4-5、6刀具几何参数的合理选择、切削用量的合理选择
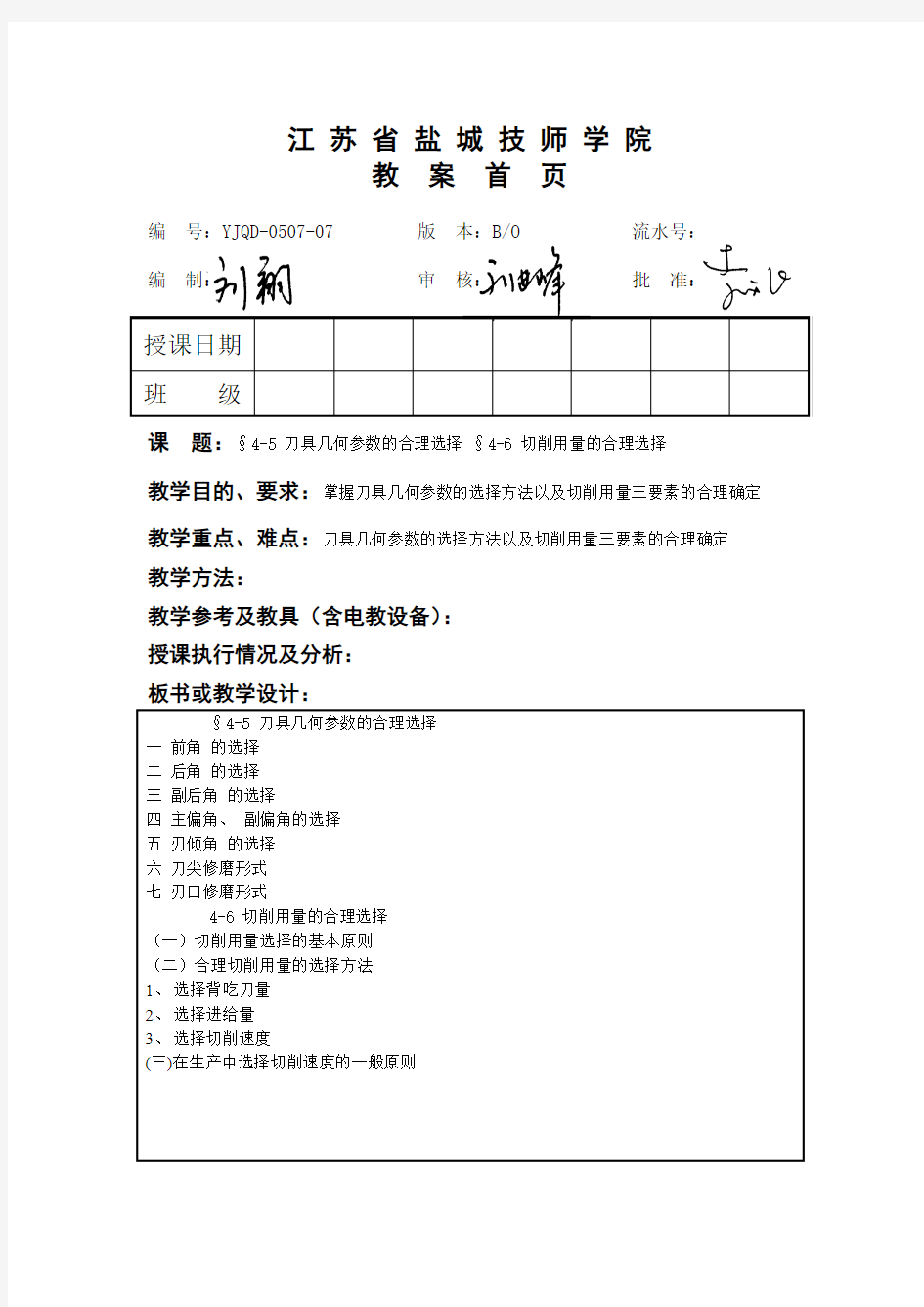

江苏省盐城技师学院
教案首页
编号:YJQD-0507-07 版本:B/O 流水号:
编制:审核:批准:
课题:§4-5 刀具几何参数的合理选择§4-6 切削用量的合理选择
教学目的、要求:掌握刀具几何参数的选择方法以及切削用量三要素的合理确定教学重点、难点:刀具几何参数的选择方法以及切削用量三要素的合理确定
教学方法:
教学参考及教具(含电教设备):
授课执行情况及分析:
板书或教学设计:
复习提问:
1、切削液的种类及用途。
2、影响表面粗糙度的因素。
讲授新课:
§4-5 刀具几何参数的合理选择
一前角的选择
(一)前角的作用
增大前角能减小切削变形和摩擦,降低切削力、切削温度,减少刀具磨损,改善加工质量,抑制积屑瘤等。但前角过大会削弱刀头强度和散热能力,容易造成崩刃。因而前角不能太小,也不能太大,应有一个合理数值。
(二)前角的选择原则
1、主要根据工件材料的性质选择
2、兼顾根据刀具材料的性质和加工性质
二后角、副后角的选择
1.后角的功用
增大后角能减小后刀面与工件上加工表面间的摩擦,减少刀具磨损,还可以减小切削刃钝圆半径,使刀刃锋利,可减小工件表面粗糙度值。但后角过大会减小刀刃强度和散热能力。
2.后角的选择原则
后角主要根据切削厚度选择。粗加工取小一点,精加工取大一点。
三副后角的选择
副后角通常等于后角的数值。
四主副偏角的选择
1.主、副偏角的功用
主偏角κr 影响切削分力的大小,增大κr,会使Ff力增加,Fp力减小;
主偏角影响加工表面粗糙度值的大小,增大主偏角,加工表面粗糙度值增大;
主偏角影响刀具耐用度,增大主偏角,刀具耐用度下降;
主偏角也影响工件表面形状,车削阶梯轴时,选用κr =90o,车削细长轴
时,选用κr =75o~90o;为增加通用性,车外圆、端面和倒角时,可选用
κr =45o。
减小副偏角κr。,会增加副切削刃与己加工表面的接触长度,能减小表面粗糙度数值,并能提高刀具耐用度。但过小的副偏角会引起振动。
2.主、副偏角的选择
主偏角的选择原则是,在工艺系统刚度允许的情况下,选择较小的主偏角这样有利于提高刀具耐用度。在生产中,主要按工艺系统刚性选取,见表5-3。副偏角κr,主要是根据加工性质选取,一般情况下选取κr ′=10°~15°精加工时取小值。特殊情况,如切断刀,为了保证刀头强度,可选κr ′=1°~2°。
五刃倾角的选择
1.刃倾角的功用
(1)控制切屑的流向
如图
(2)控制切削刃切入时首先与工件接触的位置
如图所示
(3)控制切削刃在切入与切出时的平稳性如上图所示,断续切削时,当刃倾角为零,切削刃与工件同时接触,同时切离,会引起振动;若刃倾角不等于零则切削刃上各点逐渐切入
工件和逐渐切离工件,故切削过程平稳。
(4)控制背向力与进给力的比值
2.刃倾角的选择
选择刃倾角时,应按照刀具的具体工作条件进行具体分析,一般情况可按加工性质选取。精车λs =0o~5o;粗车λs =0o~-5o;断续车削λs=-30o~-45o;大刃倾角精刨刀λs=75o~80o。
六刀尖修磨形式
1.直线过渡刃
如图a所示,过渡刃的偏角κrε≈κr/2、长度bε≈(1/4~1/5)ap ,这种过渡刃多用于粗加工或强力切削的车刀上。
2.圆弧过渡刃
如图b所示,过渡刃也可磨成圆弧形。它的参数就是刀尖圆弧半径rε。
刀尖圆弧半径增大时,使刀尖处的平均主偏角减小,可以减小表面粗糙度数值,且能提高刀具耐用度。但会增大背向力和容易产生振动,所以刀尖圆弧半径不能过大。通常高速钢车刀rε=0.5~5mm,硬质合金车刀rε=0.5~2mm。
3.水平修光刃
如图c所示,修光刃是在副切削刃靠近刀尖处磨出一小段κr‘=0o的平刀刃。其长度bε‘≈(1.2~1.5)f,即bε‘ 应略大于进给量f。但bε‘ 过大易引起振动。
4.大圆弧刃
如图d所示,大圆弧刃是把过渡刃磨成非常大的圆弧形,它的作用相当于水平修光刃。七刃口修磨形式
见图4-22
4-6 切削用量的合理选择
切削用量三要素υc、?、ap
(一)切削用量选择的基本原则
1.根据工件加工余量和粗、精加工要求,选定背吃刀量。
2.根据加工工艺系统允许的切削力,其中包括机床进给系统、工件刚度及精加工时表
面粗糙度要求,确定进给量。
3.根据刀具耐用度,确定切削速度。
4.所选定的切削用量应该是机床功率允许的。
(二)合理切削用量的选择方法
1.确定背吃刀量
粗加工时,一次走刀尽可能切除全部余量。
半精加工时,被吃刀量取为0.5~2mm。
精加工时,被吃刀量取为0.1~0.4mm。
2. 确定进给量
粗加工时,进给量由机床进给机构强度、刀具强度与刚性、工件的装夹刚度决定。
精加工时,进给量由加工精度和表面粗糙度决定。
生产实际中多采用查表法确定进给量。
3.确定切削速度
在ap、f 值选定后,根据合理的刀具耐用度或查表来选定切削速度。
(三) 在生产中选择切削速度的一般原则
(1)粗车时,ap、f 较大,故选择较低的v;精车时,ap 、f均较小,故选择较高的v。(2)工件材料强度、硬度高时,应选较低的v。
(3)切削合金钢比切削中碳钢切削速度应降低20%~30%;切削调质状态的钢比正火、退火状态钢要降低20%~30%;切削有色金属比切削中碳钢的切削速度可提高100%~300%;
(4)刀具材料的切削性能愈好,切削速度也选得愈高。
(5)精加工时,应尽量避开积屑瘤和鳞刺产生的区域。
(6)断续切削及加工大件、细长件和薄壁工件时,应适当降低切削速度。
(7)在易发生振动的情况下,切削速度应避开自激振动的临界速度。
课堂小结
1、刀具几何参数的合理选择
2、切削用量三要素的合理选择
布置作业P90 4-12 4-16
刀具切削参数
白钢刀 刀具类型 最大加工 深度(mm) 普通长度(mm) 刃长/刀长 普通加长(mm) 刃长/加长 主轴转速 (r/m) 进给速度 (mm/min) 吃刀量 (mm) D32 120 60/125 106/186 300~400 500~1000 0.1~1 D25 120 60/125 90/166 300~400 500~1000 0.1~1 D20 120 50/110 75/141 500~700 500~1000 0.1~1 D16 120 40/95 65/123 500~800 500~1000 0.1~0.8 D12 80 30/80 53/110 500~1000 500~1000 0.1~0.8 D10 80 23/75 45/95 800~1000 500~1000 0.2~0.5 D8 50 20/65 28/82 800~1200 500~1000 0.2~0.5 D6 50 15/60 不存在800~1200 500~1000 0.2~0.4 R8 80 32/92 35/140 800~1000 500~1000 0.2~0.4 R6 80 26/83 26/120 800~1000 500~1000 0.2~0.4 R5 60 20/72 20/110 800~1000 500~1000 0.2~0.4 R3 30 13/57 15/90 1000~1500 500~1000 0.2~0.4 飞刀 刀具类型最大加工深 度(mm) 普通长度 (mm) 普通加长 (mm) 主轴转速 (r/m) 进给速度 (mm/min) 吃刀量 (mm) D63R6 300 150 320 700~1000 2500~4000 0.2~1 D50R5 280 135 300 800~1500 2500~3500 0.1~1 D35R5 150 110 180 1000~1800 2200~3000 0.1~1 D30R5 150 100 165 1500~2200 2000~3000 0.1~0.8 D25R5 130 90 150 1500~2500 2000~3000 0.1~0.8 D20R0.4 110 85 135 1500~2500 2000~2800 0.2~0.5 D17R0.8 105 75 120 1800~2500 1800~2500 0.2~0.5 D13R0.8 90 60 115 1800~2500 1800~2500 0.2~0.4 D12R0.4 90 60 110 1800~2500 1500~2200 0.2~0.4 D16R8 100 80 120 2000~2500 2000~3000 0.1~0.4 D12R6 85 60 105 2000~2800 1800~2500 0.1~0.4 D10R5 78 55 95 2500~3200 1500~2500 0.1~0.4 U G 学习群:1 8 3 9 6 0 8 9 6 欢迎大家的加入!
刀具几何参数的选择
2.4 刀具磨损和刀具耐用度 2.4.1 刀具的磨损形式及原因 (1)刀具的正常磨损形式 1)前面磨损 前面上形成月牙洼磨损(速度高,厚度大,形成月牙洼) 2)后面磨损 后面的磨损形式是磨成后角等于零的磨损棱带。后面磨损棱带的中间部位 表示。(B区),磨损比较均匀,其平均宽度以VB表示,而且最大宽度以VB max 3)前后面同时磨损或边界磨损(速度底,切削厚度较小的塑性金属及加工脆性金属时) 非正常磨损:刀具在切削的过程中突然或者过早的损现象叫~ 。又叫破损。常常分为两类:1.脆性破损(硬质合金和陶瓷刀具时)2.塑性破损(高速刚)(2)刀具磨损的原因 1)硬质点磨损(磨粒磨损)(碳化物,氧化物等) 工件材料中的杂质在刀具表面上擦伤,划出一条条的沟纹造成的机械磨损。 2)粘结磨损 在一定的压力和温度作用下,在切屑与前面、已加工表面与后面的磨擦面上,产生塑性变形,形成粘结点,这些粘结点又因相对运动而破裂,粘结点的破裂也常常发生在刀具一方面被工件材料带走,从而形成刀具的粘结磨损。 3)扩散磨损 切削过程中,刀具表面与工件由于高温与高压的作用,两磨擦表面上的化学元素有可能互相扩散到对方去,使两者的化学成分发生变化,从而削弱了刀具材料的性能,加速了刀具的磨损。扩散速度随切削温度的升高而增加。 4)化学磨损(氧化磨损,相变磨损) 化学磨损是在一定温度下,刀具材料与某些周围介质起化学作用,在刀具表面形成一层硬度较低的化合物,而被切屑带走,加速了刀具的磨损。由于切屑不易进入刀具与切屑的接触区,故氧化磨损容易在主、副切削刃的工作面处形成。
3.2 刀具合理几何参数的选择 3.2.1 概述 刀具几何参数包括:刀具角度、刀面形式、切削刃形状等。 刀具合理的几何参数,是指在保证加工质量的前提下,能够获得最高刀具耐用度,从而达到提高切削效率或降低生产成本目的的几何参数。刀具合理几何参数的选择决定于工件材料、刀具材料、刀具类型及其他具体工艺条件。 3.2.2 前角及前面形状的选择 (1)前角的功用及合理前角的选择 1)前角的主要功用 ①影响切削区的变形程度 ②影响切削刃与刀头的强度 ③影响切屑形态和断屑效果 ④影响已加工表面质量 2)增大或减小前角各有利弊,前角有一个合理的数值。 3)合理前角的选择原则 ①工件 ropt塑>ropt脆,ropt低强度纲>ropt高强度钢 ②刀具 ropt硬 第一. 合理的刀具几何参数是提高刀具切削性能的重要因素,传统的刀具合理几何参数的研究方法一般是先设计并选择不同的刀具几何参数及工艺参数,并借助于一定的测试手段,来进行实际的切削实验。用这种方法来进行研究,往往要经历一个很长的过程,耗时、耗力、实验成本高。所以刀具合理几何参数的选择是切削理论与实践的重要课题。所谓刀具的合理的(或者最佳)几何参数 是在保证加工质量的前提下,能够满足生产效率高、加工成本高的刀具几何参数。一般的说,选定刀具几何参数的合理值问题,本质上是多变量函数针对某一目标计算求解最佳值的问题,但是,由于影响切削加工效益的因素太多,而且影响因素之间又是相互作用的,因而建立数学模型的难度很大。实用的优化或最佳化工作,只能在固定若干因素后,改变少量参数,取得实验数据,并且采用适当方法(例如方差分析法、回归分析法)进行处理,得出优选结论。 可见,选择合理的刀具几何参数的重要性,所以利用相关软件进行直接模拟优化结构、几何参数有其极其重要的现实意义。 刀具角度包括主切削刃的前角、后角、主偏角、刃倾角和副切削刃的副后角、副偏角等。不同的角度对刀具具体切削过程的影响是不同的。 1、前角变化对切削过程中的切削力、切屑变形等有很大的影响,其中前角对切削力的影响最大。有人曾研究认为:前角每变化一度,主切削力约改变1.5%。在切削过程中,切削力随着前角的增大而减小。这是因为当前角增大时,剪切角也随之增大,金属塑性变形减小,变形系数减小,沿前刀面的摩擦力也减小,因此切削力降低。这种变化趋势在较低速的切削中尤为明显。通过前述有限元分析,将刀具上沿接触长度上各节点的应力值相加可以获得主切削力,而在构成主切削力的各节点应力值中,刀刃部分具有最大等效力值的节点贡献最大。因此可以这么说,为其前角变化对于切削力的影响,可以通过研究刀具前刀面上具有最大等效应力的节点的应力状况而表现出来。所以,我们选取刀具接触长度上节点的最大等效应力作为刀具前角优化的标准。 2、后角的主要功用是减小切削过程中刀具后刀面与加工表面之间的摩擦。后角的大小还影响作用在后刀面上的力,后刀面与工件的接触长度以及后刀面的西华大学硕士学位论文 高速铣削刀具及切削参数的选择 摘要:通过等效类比的方法研究了高速铣削刀具选择的一般原则。推导了球头铣刀的有效直径和有效线速度的计算公式,以此进一步确定转速,通过试验的方法测定了径向铣削深度和每 齿进给量对表面粗糙度的影响。 关键词:高速铣削刀具;有效直径;有效线速度;切削参数;表面粗糙度 作者:宋志国,宋艳,常州信息职业技术学院 0 引言 传统意义上的高速切削是以切削速度的高低来进行分类的,而铣削机床则是以转速的高低进行分类。如果从切削变形的机理来看高速切削,则前一种分类比较合适;但是若从切削工艺的角度出发,则后一种更恰 当。 这是因为随着主轴转速的提高,机床的结构、刀具结构、刀具装夹和机床特性都有本质上的改变。高转速意味着高离心力,传统的7∶24锥柄,弹簧夹头、液压夹头在离心力的作用下,难以提供足够的夹持力; 同时为避免切削振动要求刀具系统具有更高的动平衡精度。 高速切削的最大优势并不在于速度、进给速度提高所导致的效率提高;而是由于采用了更高的切削速度和进给速度,允许采用较小的切削用量进行切削加工。由于切削用量的降低,切削力和切削热随之下降,工 艺系统变形减小,可以避免铣削颤振。 1 刀具的选择 通常选用图1所示的3种立铣刀进行铣削加工,在高速铣削中一般不推荐使用平底立铣刀。平底立铣刀在切削时刀尖部位由于流屑干涉,切屑变形大,同时有效切削刃长度最短,导致刀尖受力大、切削温度高,导致快速磨损。在工艺允许的条件下,尽量采用刀尖圆弧半径较大的刀具进行高速铣削。 图1 立铣刀示意图 随着立铣刀刀尖圆弧半径的增加,平均切削厚度和主偏角均下降,同时刀具轴向受力增加可以充分利用机 床的轴向刚度,减小刀具变形和切削振动(图2)。 刀具合理几何参数的选择是切削刀具理论与实践的重要课题。中国有句谚语说:“工欲善其事,必先利其器”,刀具正是切削加工的直接作用工具,它的完善程度对切削加工的现状和发展起着决定性的作用。CIRP的一项研究报告指出:“由于刀具材料的改进,刀具的允许切削速度每隔十年几乎提高一倍;由于刀具结构和几何参数的改进,刀具使用寿命每隔十年几乎提高二倍。”这也说明了选择刀具合理几何参数的重要意义。 什么是刀具的合理(或最佳)几何参数呢? 在保证加工质量的前提下,能够满足刀具使用寿命长、生产效率高、加工成本低的刀具几何参数,称为刀具的合理几何参数。 一般地说,选定刀具几何参数的合理值问题,本质上是多变量函数针对某一目标计算求解最佳值的问题。但是,由于影响切削加工效益的因素很多,而且影响因素之间又是相互作用的,因而建立数学模型的难度甚大。实用的优化或最佳化工作,只能在固定若干因素后,改变少数参量,取得实验数据,并且采用适当方法(例如方差分析法、回归分析法等)进行处理,得出优选结果。 二、刀具合理几何参数的基本内容 刀具的合理几何参数包含以下四个方面基本内容: 1.刃形 刃形即是切削刃的形状。从简单的直线刃发展到折线刃、圆弧刃、月牙弧刃、波形刃、阶梯刃及其他适宜的空间曲线刃,同时也明确了一定的切削加工条件必定对应有某种适宜的刃形。这是刀具几何构形趋于合理的一种标志。刀尖形状的变革,也是刃形变革的内容之一。 刃形直接影响切削层的形状,影响切削图形的合理性;刃形的变化,将带来切削刃各点工作角度的变化。因此,选择合理的刃形,对于提高刀具使用寿命、改善已加工表面质量、提高刀具的抗振性和改变切屑形态等,都有直接的意义。以切断刀为例(图10—1),说明 刀具的几何参数包括刀具的切削角度,刀面的形式(如平前刀面,带卷屑断屑槽的前刀面、波形刀面等)以及切削刃的形状(直线形、折线形、圆弧形等)。 刀具的几何参数对切屑变形、切削力、切削温度和刀具磨损都有显著影响,从而影响切削加工生产率、刀具耐用度、加工质量和加工成本。 刀具的合理几何参数.是指在保证加工质量的前提下,能够获得最高刀具耐用度,从而能达到提高切削效率,降低加工成本目的的几何参数。 选择刀具合理几何参数主要取决于工件材料、刀具材料、刀具类型,也与切削用量、工艺系统刚性和机床功率等因素有关。 第一节前角及前刀面形状的选择 一、前角的功用及选择 前角是刀具上重要的几何参数之一,它的大小决定切削刃的锋利程度和强固程度,直接影响切 削过程。前角有正前角和负前角之分。 取正前角的目的是为了减小切屑被切下时的弹塑性变形和切屑 流出时与前面的摩擦阻力,从而可减小切削力和切削热,使切削轻 快,提高刀具寿命,并提高已加工表面质量。但前角过大时,楔角 过小,会削弱切削刃部的强度并降低散热能力,反而会使刀具寿命 降低。由图可知,加工不同材料时,前角太大或太小,刀具耐用度 都较低。在一定加工条件下,存在一个耐用度为最大的前角,即合 理前角。 取负前角的目的在于改善刃部受力状况和散热条件,提高切削 刃强度和耐冲击能力。负前角刀具通常在用脆性 刀具材料加工高强度高硬度工件材料而当切削刃强度不够、易 产生崩刃时才采用。 前角的合理数值选取原则 刀具合理前角的选择主要取决于刀具材料、工件材料的种类与性质: 1.刀具材料:强度和韧性较高时可选择较大的前角。高速钢的强度高,韧性好;硬质合金脆性大,怕冲击,易崩刃。因此,高速钢刀具的前角可比硬质合金刀具选得大一些,可大5°~10°。陶瓷刀具的脆性更大,故前角应选择得比硬质合金还要小一些。选择要充分注意增加切削刃强度,常取负值(多在-4°~-15°范围)以改善刀具受力时的应力状态,并选负的刃倾角(取0°~-10°)与之配合以改善切入时承受冲击的能力。立方氮化硼由于脆性更大,都采用负前角高速切削。 2.工件材料 1)加工塑性材料时,切屑呈带状,沿刀具前面流出时和前面接触长度较长,摩擦较大,为减小变形和摩擦,一般都采用正前角。工件材料塑性愈大,强度和硬度愈低时,前角应选得愈大。如加工 铝及铝合金取γo=25°~35°,加工低碳钢常取γo=20°~25°。当工件材料强度较大、硬度较高时,前角宜取小值,如正火高碳钢取γo=10°~l5°。当加工高强度钢时,为增强切削刃,才取负前角。 2)加工脆性材料(如灰铸铁)时,塑性变形小,切屑呈崩碎状,刀屑接触长度短,摩擦不大,切削力集中在切削刃附近且产生冲击,容易造成崩刃。所选前角应比加工塑性材料时小一些,以提高切 削刃强度和散热能力。如加工灰铸铁取γo=5°~15°。前角数值随脆性材料强度和硬度的增大而逐渐 减小。在加工淬火钢、冷硬铸铁等高硬度难加工材料时,宜取负前角。实验证明,用正前角硬质合金车刀加工高硬度淬火钢时,切削刃几乎一开始切削就会发生崩刃。 3.具体加工条件:粗加工时或断续切削时,切削力和冲击较大,为使切削刃有足够强度,宜取较小前角;精加工时,切削刃强度要求较低,为使刀具刀刃锋利,降低切削力,以减小工件变形和减 切削参数选择原则: 切削用量不仅是在机床调整前必须确定的重要参数,而且其数值合理与否对加工质量、加工效率、生产成本等有着非常重要的影响。所谓“ 合理的” 切削用量是指充分利用刀具切削性能和机床动力性能 (功率、扭矩 ,在保证质量的前提下,获得高的生产率和低的加工成本的切削用量。 一制订切削用量时考虑的因素 切削加工生产率 在切削加工中,金属切除率与切削用量三要素 ap 、 f 、 v 均保持线性关系, 即其中任一参数增大一倍, 都可使生产率提高一倍。然而由于刀具寿命的制约, 当任一参数增大时,其它二参数必须减小。因此,在制订切削用量时,三要素获得最佳组合,此时的高生产率才是合理的。 刀具寿命 切削用量三要素对刀具寿命影响的大小,按顺序为 v 、 f 、 ap 。因此,从保证合理的刀具寿命出发, 在确定切削用量时, 首先应采用尽可能大的背吃刀量; 然后再选用大的进给量;最后求出切削速度。 加工表面粗糙度 精加工时,增大进给量将增大加工表面粗糙度值。因此,它是精加工时抑制生产率提高的主要因素。 二刀具寿命的选择原则 切削用量与刀具寿命有密切关系。在制定切削用量时,应首先选择合理的刀具寿命, 而合理的刀具寿命则应根据优化的目标而定。一般分最高生产率刀具寿命和 最低成本刀具寿命两种,前者根据单件工时最少的目标确定,后者根据工序成本最低的目标确定。选择刀具寿命时可考虑如下几点: 根据刀具复杂程度、制造和磨刀成本来选择。复杂和精度高的刀具寿命应选得比单刃刀具高些。 对于机夹可转位刀具,由于换刀时间短,为了充分发挥其切削性能,提高 生产效率,刀具寿命可选得低些,一般取 15-30min 。 对于装刀、换刀和调刀比较复杂的多刀机床、组合机床与自动化加工刀具, 刀具寿命应选得高些,尤应保证刀具可靠性。 车间内某一工序的生产率限制了整个车间的生产率的提高时,该工序的刀具寿命要选得低些;当某工序单位时间内所分担到的全厂开支 M 较大时,刀具寿命也应选得低些。 大件精加工时,为保证至少完成一次走刀,避免切削时中途换刀,刀具寿命应按零件精度和表面粗糙度来确定。 三切削用量制定的步骤 背吃刀量的选择 进给量的选择 切削速度的确定 校验机床功率 四提高切削用量的途径 采用切削性能更好的新型刀具材料; 在保证工件机械性能的前提下,改善工件材料加工性; 卧式数控车床刀具及切削参数选择 目录 一机卡车刀的选用 (1) 二孔加工刀具的选用 (9) 三切断和切槽刀 (12) 四螺纹车刀 (13) 五刀具材料 (16) 六刀具厂商 (17) 七刀具干涉图 (18) 八刀具允许的最大转动惯量 (19) 数控车床刀具系统比卧车复杂。要求安装数量多,安装可靠,自动换刀,装卸方便迅速还要求切削时间短以提高生产率。因此普遍采用机卡车刀。 机卡车刀是把压制有合理的几何参数,在一定的切削用量范畴内保证卷屑,断屑并有几个刀刃的刀片,用机械卡固方式装卡在标准刀体上的一种新型刀具。它避免了硬质合金刀片在焊接中产生的种种不良后果,因此能充分发挥刀片材料原有的切削性能,提高了车刀的耐用度和切削加工的生产率.另外刀体可重复使用,能节约大量制造刀体的钢材.还便于使刀具标准化和集中生产,同一型号刀片的几何形状较一致切削效果稳定.有利于提高零件加工质量,简化了刀具的管理工作.使用时,当刀刃磨损后,只需松开卡紧机构将刀片转一个角度,不必重磨,大大缩短了换刀.磨刀.装刀的辅助时间,而且可以避免刀片由于重磨而造成的缺陷.因此机卡车刀也叫不重磨车刀或可转位车刀。 除不可避免的情况外,为用户选用的都应该是机卡车刀。 一机卡车刀的选用 侧重外表面车刀的选用。内孔车刀大体相同,其特殊性问题另做叙述。 ISO对外表面车刀型号是如下表示的,它是国内外刀具厂商的统一标准。 选刀工作也就是确定型号中的各项内容,按选刀时考虑问题的大体顺序分叙如下: (一)刀片形状的选择:外内表面车刀刀片形状关系车刀类型,它取决于加工部位的形状,是选刀的最重要内容。它主要涉及刀具的主偏角,刀尖角和有效刃数等。一般来讲刀尖角愈大刀尖强度愈高,应尽量采用。但刀尖角小干涉现象少,适用于复杂型面,开挖沟槽及下坡的型面。 刀片形状甚多,某些厂家列出十几种,本厂实际只用过图1所示七种,也正是ISO规定的七种基本类型。 切削参数的控制 切削参数的选择对加工质量、加工效率以及刀具耐用度有着直接的影响。在CAM软件中与切削相关的参数主要有主轴转速(Spindlespeed)、进给速率(Cut feed)、刀具切入时的进给速率(Lead in feed rate)、步距宽度(Step-over)和切削深度(Step depth)等。 1.主轴转速 主轴转速一般根据切削速度来计算,其计算公式为:n = 1 0 0 0 V c /πd,式中d为刀具直径(mm),Vc为切削速度(m/min)。切削速度的选择与刀具的耐用度密切相关,当工件材料、刀具材料和结构确定后,切削速度就成为影响刀具耐用度的最主要因素,过低或过高的切削速度都会使刀具耐用度急剧下降。在模具加工,尤其是模具的精加工时,应尽量避免中途换刀,以得到较高的加工质量,因此应结合刀具耐用度认真选择切削速度。 2.进给速度与刀具切入进给速度 进给速度的选择直接影响着模具零件的加工精度和表面粗糙度,其计算公式为F=nzf,式中n为主轴转速(r/min),z为铣刀齿数,f为每齿进给量(mm/齿)。每齿进给量的选取取决于工件材料的力学性能、刀具材料和铣刀结构。工件的硬度和强度越高,每齿进给量越小;硬质合金铣刀比同类高速钢铣刀每齿进给量要高;当加工精度和表面粗糙度要求较高时,应选择较低的进给量;刀具切入进给速度应小于切削进给速度。 3.吃刀量 吃刀量的大小主要受机床、工件和刀具刚度的限制,其选择原则是在满足工艺要求和工艺系统刚度许可的条件下,选用尽可能大的吃刀量,以提高加工效率。为保证加工精度和表面粗糙度,应留0.2~0.5mm的精加工余量。在粗加工时,余量的切除往往采用层切的方法,在CAM编程时,需要设置每层切削深度和最大步距宽度,而实际步距往往与工件形状有关。 数控加工刀具及参数选择 【摘要】数控刀具的选择和切削切削参数的确定是数控加工工艺中的重要内容,它不仅影响数控机床的加工效率,而且直接影响加工质量。一般说来,我们考评加工效率,主要是从加工时间考虑,但某些情况下,刀具寿命也是加工要素之一。 【关键词】数控;刀具;参数 中图分类号:tp27文献标识码:a文章编号: 1006-0278(2012)04-125-01 数控加工具有高速、高效和自动化程度高的特点,数控刀具一般分为通用刀具、专用刀具及某些特殊刀具。刀具通过刀柄连接并装在机床动力头上,因此已逐渐标准化和系列化。数控刀具的分类有多种方法。根据刀具结构可分为:①整体式。②镶嵌式(采用焊接或机夹式联接,机夹式又可分为不转位和可转位两种)。③特殊形式,如复合式刀具、减振式刀具等根据制造刀具所用的材料可分为:①高速钢刀具。②硬质合金刀具(涂层和非涂层)。③金刚石刀具。 ④其他材料刀具,如立方氮化硼刀具、陶瓷刀具等。随着数控技术的发展,要求我们换刀迅速,近几年机夹式可转位刀具得到广泛的应用,在数量上达到整个数控刀具的30%~40%,金属切除量占总数的80%一90%。 数控刀具与普通机床上所用的刀具相比,有许多不同的要求,主要有以下特点:①刚性好(尤其是粗加工刀具)、精度高、抗振及热 变形小。②互换性好,便于快速换刀。③寿命高,切削性能稳定、可靠。④刀具的尺寸便于调整,以减少换刀调整时间。⑤刀具应能可靠地断屑或卷屑,以利于切屑的排除。⑥系列化、标准化,以利于编程和刀具管理。 由于数控刀具具有以上特点,以及数控技术发展需要,市面上各类辅导书花样翻新,层出不穷,其质量参差不齐,有的作者只是为了赚取稿费,其中设置参数很是随意,直接造成的后果就是很多学生拿到书籍,不知道应该相信哪本书,也给我们日常教学带来很多的麻烦,经常出现的事情就是,学生拿着书怀疑我们教学内容的准确性。 这里有一个我经历的例子,某次全国性质的金工实习培训项目,有数十位相关人员参加,我们单位负责数控铣床实习操作,我们准备的材料为易切削刚,45#钢,使用的刀具为16高速钢键槽铣刀,刀具为新刀具,倒角大小为0.5mm。机床种类为自贡数控加工中心,x轴行程1050mm,机床的刚性良好。无冷却液状态加工。我们指导人员设置的加工参数分别为:s=400n/min,t=1mm.f=150mm/min。按照这一组参数加工,机床加工状态良好,噪音很小,机床没有什么明显的抖动。操作工程中,其中一位年轻老师反对我们设置的参数,要求更改s=600n/min,及t=2mm,我们分别做了实验: 采取s=600n/min时,刀具很快磨损,铁屑形状有片状变为碎末,铁屑颜色由淡黄色变为蓝色,直至加工过程中产生刺耳的摩擦声 铣床选择 XK5025 数控立式升降台铣床技术参数 由加工零件尺寸、表面形状、零件整体造型及加工内容,选择数控立式升降台铣床。因为此零件精度要求不高,该机床的精度满足要求,机床的价格成本低,故选择此型号。 刀具及铣削参数的确定 1.刀具选择 各工序所涉及的加工方法有:粗铣、半精铣、钻和扩,材料为HT150 ,可选用硬质合 金铣刀、高速钢麻花钻和高速钢扩孔钻。加工铸铁类零件采用 YG 类硬质合金,粗加工用YG8 ,半精加工用 YG6。 工序 4 中粗铣加工的表面均为平面,可选用莫氏锥柄立铣刀。查表莫氏锥柄立铣刀规格表,选 d=36,l=53,L=155, 粗齿 Z=4 ,莫氏锥柄号为 3号。 工序 5 中粗铣加工的表面均为平面,可选用莫氏锥柄立铣刀。查表莫氏锥柄立铣刀规格表,选 d=36,l=53,L=155, 细齿 Z=8 ,莫氏锥柄号为 3号。 工序 6 为钻孔及扩孔。查标准高速钢直柄麻花钻直径系列选取钻头直径d=6.5 ,查整 体高速 钢直柄扩孔钻形式和规格表,选 d=7.00,L=109 ,l=69 工序 7 为粗铣,可选用莫氏锥柄立铣刀。查表莫氏锥柄立铣刀规格表,选 d=32,l=53,L=155, 粗齿 Z=4,莫氏锥柄号为 3 号。 工序 8 为半精铣,可选用莫氏锥柄立铣刀。查表莫氏锥柄立铣刀规格表,选 d=32,l=53,L=155, 细齿 Z=8,莫氏锥柄号为 3 号。 工序 9 为钻孔。查标准高速钢直柄麻花钻直径系列选取钻头直径d=18、 d=9。 工序 10 为粗铣,可选用莫氏锥柄立铣刀。查表莫氏锥柄立铣刀规格表,选 d=26,l=45,L=147, 粗齿 Z=3,莫氏锥柄号为 3 号。 工序 11为半精铣,可选用莫氏锥柄立铣刀。查表莫氏锥柄立铣刀规格表,选 d=26,l=45,L=147, 细齿 Z=6,莫氏锥柄号为 3 号。 工序 12 为钻孔、扩孔及攻螺纹。查标准高速钢直柄麻花钻直径系列选取钻头直径 d=7,d=6。 查整体高速钢直柄扩孔钻形式和规格表,选d=6.7, L=109 , l=69 。查长柄机用丝锥表,选 M8 丝锥, d=8.0,螺距 1.25, dl=6.3,l=22,L=97 。 切削参数选择原则: 切削用量不仅是在机床调整前必须确定的重要参数,而且其数值合理与否对加工质量、加工效率、生产成本等有着非常重要的影响。所谓“合理的”切削用量是指充分利用刀具切削性能和机床动力性能(功率、扭矩),在保证质量的前提下,获得高的生产率和低的加工成本的切削用量。 一制订切削用量时考虑的因素 切削加工生产率 在切削加工中,金属切除率与切削用量三要素ap、f、v均保持线性关系,即其中任一参数增大一倍,都可使生产率提高一倍。然而由于刀具寿命的制约, 当任一参数增大时,其它二参数必须减小。因此,在制订切削用量时,三要素获得最佳组合,此时的高生产率才是合理的。 刀具寿命 切削用量三要素对刀具寿命影响的大小,按顺序为v、f、ap。因此,从保证合理的刀具寿命出发,在确定切削用量时,首先应采用尽可能大的背吃刀量;然后再选用大的进给量;最后求出切削速度。 加工表面粗糙度 精加工时,增大进给量将增大加工表面粗糙度值。因此,它是精加工时抑制生产率提高的主要因素。 二刀具寿命的选择原则 切削用量与刀具寿命有密切关系。在制定切削用量时,应首先选择合理的刀具寿命,而合理的刀具寿命则应根据优化的目标而定。一般分最高生产率刀具寿命和最低成本刀具寿命两种,前者根据单件工时最少的目标确定,后者根据工序成本最低的目标确定。选择刀具寿命时可考虑如下几点:根据刀具复杂程度、制造和磨刀成本来选择。复杂和精度高的刀具寿命应选得比单刃刀具高些。 对于机夹可转位刀具,由于换刀时间短,为了充分发挥其切削性能,提高 生产效率,刀具寿命可选得低些,一般取15-30min。 对于装刀、换刀和调刀比较复杂的多刀机床、组合机床与自动化加工刀具,刀具寿命应选得高些,尤应保证刀具可靠性。 车间内某一工序的生产率限制了整个车间的生产率的提高时,该工序的刀具寿命要选得低些;当某工序单位时间内所分担到的全厂开支M较大时,刀具寿命也应选得低些。 大件精加工时,为保证至少完成一次走刀,避免切削时中途换刀,刀具寿命应按零件精度和表面粗糙度来确定。 三切削用量制定的步骤 背吃刀量的选择 进给量的选择 切削速度的确定 校验机床功率 四提高切削用量的途径 采用切削性能更好的新型刀具材料; 在保证工件机械性能的前提下,改善工件材料加工性; 改善冷却润滑条件; 改进刀具结构,提高刀具制造质量。 其中:ap背吃刀量,f进给量,Vc切削速度 Vc=πdn/1000(单位为m/min); d——工件或刀具上某一点的回转直径(mm) n——工件或刀具的转速(r/min) 由于切削刃上各点相对于工件的旋转半径不同,因而刀刃上各点的切削速度也不同,在计算时应取最大的切削速度。 外圆车削时计算待加工表面上的速度,内孔车削时计算已加工表面上的速度,钻削时计算钻头外径处的速度。 t1=(L÷nf)×(A÷ap)=L×A×π×d/(1000×v×f×ap) t1:切削工时 L:每次进给的行程长度(mm) 刀具直径种类参数切削参数粗加工半精加工精加工平面加工备注加工材料 E80R8飞刀普通机床Aa(切深) 1.2\\0.5刀长170一般构造用钢S55C,45# E80R8飞刀普通机床Ar(切宽)50\\32刀长170一般构造用钢S55C,45# E80R8飞刀普通机床F(mm/min)1800\\400刀长170一般构造用钢S55C,45# E80R8飞刀普通机床S(转/min)1000\\1000刀长170一般构造用钢S55C,45# E80R8飞刀普通机床寿命(min)480\\480刀长170一般构造用钢S55C,45# E80R8飞刀普通机床金属去除率刀长170一般构造用钢S55C,45# E80R8飞刀普通机床Aa(切深)1\\0.5刀长170调质钢(30 刀具直径种类参数切削参数底刃切削平面光刀侧刃切削高速切削刀具精度E32焊接式铣刀4a a(mm)不提倡底刃切削50 E32焊接式铣刀4a r(mm)不提倡底刃切削0.2 E32焊接式铣刀4F(mm/min)不提倡底刃切削180 E32焊接式铣刀4S(转/min)不提倡底刃切削400 E32焊接式铣刀4寿命(min)不提倡底刃切削\ E32焊接式铣刀4金属去除率不提倡底刃切削\ E25焊接式铣刀4a a(mm)不提倡底刃切削5050-0.005高速推荐侧刃切削E25焊接式铣刀4a r(mm)不提倡底刃切削0.20.2-0.005高速推荐侧刃切削E25焊接式铣刀4F(mm/min)不提倡底刃切削180220-0.005高速推荐侧刃切削E25焊接式铣刀4S(转/min)不提倡底刃切削4001200-0.005高速推荐侧刃切削E25焊接式铣刀4寿命(min)不提倡底刃切削\\-0.005高速推荐侧刃切削E25焊接式铣刀4金属去除率不提倡底刃切削\\-0.005高速推荐侧刃切削E20焊接式铣刀4a a(mm)不提倡底刃切削40/-0.005高速推荐侧刃切削E20焊接式铣刀4a r(mm)不提倡底刃切削0.2/-0.005高速推荐侧刃切削E20焊接式铣刀4F(mm/min)不提倡底刃切削180/-0.005高速推荐侧刃切削E20焊接式铣刀4S(转/min)不提倡底刃切削400/-0.005高速推荐侧刃切削E20焊接式铣刀4寿命(min)不提倡底刃切削\\-0.005高速推荐侧刃切削E20焊接式铣刀4金属去除率不提倡底刃切削\\-0.005高速推荐侧刃切削E15.5合金4a a(mm)不提倡底刃切削36/-0.05高速推荐侧刃切削E15.5合金4a r(mm)不提倡底刃切削0.15/-0.05高速推荐侧刃切削E15.5合金4F(mm/min)不提倡底刃切削180/-0.05高速推荐侧刃切削E15.5合金4S(转/min)不提倡底刃切削600/-0.05高速推荐侧刃切削E15.5合金4寿命(min)不提倡底刃切削\\-0.05高速推荐侧刃切削E15.5合金4金属去除率不提倡底刃切削\\-0.05高速推荐侧刃切削 E12合金2a a(mm)0.218\0--0.051 E12合金2a r(mm)120.2\0--0.051 E12合金2F(mm/min)1200400\0--0.051 E12合金2S(转/min)1500800\0--0.051 E12合金2寿命(min)5060\0--0.051 E12合金2金属去除率 2.88 1.44\0--0.051 E12高速涂层2aa(mm)0.218/-0.032--0.059 E12高速涂层2ar(mm)110.24/-0.032--0.059刀具几何参数
高速铣削刀具及切削参数的选择
刀具合理几何参数的选择
刀具合理几何参数的选择
切削参数的选择(精)
卧式数控车床刀具及切削参数选择
刀具切削参数控制
数控加工刀具及参数选择
机械加工工艺设计-铣床刀具及切削参数选择和工步时间计算
切削参数的选择
04 切削刀具-飞刀参数表【14表全】
02 切削刀具-铣刀参数表【14表全】