有以下几种,直列,水平对置,V型,W型等 直列是比较简单的构造,成本较低,体积较小,一般用在普通轿车上。V6比较复杂些,V8以上的构造就非常复杂了,成本非常高,一般用在高级车上。W12一般大概可以看做是2具V6结合起来,构造也很复杂!至于水平对置只有斯巴鲁和保时捷才有。还有一种更为复杂的就是转子发动机,目前全世界只有马自达有在研究和生产,并且只有马自达的RX-8有装载转子引擎,1.3的排量,而功率和扭距则达到普通3.0发动机的水平,0-100KM/H的加速时间6秒左右!
国产300MW汽轮机高、中压缸膨胀不畅的原因分析及处理,经营管理者.doc
国产300MW汽轮机高、中压缸膨胀不畅的原因分析及处理,经营管理者, 《经营管理者》 国产300MW汽轮机高、中压缸膨胀不畅的原因分析及处理 广东粤电集团韶关发电厂张泉 摘要:本文对国产300MW汽轮机组膨胀对轴承座和滑销系统的要求进行了阐述,针对国产N300-167(170)/537/537-4型汽轮机因缸体膨胀不畅而导致运行中瓦温过高,汽封出现磨损,汽缸产生变形、裂纹,暖机时间延长等问题,分析了产生缸体膨胀不畅的种种原因,并提出了消除滑销系统卡涩,改造前箱座底部基础台板润滑面等相应的技术措施。通过这些技术改进解决国产300MW汽轮机的膨胀不畅问题,使汽缸膨胀达到设计要求,进而保障机组正常运行的目的。 关键词:前箱座;汽缸膨胀不畅;滑销系统;石墨;润滑 1引言 韶关发电厂#10机组为东方汽轮机厂生产的亚临界、中间再热、高中压合缸、双缸双排汽、单轴凝汽式汽轮机,型号为N300-16.7/537/537-4型(合缸)。该机组承座底部滑动面采用在前箱座底部或台板上开润滑油槽,运行中定期加注润滑油脂来
改善膨胀性能,使前箱座在基础台板上顺利滑动。滑销系统的正常膨胀是保证汽机安全运行的重要条件之一,任何滑销系统的损坏、卡涩都可能引起机组中心偏斜、前箱箱负荷过重、摩擦阻力过大,机组因膨胀不畅而引起启停时间过长及振动超标,轴瓦温度偏高等问题,甚至造成动、静部分碰磨、前箱合金烧坏、机组跳闸以及缸体出现变形、裂纹等事故,大大降低了机组运行的安全系数、可靠性,使机组达不到设计出力、不能适应电网调峰的要求等。因而解决这一问题,对保证机组安全运行,提高机组运行经济性至关重要。 2汽轮机组存在的问题 韶关发电厂#10机在投运初期,高、中压缸膨胀基本正常,能够达到制造厂的设计要求,但随着机组服役年限的增长,启、停次数的增加,高、中压缸缸体膨胀不畅的现象逐渐明显,且越来越严重。主要表现在以下几方面: (1)暖机时间延长; (2)启、停机过程低压缸差胀大; (3)轴瓦冷态负荷分配不均; (4)高、中压缸缸体有变形; (5)动、静碰磨,汽封齿有磨损; (6)高中压缸膨胀值明显减小。. 3机组膨胀不畅的原因分析 3.1前箱座无润滑膨胀 (1)基础台板设计的不合理,使前箱座下部与基础台板间滑动不畅; (2)注油周期过长,造成局部干性磨擦; (3)台板底部油槽被杂物堵塞,无法正常注油,导致出现
热处理工艺规程(工艺参数)
热处理工艺规程 B/Z61.012-95 (工艺参数) 热处理工艺规程(工艺参数) 1.主题内容与适用范围 本标准为“热处理工艺规程”(工艺参数),它主要以企业标准《金属材料技术条件》B/HJ-93年版所涉及的金属材料和技术要求为依据(不包括高温合金),并收集了我公司生产常用的工具、模具及工艺装备用的金属材料。 本标准适用于汽轮机、燃气轮机产品零件的热处理生产。 2.常用钢淬火、回火温度 2.1 要求综合性能的钢种: 表1
注:①采用日本材料时,淬火温度为960~980℃,回火温度允许比表中温度高10~30℃。 ②有效截面小于20mm者可采用空冷。
2.2要求淬硬的钢种(新HRC>30) 表2
注:①回火后油冷。 ②淬火加热时要加以保护,以防脱碳。 ③回火脆性区为500~510℃,严禁采用。 ④回火脆性区为470~530℃,严禁采用。 2.3 要求渗碳淬硬的钢种 表3
2.4几点说明: ⑴表1~3中提供的淬火、回火温度范围,是供生产时按具体情况选定参数用的,不是某一炉允许的温度偏差。 ⑵凡水冷的钢种(奥氏体钢除外)均应及时回火以防开裂。 ⑶表1中的σs数值为σ0.2的数值。 ⑷45、35CrMoA、40CrNiMoA为保证取样部位合格,毛坯送检硬度允许适当提高。 ⑸对感应加热,快速加热的零件淬火温度允许适当提高。 ⑹表中标有*者生产上尚未用过或较少用过,其参数不够成熟,尚待生产中进一步验证,生产中允许在验证基 础上进行修改。 ⑺表1~3中冷却为水→油者,允许用水→空→水代替,具体方法为:水冷一段时间后将零件提起空中(让零 件反热后)再入水继续冷却。 3.常用钢正火、回火及退火温度 3.1要求综合性能的钢种 表4
汽缸膨胀不畅的原因及处理
汽缸膨胀不畅的原因及处理 李勇鸿齐晔 (海勃湾发电厂) 摘要:通过分析机组运行与启停机参数的变化,查找汽轮机汽缸膨胀不畅的原因,采取防范措施。 关键词:汽轮机;膨胀不畅 1现象 海勃湾发电厂两台200MW机组是东方汽轮机厂生产的机组,于2003年元月投产。2004年11月3日#4机(200MW)机组在机组温态启动过程中曾出现过高压汽缸膨胀不畅的现象。当时机组参数:负荷20MW,主汽压力:2.5MPa,主汽温度310/312℃,再汽压力0.5MPa,再汽温度308/309℃,高压汽缸膨胀值10.8mm,中压汽缸膨胀值4.96mm,高缸胀差1.87mm,中缸胀差0.69mm。暖机结束后,继续升温升压带负荷,负荷26MW,主汽压力:2.9MPa,主汽温度328/3329℃,再汽压力0.6MPa,再汽温度325/3327℃,高压汽缸膨胀值10.9mm,中压汽缸膨胀值4.97mm,高缸胀差2.2mm,中缸胀差0.93mm。发现汽缸膨胀值几乎不增加,立即停止升温升压带负荷,热工检查表计指示正常,经过45分钟暖机后,高压汽缸膨胀值突增至11.85mm,中压汽缸膨胀值突增至5.24mm,检查机组各部正常,继续升温升压带负荷至额定,高压汽缸膨胀值均匀增至29.3mm,中压汽缸膨胀值14.75mm,恢复至停机前参数。这样现象在2005年4月7日#4机又曾出现过一次。 2原因分析: 2.1启动参数异常 通过DCS工程师查阅机组启动的暖管、冲车、并网、暖机、带负荷等参数完全符合规程及厂家规定,且与2003年试运结束后多次起机的启机参数相同,因此可以排除启动参数异常的原因。2.2值班员调整不当 汽机、锅炉、电气值班员严格执行规程,且有专业人士现场监护,升负荷、主汽压力主汽温度、再汽压力、再汽温度纪录曲线可以检查出操作水平,可以排除人为原因。 2.3汽缸膨胀和收缩受阻 本机组设计的汽缸死点在低压缸前部横销与纵销连线的交点,机组在运行中受热后,高、中压缸及低压缸前半部分以此为起点向前膨胀,低压缸后半部分向后膨胀;前轴承座和后轴承座分别在高中压缸和低压缸的推力作用下,在台板的滑动面上前后滑动。轴承座底部采用润滑块进行润滑,轴承座因锈蚀或灰尘等原因造成滑销系统均存在一定程度上的卡涩现象,导致汽缸膨胀和收缩受阻,具体有两方面: 266
发动机气缸布置形式
发动机气缸布臵类型 目前来说,汽缸分为直列L型、v型、水平对臵B、和新出现的W型。 直列汽缸 也有人称之为并列汽缸,一般为4缸或6缸。 其优点在于:稳定,成本低,结构简单,运转平衡性好,体积小。 但缺点是:当排气量和汽缸数增加时,发动机的长度将大大增加。(也就是说,如果我们制造了一个直列12缸的发动机的话,那个发动机将会有汽车的一小半那么大:) 4缸直列发动机,一般广泛运用于2.2升排量以下的发动机中。例如,(普)桑塔纳、捷达等等。 6缸直列发动机,最著名的例子就是BMW的M3,BMW选用6缸直列发动机的主要目的是为了方便配重,和稳定性。可见,直列发动机虽然比较简单,但绝对不是不好的。 V型发动机 我们常见的V型发动机有V6、V8、V10、V12其实不光这些,V型发动机,还有V3、V5以及V16。顾名思义,V代表发动机气缸成V型排列,一般是90度,因为这样以最好的抵消运转时的震动,更加稳定。当然,也有75度和72度的。上赛季的雷诺赛车甚至用了超过90度的广角V10 引擎。 V兴引擎的优点在于:运转稳定(针对V6、V8、V12)、节省空间。缺点在于:结构比较复杂,不利于保养和维修,并且造价较高。同时,V3、V5包括V10都由于其结构或排量的原因,并不非常稳定,尤其是作为F1发动机的V10 3L 引擎,更是需要投入大量的精力和经费用于保证其稳定性。 代表车型太多了,奥迪的A6、法拉利360、F1赛车和保时捷carrear GT、奔驰S600。分别使用V6,V8,V10,V12发动机。而V3主要是出现在一些摩托车上,V5据说在上一代大众高尔夫上有使用。而V16则在一些豪华的老爷车上可以找到。 水平对臵发动机B 说白了,这也是V型发动机,只不过V的夹角变成了180度了:)一般为4缸或6缸。 优点:重心低(废话,都180度了,还能有比它更低的吗)易与操控、平衡性非常的好。 缺点:还是造价高,发动机太宽。 水平对臵发动机最出名的运用在于保时捷著名的911上。 目前市面上只有日本的斯巴鲁,以及德国的保时捷在采用水平对臵发动机。
26 高低压联合转子材料及热处理工艺研究_金嘉瑜
试验研究 高低压联合转子材料及热处理工艺研究 金嘉瑜 (中国第一重型机械集团公司冶金研究所,黑龙江161042) 荆天辅 (燕山大学材料科学与工程学院,河北066004) 摘 要 根据高低压联合转子使用特性和技术要求,设计了相应的2.5%C r N i M oV钢转子材料,并进行了相关的物理和工艺参数试验,对试验结果进行了对比和讨论,认为该材料适用于生产高低压联合转子。 关键词 高低压转子 2.5%C r N i M oV钢 热处理 T he P rocess R esearch fo r of T he H P&L P Jo in t Ro to r M aterial and T he H eat T reatm en t J i n J i ayu J i ng T i anfu Abstract A cco rding to the characteristic and the technical specificati on of the H P&L P j o int ro to rs, the m aterial2.5%C r N i M oV fo r ro to rs has been developed,and relative m echanical and p rocess param eter tests have been perfo r m ed as w ell.T h is paper describes and contrast w ith the test results,w h ich confir m s that th is m aterial is suitable to the m anufacturing of the H P&L P ro to rs. Key W ords H P&L P Ro to r,2.5%C r N i M oV Steel,H eat T reatm ent. 1 前言 大容量汽轮机通常有高压、低压两根或两根以上的转子锻件。汽轮机组不同温度区段的汽缸中的转子锻件使用不同的材料制造。高、中压转子一般偏重考虑高温蠕变和持久强度,转子材料应该具有足够的强度、塑性和韧性,同时还应该有好的抗高温蠕变,持久强度和抗低周疲劳性能,所以都采用具有好的高温性能和淬透性的C r2M o2V合金钢。低压转子一般在350℃以下工作,但由于考虑到设计结构的要求和最后几级叶片的作用,因此低压转子一般重量重、直径大;要求制作低压转子的材料应具有很好的大截面淬透性,有高的强度和韧性的综合性能以及低的断口形貌转变温度和高的断裂韧性等。所以一般选用淬透性好的N i C r M oV钢作低压转子。 近年来,由于能源紧张等问题的日益突出,人们对大型火电发电设备的节能性提出了越来越高的要求。从节约能源、燃料的多样化、运转控制的多样化以及单机容量的大型化的观点来看,高低压联合转子构成的发电机组具有起动快、控制性能好、经济、使用寿命高的特点。因此,高低压联合转子的开发与使用便具有了重要的意义。 从80年代初起,美国、德国、英国和日本等国家就着手研究并制造了新型的高、低压一体化新型转子,使同一支转子分别兼具有高压转子和低压转子的性能[1]。目前国内尚没有开发出这种转子材料,所用转子完全依靠进口。为了满足开发新产品和拓宽市场的需要,我厂开始了高低压联合转子材料和工艺的研究。 大型铸锻件
发动机的汽缸布置与振动
发动机的汽缸布置与振动 自从活塞式内燃机出现以来,100多年过去了。虽然发动机的性能有了很大的提高,但一些问题可是生下来就有的,也就是人们常说的原理上的缺陷,到现在都有没能解决。 活塞式内燃机是通过燃料燃烧从而推动活塞进行直线往复运动,活塞再通过连杆和曲柄将活塞的直线运动转变成曲轴的旋转动动。这样一来,由于活塞与连杆,连杆与曲柄之间的磨擦必然造成能量的损失,而连杆和活塞的往复运动也会带来振动。 为了克服活塞发动机的问题,人们设计了很多的旋转式发动机,如汪克尔转子发动机,燃气轮机等。但汪克尔发动机低速性能差,密封困难,原来日本的松田公司(马自达)搞过一阵,后来放弃了,到现在都没几个人用,燃气轮机重量轻,振动很小,但功率太大,成本高,耗油量也大,大多用于航空和航海,在车辆上只有美国的M1和前苏联的T-80坦克使用。所以在汽车上还得使用活塞式发动机。 既然没办法完全解决活塞发动机的的振动等问题问题,那只能减小它,或者通过合适的结构将它的影响相互抵消。 要解决活塞发动机的振动,首先得算出振动的力的大小,这首先要对活塞、连杆、曲柄的加速度进计算,当算出加速度后,再乘以它们的重量,那么力也就算出来了。 活塞的重量很容易得到,用个天平称一下就知道了。曲柄的重量也不难。连杆就有点麻烦了,它的小头和活塞一起做直线往复运动,而大头则和曲柄一起做圆周运动,所以可以把它用两个重量代替,一个重量随活塞做直线运动,另一个随曲柄做圆周运动。当然这两个重量可不能乱用,它要满足什么重量条件、重心条件,还有旋转惯量条件等,而实际上旋转惯量条件是无法满足的,那么用两个重量代替就一定有误差,不过这个误差不大,在工程上可以接受。 曲柄做的是圆周运动,它的加速度很好计算,而活塞的加速度就要麻烦一些,计算的结果有三角函数,还要平方再开平方。为了方便分析,人们把它分解成一系列振动再加起来,其中有的和曲柄的运动一样快,称为一阶加速度,有的是曲柄运动的两倍,称为二阶加速度,还有三阶、四阶等。在实际中,由于二阶以上的加速度很小,在设计和计算中可以不考虑。 有了重量和加速度就可计算中心发动机的振动的力了,其中曲柄转动的产生的力叫旋转惯性力,而随活塞运动产生的力叫往复惯性力。往复惯性力又有一阶惯性力,二阶惯性力等。这些惯性力都随着发动机的转速的增加而增大,并与运动件,如活塞、连杆等的重量成正比。 这些力的计算不算太复杂,但是要设计一个好的发动机还得靠我们
发动机气缸体
发动机气缸体 1 专用工具 参考号 工具号码 说明 数量○107PAF-0010400 活塞座盖 1 ○207PAF-0010500 导向座盖附件 1 ○307PAF-0010700 插销 1 ○407ZAD-PNA0100 油封拆装器附件,96 mm 1 ○5070AF-PWC0110 导向销 1 ○6070AF-PWC0120 嵌入调节器 1 ○7070AF-PWC0130 导向环,外径18 mm 1 ○807749-0010000 拆装器手柄,15 x 135L 1 ○907946-1870100 轴承拆装器附件,28 x 30 mm 1 ○1007973-6570500 活塞座 1 ○1107973-6570600 活塞座弹簧 1
2 部件位置 2.1 L15A7发动机
2.2 L13Z1发动机
3 连杆和曲轴轴向间隙检查 1).拆下机油泵。 2).用间隙规测量连杆和曲轴之间的连杆轴向间隙。 连杆轴向间隙 标准(新):0.15–0.35 mm (0.006–0.014 in.) 维修极限: 0.40 mm (0.016 in.) 3).如果连杆轴向间隙超出维修极限,则安装新的连杆并重新检查。如果仍然 超出维修极限,则更换曲轴。 4).将曲轴完全推离百分表,使百分表顶住曲轴端部并调零。然后将曲轴完全拉向百分表,百分表的读数不能超出维修极限。 曲轴轴向间隙 标准(新):0.10–0.35 mm (0.004–0.014 in.) 维修极限: 0.45 mm (0.018 in.) 5).如果轴向间隙超出维修极限,则更换止推垫圈并重新检查,如果仍然超出 维修极限,则更换曲轴。
钢 的热处理工艺
钢的热处理工艺 钢的热处理工艺就是通过加热、保温和冷却的方法改变钢的组织结构以获得工件所要求性能的一种热加工工艺。钢在加热和冷却工程中的组织转变规律为制定正确的热处理工艺提供了理论依据,为使钢获得限定的性能要求,其热处理工艺参数的确定必须使具体工件满足钢的组织转变规律性。 根据加热、冷却方式及获得的组织的性能的不同,钢的热处理工艺可分为普通热处理(退火、正火、淬火和回火)、表面热处理(表面淬火和化学热处理)及形变热处理等。 按照处理在零件整个工艺过程中位置和作用的不同,热处理工艺又分为预备热处理和最终热处理。 钢的退火与正火 退火和正火是生产上应用很广泛的预备热处理工艺。在机器零件加工工艺过程中,退火和正火是一种先行工艺。具有承上启下的作用。大部分机器零件及工、模具的毛坯经退火或正火后,不仅可以消除铸件、锻件及焊接件的内应力及成分和组织的不均匀性,而且也能改善和调整钢的机械性能和工艺性能,为下道工序作好组织性能准备。对于一些受力不大、性能要求不高的机器零件,退火和正火亦可作为最终热处理。对于铸件,退火和正火通常就是最终热处理。 一、退火目的及工艺 退火是将钢加热至临界点Ac1以上或以下温度,保温以后随炉缓慢冷却以获得近似于平衡状态组织的热处理工艺。其主要目的是均匀钢的化学成分及组织,细化晶粒,调整硬度,消除能应力和加工硬化,改善钢的成形及切削加工性能,并为淬火作好组织准备。 退火工艺种类很多,按加热温度可分为在临界温度(Ac1或Ac3)以上或以下的退火。前者又称相变结晶退火,包括完全退火、扩散退火、不完全退火和球化退火。后者包括再结晶退火及去应力退火。各种退火方法的加热温度范围如图10-1所示。按照冷却方式,退火可分为等温退火和连续冷却退火。 (一)完全退火 完全退火是将钢件或刚才加热至Ac3以上20~30℃,经完全奥氏体化后进行缓慢冷却,以获得近于平衡组织的热处理工艺。它主要用于亚共析钢(wc=0.3~0.6%),其目的是细化晶粒、均匀组织、消除内应力、降低硬度和改善钢的切削加工性。低碳钢和过共析钢不宜采用完全退火。低碳钢完全退火后硬度偏低,不利于切削加工。过共析钢加热至ACcm 以上奥氏体状态缓冷退火时,有网状二次渗碳体析出,使钢的强度、塑性和冲击韧性显著降低。 在中碳结构铸件、锻件中,常见的缺陷组织有魏氏组织、晶粒粗大和带状组织等。在焊接工件焊缝处的组织也不均匀,热影响区具有过热组织和魏氏组织,造成很大的内应力。魏氏组织和晶粒粗大能显著降低钢的塑性和冲击韧性。而带状组织使钢的机械性能出现各向异性,断面收缩率较低,尤其是横向冲击韧性很低。通过完全退火或正火,组织发生重结晶,使钢的晶粒细化、组织均匀,魏氏组织难以形成,并能消除带状组织。 完全退火采用随炉缓冷可以保证先共析铁素体的析出和过冷奥氏体在Ar1以下较高温度范围内转变为珠光体,从而达到消除内应力、降低硬度和改善切削加工性的目的。 工件在退火温度下的保温时间不仅要使工件烧透,即工件心部达到要求的加热温度,而要保证全部得到均匀化的奥氏体,达到完全重结晶。完全退火保温时间与钢材成分、工件厚度、装炉量和装炉方式等因素有关。通常,加热时间以工件的有效厚度来计算。 一般碳素钢或低合金钢工件,当装炉量不大时,在箱式炉中退火的保温时间可按下式计算:τ=(3~4)+(0.2~0.5)Q(单位为h)。式中Q表示装炉量(单位为t)。 实际生产时,为了提高生产率,退火冷却至600℃左右即可出炉空冷。