苯酚生产的市场分析与技术进展

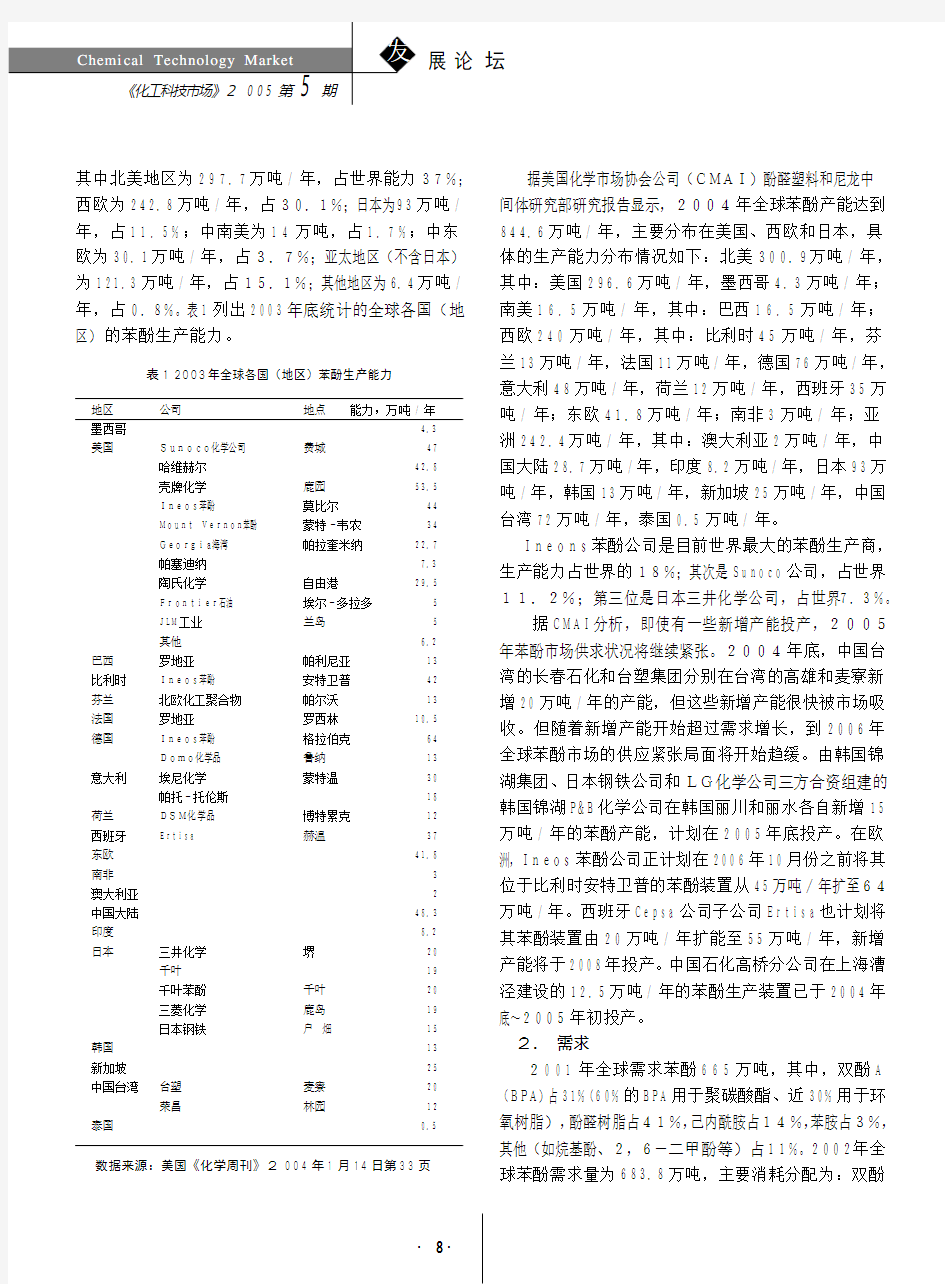
收稿日期:2005-4-12
苯酚生产的市场分析与技术进展
钱伯章,朱建芳
(上海擎督信息科技公司金秋石化科技传播工作室,上海 200127)
摘要:本文评述了近年来苯酚的世界生产能力和需求现状与扩能趋势,阐述了我国苯酚工业的发展现状(产能、
需求和扩能进展),以及苯酚生产技术的新进展。
关键词:苯酚;生产能力;需求;现状;发展趋势;技术进展;世界;中国
中图分类号:TQ243.1+2 文献标示码:A 文章编号:1009-4725(2005)5-0007-06
Phenol Product Market Analysis and Technical Advance
QIAN Bo- zhang ,ZHU Jian- fang
(Shanghai Kingdom Information Technology Co., Golden-Autumn Petrochemical Scientific Propagation-Room,
Shanghai 200127,China)
Abstract:The paper commentate recent years phenol world production capacity and the demand present situation
against enlarge capacity tendency ,elaborate our country phenol industry developing status (produce capacity ,demand and enlarge production progress ),along with new progress of phenol manufacture technique.
Key words:phenol ;production capacity ;demand ;present situation ;developing tendency ;technical advance ;world ;
China
苯酚是重要的有机化工原料之一,苯酚主要应用于制造酚醛树脂、双酚A、己内酰胺、己二酸、烷基酚、苯胺,并作为染料、医药、炸药、农药等精细化学品的原料。 一 世界产能和需求 1. 产能
据统计,2001年全球苯酚生产能力为778万吨,其中,北美占37%,西欧占31%,亚太地区占24%,东欧占3%,南美占2%,其他地区占3%。2002年全球苯酚生产能力达到790.6万吨,其中,北美289.6万吨,占36.7%;西欧为241.5万吨,占30.5%;日本89万吨,占13.2%;其他国家66.1万吨,占8.3%。
2003年世界苯酚总生产能力为805.3万吨/年,
其中北美地区为297.7万吨/年,占世界能力37%;西欧为242.8万吨/年,占30.1%;日本为93万吨/年,占11.5%;中南美为14万吨,占1.7%;中东欧为30.1万吨/年,占3.7%;亚太地区(不含日本)为121.3万吨/年,占15.1%;其他地区为6.4万吨/年,占0.8%。表1列出2003年底统计的全球各国(地区)的苯酚生产能力。 据美国化学市场协会公司(CMAI)酚醛塑料和尼龙中间体研究部研究报告显示,2004年全球苯酚产能达到844.6万吨/年,主要分布在美国、西欧和日本,具体的生产能力分布情况如下:北美300.9万吨/年,其中:美国296.6万吨/年,墨西哥4.3万吨/年;南美16.5万吨/年,其中:巴西16.5万吨/年;西欧240万吨/年,其中:比利时45万吨/年,芬兰13万吨/年,法国11万吨/年,德国76万吨/年,意大利48万吨/年,荷兰12万吨/年,西班牙35万吨/年;东欧41.8万吨/年;南非3万吨/年;亚洲242.4万吨/年,其中:澳大利亚2万吨/年,中国大陆28.7万吨/年,印度8.2万吨/年,日本93万吨/年,韩国13万吨/年,新加坡25万吨/年,中国台湾72万吨/年,泰国0.5万吨/年。
Ineons苯酚公司是目前世界最大的苯酚生产商,生产能力占世界的18%;其次是Sunoco公司,占世界11.2%;第三位是日本三井化学公司,占世界7.3%。 据CMAI分析,即使有一些新增产能投产,2005年苯酚市场供求状况将继续紧张。2004年底,中国台湾的长春石化和台塑集团分别在台湾的高雄和麦寮新增20万吨/年的产能,但这些新增产能很快被市场吸收。但随着新增产能开始超过需求增长,到2006年全球苯酚市场的供应紧张局面将开始趋缓。由韩国锦湖集团、日本钢铁公司和LG化学公司三方合资组建的韩国锦湖P&B化学公司在韩国丽川和丽水各自新增15万吨/年的苯酚产能,计划在2005年底投产。在欧洲,Ineos苯酚公司正计划在2006年10月份之前将其位于比利时安特卫普的苯酚装置从45万吨/年扩至64万吨/年。西班牙Cepsa公司子公司Ertisa也计划将其苯酚装置由20万吨/年扩能至55万吨/年,新增产能将于2008年投产。中国石化高桥分公司在上海漕泾建设的12.5万吨/年的苯酚生产装置已于2004年底~2005年初投产。
2. 需求
2001年全球需求苯酚665万吨,其中,双酚A(BPA)占31%(60%的BPA用于聚碳酸酯、近30%用于环氧树脂),酚醛树脂占41%,己内酰胺占14%,苯胺占3%,其他(如烷基酚、2,6-二甲酚等)占11%。2002年全球苯酚需求量为683.8万吨,主要消耗分配为:双酚
地区公司地点能力,万吨/年墨西哥4.3美国Sunoco化学公司费城47哈维赫尔42.8
壳牌化学鹿园53.5
Ineos苯酚莫比尔44
Mount Vernon苯酚蒙特-韦农34
Georgia海湾帕拉奎米纳22.7
帕塞迪纳7.3
陶氏化学自由港29.5
Frontier石油埃尔-多拉多5
JLM工业兰岛5
其他6.2巴西罗地亚帕利尼亚13比利时Ineos苯酚安特卫普42芬兰北欧化工聚合物帕尔沃13法国罗地亚罗西林10.5德国Ineos苯酚格拉伯克64Domo化学品鲁纳13意大利埃尼化学蒙特温30帕托-托伦斯18荷兰DSM化学品博特累克12西班牙Ertisa赫温37东欧41.8南非3澳大利亚2中国大陆48.3印度8.2日本三井化学堺20千叶19
千叶苯酚千叶20
三菱化学鹿岛19
日本钢铁户 畑15韩国13新加坡25中国台湾台塑麦寮20荣昌林园12泰国0.5表1 2003年全球各国(地区)苯酚生产能力
数据来源:美国《化学周刊》2004年1月14日第33页
A占31.4%,酚醛树脂占41.5%,己内酰胺占13.7%,苯胺占2.6%,其他占10.8%。表2和3分别列出世界苯酚按用途分和按地区分的需求量和所占比例。
表2 按用途分世界苯酚的需求量,万吨
表3 按地区分世界苯酚的需求量,万吨
据CMAI分析,2003年世界苯酚需求接近700万吨,为698万吨。2003年苯酚需求量中,双酚A占38%、酚醛树脂占27%、己内酰胺占13%、聚苯醚占4%、烷基酚占6%、苯胺占2%、其他占10%。尽管欧美苯酚树脂(环氧树脂和酚醛树脂)维持与GDP相同水平增长,但受亚洲BPA 20万吨/年新装置投产影响,美国苯酚需求下降0.6%,减至210万吨;欧洲仅增长2.1%,达197万吨。亚洲因BPA继续高速增长(19%),达140万吨。2003年BPA世界需求286.6万吨(增加6%)。
据CMAI报告,2004年世界苯酚需求量达到748万吨,其中:40%用于双酚A的生产,28%用于酚醛树脂的生产,12%用于尼龙/KA油,5%用于烷基酚,3%用于聚苯醚,2%用于苯胺,其它用途占10%。
据预测,在2005年后的5年内,随着苯酚衍生物双酚A、聚碳酸酸和聚苯醚的增长需求(其年均增长率可望达到8%~10%),全球苯酚需求的年均增长率仍将达到4.5%~5.4%,到2006年苯酚需求量可望达到800万吨,其中,亚洲尤其是中国将成为需求增长最快的地区。
3. 近期扩能项目
壳牌化学公司是北美仅次于Sunoco化学公司的第二大苯酚生产商,也是世界上仅次于Ineos苯酚公司、Sunoco公司和三井化学公司的世界第四大苯酚生产商,壳牌在美国得州鹿园拥有苯酚装置。
据统计,2003年北美领先的苯酚生产商生产能力为:1.Sunoco化学公司95万吨/年;2.壳牌化学公司57万吨/年;3. Ineos苯酚公司41万吨/年;4.Mount Vernon公司(辛特果、GE塑料与JLM工业公司的合资企业)32万吨/年;5.陶氏化学公司27万吨/年;6.Georgia海湾公司21万吨/年。
2004年初统计的亚洲地区主要的苯酚生产商为:三井化学公司70万吨/年;锦湖 P & B化学品公司28万吨/年;日本千叶苯酚公司20万吨/年;台塑集团20万吨/年;三菱化学公司19万吨/年;日本苯酚公司12万吨/年;中国台湾荣昌化学公司12万吨/年。
三井化学子公司--三井苯酚新加坡公司(MPS)是新加坡唯一的苯酚生产商,拥有25万吨/年装置。三井最近在新加坡建成第三条双酚A(BPA)生产线,使当地BPA总能力增加到21万吨/年,大部分BPA产能用于帝人聚碳酸酯(PC)公司在新加坡的19万吨/年PC装置。帝人公司计划在中国嘉兴建设二条PC生产线,总能力为12万吨/年,三井也研究在该地附近建设BPA装置。
韩国Kumho (锦湖)P & B化学品公司(韩国锦湖集团和日本钢铁公司的合资企业)扩增其在韩国丽川的苯酚和异丙苯产能,使异丙苯产能提高33万吨/年,达到42万吨/年,苯酚产能提高15万吨/年,达到28万吨/年。从而使该公司成为在亚太地区仅次于三井化学公司的第二大苯酚生产商。锦湖 P & B化学品公司采用UOP公司技术扩建15万吨/年苯酚装置,项目投资6900万美元,已经于2004年上半年完成。该项扩能满足了当地对苯酚的需求,也向该公司双酚A装置(由10万吨/年扩增至13.5万吨/年)提供原料。
罗地亚公司计划于2007年使巴西的苯酚能力由16.5万吨/年扩增至21万吨/年。
综合CMAI预测表明,到2007年,亚洲将成为苯酚的第一生产地区。2004~2008年间,全球将有212万吨/年苯酚能力投运(见表4),2008~2009年间将另有300万吨/年能力扩增。
2001年2002年2003年2006年双酚A228.6214.8256.8336.6酚醛树脂187.9233.8211.5216.9己内酰胺62.493.579.571.3烷基酚24.925.526.928.3其他117.1116.2123.3133合计620.9683.8698786.1
2000年 2001年 2002年
需求占%需求占%需求占%美国214.332204.431200.629西欧194.929193.9 29190.228日本76.81173.21174.911亚洲(除日本)95.21496.915119.417其他93.01496.21498.714合计674.2100620.9100683.8100
表4 2004-2008年全球苯酚扩增项目,万吨/年
二 技术进展
目前,苯酚生产工艺主要有:异丙苯法、甲苯-苯甲酸法和苯直接氧化法三种。
苯酚早期从煤焦油中制得,最早的苯酚化学合成工艺路线是磺化法,由于腐蚀和污染等原因,已基本废弃,此后相继出现了氯苯法、环己烷法、甲苯氧化法、联产丙酮的异丙苯法等,在这些方法中异丙苯法最具竞争力。据统计,目前世界上92%以上的苯酚采用异丙苯法生产工艺。从异丙苯出发生产苯酚要经过异丙苯氧化、氧化物提纯、过氧化氢异丙苯(CHP)分解、产品精制等工序。其工艺步骤是:苯和丙烯反应得到异丙苯;异丙苯经氧气或空气氧化,生成过氧化氢异丙苯(CHP);CHP分解生成苯酚和丙酮。该方法以KBR(凯洛格-布朗?路特)公司的苯酚法工艺最为典型。除从异丙苯生产高纯度苯酚和丙酮外,还回收副产物α-甲基苯乙烯(AMS)和苯乙酮(AP)。在该工艺中,异丙苯用空气氧化成CHP的效率高达95%以上,CHP被浓缩,并在酸催化剂存在下高产率(大于99%)地分解为苯酚和丙酮。AMS加氢为异丙苯,用于循环氧化或回收。
带有AMS加氢的KBR流程,1.31吨异丙苯可生产1吨苯酚和0.615吨丙酮。KBR苯酚工艺具有低能耗、低原材料消耗、低生产费用和低排放污染的特点。迄至2003年初统计,已采用该工艺建设了30套生产装置,生产苯酚总能力超过280万吨/年。20世纪90年代底,Aristech公司和壳牌化学公司采用该工艺分别在美国建成10万吨/年和22.5万吨/年装置,中国石化上海高桥分公司也引进了这一工艺。采用KBR苯酚技术建设的4套新装置于1999-2002年投运,另有3套在设计中。采用该工艺生产的苯酚占世界能力的50%以上。
甲苯-苯甲酸法先将甲苯液相氧化为苯甲酸,苯甲酸再转化为苯酚。具有甲苯原料来源广泛、流程简单等优点。
目前苯酚合成工艺在继续完善异丙苯法的同时,正在向无废、少废、不联产丙酮技术的方向发展,研发热点有:
1. 异丙苯法的改进
异丙苯法改进的重点集中于开发新型催化剂、完善分解工序和提纯工序、
UOP工艺、鲁姆斯工艺、KBR工艺继续对原有工艺加以改进,在降低副产物量、提高苯酚纯度方面,较前有所改进,其中UOP工艺采用加入催化剂或化学品帮助分离的技术,提高苯酚的纯度。以上三种技术均能获得纯度99.99%以上的苯酚,从而可满足生产聚碳酸酯的要求,同时,在热量利用上都有所改进。
埃克森美孚公司开发了由过氧化氢异丙苯(CHP)制取苯酚的催化精馏技术,塔器催化剂床层中采用Zr-Fe-W氧化物固体催化剂,转化率可达100%,苯酚和丙酮选择率高,而4-异丙苯基苯酚、α-甲基苯乙烯(AMS)二聚物及焦油等高沸点的联产杂质数量很少。该工艺对苯酚的选择性为89.5%,稍低于采用硫酸为催化剂的传统工艺。反应器催化剂床层操作条件为:50-90℃、34KPa、液时空速4h-1。联产物α-甲基苯乙烯和苯乙酮的选择性分别为9.7%和0.8%。该催化精馏工艺有效地将反应热用于丙酮精馏过程,将反应过程和精馏过程结合在一起,降低了能耗和投资。由于采用固体酸催化剂代替通用的硫酸催化剂,可免除产物的中和过程。
Aristech公司提出异丙苯两步裂解生产苯酚/丙酮的改进工艺,在第一反应段以酸催化剂使95%的含二甲苄基醇的异丙苯过氧化物分解,在第二反应段,采用钯加氢催化剂和氢气使α-甲基苯乙烯(AMS)氢化成异丙苯,同时,第一反应段残余的CHP分解成苯酚和丙酮,残余的二甲苄基醇脱水成为α-甲基苯乙烯(AMS)。
GE公司提出的酸催化裂解CHP改进工艺,在第一
公司地点扩增能力投运时间台湾化学和纤维中国台湾省402004-2007长春石化中国台湾省202004
Ineos苯酚比利时192006
锦湖石化韩国152005
LG化学韩国152005
Ineos苯酚美国82005-2006北欧化工芬兰5.52005
Sunoco美国52007
Ertisa西班牙52006
罗地亚巴西3.52004
中国大陆中国大陆952004-2006合计212
容器中裂解CHP,得到含有过氧化氢二异丙苯的裂解产物后,再在第二容器中裂解过氧化氢二异丙苯。据称该工艺在选择性最高的情况下,可大大提高装置生产率,降低工艺能耗,并使建设新的裂解单元的投资费用大大降低。
美国Allied Signal公司设计了节能型高纯度苯酚提纯工艺,在冷凝塔水冷凝蒸气的同时回收热能以产生蒸汽,而从冷凝塔抽出少量蒸气被送入酸分离蒸馏塔处理,得到的部分塔釜组分送回苯酚蒸馏塔,可有效地节约能源。该公司还设计了另一种以胺处理提纯苯酚的方法,该方法以胺处理将苯酚粗产物中的丙酮醇和2-苯基丙醛转化成高沸点化合物,然后将粗产物蒸馏除去高沸点化合物,与水进行蒸汽蒸馏,再向塔釜产物中加入一定量的胺将一缩二丙酮和羰基化合物杂质转化为轻、重杂质,然后将蒸汽蒸馏工序得到的重组分蒸馏,可得到高纯度苯酚。
三井化学公司与新日铁等公司建立了不联产丙酮的生产装置。在该工艺中,丙酮不作为产品取出,而是通过专门设计的磷酸镁沸石催化剂在固定床反应器中将丙酮氢化成异丙醇,异丙醇与苯进行烷基化反应生成异丙苯。该工艺己于1997年应用于比利时安特卫普的21万吨/年扩建装置中。
2. 苯直接氧化制苯酚
由苯和丙烯出发经异丙苯生产苯酚的路线要联产大量丙酮(丙酮和苯酚产率比为0.6∶1),同时苯酚需精制而耗用能源。从全球范围看,两者的产需基本上平衡,但就局部而言,市场仍然往往互相牵制,因此由苯为原料直接氧化(也可称羟基化)制取苯酚的工艺已成研发热点。目前研究的氧化剂类型有氧、过氧化氢、一氧化二氮等,研究结果表明,采用分子氧作氧化剂时,苯
的转化率较低,而采用N
2O或H
2
O
2
一类专用氧化剂时,
苯转化率较高。该法具有工艺简单、收率高、对环境污染小等特点,具有工业开发和应用前景。该路线的研究重点是开发高效催化剂,目前研究的类型有H-ZSM-5、负载ZSM-5(Fe-ZSM-5、Na-ZSM5-5)、钛硅沸石TS-1、羟基磷灰石等。
美国Solutia(首诺)公司和俄罗斯博里斯可夫(Boreskov)催化剂研究所(BIC)共同研究开发了无联产
丙酮的苯直接氧化法新工艺—Alphox技术,利用N
2O在
分子筛催化剂上进行反应,反应在气相、低压运转的固
定床绝热反应器中进行,经过简单的分离和精馏后,可
得到高产率、高纯度的苯酚。BIC对催化剂进行反复试
验后证实,含有铁的酸性ZSM5-5和ZSM-11沸石催化剂
用500-900℃水蒸汽处理2h后,可极大地提高苯酚的
产率,抑制苯与N
2
O的燃烧反应,延缓催化剂的失活。
该工艺过程产生的废弃物不足原料苯量的2%,并能有
效地将苯酚生产装置与己二酸装置整合起来,既能有
效地利用N
2
O,又能将苯酚用于生产己二酸,或作商品销售。美国斯坦福研究所对Alphox法的技术经济评
估数据表明,该法的总固定投资费用比一套同等的异
丙苯法苯酚装置要低,其净生产费用具有竞争力,而
且不受丙酮市场波动的影响。由于采用该方法的苯酚
装置要受到相联结的己二酸生产装置规模的牵制,故
适用于建较小规模的苯酚装置。但由于中试验证的催
化剂的选择性/连续运转周期较差,以N
2
O计苯酚选择性较低,故要实现工业化尚存在许多问题。
首诺与俄罗斯西伯利亚Boreskov催化研究所共同
开发的苯一步法制苯酚工艺,与传统的异丙苯工艺相
比,操作简便,且投资费用可大大降低。美国GTC技术
公司与首诺合作拟将该技术推向市场。Alphox工艺由
苯与N
2
O在改性沸石催化剂上气相反应制得苯酚。当
N
2
O与催化剂接触时会分解成N
2
和一种高活性、且与催化剂键合在一起的氧,即α-氧。α-氧插入苯的C-
H链后生成苯酚。由于该工艺中苯酚选择性较高,可达
90%-99%,因此Alphox工艺的苯酚分离部分比异丙苯
工艺简单。原料N
2
O可来自己二酸生产的尾气,但需
经纯化以降低其中NO
x
、CO和O
2
等杂质含量,或由氨催化氧化反应制得。一套13.62万吨/年采用Alphox
工艺的苯酚装置的投资费用约为异丙苯工艺的55%-
60%。Alphox技术己在首诺公司位于美国佛罗里达州佩
森库拉的示范装置上得以验证,GTC公司己与一家石化
公司商讨建设首套工业化装置。
日本产业技术综合研究所、丸善石化公司、NOK
公司合作开发了苯直接氧化生成苯酚的新气相合成工
艺,用离解氢将氧活化后引入苯中,氢被钯膜吸附,而
解离活化的氧透过膜,与苯环加成为苯环氧化物,再异
构化为苯酚。据称该工艺不副产丙酮,合成工艺大幅度
简化,能耗费用也大为节减。
埃尼化学公司以H2O2为氧化剂,采用两相反应溶剂体系,有机相由原料苯和一种有机溶剂(最好为乙腈)组成,含水相由H2O2和催化剂组成。催化体系由含氮的杂芳族化合物羧酸配体、无机或有机酸性溶剂和Fe2+或Fe3+盐类物质组成。据称,由于存在两相溶剂体系,使合成苯酚选择性较高。
日本东京理工学院开发了以铕-钛-铂为催化剂的苯直接制苯酚工艺,据称加入钛络合物作为助催化剂,可以促进直接氧化反应。
Sunoco公司开发了以氧气为氧化剂,以螯合物为催化剂的工艺,该工艺以负载在二氧化钛上的钒基螯合物(含1.2%金属)为催化剂,在苯转化率为1%时苯酚的选择性大于97%。
韩国化学技术研究院开发的催化体系由Y-分子筛和ZSM-5分子筛组成,ZSM-5分子筛中含2%的钛,在催化剂作用下,产出的苯酚选择性大于97%。 最近日本先进工业科技国家研究院(AIST)开发了由苯一步法合成苯酚的膜法催化工艺,而常规工艺从苯开始需三个步骤,并且产生需处理的废酸。AIST的工艺使用不锈钢外管和多孔α-氧化铝内管组成的反应器,关键元件是厚1μm的钯膜催化剂,用化学蒸气沉积法涂覆在氧化铝管的外侧。膜由AIST与丸善石化公司和NOK公司共同开发。反应器置于加热至150-250℃的加热炉内,苯和氧气流过氧化铝内管,0.2MPa压力的氢气沿管外侧通过。氢被吸附在膜上,在此被离解和活化,然后通过氧化铝管内表面,活化的氢捕集
管子内表面上的氧分子,生成活化的氧,活化的氧与苯环的双键反应通过苯环氧化物由苯生成苯酚。实验室中,在转化率低于3%时,生成苯酚的选择性大于90%。10%~15%转化率时,选择性大于80%。苯酚产率为每千克催化剂1.5千克/时,随着工艺过程的改进,预计转化率还可提高。
日本化学创新研究院(JCII)与东曹公司合作,正在开发从苯制取苯酚而不产生副产物的新工艺。目前制取苯酚的主要合成路线是异丙苯工艺,需使用过氧化物并生成丙酮副产品;甲苯法工艺会产生大量CO2;二步氯-苯法工艺的设备需采用防腐材料,并且产生含氯废液。为解决这些问题,需开发由苯直接氧化法工艺。新工艺由二步组成,首先,苯与醋酸在150-200℃和控制氧分压下反应,生成乙酸苯酯,该反应藉助Pd-硫属体系载于氧化硅上的新催化剂,单程下可达10%转化率。乙酸苯酯再用离子交换树脂,在低于100℃下进行水解,生成苯酚和醋酸,醋酸回收并循环至第一反应器。目前,研究人员正在改进第一步反应的转化率。
东曹公司开发了碲-钯催化剂,用于将苯、氧气和氢气转化成苯酚,具有低费用和催化剂能长时间保持活性等特点。反应物先被转化成苯醋酸酯,苯醋酸酯再利用离子交换树脂分解成苯酚和氧气。目前,苯转化率仅约10
%,现正在进一步改进苯的转化率。 (未完待续)
(市场分析)2020年苯酚/丙酮国内外市场分析与技术进展
苯酚/丙酮 国内外市场分析与技术进展
摘要 苯酚 2005年世界苯酚生产能力约950万t/a,表观消费量达到813.9万t,美国是世界最大的苯酚生产和消费国家,其次是日本,北美、西欧、中东欧和非洲产能均有过剩,其他地区处于供不足需的状态。至2012年,世界苯酚生产能力将达到1118万t/a左右,需求量为968万t,开工率为87%。 2005年我国苯酚总生产能力达到54万吨。表观消费量约为73.341万吨,具有一定规模的企业仅有4家,总生产能力约为50.6万吨/年,约占我国苯酚总生产能力的94.26%。均采用异丙苯法。我国苯酚产量不能满足国内消费的需求,每年都得大量进口。 预计2006年国内苯酚总产量可增加至52.5万t,市场供需缺口在25万-30万t。到2007年国内市场对苯酚的需求总量将达到约85万吨,但到2007年我国苯酚生产能力最多能达到约85万吨,按装置90%开工率计算,仍然不能满足当年国内消费需求。但到2007年全球苯酚生产能力将出现过剩。世界新建、扩建苯酚装置几乎都集中在亚洲地区,新增苯酚产品将不可避免地渗入到我国市场,竞争将更加激烈。 丙酮 2005年世界丙酮生产能力达到599.5万t/a,表观消费量为527.6万t,世界丙酮的产能主要集中在北美、西欧和亚洲,消费量最大的地区是西欧其次是亚洲和北美。2006-2008年世界丙酮能力将新增加37.9万t/a。预计2006年全球丙酮的供应将有30万~60万t的余量,至2011年,全球丙酮产能将达到727万t/a,需求量达到631.5万t,开工率为87%,丙酮的余量将超过90万t。全球丙酮市场将面临过剩。 我国丙酮2005年年产量达到35.0万t。其中采用异丙苯法技术的生产厂家有4家,产能合计为31.2万t/a。我国丙酮产不足需,每年都需大量进口。2005年底全国丙酮的进口量达到33.74万t,年均增长率达到23.7%占国内表观消费量的49.1%。进口产品主要来自于俄罗斯、中国台湾、日本、美国和新加坡等国家和地区。 预计2006年国内丙酮总产量可增加至40万吨,市场供需缺口在35万吨。2006年国内丙酮进口市场环境仍将较为严峻,近年新建、扩建装置几乎都集中在亚洲地区,新增丙酮产品将不可避免地渗入到我国市场;同时亚洲地区诸多扩产项目集中投产等因素,还可能会继续加剧市场价格的震荡,丙酮市场竞争将更加激烈。预计到2010年,我国丙酮的总消费量将达到90万~95万t,仍存在较大的市场缺口。 建议采用具有世界领先水平的美国Sunoco/UOP公司工艺技术建设30万吨/年的苯酚/丙酮生产装置,同时考虑与上下游生产装置的配套问题,采用下游产品一体化的生产模式,如配套建设双酚A装置进而生产国内十分紧俏的下游产品聚碳酸酯和环氧树脂等形成产业链,形成苯酚/丙酮与其下游产品生产一体化,互惠、互利、互助,提高抵御市场风险的能力,共同参与国际竞争。
邻氨基苯酚的生产工艺与技术路线的选择
邻氨基苯酚的生产工艺与技术路线的选择 2.1 邻氨基苯酚的生产工艺 邻氨基苯酚的制备方法主要有铁粉还原法、硫化钠还原法、电解合成法和加氢还原法等四种方法。 2.1.1 铁粉还原法 邻氨基苯酚传统的合成方法是以邻硝基苯酚为原料,经水解,铁粉还原制得。还原过程中三废污染严重,产生大量的铁泥,产品包在铁泥中使得产品收率不高。 目前实验室和小型的企业生产多采用铁粉还原法。…… 2.1.2 硫化钠还原法 …… 2.1.2 电解合成法 电解合成法与传统的化学法相比,具有产物纯,产率高,污染小等优点。关于邻氨基苯酚的电解合成,曾有报道用滴Hg电极在醇的酸溶液中电解还原邻硝基酚以制备邻氨基苯酚,但Hg电极实施不便。 另外有一种新的电解合成方法,在碱性溶液介质中,以铜为阴极,电解还原邻硝基苯酚以制备邻氨基苯酚。该法有产物易分离,污染小的优点,在选定条件下,邻氨基苯酚的最大产率为97%,收率在90%以上。但是产率和产品纯度受电极电位的影响,而控制电极电位的稳定性仍在研究中。…… 2.1.3 催化加氢法 目前工业生产邻氨基苯酚一般采用催化加氢法,即在高压或者常压加氢装置
中,Ni,Pd,或Pt催化下还原邻硝基苯酚,其工艺简单,收率、纯度高,成本较低,邻硝基苯酚催化加氢制取邻氨基苯酚时醇水最佳体积比为2:1.邻硝基苯酚液相催化加氢制取邻氨基苯酚产品的纯度98%以上,收率接近80%。但是设备投资大,适合于大吨位的工厂生产。…… 2.2 邻氨基苯酚的生产工艺比较 表2.1 几种工艺技术比较表 2.3 邻氨基苯酚的生产工艺研究及进展 催化加氢常用的催化剂有兰尼镍、Pd/C等。以液相加氢法,采用混合溶剂,不但克服了三废污染严重问题,还提高了收率。 早期催化加氢法生产邻氨基苯酚,多以水为介质在强酸或强碱条件下反应。还原过程中由于邻硝基苯酚在水中的溶解度太小,因而以前的工作大多采用有机溶剂。但由于邻氨基苯酚在有机溶剂中溶解度较大,且很不稳定,因而收率一直不高。在强碱条件下邻硝基苯酚溶解良好,但催化剂活性下降,反应时间长,且邻氨基苯酚在碱性条件下极不稳定。在强酸性条件下邻硝基苯酚的溶解性不好,反应明显受传质阻力影响。反应到最后几乎不进行,但还有大量邻硝基苯酚未反应,且强酸性条件对反应设备腐蚀严重。 后期工作大多数采用醇作反应介质,其中绝大部分以甲醇为溶剂。以醇为溶剂邻硝基苯酚溶解良好,反应速度很快,催化剂用量很少。但反应放热太剧烈,产率不高。…… 详细内容参见六鉴网(https://www.360docs.net/doc/6711085780.html,)发布《邻氨基苯酚技术与市场调研报告》。
年产10000吨苯酚生产工艺设计开题报告
一、毕业论文内容及研究意义 1. 内容 设计过程中,查阅本论文的相关资料,了解苯酚合成工艺的进展,明确论文的目的和意义。 本文主要介绍合成苯酚各种工艺方法。目前,苯酚主要通过化学合成方法得到,国内外厂家主要是采用异丙苯法和磺化法制苯酚[1]。除此以外,在生产中还有其他工艺,如甲苯-苯甲酸法和氯苯法等。本文重点对异丙苯法进行了介绍,并将它的反应原理,生产工艺和方法分别进行了比较。 在以后的论文撰写过程中,将对异丙苯氧化合成苯酚的具体工艺流程,以及对吸收塔设备的各个部件进行设计,并将此反应过程中物料和能量进行衡算。同时我们将在论文中设计吸收塔设备的内容和步骤,塔设备的强度和稳定性计算。并用AutoCAD将化工工艺流程设计和设备设计,且对吸收塔和厂区设备布置图进行绘制,在最后将阐述苯酚的发展前景[2]。 2. 研究意义 苯酚是重要的化工产品,本文介绍了苯酚的性质和用途,以及苯酚的生产﹑市场需求和生产规模,发展前景。通过设计年产10000吨异丙苯法法生产苯酚工艺的最优方案。学习有关设计方面的知识,设备计算和化工原理基础数据的计算,以及用AutoCAD绘图的知识[3]。 二、毕业设计研究现状和发展趋势 1. 研究现状 国内现有生产厂家20多家,年生产能力20多万吨。其中异丙苯法约占70%以上,主要生产厂家有上海高桥石化公司、燕山石化公司、吉化集团公司、哈尔滨华宇股份有限公司等;磺化法约占26.7%,主要厂家有锦西化工总厂、太原化工厂、包头第一化工厂等;煤焦油精制法能力较小,主要是由各大钢铁公司焦化厂生产。以前我国苯酚生产主要是磺化法和煤焦油精制法,一般生产规模较小、产量低、成本高、环境污染严重。当时主要原料纯苯、硫酸、烧碱等供应紧张,不能满足苯酚生产的需要,影响了生产能力的发挥。由于我国苯酚的产量不能满足国内实际生产的需求,因而每年都得大量进口,且进口量呈不断增加的趋势,因此许多生产厂家准备新建或扩建苯酚生产能力。我国苯酚主要生产公司和生产能力见表1-1[4]。 表1-1我国苯酚主要生产公司和生产能力
苯酚检测方法
1、工业苯酚(GB/T 339-2001) 1.1技术指标: 1.1.1结晶点℃:≥40.2 1.1.2外观:熔融液体或结晶固体,无沉淀、无浑浊。 1.2仪器 一般化验室仪器、水银温度计、玻璃套管。 1.3检验方法 1.3.1外观:将液态试样置于50mL比色管中目测。溶液应无沉沉、无浑浊。 1.3.2结晶点的测定: 1.3. 2.1温度计: 温度范围℃ 0—50 液体:水银最小分度℃:0.1 1.3. 2.2玻璃套管结晶管:长150±2mm,内径:25±1 mm 保护管:长160±2mm,内径:38±2 mm 1.3. 2.3测定步骤 (1)样品预先不干燥。 (2)将试样倒入结晶管里,调节试样液面,高于主温度计中间泡上缘15mm,试样填充高度约在60mm。控制结晶管内试样温度不超过结晶点5℃,然后将结晶管插入保护管中,在室温下冷却。 (3)当试样温度下降至高于结晶温度3℃时,开始上下移动进行搅拌,搅拌时不得接触温度计和结晶管壁。 (4)当发现有结晶出现时,观察温度计读数,当温度恒定(此时停止搅拌)不再升高,继而重新下降,此恒定温度为结晶点,读取结晶点温度。 1.3. 2.4精密度:苯酚结晶点两次平行测定之差不应大于0.05℃,取平均值为测定结果。
3.3.1检测方法:按照高效液相色谱法(附录V D)测定。 3.3.2色谱条件:内径 4.6mm,长150mm内装十八烷基硅烷键合硅胶为填充剂的不锈钢色谱柱;以甲醇-水-冰醋酸(60:40:1)为流动相;流速0.5ml /分钟或1ml /分钟,检测波长为270nm。 3.3.3溶液配制: 3.3.3.1供试品溶液: 取本品约0.5g,精密称定,置100ml量瓶中用流动相溶解并稀释至刻度; 这个是水杨酸中含苯酚杂质的检测方法,波长和色谱柱条件合适,样品液浓度和灵敏度可根据具体情况再调整
苯酚市场分析
苯酚的市场分析生产现状和发展趋势产品简介 苯酚(phonel,C6H5OH)是一种具有特殊气味的无色针状晶体,有毒,是生产某些树脂、杀菌剂、防腐剂以及药物(如阿司匹林)的重要原料。也可用于消毒外科器械和排泄物的处理,皮肤杀菌、止痒及中耳炎。熔点43℃,常温下微溶于水,易溶于有机溶剂;当温度高于65℃时,能跟水任意比例互溶。能部蛋白质变性,其溶液沾到皮肤上可用酒精洗涤。小部分苯酚在空气中被氧气氧化为醌而成粉红色。遇三价铁离子变色,通常用此方法检验苯酚 市场分析 苯酚为一重要的基本有机化工原料,在合成树脂、塑料、医药、农药等诸多领域中的应用量很大。如它是合成水杨酸及水杨酸钠的起始原料,水杨酸又是合成阿司匹林的起始原料,每年我国用于合成水杨酸的苯酚数量就有十几万吨,近年来这方面的用量在不断增加,现已接近20万吨,占当年全国苯酚消耗量的12%左右。 近十多年来,我国经济在快速发展,市场对苯酚的需求量不断上升,且幅度较大。2001年,全国市场苯酚的消费量为45万吨;2005年,消费量达到73万吨;2007年,消费量达到100万吨;2009年,全国苯酚消费量为120万吨;2011年,消费量达到142万吨;2013年,消费量达到155万吨。目前,我国苯酚的市场需求量已达到170余万吨。从地域看,华东、华北、华南是我国苯酚消费的主要地区,其中华东地区消费量最多,一般占到全国的40%左右。从消费领域看,酚醛树脂、双酚A、水杨酸等是苯酚消费的主要产品,2013年这三大产品消耗苯酚的量分别为67万吨、34万吨和19万吨,分别占总量的43%、22%和12%左右。
国内市场苯酚旺盛的需求拉动了生产,近十多年来,我国苯酚的产量呈现不断增长的态势。2001年,我国苯酚产量为25万吨;2005年,苯酚产量达到44万吨;2009年,我国苯酚产量为53万吨,约占国内市场需求量的49.2%;2011年产量为70.4万吨,占国内市场需求量的49.3%;2013年,我国苯酚产量突破百万吨大关,达到119万吨,占国内市场需求量的76.7%。目前,我国苯酚的总生产能力已达到180万吨,年产量130万吨。长期以来,国产苯酚的产量远远不能满足市场的需求,每年都需要从国外大量进口,尤其是近十几年的进口量增长很快。2001年,我国苯酚进口量为21万吨;2005年,进口量为29万吨;2007年,进口量为46万吨;2009年,进口量达56万吨,2010年进口量为63万吨,比上年增长了12.5%;2011年进口量为76万吨,比上年增长了20.6%。庞大的需求,刺激了国内一些企业纷纷投资扩大苯酚的生产能力,全国苯酚产能快速增长,新增产量大量增加,国产苯酚对市场的供应量越来越大,自给率明显提升,进口苯酚的数量则逐年大幅下降。2011年,我国苯酚的进口量为76.2万吨,自给率为49.3%;2012年,苯酚的进口量降到59.4万吨,自给率上升到了62.6%;2013年,苯酚的进口量降到36.5万吨,自给率则上升到了76.7%。 目前全世界苯酚的生产能力已达1500余万吨,绝大部分企业均采用异丙苯法生产。经过多年的市场洗礼,全球苯酚的生产已集中到少数大型企业中。据有关资料显示,现在全世界苯酚生产企业的生产能力普遍达到几十万吨以上,全球前十大苯酚企业的年生产能力都达到了70万吨,最大的3家企业其生产规模都超过了100万吨,排名第一的美国化学公司年生产规模达到150万吨。 和国际苯酚生产巨头相比,我国企业的生产能力都比较小,且单套装置的生产规模也比
间氨基苯酚制备及产物分离工艺的研究_张敏
摘要 间氨基苯酚(MAP)是一种重要的精细化工原料和有机中间体,在石油化学工业、农药、医药、染料等领域的应用十分广泛。到目前为止,开发出了多种合成间氨基苯酚的工艺,主要有硝基苯磺化碱熔法、间苯二酚氨解法、间硝基苯酚电解法、苯胺羟基化法和间苯二胺盐酸水解法等,但它们大都分别存在着工艺落后、污染严重、成本较高和对设备要求较高等的问题。 本文重点研究了间苯二胺硫酸水解制备间氨基苯酚的合成新工艺和水解产物结晶分离制备MAP的纯化工艺两部分。具体研究内容和结果如下: 通过单因素实验和正交实验,考察了反应时间、温度、物料配比和酸的浓度对间苯二胺水解反应的影响,确定了最佳的工艺条件为:酸的浓度为23%,反应温度为190 ℃,间苯二胺与浓硫酸的摩尔比为1:2.10,反应时间为20 h。在此条件下间苯二胺的转化率达到了99.0%,间氨基苯酚的收率为43.8%,间苯二酚的收率是54.4%。通过动力学实验,分别得到了在190 ℃、200 ℃、210 ℃温度条件下间苯二胺水解反应的速率方程,并求得水解反应的频率因子和活化能。 鉴于间苯二胺硫酸水解制备间氨基苯酚工艺的水解产物包含间氨基苯酚、间苯二酚和少量间苯二胺三种组分的情况,先用乙酸丁酯萃取分离间苯二酚,然后对间苯二胺和MAP进行结晶分离得到纯净的MAP,并确定了结晶工艺条件。其条件为:溶液的pH值为7.08,结晶温度为15 ℃,结晶时间为40 min,搅拌转速为500 r·min-1。 本文提出了硫酸法水解制备间氨基苯酚的新工艺,优化了水解工艺条件,得出不同温度条件下的间苯二胺水解反应的速率方程,并对产物进行先萃取后结晶的分离工艺进行研究。对此未见国内外文献报导,为该工艺的深入研究打下了基础。 关键词:间氨基苯酚 间苯二胺 间苯二酚 萃取 结晶
苯酚 性质、用途与生产工艺
苯酚性质、用途与生产工艺 概述 苯酚(英文Phenol)又称石炭酸,分子式C6H5OH,常温下纯净的苯酚是无色针状晶体,具有特殊的气味(与浆糊的味道相似),酸性极弱(弱于碳酸),熔点是43℃,凝固点40.9℃,比重1.071,沸点182℃,燃点79℃。露置在空气中因小部分发生氧化而显粉红色,在有氨、铜、铁存在时会加快变色,在潮湿空气中,吸湿后,由结晶变成液体。常温时苯酚含水27%就成为均匀液体,随含水率继续增加,液体分二层,上层为苯酚在水中溶液;下层为水在苯酚中溶液。苯酚含水时其凝固点急剧下降。含水1%凝固点为37℃,含水5%凝固点为24℃。苯酚剧毒,空气中最大允许蒸汽浓度0.005mg/L,其浓溶液对皮肤有强烈的腐蚀性,如果不慎沾到皮肤上,应立即用酒精洗涤。实验室可用溴(C6H5—OH + Br2 = C6H2(Br3)—OH + 3HBr生成白色沉淀2,4,6-三溴苯酚,十分灵敏)及FeCL3(6C6H5OH+FeCL3 →H3[Fe(C6H5O)6] +3HCl生成〔Fe(C6H5O)6]3-络离子呈紫色)检验. 溶解性 室温微溶于水,能溶于苯及碱性溶液,易溶于乙醇、乙醚、氯仿、甘油、丙三醇、冰醋酸等有机溶剂中,难溶于石油醚。在水中的溶解度为:11℃时为4.832%;35℃时为2.360%;58℃时为7.330%;77℃时为11.830%;84℃时苯酚与水可以任意比例混溶。 水中溶解度(g/100ml) 不同温度(℃)时每100毫升水中的溶解克数: 8.3g/20℃;混溶/40℃ 与浓溴水的反应 苯酚与溴水的取代反应,由于苯酚能溶解难溶于水的三溴苯酚,为了防止没有反应完的苯酚对三溴苯酚的溶解作用,实验时要使用浓溴水,最好用饱和溴水。同时,苯酚水溶液要尽量稀一些。实验时还应注意控制溴水的用量,因过量的浓溴水会跟三溴苯酚反应生成黄色沉淀,因此,溴水的量也不要过多。当出现白色沉淀时,立即停止加溴水,如果改向溴水中滴加苯酚,生成
苯酚市场分析报告
2.13 苯酚 苯酚(Phenol,CAS:108-95-2,EINECS:203-632-7)俗名石炭酸,分子式C6H5OH,相对密度1.071,熔点42~43℃,沸点182℃,燃点79℃。苯酚呈无色结晶或结晶熔块,具有特殊气味(与浆糊的味道相似)。放置空气中或日光下被氧化逐渐变成粉红色至红色,在潮湿空气中,经过吸湿后,由结晶变成液体。酸性极弱(弱于碳酸),有毒,有强腐蚀性。室温下微溶于水,能溶于苯及碱性溶液,易溶于乙醇、乙醚、氯仿、甘油等有机溶剂中,难溶于石油醚。 苯酚可来源于炼焦副产回收,早年工业合成采用苯磺化碱熔法,由于消耗高、污染严重已被淘汰,现在全球苯酚的生产都采用异丙苯氧化法工艺。 苯酚是一种重要的有机化工原料,是丙烯和苯的重要衍生物之一,其用途非常广泛。苯酚在塑料工业中主要用于生产酚醛树脂,生产双酚A,最终生产环氧树脂和聚碳酸酯;在医药工业中用于生产阿斯匹林、氯奎、酚酞和酚乙酸等药物,以及用作防腐剂和杀菌消毒剂;在有机合成工业中用于生产水杨酸、苦味酸、二苯醚、己二酸和烷基酚等。 2.1 3.1世界供需分析及预测 近年来,全球苯酚生产企业兼并及投资活动较为活跃。2013年,世界苯酚的生产能力约为1140万吨/年,产量约为945万吨,开工率为82.9%。世界苯酚的生产主要集中在亚洲、北美和西欧。 表2.13-1 2013年世界各地区苯酚供需状况
2.1 3.1.1世界供应状况分析及预测 近年来,全球苯酚生产企业兼并及投资活动较为活跃,经过一系列的兼并重组,目前全球苯酚生产企业的前三甲为英力士苯酚公司、日本三井化学和壳牌公司。其中,英力士苯酚公司的苯酚产能居行业首位,在德国格拉德贝克、比利时安特卫普和美国亚拉巴马州均设有工厂,总产能达到187万吨/年,占全球总产能的17.4%。英力士苯酚公司已和中石化扬子石化合资,在江苏扬州建设65万吨/年酚酮装置,其中苯酚产能为40万吨/年,目前该项目报告已获批,2014年开工建设,预计2016年建成投产。苯酚产能排在全球第二位的是日本三井化学,三井化学在新加坡设有一套生产装置,在日本设有三套生产装置,其中大阪装置产能为20万吨/年,千叶有两套装置,产能分别为19万吨/年和23万吨/年,其中23万吨/年的装置为三井化学和出光兴产合资建设。2006年,日本三井化学和中石化以50:50的比例合资,成立了上海中石化三井化学有限公司,2011年该公司开工建设一套40万吨/年酚酮装置,苯酚产能为25万吨/年,预计2014年底建成投产。苯酚产能排在全球第三位的是壳牌公司,其在美国的苯酚装置产能为60万吨/年,占全球总产能的5.6%。 表2.13-2 2013年苯酚世界主要生产企业概况
叔丁基对苯酚的制备工艺
4-叔丁基苯氯磺酸酯的合成试验报告 一、目的 在实验室验证、优化4-叔丁基苯氯磺酸酯的合成工艺路线。 二、原理 主反应: OH NaOH ONa 2 OSO 2CL SO 2CL ONa 付反应: OH OH SO 22 CL 三、物化数据 四、合成步骤及反应现象 1. 在500ml 的四口烧瓶中加入96%的氢氧化钠10.5克(0.25mol ),40ml 的水,37.6克叔 丁基对苯酚(0.25mol ),搅拌加热至100℃直至酚溶解。 实验现象:酚盐的的制备时,注意反应液是否完全溶解于水溶液中,保证酚完全生成钠盐。反应液应为黄绿色透明状,并有泡沫产生。 2. 溶解后等温度稍降,加入正辛烷200ml 并加装分水器,搅拌下加热至回流,分水3小时。 3. 将水分完全除尽,大约蒸去10ml 的正辛烷,剩余物降温至室温备用。 实验现象:分水时一定将水分完全除尽,约为3~4小时,分完水后反应液呈乳白色泡沫状固体。 4. 将剩余物预冷至- 40℃以下,然后在滴液漏斗中加入33.75克磺酰氯(0.25mol ),搅拌下 缓慢滴加,并控制温度在- 35℃以下,反应约4小时。 实验现象:成酯反应的反应温度尽可能在-35℃以下,温度高易反应生成付产物,反应完成后升温到室温反应液呈黄色粘稠液体,内有白色沉淀。 5. 反应完成后升温至室温,反应液进行减压抽滤(抽滤过程很慢),滤液先蒸去正辛烷后
再进行减压蒸馏并收集100~130℃/1mmHg的馏分。 实验现象:馏出液为淡黄色透明油状物,4℃静止过夜有白色针状晶体产生。6.馏出液4℃静止过夜,析出白色固体,过滤,取样分析。 7.滤液再进行减压蒸馏,并收集114~116℃/1mmHg的馏分,取样分析。 实验现象:产品为淡黄色透明油状物。 由于反应1、4反应温度较高,致使反应收率较低。 在-35℃以下反应,收率可以达到60%。 六、检测结果: 实验1取样进行HNMR检测,结果附后。 七、小试工艺流程图
我国市场上苯酚的需求量
长期以来,我国市场上苯酚的需求量不断增加,但国内苯酚的产量远远不能满足市场的需求,每年都要从国外进口,近年来进口量增加较多。 苯酚在合成树脂、塑料、医药、农药等诸多领域中的应用量很大。如:苯酚是合成水杨酸及水杨酸钠的起始原料,水杨酸又是合成阿司匹林的起始原料,每年我国用于合成水杨酸的苯酚就有十几万吨,占当年我国苯酚消耗量的十分之一左右。 年需求量增幅较大 目前我国有十余家企业生产苯酚,全国总生产能力达到160万吨。其中主要的生产企业有6家,它们是:上海高桥石化,年产能为36万吨;中沙合资天津石化,年产能为35万吨;北京燕山石化,年产能为26万吨;广东建滔石化,年产能为20万吨;蓝星哈华宇石化,年产能为12.5万吨;吉林石化,年产能为12万吨。2010年,我国苯酚产量为69万吨,占国内市场需求量的49%;2011年产量为70万吨,占国内市场需求量的45%,比上年下降了4个百分点。 近几年,我国市场对苯酚的需求量逐年上升,且上升幅度较大。2009年,全国苯酚消费量为120万吨;2010年,消费量达到140万吨,比上年增长了16.7%%;2011年,消费量达到157万吨,比上年增长了12.1%。从地域看,华东、华北、华南是我国苯酚消费的主要地区,其中华东地区消费量最多,占到全国的40%左右。从消费领域看,酚醛树脂、双酚A、水杨酸是苯酚消费的主要产品,2011年这三大产品的苯酚消耗量分别为60万吨、40万吨和15万吨,分别占总量的大约40%、25%和10%。 国内售价背离需求面 由于国产苯酚的产量远远不能满足市场的需求,我国每年都要从国外大量进口。近几年进口量增长很快。2009年,我国进口苯酚达56万吨;2010年进口量为63万吨,比上年增长了12.5%;2011年进口量为76万吨,比上年增长了20.6%。 我国苯酚的进口地主要在华东地区,由于华东地区苯酚生产企业的产量大部分配套供应了下游工厂,较少供应市场,而华东地区对苯酚的需求量又很大,因此就需大量进口。 虽然最近几年我国市场苯酚的需求较为旺盛,但是其销售价格由于受到国内外市场多种因素的影响,并非呈现出单边上升的态势。2011年国内苯酚的市场价格呈现出下降走势:2011年1月,我国市场苯酚销售价格为14000元/吨;2011年7月,销售价格为每吨12200
苯酚的工业生产合成路线
四、简述制备以下产品的工艺过程,并写出反应方程式 C l SO 3H N H 2 SO 3H 答:氯苯用过量的98%的硫酸在100℃左右进行一磺化,生成4-氯苯磺酸,向磺化液中加入稍过量的98%的发烟硝酸进行一硝化,得3-硝基-4-氯苯磺酸,后者在水介质中与亚硫酸氢钠进行磺基置换氯的反应,得2-硝基苯-1,4-二磺酸,最后经硝基还原,即得到2- 氨基苯-1,4-二磺酸(即苯胺-2,5-双磺酸)。其合成路线如下: C l C H 3SO 3H C l NO 2 SO 3H SO 3H NO 2SO 3H SO 3H N H 2 SO 3H 五、总结苯酚的工业生产曾用过哪些合成路线,写出反应方程式,标明分别属于哪类单元反应,指出各种路线的优缺点。 答:1、异丙苯法: CH 2CHCH 3C CH 3CH 3H C-烷化 氧化 C CH 3 CH 3O OH OH 酸性重排 分解 此法优点是,原料费用低,排放废液很少。但此法必须与石油化工相结合,利用石油馏分裂解时产生的丙烯进行大规模生产。 2、苯的磺化-碱熔法:
SO 3 H O H 磺化水解(碱熔) 此法的优点是技术要求不高、苯酚质量好。缺点是消耗大量的硫酸和氢氧化钠,废液多,工艺落后。 3、氯苯的气固相接触催化水解法: C l O H 氯化气固相接触催化水解 此法与苯用氯化氢的氧化氯化法生产氯苯相结合,理论上只消耗苯,但由于两步反应的单程转化率都比较低,反应混合物的分离和后处理相当复杂,并且有大量含酚废水需处理。 4、氯苯的高压液相碱性水解法: C l O H 氯化高压液相碱性水解 此法的缺点是消耗大量的氯气和氢氧化钠,并且需要使用耐高温、高压的管式反应器。 5、苯甲酸的氧化-脱羧法: O H C O O H 氧化氧化-脱羧CH 3 此法的优点是以甲苯为起始原料,苯甲酸可在一个反应器完成氧化和脱羧反应,不需要依赖石油化工,缺点是有副产的焦油废渣需处理,成本高于异丙苯法。 重氮盐的脱氮反应也可以制取酚类,但常用于制取萘酚蒽酚等;苯的直接氧化制苯
苯酚合成路线
苯酚合成路线 合成苯酚的方法主要有磺酸盐碱熔法、氯苯水解法、环己酮一环己醇法、甲苯一苯甲酸法、异丙苯氧化法、苯直接氧化法、直接加成法等生产方法;其中异丙苯法是目前世界上生产苯酚最主要的方法,其生产能力约占世界苯酚总生产能力的92%。化学发展方向是向绿色化学前进,苯直接氧化法,尤其是催化剂催化法符合绿色化学的要求是研究的重点,近来也取得了一定的成绩.关键词:苯酚,合成 苯酚及其同系物存在与煤焦油中,可以用NaOH溶液从各馏分中提取出来.但是这远远不够工业上用的,促使科研工作者找合成方法.人们开始采用化学方法含成苯酚,最早的苯酚化学合成工艺是1923年由美国孟山都公司首次研究开发成功的苯磺化法,于该方法腐蚀性强以及污染严重等原因,目前已经基本上被淘汰。后来又有新的合成方法出现如:氯苯水解法,环己酮一环己醇法,甲苯一苯甲酸法、异丙苯氧化法.目前主要的合成方法是异丙苯氧化法. 磺酸盐碱熔法 把加热到170℃的苯蒸汽通如浓硫酸中,一部分苯磺化产生苯磺酸,一部分苯把生成的水带出. 生成的苯磺酸用亚硫酸钠中和,得到的苯磺酸钠与氢氧化钠一起熔融,生成苯酚钠: 在苯酚钠的水溶液中通如二氧化硫,就得到苯酚: 亚硫酸钠在生产过程中循环利用.这是使用较早的方法,流程复杂,操作麻烦,原子利用率低,利用率只有36. 7%;在生产过程中产生大量的二氧化硫,而且由于过程中大量使用酸和碱,设备腐蚀严重,每年均需要更换部分设备,维修费用大. 氯苯水解法 苯蒸汽、氯花氢和空气在230℃下通过催化剂,可以得到用做原料的氯苯: 氯苯在425℃一定压力和催化剂存在下用过热的水蒸气水解,可产生苯酚和氯花氢: 此方法对设备要求不高,生产成本较低.原料的生产可以在常压,不太高的温度下进行.而且氯化氢可以循环利用.但是该反应第二不要在高温下进行,反应需要消耗大量的酸和氢氧化钠,对设备腐蚀严重,苯酚收率不高,原子利用率为61. 6%. 环己酮一环己醇法 此法分三步进行,(1)苯加氢通常用Ni/A1z0,或reney-ni作催化剂,反应在200一250℃和0. 03一5. 5 MPa下进行 环己烷氧化为环己酮和环己醇的混合物氧化反应的反应温度为155℃,压力为1一1. 5 MPa
苯酚
苯酚生产技术的进展 [摘要]本文概述了苯酚的生产技术及其最新进展,指出了异丙苯路线仍是今后生产苯酚的主要路线,以及该路线目前的研究重点;丙烯循环工艺有可能用于异丙苯路线的改造;苯直接氧化路线中以N20为氧化剂的工艺有可能实现工业化。[关键词]苯酚;异丙苯;丙烯;丙酮;氧化 由于聚碳酸酯需求的增长,双酚A成了苯酚的主要衍生物,2001年全球双酚A 消耗了苯酚量的36%、苯酚的树脂类物质消耗了苯酚量的30%、己内酰胺消耗了苯酚量的10%。在美国,双酚A消耗量占苯酚量的41%,西欧双酚A的消耗量更高,占苯酚量的46%。另外,工程塑料及医药行业对苯酚也有一定的需求。 目前,异丙苯路线是制备苯酚的主要方法,由于受丙酮市场的影响,世界上许多公司都在致力于开发不联产丙酮的苯酚路线,包括苯直接氧化制苯酚路线、Mitsui石化制备苯酚的丙烯循环工艺等。本文对苯酚的生产技术及其进展作了概述。 1.苯酚生产工艺 1.1异丙苯法制苯酚/丙酮 异丙苯法是生产苯酚/丙酮的主要方法。该法以丙烯和苯为原料,经烷基化制得异丙苯,然后氧化为过氧化氢异丙苯(cHP),最后分解成苯酚和丙酮。每生产1 t苯酚大约可副产0.62 t丙酮。异丙苯氧化为CHP通常在100℃、常压或几个大气压下进行,用空气作氧化剂,在碱性介质内进行。CHP的分解,一般用10%硫酸作催化剂,在45~75℃下进行。也有采用离子交换树脂为催化剂,使分解的产物不必中和,从而降低了生产成本。 1.2甲苯法制苯酚 该法由美国Dow化学公司开发,在1962年实现工业化。由甲苯与空气在钴盐催化剂作用下液相氧化生成苯甲酸,苯甲酸再在铜盐作用下与空气和水蒸气作用生成苯酚。该工艺流程较为简单,投资小,可根据市场需求改产苯甲酸或苯甲醛。由于在氧化脱羧过程中产生一些焦油状物,给苯酚收率及催化剂的使用寿命带来一定影响。甲苯法成本比异丙苯法高,没有联产品,只副产c02和焦油。 1.3氯苯法制苯酚 该法可采用氯苯在10%~15%的烧碱或纯碱溶液中,于360~390℃、28~30 MPa下进行液相水解,然后用氯化氢使苯酚从钠盐中游离出来。也可采用磷酸钙/化硅作催化剂,在400~450℃下使氯苯水解生成苯酚。该法氯苯可由苯与氯气反应或苯与氯化氢/空气进行氧氯化反应制得,投资较大。 2.技术进展 2.1异丙苯路线技术 2.1.1 Exxon Mobil公司苯酚生产中的催化精馏技术和异丙苯制苯酚的固体酸催化剂. Exxon Mobil公司的催化精馏技术[1,2]将反应过程和丙酮精馏过程结合在一起,降低了能耗,具有潜在的节能效益。此外,由于用固体酸催化剂[3,4]替代了通用的硫酸催化剂,还可免去产物的中和过程。催化剂床层中装填了直径为1 mm 的丸形粒子,床层呈松驰状,充裕的空隙间隔足以保证液相物流从床层上方向下流动,丙酮蒸汽从床层下方向上流动。纯度为99.57%的丙酮作为反应器顶端产物不断地被回收,同时从反应器塔底得到苯酚和其它重组分,再去下游精馏工序进行处理。通人反应器的液相CHP的流速,足以保持催化剂床层的湿度,实现等
苯酚文献综述论文
《文献检索与论文写作》课程论文 论文题目:苯酚工艺设计 学生姓名:罗苗苗 学号:200908014227 专业:化学工程与工艺 年级:2009级化工2班 得分:
苯酚工艺设计 摘要 本文概述了苯酚的生产技术及其最新进展,指出了异丙苯路线仍是今后生产苯酚的主要路线,以及该路线目前的研究重点;丙烯循环工艺有可能用于异丙苯路线的改造;苯直接氧化路线中以N20为氧化剂的工艺有可能实现工业化。 关键词:苯酚;异丙苯;丙烯;丙酮;氧化 Phenol Process of The T echnological Design ABSTRACT This article provides an overview of phenol production technology and its latest development, pointed out the toluene-benzoic route is still the future production of phenol to the main line, as well as the route of current research. KEY WORDS:phenol;toluene-benzoic ;propylene;acetone;oxidize
一、课题背景 苯酚,又称石炭酸,是一种重要的基础有机化工原料,主要用于生产酚醛树脂、己内酰胺、双酚A、水杨酸、苦味酸、烷基酚,己二酸等化工产品及中间体。苯酚的市场需求量大,在各种化工产品中其产量居前十位。在合成橡胶、农药、医药、染料、香料、涂料等领域都有重要应用。此外,还可用作溶剂、试剂和消毒制剂等。近年来,由于电子通讯、汽车工业和建筑业的迅猛发展,导致双酚A和酚醛树脂需求的快速增加,从而带动苯酚的强劲增长。 目前,工业生产苯酚的工艺主要有磺化法、异丙苯法和甲苯-苯甲酸法等,其中异丙苯法是目前主要生产方法。磺化法是最早的苯酚生产工艺,因为工艺落后、反应复杂、消耗大量的酸﹙硫酸﹚和碱﹙氢氧化钠﹚、设备腐蚀严重和维修费用高等问题,目前基本上已被淘汰。异丙苯法由于采用了短缺原料—丙烯,且生产成本受副产物丙酮的影响,制约了苯酚产量的提高。甲苯-苯甲酸法也存在环境污染等问题。因此,考虑苯酚生产的经济效益和环境问题,不仅需要对现有生产工艺进行改进,而且还要开发新的合成方法和工艺路线。 二、国内苯酚产业的现状 2.1 生产情况 我国苯酚的工业生产始于20世纪50年代,最初主要采用苯磺化法和煤焦油精制法进行生产,生产规模小,产量低,成本高,环境污染严重,并且产量远远不能满足国内实际生产的需求。1970年北京燕山石化公司建成我国第一套异丙苯法苯酚生产装置,生产能力为1万吨/年,此后,上海高桥化工厂建成生产能力为1.6万吨/年的异丙苯法苯酚生产装置,但产量仍不能满足实际生产的需求,供求矛盾依然突出。 1986年,北京燕山石化公司引进日本三井油化公司技术建成一套生产能力为5万吨/年异丙苯法苯酚生产装置,2003年扩建到15万吨/年;1996年吉林化学工业公司染料厂引进美国UOP公司技术建成一套5万吨/年异丙苯法苯酚生产装置,2003年扩建到7.5万吨/年;1997年哈尔滨华宇公司引进美国UOP公司技术建成一套生产能力为1.6万吨/年异丙苯法苯酚生产装置,2003年扩建到2.8万吨/年,2000年上海高桥石化公司引进Kellog技术建成一套生产能力为7.5万吨/年异丙苯法苯酚生产装置。此外还有一些苯酚生产厂家采用苯磺化法进行生产。
生产苯酚新工艺详细介绍
1.以N 2O 为氧化剂 Solutia 公司(原Monsanto 公司)和俄罗斯Boreskov 催化研究院共同开发了AlphOx 工艺 。该工艺以改性的ZSM 一5分子筛为催化剂,采用己二酸装置副产的N 20为氧化剂,以苯为原料直接合成苯酚。以苯计的苯酚收率为0.4 kg / (kg ·h),即苯酚选择性可达37%。但在Solutia 公司位于美国佛罗达州Pensacola 的示范装置,催化剂的活性较差,且寿命只能持续24 h ,苯酚选择性小于30%因此要实现工业化尚存在许多问题。 Gopalakrishnan 等通过湿法研磨改进了Fe —ZSM 一5催化剂,得到了晶粒大小接近220 nm 的催化剂,虽然选择性只略有提高,催化剂寿命大幅度延长,在440 ℃下反应3 h 后,催化剂失活率为33% ,较之原失活率(87%)有很大的改进:以N 2O 为氧化剂,需要保证其来源充足,气态N 20的生产、储存和使用都 很方便,单独生产价格很高,凡现在没有较成熟的原位生产技术。中试结果表明,催化剂的连续运转周期较短,苯酚选择性较低 。因此,以N 2O 为氧化剂的苯一 步氧化法的应用和推广受到限制。 2.以H 2O 2为氧化剂 用H 202 为氧化剂,惟一的副产物足H 2O ,原子经济性高(83.9%),对环境 没有污染,H 202是一种清洁型氧化剂。以H 202为氧化剂的苯一步氧化法的关键在 于如何最大限度地提高笨酚的选择件和H 2O 2 的有效利用率。因为H 2O 2 极易分解损失,而且与苯相比苯酚更易被氧化成醌类和焦油类等物质。 Peng 等硼设计了离子液体一水 相反应体系,十二烷基磺酸铁催化剂和苯溶于离子液体相,H 202和水成一相,反应生产的苯酚可进入水相,避免在离子液体 相中被深度氧化,苯的转化率达54% ,苯酚的选择性几乎达100% ,而且包含催化剂的离子液体相和水相分离简便,可实现含催化剂离子液体的重复使用。Liu 等 利用微乳液催化有效实现了苯氧化合成苯酚,使苯酚的选择性达剑92.9% ,H 2O 2的有效利用率达93.1% Molinari 等采用PDMS 膜和NaX —PDMS 膜反应装置研究厂苯与H 202 的氧化 反应,反应体系分成两相,苯酚的选择性接近100% :尽管苯转化率很低,仅为1%左右,但在苯氧化合成苯酚体系中引入膜催化反应的思路很值得借鉴。 3.仲丁基苯法 仲丁基苯法以乙烯装置和炼厂气的副产物中的正丁烯为原料,与苯发生烷基
苯酚的生产工艺与技术路线的选择
苯酚的生产工艺与技术路线的选择 2.1 苯酚生产工艺 在第一次世界大战以前,苯酚主要从煤焦油中提炼获得。目前苯酚的生产主要有七种方法,即异丙苯法、甲苯氧化法、苯直接氧化法、磺化法、氯苯水解法、拉西法、环己烷法等。除甲苯氧化法以甲苯为原料外,其余六种方法均以苯为原料。 2.1.1 异丙苯法 异丙苯法也叫异丙苯氧化法,…… 2.1.2 甲苯氧化法 甲苯氧化法也称甲苯-苯甲酸法,此法是唯一一种不用苯作原料合成苯酚的方法。…… 2.1.3 苯直接氧化法 苯直接氧化法是以苯为原料,直接氧化制取苯酚的方法,也称苯羟基化法。…… 2.1.4 磺化法 ……
2.1.5 氯苯水解法 …… 2.1.6 拉西法 …… 2.1.7 环己烷法 …… 2.2 苯酚生产工艺研究及进展 第一次世界大战以前,苯酚主要从煤焦油中提炼得到,随着苯酚需求量的不断增加,人们开始采用化学合成法生产苯酚。 最早的苯酚化学合成工艺是1923年由美国孟山都公司首次研究开发成功的苯磺化法,即由苯经磺化生产苯磺酸钠,再经水解得到苯酚。由于该方法腐蚀性强以及污染严重等原因,目前已经基本上被淘汰。此后又相继出现了氯苯法、甲苯氧化法、拉西法、环己烷法、异丙苯法以及苯直接氧化法等生产方法。 …… 2.2.1 异丙苯法的工艺改进及进展 对于异丙苯法苯酚生产工艺的改进主要集中在氧化工序的节能降耗、完善CHP提浓和分解工序等方面。 …… 2.2.2 苯直接氧化法的研究进展 ……
2.2.3 磺化法的研究进展 …… 2.2.4 Shell公司“Spam”新工艺 …… 2.3 苯酚生产工艺研究方向 传统的合成苯酚的方法存在浪费原料、副产物多、不利于环保等缺点。 …… 2.4 苯酚几种工艺路线的技术经济比较 目前,世界苯酚的生产主要是异丙苯法,还有甲苯氧化法、苯直接氧化法、磺化法、氯苯水解法等。几种苯酚生产工艺的原料消耗对比见下表。 表2.1 几种苯酚生产工艺的原料消耗对比表 表2.2 几种苯酚生产工艺的公用工程消耗对比表 2.5 苯酚生产工艺路线的选择 经过几十年的生产实践,优胜劣汰,有些路线尽管在世界上曾实现了工业化,但由于种种原因而逐渐被淘汰了。在国外,…… 2.6 苯酚质量指标 目前我国苯酚执行中华人民共和国国家标准GB/T339-2001,该标准是等效采用美国试验与材料协会标准ASTMD 2439-1996《精制苯酚》对GB339-1989工业合成苯酚的修订。 表2.3 苯酚质量指标表
邻羟基苯乙酮生产工艺
邻羟基苯乙酮项目技术调查报告 有机0911 朱耀 43 第一章产品及原料介绍 1.1 邻羟基苯乙酮 中文名称:2-羟基苯乙酮;1-(2-羟苯基)-乙酮;邻羟基苯乙酮;邻乙酰基苯酚;英文名称:1-(2-hydroxyphenyl)-Ethanone;o-hydroxy-acetophenon;1-(2-hydroxyphenyl)ethanone;;2'-hydroxy-acetophenon CAS: 118-93-4 ,分子式: C8H8O2 ,分子质量:136.15 ,沸点: 213℃,熔点: 4-6℃,性质描述: 浅绿至黄色油状液体。沸点 213℃/95.6kPa(717mmHg),106℃/2.3kPa(17mmHg),相对密度 1.131,折光率 1.5584,闪点98。 用途: 心律平的中间体。 结构式: 1.2苯酚 相对分子量或原子量94.11,密度1.071,熔点(℃)40.3,沸点(℃)182 ,折射率1.5425(41),毒性LD50(mg/kg) 大鼠经口530。 性状:无色或白色晶体,有特殊气味。在空气中因为被氧化而显粉红色 溶解情况:溶于乙醇、乙醚、氯仿、甘油、二硫化碳等。易溶于有机溶
液,常温下微溶于水,当温度高于65℃时,能跟水以任意比例互溶。 用途:用于制染料合成树脂、塑料、合成纤维和农药、水杨酸等。作外科消毒,消毒能力大小的标准(石炭酸系数)。 制备或来源:由煤焦油经分馏,由苯磺酸经碱熔。由氯苯经水解,由异丙苯经氧化重排。 其他:加热至65℃以上时能溶于水(在室温下,在水中的溶解度是9.3g,当温度高于65℃时能与水混溶),有毒,具有腐蚀性如不慎滴落到皮肤上应马上用酒精(乙醇)清洗,在空气中易被氧化而变粉红色。在民间有土方用石炭酸来治皮肤顽疾,以毒攻毒,如用来治脚底起泡。 1.3乙酐 中文名称:乙酸酐,英文名称:Acetic Anhydride。别名:醋酸酐;醋酐;乙酐;Ac2O 无水醋酸; 分子式:C4H6O3;(CH3CO)2O。外观与性状:无色透明液体,有刺激性气味(类似乙酸),其蒸气为催泪毒气。分子量:102.09 。蒸汽压:1.33kPa/36℃ 闪点:49℃。熔点:-73.1℃。沸点:138.6℃ 溶解性:溶于苯、乙醇、乙醚,氯仿;渐溶于水(变成乙酸)。 密度:相对密度(水=1)1.08;相对密度(空气=1)3.52 。 折光率:n20D 1.450 。稳定性:稳定。 1.4氯苯 中文名称:氯苯、一氯代苯。英文名称:chlorobenzene、monochlorobenzene CAS: 108-90-7 。分子式: C6H5Cl 。分子量: 112.56 。熔点(℃): -45.2 沸点(℃): 132.2 。相对密度(水=1): 1.10 。相对蒸气密度(空气=1): 3.9 饱和蒸气压(kPa): 1.33(20℃) 。临界温度(℃): 359.2 。临界压力(MPa): 4.52 辛醇/水分配系数的对数值: 2.84 。闪点(℃): 28。引燃温度(℃): 590 爆炸上限%(V/V): 9.6。爆炸下限%(V/V): 1.3 。外观与性状:无色透明液体,具有不愉快的苦杏仁味。 溶解性:不溶于水,溶于乙醇、乙醚、氯仿、二硫化碳、苯等多数有机溶剂。主要用途:作为有机合成的重要原料。