A Doubly Salient Permanent Magnet Motor Drive for Improvement of Torque-Ripple and Fault-Tolerance
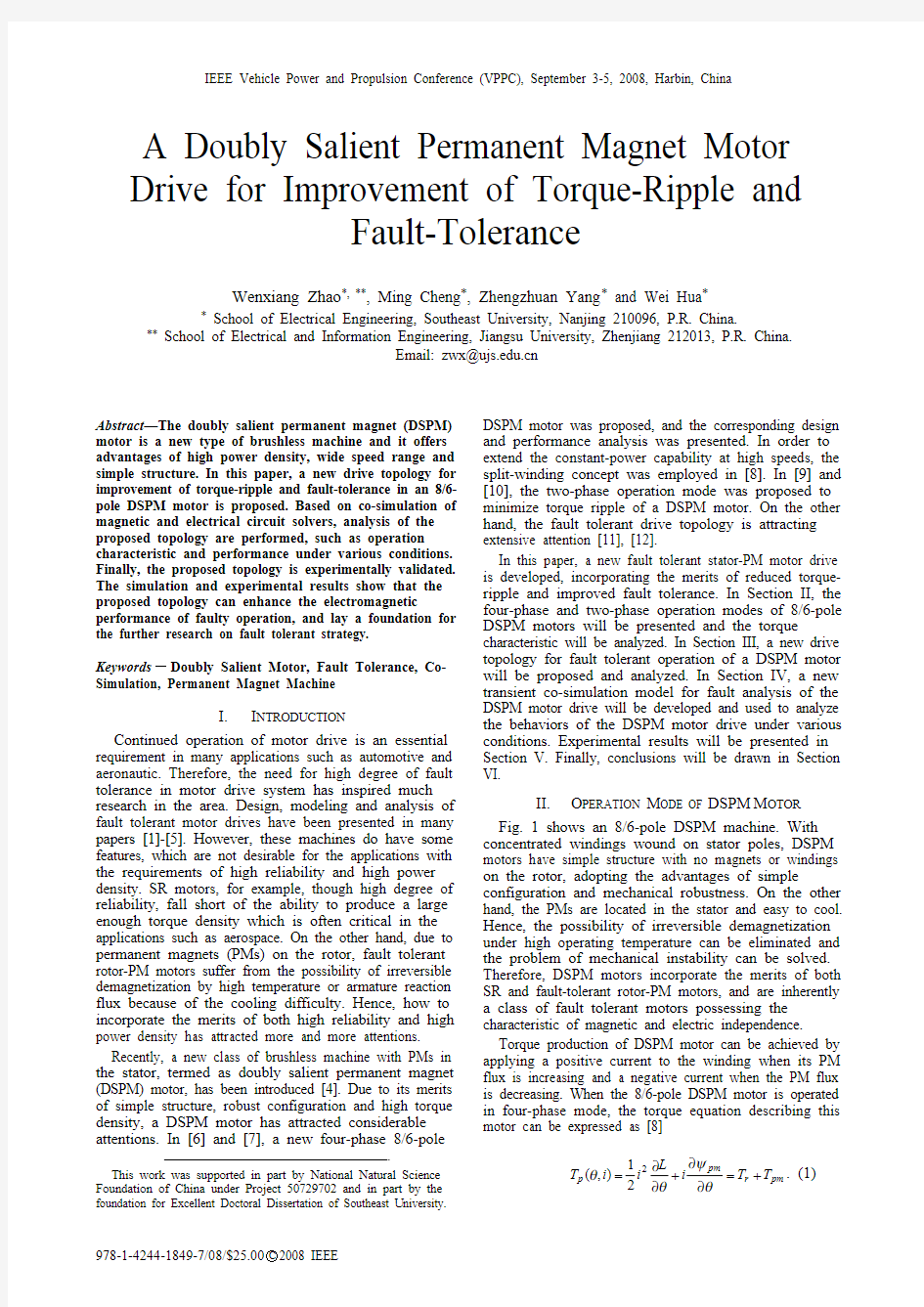

A Doubly Salient Permanent Magnet Motor Drive for Improvement of Torque-Ripple and
Fault-Tolerance
Wenxiang Zhao*, **, Ming Cheng*, Zhengzhuan Yang* and Wei Hua*
* School of Electrical Engineering, Southeast University, Nanjing 210096, P.R. China.
** School of Electrical and Information Engineering, Jiangsu University, Zhenjiang 212013, P.R. China.
Email: zwx@https://www.360docs.net/doc/957849181.html,
Abstract—The doubly salient permanent magnet (DSPM) motor is a new type of brushless machine and it offers advantages of high power density, wide speed range and simple structure. In this paper, a new drive topology for improvement of torque-ripple and fault-tolerance in an 8/6-pole DSPM motor is proposed. Based on co-simulation of magnetic and electrical circuit solvers, analysis of the proposed topology are performed, such as operation characteristic and performance under various conditions. Finally, the proposed topology is experimentally validated. The simulation and experimental results show that the proposed topology can enhance the electromagnetic performance of faulty operation, and lay a foundation for the further research on fault tolerant strategy. Keywords—Doubly Salient Motor, Fault Tolerance, Co-Simulation, Permanent Magnet Machine
I.I NTRODUCTION
Continued operation of motor drive is an essential requirement in many applications such as automotive and aeronautic. Therefore, the need for high degree of fault tolerance in motor drive system has inspired much research in the area. Design, modeling and analysis of fault tolerant motor drives have been presented in many papers [1]-[5]. However, these machines do have some features, which are not desirable for the applications with the requirements of high reliability and high power density. SR motors, for example, though high degree of reliability, fall short of the ability to produce a large enough torque density which is often critical in the applications such as aerospace. On the other hand, due to permanent magnets (PMs) on the rotor, fault tolerant rotor-PM motors suffer from the possibility of irreversible demagnetization by high temperature or armature reaction flux because of the cooling difficulty. Hence, how to incorporate the merits of both high reliability and high power density has attracted more and more attentions. Recently, a new class of brushless machine with PMs in the stator, termed as doubly salient permanent magnet (DSPM) motor, has been introduced [4]. Due to its merits of simple structure, robust configuration and high torque density, a DSPM motor has attracted considerable attentions. In [6] and [7], a new four-phase 8/6-pole
This work was supported in part by National Natural Science Foundation of China under Project 50729702 and in part by the foundation for Excellent Doctoral Dissertation of Southeast University. DSPM motor was proposed, and the corresponding design and performance analysis was presented. In order to extend the constant-power capability at high speeds, the split-winding concept was employed in [8]. In [9] and [10], the two-phase operation mode was proposed to minimize torque ripple of a DSPM motor. On the other hand, the fault tolerant drive topology is attracting extensive attention [11], [12].
In this paper, a new fault tolerant stator-PM motor drive
is developed, incorporating the merits of reduced torque-ripple and improved fault tolerance. In Section II, the four-phase and two-phase operation modes of 8/6-pole DSPM motors will be presented and the torque characteristic will be analyzed. In Section III, a new drive topology for fault tolerant operation of a DSPM motor
will be proposed and analyzed. In Section IV, a new transient co-simulation model for fault analysis of the DSPM motor drive will be developed and used to analyze
the behaviors of the DSPM motor drive under various conditions. Experimental results will be presented in Section V. Finally, conclusions will be drawn in Section VI.
II.O PERATION M ODE OF DSPM M OTOR
Fig. 1 shows an 8/6-pole DSPM machine. With concentrated windings wound on stator poles, DSPM motors have simple structure with no magnets or windings
on the rotor, adopting the advantages of simple configuration and mechanical robustness. On the other hand, the PMs are located in the stator and easy to cool. Hence, the possibility of irreversible demagnetization under high operating temperature can be eliminated and
the problem of mechanical instability can be solved. Therefore, DSPM motors incorporate the merits of both
SR and fault-tolerant rotor-PM motors, and are inherently
a class of fault tolerant motors possessing the characteristic of magnetic and electric independence.
Torque production of DSPM motor can be achieved by applying a positive current to the winding when its PM flux is increasing and a negative current when the PM flux
is decreasing. When the 8/6-pole DSPM motor is operated
in four-phase mode, the torque equation describing this motor can be expressed as [8]
pm
r
pm
p
T
T
i
L
i
i
T+
=
?
?
+
?
?
=
θ
ψ
θ
θ2
2
1
),
(. (1)
978-1-4244-1849-7/08/$25.00○C2008 IEEE
Figure 1. Cross-section of 8/6-pole DSPM motor.
where
T p instantaneous
electromagnetic
torque
per phase;
T pm PM torque component due to the
Interaction between PM flux linkage
and armature current;
T r reluctance torque component due to the
variation of reluctance;
Ψpm PM flux linkage;
θrotor angle;
L phase inductance.
When the windings A and C as well as the windings B
and D are reversely connected in series, respectively,
constituting the windings W and V shown in Fig. 2, the
DSPM motor is operated in two-phase mode. In order to
achieve a sinusoidal back-EMF waveform in a DSPM
motor, the rotor skewing method is adopted. It can be
known that the back-EMF of phases W and V can be
expressed as
?
?
?
°
?
=
=
)
90
6
sin(
)
6
sin(
θ
θ
E
e
E
e
V
W. (2)
If the DSPM motor is excited as sinusoidal currents
?
?
?
°
?
=
=
)
90
6
sin(
)
6
sin(
θ
θ
I
I
I
I
V
W. (3)
The phase torque equation can be expressed as
?
?
?
??
?
?
°
?
=
=
ω
θ
ω
θ
)
90
6(
sin
)
6(
sin
2
2
EI
T
EI
T
W
V
. (4)
Then the total torque equation can be obtained as
EI
T
T
T W
V
=
+
=. (5)
Equation (5) shows that during the two-phase operation,
the total electromagnetic torque does not vary with rotor
position and keeps constant.
Figure 2. Winding configuration during two-phase operation.
III.F AULT-T OLERANT D RIVE T OPOLOGY
It should be noted that the two-phase operation has its
disadvantage to fault tolerance. Owing to the connection
of windings A and C (B and D), the two-phase DSPM
motor drive has low performance in fault tolerant
operation. To meet the requirement of the electric
independence, a fault tolerant motor drive should detect
and isolate the fault phase without any effect on other
healthy phases. The motor drive can be operated with
other healthy phases working during loss of one phase.
Hence, a new fault tolerant drive topology is proposed in
this work. Fig 3 illustrated the proposed topologies under
various operations. The proposed fault tolerant topology
differs from the conventional DSPM motor drive topology
only in that the neutral points of two windings (windings
W and V) in the motor is separately connected to the mid-
point on the DC voltage link. The mid-point is created by
simply splitting the capacitor bank into two equal sections.
Two triacs (TR1 and TR2) are connected between the
capacitor midpoint and the motor two neutral points.
During normal operation, the triac is blocked, so no
current will flow in the neutral of the DSPM motor. When
one of the windings A, B, C and D is with fault, the
corresponding triac will be triggered “on”, and then
continued operation in other phases can be preserved.
(a)
(b)
(c)
Figure 3. Operation of drive under various conditions. (a) Normal
operation. (b) Faulty operation. (c) Remedial operation.
On the other hand, proper fault detectors must be employed. Detailed discussion on the fault detectors for motor drives can be seen in [13]-[16]. In this work, a detection technique is introduced, employing a
comparison of the measured current to their reference value A current error εp (p =a , b , c , d ) can be expressed as
p p p i i ?=?ε. (6) where
i p * the reference current of phase-p ; i p the measured current of phase-p .
As shown in Fig. 4, this work employs a hysteresis detector that considers the acceptable values for normal condition. Once the fault is detected, it can be dealt with.
i
Figure 4. Fault detector of DSPM motor drive.
IV. S IMULATION
To examine the developed drive topology, computer simulations are carried out. In this work, a new co-simulation method is employed to analyze electromagnetic characteristic of the DSPM machine, using coupled magnetic circuit solver (MCS) and electrical circuit solver (ECS). Firstly, a finite-element
conducted in MCS. Secondly, a Thevenin equivalent circuit, including the coupling inductance matrix, induced voltages and winding currents, is carried out and fed into ECS. After the calculation of the obtained nodal matrix, ECS extracts a Norton equivalent circuit, which consists of the conductance matrix and source currents flowing into the windings. Finally, MCS incorporates electric circuit equations into equations of the FE system for the next co-simulation step, using a loop form of the magnetic
equations. In brief, both solvers exchange the calculated
data at each co-simulation time-step, and the results achieved by one solver will be exported to the other solver in the next step. Based on the transient coupling technology in time-domain, the system level simulation can calculate coupling data and coefficients in each co-simulation time-step more efficiently. Therefore, this
parameter-based coupling technique has the ability of enhancing the solution accuracy and stability, providing
an important way for fault analysis of drive system. As shown in Fig. 5, the new type of co-simulation model for fault analysis of a DSPM motor drive has been developed.
The torque output is an important factor to evaluate fault tolerant performance in motor drive. Hence, this
study will focus on the torque characteristics of the motor drive under fault conditions. To assess the level of the torque ripple under various conditions, a torque ripple
factor is defined as follows [14]
%100)(min max ×?=av T T T T K . (7)
where
T max the maximum value of the output torque; T min the minimum value of the output torque; T av the average value of the output torque.
Based on the developed co-simulation model, the
electromagnetic performance of the DSPM motor drive
under normal condition is shown in Fig. 6. It can be seen that the K T is 57.1%, and the T av is 3.19 Nm. When a
power switch is with open-circuited fault during the DSPM motor is operated in two-phase mode, the current and torque waveforms are shown in Fig. 7, where the K T and T av are 227.3% and 2.27 Nm, respectively. After the switch fault is detected, by trigging the corresponding
triac “on”, the DSPM motor can run in four-phase operation mode. The current and torque waveforms are
shown in Fig. 8. It should be noted that the torque performance has improved. During fault tolerant operation, the K T is 118.6%, and the T av is 2.74 Nm. Figure 5. Co-simulation model of DSPM motor drive.
-3-2-101230
30
6090120150
180
Rotor angle (degree)
C u r r e n t (A )
(a)
-10123450
30
6090120150
180
Rotor angle (degree)
T o r q u e (N m )
(b)
Figure 6. Normal performance during two-phase operation. (a) Current
waveform of phase W. (b) Torque waveform.
-3-2-101230
30
6090120150
180
Rotor angle (degree)
C u r r e n t (A )
(a)
-10123450
30
6090120150
180
Rotor angle (degree)
T o r q u e (N m )
(b)
Figure 7. Faulty performance during two-phase operation mode. (a)
Current waveform of phase W. (b) Torque waveform.
-3-2-101230
30
6090120150
180
Rotor angle (degree)
C u r r e n t (A )
(a)
-3-2-101230
30
6090120150
180
Rotor angle (degree)
C u r r e n t (A )
(b)
-10123450
30
6090120150180
Rotor angle (degree)
T o r q u e (N m )
(c)
Figure 8. Fault tolerant performance during four-phase operation mode. (a) Current waveform of phase A. (a) Current waveform of phase
C. (b) Torque waveform.
V. E XPERIMENTAL R ESULTS
An experimental 8/6-pole DSPM motor with the ratings of 750 W and 1500 r/min has been designed and built for verification, as shown in Fig. 9. An IPM-based converter and a microcomputer-based digital controller are designed and implemented to drive the motor. The measured four-phase back-EMF waveforms are shown in Fig. 10. Therefore the presented two-phase operation can be performed in the DSPM motor for the purposed of minimization of torque ripple.
Figure 9.
Experimental DSPM motor.
Figure 10. Measured four-phase back-EMF waveforms
Fig. 11 shows the measured torque and current waveforms of the DSPM motor under various conditions. It can be observed from Fig. 11(b) that open-circuit fault results in reduced availability of net torque due to the absent electromagnetic torque of faulty phase Furthermore, as shown in Fig. 11(c), the torque output with remedial topology has improved. Hence, it can be concluded that high performance of fault tolerance is
achieved in DSPM motor drives.
(a)
(b)
(c)
Figure 11. Measured torque (upper trace) and current (lower trace) waveforms under (a) Normal, (b) Open-circuited and (c) Fault tolerant
conditions (20 ms/div, 1Nm/div, 1A/div).
VI. C ONCLUSION
In this paper, the merits of reduced torque ripple and enhanced fault tolerance have been incorporated in a DSPM motor drive. In order to minimize the torque ripple of an 8/6-pole DSPM motor, a new two-phase operation has been presented and analyzed. A new fault tolerant
topology for the two-phase operation of the DSPM motor has been proposed. A new co-simulation method has been employed to predict the faulty performance of the DSPM motor. The operation performance has been tested and high performance of the developed DSPM motor drive has been verified.
The proposed fault tolerant motor drive can be expected to have a bright future in a wide variety of drive applications with the requirements of high reliability and high power density.
R EFERENCES
[1] C.M. Stephens, “Fault detection and management system for fault
tolerant SR motor drives,” IEEE Trans. Ind. Appl., vol. 27, no. 6, pp. 1098-1102, Nov./Dec. 1991.
[2] S. Gopalakrishnan, A.M. Omekanda, and B. Lequesne,
“Classification and remediation of electrical faults in the switched reluctance drive,” IEEE Trans. Ind. Appl., vol. 42, no. 2, pp. 479-486, Mar./Apr. 2006.
[3] A.G. Jack, B.C. Mecrow, and J. Haylock, “A comparative study of
PM and SR motors for high performance fault tolerant applications,” IEEE Trans. Ind. Appl., vol. 32, no. 4, pp. 889-895, Jul./Aug. 1996.
[4] N. Bianchi, S. Bolognani, and M.D. Pre, “Strategies for the fault-tolerant current control of a five-phase permanent-magnet motor,” IEEE Trans. Ind. Appl., vol. 43, no. 4, pp. 960-970, July/Aug. 2007.
[5] L. Parsa, and H.A. Toliyat, “Fault-tolerant interior-permanent-magnet machines for hybrid electric vehicle applications,” IEEE Trans. Veh. Technol., vol. 56, no. 4, pp. 1546-1552, Jul. 2007.
[6] Y. Liao, F. Liang, and T. A. Lipo, “A novel permanent magnet
motor with doubly salient structure,” IEEE Trans. Ind. Appl ., vol. 31, no. 5, pp. 1069-1078, Sep./Oct. 1995.
[7] M. Cheng, K.T. Chau, and C. C. Chan, “Design and analysis of a
new doubly salient permanent magnet motor,” IEEE Trans. Mag., vol. 37, no. 4, pp. 3012-3020, Jul. 2001..
[8] M. Cheng, K.T. Chau , and C.C. Chan, “New split-winding doubly
salient permanent magnet motor drive,” IEEE Trans. Aerosp. and Electron. Syst., vol. 39, no. 1, pp. 202-210, Jan. 2003.
[9] M. Cheng, K.T. Chau, C.C. Chan, and Q. Sun, “Control and
operation of a new 8/6-pole doubly salient permanent-magnet motor drive,” IEEE Trans. on Ind. Appl., vol. 39, pp. 1363-1372, Sept./Oct. 2003.
[10] M. Cheng, W. Hua, X.Y. Zhu, and et al, “A simple method to
improve the sinusoidal static characteristics of doubly-salient PM machine for brushless AC operation”, Proc. ICEMS2007, Soul, Korea, 2007, 665-669.
[11] D. Kastha, and B.K. Bose, “Investigation of fault modes of
voltage-fed inverter system for induction motor drive,” IEEE Trans. Ind. Appl., vol. 34, no. 4, pp. 1028-1038, Jul./Aug. 1994. [12] B.A. Welchko, T.A. Lipo, T.M. Jahns, and S.E. Schulz, “Fault
tolerant three-phase ac motor drive topologies: a comparison of features, cost, and limitations,” IEEE Trans. Power Electron ., vol. 19, no. 4, pp. 1108-1116, Jul. 2004.
[13] X. Tu, L.-A. Dessaint, N. Fallati, and B.D. Kelper, “Modeling and
real-time simulation of internal faults in synchronous generators with parallel-connected windings,” IEEE Trans. Ind. Electron ., vol. 54, no. 3, pp. 1400-1409, Jun. 2007.
[14] C.H. Lo, Y.K. Wong, and A.B. Rad, “Intelligent system for
process supervision and fault diagnosis in dynamic physical systems,” IEEE Trans. Ind. Electron ., vol. 53, no. 2, pp. 581-592, Jun. 2006.
[15] O.A. Mohammed, Z. Liu, S. Liu, and N.Y. Abed, “Internal short
circuit fault diagnosis for PM machines using FE-based phase variable model and wavelets analysis,” IEEE Trans. Magn., vol. 43, no. 4, pp. 1729-1732, Apr. 2007.
[16] J.F. Martins, V.F. Pires, and A.J. Pires, “Unsupervised neural-network-based algorithm for an on-line diagnosis of three-phase induction motor stator fault,” IEEE Trans. Ind. Electron ., vol. 54, no. 1, pp. 559-264, Feb. 2007.