车梯形螺纹
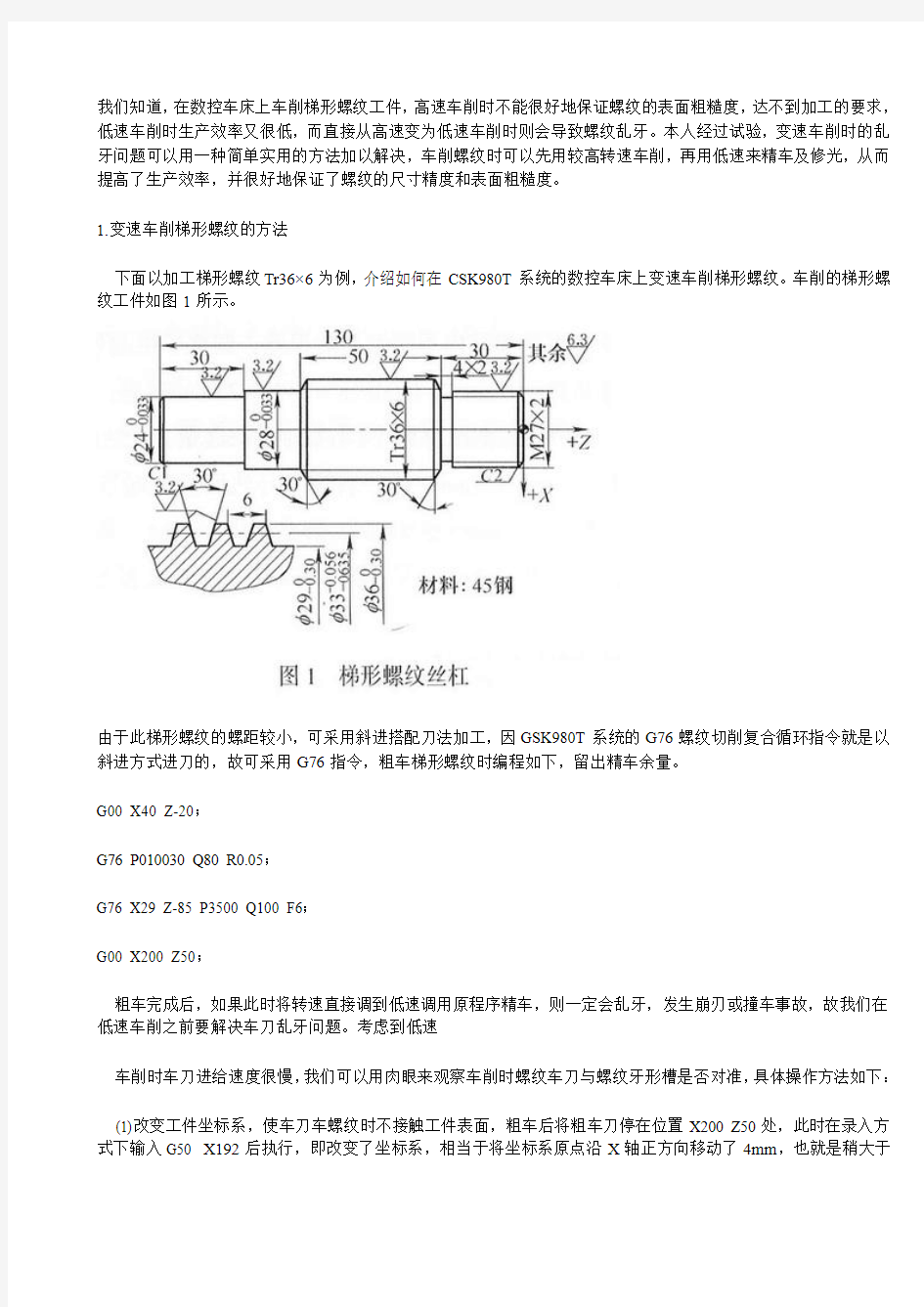

我们知道,在数控车床上车削梯形螺纹工件,高速车削时不能很好地保证螺纹的表面粗糙度,达不到加工的要求,低速车削时生产效率又很低,而直接从高速变为低速车削时则会导致螺纹乱牙。本人经过试验,变速车削时的乱牙问题可以用一种简单实用的方法加以解决,车削螺纹时可以先用较高转速车削,再用低速来精车及修光,从而提高了生产效率,并很好地保证了螺纹的尺寸精度和表面粗糙度。
1.变速车削梯形螺纹的方法
下面以加工梯形螺纹Tr36×6为例,介绍如何在CSK980T系统的数控车床上变速车削梯形螺纹。车削的梯形螺纹工件如图1所示。
由于此梯形螺纹的螺距较小,可采用斜进搭配刀法加工,因GSK980T系统的G76螺纹切削复合循环指令就是以斜进方式进刀的,故可采用G76指令,粗车梯形螺纹时编程如下,留出精车余量。
G00 X40 Z-20;
G76 P010030 Q80 R0.05;
G76 X29 Z-85 P3500 Q100 F6;
G00 X200 Z50;
粗车完成后,如果此时将转速直接调到低速调用原程序精车,则一定会乱牙,发生崩刃或撞车事故,故我们在低速车削之前要解决车刀乱牙问题。考虑到低速
车削时车刀进给速度很慢,我们可以用肉眼来观察车削时螺纹车刀与螺纹牙形槽是否对准,具体操作方法如下:
(1)改变工件坐标系,使车刀车螺纹时不接触工件表面,粗车后将粗车刀停在位置X200 Z50处,此时在录入方式下输入G50 X192后执行,即改变了坐标系,相当于将坐标系原点沿X轴正方向移动了4mm,也就是稍大于
一个牙高的距离。此时将车床主轴转速调低,如调到25r/min,重新运行程序,粗车刀将车不到工件表面,在接近工件表面的位置移动。如图2所示。
(2)使车刀与车出的梯形螺纹槽重新对正,由于车刀进给速度很慢,此时我们可以看出车刀与原先车出的梯形螺纹槽是不重合的,车刀偏移了一小段距离,如图2 所示,目的就是要使车刀重新对准车出的梯形螺纹槽。操作的原理跟在数控车床上车削多头螺纹是一样的,就是通过改变螺纹车刀车削前的轴向起点位置来达到目的,即修改上述程序段G00 X40 Z-20中的Z-20。我们可以通过肉眼判断需调整的大慨距离,如可先将Z-20改为-21,运行程序后,发现车刀与车出的梯形螺纹槽还没有完全对正。则再修改Z值,重新运行程序,直到车刀与梯形螺纹槽完全对正。如图3所示。
3)恢复原来的工件坐标系,开始精加工为了便于理解和不易出错,仍将车刀移到X200 Z50位置,在录入方式下,执行G50 X208,修复原来的工件坐标系,重新运行程序,就可以低速精车梯形螺纹了。精车时也是通过上述改
变螺纹车刀车削前的轴向起点位置的方法来修光梯形螺纹的两侧面,同时通过测量,控制切削的次数使螺纹达到尺寸精度的要求。
经过实验,在高速与低速车削的转数郁固定时,车刀需要偏移的位移是固定的,有了这个数据,以后在车刀崩刃,或磨损后需换刀时就可以不用再重复调整步骤,直接在低速精车时将车螺纹的起点偏移相应位置就可以了。本文所举加工例子在广州数控机床厂的叫CJK61352ACNC数控车床上完成,当车床主轴转速从560r/min变速到25r/min时梯形螺车刀在Z轴上需向左偏移1.8mm。
当然如果在批量生产加工时还是要一次一次地改变螺纹车刀车削前的轴向起点位置来修光梯形螺纹的两侧面,生产效率将大大降低,为了解决这个问题,我们可以将梯形螺纹左右两侧面的加工过程分别编成两个子程序,每次调用时使车刀轴向偏移0.1mm,在工件的首件试切中确定需调用子程序的次数,从而将整个加工过程编入程序当中,即从加工第二件工件时车床就可以一直自动运行下去,直到工件被加工合格。
2.变速车削梯形螺纹在简易数控车床上的实现
像GSK980T、FANUC-OTE等一些功能较全的数控系统由于有复合指令的存在使得编程变得比较简单,但在一些国产经济型数控车床上却不具备这样的功能。这时我们可以将刚斜进法的粗车过程编成子程序,每调用一次车刀都在X轴和Z轴上进给一小段距离,并在首件试切中确定子程序需被主程序调用的次数。粗车完成后,仍用文中所述方法调试出从高速粗车变为低速精车后螺纹车刀需轴向移动的位移,再把精车螺纹左右侧面的加工过程分别编成子程序,在主程序调用即可。
3.几点注意事项
(1)切削时加切削液,根据情况看是否要加顶尖。
(2)车刀从高速变为低速后要严格对准梯形螺纹槽,操作时要仔细认真,不能马虎。可采用逐步恢复坐标系的方法,即分几次校正车刀,使车刀逐步车削到牙槽底部。
(3)梯形螺纹精粗车刀的刀头宽度不能相差太大,不然换刀后会使切削余量过大,发生崩列等问题。
(4)对于一些大螺距的螺纹,车削时主轴转速不能过高,需参考机床的最高进给速度,否则会发生失步等问题。
4.结论
实际的加工证明,以上在数控车床上变速车削梯形螺纹的方法是切实可行的,且取得了很好的加工效果。对于另外一些大螺距三角形螺纹、蜗杆等只需把粗车进刀的方法如斜进法、分层进刀法等编成子程序,调试出从高速粗车变为低速精车后车刀需轴向移动的位移后,也把精车螺纹左右侧面分别编成子程序,在主程序中将其调用就能完成加工。
梯形螺纹详解
梯形螺纹的基础知识 1.梯形螺纹的作用及种类 梯形螺纹是常用的传动螺纹,精度要求比较高。如车床的丝杠和中、小滑板的丝杆等。梯形螺纹有两种,国家标准规定梯形螺纹牙型角为30o。英制梯形螺纹的牙型角为29o,在我国较少采用。2.梯形螺纹的标记 梯形螺纹的标记由螺纹代号、公差带代号及旋合长度代号组成。梯形螺纹代号用字母Tr及公称直径×螺距与旋向表示,左旋螺纹旋向为LH,右旋不标。 梯形螺纹公差带代号仅标注中径公差带,如7H、7e,大写为内螺纹,小写为外螺纹。 梯形螺纹的旋合长度代号分N、L两组,N表示中等旋合长度,L表示长旋合长度。 标记示例: Tr22×5—7H 表示梯形螺纹,公称直径为22mm,螺距为5mm,中径公差带代号为7H。
3.梯形螺纹的牙型
4.梯形螺纹各部分名称、代号、计算公式及基本尺寸确定
5、梯形螺纹的车削方法 a)左右切削法 b)车直槽法 c)车阶梯槽法 1.梯形外螺纹的车削 (1)螺距小于4mm和精度要求不高的工件,可用一把梯形螺纹车刀,并用少量的左右切削法车削。 (2)螺距大于4mm和精度要求高的梯形螺纹,一般采用车直槽法,分刀车削,先用车槽刀车出螺旋槽,再用梯形螺纹车刀进行车削。具体做法如下: a)车梯形螺纹时,螺纹顶径留0.3mm左右余量,且倒角与端面成15°。 b)选用刀头宽度稍小于槽底宽的车槽刀,粗车螺纹(每边留0.25~ 0.35mm左右的余量)。 c)用梯形螺纹车刀采用左右切削法车削梯形螺纹牙型两侧面,每边留01~0.2mm的精车余量,并车准螺纹小径尺寸。
d)精车大径至图样要求。 e)选用梯形螺纹精车刀,采用左右切削法完成螺纹加工。 2.梯形内螺纹的车削 梯形内螺纹的车削与车削三角形内螺纹基本相同。车削梯形内螺纹时,进刀深度不易掌握,可先车准螺纹孔径尺寸,然后粗车。精车时应不进刀车削2~3次,以消除刀杆的弹性变形,保证螺纹的精度要求。
任务一车梯形外螺纹
任务6 车梯形外螺纹 学习目标 1.了解梯形螺纹的特点,掌握梯形螺纹的基本要素的计算方法。 2.掌握梯形螺纹的技术要求以及梯形外螺纹车刀的刃磨方法。 3.掌握梯形螺纹的三针、单针测量方法。 4.学会用车梯形外螺纹。 工作任务 本任务是加工如图8-1所示梯形螺纹,材料为45钢。 图8-1 梯形螺纹 相关理论 梯形螺纹分为米制和英制两种,米制梯形螺纹的牙型角为300,英制梯形螺纹的牙型角为290。在我国规定采用米制梯形螺纹。下面只介绍国标300牙型角的米制梯形螺纹(以下简称梯形螺纹)。 一、梯形螺纹的标记 梯形螺纹的代号用字母“Tr”及“公称直径x 螺距”表示。如Tr40 x 7 、Tr28 x 4 等。梯形螺纹的完整标注包括螺纹特征代号、螺纹公差代号和螺纹旋合长度代号。标注范例如下:
二、梯形螺纹的尺寸计算 梯形螺纹各部分名称、代号及计算公式见表8-1。 表8-1 梯形螺纹各部分名称、代号及计算公式 续表
三、梯形外螺纹车刀的刃磨要求 梯形外螺纹车刀分为粗车刀和精车刀两种,常用高速钢车刀来刃磨,刃磨要求如下∶ 1.螺纹车刀的刀尖角应略小于梯形螺纹的牙型角,一般取29030‘;精车刀刀尖角应等于梯形螺纹的牙型角,即300。 2.粗车刀的刀头宽度一般取0.7倍的牙槽底宽;精车刀刀头宽则应略小于牙槽底宽,为0.9倍的刀宽。 3.刃磨前刀面时,由于受螺纹升角的影响,梯形外螺纹粗车刀应磨出50~150的径向前角,而精车为保证牙型准确,径向前角为50。 4.刃磨两侧副后刀面时,由于受螺纹升角的影响,车刀进给方向的后角应为(30~50)+ψ,背进给方向的后角应为(30~50)- ψ(ψ为螺纹升角)。 5.梯形外螺纹车刀刃磨方法参看三角形螺纹车刀刃磨过程。 四、车梯形外螺纹的方法 1.对于螺距小于4mm或精度要求不高的梯形螺纹可用一把车刀进行粗、精车。 2. 对于螺距大于4mm或精度要求高的梯形螺纹的加工步骤如下∶ (1)粗车螺纹大径,留余量3mm左右。 (2)采用左右切削法粗加工梯形螺纹至小径尺寸,留余量0.3mm左右,两侧面分别留0.2~0.3mm精车余量,如图8-2(a)所示。 (3)精车螺纹至大径尺寸。 (4)精车螺纹两侧面,如图8-2(b)所示,控制中径尺寸符合图样要求。 (a)(b) 图8-2 梯形螺纹的车削方法
教案:车外梯形螺纹
《车工工艺与技能训练》教案
1、梯形螺纹的尺寸计算 梯形螺纹一般作传动用,精度高,如车床上的长丝杠和中、小滑板的丝杠等。梯形螺纹分米制和英制两种,国家标准规定米制梯形螺纹的牙型角为30°。英制梯形螺纹(其牙型角为29°)在我国较少采用。因此,下面只介绍30°牙型角的梯形螺纹。 30°梯形螺纹(以下简称梯形螺纹)的标记,用字母“Tr”及公称直径×螺距表示,单位均为mm。左旋螺纹需在尺寸规格之后加注“LH”,右旋则不注出。 例如:
梯形螺纹各部分名称、代号及计算公式 教学过程 名称 代 号 计算公式 牙型角αα=30° 螺距P 由螺纹标准确定 牙顶间隙ac P 1.5~5 6~12 14~44 ac 0.25 0.5 1 外 螺 纹 大径 d 公称直径 中径d2 d2= d-0.5 P 小径d3 d3= d-2 h3 外螺纹 内螺纹 d d 2 d 3 Z h 3 R1 R1 30° P R2 a c H 4 D 1 D 2 、 d 2 D 4 梯形螺纹牙型 图8-1-1 梯形螺纹的牙型
牙高h3 h3=0.5 P+ac 内 螺 纹 大径D4 D4= d+2ac 中径D2 D2=d2 小径D1 D1= d- P 牙高H4 H4=h3 牙顶宽 f、 f′ f= f′=0.366P 牙槽底宽 W、 W′ W=W′=0.366P-0.536 ac 2、梯形螺纹车刀 车梯形外螺纹时,径向切削力较大,为了减小切削力,螺纹车刀也应分为粗车刀和精车刀两种。 (1)高速钢梯形螺纹粗车刀。高速钢梯形螺纹粗车刀如图8-1-2所示。在加工中采用左右切削并留有精车余量,刀尖角应小于牙型角,刀尖宽度应小于牙型槽底宽W。 (2)高速钢梯形螺纹精车刀。高速钢梯形螺纹精车刀如图8-1-3所示。车刀的径向前角为0°,两侧切削刃之间的夹角等于牙型角。为了保证两侧切削刃切削顺利,在两侧都磨有较大前角( γ0=10°~16°)的卷屑槽, 图8-1-2 高速钢梯形螺纹粗车刀
梯形螺纹车
二、梯形螺纹车刀的几何角度和刃磨 梯形螺纹有米制和英制两类,米制牙型为30。,英制为29。。一般常用的是米制梯形螺纹。 梯形螺纹车刀分粗、精车刀两种。 1.梯形螺纹车刀的参数和角度(图2-8-1a、b) (1)两刃夹角 粗车刀应小于螺纹牙型角;精车刀应等于螺纹牙型角。 (2)刀头宽度 粗车刀的刀头宽度应为1/3螺距宽;精车刀的刀头宽度应等于牙底槽宽减0.05 Inln。 (3)纵向前角 1)高速钢车刀精车刀的纵向前角一般为10。~15。。精车刀为了保证牙型角正确,前角应等于0。,但实际生产时取5。~10。。此时应注意修正两刃夹角,以保证牙型角为30。。 2)硬质合金车刀一般纵向前角取0。(图2-8-2)。为解决3个刀刃同时切削,切削力较大,容易引起振动和排屑呈带状不完全的问题,采用图2-8-3所示的刀头形状,即有纵向圆弧 型的屑槽和一定的纵向前角。 (4)两侧刀刃主剖面前角 粗车刀为0。或为负前角,如图2-8-3所示。高速钢精车刀,两侧刀刃磨出了较大前角的卷 屑槽,前角为12。~20。,见图2-8-4。 (5)纵向后角 纵向后角一般为6。~8。。 (6)两侧刀刃主剖面后角 与矩形螺纹车刀相同。 174 第八章车削矩形、梯形螺纹 图2-8-2硬质合金梯形螺纹车刀
U日 图2-8-3 g~圆弧硬质合金梯形螺纹车刀 图2-8-4高速钢梯形螺纹精车刀 2.梯形螺纹车刀的刃磨 梯形螺纹车刀的刃磨与三角形螺纹车刀刃磨相似,但要注意以下问题:①用样板(图2培.5)或角度器校对刃磨两刀刃夹 角; ②有纵向前角的两刃夹角£’应进行修正; ③用角尺或角度器检验刃磨的两侧刀刃的后角; ④车刀刃口要光滑、平直、无爆口(虚刃),两侧刀 刃必须对称,刀头不歪斜; ⑤刀头磨出的各部分尺寸要符合被加工螺纹的图
5一5车矩形螺纹、梯形螺纹和锯齿形螺纹
广东省技工学校一体化教案(首页)(代号A——3) 填表人:杨长庆审阅签名:
组织教学:3分钟 教学要求:5分钟 授课内容:60分钟 组织学生点名,检查出勤人数、衣帽、校卡是否穿戴整齐,是否符合学生的要求,然后安 定情绪。讲述本课堂的内容,时间安排和听课要求,学习意义。板书本课题名称:《车矩形螺纹、梯形螺纹和锯齿形螺纹》 学习目的 1、掌握计算梯形螺纹各部分的基本要素的尺寸。 2、掌握矩形螺纹、梯形螺纹的表达式。 3、了解矩形螺纹、梯形螺纹、锯齿形螺纹车刀的几何角度。 4、了解矩形螺纹、梯形螺纹、锯齿形螺纹的车削方法。 学习指导 矩形螺纹、梯形螺纹和锯齿形螺纹是应用很广泛的传动螺纹,其工作长度较长,精度要求 较高,而且导程和螺纹升角较大,所以要比车削三角形螺纹困难。 一、矩形螺纹、梯形螺纹和锯齿形螺纹的基本要素的计算 1、矩形螺纹基本要素的尺寸计算 矩形螺纹也称方牙螺纹,是一种非标准螺纹。因此,在零件图上的标记为“矩形公称直径×螺距”,如:矩形40×6。
2、梯形螺纹尺寸计算 梯形螺纹分米制和英制两种。我国常采用米制梯形螺纹(牙型角为30。)
3、锯齿形螺纹的尺寸计算 锯齿形螺纹的牙型角为33o锯齿形螺纹能承受较大的单向力,通常用于起重和压力设备中。锯齿形螺纹基本要素的尺寸及计算公式可查阅有关资料。 二、矩形螺纹车刀、梯形螺纹车刀和锯齿形螺纹车刀 1、 矩形螺纹车刀 矩形螺纹车刀与车槽刀十分相似,其几何形状如图5—17所示。刃磨矩形螺纹车刀应注意以下问题: (1)精车刀的主切削刃宽度直接决定着螺纹的牙槽宽,其主切削刃宽度b=0.5P+(0.02~0.04)mm。 (2)为了使刀头有足够的强度,刀头长度^不宜过长,一般取L=0.5 P+(2~4)mm。 (3)矩形螺纹的螺纹升角一般都比较大,刃磨两侧后角时必须考虑螺纹升角的影响。 (4)为了减小螺纹牙侧的表面粗糙度,在精车刀的两侧面切削刃上应磨有 b=O.3~0.5修光刃。
用宏程序编程车削梯形螺纹ok
用宏程序编程车削梯形螺纹梯形螺纹较之三角螺纹,其螺距和牙型都大,而且精度高,牙型两侧面表面粗糙度值较小,致使梯形螺纹车削时,吃刀深、走刀快、切削余量大、切削抗力大,这就导致了梯形螺纹的车削加工难度较大。 1普通车床车削梯形螺纹方法 车削梯形螺纹时,通常采用高速钢材料刀具进行低速车削,低速车削梯形螺纹一般有如图1所示的四种进刀方法:直进法、左右切削法、车直槽法和车阶梯槽法。通常直进法只适用于车削螺距较小(P<4mm)的梯形螺纹,而粗车螺距较大(P>4mm)的梯形螺纹常采用左右切削法、车直槽法和车阶梯槽法。下面分别探究 一下这几种车削方法: 图1梯形螺纹车削的四种进刀方法 直进法:直进法也叫切槽法,如图1(a)所示。车削螺纹时,只利用中拖板进行横向(垂直于导轨方向)进刀,在几次行程中完成螺纹车削。这种方法虽可以获得比较正确的齿形,运动轨迹也很简单,但由于刀具三个切削刃同时参加切削,振动比较大,牙侧容易拉出毛刺,不易得到较好的表面品质,并容易产生扎刀现象,因此,它只适用于螺距较小的梯形螺纹车削。 左右切削法:左右切削法车削梯形螺纹时,除了用中拖板刻度控制车刀的横向进刀外,同时还利用小拖板的刻度控制车刀的左右微量进给,直到牙形全部车好,如图1(b)所示。用左右切削法车螺纹时,由于是车刀两个主切削刃中的一 个在进行单面切削,避免了三刃同时切削,所以不容易产生扎刀现象。另外,精
车时尽量选择低速(v=4~7m/min),并浇注切削液,一般可获得很好的表面质量。 车直槽法:车直槽法车削梯形螺纹时一般选用刀头宽度稍小于牙槽底宽的矩 形螺纹车刀,采用横向直进法粗车螺纹至小径尺寸(每边留有0.2~0.3mm的余量),然后换用精车刀修整,如图1(c)所示。这种方法简单、易懂、易掌握,但是在车削较大螺距的梯形螺纹时,刀具因其刀头狭长,强度不够而易折断:切削的沟槽较深,排屑不顺畅,致使堆积的切屑把刀头“砸掉”:进给量较小,切削 速度较低,因而很难满足梯形螺纹的车削需要。 车阶梯槽法:为了降低“直槽法”车削时刀头的损坏程度,我们可以采用车阶梯槽法,如图1(d)所示。此方法同样也是采用矩形螺纹车刀进行切槽,只不 过不是直接切至小径尺寸,而是分成若干刀切削成阶梯槽,最后换用精车刀修整至所规定的尺寸。这样切削排屑较顺畅,方法也较简单,但要换刀效率不高。 综上所述:除直进法外,其他三种车削方法都能不同程度地减轻或避免三刃 同时切削,使排屑较顺畅,刀尖受力、受热情况有所改善,从而不易出现振动和 扎刀现象,还可提高切削用量,改善螺纹表面品质。所以,左右切削法、车直槽 法和车阶梯槽法获得了广泛的应用。 2数控车削梯形螺纹方法的选用 根据上述分析,数控车床车削梯形螺纹采用“分层法“比较合适。分层法” 车削梯形螺纹实际上是直进法和左右切削法的综合应用。在车削梯形螺纹时, “分层法”通常不是一次性就把梯形槽切削出来,而是把牙槽分成若干层(每层深度根据具体情况设定),转化成若干个较浅的梯形槽来进行切削,从而降低了 车削难度。每一层的切削都采用先直进后左右的车削方法,由于左右切削时槽深不变,刀具只须做向左或向右的纵向进给即可(如图2所示),因此它比上面提到的左右切削法的运动轨迹要简单得多。
左右车削法车梯形螺纹
左右车削法车梯形螺纹
左右车削法车梯形螺纹 【摘要】梯形螺纹用来准确传递运动和动力故对精度要求较高,本人结合多年在工厂一线机加工的实际经验在文中详细论述梯形螺纹车削过程中车刀的刃磨要求、工件的装夹、车刀的装夹和机床的调整以及如何使用数学的等方法在车削中保证梯形螺纹粗加工余量的快速去除和精加工余量的有效预留,从而高效地车削出高质量的梯形螺纹。 【关键词】左右车削法梯形螺纹技法 梯形螺纹是螺纹的一种,是最常用的传动螺纹。牙型为等腰梯形,牙型角为30。内外螺纹以锥面贴紧不易松动。与矩形螺纹相比,传动效率略低,但工艺性好,牙根强度高,对中性好,得到广泛的应用,因此掌握高效、高质量的车削梯形螺纹的方法具有重要的实际意义。 我国标准规定30°梯形螺纹代号用“Tr”及公称直径×螺距表示,左旋螺纹需在尺寸规格之后加注“LH”,右旋则不注出。例如Tr36×6;Tr44×8LH等。梯形螺纹一般作传动用,可以传递准确的运动和动力,所以精度要求比较高,例如车床上的长丝杠和中、小滑板的丝杆等,而且其精度直接影响传动精度和被加工零件的尺寸精度。梯形螺纹的工件广泛的被用在各种机床上,其螺距和牙型都大,而
且精度高,牙型两侧面表面粗糙度值较小,致使梯形螺纹车削时,吃刀深,走刀快,切削余量大,切削抗力大。这就导致了梯形螺纹的车削加工
难度较大,初学者操作容易产生扎刀现象,很多操作者都在快速的去除粗加工余量和预留精加工余量的问题上有较大困难,在工厂实际中加工速度太慢导致生产效率低下甚至加工精度不行导致过高的废品率。在多年的工厂一线机加工的通过不断的摸索、总结、完善,对实际车削方法有了自己的一套总结,在此谈谈左右车削法车削梯形螺纹时的几点心得体会。 一、梯形螺纹车刀的刃磨要求。 1.高速钢右旋梯形螺纹粗车刀(以车Tr42×6-7h螺纹为例)。下图为高速钢右旋梯形螺纹粗车刀,为了便于左右切削并留有精车余量,两侧切削刃之间的夹角应小于牙型角30°,取29°左右。刀头宽度应小于牙槽底宽W(W=1.93),刀头宽度取1.3mm左右。为了高效去除大部分切削余量,将刀头磨成圆弧型,以增加刀头强度,并将刀头部分的应力分散。为了使车刀两条侧切削刃锋利且受力、受热均衡,将前刀面磨成左高右低、前翘的形状,使纵向前角γp=10°-15°、γ右=(3°-5°)+a°、γ左=(3°-5°)-a°、a为螺旋升角;如果是左旋螺纹,则γ右、γ左、相反。
分层法车梯形螺纹
“分层法”车削梯形螺纹 “分层法”车削梯形螺纹实际上是直进法和左右切削法的综合应用。在车削较大螺距的梯形螺纹时,“分层法”通常不是一次性就把梯形槽切削出来,而是把牙槽分成若干层(每层大概1~2mm深),转化成若干个较浅的梯形槽来进行切削,从而降低了车削难度。每一层的切削都采用先直进后左右的车削方法,由于左右切削时槽深不变,刀具只须做向左或向右的纵向(沿导轨方向)进给即可(如图2所示),因此它比上面提到的左右切削法要简单和容易操作 得多。 图2 分层法车削梯形螺纹图 表1 梯形螺纹的计算式及其参数值
梯形螺纹的计算公式及其参数值列于表1。下面就以车削Tr36×6-7e为例,介绍一下“分层法”车削梯形螺纹: 1) “分层法”车削梯形螺纹的刀具选择:“分层法”车削梯形螺纹所用的粗车刀和精车刀与其它加工方法基本相同,只是粗车刀的刀头宽度(w刀=1.2~1.5mm)小于牙槽底宽(w=1.928mm),刀具刀尖角(εr=29°;~29°;30')略小于梯形螺纹牙型角(α=30°;)。 2) “分层法”车削梯形螺纹的操作步骤: ·粗、精车梯形螺纹大径(?36-0.3750)且倒角与端面成15°;。这里螺纹大径也可留有0.15mm左右的修整余量,以便螺纹精车完后,发现牙顶有撕裂和变形时可以进行修整; ·用梯形螺纹粗车刀直进法大概车至1/3牙槽深处(h1=1mm),因为切削深度不大,切削力较小,一般不会产生振动和扎刀,如图2和图3(a)所示。此时,中拖板停止进刀而做横向进刀(车刀每次进到原来的吃刀深度),只用小拖板使车刀向左或向右做微量进给,进给量大概为0.2~0.4mm,进刀次数视具体情况而定,以较快的速度将牙槽拓宽如图2和图(b)所示。拓宽后牙顶宽f'(f'为2.5mm左右)应大于理论计算值f(f=2.196mm),保证螺纹两侧面留有0.15mm左右的精车余量; 图3 梯形螺纹“分层法”车削的步骤 ·将车刀刀头退回至第一层拓宽牙槽的中间位置(只需将小拖板退回借刀格数的一半),接着再用直进法切削第二层,大概车至2/3牙槽深处[h2=2mm,如图3(c)],然后中拖板停止横向进刀,用左右切削法拓宽牙槽[如图3(d)]。拓宽牙槽时,应把第二层的两牙槽侧面与第一层的重合,注意不要再次车削到第一层牙槽的侧面,否则牙顶的精车余量就可能不够了; ·重复上述步骤,继续用直进法和左右切削法车至第三层(牙高h3=3mm)和第四层(牙高h4=3.5mm左右,d3=?29-0.5370),然后拓宽牙槽(图2)。“分层法”车削的次数可以为两次、三次,甚至更多次,具体情况视螺距的大小、车刀强度等而定;
车削螺距为6的梯形螺纹
车削螺距为6的梯形螺纹 【摘要】梯形螺纹的车削不管是在生产实践中,还是在技能训练模块中,是非常重要的。本文就梯形螺纹车削过程中车刀的刃磨要求、工件的装夹、车刀的装夹和机床的调整以及车削时如何利用梯形螺纹的计算公式从数学方面来保证粗加工余量的快速去除和精加工余量的有效预留,从而达到高效、稳定地车削梯形螺纹。 【关键词】左右车削法梯形螺纹螺旋升角借刀 梯形螺纹是螺纹的一种,牙型为等腰梯形,牙型角为30。内外螺纹以锥面贴紧不易松动。我国标准规定30°梯形螺纹代号用“Tr”及公称直径×螺距表示,左旋螺纹需在尺寸规格之后加注“LH”,右旋则不注出。例如Tr36×6;Tr44×8LH等。梯形螺纹一般作传动用,用以传递准确的运动和动力,所以精度要求比较高,例如车床上的长丝杠和中、小滑板的丝杆等,而且其精度直接影响传动精度和被加工零件的尺寸精度。梯形螺纹的工件不仅广泛的被用在各种机床上,其螺距和牙型都大,而且精度高,牙型两侧面表面粗糙度值较小,致使梯形螺纹车削时,吃刀深,走刀快,切削余量大,切削抗力大。这就导致了梯形螺纹的车削加工难度较大,学生在车工技能培训中难于掌握,容易产生扎刀现象,进而使学生对此产生紧张和畏惧的心理,很多操作者都是因为无法快速的去除粗加工余量和将精加工余量留得过多或过少,导致加工速度太慢或将工件报废。在多年的车工实习教学中,通过不断的摸索、总结、完善,对于梯形螺纹的车削也有了一定的认知,,在此谈谈左右车削法车削梯形螺纹时的几点心得体会。 一、梯形螺纹车刀的刃磨要求。 1.高速钢右旋梯形螺纹粗车刀(以车Tr42×6-7h螺纹为例)。下图为高速钢右旋梯形螺纹粗车刀,为了便于左右切削并留有精车余量,两侧切削刃之间的夹角应小于牙型角30°,取29°左右。刀头宽度应小于牙槽底宽W(W=1.93),刀头宽度取1.3mm左右。为了高效去除大部分切削余量,将刀头磨成圆弧型,以增加刀头强度,并将刀头部分的应力分散。为了使车刀两条侧切削刃锋利且受力、受热均衡,将前刀面磨成左高右低、前翘的形状,使纵向前角γp=10°-15°、γ右=(3°-5°)+a°、γ左=(3°-5°)-a°、a为螺旋升角;如果是左旋螺纹,则γ右、γ左、相反。
教学案例15车梯形外螺纹
教学案例十五车梯形外螺纹知识目标 ⒈了解梯形外螺纹的作用、种类、标记、牙型。 ⒉了解梯形外螺纹各部分名称、代号、计算公式及基本尺寸确定。 ⒊了解梯形外螺纹的技术要求。 ⒋了解梯形外螺纹车刀的几何形状和角度要求。 ⒌学会确定梯形外螺纹的参数。 技能目标 ⒈掌握梯形外螺纹车刀的刃磨方法; ⒉掌握梯形外螺纹车削方法; ⒊学会梯形螺纹车刀的装夹方法; ⒋掌握梯形螺纹的检测方法。
任务分析 如图15-1所示,梯形外螺纹轴材料为45钢,毛坯尺寸为10535×φmm ,通过查阅梯形外螺纹相关的国家标准,通过公式,计算主要参数。
牙高 H 4 H 4=h 3 牙顶宽 f ,f ′ f =f ′=0.366P 牙槽底宽 W ,w ′ w =w ′=0.366P -0.536α c 二、梯形螺纹车刀几何形状 梯形螺纹车刀分为粗车刀和精车刀两种。 ⒈高速钢梯形螺纹车刀 高速钢梯形螺纹车刀几何形状,如图15-2所示。 图15-2高速钢梯形螺纹粗车刀 图15-3高速钢梯形螺纹精车刀 ⑴两刃夹角 粗车刀应小于梯形螺纹牙形角(030-20′°),精车刀应等于螺纹牙形角30°+10′。 ⑵刀头宽度 粗车刀刀头宽度应为三分之一螺距宽,精车刀的刀头宽度就等于牙底槽宽减0.05mm. ⑶纵向前角 粗车刀一般为15°左右;精车刀为了保证牙型正确,前角就等于0°,如图15-3所示。 ⑷纵向后角 一般为6°~8°。 ⒉硬质合金梯形螺纹车刀 硬质合金梯形螺纹车刀的几何形状,如图15-4所示。 图15-4 硬质合金梯形螺纹车刀 图15-5硬质合金双圆弧梯形螺纹车刀 高速切削螺纹时,由于车刀三个切削刃同时参加切削,且切削力较大,容易引起振动。因此,
数控车床车削梯形螺纹
数控车床车削梯形螺纹 梯形螺纹有低速切削和高速切削两种方法。 (1)低速切削梯形螺纹对精度要求较高的梯形螺纹,以及在修配或单件生产时,常采用低速切削的方法。 当车削螺距较大的梯形螺纹时,为避免三个切削刃同时参与切削而产生振动,应先用粗车刀,采用左右赶刀法的进给方式进行租车。数控车床厂在保证牙型高度后,再采用精车刀采用直进法进行精加工成形;当螺距很大时,则用径向前角为零、两侧磨有卷屑槽的精车刀,采用左右赶刀的方法精车梯形螺纹。 (2)高速切削梯形螺纹在车削刚度、精度要求不高的梯形螺纹时,可用硬质合金螺纹车刀进行高速切削。采用这种车刀切削时,由于三个切削刃同时参与切削,会产生带状切屑流出,操作很不安全。 为此,可采用数控车床厂螺纹车刀。这种螺纹车刀在前面磨出对称的两个圆弧,使径向前角y。增大。数控车床厂两圆弧还使前刀面呈3。~5。的屋脊状结构。这种车刀可减小切削力,增加了车刀的强度,从而减轻了切削振动。数控车床厂同时形成球状切屑,使排屑顺畅。 可以用G76或G92编程,螺距大的螺纹采取左右进刀法车削比较好。先用G76车, G76 P0100**(**为梯形螺纹牙型角)Q150 R0.03; G76 X Z P Q R F ; (第一行可以套用,Q是每次吃刀量,单位微米。R是精车余量,半径值)(第二行:X、Z是目标点坐标,P是牙型高,Q是第一刀的吃刀量,R是锥螺纹编程的螺纹起点与终点的半径差(直螺纹不用),F是螺距。)大螺距螺纹用G76粗车过之后,留点余量用G92车效果好点,车削起点不要变化。 先走一刀G92 X Z F ;, 然后起点分别往左边和右边偏0.01或0.02毫米再走第二刀和第三刀。 如M100X4的螺纹长度50 T0101 M3S500 M8 G0X105.Z2. G92X99.Z-50.F2. X98.5 X98. X97.5 X97. X96.5 X96.1 X96. 也就是车床的左右借刀法程序没什么特殊的,主要就是你的起刀点的位置变化,比如开粗的起点为X60 Z3 先车到底径或留点精光一刀(刀要小于30度要么用槽刀)那么第二把刀(30度但刀头是比标准的小的好像是0.366*螺距)
论车削梯形螺纹方法
论车削梯形螺纹方法 摘要:常见的梯形螺纹车削,由于车削加工难度较大,操作技能要求较高,因而使初学者学习起来较困难。为了解决此难题,笔者提出了操作简单、易理解和掌握的“分层”车削方法。 关键词:牙型角螺距表面粗糙度 梯形螺纹较之三角螺纹,其螺距和牙型都大,而且精度高,牙型两侧面表面粗糙度值较小,致使梯形螺纹车削时,吃刀深,走刀快,切削余量大,切削抗力大。这就导致了梯形螺纹的车削加工难度较大,初学者在车工技能培训中难于掌握,容易产生扎刀现象,进而初学者对此产生紧张和畏惧的心理。在多年的车工工作中,通过不断的摸索、总结、完善,对于梯形螺纹的车削也有了一定的认知,下面我们就来探究一下哪种车削方法更适合初学者理解、学习和掌握。 一、梯形螺纹车削方法的选用 车削梯形螺纹时,通常采用高速钢材料刀具进行低速车削,低速车削梯形螺纹一般有如图1所示的四种进刀方法:直进法、左右切削法、车直槽法和车阶梯槽法。通常直进法只适用于车削螺距较小(P<4mm)的梯形螺纹,而粗车螺距较大(P>4mm)的梯形螺纹常采用左右切削法、车直槽法和车阶梯槽法。下面我们分别探究一下这几种车削方法: (a)直进法 (b)左右切削法 (c)车直槽法 (d)车阶梯槽法
图1 梯形螺纹车削的四种进刀方法 1.直进法:直进法也叫切槽法,如图1(a)所示。车削螺纹时,只利用中拖板进行横向(垂直于导轨方向)进刀,在几次行程中完成螺纹车削。这种方法虽可以获得比较正确的齿形,操作也很简单,但由于刀具三个切削刃同时参加切削,振动比较大,牙侧容易拉出毛刺,不易得到较好的表面品质,并容易产生扎刀现象,因此,它只适用于螺距较小的梯形螺纹车削。 2.左右切削法:左右切削法车削梯形螺纹时,除了用中拖板刻度控制车刀的横向进刀外,同时还利用小拖板的刻度控制车刀的左右微量进给,直到牙形全部车好,如图1(b)所示。用左右切削法车螺纹时,由于是车刀两个主切削刃中的一个在进行单面切削,避免了三刃同时切削,所以不容易产生扎刀现象。另外,精车时尽量选择低速(v=4~7m/min),并浇注切削液,一般可获得很好的表面粗糙度。在初学者实际操作过程中,要根据实际经验,一边控制左右进给量,一边观察切屑情况,当排出的切屑很薄时,就可采用光整加工使车出的螺纹表面光洁,精度也很高。但左右切削法操作比较复杂,小拖板左右微量进给时由于空行程的影响易出错,而且中拖板和小拖板同时进刀,两者的进刀量大小和比例不固定,每刀切削量不好控制,牙型也不易车得清晰。所以,左右切削法对操作者的熟练程度和切削技能要求较高,不适合初学者学习和掌握。 3.车直槽法:车直槽法车削梯形螺纹时一般选用刀头宽度稍小于牙槽底宽的矩形螺纹车刀,采用横向直进法粗车螺纹至小径尺寸(每边留有0.2~0.3mm的余量),然后换用精车刀修整,如图1(c)所示。这种方法简单、易懂、易掌握,但是在车削较大螺距的梯形螺纹时,刀具因其刀头狭长,强度不够而易折断:切削的沟槽较深,排屑不顺畅,致使堆积的切屑把刀头“砸掉”,进给量较小,切削速度较低,因而很难满足梯形螺纹的车削需要。 4.车阶梯槽法:为了降低“直槽法”车削时刀头的损坏程度,我
车工教案车梯形螺纹
课题车梯形螺纹 参考资料教材、教参《车工工艺与技能训练》教学配套课件教学方法学生讨论,示范,讲解与展示授课节数2节 知识与技能目标1.了解梯形螺纹的特点,掌握梯形螺纹基本要素的计算方法2.掌握梯形螺纹的技术要求以及梯形外螺纹车刀的刃磨方法3.掌握梯形外螺纹的三针、单针测量法 4.掌握梯形内螺纹孔径的计算方法 5.了解梯形内螺纹车刀的特点及安装注意事项 6.学会车梯形螺纹 知识连接1. 梯形螺纹的标记 2.梯形螺纹的基本尺寸 3.梯形外螺纹车刀的刃磨要求4.车梯形螺纹的方法 5.梯形螺纹的测量 6.车梯形螺纹的注意事项7.梯形内螺纹孔径计算 8.梯形内螺纹车刀刀杆的选择9.梯形内螺纹车削方法10.梯形内螺纹的测量11.注意事项 学习重点1. 梯形螺纹的标记 2.梯形螺纹的基本尺寸 3.梯形外螺纹车刀的刃磨要求4.车梯形螺纹的方法 5.梯形螺纹的测量 6.梯形内螺纹孔径计算 7.梯形内螺纹车削方法 8.梯形内螺纹的测量 实施建议 1.以普通螺纹为基础,来讲解梯形螺纹 2.展示带有梯形螺纹零、部件的实物。播放车削梯形螺纹和应用梯形螺纹丝杠的视频。 让学生去实习车间,观看CA6140型卧式车床上的进刀丝杠和中、小滑板丝杠。以加深学生 对梯形螺纹的理解,增强感性认识 3.从螺纹的牙型开始讲起,展示三角形螺纹和梯形螺纹的牙型,逐渐由三角形螺纹导引 到梯形螺纹,并开始讲授新课 4.本此课也可按以下思路来讲授:梯形螺纹基本要素的计算→梯形螺纹车刀的几何形状→梯形螺纹的车削方法 5.采取比较法来学习效果会更好。注意比较三角螺纹和梯形螺纹基本要素的计算、标记、 几何形状、车削方法和测量的异同。还要比较外、内梯形螺纹车刀几何形状的异同 1
用宏程序编程车削梯形螺纹方法
用宏程序编程车削梯形螺纹 梯形螺纹螺距和牙型都大,而且精度高,牙型两侧面表面粗糙度较小,致使梯形螺纹车削时,吃刀深、走刀快、切削余量大、切削力大,这就导致了梯形螺纹的车削加工难度较大。 1 普通车床车削梯形螺纹方法 车削梯形螺纹时,通常采用高速钢材料刀具进行低速车削,低速车削梯形螺纹一般有四种进刀方法:直进法、左右切削法、车直槽法和车阶梯槽法。通常直进法只适用于车削螺距较小(P<4mm)的梯形螺纹,而粗车螺距较大(P>4mm)的梯形螺纹常采用左右切削车直槽法和车阶梯槽法。下面分别梯形螺纹车削的四种进刀方法: 2 数控车削梯形螺纹方法的选用 根据上述分析,数控车床车削梯形螺纹采用“分层法“比较合适。分层法”车削梯形螺纹实际上是直进法和左右切削法的综合应用。在车削梯形螺纹时,“分层法”通常不是一次性就把梯形槽切削出来,而是把牙槽分成若干层(每层深度根据具体情况设定),转化成若干个较浅的梯形槽来进行切削,从而降低了车削难度。每一层的切削都采用先直进后左右的车削方法,由于左右切削时槽深不变,刀具只须做
向左或向右的纵向进给即可,因此它比上面提到的左右切削法的运动轨迹要简单得多。 3应用宏指令将梯形螺纹加工程序模块化 应用宏指令,将左右排刀法加工梯形螺纹模块化,应用时只需将主宏程序指令中的自变量赋值修改一下即可加工不同尺寸的梯形螺纹,而子宏程序中的内容不需修改。 (1)数值计算 ①梯形螺纹加工尺寸计算及其参数值:
②左(右)移刀量的计算 如上图可以得出当刀头宽度小于牙槽底宽时左(右)移刀量计算式为: 左(右)移刀量=tan15°×每一刀的进刀深度(半径值)+(牙槽底宽—刀头宽度)/2 (2)“分层法”车削梯形螺纹的刀具选择 “分层法”车削梯形螺纹所用的粗车刀和精车刀与其它加工方法基本相同,只是粗车刀的刀头宽度小于牙槽底宽,刀具刀尖角略小于梯形螺纹牙型角。 (3)通过上述分析,梯形螺纹加工需要的自变量有: #1=(A)每一刀的进刀深度(半径值), #2=(B)背吃刀量; #3=(C)刀头宽度偏差=(牙槽底宽—刀头宽度)/2; #4=(I)螺纹小径; #5=(J)螺距; #6=(K)螺纹长度;
梯形螺纹车削
模块一:车削加工梯形螺纹 相关理论知识 一、梯形螺纹的尺寸计算 国家标准规定梯形螺纹的牙型角为30°。下面就介绍30°牙型角的梯形螺纹。 30°梯形螺纹(以下简称梯形螺纹)的代号用字母“T r ”及公称直径×螺距表示,单位均为mm 。左旋螺纹需在尺寸规格之后加注“LH ”,右旋则不注出。例如T r36×6等。 图8.1 梯形螺纹的牙型 二、梯形螺纹车刀 车刀分粗车刀和精车刀两种。 ⑴.梯形螺纹车刀的角度。 ①.两刃夹角 粗车刀应小于牙型角,精车刀应等于牙形角。 ②.刀尖宽度 粗车刀的刀尖宽度应为1/3螺距宽。精车刀的刀尖宽应等于牙底宽减0.05㎜。 ③纵向前角 粗车刀一般为15左右,精车刀为了保证牙型角正确,前角应等于0,但实际生产时取 5°~10°。 ④纵向后角 一般为6°~8°。 ⑤两侧刀刃后角 a 1=(3°~5°)+φ a 2=(3°~5°)-φ ⑵梯形螺纹的刃磨要求。 ①用样板校对刃磨两刀刃夹角。图示8.2 图8.2 样板 ②有纵向前角的两刃夹角应进行修正。 ③车刀刃口要光滑、平直、无虚刃,两侧副刀刃必须对称刀头不能歪斜。 梯形螺纹牙型
④用油石研磨去各刀刃的毛刺。 相关实践知识 梯形螺纹的轴向剖面形状是一个等腰梯形,一般作传动用,精度高;如车床上的长丝杠和中小滑板的丝杠等。 一、螺纹的一般技术要求 (1)螺纹中径必须与基准轴颈同轴,其大径尺寸应小于基本尺寸。 (2)车梯形螺纹必须保证中径尺寸公差。 (3)螺纹的牙形角要正确。 (4)螺纹两侧面表面粗糙度值要低。 二、梯形螺纹车刀的选择和装夹 1、车刀的选择通常采用低速车削,一般选用高速钢材料。 (1)高速钢梯形螺纹粗车刀为了便于左右切削并留有精车余量,刀头宽度应小于槽底宽W。 (2)高速钢梯形螺纹精车刀 车刀纵向前角γp=0°,两测切削刃之间的夹角等于牙型角。为了保证两测切削刃切削顺利,都磨有较大前角(γo=10°~20°)的卷屑槽。但在使用时必须注意,车刀前端切削刃不能参加切 削。 < M ~ ~ 高速钢梯形螺纹粗车刀 -30'
任务一 梯形螺纹的型号及有关计算
任务一梯形螺纹的型号及有关计算 教学目标: 1. 正确识别梯形螺纹 2.能利用有关公式进行简单的计算。 教学重点:正确识别梯形螺纹 教学难点:梯形螺纹的有关计算 教学方法:理论教学 教具:CA6136、有关的刀具、卡盘扳手等工具、游标卡尺。 加工使用棒料。 教学过程: 一、组织教学 检查学生人数,填写教室日志,组织学生上课秩序。 二、复习导入 三角螺纹的型号及有关计算 三、讲授过程 梯形螺纹是应用广泛的一种传动螺纹,其工作长度较长,精度要求较高,而且导程和螺纹升角较大。车床上的长丝杠和中、小滑板丝杠都是梯形螺纹。 (一)梯形螺纹的型号 梯形螺纹的牙形如图7--1所示: 图7--1 梯形螺纹牙形 梯形螺纹的标记由螺纹代号、公差带代号及旋合长度代号组成,彼此间用“—”分开。具体标记方法见表7-1。
(二)梯形螺纹基本尺寸的计算 梯形螺纹各部分名称、代号及计算公式见表7—2。 例7—1:车削一对Tr42×10的丝杠和螺母,试求内、外螺纹的大径、牙形高度、小径、牙顶宽、牙槽底宽和中径尺寸。 解:根据表7—2中的公式有: 外螺纹d=42mm h=0.5P+a c=0.5×10+0.5=5.5mm d2=d-0.5P=42-0.5×10=37mm d1=d-2h=42-2×5.5=31mm 内螺纹D=d+2 a c=42+2×0.5=43mm H=h=5.5mm D2=d2=37mm D1=d-P=42-10=32mm 牙顶宽f= f′=0.366P=0.366×10=3.66mm 牙槽底宽W=W′=0.366P-0.536 a c=0.366×10-0.536×0.5=3.392mm 注:外螺纹用小写字母表示,内螺纹用大写字母表示。 (三)课堂练习 1、试说明Tr28×4—7h的含义。 2、试说明Tr36×10(P5)—7h的含义 3、试计算Tr36x6—7h的中径d2,牙形高h,小径d1,牙顶宽f、牙槽底宽w。
高效粗车梯形螺纹的方法
高效粗车梯形螺纹的方法 王涛 [摘要]梯形螺纹粗加工,一直采用传统的左右车削法或斜进法加工,不但效率低、刀具易磨损,还经常由于尺寸控制不准,使精加工余量不够出现废品。在此介绍一种实践中摸索出来的简单实用,效率高的梯形螺纹粗车方法。 [关键词]梯形螺纹、滑板刻度、左右车削法、进刀格数 1前言 在车削加工中,梯形螺纹丝杠的加工特别是粗加工,由于总的切削深度大,刀具尺寸受到梯形螺纹几何尺寸的限制,刀头宽度较小,刀具刚度性差,粗加工时采用较小的吃刀量效率太低,吃刀量稍微大一些经常产生蹦刃或刀尖磨损。在实际产生和实习教学中采用传统的车削法,费时间又费力,且不能很好的的控制加工的尺寸。 2传统的加工方法的弊端 传统的加工方法如表1所示,左右车削法、斜进法适合较大导程螺纹的粗加工,直进法只适合较小导程螺纹加工,后面3种方法适合较大导程螺纹的粗精加工,但是需要2把以上的刀具加工,并计算过程很繁琐,一不小心就可能出现差错,导致加工零件的报废。 左右车削法和斜进法没有明确每次的切削用量,只是要求随着梯形螺纹的深度增加切削深度和2个方向的进刀量逐渐减少,左右赶刀频繁,不好控制尺寸,如表1所示。 3高效粗车梯形螺纹的方法 通过多年的加工实践总结了一种综合了直进法和斜进法既简单实用又高效的粗加工加工方法,下面以Tr36×6为例介绍。
3.1梯形螺纹Tr36×6的几何尺寸计算 梯形螺纹的计算式及其参数值: 牙顶间隙 k=0.5mm 大径(公称直径)d (1 )=36mm 中径d2= d -0.5p=33 mm 小径d3= d-2h=36-(0.5×6+0.5 )=29 mm 牙高h3=0.5p+ac=3.5mm 牙顶宽a=0.366p=3.5mm 牙槽底宽w=0.366p-0.536ac=1.928mm 牙顶槽宽a1=6-2.196=3.804mm 3.2 Tr36×6的加工方法 3.2.1牙型尺寸 图1为Tr36×6的牙型尺寸 2.2.2 螺纹车削过程 (1)刃磨刀具 刃磨粗车刀刀头宽度b=1.5mm,前角取10~15°,刀尖角29°30′,取较大前角使切削轻快。 (2)加工过程 加工示意图如图2,利用车床中滑板和小滑板刻度控制进刀尺寸。
普车车梯形螺纹
普车车梯形螺纹 一、实习教学要求 1.了解梯形螺纹的作用和技术要求。 2.掌握梯形螺纹车刀的选择和装夹。 3.掌握梯形螺纹的车削方法。 4.掌握梯形螺纹的测量、检查方法。 二、相关工艺知识 1.梯形螺纹的一般技术要求 (1)螺纹中径必须与基准轴颈同轴,其大径尺寸应小于基本尺寸。 (2)车梯形螺纹必须保证中径尺寸公差(梯形螺纹以中径配合定心)。 (3)螺纹的牙型角要正确。 (4)螺纹两侧面表面粗糙度值较小。 2.梯形螺纹车刀的选择和装夹 (1)车刀的选择通常采用低速切削,一般选用高速钢材料。 (2)车刀的装夹 ①车刀主切削刃必须与工件轴线等高,同时应和工件 轴线平行。 ②刀头的角平分线要垂直于工件轴线。用样板找正装夹,以免产生螺纹 半角误差,如图9.4所示。 图9.4 梯形螺纹车刀的装夹 3.工件的装夹 一般采用两顶尖或一夹一顶装夹。粗车较大螺距时,可采用一夹一顶,以保证装夹牢固;同时使工件的一个台阶靠住卡爪平面(用轴向限位),以防止因切削力过火,使工件移位而车坏螺纹。 4.车床的选择和调整 (1) 正确调整机床各处间隙.对床鞍、中、小滑板的配合部分进行检查和调整,注意控制机床主轴的轴向窜动、径向圆跳动以及丝杆轴向窜动。 (2)选用正确的交换齿轮。 5.梯形螺纹的车削方法 梯形螺纹的车削方法有四种车削方法。
1)左右切削法 2)斜进法 3)直进法 4)车槽法 (1)螺距小于4mm 和精度要求不高的工件。可用一把梯形螺纹车直进法或斜进法车削。 (2)螺距大于6mm 和精度要求高的梯形螺纹,一般采用左右切削法或车槽法分刀车削。 用梯形螺纹车采用左右切削法或车槽法车削梯形螺纹两侧面,每边留0.1~0.2mm 的精车余量(见图9.5),并车准螺纹小径尺寸。 a ) b ) c ) d ) 图9.5梯形螺纹的车削方法 a 、 b )左右切削法粗、精车 c 、 d )切槽法粗车 6.梯形螺纹的测量方法 (1)综合测量法 用标准螺纹环规综合测量。(用于精度一般的测量)。 (2)三针测量法 这种方法是测量外螺纹中径的一种比较精密的方法。适用于测量一些精度要求较高,螺纹升角小于4 °的螺纹工件。测量时把三根直径相等的量针放置在螺纹相对应的螺旋槽中,用干分尺量出两边量针顶点之间的距离M ,如图9.6所示。 例: 车Tr32×6梯形螺纹,用三针测量螺纹中径,求量针直径和千分尺读数值M 。 解: 量针直径 干分尺读数值P D d d M 866.1864.42-+= =29+4.864×3.1-1.866×6 =29+15.08-11.2 =32.88mm 测量时需考虑公差,则M=32.88118.045.0--mm 为合格。 三针测量法采用的量针一般是专门制造的。在实际应用中,有时也用优质钢丝或新钻头的柄部来代替,但与计算出的量针直径尺寸往往不相符合,这就需要认真选择。要求所代用的钢丝或钻柄直径尺寸,最大不能在放入螺旋槽时被顶在螺纹牙尖上.最小不能在放入螺旋槽时和牙底相碰,可根据表9.7所示的范围内进行选用。
车梯形螺纹
项目二车梯形螺纹 一、学习要求: 1.掌握梯形螺纹各部分尺寸的计算方法 2.了解梯形螺纹车刀的几何形状及刃磨方法 3.掌握车削梯形螺纹技能及梯形螺纹的测量方法 二、使用工、量具 90°车刀45°车刀车槽刀梯形螺纹刀角度样板 三、学习过程 学习过程:观察不同种类的滚花刀,认识不同滚花刀的滚花花纹效果,最后练习 四、相关工艺知识 1.梯形螺纹各部分尺寸的计算 梯形螺纹有两种:一种是米制梯形螺纹,它的牙形角是30°;另一种是英制梯形螺纹,它的牙形角是29°。梯形螺纹的代号用字母“Tr”表示,记作“代号公称直径×螺距“来表示,左旋螺纹需要在尺寸之后加注“LH”,右旋不标注。
表8-1 米制梯形螺纹的各部分尺寸计算(mm) 2.梯形螺纹车刀几何形状 梯形螺纹车刀分为粗车刀和精车刀两种。 (1)高速钢梯形螺纹车刀
高速钢梯形螺纹车刀几何形状,如图6-8。 1)两刃夹角粗车刀应小于梯形螺纹牙形角(29°30′),精车刀应等于螺纹牙形角30 _+ _ 5′. 2)刀头宽度粗车刀刀头宽度应为三分之一螺距宽,精车刀的刀头宽度就等于牙底槽宽减0.05mm. 3)纵向前角粗车刀一般为15°左右;精车刀为了保证牙型正确,前角就等于0°,如图6-9。 4)纵向后角一般为6°~8°。 (2)硬质合金梯形螺纹车刀 硬质合金梯形螺纹车刀的几何形状,如图6-10。
高速切削螺纹时,由于车刀三个切削刃同时参加切削,且切削力较大,容易引起振动。因此,在实际生产上,多采用在螺纹车刀前刀面上磨出两个圆弧(如图6-11),这样可使径向前角增大,切削轻快,不易振动;切屑呈球状排出,保证操作安全。缺点是牙形精度较差。 (3)梯形内螺纹车刀 梯形内螺纹车刀的几何形状,如图6-12。
梯形螺纹的车削浅析
梯形螺纹的车削浅析 摘要:梯形螺纹牙型为等腰梯形,牙型角为30度,内外螺纹以锥面贴紧不易松动,工艺较好,牙根强度高,对中性好,主要用于传动螺纹。在生产实践中梯形螺纹的车削是相当复杂的,车削过程中不可仅仅应用一种方法去车削,而应融会贯通,因此学生只有掌握和熟练了各种车削方法,才能在车削过程中灵活运用,高效率、高精度、高品质地完成梯形螺纹车削。 关键词:“直进法”;“左右进刀切削法”;三针测量 梯形螺纹的工件不仅广泛的被用在各种机床上,其螺距和牙型都大,而且精度高,牙型两侧面表面粗糙度值较小,致使梯形螺纹车削时,吃刀深,走刀快,切削余量大,切削抗力大。这就导致了梯形螺纹的车削加工难度较大,学生在车工技能培训中难于掌握,容易产生扎刀现象,进而使学生对此产生紧张和畏惧的心理,很多操作者都是因为无法快速的去除粗加工余量和将精加工余量留得过多或过少,导致加工速度太慢或将工件报废。在多年的车工实习教学中,通过不断的摸索、总结、完善,对于梯形螺纹的车削也有了一定的认知,,在此谈谈车削梯形螺纹时的几点心得体会。 我们在车削梯形螺纹时,常用的是“直进法”“斜进法”和“左右进刀切削法”,“直进法”一般适用于螺距小于4mm或精度要求不高的工件,“斜进法” 和“左右进刀切削法”一般适用于螺距大于4mm或精度要求高的梯形螺纹。 学生练习时,先练习车P=2.5的三角螺纹,采用的是直进法车削,最后练习车P=6的梯形螺纹,采用的是左右车削法,方便学生进行比较。现以车Tr42×6-7h螺纹来介绍我是如何指导学生用左右车削法车削梯形螺纹的。 1.将螺纹大径(略小0.15左右)和两端倒角(2X15°)车好,然后将梯形螺纹粗车刀对到工件外圆上,将中滑板调至零位,同时小滑板朝前进方向消除间隙后对零。此举目的是方便学生记住刻度,不易出错。 2.以直进法车螺纹。由于粗车刀刃磨得锋利又耐用,可加大切削深度。如Tr42×6的螺纹,螺纹牙型高度h3=0.5P+ac ,Ac为间隙量取0.5mm,牙高 h3=0.5P+ac=0.5x6+0.5=3.5mm;直径方向为7mm,可第一刀进1.5mm,第二刀 1mm,第三刀0.5mm,共计3mm(此时因刀具三刃受力,难以继续采用大切削深度的直进法车削,如继续切削则会产生卡刀现象,开始使用左右借刀法)。如图所示: 3.用游标卡尺测量此时牙顶宽,将测量牙顶宽减去理论牙顶宽 (W=2.196≈2.2),再减去所留两侧精车余量(0.2~0.4左右,精车余量以两侧面表面粗糙情况而定,表面光洁时取0.2mm,表面粗糙时取0.4mm),这就是借刀的余量,将这个余量除以2,就是每侧借刀的量。例如:我现测得牙顶宽为 4.4mm,则我应向左边借刀的量是[(4.4-2.2)-0.3]/2=0.95mm。当我仍以进刀深度为3mm,向左借刀量为0.95mm车时,梯形螺纹刀只有左侧刃在切削,这个时候只有2条切削刃在受力,切削力不会太大。车完左边借刀的一刀,将小滑板先退后进(消除空行程)对应地在零线右边借刀0.95mm车一刀(也可分两至三刀将借刀量0.95车完),如下图a。车完后将小滑板再次对零。此时刀具就落在车宽了的槽中间,如下图b。