反应烧结制备Si_3N_4_SiC复相陶瓷及其力学性能研究_胡海龙

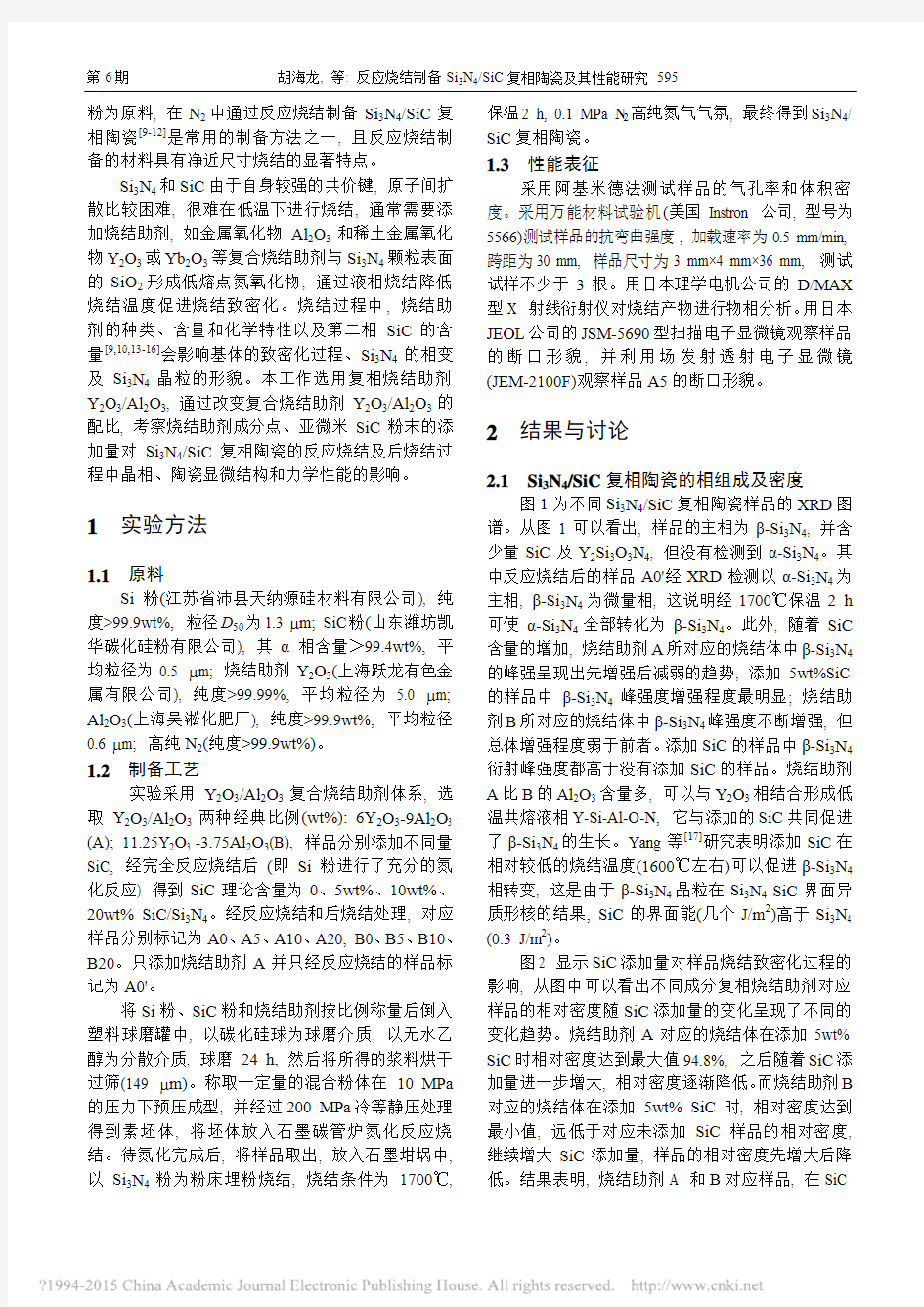
第29卷 第6期 无 机 材 料 学 报
Vol. 29
No. 6
2014年6月
Journal of Inorganic Materials Jun., 2014
收稿日期: 2013-09-17; 收到修改稿日期: 2013-11-11
作者简介: 胡海龙(1989–), 男, 硕士研究生. E-mail:dasmeer@https://www.360docs.net/doc/6218217767.html, 文章编号: 1000-324X(2016)06-0594-05 DOI: 10.3724/SP.J.1077.2014.13469
反应烧结制备Si 3N 4/SiC 复相陶瓷及其力学性能研究
胡海龙1,2, 姚冬旭1, 夏咏锋1, 左开慧1, 曾宇平1
(1. 中国科学院 上海硅酸盐研究所, 高性能陶瓷和超微结构国家重点实验室, 上海 200050; 2. 中国科学院大学,
北京100049)
摘 要: 以两种不同配比Y 2O 3/Al 2O 3 (A, 2:3; B, 3:1, 总量15 wt%)为烧结助剂, 通过添加不同质量分数的SiC 粉体,反应烧结制备了高强度的氮化硅/碳化硅复相陶瓷。并对材料的相组成、相对密度、显微结构和力学性能进行了分析。结果表明: 在1700℃保温2 h 情况下, 烧结助剂A 与B 对应的样品中α-Si 3N 4相全部转化为β-Si 3N 4; 添加5wt% SiC, 烧结助剂A 对应样品的相对密度达到最大值94.8%, 且抗弯强度为521.8 MPa, 相对于不添加SiC 样品的抗弯强度(338.7 MPa)提高了约54.1%。SiC 能有效改善氮化硅基陶瓷力学性能, 且Si 3N 4/SiC 复相陶瓷断裂以沿晶断裂方式为主。
关 键 词: 反应烧结; Si 3N 4/SiC 复相陶瓷; 烧结助剂; SiC 含量 中图分类号: TQ174 文献标识码: A
Mechanical Properties of Reaction-bonded Si 3N 4/SiC Composite Ceramics
HU Hai-Long 1,2, YAO Dong-Xu 1, XIA Yong-Feng 1, ZUO Kai-Hui 1, ZENG Yu-Ping 1
(1. State Key Laboratory of High Performance Ceramics and Superfine Microstructures, Shanghai Institute of Ceramics, Chinese Academy of Sciences, Shanghai 200050, China; 2. University of Chinese Academy of Sciences, Beijing 100049, China)
Abstract: With Y 2O 3:Al 2O 3 (A 2:3; B 3:1 total amount 15wt%) as sintering additives and SiC as the second phase, high flexural strength Si 3N 4/SiC composite ceramics were prepared via nitridation of Si powder. The phase composition, relative density, microstructure as well as mechanical properties were investigated. The experimental results showed that the α→β-Si 3N 4 phase transformation could be completed at 1700℃ for 2 h with sintering additives A or B. With the sintering additive A and 5wt% SiC addition, the maximum relative density of 94.8% and maximum flexural strength of 521.8 MPa were obtained for the Si 3N 4/SiC composite ceramics. As compared with the specimen without SiC addition which flexural strength was 338.7 MPa, flexural strength of the above mentioned Si 3N 4/SiC composite ceramics was improved by 54.1%. SiC powder can effectively improve the mechanical properties of the specimen and the fracture of Si 3N 4/SiC composite ceramics followed the typical intergranular fractural mode.
Key words: reaction-bonded; Si 3N 4/SiC composite ceramics; sintering additives; SiC content
Si 3N 4是性能优异的高温结构陶瓷, 具有高强度、高韧性、高热导、抗热震性等优异特点, 广泛应用于航空、机械、化工等领域。SiC 陶瓷具有良好的热稳定性、耐磨性、耐腐蚀性和抗蠕变性, 广泛应用于密封材料、结构器件及高温耐蚀部件
等[1-3]。通常采用热压烧结[4-5]、气氛烧结[6-7]和高温自蔓延烧结[8]等工艺制备Si 3N 4、SiC 及其复相陶瓷。Si 3N 4/SiC 复相陶瓷结合了Si 3N 4和SiC 陶瓷两者的特性, 具有抗弯强度高、断裂韧性强、抗氧化性好、耐磨和耐腐蚀性好等优异力学性能。以Si 粉和SiC
第6期胡海龙, 等: 反应烧结制备Si3N4/SiC复相陶瓷及其性能研究 595
粉为原料, 在N2中通过反应烧结制备Si3N4/SiC复相陶瓷[9-12]是常用的制备方法之一, 且反应烧结制备的材料具有净近尺寸烧结的显著特点。
Si3N4和SiC由于自身较强的共价键, 原子间扩散比较困难, 很难在低温下进行烧结, 通常需要添加烧结助剂, 如金属氧化物Al2O3和稀土金属氧化物Y2O3或Yb2O3等复合烧结助剂与Si3N4颗粒表面的SiO2形成低熔点氮氧化物, 通过液相烧结降低烧结温度促进烧结致密化。烧结过程中, 烧结助剂的种类、含量和化学特性以及第二相SiC的含量[9,10,13-16]会影响基体的致密化过程、Si3N4的相变及Si3N4晶粒的形貌。本工作选用复相烧结助剂Y2O3/Al2O3, 通过改变复合烧结助剂Y2O3/Al2O3的配比, 考察烧结助剂成分点、亚微米SiC粉末的添加量对Si3N4/SiC复相陶瓷的反应烧结及后烧结过程中晶相、陶瓷显微结构和力学性能的影响。
1 实验方法
1.1原料
Si粉(江苏省沛县天纳源硅材料有限公司), 纯度>99.9wt%, 粒径D50为1.3 μm; SiC粉(山东潍坊凯华碳化硅粉有限公司), 其α相含量>99.4wt%, 平均粒径为0.5 μm; 烧结助剂Y2O3(上海跃龙有色金属有限公司), 纯度>99.99%, 平均粒径为 5.0 μm; Al2O3(上海吴淞化肥厂), 纯度>99.9wt%, 平均粒径
0.6 μm; 高纯N2(纯度>99.9wt%)。
1.2制备工艺
实验采用Y2O3/Al2O3复合烧结助剂体系, 选取Y2O3/Al2O3两种经典比例(wt%): 6Y2O3-9Al2O3 (A); 11.25Y2O3 -3.75Al2O3(B), 样品分别添加不同量SiC, 经完全反应烧结后(即Si粉进行了充分的氮化反应) 得到SiC理论含量为0、5wt%、10wt%、20wt% SiC/Si3N4。经反应烧结和后烧结处理, 对应样品分别标记为A0、A5、A10、A20; B0、B5、B10、B20。只添加烧结助剂A并只经反应烧结的样品标记为A0'。
将Si粉、SiC粉和烧结助剂按比例称量后倒入塑料球磨罐中, 以碳化硅球为球磨介质, 以无水乙醇为分散介质, 球磨24 h, 然后将所得的浆料烘干过筛(149 μm)。称取一定量的混合粉体在10 MPa 的压力下预压成型, 并经过200 MPa冷等静压处理得到素坯体, 将坯体放入石墨碳管炉氮化反应烧结。待氮化完成后, 将样品取出, 放入石墨坩埚中, 以Si3N4粉为粉床埋粉烧结, 烧结条件为1700℃, 保温2 h, 0.1 MPa N2高纯氮气气氛, 最终得到Si3N4/ SiC复相陶瓷。
1.3性能表征
采用阿基米德法测试样品的气孔率和体积密度。采用万能材料试验机(美国Instron 公司, 型号为5566)测试样品的抗弯曲强度, 加载速率为0.5 mm/min, 跨距为30 mm, 样品尺寸为3 mm×4 mm×36 mm, 测试试样不少于3根。用日本理学电机公司的D/MAX 型X 射线衍射仪对烧结产物进行物相分析。用日本JEOL公司的JSM-5690型扫描电子显微镜观察样品的断口形貌, 并利用场发射透射电子显微镜(JEM-2100F)观察样品A5的断口形貌。
2 结果与讨论
2.1Si3N4/SiC复相陶瓷的相组成及密度
图1为不同Si3N4/SiC复相陶瓷样品的XRD图谱。从图1可以看出, 样品的主相为β-Si3N4, 并含少量SiC及Y2Si3O3N4, 但没有检测到α-Si3N4。其中反应烧结后的样品A0'经XRD检测以α-Si3N4为主相, β-Si3N4为微量相, 这说明经1700℃保温2 h 可使α-Si3N4全部转化为β-Si3N4。此外, 随着SiC 含量的增加, 烧结助剂A所对应的烧结体中β-Si3N4的峰强呈现出先增强后减弱的趋势, 添加5wt%SiC 的样品中β-Si3N4峰强度增强程度最明显; 烧结助剂B所对应的烧结体中β-Si3N4峰强度不断增强, 但总体增强程度弱于前者。添加SiC的样品中β-Si3N4衍射峰强度都高于没有添加SiC的样品。烧结助剂A比B的Al2O3含量多, 可以与Y2O3相结合形成低温共熔液相Y-Si-Al-O-N, 它与添加的SiC共同促进了β-Si3N4的生长。Yang等[17]研究表明添加SiC在相对较低的烧结温度(1600℃左右)可以促进β-Si3N4相转变, 这是由于β-Si3N4晶粒在Si3N4-SiC界面异质形核的结果, SiC的界面能(几个J/m2)高于Si3N4 (0.3 J/m2)。
图2 显示SiC添加量对样品烧结致密化过程的影响, 从图中可以看出不同成分复相烧结助剂对应样品的相对密度随SiC添加量的变化呈现了不同的变化趋势。烧结助剂A对应的烧结体在添加5wt% SiC时相对密度达到最大值94.8%, 之后随着SiC添加量进一步增大, 相对密度逐渐降低。而烧结助剂B 对应的烧结体在添加5wt% SiC时, 相对密度达到最小值, 远低于对应未添加SiC样品的相对密度, 继续增大SiC添加量, 样品的相对密度先增大后降低。结果表明, 烧结助剂A 和B对应样品, 在SiC
596
无 机 材 料 学 报 第29卷
图1 不同Si 3N 4/SiC 复相陶瓷样品的XRD 图谱
Fig. 1 XRD patterns of different Si 3N 4
/SiC composite ceramics
图2 SiC 添加量对Si 3N 4/SiC 复相陶瓷相对密度的影响
Fig. 2 Effect of SiC content on the relative density of Si 3N 4/SiC composite ceramics
添加量低于10wt%时, 烧结助剂成分的差异对氮化硅陶瓷的烧结过程具有较明显的影响, Al 2O 3含量越多越易与Y 2O 3相结合形成低温液相, 从而有助于烧结体的致密化。当SiC 添加量大于10wt%时, SiC 对烧结体的致密化过程起强烈抑制作用。
在氮化硅陶瓷的烧结过程中, α→β相变及晶粒的生长基于溶解沉淀机理[18], 通过晶体及晶界表面的四价Si 离子及三价N 离子的扩散或者是两者之间的反应来控制。早期研究认为相变过程与晶粒生长没有直接联系, Yang 等[19]研究发现相变促进晶粒生长和致密化, 而致密化在温度较低时通过晶粒的颈部相互连接实现。并且晶粒生长致密化受烧结助剂的影响, 如Y 2O 3-Al 2O 3复合烧结助剂与Si 3N 4形成Y-Si-Al-O-N 液相, 使氮化硅陶瓷烧结充分, 而相转变则几乎不受其影响。Yang 等[17]研究还发现在相对较低温度时, 添加SiC 有助于β-Si 3N 4晶粒的形核, 这主要是由于SiC 表面能较高, 使得Si 3N 4/SiC 具有较高的表面能(相对于Si 3N 4/Si 3N 4),从而在很大程度上提高了β-Si 3N 4晶粒的结晶形核率。因此, 本实验在SiC 、烧结助剂Al 2O 3与Y 2O 3的共同作用下,
β-Si 3N 4结晶峰强度得以提升。此外, 依据Al 2O 3与Y 2O 3的相图[20], 由于烧结助剂A 的成分点形成低共熔相的温度低于烧结助剂B, 故同一烧结温度下, 相同SiC 添加量, 烧结助剂A 对应烧结体中更易结晶形成β-Si 3N 4。
2.2 Si 3N 4/SiC 复相陶瓷的显微结构
图3是不同SiC 添加量, 烧结助剂A 对应Si 3N 4/SiC 复相陶瓷的断面SEM 照片。由于SiC 的添加及烧结助剂A 含Al 2O 3量较多, 在SiC 的抑制作用下, 样品A0、A5、A10、A20的颗粒中没有明显的β-Si 3N 4柱状晶粒, 样品A5的孔隙率最小。
图4是不同SiC 添加量, 烧结助剂B 对应Si 3N 4/SiC 复相陶瓷的断面SEM 照片。由于烧结助剂B 所含的Al 2O 3量较少, 以Y 2O 3含量为主, 所有样品中都出现了不同长径比的柱状β-Si 3N 4晶粒, 这
图3 不同SiC 添加量, 烧结助剂A 对应Si 3N 4/SiC 复相陶瓷
的断面SEM 照片
Fig. 3 SEM fracture surfaces of Si 3N 4/SiC composite ceramics prepared with additive A and different contents of SiC
图4 不同SiC 添加量, 烧结助剂B 对应Si 3N 4/SiC 复相陶瓷的断面SEM 照片
Fig. 4 SEM fracture surfaces of Si 3N 4/SiC composite ceramics prepared with B additive and different contents of SiC
第6期胡海龙, 等: 反应烧结制备Si3N4/SiC复相陶瓷及其性能研究 597
与Satio等[21]的研究结果相符合。他们的研究表明, 在SiO2/Al2O3为定值的情况下, 随着Y2O3含量的增加, 烧结熔体的粘度会线性降低, 从而促进β-Si3N4晶粒的生长[21]。但是随着SiC添加量增大, 在液相烧结过程中晶粒重排及偏转受阻, 致密化过程难以进行, 样品中会出现不同程度的空隙。Hirao等[22]在研究中发现Si3N4晶粒的尺寸和长径比对材料的微观结构和力学性能有很大影响。烧结助剂B对应样品B5与B20相比较, 其相对密度几乎相同(图2), 显微结构相同, 都存在β-Si3N4晶粒的相互交叠堆积, 但样品B20 的β-Si3N4晶粒长径比较大, 且晶粒相互交叠程度更加明显, 故抗弯强度会高于样品 B5。而对于B5, 由于此时SiC添加量为5wt%, 此时形成长径比相对较小的β-Si3N4晶粒, 晶粒之间相互交错和桥联导致基体出现了较多的显微孔洞, 降低了基体的致密度, 最终降低了材料的力学性能。另外, 由于样品B10相对密度高于B5和B20, 故其抗弯曲强度会较高, 这结果符合抗弯曲强度与孔隙率的理论方程。
图5 所示为烧结助剂A 与B对应样品A5与B0的断面SEM照片。从图5可得知, 样品A5、B0中都出现了柱状的β-Si3N4晶粒, 样品B0颗粒的长径比更大, 大约为3, 但样品A5颗粒大小分布更加均匀, 并有亚微米(0.5 μm左右)的SiC颗粒钉扎于其中, 增强了基体, 如图5(a)插图的白色三角形所示。由图2显示A5的相对密度为94.8%, B0的相对密度为96.0%; 由图6显示A5的抗弯强度为521.8 MPa, B0的抗弯强度373.3 MPa。这说明SiC 颗粒虽然降低了氮化硅陶瓷基体的致密度, 但由于其钉扎作用, 增强了基体, 反而使抗弯强度得以提高, 且A5与 B0样品的断面SEM表明, 晶粒的断裂模式均以沿晶断裂为主。
2.3 Si3N4/SiC复相陶瓷的力学性能
氮化硅陶瓷的力学性能取决于显微结构及相对
图5 (a) 烧结助剂A对应的烧结体A5的SEM照片(插图为对应TEM照片); (b) 烧结助剂B对应的烧结体B0的SEM照片Fig. 5 (a) SEM image of fracture surface of the sintered sample A5 (Inset is the corresponding TEM image); (b) SEM
image of fracture surface of the sintered sample B0 图6 SiC添加量对Si3N4/SiC复相陶瓷抗弯强度的影响Fig. 6 Effect of SiC content on the flexural strength of Si3N4/SiC composite ceramics with additives A or B
密度, 尤其是显微结构中β-Si3N4晶粒的形貌与尺寸[23](即长径比的大小)。根据裂纹扩展中晶粒的桥接, 晶粒的拔出及偏韧化模型, 当氮化硅显微结构中高长径比的晶粒数量增多时, 将呈现良好的力学性能。另外抗弯强度与相对密度的关系可由以下方程表述[24]:
=exp()p
σσβ-(1) 其中σ0 为孔隙率为0时对应的抗弯强度, β为材料的结构因子, p为孔隙率。由方程(1)可知, 材料的孔隙率越低, 即相对密度越高, 则材料的抗弯强度越大。
图6 是SiC添加量对Si3N4/SiC复相陶瓷抗弯强度的影响, 从图中可以看出, 随着SiC添加量增加, 样品的抗弯强度呈现倒“V”型或倒“N”型的变化趋势。添加5wt% SiC, 样品A5的抗弯强度达到最大值521.8 MPa, 相对于未添加SiC的样品A0, 抗弯强度提高了约54.1%, 此值优于文献[9]报道的Si3N4/SiC复相陶瓷最大抗弯曲强度值。文献[9]采用放电等离子体烧结与反应烧结相结合, 不添加烧结助剂, 在SiC晶须含量为50wt%时, 即50wt% SiC/Si3N4的抗弯强度达到275 MPa。而样品B5的抗弯强度达到最小值, 随着SiC添加量继续增大, 样品B10的抗弯强度升高至343.3 MPa(低于不添加SiC的样品B0的抗弯强度373.3 MPa), 但此抗弯强度仍优于文献[10]的最大抗弯强度(165 MPa左右) (15wt% SiC/Si3N4, 采用复合烧结助剂Al2O3/MgO, 且SiC为纳米级, 45 nm)。由此可看出SiC添加量少于10wt%时, SiC对烧结体的抗弯强度影响很大。且烧结助剂中Al2O3含量较多时, 有助于SiC增强基体Si3N4 陶瓷; 而当Y2O3含量较多时, 由于液相粘度的降低[20], 形成的β-Si3N4晶粒会出现晶粒交错和晶粒桥联现象(如图4所示), 导致出现更多的显微孔洞, 降低了材料的力学性能, 从而抑制了SiC
598 无机材料学报第29卷
的增强作用。当SiC添加量大于10wt%时, SiC对烧结体致密化过程产生明显抑制, 此时相对密度和抗弯强度都随着SiC量的增加不断降低。
3结论
1) 以Si和SiC粉, 高纯N2, 烧结助剂Y2O3与Al2O3为起始原料, 利用反应烧结制备技术, 通过调节烧结助剂的成分和SiC的添加量, 采用常压烧结制备了力学性能优良的Si3N4/SiC复相陶瓷。
2) 当SiC添加量低于10wt%时, 烧结助剂成分中更多含量的Al2O3有助于β-Si3N4的结晶形成和基体致密度的提高, 从而提升了基体的抗弯强度; 而更多含量的Y2O3有助于β-Si3N4柱状晶粒的生长, 降低了基体的致密度, 使基体的抗弯强度降低。SiC 添加量大于10wt%时, SiC对烧结体致密化过程产生明显抑制。
3) SiC颗粒的存在很大程度上增加了β-Si3N4的形核率, 促进了β-Si3N4的结晶形成。添加少量SiC, 可以提高复相陶瓷的抗弯强度, 且烧结体的断面模式以晶粒的沿晶断裂为主。
参考文献:
[1]RILEY F L. Silicon nitride and related materials. J. Am. Ceram.
Soc., 2000, 83(2): 245–265.
[2]NIHARA K. New Design concept of structural ceramics - ceramic
nanocomposites. Nippon Seram Kyo Gak., 1991, 99(10): 974?982. [3]STREHLER C, GRAULE T, KUEBLER J, et al. Lifetime and
wear behavior of near net shaped Si3N4/SiC wood cutting tools. Int.
J. Appl. Ceram. Technol., 2012, 9(2): 280?290.
[4]LUO F, ZHU D M, SU X L, et al. Properties of hot-pressed of
SiC/Si3N4 nanocomposites. Mater. Sci. Eng., 2007, 458(1/2): 7?10.
[5]SAJGALIK P, HNATKO M, COPAN P, et al. Influence of graphite
additives on wear properties of hot pressed Si3N4 ceramics. J.
Ceram. Soc. Jpn., 2006, 114(1335): 1061?1068.
[6]RENDTEL P, RENDTEL A, HUBNER H. Mechanical properties
of gas pressure sintered Si3N4/SiC nanocomposites. J. Eur. Ceram.
Soc., 2002, 22(12): 2061?2070.
[7]SANTOS C, KELLY C A, RIBEIRO S, et al. α-SiAlON-SiC
composites obtained by gas-pressure sintering and hot-pressing. J.
Mater. Process. Technol., 2007, 189(1/2/3): 138?142.
[8]ZHENG C S, YAN Q Z, XIA M, et al. In situ preparation of
SiC/Si3N4-NW composite powders by combustion synthesis.
Ceram. Int., 2012, 38(1): 487?493.
[9]LI J F, SATOMI S, WATANABE R, et al. Fabrication and
characterization of SiC rod particulate reinforced reaction-bonded S i3N4 composites. J. Eur. Ceram. Soc., 2000, 20(11): 1795?1802. [10]LUO F, ZHU D M, ZHANG H, et al. Properties of reaction-
bonded SiC/Si3N4 ceramics. Mater. Sci. Eng. A, 2006, 431(1/2):
285?289.
[11]YUAN L, JING K Y, ZHANG S W. Fabrication of porous reaction-
bonded Si3N4-SiC composites. Adv. Mater. Res., 2011, 391-392:
575?579.
[12]LI J, YUAN W J, WANG S, et al. Effect of sintering temperatures
on the reaction-bonded Si3N4/SiC composite ceramics. Adv. Mater.
Res., 2011, 399-401: 331?335.
[13]YANG J, YANG J F, SHAN X Y, et al. Effect of sintering additives
on microstructure and mechanical properties of porous silicon nitride ceramics. J. Am. Ceram. Soc., 2006, 89(12): 3843?3845. [14]ZHU X W, ZHOU Y, HIRAO K. Effect of sintering additive on the
processing and thermal conductivity of intered reaction-bonded Si3N4.J. Am. Ceram. Soc., 2004, 87(7): 1398?1400.
[15]LEE B T, KIM H D. Effect of sintering additives on the nitridation
behavior of reaction-bonded silicon nitride. Mater. Sci. Eng., 2004,
A(364): 126?131.
[16]STREHLER C, BLUGAN G, EHRLE B, et al. Influence of
sintering and sintering additives on the mechanical and microstructural characteristics of Si3N4/SiC wood cutting tools. J.
Eur. Ceram. Soc., 2010, 30(10): 2109?2115.
[17]YANG J F, TATSUKI O, SEKINO T, et al. Phase transformation,
microstructure and mechanical properties of Si3N4/SiC composite.
J. Eur. Ceram. Soc., 2001, 21(12): 2179?2183.
[18]SARIN V K. On the α to β phase transformation in silicon nitride.
Mater. Sci. Eng.,1988, 105-106(1): 151?159.
[19]YANG J F, TATSUKI O. Influence of yttria-alumina content on
sintering behavior and microstructure of silicon nitride ceramics. J.
Am. Ceram. Soc., 2000, 83(8): 2094?2096.
[20]TAGUCHI S P, MOTTA F V, BALESTRA R M, et al. Wetting
behaviour of SiC ceramics. II. Y2O3/Al2O3 and Sm2O3/Al2O3.
Mater. Lett., 2004, 58(22): 2810?2844.
[21]SAITO N, KAI K, FURUSHO S, et al. Properties of nitrogen-
containing yttria-alumina-silica melts and glasses. J. Am. Ceram.
Soc., 2003, 86(4): 711?716.
[22]HIRAO T, NIIHARA K. Microstructure and mechanical properties
of Si3N4/SiC composites. Mater. Lett., 1995, 22(5/6): 249?254. [23]HEINRICH J, BACKER E, BOHMER M. Hot isostatic pressing of
Si3N4 powder compacts and reaction-bonded Si3N4. J. Am. Ceram.
Soc., 1988, 71(1): C28?C31.
[24]COBLE R L, KINGERY W D. Effect of porosity on physical
properties of sintered alumina. J. Am. Ceram. Soc., 1956, 39(11):
337?385.
最新金属的力学性能测试题及答案
第一章金属的力学性能 一、填空题 1、金属工艺学是研究工程上常用材料性能和___________的一门综合性的技术基础课。 2、金属材料的性能可分为两大类:一类叫_____________,反映材料在使用过程中表现出来的特性, 另一类叫__________,反映材料在加工过程中表现出来的特性。 3、金属在力作用下所显示与弹性和非弹性反应相关或涉及力—应变关系的性能,叫做金属________。 4、金属抵抗永久变形和断裂的能力称为强度,常用的强度判断依据是__________、___________等。 5、断裂前金属发生不可逆永久变形的能力成为塑性,常用的塑性判断依据是________和_________。 6、常用的硬度表示方法有__________、___________和维氏硬度。 二、单项选择题 7、下列不是金属力学性能的是() A、强度 B、硬度 C、韧性 D、压力加工性能 8、根据拉伸实验过程中拉伸实验力和伸长量关系,画出的力——伸长曲线(拉伸图)可以确定出金 属的() A、强度和硬度 B、强度和塑性 C、强度和韧性 D、塑性和韧性 9、试样拉断前所承受的最大标称拉应力为() A、抗压强度 B、屈服强度 C、疲劳强度 D、抗拉强度 10、拉伸实验中,试样所受的力为() A、冲击 B、多次冲击 C、交变载荷 D、静态力 11、属于材料物理性能的是() A、强度 B、硬度 C、热膨胀性 D、耐腐蚀性 12、常用的塑性判断依据是() A、断后伸长率和断面收缩率 B、塑性和韧性 C、断面收缩率和塑性 D、断后伸长率和塑性 13、工程上所用的材料,一般要求其屈强比() A、越大越好 B、越小越好 C、大些,但不可过大 D、小些,但不可过小 14、工程上一般规定,塑性材料的δ为() A、≥1% B、≥5% C、≥10% D、≥15% 15、适于测试硬质合金、表面淬火刚及薄片金属的硬度的测试方法是() A、布氏硬度 B、洛氏硬度 C、维氏硬度 D、以上方法都可以 16、不宜用于成品与表面薄层硬度测试方法() A、布氏硬度 B、洛氏硬度 C、维氏硬度 D、以上方法都不宜 17、用金刚石圆锥体作为压头可以用来测试() A、布氏硬度 B、洛氏硬度 C、维氏硬度 D、以上都可以 18、金属的韧性通常随加载速度提高、温度降低、应力集中程度加剧而() A、变好 B、变差 C、无影响 D、难以判断 19、判断韧性的依据是() A、强度和塑性 B、冲击韧度和塑性 C、冲击韧度和多冲抗力 D、冲击韧度和强度 20、金属疲劳的判断依据是() A、强度 B、塑性 C、抗拉强度 D、疲劳强度 21、材料的冲击韧度越大,其韧性就() A、越好 B、越差 C、无影响 D、难以确定 三、简答题 22、什么叫金属的力学性能?常用的金属力学性能有哪些?
橡胶力学性能测试标准
序号标准号:发布年份标准名称(仅供参考) 1 GB 1683-1981 硫化橡胶恒定形变压缩永久变形的测定方法 2 GB 1686-1985 硫化橡胶伸张时的有效弹性和滞后损失试验方法 3 GB 1689-1982 硫化橡胶耐磨性能的测定(用阿克隆磨耗机) 4 GB 532-1989 硫化橡胶与织物粘合强度的测定 5 GB 5602-1985 硫化橡胶多次压缩试验方法 6 GB 6028-1985 硫化橡胶中聚合物的鉴定裂解气相色谱法 7 GB 7535-1987 硫化橡胶分类分类系统的说明 8 GB/T 11206-1989 硫化橡胶老化表面龟裂试验方法 9 GB/T 11208-1989 硫化橡胶滑动磨耗的测定 10 GB/T 11210-1989 硫化橡胶抗静电和导电制品电阻的测定 11 GB/T 11211-1989 硫化橡胶与金属粘合强度测定方法拉伸法 12 GB/T 1232.1-2000 未硫化橡胶用圆盘剪切粘度计进行测定第1部分:门尼粘度的测定 13 GB/T 12585-2001 硫化橡胶或热塑性橡胶橡胶片材和橡胶涂覆织物挥发性液体透过速率的测定(质量法) 14 GB/T 12829-2006 硫化橡胶或热塑性橡胶小试样(德尔夫特试样)撕裂强度的测定 15 GB/T 12830-1991 硫化橡胶与金属粘合剪切强度测定方法四板法 16 GB/T 12831-1991 硫化橡胶人工气候(氙灯)老化试验方法 17 GB/T 12834-2001 硫化橡胶性能优选等级 18 GB/T 13248-1991 硫化橡胶中锰含量的测定高碘酸钠光度法 19 GB/T 13249-1991 硫化橡胶中橡胶含量的测定管式炉热解法 20 GB/T 13250-1991 硫化橡胶中总硫量的测定过氧化钠熔融法 21 GB/T 13642-1992 硫化橡胶耐臭氧老化试验动态拉伸试验法 22 GB/T 13643-1992 硫化橡胶或热塑性橡胶压缩应力松弛的测定环状试样 23 GB/T 13644-1992 硫化橡胶中镁含量的测定CYDTA滴定法 24 GB/T 13645-1992 硫化橡胶中钙含量的测定EGTA滴定法 25 GB/T 13934-2006 硫化橡胶或热塑性橡胶屈挠龟裂和裂口增长的测定(德墨西亚型) 26 GB/T 13935-1992 硫化橡胶裂口增长的测定 27 GB/T 13936-1992 硫化橡胶与金属粘接拉伸剪切强度测定方法 28 GB/T 13937-1992 分级用硫化橡胶动态性能的测定强迫正弦剪切应变法 29 GB/T 13938-1992 硫化橡胶自然贮存老化试验方法 30 GB/T 13939-1992 硫化橡胶热氧老化试验方法管式仪法 31 GB/T 14834-1993 硫化橡胶与金属粘附性及对金属腐蚀作用的测定 32 GB/T 14835-1993 硫化橡胶在玻璃下耐阳光曝露试验方法 33 GB/T 14836-1993 硫化橡胶灰分的定性分析 34 GB/T 15254-1994 硫化橡胶与金属粘接180°剥离试验 35 GB/T 15255-1994 硫化橡胶人工气候老化(碳弧灯)试验方法 36 GB/T 15256-1994 硫化橡胶低温脆性的测定(多试样法) 37 GB/T 15584-1995 硫化橡胶在屈挠试验中温升和耐疲劳性能的测定第一部分:基本原理 38 GB/T 15905-1995 硫化橡胶湿热老化试验方法 39 GB/T 16585-1996 硫化橡胶人工气候老化(荧光紫外灯)试验方法 40 GB/T 16586-1996 硫化橡胶与钢丝帘线粘合强度的测定 41 GB/T 16589-1996 硫化橡胶分类橡胶材料
力学性能检测试验仪器
力学性能检测试验仪器 一、力学性能检测试验仪器技术参数:最大试验力:5KN负荷传感器容量:0.5T(5KN)(能加配1个或多个其他容量的负荷传感器) ?精度等级:0.5级试验力测量范围:0.4%~100%FS(满量程)试验力分辨率:最大试验力的±1/300000,全程不分档,且分辨率不变。力控制:力控控制速度范围:0.001%~5%FS/s。力控速度控制精度:0.001%~1%FS/s 时,±0.2%;1%~5%FS/s时,±0.5力控保持精度: ±0.002%FS。变形控制:变形控控制速度范围:0.001%~5%FS/s。变形控速度控制精度:0.001%~1%FS/s时,±0.2%;1%~5%FS/s时,±0.5%。变形控保持精度:±0.002%FS。位移控制:位移控控制速度范围:0.0001~1000mm/min。位移控速度控制精度:±0.2%;位移控保持精度:无误差。有效试验宽度:120mm、360mm、410mm三种规格有效拉伸空间:800mm有效压缩行程:800mm控制系统:全微机自动控制。单位选择:g/Kg/N/KN/Lb多重保护:系统具有过流、过压、欠流、欠压等保护;行程具有程控限位、极限限位、软件限位三重保护。出现紧急情况可进行紧急制动。主机结构:门式,结构新颖,美观大方,运行平稳电源:220V 50Hz功率:0.4Kw主机重量:95,130Kg主机外型尺寸:650*360*1600,800*410*1600 ?二、力学性能检测试验仪器使用范围及技术说明:1、适用范围QX-W400 微机控制电子万能试验机为材料力学性能测量的试验设备,可进行金属线材与非金属、高分子材料等的拉伸、剥离、压缩、弯曲、剪切、顶破、戳穿、疲劳等项目的检测。可根据客户产品要求按GB、ISO、ASTM、JIS、EN等标准编制,能自动求取最大试验力,断裂力,屈服力,抗拉强度,抗压强度,弯曲强
烧结工艺技术操作要点
烧结工艺技术操作要点 根据公司颁发《关于工艺技术标准化操作推进实施方案的通知》要求,为确保我厂烧结、球团生产过程正常、稳顺进行,实现生产、工艺、技术、操作精细化管理,达到提高产品质量、降低生产成本,为下道工序高炉稳顺及增铁节焦创造条件。特此,在中和预配料、烧结及球团主要工序和关键岗位制定以下工艺技术操作要点。 一、中和预配料 1、严格按厂(技术室)下达的预配比通知单进行配料,并要求认真做好配料原始记录。 2、每班进行1-2次清理配料圆盘闸门口、电子皮带秤杂物,给料不畅及时挫料,严禁缺品种配料或少配后补。 3、配料作业中,做到勤检查,岗位巡回检查30分种一次。 4、电子皮带秤:每班校皮不少于一次;电子皮带秤校秤为6个月一次,配料工及车间工艺员配合校验,并要求有校秤文字记录。发现电子皮带秤计量不准,应在4小时反映。电子皮带秤架必须保持清洁,辊子无粘料,清扫器要刮料干净,配料误差控制在1%之内。 5、二次料场:堆料机在规定堆位及长度上逐层平铺造堆,保证混匀效果;禁止分段平铺、空段和定点堆料;料层数控制在300层以上。 6、产量:配料流量控制在1100t/h之内,二次料场A跨每堆控制在6万吨±5000吨,B跨控制在9.5万吨±5000吨,C跨每堆控制在8.5万吨±5000吨,雨季各减1万吨。
7、质量:每堆料品位稳定率(Fe±0.5%)达75%之上,二氧化硅稳定率(SiO2±0.5%)达95%之上。 二、烧结 1、配料工序 1.1严格执行技术科下达的配料通知单,精心配料,坚决杜绝断品种配料和乱配现象。如发生碱度波动:三烧由配料工可调节石粉和中和料配比,二烧由主控工调节石粉和中和料配比,并要求认真做好配料原始记录。 1.2根据烧结生产需要,确保烧结矿实物质量的前提下,三烧(130/180)双机生产配重按580—650t/h控制为宜;三烧如遇单机生产则配重减半范围控制;二烧(280m2)配重按630—700t/h控制为宜。 1.3配料电子皮带秤:如发现皮带秤计量不准,应在4小时内联系信息自动化中心组织校秤,配料工及车间工艺员配合校验,并要求有校秤文字记录。 1.4配料作业中,做到勤检查,岗位巡回检查60分种一次。 2、混合工序 2.1一次混合主要是加水混匀,包括生石灰消化;混合料水份配加以一次圆筒加足所需水份的80—90%为宜。 2.2二次混合:一是补充加水,另二主要是混匀制粒,提高混合料透气性。二次圆筒加水20—10%为宜。 2.3一次、二次混合料的水分测定,由红外测水仪监控与调节;二烧 (280m2)、三烧(130/180)混合料控制适宜水份分别为6—9%。正常生产时,由红外线自动加水系统自动控制混合加水量。 2.4当水份自动检测系统出现故障时,岗位人员根据上料量、返矿量的变
金属材料的力学性能及其测试方法
目录 摘要1 1引言2 2金属材料的力学性能简介2 2.1 强度3 2.2 塑性3 2.3 硬度3 2.4 冲击韧性4 2.5 疲劳强度4 3金属材料力学性能测试方法4 3.1拉伸试验5 3.2压缩试验8 3.3扭转试验11 3.4硬度试验15 3.5冲击韧度试验22 3.6疲劳试验27 4常用的仪器设备简介29 4.1万能试验机29 4.2扭转试验机34 4.3摆锤式冲击试验机40 5金属材料力学性能测试方法的发展趋势42 参考文献42
金属材料的力学性能及其测试方法 摘要:金属的力学性能反映了金属材料在各种形式外力作用下抵抗变形或破坏的某些能力,它与材料的失效形式息息相关。本文主要解释了金属材料各项力学性能的概念,介绍了几个常见的测试金属材料力学性能的试验以及相关的仪器设备,最后阐述了金属材料力学性能测试方法的发展趋势。 关键词:金属材料,力学性能,测试方法,仪器设备,发展趋势 Test Methods for The Mechanical Properties of Metal Material Abstract:The mechanical properties of metal material which reflect some abilities of deformation and fracture resistance under various external forces are closely linked with failure forms. This paper mainly introduces some concepts of mechanical properties of metal material, mon experiments testing mechanical properties of metal material and apparatuses used. The trend of development of test methods for mechanical properties of metal material is also discussed. Keywords:metal material,mechanical properties,test methods,apparatuses,development trend
烧结技术综述
1文献综述 1.1烧结生产概况 1.1.1烧结及其发展 烧结法是迄今为止除北美以外使用最为广泛的铁矿石造块方法。自20世纪80年代起烧结技术得到了快速发展,主要体现在烧结工艺和新技术的研究开发和应用上。烧结工艺方面如自动化配料、混合料强化制粒、偏析布料、冷却筛分、整粒技术及铺底料技术等;新技术主要表现为球团烧结技术、小球烧结技术、低温烧结技术等。上述工艺和技术目前已经在大部分钢铁企业推广应用,并取得了显著的经济效益。 1897年,T.Huntington和F,Heberlein申请并注册了第一个有关烧结方面的专利。1905年,E.J.Savelsberg首先把T.Huntington-F.Heberlein烧结杯用于铁矿石烧结,从而开辟了烧结法进行铁矿粉造块的新纪元。在当今的冶金生产中,烧结已成为一道重要的单元工序并占有相当重要地位。据统计,全世界约有一半的生铁是用烧结矿生产的。过去十年中,世界上烧结矿年产量维持在538×106t~586×106t范围内。从1989年起,由于独联体和其他部分东欧国家发生巨变,因此,它们的钢铁工业进行了重新调整,导致烧结矿产量有所下降。欧洲和日本的经济衰退也影响了产量,但是不久烧结矿的产量又慢慢恢复。东欧和独联体的产量将下降,而中国、朝鲜和台湾的产量将继续上升。尽管出现新的炼铁工艺,但是在下一个十年中或更长的时间内,它们仍不可能对高炉产量有巨大影响。因此,烧结矿产量在未来相当长的时间内仍将维持在目前水平。 1.1.2烧结生产目的 铁矿粉烧结是一种铁矿粉造块的方法,是将细粒含铁物料与燃料、熔剂按一定比例混合,再加水润湿、混匀和制粒成为烧结料,加于烧结设备上,点火、抽风,借助燃料燃烧产生高温和一系列物理化学变化,生成部分低熔点物质,并软化熔融产生一定数量的液相,将铁矿物颗粒润湿粘结起来,冷却后,即成为具有一定强度的多孔块状产品一侥结矿。 烧结生产的目的主要是: 1.将粉状物料制成具有高温强度的块状料以适应高炉冶炼、直接还原等在流体力学方面的要求; 2.通过烧结改善铁矿石的冶金性能,使高炉冶炼指标得到改善; 3.通过烧结去除某些有害杂质,回收有益元素以达到综合利用资源和扩大炼铁矿石原料资源的目的。 1.1.3烧结反应过程 烧结反应过程是分层依次向下进行的。抽入的空气通过已烧结好的热烧结矿
聚四氟乙烯的烧结工艺技术
万方数据
万方数据
万方数据
聚四氟乙烯的烧结工艺技术 作者:汪萍, Wang Ping 作者单位:武汉市工程塑料有限公司 刊名: 工程塑料应用 英文刊名:ENGINEERING PLASTICS APPLICATION 年,卷(期):2001,29(3) 被引用次数:16次 参考文献(1条) 1.钱知勉氟塑料加工 1987 本文读者也读过(10条) 1.杜小刚.刘亚青.DU Xiao-gang.LIU Ya-qing聚四氟乙烯的加工成型方法[期刊论文]-绝缘材料2007,40(3) 2.陈旭.回素彩.CHEN Xu.HUI Su-cai聚四氟乙烯烧结成型的制备工艺[期刊论文]-塑料工业2005,33(10) 3.刘先兰聚四氟乙烯(PTFE)制品的成型工艺及质量分析[期刊论文]-现代机械2003(3) 4.徐下忠.乐启发.张良武聚四氟乙烯的加工成型技术[期刊论文]-工程塑料应用2002,30(3) 5.谭清明.Tan Qingming聚四氟乙烯复合材料烧结过程温度控制研究[期刊论文]-润滑与密封2009,34(7) 6.付海梅.王伟明.刘继红.FU Hai-rmei.WANG Wei-ming.LIU Ji-hong聚四氟乙烯成型加工新技术[期刊论文]-塑料工业2005,33(z1) 7.于清.丛培强聚四氟乙烯缠绕吹胀成型制品与橡胶复合的技术[期刊论文]-塑料科技2003(5) 8.姚荣庆.YAO Rong-qing基于工艺创新的聚四氟乙烯模压成型设备[期刊论文]-轻工机械2007,25(3) 9.蔡之桂.CAI Zhi-gui冷拉伸、热收缩聚四氟乙烯制品成型技术[期刊论文]-塑料2000,29(2) 10.伍昭平填充四氟烧结工艺改进[会议论文]-2000 引证文献(16条) 1.周晓亮.周军霞聚四氟乙烯同轴电缆推挤成型工艺及难点解析[期刊论文]-现代传输 2012(4) 2.杜小刚.刘亚青聚四氟乙烯的加工成型方法[期刊论文]-绝缘材料 2007(3) 3.胡萍.姜明.汪巍.吴愧.石亚铃聚四氟乙烯基固体润滑剂结晶度、冷却工艺及摩擦性能相关性研究[期刊论文]-润滑与密封 2006(2) 4.王科.谢苏江陶瓷填充聚四氟乙烯密封材料的制备与性能研究[期刊论文]-液压气动与密封 2010(7) 5.谭清明聚四氟乙烯复合材料烧结过程温度控制研究[期刊论文]-润滑与密封 2009(7) 6.张明强.曾黎明.向昊空心玻璃微珠/聚四氟乙烯复合材料的性能研究[期刊论文]-塑料工业 2008(9) 7.胡思前.张玉敏聚四氟乙烯绝缘子的研制与应用[期刊论文]-绝缘材料 2005(5) 8.田华.解旭东.宋希文TiO2改性PTFE复合材料力学与摩擦性能的研究[期刊论文]-内蒙古科技大学学报 2010(4) 9.廖立聚四氟乙烯加工技术、填充改性及应用进展[期刊论文]-当代化工 2010(6) 10.豆立新.龚烈航.沈健.吕振坚.龚天平.周键钊复合材料添加剂对改性PTFE的摩擦转移膜的形成和稳定作用[期刊论文]-复合材料学报 2004(2) 11.豆立新.龚烈航.沈健.吕振坚.何晓晖.龚天平纳米稀土对复合材料中超细粒子团聚现象的抑制(Ⅰ)--超细金属铜粉团聚现象及其团聚成因[期刊论文]-中国稀土学报 2003(z1) 12.马红钦.朱慧铭.谭欣.张晓军聚四氟乙烯在烧碱蒸发器防、除垢中应用的研究[期刊论文]-氯碱工业 2002(6) 13.孙小波.李建星.时连卫.王子君聚四氟乙烯/聚苯酯耐磨自润滑保持架材料的研究[期刊论文]-轴承 2011(2) 14.康玉昆化工用衬四氟管的损坏分析和处理[期刊论文]-化工设备与管道 2010(5)
金属材料的力学性能及其测试方法
目录 摘要 (1) 1引言 (1) 2金属材料的力学性能简介 (2) 2.1 强度 (2) 2.2 塑性 (2) 2.3 硬度 (2) 2.4 冲击韧性 (3) 2.5 疲劳强度 (3) 3金属材料力学性能测试方法 (3) 3.1拉伸试验 (3) 3.2压缩试验 (6) 3.3扭转试验 (8) 3.4硬度试验 (11) 3.5冲击韧度试验 (16) 3.6疲劳试验 (19) 4常用的仪器设备简介 (20) 4.1万能试验机 (20) 4.2扭转试验机 (23) 4.3摆锤式冲击试验机 (28) 5金属材料力学性能测试方法的发展趋势 (30) 参考文献 (30)
金属材料的力学性能及其测试方法 摘要:金属的力学性能反映了金属材料在各种形式外力作用下抵抗变形或破坏的某些能力,它与材料的失效形式息息相关。本文主要解释了金属材料各项力学性能的概念,介绍了几个常见的测试金属材料力学性能的试验以及相关的仪器设备,最后阐述了金属材料力学性能测试方法的发展趋势。 关键词:金属材料,力学性能,测试方法,仪器设备,发展趋势 Test Methods for The Mechanical Properties of Metal Material Abstract:The mechanical properties of metal material which reflect some abilities of deformation and fracture resistance under various external forces are closely linked with failure forms. This paper mainly introduces some concepts of mechanical properties of metal material, common experiments testing mechanical properties of metal material and apparatuses used. The trend of development of test methods for mechanical properties of metal material is also discussed. Keywords:metal material,mechanical properties,test methods,apparatuses,development trend 1引言 材料作为有用的物质,就在于它本身所具有的某种性能,所有零部件在运行过程中以及产品在使用过程中,都在某种程度上承受着力或能量、温度以及接触介质等的作用,选用材料的主要依据是它的使用性能、工艺性能和经济性,其中使用性能是首先需要满足的,特别是针对性的材料力学性能往往是材料设计和使用所追求的主要目标。材料性能测试与组织表征的目的就是要了解和获知材料的成分、组织结构、性能以及它们之间的关系。而人们要有效地使用材料,首先必须要了解材料的力学性能以及影响材料力学性能的各种因素。因此,材料力学性能的测试是所有测试项目中最重要和最主要的内容之一。 在人类发展的历史长河过程中,人们已经建立了许多反映材料表面的和内在的各种关于力学、物理等相关材料性能的测试和分析技术,近现代科学的发展已使材料性能测试分析从经验发展并建立在现代物理理论和试验的基础之上,并且
烧结工艺流程图
烧结工艺流程图: 图片: 烧结工艺流程图: 烧结是钢铁生产工艺中的一个重要环节,它是将铁矿粉、粉(无烟煤)和石灰按一定配比混匀。经烧结而成的有足够强度和粒度的烧结矿可作为炼铁的熟料。利用
烧结熟料炼铁对于提高高炉利用系数、降低焦比、提高高炉透气性保证高炉运行均 有一定意义。 由于烧结技术具体的作用和应用太广泛了, 以下介绍一下烧结生产在钢铁工业 粉矿造块的意义和作用 我国的铁矿石大部分都是贫矿,贫矿直接入炉炼铁是很不合算b,因此必须将贫矿进行破碎、选出高品位的精矿后,再将精矿粉造块成为人造富矿才能入高炉冶炼。 所以,粉矿造块是充分合理利用贫矿的不可缺少的关控环节。 富矿的开采过程中要产生粉矿,为了满足高炉的粒度要兔在整较过程中也会产生粉矿,粉矿直接入炉会51起高炉不顺。恶化高炉技术经济指标,因此粉矿也必须经 过造块才能入炉。 粉矿经过迭决后,可以进一步控制相改善合铁原料的性肠获得气孔串高、还原性好、强度合适、软熔温度较高、成份稳定的优质冶金原料,有助于炉况的稳定和技术经济指标的改善。粒矿造块过程中,还可以除去部份有害杂质,如硫、氟、砷、锌等,有利于提高生铁的质量。因为人造富矿比天然富矿更具有优越性,成为了现 代商炉原料的主要来源。 粉矿迭块还可综合利用含铁、合被、台钙的粉状工业废料,如高炉炉尘、钢迢、轧钢皮、均热炉渣、硫酸渣、染料铁红、电厂烟尘灰笔适当配入可以成为廉价的高炉好原料,又可以减少环境污染,取得良好的经济效益和社会效益。 粉矿造铁是现代高炉冶炼并获得优质高产的基础,对于高炉冶炼有君十分重要的意义,是钢铁工业生产必不可少的重要工序,对钢铁生产的发展起着重要作用。
炼铁烧结厂工艺流程
烧结生产工艺流程 钢铁生产过程中的烧结 1.烧结的概念 将各种粉状含铁原料,配入适量的燃料和熔剂,加入适量的水,经混合和造球后在烧结设备上使物料发生一系列物理化学变化,将矿粉颗粒黏结成块的过程。 2. 烧结生产的工艺流程 目前生产上广泛采用带式抽风烧结机生产烧结矿。烧结生产的工艺流程如图2—4所示。主要包括烧结料的准备,配料与混合,烧结和产品处理等工序。 抽风烧结工艺流程 ◆烧结原料的准备 ①含铁原料 含铁量较高、粒度<5mm的矿粉,铁精矿,高炉炉尘,轧钢皮,钢渣等。 一般要求含铁原料品位高,成分稳定,杂质少。 ②熔剂 要求熔剂中有效CaO含量高,杂质少,成分稳定,含水3%左右,粒度小于3mm的占90%以上。 在烧结料中加入一定量的白云石,使烧结矿含有适当的MgO,对烧结过程有良好的作用,可以提高烧结矿的质量。 ③燃料 主要为焦粉和无烟煤。 对燃料的要求是固定碳含量高,灰分低,挥发分低,含硫低,成分稳定,含水小于10%,粒度小于3mm 的占95%以上。 对入厂烧结原料的一般要求见表2—2。 入厂烧结原料一般要求 ◆配料与混合 ①配料
配料目的:获得化学成分和物理性质稳定的烧结矿,满足高炉冶炼的要求。 常用的配料方法:容积配料法和质量配料法。 容积配料法是基于物料堆积密度不变,原料的质量与体积成比例这一条件进行的。准确性较差。 质量配料法是按原料的质量配料。比容积法准确,便于实现自动化。 ②混合 混合目的:使烧结料的成分均匀,水分合适,易于造球,从而获得粒度组成良好的烧结混合料,以保证烧结矿的质量和提高产量。 混合作业:加水润湿、混匀和造球。 根据原料性质不同,可采用一次混合或二次混合两种流程。 一次混合的目的:润湿与混匀,当加热返矿时还可使物料预热。 二次混合的目的:继续混匀,造球,以改善烧结料层透气性。 用粒度10~Omm的富矿粉烧结时,因其粒度已经达到造球需要,采用一次混合,混合时间约50s。 使用细磨精矿粉烧结时,因粒度过细,料层透气性差,为改善透气性,必须在混合过程中造球,所以采用二次混合,混合时间一般不少于2.5~3min。 我国烧结厂大多采用二次混合。 ◆烧结生产 烧结作业是烧结生产的中心环节,它包括布料、点火、烧结等主要工序。 ①布料 将铺底料、混合料铺在烧结机台车上的作业。 当采用铺底料工艺时,在布混合料之前,先铺一层粒度为10~25mm,厚度为20~25mm的小块烧结矿作为铺底料,其目的是保护炉箅,降低除尘负荷,延长风机转子寿命,减少或消除炉箅粘料。 铺完底料后,随之进行布料。布料时要求混合料的粒度和化学成分等沿台车纵横方向均匀分布,并且有一定的松散性,表面平整。 目前采用较多的是圆辊布料机布料。
材料力学性能测试实验报告
材料力学性能测试实验 报告 标准化管理部编码-[99968T-6889628-J68568-1689N]
材料基本力学性能试验—拉伸和弯曲一、实验原理 拉伸实验原理 拉伸试验是夹持均匀横截面样品两端,用拉伸力将试样沿轴向拉伸,一般拉 至断裂为止,通过记录的力——位移曲线测定材料的基本拉伸力学性能。 对于均匀横截面样品的拉伸过程,如图 1 所示, 图 1 金属试样拉伸示意图 则样品中的应力为 其中A 为样品横截面的面积。应变定义为 其中△l 是试样拉伸变形的长度。 典型的金属拉伸实验曲线见图 2 所示。 图3 金属拉伸的四个阶段 典型的金属拉伸曲线分为四个阶段,分别如图 3(a)-(d)所示。直线部分的斜率E 就是杨氏模量、σs 点是屈服点。金属拉伸达到屈服点后,开始出现颈缩 现象,接着产生强化后最终断裂。 弯曲实验原理 可采用三点弯曲或四点弯曲方式对试样施加弯曲力,一般直至断裂,通过实 验结果测定材料弯曲力学性能。为方便分析,样品的横截面一般为圆形或矩形。 三点弯曲的示意图如图 4 所示。 图4 三点弯曲试验示意图 据材料力学,弹性范围内三点弯曲情况下C 点的总挠度和力F 之间的关系是 其中I 为试样截面的惯性矩,E 为杨氏模量。 弯曲弹性模量的测定 将一定形状和尺寸的试样放置于弯曲装置上,施加横向力对样品进行弯曲, 对于矩形截面的试样,具体符号及弯曲示意如图 5 所示。 对试样施加相当于σpb0.01。 (或σrb0.01)的10%以下的预弯应力F。并记录此力和跨中点处的挠度,然后对试样连续施加弯曲力,直至相应于σpb0.01(或σrb0.01)的50%。记录弯曲力的增量DF 和相应挠度的增量Df ,则弯曲弹性模量为 对于矩形横截面试样,横截面的惯性矩I 为 其中b、h 分别是试样横截面的宽度和高度。 也可用自动方法连续记录弯曲力——挠度曲线至超过相应的σpb0.01(或σrb0.01)的弯曲力。宜使曲线弹性直线段与力轴的夹角不小于40o,弹性直线段的高度应超过力轴量程的3/5。在曲线图上确定最佳弹性直线段,读取该直线段的弯曲力增量和相应的挠度增量,见图 6 所示。然后利用式(4)计算弯曲弹性模量。 二、试样要求
第九章 陶瓷的烧结原理及工艺
第九章 陶瓷的烧结原理及工艺 1.烧结通常是指在高温作用下粉粒集合体(坯体)表面积减少,气孔率降低、致密度提高、颗粒间接触面积加大以及机械强度提高的过程。 2.陶瓷的烧结可以分为气相烧结、固相烧结、液相烧结 若物质的蒸汽压较高,以气相传质为主,叫做气相烧结; 若物质的蒸汽压较低,烧结以固相扩散为主,叫固相烧结; 有些物质因杂质存在或人为添加物在烧结过程中有液相出现,称为液相烧结; 3.烧结过程中的物质的传递即传质过程,包括:(1)蒸发和凝聚;(2)扩散;(3)粘性流动; (4)塑性流变;(5)溶解和沉淀 a 、气相传质(气相烧结)……公式要记住 气相烧结中的传质过程主要是蒸发和凝聚 b 、固相传质(固相烧结)………….. 公式要记住 目前公认的机制有(1)扩散机制;(2)粘滞性流动和塑性流变 c 、液相传质(液相烧结) s 与s 0分别为颗粒和大块物质的溶解度; γsl 为液固表面张力; V 0为摩尔体积;r 为颗粒半径 液相烧结可以分成三个阶段: (1)在成形体中形成具有流动性的液相,并在表面张力的作用下,使固体颗粒以更紧密方式重新排列的粘滞流动过程,称为重排过程; (2)通过颗粒向液相中溶解和重新淀析而发生致密度增大的阶段,称为溶解与沉淀过程; (3)液相的重新结晶和颗粒长大,最终形成固相陶瓷-凝结过程 二、影响烧结的因素 烧结时间,颗粒半径,气泡和晶界,杂质及添加剂 烧结促进剂、烧结阻滞剂、反应接触剂或矿化剂,烧结气氛 氧化性气氛、中性气氛、还原性气氛 9.2陶瓷的烧结方法 1、根据烧结时是否有外界加压可以将烧结方法分为常压烧结和压力烧结 常压烧结又称为普通烧结,指在通常的大气条件下无须加压进行烧结的方法(传统陶瓷大都在隧道窑中进行烧结,而特种陶瓷大都在电窑中烧成) 压力烧结可以分为热压烧结和热等静压烧结 a 、热压烧结是指在粉体加热时进行加压,以增大粉体颗粒间的接触应力,加大致 密化的动力,使颗粒通过塑性流动进行重新排列,改善堆积状况。 b 、热等静压烧结工艺是将粉体压坯或将装入包套的粉料放入高压容器中,在高温 和均衡的气体压力作用下,将其烧结为致密的陶瓷体。 2、根据烧结时是否有气氛可以将烧结方法分为普通烧结和气氛烧结 3、根据烧结时坯体内部的状态可以分为气相烧结、固相烧结、液相烧结、活化烧结,反 应烧结 反应烧结是通过多孔坯件同气相或液相发生反应,使坯体的质量增加、气孔率减少并烧结成具有一定强度和尺寸精度的成品的一种烧结工艺 9.3 陶瓷烧结后的处理 rRT V s s sl 0 02γ=ln
烧结生产工艺流程
烧结工艺流程 一、我厂烧结机概况: 我厂90M2带式抽风机是有鞍山冶金设计研究总院设计。设计利用系数为 1.57t/m·h。(设备能力为 2.0 t/m·h)作业率90.4%,年产烧结矿224万吨。产品 为冷烧结矿;温度小于120℃;粒度5—150mm;0—5mm粉末含量小于5%; TFe55%;FeO小于10%;碱度2.0倍。配料采用自动重量配料强化制粒烧结工艺。 厚料层烧结、环式鼓风冷却机冷却烧结矿。冷烧结矿经整粒筛分;分出冷返矿及烧结机铺底料和成品烧结矿。选用了高效主抽风机等节能设备,电器控制及自动化达到国内同类厂先进水平,采用以PLC为核心的EIC控制系统,构成仪电合一的计算机控制系统。仪表选用性能良好的电动单元组合仪表智能型数字显示仪表等,对生产过程的参数进行指示;记录;控制;自动调节,对原料成品及能源进行计量,在环境保护方面采用静电除尘器,排放浓度小于100mg/m3,生产水循环使用,实现全厂污水零排放。采取多项措施对薄弱环节设备采用加强型及便于检修的设备,关键部位设电动桥式吊车,有储存时间8小时的成品矿槽以提高烧结机作业率,使烧结和高炉生产互不影响。 二、什么叫烧结工艺: 烧结工艺就是按高炉冶炼的要求把准备好的铁矿粉、熔剂、燃料及代用品,按一定比例经配料、混料、加水润滑湿。再制粒、布料点火、借助风机的作用,使铁矿粉在一定的高温作用下,部分颗粒表面发生软化和熔化,产生一定的液相,并与其他末熔矿石颗粒作用,冷却后,液相将矿粉颗粒粘成块这个过程为烧结工艺。 三.烧结的方法 按照烧结设备和供风方式的不同烧结方法可分为:1)鼓风烧结如:
烧结锅、平地吹;2)抽风烧结:①连续式如带式烧结机和环式烧结机等;②间歇式如固定式烧结机有盘式烧结机和箱式烧结机,移动式烧结 机有步进式烧结机;3)在烟气中烧结如回转窑烧结和悬浮烧结。 四.烧结矿的种类: CaO/SiO2小于1为非自熔性烧结矿;碱度为1-1.5是自熔性烧结. 矿碱度为1.5~2.5是高碱度烧结矿;大于2.5是超高或熔剂性烧结矿。 五. 烧结的意义 通过烧结可为高炉提供化学成分稳定、粒度均匀、还原性好、冶金性能高的优质烧结矿,为高炉优质、高产、低耗、长寿创造了良好的条件;可以去除有害杂质如硫、锌等;可利用工业生产的废弃物,如高炉炉尘、轧钢皮、硫酸渣、钢渣等;可回收有色金属和稀有稀土金属。 六.烧结工艺流程的组成 (1)含铁原料、燃料和熔剂的接受和贮存;(2)原料、燃料和熔剂的破碎筛分;(3)烧结料的配料、混合、制粒、布料、点火和烧结;(4)烧结矿的破碎、筛分、冷却和整粒。 七.烧结原料 1.含铁原料主要有磁铁矿、赤铁矿、褐铁矿、菱铁矿,铁矿粉是烧结生产的主要原料,它的物理化学性质对烧结矿质量的影响最大。要求铁矿粉品位高、成分稳定、杂质少、脉石成分适于造渣,粒度适宜、精矿水分大于12%时影响配料准确性,不宜混合均匀。粉矿粒度要求控制在8mm以下便于烧结矿质量提高,褐铁矿、菱铁矿的精矿或粉矿烧结时要考虑结晶水、二氧化碳的烧损(一般褐铁矿烧损 9~15%,收缩8%左右,菱铁矿烧损17~36%,收缩10%。) 2.烧结熔剂按其性质可分为碱性熔剂、中性熔剂(Al2O3)和酸性熔剂(石英、蛇绞石等)三类,烧结常用碱性熔剂有石灰石(CaCO3)消石灰(Ca(OH)2)生石灰
烧结工艺流程
烧结工艺流程 烧结是钢铁生产工艺中的一个重要环节,它是将铁矿粉、粉(无烟煤)和石灰按一定配比混匀。经烧结而成的有足够强度和粒度的烧结矿可作为炼铁的熟料。利用烧结熟料炼铁对于提高高炉利用系数、降低焦比、提高高炉透气性保证高炉运行均有一定意义。 由于烧结技术具体的作用和应用太广泛了, 以下介绍一下烧结生产在钢铁工业粉矿造块的意义和作用 我国的铁矿石大部分都是贫矿,贫矿直接入炉炼铁是很不合算b,因此必须将贫矿进行破碎、选出高品位的精矿后,再将精矿粉造块成为人造富矿才能入高炉冶炼。所以,粉矿造块是充分合理利用贫矿的不可缺少的关控环节。 富矿的开采过程中要产生粉矿,为了满足高炉的粒度要兔在整较过程中也会产生粉矿,粉矿直接入炉会51起高炉不顺。恶化高炉技术经济指标,因此粉矿也必须经过造块才能入炉。 粉矿经过迭决后,可以进一步控制相改善合铁原料的性肠获得气孔串高、还原性好、强度合适、软熔温度较高、成份稳定的优质冶金原料,有助于炉况的稳定和技术经济指标的改
善。粒矿造块过程中,还可以除去部份有害杂质,如硫、氟、砷、锌等,有利于提高生铁的质量。因为人造富矿比天然富矿更具有优越性,成为了现代商炉原料的主要来源。 粉矿迭块还可综合利用含铁、合被、台钙的粉状工业废料,如高炉炉尘、钢迢、轧钢皮、均热炉渣、硫酸渣、染料铁红、电厂烟尘灰笔适当配入可以成为廉价的高炉好原料,又可以减少环境污染,取得良好的经济效益和社会效益。 粉矿造铁是现代高炉冶炼并获得优质高产的基础,对于高炉冶炼有君十分重要的意义,是钢铁工业生产必不可少的重要工序,对钢铁生产的发展起着重要作用。 1.2 粉矿造块的方法 粉矿造块方法很多,主要是烧结矿和球团矿。此外,还有压制方团矿、辊压团矿、蒸养球团t碳酸化球团,其成球方式和固结方法与球团矿不同,还有小球烧结,国外称为HPs球团化挠结矿,界于球团和烧结之间;还有铁焦生产,是炼焦和粉矿造块相结合。 球团矿的焙烧方法主要乞竖队带式焙烷仇链蓖机—回转窃。目前地方小铁厂还有平地堆烷的。 烧结方法主要有吹风烧结法和抽风烧结法两大类。吹风烧结有平地堆挠、饶结识、挠结盘,抽风烧结有路式侥结、艰面步进式烧绍机、带式烧结机、环形挠结机电即日本矢作式)。 国内外苫遍采用的是常式抽风烧结机,在我国地方小铁广还有相当一部分用平地吹风堆烧和箱式抽风烧结。比外,还有回转窑浇结法、悬浮烧结法。 所谓“烧结”就是指粉状物料加热到熔点以下而粘结成固体的现象. 烧结过程简单来说,就是把品位满足要求,但粒度却不满足的精矿与其他辅助原料混合后在烧结机上点火燃烧,重新造块,以满足高炉的要求。点火器就是使混合料在烧结机上燃烧的关键设备,控制好点火器的温度、负压等,混合料才能成为合格的烧结成品矿。 烧结的主要体系是,配料,混料,看火等。看火的经验:看火主要控制的三点温度是;点火温度,终点温度,和总管废气温度。一般来说把终点温度控制在倒数第2号风箱的温度。 铁矿粉造块 铁矿粉造块目前主要有两种方法:烧结法和球团法。两种方法所获得的块矿分别为烧结矿和球团矿。 铁矿粉造块的目的: ◆综合利用资源,扩大炼铁用的原料种类。 ◆去除有害杂质,回收有益元素,保护环境。 ◆改善矿石的冶金性能,适应高炉冶炼对铁矿石的质量要求。
力学性能检验规范
力学性能检验规范 编制: 审核: 批准: 日期:
1、目的 本规程指在为公司质量检测部力学性能试验的操作和判定做出指导,规范其操作,保证力学性能试验能够快速、准确的完成。 2、依据标准 2.1 ASTM A370-2014 钢制品力学性能试验的标准试验方法和定义 ASTM_E23-2012C 金属材料切口试棒冲击试验的试验方法 GB2975-1998 钢及钢产品力学性能试验取样位置及试样制备 GB/T228.1-2010 金属材料_室温拉伸试验方法 GB/T 229-2007 金属材料夏比摆锤冲击试验方法 3、拉伸试验 3.1、取样 3.1.1试样尺寸执行相关技术文件或标准取样。 3.1.2试样在机加工过程中要防止冷变形或受热而影响其力学性能。通常以切削加工为宜,进刀深度要适当,并充分冷却。特别是最后一道切削或磨削的深度不宜过大,以免影响性能。 3.2、方法 拉伸试验应按产品的技术要求,选择GB/T228或ASTM A370的方法进行。 3.3、设备 微机屏显式液压万能试验机 主要性能参数最大试验力300KN、试验力准确度优于示值±1%,变形测量准确度在引伸计满量程的2%~100%范围内优于±1% 电子引伸计 主要参数级别 1.0 ;标距Le(mm) 50 ;计算方法端点法; 最大变形(mm)10.0 ; 灵敏度(mV/V) 2 3.4、实验设备的校准 3.3.1效准依据:ISO 7500-1或ASTM E4 3.3.2效准频率:每年 4、夏比V型缺口冲击试验 4.1、取样 4.1.1试样尺寸执行相关技术文件或标准取样。
4.1.2由于冲击试样缺口深度、缺口根部曲率半径及缺口角度决定着缺口附近的应力集中程度,从而影响该试样的吸收能量,因此对缺口的制备应特别仔细,以保证缺口根部处没有影响吸收的加工痕迹。缺口对称面应垂直于试样纵向轴线。另外,加工时,除端部外,试样表面粗糙度值应优于5μm。 4.2.、方法 夏比V型冲击试验应按照按产品的技术要求,选择ASTM A370和ASTM E23或GB/T229的方法执行。 只要能达到规定温度下的吸收能要求,在低于规定温度的温度下进行的试验是合格的。 4.3.、设备 冲击试验机 最大试验力300J,冲击能量30/15公斤每米 冲击试验低温槽 主要参数控温范围 -60℃;控温精度<±0.5℃; 保温时间 8min ;冷却介质乙醇或其他不冻液 4.4、实验设备的校准 3.3.1效准依据:ISO 7500-1或ASTM E4 3.3.2效准频率:每年
(整理)陶瓷烧成与烧结
7 烧成与烧结 7.1 烧成原理 为制定合理的煅烧工艺,就必须对物料在烧成时所发生的物理化学变化的类型和规律有深入的了解。但是物料烧成时的变化较所用的原料单独加热时更为复杂,许多反应是同时进行的。一般而言,物料的烧成变化首先取决于物料的化学组成,正确的说是物料中的矿物组成。使用不同的地区的原料,即使物料的化学组成相同,也不能得到完全相同的烧成性质。其次,物料的烧成变化在很大程度上还取决于物料中各组分的物理状态,即粉碎细度、混合的均匀程度、物料的致密度等,因为物料的烧成是属于液相参与的烧结过程,因此物料的分散性和各组分的接触的密切程度直接影响固相反应、液相的生成和晶体的形成。此外,烧成温度、时间和气氛条件对物料的烧成变化影响也很大。要将这些复杂的因素在物料烧成过程中的变化上反映出来是困难的。为研究方便本书以长石质陶瓷坯体为例进行讨论。 7.1.1 陶瓷坯体在烧成过程中的物理化学变化 陶瓷坯体在烧成过程中一般经过低温阶段、氧化分解阶段和高温阶段。 1.低温阶段(由室温~300℃) 坯料在窑内进行烧成时,首先是排除在干燥过程中尚未除去的残余水分。这些残余水分主要是吸附水和少量的游离水,其量约为2~5%。 随着水分排除固体颗粒紧密靠拢,发生少量的收缩。但这种收缩并不能完全填补水分所遗留的空间,因此物料的强度和气孔率都相应的增加。 在120~140℃之前,由于坯体内颗粒间尚有一定的孔隙,水分可以自由排出,可以迅速升温,随着温度进一步提高,坯体中毛细管逐渐变小,坯体内汽化加剧,使得开裂倾向增大。例如,当加热至120℃时,一克水占有的水蒸气容积为:22.4×(1+120/273)/18=1.79(升)。如果坯体中含有4~5%的游离水,则100克坯体的水蒸气体积达7.16--8.95升,相当于坯体体积的155倍。这些水蒸气主要由坯体的边角部位排出。为了保证水分排出不致使坯体开裂,在此阶段应注意均匀升温,速度要慢(大制品30℃/时,中小制品50~60℃/时),尤其是厚度和形状复杂的坯体更应注意。此外,要求通风良好,以便使排出的水蒸气能迅速排出窑外,避免冷聚在坯体表面。 2.分解与氧化阶段(300~950℃) 此阶段坯体内部发生了较复杂的物理化学变化,粘土和其它含水矿物排除结构水;碳酸盐分解;有机物、碳素和硫化物被氧化,石英晶型转化等。这些变化与窑内温度气氛和升温速度等因素有关。 (1)粘土和其它含水矿物排除结构水 粘土矿物因其类型不同、结晶完整程度不同、颗粒度不同、坯体厚度不同,脱水温度也有所差别,见表11-1。 Al2O3·2SiO2·2H2O 加热——→Al2O3·2SiO2+2H2O↑ (高岭土) (偏高岭土)(水蒸气) 表11-1 各类粘土矿物脱水温度单位:℃ 原料 吸热交换放热效应 排除吸附 水 排除结晶水晶格破坏新结晶物质形成重结晶 高岭土450~600 950~1050 1200~1300