通用版—填料塔工艺流程图
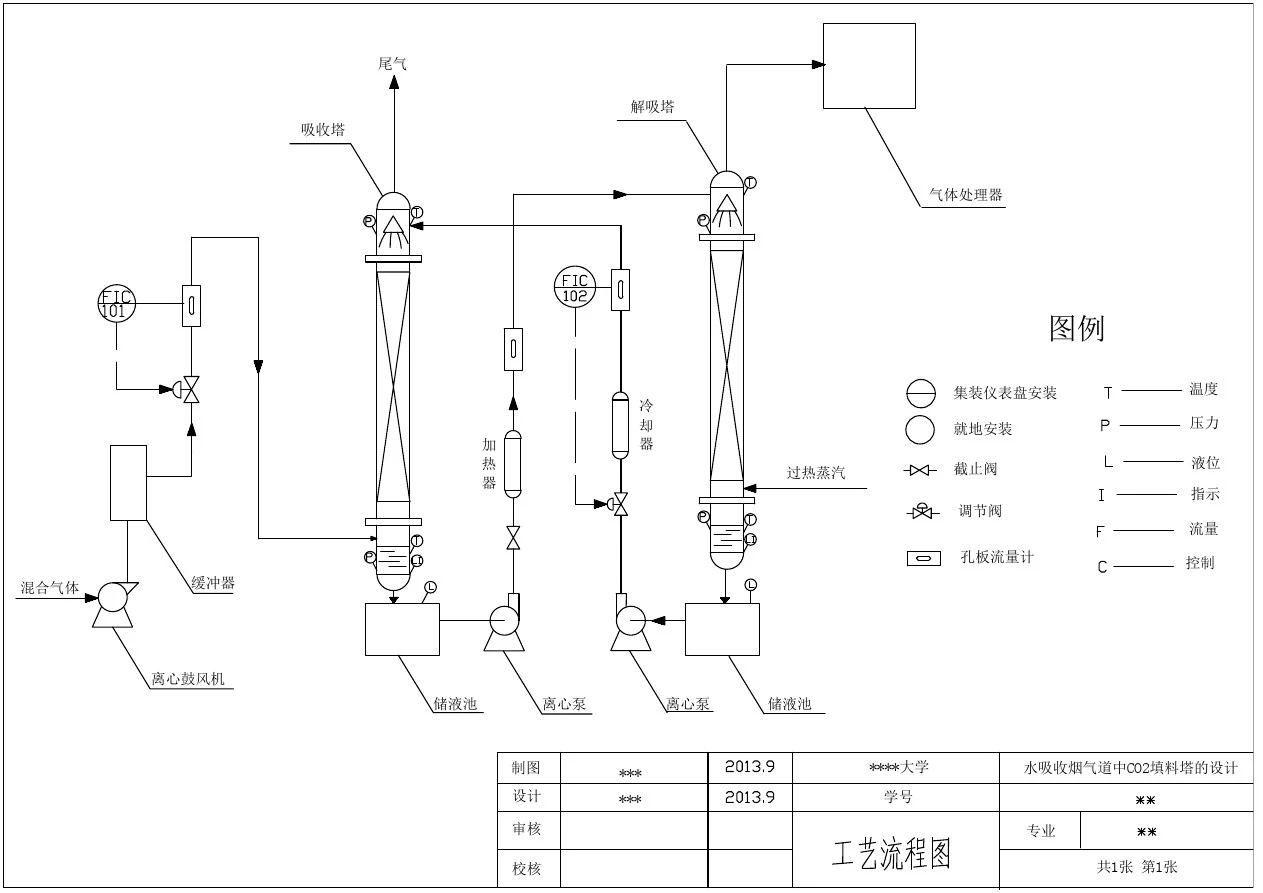
水吸收丙酮填料塔设计(化工课程设计)[1]
兰州交通大学化工原理课程设计 化工原理课程设计 课程名称: ____填料塔设计____ 设计题目: ____水吸收丙酮____ 院系: ___ 化学学院_____ 学生姓名: _____ 荆卓_______ 学号: ____ 200907134____ 专业班级: ____化艺093班____ 指导教师: ______张玉洁______
化工原理课程设计任务书 (一)设计题目:水吸收空气中的丙酮填料塔的工艺设计(二)设计条件 1.生产能力:每小时处理混合气体9000Nm3 /h 2.设备形式:填料塔 3.操作压力:101.3KPa 4.操作温度:298K 5.进塔混合气体中含丙酮4%(体积比) 6.丙酮的回收率为99% 7.每年按330天计,每天按24小时连续生产 8.建厂地址:兰州地区 9.要求每米填料的压降都不大于103Pa。 (三)设计步骤及要求 1.确定设计方案 (1)流程的选择 (2)初选填料的类型 (3)吸收剂的选择 2.查阅物料的物性数据 (1)溶液的密度、粘度、表面张力、氨在水中的扩散系数(2)气相密度、粘度、表面张力、氨在空气中的扩散系数
(3)丙酮在水中溶解的相平衡数据 3.物料衡算 (1)确定塔顶、塔底的气流量和组成 (2)确定泛点气速和塔径 (3)校核D/d>8~10 (4)液体喷淋密度校核:实际的喷淋密度要大于最小的喷淋密度。4.填料层高度计算 5.填料层压降核算 如果不符合上述要求重新进行以上计算 6.填料塔附件的选择 (1)液体分布装置 (2)液体再分布装置 (3)填料支撑装置 (4)气体的入塔分布. (四)参考资料 1、《化工原理课程设计》贾绍义柴诚敬天津科学技术出版 2、《现代填料塔技术》王树盈中国石油出版 3、《化工原理》夏清天津科学技术出版 (五)计算结果列表(见下页)
填料塔计算部分
填料吸收塔设计任务书 一、设计题目 填料吸收塔设计 二、设计任务及操作条件 1、原料气处理量:5000m3/h。 2、原料气组成:98%空气+%的氨气。 3、操作温度:20℃。 4、氢氟酸回收率:98%。 5、操作压强:常压。 6、吸收剂:清水。 7、填料选择:拉西环。 三、设计内容 1.设计方案的确定及流程说明。 2.填料吸收塔的塔径,填料层的高度,填料层的压降的计算。 3.填料吸收塔的附属机构及辅助设备的选型与设计计算。 4.吸收塔的工艺流程图。 5.填料吸收塔的工艺条件图。
目录 第一章设计方案的简介 (4) 第一节塔设备的选型 (4) 第二节填料吸收塔方案的确定 (6) 第三节吸收剂的选择 (6) 第四节操作温度与压力的确定 (7) 第二章填料的类型与选择 (7) 第一节填料的类型 (7) 第二节填料的选择 (9) 第三章填料塔工艺尺寸 (10) 第一节基础物性数据 (10) 第二节物料衡算 (11) 第三节填料塔的工艺尺寸的计算 (12) 第四节填料层压降的计算 (16) 第四章辅助设备的设计与计算 (16) 第一节液体分布器的简要设计 (16) 第二节支承板的选用 (17) 第三节管子、泵及风机的选用 (18) 第五章塔体附件设计 (20) 第一节塔的支座 (20) 第二节其他附件 (20)
第一章设计方案的简介 第一节塔设备的选型 塔设备是化工、石油化工、生物化工制药等生产过程中广泛采用的气液传质设备。根据塔内气液接触构件的结构形式,可分为板式塔和填料塔两大类。 1、板式塔 板式塔为逐级接触式气液传质设备,是最常用的气液传质设备之一。传质机理如下所述:塔内液体依靠重力作用,由上层塔板的降液管流到下层塔板的受液盘,然后横向流过塔板,从另一侧的降液管流至下一层塔板。溢流堰的作用是使塔板上保持一定厚度的液层。气体则在压力差的推动下,自下而上穿过各层塔板的气体通道(泡罩、筛孔或浮阀等),分散成小股气流,鼓泡通过各层塔板的液层。在塔板上,气液两相密切接触,进行热量和质量的交换。在板式塔中,气液两相逐级接触,两相的组成沿塔高呈阶梯式变化,在正常操作下,液相为连续相,气相为分散相。 一般而论,板式塔的空塔速度较高,因而生产能力较大,塔板效率稳定,操作弹性大,且造价低,检修、清洗方便,故工业上应用较为广泛。 2、填料塔 填料塔是最常用的气液传质设备之一,它广泛应用于蒸馏、吸收、解吸、汽提、萃取、化学交换、洗涤和热交换等过程。几年来,由于填料塔研究工作已日益深入,填料结构的形式不断更新,填料性能也得到了迅速的提高。金属鞍环,改型鲍尔环及波纹填料等大通量、低压力降、高效率填料的开发,使大型填料塔不断地出现,并已推广到大型汽—液系统操作中,尤其是孔板波纹填料,由于具有较好的综合性能,使其不仅在大规模生产中被采用,且由于其在许多方面优于各种塔盘而越来越得到人们的重视,在某些领域中,有取代板式塔的趋势。近年来,在蒸馏和吸收领域中,最突出的变化是新型填料,特别是规整填料在大直径
塔的水力学计算手册
塔的水力学计算手册
1.目的与适用范围 (1) 2.塔设备特性 (1) 3.名词术语和定义 (1) 4.浮阀/筛孔板式塔盘的设计 (1) 5.填料塔的设计 (1)
1.目的与适用范围 为提高工艺工程师的设计质量,推广计算机应用而编写本手册。 本手册是针对气液传质塔设备中的普遍性问题而编写。对于某些具体塔设备的数据(比如:某生产流程中针对某塔设备的板效率而采用的计算关联式,或者对于某吸收填料塔的传质单元高度或等板高度而采用的具体计算公式)则未予收入。本设计手册以应用为主,主要是指导性的计算方法和步骤,并配合相应的计算程序,具体公式及理论推阐可参考有关文献。 2.塔设备特性 作为气(汽)、液两相传质用的塔设备,首先必须能使气(汽)、液两相得到充分的接触,以得到较高的传质分离效率。 此外,塔设备还应具有以下一些特点: (1)当气(汽)、液处理量过大(超过设计值)时,仍不致于发生大量的雾 沫挟带或液泛等影响正常操作的现象。 (2)当操作波动(设计值的50%~120%)较大时,仍能维持在较高的传 质效率下稳定操作,并具有长期连续操作所必须具备的可靠性。 (3)塔压力降尽量小。 (4)结构简单、耗材少、制造和安装容易。 (5)耐腐蚀、不易堵塞。 (6)塔内的滞留液量要小。 3.名词术语和定义 3.1 塔径(tower diameter),D T 塔筒体内壁直径,见图3.1-(a)。 3.2 板间距(tray spacing),H T 塔内相邻两层塔盘间的距离,见图3.1-(a)。 3.3 降液管(downcomer),DC 各层塔盘之间专供液相流体通过的组件,单溢流型塔盘为侧降液管,双溢流型塔盘有侧降液管和中央降液管,三或多溢流型塔盘有侧降液管、偏侧降液管、偏中央降液管及中央降液管。 3.4 降液管顶部宽度(DC top width),Wd 弓形降液管面积的弦高。掠堰另有算法,见图3.1-(a),-(b)。 3.5 降液管底间隙(DC clearance),ho 降液管底部边缘至塔盘(或受液盘)之间的距离,见图3.1-(a)。 3.6 溢流堰高度(weir height),hw 降液管顶部边缘高出塔板的距离,见图3.1-(a)。 3.7 总的塔盘横截面积(total tower cross-section area),A T
填料塔工艺尺寸的计算
第三节 填料塔工艺尺寸的计算 填料塔工艺尺寸的计算包括塔径的计算、填料能高度的计算及分段 3.1 塔径的计算 1. 空塔气速的确定——泛点气速法 对于散装填料,其泛点率的经验值u/u f =0.5~0.85 贝恩(Bain )—霍根(Hougen )关联式 ,即: 2213lg V F L L u a g ρμερ?? ?????? ? ???????=A-K 141V L V L w w ρρ???? ? ??? ?? (3-1) 即:1 124 8 0.23100 1.18363202.59 1.1836lg[ ()1]0.0942 1.759.810.917998.24734.4998.2F u ?????? =- ? ? ??????? 所以:2 F u /9.81(100/0.9173)(1.1836/998.2)= UF=m/s 其中: f u ——泛点气速,m/s; g ——重力加速度,9.81m/s 2 W L =5358.89572㎏/h W V =7056.6kg/h A=0.0942; K=1.75; 取u=0.7 F u =2.78220m/s
0.7631D = = = (3-2) 圆整塔径后 D=0.8m 1. 泛点速率校核:2 6000 3.31740.7850.83600 u = =?? m/s 则 F u u 在允许范围内 2. 根据填料规格校核:D/d=800/50=16根据表3-1符合 3. 液体喷淋密度的校核: (1) 填料塔的液体喷淋密度是指单位时间、单位塔截面上液体的喷淋量。 (2) 最小润湿速率是指在塔的截面上,单位长度的填料周边的最小液体体积流量。对于直径不超过75mm 的散装填料,可取最小润湿速率()3min 0.08m /m h w L ?为。 ()32min min 0.081008/w t U L m m h α==?=? (3-3) 22 5358.8957 10.6858min 0.75998.20.7850.8 L L w U D ρ= ==>=???? (3-4) 经过以上校验,填料塔直径设计为D=800mm 合理。 3.2 填料层高度的计算及分段 *110.049850.75320.03755Y mX ==?= (3-5) *220Y mX == (3-6) 3.2.1 传质单元数的计算
填料塔计算部分
二 基础物性参数的确定 1 液相物性数据 对于低浓度吸收过程,溶液的物性数据可近似取纯水的物性数据。由手册查得,2 气相物性参数 设计压力:101.3kPa ,温度:20C ? 氨气在水中的扩散系数:92621.7610/ 6.33610/L D cm s m h --=?=? 氨气在空气中的扩散系数: 查表得,氨气在0°C ,101.3kPa 在空气中的扩散系数为0.17 2/cm s , 根据关系式换算出20C ?时的空气中的扩散系数: 33 2 2 0002 2 293.150.171273.150.189/0.06804/V P T D D P T cm s m h ??????==?? ? ? ??????? == 混合气体的平均摩尔质量为 m i 0.05170.982929.27V i M y M ==?+?=∑ 混合气体的平均密度为 3 m 101.329.27 1.2178.314293.15 V V m P M kg m R T ρ?= = =? 混合气体的粘度可近似取空气的粘度,查手册得20C ?空气粘度为
51.81100.065()V Pa s kg m h μ-=??=? 3 气液相平衡数据 由手册查得,常压下20C ?时,氨气在水中的亨利系数 76.3a E kP = 相平衡常数 76.30.7532 101.3 E m P = == 溶解度系数 3 s 998.20.726076.318.02 L H km ol kPa m EM ρ= = =?? 4 物料衡算 进塔气相摩尔比 1= 11 0.050.05263110.05 y Y y = =-- 出塔气相摩尔比 3 21(1)0.05263(10.98) 1.05310 A Y Y ?-=-=-=? 混合气体流量 33 0.1013(273.1520) 16.10100.1013273.15V N Q Q m h ? ?+==?? 惰性气体摩尔流量 273.15(10.05)636.1622.4 273.1520 V Q V km ol h = ? -=+ 该吸收过程属低浓度吸收,平衡关系为直线,最小液气比可按下式计算: 1212 L Y Y V Y m X -??= ? -?? 对于纯溶剂吸收过程,进塔液相组成 20X = m in 0.052630.0010530.73810.052630.7532L V -?? == ? ?? 取操作液气比为 m in 1.4L L V V ?? = ??? 1.40.7381 1.0333L V =?= 1.0333636.16657.34L kmol h =?=
填料塔的计算.doc
一、设计方案的确定 (一) 操作条件的确定 1.1吸收剂的选择 1.2装置流程的确定 1.3填料的类型与选择 1.4操作温度与压力的确定 45℃常压 (二)填料吸收塔的工艺尺寸的计算 2.1基础物性数据 ①液相物性数据 对于低浓度吸收过程,溶液的物性数据可近似取质量分数为30%MEA 的物性数据
7.熔 根据上式计算如下: 混合密度是:1013.865KG/M3 混合粘度0.001288 Pa ·s 暂取CO2在水中的扩散系数 表面张力б=72.6dyn/cm=940896kg/h 3 ②气相物性数据 混合气体的平均摩尔质量为 M vm = y i M i =0.133*44+0.0381*64+0.7162*14+0.00005*96+0.1125*18 =20.347 混合气体的平均密度ρvm = =??=301 314.805 .333.101RT PMvm 101.6*20.347/(8.314*323)=0.769kg/m 3 混合气体粘度近似取空气粘度,手册28℃空气粘度为
μV =1.78×10-5Pa ·s=0.064kg/(m ?h) 查手册得CO2在空气中的扩散系数为 D V =1.8×10-5m 2/s=0.065m 2/h 由文献时CO 2在MEA 中的亨利常数: 在水中亨利系数E=2.6?105kPa 相平衡常数为m=1.25596 .101106.25 =?= P E 溶解度系数为H=)/(1013.218 106.22.9973 45 kPa m kmol E M s ??=??= -ρ 2.2物料衡算 进塔气相摩尔比为Y1=0.133/(1-0.133)= 0.153403 出塔气相摩尔比为Y2= 0.153403×0.05=0.00767 进塔惰性气相流量为V=992.1mol/s=275.58kmol/h 该吸收过程为低浓度吸收,平衡关系为直线,最小液气比按下式 计算,即 2 121min /X m Y Y Y )V L ( --= 对于纯溶剂吸收过程,进塔液组成为X2=0 2 121min /X m Y Y Y )V L ( --==(0.153403-0.00767)/(0.1534/1.78)=1.78 取操作液气比(?)为L/V=1.5L/V=1.5×1.78=2.67 L=2.67×275.58=735.7986kmol/h ∵V(Y1-Y2)=L(X1-X2) ∴X1=0.054581
填料塔-文献综述
现代填料塔技术发展现状与展望 摘要 填料塔作为一种传质设备, 具有效率高、压降低、持液量小、构造简单、安装容易、投资少等优点, 广泛用于分离操作。论述了国内外填料塔技术的发展现状, 详细介绍了各种新型散堆填料、规整填料、液体分布器和气体分布器的结构特点、流体力学性能和传质性能, 并比较了各自的优缺点。同时展望了填料塔今后发展趋势和技术开发方向。 关键词填料塔散堆填料规整填料液体分布器气体分布器填料塔具有效率高、压降低、持液量小、构造简单、安装容易、投资少等优点, 是石油、化工、化纤、轻工、制药及原子能等工业中广泛应用的气液接触传质设备之一。过去,由于其存在着放大效应和壁流效应, 使其应用仅仅局限于小塔上。近年来, 人们进行了大量的研究, 取得了突破性进展, 目前应用的规整填料最大直径可达14~20m, 突破了仅限于小塔的传统观念, 并在现代化工生产中得到更为普遍的应用。目前的研究主要集中在填料、液体分布器和气体分布器等方面。本文就是这几个方面的一个综述和展望。 1 新型填料 11散堆填料 散堆填料是具有一定几何尺寸的颗粒体,在塔内以散堆方式堆积。散堆填料及其塔设备 主要用在吸收、解吸、精馏、干燥和萃取等气-液或液-液接触的传质传热过程。近年来一 些新型高效散堆填料的出现以及在一些行业的成功应用, 如环保行业从烟气中除去HCl和 SO2等, 说明散堆填料将在某些领域得到新的发展[ 1 ]。另外, 国内外最新的研究表明, 在液液萃取、液气比很大的吸收和高压精馏情况下, 应用散堆填料的操作性能优于规整填料和塔盘[ 2 ]。因此在合成氨的气体净化、石油化工和焦化等
领域, 散堆填料得到广泛的应用。此外, 反应蒸馏、硫化干燥和超重力分离等领域也在使用散堆填料。 (1) I MPAC填料[ 3 ] I MPAC填料最初由美国Lantc公司提出,它集扁、鞍和环结构于一体。它可以看作由若干个I ntal ox填料连体而成, 采用多褶壁面、多层筋片、消除床内死角和单体互相嵌套等技术, 所以该填料兼有规整填料和散堆填料之特性。其特点如下: ①与一般的散堆填料相比,通量可以提高10% ~30%; ②具有高比表面积, 可达131m2/m3, 与一般的散堆填料相比,单元传质高度低, 可下降5%~35%; ③无翻边结构, 避免了气液滞留; ④多层翅片, 自分布性能优良, 故对气液分布器的要求远不如规整填料严格; ⑤压降小, 可比一般散堆填料下降5%~15%; ⑥单位外形呈扁环, 填料单元立放最稳, 有利于加强气液湍动, 活化内表面; ⑦既具有一般散堆填料拆装方便、维修改造灵活的特性, 又具有规整填料比表面积大、空隙率高、流体分布均匀的优点。 (2) 阶梯短环填料 阶梯短环填料(Cascade Mini Ring, CMR)是美国Glitsch公司兼并英国传质公司后大力推广的一种散堆填料, 与其前身阶梯环相比,其高径比从原来的015降到013。这种看似简单的几何特性却是CMR性能优越的关键。大量试验表明, CMR的性能确实明显优于鲍尔环和筛板塔, 其压降约为拉西环的30% , 传质系数比拉西环大约提高50%。因此, CMR的应用很广泛, 已在近千座工业塔中得到广泛应用。 (3) 超级扁环填料[ 4 ] 清华大学研制的内弯弧型筋片扁环填料(QU - 1型扁环填料) , 其结构特点为: ①采用和传统填料不同的内弯弧型筋片结构, 使填料内部的流道更为合理, 提高了传质效率, 同时这种结构可提高填料的强度; ②针对液体系轴向混合严重的特点, 采用012~013的高径比, 使填料在乱堆时也能体现一定程度的有序排列, 从而降低了阻力, 在有效抑制了两相的非理想流动, 有助于进一步提高处理能力和传质系数; ③可根据体系和生产要求, 采用多种材质加工制造, 且有多种规格, 因而选用范围宽, 操作弹性大。试验研究和工业应用表明,QH - 1型扁环填料具有优异的性能; 用于液液萃取时, 此填料的性能明显优于鲍尔
填料塔计算部分 (2)
二基础物性参数的确定 由手册查得,常压下20C ?时,氨气在水中的亨利系数 相平衡常数 溶解度系数 4物料衡算 进塔气相摩尔比 出塔气相摩尔比 混合气体流量 惰性气体摩尔流量 该吸收过程属低浓度吸收,平衡关系为直线,最小液气比可按下式计算: 对于纯溶剂吸收过程,进塔液相组成
取操作液气比为 Eckert 通用关联图: 气体质量流量为 液体质量流量可近似按纯水的流量计算: Eckert 通用关联图的横坐标为 根据关联图对应坐标可得 由表2-4-1可知 F φ=2601m - 取0.80.8 2.360 1.888/F u u m s ==?=
由 1.737 D===m 圆整塔径(常用的标准塔径有400mm、500mm、600mm、800mm、1000mm、1200mm、1400mm、1600mm、 2000mm、2200mm等)本设计方案取D=2000mm。 泛点率校核: 因为填料塔的适宜空塔气速一般取泛点气速的50%-80%,泛点率值在允许范围内。 填料塔规格校核: 2000 808 25 D d ==>(在允许范围之内) 液体喷淋密度校核: max D 取8 h D =,则 计算得填料层高度为4000mm,故不需分段 5.3填料层压降计算 采用Eckert通用关联图计算 横坐标为 由表2-4-1得,1 176 P m φ- = 纵坐标为 查Eckert通用关联图,P ?/Z位于40g~50gPa/m范围内,取 P ?/Z=45g=441.45Pa/m
填料层压降为 ?=441.45?4.0=1765.80Pa P 6液体分布器的简要设计 6.1液体分布器的选型 本设计的吸收塔气液相负荷相差不大,无固体悬浮物和液体粘度不大,加上设计建议是优先选用槽 盘式分布器,所以本设计选用槽盘式分布器。 6.2分布点密度计算 按Eckert建议值,1200 m,由于该塔喷淋密度较小,设计区分喷淋D≥时,喷淋点密度为42点/2 点密度为90点/2 m。 槽宽度为
第四章塔径泛点气速空塔气速填料高度压降等计算
第四章 填料精馏塔的工艺计算 4.1 低压塔塔径、泛点气速、空塔气速、填料高度及压降计算 由第一章PROII 模拟出的说明书可以得到数据表4.1 塔顶蒸汽量G 2 塔中蒸汽量G 14 塔中蒸汽量G 15 塔底蒸汽量G 27 4368Kg/HR 4383Kg/HR 4445Kg/HR 4886Kg/HR 塔顶液体量L 1 塔中液体量L 13 塔中液体量L 14 塔底液体量L 26 3140Kg/HR 3155Kg/HR 7784Kg/HR 8224Kg/HR 汽相密度ρG2 汽相密度ρG14 汽相密度ρG15 汽相密度ρG27 2.874369Kg/m 3 3.03973Kg/m 3 3.06215Kg/m 3 3.34082Kg/m 3 液相密度ρL1 液想密度ρL13 液相密度ρL14 液相密度ρL26 816.676Kg/m 3 796.028Kg/m 3 793.248Kg/m 3 777.496Kg/m 3 汽相粘度μG2 汽相粘度μG14 汽相粘度μG15 汽相粘度μG27 8.9907E-06Pa ·s 9.1563E-06Pa ·s 9.1528E-06Pa ·s 9.0660E-06Pa ·s 液相粘度μL1 液想粘度μ L13 液相粘度μ L14 液相粘度μ L26 3.1054E-04Pa ·s 2.6658E-04Pa ·s 2.6165E-04Pa ·s 2.2445E-04Pa ·s 根据表4.1求平均值可得下表4.2 表4.2 低压塔 精馏段 提馏段 液体量L Kg/HR 3147.5 8004 液相密度ρ Kg/m 3 806.352 785.372 液相粘度μ Pa ·s 2.8856 E-04 2.4305 E-04 蒸汽量G Kg/HR 4375.5 4665.5 汽相密度ρ Kg/m 3 2.957045 3.201485 4.1.1 塔经的计算 L G G L FP ρρ= 式中:L ——塔内液相流率,Kg/h ; G ——塔内气相流率,Kg/h ; ρG ——塔内气相密度,Kg/m 3; ρL ——塔内液体密度,Kg/m 3。 由表4-2数据代入公式得: 对于精馏段:
填料塔工艺尺寸的计算
填料塔工艺尺寸的计算 Document number:NOCG-YUNOO-BUYTT-UU986-1986UT
第三节 填料塔工艺尺寸的计算 填料塔工艺尺寸的计算包括塔径的计算、填料能高度的计算及分段 塔径的计算 1. 空塔气速的确定——泛点气速法 对于散装填料,其泛点率的经验值u/u f =~ 贝恩(Bain )—霍根(Hougen )关联式 ,即: 2213lg V F L L u a g ρμερ?? ?????? ? ???????=A-K 14 18 V L V L w w ρρ???? ? ??? ?? (3-1) 即:1124 8 0.23100 1.18363202.59 1.1836lg[ ()1]0.0942 1.759.810.917998.24734.4998.2F u ?????? =- ? ? ??????? 所以:2 F u /(100/3)()= UF=3.974574742m/s 其中: f u ——泛点气速,m/s; g ——重力加速度,9.81m/s 2 W L =㎏/h W V =7056.6kg/h A=; K=; 取u= F u =2.78220m/s 0.7631D = = = (3-2) 圆整塔径后 D=0.8m 1. 泛点速率校核:2 6000 3.31740.7850.83600 u = =?? m/s 则 F u u 在允许范围内 2. 根据填料规格校核:D/d=800/50=16根据表3-1符合 3. 液体喷淋密度的校核: (1) 填料塔的液体喷淋密度是指单位时间、单位塔截面上液体的喷淋量。
(2) 最小润湿速率是指在塔的截面上,单位长度的填料周边的最小液体体积流量。对于直径不超过75mm 的散装填料,可取最小润湿速率()3min 0.08m /m h w L ?为。 ()32min min 0.081008/w t U L m m h α==?=? (3-3) 22 5358.8957 10.6858min 0.75998.20.7850.8L L w U D ρ= ==>=???? (3-4) 经过以上校验,填料塔直径设计为D=800mm 合理。 填料层高度的计算及分段 *110.049850.75320.03755Y mX ==?= (3-5) *220Y mX == (3-6) 3.2.1 传质单元数的计算 用对数平均推动力法求传质单元数 12 OG M Y Y N Y -= ? (3-7) ()* *1 1 22*11*22 () ln M Y Y Y Y Y Y Y Y Y ---?= -- (3-8) = 0.063830.00063830.03755 0.02627ln 0.0006383 -- = 3.2.2 质单元高度的计算 气相总传质单元高度采用修正的恩田关联式计算: () 0.75 0.10.05 2 0.2 2 21exp 1.45/t c l L t L L V t w l t l L U U U g ασαρσαασαμρ-????????? ? =--?? ? ? ??? ????? ?? ? (3-9) 即:αw/αt =0. 液体质量通量为:L u =WL/××=10666.5918kg/(㎡?h ) 气体质量通量为: V u =60000×=14045.78025kg/(㎡?h)
现代填料塔技术在氯气干燥中的应用_董谊仁
【氯氢处理】 现代填料塔技术在氯气干燥中的应用 董谊仁1 *,黄奕平 2 (1.浙江工业大学化材学院,浙江杭州310053;2.杭州中昊科技有限公司,浙江杭州310053) [关键词]氯气;干燥;填料塔;塔填料;液体分布器;气体分布器 [摘 要]介绍现代填料塔技术在氯气干燥工艺中的应用,包括塔填料的选择,液体分布器和气体分布器等塔内件的合理应用,氯气干燥塔优化设计要点,氯气干燥装置工业应用实例。 [中图分类号]TQ 028.2 [文献标识码]B [文章编号]1008-133X (2006)09-0014-03 1 概 述 近10年来,我国烧碱生产能力已达到1200多万t /a 。氯气干燥工艺却相对落后,许多企 业氯中含水量偏高,在0.01%以上,除雾问题也解决得不够好。为改变这种状况,通过不懈的工作,研究出现代填料塔技术,并应用于氯气干燥。氯气干燥工艺的特点是:①干燥的要求高,水分含量应达到国际水平,低于0.002%;②系统多微负压操作,允许的总压降小,一般控制在不高于10kPa ;③操作负荷可能有较大波动,故要求装置的操作弹性大;④氯气属于剧毒介质,腐蚀性强,对安全操作要求高,绝对不允许外漏。 填料塔具有效率高、通量大、压降低、操作弹性大、持液量小、适应性强等优点,可以满足氯气干燥工艺的各项要求。而要达到这些要求,在实际生产过程中能稳定地实现诸项工艺指标,绝非易事,除了通过保持生产的稳定性,严格控制流程中各项操作工艺指标外,填料塔技术的合理应用是关键一环。 2 现代填料塔技术在氯气干燥中的应用 作为化工生产中最常用的气液传质设备,填料塔结构看似简单,其理论问题却十分深奥,涉及到填料层内气、液两相随机流动和传质、气体入塔的预分布规律、液体分布器中液体均匀分布规律及其评价 方法、填料层结构对气、液流动影响等众多课题的研究。为此,笔者曾进行20多年探索,近10年又完成了百余座大中型工业氯气干燥塔的设计、制作和应用,以下就此谈些粗浅体会。 2.1 合理选择塔填料 [1、2、3] 金属板波纹是1982年、短阶梯环填料是1996年由浙江工业大学首先开发并应用于氯气干燥塔中,前者是公认的高效规整填料,后者具有几何结构合理、比表面积大、孔隙率大、床层耐压、不易破损等优点,因此其流体均布性能好,传质效率高,通量大,压降低,持液量小,是综合性能优良的散装填料。多年实践证明,这两种物质适用于氯气干燥塔。其材质有多种,如聚丙烯(PP )、聚氯乙烯(PVC )、氯化聚氯乙烯(CPVC )。PP 适于在硫酸质量分数80%左右的干燥塔中使用,价格便宜,相对密度较小;PVC 适于在以浓硫酸为介质的干燥塔中使用,多年操作仍不会脆化;当温度在60℃以上时,宜选CPVC 。实践证明,按此原则选择填料的使用寿命超过4年。 当氯气中含水量已降到很低时(如0.01%左右),由于其水蒸气分压很小,干燥过程的传质推动力亦相应下降到很低值,过程的进行会变得非常困难,为此,最后一座塔选用了不同型号优化组合的高效金属板波纹填料,经3年实践证明,效果良好。2.2 匹配合适的液体分布器 [4、5] 填料塔设计中,塔内件尤其是液体分布器至关重要。特别是大型塔,合理选用液体分布器是成功的关键。其原因是:①不良液体初始分布必然导致干燥效率急剧下降;②不良初始分布难以达到填料层的自然流分布;③新型高效填料径向扩散系数一般较小,更依赖于良好的初始分布。 评价液体分布器性能的标准有5条:①操作可 14 第9期2006年9月 氯碱工业C hlor -A lka li I ndustr y N o .9Sep.,2006*[作者简介]董谊仁(1937-),男,教授,1960年毕业于浙江工业大学化工系,现在浙江工业大学化材学院任教,专业 从事塔设备研究20多年,发表论文40余篇。近10多年在国内7省15个大中型氯碱企业推广了氯气干燥和除雾成套技术,在3个大型聚氯乙烯企业推广水碱洗系统组合塔技术,效益显著。 [收稿日期]2005-12-12
填料塔计算部分
填料塔计算部分 This manuscript was revised by the office on December 10, 2020.
二 基础物性参数的确定 1 液相物性数据 对于低浓度吸收过程,溶液的物性数据可近似取纯水的物性数据。由手册查得,2 气相物性参数 设计压力: ,温度:20C ? 氨气在水中的扩散系数:92621.7610/ 6.33610/L D cm s m h --=?=? 氨气在空气中的扩散系数: 查表得,氨气在0°C ,在空气中的扩散系数为 2/cm s , 根据关系式换算出20C ?时的空气中的扩散系数: 3 32 2 00022293.150.171273.150.189/0.06804/V P T D D P T cm s m h ?????? ==?? ? ? ??????? == 混合气体的平均摩尔质量为 m i 0.05170.982929.27V i M y M ==?+?=∑ 混合气体的平均密度为 3m 101.329.27 1.2178.314293.15 V Vm PM kg m RT ρ?===? 混合气体的粘度可近似取空气的粘度,查手册得20C ?空气粘度为 51.81100.065()V Pa s kg m h μ-=??=? 3 气液相平衡数据
由手册查得,常压下20C ?时,氨气在水中的亨利系数 76.3a E kP = 相平衡常数 76.30.7532101.3 E m P === 溶解度系数 3s 998.2 0.726076.318.02 L H kmol kPa m EM ρ= = =?? 4 物料衡算 进塔气相摩尔比 1= 110.05 0.05263110.05 y Y y ==-- 出塔气相摩尔比 321(1)0.05263(10.98) 1.05310A Y Y ?-=-=-=? 混合气体流量 330.1013(273.1520) 16.10100.1013273.15 V N Q Q m h ? ?+==?? 惰性气体摩尔流量 273.15(10.05)636.1622.4273.1520 V Q V kmol h =?-=+ 该吸收过程属低浓度吸收,平衡关系为直线,最小液气比可按下式计算: 1212 L Y Y V Y m X -??= ? -?? 对于纯溶剂吸收过程,进塔液相组成 20X = min 0.052630.0010530.73810.052630.7532L V -??== ??? 取操作液气比为 min 1.4L L V V ?? = ??? 1.40.7381 1.0333L V =?= 1.0333636.16657.34L kmol h =?= 1212()636.16(0.052630.001053) 0.0499657.34 V Y Y X X L -?-=+==
精馏工段文献综述
吉林化工学院化工与生物技术学院课程设计文献综述 学生学号: 学生姓名: 专业班级: 指导教师: 起止日期: 吉林化工学院 Jilin Institute of Chemical Technology
1前言 填料塔技术用于各类工业物系的分离,虽然设计的重点在塔体及塔内件等核心部分,但与之相配套的外部工艺和换热系统应视具体的工程特殊性作相应的改进。例如在DMF回收装置的扩产改造项目中,要求利用原常压塔塔顶蒸汽,工艺上可以在常压塔及新增减压塔之间采用双效蒸馏技术,达到降低能耗、提高产量的双重效果,在硝基氯苯分离项目中;改原多塔精馏、两端结晶工艺为单塔精馏、端结晶流程,并对富间硝基氯苯母液进行精馏分离,获得99%以上的间硝基氯苯,既提高产品质量,又取得了降低能耗的技术效果。 综合考察各分离过程的优缺点:分离技术就是指在没有化学反应的情况下分离出混合物中特定组分的操作。这种操作包括蒸馏,吸收,解吸,萃取,结晶,吸附,过滤,蒸发,干燥,离子交换和膜分离等。利用分离技术可为社会提供大量的能源,化工产品和环保设备,对国民经济起着重要的作用。 为了使填料塔的设计获得满足分离要求的最佳设计参数(如理论板数、热负荷等)和最优操作工况(如进料位置!回流比等),准确地计算出全塔各处的组分浓度分布(尤其是腐蚀性组分)、温度分布、汽液流率分布等,常采用高效填料塔成套分离技术。而且,20世纪80年代以来,以高效填料及塔内件为主要技术代表的新型填料塔成套分离工程技术在国内受到普遍重视。由于其具有高效、低阻、大通量等优点,广泛应用于化工、石化、炼油及其它工业部门的各类物系分离。 2 国内外研究现状 2.1我国酒精精馏技术发展背景 食用酒精新标准的颁布实施国家有关部门根据我国酒精生产企业生产状况,并参照目前国际上发达国家的酒精质量标准,决定修订我国现有的酒精产品质量的国家标准,新的食用酒精标准于2012年9月1日实施。新标准中的各项杂质指标与原标准相比都有一定的改善,新增的特优级酒精产品的指标与目前发达国家食用酒精标准接轨,可直接用于各种高级饮料酒的勾兑。从长远看,修订后的国家酒精产品的质量标准,将促进我国各酒精企业的结构调整,提高酒精产品的总体生产技术水平,增强中国酒精企业参与国际市场的竞争能力。
现代传质理论与塔器技术课程论文
填料塔技术发展 摘要:填料塔作为一种传质设备,具有效率高、压降低、持液量小、构造简单、安装容易、投资少等优点,广泛用于分离操作。本文论述了国内外填料塔技术的发展现状,详细介绍了各种散堆填料、规整填料,塔内件等,同时展望了填料塔今后发展趋势和技术开发方向。 关键词:填料塔、散装填料、规整填料、液体分布装臵 1.引言 填料塔是以塔内的填料作为气液两相间接触构件的传质设备,它是化工类企业中最常用的气液传质设备之一。而塔填料、塔内件及工艺流程又是填料塔技术发展的关键。近年来,随着高效新型填料和其他高性能塔内件的开发,以及人们对填料流体力学、放大效应及传质机理的深入研究,使填料塔技术得到了迅速的发展。 2.填料分类及发展 2.1填料塔 填料塔是气、液呈逆流的连续性接触的气液传质设备,它的结构和安装比板式塔简单。塔的底部有支撑板用来支撑填料,并允许气、液通过。支撑板上的填料有整砌和乱堆两种方式。填料层的上方有液体分布装臵,从而使液体均匀喷洒于填料层上。填料层中的液体有向塔壁流动的“趋壁”倾向,因此填料层较高时往往将其分为几段,每一段填料层上方设有液体再分布器,使流到壁面的液体集于液体在分布器作重新分布。
2.2塔填料 塔填料的发展,大致分四个阶段:以焦炭、卵石、铁屑等作为填料的初始阶段;拉西环诞生和弧鞍填料的出现为第二阶段;1948年鲍尔环问世,作为第三阶段起点;70年代开始各种高效规整和散装填料开发和应用,填料塔大型化为第四阶段。 填料的类型很多,按照制成填料的材料是实体还是网体可分为实体填料和网体填料两类。实体填料有陶瓷、金属或塑料等制成,如拉西环、鲍尔环、阶梯环、弧鞍形和矩鞍填料等;网体填料有金属丝制成,如形网环、网状鞍形填料、网波纹填料等。按照填料在塔内堆积的方法不同可分为乱堆填料和整砌填料两类。乱堆填料有颗粒形填料如拉西环、鞍形填料、鲍尔环、阶梯环等作无规则推挤而成;整砌填料则常由规整的填料整齐砌成,也可由拉西环等颗粒填料砌成。 (1)散装填料 矩鞍环:对弧鞍形环的改进,主要区别在于将一对弧形面改为矩形面,且内外曲率半径不同,从而避免了容易叠套的缺陷,使床层孔隙率均匀,改善了液体分布性能与拉西环相比液泛点高,压降和传质单元高度较低。 扁环填料:高径比为1:2,取消了阶梯环的翻边,采用内弯弧形筋片来提高填料的强度,在乱堆时能有序排列,流道更合理,压降低。 阶梯环:吸取拉西环的优点又对鲍尔环进行改进,即环的高径比仅为鲍尔环的一半,关在环的一端增加了锥形翻边。这样减少了气体通量,填料的强度也提高了,由于结构特点,使气液分布均匀。
填料塔计算和设计
填料塔计算和设计
填料塔计算和设计 Pleasure Group Office【T985AB-B866SYT-B182C-BS682T-STT18】
填料塔设计 2012-11-20 一、填料塔结构 填料塔是以塔内装有大量的填料为相间接触构件的气液传质设备。填料塔的塔身是一直立式圆筒,底部装有填料支承板,填料以乱堆或整砌的方式放置在支承板上。在填料的上方安装填料压板,以限制填料随上升气流的运动。液体从塔顶加入,经液体分布器喷淋到填料上,并沿填料表面流下。气体从塔底送入,经气体分布装置(小直径塔一般不设置)分布后,与液体呈逆流接触连续通过填料层空隙,在填料表面气液两相密切接触进行传质。填料塔属于连续接触式的气液传质设备,正常操作状态下,气相为连续相,液相为分散相。二、填料的类型及性能评价 填料是填料塔的核心构件,它提供了气液两相接触传质的相界面,是决定填料塔性能的主要因素。填料的种类很多,根据装填方式的不同,可分为散装填料和规整填料两大类。散装填料根据结构特点不同,分为环形填料、鞍形填料、环鞍形填料等;规整填料按其几何结构可分为格栅填料、波纹填料、脉冲填料等,目前工业上使用最为广泛的是波纹填料,分为板波纹填料和网波纹填料; 填料的几何特性是评价填料性能的基本参数,主要包括比表面积、空隙率、填料因子等。1.比表面积:单位体积填料层的填料表面积,其值越大,所提供的气液传质面积越大,性能越优; 2.空隙率:单位体积填料层的空隙体积;空隙率越大,气体通过的能力大且压降低;
3.填料因子:填料的比表面积与空隙率三次方的比值,它表示填料的流体力学性能,其值越小,表面流体阻力越小。 三、填料塔设计基本步骤 1.根据给定的设计条件,合理地选择填料; 2.根据给定的设计任务,计算塔径、填料层高度等工艺尺寸; 3.计算填料层的压降; 4.进行填料塔的结构设计,结构设计包括塔体设计及塔内件设计两部分。 四、填料塔设计 1.填料的选择 填料应根据分离工艺要求进行选择,对填料的品种、规格和材质进行综合考虑。应尽量选用技术资料齐备,适用性能成熟的新型填料。对性能相近的填料,应根据它的特点进行技术经济评价,使所选用的填料既能满足生产要求,又能使设备的投资和操作费最低。 (1)填料种类的选择 填料的传质效率要高:传质效率即分离效率,一般以每个理论级当量填料层高度表示,即HETP值; 填料的通量要大:在同样的液体负荷下,在保证具有较高传质效率的前提下,应选择具有较高泛点气速或气相动能因子的填料; 填料层的压降要低:填料层压降越低,塔的动力消耗越低,操作费越小;对热敏性物系尤为重要;
现代塔器技术11
填料塔技术及其应用 摘要:填料塔是化工工业中最常见气液分离设备之一,本文介绍了填料塔的塔型,填料选取,填料塔内件,及其内部流体力学的模拟,并对填料塔的前景进行展望。 关键字:填料塔;分离设备;填料 Abstacat:Packed column is one of the most common liquid-vapor separation equipment in the chemical industry , In this paper, it has introduced the column type , the packing selected , the packing internals, and its internal fluid dynamics simulation ,of the packed column. It also make a prospect of the packed column. Key Words: Packed column Separation equiment Packings 塔设备早已广泛用于蒸馏、吸收、解吸、萃取、洗涤冷却等各种过程。塔设备根据结构不同可分为板式塔和填料塔两大类。填料塔可细分为规整填料塔和散堆填料塔。有时也采用混合型填料塔,即在同一座填料塔中,有散堆填料层,也有规整填料层。由于板式塔和填料塔的传质机理不同,故二者的性能有较大的差别。塔性能比较最主要考虑效率、通量、和压降三个因素[1]。塔板的开孔率一般为塔截面积的8%~15%。时要考虑塔板有效面积和降液管面积的权衡。填料塔的开孔面积大于塔截面积空隙率都在50%以上。其液泛点都较高,故填料塔的生产能力较大。通常塔板的等板高度都大于500mm,即每米理论板数不超过2块,而工业填料塔的当量理论板数可达10块以上。因而填料塔效率较高。一般情况下塔的每块理论板压降塔式板为0.4~1.07kp散堆填料为0.13~0.27kp规整填料为0.0013~0.107kp。压降小有利于节能。 1塔型的选择 在填料塔设计中,首要的是塔型的选择,填料塔塔型选择的一般原则为[1]:(1)易起泡沫的物系以选用填料塔为宜,填料能使泡沫破裂。而板式塔上泡沫易引起塔的液泛。(2)热敏性物料的分离,尽可能降低塔釜温度,避免由于过热而导致的物料聚集或分解。目前这个物系已普遍采用高效、低压降的规整填料。其压降小、持液量低。(3)对难分离物系,采用热泵技术可节能80%以上,宜采用填料塔难。分离物系的塔顶塔底温度较接近,采用低压降填料,会有更好的节能效果。(4)现有塔器的增产、节能、降耗一般可采用高效填料改造原有塔板,达到与其目标。(5)厂房高度受限场合或精密分离需要很多理论分离级时,应优先考虑采用高效填料塔。(6)对腐蚀性介质,宜采用填料塔,因为填料容易实现用各种防腐材料来制作。(7)粘度较大的物系,选用水力直径较大的填料,而板式塔的传质效率较差。(8)含固体颗粒或污浊的物料,不宜采用填料塔,因为容易将填料通道堵塞。(9)在塔内易产生聚合物,经常需要清洗的塔,以选用板式塔为宜,填料塔易堵,且填料表面的聚合物积聚清理困难。(10)新建项目,一般板式塔造价低于填料塔。只有在高压操作情况下,采用大通量填料,可减小塔径从而使塔壁厚减小。权衡投资比较填料塔的造价有可能低于板式塔,(11)一般而言,板式塔的操作弹性要大于填料塔。规整填料自身的操作弹性较大,但其弹性受制于液体分布器的操作弹性。(12)具有多侧线进料或出料的塔器,板式塔较易实现。填料塔则在每个侧线口必须分段,各填料层之间,都应设置液体收集和再分布装置。 2 填料的选取