热加工处理对Ti-Cu基非晶合金组织与力学性能的影响

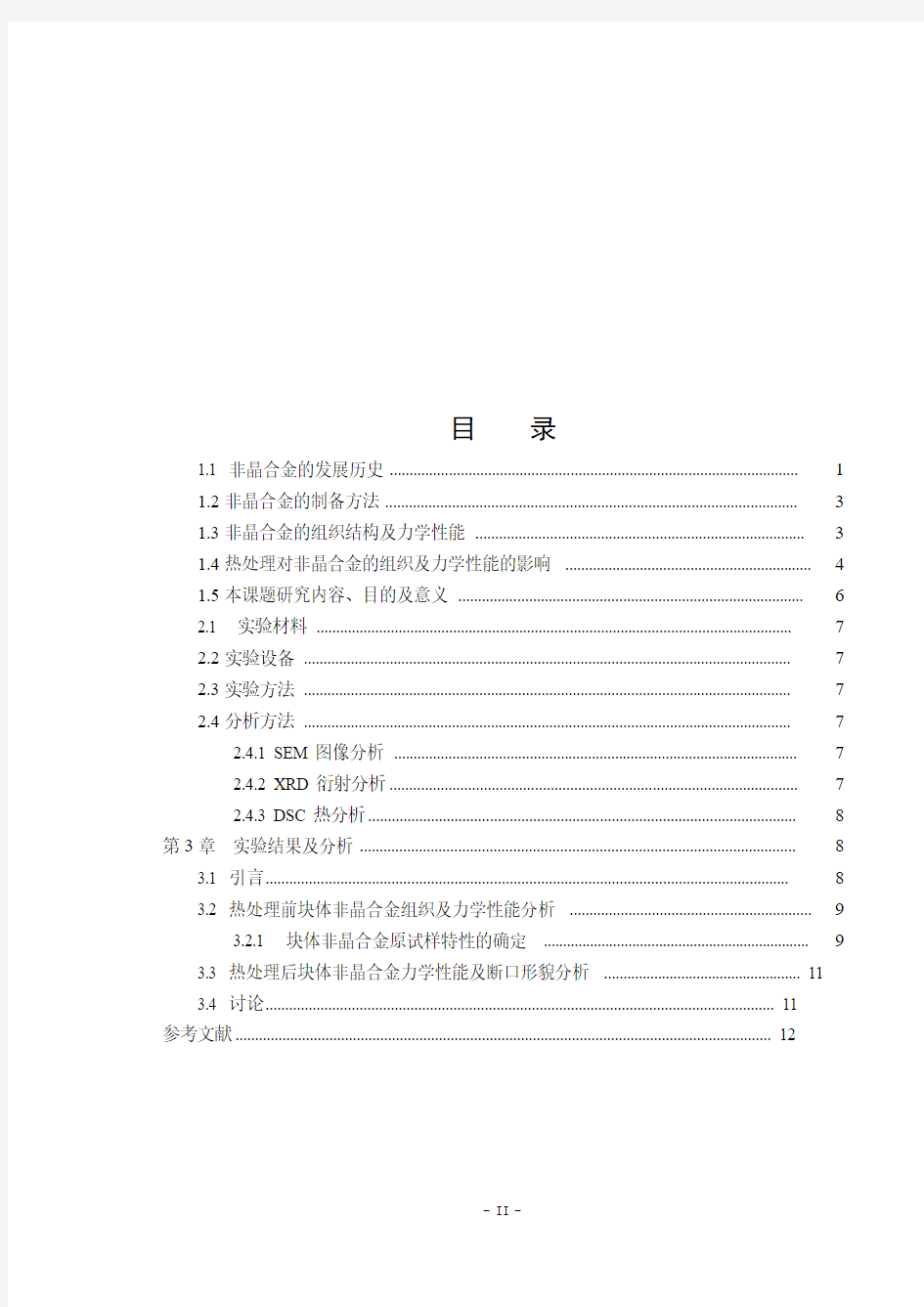
热加工处理对Ti-Cu基非晶合金组织与力
学性能的影响
目录
1.1 非晶合金的发展历史 (1)
1.2非晶合金的制备方法 (3)
1.3非晶合金的组织结构及力学性能 (3)
1.4热处理对非晶合金的组织及力学性能的影响 (4)
1.5本课题研究内容、目的及意义 (6)
2.1 实验材料 (7)
2.2实验设备 (7)
2.3实验方法 (7)
2.4分析方法 (7)
2.4.1 SEM图像分析 (7)
2.4.2 XRD衍射分析 (7)
2.4.3 DSC热分析 (8)
第3章实验结果及分析 (8)
3.1 引言 (8)
3.2 热处理前块体非晶合金组织及力学性能分析 (9)
3.2.1 块体非晶合金原试样特性的确定 (9)
3.3 热处理后块体非晶合金力学性能及断口形貌分析 (11)
3.4 讨论 (11)
参考文献 (12)
第1章绪论
1.1 非晶合金的发展历史
非晶合金是指不具有长程有序但短程有序(包括化学短程有序和拓扑短程有序两种)的金属和合金,因其具有金属合金的一些特性,故它们也被称为金属玻璃或者非结晶合金,属于非晶态材料中新兴的分支。非晶态薄膜的出现起源于20世纪30年代末,1938年,Kramer[1]用蒸发沉积方法获得的非晶合金薄膜。此后不久,Brenner等人[2]采用电沉积法制备了Ni-P非晶薄膜,用作耐磨、耐腐蚀涂层。1959年,美国物理学家Turnbull[3]提出液态金属可以过冷到远离平衡熔点以下而不产生形核与长大。根据他的理论,在一定条件下,液态金属可以冷却到非晶态,因此,Turnbull实际上是非晶态合金的理论奠基人。
1960年,Duwez等人[4]采用熔体快速冷却的方法(急冷法,冷却速度可以达到105~106K/s)首先制得20μm厚的Au-Si非晶合金薄片,预示着没有晶界的新型金属材料的问世,这就是大家所熟知的世界上首次报道的非晶合金。Duwez工作的重要意义在于采用快冷技术比气相沉积其他方法更容易使大量合金形成非晶态。1969年,非晶合金的制备有了突破性进展,Pond等人[5]用轧辊法制备出了长达几十米的非晶薄带。同年,Chen 和Turnbull[6]制备出三元Pd77.5Cu6Si16.5合金可以形成直径为0.5mm的玻璃态样品,并且存在玻璃化转变,其过冷液态区间T xg(T xg=T x-T g,晶化温度T x、玻璃转变温度T g)可达40K,这使研究人员能够从事有关金属玻璃晶化的详细研究。1974年,Chen等[7]用吸铸方式成功获得毫米级的Pd-Cu-Si非晶合金,标志着块状非晶合金的问世(通常将临界尺寸不小于1mm 的非晶合金称为块状非晶)。
20世纪80年代,贵金属非晶合金仍然一统天下。先后出现Au55Pb22.5Sb22.5[8]、Pd40Ni40P20[9,10]等块体非晶。Turnbull小组[9,10]通过一系列连续加热-冷却-再加热处理,减少了样品中的异质形核点,获得了直径为5mm的Pd40Ni40P20非晶铸锭;随后,用B2O3对Pd40Ni40P20合金熔体进行“渣化”处理技术来消除合金中的非均质形核,临界冷却速度大大降低,仅为10K?s-1,最终获得10mm的非晶棒。Pd-Ni-P合金的开发通常被认为是第一次块状金属玻璃(bulk metallic glass,BMG)研究工作的高潮。在这一阶段,由于非晶制备尺寸的限制,使得非晶合金无法作为结构材料得到应用,但当时人们却利用
连续铸造工艺制备商用非晶带、线和板材,在变压器铁芯和磁传感器方面获得了广泛应用,非晶科学和工业研究达到了一个高峰。
贵金属基块体非晶合金的形成是令人振奋的,但其价格昂贵,人们对块体非晶合金的兴趣从新颖性逐渐消退。尽管如此,人们对新块体非晶合金体系的探索和相关研究始终在继续。20世纪80年代末,Inoue等在日本东北大学成功发现了主要由普通元素组成的新多组元合金系。La-Al-Ni和La-Al-Cu[11]等三元合金系,通过水冷铜模铸造法(copper mould casting,CMC)获得了直径为5mm的完全非晶柱状样品,用部分Cu取代该合金中的Ni元素,La55Al25Ni10Cu10的临界直径可达9mm。在1991年,该组分别采用铜模铸造法和高压模铸造法制备出临界直径分别可达4mm(CMC)和7mm(high pressure die casting,HPDC)的Mg65Cu25Y10块体非晶[12,13]。与此同时Inoue小组还开发出Zr基非晶合金[14],Zr-Al-Ni-Cu体系具有高的玻璃形成能力与热稳定性,合金的临界尺寸可达15mm,过冷液相区扩大到127K。Johnson很快认识到Inoue工作的重要性,开始研究块体非晶成分的制备,并在1993年开发出五元(quinary)Zr-Ti-Ni-Cu-Be非晶合金[15],该合金具有明显的玻璃转变、高的过冷液态稳定性和反晶化热稳定性,临界尺寸可达几十毫米,被称为Vitreloy1(Vit 1)。这项工作连同Inoue的工作可以视为块状玻璃态材料在结构材料方面应用的起点,从而掀起了非晶合金研究工作的第二次高潮。Inoue的工作打开了一扇新的块体非晶合金体系设计之门,20世纪90年代以来,越来越多的材料和物理学家将注意力集中到块体非晶合金的研究上来。迄今为止,短短的十几年间,研究者们已经发现了一系列包括Pd、Mg、La、Zr、Ti、Fe、Ni、Cu、Nd、Pt基等在内的具有较大玻璃形成能力的非晶合金。目前,Pd40Cu30Ni10P20合金可以形成块体非晶合金的最低冷却速率为0.1K/s,其最大样品直径可以达到72mm以上[16]。
2007年中国科学院物理研究所汪卫华研究组在非晶合金的塑性研究中取得的重要进展[17]。他们成功研制出在室温条件下同时具有超高塑性和超高强度的块体非晶合金材料,并对其进行了结构分析,提出了探索塑性大块非晶的新方法,在物理上证明高强度和大塑性(结构材料最重要的两个性质)在非晶材料中可以有机结合在一起。此外,该材料的组元均是价格较低廉的常见金属,结合其优良的性能,使得该非晶合金有望得到广泛的实际应用。该组研究人员利用常用的Zr、Cu、Ni和Al金属元素,根据自己提出的模量判据,通过快速凝固的现代冶金手段,合成出了在室温条件下具有超高压缩塑性的非晶合
金。不同于以往的非晶合金,这种新开发的材料在室温下的压缩塑性变形能力非常强,可以像常见的纯Cu,纯Al一样弯曲或形变成一定的形状。在具有超高塑性的同时,该材料还具有非晶合金高强度的特点。结构分析表明,这种非晶合金具有一种特殊的微观结构,正是这种特殊的结构使其具有优异的塑性。人们通常认为高度局域化并软化的剪切带是非晶合金材料脆性的原因,这项工作表明通过合适的成分和结构调制,可以有效控制剪切带的形成、运动和扩展,从而有效改善非晶合金的塑性,而且不影响非晶的高强度的特点。同时,他们还提出探索塑性大块非晶的新方法:即非晶合金的塑性对其成分很敏感,这种成分敏感性可用泊松比来有效地标定,从而可利用材料成分随泊松比的变化规律来探索出具有大塑性的非晶材料。
1.2非晶合金的制备方法
在早期,非晶材料的制备,首先采用快速凝固法制备非晶粉末,然后用粉末冶金方法将粉末压制或粘结成型。20世纪90年代初发现了具有极低临界冷却速率的合金系列,可以直接从液相获得块体非晶固体。目前,块体非晶合金的制备方法基本可划分为直接凝固法和粉末固结成形法。
1.3非晶合金的组织结构及力学性能
非晶合金是指短程有序(包括化学短程有序和拓扑短程有序两种)的金属和合金。由于它具备金属合金的一些特性,又被称为玻璃态合金或者非结晶合金。其主要主要特征有以下四点:
1)以金属键为主要结构特征;
2)短程有序,长程无序;
3)均匀成无序结构;
4)亚稳性,熔点以下晶态总是自由能最低的状态,非晶态固体总有向晶态转化的
趋势;
5)各向异性。
晶体结构的根本特点是周期性,即通过点阵平移操作可以实现自身重合。而在非晶体中,不存在这种周期性,非晶态合金呈无规则密堆结构,其原子在空间排布无长程有序。但是它与液体无序结构中的原子的自由运动不同,非晶态合金中原子的主要运动是在平衡位置附近的热振动。理想的非晶体可以看做是由一个无限延伸的单胞组成。
非晶合金的这种无序性结构是在由液态金属向非晶态转化的过程中保留下来的。当液态金属在T g(玻璃转变温度) 块体非晶合金由长程无序短程有序的结构而具有优异的性能,作为一种新型材料,块体非晶合金不仅具有极高的强度、硬度、耐磨性、耐腐蚀性等。 1.4热处理对非晶合金的组织及力学性能的影响 热处理工艺在在材料尤其是金属合金材料领域占有不可或缺的地位。热处理可以明显改善材料的力学、化学等性能,也因此得到了相当广泛的研究。但在非晶材料领域,对于热处理的研究却是刚刚起步。2005年曾有人研究了热处理对Zr57Cu15.4Ni12.6Al10Nb5[31]和Fe61Co10Zr5W4B20[33]的块体非晶合金的微观结构、性能及显微硬度的影响,他们对 Zr57Cu15.4Ni12.6Al10Nb5所采用的试验方法是在703K和743K(该合金的T g为697.5K,T x 为747.4K)等温退火5min,10min,20min,30min,60min,然后观察组织结构并测试压缩应力曲线。试验结果为该合金在703K下长达60min时间内依然表现为非晶态。但在743K时,20min后,XRD衍射曲线的主峰出现分离,到60min后出现多个晶态衍射峰。由此他们认为决定非晶合金晶化的主要外因是温度。在稍高于玻璃转变温度T g但远低于晶化温度T x下进行热处理,非晶合金主要发生结构驰豫,在远高于玻璃转变温度T g稍低于晶化温度T x的温度进行热处理,主要发生晶化过程。研究表明: 1) 块体非晶合金Zr57Cu15.4Ni12.6Al10Nb5在稍高于玻璃转变温度T g下热处理时,主要发生结构驰豫,在远高于玻璃转变温度T g但稍低于晶化温度T x下进行热处理,在时间稍长时将出现晶化转变。 2) 非晶合金的显微硬度约为462 HV,热处理后其硬度随热处理时间增长有整体升高的趋势。 3) Zr57Cu15.4Ni12.6Al10Nb5非晶合金原始态的抗压强度与相对压缩率均为最大,σbc达1705MPa,εc约为0.104%。热处理后合金的σbc与εc随着退火时间的增加,抗压强度和相对压缩率有下降趋势。 4) Zr57Cu15.4Ni12.6Al10Nb5合金的压缩断口显微形貌,对热处理反映敏感。随着退火时间的增长,合金断裂特征由典型脉状河流花纹的准延性断裂逐渐向脆性断裂转变。 针对非晶合金Fe61Co10Zr5W4B20取了四个热处理温度点分别是530℃、570℃、630℃和670℃,其中该非晶合金的玻璃转变温度T g=561.1℃,晶化起始温度T x=619.0℃。在这四个不同温度下等温热处理60min,结果表明: 1) 随着热处理温度的升高,合金硬度明显增大,推测可能是析出纳/亚微米晶态相的弥散强化的结果。 2) 在高于玻璃转变温度(T g=561.1℃)且低于晶化起始温度(T x=619.0℃)的570℃等温热处理后,Fe61Co10Zr5W4B20块体非晶合金基本保持非晶结构,其显微硬度值也基本保持不变。该块体非晶合金在高于晶化峰值温度(T p=632.6℃)的670℃等温热处理后,合金会有晶态相析出。同时由于有晶态相析出,出现弥散强化,从而引起合金的显微硬度的提高。但处理时间较长时,析出相可能长得过大,弥散强化效果可能下降,硬度又出现下降。块体非晶合金在热处理时间相同的条件下,随着热处理温度的升高,合金的硬度增大,但压缩强度逐步减小。 李萍,郝静燕等[34]系统地研究了结构驰豫对Cu58.1Zr35.9Al6块状非晶合金弹性性能的影响。他们将Cu58.1Zr35.9Al6非晶合金在150℃、300℃、450℃分别保温1 h。测量退火样品的纵、横波声速,并推算其弹性性能。结果表明:随退火温度的升高,声速与弹性性能呈现逐渐增加的趋势。低温驰豫时声速与弹性性能变化缓慢,高温驰豫时增加明显。基于结构驰豫谱模型分析了上述现象的产生在于:提高温度,原子有足够的条件进行中程与长程扩散,通过发生原子的积聚重排,大量自由体积的湮灭,使非晶样品的有序度得到大大的改善。 元光阴,尹健,丁文江三人采用差示扫描热分析仪,射线衍射和透射电镜研究了Mg-Cu-Ni-Gd系非晶合金的结构弛豫以及力学性能。分析Ni元素对Mg基非晶合金的结构弛豫和力学性能的影响。结果表明,Mg65Cu25Gd10非晶合金在305K下保温180s发生结构弛豫后,出现约1-2nm的中程有序畴。 Mg65Cu25Gd10非晶合金结构弛豫后,局部原子重排而有序化,导致非晶相的自由体积发生变化。可解释为弛豫后中程有序区的产生一方面使自由体积湮灭,另一方面也使自由体积重新分布。上述自由体积变化的结果导致了非晶的脆化。考虑到Mg65Cu25Gd10非晶合金的韧-脆转变温度接近室温,可见Mg-Cu-Gd基非晶结构弛豫易在室温环境中发生,由此可见结构弛豫引起的脆化是非晶合金室温下存放一段时间后力学性能大幅度下降的根源。 可以看出热处理会在一定程度上影响非晶合金的性能。但是,在这方面的研究还有很欠缺。Ti基非晶合金作为非晶中一大类,他具有重量轻,比强度大,非晶形成能力强,制备容易等特点引起了广泛的关注。 1.5本课题研究内容、目的及意义 Ti基非晶合金Ti-Zr-Cu-Nb具有极高的强度、比强度、硬度,良好的弹性、耐蚀性等优点,工程应用前景广阔。但作为非晶合金的共同特点,低塑性使其成为在工程材料方面应用的瓶颈。基于前人的研究,本课题试图通过热处理对Ti-Zr-Cu-Nb非晶合金组织进行改善,非晶合金在室温单向拉伸或压缩条件下通常只有很小或没有宏观的塑性变形,这将导致材料的突然断裂。该现象是由于非晶合金变形时剪切面上只有一个或很少的几个剪切带开动,且剪切带的快速扩展导致的。采用原位析出纳米晶或韧性微米晶,使得材料变形时产生更多的剪切带,导致应力集中分散,从而增强材料的宏观塑性。这种具有高强度、高韧性的非晶基复合材料,将有很好的应用前景。 第2章实验材料及方法 2.1 实验材料 原材料:Ti(99.9wt%)、Zr(99.9wt%)、Cu(99.9wt%)、Ni(99.9wt%)、Nb(99.9wt%)等金属。 其它辅助材料:石墨粉、无水乙醇、清水、氢氟酸、硝酸、蒸馏水等。 2.2实验设备 本实验所需设备主要有: 熔炼采用DSL-300型真空电弧炉;样品浇铸采用SP-30AB型高频感应加热并利用铜模浇铸系统完成样品制备;试样用钳子剪断;非晶鉴定用X射线衍射仪;非晶热稳定性测定用DSC差式扫描量热仪;热处理用热处理炉;力学性能测试采用CSS-55100型电子万能试验机;组织与断口观察用S-3400N型扫描电镜;原料及合金清洗用KQ-50超声波清洗器;以及金相试样制备用预磨机、抛光机。 辅助设备:台式钳、试样夹、砂纸、坩埚、电吹风、镊子等。 2.3实验方法 2.4分析方法 通过热处理前后性能对比分析热处理引起的变化,在通过断口及组织结构观察分析原因。 2.4.1 SEM图像分析 在S-3400N扫描电子显微镜上观察非晶合金及其复合材料棒材横断面的组织、压缩试样的断裂表面和侧表面。采用二次电子像和背散射电子像两种成像模式。二次电子由样品中原子外壳层释放出来,主要用于反映样品表面的形貌特征,背散射电子为入射电子在样品中经散射后再从样品表面射出来的电子,可反映样品表面不同平均原子量的区域差别,用于观察组织中不同原子序数的原子所导致的相的差异。 2.4.2 XRD衍射分析 为确定样品的结构,须进行X-射线衍射分析,所用设备为Rigaku D/max 2400型 X射线衍射仪(Cu Kα辐射,波长λ=1.5405 nm)。扫描范围为15-85°,扫描速度为4deg/min,步长为0.02°,功率为12kW。非晶合金的衍射曲线通常表现为漫散的衍射峰,而晶态合金则表现为衍射曲线上强度各不相同的明锐的衍射峰。 2.4.3 DSC热分析 差示扫描量热分析(DSC)主要用于研究快速凝固合金中亚稳相的转变温度以及转变动力学。对非晶合金而言,采用DSC分析可测定玻璃转变温度T g、晶化温度T x、熔化温度T m、液相线温度T l、晶化焓ΔE和熔化焓ΔH等热力学参数。本文所采用的DSC 差热分析仪为Perkin-Elmer DSC/TGA/D-7,其升温速率最高可达100K?min-1,工作气氛为流动高纯氩气,保护气流60ml?min-1,吹扫气流20ml?min-1。DSC的温度经高纯In和Zn标样校定,温度测量误差为±0.1K,热量测量误差为±0.01mcal。实验中采用石墨坩埚,测量样品的重量一般为20~30mg的片状(块状)样品,升温速率为20K?min-1。 第3章实验结果及分析 3.1 引言 块体非晶合金热处理分析进行的较晚,2005年至今,国内一些学者,如谷建生,魏炳忱,李磊等[35]研究了结构弛豫对Zr64.13Cu15.75Ni10.12Al10块体非晶合金硬度和剪切带特征的影响,根据他们的研究在稍高于玻璃转变温度T g但远低于晶化温度T x下进行热处理,非晶合金主要发生结构驰豫,在远高于玻璃转变T g但稍低于晶化温度T x的温度进行热处理,主要发生晶化过程。铸态DSC曲线在焓弛豫峰之前有一个明显的放热峰。这是由于升温过程中原子运动被激活,由冻结无序的高能态走向较为有序的低能态的低温弛豫过程。都要在已有拓扑结构的基础上,吸收热量达到平衡过冷液的较为无序的高能态,在连续加热的DSC曲线上表现为焓弛豫峰的出现。 国外学者Van den Beukel等[36]人将结构弛豫直观而简洁的用自由体积模型来描述,假设单个原子的平均自由体积变化ΔVf正比于弛豫焓的变化ΔH,即ΔH=βΔVf,其中β对于特定的合金来说是常数。最近Eckert等人测量了块体非晶合金Zr55Cu30Ni5Al10在不同退火程度时的焓变和密度,从实验上证实了弛豫过程中弛豫焓的变化与自由体积的减少呈线性关系[37]。 到目前为止,只有对部分Zr基非晶、Fe基非晶、Mg基合金进行了热处理研究,结果还各不相同。块体非晶合金热处理研究至今也没有形成完整的理论,热处理之后合金 的性能具体变化还不清楚。因此本文利用Ti 基非晶合金为基础,研究Ti 基非晶合金在热处理后组织和性能的变化规律,期望为非晶合金热处理的理论积累一些数据;同时也为开发大塑性Ti 基块体非晶合金做尝试,以其成为工程材料中重要的一员。 3.2 热处理前块体非晶合金组织及力学性能分析 3.2.1 块体非晶合金原试样特性的确定 1)XRD 分析 图3.1为直径2mm 的Ti 33Cu 47Zr 9Ni 6Sn 2Si 1Nb 2非晶合金未进行热处理XRD 图像。从图中可以看出,合金曲线均表现出明显的非晶合金的漫衍射峰,并未发现尖锐的晶化峰出现,可以确定试样在直径为2mm 时为完全的非晶态结构。 图3.1 Ti 33Cu 47Zr 9Ni 6Sn 2Si 1Nb 2非晶合金热处理前的XRD 曲线 2)组织形貌分析 图3.2为直径2mm 的Ti 33Cu 47Zr 9Ni 6Sn 2Si 1Nb 2块体非晶合金热处理前二次电子扫描形貌,分别对应图中3.2。从图中我们可以清楚的看出合金组织形貌为非晶合金特有的无特征形貌,未出现晶粒等晶体,这一结果与图3.1中的XRD 分析结果是完全对应的,因此可以说明Ti 33Cu 47Zr 9Ni 6Sn 2Si 1Nb 2合金热处理前为完全的非晶态合金。 20304050607080 Cast rod φ 2mm I n t e n s i t y (a .u .) 2θ 图3.2 Ti 33Cu 47Zr 9Ni 6Sn 2Si 1Nb 块体非晶合金热处理前的SEM 形貌 3)DSC 分析 图3.3为直径2mm 的Ti 33Cu 47Zr 9Ni 6Sn 2Si 1Nb 2非晶合金热处理前DSC 曲线,加热速率为20K/min 。利用切线法确定玻璃转变温度点(T g )和晶化温度点(T x )分别标定与曲线上。 图3.3 Ti33Cu47Zr9Ni6Sn2Si1Nb2非晶合金热处理前DSC 曲线 500600700800900100011001200 1300 E n d o t h e r m i c (a .u .)Temperature(T/K) T g T x T m T l 0.33K/s 测定结果为玻璃转变温度(T g)为462℃、晶化温度(T x)为472℃。从热稳定性曲线上可以看出,非晶表现出了明显的玻璃转变点,并具有两次较大放热现象出现,反应了合金在过冷液相区到平衡晶相的温度区间发生了连续转变,即该非晶合金的晶化过程分两步完成。非晶相失稳后,经过较大温区(100K)并两次放热才完全转变为晶体合金。 3.3 热处理后块体非晶合金力学性能及断口形貌分析 3.4 讨论 块体非晶合金在热处理前后塑性变形过程中均表现为锯齿状的应力-应变行为,如图3.4、图3.6所示。非晶合金的变形与晶态合金不同,没有位错滑移等变形行为,大多为弹性断裂。而非晶合金的微量塑性变形可以看作由多个微小的弹性变形区段组成。应力随着应变的增加而上升的区段基本发生的是弹性变形,因为该区段与压缩初期宏观的弹性变形部分近似平行;当应力达到极限值时,将以剪切带方式发生局域变形,变形减小的试样高度迅速被整个试样的弹性变形所补偿,导致应力的突然下降,从而形成锯齿状的波动曲线。 脉纹形貌是非晶合金断裂时典型的断面形貌,断口上的局部熔化现象在很多合金体系中都能观察到。应该指出的是,断口上的这些形貌特别是对于局部熔化现象不能断定是剪切带扩展过程中温度升高的必然结果。另外一种可能就是,断裂瞬间断裂能高密度释放造成的功热转化的结果,明显的室温塑性,并不总是对应着断口上的局部熔化现象,因此,单用断口形貌的变化解释力学性能的改善是不合适的。 根据Van den Beukel等人[39]对结构弛豫的自由体积理论描述,可以理解为铸态块体非晶合金含有大量的过剩自由体积,退火温度T p处于大块非晶合金的高温结构弛豫区时,随退火的开始,冻结的原子很快被热激活,原子重排速率较快,与之对应的自由体积会迅速进行迁移和消失。随着退火的持续进行,原子运动重排节奏变缓,材料中的自由体积数量逐渐减少,最后趋于稳定值。根据结构弛豫的自由体积模型观点,在结构弛豫过程中非晶合金的自由体积湮灭,缺陷浓度降低,材料致密度增加,但剪切带开动需要临界的自由体积增加。在这种情况下,剪切带的形核需要更大空间范围内原子的扩散以满足剪切带形核的自由体积需求,造成剪切带形核困难。而铸态样品中由于具有高自由体积浓度和低的临界剪切带浓度,趋向于多重剪切带的开动。因此在一定温度下,保温一定时间,自由体积达到临界浓度时,合金在变形过程中会同时开动多重剪切带,增加合金的塑性变形,当自由体积与临界剪切带不匹配时就无法获得高塑性。 参考文献 [1]Cohen M H,Turnbull D. Molecular transport in liquids and glasses. Chemistry Physics,1959,(31): 1164-1169. [2]Klement W,Willens R,Duwez P. Non-crystalline structure in solidified gold-silicon alloy. Nature, 1960,(187):869-890. [3]Chen H S,Turnbull D. Formation,stability and structure of palladium-silicon based alloy glasses[J]. Acta Materialia,1969,(17):1021-1031. [4]Chen H S. Thermodynamic considerations on the formation and stability of metallic glasses[J]. Acta Materialia,1974,(22):1505-1511. [5]Lee M C,Kendall J M,Johnson W L. Spheres of the metallic glasses Au55Pb22.5Sb22.5 and their surface characteristics[J]. Applied Physics Letters,1982,(40):382-384. [6]Inoue A,Zhang T,Masumoto T. La-Al-Ni amorphous alloys with a wide supercooled liquid region.[J]. Materials Transactions JIM,1989:(30):965-972. [7]Inoue A,Kato A,Zhang T,et al. Mg-Cu-Y amorphous alloys with high mechanical strengths produced by a metallic mold casting method.[J] .Materials Transactions JIM,1991:(32):609-616. [8]Peker A,Johnson W L. A highly processing metallic glass:Zr41.5Ti13.8Cu12.5Ni10Be22.5[J]. Applied Physics Letters,1993,(63):2342-2344. [9] Inoue A,Nishiyama N,Kimura H. Preparation and thermal stability of bulk amorphous Pd40Cu30Ni10P20 alloy cylinder of 72mm in diameter[J]. Materials Transactions JIM,1997,(38):179-183. [10] 闫相全,宋晓艳,张久兴. 块体非晶合金材料的研究进展[J].稀有金属材料与工程,2008,37(5) [11] Inoue A. Materials Transactions JIM[J].High pressure casting,2000,41(11):1372 [12] Jia Binbin,Xia Long,Wang Weiwei.Light Alloy Fabrication Technology[J]. Single melting method, 2006,34(10):20 [13]Xiaoyan Song,Jiuxing Zhang,Ming Yue et al. Advanced Materials[J]. Materials Transactions , 2006,(18):1210 [14] Slipenyuk A,Eckert J.Scripta Mater[J]. Physics Review Letters ,2004,(50):39 第一章 材料的力学性能试验 材料的力学性能试验是工程中广泛应用的一种试验,它为机械制造、土木工程、冶金及其它各种工业部门提供可靠的材料的力学性能参数,便于合理地使用材料,保证机器(结构)及其零件(构件)的安全工作。 材料的力学性能试验必须按照国家标准进行。 第一节 拉伸试验 一、实验目的 1.验证胡克定律,测定低碳钢的弹性常数:弹性模量E 。 2.测定低碳钢拉伸时的强度性能指标:屈服应力s σ和抗拉强度b σ。 3.测定低碳钢拉伸时的塑性性能指标:伸长率δ和断面收缩率ψ。 4.测定灰铸铁拉伸时的强度性能指标:抗拉强度b σ。 5.绘制低碳钢和灰铸铁的拉伸图,比较低碳钢与灰铸铁在拉伸时的力学性能和破坏形式。 二、实验设备和仪器 1.万能试验机。 2.引伸仪。 3.游标卡尺。 三、实验试样 按照国家标准GB6397—86《金属拉伸试验试样》,金属拉伸试样的形状随着产品的品种、规格以及试验目的的不同而分为圆形截面试样、矩形截面试样、异形截面试样和不经机加工的全截面形状试样四种。其中最常用的是圆形截面试样和矩形截面试样。 如图1-1所示,圆形截面试样和矩形截面试样均由平行、过渡和夹持三部分 组成。平行部分的试验段长度l 称为试样的标距,按试样的标距l 与横截面面积A 之间的关系,分为比例试样和定标距试样。圆形截面比例试样通常取d l 10=或 d l 5=,矩形截面比例试样通常取A l 3.11=或A l 65.5=,其中,前者称为长比例试样(简称长试样),后者称为短比例试样(简称短试样)。定标距试样的l 与A 之间无上述比例关系。过渡部分以圆弧与平行部分光滑地连接,以保证试样断裂时的断口在平行部分。夹持部分稍大,其形状和尺寸根据试样大小、材料特性、试验目的以及万能试验机的夹具结构进行设计。 对试样的形状、尺寸和加工的技术要求参见国家标准GB6397—86。 (a ) (b ) 图1-1 拉伸试样 (a )圆形截面试样;(b )矩形截面试样 四、实验原理与方法 1.测定低碳钢的弹性常数 实验时,先把试样安装在万能试验机上,再在试样的中部装上引伸仪,并将指针调整到0,用于测量试样中部0l 长度(引伸仪两刀刃间的距离)内的微小变形。开动万能试验机,预加一定的初载荷(可取kN 4),同时读取引伸仪的初读数。 为了验证载荷与变形之间成正比的关系,在弹性范围内(根据A ?P σ求出的最大弹性载荷不超过kN 14)采用等量逐级加载方法,每次递加同样大小的载荷增量F ?(可选kN 2=?F ),在引伸仪上读取相应的变形量。若每次的变形增量大致相等,则说明载荷与变形成正比关系,即验证了胡克定律。弹性模量E 可按下式算出 l A l F E ????= 第一章 钢筋混凝土的材料力学性能 一、填空题: 1、《混凝土规范》规定以 强度作为混凝土强度等级指标。 2、测定混凝土立方强度标准试块的尺寸是 。 3、混凝土的强度等级是按 划分的,共分为 级。 4、钢筋混凝土结构中所用的钢筋可分为两类:有明显屈服点的钢筋和无明显屈服点 的钢筋,通常称它们为 和 。 5、钢筋按其外形可分为 、 两大类。 6、HPB300、 HRB335、 HRB400、 RRB400表示符号分别为 。 7、对无明显屈服点的钢筋,通常取相当于于残余应变为 时的应力作为名 义屈服点,称为 。 8、对于有明显屈服点的钢筋,需要检验的指标有 、 、 、 等四项。 9、对于无明显屈服点的钢筋,需要检验的指标有 、 、 等三项。 10、钢筋和混凝土是两种不同的材料,它们之间能够很好地共同工作是因 为 、 、 。 11、钢筋与混凝土之间的粘结力是由 、 、 组成的。其 中 最大。 12、混凝土的极限压应变cu ε包括 和 两部分, 部分越 大,表明变形能力越 , 越好。 13、钢筋的冷加工包括 和 ,其中 既提高抗拉又提高抗 压强度。 14、有明显屈服点的钢筋采用 强度作为钢筋强度的标准值。 15、钢筋的屈强比是指 ,反映 。 二、判断题: 1、规范中,混凝土各种强度指标的基本代表值是轴心抗压强度标准值。( ) 2、混凝土强度等级是由一组立方体试块抗压后的平均强度确定的。( ) 3、采用边长为100mm 的非标准立方体试块做抗压试验时,其抗压强度换算系数为 0.95。( ) 4、采用边长为200mm 的非标准立方体试块做抗压试验时,其抗压强度换算系数为 1.05。( ) 5、对无明显屈服点的钢筋,设计时其强度标准值取值的依据是条件屈服强度。( ) 6、对任何类型钢筋,其抗压强度设计值y y f f '=。( ) 判断 1.由内力引起的内力集度称为应力。(×) 2.当应变为一个单位时,弹性模量即等于弹性应力,即弹性模量是产生100%弹性变形所需的应力。(√) 3.工程上弹性模量被称为材料的刚度,表征金属材料对弹性变形的抗力,其值越大,则在相同应力条件下产生的弹性变形就越大。(×) 4.弹性比功表示金属材料吸收弹性变形功的能力。(√) 5.滑移面和滑移方向的组合称为滑移系,滑移系越少金属的塑性越好。(×) 6.高的屈服强度有利于材料冷成型加工和改善焊接性能。(×) 7.固溶强化的效果是溶质原子与位错交互作用及溶质浓度的函数,因而它不受单相固溶合金(或多项合金中的基体相)中溶质量所限制。(×) 8.随着绕过质点的位错数量增加,留下的位错环增多,相当于质点的间距减小,流变应力就增大。(√) 9.层错能低的材料应变硬度程度小。(×) 10.磨损、腐蚀和断裂是机件的三种主要失效形式,其中以腐蚀的危害最大。(×) 11.韧性断裂用肉眼或放大镜观察时断口呈氧化色,颗粒状。(×) 12.脆性断裂的断裂面一般与正应力垂直,断口平齐而光亮,长呈放射状或结晶状。(√) 13.决定材料强度的最基本因素是原子间接合力,原子间结合力越高,则弹性模量、熔点就越小。(×) 14.脆性金属材料在拉伸时产生垂直于载荷轴线的正断,塑性变形量几乎为零。(√) 15.脆性金属材料在压缩时除产生一定的压缩变形外,常沿与轴线呈45°方向产生断裂具有切断特征。(√) 16.弯曲试验主要测定非脆性或低塑性材料的抗弯强度。(×) 17.可根据断口宏观特征,来判断承受扭矩而断裂的机件性能。(√) 18.缺口截面上的应力分布是均匀的。(×) 19.硬度是表征金属材料软硬程度的一种性能。(√) 20.于降低温度不同,提高应变速率将使金属材料的变脆倾向增大。(×) 21.低温脆性是材料屈服强度随温度降低急剧下降的结果。(×) 22.体心立方金属及其合金存在低温脆性。(√) 23.无论第二相分布于晶界上还是独立在基体中,当其尺寸增大时均使材料韧性下降,韧脆转变温度升高。(√) 24.细化晶粒的合金元素因提高强度和塑性使断裂韧度K IC下降。(×) 25.残余奥氏体是一种韧性第二相,分布于马氏体中,可以松弛裂纹尖端的应力峰,增大裂纹扩展的阻力,提高断裂韧度K IC。(√) 26.一般大多数结构钢的断裂韧度K IC都随温度降低而升高。(×) 27.金属材料的抗拉强度越大,其疲劳极限也越大。(√) 28.宏观疲劳裂纹是由微观裂纹的形成、长大及连接而成的。(√) 29.材料的疲劳强度仅与材料成分、组织结构及夹杂物有关,而不受载荷条件、工作环境及表面处理条件的影响。(×) 30.应力腐蚀断裂并是金属在应力作用下的机械破坏与在化学介质作用下的腐蚀性破坏的叠加所造成的。(×) 31.氢蚀断裂的宏观断口形貌呈氧化色,颗粒状。(√) 32.含碳量较低且硫、磷含量较高的钢,氢脆敏感性低。(×) 33.在磨损过程中,磨屑的形成也是一个变形和断裂的过程。(√) 材料力学性能实验指导书(材料成型及控制工程专业) 张学萍 沈阳理工大学 二零一二年三月 目录 实验一硬度实验......................................................................... (3) 前言 《材料力学性能》这门课的实验是该课的重要组成部分,是该理论课的基础,正确地掌握实验的理论和方法,对提高学生的动手能力、分析问题和解决问题的能力有重要意义。 编写本实验指导书,是根据《材料力学性能》教学大纲及教材的有关内容、又根据我院设备、仪器实际情况编写的,这样,与教材的内容相一致,便于安排实验教学。 本实验指导书适用于:材料成型及控制工程专业 编者 2012 年3月 实验一硬度实验 一.实验目的 1.掌握洛氏、布氏硬度的基本原理及测试方法。 2.根据材料的性质正确选择硬度计类型及压入条件。 3.熟悉各种硬度值之间的换算。 二、实验内容 用洛氏硬度计测定试样热处理前后的硬度;用布氏硬度计测定45刚退火后的硬度。 三、概述 硬度试验操作简便,对工件损伤小,可在零件上直接测试,故在生产实践中应用很普遍。 硬度所表征的不是一个确定的物理量,它是衡量材料软硬程度的一种性能指标。硬度值的意义随试验方法而不同。硬度试验基本上可分为压入法和刻划法。对于以压入法进行的硬度试验,其硬度值是表示材料抵抗另一物体压入其表面的能力,洛氏、布氏和维氏硬度都属于压入法硬度试验。 (一)洛氏硬度试验法。 1.洛氏硬度是以压痕的深度来表示 材料的硬度值。图1-1为洛氏硬度试验 原理图。 测试洛氏硬度时,用规定的压头, 先后施加两个负荷:预负荷F0和主负 荷F1。总负荷F= F0+F1。图1-1中, 0-0位置为未加负荷时的压头位置;l-l 位置为施加10kg预负荷后的位置,压 入深度为h1;2-2位置为加上主负荷后 的位置,此时压入深度为h2;3-3位置图1-1 洛氏硬度试验原理 为卸除主负荷后由于弹性变形的恢复而 使压头略微提高的位置,此时压头的实际压入深度为h3。由主负荷引起的残余压入深度h=h3-h1,用此来衡量金属硬度值的大小。若直接用h来表示硬度,则会出现硬的金 07 秋材料力学性能 一、填空:(每空1分,总分25分) 1.材料硬度的测定方法有、和。 2.在材料力学行为的研究中,经常采用三种典型的试样进行研究,即、和。 3.平均应力越高,疲劳寿命。 4.材料在扭转作用下,在圆杆横截面上无正应力而只有,中心处切 应力为,表面处。 5.脆性断裂的两种方式为和。 6.脆性材料切口根部裂纹形成准则遵循断裂准则;塑性材料切口根 部裂纹形成准则遵循断裂准则; 7.外力与裂纹面的取向关系不同,断裂模式不同,张开型中外加拉 应力与断裂面,而在滑开型中两者的取向关系则为。 8.蠕变断裂全过程大致由、和 三个阶段组成。 9.磨损目前比较常用的分类方法是按磨损的失效机制分为、和腐蚀磨损等。 10.深层剥落一般发生在表面强化材料的区域。 11.诱发材料脆断的三大因素分别是、和 。 二、选择:(每题1分,总分15分) ()1. 下列哪项不是陶瓷材料的优点 a)耐高温 b) 耐腐蚀 c) 耐磨损 d)塑性好 ()2. 对于脆性材料,其抗压强度一般比抗拉强度 a)高b)低c) 相等d) 不确定 ()3.用10mm直径淬火钢球,加压3000kg,保持30s,测得的布氏硬度值为150的正确表示应为 a) 150HBW10/3000/30 b) 150HRA3000/l0/ 30 c) 150HRC30/3000/10 d) 150HBSl0/3000/30 ()4.对同一种材料,δ5比δ10 a) 大 b) 小 c) 相同 d) 不确定 ()5.下列哪种材料用显微硬度方法测定其硬度。 a) 淬火钢件 b) 灰铸铁铸件 c) 退货态下的软钢 d) 陶瓷 ()6.下列哪种材料适合作为机床床身材料 a) 45钢 b) 40Cr钢 c) 35CrMo钢 d) 灰铸铁()7.下列哪种断裂模式的外加应力与裂纹面垂直,因而 它是最危险的一种断裂方式。 实验一、测定金属材料拉伸时的力学性能 一、实验目的 1、测定低碳钢的屈服极限s σ,强度极限b σ,延伸率δ和面积收缩率ψ。 2、测定铸铁的强度极限b σ。 3、观察拉伸过程中的各种现象,并绘制拉伸图(l F ?-曲线)。 二、仪器设备 1、液压式万能试验机。 2、游标卡尺。 三、实验原理简要 材料的力学性质s σ、b σ、δ和ψ是由拉伸破坏试验来确定的。试验时,利用试验机自动绘出低碳钢拉伸图和铸铁拉伸图。对于低碳材料,确定屈服载荷s F 时,必须缓慢而均匀地使试件产生变形,同时还需要注意观察。测力回转后所指示的最小载荷即为屈服载荷s F ,继续加载,测得最大载荷b F 。试件在达到最大载荷前,伸长变形在标距范围内均匀分布。从最大载荷开始,产生局部伸长和颈缩。颈缩出现后,截面面积迅速减小,继续拉伸所需的载荷也变小了,直至断裂。 铸铁试件在极小变形时,就达到最大载荷,而突然发生断裂。没有流动和颈缩现象,其强度极限远低于碳钢的强度极限。 四、实验过程和步骤 1、用游标卡尺在试件的标距范围内测量三个截面的直径,取其平均值,填入记录表内。取三处中最小值作为计算试件横截面积的直径。 2、 按要求装夹试样(先选其中一根),并保持上下对中。 3、 按要求选择“试验方案”→“新建实验”→“金属圆棒拉伸实验”进行试验,详细操 作要求见万能试验机使用说明。 4、 试样拉断后拆下试样,根据试验机使用说明把试样的l F ?-曲线显示在微机显示屏 上。从低碳钢的l F ?-曲线上读取s F 、b F 值,从铸铁的l F ?-曲线上读取b F 值。 5、 测量低碳钢(铸铁)拉断后的断口最小直径及横截面面积。 6、 根据低碳钢(铸铁)断口的位置选择直接测量或移位方法测量标距段长度1l 。 7、 比较低碳钢和铸铁的断口特征。 《工程材料力学性能》课后答案 机械工业出版社第2版 第一章单向静拉伸力学性能 1、解释下列名词。 1弹性比功: 金属材料吸收弹性变形功的能力, 一般用金属开始塑性变形前单位体积吸收的最大弹性变形功表示。 2.滞弹性: 金属材料在弹性范围内快速加载或卸载后, 随时间延长产生附加弹性应变的现象称为滞弹性, 也就是应变落后于应力的现象。 3.循环韧性: 金属材料在交变载荷下吸收不可逆变形功的能力称为循环韧性。 4.包申格效应: 金属材料经过预先加载产生少量塑性变形, 卸载后再同向加载, 规定残余伸长应力增加; 反向加载, 规定残余伸长应力降低的现象。 5.解理刻面: 这种大致以晶粒大小为单位的解理面称为解理刻面。6.塑性: 金属材料断裂前发生不可逆永久( 塑性) 变形的能力。 韧性: 指金属材料断裂前吸收塑性变形功和断裂功的能力。 7.解理台阶: 当解理裂纹与螺型位错相遇时, 便形成一个高度为b 的台阶。 8.河流花样: 解理台阶沿裂纹前端滑动而相互汇合,同号台阶相互汇合长大,当汇合台阶高度足够大时,便成为河流花样。是解理台阶的一种标志。 9.解理面: 是金属材料在一定条件下, 当外加正应力达到一定数值 后, 以极快速率沿一定晶体学平面产生的穿晶断裂, 因与大理石断 裂类似, 故称此种晶体学平面为解理面。 10.穿晶断裂: 穿晶断裂的裂纹穿过晶内, 能够是韧性断裂, 也能够 是脆性断裂。 沿晶断裂: 裂纹沿晶界扩展, 多数是脆性断裂。 11.韧脆转变: 具有一定韧性的金属材料当低于某一温度点时, 冲击 吸收功明显下降, 断裂方式由原来的韧性断裂变为脆性断裂, 这种 现象称为韧脆转变 12.弹性不完整性: 理想的弹性体是不存在的, 多数工程材料弹性 变形时, 可能出现加载线与卸载线不重合、应变滞后于应力变化等 现象,称之为弹性不完整性。弹性不完整性现象包括包申格效应、 弹性后效、弹性滞后和循环韧性等 2、说明下列力学性能指标的意义。 答: E弹性模量G切变模量 σ规定残余伸长应力2.0σ屈服强 r 度 δ金属材料拉伸时最大应力下的总伸长率n 应变硬化指数gt 【P15】 3、金属的弹性模量主要取决于什么因素? 为什么说它是一个对组 织不敏感的力学性能指标? 答: 主要决定于原子本性和晶格类型。合金化、热处理、冷塑 性变形等能够改变金属材料的组织形态和晶粒大小, 可是不改 变金属原子的本性和晶格类型。组织虽然改变了, 原子的本性和 篇一:材料力学实验报告答案 材料力学实验报告 评分标准拉伸实验报告 一、实验目的(1分) 1. 测定低碳钢的强度指标(σs、σb)和塑性指标(δ、ψ)。 2. 测定铸铁的强度极限σb。 3. 观察拉伸实验过程中的各种现象,绘制拉伸曲线(p-δl曲线)。 4. 比较低碳钢与铸铁的力学特性。 二、实验设备(1分) 机器型号名称电子万能试验机 测量尺寸的量具名称游标卡尺精度 0.02 mm 三、实验数据(2分) 四、实验结果处理(4分) ?s??b? psa0pba0 =300mpa 左右=420mpa 左右 =20~30%左右=60~75%左右 ?? l1?l0 ?100% l0a0?a1 ?100% a0 ?= 五、回答下列问题(2分,每题0.5分) 1、画出(两种材料)试件破坏后的简图。略 2、画出拉伸曲线图。 3、试比较低碳钢和铸铁拉伸时的力学性质。 低碳钢在拉伸时有明显的弹性阶段、屈服阶段、强化阶段和局部变形阶段,而铸铁没有明显的这四个阶段。 4、材料和直径相同而长短不同的试件,其延伸率是否相同?为什么?相同 延伸率是衡量材料塑性的指标,与构件的尺寸无关。压缩实验报告 一、实验目的(1分) 1. 测定压缩时铸铁的强度极限σb。 2. 观察铸铁在压缩时的变形和破坏现象,并分析原因。 二、实验设备(1分) 机器型号名称电子万能试验机(0.5分) 测量尺寸的量具名称游标卡尺精度 0.02 mm (0.5分) 三、实验数据(1分)四、实验结果处理(2分) ?b? pb =740mpaa0 左右 五、回答下列思考题(3分) 1.画出(两种材料)实验前后的试件形状。略 2. 绘出两种材料的压缩曲线。略 3. 为什么在压缩实验时要加球形承垫? 《工程材料力学性能》(第二版)课后答案 第一章材料单向静拉伸载荷下的力学性能 一、解释下列名词 滞弹性:在外加载荷作用下,应变落后于应力现象。 静力韧度:材料在静拉伸时单位体积材科从变形到断裂所消耗的功。 弹性极限:试样加载后再卸裁,以不出现残留的永久变形为标准,材料 能够完全弹性恢复的最高应力。 比例极限:应力—应变曲线上符合线性关系的最高应力。 包申格效应:指原先经过少量塑性变形,卸载后同向加载,弹性极限 (σP)或屈服强度(σS)增加;反向加载时弹性极限(σP)或屈服 强度(σS)降低的现象。 解理断裂:沿一定的晶体学平面产生的快速穿晶断裂。晶体学平面--解理面,一般是低指数,表面能低的晶面。 解理面:在解理断裂中具有低指数,表面能低的晶体学平面。 韧脆转变:材料力学性能从韧性状态转变到脆性状态的现象(冲击吸收功明显下降,断裂机理由微孔聚集型转变穿晶断裂,断口特征由纤维状转变为结晶状)。 静力韧度:材料在静拉伸时单位体积材料从变形到断裂所消耗的功叫做静力韧度。是一个强度与塑性的综合指标,是表示静载下材料强度与塑性的最佳配合。 二、金属的弹性模量主要取决于什么?为什么说它是一个对结构不敏感的力学性能? 答案:金属的弹性模量主要取决于金属键的本性和原子间的结合力,而材料的成分和组织对它的影响不大,所以说它是一个对组织不敏感的性能指标,这是弹性模量在性能上的主要特点。改变材料的成分和组织会对材料的强度(如屈服强度、抗拉强度)有显著影响,但对材料的刚度影响不大。 三、什么是包申格效应,如何解释,它有什么实际意义? 答案:包申格效应就是指原先经过变形,然后在反向加载时弹性极限或屈服强度降低的现象。特别是弹性极限在反向加载时几乎下降到零,这说明在反向加载时塑性变形立即开始了。 一、什么是蠕变,蠕变变形的机理是什么? 蠕变就是金属在长时间恒温、恒载荷作用下,缓慢地产生塑性变形的现象。金属的蠕变变形主要是通过位错滑移,原子扩散等机理进行的。其中位错滑移蠕变是由于在高温下位错借助外界提供的热激活能和空位扩散来克服某些短程障碍,从而使变形不断产生,其中高温下的热激活能过程主要是刃型位错的攀移;原子扩散蠕变是在较高温度下晶体内空位将从受拉应力晶界向受压应力晶界迁移,原子则朝相反方向流动,致使晶体逐渐产生伸长的蠕变。二、什么是脆性断裂?什么是应力腐蚀现象,防止应力腐蚀的措施有哪些? 脆性断裂是突然发生的断裂,断裂前基本不发生什么塑性变形,没有明显的征兆,危害性很大。 金属在拉应力和特定的化学介质共同作用下,经过一段时间后所产生的低应力脆断现象,称为应力腐蚀现象 防止应力腐蚀的措施1.合理选择金属材料针对机件所受的应力和接触的化学介质,选用耐应力腐蚀的金属材料并尽可能选择较高的合金。2.减少或消除机件中的残余拉应力应尽量减少机件上的应力集中效应,加热和冷却都要均匀。必要时可采用退火工艺以消除应力。如果能采用喷丸或者其他表面处理方法,使机件表层中产生一定的残余应力,则更为有效。3.改善化学介质一方面设法减少和消除促进应力腐蚀开裂的有害化学离子,另一方面,也可以在化学介质中添加缓蚀剂。4.采用电化学保护采用外加电位的方法,使金属在化学介质中的电位远离应力腐蚀敏感电位区域,一般采用阴极保护法,但高强度钢或其他氢脆敏感的材料,不能采用阴极保护法。 三、什么是应力软性系数?计算单向拉伸、单向压缩和扭转变形的应力状态软性系数。 最大切应力与最大正应力的比值来表示它们的相对大小,称为应力软性系数,记为 用来描述金属材料在某应力状态下的"软"和"硬",越大表示应力状态越"软",金属越容易产生塑性变形和韧性断裂。反之,越小表示应力状态越"硬",金属越不易产生塑性变形和韧性断裂 对于金属材料 单向拉伸时=,=0,=0 :=0.5 单向压缩时=0,=0,=-:=2 扭转变形时=,=0,=-:=0.8 四、简述粘着磨损的机理,什么情况产生粘着磨损。 在滑动摩擦条件下,由于摩擦副实际表面上总存在局部凸起,当摩擦副双方接触时,即使施加较小的载荷,在真是接触面上的局部应力就足以引起塑性变形,若接触表面洁净未被腐蚀,则局部塑性变形会使两个基础面的原子彼此十分接近而产生强烈粘着,实际上就是原子间的键合作用。随后在继续滑动时,粘着点被剪断并转移到一方金属表面,然后脱落下便形成磨屑。一个粘着点剪断了,又在新的地方产生粘,随后也被剪断、转移,如此粘着→剪断→转移→再粘着循环不已,这就构成粘着磨损过程。 粘着磨损又称咬合磨损,是在滑动摩擦条件下,当摩擦副相对滑动速度较小时发生的。它是因缺乏润滑油,摩擦副表面无氧化膜,且单位法向载荷很大,以至接触应力超过实际接触点处屈服强度的条件下而产生的一种磨损。 五、金属疲劳断裂有哪些特征?什么是疲劳裂纹扩展门槛值?简述疲劳裂纹扩展至断裂的过程。影响疲劳强度的主要因素有哪些? 金属机件或构件在变动应力和应变长期作用下,由于积累损伤而引起的断裂现象称为疲劳。特点:(1)疲劳是低应力循环延时断裂,即具有寿命的断裂,当应力低于某一临界时,寿命 安徽工业大学材料力学性能复习总结题 第一章金属在单向静拉伸载荷下的力学性能— 1、名词解释 强度、塑性、韧性、包申格效应 2、说明下列力学性能指标的意义 E、σ0.2、σs、n、δ、ψ 3、今有45、40Cr、35CrMo钢和灰铸铁几种材料,你选择哪些材料作机床床身?为什么? 4、试述并画出退火低碳钢、中碳钢和高碳钢的屈服现象在拉伸-伸长曲线图上的区别。 *5、试述韧性断裂和脆性断裂的区别?(P21-22) 6、剪切断裂与解理断裂都是穿晶断裂,为什么断裂性质完全不同? 7、何谓拉伸断口三要素? 8、试述弥散强化与沉淀强化的异同? 9、格雷菲斯判据是断裂的充分条件、必要条件还是充分必要条件?*10、试述构件的刚度与材料的刚度的异同。(P4) 第二章金属在其它静载荷下的力学性能— 1、名词解释 缺口效应、缺口敏感度、应力状态软性系数 2、说明下列力学性能指标及表达的意义 σbc、NSR、600HBW1/30/20 3、缺口试样拉伸时应力分布有何特点? 4、根据扭转试样的宏观断口特征,可以了解金属材料的最终断裂方式,比如切断、正断和木纹状断口。试画出这三种断口特征的宏观特征。 第三章金属在冲击载荷下的力学性能— 1、名词解释 低温脆性、韧脆转变温度 2、说明下列力学性能指标的意义 A K、FATT50 3、现需检验以下材料的冲击韧性,问哪种材料要开缺口?哪些材料不要开缺口?为什么? W18Cr4V、Cr12MoV、3Cr2W8V、40CrNiMo、30CrMnSi、20CrMnTi、铸铁 第四章金属的断裂韧度— 1、名词解释 应力场强度因子K I、小范围屈服 2、说明断裂韧度指标K IC和K C的意义及其相互关系。 3、试述K I与K IC的相同点和不同点。 4、试述K IC和A KV的异同及其相互关系。 *5、合金钢调质后的性能σ0.2=1400MPa, K IC=110MPa?m1/2,设此种材料厚板中存在垂直于外界应力的裂纹,所受应力σ=900MPa,问此时的临界裂纹长度是多少? *6、有一大型薄板构件,承受工作应力为400MN/m2,板的中心有一长为3mm的裂纹,裂纹面垂直于工作应力,钢材的σs=500 MN/m2,试确定:裂纹尖端的应力场强度因子K I及裂纹尖端的塑性区尺寸R 。 静拉伸试验 一、实验目的 1、测45#钢的屈服强度s σ、抗拉强度m R 、断后伸长率δ和断面收缩率ψ。 2、测定铝合金的屈服强度s σ、抗拉强度m R 、断后伸长率δ和断面收缩率ψ。 3、观察并分析两种材料在拉伸过程中的各种现象。 二、使用设备 微机控制电子万能试验机、0.02mm 游标卡尺、试验分化器 三、试样 本试样采用经过机加工直径为10mm 左右的圆形截面比例试样,试样成分分别为铝合金和45#,各有数支。 四、实验原理 按照我国目前执行的国家 GB/T 228—2002标准—《金属材料 室温拉伸试验方法》的规定,在室温1035℃℃的范围内进行试验。将试样安装在试验机的夹头当中,然后开动试验机,使试样受到缓慢增加的拉力(一般应变速率应≤0.1m/s ),直到拉断为止,并且利用试验机的自动绘图装置绘出材料的拉伸图。 试验机自动绘图装置绘出的拉伸变形L ?主要是整个试样,而不仅仅是标距部分的伸长,还包括机器的弹性变形和试样在夹头中的滑动等因素,由于试样开始受力时,头部在头内的滑动较大,故绘出的拉伸图最初一段是曲线。 塑性材料与脆性材料的区别: (1)塑性材料: 脆性材料是指断后伸长率5%δ≥的材料,其从开始承受拉力直至试样被拉断,变形都比较大。塑性材料在发生断裂时,会发生明显的塑性变形,也会出现屈服和颈缩等现象; (2)脆性材料: 脆性材料是指断后伸长率5%δ<的材料,其从开始承受拉力直至试样被拉断,变形都很小。并且,大多数脆性材料在拉伸时的应力—应变曲线上都没有明显的直线段,几乎没有塑性变形,在断裂前不会出现明显的征兆,不会出现屈服和颈缩等现象,只有断裂时的应力值—强度极限。 脆性材料在承受拉力、变形记小时,就可以达到m F 而突然发生断裂,其抗拉强度也远远 小于45钢的抗拉强度。同样,由公式0m m R F S =即可得到其抗拉强度,而根据公式,10 l l l δ-=。 五、实验步骤 1、试样准备 用笔在试样间距0L (10cm )处标记一下。用游标尺测量出中间横截面的平均直径,并且测出试样在拉伸前的一个总长度L 。 2、试验机准备: 金属材料力学性能基本知识 及钢材的脆化 金属材料是现代工业、农业、国防以及科学技术各个领域应用最广泛的工程材料,这不仅是由于其来源丰富,生产工艺简单、成熟,而且还因为它具有优良的性能。 通常所指的金属材料性能包括以下两个方面: 1.使用性能即为了保证机械零件、设备、结构件等能正常工作,材料所应具备的性能,主要有力学性能(强度、硬度、刚度、塑性、韧性等),物理性能(密度、熔点、导热性、热膨胀性等),化学性能(耐蚀性、热稳定性等)。使用性能决定了材料的应用范围,使用安全可靠性和使用寿命。 2 工艺性能即材料在被制成机械零件、设备、结构件的过程中适应各种冷、热加工的性能,例如锻造,焊接,热处理,压力加工,切削加工等方面的性能。工艺性能对制造成本、生成效率、产品质量有重要影响。 1.1材料力学基本知识 金属材料在加工和使用过程中都要承受不同形式外力的作用,当外力达到或超过某一限度时,材料就会发生变形以至断裂。材料在外力作用下所表现的一些性能称为材料的力学性能。锅炉压力容器材料的力学性能指标主要有强度、硬度、塑性、韧性等这些性能指标可以通过力学性能试验测定。 1.1.1强度 金属的强度是指金属抵抗永久变形和断裂的能力。材料强度指标可以通过拉伸试验测 出。把一定尺寸和形状的金属试样(图1~2)装夹在试验机上,然后对试样逐渐施加拉伸载荷,直至把试样拉断为止。根据试样在拉伸过程中承受的载荷和产生的变形量之间的关系,可绘出该金属的拉伸曲线(图1—3)。在拉伸曲线上可以得到该材料强度性能的一些数据。图1—3所示的曲线,其纵坐标是载荷P(也可换算为应力d),横坐标是伸长量AL(也可换算为应变e)。所以曲线称为P—AL曲线或一一s曲线。图中曲线A是低碳钢的拉伸曲线,分析曲线A,可以将拉伸过程分为四个阶段: 一、填空: 1.提供材料弹性比功的途径有二,提高材料的,或降低。 2.退火态和高温回火态的金属都有包申格效应,因此包申格效应是 具有的普遍现象。 3.材料的断裂过程大都包括裂纹的形成与扩展两个阶段,根据断裂过程材料的宏观塑性变形过程,可以将断裂分为与;按照晶体材料断裂时裂纹扩展的途径,分为和;按照微观断裂机理分为和;按作用力的性质可分为和。 4.滞弹性是指材料在范围内快速加载或卸载后,随时间延长产生附加的现象,滞弹性应变量与材料、有关。 5.包申格效应:金属材料经过预先加载产生少量的塑性变形,而后再同向加载,规定残余伸长应力;反向加载,规定残余伸长应力的现象。消除包申格效应的方法有和。 6.单向静拉伸时实验方法的特征是、、必须确定的。 7.过载损伤界越,过载损伤区越,说明材料的抗过载能力越强。 8. 依据磨粒受的应力大小,磨粒磨损可分为、 、三类。 9.解理断口的基本微观特征为、和。10.韧性断裂的断口一般呈杯锥状,由、和三个区域组成。 11.韧度是衡量材料韧性大小的力学性能指标,其中又分为、 和。 12.在α值的试验方法中,正应力分量较大,切应力分量较小,应力状态较硬。一般用于塑性变形抗力与切断抗力较低的所谓塑性材料试验;在α值的试验方法中,应力状态较软,材料易产生塑性变形,适用于在单向拉伸时容易发生脆断而不能充分反映其塑性性能的所谓脆性材料; 13.材料的硬度试验应力状态软性系数,在这样的应力状态下,几乎所有金属材料都能产生。 14. 硬度是衡量材料软硬程度的一种力学性能,大体上可以分为 、和三大类;在压入法中,根据测量方式不同又分为 、和。 15. 国家标准规定冲击弯曲试验用标准试样分别为试样 和试样,所测得的冲击吸收功分别用 、标记。 16. 根据外加压力的类型及其与裂纹扩展面的取向关系,裂纹扩展的基本方式有、和。 17. 机件的失效形式主要有、、三种。 18.低碳钢的力伸长曲线包括、、、 第一章单向静拉伸力学性能 1、解释下列名词。 1弹性比功:金属材料吸收弹性变形功的能力,一般用金属开始塑性变形前单位体积吸收的最大弹性变形功表示。 2.滞弹性:金属材料在弹性范围内快速加载或卸载后,随时间延长产生附加弹性应变的现象称为滞弹性,也就是应变落后于应力的现象。3.循环韧性:金属材料在交变载荷下吸收不可逆变形功的能力称为循环韧性。 4.包申格效应:金属材料经过预先加载产生少量塑性变形,卸载后再同向加载,规定残余伸长应力增加;反向加载,规定残余伸长应力降低的现象。 5.解理刻面:这种大致以晶粒大小为单位的解理面称为解理刻面。6.塑性:金属材料断裂前发生不可逆永久(塑性)变形的能力。 韧性:指金属材料断裂前吸收塑性变形功和断裂功的能力。 7.解理台阶:当解理裂纹与螺型位错相遇时,便形成一个高度为b的台阶。 8.河流花样:解理台阶沿裂纹前端滑动而相互汇合,同号台阶相互汇合长大,当汇合台阶高度足够大时,便成为河流花样。是解理台阶的一种标志。 9.解理面:是金属材料在一定条件下,当外加正应力达到一定数值后,以极快速率沿一定晶体学平面产生的穿晶断裂,因与大理石断裂类似,故称此种晶体学平面为解理面。 10.穿晶断裂:穿晶断裂的裂纹穿过晶内,可以是韧性断裂,也可以是脆性断裂。 沿晶断裂:裂纹沿晶界扩展,多数是脆性断裂。 11.韧脆转变:具有一定韧性的金属材料当低于某一温度点时,冲击吸收功明显下降,断裂方式由原来的韧性断裂变为脆性断裂,这种现象称为韧脆转变 12.弹性不完整性:理想的弹性体是不存在的,多数工程材料弹性变形时,可能出现加载线与卸载线不重合、应变滞后于应力变化等现象,称之为弹性不完整性。弹性不完整性现象包括包申格效应、弹性后效、弹性滞后和循环韧性等 2、 说明下列力学性能指标的意义。 答:E 弹性模量 G 切变模量 r σ规定残余伸长应力 2.0σ屈服强度 gt δ金属材料拉伸时最大应力下的总伸长率 n 应变硬化指数 【P15】 3、 金属的弹性模量主要取决于什么因素?为什么说它是一个对组织不敏感的力学性能指标? 答:主要决定于原子本性和晶格类型。合金化、热处理、冷塑性变形等能够改变金属材料的组织形态和晶粒大小,但是不改变金属原子的本性和晶格类型。组织虽然改变了,原子的本性和晶格类型未发生改变,故弹性模量对组织不敏感。【P4】 4、 试述退火低碳钢、中碳钢和高碳钢的屈服现象在拉伸力-伸长曲线图上的区别?为什么? 5、 决定金属屈服强度的因素有哪些?【P12】 答:内在因素:金属本性及晶格类型、晶粒大小和亚结构、溶质元素、第二相。 外在因素:温度、应变速率和应力状态。 6、 试述韧性断裂与脆性断裂的区别。为什么脆性断裂最危险?【P21】 答:韧性断裂是金属材料断裂前产生明显的宏观塑性变形的断裂,这种断裂有一个缓慢的撕裂过程,在裂纹扩展过程中不断地消耗能量;而脆性断裂是突然发生的断裂,断裂前基本上不发生塑性变形,没有明显征兆,因而危害性很大。 7、 剪切断裂与解理断裂都是穿晶断裂,为什么断裂性质完全不同?【P23】 答:剪切断裂是在切应力作用下沿滑移面分离而造成的滑移面分离,一般是韧性断裂,而解理断裂是在正应力作用以极快的速率沿一定晶体学平面产生的穿晶断裂,解理断裂通常是脆性断裂。 8、 何谓拉伸断口三要素?影响宏观拉伸断口性态的因素有哪些? 答:宏观断口呈杯锥形,由纤维区、放射区和剪切唇三个区域组成,即所谓的断口特征三要素。上述断口三区域的形态、大小和相对位置,因试样形状、尺寸和金属材料的性能以及试验温度、加载速率和受力状态不同而变化。 9、 论述格雷菲斯裂纹理论分析问题的思路,推导格雷菲斯方程,并指出该理论的局限性。【P32】 答: 2 12?? ? ??=a E s c πγσ,只适用于脆性固体,也就是只适用于那些裂纹尖端塑性变形可以忽略的情况。 第二章 金属在其他静载荷下的力学性能 一、解释下列名词: (1)应力状态软性系数—— 材料或工件所承受的最大切应力τmax 和最大正应力σmax 比值,即: () 32131max max 5.02σσσσσστα+--== 【新书P39 旧书P46】 (2)缺口效应—— 绝大多数机件的横截面都不是均匀而无变化的光滑体,往往存在截面的急剧变化,如键槽、油孔、轴肩、螺纹、退刀槽及焊缝等,这种截面变化的部分可视为“缺口”,由于缺口的存在,在载荷作用下缺口截面上的应力状态将发生变化,产生所谓的缺口效应。【P44 P53】 (3)缺口敏感度——缺口试样的抗拉强度σbn 的与等截面尺寸光滑试样的抗拉强度σb 的比值,称为缺口敏感度,即: 【P47 P55 】 (4)布氏硬度——用钢球或硬质合金球作为压头,采用单位面积所承受的试验力计算而得的硬度。【P49 P58】 (5)洛氏硬度——采用金刚石圆锥体或小淬火钢球作压头,以测量压痕深度所表示的硬度【P51 P60】。 第一章 包申格效应:指原先经过少量塑性变形,卸载后同向加载,弹性极限(σP)或屈服强度(σS)增加;反向加载时弹性极限(σP)或屈服强度(σS)降低的现象。 解理断裂:沿一定的晶体学平面产生的快速穿晶断裂。晶体学平面--解理面,一般是低指数,表面能低的晶面。 解理面:在解理断裂中具有低指数,表面能低的晶体学平面。 韧脆转变:材料力学性能从韧性状态转变到脆性状态的现象(冲击吸收功明显下降,断裂机理由微孔聚集型转变微穿晶断裂,断口特征由纤维状转变为结晶状)。 静力韧度:材料在静拉伸时单位体积材料从变形到断裂所消耗的功叫做静力韧度。是一个强度与塑性的综合指标,是表示静载下材料强度与塑性的最佳配合。 可以从河流花样的反“河流”方向去寻找裂纹源。 解理断裂是典型的脆性断裂的代表,微孔聚集断裂是典型的塑性断裂。 5.影响屈服强度的因素 与以下三个方面相联系的因素都会影响到屈服强度 位错增值和运动 晶粒、晶界、第二相等 外界影响位错运动的因素 主要从内因和外因两个方面考虑 (一)影响屈服强度的内因素 1.金属本性和晶格类型(结合键、晶体结构) 单晶的屈服强度从理论上说是使位错开始运动的临界切应力,其值与位错运动所受到的阻力(晶格阻力--派拉力、位错运动交互作用产生的阻力)决定。 派拉力: 位错交互作用力 (a是与晶体本性、位错结构分布相关的比例系数,L是位错间距。)2.晶粒大小和亚结构 晶粒小→晶界多(阻碍位错运动)→位错塞积→提供应力→位错开动→产生宏观塑性变形。 晶粒减小将增加位错运动阻碍的数目,减小晶粒内位错塞积群的长度,使屈服强度降低(细晶强化)。 屈服强度与晶粒大小的关系: 霍尔-派奇(Hall-Petch) σs= σi+kyd-1/2 3.溶质元素 加入溶质原子→(间隙或置换型)固溶体→(溶质原子与溶剂原子半径不一样)产生晶格畸变→产生畸变应力场→与位错应力场交互运动→使位错受阻→提高屈服强度(固溶强化)。 4.第二相(弥散强化,沉淀强化) 不可变形第二相 提高位错线张力→绕过第二相→留下位错环→两质点间距变小→流变应力增大。 不可变形第二相 位错切过(产生界面能),使之与机体一起产生变形,提高了屈服强度。 弥散强化: 判断 1. 由内力引起的内力集度称为应力。 ( X ) 2. 当应变为一个单位时,弹性模量即等于弹性应力,即弹性模量是产生 的应 力。( V ) 3. 工程上弹性模量被称为材料的刚度,表征金属材料对弹性变形的抗力,其值越大,则在相 同应力 条件下产生的弹性变形就越大。 ( X ) 4. 弹性比功表示金属材料吸收弹性变形功的能力。 ( V ) 5. 滑移面和滑移方向的组合称为滑移系,滑移系越少金属的塑性越好。 6. 高的屈服强度有利于材料冷成型加工和改善焊接性能。 ( X ) 7. 固溶强化的效果是溶质原子与位错交互作用及溶质浓度的函数, 因而它不受单相固溶合金 (或多项合金中的基体相)中溶质量所限制。 ( X ) 8. 随着绕过质点的位错数量增加,留下的位错环增多,相当于质点的间距减小,流变应力就 增大。 ( V ) 9. 层错能低的材料应变硬度程度小。 ( X ) 10. 磨损、腐蚀和断裂是机件的三种主要失效形式,其中以腐蚀的危害最大。 11. 韧性断裂用肉眼或放大镜观察时断口呈氧化色,颗粒状。 ( X ) 12. 脆性断裂的断裂面一般与正应力垂直,断口平齐而光亮,长呈放射状或结晶状。 ( V ) 13. 决定材料强度的最基本因素是原子间接合力,原子间结合力越高,则弹性模量、熔点就 越小。 ( X ) 14. 脆性金属材料在拉伸时产生垂直于载荷轴线的正断,塑性变形量几乎为零。 ( V ) 15. 脆性金属材料在压缩时除产生一定的压缩变形外,常沿与轴线呈 45°方向产生断裂具有 切断特征。( V ) 16. 弯曲试验主要测定非脆性或低塑性材料的抗弯强度。 ( X 17. 可根据断口宏观特征,来判断承受扭矩而断裂的机件性能。 18. 缺口截面上的应力分布是均匀的。 ( X ) 19. 硬度是表征金属材料软硬程度的一种性能。 ( V ) 20. 于降低温度不同,提高应变速率将使金属材料的变脆倾向增大。 21. 低温脆性是材料屈服强度随温度降低急剧下降的结果。 ( X ) 22. 体心立方金属及其合金存在低温脆性。 ( V ) 23. 无论第二相分布于晶界上还是独立在基体中,当其尺寸增大时均使材料韧性下降,韧脆 转变温 度升高。 ( V ) 24. 细化晶粒的合金元素因提高强度和塑性使断裂韧度 K IC 下降。( X ) 25. 残余奥氏体是一种韧性第二相,分布于马氏体中,可以松弛裂纹尖端的应力峰,增大裂 纹扩展的阻力,提高断裂韧度 K IC 。( V ) 26. —般大多数结构钢的断裂韧度 K ic 都随温度降低而升高。(X ) 27. 金属材料的抗拉强度越大,其疲劳极限也越大。 ( V ) 28. 宏观疲劳裂纹是由微观裂纹的形成、长大及连接而成的。 ( V ) 29. 材料的疲劳强度仅与材料成分、组织结构及夹杂物有关,而不受载荷条件、工作环境及 表面处 理条件的影响。 ( X ) 30. 应力腐蚀断裂并是金属在应力作用下的机械破坏与在化学介质作用下的腐蚀性破坏的叠 加所造 成的。 ( X ) 31. 氢蚀断裂的宏观断口形貌呈氧化色,颗粒状。 ( V ) 32. 含碳量较低且硫、磷含量较高的钢,氢脆敏感性低。 ( X ) 100%弹性变形所需 X) 《材料力学性能》实验教学指导书 实验总学时:4 实验项目:1.准静态拉伸 2. 不同材料的冲击韧性 材料科学与工程学院实验中心 工程材料及机制基础实验室 实验一 准静态拉伸 一、实验目的 1.观察低碳钢(塑性材料)与铸铁(脆性材料)在准静态拉伸过程中的各种现象(包括屈服、强化和颈缩等现象),并绘制拉伸图。 2.测定低碳钢的屈服极限σs ,强度极限σb ,断后延伸率δ和断面收缩率ψ。 3.测定铸铁的强度极限σb 。 4.比较低碳钢和铸铁的力学性能的特点及断口形貌。 二、概述 静载拉伸试验是最基本的、应用最广的材料力学性能试验。一方面,由静载拉伸试验测定的力学性能指标,可以作为工程设计、评定材料和优选工艺的依据,具有重要的工程实际意义。另一方面,静载拉伸试验可以揭示材料的基本力学行为规律,也是研究材料力学性能的基本试验方法。 静载拉伸试验,通常是在室温和轴向加载条件下进行的,其特点是试验机加载轴线与试样轴线重合,载荷缓慢施加。 在材料试验机上进行静拉伸试验,试样在负荷平稳增加下发生变形直至断裂,可得出一系列的强度指标(屈服强度s σ和抗拉强度b σ)和塑性指标(伸长率δ和断面收缩率ψ)。通过试验机自动绘出试样在拉伸过程中的伸长和负荷之间的关系曲线,即P —Δl 曲线,习惯上称此曲线为试样的拉伸图。图1即为低碳钢的拉伸图。 试样拉伸过程中,开始试样伸长随载荷成比例地增加,保持直线关系。当载荷增加到一定值时,拉伸图上出现平台或锯齿状。这种在载荷不增加或减小的情况下,试样还继续伸长的现象叫屈服,屈服阶段的最小载荷是屈服点载荷s P ,s P 除以试样原始横截面面积Ao 即得到屈服极限s σ: 0 s s A P =σ 试样屈服后,要使其继续发生变形,则要克服不断增长的抗力,这是由于金属材料在塑性变形过程中不断发生的强化。这种随着塑性变形增大,变形抗力不断增加的现象叫做形变强化或加工硬化。由于形变强化的作用,这一阶段的变形主要是均匀塑性变形和弹性变形。当载荷达到最大值b P 后,试样的某一部位截面积开始急剧缩小,出现“缩颈”现象,此后的变形主要集中在缩颈附近,直至达到P b 试样拉断。P b 除以试样原始横截面面积A 0即得到材料的力学性能试验
钢筋混凝土材料的力学性能 复习题
材料力学性能试题(卷)集
材料力学性能实验指导书(材料成型及控制工程专业)
材料力学性能考试题及答案
材料力学实验参考
工程材料力学性能习题答案模板
材料力学实验报告答案
工程材料力学性能课后习题答案
材料力学性能复习题
安徽工业大学材料力学性能复习总结题
材料力学性能静拉伸试验报告
第二章 金属材料力学性能基本知识及钢材的脆化
2015年材料力学性能思考题大连理工大学
材料力学性能-第2版课后习题答案
材料力学性能复习重点汇总
完整word版材料力学性能试题集
材料力学性能实验(2个)..