超声深滚对30CrMnSiNi2疲劳性能的影响
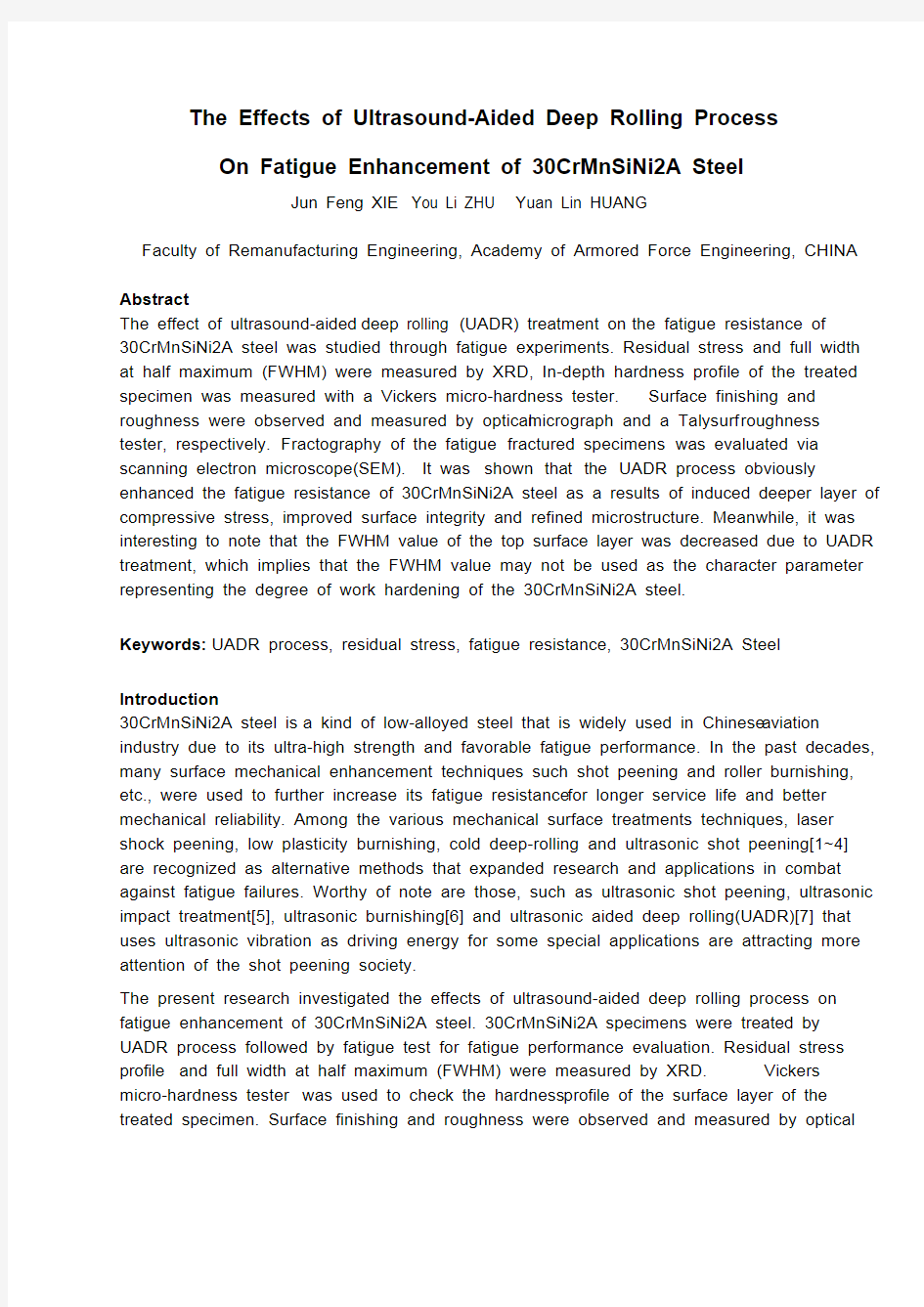
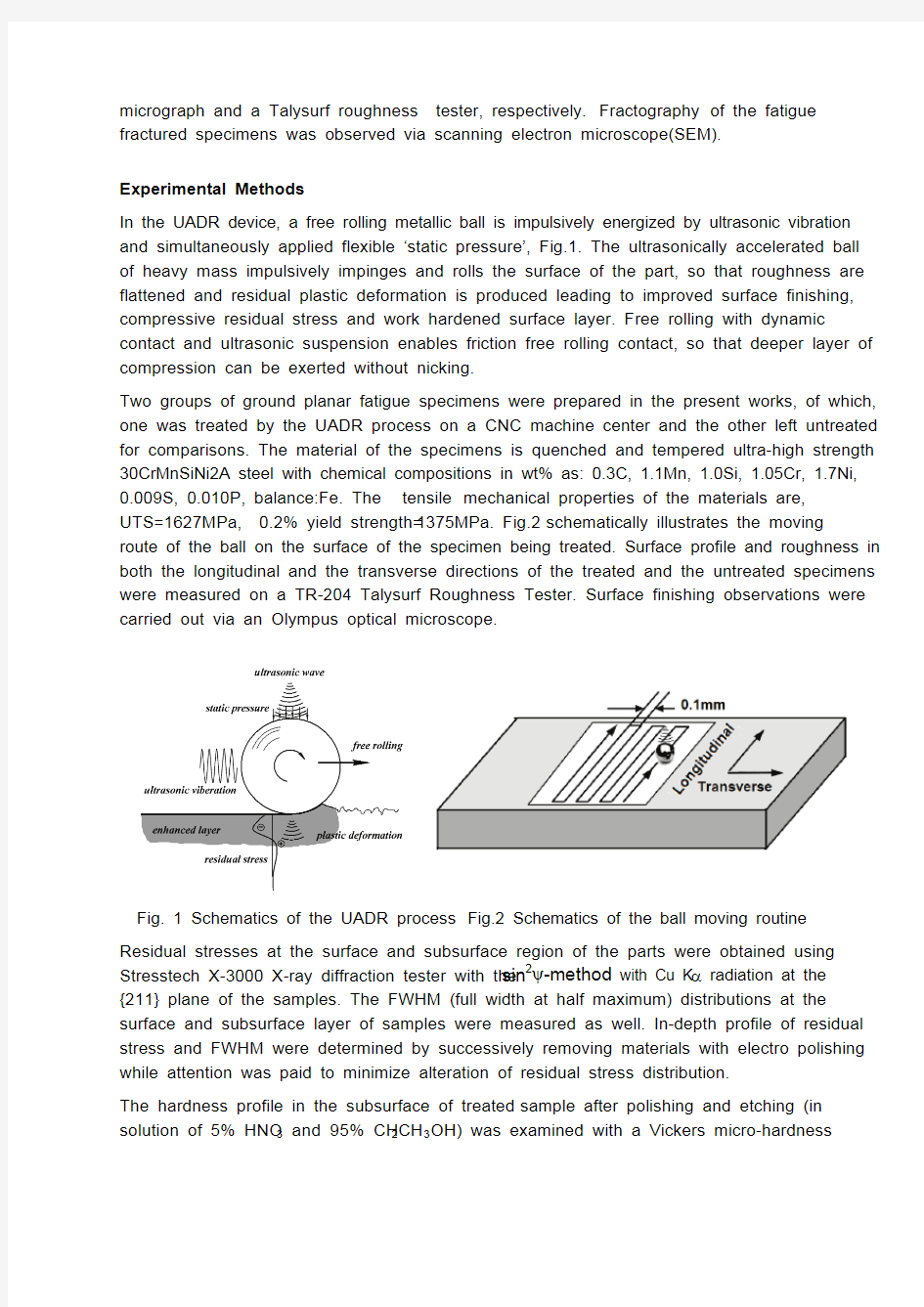
The Effects of Ultrasound-Aided Deep Rolling Process On Fatigue Enhancement of 30CrMnSiNi2A Steel
Jun Feng XIE You Li ZHU Yuan Lin HUANG
Faculty of Remanufacturing Engineering, Academy of Armored Force Engineering, CHINA Abstract
The effect of ultrasound-aided deep rolling (UADR) treatment on the fatigue resistance of 30CrMnSiNi2A steel was studied through fatigue experiments. Residual stress and full width at half maximum (FWHM) were measured by XRD, In-depth hardness profile of the treated specimen was measured with a Vickers micro-hardness tester. Surface finishing and roughness were observed and measured by optical micrograph and a Talysurf roughness tester, respectively. Fractography of the fatigue fractured specimens was evaluated via scanning electron microscope(SEM). It was shown that the UADR process obviously enhanced the fatigue resistance of 30CrMnSiNi2A steel as a results of induced deeper layer of compressive stress, improved surface integrity and refined microstructure. Meanwhile, it was interesting to note that the FWHM value of the top surface layer was decreased due to UADR treatment, which implies that the FWHM value may not be used as the character parameter representing the degree of work hardening of the 30CrMnSiNi2A steel.
Keywords: UADR process, residual stress, fatigue resistance, 30CrMnSiNi2A Steel Introduction
30CrMnSiNi2A steel is a kind of low-alloyed steel that is widely used in Chinese aviation industry due to its ultra-high strength and favorable fatigue performance. In the past decades, many surface mechanical enhancement techniques such shot peening and roller burnishing, etc., were used to further increase its fatigue resistance for longer service life and better mechanical reliability. Among the various mechanical surface treatments techniques, laser shock peening, low plasticity burnishing, cold deep-rolling and ultrasonic shot peening[1~4] are recognized as alternative methods that expanded research and applications in combat against fatigue failures. Worthy of note are those, such as ultrasonic shot peening, ultrasonic impact treatment[5], ultrasonic burnishing[6] and ultrasonic aided deep rolling(UADR)[7] that uses ultrasonic vibration as driving energy for some special applications are attracting more attention of the shot peening society.
The present research investigated the effects of ultrasound-aided deep rolling process on fatigue enhancement of 30CrMnSiNi2A steel. 30CrMnSiNi2A specimens were treated by UADR process followed by fatigue test for fatigue performance evaluation. Residual stress profile and full width at half maximum (FWHM) were measured by XRD. Vickers micro-hardness tester was used to check the hardness profile of the surface layer of the treated specimen. Surface finishing and roughness were observed and measured by optical
micrograph and a Talysurf roughness tester, respectively. Fractography of the fatigue fractured specimens was observed via scanning electron microscope(SEM).
Experimental Methods
In the UADR device, a free rolling metallic ball is impulsively energized by ultrasonic vibration
and simultaneously applied flexible ‘static pressure’, Fig.1. The ultrasonically accelerated ball
of heavy mass impulsively impinges and rolls the surface of the part, so that roughness are flattened and residual plastic deformation is produced leading to improved surface finishing, compressive residual stress and work hardened surface layer. Free rolling with dynamic contact and ultrasonic suspension enables friction free rolling contact, so that deeper layer of compression can be exerted without nicking.
Two groups of ground planar fatigue specimens were prepared in the present works, of which,
one was treated by the UADR process on a CNC machine center and the other left untreated
for comparisons. The material of the specimens is quenched and tempered ultra-high strength
30CrMnSiNi2A steel with chemical compositions in wt% as: 0.3C, 1.1Mn, 1.0Si, 1.05Cr, 1.7Ni,
0.009S, 0.010P, balance:Fe. The tensile mechanical properties of the materials are,
UTS=1627MPa, 0.2% yield strength=1375MPa. Fig.2 schematically illustrates the moving
route of the ball on the surface of the specimen being treated. Surface profile and roughness in
both the longitudinal and the transverse directions of the treated and the untreated specimens
were measured on a TR-204 Talysurf Roughness Tester. Surface finishing observations were carried out via an Olympus optical microscope.
Fig. 1 Schematics of the UADR process Fig.2 Schematics of the ball moving routine Residual stresses at the surface and subsurface region of the parts were obtained using Stresstech X-3000 X-ray diffraction tester with the sin2ψ-method with Cu Kα radiation at the
{211} plane of the samples. The FWHM (full width at half maximum) distributions at the surface and subsurface layer of samples were measured as well. In-depth profile of residual
stress and FWHM were determined by successively removing materials with electro polishing
while attention was paid to minimize alteration of residual stress distribution.
The hardness profile in the subsurface of treated sample after polishing and etching (in solution of 5% HNO3 and 95% CH2CH3OH) was examined with a Vickers micro-hardness
tester with a load of 0.1 N and loading duration of 15s. The surface hardness of the untreated sample was also tested with the same method.
For both groups of specimens, tension-compression fatigue tests were performed with stress ratio R=-0.976, maximum stress=670MPa, minimum stress=-653.92MPa, and loading frequency of 10Hz at ambient temperature. The fractured fatigue specimens were ultrasonically cleaned in acetone solution for 5 min. followed by fractographic observation with scanning electron microscope (SEM).
Results and discussions
Fatigue performance
Table. 1 shows the fatigue test results. It indicates that all the 5 specimens UADR treated were not failed until 5×105cycles, while the average cycles to failure for the untreated specimens is about 1.29×105, which means that the fatigue improvement of the UADR treatment is evident.
Table. 1 Fatigue test results
Fig.3 In-depth hardness profile after UADR
Hardness distribution
The hardness distribution along the depth from the surface of the treated specimens is shown in Fig.3. It is shown that the hardness value decrease with increasing depth from the surface to 500 μm, while the hardness of the untreated surface is about 530 HV, which implies that the UADR treatment resulted in work hardening of the surface layer of the 30CrMnSiNi2A steel.
Residual stress and FWHM
Fig.4 shows the residual stress distribution in the depth direction of the surface layer of the UADR treated sample. The residual stress along the depth direction distributes parabolically with a local extreme value of -1418MPa at depth about 150μm, and the residual stress on the immediate surface is -1120.9MPa, while the top surface residual stress of the untreated specimen (ground state) is -91.7MPa. Fig.4 also indicates that the depth of compressive residual stress layer produced by the UADR process is greater than 500 μm. The formation of a deep layer of compressive residual stress is believed to be the primary contribution of the
UADR process in improving the fatigue performance of the 30CrMnSiNi2A steel specimen in view of retarding fatigue crack initiation and propagation. Compared to the conventional shot peening process[8], the compressive residual stress generated by the UADR treatment is higher and the depth of the compressive residual stress layer is greater.
Fig.4 P rofile of residual stress after UADR Fig.5Profile of FWHM after UADR
The FWHM value vs. depth profile in the layer of compressive residual stress is depicted in Fig.5. While exists a small fluctuation at about 50 μm, the general distribution tendency of FWHM value is increasing in the depth direction and attained a maximum at about 500 μm which is close to that of the untreated surface of 5.127. This phenomenon is a little bit confusing, as generally the FWHM value is considered to be a character parameter representing the degree of work hardening. The larger the FWHM value the greater the work hardening degree. However, the present FWHM results is in contradiction with the hardness distribution tendency discussed above, which implies that the value of FWHM could not describe the degree of work hardening for the ultra-high strength steel 30CrMnSiNi2A in the current work. In fact, the same phenomenon has been found in a previous research[9]. Surface roughness and finishing
After UADR treatment, the surface roughness Rz in the longitudinal direction decreased from 0.56 μm to 0.293 μm, while that in the transverse direction decreased from 0.973 μm to 0.653μm. Fig.6 is the optical micrograph of the surface topography of the specimens with and without UADR treatment. It shows that the surface finishing of treated surface area is much smoother than the untreated area. Besides, the pittings or scars on the untreated surface are diminished after UADR treatment which helps in reducing stress concentration.
The above results show a visible improvement of surface finishing after UADR treatment. Surface roughness and finishing are consider to be detrimental to fatigue crack nucleation due to stress concentration, so that reduction in surface roughness is one of the major contributions of the UADR process in improving the fatigue resistance of the specimens.
Fig.6 Surface topography
Fractography of the fractured specimens
The fatigue fractures of the specimens s are shown in Fig.7. A white layer(refer to the arrow) with the thickness of about 10 μm was generated in the top surface of the UADR treated specimen, while for the untreated specimens, no such feature can be observed. Previous researches explained that the white layer is composed of high density dislocations and ultra-refine grains due to severe plastic deformation and exhibits intense work hardening and this layer play the role of inhibiting crack initiation[10].
Fig.8 shows that the fatigue crack initiated from a pitting like defect on the surface of the untreated specimen, while the fatigue crack of the treated specimen initiated due to a
Fig.8 Crack initiation site of the specimens (a) untreated (b) UADR treated
Conclusions
(1) The UADR treatment improved the fatigue resistance of the 30CrMnSiNi2A steel
substantially.
(2) The UADR treatment produced deeper layer of compressive residual stress with
maximum value of about -1418MPa and 150μm in depth.
(a ) 200m μ
(3) After UADR treatment, the surface roughness Rz in the longitudinal direction decreased
from 0.56 μm to 0.293 μm, while that in the transverse direction decreased from 0.973 μm to 0.653μm, which means that the UADR treatment can improve the surface finishing of the 30CrMnSiNi2A steel.
(4) UADR treatment resulted in surface work hardening and a thin layer of ultra-refined
microstructure.
(5) The current research results indicated that the FWHM value cannot correctly character
the degree of work hardening of the 30CrMnSiNi2A steel.
References
[1] Charles S. Montross, Tao Wei, Lin Ye, Graham Clark, Yiu-Wing Mai, Laser shock
processing and its effects on microstructure and properties of metal alloys: a review, International Journal of Fatigue, 24 (2002), pp1021–1036.
[2] Paul S. Prevéy, N.Jayarman, Dr. John Cammett, Overview of low plasticity burnishing
for mitigation of fatigue mechanism, Proceedings: 9th international conference on shot peening, Paris, 2005,pp260-265.
[3] I. Altenberger, B. Scholtes, U. Martin, H. Oettel, Cyclic deformation and near surface
microstructures of shot peened or deep rolled austenitic stainless steel AISI 304, Materials Science and Engineering A, 264 (1999), pp1–16.
[4] Yoshihiro Watanabe, Kaneshi Hattori, Mitsuru Handa, Effect of Ultrasonic Shot Peening
on Fatigue Strength of High Strength Steel, Proceedings: 8th international conference on shot peening, Germany, 2002, pp: 305-310.
[5] Sougata Roy , John W. Fisher, Ben T. Yen, Fatigue resistance of welded details
enhanced by ultrasonic impact(UIT), International Journal of Fatigue, 25 (2003) ,pp1239–1247.
[6] Chul-Hee Han, Young Shik Pyoun, Chang Sik KIM, Ultrasonic micro-burnishing in view
of ECO-materials processing, ATM, Vol4.1, (2002), pp25-28.
[7] You-Li Zhu, Kan Wang, Li Li, Yuan-Lin Huang, Evaluation of an ultrasound-aided deep
rolling process for anti-fatigue applications, Journal of Materials Engineering and Performance, 2009, vol.18(8): 1036-1040.
[8] Yu-kui Gao, Xiang-bin Li, Qing-xiang Yang, Mei Yao, Influence of surface integrity on
fatigue strength of 40CrNi2Si2MoVA steel, Materials Letters, 61 (2007), 466–469.
[9] GAI Xiu ying, LI Jia bao, KANG Zeng qiao, WANG Zhong guang, Mechanical property of
shot peened surface for steel 65Mn, Acta Metallurgica Sinica, Vol.32, No.6(1996), pp607-610.
[10] M. Turski, S. Clitheroe, A.D. Evans,C, Rodopoulos, D.J. Hughes,P.J, Withers,
Engineering the residual stress state and microstructure of stainless steel with mechanical surface treatments, Applied Physics A, 99 (2010), 549–556.
超声波法检测混凝土试验报告
哈尔滨工程大学 实验报告 实验名称:超声波法检测混凝土实验 班级:212 学号:05 姓名:纪强 合作者:黄昊、张艳慧 成绩:____________________________ 指导教师:梁晓羽 实验室名称:工程测试与检测技术实验室
目录 一.试验目的 二.试验仪器和设备 三.原理及试验装置 四.试验步骤 五.试验数据记录表格 六.注意事项 七.试验结果分析 八.问题讨论
一.试验目的 检测混凝土裂缝宽度,检测裂缝尺寸从而确定混凝土结构安全性。对混凝土裂缝超声检测进行实验研究,对预先设置在混凝土试件中的裂缝进行超声检测,将得到的检测数据与相应的理论值进行对比分析,讨论裂缝超声检测中存在的问题,对裂缝的检测方法提出建议。 二.试验仪器和设备 GTJ—F800 混凝土裂缝综合检测仪器,8500~11000RMB。 三.原理及试验装置 混凝土裂缝宽度检测试验原理:通过摄像头拍摄裂缝图像并放大显示在显示屏上,然后对裂缝图像进行图像处理和识别,执行特定的算法程序自动判读出裂缝宽度,仪器采用新型高精度、高灵敏度的光电转换器件进行图像采集,利用DSP 系统实现图像分析与处理,通过特征提取与优化算法自动判读裂缝宽度,同时在液晶屏上实时显示裂缝图像和裂缝宽度的测试结果。
裂缝深度检测试验原理:超声波在不同介质中传播时,将发生反射、折射、绕射和衰减等现象,表现为接收换能器上接收的超声波信号的声时、振幅、波形和频率发生相应变化,对这些变化分析处理就可以判定结构内部裂缝的深度。图中, H为试件高度;h为构造裂缝度 ;L1为射换能器距构造裂缝的水平距离;L2 为接收换能器距构造裂缝的水平距离。 四.试验步骤 制作带裂缝混凝土试件:该试件长0·6m,宽0·5m,高0·4m,混凝土强度C25,采用石子粒径30mm左右,裂缝深度90~100mm,缝宽 0~10mm。
超声波探伤作业指导
超声波探伤作业指导书 一、适用范围 超声检测适用于板材、复合板材、碳钢和低合金钢锻件、管材、棒材、奥氏体不锈钢锻件等承压设备原材料和零部件的检测;也适用于承压设备对接焊接接头、T型焊接接头、角焊缝以及堆焊层等的检测。 二、引用规范 JB/T4730.3 承压设备无损检测第三部分:超声检测 GB/T12604 无损检测术语 三、一般要求 1、超声检测人员应具有一定的基础知识和探伤经验。并经考核取得有关部门认可的资格证书。 2、探伤仪 ①采用A型脉冲反射式超声波探伤仪,其频率应为1~5MHz。 ②仪器至少应在满刻度的75%范围内呈线性显示,垂直线性误差不得大于5%。 ③仪器的水平线性、分辨力和衰减器的精度等指标均应复合JB/T 10061的规定。 3、探头 ①纵波直探头的晶片直径应在10~30mm之间,工作频率1~5MHz,误差不得超过±10%。 ②横波斜探头的晶片面积应在100~400mm2之间,K值一般取1~3. ③纵波双晶直探头晶片之间的声绝缘必须良好。 4、仪器系统的性能 ①在达到所探工件的最大检测声程时,其有效灵敏度余量不得小于10dB。 ②仪器与探头的组合频率与公称频率误差不得大于±10%。 ③仪器与直探头组合的始脉冲宽度(在基准灵敏度下):对于频率为5MHz的探头,宽度不大于10mm; 对于频率为2.5MHz的探头,宽度不大于15mm。 ④直探头的远场分辨力应不小于30dB,斜探头的远场分辨力应不小于6dB。 ⑤仪器与探头的系统性能应按JB/T 9124和JB/T 10062的规定进行测试。 四、探伤时机及准备工作 1、探伤一般应安排在最终热处理后进行。若因热处理后工件形状不适于超声探伤,也可将探伤安排在热处理前,但热处理后仍应对其进行尽可能完全的探伤。 2、工件在外观检查合格后方可进行超声探伤,所有影响超声探伤的油污及其他附着物应予以清除。 3、探伤面的表面粗糙度Ra为6.3μm。 五、探伤方法 1、为确保检测时超声波声束能扫查到工件的整个被检区域,探头的每次扫查覆盖率应大于探头直径的15%。探头的扫查速度不应超过150mm/s。耦合剂应透声性好,且不损伤检测表面,如机油,浆糊,甘油和水等。 2、灵敏度补偿 ①耦合补偿在检测和缺陷定量时,应对由表面粗糙度引起的耦合损失进行补偿。 ②衰减补偿在检测和缺陷定量时,应对材质衰减引起的检测灵敏度下降和缺陷定量误差进行补偿。 ③曲面补偿对探测面是曲面的工件,应采用曲率半径与工件相同或相近的试块,通过对比实验进行曲率补偿。 六、系统校准与复核
《超声检测实验》word版
《超声检测学》 实验指导书(机电学院测控技术及仪器专业使用) 彭光俊赵志编 武汉理工大学教材中心 2003年6月
第一部分 A型脉冲反射式超声探伤 系统工作性能测试 实验一水平线性的测定 一、实验目的 学会使用超声波探伤仪,熟练掌握超声探伤系统水平线性的测试方法。 二、概要 水平线性即超声探伤仪对距离不同的反射体所产生的一系列回波的显示距离与反射体距离之间能够按比例方式显示的能力。 A型显示超声探伤仪示波管内的电子束受与时间成线性关系的扫描电压作用,而在水平方向扫描形成时间基线。由于反射体的回波位置是在有线性刻度的时间基线标尺上读出的,因此,水平扫描线(时间基线)的非线性会引起定位误差。本测试就是为了检查超声探伤系统的时基线性。 三、实验用品 仪器:CTS-22型超声波探伤仪 1台 探头:2.5P 20-D型直探头,2.5P 13×13 K1.5-D型斜探头各1个电缆:QQ9-2电缆线(带接头) 1条 试块:CSK-ⅠA型试块 1块 耦合剂:机油 1杯 工具:小螺丝刀 1把 四、实验内容及步骤 (一)采用直探头测定水平线性 1.将探伤仪的[抑制]置于“0”, 其它调整取适当值。 2.将直探头压在CSK-ⅠA型试 块的A位置,中间加适当的耦合剂, 以保持稳定的声耦合,如图1-1所示。 3.调节[深度范围]、[深度微调] 和[脉冲移位]旋钮,使屏幕上显示出图1-1
第6次底波。 4.调节[粗调衰减]、[细调衰减]和[增益]旋钮,当底波B1和B6的幅度分别为50%满刻度时,将它们的前沿分别对准刻度0和100(设水平全刻度为100格)。B1和B6的前沿位置在调整中如果相互影响,则应反复进行调整。 5.再依次分别地将底波动B2、B3、B4、B5调到50%满刻度,并分别读出底波B2、B3、B4、B5的前沿与刻度20、40、60、80的偏差α2、α3、α4、α5(以格数计),如图1-2所示,将数据填入表1-1。 6.取其中最大的偏差值αmax。 则水平线性误差ΔL为: ΔL = | αmax | % 注意事项:图1-2中的B1~B6是分别调 到同一幅度,而不是同时达到此幅度。 (二)采用斜探头测定水平线性 采用斜探头测定水平线性的测试方 法与采用直探头测定水平线性的测试方 法相同。 五、实验报告要求 1.列出实验数据,计算水平线性 误差。 2.为什么读回波在水平标尺上的 位置时应将回波幅度分别调到某一相同 高度(如满刻度的50%)?图1-2 3.在水平线性误差很大的情况下,如何较精确地测定反射体深度? 4.水平线性误差影响什么?
超声波表面波探伤法
表面波探伤法 对于近表面缺陷的检查,表面波十分有效。正如理论论述的那样,由于表面波的能量集中于表面下2个波长之内,检查表面裂纹灵敏度极高。 表面波的位置分布可分解为与表面垂直和平行两个方向的振动,即纵波与横波所组成的椭圆形振动。表面下2个波长深度范围之内集中总能量的99%(40dB)。 表面波的声速约为纵波的1/2,比横波稍小(见表1)。 1、表面波的产生 表面波产生方法有着原理不同的两种方法。即Y切割石英晶体和透声楔方法。 常用的表面波探头采用与斜探头相似的楔块,当横波折射角为90°时,即产生表面波(见图1)。 2、表面波在表面的传播规律 2.1、在平面上的传播 2.1.1、油的影响 若在反射波传播的表面上涂上油,那么所传播的波几乎完全衰减。用手压也一样。这是因为理论上在试件的一侧为真空下求解,而有液体处理方法截然不同。另一种观点可以理解为表面波的垂直分量在液体层中引起衰减所致。用手按传播表面可以判断表面是否是裂纹或棱边的反射。同时也说明,探伤中探头前面不得有油污的重要性。 2.1.2、表面波的反射 表面波遇到表面或近表面缺陷会产生反射。作为缺陷,有裂纹或体积状缺陷(气孔、夹渣)。表面波重点检查裂纹。这里不讨论体积型缺陷。 (1)槽矩形槽的反射(裂纹) 与裂纹相似的人工伤,一般刻矩形槽缺陷。(见图2)。 刻槽深度与回波高度关系绘于图3中。
(2)棱边反射 如表面波传播中遇到工件的棱边会产生反射波,也有一部能量超过棱边继续传播(见图4)。 表面波在棱边上的反射理论上无法解释,但实验却十分简单。棱边为直角时,反射率最高。 (3)带曲率的棱边反射 如果棱边倒角,其曲率半径为r,反射回波降低。图5画出反射率与曲率半径的关系。从图中可以看出直角边(r=0)反射率52%;r=5时,反射率约为6%。即可以有更多能量通过圆弧面。 在A、D棱边反射信号中间,有时会出现其他回波信号B、C。这可能是入射波与回波干涉的结果。改变探伤频率,结果会不同。 2.1.3、表面波所产生的变型波 (1)表面波在边角处会产生的变型横波(S),如图7所示。其表面有一定曲率时,表面波的产生是逐点进行的(如图C所示)。产生变型波会使表面波产生衰减,变型波也会影响回波波形判断。有时也可加以利用。
超声波探伤仪探伤技术
超声波探伤仪探伤技术
超声波探伤仪就是频率高于20kHz、超出人们耳朵辨别能力并且穿透性很强的声波。是一种便携式工业无损探伤仪器,它能够快速、便捷、无损伤、精确地进行工件内部多种缺陷(焊缝、裂纹、折叠、疏松、砂眼、气孔、夹杂等)的检测、定位、评估和诊断。既可以用于实验室,也可以用于工程现场。广泛应用在锅炉、压力容器、航天、航空、电力、石油、化工、海洋石油、管道、军工、船舶制造、汽车、机械制造、冶金、金属加工业、钢结构、铁路交通、核能电力、高校等行业。 超声波探伤仪原理:运用超声波反射原理对于材料中的缺陷进行无损侦测,超声波在被检测材料中传播时,材料的声学特性和内部组织的变化对超声波的传播产生一定的影响,通过对超声波受影响程度和状况的探测了解材料性能和结构变化的技术称为超声检测。 彩屏超声波探伤仪是LED显示屏是彩色的,多颜色选择,适用于不同的光线条件,电火花检漏仪 https://www.360docs.net/doc/427402346.html,背光连续可调,更为直观和好看. 超声波探伤仪的应用有很多,比如用超声的反射来测量距离,利用大功率超声的振动来清除附着在锅炉上面的水垢,利用高能超声做成 "超声刀"来消灭、击碎人体内的癌变、结石等,超声波探伤仪而利用超声的反射等效应和穿透力强、能够直线传播等的特性来进行检测也是其中一个很大的应用领域。超声波探伤仪的检测应用主要包括在工业上对各种材料的检测和在医疗上对人体的检测诊断,通过它人们可以探测出金属等工业材料中有没有气泡、伤痕、裂缝等缺陷,可以检测出人们身体的软组织、血流等是否正常。 那么人们是怎么样利用超声来进行检测的呢?超声波探伤仪现在通常是对被测物体(比如工业材料、人体)发射超声,然后利用其反射、多普勒效应、透射等来获取被测物体内部的信息并经过处理形成图像。超声波探伤仪其中多普勒效应法是利用超声在遇到运动的物体时发生的多普勒频移效应来得出该物体的运动方向和速度等特性;透射法则是通过分析超声穿透过被测物体之后的变化而得出物体的内部特性的,其应用目前还处于研制阶段;超声波探伤仪这里主要介绍的是目前应用最多的通过反射法来获取物体内部特性信息的方法。反射法是基于超声在通过不同声阻抗组织界面时会发生较强反射的原理工作的,正如我们所知道,声波在从一种介质传播到另外一种介质的时候在两者之间的界面处会发生反射,而且介质之间的差别越大反射就会越大,所以我们可以对一个物体发射出穿透力
第二讲应力疲劳
第二讲应力疲劳 上节回顾 疲劳问题的特点 足够多次循环扰动荷载作用、疲劳是一个发展过程、疲劳破坏的三个阶段、断口特征、局部化 循环应力应变特性 循环硬化和循环软化 应力控制下的循环蠕变和应变控制下的循环松驰 Bauschinger效应 稳态循环应力应变曲线及数学描述 材料的记忆特性 疲劳问题分类 按循环应力作用的大小,疲劳可分为应力疲劳和应变疲劳 应力疲劳:最大循环应力S max小于屈服应力S y 寿命一般较高(>104),高周疲劳 应变疲劳:最大循环应力S max大于屈服应力S y(材料屈服后应变变化较大而应力变化较小,故一般以应变为 控制参量) 寿命一般较低(<104),低周疲劳材料应力疲劳特性
1. S -N 曲线 评价和估算疲劳寿命或强度需建立外荷载与寿命之间的关系。反映外加应力S 和疲劳寿命N 之间关系的曲线称为S -N 曲线。 基本S -N 曲线 在最简单的荷载谱-恒幅循环应力作用下,R = -1时(对称恒幅荷载)实验给出的应力-寿命关系曲线 2.S -N 曲线的一般形状 材料的S -N 曲线一般由实验得到 用一组标准试件在给定应力比和应力幅作用下,记录相应的寿命所得到的曲线。 典型S -N 曲线可分为 三段:低周疲劳区(LCF ), 高周疲劳区(HCF )和亚 疲劳区(SF )。 由S-N 曲线确定的对 应于寿命N 的应力称为寿 命为N 次循环的疲劳强度S N 。N = 1/4对应材料的静拉伸强度 S b ,N = 106~7对应的疲劳强度为疲劳极限S f 。特别地,R = -1的疲 劳极限记为S 1。 在HCF 区,S -N 曲线在对数坐标系上近似为直线。 1 04 106~7 S S L CF H CF S F S N S
超声波测距实验报告
电子信息系统综合设计报告 超声波测距仪
目录 摘要 (3) 第一章绪论 (3) 1.1 设计要求 (3) 1.2 理论基础 (3) 1.3 系统概述 (4) 第二章方案论证 (4) 2.1 系统控制模块 (5) 2.2距离测量模块 (5) 2.3 温度测量模块 (5) 2.4 实时显示模块 (5) 2.5 蜂鸣报警模块 (6) 第三章硬件电路设计 (6) 3.1 超声波收发电路 (6) 3.2 温度测量电路 (7) 3.3 显示电路 (8) 3.4 蜂鸣器报警电路 (9) 第四章软件设计 (10) 第五章调试过程中遇到的问题及解决 (11) 5.1 画PCB及制作 (11) 5.2 焊接问题及解决 (11) 5.3 软件调试 (11) 实验总结 (13) 附件 (14) 元器件清单 (14) HC-SR04超声波测距模块说明书 (15) 电路原理图 (17) PCB图 (17) 程序 (18)
摘要 该系统是一个以单片机技术为核心,实现实时测量并显示距离的超声波测距系统。系统主要由超声波收发模块、温度补偿电路、LED显示电路、CPU处理电路、蜂鸣器报警电路等5部分组成。系统测量距离的原理是先通过单片机发出40KHz 方波串,然后检测超声波接收端是否接收到遇到障碍物反射的回波,同时测温装置检测环境温度。单片机利用收到回波所用的时间和温度补偿得到的声速计算出距离,显示当前距离与温度,按照不同阈值进行蜂鸣报警。由于超声波检测具有迅速、方便、计算简单、易于做到实时控制的特点,并且在测量精度方面能达到工业实用的要求,因此在生产生活中得到广泛的应用,例如超声波探伤、液位测量、汽车倒车雷达等。 关键词:超声波测距温度测量单片机 LED数码管显示蜂鸣报警 第一章绪论 1.1设计要求 设计一个超声波测距仪,实现以下功能: (1)测量距离要求不低于2米; (2)测量精度±1cm; (3)超限蜂鸣器或语音报警。 1.2理论基础 一、超声波传感器基础知识 超声波传感器是利用晶体的压电效应和电致伸缩效应,将机械能与电能相互转换,并利用波的特性,实现对各种参量的测量。 超声波的传播速度与介质的密度和弹性特性有关,与环境条件也有关: 在气体中,超声波的传播速度与气体种类、压力及温度有关,在空气中传播速度为C=331.5+0.607t/0C (m/s) 式中,t为环境温度,单位为0C. 二、压电式超声波发生器原理 压电式超声波发生器实际上是利用压电晶体的谐振来工作的。它有两个压电晶片和一个共振板。当它的两极外加脉冲信号,其频率等于压电晶片的固有振荡频率时,压电晶片将会发生共振,并带动共振板振动,便产生超声波。反之,如果两电极间未外加电压,当共振板接收到超声波时,将压迫压电晶片作振动,将机械能转换为电信号,这时它就成为超声波接收器了。 三、超声波测距原理 由于超声波指向性强,能量消耗缓慢,在空气中传播的距离较远,因而超声波
超声波检测实验
超声波检测实验 一、实验目标 1)了解超声波探伤仪的原理并学会使用CTS-22型超声波探伤仪 2)掌握现场测试超声仪器性能的基本方法,包括:垂直线性、水平线性、探伤仪与仪器的组合性能。 3)初步学会超声波探伤 二、实验仪器设备 CTS-22型超声波探伤仪1台 2.5MHZ直探头1只 平面锻件(工件)1块 ⅡW试块(荷兰试块) 1块 平底孔试块(CS-1试块)1块 三、实验原理 1. 超声传感器结构及原理 超声波传感器又称超声波探头或超声波换能器,是利用压电效应将电能转换为超声振动能,或将超声振动能转为电能的实验装置。在实际应用中,我们利用压电效应的可逆性,也可将换能器作为“发射”或“接收”兼用。亦即将交流电压加在压电元件上,使其向介质发射超声波,同时又利于它接收从介质反射回来的超声波,并将反射转换成电信号。 图4-1是超声波纵波换能器的结构图,压电晶片是换能器的主要元件。压电晶体的厚度与超声波的频率成反比,如铁钛酸铅的频率厚度常数为1890KHz/mm,压电片的厚度为1mm时,固有频率为1.89MHz。压电片的两面敷有银层,作为导电的极板,压电片的地面接地线,上面接导线引致电路中。 2. 超声检测的基本原理 超声检测是一种利用超声波在介质中传播的性质来判断工件和材料是否异常的检验和测量方法。在超声检测中,所使用的电声、声电换能器,主要是利用
压电效应制作的,直探头可发射和接受纵波,主要由压电晶片和保护膜组成。超声波是由发射电路即高频脉冲电路产生的高频电压,加在发射探头上。发射探头将电波变成超声波,传入工件中。超声在缺陷或介面上反射后回到接收探头,转变为电波后输入给接收电路进行放大、检波,最后加到示波管上显示出来。通过缺陷在荧光屏上横坐标的位置,可以对缺陷定位;根据缺陷波的高度可确定缺陷的大小。 四、实验数据整理与分析 1.测试超声波探伤仪的垂直线性误差 绘制衰减测量曲线: 垂直线性误差: ?=++-=≤ d d d [()()] 6.9%8% 满足ZBY-84 标准规定
关于超声波探伤仪技术
超声波探伤仪就是频率高于20kHz、超出人们耳朵辨别能力并且穿透性很强的声波。是一种便携式工业无损探伤仪器,它能够快速、便捷、无损伤、精确地进行工件内部多种缺陷(焊缝、裂纹、折叠、疏松、砂眼、气孔、夹杂等)的检测、定位、评估和诊断。既可以用于实验室,也可以用于工程现场。广泛应用在锅炉、压力容器、航天、航空、电力、石油、化工、海洋石油、管道、军工、船舶制造、汽车、机械制造、冶金、金属加工业、钢结构、铁路交通、核能电力、高校等行业。 超声波探伤仪原理:运用超声波反射原理对于材料中的缺陷进行无损侦测,超声波在被检测材料中传播时,材料的声学特性和内部组织的变化对超声波的传播产生一定的影响,通过对超声波受影响程度和状况的探测了解材料性能和结构变化的技术称为超声检测。 彩屏超声波探伤仪是LED显示屏是彩色的,多颜色选择,适用于不同的光线条件,背光连续可调,更为直观和好看. 超声波探伤仪的应用有很多,比如用超声的反射来测量距离,利用大功率超声的振动来清除附着在锅炉上面的水垢,利用高能超声做成"超声刀"来消灭、击碎人体内的癌变、结石等,超声波探伤仪而利用超声的反射等效应和穿透力强、能够直线传播等的特性来进行检测也是其中一个很大的应用领域。超声波探伤仪的检测应用主要包括在工业上对各种材料的检测和在医疗上对人体的检测诊断,通过它人们可以探测出金属等工业材料中有没有气泡、伤痕、裂缝等缺陷,可以检测出人们身体的软组织、血流等是否正常。 那么人们是怎么样利用超声来进行检测的呢?超声波探伤仪现在通常是对被测物体(比如工业材料、人体)发射超声,然后利用其反射、多普勒效应、透射等来获取被测物体内部的信息并经过处理形成图像。超声波探伤仪其中多普勒效应法是利用超声在遇到运动的物体时发生的多普勒频移效应来得出该物体的运动方向和速度等特性;透射法则是通过分析超声穿透过被测物体之后的变化而得出物体的内部特性的,其应用目前还处于研制阶段;超声波探伤仪这里主要介绍的是目前应用最多的通过反射法来获取物体内部特性信息的方法。反射法是基于超声在通过不同声阻抗组织界面时会发生较强反射的原理工作的,正如我们所知道,声波在从一种介质传播到另外一种介质的时候在两者之间的界面处会发生反射,而且介质之间的差别越大反射就会越大,所以我们可以对一个物体发射出穿透力强、能够直线传播的超声波,超声波探伤仪然后对反射回来的超声波进行接收并根据这些反射回来的超声波的先后、幅度等情况就可以判断出这个组织中含有的各种介质的大小、分布情况以及各种介质之间的对比差别程度等信息(其中反射回来的超声波的先后可以反映出反射界面离探测表面的距离,幅度则可以反映出介质的大小、对比差别程度等特性),超声波探伤仪从而判断出该被测物体是否有异常。在这个过程中就涉及到很多方面的内容,包括超声波的产生、接收、信号转换和处理等。其中产生超声波的方法是通过电路产生激励电信号传给具有压电效应的晶体(比如石英、硫酸锂等),使其振动从而产生超声波;而接收反射回来的超声波的时候,这个压电晶体又会受到反射回来的声波的压力而产生电信号并传送给信号处理电路进行一系列的处理,超声波探伤仪最后形成图像供人们观察判断。这里根据图像处理方法(也就是将得到的信号转换成什么形式的图像)的种类又可以分为A型显示、M型显示、B 型显示、C型显示、F型显示等。其中A型显示是将接收到的超声信号处理成波形图像,根据波形的形状可以看出被测物体里面是否有异常和缺陷在那里、有多大等,超声波探伤仪主要用于工业检测;M型显示是将一条经过辉度处理的探测信息按时间顺序展开形成一维的"空间多点运动时序图",适于观察内部处于运动状态的物体,超声波探伤仪如运动的脏器、动脉血管等;B型显示是将并排很多条经过辉度处理的探测信息组合成的二维的、反映出被测物体内部断层切面的"解剖图像"(医院里使用的B超就是用这种原理做出来的),超声波探伤仪适于观察内部处于静态的物体;而C型显示、F型显示现在用得比较少。超声波探伤仪检测不但可以做到非常准确,而且相对其他检测方法来说更为方便、快捷,也不会对
无损探伤实验
实验一过程装备超声波检测 一.实验目的 1.熟悉CTS-26型超声波探伤仪的操作方法; 2.了解CTS-26型超声波探伤仪的技术性能指标; 5.绘制距离一波幅曲线。 二、实验内容 1.使用标准试块测定CTS-26型超声波探伤仪的水平技术性能; 2.测定校核斜探头的入射点及折射角 3.使用标准试块测定并绘制距离一波幅曲线; 三、主要仪器、设备、试块 CTS-26型超声波探伤仪; 探头:常用SHN—D系列、 直探头2.5P20—D 斜探头2.5Pl3×13K0.8~K3—D, 超声波探伤试块:CSK—1A、CSK-3A一1、CTK—B1、TSK一1A, 耦合剂:机油, 工具:卡尺、钢板尺、方格纸,锤子等。 四、实验步骤 1、熟悉超声波探伤仪的工作原理及主要旋钮的功能和调节方法; 2、超声波探伤仪线性误差测定; 3、测定校核斜探头的入射点及折射角; 4、测定并绘制距离一波幅曲线; 五、实验方法: 1、水平线性误差的测定 l)调节仪器水平零点,使用单探头工作:可用φ14(或φ20〉的直探头并选用工作频率为2.5MHz。此时应将探头电缆接于"发"的插座而探头开关拨到"单"的位置。开动电源之后,将探头放在试块F(CSK-1A〉的位置,调节水平和深度(粗调、微调〉旋钮,使底波位于10格(代表100mm〉。对于其它旋钮如增益、衰减和抑制等可作适当调节,务求清晰无杂波为原则。
2)再将探头放于试块A(CSK一1A)的位置,抑制置于"O"。深度粗调置被测深度的那一档级。调整扫描量程、水平位移,使荧光屏上只出现第四个回波(B1B2B3B4)如图所示使。B1B4分另别对应于时间轴上的刻线2.5格和l0格(25mm、100mm)如图找出最大偏差为a max。时间轴全刻度为b(l00mm),则水平线性误差为 L=(|a max|/0.75b)×100% 2、距离(深度)一波幅(dB)曲线的测定 1)斜探头入射点和折射角的校验:将斜探头置于CSK-1A试块B的位置,探测R50圆弧并在试块一侧移动探头,找出其最大的反射波。 2)调节始波零位和扫描量程:将探头置于CSK—ⅢA试块的探测面上,如图所示,探测150mm底面回波,同时调节脉冲位移旋钮使始波处于零位,调节扫描微调,使底波回波处于显示屏右侧;
混凝土超声波检测实验
混凝土超声波检测实验 一、实验目的: 学习超声波检测仪的使用,掌握混凝土超声波检测的基本原理和方法。掌握首波声时、振幅、频率测定的基本方法。 二、实验仪器及装置: CTS-35A非金属超声波检测仪、超声换能器、混凝土试块。 三、实验原理: 超声波检测技术是利用超声波在物体传播中的反射、绕射和衰减等物理特性,测定物体内部缺陷的一种无损检测方法。 混凝土超声波缺陷检测,目前主要采用“穿透法”,即用发射换能器发射超声波,让超声波在所检测的混凝土中传播,然后由接收换能器接收,它将携带有关混凝土材料性能和内部结构等信息。 超声波在混凝土中传播的速度与混凝土的组成成分,混凝土弹性性质,内部结构的孔隙、密实度等因素有关。混凝土弹性模量高、强度高、混凝土致密,超声波在混凝土中传播的速度也高,因此随混凝土强度不同,超声波传播的声速不同。 超声波在所检测的混凝土传播,遇到空洞、裂缝、疏松等缺陷部位时,超声波振幅和超声波的高频成分发生衰减。超声波传播中碰到混凝土的内部缺陷时,由于超声波的绕射、反射和传播路径的复杂化,不同波的叠加会使波形发生畸变。因此当超声波穿过缺陷区时,其声速、振幅、波形和频率等参数发生变化。 目前对混凝土的超声波检测主要是检测结构混凝土的强度,混凝土的密实度、有无空洞、裂缝等缺陷。 四、实验内容和步骤: 1.根据首波声时判定混凝土试块的强度。 由于混凝土试块的不均匀性,在每个混凝土试块的不同部位进行测试,取其平均值。 表1 混凝土强度与波速关系参考表 混凝土试块强度C25 C30 C35 C40 波速(m/s) 3500-3800 3700-4000 3900-4200 4100-4500 2.混凝土浅裂缝的检测 用平测法(斜测法)测量浅裂缝的位置及深度,如图1所示。 混凝土试块 图1 平测法测量浅裂缝位置及深度示意图
实验八超声波检测
实验八超声波检测 一、实验目的 1、了解超声波检测的基本原理和方法; 2、了解超声波检测的特点和适用范围; 3、掌握斜探头横波探伤的距离-波幅(DAC)曲线制作方法。 二、实验设备器材 1、ZXUD-40型数字式超声波探伤仪 ZXUD-40型数字式超声波探伤仪是小型化的便携式超声波探伤仪器,特别适用于材料缺陷的评估与定位、壁厚测量等,适合各种大型工件和高分辨率测量的要求。主要参数指标如下: 采样平率:100MHz(最高) 增益范围:0 ~ 110dB;0.1,1.0,2.0,6.0步进 动态范围:≥35dB 垂直线性:≤3% 水平线性:≤0.1% 探测范围:0-10m;0.1,1以及10mm步进自动设置 延迟:0-500.0μS 分辨率:≥40Db(5N14)) 灵敏度余量:≥63Db 抑制:0-90%;线性 探头类型:单探头,双晶探头,穿透探头 声速:1000~ 16000 m/s,步进为1 m/s 闸门:进波门(直方门,DAC门)、失波门 报警:声光报警 显示: 5.7英寸,高亮、真彩TFT显示器 电池:锂聚合电池,工作时间≥10h 仪器重量: 1.8Kg(带电池) 环境温度:-5℃~60℃ 相对湿度:20~90%RH 仪器外观如图一所示:
图一:仪器外观 本仪器采用软启动模式。再冷机状态下,当按住键持续2s后,将开启仪器电源,进入启动屏幕此时该屏幕上将显示初仪器的软件版本号以及软件发布日期,仪器自动进入系统自检并显示自检状态。系统自检完成后,自动进入仪器工作主界面。 在系统自检过程中,若电池电量过低,仪器会自行关机。 若在自检过程中,出现错误或用户按下任意键,那么在系统自检结束后,系统需要用户按下任意键(不包含电源按键),才进入仪器工作主界面。 在开机状态下,若用户持续2s按下,仪器将显示关机对话框,然后自动关机。 键盘及其功能 本仪器包含27个按键。这些按键分成5大类:电源键、方向键、功能菜单键,子菜单键和功能热键。关于各按键的具体功能概述,参见表8-1。 表8-1 各按键的具体功能概述
超声检测实验(精)
---------------------------------------------------------------最新资料推荐------------------------------------------------------ 超声检测实验(精) 《超声检测学》实验指导书(机电学院测控技术及仪器专业使用)(机电学院测控技术及仪器专业使用)彭光俊赵志编武汉理工大学教材中心 2003 年 6 月第一部分第一部分 A 型脉冲反射式超声探伤型脉冲反射式超声探伤系统工作性能测试系统工作性能测试实验一水平线性的测定一、实验目的一、实验目的学会使用超声波探伤仪,熟练掌握超声探伤系统水平线性的测试方法。 二、概要二、概要水平线性即超声探伤仪对距离不同的反射体所产生的一系列回波的显示距离与反射体距离之间能够按比例方式显示的能力。 A 型显示超声探伤仪示波管内的电子束受与时间成线性关系的扫描电压作用,而在水平方向扫描形成时间基线。 由于反射体的回波位置是在有线性刻度的时间基线标尺上读出的,因此,水平扫描线(时间基线)的非线性会引起定位误差。 本测试就是为了检查超声探伤系统的时基线性。 三、实验用品三、实验用品仪器: CTS-22 型超声波探伤仪 1 台探头: 2.5P 20-D 型直探头,2.5P 1313 K1.5-D 型斜探头各 1 个电缆: 1 / 19
QQ9-2 电缆线(带接头) 1 条试块: CSK-ⅠA型试块 1 块耦合剂: 机油 1 杯工具: 小螺丝刀 1 把四、实验内容及步骤四、实验内容及步骤(一)采用直探头测 定水平线性 1.将探伤仪的[抑制]置于0 ,其它调整取适当值。 2.将直探头压在 CSK-ⅠA 型试块的 A 位置,中间加适当的 耦合剂,以保持稳定的声耦合,如图1-1 所示。 3.调节[深度范围]、[深度微调] 和[脉冲移位]旋钮,使屏幕上显示出图 1-1 第 6 次底波。 4.调节[粗调衰减]、[细调衰减]和[增益]旋钮,当底波B1 和B6的幅度分别为50%满刻度时,将它们的前沿分别对准刻度 0 和 100(设水平全刻度为 100 格)。 B1和 B6的前沿位置在调整中如果相互影响,则应反复进行调整。 5.再依次分别地将底波动 B2、B3、B4、B5调到 50%满刻度, 并分别读出底波 B2、B3、B4、B5的前沿与刻度 20、40、60、80 的 偏差 2、3、4、5(以格数计),如图 1-2 所示,将数据填入表 1-1。 表 1-1 水平线性测试记录底面回
超声探伤实验报告
班 级__wl.10.b2___ 组 别_____________ 姓 名___陈婵___ _ 学 号 1100600050 日 期_2012.10.12__ 指导教师__贺老师 【实验题目】 超声探伤 【实验目的】 1.了解超声探伤的物理基础,学习超声探伤的一些基本方法; 2. 测量钢块厚度以及钢件中缺陷当量; 3. 测定超声在钢介质和非钢介质中的速度. 【实验仪器】 标准探头;测量探头,超声探伤仪,钢块,有机玻璃 【实验原理】 1·缺陷定位: 用探头直接接触工件,超声探伤仪输出的高频电脉冲,通过探头转换,变成等时间间隔的向工件发射的超声脉冲.在同步电路的控制下将x 轴的时间扫描转换为x 轴的线性扫描。Y 轴的偏转由探头上的脉冲电压或检波后的电压决定。超声波碰到缺陷反射回的波形被探头接收,由压电换能器转换而在屏上显示出缺陷波F 。缺陷波及底波到达探头的时间小于一个周期可以使下一次扫描时的图形与上一次完全一样,可以显示出稳定的波形。 2.缺陷当量: 在入射超声波辐射下,由波的衍射可知缺陷变成了一个新的波源,缺陷波向探头方向传播,其近场长度为2f f R N l = ,声压比为: 2////f b f b f b P R Z rp l =。缺陷波 与底波分贝数为 ) 2lg( 202 2 f f b Z R Z V λπ=,又因为20lg 20lg 20lg f f b b H V H H H ==-。 在实验中,可以通过调节衰减旋钮使底波衰减到虚线处,同时使缺陷波增至同一条曲线,V 的数值即为两次衰减旋钮读数之差。从而可以导出缺陷当量f R 。 3.超声波在非钢介质和钢介质中的传播速度: 2s Z c t t == V
超声波探伤与测厚
超声波探伤与测厚实验 【实验目的】 1、通过实验了解超声波探伤的基本原理,并掌握超声波探伤仪的使用及基本探伤方法。 2、探测不同样块的厚度及不同材料中超声波的传播速度。 【实验原理】 一、超声波探伤原理 1.超声波的传播特性 声波是由物体的机械振动所发出的波动,它在均匀弹性介质中匀速传播,其传播距离与时间成正比。当声波的频率超过20000赫时,人耳已不能感受,即为超声波。声波的频率、波长和声速间的关系 是: f c =λ (1) 式中 λ——波长;c ——波速;f ——频率。 由公式可见,声波的波长与频率成反比,超声波则具有很短的波长。 超声波探伤技术,就是利用超声波的高频率和短波长所决定的传播特性。即: (1)具有束射性(又叫指向性),如同一束光在介质中是直线传播的,可以定向控制。 (2)具有穿透性,频率越高,波长越短,穿透能力越强,因此可以探测很深(尺寸大)的零件。穿透的介质超致密,能量衰减越小,所以可用于探测金属零件的缺陷。 (3)具有界面反射性、折射性,对质量稀疏的空气将发生全反射。声波频率越高,它的传播特性越和光的传播特性接近。如超声波的反射、折射规律完全符合光的反射、折射规律。 利用超声波在零件中的匀速传播以及在传播中遇到界面时发生反射、折射等特性,即可以发现工件中的缺陷。因为缺陷处介质不再连续,缺陷与金属的界面就要发生反射等。如图1所示超声波在工件中传播,没有伤时,如图1a ,声波直达工件底面,遇界面全反射回来。当工件中有垂直于声波传播方向的伤,声波遇到伤界面也反射回来,如图1b 。当伤的形状和位置决定界面与声波传播方向有角度时,将按光的反射规律产生声波的反射传播。 2.超声波探伤仪的工作原理 图1 超声波在工件中的传播
超声波检测技术的实验原理和方法
实验超声波检测 一、实验目的 1、了解超声波检测的基本原理和方法; 2、了解超声波检测的特点和适用范围; 3、掌握斜探头横波探伤的距离-波幅(DAC)曲线制作方法。 二、实验设备器材 1、ZXUD-40E型智能超声波探伤仪 ZXUD-40E型数字式超声波探伤仪是小型化的便携式超声波探伤仪器,特别适用于材料缺陷的评估和定位、壁厚测量等,适合各种大型工件和高分辨率测量的要求。
⑴仪器外观如图9-1所示:
图9-1 仪器外观 当连接仅带有一个超声晶片的探头(自发自收)时,可以任意插入一个仪器上的探头连接器。 当连接带有双超声晶片的探头(一个为发射晶片,一个为接收晶片)或连接两个探头(一个发射探头,一个接收探头)时,必须注意:发射的一端接入左边一个探头连接器插孔,接收的一端接入右边一个探头连接器插孔,如图9-1所示。 ⑶键盘及其功能 图9-2ZXUD-40E的薄膜键盘按键排列 仪器包含27个按键。这些按键分成5大类:电源键、方向键、功能菜单键、子菜单键和功能热键。关于各按键的具体功能概述,参见表9-1。 表9-1各按键的具体功能概述
⑷参数设置规程 参数设置可通过以下两种规程来完成。 有些参数设置仅遵照“方向键增减调节规程”,比如:探头类型、声程跨距等;有些参数设置又仅遵照“直接数字输入规程”,比如:探头频率、探头规格等;还有些参数设置可遵照两种规程,比如:检测范围、零位偏移等。 ⑸方向键增减调节规程 可按下或
来增减参数设置。 ⑹直接数字输入规程 对于垂直菜单探伤通道设置,按下进入探伤通道设置状态,再次按下则进入直接数字输入状态;对于水平菜单,按下子菜单键选中子菜单项,再次按下子菜单键则也进入直接数字输入状态。 一旦进入直接数字输入状态,将在菜单项上出现闪烁光标,等待用户直接输入数字。在输入的过程中,若发现先前输入的数字错误,可按下 使得光标回退,删除刚才输入的错误数字。输入完成之后,用户可按下来接受输入,也可按下
探伤实验
超声波探伤和磁粉检测实验小结 在机械设备方面探测金属材料或部件内部的裂纹或缺陷非常重要,1、改进制造工艺;2、降低制造成本;3、提高产品的可能性;4、保证设备的安全运行。常用的探伤方法有:X光射线探伤、超声波探伤、磁粉探伤、渗透探伤、涡流探伤、γ射线探伤、萤光探伤、着色探伤等方法。这些方法都是物理探伤,物理探伤就是不产生化学变化的情况下进行无损探伤。本学期学习了超声波探伤和磁粉探伤方法。下面先对两种探伤方法简单叙述。 一.超声波探伤 利用材料及其缺陷的声学性能差异对超声波传播的影响来检验材料内部缺陷的无损检验方法。常用的检验仪器为 A型显示脉冲反射式超声波探伤仪。根据仪器示波屏上反射信号的有无、反射信号和入射信号的时间间隔、反射信号的高度,可确定反射面的有无、其所在位置及相对大小。 1.基本原理: 超声波探伤是利用超声能透入金属材料的深处,并由一截面进入另一截面时,在界面边缘发生反射的特点来检查零件缺陷的一种方法,当超声波束自零件表面由探头通至金属内部,遇到缺陷与零件底面时就分别发生反射波来,在萤光屏上形成脉冲波形,根据这些脉冲波形来判断缺陷位置和大小。超声波在介质中传播时有多种波型,检验中最常用的为纵波、横波、表面波和板波。用纵波可探测金属铸锭、坯料、中厚板、大型锻件和形状比较简单的制件中所存在的夹杂物、裂缝、缩管、白点、分层等缺陷;用横波可探测管材中的周向和轴向裂缝、划伤、焊缝中的气孔、夹渣、裂缝、未焊透等缺陷;用表面波可探测形状简单的制件上的表面缺陷;用板波可探测薄板中的缺陷。超声波在材料中传播,由于吸收和散射等,强度会衰减,因此测量在诸如真空自耗炉中熔炼的合金材料中的衰减,有可能无损地了解材料组织均匀性的情况。超声波焊缝探伤时为缺陷定位仪器时间扫描线的调整有水平定位仪、垂直定位、声程定位三种方法。 2.应用: 水浸(喷水)法检测钢管、锻件;单(双)探头检测焊缝;多探头检测大型管道 3.优缺点: 超声波探伤的优点是检测厚度大、灵敏度高、速度快、成本低、对人体无害,能对缺陷进行定位和定量。然而,超声波探伤对缺陷的显示不直
实验报告--超声波
四川大学实验报告书 课程名称:实验名称:超声波探伤实验系别:专业:班号:姓名:学号: 实验日期:2013年3月10日同组人姓名:教师评定成绩:
五、实验内容与步骤 一.超生波探伤仪的使用、仪器性能的测定、仪器与直探头综合性能测定 实验要求:1.掌握仪器主要性能:水平线性、垂直线性和动态范围的测试方法; 2.掌握仪器和直探头主要综合性能:盲区、分辨力、灵敏度余量的测试方法。 背景知识: 1.仪器的主要性能: A.水平线性 仪器荧光屏上时基线水平刻度值与实际声程成正比的程度。 B.垂直线性 仪器荧光屏上的波高与输入信号幅度成正比的程度。 C.动态范围 指反射信号从垂直极限衰减到消失所需的衰减量。 2.仪器与探头的主要综合性能: A.盲区 从探侧面到能发现缺陷的最小距离成为盲区,其内缺陷不能发现。 B.分辨力 在荧光屏上区分距离不同的相邻两缺陷的能力。 C.灵敏度余量 指仪器与探头组合后在一定范围内发现微小缺陷的能力。 D.声束扩散角 扩散角的大小取决于超声波的波长与探头晶片直径的大小。 D λ θ700 = 式中D 为探头直径 0θ为波长 实验步骤: 1.水平线性的测试 A.调节有关旋钮。使时基线清晰明亮,并与水平刻度线重合。 B.将探头通过耦合剂置于CSK-IA 试块上,如图所示。 C.调节有关旋钮,使荧光屏上出现五次底波B1~B5,且使B1、B5前沿分别对准水平刻度2.0和10.0,如图所示。 D.观察记录B2、B3、B4与水平刻度值的偏差值a2、a3、a4。
4.盲区的测试 A.[抑制]至“0”,其它旋钮位置适当。 B.将探头置于图中所示。 C.调[增益]、[水平]等旋钮,观察始波后有无独立回波。 D.盲区范围的估计:探头置于Ⅰ处有独立回波,盲区小于5mm ;探头置于Ⅰ处无独立回波,与Ⅱ处有独立回波,盲区在5~10mm 之间;探头置于Ⅱ处无独立回波,盲区大于10mm ;一般规定盲区不大于7mm 。 5.分辨力的测定 A.[抑制]至“0”,其它旋钮位置适当。 B.探头置于图示位置的Ⅲ处,前后左右移动探头,使荧光屏上出现声程为85、91、100的三个反射波A 、B 、C 。 C.当A 、B 、C 不能分开时,则分辨力F1为:(mm)-6-a a )8591(1b a a b F =-= D.当A 、B 、C 能分开时,则分辨力F2为:a F c 6a c )8591(2=-=(mm ) JB1834-76标准规定分辨力不大于6mm 。 6.灵敏度余量的测试 A.[抑制]至“0”,[增益]最大,[发射强度]至强。 B.连接探头,探头置于图示的位置(灵敏度余量试块200/φ2平底孔试块),调[衰减器]使φ2平底孔回波达满幅的50%,记录此时[衰减器]的读数N1=58. C.灵敏度余量?N=80-N1=22.
超声波探伤检验标准
超声波探伤检验标准 超声波探伤检验标准 1目的 为了满足公司发展需要,特制定我公司液压支架超声波探伤件检验标准,提供超声波探伤检验 依据,制定超声波探伤结果评定标准。 2主要内容及使用范围 规定了检验焊缝及热影响区缺陷,确定缺陷位置、尺寸和缺陷评定的一般方法及探伤结果的分级方法,适用于母材不小于8mm的铁素体类钢全焊透熔化焊对接焊缝脉冲反射法手工超声波探伤检验,不适用于以下情况焊缝的探伤检验:1)铸钢及奥氏体不锈钢焊缝; 2)外径小于159mm的钢管对接焊缝; 3)内径小于等于200mm的管座角焊缝; 4)外径小于250mm和内外径之比小于80%的纵向焊缝。 3检验等级 3.1检验等级的分级 注:A级难度系数为1,B级为5-6,C级为10-12。 3.2检验等级的检验范围 A级检验采用一种角度的探头在焊缝的单面单侧进行检验,只对允许扫查到的焊缝截面进行探测。一般不要求作横向缺陷的检验。母材厚度大于50mm时,不得采用A级检验。 B级检验原则上采用一种角度探头在焊缝的单面双侧进行检验,对整个焊缝截面进行探测。受几何条件的限制,可在焊缝的双面单侧采用两种角度探头进行探伤。母材厚度大于100mm时,采用双面双侧检验。条件允许时应作横向缺陷的检验。 C级检验至少要采用两种角度探头在焊缝的单面双侧进行检验。同时要作两个扫查方向和两种探头角度的横向缺陷检验。母材厚度大于100mm时,采用双面双侧检验。其它附加要求是: a.对接焊缝余高要磨平,以便探头在焊缝上作平行扫查; b.焊缝两侧斜探头扫查经过的母材部分要用直探头作检查; c.焊缝母材厚度大于等于100mm,窄间隙焊缝母材厚度大于等于40mm时,一般要增加串列式扫 查。 3.3检验等级的区别 A、B、C三种检验等级之间有所区别,现将其探头种类数、面数、侧数、板厚等方面的区别 简单列于表一中: 表一 检验等级 板厚 A B C <50 一种角度探头 单面单侧 一种角度探头 单面双侧或双面单 侧 两种角度探头 单面双侧或双面单 侧 >50~100 不适用