TL681_EN_2002-12-01
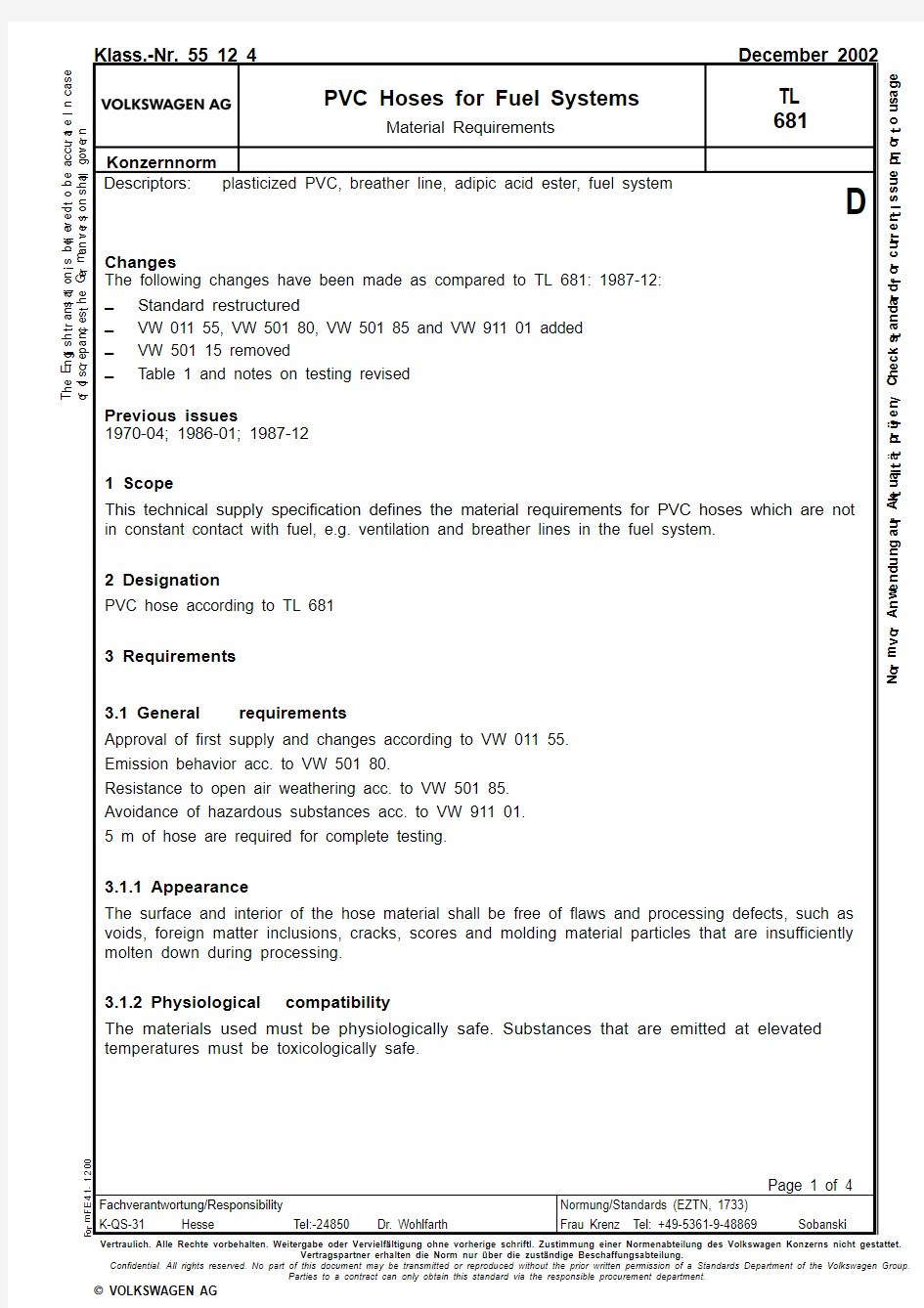

Vertragspartner erhalten die Norm nur über die zust?ndige Beschaffungsabteilung.
Confidential. All rights reserved. No part of this document may be transmitted or reproduced without the prior written permission of a Standards Department of the Volkswagen Group.
Parties to a contract can only obtain this standard via the responsible procurement department.
VOLKSWAGEN AG
N o r m v o r A n w e n d u n g a u f A k t u a l i t ?t p r üf e n / C h e c k s t a n d a r d f o r c u r r e n t i s s u e p r i o r t o u s a g e .
T h e E n g l i s h t r a n s l a t i o n i s b e l i e v e d t o b e a c c u r a t e . I n c a s e o f d i s c r e p a n c i e s t h e G e r m a n v e r s i o n s h a l l g o v e r n .
Page 2
TL 681: 2002-12
D
method
3.2 Manufacturing
Extrusion method
3.3 Identification according to VDA 260
>PVC-P<
3.4 Conditioning
Prior to testing, the specimens required for the individual tests must be conditioned for at least 48 h in the DIN 50 014-23/50-2 standard climate.
3.5 Validity of requirements
The required numerical values apply to each individual measurement.
3.6 Material
See section 5.1.
Polyvinyl chloride suspension polymer with plasticizers based on adipic acid ester.
3.7 Color
No coloring, unless otherwise specified in the drawing and/or release.
4 Physical properties
See Table 1.
Table 1
No. Property Unit Requirement
g/cm3 1.29 to 1.31
1 Density
acc. to DIN 53 479, buoyancy method
Shore A 85 to 90
2 Hardness
acc. to DIN 53 505-A, measurement
time 3 s
N/mm2 ≥ 19.5
3 Tensile strength
acc. to DIN 53 504 and section 5.2
% ≥ 300
4 Elongation at tear
acc. to DIN 53 504 and section 5.2
5 Fuel resistance
Shore A ≥ 60
5.1 Hardness in moist condition
acc. to DIN 53 505-A, measurement
time 3 s and section 5.3
Shore A 80 to 90
5.2 Hardness in dry condition
acc. to DIN 53 505, measurement time
3 s and section 5.4
N/mm2 ≥ 9
5.3 Tensile strength in moist condition
t DIN53504d ti55
Page 3
TL 681: 2002-12
5 Notes on testing
5.1 Material
The identity test is performed using infrared spectroscopy.
5.2 Tensile strength and elongation at tear
S3A specimens. The tensile specimens shall be taken from the hose material to be tested in the direction of extrusion; test rate 100 mm/min.
5.3 Shore A hardness in moist condition
Aging of five hose sections, 50 ±1 mm in length, in 250 ±10 ml FAM test fluid according to DIN 51 604-2; aging duration 48 - 2 h; aging temperature 23 ± 2 °C. The hardness measurement shall be performed after the specimens have been aged in air for 15 + 2 min at 23 ± 2 °C.
5.4 Shore A hardness in dry condition
Aging of five hose sections, 50 ±1 mm in length, in 250 ±10 ml FAM test fluid according to DIN 51 604-2; aging duration 48 - 2 h; aging temperature 23 ± 2 °C. The hardness measurement shall be performed after the specimens have been dried in mechanically circulated air at 70 ± 2 °C for 48 - 2 h and subsequent cooling to 23 ± 2 °C.
5.5 Tensile strength and elongation at tear in dry condition
Five S3A tensile specimens which have been previously measured in the cross section and taken from the hose material to be tested in the direction of extrusion are aged according to DIN 53 504 in 250 ±10 ml of FAM test fluid according to DIN 51 604-2; aging duration 48 - 2 h; aging temperature 23 ± 2 °C. The measurements shall be taken after the specimens have been aged in air for 15 + 2 min at 23 ± 2 °C in accordance with section 5.2.
Page 4
TL 681: 2002-12
D
change
5.6 Weight
Aging of five hose sections, measuring 50 ± 1 mm in length, which have been previously weighed accurate to 0.001 g, in 250 ±10 ml FAM test fluid according to DIN 51 604-2; aging duration 48 – 2 h; aging temperature 23 ±2 °C. The specimens shall be re-weighed after being dried in mechanically circulated air at 70 ± 2 °C and subsequent cooling to 23 ± 2 °C.
behavior
5.7 Low-temperature
Hose sections measuring approx. 100 mm in length shall be mounted on connecting t-pieces or adapters in accordance with the drawing, secured using the clamps provided and aged immediately after assembly for 22 + 2 h in air at -40 ±1 °C. The specimens are evaluated immediately after removing them from the cold chamber. A minimum of 3 specimens must be tested.
6 Referenced standards
TL 1010 Materials for Vehicle Interiors, Burning Behavior; Material Requirements
PV 1300 PVC and PVC Copolymer; Thermal Stability Test
VW 011 55 Vehicle Supply Parts – General; Approval of First Supply and Changes
VW 501 80 Vehicle Interior Components; Emissions Behavior
VW 501 85 Vehicle Components; Resistance to Open Air Weathering
VW 911 01 Environmental Standard For Vehicles, Vehicle Parts, Materials, Fuels; Avoidance of Hazardous Substances
DIN 50 014 Climates and their Technical Application; Standard Atmospheres
DIN 51 604-2 FAM Test Fluid Containing Methanol for Polymer Materials; Composition and Requirements
DIN 53 479 Testing of Plastics and Elastomers; Determination of Density
DIN 53 504 Testing of Rubber and Elastomers; Determination of Tensile Strength at Break, Tensile Stress at Yield, Elongation of Break and Stress Values in a Tensile Test
DIN 53 505 Testing Rubber and Elastomers; Shore A and Shore D Hardness Test
VDA 260 Automotive Components; Identification of Materials