第六章 铸件与锻件超声波探伤
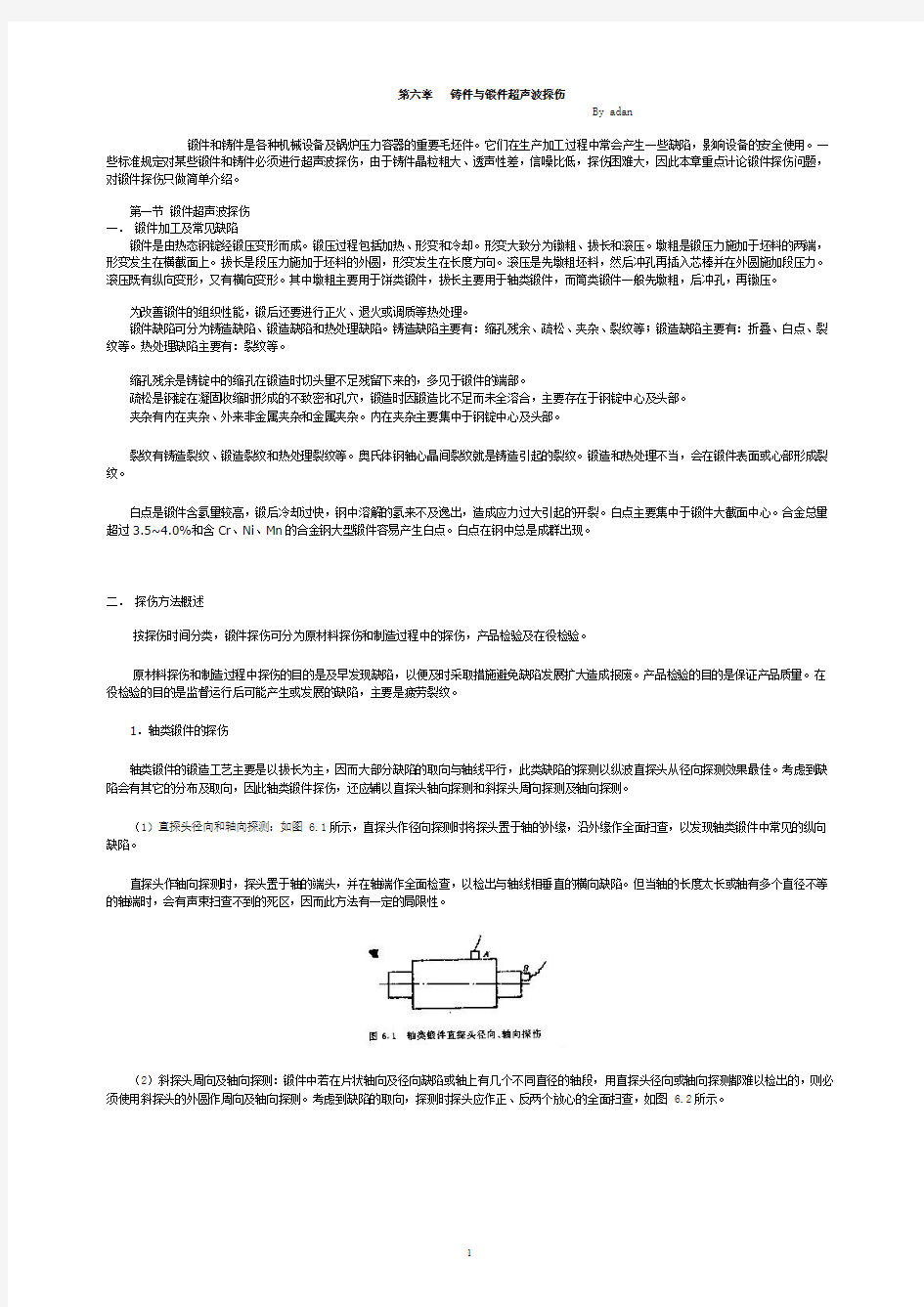
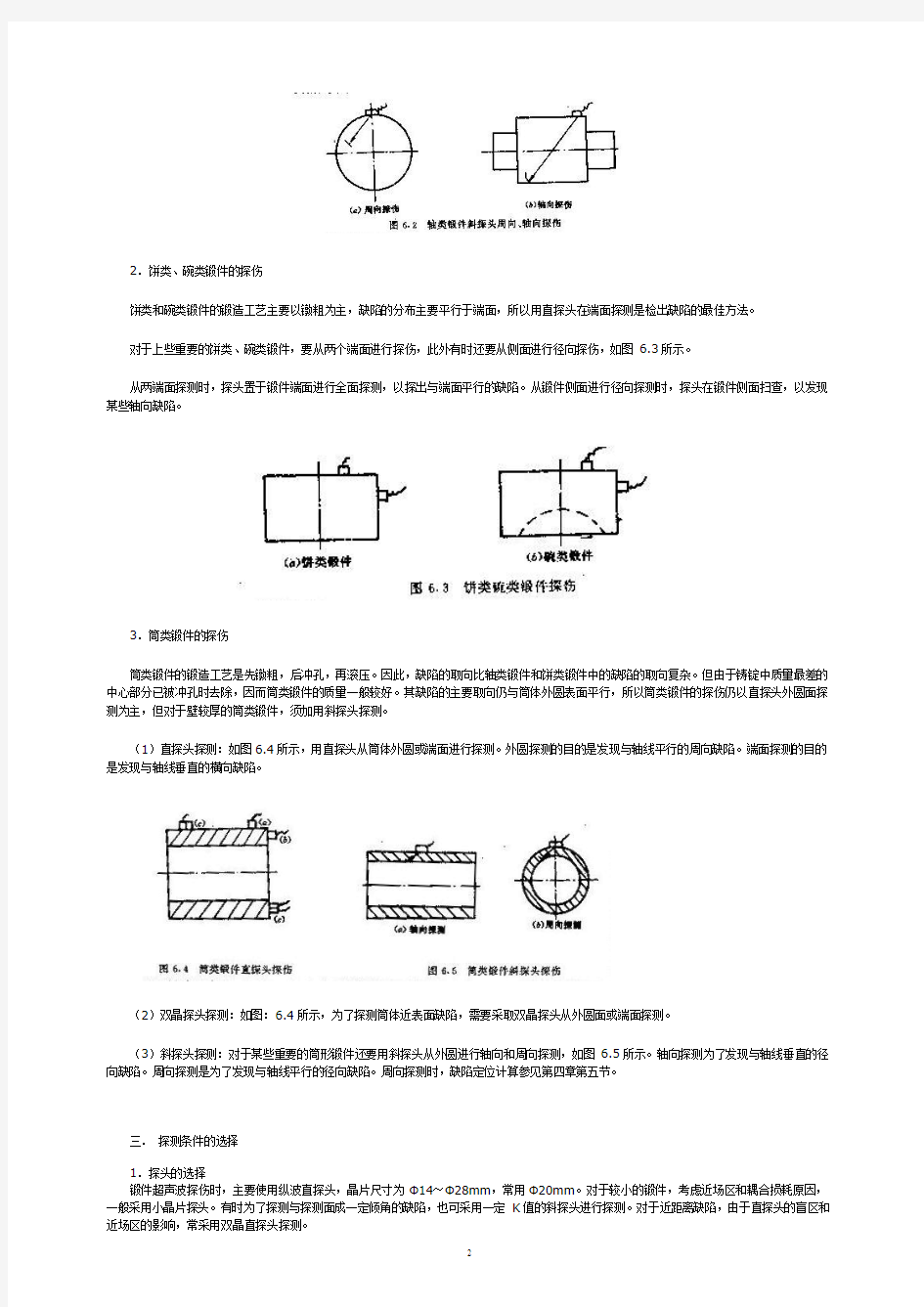
第六章铸件与锻件超声波探伤
By adan
锻件和铸件是各种机械设备及锅炉压力容器的重要毛坯件。它们在生产加工过程中常会产生一些缺陷,影响设备的安全使用。一些标准规定对某些锻件和铸件必须进行超声波探伤,由于铸件晶粒粗大、透声性差,信噪比低,探伤困难大,因此本章重点计论锻件探伤问题,对锻件探伤只做简单介绍。
第一节锻件超声波探伤
一.锻件加工及常见缺陷
锻件是由热态钢锭经锻压变形而成。锻压过程包括加热、形变和冷却。形变大致分为镦粗、拔长和滚压。墩粗是锻压力施加于坯料的两端,形变发生在横截面上。拔长是段压力施加于坯料的外圆,形变发生在长度方向。滚压是先墩粗坯料,然后冲孔再插入芯棒并在外圆施加段压力。滚压既有纵向变形,又有横向变形。其中墩粗主要用于饼类锻件,拔长主要用于轴类锻件,而筒类锻件一般先墩粗,后冲孔,再镦压。
为改善锻件的组织性能,锻后还要进行正火、退火或调质等热处理。
锻件缺陷可分为铸造缺陷、锻造缺陷和热处理缺陷。铸造缺陷主要有:缩孔残余、疏松、夹杂、裂纹等;锻造缺陷主要有:折叠、白点、裂纹等。热处理缺陷主要有:裂纹等。
缩孔残余是铸锭中的缩孔在锻造时切头量不足残留下来的,多见于锻件的端部。
疏松是钢锭在凝固收缩时形成的不致密和孔穴,锻造时因锻造比不足而未全溶合,主要存在于钢锭中心及头部。
夹杂有内在夹杂、外来非金属夹杂和金属夹杂。内在夹杂主要集中于钢锭中心及头部。
裂纹有铸造裂纹、锻造裂纹和热处理裂纹等。奥氏体钢轴心晶间裂纹就是铸造引起的裂纹。锻造和热处理不当,会在锻件表面或心部形成裂纹。
白点是锻件含氢量较高,锻后冷却过快,钢中溶解的氢来不及逸出,造成应力过大引起的开裂。白点主要集中于锻件大截面中心。合金总量超过3.5~4.0%和含Cr、Ni、Mn的合金钢大型锻件容易产生白点。白点在钢中总是成群出现。
二.探伤方法概述
按探伤时间分类,锻件探伤可分为原材料探伤和制造过程中的探伤,产品检验及在役检验。
原材料探伤和制造过程中探伤的目的是及早发现缺陷,以便及时采取措施避免缺陷发展扩大造成报废。产品检验的目的是保证产品质量。在役检验的目的是监督运行后可能产生或发展的缺陷,主要是疲劳裂纹。
1.轴类锻件的探伤
轴类锻件的锻造工艺主要是以拔长为主,因而大部分缺陷的取向与轴线平行,此类缺陷的探测以纵波直探头从径向探测效果最佳。考虑到缺陷会有其它的分布及取向,因此轴类锻件探伤,还应辅以直探头轴向探测和斜探头周向探测及轴向探测。
(1)直探头径向和轴向探测:如图6.1所示,直探头作径向探测时将探头置于轴的外缘,沿外缘作全面扫查,以发现轴类锻件中常见的纵向缺陷。
直探头作轴向探测时,探头置于轴的端头,并在轴端作全面检查,以检出与轴线相垂直的横向缺陷。但当轴的长度太长或轴有多个直径不等的轴端时,会有声束扫查不到的死区,因而此方法有一定的局限性。
(2)斜探头周向及轴向探测:锻件中若在片状轴向及径向缺陷或轴上有几个不同直径的轴段,用直探头径向或轴向探测都难以检出的,则必须使用斜探头的外圆作周向及轴向探测。考虑到缺陷的取向,探测时探头应作正、反两个放心的全面扫查,如图6.2所示。
2.饼类、碗类锻件的探伤
饼类和碗类锻件的锻造工艺主要以镦粗为主,缺陷的分布主要平行于端面,所以用直探头在端面探测是检出缺陷的最佳方法。
对于上些重要的饼类、碗类锻件,要从两个端面进行探伤,此外有时还要从侧面进行径向探伤,如图6.3所示。
从两端面探测时,探头置于锻件端面进行全面探测,以探出与端面平行的缺陷。从锻件侧面进行径向探测时,探头在锻件侧面扫查,以发现某些轴向缺陷。
3.筒类锻件的探伤
筒类锻件的锻造工艺是先镦粗,后冲孔,再滚压。因此,缺陷的取向比轴类锻件和饼类锻件中的缺陷的取向复杂。但由于铸锭中质量最差的中心部分已被冲孔时去除,因而筒类锻件的质量一般较好。其缺陷的主要取向仍与筒体外圆表面平行,所以筒类锻件的探伤仍以直探头外圆面探测为主,但对于壁较厚的筒类锻件,须加用斜探头探测。
(1)直探头探测:如图6.4所示,用直探头从筒体外圆或端面进行探测。外圆探测的目的是发现与轴线平行的周向缺陷。端面探测的目的是发现与轴线垂直的横向缺陷。
(2)双晶探头探测:如图:6.4所示,为了探测筒体近表面缺陷,需要采取双晶探头从外圆面或端面探测。
(3)斜探头探测:对于某些重要的筒形锻件还要用斜探头从外圆进行轴向和周向探测,如图6.5所示。轴向探测为了发现与轴线垂直的径向缺陷。周向探测是为了发现与轴线平行的径向缺陷。周向探测时,缺陷定位计算参见第四章第五节。
三.探测条件的选择
1.探头的选择
锻件超声波探伤时,主要使用纵波直探头,晶片尺寸为Φ14~Φ28mm,常用Φ20mm。对于较小的锻件,考虑近场区和耦合损耗原因,一般采用小晶片探头。有时为了探测与探测面成一定倾角的缺陷,也可采用一定K值的斜探头进行探测。对于近距离缺陷,由于直探头的盲区和近场区的影响,常采用双晶直探头探测。
锻件的晶粒一般比较细小,因此可选用较高的探伤频率,常用2.5~5.0MHz。对于少数材质晶粒粗大衰减严重的锻件,为了避免出现“林状回波”,提高信噪比,应选用较低的频率,一般为1.0~2.5MHz。
2.耦合选择
在锻件探伤时,为了实现较好的声耦合,一般要求探测面的表面的粗糙度Ra,不高于6.3μm,表面平整均匀,无划伤、油垢、污物、氧化皮、油漆等。
挡在试块上调节探伤灵敏度时,要注意补偿块与工件之间因曲率半径和表面粗糙度不同引起的耦合损失。
锻件探伤时,常用机油、浆糊、甘油等作耦合剂。当锻件表面较粗糙时也可选用水玻璃作耦合剂。
3.扫查方法的选择
锻件探伤时,原则上应在探测面上从两个相互垂直的方向进行全面扫查。扫查覆盖面应为探头直径的15%,探头移动速度不大于150mm/s。扫查过程中要注意观察缺陷波的情况和底波的变化情况。
4.材质衰减系统的测定
当锻件尺寸较大时,材质的衰减对缺陷定量有一定的影响。特别是材质衰减严重时,影响更明显。因此,在锻件探伤中有时要测定材质的衰减系数α。衰减系数可利用下式来计算:
(6.1)
值得注意的是:测定衰减系数时,探头所对锻件底面应光洁干净,底面形状为大平底或圆柱面,x≥3N,测试处无缺陷。一般选取三处进行测试,最后去平均值。
5.试块选择
锻件探伤中,要根据探头和探测面的情况选择试块。
采用纵波直探头探伤时,常选用CS-1和CS-2试块来调节探伤灵敏和对缺陷定量。采用纵波双晶直探头探伤时常选用图6.6所示的试块来调节探伤灵敏度和对缺陷定量。该试块的人工缺陷为平底孔,孔径有φ2、φ3、φ4、φ6等四种,距离L分别为5、10、15、20、25、30、35、40、45mm
当探测面为曲面时,应采用曲面对比试块来测定由于曲率不同引起的耦合损失。对比试块如图6.7所示
6.探伤时机
锻件超声波探伤应在热处理后进行,因为热处理可以细化晶粒,减少衰减。此外,还可以发现热处理过程中产生的缺陷。
对于带孔、槽和台阶的锻件,超声波探伤应在孔、槽、台阶加工前进行。因为孔、槽、台阶对探伤不利,容易产生各种非缺陷回波。
当热处理后材质衰减仍较大且对于探测结果有较大影响时,应重新进行热处理。
四、扫描速度和灵敏度的调节
(一)扫描速度的调节
锻件探伤前,一般根据锻件要求的探测范围来调节扫描速度,以发现缺陷,并对缺陷定位。
扫描速度的调节可在试块上进行,也可在锻件上尺寸已知的部位上进行,在试块上调节扫描速度时,试块上的声速应尽可能与工件相同或相近。
调节扫描速度时,一般要求第一次底波前沿位置不超过水平刻度极限的80%,以利观察一次底波之后的某些信号情况。
(二)探伤灵敏度的调节
锻件探伤灵敏度是由锻件技术要求或有关标准确定的。一般不低于φ2平底孔当量直径。
调节锻件探伤灵敏度的方法有两种,一种是利用锻件底波来调节,另一种是利用试块来调节。
1.底波调节法
当锻件被探伤部位厚度x≥3N,且锻件具有平行底面或圆柱曲底面时,常用底波来调节探伤灵敏度。
底波调节法,首先要计算或查AVG曲线求得底面回波与某平底孔回波的分贝差,然后再调节。
(1)计算:对于平底面或实心圆柱体底面,同距离处底波与平底孔回波的分贝差为:
(6.2)对于空心圆柱体,同距离处圆柱曲底面与平底孔回波分贝差为:
(6.3)
(2)调节:探头对准完好区的底面,衰减(Δ+5~10)dB,调节“增益”使底波B1达基准高,然后用“衰减器”增益ΔdB,这时灵敏度就调好了。为了便于发现缺陷可再增益5~10dB作为搜索灵敏度,即扫查灵敏度。
例1,用2.5P20Z探头径向探伤φ500mm的实心圆柱体锻件,CL=5900m/S,问如何利用底波调节500/φ2灵敏度?
解:由题意得:λ=C/f=5.9/2.5=2.36(mm)
①计算:500mm处底波与φ2平底孔回波分贝差为:
②调节:探头对准完好区圆柱底面,衰减55dB,调“增益”使底波B1最高达基准60%高,然后用“衰减器”增益46dB,即去掉46dB,保留9dB,这是φ2灵敏度就调好了。必要时再增益6dB作为扫查灵敏度。
例2,用2.5P20Z探头径向探伤外径为φ1000mm,内经为φ100mm的空心圆柱体锻件,CL=5900m/s,问如何利用内孔回波调节450/φ2灵敏度?
解:由题意得:λ=C/f=5.9/2.5=2.36(mm),D=1000mm。D=100mm,x=(D-d)/2=(1000-100)/2=450mm
①450mm处底波与φ2平底孔回波分贝差为:
②调节:探头对准完好区的内孔,衰减45dB,调“增益”使底波B1最高达基准60%高,然后用“衰减器”增益35dB作为探伤灵敏度,再增益6dB作为扫查灵敏度
2.试验块调节法
(1)单直探头探伤:当锻件的厚度x<3N或由于几何形状所限或底面粗糙时,应利用具有人工缺陷的试块来调节探伤灵敏度,如CS-1和CS-2试块。调节时将探头对准所需试块的平底孔,调“增益”使平底孔回波达基准高即可。
值得注意的是,当试块表面形状、粗糙度与锻件不同时,要进行耦合补偿。当试块与工件的材质衰减相差较大时,还要考虑介质衰减补偿。
例1,用2.5P20Z探头探伤厚度为50mm的小锻件,采用CS-1试块调节50/φ2灵敏度,试块与锻件表面耦合差3dB,问如何调节灵敏度?
解:利用CS-1试块调节灵敏度的方法如下:
将探头对准CS-1试块中1号试块的φ2平底孔距离为50mm,衰减10dB,调“增益”使φ2回波达60%高,然后再用“衰减器”增益3dB,这时50/φ2灵敏度就调好了。
例2,用2.5P14Z探头探测底面粗糙厚为400mm的锻件,问如何利用100/φ4平底孔试块调节400/φ2灵敏度?试块与工件表面耦合差6dB。
解:①计算:100/φ4与400/φ2回波分贝差:
②调节:探头对准100/φ4平底孔试块的平底孔,衰减50dB,调“增益”使φ4平底孔回波达基准高,然后用“衰减器”增益42dB,这时400/φ2灵敏度就调好了。这时工件上400/φ2平底孔缺陷回波正好达基准高。
(2)双晶直探头探伤:采用双晶直探头探伤,要利用图6.6所示的双晶探头平底孔试块来调节探伤灵敏度。先根据需要选择相应的平底孔试验块,并测试验一组距离不同直径相同的平底孔的回波,使其中最高回波达满刻度的80%,在此灵敏条件下测出其它平底孔的回波最高点,并标在示波屏上,然后连接这些回波最高点,从而得到一条平底孔距离——波幅曲线,并以此作为探伤灵敏度。
五、缺陷位置和大小的测定
(一)缺陷位置的测定
在锻件探伤中,主要采取纵波直探头探伤,因此可根据示波屏上缺陷波前沿所对的水平刻度值ιf和扫描速度1:n来确定缺陷在锻件中的位置。缺陷至探头的距离xf为:
Xf=nι f (6.4)
(二)缺陷大小的测定
在锻件探伤中,对于尺寸小于声束截面的缺陷一般用当量法定量。若缺陷位于x≥3N区域内时,常用当量计算法和当量AVG曲线法定量;若缺陷位于x<3N区域内,常用试块比较法定量。对于尺寸大于声束截面的缺陷一般采用测长法,常用的测长法有6dB法和端点6dB法。必要时还可以采用底波高度法来确定缺陷的相对大小。下面重点介绍当量计算法和6dB法在锻件探伤中的应用。
1.当量计算法
当量计算法是利用各种规则反射体的回波声压公式和实际探伤中测得的结果(缺陷的位置和波高)来计算缺陷的当量大小。当量计算法当时目前锻件探伤中应用最广的一种定量方法。用当量计算法定量时,要考虑调节探伤灵敏度的基准。
当用平底面和实心圆柱体曲底面调节灵敏度时,当量计算公式为:
(6.5)当用空心圆柱体内孔或外圆曲底面调节灵敏度时,当量计算公式为:
(6.6)
例1,用2.5P20Z探头探伤φ600的实心圆柱体锻件,CL=5900m/s,α=0.005dB/mm,利用锻件底波调节600/φ2灵敏度,底波达基准高时衰减读数为50dB,探伤中在400mm处发现一缺陷,缺陷波达基准高时衰减器度数为30dB,求次缺陷的当量平底孔直径为多少?
解:由已知得,λ=C/f=5.9/2.5=2.36(mm),xB=600mm,xf=400mm,ΔBf=50-30=20dB,α=0.005dB/mm,经此代入(6.5)式得:
答:此缺陷的当量平底孔直径为φ5.6mm。
例2,用2.5P20Z探头探伤外径为1000mm,内经为100mm的空心圆柱体锻件,CL=5900m/s,α=0.005dB/mm,探伤中在200mm处发现一缺陷,
其回波比内孔回波低12dB,求此缺陷的当量大小?
解:由已知得,λ=C/f=5.9/2.5=2.36(mm),D=1000mm。D=100mm,x=(D-d)/2=(1000-100)/2=450mm,xf=200mm,α=0.005dB/mm,ΔBf=12dB。
由(6.6)式得:
答:此缺陷的当量平底孔直径为φ2.8mm。
此外,锻件探伤中,还可利用当量AVG曲线法来定量,具体方法见第四章第六节。
2.6dB测长法
在平面探伤中,用6dB法测定缺陷的长度时,探头的移动距离就是缺陷的指示长度,如图6.8所示。然而在对圆柱形锻件进行周向探伤时,探头的移动距离不再是缺陷的指示长度了,这时要按几何关系来确定缺陷的指示长度,如图6.9所示。
外圆周向探伤测长时,缺陷的指示长度Lf为:
内孔周向探伤测长时,缺陷的指示长度Lf为:
(6.8)
六、缺陷回波的判别
在锻件探伤中,不同性质的缺陷回波是不同的,实际探伤时,可根据示波屏上的缺陷回波情况来分析缺陷的性质和类型
1、单个缺陷回波
锻件探伤中,示波屏上单独出现的缺陷回波称为单个缺陷回波。一般单个缺陷的指与邻近缺陷间距大于50mm、回波高不小于φ2mm的缺陷。如锻件中单个的夹层、裂纹等。探伤中遇到单个缺陷时,要测定缺陷的位置和大小。当缺陷较小时,用当量法定量,当缺陷较大时,用6dB法测定其面积范围。
2.分散缺陷回波
锻件探伤时,工件中的缺陷较多且较分散,缺陷彼此间距较大,这种缺陷回波称为分散缺陷回波。一般在边长为50mm的立方体内少于5个,不小于φ2mm。如分散性的夹层。分散缺陷一般不太大,因此常用当量定量,同时还要测定分散缺陷的位置。
3、密集缺陷回波
锻件探伤中,示波屏上同时显示的缺陷回波甚多,波与波之间的间隔距离甚小,有时波的下沿连成一片,这种缺陷回波称密集缺陷回波。
密集缺陷的划分,根据不同的验收标准有不完全相同的意义。
(1)以缺陷的间距划分,规定相邻缺陷间的间距小于某一值时为密集缺陷。
(2)以单位长度时基线内显示的缺陷回波数量划分,规定在相当与工件厚度值的基线内,当探头不动或稍微移动时,一定数量的缺陷回波连续或断续出现时为密集缺陷。
(3)以单位面积中的缺陷回波划分,规定在一定探测面积下,探出的缺陷回波数量超过某一值时定为密集缺陷。
(4)以单位面积内缺陷回波数量划分,规定在一定体积内缺陷回波数量多于规定值时定为密集缺陷。
实际探伤中,以单位体积内缺陷回波数量划分较多。一般规定在边长50mm的立方体内,数量不少于5个,当量直径不小于φ2mm的缺陷为密集缺陷。
密集缺陷可能是疏松、非金属夹杂物、白点或成群的裂纹等。
锻件内不允许有白点缺陷存在,这种缺陷的危险性很大。通常白点的分布范围较大,且基本集中于锻件的中心部位,它的回波清晰、尖锐,成群的白点有时会使底波严重下降或完全消失。这些特点是判断锻件中白点的主要依据,如图6.10
4、游动回波
在圆柱形轴类锻件探伤过程中,当探头沿着轴的外圆移动时,示波屏上的缺陷会随着该缺陷探测声程的变化而游动,这种游动的动态波形称为游动回波。
游动回波的产生是由于不同波束射至缺陷产生放射引起的。波束轴线射至缺陷时,缺陷声程小,回波高。左右移动探头,扩散波束射至缺陷时,缺陷声程大,回波低。这样同一缺陷回波的位置和高度随探头移动发生移动,如图6.11。
不同的探测灵敏度,同一缺陷回波的游动情况不同。一般可根据探测灵敏度和回波的游动距离来鉴别游动回波。一般规定游动范围达20mm时,才算游动回波。
根据缺陷游动回波包络线的形状,可粗略地判别缺陷的形状。
5、底面回波
在锻件探伤中,有时还可根据底波变化情况来判别锻件中的缺陷情况。
当缺陷回波很高,并有多次重复回波,而底波严重下降甚至消失时,说明锻件中存在平行于探测面的大面积缺陷。
当缺陷回波和底波都很低甚至消失时,说明锻件中存在大面积但倾斜的缺陷或在探测面附近有大缺陷。
当示波屏上出现密集的互相彼连的缺陷回波,底波明显下降或消失时,说明锻件中存在密集缺陷。
六、非缺陷回波分析
锻件探伤中还会出现一些非缺陷回波影响对缺陷波的判别。常见的非缺陷波有以下几种。
1、三角反射波
周向探测圆柱形锻件时,由于探头与圆柱面耦合不好,波束严重扩散,在示波屏上出现两个三角反射波,这两个三角反射波的声程分别为1.3d和1.67d(d为圆柱直径),据此可以鉴别三角反射波。由于三角反射波总是位于底波B1之后,而缺陷波一般位于底波B1之前,因此三角反射波不会干扰对缺陷的判别。
2、迟到波
轴向探测细长类锻件时,由于波型转换,在示波屏上出现迟到波。迟到波的声程是特定的,而且可能出现多次。第一次迟到波位于底波B1之后0.76d处(d为轴类锻件的直径),以后各次迟到波间距为0.76d。由于迟到波总在B1之后,而缺陷波一般在B1之前,因此迟到波也不会影响对缺陷波的判别。
另外从扁平方向探测扁平锻件时,也会出现迟到波,探伤中应注意判别。
3、61o反射波
当锻件中存在与探测面成61o倾角的缺陷时,示波屏上会出现61o反射波,61o反射波是变型横波垂直入射到侧面引起的,如图6.12所示。图中F为缺陷直接波,M为61o反射波,
61o放射波的声程也是特定的,总是等于61o角所对垂直边的边长。产生61o放射时缺陷直接放射回波较低。而61o反射波较高。
另外在探测如图6.13所示的锻件时,也会出现61o反射波,同时还会产生45o反射波。探伤时可根据放射波的声程通过计算来判别。
xA=d1+1.82d2-2R(61°反射)
xB=d1+d2-1.414R(45°反射)
4、轮廓回波
锻件探伤中,锻件的台阶、凹槽等外形轮廓也会引起一些非缺陷回波,探伤中要注意判别。
此外在锻件探伤中还可能产生一些其他的非缺陷回波,这时应根据锻件的结构形状、材质和锻造工艺应用超声波放射、折射和波型转换理论进行分析判别。
七、锻件质量级别的评定(见JB4730—94标准)
锻件探伤中常见缺陷有单个缺陷和密集缺陷两大类,实际探伤中单个缺陷的当量尺寸,底波的降低情况和密集缺陷面积占探伤面积的百分比不同将锻件质量分为Ⅰ、Ⅱ、Ⅲ、Ⅳ、V等五种,其中Ⅰ级最高,V级最低,单个缺陷等级见表6—1,底波降低等级见表6—2,密集性缺陷等级见表6—3.
表6—1 单个缺陷的等级
等级ⅠⅡⅢⅣ V
缺陷当量≤φ4 φ4+(>0~8)
dB φ4+(>2~
12)dB
φ4+(>12~
16)dB
φ4+>16dB
底波降低量的等级
表6—2
等级I II III IV V
[B]c/[B]r(dB)≤8 8~14 >14~20 >20~26 >26
密集缺陷等级
表6-3
等级I II III IV V
缺陷面积占探伤面积
百分比(%)
0 0~5 >5~10 >10~20 >20
注:①表6-2中[B]c/[B]r,表示无缺陷处底波与缺陷处底波分贝差。
②以上三表的等级应作为独立的等级分别使用。
如果某缺陷被检测人员判为危害性缺陷,那么可以不受上述条件的限制,一律评为最低级,不合格。
下面举例说明锻件的评级方法。
例1 用2.5P20Z探头探测400mm厚的钢锻件,钢中C L=5900m/s。衰减系数α=0.005dB、mm ,探伤灵敏度为400mm处Φ4为0dB。探伤中在250mm 处出现一缺陷,其波高比据准波高20dB,试根据JB4730-94标准评定该锻件的质量级别。
解:(1)条件判定
λ=c/f=5.9/2.5=2.36
N=D s2/4λ=202/(4×2.36)=42.4
3N=3×42.4=127<250
∴符合当量计算的条件。
(2)求250mm处Φ4当量的dB值
Δ18=20lgp f1/p f2=40lgx2/x1+2α(x2- x1)
=40lg400/250+2×0.005×(400-250)
=9.5(dB)
(3)求该缺陷的当量病评级
缺陷当量:Φ4+20-9.5=Φ4+10.5dB
缺陷评级:该锻件评为III级。
例2用2.5P20Z探头探测面积为400cm2的锻件,探伤中发现一密集缺陷,其面积为24 cm2,缺陷处底波为30dB,无缺陷处底波为44dB。是根据JB4730-94标准评定该锻件的质量级别。
解:(1)据密集性缺陷评级
∵24÷400×100%=6%>5%
∴评为III级。
(2)据底波降低量评级
∵[B]G-[B] F=44-30=14dB
∴评为II级
第二节铸件超声波探伤
一、铸件中常见缺陷
铸件是金属液注入铸模中冷却凝固而成的,铸件中常见缺陷有气孔、缩孔、夹杂和裂纹等。
1. 气孔
气孔是由于金属液含气量过多,模型潮湿及透气性不佳而形成的空洞。铸件中的气孔分为单个分散气孔和密集气孔。
2. 缩孔
缩孔是由于金属液冷去凝固时体积收缩得不到补缩而形成的缺陷。缩孔多位于浇冒口附近和截面最大部位或截面突变处。
3. 夹杂
夹杂分为非金属夹杂和金属夹杂两类。非金属夹杂是冶金时金属与空气发生化学反应形成的产物或浇注时耐火材料、型砂等混入钢液形成的夹杂物。金属夹杂是异种金属偶尔落入钢液中未能融化而形成的夹杂物。
4. 裂纹
裂纹是指钢液冷却过程中由于内应力(热应力和组织应力)过大使铸件局部裂开而形成的缺陷。铸件截面尺寸突变处,应力集中严重处,容易出现裂纹。裂纹时最危险的缺陷。
二、铸件探伤的特点
1.透声性差
铸件重要特点是组织不致密、不均匀和晶粒粗大,透声性差。
铸件不均匀是由于铸件各部分冷却速度不同引起的。模壁冷却快,且常有大量固态生核微粒,因此模壁晶粒细。当模壁温度升高后,冷却速度减慢,于是在垂直模壁方向上形成柱状晶区。当模壁温度进一步升高,金属液温度下降,温差减少,冷却速度缓慢,晶粒方向消失,形成等轴晶区。这种铸件截面上不同取向的晶粒构成了铸件的不均匀性,此外铸件中以片状,球状或其他形态存在的石墨也可视为一种组织不均匀性。
铸件的致密性是由于树枝结晶方式引起的。铸件结晶时,先形成主干,然后在垂直于主干方向长出支干。再在支干垂直方向长出分支,就像树枝一样生长。各支干间最后结晶凝固,
冷却收缩形成的空隙难以充满金属,从而使铸件的致密性变差。
铸件晶粒大是由于高温冷却凝固过程缓慢,生核、长核时间长、使晶粒面粗。
铸件的不致密性、不均匀性和晶粒粗大,使超声波散射衰减和吸收衰减明显增加、透声性降低。
2.声耦合差
铸件表面粗糙,声耦合差,探伤灵敏度低,波束指向性不好,且探头磨损严重。铸件探伤中常采用高粘度耦合剂改善这种不良的耦合条件。
3.干扰杂波多
铸件探伤干扰杂波多。一是由于晶粒和组织不均匀性引起的散乱反射,形成草状回波,使信噪比下降。特别是频率较高时尤为严重。二是铸件形状复杂,一些轮廓回波和迟到变形波引起的非缺陷信号多。此外铸件粗糙表面也会产生一些反射回波,干扰对缺陷波的正确判定。
以上所述正是铸件探伤的困难所在,致使铸件探伤的应用和发展收到一定的限制。但另一方面由于铸件质量要求较低,允许存在单个缺陷尺寸较大,数量较多,同时铸件探伤出现的部位规律性强,因此铸件探伤还是具有一定的价值,目前国内外不少人正在研究铸件探伤中存在的问题。
铸件分为铸钢与铸铁,二者缺陷状况和材质及表面特点基本相同。因此其探伤方法也大致相同。下面以铸钢件为例说明铸件的一般探伤方法与质量级别的评定。
三、铸钢件探测条件的选择
1. 探头
铸钢件探伤,一般以纵波直探头为主,辅以横波斜探头和纵波双晶探头。
铸钢件晶粒比较粗大,衰减严重,宜选用较低的频率,一般为0.5~2.5MHz。对于厚度不大又经过热处理的铸钢件,可选用2.0~2.5MHz ,对于厚度较大和未热处理的铸钢件,宜选用0.5~2.0MHz。
纵波直探头的直径一般为Φ10~Φ30mm ,横波斜探头的折射角常为45°60°70°等
2. 试块
铸钢件探伤常用图6.14所示的ZGZ系列平底孔对比试块。试块材质与被探铸钢件相似,不
允许存在Φ2平底孔缺陷。试块平底孔直径d分别为Φ3、Φ4、Φ6等三种。平底孔声程l为25、50、75、100、150、200等六种。该试块用于测试距离——波幅曲线和调整探伤灵敏度(纵波直探头)。
3.探测表面与耦合剂
铸钢件表面粗糙,耦合条件差,探伤前应对其表面进行打磨清理,粗糙度为R a不大于12.5μm。
铸钢件探伤时,常用年度较大的耦合剂,如浆糊、黄油、甘油、水玻璃等。
4. 透声性测试
铸钢件晶粒较粗、组织不致密,对声波吸收和散射严重,透声性差,对探伤结果影响较大。一般探伤前要测试其透声性。铸钢件透声性可用纵波直探头来测试。将探头对准工件底面,用[衰减器]测出底B1与B2的dB差即可。为了减少测试误差,一般侧三点取平均值。测得的dB差愈大,说明透声性愈差。
四、距离——波幅曲线的测试与灵敏度调整
根据探测要求选定一组平底孔对比试块(平底孔直径相同声程不同)测出弓箭与对比试块的透声性和耦合损失差ΔdB,衰减量≥(Δ+10)dB。将探头置于厚度与工件相近的试块上,对准平底孔,调节仪器使平底孔最高回波达10%~20%,然后固定各旋钮,将探头分别对准不同声程的平底孔,标记各平底孔回波的最高点,连成曲线,从而得到该平底孔的距离——波幅曲线(即面板曲线)。用[衰减器]增益ΔdB,这时灵敏度就调好了。为
了便于发现缺陷,有时再增益6dB 作为扫查灵敏度。 五、缺陷的判别与测定
探头按选定的方式进行扫查,相邻两次扫查重叠15%;探头移动速度≤150mm/s 。扫描中根据缺陷波高与底波降低情况来判别工件内部是否存在缺陷。以下几种情况作为缺陷记录。
(1) 缺陷回波幅度达到距离——波幅曲线者。 (2) 底面回波幅度降低量≥12dB 者。
(3) 不论缺陷回波高低,认为是线状或片状缺陷者。 发现缺陷以后,要测定缺陷的位置与大小。
缺陷的位置由示波屏上缺陷前沿对应的水平刻度值来确定。
缺陷的面积大小用下述方法测定:当利用缺陷反射法判定缺陷时,用缺陷6dB 法测定缺陷面积的大小。当采用底波降到12dB 法判别缺陷时,用底波降低12dB 作为缺陷边界来测定缺陷面积。 六、铸钢件质量级别的评定
铸钢件超声波探伤方法及质量评级方法GB7233-87规定铸钢件质量等级,根据平面型缺陷和非平面型缺陷的尺寸,将其分为Ⅰ、Ⅱ、Ⅲ、Ⅳ、Ⅴ等五级,其中Ⅰ为最高,Ⅴ为最低。
评定时,评定区面积为 (317x317或面积相同矩形),尽可能使最严重的缺陷位于评定区内。位于评定区边界上的缺陷,若大部分在外层,则计入外层,反之计入内。若探测面积不足 ,则按比例折算允许的缺陷面积。 表6-4 平面型缺陷质量等级划分
等级
Ⅰ Ⅱ Ⅲ Ⅳ Ⅴ 单个缺陷在厚度方向尺寸(mm )
0 5 8
11
超过 Ⅳ级
单位个缺陷面积( ) 0 75
200 360
缺陷总面积( )
150 400 700
表6-5非平面型缺陷质量等级划分
等级
Ⅰ Ⅱ Ⅲ Ⅳ Ⅴ
外
层 单个缺陷在厚度方向尺寸占外层厚度百分比
(%)
20 20 20 20 超
过 Ⅳ
级
单个缺陷面积( ) 250 1000
2000
4000
缺陷总面积( )
5000 10000 20000 40000 内
层
单个缺陷在厚度方向尺寸占外层厚度百分比
(%)
10
10
15
15
缺陷总面积( ) 12500 20000 30000 50000
注:
①单个缺陷尺寸大于320mm 者为Ⅴ级。
②单个缺陷面积为缺陷最大尺寸和与其垂直方向最大尺寸之积
③位于外层间距小于25mm 的两个或多个缺陷可视为一个缺陷,其面积为各缺陷面积之和。 ④凡监测区存在裂纹的铸钢件,评为Ⅴ级。
⑤某铸钢件的质量级别,系统平面型缺陷和非平面型缺陷均满足该级别的规定。即二者中级别较低的级别为铸钢件的级别。 铸钢件声波探伤详见GB7233-87标准。 复习题
一、 锻件探伤
1. 锻件中常见缺陷有哪几种?各是怎样形成的?
2. 锻件一般分哪几类?各采用什么方法探伤?
3. 在锻件超声波探伤中,调节灵敏度的常用方法有哪几种?各适用于什么情况?
4. 利用锻件底波调灵敏度有何好处?调节时应注意什么?
5. 锻件探伤中,常用哪几种方法对缺陷定量?各适用于什么情况?
6. 锻件探伤中,常见的非缺陷回波有哪几种?各是怎样形成的?如何判别?
7. 什么是游动回波?游动回波是怎样产生的?如何鉴别游动回波?
8. 锻件探伤中,常用什么方法测定材质的衰减系数?影响测试结果精度的主要因素是什么? 9. 试制定?500x400饼形锻件超专用波探伤工艺过程。
10. 用2.5P20Z 探头探伤厚为400mm 的饼形钢锻件,CL=5900m/s 。问如何利用底波调节400/?2灵敏度?(Δ=44dB )
11. 用2.5P20Z 探头探伤外径D=800mm 的实心圆柱体锻件,CL=5900m/s ,衰减系数α0.005dB/mm ,问如何利用底波来调节800/?2和400/?2灵
敏度?(Δ1=50dB Δ2=33.5dB )
12. 用2.5P14Z 探头探伤外径D=1000mm ,内径d=200mm 空心圆柱体钢锻件,CL=5900m/s 。(1)外径探伤时,如何利用内孔回波调节400/?2灵
敏度?(Δ=37dB )
(2)内孔探伤时,如何利用外圆回波调节400/?2灵敏度?(Δ=51dB ) 13. 用2.5P20Z 探头探伤厚为400mm 的锻件,CL=5900m/s 锻件与试块同材质,α=0.01dB/mm 。(1)如何利用200/?2的试块(CS-1)来调节400/?2
灵敏度?(Δ=28dB ) (2)如何利用厚为100mm 大平底试块来调节400/?2灵敏度?(Δ=61.5dB )
14. 用2.5P20Z 探头探伤厚为400mm 的锻件,CL=5900m/s ,锻件与试块同材质,α=0.005dB/mm ,锻件与是块表面耦合损失差为5dB ,如何利用
100/?2的试块(CS-1)来调节400/?2灵敏度?(Δ=44dB )
15. 用2.5P20Z 探头探伤厚为500mm 的饼形钢锻件,CL=5900m/s 。利用底波调灵敏度,底波高50dB ,探伤中在200mm 处发现一缺陷波高26dB ,
求此缺陷的当量大小?(Df=2.75mm )
16. 用2.6P14Z 探头探伤厚为300mm 的锻件,已知300/?2回波为12dB ,170mm 处缺陷波高为32dB 。求此缺陷的当量大小?(Df=3.6mm )
17. 用2.5P20Z 探头探伤500mm 的锻件,α=0.005dB/mm ,CL=5900m/s ,探伤中在200mm 处发现一缺陷,其回波高度比底波低9dB ,求此缺陷
的当量大小?(Df=5.5mm )
18. 用2.6P14Z 探头探伤锻件,已知200/?4回波达80%高时,180mm 处缺陷波达60%,求此缺陷当量大小?(Df=3.1mm )
19. 用2.5P14Z 探头探伤锻件,CL=5900m/s ,利用100mm 大平底试块调灵度,探伤中在200mm 处发现一缺陷,其波高比试块底波低43dB ,二者
的材质相同,α=0.005dB/mm ,求此缺陷当量大小?(Df=2.2mm )
20.用2.5P14Z探头探伤锻件,利用100mm大平底试块调灵度,CL=5900m/s,底波高50dB,锻件α=0.01dB/mm,试块α=0.005dB/mm,二者表面
耦合损失差为8dB,探伤中在150mm处发现一缺陷,其波高为15dB,求此缺陷当量大小?(Df=4.4mm)
21.用2.5P20Z探头探伤400mm的锻件,利用400/?4试块调节400/?2灵敏度,二者耦合差为6dB,锻件第一次底波达100%时二次底波高为20%。
探伤中在200mm处发现一缺陷,其波高比节400/?2高18dB,求此缺陷当量大小?(Df=2.2mm)
22.用2.5P20Z探头探伤外径D=1000mm的实心圆柱体,CL=5900m/s,α=0.005dB/mm。(1)如何利用底波调节500/?2灵敏度?(Δ=35dB)
(2)探伤中在250mm处发现一缺陷,其波高比底波低10dB,求此缺陷的大小?(Df=3.5mm)
23.用2.5P20Z探头探伤外径D=1000mm,内孔d=100mm的锻件,CL=5900m/s,α=0.005dB/mm
(1)如何利用内孔回波调节450/?2灵敏度?(Δ=35dB)(2)探伤中在200mm处发现一缺陷,其波高比内孔回波低12dB,求此缺陷的大小?(Df=2.8mm)
24.用2.5P20Z探头探伤厚为400mm的锻件,CL=5900m/s,α=0.01dB/mm,仪器按1:4调节扫描速度,探伤中在示波屏80处发现一缺陷,其
波高比底波低30dB ,求此缺陷的位置和大小?(xf=320mm Df=3.2mm)
25.用2.5P14Z探头探伤300mm厚的锻件,CL=5900m/s,α=0.005dB/mm,已知300mm处?4加波高为10dB,探伤中在150mm处发现一缺陷,
其波高为26dB,试根据JB3963-85标准评定该锻件的质量级别。(?4+2.5 dB,Ⅰ级)
26.超声波探伤甲、乙、丙三锻件。甲锻件有一个?6当量平底孔缺陷。乙锻件有缺陷引起底波降低量为20dB。丙锻件探伤面积为1㎡,密集缺陷
面积为300 试根据JB3963-85标准评定甲、乙、丙三锻件的质量级别。(甲:Ⅱ级,乙:Ⅲ级,丙:Ⅱ级)
二、铸件探伤
1.铸件中常见的缺陷有哪几种?有何特点?
2.铸件超声波探伤的困难是什么?
3.铸件超声波探伤,一般采用什么方法调节探伤灵敏度?
4.铸件超声波探伤,一般选用较低的频率的原因是什么?
5.铸钢件为什么要划分为内外层?如何划分?
6.为什么要测定铸钢件的透声性?如何测定?
7.试说明铸钢件探伤中距离-------波幅曲线的测定方法和灵敏度调节法。
8.铸钢件探伤中,哪几种情况作为探伤记录?
9.铸钢件探伤中,如何测定缺陷的位置与面积?
10.铸钢件分哪几级?如何评定铸钢件的质量级别?
锻件超声波检测作业指导书
锻件超声波检测作业指导书 7.1适用范围: 本条适用于碳素钢和低合金钢锻件的超声波检测和缺陷等级评定,不适用于奥氏体粗晶材料的超声检测,也不适用于内外径之比小于80%的环形和筒形锻件的周向横波检测。 7.2检测工艺卡 7.2.1检测工艺卡由具有II级UT资质人员编制,工艺卡的编制应与所执行的技术规范及本检测作业指导书相符。 7.2.2检测工艺卡由具有UTIII资质人员或UT检测责任师审核批准。 7.3检测器材: 7.3.1仪器 选用数字式超声波检测仪或A型脉冲反射式超声波检测仪,其工作频率范围为0.5-10MHz,水平线性误差不大于1%,垂直线性误差不大于5%。 7.3.2探头 选用双晶直探头频率为 5 MHz,晶片面积不小于
150mm2;单晶直探头,频率为2-5 MHz,圆晶片直径为14-25mm。 7.3.3试块 采用纵波单晶直探头时采用JB/T4730-2005规定的CSI 试块;采用纵波双晶探头时采用JB/T4730-2005图8-5规定的CSII标准试块;检测面是曲面时采用CSIII试块。 7.3.4耦合剂:化合浆糊或机油。 7.4检测时机:原则上安排热处理后,槽、孔、台阶加工前进行。若热处理后锻件形状不适合超声波检测时,也可在热处理前进行,但在热处理后仍应对锻件进行尽可能完全的检测。 7.5检测方法 7.5.1执行检测工艺卡的规定 7.5.2锻件一般应进行纵波检测,对筒形锻件还应进行横波检测,但扫查部位 和验收标准应根据JB/T4730-2005.3附录C的规定。 7.5.3在纵波检测时,原则上应从两面相互垂直的方向进行检
测,尽可能的检测带锻件的全体积,但锻件厚度超过400mm 时,应从两端面进行100%的扫查。 7.6检测灵敏度确定 7.6.1纵波直探头检测灵敏度的确定 当被检部位的厚度大于或等于3倍进场区时,原则上选用底波计算方法确定基准灵敏度,也可以采用试块法确定基准灵敏度。 7.6.2纵波双晶直探头灵敏度确定 根据需要选择不同直径的平底孔试块,并依次测试一组不同检测深度的平底孔(至少三个),调节衰减器,使其中最高回波达到满刻度的80%。不改变仪器参数,测出其他平底孔回波的最高点,将其标在荧光屏上,连接这些点,即得到对应于不同直径平底孔的双晶直探头的距离—波幅曲线,并以此作为基准灵敏度。 7.6.3检测灵敏度一般不得低于最大检测距离处的φ2mm平底孔当量直径。 7.6.4缺陷当量的确定:
第6章 锻件与铸件超声波探伤
第六章锻件与铸件超声波探伤 锻件和铸件是各种机械设备及锅炉压力容器的重要毛坯件。它们在生产加工过程中常会产生一些缺陷,影响设备的安全使用。一些标准规定对某些锻件和铸件必须进行超声波探伤。由于铸件晶粒粗大、透声性差,信噪比低,探伤困难大,因此本章重点计论锻件探伤问题,对铸件探伤只做简单介绍。 第一节锻件超声波探伤 一、锻件加工及常见缺陷 锻件是由热态钢锭经锻压变形而成。锻压过程包括加热、形变和冷却。锻件的方式大致分为镦粗、拔长和滚压。镦粗是锻压力施加于坯料的两端,形变发生在横截面上。拔长是锻压力施加于坯料的外圆,形变发生在长度方向。滚压是先镦粗坯料,然后冲孔再插入芯棒并在外圆施加锻压力。滚压既有纵向形变,又有横向形变。其中镦粗主要用于饼类锻件。拔长主要用于轴类锻件,而简类锻件一般先镦粗,后冲孔,再镦压。 为了改善锻件的绍织性能,锻后还要进行正火、退火或调质等热处理。 锻件缺陷可分为铸造缺陷、锻造缺陷和热处理缺陷。铸造缺陷主要有:缩孔残余、疏松、夹杂、裂纹等。锻造缺陷主要有:折叠、白点、裂纹等。热处理缺陷主要有:裂纹等。 缩孔残余是铸锭中的缩孔在锻造时切头量不足残留下来的,多见于锻件的端部。 疏松是钢锭在凝固收缩时形成的不致密和孔穴,锻造时因锻造比不足而末全焊合,主要存在于钢锭中心及头部。 夹杂有内在夹杂、外来菲金属夹杂栩金属夹杂。内在夹杂主要集中于钢锭中心及头部。 裂纹有铸造裂纹、锻造裂纹和热处理裂纹等。奥氏体钢轴心晶间裂纹就是铸造引起的裂纹。锻造和热处理不当,会在锻件表面或心部形成裂纹。 白点是锻件含氢最较高,锻后冷却过快,钢中溶解的氢来不及逸出,造成应力过大引起的开裂,白点主要集中于锻件大截面中心。合金总量超过3.5~4.0%和Cr、Ni、Mn的合金钢大型锻件容易产生白点。白点在钢中总是成群出现。 二、探伤方法概述 按探伤时间分类,锻件探伤可分为原材料探伤和制造过程中的探伤,产品检验及在役检验。 原材料探伤和制造过程中探伤的目的是及早发现缺陷,以便及时采取措施避免缺陷发展扩大造成报废。产品检验的目的是保证产品质量。在役检验的目的是监督运行后可能产生或发展的缺陷,主要是疲劳裂纹。 1.轴类锻件的探伤 轴类锻件的锻造工艺主要以拨长为主,因而大部分缺陷的取向与轴线平行。此类缺陷的探测以纵波直探头从径向探测效果最佳。考虑到缺陪会有其它的分布及取向,因此辅类锻件探伤,还应辅以直探头轴向探测和斜探头周向探测及袖向探测。 (1)直探头径向和轴向探测:如图6.1所示,直探作径向探测时将探头置于轴的外缘,沿外缘作全面扫查,以发现轴类锻件中常见的纵向缺陷。 直探头作轴向探测时,探头置于轴的端头,并在轴端作全面扫查,以检出与轴线相垂直的横向缺陷。但当轴的长度太长或轴有多个直径不等的轴段时,会有声束扫查不到的死区,因而此方法有一定的局限性。
无损探伤标准
无损探伤标准 一、通用基础 1、GB 5616-1985 常规无损探伤应用导则 2、GB/T 9445-1999 无损检测人员技术资格鉴定通则 3、GB/T 14693-1993 焊缝无损检测符号 4、GB 16357-1996 工业X射线探伤放射卫生防护标准 5、JB 4730-1994压力容器无损检测 6、DL/T675-1999 电力工业无损检测人员资格考核规则 二、射线检测 1、GB 3323-1987 钢熔化焊对接接头射线照相和质量分级 2、GB 5097-1985 黑光源的间接评定方法 3、GB 5677-1985 铸钢件射线照相及底片等级分类方法 4、GB/T 11346-1989 铝合金铸件X射线照相检验针孔(图形)分级 5、GB/T 11851-1996压水堆燃料棒焊缝X射线照相检验方法 6、GB/T 12469-1990 焊接质量保证钢熔化焊接头的要求和缺陷分类 7、GB/T 无损检测术语射线检测 8、GB/T 12605-1990 钢管环缝熔化焊对接接头射线透照工艺和质量分级 9、GB/T 16544-1996 球形储罐γ射线全景曝光照相方法 10、GB/T 16673-1996 无损检测用黑光源(UV-A)辐射的测量 11、JB/T 7902-2000 线型象质计 12、JB/T 7903-1995工业射线照相底片观片灯 13、JB/T 泵产品零件无损检测泵受压铸钢件射线检测方法及底片的等级分类 14、JB/T 9215-1999 控制射线照相图像质量的方法 15、JB/T 9217-1999射线照相探伤方法 16、DL/T 541-1994 钢熔化焊角焊缝射线照相方法和质量分级 17、DL/T 821-2002 钢制承压管道对接焊接接头射线检验技术规程 18、TB/T6440-92 阀门受压铸钢件射线照相检验 三、超声波检测㈠
关于锻件超声波探伤的标准及规程
关于锻件超声波探伤的标准及规程 1.1.1筒形锻件----轴向长度L大于其外径尺寸D的轴对称空心锻件如图1(a) 所示.t为公称厚度. 环形锻件----轴向长度L小于等于其外径尺寸D的轴对称空心件如图1(a)所 示.t为公称厚度. 饼形锻件----轴向长度L小于等于其外径D的轴对称形锻件如图1(b)所示.t 为公称厚度. 碗形锻件----用作容器封头,中心部份凹进去的轴对称形锻件如图1(c)所示.t 为公称厚度. 方形锻件----相交面互相垂直的六面体锻件如图1(d)所示. 三维尺寸a、b、c中最上称厚度. 底波降低量GB/BF(dB) 无缺陷区的第一次底波高度(GB)和有缺陷区的第一次底波高度(BF)之比.由缺陷 引起的底面反射的降低量用dB值表示. 密集区缺陷 当荧光屏扫描线上相当于50mm的声程范围内同时有5个或者5个以上的缺陷反射信号;或者在50mm×50mm的探测面上发现同一深度范围内有5个或5个以上的 缺陷反射信号. 缺陷当量直径 用AVG方法求出的假定与超声波束相垂直的平底孔的直径,称为缺陷当量直径, 或简称为当量直径. AVG曲线 以纵座标轴表示相对的反射回波高度,以横座标轴表示声程,对不同直径且假定与超声波束相垂直的圆平面缺陷所画出的曲线图叫AVG曲线,亦称为DGS曲线. 2探伤人员 锻件探伤应由具有一定基础知识和锻件探伤经验,并经考核取得国家认可的资格 证书者担任. 3探伤器材
探伤仪 应采用A型脉冲反射式超声波探伤仪,其频响范围至少应在1MHz~5Mhz内. 仪器应至少在满刻度的75%范围内呈线性显示(误差在5%以内),垂直线性误差 应不大于5%. 仪器和探头的组合灵敏度:在达到所探工件最大程处的探伤灵敏度时,有效灵敏 度余量至少为10dB. 衰减器的精度和范围,仪器的水平线性、动态范围等均应队伍ZBY230-84《A型脉冲反射式超声波探伤仪通用技术条件》中的有关规定. 探头 探头的公称频率主要为,频率误差为±10%. 主要采用晶片尺寸为Φ20mm的硬保护膜直探头. 必要时也可采用2MHzs或25MHz,以及晶片尺寸不大于Φ28mm探头. 探头主声束应无双峰,无偏斜. 耦合剂 可采用机油、甘油等透声性能好,且不损害工件的液体. 4探伤时机及准备工作 探伤时机 探伤原则上应安排在最终热处理后,在槽、孔、台级等加工前,比较简单的几何形状下进行.热处理后锻件形状若不适于超声波探伤也可在热处理前进行.但在热处理后,仍应对锻件尽可能完全进行探伤. 准备工作 探伤面的光洁度不应低一地5,且表面平整均匀,并与反射面平等,圆柱形锻件其端面应与轴线相垂直,以便于轴向探伤.方形锻件的面应加工平整,相邻的端面 应垂直. 探伤表面应无划伤以及油垢和油潜心物等附着物. 锻件的几何形状及表面检查均合格后,方可进行探伤. 重要区
超声检测锻件实操步骤
考试程序步骤 一、锻件(直探头2.5Pφ14K2) 步骤:1、开机——按两次确定键——按功能键——按零(初始化)——按1(当前通道)——长按通道/设置键——改探头参数等—调校。 2、直探头纵波入射点调校:由上一步进入零点/调校键——选择1(入射点调校)(显 示调节为,波速5920M/S;一次回波声程100mm;二次回波声程0mm.)——放在CSK-ⅠA试块上,对准中间完好位置找到底面回波,待波稳定后,按确定键,完成入射点调校。 3、调整灵敏度:将直探头放在150/φ3(根据现场情况)试块上,找到其反射波,并 用“波门”键调整“+”或“—”使其波门对准150/φ3处的反射波,找到最高波,调节到80%。记下此时增益Δ1dB,然后计算出150/φ3与225/φ2的回波分贝差Δ2dB,在Δ1dB基础上,调节增益旋钮增至(Δ1+Δ2)dB。 4、锻件检测:将直探头放在225mm,锻件上,全面扫查,找到200mm处缺陷波,用“波门”键调整“+”或“—”使其波门对准200mm处的反射波,使其最高波达到80%,记下此时Δ3dB. 5、计算当量:则200mm处缺陷波比225/φ2波高高Δ=(Δ1+Δ2-Δ3)dB。由公式 计算出缺陷当量。 6、根据标准进行评级,整理报告。 最简单做法: 锻件: 步骤:1、开机——按两次确定键——按功能键——按零(初始化)——按1(当前通道)——长按通道/设置键——改探头参数等—调校。 2、直探头纵波入射点调校:由上一步进入零点/调校键——选择1(入射点调校)(显 示调节为,波速5920M/S;一次回波声程100mm;二次回波声程0mm.)——放在CSK-ⅠA试块上,对准中间完好位置找到底面回波,待波稳定后,按确定键,完成入射点调校。 3、调整灵敏度:将直探头放在150/φ3(根据现场情况)试块上,找到其反射波,并 用“波门”键调整“+”或“—”使其波门对准150/φ3处的反射波,找到最高波,调节到80%。记下此时面板的读数Δ1dB。 4、锻件检测:将直探头放在225mm,锻件上,全面扫查,找到200mm处缺陷波,用“波门”键调整“+”或“—”使其波门对准200mm处的反射波,使其最高波达到80%,记下此时面板右上角的读数Δ2dB. 5、计算当量:则200/φx缺陷波比150/φ3波高高Δ=(Δ2-Δ1)dB。由公式 计算出缺陷当量。 6、根据标准进行评级,整理报告。
锻件超声波探伤记录报告(大平底)47013-友联
锻件超声波探伤记录和报告(南通友联专用)大平底 准考号: 评分: 试件编号 X 试件名称 锻件 试件材质 45# 试件规格 φ70×225 探头规格 2.5P φ14 探头型式 单晶直探头 仪器型号 PXUT-350C 型 扫查比例 深度1:1 扫查方式 全面扫查 探测灵敏度 φ2灵敏度 执行标准 NB/T47013.3-2015 探 伤 结 果 一.检测内容:对锻件T=225mm 进行超声检测,如何利用150mm 大平底调节工件φ2当量灵敏度. 二.检测步骤: (1) 扫描比例调节; 将纵波直探头放置150mm 大平底上,找出一次(B1)和二次(B2)底面反射波,分别将两波对准水平刻度150和300处, 此时, 深度1:1比例调好. (2).计算步骤 方法A. ①计算150大平底与工件同声程处(150/φ2)回波分贝差; dB X B Bf 352150 36.22lg 202lg 202 2=???=Φ=?ππλ ②计算150/φ2与工件225/φ2回波分贝差 dB X X 71502225 2lg 40lg 401221=??=ΦΦ=? 先增益35dB 调节好150/φ2当量灵敏度,再增益7dB 工件225/φ2灵敏度调节完毕 方法B. 计算150大平底与工件225/φ2回波分贝差; 已知Xf =225 XB =150
db X D X B f 42)150214.322536.22lg(202lg 202 2 22=????==?πλ (3)灵敏度调节;探头放在150大平底试块上,使平底回波达到最高,调至基准高度(80%), 然后增益42dB,此时工件225/φ2灵敏度调好. (4).锻件检测;将探头放置225mm 锻件上进行全面扫查,距锻件表面200mm 发现一缺陷 波,波高比225/φ2灵敏度基准波高高9dB.求缺陷当量. 已知X1=200 φ2=2 X2=225 △=9 求; φX )5625.0lg(402002225lg 40lg 409122X X X X X Φ=??Φ=ΦΦ==? X Φ=5625.0lg 225.0 mm X 3=Φ 三.结论; 对该锻件垂直方向进行超声全面扫查,发现距锻件表面 200mm 处有一缺陷,缺陷当量为3mm. 根据NB/T47013-2015标准,该钢板评为Ⅰ级,合格 报告日期 年 月 日
锻件与铸件超声波探伤详细教程(附实例解析)
第六章锻件与铸件超声波探伤 第六章锻件与铸件超声波探伤 锻件和铸件是各种机械设备及锅炉压力容器的重要毛坯件。它们在生产加工过程中常会产生一些缺陷,影响设备的安全使用。一些标准规定对某些锻件和铸件 必须进行超声波探伤。由于铸件晶粒粗大、透声性差,信噪比低,探伤困难大,因此本章重点计论锻件探伤问题,对铸件探伤只做简单介绍。 第一节锻件超声波探伤 一、锻件加工及常见缺陷 锻件是由热态钢锭经锻压变形而成。锻压过程包括加热、形变和冷却。锻件的方式大致分为镦粗、拔长和滚压。镦粗是锻压力施加于坯料的两端,形变发生在横 截面上。拔长是锻压力施加于坯料的外圆,形变发生在长度方向。滚压是先镦粗坯料,然后冲孔再插入芯棒并在外圆施加锻压力。滚压既有纵向形变,又有横向形变。其中镦粗主要用于饼类锻件。拔长主要用于轴类锻件,而简类锻件一般先镦粗,后冲孔,再镦压。 为了改善锻件的绍织性能,锻后还要进行正火、退火或调质等热处理。 锻件缺陷可分为铸造缺陷、锻造缺陷和热处理缺陷。铸造缺陷主要有:缩孔残余、疏松、夹杂、裂纹等。锻造缺陷主要有:折叠、白点、裂纹等。热处理缺陷主 要有:裂纹等。 缩孔残余是铸锭中的缩孔在锻造时切头量不足残留下来的,多见于锻件的端部。 疏松是钢锭在凝固收缩时形成的不致密和孔穴,锻造时因锻造比不足而末全焊合,主要存在于钢锭中心及头部。 夹杂有内在夹杂、外来菲金属夹杂栩金属夹杂。内在夹杂主要集中于钢锭中心及头部。 裂纹有铸造裂纹、锻造裂纹和热处理裂纹等。奥氏体钢轴心晶间裂纹就是铸造引起的裂纹。锻造和热处理不当,会在锻件表面或心部形成裂纹。
白点是锻件含氢最较高,锻后冷却过快,钢中溶解的氢来不及逸岀,造成应力过大引起的开裂,白点主要集中于锻件大截面中心。合金总量超过 3.5?4.0%和Cr、
GB超声波探伤标准
GB/T4730-2005 承压设备用钢锻件超声检测和质量分级 4.2 承压设备用钢锻件超声检测和质量分级 4.2.1 范围 本条适用于承压设备用碳钢和低合金钢锻件的超声检测和质量分级。本条不适用于奥氏体钢等粗晶材料锻件的超声检测,也不适用于内外半径之比小于80% 的环形和筒形锻件的周向横波检测。 4.2.2 探头 双晶直探头的公称频率应选用5MHz。探头晶片面积不小于150mm2;单晶直探头的公称频率应选用2MHz~5MHz,探头晶片一般为φ14mm~φ25mm。 4.2.3 试块 应符合 3.5 的规定。 4.2.3.1 单直探头标准试块 采用CSI试块,其形状和尺寸应符合图4和表 4 的规定。如确有需要也可采用其他对比试块。 图 4 CSI 标准试块 4.2.3.2 双晶直探头试块 a) 工件检测距离小于45mm时,应采用CSⅡ标准试块。
b) CS Ⅱ试块的形状和尺寸应符合图 5 和表 5 的规定。 试块序号孔径 检测距离L 123456789 CSII-1φ2 51015202530354045 CSII-2φ3 CSII-3φ4 CSII-4φ6 4.2.3.3 检测面是曲面时,应采用CSⅢ标准试块来测定由于曲率不同而引起的声能损失,其形状和尺寸按图 6 所示。 4.2.4 检测时机 检测原则上应安排在热处理后,孔、台等结构机加工前进行,检测面的表面粗糙度Rα ≤ 6.3 μ m。图 5 CS Ⅱ标准试块 CSIII 标准试块
图 7 检测方向 ( 垂直检测法 ) 4.2. 5.3 横波检测 钢锻件横波检测应按附录 C (规范性附录 ) 的要求进行。 4.2.6 灵敏度的确定 4.2.6.1 单直探头基准灵敏度的确定 4.2.5 检测方法 4.2. 5.1 一般原则 锻件应进行纵波检测,对筒形和环形锻件还应增加横波检测。 4.2.5.2 纵波检测 a ) 原则上应从两个相互垂直的方向进行检测, 尽可能地检测到锻件的全体积。 方向如图 7 所示。其他形状的锻件也可参照执行。 b ) 锻件厚度超过 400mm 时,应从相对两端面进行 100%的扫查。 主要检测 注 : 为应检测方向; ※为参考检测方向。
SEP1921-84锻件超声波检测详细资料
SEP1921-84锻件和锻材的超声检验 1检验目的和对象 本方法适用于直径(边长)100mm以上(含100mm)一般要求锻件和锻材(以下称锻件)的超声检验,尤其适用于脉冲—反射技术检验材料内部缺陷。由缺陷产生的反射波可以确定缺陷的准确位置、尺寸、连续性和数量。有探伤要求的锻件,本方法可作为指导,提供检测范围(见6.2节)和允许的极限(见6.5节和6.6节)。检验所要求的技术条件包括检测系统、锻件状态和结果评级。2应用范围 检验方法上仅包括未完成和未加工的锻件的检验,还包括没有进行热处理和已进行热处理锻件的检验,尤其适于非合金钢和合金钢的检验(见6.1节)更高要求锻件的检验见SEP0000* 若使用的探头与锻件上匹配,检验结果可能会因声波或其它原因的衰减而受到影响。此时,应标注检验结果的偏差。否则,下一步检验的程序须和买方或买方责任人达成一致。 3评级 根据检验的范围分成四个检验组(见6.2节),根据允许缺陷的尺寸和缺陷所指示的长度分5个级别(见6.4节和6.5、表1),此外按允许缺陷的数量也分5个级别(见6.4.3) 4检验的准备 锻件应具有简单的形状或检测部分旋转对称(见DIN54126第1部分,6节),为了使探头和锻件表面耦合良好,检验面和其它反射面要有斜度和粗糙
SEP1921-84 度的要求。 对于无氧化铁皮光滑面的检验,只要选择合适的耦合剂,就可以取得良好的检验效果,若表面粗糙度Rq≤20,根据DIN4762的要求应对材料表面进行加工。 若钢材没经过热处理,而锻件声能的衰减仍在允许的偏差极限(或注明极限)内(只要钢适于热处理),为减少声能损失而进行热处理是必要的。 为了检验缺陷所要求的尺寸等级,通过加工和热处理来达到适于检验的结构和表面状态也是必要的。(表1) 5检测系统: 5.1检测设备 根据脉冲回声技术和回波高度测量关系,带dB幅值控制的校准,超声检测装置应在2dB误差范围内工作。若在使用的灵敏范围内,则上必显示闸门和饱和度。 检验要求的范围必须调整到与检测装置一致,水平线性应在2%以内。5.2探头 探头标称频率必须与被检验圆盘反射体、声距离长度、声波衰减一致。一般探头标称频率在1—4MHz,然而只要符合6.5节注明允许的极限值,也可使用其它频率探头。 检验通常使用直探头,然而为检验近表面缺陷和声波难以到达的环或为使缺陷特殊标定锻件部分扇域具有良好的分辨力,通常用TR探头或者斜探头检验。 为了测出圆盘反射体的当量尺寸,应该了解每类探头A VG曲线的制作方法。
锻件超声波探伤仪纵波探伤技术
锻件超声波探伤仪纵波探伤技术 要进行锻件超声波探伤首先要了解什么叫锻件,为什么要进行锻压,锻件的种类有哪些,所谓的锻件就是对金属坯料(不含板材)施加外力,使其产生塑性变形、改变尺寸、形状及改善性能,用以制造机械零件、工件、工具或毛坯的成形加工方法。锻件的种类有:飞机锻件、柴油机船用锻件、兵器锻件、石油化工矿山锻件、核电锻件、火电锻件、水电锻件。那么要对锻件进行超声探伤,应该如何做呢? 1.锻件超声波探伤仪探伤时机: 探伤原则上应安排在最终热处理后,在槽、孔、台级等加工前,比较简单的几何形状下进行.热处理后锻件形状若不适于超声波探伤也可在热处理前进行.但在热处理后,仍应对锻件尽可能完全进行探伤. 2.锻件超声波探伤仪探伤准备工作: (1)探伤面的光洁度不应低一地5,且表面平整均匀,并与反射面平等,圆柱形锻件其端面应与轴线相垂直,以便于轴向探伤.方形锻件的面应加工平整,相邻的端面应垂直. (2)探伤表面应无划伤以及油垢和油潜心物等附着物. (3)锻件的几何形状及表面检查均合格后,方可进行探伤. 3.锻件超声波探伤探伤方法 锻件一般应进行纵波探伤,对简形锻件还应进行横波探伤,但扫查部位和验收标准应由供需双方商定. (1)纵波探伤扫查方法 ①锻件原则上应从两相互垂直的方向进行探伤,尽可能地探测到锻
件的全体积,主要探测方向如图2所示,其他形状的锻件也可参照执行. ②扫查范围:应对锻件整个表面进行连续全面扫查. ③扫查速度:探头移动速度不超过150mm/s. ④扫查复盖应为探头直径的15%以上. ⑤当锻件探测厚度大于400mm时,应从相对两端面探伤. (2)探伤灵敏度的校验 ①原则上利用大平底采用计算法确定探伤灵敏度,对由于几何形状所限,以及缺陷在近场区内的工件,可采用试块法. ②用底波法校正灵敏度,校正点的位置应选以工件上无缺陷的完好区域. ③曲面补偿:对于探测面是曲面而又无法采用底波法的工件,应采用曲率与工件相同或相近(0.7-1.1倍)的参考试块;或者采用小直径晶片的探头,使其近场区的长度小于等于1/4工件半径,这样可不需进行曲面补偿. ④探伤灵敏度不得低于Φ2mm当量直径. (3)缺陷当量的确定 ①采用A VG曲线及计算法确定缺陷当量. ②计算缺陷当量时,当材质衰减系数超过4dB/m时,应考虑修正. ③材质衰减系数的测定,应在被测工件无缺陷区域,选取三处有代表性的闰,求B1/B2的值,即第一次底波高度(B1)与第二次底波高度(B2)之比的dB差值.
锻件超声波探伤标准
锻件超声波探伤标准 锻件超声波探伤标准 1.1.1筒形锻件----轴向长度L大于其外径尺寸D的轴对称空心锻件如图1(a)所示.t 为公称厚度. 1.1.2 环形锻件----轴向长度L小于等于其外径尺寸D的轴对称空心件如图1(a)所示.t 为公称厚度. 1.1.3 饼形锻件----轴向长度L小于等于其外径D的轴对称形锻件如图1(b)所示.t 为公称厚度. 1.1.4 碗形锻件----用作容器封头,中心部份凹进去的轴对称形锻件如图1(c)所示.t为公称厚度. 1.1.5 方形锻件----相交面互相垂直的六面体锻件如图1(d)所示. 三维尺寸a、b、c中最上称厚度. 1.2 底波降低量GB/BF(dB) 无缺陷区的第一次底波高度(GB)和有缺陷区的第一次底波高度(BF)之比.由缺陷引起的底面反射的降低量用dB值表示. 1.3 密集区缺陷 当荧光屏扫描线上相当于50mm的声程范围内同时有5个或者5个以上的缺陷反射信号;或者在50mm×50mm的探测面上发现同一深度范围内有5个或5个以上的缺陷反射信号. 1.4 缺陷当量直径 用A VG方法求出的假定与超声波束相垂直的平底孔的直径,称为缺陷当量直径,或简称为当量直径. 1.5 A VG曲线 以纵座标轴表示相对的反射回波高度,以横座标轴表示声程,对不同直径且假定与超声波束相垂直的圆平面缺陷所画出的曲线图叫AVG曲线,亦称为DGS曲线. 2探伤人员 锻件探伤应由具有一定基础知识和锻件探伤经验,并经考核取得国家认可的资格证书者担任. 3探伤器材 3.1 探伤仪 3.1.1 应采用A型脉冲反射式超声波探伤仪,其频响范围至少应在1MHz~5Mhz内. 3.1.2 仪器应至少在满刻度的75%范围内呈线性显示(误差在5%以内),垂直线性误差应不大于5%. 3.1.3 仪器和探头的组合灵敏度:在达到所探工件最大程处的探伤灵敏度时,有效灵敏度余量至少为10dB. 3.1.4 衰减器的精度和范围,仪器的水平线性、动态范围等均应队伍ZBY230-84《A型脉冲反射式超声波探伤仪通用技术条件》中的有关规定. 3.2 探头 3.2.1 探头的公称频率主要为2.5Mhz,频率误差为±10%. 3.2.2 主要采用晶片尺寸为Φ20mm的硬保护膜直探头. 3.2.3 必要时也可采用2MHzs或25MHz,以及晶片尺寸不大于Φ28mm探头. 3.2.4 探头主声束应无双峰,无偏斜. 3.3 耦合剂 可采用机油、甘油等透声性能好,且不损害工件的液体. 4探伤时机及准备工作
SEP 1921-1984 中文版 锻件和锻材的超声检验
锻件和锻材的超声检验 1检验目的和对象 本方法适用于直径(边长)100mm以上(含100mm)一般要求锻件和锻材(以下称锻件)的超声检验,尤其适用于脉冲—反射技术检验材料内部缺陷。由缺陷产生的反射波可以确定缺陷的准确位置、尺寸、连续性和数量。有探伤要求的锻件,本方法可作为指导,提供检测范围(见6.2节)和允许的极限(见6.5节和6.6节)。检验所要求的技术条件包括检测系统、锻件状态和结果评级。2应用范围 检验方法不仅包括未完成和未加工的锻件的检验,还包括没有进行热处理和已进行热处理锻件的检验,尤其适于非合金钢和合金钢的检验(见6.1节)更高要求锻件的检验见SEP0000* 若使用的探头与锻件不匹配,检验结果可能会因声波或其它原因的衰减而受到影响。此时,应标注检验结果的偏差。否则,下一步检验的程序须和买方或买方责任人达成一致。 3评级 根据检验的范围分成四个检验组(见6.2节),根据允许缺陷的尺寸和缺陷所指示的长度分5个级别(见6.4节和6.5、表1),此外按允许缺陷的数量也分5个级别(见6.4.3) 4检验的准备 锻件应具有简单的形状或检测部分旋转对称(见DIN54126第1部分,6节),为了使探头和锻件表面耦合良好,检验面和其它反射面要有斜度和粗糙
SEP1921-84 度的要求。 对于无氧化铁皮光滑面的检验,只要选择合适的耦合剂,就可以取得良好的检验效果,若表面粗糙度Rq≤20,根据DIN4762的要求应对材料表面进行加工。 若钢材没经过热处理,而锻件声能的衰减仍在允许的偏差极限(或注明极限)内(只要钢适于热处理),为减少声能损失而进行热处理是必要的。 为了检验缺陷所要求的尺寸等级,通过加工和热处理来达到适于检验的结构和表面状态也是必要的。(表1) 5检测系统: 5.1检测设备 根据脉冲回声技术和回波高度测量关系,带dB幅值控制的校准,超声检测装置应在2dB误差范围内工作。若在使用的灵敏范围内,则上必显示闸门和饱和度。 检验要求的范围必须调整到与检测装置一致,水平线性应在2%以内。5.2探头 探头标称频率必须与被检验圆盘反射体、声距离长度、声波衰减一致。一般探头标称频率在1—4MHz,然而只要符合6.5节注明允许的极限值,也可使用其它频率探头。 检验通常使用直探头,然而为检验近表面缺陷和声波难以到达的环或为使缺陷特殊标定锻件部分扇域具有良好的分辨力,通常用TR探头或者斜探头检验。 为了测出圆盘反射体的当量尺寸,应该了解每类探头A VG曲线的制作方法。
GB 超声波探伤标准
GB/T4730-2005承压设备用钢锻件超声检测和质量分级 承压设备用钢锻件超声检测和质量分级 4.2.1范围 本条适用于承压设备用碳钢和低合金钢锻件的超声检测和质量分级。 本条不适用于奥氏体钢等粗晶材料锻件的超声检测,也不适用于内外半径之比小于80%的环形和筒形锻件的周向横波检测。 4.2.2探头 双晶直探头的公称频率应选用5MHz。探头晶片面积不小于150mm2;单晶直探头的公称频率应选用2MHz~5MHz,探头晶片一般为φ14mm~φ25mm。 4.2.3试块 应符合的规定。 4.2.3.1单直探头标准试块 采用CSI试块,其形状和尺寸应符合图4和表4的规定。如确有需要也可采用其他对比试块。 图4 CSI标准试块 表4 CSI标准试块尺寸 mm 试块序号CSI-1 CSI-2 CSI-3 CSI-4 L 50 100 150 200 D 50 60 80 80 4.2.3.2双晶直探头试块 a) 工件检测距离小于45mm时,应采用CSⅡ标准试块。
b) CS Ⅱ试块的形状和尺寸应符合图5和表5的规定。 图5 CS Ⅱ标准试块 表5 CS Ⅱ标准试块尺寸 mm 试块序号 孔径 检测距离L 1 2 3 4 5 6 7 8 9 CSII-1 φ2 5 10 15 20 25 30 35 40 45 CSII-2 φ3 CSII-3 φ4 CSII-4 φ6 4.2.3.3 检测面是曲面时,应采用CS Ⅲ标准试块来测定由于曲率不同而引起的声能损失,其形状和尺寸按图6所示。 图6 CSIII 标准试块 4.2.4 检测时机 检测原则上应安排在热处理后,孔、台等结构机加工前进行,检测面的表面粗糙度R α≤μm 。
●锻件超声波检测时经验计算调整值
超声波检测锻件、轧辊(底面与探测面须平行或大的实心圆柱体)时经验计算调整值 不同深度Ф2当量灵敏度增益分贝值 dB x/mm 40 50 60 70 80 90 100 150 200 250 300 350 400 450 500 550 600 650 △B/Ф223.5 25.5 27.0 28.4 29.5 30.5 31.5 35.0 37.5 39.5 41.0 42.4 43.5 44.6 45.5 46.3 47.1 47.8 x/mm 700 800 900 1000 1100 1200 △Ф248.4 49.6 50.6 51.5 52.3 53.1 注:x——平底孔至波源的距离;△B/Ф2=20lg x-8.5(不同深度Φ2当量灵敏度的增益分贝值) 缺陷Фx在x1处时与最大声程时Ф2的分贝差 dB 注:x1——缺陷Фx的声程;n——缺陷Фx在超声波探伤仪示波屏上的刻度值;△Ф——不同距离处的平底孔Фx的大小Фx——在超声波探伤仪示波屏不同刻度上所显示的缺陷;△Фx=40lg(Фx x2/Ф2x1)=40lg(10Фx/nФ2)
实用AVG曲线及缺陷当量定量表
操作步骤及举例说明 1. 调节探伤灵敏度 (1)根据探件大小,确定好探测范围; (2)置探头于工件探测面上,找到工件完好部位的大平底回波(底面与探测面须平行)或大实心圆柱体底波,将其调到一定高度; (3)查曲线即得到所对应长度的分贝值,再增益其分贝值,即得所对应的Ф2当量灵敏度。另外可查表得到其他灵敏度。 2 .确定缺陷当量 (1)找出缺陷回波的最高峰,增加仪器分贝值使之处于所定的某一高度,则仪器分贝增加值已知; (2)根据此缺陷波所处的位置及分贝增加值,查表可得缺陷的当量大小。 举例:一检件规格为Φ120×1000.距离600处有一缺陷,现有PXUT-320C一台,2.5P20Z探头一个,以此条件检测此检件并确定缺陷的当量大小。 1.在试块上测好零点并保存。 2.将探测范围调至1500㎜,探头置于检件探测面找完好部位大平地回波至80﹪波高。 3.查表1000处为51.5dB,仪器再增益51.5dB。此处Ф2灵敏度调好。确定。 4.找到缺陷最高波至80﹪波高,记下此时dB增加值。 5.根据缺陷所处位置及dB增加值,查表得缺陷的当量大小。 假设2.5刻度处dB增加值31 dB,则缺陷的当量大小为Ф3。 注: 1.大平底声程差1倍,回波声压差6dB。 2.平底孔声程差1倍或孔径差1倍,回波声压均差12dB。 3.2.5MH 声程100㎜大平底与同声程Φ2平底孔声程差31.5 dB。声程100㎜×N(某一数)的大平底与同声程Φ2平底孔声程差为 Z (31.5+20LgN)dB。
锻件超声波检验
锻件超声波检验标准化管理处编码[BBX968T-XBB8968-NNJ668-MM9N]
锻件超声波检验 范围:本条适用于承压设备用碳钢和低合金钢锻件的超声检测和质量分级。 本条不适用于奥氏体钢等粗晶材料锻件的超声检测,也不适用于内外半径之比小于80%的环形和筒形锻件的周向横波检测。 探头:双晶直探头的公称频率应选用5MHz;探头晶片面积不小于150mm2;单晶直探头的公称频率应选用2MHz~5MHz,探头晶片一般为φ14mm~25mm。 试块:用标准锻件试块CSⅠ、CSⅡ、CSⅢ。 检验时机:原则上应热处理后,在槽、孔,台阶等加工前,比较简单的几何形状下进行,检测面的表面粗糙度R a≤μm。 扫查面:扫查表面应无油垢和污物等附着物。 耦合剂:机油或浆糊。 检验方法:以纵波检验为主。对筒形和环形锻件还应进行横波检验,检查部位和验收标准按产品技术要求而定。 扫查方法:以两个相互垂直的方向进行,尽可能地探测到锻件的全体积,主要探测方向如图所示。 其他形状锻件也可参照执行。
扫查速度:探头移动速度不超过150mm/s。 当锻件探测厚度大于400mm时,应从相对的两端面进行100%的扫查。 检测灵敏度的校验 当被检部位的厚度大于或等于探头的3 倍近场区长度,且探测面与底面平行时,可采用底波计算法确定检测灵敏度,校正点的位置应在工件上无缺陷的完好区域,且至少选择三点,并取得平均值;对由于几何形状所限,不能获得底波或壁厚小于探头的3 倍近场区时,可直接采用CSⅠ标准试块确定基准灵敏度。 检测灵敏度不得低于最大检测距离处的φ2mm平底孔当量直径。 缺陷当量确定,采用AVG 曲线及计算法确定缺陷当量(工件厚度大于或等于探头的三倍近场区)计算缺陷当量时,当材质衰减系数超过4dB/m时,应予修正。 记录 a.记录当量直径超过φ4mm的单个缺陷的波幅和位置; b.密集性缺陷:记录密集性缺陷中最大当量缺陷的位置和分布; c.饼形锻件应记录大于或等于φ4mm当量直径的缺陷密集区,其它锻件应记录大于或等于φ3mm当量直径的缺陷密集区; d.缺陷密集区面积以50mm×50mm的方法作为最小量度单位,其边界可由半波高度法决定。 等级分类
锻件超声波探伤
锻件超声波探伤 1.1.1筒形锻件----轴向长度L大于其外径尺寸D的轴对称空心锻件如图1(a)所示.t为公称厚度. 1.1.2 环形锻件----轴向长度L小于等于其外径尺寸D的轴对称空心件如图1(a)所示.t为公称厚度. 1.1.3 饼形锻件----轴向长度L小于等于其外径D的轴对称形锻件如图1(b)所示.t为公称厚度. 1.1.4 碗形锻件----用作容器封头,中心部份凹进去的轴对称形锻件如图1(c)所示.t为公称厚度. 1.1.5 方形锻件----相交面互相垂直的六面体锻件如图1(d)所示. 三维尺寸a、b、c中最上称厚度. 1.2 底波降低量GB/BF(dB) 无缺陷区的第一次底波高度(GB)和有缺陷区的第一次底波高度(BF)之比.由缺陷引起的底面反射的降低量用dB 值表示. 1.3 密集区缺陷 当荧光屏扫描线上相当于50mm的声程范围内同时有5个或者5个以上的缺陷反射信号;或者在50mm×50mm 的探测面上发现同一深度范围内有5个或5个以上的缺陷反射信号. 1.4 缺陷当量直径 用AVG方法求出的假定与超声波束相垂直的平底孔的直径,称为缺陷当量直径,或简称为当量直径. 1.5 AVG曲线 以纵座标轴表示相对的反射回波高度,以横座标轴表示声程,对不同直径且假定与超声波束相垂直的圆平面缺陷所画出的曲线图叫AVG曲线,亦称为DGS曲线. 2探伤人员 锻件探伤应由具有一定基础知识和锻件探伤经验,并经考核取得国家认可的资格证书者担任. 3探伤器材 3.1 探伤仪 3.1.1 应采用A型脉冲反射式超声波探伤仪,其频响范围至少应在1MHz~5Mhz内. 3.1.2 仪器应至少在满刻度的75%范围内呈线性显示(误差在5%以内),垂直线性误差应不大于5%. 3.1.3 仪器和探头的组合灵敏度:在达到所探工件最大程处的探伤灵敏度时,有效灵敏度余量至少为10dB. 3.1.4 衰减器的精度和范围,仪器的水平线性、动态范围等均应队伍ZBY230-84《A型脉冲反射式超声波探伤仪通用技术条件》中的有关规定. 3.2 探头 3.2.1 探头的公称频率主要为2.5Mhz,频率误差为±10%. 3.2.2 主要采用晶片尺寸为Φ20mm的硬保护膜直探头. 3.2.3 必要时也可采用2MHzs或25MHz,以及晶片尺寸不大于Φ28mm探头. 3.2.4 探头主声束应无双峰,无偏斜. 3.3 耦合剂 可采用机油、甘油等透声性能好,且不损害工件的液体. 4探伤时机及准备工作 4.1 探伤时机 探伤原则上应安排在最终热处理后,在槽、孔、台级等加工前,比较简单的几何形状下进行.热处理后锻件形状若不适于超声波探伤也可在热处理前进行.但在热处理后,仍应对锻件尽可能完全进行探伤. 4.2 准备工作 4.2.1 探伤面的光洁度不应低一地5,且表面平整均匀,并与反射面平等,圆柱形锻件其端面应与轴线相垂直,以便于轴向探伤.方形锻件的面应加工平整,相邻的端面应垂直. 4.2.2 探伤表面应无划伤以及油垢和油潜心物等附着物. 4.2.3 锻件的几何形状及表面检查均合格后,方可进行探伤. 4.3 重要区 锻件的重要区应在设计图样中或按JB 755-85《压力容器锻件技术条件》予以注明. 5探伤方法 锻件一般应进行纵波探伤,对简形锻件还应进行横波探伤,但扫查部位和验收标准应由供需双方商定.
超声波检测国家标准总汇(2015最新)
超声波检测国家标准超声波检测国家标准超声波检测国家标准GB 3947-83 GB/T1786-1990 GB/T 2108-1980 GB/T2970-2004 GB/T3310-1999 GB/T3389.2-1999 GB/T4162-1991 GB/T 4163-1984 GB/T5193-1985 GB/T5777-1996 GB/T6402-1991 GB/T6427-1999 GB/T6519-2000 GB/T7233-1987 GB/T7734-2004 GB/T7736-2001 GB/T8361-2001 GB/T8651-2002 GB/T8652-1988 GB/T11259-1999 GB/T11343-1989 GB/T11344-1989 GB/T11345-1989 GB/T 12604.1-2005 GB/T 12604.4-2005 GB/T12969.1-1991 GB/T13315-1991 GB/T13316-1991 GB/T15830-1995 GB/T18182-2000 GB/T18256-2000 GB/T18329.1-2001 GB/T18604-2001 GB/T18694-2002 GB/T 18696.1-2004 GB/T18852-2002/行业标准 /行业标准 /行业标准表 声学名词术语 锻制园并的超声波探伤方法 薄钢板兰姆波探伤方法 厚钢板超声波检验方法 铜合金棒材超声波探伤方法 压电陶瓷材料性能测试方法纵向压电应变常数d33 的静态测试 锻轧钢棒超声波检验方法 不锈钢管超声波探伤方法(NDT,86-10) 钛及钛合金加工产品( 横截面厚度≥13mm) 超声波探伤方法(NDT,89-11)(eqv AMS2631) 无缝钢管超声波探伤检验方法(eqv ISO9303:1989) 钢锻件超声波检验方法 压电陶瓷振子频率温度稳定性的测试方法 变形铝合金产品超声波检验方法 铸钢件超声探伤及质量评级方法(NDT,89-9) 复合钢板超声波检验方法 钢的低倍组织及缺陷超声波检验法( 取代 YB898-77) 冷拉园钢表面超声波探伤方法(NDT,91-1) 金属板材超声板波探伤方法 变形高强度钢超声波检验方法(NDT,90-2) 超声波检验用钢制对比试块的制作与校验方法(eqv ASTME428-92) 接触式超声斜射探伤方法(WSTS,91-4) 接触式超声波脉冲回波法测厚 钢焊缝手工超声波探伤方法和探伤结果的分级(WSTS,91-2 ~3) 无损检测术语超声检测代替JB3111-82 GB/T12604.1-1990 无损检测术语声发射检测代替JB3111-82 GB/T12604.4-1990 钛及钛合金管材超声波检验方法 锻钢冷轧工作辊超声波探伤方法 铸钢轧辊超声波探伤方法 钢制管道对接环焊缝超声波探伤方法和检验结果分级 金属压力容器声发射检测及结果评价方法 焊接钢管 ( 埋弧焊除外 )—用于确认水压密实性的超声波检测方法(eqv ISO 10332:1994) 滑动轴承多层金属滑动轴承结合强度的超声波无损检验 用气体超声流量计测量天然气流量 无损检测超声检验探头及其声场的表征(eqv ISO10375:1997) 声学阻抗管中吸声系数和声阻抗的测量第 1 部分 : 驻波比法 无损检测超声检验测量接触探头声束特性的参考试块和方法
超声波检测的基本方法 a
超声波检测的基本方法 利用超声波在物体中的多种传播特性,例如反射与折射、衍射与散射、衰减、谐振以及声速等的变化,可以应用于无损地测知物体的几何尺寸、表面与内部缺陷、显微组织的变化等多种应用。 在工业超声波检测中,主要利用纵波、横波、瑞利波、兰姆波、爬波以及新型的导波等各种不同波型的超声波,例如利用纵波检测锻铸件及型材、复合板材的内部缺陷,利用横波检测焊缝、管材以及在工件内倾斜取向的缺陷,利用瑞利波检测工件的表面缺陷,利用兰姆波检测薄金属板材、细棒和薄壁管,利用爬波检测工件表面下的近表层缺陷,利用导波进行长距离管线检测等等。因此,超声波检测的适用范围非常广泛,包括了金属、非金属,锻件、铸件、焊接件、型材、胶接结构与复合材料、紧固件等等。 超声波检测的优点是穿透力强、设备轻便、检测成本低、检测效率高,能即时知道检测结果(实时检测),能实现自动化检测和实现永久性记录,在缺陷检测中对危害性较大的裂纹类缺陷特别敏感等等。 超声波检测的缺点是通常需要耦合介质使声能透入被检物,需要有参考评定标准,特别是显示的检测结果不够直观,因而对操作人员的技术水平有较高要求等等,此外,对于小而薄或者形状较复杂,以及粗晶材料等的工件检测还存在一定困难。 此外,根据超声检测的结果判断缺陷的性质(定性)问题尚未很好解决,目前还主要是依靠检测人员的实践经验、技术水平以及对被检工件的材料特性、加工工艺特点、使用状况等的了解来进行综合的主观判断。
工业超声波检测方法的一般原理与分类 一.根据采用超声波的种类分类 (一)脉冲波法:超声波探头激发的是脉冲超声波,这是具有一定持续时间、按一定重复频率间歇发射的超声波,通常具有较大的频带宽度。 (1)脉冲波反射法:在超声波检测时,向被检对象发射脉冲超声波,利用超声波的反射特性,根据有无缺陷回波或工件底面反射回波、回波幅度的大小、回波信号数量、回波在示波屏时基线上的位置以及回波包络形状变化等对被检对象的质量情况进行评价。 超声波脉冲反射法是目前应用最广泛的超声波检测方法,包括一次脉冲反射法和多次脉冲反射法,前者利用一次回波脉冲,后者则利用超声波脉冲波在工件中多次反射形成的多次回波脉冲来进行评价。 (2)脉冲波穿透法:在超声波检测时,由一个探头向被检对象发射脉冲超声波,用另一个探头在适当位置接收穿越材料的超声波,根据接收的超声信号强弱来评价被检对象有无缺陷及缺陷严重程度等情况。 在利用脉冲波穿透法时,甚至可以将仪器简化成电表指示(或者更简单的是声音-声调变化指示)而省掉示波管显示系统。