双色注塑模具成型要求
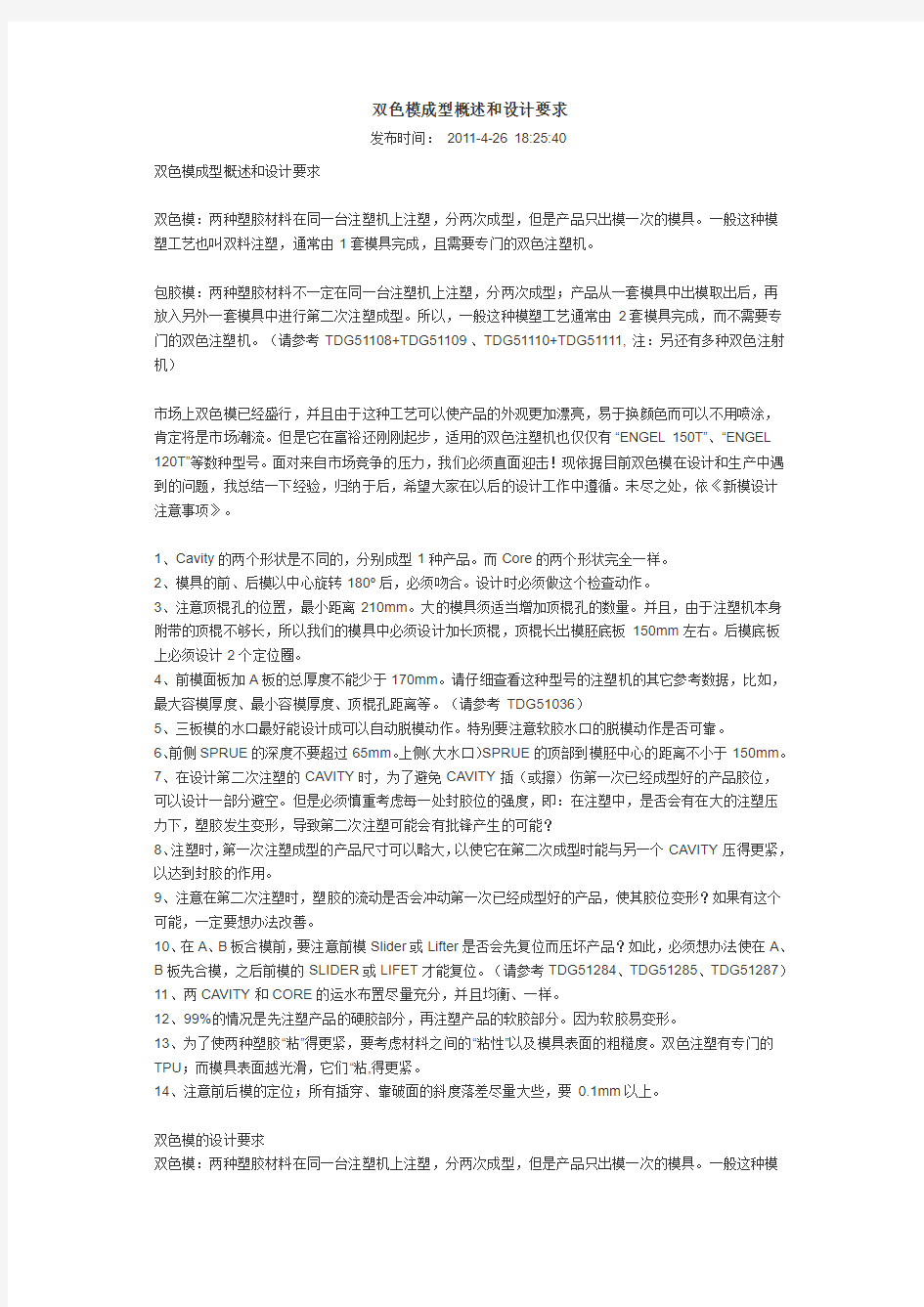
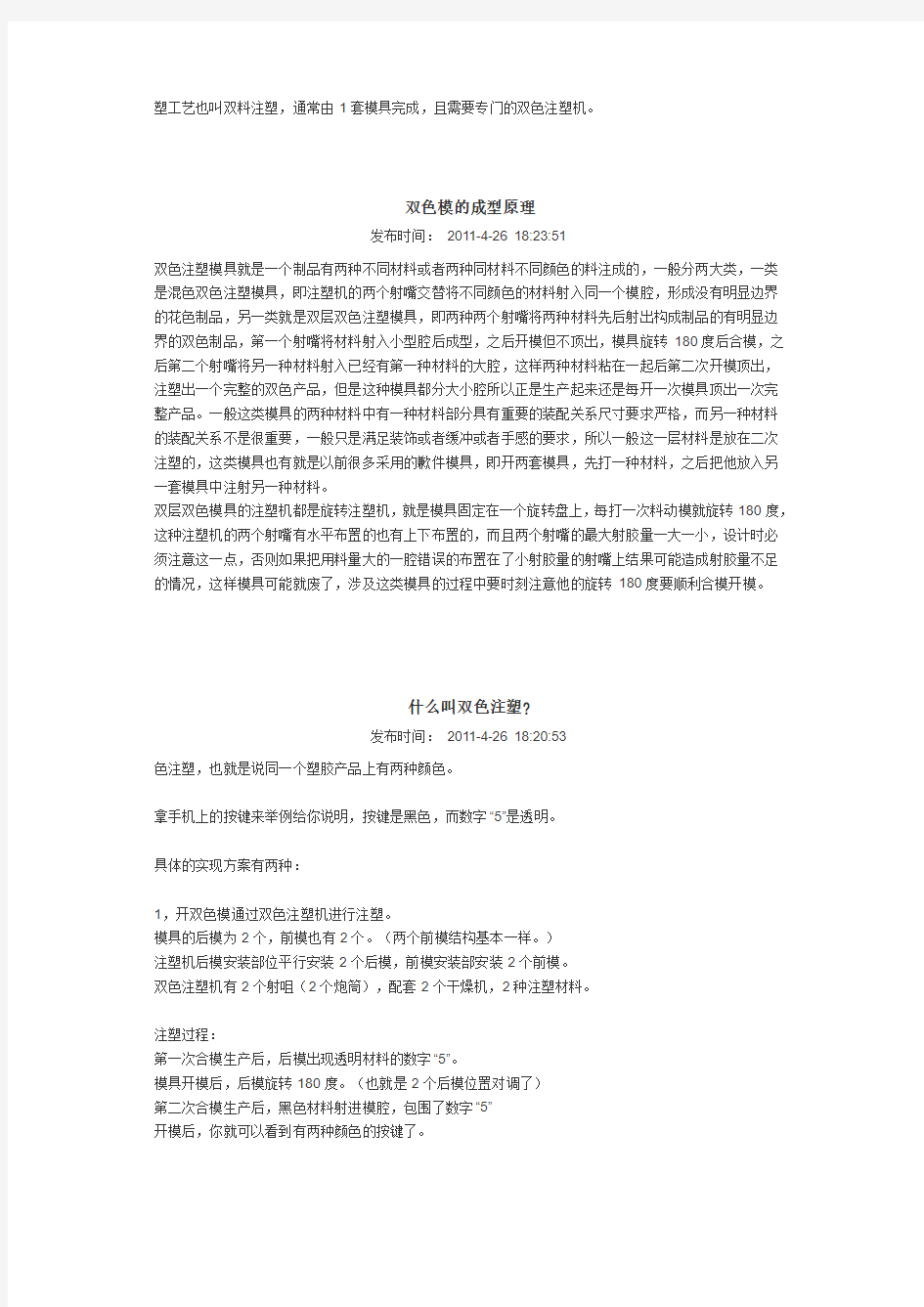
双色模成型概述和设计要求
发布时间:2011-4-26 18:25:40
双色模成型概述和设计要求
双色模:两种塑胶材料在同一台注塑机上注塑,分两次成型,但是产品只出模一次的模具。一般这种模塑工艺也叫双料注塑,通常由1套模具完成,且需要专门的双色注塑机。
包胶模:两种塑胶材料不一定在同一台注塑机上注塑,分两次成型;产品从一套模具中出模取出后,再放入另外一套模具中进行第二次注塑成型。所以,一般这种模塑工艺通常由2套模具完成,而不需要专门的双色注塑机。(请参考TDG51108+TDG51109、TDG51110+TDG51111,注:另还有多种双色注射机)
市场上双色模已经盛行,并且由于这种工艺可以使产品的外观更加漂亮,易于换颜色而可以不用喷涂,肯定将是市场潮流。但是它在富裕还刚刚起步,适用的双色注塑机也仅仅有“ENGEL 150T”、“ENGEL 120T”等数种型号。面对来自市场竞争的压力,我们必须直面迎击!现依据目前双色模在设计和生产中遇到的问题,我总结一下经验,归纳于后,希望大家在以后的设计工作中遵循。未尽之处,依《新模设计注意事项》。
1、Cavity的两个形状是不同的,分别成型1种产品。而Core的两个形状完全一样。
2、模具的前、后模以中心旋转180o后,必须吻合。设计时必须做这个检查动作。
3、注意顶棍孔的位置,最小距离210mm。大的模具须适当增加顶棍孔的数量。并且,由于注塑机本身附带的顶棍不够长,所以我们的模具中必须设计加长顶棍,顶棍长出模胚底板150mm左右。后模底板上必须设计2个定位圈。
4、前模面板加A板的总厚度不能少于170mm。请仔细查看这种型号的注塑机的其它参考数据,比如,最大容模厚度、最小容模厚度、顶棍孔距离等。(请参考TDG51036)
5、三板模的水口最好能设计成可以自动脱模动作。特别要注意软胶水口的脱模动作是否可靠。
6、前侧SPRUE的深度不要超过65mm。上侧(大水口)SPRUE的顶部到模胚中心的距离不小于150mm。
7、在设计第二次注塑的CAVITY时,为了避免CAVITY插(或擦)伤第一次已经成型好的产品胶位,可以设计一部分避空。但是必须慎重考虑每一处封胶位的强度,即:在注塑中,是否会有在大的注塑压力下,塑胶发生变形,导致第二次注塑可能会有批锋产生的可能?
8、注塑时,第一次注塑成型的产品尺寸可以略大,以使它在第二次成型时能与另一个CAVITY压得更紧,以达到封胶的作用。
9、注意在第二次注塑时,塑胶的流动是否会冲动第一次已经成型好的产品,使其胶位变形?如果有这个可能,一定要想办法改善。
10、在A、B板合模前,要注意前模Slider或Lifter是否会先复位而压坏产品?如此,必须想办法使在A、B板先合模,之后前模的SLIDER或LIFET才能复位。(请参考TDG51284、TDG51285、TDG51287)
11、两CAVITY和CORE的运水布置尽量充分,并且均衡、一样。
12、99%的情况是先注塑产品的硬胶部分,再注塑产品的软胶部分。因为软胶易变形。
13、为了使两种塑胶“粘”得更紧,要考虑材料之间的“粘性”以及模具表面的粗糙度。双色注塑有专门的TPU;而模具表面越光滑,它们“粘…得更紧。
14、注意前后模的定位;所有插穿、靠破面的斜度落差尽量大些,要0.1mm以上。
双色模的设计要求
双色模:两种塑胶材料在同一台注塑机上注塑,分两次成型,但是产品只出模一次的模具。一般这种模
塑工艺也叫双料注塑,通常由1套模具完成,且需要专门的双色注塑机。
双色模的成型原理
发布时间:2011-4-26 18:23:51
双色注塑模具就是一个制品有两种不同材料或者两种同材料不同颜色的料注成的,一般分两大类,一类是混色双色注塑模具,即注塑机的两个射嘴交替将不同颜色的材料射入同一个模腔,形成没有明显边界的花色制品,另一类就是双层双色注塑模具,即两种两个射嘴将两种材料先后射出构成制品的有明显边界的双色制品,第一个射嘴将材料射入小型腔后成型,之后开模但不顶出,模具旋转180度后合模,之后第二个射嘴将另一种材料射入已经有第一种材料的大腔,这样两种材料粘在一起后第二次开模顶出,注塑出一个完整的双色产品,但是这种模具都分大小腔所以正是生产起来还是每开一次模具顶出一次完整产品。一般这类模具的两种材料中有一种材料部分具有重要的装配关系尺寸要求严格,而另一种材料的装配关系不是很重要,一般只是满足装饰或者缓冲或者手感的要求,所以一般这一层材料是放在二次注塑的,这类模具也有就是以前很多采用的歉件模具,即开两套模具,先打一种材料,之后把他放入另一套模具中注射另一种材料。
双层双色模具的注塑机都是旋转注塑机,就是模具固定在一个旋转盘上,每打一次料动模就旋转180度,这种注塑机的两个射嘴有水平布置的也有上下布置的,而且两个射嘴的最大射胶量一大一小,设计时必须注意这一点,否则如果把用料量大的一腔错误的布置在了小射胶量的射嘴上结果可能造成射胶量不足的情况,这样模具可能就废了,涉及这类模具的过程中要时刻注意他的旋转180度要顺利合模开模。
什么叫双色注塑?
发布时间:2011-4-26 18:20:53
色注塑,也就是说同一个塑胶产品上有两种颜色。
拿手机上的按键来举例给你说明,按键是黑色,而数字“5”是透明。
具体的实现方案有两种:
1,开双色模通过双色注塑机进行注塑。
模具的后模为2个,前模也有2个。(两个前模结构基本一样。)
注塑机后模安装部位平行安装2个后模,前模安装部安装2个前模。
双色注塑机有2个射咀(2个炮筒),配套2个干燥机,2种注塑材料。
注塑过程:
第一次合模生产后,后模出现透明材料的数字“5”。
模具开模后,后模旋转180度。(也就是2个后模位置对调了)
第二次合模生产后,黑色材料射进模腔,包围了数字“5”
开模后,你就可以看到有两种颜色的按键了。
2,由于双色注塑机机器比较贵,很多公司用了另外的办法。模具一样要开两套,加工过程如下:
先利用一般的注塑机,将透明产品数字“5”做出来,
然后将透明产品“5”放到另一套模具里注塑黑色材料。
这样,产品出来后也是双色的。
属于两次成型。
双色注塑技术及工作原理(精)
双色注塑技术工及作原理 分流道设计由于本成型由 2个相互垂直的浇注系统同时注射不同型腔, 所以 2个型腔分别根据浇注形式布置不同的流道系统。旋转顶出机构原理根据塑件结构特点,这里采用先顶出再旋转的型腔互换步骤。由于这种成型方法特殊,模具整体结构呈中心对称,只是镶体和本体的型芯和型腔不同, 流道也不对称。模具上分布有 4个定模导柱、 2个回转板导柱。整副模具采用一模 2个本体和 2个镶体的布局。本模具的特点是不需要专设顶出油缸, 通过自身的机构可以充分利用注塑机的顶出油缸来实现旋转体的推出和塑件的顶出。并由斜块锁紧机构承担旋转体的重量,避免导柱受力。 该推出旋转机构的工作原理如下:开模到合理距离。向前顶出轴套 2,带动弹压挡块 4向前运动。由于拉簧 1处于受拉状态,所以旋转轴 22不会向前推出。弹压挡块 4向前运动,带动推板 a 向前运动, 推板 a 上的顶杆推动推板 b ,推板 b 带动推杆顶出塑件。油缸推出距离为 20mm 。弹压挡块 4继续向前运动,就会碰到斜楔块 7,斜楔块 7挤压弹压挡块,并使其向上运动,直到脱离轴肩。此时由顶杆外的弹簧使推板a 复位。同时推板 b 也在复位弹簧 19和限位螺栓 21的共同作用下复位。油缸推出距离为 30mm 。顶出轴套 2再向前运动,带动旋转轴向前运动, 由旋转轴带动动模和动模固定板向前运动, 直至可旋转位置。油缸推出距离为 120mm 。油缸 10启动,带动齿条,再由齿轮齿条配合带动旋转轴 22,通过键传动,带动动模和动模垫板 一起旋转。旋转角为 180。顶出轴套 2回程,通过螺栓 3带动旋转轴及旋转机构复位,并由导向机构导向,斜块定位。合模,进行物料充填。 模具工作的复杂程度和精密度都大大提高了, 所以相应的设备成本昂贵,模具设计复杂、精密,成型工艺控制难度增加。与国外相比, 国内双色注塑技术的应用还有待发展, 随着国内塑料成型技术的不断发展,塑料双色注射成型技术必将被广泛应用。
双色注塑模具设计36条经典经验分享——【塑胶件设计资料】
双色注塑模具设计36条经典经验分享! 1.双色模设计的基本原则: (1)硬胶做1次,软胶做2次; (2)透明做1次,非透明做2次; (3)成型温度高的塑料做1次,成型温度低的做2次; 上述是做双色模的基本原则,否则模具会白做;另外,封胶时尽量用靠破封胶,而不用插破封胶,哪怕是建议客户修改产品也要尽量必为靠破封胶; 2. 模胚导柱导套必须上下左右对称,前后模对称。 3. 后模要旋转180度,前模不动。 4. 产品间距必须以注塑机炮嘴的间距为准,国外有的双色注塑机的炮嘴间距是可调的,有的不可调,国内的不可调。 5. 两个独立的顶出系统,顶棍也是两个。后模两个产品相同,顶针都相同,是旋转关系,切不可做成平移关系。 6. 顶针板只能用弹簧复位,不可用螺丝强制复位,因为后模要旋转。 7. 边锁必须在模具中心的四边,且前后模对称,否则当后模旋转180后与前模对不上。 8. 如果进胶点间距和注塑机炮嘴间距不同,顶棍孔要做成腰型的,因为注塑机顶棍间距不可调。注意国产双色注塑机大部分注塑炮嘴不可调。 1
9. 注意客户提供的注塑机平行炮嘴的方向,是x轴或是y轴,以此来定产品排位的布局。 10. 运水进出水的方向必须在天地侧,且每一个循环水的进出都必须在同一面上,不可进水在天,出水在地侧,因为后模要旋转180度,要注意模胚大小不可超过注塑机出水槽的高度,否则无法接运水。 11. 第一次注塑的产品要放在非操作侧,因为第一次注塑后产品要旋转180度进行第二次注塑,正好转到操作侧,方便取产品。 12. 出口模的码模位要在操作侧和非操作侧,不可在天地侧,因为他们的产品要全自动。 13. 分型面的注意事项:后模分型面要将两个产品合并后取得的分型面为后模的;前模分型面要取单个产品的即可,不可取合并后的产品分型面。 14. 前后法兰的公差为负0.05mm,两法兰间距公差为正负0.02mm,顶棍与顶棍孔的间隙单边为0.1mm,前后模导套导柱的中心距公差为正负0.01,模框四边和深度都要加公差,否则当后模旋转180度后,因高低不一致而产生批锋。框深公差为负0.02mm。 15. 如果在模胚厂已经将模胚加工完,本厂要加工唧嘴和顶棍孔时,要以4个导柱导套孔的间距中心为基准取数,否则偏差太多,容易卡死模。订模胚时要注明是双色模胚,四个导柱导套和框对称,后模旋转180度后能与前模匹配。 1
干货分享-双色模具设计经验总结
双色注塑模具经典经验分享 1.双色模设计的基本原则: (1)硬胶做1次,软胶做2次; (2)透明做1次,非透明做2次; (3)成型温度高的塑料做1次,成型温度低的做2次; 上述是做双色模的基本原则,否则模具会白做;另外,封胶时尽量用靠破封胶,而不用插破封胶,哪怕是建议客户修改产品也要尽量必为靠破封胶; 2.模胚导柱导套必须上下左右对称,前后模对称。 3.后模要旋转180度,前模不动。 4.产品间距必须以注塑机炮嘴的间距为准,国外有的双色注塑机的炮嘴间距是可调的,有的不可调,国内的不可调。 5.两个独立的顶出系统,顶棍也是两个。后模两个产品相同,顶针都相同,是旋转关系,切不可做成平移关系。 6.顶针板只能用弹簧复位,不可用螺丝强制复位,因为后模要旋转。 7.边锁必须在模具中心的四边,且前后模对称,否则当后模旋转180后与前模对不上。 8.如果进胶点间距和注塑机炮嘴间距不同,顶棍孔要做成腰型的,因为注塑机顶棍间距不可调。注意国产双色注塑机大部分注塑炮嘴不可调。 9.注意客户提供的注塑机平行炮嘴的方向,是x轴或是y轴,以此来定产品排位的布局。 10.运水进出水的方向必须在天地侧,且每一个循环水的进出都必须在同一面上,不可进水在天,出水在地侧,因为后模要旋转180度,要注意模胚大小不可超过注塑机出水槽的高度,否则无法接运水。 11.第一次注塑的产品要放在非操作侧,因为第一次注塑后产品要旋转180度进行第二次注塑,正好转到操作侧,方便取产品。 12.出口模的码模位要在操作侧和非操作侧,不可在天地侧,因为他们的产品要全自动。 13.分型面的注意事项:后模分型面要将两个产品合并后取得的分型面为后模的;前模分型面要取单个产品的即可,不可取合并后的产品分型面。
双色模设计原理及Moldflow分析
双色模设计原理及Moldflow分析 一. 双色模分类 双色模(Overmolding):两种塑胶材料在同一台注塑机上注塑,分两次成型,但是产品只出模一次的模具。一般这种模塑工艺也叫双料注塑,通常由两幅模具,一半装在机器的固定板上,另一半装在回转板上. 两幅模具的公模是完全一样的,一次母模和二次母模不一样。当第一种颜色的塑料注塑完毕,公母模打开一次,公模带着一次产品旋转180 度,到达第二种颜色注塑的位置上,进行二次注射,即可取得双色制件.如此循环,每个成型周期内都会有一模一次产品及二次产品产生(如图1、3所示). 包胶模(Insert Molding):有时又叫假双色,两种塑胶材在不同注塑机上注塑,分两次成型;产品从一套模具中出模取出后,再放入另外一套模具中进行第二次注塑成型(所以我们把第一射叫做insert)。一般这种模塑工艺通常由2套模具完成,而不需要专门的双色注塑机(图2)。 二. 选择双色模具,一般不外乎以下几种情况. 1)產品功能的要求. 例如电源开关,手机按键,键盘指示灯,汽车开关等,要求LED的部分能够透光.例如电源开关按钮,LED 灯需要透光 2)改善手感. 一些手持產品,要求在手持部位使用Rubber,手感会比较舒适. 例如对讲机外壳, 电动工具把手,扳手,起子把手,牙刷柄,保温杯等. 3)增加美感,作為装饰品. 如一些外观件的Logo,如果採用双色注塑,又漂亮又不用担心它会被摩掉. 4)產品局部区域需要电镀.在塑料家族中,只有ABS 和聚砜(PSU)表面可以电镀, 如果要求產品的局部区域或者单侧需要电镀,就要把电镀区域注射為ABS,把不需要电镀的区域注射為其他材料如PC 等. 三. 双色模设计要求 目前市场上双色模已经非常普遍,并且由于这种工艺可以使产品的外观更加漂亮,易于换颜色而可以不用喷涂,非常符合市场潮流。双色模具再设计要点归纳如下: 1) Cavity的两个形状是不同的,分别成型1种产品,而Core的两个形状完全一样。 2) 模具的前、后模以中心旋转180度后,必须吻合。设计时必须做这个检查动作。 3) 注意顶棍孔的位置,最小距离210mm。大的模具须适当增加顶棍孔的数量。并且,由于注塑机本身附带的顶棍不够长,所以我们的模具中必须设计加长顶棍,顶棍长出模胚底板150mm左右。后模底板上必须设计2个定位圈。 4) 前模面板加A板的总厚度不能少于170mm。请仔细查看这种型号的注塑机的其它参考数据,比如,最大容模厚度、最小容模厚度、顶棍孔距离等。 5) 三板模的水口最好能设计成可以自动脱模动作。特别要注意软胶水口的脱模动作是否可靠。 6) 前侧SPRUE的深度不要超过65mm。上侧(大水口)SPRUE的顶部到模胚中心的距离不小于150mm。
双色注塑
双射注塑 一.简介 双射注塑(Bi-color injection)顾名思义就是一个部件用两种塑胶注塑来实现。广义的双射注塑包括over molding,通过普通的注塑机,两次注塑来实现,狭义的双射注塑是指利用双射注塑机,将两种不同的塑料在同一机台注塑完成部件,常见的是旋转式的。前者对设备要求不高,但是生产效率低下,基本只适用于要求不高度软、硬胶两种材料的成型1,后者的适用范围和产品质量好,生产效率高,是目前的趋势。 我们主要介绍以双射注塑机注塑的双射注塑。这样我们首先从认识双射注塑机和双射注塑模具。注塑机的动模侧的转盘如下图所示, 上面可以固定两个模具的动模,有两组和顶杆,它可以在开模后,先是将第二射的动模产品顶出,机械手取出产品,接着将上面固定的两套模具的动模旋转,从而将第一射完成的产品放到了另外一边,准备第二次注射,而第一射的动模侧换成了空的。周而复始,产品不断完成注塑。注意点是,第一次注塑时候,第二射是将整个模腔填满,注意脱模。当然注塑机在定模侧拥有两个料管,分别注塑不同的塑料。双射注塑的模具拥有自身的特点: 1.动模是一样的,因为是旋转的,需要交换的,所以必须是一模一样的。所以先成型的是动模侧的先成型的一般都是靠动模侧的(有特例,成型时候型腔可以不一样2) 2.模具的第一射的流道注塑完成后,是不能留在模具上的,最好是热浇道,不然也是可以用机械手抓取的,最差的也是潜伏类浇口,可以自动脱落,否则会浇口在上面第二射没法阖上模具。
3.产品两次射出,产品开模后,第一射必须留在动模侧,这个比较好理解,如果留在了定模侧,旋转就没用了,就变成了单色注塑机了,就一般情况而言,一般都是选择将两射的产品都是留在动模侧的,所以模具需要开闭器、拉杆等实现顺序开模,先拉开定模侧,在定模侧需要加顶出机构, 4.两组冷却系统,因为双射注塑的要求两种材料不一样,原则上要求第一射的材料的温度比第二射高出60度,可以根据实际情况而定,这个后面再讨论,因为材料不一样,模具的模温不一样,所以需要配备两套冷却系统。 二.设计要点 了解了注塑机和模具以后,我们下一定面接着讲下双射产品设计的要点,双射注塑中有无透明材料是完全不同的做法,另外如果透明材料是做主镜片是其中最难的。下面让我们从简单的说起,硬胶和软胶的组合,在手机应用就是做塞子等。 2.1 软硬、胶双射设计 1.两种材料必需熔点存在一定的温度差,一般推荐值是60度,视具体情况而定,建议至少保证30度以上的熔点温差,第一射材料的熔点温度较高,否则很容易第二射的材料将第一射材料融化。对于这一类注塑很容易实现,一般第一射是PC或者PC/ABS,第二射是TPU或者TPE等。PC厚度需要预留0.6-0.7mm,软胶预留0.4mm以上。 2尽量加宽接触面积,做些沟槽等,增加粘合力,避免分层和裂开等问题;还可以考虑在第一射采用抽芯,将第二射部分材料注塑到第一射里面,增加贴合的可靠性;第一射的模具表面尽量做粗糙,让模具厂在贴合表面部分用电极粗加工夏米尔VDI24#电火花纹路到位,不用抛光。 3.小零件提高成型效率,尽量考虑第一射用热浇道来做,模具可以做的比较小,潜伏式浇口料头乱飞,旁边还有一套模具,容易出问题,三板模效率太低,并且浪费材料,具体可以视厂家的条件而定。 2.2 透明的和非透明的双射设计 接着一种就是透明材料和非透明材料组合的情形,这种里面透明材料可以作为装饰用,或者只是用来做小屏镜片。 2.2.1小屏镜片的双射设计
双色注塑实例
这是一款手机护套,如下图 产品分析: 此款为某品牌手机的外圈护套,由二种塑料(PC+TPE)组成。由于要求外形美观光滑,分模线必须做在内侧圆弧切点,所以外模要四面滑开,再看内侧,四周全部是内扣的,必须全方位内抽芯,也就是俗称的“爆炸芯”。 关于“爆炸芯”的模具结构,假如是普通的注塑模具,已经有非常经典的机构,我下面将有详细的介绍。现在问题是双色模具,有二组动模和二组定模,二组动模的所有部件是完全一致的,要在双色注塑机的转盘上进行180度旋转,二种不同的塑料分别射进模腔,注射硬胶(PC)时动模的顶出机构和抽芯机构不动作,再注射软胶(TPE)并开模后,对准软胶料筒的一侧的动模的抽芯机构和顶出机构才开始动作,将完整的双色制品顶出。由于动模旋转后,交换又合模后的浇口必须在同一位置,所以软胶和硬胶的浇口的处理显得令人困惑。
由于模具必须四周都要进行“内外同抽”,内、外滑块怎样排列,轨道设置在哪里?这个问题同样有被逼入墙角的感觉。 且不谈模具滑块机构的复杂性,我们从双色模具的基本原理来考虑,硬胶部分的成型和内外同抽机构是一定要设置在定模一侧的,软胶部分的成型机构也要设置在定模。而且这个部分是由内外同抽的机构组成的凸起插入到动模的凹槽中。转盘旋转180度后,这组凸起刚好插入到另外一个动模的凹槽中。也就是说,二个定模上的由内外同抽滑块组成的凸起的外部形状和尺寸是完全相同的。仅仅是成型软胶和硬胶的型面不同而已。 问题的难点是,这个凸起会分成上下二层,一层向外移动,另一层向内移动,也就是俗称的“内外同抽”,合成的凸起的侧面是一个统一的斜面,但是,传统的滑块必须要有滑动轨道等必要的条件,怎样设置轨道?这便成了本案例的核心问题。 我是这样设置动模部分的凹槽和定模部分凸起的。
双色模的设计要求(精)
双色模的设计要求.txt机会就像秃子头上一根毛,你抓住就抓住了,抓不住就没了。我和你说了10分钟的话,但却没有和你产生任何争论。那么,我们之间一定有个人变得虚伪无比!过错是短暂的遗憾,错过是永远的遗憾。相遇是缘,相知是份,相爱是约定,相守才是真爱。双色模的设计要求双色模:两种塑胶材料在同一台注塑机上注塑,分两次成型,但是产品只出模一次的模具。一般这种模塑工艺也叫双料注塑,通常由1套模具完成,且需要专门的双色注塑机。$ ]1 t; x$ c( x% @ 包胶模:两种塑胶材料不一定在同一台注塑机上注塑,分两次成型;产品从一套模具中出模取出后,再放入另外一套模具中进行第二次注塑成型。所以,一般这种模塑工艺通常由2套模具完成,而不需要专门的双色注塑机。(请参考TDG51108+TDG51109、TDG51110+TDG51111)市场上双色模已经盛行,并且由于这种工艺可以使产品的外观更加漂亮,易于换颜色而可以不用喷涂,肯定将是市场潮流。但是它在富裕还刚刚起步,适用的双色注塑机也仅仅只有“ENGEL 150T”、“ENGEL 120T”两个型号。面对来自市场竞争的压力,我们必须直面迎击!现依据目前双色模在设计和生产中遇到的问题,我总结一下经验,归纳于后,希望大家在以后的设计工作中遵循。未尽之处,依《新模设计注意事项》。 1,Cavity的两个形状是不同的,分别成型1种产品。而Core的两个形状完全一样。2,模具的前、后模以中心旋转180o后,必须吻合。设计时必须做这个检查动作。3,注意顶棍孔的位置,最小距离210mm。大的模具须适当增加顶棍孔的数量。并且,由于注塑机本身附带的顶棍不够长,所以我们的模具中必须设计加长顶棍,顶棍长出模胚底板150mm左右。+ |! J f2 ^7 m+ D% A0 M% K5 ^3 E 后模底板上必须设计2个定位圈。 4,前模面板加A板的总厚度不能少于170mm。请仔细查看这种型号的注塑机的其它参考数据,比如,最大容模厚度、最小容模厚度、顶棍孔距离等。(请参考TDG51036) 5,三板模的水口最好能设计成可以自动脱模动作。特别要注意软胶水口的脱模动作是否可靠。 6,前侧SPRUE的深度不要超过 65mm。上侧(大水口)SPRUE的顶部到模胚中心的距离不小于150mm。 7,在设计第二次注塑的CAVITY时,为了避免CAVITY插(或擦)伤第一次已经成型好的产品胶位,可以设计一部分避空。但是必须慎重考虑每一处封胶位的强度,即:在注塑中,是否会有在大的注塑压力下,塑胶发生变形,导致第二次注塑可能会有
双色模具设计及双色注塑成型的36条经验
双色模具设计及双色注塑成型的36条经验: 1.双色模设计的基本原则: (1.)硬胶做1次,软胶做2次; (2.)透明做1次,非透明做2次; (3.)成型温度高的塑料做1次,成型温度低的做2次; 上述是做双色模的基本原则,否则模具会白做;另外,封胶时尽量用靠破封胶,而不用插破封胶,哪怕是建议客户修改产品也要尽量必为靠破封胶; 2.模胚导柱导套必须上下左右对称,前后模对称。 3.后模要旋转180度,前模不动。 4. 产品间距必须以注塑机炮嘴的间距为准,国外有的双色注塑机的炮嘴间距是可调的,有的不可调,国内的不可调。 5. 两个独立的顶出系统,顶棍也是两个。后模两个产品相同,顶针都相同,是旋转关系,切不可做成平移关系。 6. 顶针板只能用弹簧复位,不可用螺丝强制复位,因为后模要旋转。 7. 边锁必须在模具中心的四边,且前后模对称,否则当后模旋转180后与前模对不上。 8. 如果进胶点间距和注塑机炮嘴间距不同,顶棍孔要做成腰型的,因为注塑机顶棍间距不可调。注意国产双色注塑机大部分注塑炮嘴不可调。 9. 注意客户提供的注塑机平行炮嘴的方向,是X轴或是Y轴,以此来定产品排位的布局。 10. 运水进出水的方向必须在天地侧,且每一个循环水的进出都必须在同一面上,不可进水在天,出水在地侧,因为后模要旋转180度,要注意模胚大小不可超过注塑机出水槽的高度,否则无法接运水。 11. 第一次注塑的产品要放在非操作侧,因为第一次注塑后产品要旋转180度进行第
二次注塑,正好转到操作侧,方便取产品。 12. 出口模的码模位要在操作侧和非操作侧,不可在天地侧,因为他们的产品要全自动。 13. 分型面的注意事项:后模分型面要将两个产品合并后取得的分型面为后模的;前模分型面要取单个产品的即可,不可取合并后的产品分型面。 14. 前后法兰的公差为负0.05mm,两法兰间距公差为正负0.02mm,顶棍与顶棍孔的间隙单边为 0.1mm,前后模导套导柱的中心距公差为正负0.01,模框四边和深度都要加公差,否则当后模旋转180度后,因高低不一致而产生批锋。框深公差为负0.02mm。15.如果在模胚厂已经将模胚加工完,本厂要加工唧嘴和顶棍孔时,要以4个导柱导套孔的间距中心为基准取数,否则偏差太多,容易卡死模。订模胚时要注明是双色模胚,四个导柱导套和框对称,后模旋转180度后能与前模匹配。 16. 如果是后模旋转的双色话就简单多了..两个前模芯一样...一边注塑好硬胶后.旋转180度(注意产品转的时候不能掉落,浇口可以自动分离) , 转到另外一边后再注塑软胶...注塑硬胶无需布置顶针...只需布置在软胶这边模芯即可...另外缩水要注意...如果软胶完全把硬胶缠住..则只需放硬胶的缩水...如果是轮廓相接则硬胶软胶都要放缩水。 17. 如果是一套模具的双色模具的话 ,那就是一个直炮筒,一个90度的炮筒射胶,不需要旋转,只需一个模芯,软胶与硬胶的分离方法靠行位封胶。 18. Cavity的两个外形是不同的,分别成型1种产品。而Core的两个外形完好一样。 19.模具的前、后模以中心旋转180°后,必需吻合。设计时必需做这个检查动作。 20. 留意顶针孔的位置,最小间隔210mm。大的模具须恰当增加顶棍孔的数量。并且,由于注塑机本身附带的顶针不够长,所以我们的模具中必需设计加长顶针,顶针长出模胚底板150mm左右。 21. 后模底板上必需设计2个定位圈。
双色注塑模具设计30个经验分享
双色注塑模具设计30 个经验分享 双色注塑模具的设计过程有哪些经验呢?为大家盘点如下! 欢迎查看! 1. 双色注塑模具设计的基本原则: (1) 硬胶做1 次,软胶做2 次; (2) 透明做1 次,非透明做2 次; (3) 注塑成型温度高的塑料做1 次,成型温度低的做2 次; 2. 模胚导柱、导套必须上下左右对称,前后模对称。 3. 后模要旋转180 度,前模不动。 4. 产品间距必须以注塑机炮嘴的间距为准,国外有的双色注塑机的炮嘴间距是可调的,有的不可调,国内的不可调。 5. 两个独立的顶出系统,顶棍也是两个。后模两个产品相同,顶针都相同,是旋转关系,切不可做成平移关系。 6. 顶针板只能用弹簧复位,不可用螺丝强制复位,因为后模要旋转。 7. 边锁必须在模具中心的四边,且前后模对称,否则,当后模旋转180 度后,与前模对不上,就不好了。 8. 如果进胶点间距和注塑机炮嘴间距不同,顶棍孔要做成腰型的,因为注塑机顶棍间距不可调。注意:国产双色注塑机大部分注塑炮嘴不可调。 9. 注意客户提供的注塑机平行炮嘴方向,是X 轴或Y 轴,以此来定
产品排位的布局 10. 运水进出水的方向必须在天地侧,且每一个循环水的进出都 必须在同一面上,不可进水在天,出水在地侧,因为后模要旋转180 度,要注意模胚大小不可超过注塑机出水槽的高度,否则,无法接运水。 11. 第一次注塑的产品要放在非操作侧,因为第一次注塑后,产品要旋转180 度进行第二次注塑,正好转到操作侧,方便取产品。 12. 出口模的码模位,要在操作侧和非操作侧,不可在天地侧,因为他们产品要全自动。 13. 分型面的注意事项:后模分型面要将两个产品合并后取得的 分型面为后模的; 前模分型面要取单个产品的即可,不可取合并后的产品分型面。 14. 前后法兰的公差为负0.05mm两法兰间距公差为正负 0.02mm顶棍与顶棍孔的间隙单边为0.1mm前后模导套导柱的中心距公差为正负0.01 ,模框四边和深度都要加公差,否则,当后模旋转180 度后,因高低不一致而产生批锋; 框深公差为负0.02mm。 15. 如果在模胚厂已经将模胚加工完,本厂要加工唧嘴和顶棍孔时,要以4个导柱导套孔的间距中心为基准取数,否则偏差太多,容易卡死模。订模胚时,要注明是双色模胚,四个导柱导套和框对称,后模旋转180 度后能与前模匹配。 16. 如果是一套模具的双色模具的话,那就是一个直炮筒,一个90 度的炮筒射胶,不需要旋转,只需一个模芯,软胶与硬胶的分离方法
双色模具的设计及注塑成型
双色模具的设计及注塑成型 双色模具的设计及注塑成型 双色模具是指两种塑胶材料在同一台注塑机上注塑,分两次成型,但是产品只出模一次的模具。一般这种模塑工艺也叫双料注塑,通常由一套模具完成,且需要专门的双色注塑机。双色模具目前市场上日益盛行,这种工艺可以使产品的外观更加漂亮,易于换颜色而可以不用喷涂,但对设计及注塑成型的要求高。 1.双色模设计的基本原则: (1)硬胶做1次,软胶做2次; (2)透明做1次,非透明做2次; (3)成型温度高的塑料做1次,成型温度低的做2次; 上述是做双色模的基本原则,否则模具会白做;另外,封胶时尽量用靠破封胶,而不用插破封胶,哪怕是建议客户修改产品也要尽量必为靠破封胶。 2.模胚导柱导套必须上下左右对称,前后模对称。 3.后模要旋转180度,前模不动。 4.产品间距必须以注塑机炮嘴的间距为准,国外有的双色注塑机的炮嘴间距是可调的,有的不可调,国内的不可调。 5.两个独立的顶出系统,顶棍也是两个。后模两个产品相同,顶针都相同,是旋转关系,切不可做成平移关系。 6.顶针板只能用弹簧复位,不可用螺丝强制复位,因为后模要旋转。 7.边锁必须在模具中心的四边,且前后模对称,否则当后模旋转180后与前模对不上。 8.如果进胶点间距和注塑机炮嘴间距不同,顶棍孔要做成腰型的,因为注塑机顶棍间距不可调。注意国产双色注塑机大部分注塑炮嘴不可调。 9.注意客户提供的注塑机平行炮嘴的方向,是X轴或是Y轴,以此来定产品排位的布局。 10.运水进出水的方向必须在天地侧,且每一个循环水的进出都必须在同一面上,不可进水在天,出水在地侧,因为后模要旋转180度,要注意模胚大小不可超过注塑机出水槽的高度,否则无法接运水。 11.第一次注塑的产品要放在非操作侧,因为第一次注塑后产品要旋转180度进行第二次注塑,正好转到操作侧,方便取产品。 12.出口模的码模位要在操作侧和非操作侧,不可在天地侧,因为他们的产品要全自动。 13.分型面的注意事项:后模分型面要将两个产品合并后取得的分型面为后模的;前模分型面要取单个产品的即可,不可取合并后的产品分型面。 14.前后法兰的公差为负0.05mm,两法兰间距公差为正负0.02mm,顶棍与顶棍孔的间隙单边为0.1mm,前后模导套导柱的中心距公差为正负0.01mm,模框四边和深度都要加公差,否则当后模旋转180度后,因高低不一致而产生批锋。框深公差为负0.02mm。 15.如果在模胚厂已经将模胚加工完,本厂要加工唧嘴和顶棍孔时,要以4个导柱导套孔的间距中心为基准取数,否则偏差太多,容易卡死模。订模胚时要注明是双色模胚,四个导柱导套和框对称,后模旋转180度后能与前模匹配。 16.如果是后模旋转的双色话就简单多了..两个前模芯一样...一边注塑好硬胶后.旋转180度(注意产品转的时候不能掉落,浇口可以自动分离) , 转到另外一边后再注塑软胶...注塑硬胶无需布置顶针...只需布置在软胶这边模芯即可...另外缩水要注意...如果软胶完全把硬胶缠住..则只需放硬胶的缩水...如果是轮廓相接则硬胶软胶都要放缩水。 17.如果是一套模具的双色模具的话,那就是一个直炮筒,一个90度的炮筒射胶,不需要旋转,只需一个模芯,软胶与硬胶的分离方法靠行位封胶。 18.Cavity的两个外形是不同的,分别成型1种产品。而Core的两个外形完好一样。
双色注塑技术的原理及发展
双色注塑技术的原理及发展 作者:张林 摘要:双色注塑成型,是指将两种不同色泽的塑料注入同一模具的成型方法。它能使塑件出现两种不同的颜色,并能使塑件呈现有规则的图案或无规则的云纹状花色,以提高塑件的实用性和美观性。双色注塑成型作为现代工业中一种十分重要的加工法,用以生产各种板料零件,具有很多独特的优势,其成型件具有自轻重、刚度大、强度高、互换性好、成本低、生产过程便于实现机械自动化及生产效率高等优点。 关键词:双混色注塑成型;双花纹注塑成型;双色模具 引言 现代双色注塑生产是一种大规模继续作业的制造方式,由于高技术的参与和加入,双色注塑生产方式由初期的手工操作逐步转化成集团制作。生产过程逐步实现机械化、自动化、并且正在向集团化的方向发展。实现自动化双色注塑作业,体现安全、高效、节材等优点,已经是双色注塑发展的方向。 1.双色注塑成型原理 1.1双混色注塑成型 图1所示为双混色注塑成型原理。它有两个料筒,每个料筒的结构和使用均与普通注塑成型料筒相同。每个料筒都有各自的通道与喷嘴相通,在喷嘴通路中还装有启闭阀2,4。成型时,熔料在料筒中被塑化好后,由启闭阀2、4控制熔料进入喷嘴的先后顺序和排出料的比例,然后由喷嘴处注射入模腔。便可得到各种混色效果不同的塑料制品。 图1:双混色注塑成型原理 1—喷嘴 2—启闭阀3—料筒 4—启闭阀 5—料筒 1.2双花纹注塑成型原理 图2所示为双花纹注塑成型原理图。它也有两个料筒1和5,其喷嘴结构有些特殊,它除了有通常喷嘴的功能外,还能由安装在后部的齿轮3带动旋转。成型时,料筒1、5中分别塑化不同色彩的熔料,而齿轮3带动回转轴4回转,使不同色彩的熔料交替进入模腔,从而得到由中心向四周辐射形式的不同颜色和花纹的塑料制品。
浅谈双色注塑成型工艺
来源于:注塑塑胶网https://www.360docs.net/doc/9112575934.html, 浅谈双色注塑成型工艺 现在消费产品款式千变万化,既要外型美观、设计精巧,也要迅速配合市场需求。设计师一般因消费产品不同的用途,在不同的部位上,采用不同的物料,以应付特定环境的需要,达到延长产品寿命、增加美观及实用性的目的。这种实用性的设计要求无疑将导致生产技术也随之复杂化,双物料注塑工艺就是应这一潮流而生的。一般的双物料产品可以采用单色注塑机制造,基本上一台注塑机就可胜任,不过后加工工序相当费时复杂,直接影响产品的质量,总生产成本并不经济。双物料注塑工艺除了注塑机作出相应的改动外,模具设计的技巧是整项技术的灵魂。模具通过转动移位,达到同步注塑不同物料的效果。 模具设计大致分为两类:第一类有两个模腔,利用转动模式把半成型模件转移180度到另一个模腔内,其好处是使第一和第二工序可以同步进行;另一类是单一模腔,半制成品连同模具一起转动180度。设计上比较简单,但生产效率相应降低。由于模具或半成品需要转动,所以模具设计及注塑机的要求更为精密。 另外,由于双物料注塑的可变性很高,所以要达到生产顺利,符合预期理想,所有的模具设计必须与产品设计同步考虑,而且市面流行的双物料注塑机规格并 不统一,导致模具设计时考虑的问题更多;加上通用性少,模具制造商必须加倍留心。双物料制品一般以ABS、PC等硬塑料配合TPE软塑料为主,适合制造餐具、工具手柄、表壳、电话机外壳及按钮等制品。这使得生产企业在技术上必须注意三点:两类物料的融合性、产品的复杂性及注塑机的调校。例如,由于成本或应用的关系,采用的物料之间可能没有良好的粘合性,双物料注塑通常要在这方面进行更多地调试工作。更多的双色注塑问题精英注塑将会继续关注。 我国正逐步成为全球消费产品的生产制造基地,近年来华南地区塑料产品的制造商承接了许多需要双物料注塑技巧的订单,使双物料注塑技术在国内的应用日益广泛。 双射成型主要以双射成型机两只料管配合两套模具按先后次序经两次成型制成 双射产品。 比起传统射出成型,双料共射射出成型制程有如下的优点: 1核心料可以使用低黏度的材料来降低射出压力。 2从环保的考虑,核心料可以使用回收的二次料。 3根据不同的使用特性,如厚件成品皮层料使用软质料,核心料使用硬质料或者核心料可以使用发泡塑料来降低重量。 4可以利用较低质量的核心料以降低成本。 5 皮层料或核心料可使用价格昂贵且具特殊表面性质,如防电磁波干扰、高电导性等材料以增加产品性能。
双色模具的设计及注塑成型操作知识
双色模具的设计及注塑成型操作知识 双色模具是指两种塑胶材料在同一台注塑机上注塑,分两次成型,但是产品只出模一次的模具。一般这种模塑工艺也叫双料注塑,通常由一套模具完成,且需要专门的双色注塑机。双色模具目前市场上日益盛行,这种工艺可以使产品的外观更加漂亮,易于换颜色而可以不用喷涂,但对设计及注塑成型的要求高。 1.双色模设计的基本原则:(1)硬胶做1次,软胶做2次;(2)透明做1次,非透明做2次;(3)成型温度高的塑料做1次,成型温度低的做2次;上述是做双色模的基本原则,否则模具会白做;另外,封胶时尽量用靠破封胶,而不用插破封胶,哪怕是建议客户修改产品也要尽量必为靠破封胶。
2.模胚导柱导套必须上下左右对称,前后模对称。 3.后模要旋转180度,前模不动。 4.产品间距必须以注塑机炮嘴的间距为准,国外有的双色注塑机的炮嘴间距是可调的,有的不可调,国内的不可调。 5.两个独立的顶出系统,顶棍也是两个。后模两个产品相同,顶针都相同,是旋转关系,切不可做成平移关系。 6.顶针板只能用弹簧复位,不可用螺丝强制复位,因为后模要旋转。 7.边锁必须在模具中心的四边,且前后模对称,否则当后模旋转180后与前模对不上。 8.如果进胶点间距和注塑机炮嘴间距不同,顶棍孔要做成腰型的,因为注塑机顶棍间距不可调。注意国产双色注塑机大部分注塑炮嘴不可调。 9.注意客户提供的注塑机平行炮嘴的方向,是X轴或是Y轴,以此来定产品排位的布局。 10.运水进出水的方向必须在天地侧,且每一个循环水的进出都必须在同一面上,不可进水在天,出水在地侧,因为后模要旋转180度,要注意模胚大小不可超过注塑机出水槽的高度,否则无法接运水。 11.第一次注塑的产品要放在非操作侧,因为第一次注塑后产品要旋转180度进行第二次注塑,正好转到操作侧,方便取产品。 12.出口模的码模位要在操作侧和非操作侧,不可在天地侧,因为他们的产品要全自动。
什么是双色注塑
什么是双色注塑?双色注塑简述 https://www.360docs.net/doc/9112575934.html,/ 2007-5-30 13:51:40 Internet 什么是双色注塑?双色注塑简述 今天,消费产品款式千变万化,既要外型美观、设计精巧,也要迅速配合市场需求。设计师一般因消费产品不同的用途,在不同的部位上,采用不同的物料,以应付特定环境的需要,达到延长产品寿命、增加美观及实用性的目的。这种实用性的设计要求无疑将导致生产技术也随之复杂化,双物料注塑工艺就是应这一潮流而生的。一般的双物料产品可以采用单色注塑机制造,基本上一台注塑机就可胜任,不过后加工工序相当费时复杂,直接影响产品的质量,总生产成本并不经济。双物料注塑工艺除了注塑机作出相应的改动外,模具设计的技巧是整项技术的灵魂。模具通过转动移位,达到同步注塑不同物料的效果。 模具设计大致分为两类:第一类有两个模腔,利用转动模式把半成型模件转移180度到另一个模腔内,其好处是使第一和第二工序可以同步进行;另一类是单一模腔,半制成品连同模具一起转动180度。设计上比较简单,但生产效率相应降低。由于模具或半成品需要转动,所以模具设计及注塑机的要求更为精密。 另外,由于双物料注塑的可变性很高,所以要达到生产顺利,符合预期理想,所有的模具设计必须与产品设计同步考虑,而且市面流行的双物料注塑机规格并不统一,导致模具设计时考虑的问题更多;加上通用性少,模具制造商必须加倍留心。双物料制品一般以ABS、PC等硬塑料配合TPE软塑料为主,适合制造餐具、工具手柄、表壳、电话机外壳及按钮等制品。这使得生产企业在技术上必须注意三点:两类物料的融合性、产品的复杂性及注塑机的调校。例如,由于成本或应用的关系,采用的物料之间可能没有良好的粘合性,双物料注塑通常要在这方面进行更多地调试工作。更多的双色注塑问题精英注塑将会继续关注。 我国正逐步成为全球消费产品的生产制造基地,近年来华南地区塑料产品的制造商承接了许多需要双物料注塑技巧的订单,使双物料注塑技术在国内的应用日益广泛。 双射成型主要以双射成型机两只料管配合两套模具按先后次序经两次成型制成双射产品。 比起传统射出成型,双料共射射出成型制程有如下的优点: 1核心料可以使用低黏度的材料来降低射出压力。 2从环保的考虑,核心料可以使用回收的二次料。 3根据不同的使用特性,如厚件成品皮层料使用软质料,核心料使用硬质料或者核心料可以使用发泡塑料来降低重量。 4可以利用较低质量的核心料以降低成本。 5 皮层料或核心料可使用价格昂贵且具特殊表面性质,如防电磁波干扰、高电导性等材料以增加产品性能。 6适当的皮层料和核心料配合可以减少成型品残余应力、增加机械强度或产品表面性质。 7产生如大理石纹路的产品。 从多色射出成型、双料共射出成型的特性与应用可以看出未来有逐步取代传统射出成型制程的趋势。革新性射出成型技术不但提高了射出成型制程的精密度、提供高难度制程技术,而且开拓了射出成型制程领域的范围。创新的射出设备与制程,才足以应付愈来愈多样化、高质量、高附加价值的产品需求。
双色模具设计及双色注塑成型的36条经验
双色模具设计及双色注塑成型的36条经验
双色模具设计及双色注塑成型的36条经验: 1.双色模设计的基本原则: (1.)硬胶做1次,软胶做2次; (2.)透明做1次,非透明做2次; (3.)成型温度高的塑料做1次,成型温度低的做2次; 上述是做双色模的基本原则,否则模具会白做;另外,封胶时尽量用靠破封胶,而不用插破封胶,哪怕是建议客户修改产品也要尽量必为靠破封胶; 2.模胚导柱导套必须上下左右对称,前后模对称。 3.后模要旋转180度,前模不动。 4. 产品间距必须以注塑机炮嘴的间距为准,国外有的双色注塑机的炮嘴间距是可调的,有的不可调,国内的不可调。 5. 两个独立的顶出系统,顶棍也是两个。后模两个产品相同,顶针都相同,是旋转关系,切不可做成平移关系。 6. 顶针板只能用弹簧复位,不可用螺丝强制复位,因为后模要旋转。 7. 边锁必须在模具中心的四边,且前后模对称,否则当后模旋转180后与前模对不上。 8. 如果进胶点间距和注塑机炮嘴间距不同,顶棍孔要做成腰型的,因为注塑机顶棍间距不可调。注意国产双色注塑机大部分注塑炮嘴不可调。 9. 注意客户提供的注塑机平行炮嘴的方向,是X轴或是Y轴,以此来定产品排位的布局。 10. 运水进出水的方向必须在天地侧,且每一个循环水的进出都必须在同一面上,不可进水在天,出水在地侧,因为后模要旋转180度,要注意模胚大小不可超过注塑机出水槽的高度,否则无法接运水。 11. 第一次注塑的产品要放在非操作侧,因为第一次注塑后产品要旋转180度进行第
二次注塑,正好转到操作侧,方便取产品。 12. 出口模的码模位要在操作侧和非操作侧,不可在天地侧,因为他们的产品要全自动。 13. 分型面的注意事项:后模分型面要将两个产品合并后取得的分型面为后模的;前模分型面要取单个产品的即可,不可取合并后的产品分型面。 14. 前后法兰的公差为负0.05mm,两法兰间距公差为正负0.02mm,顶棍与顶棍孔的间隙单边为 0.1mm,前后模导套导柱的中心距公差为正负0.01,模框四边和深度都要加公差,否则当后模旋转180度后,因高低不一致而产生批锋。框深公差为负0.02mm。15.如果在模胚厂已经将模胚加工完,本厂要加工唧嘴和顶棍孔时,要以4个导柱导套孔的间距中心为基准取数,否则偏差太多,容易卡死模。订模胚时要注明是双色模胚,四个导柱导套和框对称,后模旋转180度后能与前模匹配。 16. 如果是后模旋转的双色话就简单多了..两个前模芯一样...一边注塑好硬胶后.旋转180度(注意产品转的时候不能掉落,浇口可以自动分离) , 转到另外一边后再注塑软胶...注塑硬胶无需布置顶针...只需布置在软胶这边模芯即可...另外缩水要注意...如果软胶完全把硬胶缠住..则只需放硬胶的缩水...如果是轮廓相接则硬胶软胶都要放缩水。 17. 如果是一套模具的双色模具的话 ,那就是一个直炮筒,一个90度的炮筒射胶,不需要旋转,只需一个模芯,软胶与硬胶的分离方法靠行位封胶。 18. Cavity的两个外形是不同的,分别成型1种产品。而Core的两个外形完好一样。 19.模具的前、后模以中心旋转180°后,必需吻合。设计时必需做这个检查动作。 20. 留意顶针孔的位置,最小间隔210mm。大的模具须恰当增加顶棍孔的数量。并且,由于注塑机本身附带的顶针不够长,所以我们的模具中必需设计加长顶针,顶针长出模胚底板150mm左右。 21. 后模底板上必需设计2个定位圈。
双色模具与包胶模具的区别
双色模具与包胶模具的区别 双色模具与包胶模具的区别A.双色模具:两种塑胶材料在同一台注塑机上注塑,分两次成型,但是产品只出模一次的模具。一般这种模塑工艺也叫双料注塑,通常由一套模具完成,且需要专门的双色注塑机。 B.包胶模具(二次成型):两种塑胶材料不一定在同一台注塑机上注塑,分两次成型;产品从一套模具中出模取出后,再放入另外一套模具中进行第二次注塑成型。所以,一般这种模塑工艺通常由2套模具完成,而不需要专门的双色注塑机。 双色模具与包胶模具概述: 包胶模具在设计应注意硬胶件的定位,需做到可*的封胶且在胶件上有反斜度孔,防止拉胶变形. 双色模具目前市场上日益盛行,于这种工艺可以使产品的外观更加漂亮,易于换颜色而可以不用喷涂,但造价昂贵,技术要求高. 1.Cavity的两个形状是不同的,分别成型1种产品。 而Core的两个形状完全一样。 2.模具的前、后模以中心旋转180o后,必须吻合。设计时必须做这个检查动作。 3.注意顶针孔的位置,最小距离210mm。大的模具须适当增加顶棍孔的数量。并且,由于注塑机本身附带的顶针不够长,所以我们的模具中必须设计加长顶针,顶针长出模胚底板150mm左右。 后模底板上必须设计2个定位圈。 4.前模面板加A板的总厚度不能少于170mm。请仔细查看这种型号的注塑机的其它参考数据,比如,最大容模厚度、最小容模厚度、顶棍孔距离等。 5.三板模的水口最好能设计成可以自动脱模动作。特别要注意软胶水口的脱模动作是否可*。 6.前侧SPRUE的深度不要超过65mm。上侧(大水口)SPRUE的顶部到模胚中心的距离不小于150mm。 7.在设计第二次注塑的CAVITY时,为了避免CAVITY插(或擦)伤第一次已经成型好的产品胶位,可以设计一部分避空。但是必须慎重考虑每一处封胶位的强度,即:在注塑中,是否会有在大的注塑压力下,塑胶发生变形,导致第二次注塑可能会有批锋产生的可能? 8.注塑时,第一次注塑成型的产品尺寸可以略大,以使它在第二次成型时能与另一个CAVITY压得更紧,以达到封胶的作用。 9.注意在第二次注塑时,塑胶的流动是否会冲动第一次已经成型好的产品,使其胶位变形?如果有这个可能,一定要想办法改善。 10.在A、B板合模前,要注意前模Slider或Lifter是否会先复位而压坏产品?如此,必须想办法使在A、B板先合模,之后前模的SLIDER或LIFET才能复位。 11.两CAVITY和CORE的运水布置尽量充分,并且均衡、一样。 12.99%的情况是先注塑产品的硬胶部分,再注塑产品的软胶部分。因为软胶易变形。
双色注塑技术说明
塑料加工工艺之双色注塑技术 2009-07-02 09:03:00 新闻来源:宁波塑机网 近年来,国内部分塑料制品业者在严峻的经营环境下,纷纷朝向大型高附加价值产品及特殊双色制品发展。而从近期中国展会来看,多色成型技术经常是展会亮点,展出双色机厂商成倍数增加,也显示双色机在中国日渐蓬勃发展。 华大:“共塑”注塑 华大机械有限公司是中国大型的生产注塑机的厂家之一,也是大陆首家生产研制多物料注塑机的企业。 华大的多物料注塑机采用“共塑”注塑方式比传统法可节省达50%的生产时间,能够减省达20%或以上的废/次品损耗量,且产品质量稳定,还能制造如立体穿透、底面包围等复杂制品,在国内多物料注塑机行业处于领先水平。与国内厂家双物料平行结构不同,华大的多物料注塑机是按欧洲先进思路设计,采用直角式结构,独立的副射台设置马达、油泵、射胶装置及控制系统,使机器随时能变回单物料生产方式,简单方便。 锁模部分,模板全部经有限元分析,采用优质的球墨铸铁精密制造而成,二板、尾板采用铰耳连接,减少累计误差,增加整机刚性,保证了机板的使用寿命。五点式开合模结构,机铰经优化设计,运行平稳,结构紧凑,适合各类双物料模具。 注射部分采用耐磨氮化熔胶螺杆及料筒,电子尺控制射胶位置,射胶流量阀带位置反馈,确保注射速度的精确性和重复性。副射台动作有同步或不同步等多种形式,供用户选用。 采用日本原装三菱控制系统,工作状态以图形显示,方便监控生产过程,数据输入使用触摸键,增加系统的可靠性,10段射胶,熔胶保压设定,5段螺杆转速及背压控制,适合精密注射。此外,华大还可根据客户模具要求特别编写程序。 在FT多物料系列,华大自主研制的双物料共塑技术已达国际先进水平。同时,多物料系列注塑机也正在朝更低成本、更高速度、更高精密,更低能耗的方向不断改进。 欧美厂商产品已提升至几个基本成型技术的“组合”呈现,如:双色成型加模内贴标(IML)、双色成型加模内组合(IMA)、双色成型加迭层模(Stack Mold)、双色成型加IML加IMA加迭层模、双色成型加夹层射出等。这些都可以在一部注塑机上完成。因此,双色技术愈来愈受重视,而且不只呈现双色技术,还必须与其它技术结合,创造更高的效益。 各具特色的双色注塑机 现在的双色成型,已不仅仅要求两种或是多种颜色塑料的简单结合,而在制品精度、外形美观、不同颜色塑料更好地融合,以及制品成型周期上都对注塑机提出了更高的要求。不同厂家的设备都具有各自的优点和特