齿轮轴零件加工工艺设计说明书

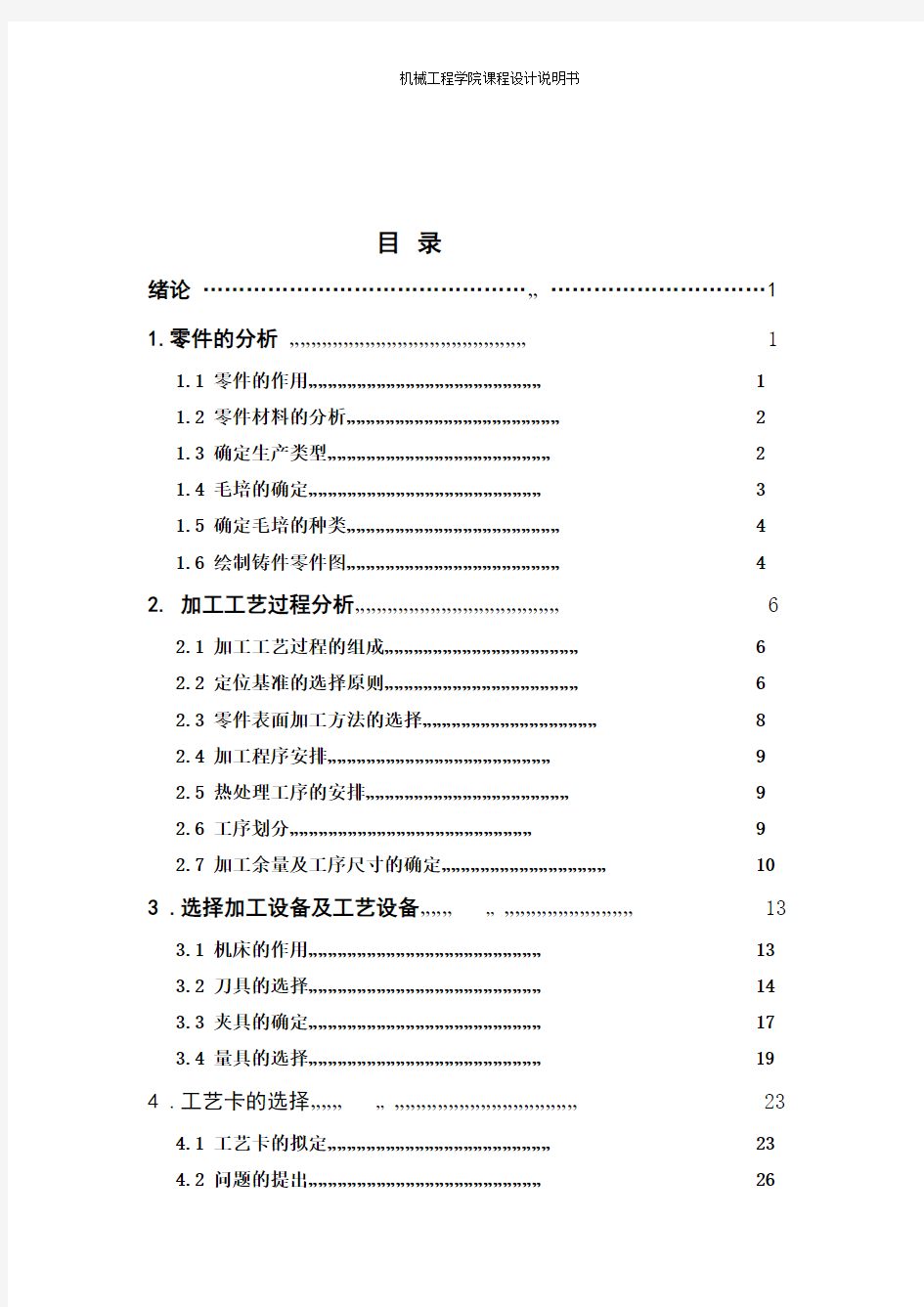
机械工程学院
机制专业课程设计说明书
设计题目:齿轮轴零件加工工艺设计说明书
专业:机械设计制造及其自动化
班级: 09级机制四班
姓名: 1111 学号 06123323299990 指导教师:王立华
2012年12 月30日
目录
绪论 (1)
1.零件的分析 (1)
1.1 零件的作用 (1)
1.2 零件材料的分析 (2)
1.3 确定生产类型 (2)
1.4 毛培的确定 (3)
1.5 确定毛培的种类 (4)
1.6 绘制铸件零件图 (4)
2. 加工工艺过程分析 (6)
2.1 加工工艺过程的组成 (6)
2.2 定位基准的选择原则 (6)
2.3 零件表面加工方法的选择 (8)
2.4 加工程序安排 (9)
2.5 热处理工序的安排 (9)
2.6 工序划分 (9)
2.7 加工余量及工序尺寸的确定 (10)
3 .选择加工设备及工艺设备 (13)
3.1 机床的作用 (13)
3.2 刀具的选择 (14)
3.3 夹具的确定 (17)
3.4 量具的选择 (19)
4 .工艺卡的选择 (23)
4.1 工艺卡的拟定 (23)
4.2 问题的提出 (26)
5 .设计总结 (29)
6 .参考文献 (30)
绪论
本课题的研究主要是加工工艺的注意点和改进的方法,通过总结零件的的加工,提高所加工工件的质量,完善产品,满足要求,提高经济效益和劳动生产率。
一般齿轮轴有两个支撑轴径,工作时通过轴径支撑在轴承上,这两个支撑轴径便是其装配基准,通常也是其他表面的设计基准,所以它的精度和表面质量要求较高。对于一些重要的轴,支撑轴除规定较高的尺寸精度外,通常还规定圆度、圆柱度以及两轴径之间的同轴度等形状精度要求等。对于其他工作轴径,如安装齿轮、带轮、螺母、轴套等零件的轴径,除了有本身的尺寸精度和表面粗糙度外,通常还要求其轴线与两支承轴径的公共线同轴,以保证轴上各运动部件的运动精度。
轴为支承转动零件并与之一起回转以传递运动、扭矩或弯矩的机械零件。一般为金属圆杆状,各段可以有不同的直径。机器中作回转运动的零件就装在轴上。根据轴线形状的不同,轴可以分为曲轴和直轴两类。根据轴的承载情况,又可分为:①转轴,工作时既承受弯矩又承受扭矩,是机械中最常见的轴,如各种减速器中的轴等;②心轴,用来支承转动零件只承受弯矩而不传递扭矩,有些心轴转动,如铁路车辆的轴等,有些心轴则不转动,如支承滑轮的轴等;③传动轴,主要用来传递扭矩而不承受弯矩,如起重机移动机构中的长光轴、汽车的驱动轴等。轴的材料主要采用碳素钢或合金钢,也可采用球墨铸铁或合金铸铁等。轴的工作能力一般取决于强度和刚度,转速高时还取决于振动稳定性。
本课题缩小到对齿轮轴的研究,本课题中的加工精度高,因此对技术也就会随之提高,包括尺寸精度、几何形状精度、相互位置精度及表面粗糙度等。使齿轮轴起到它的作用,更好的支撑传动部件、传递扭矩和承受载荷。从而使产品更加畅销,寿命延续更长,具有长远的意义,齿轮轴机件的损坏、磨损、变形以及失去动平衡,严重时会导致相关部件的损坏。
1.零件的分析
该零件是齿轮轴,它属于台阶轴类零件,由圆柱面、轴肩、螺纹、和键槽等组成。轴肩一般用来确定安装在轴上零件的轴向位置,各环槽的作用是使零件装配时有一个正确的位置,并使加工中磨削外圆或车螺纹时退刀方便;键槽用于安装键,以传递转矩;螺纹用于安装各种锁紧螺母和调整螺母。
1.1零件的作用
1.1.1 零件的作用
齿轮轴是转轴,,支撑作用,两端轴承支撑,中间安装轴承,一般键连接。用来支撑传动零部件,传递扭矩和承受载荷,以及保证装在主轴上的工件或刀具具有一定的回转精度。
1.1.2 零件的结构特点及技术要求
轴用轴承支承,与轴承配合的轴段称为轴颈。轴颈是轴的装配基准,它们的精度和表面质量一般要求较高,其技术要求一般根据轴的主要功用和工作条件制定,通常有以下几项:
(1) 尺寸精度
起支承作用的轴颈为了确定轴的位置,通常对其尺寸精度要求较高(IT5~IT7)。装配传动件的轴颈尺寸精度一般要求较低(IT6~IT9)。
(2) 几何形状精度
轴类零件的几何形状精度主要是指轴颈、外锥面、莫氏锥孔等的圆度、圆柱度等,一般应将其公差限制在尺寸公差范围内。对精度要求较高的内外圆表面,应在图纸上标注其允许偏差。
(3) 相互位置精度
轴类零件的位置精度要求主要是由轴在机械中的位置和功用决定的。通常应保证装配传动件的轴颈对支承轴颈的同轴度要求,否则会影响传动件(齿轮等)的传动精度,并产生噪声。普通精度的轴,其配合轴段对支承轴颈的径向跳动一般为0.01~0.03mm,高精度轴(如主轴)通常为0.001~0.005mm。
(4) 表面粗糙度
一般与传动件相配合的轴径表面粗糙度为Ra0.63~2.5μm,与轴承相配合的支承轴径的表面粗糙度为Ra0.16~0.63μm。
1.2零件材料分析
一般轴类零件常用45号钢,根据不同的工件条件采用不同的热处理规范(如正火、调质、淬火等),以获得一定的强度、韧度和耐磨性。淬火后表面硬度可达45~52HRC。
对中等精度而转速较高的轴类零件,可选用40Cr等合金钢。这类刚经调质和表面淬火处理后,具有较高的综合力学性能。
精度较高的轴,有时还用轴承钢GCr15和弹簧钢65MnT等材料,它们通过调质和表面淬火处理后,具有更高耐磨性和耐疲劳性能。表面硬度可达50~58HRC。
对于高转速、重载荷等条件下工作的轴,可选用20CrMnTi、20Mn2B、20Cr 等低碳合金或38CrMoAlA氮化钢。
精密机床的主轴(例如磨床砂轮轴、坐标镗床主轴)可选用38CrMoAl氮化钢,这种钢经调质和氮化后,不仅能获得较高的表面硬度,而且能保持较软的芯部,因此耐冲击韧性好,与渗碳淬火钢比较,它有热处理变形小、硬度更高的特点。
1.3确定生产类型
生产纲领是指某种产品(或零件)包括备品或废品在内的年产量。根据生产的产品特征,如产品的尺寸外形、质量等,以及生产纲领中年产量的不同,其生产可分为单件生产、成批生产和大量生产三种生产类型。
①单件生产单个地生产不同结构和尺寸的产品,并且很少重复。例如重型机器制造、专用设备制造及新产品试制等。
②成批生产一年中分批地制造相同的产品,制造过程有一定的重复性。每批制造的相同产品的数量称为批量。根据批量的大小,成批生产又可分为小批生产、中批生产和大批生产。机床制造属于成批生产。
各种生产类型的工艺过程特点,如下表1-1所示。
表1-1 各种生产类型的工艺过程特点
工艺过程特点生产类型
单件生产成批生产大量生产
工件的互换性基本上没有互换性,广泛用钳工
修配大部分有互换性,少
数用钳工修配
全部有互换性
毛坯制造方法及加工余量铸件用木模手工造型,锻造用自
由锻,毛坯精度低,加工余量大
部分采用金属模铸
造和模锻
铸件广泛采用金属模机械
造型,锻件广泛采用模锻
毛坯精度高,余量小
机床设备通用机床“机群式”排列
部分通用机床,部分
专用机床广泛采用高生产率的专用机床及自动线,机床按流
水线式排列
夹具
多用标准附件,极少采用夹具,
靠划线及试切法达到精度要求
广泛采用夹具,部分
靠划线法达到精度要求
广泛采用高生产率夹具,
靠夹具及调整法达到精度
要求
刀具与余量采用通用刀具和万能量具
较多采用专用刀具
和量具广泛采用高生产率的专用
刀量具
工人技术熟练一定的熟练程度
普通的操作工和技术较高
的调整工
工艺文件有简单的工艺路线卡
过程卡、工艺卡、关
键工序有工序卡过程卡、详细的工序卡、
检验卡
该零件轴为小批量生产。
1.4毛坯的确定
轴类毛坯常用圆棒料和锻件。大型轴或结构复杂的轴采用铸件,毛坯经过热处理后,可使金属内部纤维组织沿表面均匀分布,获得较高的硬度及较好的综合力学性能。
根据生产规模的不同,毛坯的锻造方式有自由锻和模锻两种。中小批量生产多采用自由锻,大批量生产时采用模锻。
1.5 确定毛坯种类
该齿轮轴材料为45号钢,因其属于一般齿轮轴,故选45号钢可满足其要求。本例齿轮轴属于中、小齿轮轴,并且各外圆直径尺寸相差不大。由m=3,z=9根据公式d=mz可知d=27,故选择 40mm的热轧圆钢作毛坯。
1.6 绘制铸件零件图
零件图如图1-1所示。
设计目的:
能对零件进行加工工艺分析,设计该零件的加工工艺与加工路线,及所用的刀具,夹具。
附加工图样:
如图所示为主动齿轮轴图样。m=3,z=9。
其余
图1-1 主动齿轮轴
2. 加工工艺过程分析
机器的生产过程是指将原材料转变为成品之间的所有劳动和。为了降低生产成本和便于生产组织,许多机器不一定完全有一个工厂单独生产,而常常由很多专业化的工厂生产不同的零、部件来共同完成。
在生产中,凡是改变生产对象的形状、尺寸、相对位置和性质,使其成为成品或半成品的过程称为工艺过程。如毛坯制造工艺过程、机械加工工艺过程、惹处理工艺过程及装配工艺过程等。
在许多情况下,工艺过程不是一成不变的,但在一定的生产条件下,应尽量使工艺过程制定得最为合理,最符合生产实际。
轴类零件的加工是练习车削技能的最基本也是最重要的项目,但最后完工工件的质量总是很不理想,主要是对轴类零件的工艺分析规程制定不够合理。轴类零件中工艺规程的制定,直接关系到工件质量,劳动生产率和经济效益。
2.1 加工工艺过程的组成
加工工艺过程的组成:
①工序工序是组成工艺过程的基本单元。工序是指一个(或一组)工人,在一个工作地(或一台设备)上,对同一个(或同时对几个)工件所连续完成的那一部分工艺过程。划分工序的主要依据是工作地点是否改变及加工是否连续完成。
②工步工步是指加工表面不变、加工工具不变和切削用量(转速及进给量)不变的情况下所连续完成的那一部分工序。
③走刀在一个工步中,若加工余量较大,可分几次切削,每次切削称为一次走刀。
④安装工件一次装夹后所完成的那一部分工序称为安装。一道工序可以有一次安装,也可以有几次安装。
⑤工位在一次安装中,工件在机床上所占的每个位置上所完成的那一部分工序称为工位。
2.2定位基准的选择原则
2.2.1 基准的概念
零件是由若干个要素(点、线、面)组成,各要素之间都有一定的尺寸和位置公差要求。用来确定生产对象上几何要素间的几何关系所依据的那些点、线、面称为基准。
根据零件的用途不同,可分为两类:设计基准和工艺基准。
(1)设计基准
在零件上用来确定其他点、线、面位置的基准称为设计基准。如图2-1所示轴套零件,其外圆和孔的设计基准为零件的轴心线;端面B、C的设计基准是端面A;φ25h6外圆径向圆跳动的设计基准是轴孔D的轴心线。而对于尺寸35,端面A和端面C互为基准,即端面A是端面C的设计基准,端面C也是端面A 的设计基准。
图2-1 轴套
(2)工艺基准
在加工和装配过程中使用的基准称为工艺基准。按其用途又可分为定位基准、测量基准和装配基准。
①定位基准使工件在机床和夹具中占有正确的加工位置所采用的基准。作为定位基
准的点、线、面可以使实际存在的,也可以是假想的,如外圆和内孔轴线、对称平面等。
②测量基准测量时所采用的基准,即用来确定被测量尺寸、形状和位置的基准。如图2-1所示,零件以内孔与心轴配合测量外圆φ25h6的径向跳动,则内孔φ15H7轴线是外圆的测量基准;用卡尺测量尺寸10和35时,端面A是端面B、C的测量基准。
③装配基准装配时用来确定零件在部件或产品(总成)中位置的精度。如箱体类零件的底平面、主轴的主轴颈等。
2.2.2 定位基准的选择
选择定位基准是制定工艺规程的一个十分重要的问题。在第一道工序中,只能使用工件上未加工的毛坯表面来定位,这种定位基准称为粗基准。在以后的工序中,可以采用经过加工的表面来定位,这种定位基准称为精基准。
(1)粗基准的选择
粗基准的选择如下:
①如果必须首先保证工件上加工表面与不加工表面与不加工表面之间的位置要求,应以不加工表面作为粗基准。如果在工件上有很多不需加工的表面,则应以其中与加工面的位置精度要求较高的表面作粗基准。
②如果必须首先保证工件某重要表面的余量均匀,应选择该表面粗基准。
③选作粗基准的表面,应平整,没有浇、没有浇、冒口或飞边等缺陷,以便定位可靠。
④粗基准一般只能使用一次,特别是主要定位基准,以大的位置误差。(2)精基准的选择
①“基准重合”原则
为了较容易地获得加工表面对其设计基准的相对位置精度要求,应选择加工表面的设计基准为其定位基准。这一原则称为基准重合原则。
②“基准统一”原则
当工件以某一组精基准定位可以比较方便地加工其它表面时,应尽可能在多数工序中采用此组精基准定位,这就是“基准统一”原则。例如:轴类零件大多数工序都以中心孔为定位基准;齿轮的齿坯和齿形加工多采用齿轮内孔及端面为定位基准。
③“互为基准、反复加工”原则
为了获得均匀的加工余量或较高的位置精度,可采用互为基准反复加工的原则。例如加工精密齿轮时,先以内孔定位加工齿形面,齿面淬硬后需进行磨齿。因齿面淬硬层较薄,所以要求磨削余量小而均匀。
④“自为基准”原则
有些精加工工序要求加工余量小而均匀,以保证加工质量和提高生产率,这时就以加工面本身作为精基准,称为“自为基准”原则。例如磨削床身导轨面时,就以床身导轨面作为定位基准。
⑤所选用的定位基准,应能保证工件的装夹稳定可靠、夹具结构简单、操作方便。
以上原则是实际使用时常常会相互矛盾,应用时应结合具体的生产条件和生产类型进行分析比较,找出主要矛盾,灵活运用这些原则。
根据以上原则,齿轮轴的主要加工表面是齿轮面和轴的外圆表面,同轴度要求较高,所以以齿轮轴的左端作为基准面。
2.2.3 定位基准的确定
合理的选择定位基准,对于保证零件的尺寸和位置精度有着决定性的作用。由于该齿轮轴没有径向圆跳动和端面圆跳动的要求,它又是实心轴,所以应选择两端中心孔为基准,采用双顶尖装夹方法,以保证零件的技术要求。
轴类零件的定位基准,最常用的是两中心孔。因为轴类零件各外圆表面、螺纹表面的同轴度及端面对轴线的垂直度是相互位置精度的主要项目,而这些表面的设计基准一般都是轴的中心线,采用两中心孔定位就能符合基准重合原则。而且由于多数工序都采用中心孔作为定位基面,能最大限度地加工出多个外圆和端面,这也符合基准统一原则。
但下列情况不能用两中心孔作为定位基面:
(1)粗加工外圆时,为提高工件刚度,则采用轴外圆表面为定位基面,或以外圆和中心孔同时作为定位基面,即一夹一顶。
(2)当轴为通孔零件时,在加工过程中,作为定位基面的中心孔因钻出通孔而消失。为了在通孔加工后还能用中心孔作为定位基面,工艺上常采用以下三种方法:
①当中心通孔直径较小时,可直接在孔口倒出宽度不大于2mm的60°内锥面来代替中心孔;
②当轴有圆柱孔时,可采用图2-2(a)所示的锥堵,取1:500锥度;当轴孔锥度较小时,取锥堵锥度与工件两端定位孔锥度相同;
③当轴通孔的锥度较大时,可采用带锥堵的心轴,简称锥堵心轴,如图2-2(b)所示。
使用锥堵或锥堵心轴时应注意,一般中途不得更换或拆卸,直到精加工完各处加工面,不再使用中心孔时方能拆卸。
(a)锥堵
工件
(b)锥堵心轴
图2-2 锥堵和锥堵心轴
2.3 零件表面加工方法的选择
加工方法的选择原则是保证加工质量和生产率与经济性。为了正确选择加工方法,应了解各种加工方法的特点和掌握加工表面精度以及表面粗糙度的概念。
在选择加工方法时,一般是根据经验或查表来确定,在根据实际不同情况或工艺实验进行修改。在查表时,满足同样要求的加工方法有很多种,所以选择加工方法时要考虑以下因素:
(1)选择相应能获得表面精度的加工方法。
(2)工件材料的性质。
(3)工件的结构形状和尺寸大小。
(4)结合生产类型考虑生产率与经济性。
(5)现有生产条件。
为了正确选择加工方法,应了解各种加工方法的特点和掌握加工精度以及表面粗糙度的概念。
表面精度是指在正常的加工条件下所能保证的表面精度;加工精度是指在正常的加工条件下所能保证的加工精度。加工过程中影响精度的因素很多,每种加工方法在不同的工作条件下所能达到的精度是不同的。例如:在一定的设备条件下,操作精细、选择较低的进给量和切削深度,就能获得较高的加工精度和较细的表面粗糙度。但是这必然会使生产率降低,生产成本增加,反之,提高生产率,虽然成本降低,但会增大加工误差,降低加工精度。
齿轮轴零件的加工面有外圆、孔、螺纹、退刀槽、倒角等,材料为45号钢。外圆面公差等级为IT7~IT8,表面粗糙度Ra1.6~3.2μm,采用粗车---半精车---精车保证精度要求。
端面:本零件的端面为回转体端面,尺寸精度要求不高。表面粗糙度为Ra1.6μm的端面粗车和半精车即可。
多数外圆柱面有1×45°倒角和1.5×1、2×1退刀槽要求。
2.4 加工工序安排
根据零件的功用和技术要求,先将零件的主要表面分开,然后着重考虑主要表面的加工顺序。安排加工顺序是:加工精基准---粗加工主要表面---半精加工主要表面---精加工主要表面。次要表面的加工穿插在各阶段之间进行,由于次要表面加工精度不高,一般在粗、半精加工阶段即可完成,但对于那些同主要表面有密切关系的表面,如退刀槽、螺纹等,通常置于主要表面精加工之后完成,以便保证它们的位置精度。
加工顺序安排的一般原则:
①基面先行原则。
②先粗后精原则。
③先主后次原则。
④先面后孔原则。
零件齿轮轴除了应遵循加工顺序安排的一般原则,还应注意以下三个方面:(1)外圆表面加工顺序应为,先加工大直径外圆,然后再加工小直径外圆,以免一开始就降低了工件的刚度。
(2)齿轮轴上的退刀槽、螺纹齿等表面的加工应在外圆精车之后,否则在精车外圆时产生断续切削,影响车削精度,也易损坏刀具。
(3)轴上的螺纹一般有较高的精度,如安排在局部淬火之前进行加工,则淬火后产生的变形会影响螺纹的精度,因此螺纹加工宜安排在工件局部淬火之后。
2.5热处理工序的安排
轴的热处理要根据其材料和使用要求确定。对于齿轮轴,正火、调质和表面淬火用的比较多。
45号钢经锻造后需要正火处理,以消除锻造产生的应力,改善切削性能。粗加工阶段完成后安排调质处理,一是可以提高材料的力学性能,二是作为表面淬火准备了良好的金相组织,确定表面淬火的质量。对于轴上的支撑轴颈、齿面、锥台面这些重要且在工作中经常摩擦的表面,为提高其耐磨性均需表面淬火处理,表面淬火安排在精加工前进行,以经过精加工去除淬火过程中产生的氧化皮,修正淬火变形。
2.6 工序的划分
在安排零件的工艺规程时,还要解决工序的集中与分散问题。所谓工序集中,就是在一台机床上尽可能多地加工工件的几个表面,在批量较大时,常采用多轴、多面、多工位机床和复合刀具等方法来实现工序集中,从而有效地提高生产率。加工中心和柔性生产线(FMS)是工序集中的极端情况。在单件小批量生产中,工序集中是在通用机床和数控机床上进行的。工序分散则相反,整个工艺过程的工序数目较多。工艺线长,而每道工序所完成的加工内容较少,一般适用于加工批量大的场合。
工序集中的特点:
①减少了设备的数量,减少了操作工的数量和生产面积。
②减少了工序数目,减少了运输工作量,简化了生产计划工作,缩短了生产周期。
③减少了工件的装夹次数,不仅利于提高生产率,而且在一次装夹下加工
了许多面,也有利于保证这些被加工面得位置精度。
④因为采用的专用设备和专用工艺装备数量多而复杂,因此机床和工艺装备的调整维修工作量大。
而工序分散的特点是:
①采用比较简单的机床和工艺装备,调整容易。
②对工人的技术要求低,仅需对其进行短时间的培训即可上岗。
③生产设备工作量少,产品更新换代容易。
④设备及操作工数量较多,所需工作面积大。
单件小批量生产一般采用工序集中的方式,而大批量生产既可以集中也可以分散,应根据具体情况进行分析,随着加工中心的快速发展,采用工序集中的生产方式是发展的必然。
2.7 加工余量及工序尺寸的确定
2.7.1 加工余量的概念
在从工件毛坯加工成成品的过程中,毛坯尺寸与零件图的设计尺寸之差为加工总余量,即为某被加工表面上切除的金属的总厚度。而相邻两个工序的工序尺寸之差,即被后一道工序所切除的金属层厚度就是工序余量。
2.7.2 加工余量的确定方法
加工余量的确定方法有三种。
①查表法根据生产实践和试验研究,已将毛坯余量和各种工序的工序余
量数据汇编
成手册。在确定加工余量时,可从手册中查的所需数据,然后结合本厂的实际情况进行适当修正。该方法目前应用最为广泛。
②经验估计法该法是根据实践来确定加工余量的。一般而言,为防止加工余量不足而产生废品,往往估计的数量都偏大,所以该法只适用于单件、小批量生产。
③分析计算法是根据加工余量计算公式和一定的试验资料,通过计算确定加工余量的一种方法。采用这种方法确定的加工余量比较合理,但必须有比较全面可靠的试验资料及先进的计算手段,该法在生产中应用很少。
根据零件“齿轮轴”的使用性能、劳动强度确定采用棒料,材料45号钢,结合加工工艺分析,分别确定加工余量、工序尺寸及主尺寸如下:(其中2Z为直径上的加工余量)
①外圆表面轮廓只需粗车、半精车、精车可达到要求。外圆加工余量的确定:外圆加工直径余量(mm),粗车1.5~4 mm,半精车0.5~2.5 mm。
粗车:加工余量2Z=3mm;半精车:加工余量2Z=1.5 mm。
②外圆表面轴向长度方向的加工余量:总长余量2Z=5mm。
③齿轮齿数为9,模数为3的齿轮精度为IT6,全齿高h=(2ha*+c*)m=6.75 mm。
3. 选择加工设备及工艺设备
3.1 各机床的作用
3.1.1 车床的作用
在金属切削机床中,普通车床是使用广泛的一种,它适用于加工各类轴类、套筒类和盘类零件中的回转表面,能完成钻中心孔、车外圆、车端面、钻孔、镗孔、铰孔及切断、车螺纹、滚花、车锥体、车特形表面攻丝等。
车床种类有:
(1)普通车床普通车床的加工对象广,主轴转速和进给量的调整范围大,能加工工件的内外表面、端面和内外螺纹。这种车床主要由工人手工操作,生产效率低,适用于单件、小批生产和修配车间。如CA6140、CA6240、CA6132、CA6232等。
(2)转塔车床和回转车床转塔车床和回转车床具有能装多把刀具的转塔刀架或回轮刀架,能在工件的一次装夹中由工人依次使用不同刀具完成多种工序,适用于成批生产。
(3)自动车床自动车床能按一定程序自动完成中小型工件的多工序加工,能自动上下料,重复加工一批同样的工件,适用于大批、大量生产。
(4)多刀半自动车床多刀半自动车床有单轴、多轴、卧式和立式之分。单轴卧式的布局形式与普通车床相似,但两组刀架分别装在主轴的前后或上下,用于加工盘、环和轴类工件,其生产率比普通车床提高3~5倍。
(5)仿形车床仿形车床能仿照样板或样件的形状尺寸,自动完成工件的加工循环,适用于形状较复杂的工件的小批和成批生产,生产率比普通车床高10~15倍。有多刀架、多轴、卡盘式、立式等类型。
(6)立式车床立式车床的主轴垂直于水平面,工件装夹在水平的回转工作台上,刀架在横梁或立柱上移动。适用于加工较大、较重、难于在普通车床上安装的工件,一般分为单柱和双柱两大类。
(7)铲齿车床铲齿车床在车削的同时,刀架周期地作径向往复运动,用于铲车铣刀、滚刀等的成形齿面。通常带有铲磨附件,由单独电动机驱动的小砂轮铲磨齿面。
(8)专门车床专门车床是用于加工某类工件的特定表面的车床,如曲轴车床、凸轮轴车床、车轮车床、车轴车床、轧辊车床和钢锭车床等。联合车床主要用于车削加工,但附加一些特殊部件和附件后,还可进行镗、铣、钻、插、磨等加工,具有“一机多能”的特点,适用于工程车、船舶或移动修理站上的修配工作。
该设计中主要运用的车床为CA6140型卧式车床。
3.1.2 铣床的作用
铣床类机床是平面加工的主要机床之一,其主要工件是使用铣刀铣削平面或沟槽。
铣床的种类有以下三种分类方式:
(一)按其结构分:
(1)台式铣床:小型的用于铣削仪器、仪表等小型零件的铣床。
(2)悬臂式铣床:铣头装在悬臂上的铣床,床身水平布置,悬臂通常可沿床身一侧立柱导轨作垂直移动,铣头沿悬臂导轨移动。
(3)滑枕式铣床:主轴装在滑枕上的铣床,床身水平布置,滑枕可沿滑鞍导轨作横向移动,滑鞍可沿立柱导轨作垂直移动。
(4)龙门式铣床:床身水平布置,其两侧的立柱和连接梁构成门架的铣床。铣头装在横梁和立柱上,可沿其导轨移动。通常横梁可沿立柱导轨垂向移动,工作台可沿床身导轨纵向移动。用于大件加工。
(5)平面铣床:用于铣削平面和成型面的铣床,床身水平布置,通常工作台沿床身导轨纵向移动,主轴可轴向移动。它结构简单,生产效率高。
(6)仿形铣床:对工件进行仿形加工的铣床。一般用于加工复杂形状工件。
(7)升降台铣床:具有可沿床身导轨垂直移动的升降台的铣床,通常安装在升降台上的工作台和滑鞍可分别作纵向、横向移动。
(8)摇臂铣床:摇臂装在床身顶部,铣头装在摇臂一端,摇臂可在水平面内回转和移动,铣头能在摇臂的端面上回转一定角度的铣床。
(9)床身式铣床:工作台不能升降,可沿床身导轨作纵向移动,铣头或立柱可作垂直移动的铣床。
(10)专用铣床:例如工具铣床:用于铣削工具模具的铣床,加工精度高,加工形状复杂。
(二)按布局形式和适用范围分,主要有升降台铣床、龙门铣床、单柱铣床和单臂铣床、仪表铣床、工具铣床等。
升降台铣床有万能式、卧式和立式几种,主要用于加工中小型零件,应用最广;龙门铣床包括龙门铣镗床、龙门铣刨床和双柱铣床,均用于加工大型零件;单柱铣床的水平铣头可沿立柱导轨移动,工作台作纵向进给;单臂铣床的立铣头可沿悬臂导轨水平移动,悬臂也可沿立柱导轨调整高度。单柱铣床和单臂铣床均用于加工大型零件。
仪表铣床是一种小型的升降台铣床,用于加工仪器仪表和其他小型零件;工具铣床主要用于模具和工具制造,配有立铣头、万能角度工作台和插头等多种附
件,还可进行钻削、镗削和插削等加工。其他铣床还有键槽铣床、凸轮铣床、曲轴铣床、轧辊轴颈铣床和方钢锭铣床等,它们都是为加工相应的工件而制造的专用铣床。
(三)按控制方式分,铣床又可分为仿形铣床、程序控制铣床和数控铣床等。
该设计中在加工10×5的键槽时,用到立式键槽铣床。
3.1.3 磨床的作用
磨床系指用磨具或磨料加工工件各种表面的机床。一般用于对零件淬硬表面做磨削加工。通常,磨具旋转为主运动,工件或磨具的移动为进给运动,其应用广泛、加工精度高、表面粗糙度Ra值小,磨床可分为十余种:
(1)外圆磨床:是普通型的基型系列,主要用于磨削圆柱形和圆锥形外表面的磨床。
(2)内圆磨床:是普通型的基型系列,主要用于磨削圆柱形和圆锥形内表面的磨床。
(3)座标磨床:具有精密座标定位装置的内圆磨床。
(4)无心磨床:工件采用无心夹持,一般支承在导轮和托架之间,由导轮驱动工件旋转,
主要用于磨削圆柱形表面的磨床。
(5)平面磨床:主要用于磨削工件平面的磨床。
(6)砂带磨床:用快速运动的砂带进行磨削的磨床。
(7)珩磨机:用于珩磨工件各种表面的磨床。
(8)研磨机:用于研磨工件平面或圆柱形内,外表面的磨床。
(9)导轨磨床:主要用于磨削机床导轨面的磨床。
(10)工具磨床:用于磨削工具的磨床。
(11)多用磨床:用于磨削圆柱、圆锥形内、外表面或平面,并能用随动装置及附件磨削多种工件的磨床。
(12)专用磨床:从事对某类零件进行磨削的专用机床。按其加工对象又可分为:花键轴磨床、曲轴磨床、凸轮磨床、齿轮磨床、螺纹磨床、曲线磨床等。
该设计中为了达到零件的尺寸精度,最后需要用磨床磨削外圆,主要用的是外圆磨床。
3.1.4 零件加工中各机床的确定
零件加工使用的机床为:
(1)工序001为下料采用锯床
(2)工序002~007为车削采用CA6140型卧式车床
(3)工序008为铣削采用立式铣床或键槽铣床
(4)工序009为修研中心孔采用CA6140型卧式车床
(5)工序010为磨外圆采用外圆磨床
3.2 刀具的选择
3.2.1 刀具材料的确定
刀具材料从碳素工具钢的淬火,高速钢的问世,直到今天硬质合金和超硬材料的出现,都是随着机床主轴转速,功率增大,刚性增强等而逐步发展起来的,其目的是要保证被加工件的精度
和质量的前提下,提高单位时间的切削量。
由于刀具材料的切削性能直接影响生产效率、工件的加工精度和表面质量,所以正确选择刀具材料是加工工艺的一个重要部分,刀具应具有高刚度、足够的强度和韧度、高耐磨性、良好的导热性、良好的工艺性和经济性、抗粘接性、化学稳定性等。刀具的选择取决于各工序的加工方法及所用机床的性能。刀具材料的硬度必须高于工件材料的硬度,常用的车刀材料为高速钢和硬质合金两种。
刀具要具有以下几点要求:
①良好的切削性能。
②精度高。
③可靠性高。
④用度高。
⑤断屑及性能好。
⑥刀具的长度在满足使用要求的前提下尽可能的短。
3.2.2 刀具的分类
生产中所使用的刀具种类很多,按加工方式和具体用途分为车刀、孔加工刀具、铣刀、拉刀、
螺纹刀具、齿轮刀具、传动线及数控机床刀具和磨具等几大类型。
刀具分类:
(1)按所用材料分为高速钢刀具、硬质合金刀具、陶瓷刀具、立方氮化硼刀具和金刚石刀具等。
(2)按结构分为整体刀具、镶片刀具、机夹刀具和复合刀具等。
(3)按是否标准化分为标准刀具和非标准刀具等。
车刀按用途可分为外圆车刀、端面车刀、切断刀、成形车刀、螺纹车刀和车孔刀等。
3.2.3 常用车刀刀具的用途
车削的特点:
①车削加工是指工件旋转作主运动,车刀作进给运动的切削加工方法。车削加工应用广泛,能很好适应工件材料、结构、精度、表面粗糙度及生产批量的变化。
②车削加工一般是等截面(即切削宽度、切削厚度均不变,其中粗车时毛坯余量的不均匀可忽略不计)的连续切削,因此,切削了变化小,切削过程平稳,可进行高速切削和强力切削,生产率高。
③车削采用的车刀一般为单刃刀,其结构简单、制造容易、刃磨方便、安装方便。
④车削加工尺寸精度范围一般在IT12~IT7之间,表面粗糙度值为Ra0.8~12.5μm,适于工件的粗加工、半精加工和精加工。
1.一般使用之车刀尖型式有下列几种:
(1)粗车刀主要是用来切削大量且多余部份使工作物直径接近需要的尺寸。粗车时表面光度不重要,因此车刀尖可研磨成尖锐的刀峰,但是刀峰通常要有微小的圆度以避免断裂。
(2)精车刀此刀刃可用油石砺光,以便车出非常圆滑的表面光度,一般来说精车刀之圆鼻比粗车刀大。
(3)圆鼻车刀可适用许多不同型式的工作是属于常用车刀,磨平顶面时可左右车削也可用来车削黄铜。此车刀也可在肩角上形成圆弧面,也可当精车刀来使用。
(4)切断车刀只用端部切削工作物,此车刀可用来切断材料及车度沟槽。
(5)螺丝车刀(牙刀) 用于车削螺杆或螺帽,依螺纹的形式分60度,或55度V型牙刀,29度梯形牙刀、方形牙刀。
(6)搪孔车刀用以车削钻过或铸出的孔。达至光制尺寸或真直孔面为目的。
(7)侧面车刀或侧车刀用来车削工作物端面,右侧车刀通常用在精车轴的未端,左侧车则用来精车肩部的左侧面。
2.因工件之加工方式不同而采用不同的刀刃外形,一般可区分为:
(1)右手车刀由右向左,车削工件外径。
(2)左手车刀由左向右,车削工件外径。
(3)圆鼻车刀刀刃为圆弧形,可以左右方向车削,适合圆角或曲面之车削。
(4)右侧车刀车削右侧端面。
(5)左侧车刀车削左侧端面。
(6)切断刀用于切断或切槽。
典型轴类零件的数控加工工艺设计(doc 29页)
典型轴类零件的数控加工工艺设计(doc 29页)
摘要 数控技术是用数字信息对机械运动和工作过程进行控制的技术,数控装备是以数控技术为代表的新技术对传统制造产业和新兴制造的渗透形成的机电一体化产品,即所谓的数字化装备。 本次设计就是进行数控加工工艺设计典型轴类零件,主要侧重于该零件的数控加工工艺和编程,包括完成该零件的工艺规程,主要工序工装设计,并绘制零件图、夹具图等。 通过本次毕业设计,对典型轴类零件的设计又有了深的认识。从而达到了巩固、扩大、深化所学知识的目的,培养和提高了综合分析问题和解决问题的能力以及培养了科学的研究和创新能力。 关键词:数控技术典型轴类零件加工工艺毕业设计
1.引言 数控技术集传统的机械制造技术、计算机技术、成组技术与现代控制技术、传感检测技术、信息处理技术、网络通讯技术、液压气动技术、光机电技术于一体,是现代先进制造技术的基础和核心。数控车床己经成为现代企业的必需品。随着数控技术的不断成熟和发展及市场日益繁荣,其竞争也越来越激烈,人们对数控车床选择也有了更加广阔的范围,对数控机床技术的掌握也越来越高。随着社会经济的快速发展,人们对生活用品的要求也越来越高,企业对生产效率也有相应的提高。数控机床的出现实现了广大人们的这一愿望。数控车削加工工艺是实现产品设计、保证产品的质量、保证零件的精度,节约能源、降低消耗的重要手段。是企业进行生产准备、计划调度、加工操作、安全生产、技术检测和健全劳动组织的重要依据。也是企业对高品质、高品种、高水平,加速产品更新,提高经济效益的技术保证。这不但满足了广大消费者的目的,即实现了产品多样化、产品高质量、更新速度快的要求,同时推动了企业的快速发展,提高了企业的生产效率。 数控工艺规程的编制是直接指导产品或零件制造工艺过程和操作方 法的工艺文件,它将直接影响企业产品质量、效益、竞争能力。本文通过对典型轴类零件数控加工工艺的分析,对零件进行编程加工,给出了对于典型零件数控加工工艺分析的方法,对于提高制造质量、实际生产具有一定的意义。根据数控机床的特点,针对具体的零件,进行了工艺方案的分析,工装方案的确定,刀具和切削用量的选择,确定加工顺序和加工路线,数控加工程序编制。通过整个工艺的过程的制定,充分体现了数控设备在保证加工精度,加工效率,简化工序等方面的优势。 本人以严谨务实的认真态度进行了此次设计,但由于知识水平与实际经验有限。在设计中会出现一些错误、缺点和疏漏,诚请各位评审老师提出批评和指正。
轴类零件的加工工艺资料
轴类零件的加工工艺 绪论 本课题主要研究轴类零件加工过程,加工工艺注意点及改进的方法,通过总结非标件的加工以及典型半成品轴类零件的加工实例来加以说明。现在许多制造最终成品的工厂为了提高机器的某些性能或者降低成本,需要找机械加工厂定做的,常常会因为设备、技术或者工艺规程制定的不是很好,加工出来的部件无法满足使用要求,所以需要一次次的总结,改进加工工艺,从而完善产品。经过总结了生产上出现的问题,写下了这篇论文。 轴类零件是机器中经常遇到的典型零件之一。它在机械中主要用于支承齿轮、带轮、凸轮以及连杆等传动件,以传递扭矩。按结构形式不同,轴可以分为阶梯轴、锥度心轴、光轴、空心轴、曲轴、凸轮轴、偏心轴、各种丝杠等。 图轴的种类 a)光轴 b)空心轴 c)半轴 d)阶梯轴 e)花键轴 f)十字轴 g)偏心轴 h)曲轴 i) 凸轮轴 1 轴类零件的功用、结构特点 轴类零件是机器中经常遇到的典型零件之一。它在机械中主要用于支承齿轮、带轮、凸轮以及连杆等传动件,以传递扭矩。按结构形式不同,轴可以分为阶梯轴、锥度心轴、光轴、空心轴、曲轴、凸轮轴、偏心轴、各种丝杠等。它主要用来支承传动零部件,传递扭矩
和承受载荷。轴类零件是旋转体零件,其长度大于直径,一般由同心轴的外圆柱面、圆锥面、内孔和螺纹及相应的端面所组成。根据结构形状的不同,轴类零件可分为光轴、阶梯轴、空心轴和曲轴等。 轴的长径比小于5的称为短轴,大于20的称为细长轴,大多数轴介于两者之间。 1.1轴类零件的毛坯和材料 1.1.1轴类零件的毛坯 轴类毛坯常用圆棒料和锻件;大型轴或结构复杂的轴采用铸件。毛坯经过加热锻造后,可使金属内部纤维组织沿表面均匀分布,获得较高的抗拉、抗弯及抗扭强度。 根据生产规模的不同,毛坯的锻造方式有自由锻和模锻两种。中小批生产多采用自由锻,大批大量生产时采用模锻。 1.1.2轴类零件的材料 轴类零件材料常用45钢,精度较高的轴可选用40Cr、轴承钢GCr15、弹簧钢65Mn,也可选用球墨铸铁;对高速、重载的轴,选用20Mn2B、20Cr等低碳合金钢或38CrMoAl氮化钢。 45钢是轴类零件的常用材料,它价格便宜经过调质(或正火)后,可得到较好的切削性能,而且能获得较高的强度和韧性等综合机械性能,淬火后表面硬度可达45~52HRC。 40Cr等合金结构钢适用于中等精度而转速较高的轴类零件,这类钢经调质和淬火后,具有较好的综合机械性能。 轴承钢GCr15和弹簧钢65Mn,经调质和表面高频淬火后,表面硬度可达50~58HRC,并具有较高的耐疲劳性能和较好的耐磨性能,可制造较高精度的轴。 精密机床的主轴(例如磨床砂轮轴、坐标镗床主轴)可选用38CrMoAIA氮化钢。这种钢经调质和表面氮化后,不仅能获得很高的表面硬度,而且能保持较软的芯部,因此耐冲击韧性好。与渗碳淬火钢比较,它有热处理变形很小,硬度更高的特性。 2 轴类零件一般加工要求及方法 2.1 轴类零件加工工艺规程注意点
齿轮轴加工工艺规程设计
课程设计 齿轮轴加工工艺规程设计 教学单位: 机电工程学院 专业: 机械设计制造及其自动化 班级: 机械09C(本) 学号: ………… 学生姓名: XXX 指导教师: XXX(讲师) 完成时间: 2013年5月5日
电子科技大学中山学院机电工程学院
摘要 机械加工工艺规程设计能力是从事机械制造专业的科研、工程技术人员必须具备的基本素质之一。机械加工工艺规程设计作为高等工科院校教学的基本科目,在实践中占有极其重要的地位,工艺流程设计在加深对专业课程基本理论的理解和加强对解决工程实际问题的能力培养方面所发挥的作用是显而易见的。 本设计是齿轮轴的加工工艺规程设计,其结构虽然规则,但是精度要求比较高,所以工艺要求比较复杂。需要粗车、精车、铣车、磨销,其中精车是加工关键。车床加工工艺是以机械制造中的工艺基本理论为基础,结合车床的特点,综合运用多方面的知识解决车床加工过程中面临的工艺问题。 工艺规程是保证机械产品高质量、低成本的一种重要的工艺依据,工艺规程设计在机械加工中就显得更为突出,因此中小型零件加工的规程设计常被选作毕业设计的主要内容之一。 关键字:工艺规程;齿轮轴 I
目录 1绪论 (1) 1.1引言 (1) 1.2 设计的内容及要求 (1) 2 零件分析 (3) 2.1齿轮轴的概述 (3) 2.2零件的结构工艺分析 (4) 2.3零件的校核 (5) 3齿轮轴的工艺规程分析 (10) 3.1毛坯的选择 (10) 3.2制定工艺路线 (11) 3.2.1 基本加方案 (11) 3.2.2 工艺路线的设定 (11) 3.2.3 加工工艺过程内容 (12) 3.3基准的选择 (13) 3.3.1 粗基准的选择 (13) 3.3.2 精基准的选择 (14) 3.4 机械加工工艺过程分析 (15) 3.4.1 加工阶段的划分及划分加工阶段的原因 (15) 3.4.2 加工顺序的安排 (15) 3.4.3 机床的选择 (16) 3.5 切削用量 (16) 3.5.1 粗加工时切削用量的选择原则 (16) 3.5.2 精加工时切削用量的选择原则 (17) 3.5.3 选择切削用量 (18) 3.6 确定加工余量、工序尺寸及公差 (19) 3.7基本工时 (20) 4 结束语 (22) 参考文献 (23) 致谢 (24) II
数控轴类零件加工工艺的设计
山东华宇职业技术学 院 毕业论文 题目:数控轴类零件加工工艺设计 姓名:高攀 所在学院:山东华宇职业技术学院 专业班级:机械制造及自动化 学号: 20082410127 指导教师:马合 日期:2010.10.25
摘要 随着数控技术的不断发展和应用领域的扩大,数控加工技术对国计民生的一些重要行业(IT、汽车、轻工、医疗等)的发展起着越来越重要的作用,因为效率、质量是先进制造技术的主体。高速、高精加工技术可极大地提高效率,提高产品的质量和档次,缩短生产周期和提高市场竞争能力。而对于数控加工,无论是手工编程还是自动编程,在编程前都要对所加工的零件进行工艺分析,拟定加工方案,选择合适的刀具,确定切削用量,对一些工艺问题(如对刀点、加工路线等)也需做一些处理。并在加工过程掌握控制精度的方法,才能加工出合格的产品。 本文根据数控机床的特点,针对具体的零件,进行了工艺方案的分析,工装方案的确定,刀具和切削用量的选择,确定加工顺序和加工路线,数控加工程序编制。通过整个工艺的过程的制定,充分体现了数控设备在保证加工精度,加工效率,简化工序等方面的优势。 关键词工艺分析加工方案进给路线控制尺寸
目录 第1章前言 (4) 第2章工艺方案分析 (5) 2.1 零件图 (5) 2.2 零件图分析 (5) 2.3 确定加工方法 (5) 2.4 确定加工方案 (6) 第3章工件的装夹 (7) 3.1 定位基准的选择 (7) 3.2 定位基准选择的原则 (7) 3.3 确定零件的定位基准 (7) 3.4 装夹方式的选择 (7) 3.5 数控车床常用的装夹方式 (7) 3.6 确定合理的装夹方式 (7) 第4章刀具及切削用量 (8) 4.1 选择数控刀具的原则 (8) 4.2 选择数控车削用刀具 (8) 4.3 设置刀点和换刀点 (8) 4.4 确定切削用量 (9) 第5章典型轴类零件的加工 (10) 5.1 轴类零件加工工艺分析 (10) 5.2 典型轴类零件加工工艺 (12) 5.3 加工坐标系设置 (15) 5.4 手工编程 (16)
齿轮加工工艺说明书
第一章 零件的分析 1.1零件的工作状态及工作条件 汽车行驶时,齿轮始终在重载荷、高转速中工作。在换挡时,还承受冲击载荷,所以要求齿轮具有较高的耐磨性和抗冲击性。在齿轮加工中,为保证齿轮能满足以上要求,应对齿轮在滚齿之后采取磨齿,对齿轮的热处理应采用渗碳淬火,在最终加工中还应采取磷化处理以提高齿轮的防腐性能。 第五速齿轮从结构上来分析属于多联齿轮,由结合齿和传动齿组成。为使润滑用能充分的起到润滑作用,在齿轮钻出3个油孔。换挡时为减少齿轮的冲击,在齿轮大端加工出四个止口。 1.2零件的技术条件分析 齿轮加工分为齿坯和齿轮轮齿加工。齿轮的加工部位有轮缘、轮辐、轮毂和内孔。齿坯的加工精度对齿轮的加工、检验和装配精度影响很大,所以其加工精度应满足GB10095-88的要求。 齿轮轮齿的加工部位有齿形和倒角,同时还要进行热处理,以提高承载能力和使用寿命。热处理后还要进行内孔、内孔端面的磨削加工和齿形的精整加工。 综上所述,零件的技术条件主要分以下两种: 1.零件的表面粗糙度和加工精度 如零件图所示:齿面的粗糙度Ra 0.8,加工精度IT5~IT6; 齿轮内孔尺寸?025 .00 30+,由于齿轮与第二轴上的轴承有配合要求,故其不仅加工经济公差等级比 较高而且其表面粗糙度为Ra 0.4。 一般载货汽车变速器和拖拉机变速箱齿轮的精度一般是6到7级精度,表面粗糙度不大于Ra 3.2. 2.各表面间的位置精度 如零件图所示,零件的D 、E 、F 面三处具有形位公差要求; D 面对于定位基面φ029.001.070++的定位基准垂直度为0.015,平面度为0.01; E 面对于内孔的定位基准的垂直度为0.05,端面的平面度为0.01; F 面对于内孔的定位基准的垂直度为0.03;
典型轴类零件加工工艺标准规范标准分析
阶梯轴加工工艺过程分析 图6—34为减速箱传动轴工作图样。表6—13为该轴加工工艺过程。生产批量为小批生产。材料为45热轧圆钢。零件需调质。
(一)结构及技术条件分析 该轴为没有中心通孔的多阶梯轴。根据该零件工作图,其轴颈M、N,外圆P,Q及轴肩G、H、I有较高的尺寸精度和形状位置精度,并有较小的表面粗糙度值,该轴有调质热处理要求。 (二)加工工艺过程分析 1.确定主要表面加工方法和加工方案。
传动轴大多是回转表面,主要是采用车削和外圆磨削。由于该轴主要表面M,N,P,Q的公差等级较高(IT6),表面粗糙度值较小(Ra0.8μm),最终加工应采用磨削。其加工方案可参考表3-14。 2.划分加工阶段 该轴加工划分为三个加工阶段,即粗车(粗车外圆、钻中心孔),半精车(半精车各处外圆、台肩和修研中心孔等),粗精磨各处外圆。各加工阶段大致以热处理为界。 3.选择定位基准 轴类零件的定位基面,最常用的是两中心孔。因为轴类零件各外圆表面、螺纹表面的同轴度及端面对轴线的垂直度是相互位置精度的主要项目,而这些表面的设计基准一般都是轴的中心线,采用两中心孔定位就能符合基准重合原则。而且由于多数工序都采用中心孔作为定位基面,能最大限度地加工出多个外圆和端面,这也符合基准统一原则。 但下列情况不能用两中心孔作为定位基面: (1)粗加工外圆时,为提高工件刚度,则采用轴外圆表面为定位基面,或以外圆和中心孔同作定位基面,即一夹一顶。 (2)当轴为通孔零件时,在加工过程中,作为定位基面的中心孔因钻出通孔而消失。为了在通孔加工后还能用中心孔作为定位基面,工艺上常采用三种方法。 ①当中心通孔直径较小时,可直接在孔口倒出宽度不大于2mm的60o内锥面来代替中心孔;
轴的加工工艺设计
轴的加工工艺设计 Document number:NOCG-YUNOO-BUYTT-UU986-1986UT
轴加工工艺规程设计 专业:机械设计制造及其自动化 班级: 姓名: 学号: 轴类零件加工工艺规程设计 一、设计要求: .零件任选 .零件图一张,用CAD画 .毛坯图一张 .机械加工工艺规程综合卡片一套 .说明书一份 .按大批大量生产考虑 二、零件图 轴的作用 轴主要应用在动力装置中,是主要零件之一。其主要作用是传递转矩,使主
轴获得旋转的动力,其工作中要承受较大的冲击载荷和扭矩。因此,该零件需具有足够的耐磨性和抗扭强度。 输出轴的结构特点、工艺,表面技术要求分析 从图示零件分析,该轴结构简单,属于阶梯轴类零件。主要由有φ55、φ 40、φ23、φ20的外圆柱面。φ50的外圆的粗糙度要求都为, φ20的外圆的粗糙度 要求都为,φ35的圆弧面的粗糙度要求都为,莫氏4的锥度表面要求为,形位精度也比较高,为径向跳动量小于,由于输出轴在工作中要承受较大的冲击载荷和扭矩,为了增强耐磨性和抗扭强度,要对输出轴进行调质处理,硬度为 250HBS。加工零件不能使用砂布、锉刀及其他砂磨工具进行锉修及打光。未标注的公差按IT14,未倒得角按1x45度。莫氏4锥度用涂色法检查接触70%。三、确定毛胚 选择毛胚材料 毛坯的材料 45钢 制造毛胚的种类有很多,如1、型材2、锻造3、铸造,由于该输出轴要承受较大的冲击载荷和扭矩,为了增强其刚性和韧性,所以要选择锻件做为毛胚。如果选用棒料,由于生产类型为大批,从经济上考虑,棒料要切削的余量太大,浪费材料,所以不选。 毛胚的的简图 四、工艺路线的确定 基准的选择 基准可以分为粗基准和精基准 粗基准 由于此零件为轴类零件,为了保证精度,所以选择外圆作为粗基准面。首先选用三爪卡盘自动找正原理,夹紧。以外圆为粗基准面,加工外圆、端面、中心孔。然后用已加工过的外圆作为基准,加工另一端面和钻中心孔,保证两个中心孔在同一直线上。 精基准的选择 精基准的选择对一个零件加工完成后的精度非常重要。此零件选用两端的中心孔作为精基准,所以用两端中心孔来对外圆精加工。外圆加工完成后用外圆作为精基准,加工内圆,攻螺纹。 工序集中和分散考虑 工序集中 工序集中就是将零件的加工集中在少数几道工序中完成,每道工序加工内容多,工艺路线短。其主要特点是:
齿轮轴的设计及加工工艺
浙江科技学院 本科毕业设计 (2013届) 题目螺旋输送机驱动轴设计及制造学院机械与汽车工程学院 专业材料成型与控制工程 班级材料092 学号109012050 学生姓名杨鹏飞 指导教师奚基学 完成日期2013年5 月14 号
螺旋输送机驱动轴设计及制造 学生姓名:杨鹏飞指导教师:奚基学 浙江科技学院机械学院 摘要 随着工业生产的发展,螺旋输送机的应用越来越广泛,但由于具体工作环境的不同,技术参数的不同,对螺旋输送机的一些组成设备要求也不一样。本文通过对螺旋输送机的结构,发展历程的分析,然后就对螺旋输送机性能影响较大的部分,即驱动轴作了详细的设计说明,并对轴的加工工艺做了分析。最终设计出了一种主要用于输螺旋输送机驱动端的驱动轴 关键词:螺旋输送机驱动轴加工工艺
浙江科技学院毕业设计 II II
Design of Screw Conveyor Live Axle and Product Student: Yang Pengfei Advisor: Dr. Xi Jixue School of Mechanical and Automotive Engineering Zhejiang University of Science and Technology Abstract With the development of the industry, the flexible screw conveyors are used more and more widespread, but because the concrete working conditions are different, so the leak-proof requests of spiral conveyer are different too. Through different plan contrast, This article has chosen one kind of perfect plan considering the efficiency, structure compact and the usable angle embarked. Then explaned two major parts- the reducting gear and the screw shaft detailedly that h ave large affects on the flexible screw conveyer’ performance,and has given the brief explanation to the flexible screw conveyer’s seal and lubrication. At last ,a high quality flexible screw conveyor was desiganed out,which is primarily used to transport the cement, seal completely , work safely, have high efficiency and long work life, and can proceeds the cement during the course of transporting. Key words: Screw Conveyor Live Axle Processing technic
典型轴类零件加工工艺分析
阶梯轴加工工艺过程分析? 图6—34为减速箱传动轴工作图样。表6—13为该轴加工工艺过程。生产批量为小批生产。材料为45热轧圆钢。零件需调质。
(一)结构及技术条件分析??该轴为没有中心通孔的多阶梯轴。根据该零件工作图,其轴颈M、N,外圆P,Q及轴肩G、H、I有较高的尺寸精度和形状位置精度,并有较小的表面粗糙度值,该轴有调质热处理要求。?
(二)加工工艺过程分析? 1.确定主要表面加工方法和加工方案。 传动轴大多是回转表面,主要是采用车削和外圆磨削。由于该轴主要表面M,N,P,Q的公差等级较高(IT6),表面粗糙度值较小(Ra0.8μm),最终加工应采用磨削。其加工方案可参考表3-14。 2.划分加工阶段 该轴加工划分为三个加工阶段,即粗车(粗车外圆、钻中心孔),半精车(半精车各处外圆、台肩和修研中心孔等),粗精磨各处外圆。各加工阶段大致以热处理为界。 3.选择定位基准 轴类零件的定位基面,最常用的是两中心孔。因为轴类零件各外圆表面、螺纹表面的同轴度及端面对轴线的垂直度是相互位置精度的主要项目,而这些表面的设计基准一般都是轴的中心线,采用两中心孔定位就能符合基准重合原则。而且由于多数工序都采用中心孔作为定位基面,能最大限度地加工出多个外圆和端面,这也符合基准统一原则。 但下列情况不能用两中心孔作为定位基面: ?(1)粗加工外圆时,为提高工件刚度,则采用轴外圆表面为定位基面,或以外圆和中心孔同作定位基面,即一夹一顶。? (2)当轴为通孔零件时,在加工过程中,作为定位基面的中心孔因钻出通孔而消失。为了在通孔加工后还能用中心孔作为定位基面,工艺上常采用三种方法。 ①当中心通孔直径较小时,可直接在孔口倒出宽度不大于2mm的60o内锥面来代替中心孔;
齿轮箱加工工艺说明书
目录 第一章绪论----------------------------------------------------------------------------------3 第二章零件的工艺分析-----------------------------------------3 2.1零件的工艺分析----------------------------------------------3 2.2确定毛坯的制造形式-------------------------------------------3 2.3箱体零件的工艺性---------------------------------------------3第三章拟定箱体加工的工艺路线--------------------------------4 3.1 定位基准的选择-----------------------------------------------4 3.2 加工路线的拟定-----------------------------------------------5第四章加工余量,工序尺寸及毛坯尺寸的确定------------------7 4.1 确定毛坯----------------------------------------------------------------------------------7 4.2 机体----------------------------------------------------------------------------------------8 4.3 箱体----------------------------------------------------------------------------------------8第五章确定切削用量及基本工时-------------------------------------------------9 5.1 机座----------------------------------------------------------------------------------------9 5.2机体---------------------------------------------------------------------------------------18 参考文献----------------------------------------------------------------------------------------35 结论-------------------------------------------------------------------------------------- 36
数控机床轴类零件加工工艺分析
数控机床轴类零件加工工 艺分析 Prepared on 22 November 2020
X X X学院 毕业 设计 任务书 论文 机械工程系数控技术专业 XX 班 毕业设计 题目 数控机床轴类零件加工工艺分析论文 专题题目 数控机床轴类零件加工工艺分析 发题日期:2010年11月15日设计、论文自2010年11月20日完成期限:至2010年月日答辩日期:2010年月日 学生姓名: 指导教师: 系主任:
毕业设计版权使用授权书 本人完全了解云南机电职业技术学院关于收集、保存、使用毕业设计的规定,同意如下各项内容:按照学校要求提交毕业设计的印刷本和电子版本;学校有权保存毕业设计的印刷本和电子版,并采用影印、缩印、扫描、数字化或其它手段保存毕业设计;学校有权提供目录检索以及提供本
毕业设计全文或者部分的阅览服务;学校有权按有关规定向国家有关部门或者机构送交毕业设计的复印件和电子版;在不以赢利为目的的前提下,学校可以适当复制毕业设计的部分或全部内容用于学术活动。 作者签名: 年月日 作者签名: 年月日 摘要 世界制造业转移,中国正逐步成为世界加工厂。美国、德国、韩国等国家已经进入发展的高技术密集时代与微电子时代,钢铁、机械、化工等重化工业发展中期。 由于数控机床综合应用了电子计算机、自动控制、伺服系统、精密检测与新型机械结构等方面的技术成果,具有高的高柔性、高精度与高度自动化的特点,因此,采用数控加工手段,解决了机械制造中常规加工技术难以解决甚至无法解决的单件、小批量,特别是复杂型面零件的加工,应用数控加工技术是机械制造业的一次技术革命,使机械制造的发展进入了一个新的阶段,提高了机械制造业的制造水平,为社会提供高质量,多品种及高可靠性的机械产品。 本次设计主要是对数控加工工艺进行分析与具体零件图的加工,首先对数控加工技术进行了简单的介绍,然后根据零件图进行数控加工分析。第一,根据本零件材料的加工工序、切削用量以及其他相关因素选用刀具及
轴类零件机械加工工艺规程设计
轴类零件机械加工工艺规程设计 零件图七
摘要 本设计所选的题目是有关轴类零件的设计与加工,通过设计编程,最终用数控机床加工出零件,数控加工与编程毕业设计是数控专业教学体系中构成数控加工技术专业知识及专业技能的重要组成部分,它是运用数控原理,数控工艺,数控编程,制图软件和数控机床实际操作等专业知识对零件进行设计,是对所学专业知识的一次全面训练。熟悉设计的过程有利于对加工与编程的具体掌握,通过设计会使我们学会相关学科的基本理论,基本知识,进行综合的运用,同时还会对本专业有较完善的系统的认识,从而达到巩固,扩大,深化知识的目的。 此次设计也是我们走出校园之前学校对我们的最后一次全面的检验以及提高我们的素质和能力。毕业设计和完成毕业论文也是我们获得毕业资格的必要条件。 设计是以实践为主,理论与实践相结合的,通过对零件的分析与加工工艺的设计,提高我们对零件图的分析能力和设计能力。达到一个毕业生应有的能力,使我们在学校所学的各项知识得以巩固,以更好的面对今后的各种挑战。 此次设计主要是围绕设计零件图七的加工工艺及操作加工零件来展开的,我们在现有的条件下保证质量,加工精度及以及生产的经济成本来完成,对我们来说具有一定的挑战性。其主要内容有:分析零件图,确定生产类型和毛坯,确定加工设备和工艺设备,确定加工方案及装夹方案,刀具选择,切削用量的选择与计算,数据处理,对刀点和换刀点的确定,加工程序的编辑,加工时的实际操作,加工后的检验工作。撰写参考文献,组织附录等等。 关键词 加工工艺、工序、工步、切削用量:切削速度(m/min)、切削深度(mm)、进给量(mm/n、mm/r)。
齿轮轴的加工工艺设计
西南科技大学 机械制造与自动化专业 毕业设计(论文)齿轮轴的加工工艺设计 学院: 四川航天职业技术学院 系部: 飞行器制造系 班级: G11飞行器制造工艺套读班学生姓名: 准考证号: 指导教师(签名): 成绩:
I 摘要 毕业设计是我们学完了大学的全部基础课、技术基础课以及大部分专业课之后进行的.这是由我们大学三年学习课程的综合分析而做出的设计,也是一次理论联系实际的训练,是我们用实际与理论的结合,因此,它是我们在社会上实习所做出的一份对大学三年的答卷。 这次设计的是齿轮轴,有零件图、毛坯图、装配图、夹具装配图各一张,机械加工零件工艺卡一张,设计说明书一份。首先我们要熟悉零件,题目所给的零件是齿轮轴。首先必须要了解齿轮轴的作用,接下来根据零件的性质和零件图上各端面的粗糙度确定毛坯的尺寸和机械加工余量。然后我们再根据定位基准先确定精基准,后确定粗基准,最后拟定主动齿轮的工艺路线图,制定该工件的夹紧方案,画出夹具装配图,夹具体零件图。 这就是我设计的基本过程。 齿轮轴是机械传动中的最主要部件,一般是电机通过带传动在大小齿轮间传递力矩以及调整好转速最后达到所需要的转速。各齿轮间相互齿合相互传递力矩,齿轮与筒体把合,齿轮的精度决定传递的准确性,而齿轮的热处理工艺—加工
工艺决定了齿轮的使用的寿命和承载的最大力矩。齿轮传动很早以前就出现了,随着科学技术的进步,出现了一系列的齿轮传动形式,并形成了相应的齿轮啮合理论、设计、加工方法,这些工作都丰富和发展了齿轮传动理论体系。 齿轮是机械行业量大面广的基础件,广泛应用于机床,汽车,摩托车,农机,建筑机械,工程机械,航空,兵器,工具等领域,而且对加工精度,效率和柔性提出的要求越来越高。目前在国内绝大部分仍采用普通机床加工齿轮,精度很难提高。近几年,我国齿轮加工技术在发展的过程中取得了一定的进,但是总体还远远落后与西方发达国家,很多东西都在格里森齿轮等基础上发展过来的。随着科学技术的发展,齿轮加工技术必定会朝着数控化、智能化、高速化、集成化、环保化的方向发展。
低速级斜齿轮零件的机械加工工艺规程
目录 第一章任务书 (1) 第二章前言 (3) 第三章零件的分析 (3) 第四章毛坯的选择 (4) 第五章工艺规程的设计 (5) 第六章填写工艺过程卡和工序卡 (14)
第七章夹具的设计 (14) 第八章心得体会 (15) 第九章参考文献 (16) 第二章前言 机械制造工艺学课程设计是在学完了机械制造工艺学和大部分专业课,并进行了生产实习的基础上进行的一个教学环节。这次设计使我们能综合机械制造工艺中的基本理论,并能结合生产实习中学到的实践知识,独力的分析和解决工艺问题,初步具备了设计一个中等复杂程度零件的工艺规程的能力和运用夹具设计的基本原理和方法通过此设计,使我加深了对机械设计基础及有关专业课程知识
的了解,提高了熟悉和运用有关手册、图表等技术资料及技术文件等基本技能及综合运用这些知识的能力,并为在今后学习本专业和进行此类设计打下了坚实的基础,对自己将来设计产品有很大的帮助。 由于能力所限,经验不足,设计中还有许多不足之处,希望各位老师多加指点。 第三章零件的分析 一、零件技术要求的分析 (1)齿顶圆Φ750.141h11对孔Φ75有公差为0.056的径向的跳动要求。 (2)两端面对孔轴线分别有公差为0.02的端面圆跳动要求。 (3)键槽两侧面对孔轴线有公差为0.03的对称要求。 二、零件的工艺分析 由附图一得知,其材料为40Cr。该材料具有较高的硬度,耐磨性,耐热性。主要加工表面是齿轮的齿面:表面质量要求是0.8和内圈
的端面:表面要求达到1.6,还有齿轮内径表面质量要求达到1.6。 第四章毛坯的选择 一、该零件材料为40Cr,齿轮的内孔Φ195和外圆直径Φ750.14,都是直径比较大的圆,又由题目的生产纲领为3000件/年,由参考文献表5.6(划分生产类型的参考数据)可知该零件批量生产为大批量生产,毛坯应选用锻造。毛坯的锻造方法用模锻。 二、模锻锻件机械性能较好,有较高的强度和冲击韧性,但是毛坯的形状不宜复杂,如轴类和齿轮类零件的毛坯常用锻造。 三、锻造毛坯的工艺特点 参考文献[1]表9-1,常用毛坯的制造方法与工艺特点:
轴类零件工艺制定实例
一、轴类零件是机器中经常遇到的典型零件之一。它主要用来支承传动零部件,传递扭矩 和承受载荷。轴类零件是旋转体零件,其长度大于直径,一般由同心轴的外圆柱面、圆锥面、内孔和螺纹及相应的端面所组成。根据结构形状的不同,轴类零件可分为光轴、阶梯轴、空心轴和曲轴等。 轴的长径比小于5的称为短轴,大于20的称为细长轴,大多数轴介于两者之间。 轴用轴承支承,与轴承配合的轴段称为轴颈。轴颈是轴的装配基准,它们的精度和表面质量一般要求较高,其技术要求一般根据轴的主要功用和工作条件制定,通常有以下几项: (一)尺寸精度起支承作用的轴颈为了确定轴的位置,通常对其尺寸精度要求较高 (IT5~IT7)。装配传动件的轴颈尺寸精度一般要求较低(IT6~IT9)。 (二)几何形状精度轴类零件的几何形状精度主要是指轴颈、外锥面、莫氏锥孔等的 圆度、圆柱度等,一般应将其公差限制在尺寸公差范围内。对精度要求较高的内外圆表面,应在图纸上标注其允许偏差。 (三)相互位置精度轴类零件的位置精度要求主要是由轴在机械中的位置和功用决定 的。通常应保证装配传动件的轴颈对支承轴颈的同轴度要求,否则会影响传动件(齿轮等)的传动精度,并产生噪声。普通精度的轴,其配合轴段对支承轴颈的径向跳动一般为0.01~0.03mm,高精度轴(如主轴)通常为0.001~0.005mm。 (四)表面粗糙度一般与传动件相配合的轴径表面粗糙度为Ra2.5~0.63μm,与轴承相 配合的支承轴径的表面粗糙度为Ra0.63~0.16μm。 一、概述 (一)、轴类零件的功用与结构特点 1、功用:为支承传动零件(齿轮、皮带轮等)、传动扭矩、承受载荷,以及保证装在主轴上的工件或刀具具有一定的回转精度。 2、2、分类:轴类零件按其结构形状的特点,可分为光轴、阶梯轴、空心 轴和异形轴(包括曲轴、凸轮轴和偏心轴等)四类。
传动齿轮轴的加工工艺设计说明书
摘要 齿轮轴零件的主要作用是支撑回转零件、实现回转运动并传递转矩和动力。齿轮轴具备传动效率高、结构紧凑和使用寿命长等一系列优点,是通用机械特别是工程机械传动中的重要零件之一。齿轮轴加工材料、热处理方式、机械加工工艺过程的优化,将对提高齿轮轴的加工质量及寿命有着重要借鉴意义。 本设计首先分析了齿轮轴零件的作用和零件的材料,之后把加工传动齿轮轴所用的材料和生产类型确定下来。然后确定毛坯的种类,绘制铸件零件图。接下来设计零件的加工工艺性,包括零件表面的加工方法及热处理方法等。最后进行工艺规程设计,选定加工所用的机床,刀具,夹具等。齿轮轴零件的机械综合性能要求较高,一般选择锻件作为毛坯。合理安排工艺路线,划分加工阶段对保证零件加工质量至关重要. 关键词: 齿轮轴;工艺分析;工艺规程设计
Abstract The main function of the gear shaft is to support rotating parts, achieve rotary mo tion and transfer torque and power. Gear shaft has a series of advantages, such as high transmission efficiency, compact structure, long service life and so on. It is one of the important parts in the general machinery, particularly the engineering machinery tran smission. The optimization of the gear shaft’s machining materials, thermal treatment method and machining process will have great significance on the machining quality of the gear shaft and the service life. The first design of the gear shaft parts and parts of the material, then fix the processing gear shaft of the materials used and the type of production. And then determine the blank type, drawing casting parts diagram. The processing of the next design of parts, including the components surface processing method and heat treatment method. Finally, technological process design ,selection of the machine tool, cutting tool, fixture etc…Comprehensive mechanical performance requirements higher gear shaft parts, as general forging blank. Reasonable arrangements for the process, dividing the processing stage is very important to ensure the machining quality of parts. Keywords gear shaft; process analysis; process planning design
齿轮轴零件加工工艺设计
绪论 本课题的研究主要是加工工艺的注意点和改进的方法,通过总结零件的的加工,提高所加工工件的质量,完善产品,满足要求,提高经济效益和劳动生产率。 一般齿轮轴有两个支撑轴径,工作时通过轴径支撑在轴承上,这两个支撑轴径便是其装配基准,通常也是其他表面的设计基准,所以它的精度和表面质量要求较高。对于一些重要的轴,支撑轴除规定较高的尺寸精度外,通常还规定圆度、圆柱度以及两轴径之间的同轴度等形状精度要求等。对于其他工作轴径,如安装齿轮、带轮、螺母、轴套等零件的轴径,除了有本身的尺寸精度和表面粗糙度外,通常还要求其轴线与两支承轴径的公共线同轴,以保证轴上各运动部件的运动精度。 轴为支承转动零件并与之一起回转以传递运动、扭矩或弯矩的机械零件。一般为金属圆杆状,各段可以有不同的直径。机器中作回转运动的零件就装在轴上。根据轴线形状的不同,轴可以分为曲轴和直轴两类。根据轴的承载情况,又可分为:①转轴,工作时既承受弯矩又承受扭矩,是机械中最常见的轴,如各种减速器中的轴等;②心轴,用来支承转动零件只承受弯矩而不传递扭矩,有些心轴转动,如铁路车辆的轴等,有些心轴则不转动,如支承滑轮的轴等;③传动轴,主要用来传递扭矩而不承受弯矩,如起重机移动机构中的长光轴、汽车的驱动轴等。轴的材料主要采用碳素钢或合金钢,也可采用球墨铸铁或合金铸铁等。轴的工作能力一般取决于强度和刚度,转速高时还取决于振动稳定性。 本课题缩小到对齿轮轴的研究,本课题中的加工精度高,因此对技术也就会随之提高,包括尺寸精度、几何形状精度、相互位置精度及表面粗糙度等。使齿轮轴起到它的作用,更好的支撑传动部件、传递扭矩和承受载荷。从而使产品更加畅销,寿命延续更长,具有长远的意义,齿轮轴机件的损坏、磨损、变形以及失去动平衡,严重时会导致相关部件的损坏。
齿轮轴的制造工艺规程设计(2013).
机械制造工艺学 课程设计 设计题目:齿轮轴的制造工艺规程设计 班级:10机械本B班 学号:2010210279 姓名:云大宝 指导教师:支新涛 日期:2013.06.16
机制工艺课程设计任务书 Ⅰ、课程设计名称: 机制工艺课程设计 Ⅱ、课题名称: 齿轮轴的制造工艺规程设计 Ⅲ、课程设计使用的原始资料(数据)及设计技术要求: 1.生产要求:产品的生产纲领为379台/年,每台产品齿轮轴数量 2件;齿轮轴的备品百分率为4%,废品百分率为0.4% 2.生产条件和资源:毛坯为外协件,生产条件可根据需要确定; 设备可以根据需要选择且各设备均达到机床规定的工作精度要求。 3.零件图见下页 4.零件的分析及毛坯的确定。 5.拟定机械加工工艺过程。 6.合理选择各工序的定位基准。 7.确定加工工序的余量和切削用量。 8.确定工序尺寸,正确拟定工序技术要求。 9.编制加工工艺规程。 10.撰写设计说明书。
1齿轮轴的分析 (1) 1.1齿轮轴的作用 (1) 1.2齿轮轴的工艺分析 (1) 2零件的生产类型 (1) 2.1生产纲领 (1) 2.2生产类型及工艺特征 (1) 3工艺规程的设计 (2) 3.1毛坯的确定 (2) 3.2选择定位基 (2) 3.3制定工艺路线 (3) 3.4机械加工余量、工序尺寸及毛坯尺寸的确定 (4) 3.5确定切削用量和基本工时 (5) 4设计总计 (7) 附录:轴的机械加工工艺卡 (8) 参考文献 (17)
课程设计说明书 1、齿轮轴分析 1.1齿轮轴的作用 齿轮轴是传动系配件,作用是指支承转动零件并与之一起回转以传递运动、扭矩或弯矩的机械零件。一般为金属圆杆状,各段可以有不同的直径。机器中作回转运动的零件就装在轴上。 1.2零件工艺分析 1)工序安排热处理调质处理后,再进行精车、磨削加工,以保证加工质量稳定。 2)精车、粗磨、精磨工序均以两中心孔定位装夹工件,其定位基准统一,可以更好保证零件的加工质量。 3)以工件两中心孔为定位基准,在偏摆仪上检查,φ60021 .0002.0++mm 、φ141.780063.0-mm 、φ60021 .0002.0++mm 三处轴径外圆对公共轴心线A —B 的圆跳动0.025mm 。 4)工序14对组合夹具应要求备有键槽对称度检查基准,可供加工对刀及加工后检查使用。 2、零件的生产类型 2.1生产纲领 根据任务书已知: ⑴产品的生产纲领为379台/年,每台产品齿轮轴数量2件 ⑵齿轮轴的备品百分率为%,废品百分率为0.4%。 齿轮轴生产纲领计算如下: N=Qn(1+a)(1+b) =379x2(1+4%)(1+0.4%) =791.47≈792(件/年) 2.2生产类型及工艺特征 查表确定齿轮轴属于大批量生产零件,工艺特征见表(如下): 生产纲领 生产类型 工艺特征
数控轴类零件加工工艺设计毕业论文
数控轴类零件加工工艺设计毕业论文 目录 第1章前言 (1) 第2章工艺方案分析 (2) 2.1 零件图 (2) 2.2 零件图分析 (2) 2.3 确定加工方法 (2) 2.4 确定加工方案 (2) 第3章 (4) 3.1 定位基准的选择 (4) 3.2 定位基准选择的原则 (4) 3.3 确定零件的定位基准 (4) 3.4 装夹方式的选择 (4) 3.5 数控车床常用的装夹方式 (4) 3.6 确定合理的装夹方式 (4) 第4章刀具及切削用量 (5) 4.1 选择数控刀具的原则 (5) 4.2 选择数控车削用刀具 (5) 4.3 设置刀点和换刀点 (6) 4.4 确定切削用量 (6) 第5章典型轴类零件的加工 (7) 5.1 轴类零件加工工艺分析 (7) 5.2 典型轴类零件加工工艺 (9) 5.3 加工坐标系设置 (11) 5.4 手工编程 (12) 第6章结束语 (15) 第7章致谢词 (16) 参考文献 (17)
第一章前言 在机械加工工艺教学中,机械制造专业学生及数控技术专业学生都要学习数控车床操作技术。让学生了解相关工种的先进技术,同时培养工作岗位的前瞻性。数控车工基础工艺理论及技能有机融合,包括夹具的使用、量具的识读和使用、刃具的刃磨及使用、基准定位等,分类叙述了车床操作、数控车床自动编程仿真操作、数控车床编程与操作的初、中级容。以机械加工中车工工艺学与数控车床技能训练密切结合为主线,常用量具识读及工件测量、刀具及安装、工件定位与安装、金属切削过程及精加工,较清晰地展示了数控车工必须掌握的知识和技能的训练途径。对涉及与数控专业相关的基础知识、专业计算,都进行了有针对性的论述,目的在于塑造理论充实、技能扎实的专业技能型人才。 本文以与切削用量的选择,工件的定位装夹,加工顺序和典型零件为例,结合数控加工的特点,分别进行工艺方案分析,机床的选择,刀具加工路线的确定,数控程序的编制,最终形成可以指导生产的工