DBL_5410_2007-08

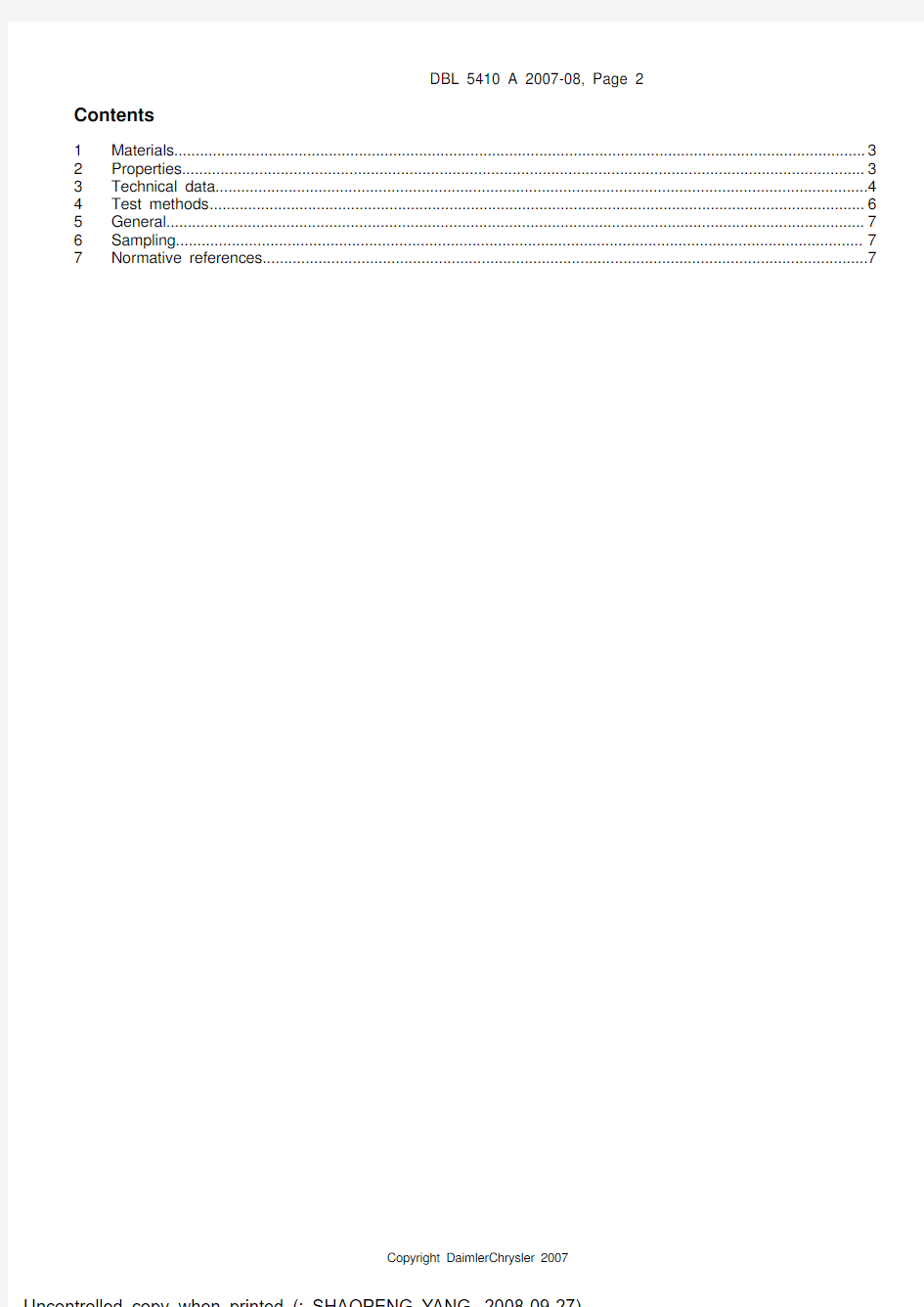
Mercedes-Benz DBL 5410
Date Published: 2007-08
Total No. of Pages: 7
Person in charge: Ulrich Remmele
PWT/VWK
Telephone: +49-(0)7031 90-44267
Supply Specification
Parts manufactured from thermoplastics for
control elements, bearing elements,
fasteners, and spacers
Preface
DBL 5410 describes the Supply Specifications for parts manufactured from thermoplastics for con-trol elements, bearing elements, fasteners and spacers.
The latest version of this document is available through the standards information systems of Chrys-ler and Mercedes-Benz.
Changes
The following changes were carried out as against DBL 5410 edition 1999-05:
- Revised in line with DBL 4000
- Hot light aging new DIN / EN / ISO standard.
Copyright DaimlerChrysler 2007
Contents
1Materials (3)
2Properties (3)
3Technical data (4)
4Test methods (6)
5General (7)
6Sampling (7)
7Normative references (7)
1 Materials
Table 1
PV Material Material description Application examples 00 PA6 GF 30 Polyamide 6 with 30 % glass fibers
00 PA66 GF 30 Polyamide 66 with 30 % glass fibers
00 PA6 GF 25 Polyamide 6 with 25 % glass fibers 00 PA66 GF 25 Polyamide 66 with 25 % glass fibers 00 PA6 GF 15 Polyamide 6 with 15 % glass fibers 00 POM GF 30 Polyacetal with 30 % glass fibers
00 PA6 Polyamide 6
00 PA66 Polyamide 66 Fasteners rings, washers, spacer bushings
00 PBT Polybutylene terephthalate
00 POM Polyacetal (POM-C; POM-H)
00 POM PTFE 20 Polyacetal with 20 % polytetrafluoroethylene Plain bearing bushes, sliding blocks, clips
00 PA12 Polyamide 12
00 PP-PE Propylene/Ethylene copolymer 00 PE – HD High-density polyethylene
00 PE-LD Low-density polyethylene Air flaps,
controls,
steering wheel coverings
01 PA6 GF 15 Polyamide 6 with 15 % glass fibers,
dry impact resistant
01 PA66 GF 15 Polyamide 66 with 15 % glass fibers,
dry impact resistant
01 PA6-I Polyamide 6, dry impact resistant
01 PA66-I Polyamide 66, dry impact resistant 01 POM-I Polyacetal, impact modified (POM-C) Covers, fasteners
PV = Product version
Abbreviated designation for drawings in the block for material, e.g:
Thermoplastic PA6 GF 30, DBL 5410.00
2 Properties
Parts manufactured from thermoplastics with
- low specific surface loads and low sliding speeds for bearing elements
- control surfaces with high visual impact
- impact resistant (dry impact resistant) modification for easy-to-install quick-release systems which can be detached several times.
The supply parts shall comply with the requirements of DBL 8585 "Negative Substance List for the Selection of Mate-rials".
The availability of a certificate of testing in accordance with the following method is specified as an overriding re-quirement for adherence to the emission values for interior trim materials: VDA 278; threshold values DBL 8585. The user is responsible for checking whether the version in his possession is the latest version. In particular in the case of substances listed in DBL 8585 Section 2.3, the supplier is required to continuously minimize the concentra-tion and emission at least in accordance with the state of the art, even when values have fallen below the required DBL threshold values.
3 Technical data
* Tensile stress at yield /
Values represent maximum requirements.
** Values apply to the water content indicated.
For water content on delivery, refer to specification on drawing
* Tensile stress at yield
Values represent maximum requirements.
** Values apply to the water content indicated.
For water content on delivery, refer to specification on drawing Values indicated in Section 3 represent maximum requirements.
Hot light aging (UV resistance)
For parts located in the directly visible area of vehicle interior, the hot light aging test in accordance with VDA 75 202-3 A4 shall be performed.
Extractable matter
For polyamide 11 and polyamide 12, the extractable matter shall be indicated in accordance with DBL 5555. Supplies shall be in accordance with the sample.
4 Test methods
Tests Units
Test
specifica-
tion
Remarks
Density g/cm3ISO 1183 A Buoyancy method
Water content for determining the test value % DBL
5555
Residue on ignition % DIN EN 60 Tensile test:
Tensile strength Elongation at break MPa
%
ISO 527 Standard bar 1A (molded material)
Standard bar 1BA (component, 0.5 * test rate)
Test rates:
50 mm/min for unreinforced plastics
5 mm/min for reinforced plastics
Impact strength (Notched) impact strength kJ/m2ISO 179
DIN 53 435 *
Molded material
Standard bar 80 x 10 x 4 mm
Component:
Dynstat test
Deformation follow-ing hot storage tem-perature %
°C
DBL 5555 Heating cabinet in accordance with DIN 50011
Emission analysis:**
VOC value FOG value μg/g (ppm)
μg/g (ppm)
Target value < 100
Target value < 250
DBL 8585
VDA 278
Critical individual substances shall not exceed the
limit/target values indicated in DBL 8585.
For POM, VDA 278 is not required.
Fogging ** mg DBL 5306 0,7 max. Odor ** Rating VDA 270 Rating 3
Formaldehyde emis-sion of POM** mg/kg VDA
275 Colorless parts ≤ 5
Dyed parts ≤ 20
Aging under the in-fluence of heat and light ** Rating DIN EN ISO 105-
B06
Black panel temperature 90 ± 3 °C,
without non-woven backing
Burning test ** DBL 5307.10 According to definition in FMVSS 302 Extractable matter % DBL 5555
* Test method DIN 53 435 to be replaced by ISO 179
** for applications in vehicle interior
5 General
The general conditions laid down in DBL 5555 shall be observed. These include, for examples, duties of the supplier, samples, test certificate, environmental requirements, recycling and storability.
6 Sampling
The sampling location shall be agreed with the materials engineering department of the receiving plant or Production and Materials Engineering using the drawing as assistance.
7 Normative references
DBL 5555
DBL 8585
DBL 5306
DBL 5307
VDA 270
VDA 275
VDA 278
DIN 50011
DIN EN 60
DIN 53435
DIN EN ISO 105 B06
ISO 1183A
ISO 527
ISO 179