horngren16e_ch12_im
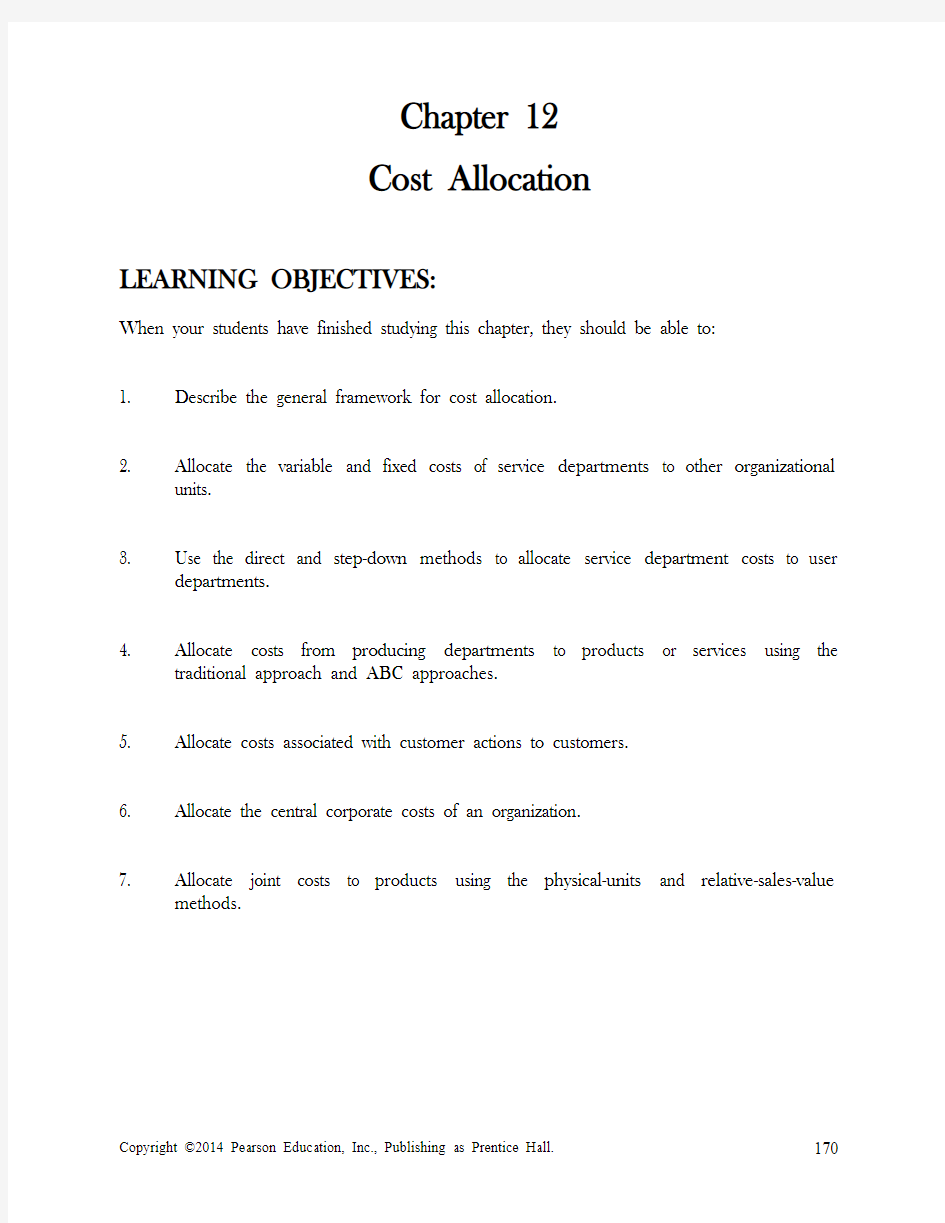

Chapter 12
Cost Allocation
LEARNING OBJECTIVES:
When your students have finished studying this chapter, they should be able to:
1. Describe the general framework for cost allocation.
2. Allocate the variable and fixed costs of service departments to other organizational
units.
3. Use the direct and step-down methods to allocate service department costs to user
departments.
4. Allocate costs from producing departments to products or services using the
traditional approach and ABC approaches.
5. Allocate costs associated with customer actions to customers.
6. Allocate the central corporate costs of an organization.
7. Allocate joint costs to products using the physical-units and relative-sales-value
methods.
CHAPTER 12: ASSIGNMENTS
CRITICAL THINKING EXERCISES
25. Allocation and Cost Behavior
26.Allocation and the Sales Function
27.Allocation and Marketing
EXERCISES
28. Allocation of Computer Costs
29. Fixed- and Variable-Cost Pools
30. Sales-Based Allocations
31. Direct and Step-Down Allocations, Activity-Based Allocation
32. Direct and Step-Down Allocations
33. Customer Profitability: Strategy
34. Joint Costs
35. Joint Costs
36. By-Product Costing
PROBLEMS
37. General Framework of Allocation, Service Departments, ABC,
Customer Profitability, and Process Maps
38. Allocation of Automobile Costs
40. Allocation of Costs
41. Service Department Allocation and ABC (Customer Profitability)
42. Customer Profitability at a Distributor
43. Customer Profitability and Allocation of Costs to Service
44. Medical Equipment
45. Direct Method for Service Department Allocation
46. Step-Down Method for Service Department Allocation
47. ABC Allocations; Process Map; What-if Analysis
48. Activity-Based Allocations
49. Allocation of Central Costs
50. Joint Costs and Decisions
CASES
51. Customer Profitability
52. Allocation of Data Processing Costs
53. Nike 10-K Problem: Customer Profitability
EXCEL APPLICATION EXERCISE
54 Allocating Costs Using Direct and Step-Down Methods COLLABORATIVE LEARNING EXERCISE
55.Library Research on ABC and Customer Profitability INTERNET EXERCISE
56. Cost Allocation at Sears Holdings Corporation
(https://www.360docs.net/doc/6b2936407.html,)
CHAPTER 12: OUTLINE
I. A General Framework for Cost Allocation {L. O. 1}
Cost allocation is fundamentally a problem of linking (1) some cost or groups of costs with (2) one or more cost objectives (e.g., products, departments, and divisions).
Ideally, cost allocation should assign each cost to the cost objective that caused it.
Linking of costs with cost objectives is accomplished by selecting cost drivers (i.e., activities that cause costs). Cost-Allocation Base—a cost driver when it is used for allocating costs. Cost Pool—a group of individual costs that is allocated to cost objectives using a single cost driver. Several terms are used to describe the process of assigning costs to cost objectives. Terms frequently used include allocate, apply, absorb, reallocate, trace, assign, distribute, redistribute, load, burden, apportion, and reapportion.See EXHIBIT 12-1. There are two types of departments: 1) producing departments, where employees work directly on the organization’s products or services, and 2) service departments(e.g., personnel department and facility management department), which exist only to support other departments or customers. Some service department activities (e.g., order processing and customer service) support customers rather than the production process.
II. Allocation of Service Department Costs {L. O. 2}
A. General Guidelines (see EXHIBIT 12-2)
The preferred guidelines for allocating service departments are:
1.Evaluate performance using budgets for each service (staff) department,
just as they are used for each production or operating (line) department.
The performance of a service department is evaluated by comparing
actual costs with a budget, regardless of how the costs are later allocated.
From the budget, variable-cost pools and fixed-cost pools can be
identified for use in allocation.
2.Allocate variable- and fixed-cost pools separately (sometimes called the
dual method of allocation). Note that one service department (e.g., a
computer department) can contain multiple cost pools if more than one
cost driver causes the department's cost. At a minimum, there should
be a variable-cost pool and a fixed-cost pool.
3.Establish part or all of the details regarding cost allocation in advance
of rendering the service rather than after the fact. This approach
establishes the “rules of the game” so that all departments can plan
appropriately.
B. Variable-Cost Pool
Variable costs should be allocated as follows:
budgeted unit rate x actual hours of cost driver
The use of budgeted cost rates rather than actual cost rates for allocating variable costs of service departments protects the using departments from intervening price fluctuations and inefficiencies in the service departments.
When an organization allocates actual total service department costs, it holds user department managers responsible for costs beyond their control and provides less incentive for service departments to be efficient.
C. Fixed-Cost Pool
The cost driver for the fixed-cost pool is the amount of capacity required when the service department was instituted. Therefore, fixed costs should be allocated as follows:
budgeted percent of capacity x total budgeted fixed costs
available for use
The predetermined lump-sum approach is based on the long-run capacity available to the user, regardless of actual usage from month to month. The level of fixed costs is affected by long-range planning regarding the overall level of service and the relative expected usage, not by short-run fluctuations in service levels and relative actual usage. A major strength is that a user department's allocation is not affected by the actual usage of other user departments.
D. Budgeted Cost-Allocation Rates
If fixed costs are allocated based on long-range plans, there is a natural tendency on the part of consumers to underestimate their planned usage and thus obtain a smaller fraction of the cost allocation. Top management can counteract these tendencies by monitoring predictions, and by following up and using feedback to keep future predictions more honest. In addition, rewards may be given for accurate predictions and penalties set (e.g., through higher charges) for usage above that predicted.
E. Allocating Fixed Costs Based on Capacity Available
Allocation will be based on the long-run capacity available to the user
regardless of the actual usage.
III. Allocation of Service Department Costs to Producing Departments {L. O. 3}
Service departments often support other service departments in addition to
producing departments. See EXHIBIT 12-3 for relevant data in regard to an
example, which is used to demonstrate two popular methods for allocating
service department costs: the direct method and the step-down method.
1. Direct Method
Direct Method—ignores other service departments when any given
service department’s costs are allocated to the revenue-producing
(operating) departments. The costs of operating the service departments
are allocated directly to operating departments with no intermediate
allocations for the services provided to other service departments.
2. Step-Down Method
Step-Down Method—recognizes that some service departments support
the activities in other service departments as well as those in production
departments. A sequence of allocations is chosen, usually by starting
with the service department that renders the greatest service (as
measured by costs) to the greatest number of other service departments.
The last service department in the sequence is the one that renders the
least service to the least number of other service departments. Once a
department’s costs are allocated to other departments, no subsequent
service department costs are allocated back to it. See EXHIBIT 12-4
for an illustration of the application of the step-down allocation method
for the text example.
3. Comparison of the Methods
See EXHIBIT 12-5 for a comparison of the costs ultimately allocated
to the producing departments. The method of allocation can greatly
affect the amounts distributed to different producing departments. If
significant differences are not generated, companies typically use the
direct method due to its simplicity.
A third method, the Reciprocal Method, provides the most theoretical
accuracy because it fully realizes reciprocal services by service departments to each other. With this method, simultaneous equations and linear algebra are used to solve for the impact of mutually interacting services. Due to the difficulty managers have in understanding the application of this method, it is rarely used in practice.
This method is described in a footnote in the text.
4. Costs Not Related to Cost Drivers
The examples used in the text thus far have assumed that the costs in a given service department were caused by a single cost driver. The costs were then allocated using this single cost driver. If some costs in the service department are not related to a single cost driver, three alternative methods of cost allocation should be considered.
a. Identify additional cost drivers. Divide the costs in the service
department into two or more cost pools and use a different cost
driver to allocate the costs in each pool.
b. Divide the service department costs into two cost pools, one
with costs that vary in proportion to the cost driver (variable
costs), and one with costs not affected by the cost driver (fixed
costs). Allocate the former using the direct or step-down method,
but do not allocate the latter. Costs not allocated are period costs
for the organization and are not regarded as a cost of a particular
production department.
c. Allocate all costs by the direct or step-down method using a
single cost driver. This assumption implicitly assumes that, in
the long run, the cost driver causes all of the service
department’s costs, even if a short-term causal relationship is not
easily identifiable.
IV. Allocation of Costs to Product or Service Cost Objects {L. O. 4} So far the chapter has discussed allocations of costs to departments or segments of an organization. Cost allocation is often carried one step further, to the outputs (e.g., products, parts, services) of these departments. Cost Application (or cost attribution)—the allocation of total departmental costs to the revenue-producing products or services.
A. Traditional Approach (see EXHIBIT 12-6)
1. Divide the costs in each producing department, including both the
direct department costs and all the costs allocated to it, into two
categories: 1) the direct costs that you can physically trace to the final
cost objectives, and 2) the remainder, the indirect costs.
2. Assign the direct costs to the appropriate products, services, or
customers.
3. Select one or more cost pools and related cost drivers in each
production department, and assign all the indirect departmental costs to
the appropriate cost pool.
4. Allocate (apply) the total costs accumulated in Step 1to products or
services that are the outputs of the operating departments, using the cost
drivers specified in Step 3. If only one cost driver is used, two cost pools
should be maintained: one for variable costs and one for fixed costs.
Variable costs should be allocated based on actual cost-driver activity.
Fixed costs should either remain unallocated or be allocated based on
budgeted cost-driver activity.
B. An ABC Approach
In the past, companies used direct-labor hours to apply the costs of
departments to units of product. However, direct-labor hours are not a very
good measure of the cause of costs in modern, highly automated departments.
As a result, companies are implementing activity-based costing (ABC)to
develop measures that better reflect the consumption of resources and related
costs in their environment by accumulating costs into key activities.
Both direct-labor hours and machine hours are volume measures. If many
costs are caused by non-volume-based cost drivers, ABC should be considered.
As Chapter 4 states, ABC is a system that first accumulates the costs of each
activity of an organization and then applies the costs of activities to the products,
services, or other cost objects using appropriate cost drivers. The ABC system
takes one large overhead cost pool and breaks it down into several pools, each
associated with a key activity.
The goal of activity-based costing is to trace the costs to products or services
instead of arbitrarily allocating them. Although it is relatively easy to trace direct
material and labor to products using physical measures, advocates of ABC
maintain that, by using appropriate cost drivers, many manufacturing overhead
costs can also be physically traced to products or services.
1. Illustration of Activity-Based Costing Approach in Manufacturing
The text provides an illustration of an ABC system for a manufacturer
using the four-step procedure that was introduced in Chapter 4.
a.First, the costing objective is to determine the costs of custom
and standard displays for L. A. Darling Company.
b.Next, the interrelationships among activities, cost objectives, and
resources were determined based on interviews with key
personnel, and a process-based map representing the flow of
activities, resources, and their interrelationship was developed.
See EXHIBIT 12-7 for the process-based map.
https://www.360docs.net/doc/6b2936407.html,ing the process map as a guide, the accountants then collected
the required cost and operational data via further interviews.
d.Finally, EXHIBIT 12-8 presents the key results of the activity-
based costing study. These results indicate that Custom Displays
is indeed being undercosted.
V. Allocation of Costs to Customer Cost Objects to Determine Customer Profitability {L. O. 5}
Customer profitability depends on more than the gross margin on the products or services they buy. It also depends on the costs incurred to fulfill customer orders and then provide other customer services such as order changes, returns, and expedited scheduling or delivery (see EXHIBIT 12-9). The following list is a profile of low and
high cost-to-serve customers.
Low Cost To Serve High Cost To Serve
Large order quantity Small order quantity
Few order changes Many order changes
Little pre- and post-sales support Large amounts of pre- and post-sales
support
Regular scheduling Expedited scheduling
Standard delivery Special delivery requirements
Few returns Frequent returns
A. Measuring and Managing Customer Profitability
If service-department costs are assigned to producing departments and then to
products, the allocation to products would be based on production-related
output measures that may have little relationship to the cause of customer-
service costs. An example in the text (Cedar City Distributors) is given to
demonstrate this important concept (see EXHIBITS 12-10, 12-11, 12-12, 12-
13, 12-14, and 12-15).
VI. Allocation of Central Corporate Support Costs{L. O. 6} Whenever possible, the preferred cost driver for central services is usage, either actual or estimated. For some central services (e.g., data processing, advertising, and operations research), usage appears to be a reasonable basis to allocate costs. For others (e.g., public relations, top corporate management overhead, a real estate department, and a corporate planning department), usage seems an inappropriate base. For these types of costs, companies frequently use revenues as the cost driver, which represents an “ability to bear” philosophy rather than portraying any cause-and-effect relationship.
A. Use of Budgeted Sales for Allocation
If the costs of central services are to be allocated based on sales, even though
the costs do not vary in proportion to sales, the use of budgeted sales is
preferable to the use of actual sales. At least this method means that the short-
run costs of a given consuming department will not be affected by the fortunes
of other consuming departments.
VII. Allocation of Joint Costs and By-Product Costs {L. O. 7}
A. Joint Costs
Sometimes inputs are added to the production process before individual
products are separately identifiable (i.e., before the split-off point). The costs of
these inputs (e.g., materials, labor, and overhead costs) are called joint costs.
Although allocations of these costs to the products, which emerge from the
joint process, should not affect decisions regarding whether to process the
products further, allocations are routinely made for inventory valuation and
income determination purposes.
Two conventional ways of allocating joint costs to products are widely used:
physical units and relative sales values. They allocate the joint costs to the joint
products in proportion to their number of physical units or sales dollars
generated by the joint products. A twist on the relative-sales-value method is
necessary when a joint product cannot be sold at the split-off point. Therefore,
the sales value is approximated using:
sales value at split-off = final sales value - separable costs
B. By-Product Costs
By-Product—a product that, like a joint product, is not individually identifiable
until manufacturing reaches a split-off point. By-products differ from joint
products because they have relatively insignificant total sales values in
comparison with other products emerging at split-off (e.g., glycerin from soap
making and mill ends of cloth and carpets).
If an item is accounted for as a by-product, only separable costs are allocated to
it. All joint costs are allocated to the main products. Any revenues from by-
products, less their separable costs, are deducted from the cost of the main
products.
VIII. APPENDIX 12: Multistage ABC (MSABC) Systems
Some organizations prefer to design a multistage ABC (MSABC) with more than two stages of allocations and resource cost drivers other than percentages. The added complexity yields more accurate costs and a deeper understanding of operations. This leads to better ideas for process improvement, with more satisfied customers and a competitive edge.
Three key attributes distinguish MSABC systems from two-stage ABC systems:
1.There are more than two stages of allocation.
2.Cost behavior of resources is considered.
3. There is greater use of operational information, such as cost drivers and
consumption rates.
To better understand the relationships among activities, resources, resource costs, and cost drivers, a detailed example is introduced. A product produced by Woodland Park Company, a manufacturer of plastic components used in commercial trucks and buses, is examined (see EXHIBIT 12-19).
CHAPTER 12: Quiz/Demonstration Exercises
Learning Objective 1
1. Major purposes for allocating costs are _____.
a. to predict the economic effects of planning and control decisions
b. to obtain desired motivation
c. to compute income and asset valuations
d. to justify costs or obtain reimbursement
e. all of these
2.Which of the following purposes of allocation relate to planning and control?
a.obtain desired motivation and compute income and asset valuations
b.predict economic consequences and justify costs
c.obtain economic consequences and justify costs
https://www.360docs.net/doc/6b2936407.html,pute income valuations and obtain reimbursement
Learning Objective 2
Use the following information for questions 3 and 4.
The city of Mars leases a photocopy machine, which it uses in its Copy Services Department for $2,500 per month plus 4¢ per copy made. In addition to the lease costs, operating costs for toner, paper, operator salaries, and so on are variable at 7¢/copy. All departments of the city combined estimated that they would make 70,000 copies per month. The Recreation Department estimated that they would make 10,000 copies per month on average. In May, the Recreation Department made 12,000 copies and the total number of copies made by Copy Services for the month was 58,000.
3. Following the guidelines of allocating variable and fixed costs of service departments
separately, the variable costs of the Copy Services Department that should be allocated to the Recreation Department in June are _____.
a. $1,320
b. $840
c. $1,130
d. $480
e. some other amount
4. Following the guidelines of allocating variable and fixed costs of service departments
separately, the fixed costs of the Copy Services Department that should be allocated to the Recreation Department in June are _____.
a. $0
b. $200
c. $2,500
d. $357
Learning Objective 3
Use the following information for questions 5 and 6.
The Francis Corporation operates two service and two producing departments in its production of go carts. The budgeted direct costs and other pertinent data for an upcoming month follow.
Service Departments Production Departments
Maintenance Personnel Tooling Assembly Direct costs $144,000 $80,000 $280,000 $320,000
Machine hours - - 30,000 20,000
# of employees 20 16 60 100
Personnel costs are allocated based on the number of employees, and maintenance costs are allocated based on machine hours.
5. The amount of maintenance costs allocated to the Assembly Department using the
direct method of cost allocation would be _____.
a. $32,000
b. $48,000
c. $86,400
d. $57,600
6. The amount of maintenance costs (to the nearest dollar) allocated to the Tooling
Department using the step-down method would be _____.
a. $91,733
b. $54,000
c. $86,400
d. $8,888
Learning Objective 4
7.The traditional approach to allocation of costs to the final cost objects focuses on
_____.
a.accumulating costs within producing departments and then allocating
producing departments costs; and finally to products, services, or customers
b.accumulating costs within departments and then allocating departmental costs
to departments, and finally to products, services, or customers
c.accumulating costs by products, services, or customers and deriving a cost per
unit
d.none of the above
Learning Objective 5
8.Which of the following is a profile of a high cost-to-serve customer?
https://www.360docs.net/doc/6b2936407.html,rge order quantity
b.standard delivery
c.frequent returns
d.regular scheduling
e.none of the above
Use the following information for questions 9 and 10.
Bally Inc. has four categories of overhead. The four categories and expected overhead costs for each category for next year are:
Inspection $ 30,000
Maintenance 60,000
Materials Handling 9,000
Setups 8,000
Currently, overhead is applied using a predetermined overhead rate based upon budgeted direct labor hours, and 20,000 direct labor hours are budgeted for next year.
The company has been asked to submit a bid for a proposed job. The company bases its bids on full manufacturing costs. Estimates for the proposed job are as follows:
Direct materials $ 2,000
Direct labor (400 hours) 4,000
Number of material moves 10 Number of inspections 2
Number of setups 5 Number of machine hours 40
In the past, full manufacturing cost has been calculated by allocating overhead using a volume-based cost driver, direct labor hours. Expected activity for the four activity-based cost drivers that would be used is:
Machine hours 5,000 Material moves 600
Setups 200 Quality inspections 1,000
9. If direct labor hours were used as the cost driver, the total cost of the proposed job
would be _____.
a. $5,140
b. $6,000
c. $10,280
d. $8,140
10. If the activity-based cost drivers were used to assign overhead, the total cost of the
proposed job would be _____.
a. $890
b. $8,140
c. $6,890
d. $10,280 Learning Objective 6
11. A method of allocating central costs of an organization to divisions, which clearly fails
to demonstrate a cause-and-effect relationship, is to _____.
a. allocate based on the actual usage of the service
b. allocate on the basis of sales dollars
c. allocate based on the estimated usage of the service
d. do none of these
12.Which of the following is an example of a central service?
a.public relations
b.legal services
c.accounting
d.advertising
e.all of the above
Learning Objective 7
Use the following for questions 13 and 14.
ABC Co., produces two products through a single manufacturing process. Each batch of product results in 400 pounds of product X and 600 pounds of product Y. The process requires materials, labor, and manufacturing overhead costing $50,000 per batch. X sells for $30 per pound, whereas Y sells for $20 per pound.
13. Using the physical units method of allocating joint production costs would result in an
allocation to product X of: _____.
a. $0
b. $30,000
c. $20,000
d. $50,000
14. Using the relative sales value approach of allocating joint production costs would result
in an allocation to product X of _____.
a. $10,000
b. $30,000
c. $25,000
d.$40,000
CHAPTER 12: Solutions to Quiz/Demonstration Exercises
1. [e]
2. [c]
3. [a]The allocation of variable costs: the variable portion of the lease of 4¢ per copy
and the Copying Services variable operating costs of 7¢ per copy. The actual
number of copies made (12,000) is multiplied by the variable cost of 11¢ per
copy to give $1,320 allocated.
4. [d]
5. [d]The $144,000 of maintenance cost is allocated based on machine hours.
Assembly uses 40% [20,000 of 50,000 total machine hours] resulting in a
$57,600 allocation.
6. [a]With the step-down method, Personnel costs are allocated first with $8,888.88
[$80,000 x (20/(20 + 60 + 100))] allocated to the Maintenance department.
Then, of the $152,888.88 now in Maintenance, $91,733.33 [$152,888.88 x
(30,000 / (30,000 + 20,000))] would be allocated to the Fabrication Department.
7. [b]8. [e]
9. [d]The total cost consists of direct material ($2,000), direct labor ($4,000), and
applied overhead. The overhead rate is $5.35 per labor hour [($30,000 +
$60,000 + $9,000 + $8,000)/20,000 direct labor hours]. Applying the $5.35 rate
to 400 direct labor hours for the job gives $2,140 of overhead applied to this
job. Adding this to the $2,000 direct materials and $4,000 direct labor gives
$8,140 total cost.
10. [c]Rates are $12/machine hour for maintenance [$60,000/5,000], $15/move for
materials handling [$9,000/600], $40/setup [$8,000/200], and $30/inspection
[$30,000/1,000]:
Maintenance (40 machine hours @ $12) $480
Materials handling (10 moves @ $15) 150
Setups (5 setups @ $40) 200
Inspections (2 @ $30) 60
Total overhead costs applied $890
Adding this to the $6,000 of materials and labor costs gives $6,890.
11. [b]12. [e]
13. [c]Based on physical units, X would be allocated 40% [400 pounds / (400 pounds
+ 600 pounds)] of the $50,000 of joint processing costs, or $20,000.
14. [c]Each product can be sold for $12,000. Product X has 400 pounds at $30 per
pound, and product Y has 600 pounds at $20 per pound. Thus, the total sales
value of the two products is $12,000, and each product would be allocated
$25,000 [50% x $50,000 joint production costs].