熔渗烧结制备Ti_3SiC_2反应机理的研究
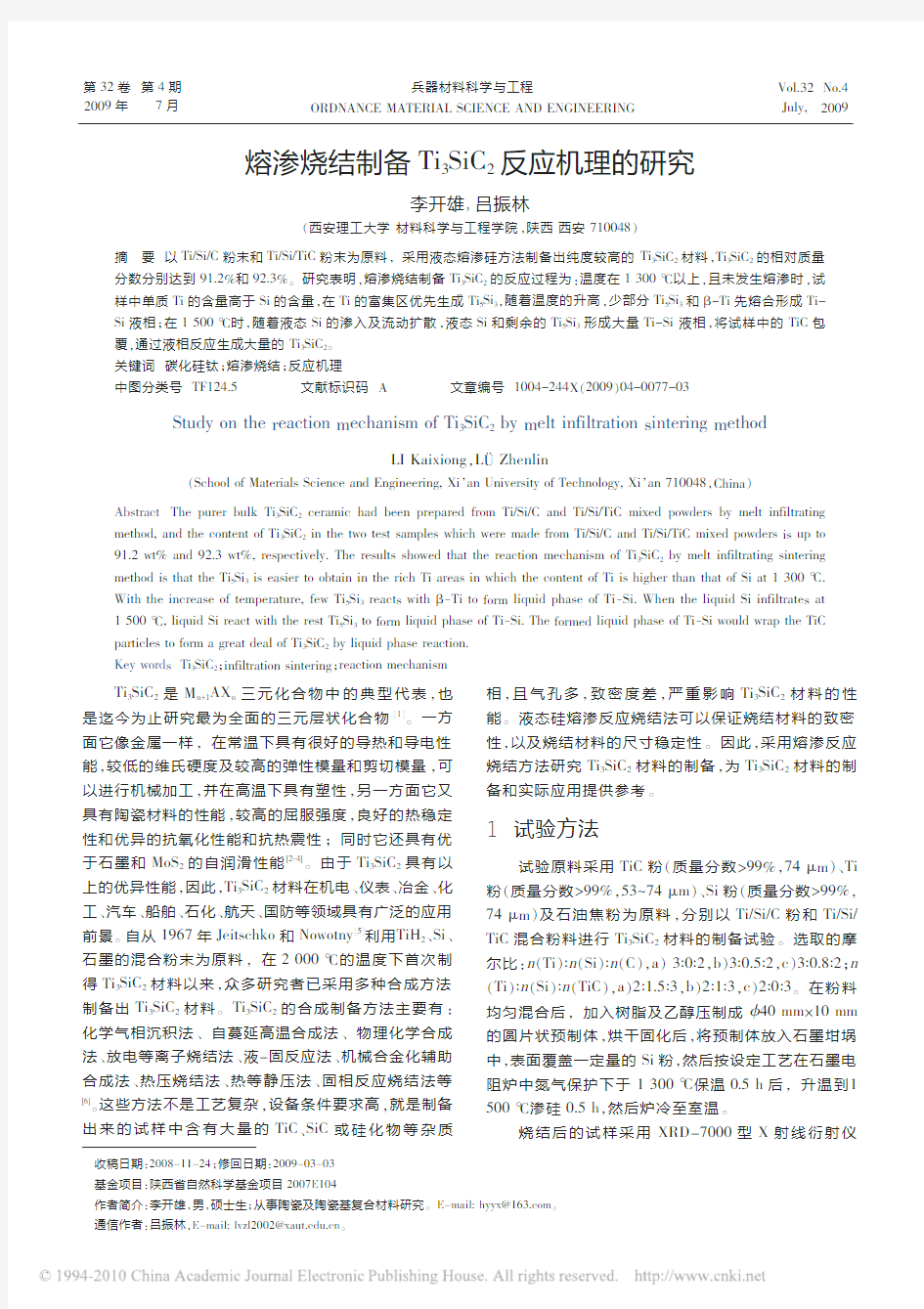

Ti 3SiC 2是M n+1AX n 三元化合物中的典型代表,也
是迄今为止研究最为全面的三元层状化合物[1]。一方面它像金属一样,在常温下具有很好的导热和导电性能,较低的维氏硬度及较高的弹性模量和剪切模量,可以进行机械加工,并在高温下具有塑性,另一方面它又具有陶瓷材料的性能,较高的屈服强度,良好的热稳定性和优异的抗氧化性能和抗热震性;同时它还具有优于石墨和MoS 2的自润滑性能[2-4]。由于Ti 3SiC 2具有以上的优异性能,因此,Ti 3SiC 2材料在机电、仪表、冶金、化工、汽车、船舶、石化、航天、国防等领域具有广泛的应用前景。自从1967年Jeitschko 和Nowotny [5]
利用TiH 2、Si 、
石墨的混合粉末为原料,在2000℃的温度下首次制得Ti 3SiC 2材料以来,众多研究者已采用多种合成方法制备出Ti 3SiC 2材料。Ti 3SiC 2的合成制备方法主要有:化学气相沉积法、自蔓延高温合成法、物理化学合成法、放电等离子烧结法、液-固反应法、机械合金化辅助合成法、热压烧结法、热等静压法、固相反应烧结法等
[6]
。这些方法不是工艺复杂,设备条件要求高,就是制备
出来的试样中含有大量的TiC 、SiC 或硅化物等杂质
相,且气孔多,致密度差,严重影响Ti 3SiC 2材料的性能。液态硅熔渗反应烧结法可以保证烧结材料的致密性,以及烧结材料的尺寸稳定性。因此,采用熔渗反应烧结方法研究Ti 3SiC 2材料的制备,为Ti 3SiC 2材料的制备和实际应用提供参考。
1试验方法
试验原料采用TiC 粉(质量分数>99%,74μm )、Ti 粉(质量分数>99%,53~74μm )、Si 粉(质量分数>99%,
74μm )及石油焦粉为原料,分别以Ti/Si/C 粉和Ti/Si/TiC 混合粉料进行Ti 3SiC 2材料的制备试验。选取的摩尔比:n (Ti )∶n (Si )∶n (C ),a )3∶0∶2,b )3∶0.5∶2,c )3∶0.8∶2;n (Ti )∶n (Si )∶n (TiC ),a )2∶1.5∶3,b )2∶1∶3,c )2∶0∶3。在粉料均匀混合后,加入树脂及乙醇压制成准40mm ×10mm
的圆片状预制体,烘干固化后,将预制体放入石墨坩埚中,表面覆盖一定量的Si 粉,然后按设定工艺在石墨电阻炉中氮气保护下于1300℃保温0.5h 后,升温到1
500℃渗硅0.5h ,然后炉冷至室温。
烧结后的试样采用XRD -7000型X 射线衍射仪
熔渗烧结制备Ti 3SiC 2反应机理的研究
李开雄,吕振林
(西安理工大学材料科学与工程学院,陕西西安710048)
摘
要以Ti/Si/C 粉末和Ti/Si/TiC 粉末为原料,采用液态熔渗硅方法制备出纯度较高的Ti 3SiC 2材料,Ti 3SiC 2的相对质量
分数分别达到91.2%和92.3%。研究表明,熔渗烧结制备Ti 3SiC 2的反应过程为:温度在1300℃以上,且未发生熔渗时,试样中单质Ti 的含量高于Si 的含量,在Ti 的富集区优先生成Ti 5Si 3,随着温度的升高,少部分Ti 5Si 3和β-Ti 先熔合形成Ti-
Si 液相;在1500℃时,随着液态Si 的渗入及流动扩散,液态Si 和剩余的Ti 5Si 3形成大量Ti-Si 液相,将试样中的TiC 包
覆,通过液相反应生成大量的Ti 3SiC 2。关键词碳化硅钛;熔渗烧结;反应机理中图分类号TF124.5
文献标识码A
文章编号1004-244X (2009)04-0077-03
Study on the r eaction m echanism of Ti 3SiC 2by m elt infiltration s intering m ethod
LI Kaixiong ,L 譈Zhenlin
(School of Materials Science and Engineering,Xi ’an University of Technology,Xi ’an 710048,China )
Abstract The purer bulk Ti 3SiC 2ceramic had been prepared from Ti/Si/C and Ti/Si/TiC mixed powders by melt infiltrating method,and the content of Ti 3SiC 2in the two test samples which were made from Ti/Si/C and Ti/Si/TiC mixed powders is up to 91.2wt%and 92.3wt%,respectively.The results showed that the reaction mechanism of Ti 3SiC 2by melt infiltrating sintering method is that the Ti 5Si 3is easier to obtain in the rich Ti areas in which the content of Ti is higher than that of Si at 1300℃.With the increase of temperature,few Ti 5Si 3react s with β ̄Ti to form liquid phase of Ti  ̄Si.When the liquid Si infiltrate s at 1500℃,liquid Si react with the rest Ti 5Si 3to form liquid phase of Ti  ̄Si.The formed liquid phase of Ti  ̄Si would wrap the TiC particles to form a great deal of Ti 3SiC 2by liquid phase reaction.
Key word s Ti 3SiC 2;infiltration sintering ;reaction mechanism
收稿日期:2008-11-24;修回日期:2009-03-03基金项目:陕西省自然科学基金项目2007E104
作者简介:李开雄,男,硕士生;从事陶瓷及陶瓷基复合材料研究。E-mail:hyyx@https://www.360docs.net/doc/a118695473.html, 。通信作者:吕振林,E-mail:lvzl2002@https://www.360docs.net/doc/a118695473.html, 。
2009年7月
兵器材料科学与工程
ORDNANCE MATERIAL SCIENCE AND ENGINEERING
Vol.32No.4
July,2009
第32卷第4期
兵器材料科学与工程
第32卷
测定分析其相组成,在JSM-6700F 场发射扫描电子显微镜(SEM )观察其显微组织。
为了定量确定熔渗法制备的Ti 3SiC 2材料中
Ti 3SiC 2相的含量,根据X 射线衍射结果,采用公式(1)计算Ti 3SiC 2的含量。
W 1%=
I 1/K 1
i =1
ΣI i
/K
i
×100%
(1)
式中:W 1—第1相的含量;I 1—第1相的衍射强度;
K 1—第1相的参比强度;I i —第i 相的衍射强度;K i —第i 相的参比强度。
2实验结果及讨论
2.1Ti/Si/C 为原料制备Ti 3SiC 2的相组成
不同摩尔比的Ti/Si/C 混合粉料的预制体熔渗烧结后试样的相组成如图1所示。从中可见:熔渗烧结的
试样中主要是Ti 3SiC 2和TiC 两相,TiSi 2含量很少。当
Si 的摩尔比由0~0.5时,烧结试样中的Ti 3SiC 2相的衍射峰值增强,TiC 相的衍射峰值稍微减弱,表明试样b 中Ti 3SiC 2的含量增加较多。当硅含量达到0.8(摩尔比)时,Ti 3SiC 2相的衍射峰值变化不大,但TiC 相的衍
射峰值进一步减弱;表明在熔渗烧结过程中,当试样中
Si 的含量在0.5(摩尔比)的基础上增加时,Ti 3SiC 2的含量变化不大,但TiC 相的含量进一步减少。这主要是因为随着Si 含量的增加,试样中Si 的分布更均匀;Ti-Si 液相与TiC 反应越充分。因此在c 配比下,采用熔渗硅烧结,可以得到高含量的Ti 3SiC 2复合材料。
根据公式(1)计算出烧结体中Ti 3SiC 2的含量,绘制出Ti 3SiC 2含量与Si 含量关系曲线,如图2所示。由此可见,粉料中Si 量增加,可以提高Ti 3SiC 2陶瓷中的Ti 3SiC 2相的含量。
2.2Ti/Si/TiC 为原料制备Ti 3SiC 2的相组成
不同摩尔比的Ti/Si/TiC 混合料的预制体熔渗烧
结后的相组成如图3所示。可以看出,加Si 摩尔比为
1.5的a 号试样Ti 3SiC 2质量分数最高,由XRD 衍射峰计算为9
2.3%以上,其中还有微量的TiC ;加Si 摩尔比为1的b 试样,其Ti 3SiC 2质量分数也较高,约在81.5%以上,试样中TiC 含量较a 号试样的高;不加Si 的c 试样,其相组成为Ti 3SiC 2和TiC 两相。与a 、b 两试样
相比,其Ti 3SiC 2含量最少,其TiC 质量分数最高,约为
30%。由此表明,在预制体中加入适量的Si 作为引导相,有助于Ti 3SiC 2的生成。
2.3熔渗烧结制备Ti 3SiC 2的热力学反应过程分析
为了说明合成Ti 3SiC 2的反应过程,将Ti-Si-C 系统分成3个二元系统,即Ti-C 、Si-C 、Ti-Si 。分析这3个系统中可能发生的反应及在1500℃(反应的主要温度)时的吉布斯自由能来确定Ti 3SiC 2相的形成过程[7]。在Ti-C 二元系统中,
Ti +C TiC
(2)ΔG (T )=-184096+12.14T (J/mol ),1500℃时ΔG 1500℃=-163(kJ/mol )。在Si-C 二元系统中,
Si +C SiC
(3)ΔG (T )=-73220+7.91T (J/mol ),1500℃时ΔG 1500℃=-
图3Ti/Si/TiC 为原料制备的试样的XRD 图谱
Fig.3XRD patterns of samples made from Ti/Si/TiC powders
70
60
5080
30
40
TiC
Ti 3SiC 2a
2θ/(觷)
c p s
b
c
70
60
5080
30
40
TiC
Ti 3SiC 2TiSi 2
2θ/(觷)
c p s
图1Ti/Si/C 粉为原料制备的试样的XRD 图谱
Fig.1XRD patterns of samples made from Ti/Si/C powders
c b a 706050
80900.00.61000.40.20.8T i 3S i C 2的质量分数/%
1.0
Si 的摩尔分数/%
图2粉料中Si 量与Ti 3SiC 2含量的关系曲线
Fig.2Relationship of Si amount in powders and Ti 3SiC 2
amount in sample
78
第4期李开雄等:熔渗烧结制备Ti 3SiC 2反应机理的研究
59.48(kJ/mol )。
在Ti-Si 二元系统中,由Ti-Si 二元系相图可以看出(见图4),可能生成的物相有Ti 5Si 3、Ti 5Si 4和TiSi 。
Ti +Si TiSi
(4)ΔG (T )=-129702+0.5T (J/mol ),1500℃时ΔG 1500℃=-
128.83(kJ/mol )。
Ti +Si
Ti 5Si 3(5)
ΔG (T )=-579066-8.36T (J/mol ),1500℃时ΔG 1500℃=-593.59(kJ/mol )。
Ti +Si Ti 5Si 4
(6)ΔG (T )=-324176-11.6T (J/mol ),1500℃时ΔG 1500℃=-344.33(kJ/mol )。
由Ti-Si 二元系相图可以看出(见图4),当温度为
862℃时,α-Ti 转化为β-Ti 。当温度达到1500℃时,Ti 5Si 3就会和β-Ti 、液态Si 共熔生成Ti-Si 液相,即:
Ti 5Si 3+β-Ti Ti-Si (L )(7)Ti 5Si 3+Si (L )
Ti-Si (L )
(8)
由于Si 的熔点为1414℃,所以熔渗过程中参与反应的液相也可能是Si 熔化后得到的液相,而不仅仅是Ti-Si 液相。
在Ti-C 和Si-C 系统中,随着反应温度的升高,Ti 与C 反应生成TiC 的吉布斯自由能比Si 与C 反应生成SiC 的吉布斯自由能小,因此Ti 原子与C 原子优先反应生成TiC ,且在该二元系中稳定存在;在Ti-Si 二元系中,Ti 原子与Si 原子反应合成Ti 5Si 3的吉布斯自由能最小,因此优先生成Ti 5Si 3;随着温度的升高,Ti 5Si 3逐渐与β-Ti 形成Ti-Si (L ),而Ti-Si (L )再与TiC 反应合成Ti 3SiC 2。随着Si 原子的渗入,硅不断补充到Ti-Si (L )中,从而使合成Ti 3SiC 2的含量增加。
因此可认为在熔渗烧结制备Ti 3SiC 2的过程中,发生的化学反应为:
Ti +C=TiC
5Ti +3Si=Ti 5Si 3
Ti 5Si 3+2Si +10TiC=Ti 3SiC 2。
图5是以Ti/Si/TiC 为原料,在1500℃下熔渗硅0.5h 后制得的Ti 3SiC 2材料的断口显微形貌。从中可见,存在大量层片状的Ti 3SiC 2颗粒,并且颗粒之间能
平滑的连续的堆叠或连接在一起,没有明显的界面。而且片状的Ti 3SiC 2连接在一起,形成了块状结构,有明显的液相流动的痕迹。由此表明,在烧结过程中有大量的液相产生,并发生流动迁移。这与Ti-Si(L)与TiC 反应合成Ti 3SiC 2的分析相符。因此,可以得出熔渗烧结制备Ti 3SiC 2的反应过程为:温度在1300℃以上,且未发生熔渗时,试样中单质Ti 的含量高于Si 的含量,在
Ti 的富集区优先生成Ti 5Si 3和TiC ,随着温度的升高,少部分Ti 5Si 3和β-Ti 先熔合形成Ti-Si 液相;随着液态Si 的渗入及流动扩散,液态的Si 和剩余的Ti 5Si 3形
成大量Ti-Si 液相,将试样中的TiC 包覆,通过液相反应生成大量的Ti 3SiC 2。
3结论
1)以Ti/Si/C 粉料和Ti/Si/TiC 粉料为原料在1500℃保温0.5h 熔渗Si 均可制备出纯度较高的Ti 3SiC 2块体材料,Ti 3SiC 2相的质量分数分别达到93.2%和92.3%。
2)熔渗烧结制备Ti 3SiC 2的反应机理为:温度在1300℃以上,且未发生熔渗时,单质Ti 与单质C 及单质Si 优先反应,在Si 的富集区生成TiC 和Ti 5Si 3,随着
温度的升高,少部分Ti 5Si 3和β-Ti 熔合形成Ti-Si 液相;在1500℃时,随着液态Si 的渗入及流动扩散,液态的Si 和剩余的Ti 5Si 3形成大量Ti-Si 液相,将试样中的TiC 包覆,通过液相反应生成大量的Ti 3SiC 2。
4参考文献
[1]Barsoum M W.The M N +1AX N phases:a new class of solid ;
图51500℃熔渗硅0.5h 的Ti 3SiC 2材料断口结构
Fig.5Fractograph of Ti 3SiC 2infiltrated at 1500℃for 0.5h
图4Ti  ̄Si 二元系稳定相图[8]
Fig.4Ti  ̄Si binary phase diagram
Ti
0.60.4Si
T e m p e r a t u r e /℃
05Mole traction Si
0.220102515α-Ti β-Ti 0.8
1(×102)
1570
1485
2130
133719201170
1480
133079
thermodynamically stable nanolaminate [J ].Progress in Solid State Chemistry ,2000,28:201-281.
[2]El-Raghy T ,Barsoum M W ,Zaval Iangos A ,et al.Processing
and mechanical properties of Ti 3SiC 2:Ⅱ.Effect of grain size and formation temperature [J ].J Am Ceram Soc ,1999,82(10):2855-2860.
[3]Barsoum M W,Brodkin D ,El-Raghy https://www.360docs.net/doc/a118695473.html,yered machinable
ceramics for high temperature applications [J ].Scripta Materi -ala,1997,36(5):535-541.
[4]Myhra S,Summers J W B ,Kisi E H .Ti 3SiC 2-a layered
ceramic exhibiting ultra-low friction [J ].Materials Letter ,1999
(39):6-11.
[5]Jeitschko W,Nowotny H.Die kristallstructur von Ti 3SiC 2-ein
neuer komplxcar-bid type [J ].Monatash fur Chem ,1967,98
(2):329-337.
[6]朱教群.三元层状碳合物Ti 3SiC 2的制备及性能的研究[D ].
武汉:武汉理工大学博士学位论文,2003.
[7]程兰征,章燕豪.物理化学[M ].上海:上海科学技术出版
社,2005.
[8]Seifert H J ,Lukas H L ,Petzow G.Thermodynamic optimiza -
tion of the Ti-Si System [J ].1996,87(1):2-13.
镁合金是迄今为止实际应用中最轻的金属结构材料,具有密度小、比强度和比刚度高、减震性和切削加工性好等优点。近年来,为应对全球性的能源危机和环境污染问题,镁合金作为汽车工业的一种轻量化结构材料备受关注。然而,镁合金腐蚀性能差的缺点已成为大规模工业化应用的障碍。因此,如何提高其耐腐蚀性能显得十分重要[1-5]。AZ91D 镁合金具有优异的铸造性能和良好的室温力学性能,是目前成功商业应用的镁合金,在镁合金中添加稀土元素是提高合金性能的一种重要手段。稀土元素不但可以强化镁合金基体,改善其铸造性能[6],而且有可能与镁合金中的氢以及镁合金中的氧离子反应[7]
,生成密度大、易于排除的夹杂,达到除氢和除渣的效果。目前已有的相关文献
中,关于稀土元素对镁合金力学性能影响机制的研究占了研究工作的大部分,但就稀土元素对合金腐蚀性能的影响研究相对要少得多。本试验选择在通氩气下,加入稀土Y 作为精炼剂的复合净化处理工艺。试验以
AZ91D 镁合金为研究对象,探讨加入Y 稀土精炼剂对AZ91D 镁合金微观组织和腐蚀性能的影响。
1试验
1.1试验材料及工艺
试验原料为山西闻喜银光镁业公司生产的
AZ91D 镁合金铸锭(具体成分见表1)和Mg-25.28%Y (质量分数)中间合金,氩气的质量分数为99.6%。参考前人的研究成果[8],当Y 的质量分数超过1.0%以后,
稀土钇对AZ91D 镁合金微观组织和腐蚀性能影响的研究
齐伟光,王进华,邢志媛,吕绯,刘环恩,李冬梅
(中国兵器科学研究院宁波分院,浙江宁波315103)
摘要为改善镁合金的耐腐蚀性能,进一步拓宽镁合金的应用范围,研究通氩气下加入稀土Y 对AZ91D 镁合金组织和性能的影响。结果表明:AZ91D 镁合金加入Y 后,显微组织主要由α-Mg 基体相、β相(Mg 17Al 12)、Al 2Y 相和Al 6Mn 6Y 相组成。加入1%Y 能显著降低合金的腐蚀速度,提高合金的平衡电位和腐蚀电位,降低腐蚀电流。关键词镁合金;显微组织;腐蚀性能中图分类号TG146.2+2
文献标识码A
文章编号1004-244X (2009)04-0080-04
Effects of Y on m icrostructure and corrosion resistance of AZ91D magnesium alloy
QI Weiguang ,WANG Jinhua ,XING Zhiyuan ,L 譈Fei ,LIU Huan ’en ,LI Dongmei
(Ningbo Branch of China Academy of Ordna n ce Science ,Ningbo 315103,China )
Abstract In order to improve the corrosion resistance and enlarge the applied scope of magnesium alloys.The effects of yttrium on the microstructure and mechanical properties of AZ91D magnesium alloy were studied in this paper .The experimental results showed that the microstructure of AZ91D magnesium alloy was mainly composed of α ̄Mg matrix ,β(Mg 17Al 12)phase ,Al 2Y phase and Al 6Mn 6Y phase when yttrium was added.It was found that 1%amount of yttrium significantly reduced corrosion rate ,enhanced the electrode voltage and lowered corrosion current of AZ91D magnesium.
Key words magnesium alloy ;microstructure ;corrosion resistance
收稿日期:2008-04-16;修回日期:2009-02-27
作者简介:齐伟光,男,硕士研究生;主要从事镁合金材料研究。Email :qwguang@https://www.360docs.net/doc/a118695473.html, 。
!!!!!!!!!!!!!!!!!!!!!!!!!!!!!!!!!!!!!!!!!!!!!!!!!!!!!!!!!!!!
2009年7月
兵器材料科学与工程
ORDNANCE MATERIAL SCIENCE AND ENGINEERING
Vol.32No.4
July,2009
第32卷第4期
粉末冶金烧结技术的研究进展
总第56期第4期 贵阳金筑大学学报 2004年12月 粉末冶金烧结技术的研究进展 林 芸 ① (西安交通大学材料科学与工程学院 西安 710049) 摘 要:烧结作为粉末冶金最重要的一个工艺环节一直以来是人们研究的重点,介绍粉末冶金烧结技术的研究进展,以体现烧结在粉末冶金中的重要地位,推进新材料制备技术的发展。 关键词:粉末冶金 烧结 新技术中图分类号:TF124 文献标识码:B 文章编号:1671-3621(2004)04-0106-0108 现代科学技术的不断发展牵引着工程材料向着复合化、高性能化、功能化、结构功能一体化和智能化方向发展,各行业对材料的性能提出了越来越高的要求。在不断开发新材料的同时,人们也在不断地寻求新型材料的制备方法,小型化、自动化、精密化、省能源、无污染的材料制备方法成为人们追求的目标。现代粉末冶金技术由于其少切屑、无切屑及近净成形的工艺特点,在新材料的制备中发挥了越来越大的作用。它的低耗、节能、节材,易控制产品孔隙度,易实现金属-非金属复合,金属-高分子复合等特点使其成为制取各种高性能结构材料、特种功能材料和极限条件下工作材料的有效途径[1],受到了人们的广泛关注。 从现代复合材料技术的理论来看,粉末冶金复合技术从微观上改变了单一材料的性能,依靠扩散流动使物质发生迁移,同时原材料的晶体组织发生变化,最终“优育”出高性能的复合材料。而烧结作为粉末冶金生产过程中最重要的工序,一直以来是人们研究的重点,各种促进烧结的方法不断涌现,对改进烧结工艺,提高粉末冶金制品的力学性能,降低物质与能源消耗,起了积极的作用。本文简单介绍近几年出现的几种烧结新技术,以期反映粉末冶金在高技术领域所起的重要作用。 1、放电等离子体烧结(Spark Plasma Sintering , SPS ) 放电等离子体烧结(SPS )也称作等离子体活化 烧结(Plasma Activated Sintering ,PAS )或脉冲电流热压烧结(Pulse Current Pressure Sintering ),是自90年代以来国外开始研究的一种快速烧结新工艺[2]。由于它融等离子体活化、热压、电阻加热为一体,具有烧结时间短、温度控制准确、易自动化、烧结样品颗粒均匀、致密度高等优点,仅在几分钟之内就使烧结产品的相对理论密度接近100%,而且能抑制样品颗粒的长大,提高材料的各种性能,因而在材料处理过程中充分显示了优越性。 将瞬间、断续、高能脉冲电流通入装有粉末的模具上,在粉末颗粒间即可产生等离子放电,由于等离子体是一种高活性离子化的电导气体,因此,等离子体能迅速消除粉末颗粒表面吸附的杂质和气体,并加快物质高速度的扩散和迁移,导致粉末的净化、活化、均化等效应。第三代SPS 设备采用的是开关直流脉冲电源,在50Hz 供电电源下,发生一个脉冲的时间为312ms ,由于强脉冲电流加在粉末颗粒间,即可产生诸多有利于快速烧结的效应。首先,由于脉冲放电产生的放电冲击波以及电子、离子在电场中反方向的高速流动,可使粉末吸附的气体逸散,粉末表面的起始氧化膜在一定程度上可被击穿,使粉末得以净化、活化;其次,由于脉冲是瞬间、断续、高频率发生, ? 601?①收稿日期:2004-6-10作者简介:林芸(1965-),女,高级工程师,西安交通大学材料与工程学院在读工程硕士,主要研究方向:金属基复合材料制备工艺。
一烧结基本原理
一烧结基本原理集团标准化办公室:[VV986T-J682P28-JP266L8-68PNN]
一、烧结 (1)、烧结基本原理 烧结是粉末冶金生产过程中最基本的工序之一。烧结对最终产品的性能起着决定性作用,因为由烧结造成的废品是无法通过以后的工序挽救的;相反,烧结前的工序中的某些缺陷,在一定的范围内可以通过烧结工艺的调整, 例如适当改变温度,调节升降温时间与速度等而加以纠正。 烧结是粉末或粉末压坯,加热到低于其中基本成分的熔点温度,然后以一定的方法和速度冷却到室温的过程。烧结的结果是粉末颗粒之间发生粘结,烧结体的强度增加。在烧结过程中发生一系列物理和化学的变化,把粉末颗粒的聚集体变成为晶粒的聚结体,从而获得具有所需物理,机械性能的制品或材料。烧结时,除了粉末颗粒联结外,还可能发生致密化,合金化,热处理,联接等作用。人们一般还把金属粉末烧结过程分类为:1、单相粉末(纯金属、古熔体或金属化合物)烧结;2、多相粉末(金属—金属或金属—非金属)固相烧结;3、多相粉末液相烧结;4、熔浸。 通常在目前PORITE微小轴承所接触的和需要了解的为前三类烧结。通常在烧结过程中粉末颗粒常发生有以下几个阶段的变化:1、颗粒间开始联结;2、颗粒间粘结颈长大;3、孔隙通道的封闭;4、孔隙球化;5、孔隙收缩;6、孔隙粗化。 上述烧结过程中的种种变化都与物质的运动和迁移密切相关。理论上机理为:1、蒸发凝聚;2、体积扩散;3、表面扩散;4、晶间扩散;5、粘性流动;6、塑性流动。
(2)、烧结工艺 2-1、烧结的过程 粉末冶金的烧结过程大致可以分成四个温度阶段: 1、低温预烧阶段,在此阶段主要发生金属的回复及吸附气体和水分的挥发,压坯内成形剂的分解和排除等。在PORITE微小铜、铁系轴承中,用R、B、O(Rapid Burning Off)来代替低温预烧阶段,且铜、铁系产品经过R、B、O后会氧化,但在本体中可以被还原,同时还可以促进烧结。 2、中温升温烧结阶段,在此阶段开始出现再结晶,首先在颗粒内,变形的晶粒得以恢复,改组为新晶粒,同时颗粒表面氧化物被完全还原,颗粒界面形成烧结颈。 3、高温保温完成烧结阶段,此阶段是烧结得主要过程,如扩散和流动充分地进行和接近完成,形成大量闭孔,并继续缩小,使得孔隙尺寸和孔隙总数均有减少,烧结体密度明显增加
陶瓷材料烧结技术的研究进展
Material Sciences 材料科学, 2017, 7(6), 628-632 Published Online September 2017 in Hans. https://www.360docs.net/doc/a118695473.html,/journal/ms https://https://www.360docs.net/doc/a118695473.html,/10.12677/ms.2017.76083 Research and Application on Sintering Technology of Ceramic Materials Haitao Zheng1, Tingting Pan2 1Harbin Aurora Optoelectronics Technology Co., Ltd., Harbin Heilongjiang 2Heilongjiang University of Finance and Economics, Harbin Heilongjiang Received: Sep. 3rd, 2017; accepted: Sep. 22nd, 2017; published: Sep. 28th, 2017 Abstract Advanced ceramic materials are widely used in aerospace, electronics, mechanical, biological, medical and other fields because of its fine structure and high strength, high hardness, high tem-perature resistant, corrosion resistance, wear-resisting property and a series of excellent features. The sintering technology of ceramic materials has an important influence on the structure and property of the material itself. This paper summarized the ceramic sintering mechanism, research progress and application, and indicated the future research direction. Keywords Sintering Technology, Mechanism, Research Development, Application 陶瓷材料烧结技术的研究进展 郑海涛1,潘婷婷2 1哈尔滨奥瑞德光电技术有限公司,黑龙江哈尔滨 2黑龙江财经学院,黑龙江哈尔滨 收稿日期:2017年9月3日;录用日期:2017年9月22日;发布日期:2017年9月28日 摘要 先进陶瓷材料由于其精细的结构组成及高强度、高硬度、耐高温、抗腐蚀、耐磨等一系列优良特性被广泛应用于航空航天、电子、机械、生物医学等各个领域。陶瓷材料的烧结技术对材料本身的结构及性能有着重要影响。本文对陶瓷材料的烧结机理、研究进展及应用进行了总结,并提出了今后的研究方向。
烧结工序节能降耗新技术发展趋势
烧结工序节能降耗新技术发展趋势 王 梁 (中钢设备有限公司烧结部,北京100080 )摘 要:通过分析节能降耗的意义和国内烧结能耗现状,从改善原料条件、回收利用及降低电耗方面总结了国内外常用烧结节能降耗的技术措施,并阐述了部分技术措施的实际运行效果;结合设计经验及考察部分烧结厂实际运行情况,通过分析部分设计和生产参数,探讨了近几年国内采用的烧结节能降耗技术及实际运行效果,提出了烧结节能降耗技术未来发展的建议。关键词:烧结;节能;降耗 文献标志码:A 文章编号:1006-9356(2015)12-0064- 04Development tendency of new energy saving andconsumption reducing technology during sintering processWANG Liang (Sintering Engineering Department,Sinosteel Equipment and Engineering Co.,Ltd.,Beijing 100080,China)Abstract:Through the analysis of the significance of energy saving and consumption reducing as well as the presentsituation of sintering energy consumption in our country,sintering energy saving and consumption reducing technol-ogies commonly used at home and abroad are summarized from improving the raw material conditions,recycling andreducing power consumption,and the actual operating effect of some technical measures is expounded.Combinedwith the individual design experience and actual running condition in some sintering plants,the sintering energy sav-ing technologies used in our country in recent years and the actual operating effect are discussed by analyzing the de-sign of the plant and the production parameters.Moreover,some suggestions for the future development of the sin-tering energy consumption technology are put forward.Key words:sintering;energy saving;consumption reducing作者简介:王 梁(1979—),男,硕士,工程师; E-mail:254849151@qq .com; 收稿日期:2014-12-12 节能降耗是指加强用能管理, 采取技术上可行、经济上合理以及环境和社会可以承受的措施,从能源生产到消费的各个环节,降低消耗,减少损失和污染物排放,有效、合理地利用能源。节能降耗对国民经济的持续发展、技术的进步、保护自然资源和环境都具有深远的战略意义。钢铁企业是能源消耗的大户,其中烧结能耗占10%~15%, 采取有效措施最大幅度地降低烧结过程中的能源消耗具有重大意义。 1 国内烧结能耗现状 中国在2010年公布的《钢铁企业节能设计规范》中明确说明烧结工序能耗设计指标应符合以下 标准:电按当量值算时不小于300m2 的大型烧结机,其能耗应不高于53kg /t(矿);180~300m2 的中型烧结机不高于55kg/t(矿),但在实际生产时,由于能源条件、装备水平、自动化水平、操作水平等各种条件的限制其能耗会高于国家标准能耗参数。所 以在设计、生产中采取各种有效措施,最大幅度地降低烧结过程中的能耗指标对节能降耗有重大意义。 2 已成熟推广的节能降耗技术 2.1 改善原料及混合料的条件2.1.1 强化原料及烧结混合料的混匀效果 对于烧结而言,原料混匀能够使矿种结构稳定、粒度均匀,对于一些矿种较多,原料化学成分、粒度等波动较大的企业来说,原料混匀就显得尤为重要;在烧结的配料工艺中要配入燃料、熔剂、返矿等物料,将这些物料混匀能使烧结过程稳定进行、减少波动。所以强化原料及烧结混合料的混匀效果能够使烧结过程便于控制、烧结矿成分稳定、有利于烧结能 耗的降低[ 1- 2]。2.1.2 完善燃料破碎系统 燃料破碎工艺设计中要确定正确的燃料使用制度和改善其粒度组成。因为燃料过细使得烧结速度
一烧结基本原理
一、烧结 (1)、烧结基本原理 烧结是粉末冶金生产过程中最基本的工序之一。烧结对最终产品的性能起着决定性作用,因为由烧结造成的废品是无法通过以后的工序挽救的;相反,烧结前的工序中的某些缺陷,在一定的范围内可以通过烧结工艺的调整,例如适当改变温度,调节升降温时间与速度等而加以纠正。 烧结是粉末或粉末压坯,加热到低于其中基本成分的熔点温度,然后以一定的方法和速度冷却到室温的过程。烧结的结果是粉末颗粒之间发生粘结,烧结体的强度增加。在烧结过程中发生一系列物理和化学的变化,把粉末颗粒的聚集体变成为晶粒的聚结体,从而获得具有所需物理,机械性能的制品或材料。烧结时,除了粉末颗粒联结外,还可能发生致密化,合金化,热处理,联接等作用。人们一般还把金属粉末烧结过程分类为:1、单相粉末(纯金属、古熔体或金属化合物)烧结;2、多相粉末(金属—金属或金属—非金属)固相烧结;3、多相粉末液相烧结;4、熔浸。 通常在目前PORITE微小轴承所接触的和需要了解的为前三类烧结。通常在烧结过程中粉末颗粒常发生有以下几个阶段的变化:1、颗粒间开始联结; 2、颗粒间粘结颈长大; 3、孔隙通道的封闭; 4、孔隙球化; 5、孔隙收缩; 6、孔隙粗化。 上述烧结过程中的种种变化都与物质的运动和迁移密切相关。理论上机理为:1、蒸发凝聚;2、体积扩散;3、表面扩散;4、晶间扩散;5、粘性流动;6、塑性流动。
(2)、烧结工艺 2-1、烧结的过程 粉末冶金的烧结过程大致可以分成四个温度阶段: 1、低温预烧阶段,在此阶段主要发生金属的回复及吸附气体和水分的挥发,压坯内成形剂的分解和排除等。在PORITE微小铜、铁系轴承中,用R、B、O(Rapid Burning Off)来代替低温预烧阶段,且铜、铁系产品经过R、B、O 后会氧化,但在本体中可以被还原,同时还可以促进烧结。 2、中温升温烧结阶段,在此阶段开始出现再结晶,首先在颗粒内,变形的晶粒得以恢复,改组为新晶粒,同时颗粒表面氧化物被完全还原,颗粒界面形成烧结颈。 3、高温保温完成烧结阶段,此阶段是烧结得主要过程,如扩散和流动充分地进行和接近完成,形成大量闭孔,并继续缩小,使得孔隙尺寸和孔隙总数均有减少,烧结体密度明显增加 4、冷却阶段:实际的烧结过程,都是连续烧结,所以从烧结温度缓慢冷却一段时间然后快冷,到出炉量达到室温的过程,也是奥氏体分解和最终组
热压烧结技术的研究与应用
热压烧结技术的研究与应用 姓名:陈琼毅 专业:无机非金属 学号:20080800301
热压烧结技术的研究与应用 陈琼毅无机非金属 20080800301 摘要:热压烧结是一种压制成形和烧结同时进行的粉体材料成形工艺方法,是将粉末装在压模内,在专门的热压机中加压同时把粉末加热到熔点以下,在高温下单向或双向施压成形的过程。热压烧结具有烧结时间短、温度低、晶粒细、产品性能高等优点。 关键词:烧结热压热压烧结 1热压烧结技术发展背景 自20世纪70年代中期以来,除北美外,烧结矿一直是国内外高炉的主要原料。但由于金融危机,钢铁产业的不景气,烧结技术研究发展受到限制。所幸的是随着人们对产品质量和能源节约的重视,烧结技术再一次焕发出新生。1826年索波列夫斯基首次利用常温压力烧结的方法得到了白金。1912年,德国发表了用热压将钨粉和碳化钨粉混合制造成致密件的专利。从1930年以后,热压更快地发展起来,主要应用于大型硬质合金制品、难熔化合物和现代陶瓷等方面。在这个日新月异的新世纪中,有人大胆的将热压烧结技术与纳米材料、超导材料和复合材料等相联系结合,开创了热压烧结技术的新天地。 2热压烧结技术的原理 2.1烧结定义与特点 其宏观定义为:粉体原料经过成型、加热到低于熔点的温度,发生固结、气孔率下降、收缩加大、致密度提高、晶粒增大,变成坚硬的烧结体,这个现象称为烧结。 其微观定义为:固态中分子(或原子)的相互吸引,通过加热,质点获得足够的能量,进行迁移使粉末体产生颗粒粘结,增加强度并导致致密化和再结晶的过程称为烧结。
烧结的特点有三点:第一,烧结温度远低于熔点温度下,质点发生迁移、扩散、开始烧结温度在0.3-0.5T m范围内,这样便节省了大量的能源利于环境保护,而且便于制造高熔点物质如钨丝等;第二,同样对于硅酸盐材料,完全烧结温度在0.7-0.8T m;第三,烧结主要是物理过程,但也伴随有固相反应,烧结前后主晶相不变化。这样便易于控制烧结成品的物象成分。 2.2热压定义与优缺点 热压的定义:热压是指在对置于限定形状的石墨模具中的松散粉末或对粉末压坯加热的同时对其施加单轴压力的烧结过程。 热压的优点:由于热压时粉料处于热塑性状态,形变阻力小,易于塑性流动和致密化,因此其所需的成型压力仅为冷压法的1/10,可以成型大尺寸的A12O3、BeO、BN和TiB2等产品。由于同时加温、加压,有助于粉末颗粒的接触和扩散、流动等传质过程,降低烧结温度和缩短烧结时间,因而抑制了晶粒的长大。热压法容易获得接近理论密度、气孔率接近于零的烧结体,容易得到细晶粒的组织,容易实现晶体的取向效应和控制有高蒸气压成分纳米系统的组成变化,因而容易得到具有良好的机械性能、电学性能的产品,而且能生产形状较复杂、尺寸较精确的产品。 热压的缺点:热压法生产工艺复杂生产率低、成本高,不能普及生产工艺。 2.3热压烧结定义、过程与特点 热压烧结的定义:热压烧结就是一种压制成形和烧结同时进行的粉体材料成形工艺方法,是将粉末装在压模内,在专门的热压机中加压同时把粉末加热到熔点以下,在高温下单向或双向施压成形的过程。 热压烧结的过程:在烧结过程中,高温高压的交互作用使粉体颗粒的粘性、塑性流动及原子的扩散得以加强;同时颗粒与颗粒间的接触点因有较大的接触电阻,在烧结时的大电流下产生电弧放弧或局部大量发热,而且电磁场的作用进一步加速了原子的扩散,有利于烧结颈的形成和长大,具有催化和活化烧结功效,并有利于坯件的烧成,使烧结温度降低、时间缩短、性能提高。 热压烧结的特点:热压烧结的优点是烧结时间短、温度低、晶粒细、产品性能高等;热压烧结的缺点是过程及设备复杂,生产控制要求严,模具材料要求高,能源消耗大,生产效率较低,生产成本高。 2.4烧结过程驱动力
烧结工艺技术操作要点
烧结工艺技术操作要点 根据公司颁发《关于工艺技术标准化操作推进实施方案的通知》要求,为确保我厂烧结、球团生产过程正常、稳顺进行,实现生产、工艺、技术、操作精细化管理,达到提高产品质量、降低生产成本,为下道工序高炉稳顺及增铁节焦创造条件。特此,在中和预配料、烧结及球团主要工序和关键岗位制定以下工艺技术操作要点。 一、中和预配料 1、严格按厂(技术室)下达的预配比通知单进行配料,并要求认真做好配料原始记录。 2、每班进行1-2次清理配料圆盘闸门口、电子皮带秤杂物,给料不畅及时挫料,严禁缺品种配料或少配后补。 3、配料作业中,做到勤检查,岗位巡回检查30分种一次。 4、电子皮带秤:每班校皮不少于一次;电子皮带秤校秤为6个月一次,配料工及车间工艺员配合校验,并要求有校秤文字记录。发现电子皮带秤计量不准,应在4小时反映。电子皮带秤架必须保持清洁,辊子无粘料,清扫器要刮料干净,配料误差控制在1%之内。 5、二次料场:堆料机在规定堆位及长度上逐层平铺造堆,保证混匀效果;禁止分段平铺、空段和定点堆料;料层数控制在300层以上。 6、产量:配料流量控制在1100t/h之内,二次料场A跨每堆控制在6万吨±5000吨,B跨控制在9.5万吨±5000吨,C跨每堆控制在8.5万吨±5000吨,雨季各减1万吨。
7、质量:每堆料品位稳定率(Fe±0.5%)达75%之上,二氧化硅稳定率(SiO2±0.5%)达95%之上。 二、烧结 1、配料工序 1.1严格执行技术科下达的配料通知单,精心配料,坚决杜绝断品种配料和乱配现象。如发生碱度波动:三烧由配料工可调节石粉和中和料配比,二烧由主控工调节石粉和中和料配比,并要求认真做好配料原始记录。 1.2根据烧结生产需要,确保烧结矿实物质量的前提下,三烧(130/180)双机生产配重按580—650t/h控制为宜;三烧如遇单机生产则配重减半范围控制;二烧(280m2)配重按630—700t/h控制为宜。 1.3配料电子皮带秤:如发现皮带秤计量不准,应在4小时内联系信息自动化中心组织校秤,配料工及车间工艺员配合校验,并要求有校秤文字记录。 1.4配料作业中,做到勤检查,岗位巡回检查60分种一次。 2、混合工序 2.1一次混合主要是加水混匀,包括生石灰消化;混合料水份配加以一次圆筒加足所需水份的80—90%为宜。 2.2二次混合:一是补充加水,另二主要是混匀制粒,提高混合料透气性。二次圆筒加水20—10%为宜。 2.3一次、二次混合料的水分测定,由红外测水仪监控与调节;二烧 (280m2)、三烧(130/180)混合料控制适宜水份分别为6—9%。正常生产时,由红外线自动加水系统自动控制混合加水量。 2.4当水份自动检测系统出现故障时,岗位人员根据上料量、返矿量的变
选择性激光烧结技术的研究现状与展望
选择性激光烧结技术的研究现状与展望 【摘要】选择『生激光加工是20世纪80年代末出现的一种新的快速成型工艺,它利用激光束烧结粉末材料制造原型,具有原料广泛、制作工艺简单、周期短等特点,在诸多领域得到了广泛的应用。介绍了选择性激光烧结技术的原理、特点及实际应用,综述了选择}生激光烧结技术发展状况、存在的问题及研究热点。 键词:快速成形;选择性激光烧结;综述 1引言 20世纪90年代开始,随着世界经济竞争的日益激烈化和全球化,产品制造商们越来越需要以最短的时间制造出符合人们消费需求的新产品来抢占市场。20世纪80年代末出现的快速成型(Rapid Prototyping,简称RP)就是在这样的背景下提出并逐步得以发展的。RP技术是一种逐层零件制造工艺,它突破传统的材料变形成型和去除材料成型的工艺方法,使用近乎全自动化的工艺从CAD文件直接生产所需要的模型或模具,可以显著减少产品原型的开发时间和成本,极大的提高产品的质量,另外,RP制造过程中不需要任何传统意义上的工装夹具、刀具或模具即可制造出任何复杂形状的零部件。因此。RP技术在现代制造业巾越来越具有竞争力,有望成为21世纪的的主流制造技术。目前典型的快速成型的方法有:光固化立体造型SLA(StereoLithography Apparatus)、分层物件制作LOM(Laminated ObjectManufacturing)、选择性激光烧结SIS(Selective LArSintering)和熔融沉积造型FDM(Fused Deposition Modeling)等。各种RP方法具有其自身的特点和适用范围。由于SIS工艺具有粉末选材广泛、适用性广、制造工艺比较简单、成形精度高、无需支撑结构、可直接烧结零件等诸多优点,在现代制造业得到越来越广泛的重视。主要综述SIS技术的工艺原理、实际应用、发展历程和现状。 2 SLS技术的原理 选择性激光加工(SLS)又称选区激光烧结是以C02激光器为能源,利用计算机控制红外激光束对非金属粉末、金属粉末或复合物的粉末薄层,以一定的速度和能龟密度按分层面的二维数据进行扣描烧结,层层堆积,最后形成成形件。SIS技术集CAD技术、数控技术、激光加工技术和材料科学技术于一体,整个工艺装置由粉末缸(PowderCylinder)、成型缸(ModelCylinder)、激光器、计算机控制系统四部分组成。工作时,粉末缸活寒(送粉活塞)上升,先在皋体上用滚筒均匀铺上一薄层金属粉末,并将其加热至略低于材料熔点,以减少热变形,并利于与前一层面的结合。然后,激光束在计算机控制光路系统的精确引导F,按照零件的分层轮廓有选择地进行烧结,使材料粉末烧结或熔化后凝固形成零件的一个层面,没有烧过的地方仍保持粉末状态,并可作为有悬臂的微结构下一层烧结的支撑。烧结完一层后,基体下移一个截面层厚,铺粉系统铺设新粉,计算机控制激光束再次扫描进行下一层的烧结。如此循环,层层叠加,就得到三维零件。最后,将未烧结的粉末同收剑粉未缸中,取出成型件,再进行打磨、烘干等后处理工艺,最终形成满足要求的原形或制件。 3 SLS技术实际应用 SIS工艺已经成功应用于汽车、造船、航天、航空、通汛、微机电系统、建筑、医疗、考古等诸多行业,为许多传统制造业注入了新的创造力,也带来了信息化的气息。概括来说,SIS 工艺可以应用于一下场合:(1)快速原型制造。SI.S工艺可快速制造所没计零件的原形,并对产品及时进行评价、修正以提高设计质量;可使客户获得直观的零件模型;能制造教学、试验用复杂模型。(2)新型材料的制备及研发。利用SIS工艺可以开发一些新型的颗粒以增强复合材料和硬质合金。(3)小批量、特殊零件的制造加工。在制造业领域,经常遇到小批最及特殊零件的生产。这类零件加工周期长,成本高,对于某些形状复杂零件,甚至无法制造。采用SIS技术可经济地实现小批量和形状复杂零件的制造。(4)快速模具和工具制造。SIS制造的零件可直接作为模具使用,如熔模铸造、砂型铸造、注甥模型、高精度形状复杂的金属
烧结技术综述
1文献综述 1.1烧结生产概况 1.1.1烧结及其发展 烧结法是迄今为止除北美以外使用最为广泛的铁矿石造块方法。自20世纪80年代起烧结技术得到了快速发展,主要体现在烧结工艺和新技术的研究开发和应用上。烧结工艺方面如自动化配料、混合料强化制粒、偏析布料、冷却筛分、整粒技术及铺底料技术等;新技术主要表现为球团烧结技术、小球烧结技术、低温烧结技术等。上述工艺和技术目前已经在大部分钢铁企业推广应用,并取得了显著的经济效益。 1897年,T.Huntington和F,Heberlein申请并注册了第一个有关烧结方面的专利。1905年,E.J.Savelsberg首先把T.Huntington-F.Heberlein烧结杯用于铁矿石烧结,从而开辟了烧结法进行铁矿粉造块的新纪元。在当今的冶金生产中,烧结已成为一道重要的单元工序并占有相当重要地位。据统计,全世界约有一半的生铁是用烧结矿生产的。过去十年中,世界上烧结矿年产量维持在538×106t~586×106t范围内。从1989年起,由于独联体和其他部分东欧国家发生巨变,因此,它们的钢铁工业进行了重新调整,导致烧结矿产量有所下降。欧洲和日本的经济衰退也影响了产量,但是不久烧结矿的产量又慢慢恢复。东欧和独联体的产量将下降,而中国、朝鲜和台湾的产量将继续上升。尽管出现新的炼铁工艺,但是在下一个十年中或更长的时间内,它们仍不可能对高炉产量有巨大影响。因此,烧结矿产量在未来相当长的时间内仍将维持在目前水平。 1.1.2烧结生产目的 铁矿粉烧结是一种铁矿粉造块的方法,是将细粒含铁物料与燃料、熔剂按一定比例混合,再加水润湿、混匀和制粒成为烧结料,加于烧结设备上,点火、抽风,借助燃料燃烧产生高温和一系列物理化学变化,生成部分低熔点物质,并软化熔融产生一定数量的液相,将铁矿物颗粒润湿粘结起来,冷却后,即成为具有一定强度的多孔块状产品一侥结矿。 烧结生产的目的主要是: 1.将粉状物料制成具有高温强度的块状料以适应高炉冶炼、直接还原等在流体力学方面的要求; 2.通过烧结改善铁矿石的冶金性能,使高炉冶炼指标得到改善; 3.通过烧结去除某些有害杂质,回收有益元素以达到综合利用资源和扩大炼铁矿石原料资源的目的。 1.1.3烧结反应过程 烧结反应过程是分层依次向下进行的。抽入的空气通过已烧结好的热烧结矿
烧结机节能环保新技术应用研究
烧结机节能环保新技术应用研究 发表时间:2019-06-25T09:30:53.663Z 来源:《基层建设》2019年第7期作者:吉伟[导读] 摘要:烧结是钢铁联合企业最重要的生产工艺环节之一,不仅能耗高,且产生大量高温有害烟气。 陕西龙门钢铁有限责任公司陕西韩城 715405摘要:烧结是钢铁联合企业最重要的生产工艺环节之一,不仅能耗高,且产生大量高温有害烟气。近年来烧结工艺通过不断的技术创新,电能、燃气、固体燃料等消耗不断下降,加之环冷机余热回收技术的发展,进一步降低了工序能耗,机头烟气的脱硫、脱硝以及二恶英治理技术也取得了突破性发展。文章以国内某钢厂一台烧结机改造为例,汇总分析了主要节能技术和污染治理措施,并从环保角度提出 了一些建议。 关键词:烧结;节能;环保 一、前言 随着钢铁工业的快速发展,烧结机规模也在不断扩大,2005 年 7 月国家发改委发布了《钢铁产业发展政策》,要求烧结机使用面积达到 180 m2 及以上,目前国内实际最大的烧结机已达 600 m2。设备朝着大型化发展的同时,生产技术也逐步得到提高,这不仅体现在工艺的先进性,还表现在将节能技术贯穿于整个生产过程。国家环保部于 2012 年发布了《钢铁烧结、球团工业大气污染物排放标准》(GB28662- 2012),对烧结机头烟气中多种有害物质以及机尾等设施颗粒物排放,均严格进行了浓度限值,这意味着钢铁企业必须在这几年完成对现有烧结系统的环保设施改造,新建的烧结机在设计时就需考虑选用高效的治理设施,确保达标排放。 二、工艺技术和设备方面的节能措施 1、混合制粒技术 设计采用三段式混合技术,一次混合为强力混合机,主要目的是混匀;二、三段混合均为圆筒混合机,主要目的是制粒。总混合时间超过 8 min,使造球性能得到进一步提高,明显改善了烧结料层的透气性,并且燃料在圆筒混合机的作用下,均匀地粘在混合料表面,有助于强化烧结和降低固体燃耗。 2、厚料层烧结技术 设计料层厚度 1000 mm,其中铺底料厚度控制在 20~40 mm,有利于保护台车篦条,增加烧结透气性。 烧结过程是从料层表面开始逐惭往下进行,因而沿料层高度方向就有明显的分层性,抽入烧结料层的空气经过热烧结矿层被预热,参与燃烧层的燃烧,燃烧后的废气又将下层的烧结料预热,因而料层越是向下,热量积蓄得越多,以至于达到更高的温度,这种积蓄热量的过程称为自动蓄热作用[1]。采用厚料层烧结强化了自动蓄热作用,使烧结温度随料层的提高而提高,因而烧结矿强度增加,成品率提高,返矿率下降,从而减少了固体燃耗。 3、多辊布料技术 采用圆辊给料机和九辊布料装置,将混合料均匀布在烧结机台车上,使料层均匀,降低燃料配比。通过调节布料辊的转速,可控制混合料粒度的偏析度,使烧结料层上下温度趋于均匀,提高垂直烧结速度,从而降低烧结能耗。 4、采用双斜带式节能型点火炉及保温炉点火炉炉顶设三排烧嘴,采用双斜交叉烧嘴气氛点火技术,其高温火焰带宽度适中,温度均匀,高温点火时间可与机速良好匹配,特别是保温段设有烧嘴,可以提高料面质量。 三、主要环保措施 1、无组织粉尘减排 环冷机高温段废气经热回收和除尘后返回环冷机风箱,中温段废气经热回收后与低温段烟气一并返回烧结机进行热风烧结。通过这些循环方式,以及环冷机自身漏风率的降低,可以大大减少环冷区域无组织粉尘排放量。 2、颗粒物的治理 塑烧板除尘器是以独特的波浪式塑烧板过滤芯取代传统布袋,塑烧板表面经过深度处理,孔径细小均匀,具有疏水性,特别适用于治理含水率较高的粉尘,因此选用该除尘器治理一、二次混合工序粉尘,根据实践经验,颗粒物排放浓度可控制在 10 mg/m3以下。 3、烧结机头烟气治理 烧结机头烟气是烧结混合料点火后,随台车运行,在高温烧结成型过程中产生的烟气,含烟粉尘、SO2、NOX、HCl、HF、二恶英等多种污染物。烧结机头烟气是烧结工序乃至整个全流程钢铁企业环境治理的重中之重。 (1)脱硫脱硝烧结烟气脱硫工艺多数是借鉴火电燃煤锅炉烟气脱硫工艺发展而来,种类较多,可简单分为湿法、半干法和干法,大多属于钙基法,脱硫率一般可达到70%以上。由于烟气中 NOX 与脱硫剂也会发生酸碱反应,从而具有一定的脱硝效率。宝钢某烧结机采用气喷旋冲塔石灰石 - 石膏湿法脱硫工艺,实测的脱硝率为 10%左右。 (2)二恶英减排措施二恶英产生于烧结机台车料层中,在 250~450℃的温度区间和氧化气氛条件下, 大分子碳与有机氯在铜等重金属离子的催化作用下生成。 减排方法一是从源头控制,即减少氯源,对烧结工艺进行优化,改善混合料的透气性;二是末端治理,由于二恶英绝大部分都以固态形式吸附在微细颗粒上,采用高效除尘技术可减少排放量,静电除尘器净化效率 50%左右,袋式除尘器 80%~90%;TiO2加紫外光催化分解技术,二恶英去除率可达 95%以上,同时还能分解烟气中 55%左右的 NOX,但该技术投资大,运行成本也高,尚未工业应用;三是协同净化,利用脱硫脱硝技术,可同时脱除一定量的二恶英,如采用半干法脱硫,二恶英减排 70%左右;SCR脱硝工艺可以同时催化氧化二恶英,效率达到80%;活性炭净化工艺,二恶英在解析塔内催化裂解,可减排 80%以上。 (3)烧结烟气协同净化经综合比选后,该烧结机机头烟气治理设计采用能综合处理烟粉尘、SO2、NOX 及二恶英等有害物质的协同净化工艺——活性炭吸附。 a工艺原理
粉末冶金烧结技术的研究进展.
总第 56期第 4期 贵阳金筑大学学报 2004年 12月 粉末冶金烧结技术的研究进展 林芸 ① (西安交通大学材料科学与工程学院西安 710049 摘要 :烧结作为粉末冶金最重要的一个工艺环节一直以来是人们研究的重点 , 研究进展 , 以体现烧结在粉末冶金中的重要地位 , 推进新材料制备技术的发展。 关键词 :粉末冶金烧结新技术中图分类号 :TF124文献标识码 :B 0106-0108复合化、高性能化、功能化、方向发展 , 求。 , , 小型化、自动化、精密化、省能源、无污染的材料制备方法成为人们追求的目标。现代粉末冶金技术由于其少切屑、无切屑及近净成形的工艺特点 , 在新材料的制备中发挥了越来越大的作用。它的低耗、节能、节材 , 易控制产品孔隙度 , 易实现金属 -非金属复合 , 金属 -高分子复合等特点使其成为制取各种高性能结构材料、特种功能材料和极限条件下工作材料的有效途径 [1], 受到了人们的广泛关注。 从现代复合材料技术的理论来看 , 粉末冶金复合技术从微观上改变了单一材料的性能 , 依靠扩散流动使物质发生迁移 , 同时原材料的晶体组织发生变化 , 最终“ 优育” 出高性能的复合材料。而烧结作为粉末冶金生产过程中最重要的工序 , 一直以来是人们研究的重点 , 各种促进烧结的方法不断涌现 , 对改进烧结工艺 , 提高粉末冶金制品的力学性能 , 降低物质与能源消耗 , 起了积极的作用。本文简单介绍近几年出现的几种烧结新技术 , 以期反映粉末冶金在高技术领域所起的重要作用。
1、放电等离子体烧结 (Spark Plasma Sintering , 放电等离子体烧结 (SPS 也称作等离子体活化 烧结 (Plasma Activated Sintering ,PAS 或脉冲电流热压烧结 (Pulse Current Pressure Sintering , 是自 90年代以来国外开始研究的一种快速烧结新工艺 [2]。由于它融等离子体活化、热压、电阻加热为一体 , 具有烧结时间短、温度控制准确、易自动化、烧结样品颗粒均匀、致密度高等优点 , 仅在几分钟之内就使烧结产品的相对理论密度接近 100%, 而且能抑制样品颗粒的长大 , 提高材料的各种性能 , 因而在材料处理过程中充分显示了优越性。 将瞬间、断续、高能脉冲电流通入装有粉末的模具上 , 在粉末颗粒间即可产生等离子放电 , 由于等离子体是一种高活性离子化的电导气体 , 因此 , 等离子体能迅速消除粉末颗粒表面吸附的杂质和气体 , 并加快物质高速度的扩散和迁移 , 导致粉末的净化、活化、均化等效应。第三代 SPS 设备采用的是开关直流脉冲电 源 , 在 50Hz 供电电源下 , 发生一个脉冲的时间为 312ms , 由于强脉冲电流加在粉末颗粒间 , 即可产生诸多有利于快速烧结的效应。首先 , 由于脉冲放电产生的放电冲击波以及电子、离子在电场中反方向的高速流动 , 可使粉末吸附的气体逸散 , 粉末表面的起始氧化膜在一定程度上可被击穿 , 使粉末得以净化、活化 ; 其次 , 由于脉冲是瞬间、断续、高频率发生 , ? 601?①收稿日期 :2004-6-10作者简介 :林芸 (1965- , 女 , 高级工程师 , 西安交通大学材料与工程学院在读工程硕士 , 主要研究方向 :金属基复合材料制备工艺。
聚四氟乙烯的烧结工艺技术
万方数据
万方数据
万方数据
聚四氟乙烯的烧结工艺技术 作者:汪萍, Wang Ping 作者单位:武汉市工程塑料有限公司 刊名: 工程塑料应用 英文刊名:ENGINEERING PLASTICS APPLICATION 年,卷(期):2001,29(3) 被引用次数:16次 参考文献(1条) 1.钱知勉氟塑料加工 1987 本文读者也读过(10条) 1.杜小刚.刘亚青.DU Xiao-gang.LIU Ya-qing聚四氟乙烯的加工成型方法[期刊论文]-绝缘材料2007,40(3) 2.陈旭.回素彩.CHEN Xu.HUI Su-cai聚四氟乙烯烧结成型的制备工艺[期刊论文]-塑料工业2005,33(10) 3.刘先兰聚四氟乙烯(PTFE)制品的成型工艺及质量分析[期刊论文]-现代机械2003(3) 4.徐下忠.乐启发.张良武聚四氟乙烯的加工成型技术[期刊论文]-工程塑料应用2002,30(3) 5.谭清明.Tan Qingming聚四氟乙烯复合材料烧结过程温度控制研究[期刊论文]-润滑与密封2009,34(7) 6.付海梅.王伟明.刘继红.FU Hai-rmei.WANG Wei-ming.LIU Ji-hong聚四氟乙烯成型加工新技术[期刊论文]-塑料工业2005,33(z1) 7.于清.丛培强聚四氟乙烯缠绕吹胀成型制品与橡胶复合的技术[期刊论文]-塑料科技2003(5) 8.姚荣庆.YAO Rong-qing基于工艺创新的聚四氟乙烯模压成型设备[期刊论文]-轻工机械2007,25(3) 9.蔡之桂.CAI Zhi-gui冷拉伸、热收缩聚四氟乙烯制品成型技术[期刊论文]-塑料2000,29(2) 10.伍昭平填充四氟烧结工艺改进[会议论文]-2000 引证文献(16条) 1.周晓亮.周军霞聚四氟乙烯同轴电缆推挤成型工艺及难点解析[期刊论文]-现代传输 2012(4) 2.杜小刚.刘亚青聚四氟乙烯的加工成型方法[期刊论文]-绝缘材料 2007(3) 3.胡萍.姜明.汪巍.吴愧.石亚铃聚四氟乙烯基固体润滑剂结晶度、冷却工艺及摩擦性能相关性研究[期刊论文]-润滑与密封 2006(2) 4.王科.谢苏江陶瓷填充聚四氟乙烯密封材料的制备与性能研究[期刊论文]-液压气动与密封 2010(7) 5.谭清明聚四氟乙烯复合材料烧结过程温度控制研究[期刊论文]-润滑与密封 2009(7) 6.张明强.曾黎明.向昊空心玻璃微珠/聚四氟乙烯复合材料的性能研究[期刊论文]-塑料工业 2008(9) 7.胡思前.张玉敏聚四氟乙烯绝缘子的研制与应用[期刊论文]-绝缘材料 2005(5) 8.田华.解旭东.宋希文TiO2改性PTFE复合材料力学与摩擦性能的研究[期刊论文]-内蒙古科技大学学报 2010(4) 9.廖立聚四氟乙烯加工技术、填充改性及应用进展[期刊论文]-当代化工 2010(6) 10.豆立新.龚烈航.沈健.吕振坚.龚天平.周键钊复合材料添加剂对改性PTFE的摩擦转移膜的形成和稳定作用[期刊论文]-复合材料学报 2004(2) 11.豆立新.龚烈航.沈健.吕振坚.何晓晖.龚天平纳米稀土对复合材料中超细粒子团聚现象的抑制(Ⅰ)--超细金属铜粉团聚现象及其团聚成因[期刊论文]-中国稀土学报 2003(z1) 12.马红钦.朱慧铭.谭欣.张晓军聚四氟乙烯在烧碱蒸发器防、除垢中应用的研究[期刊论文]-氯碱工业 2002(6) 13.孙小波.李建星.时连卫.王子君聚四氟乙烯/聚苯酯耐磨自润滑保持架材料的研究[期刊论文]-轴承 2011(2) 14.康玉昆化工用衬四氟管的损坏分析和处理[期刊论文]-化工设备与管道 2010(5)
Ag基材料烧结技术研究进展
Ag基材料烧结工艺研究进展 李岩 1600516 摘要:银基材料广泛应用于工业生产中,许多研究者对于银基材料的烧结工艺也进行了探索。本文总结了近二十多年来Ag基材料的烧结工艺,并对其未来的发展前景进行了展望。 关键词:Ag 烧结工艺粉末冶金 1.前言 单质银是面心立方晶体,具有良好的塑变能力和优良的电学热学性能。银的磁化系数小,是反磁性物质,银的标准电极电位比氢高,具有稳定的化学性能,同时抗腐蚀性也相对较好。所以在银基合金基体中添加高强度增强体,既可保持银合金原有良好导电、抗强磁场等性能的同时,又提高了银基合金的应变强度、抗摩擦磨损性能等,进一步满足电子电路、电器系统及和导电有关的其他领域的需要。 银粉是电气和电子工业的重要材料,是电子工业中应用最广泛的一种贵金属粉末,为厚膜、电阻、陶瓷、介质等电子浆料的基本功能材料[1,2]。近年来,纳米微粒和纳米材料已成为材料科学领域的研究的热点之一。纳米级银粉,除了具有常规银粉的一些性能外,还具有特殊的性能,可用作导电银浆,在化纤织物中添加纳米银,可改变其导电性能,并使化纤织物有很强的杀菌能力;纳米银晶体,作为稀释致冷机的热交换器,效率比传统材料高30 %,纳米银粉还是有机合成中非常好的催化剂。 目前银基粉末复合材料包括热电材料、陶瓷复合材料及电触头材料等,所利用的仍然是银所具有的良好的导电性和导热性[3]。随着科技的发展和理论基础的进步,依托先进设备,银基粉末复合材料的制备工艺越来越多,比如快速热压法,高分子网络凝胶法和放电等离子烧结技术,溶液浸泡法等。本文总结了一些Ag基材料烧结工艺的研究现状,并对其未来发展前景进行了展望。 2.工艺 早期的银基材料多采用传统的粉末冶金法,即将粉末机械混合、压制、烧结。采用这种方法,设备简单,添加元素容易控制,可以在较大范围内调整合金的成分,但是制备的材料密度较低,氧化物质点较粗大,耐电弧腐蚀性较差。为提高材料的密度与性能,几十年来新工艺、新技术不断涌现,如熔渗法、快速热压法等。 曾德麟[4]采明粉末烧结冷轧的复合工艺制得的人Ag-Cu双金属片材,其物理力学性能二接近用其它方法得到的致密双金属材料,而且具有复层晶粒细、界面结合力强的优点,塑性性质可完全满足进一步加工的要求。张万胜[5]研究了双层挤压和烧结复压及粉末的混合方式对制备的AgSnO2触头材料的性能比较,发现制造工艺和所用粉末的类型可引起材料接触电阻、熔焊力和电损蚀等性质方面发生很大变化。 刘想梅等人[6]采用溶胶-凝胶法制备了SnO2-TiO2混合纳米粉末,把制得的纳米粉末用化学镀的方法进行包覆后与纯银粉按90 :10(质量比)混合,将粉末放入模具中,对压制成型的试样采用分级保温烧结的热处理方法,制成Ag-SnO2-TiO2触头材料。研究发现溶胶-凝胶法制得的粉末比机械混合法制得的