中国催化重整技术进展

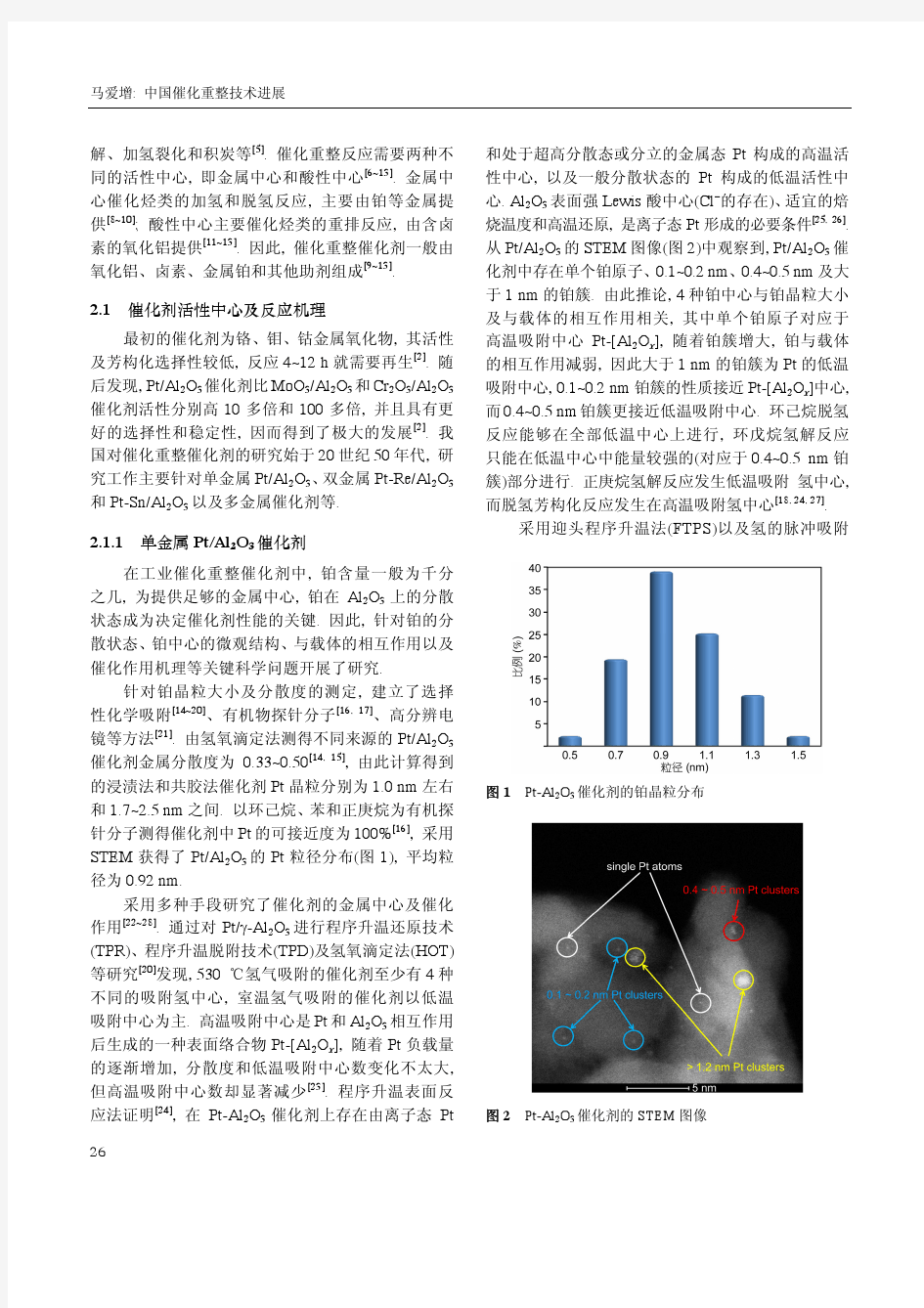
催化精馏技术在石油化工中的应用
催化精馏技术在石油化工中的应用 发表时间:2019-08-13T16:33:30.757Z 来源:《防护工程》2019年9期作者:蔡永超1 曹慧斌2 [导读] 结合实践,证明了精馏工艺改进节能的可行性。此外精馏系统节能空间极大,还需要进一步研究更加可靠可行的节能方案。 1.天津晟宸科技有限公司天津 300384; 2.重庆川维石化工程有限责任公司重庆 401254 摘要:催化精馏即基于催化剂的反应精馏技术,是目前石油化工行业应用较为普遍的科学技术。科学有效的催化精馏技术可以在催化剂的活性中心上得到反应产物及早移离,进而使得整个反应逐渐向得到目的产物慢慢靠近。通常将利用合成以及分离耦合等手段提高催化精馏塔性能的技术称为催化精馏技术。但就实际而言,该技术的实现相对复杂,对于过程中的各个反应环境也有相当高的要求。除此之外,反应所得到的热为精馏进一步利用,可以大大降低损耗,为企业节省生产成本。基于该技术的诸多优势,目前国际上已经广泛将催化精馏应用于石油化工行业中。 关键词:催化精馏技术;石油化工;应用 1催化精馏系统的基本原理 国内催化精馏技术的发展是随着MTBE生产技术的需要而发展起来的。1988年齐鲁石化公司从美国引进一套MTBE催化精馏装置后,齐鲁石化研究院开发了散装塔催化精馏技术应用于MTBE生产。丹东化工三厂(丹东明珠特种树脂公司前身),于20世纪90年代末开发了捆扎包式催化蒸馏组件并申请专利,缩小了国内催化精馏技术与国际先进水平的差距,丹东明珠特种树脂有限公司引进天津大学专利《一种具有交替流动结构的催化精馏填料》和天津大学和中建安装工程有限公司申请的专利《圆形排布的催化精馏填料》开发的CDM系列新型开窗导流式催化精馏模块使催化精馏填料的效率得到大幅度提高。 精馏工序的目的在于有效分离化工产品的相关物料组分。具体而言,所谓精馏就是采取一定的物理方法,结合物料液相组分的挥发差异性,通过一系列的物理作用,实现对物料组分的有效分离。一般来说,精馏作业都由专门的精馏塔来进行实现。 典型的精馏工艺流程如下:首先对精馏塔进行加热处理,在高温环境下,精馏塔中的物料会首先产生汽化,物料汽化上升过程中的气相和塔顶上面下降的液相物料再次产生汽化或者冷凝,具体位置可以为任意一个塔板或者是填料中,然而随着传质过程的持续进行,汽化和冷凝能够促使气相和液相组分出现一定的变化,反复多次反应后,混合液就能够被分离成为相对较纯的一个组分。精馏系统在作业中,连续的进料、回流和采出,使得精馏塔能够连续作业,最终实现对相关物料的有效分离。但是,若物料存在较为相似的挥发比时,对其分离的难度显著增加,且能耗也显著提升。 现阶段,高效导向筛板以及金属丝网规整填料等的有效开发,能够进一步提升分离效率。同时采取一定的措施来对精馏工艺予以改进,还能够在高效分离物料组分的同时,实现能耗的有效降低。 2催化精馏技术在石油化工中的应用 2.1酯化反应 催化精馏技术在得到乙酸乙酯的过程中,可以利用过量的乙酸从而确保醇得到彻底反应,得到的产物(水以及酯)则以气相混合物的方式全部由塔顶端慢慢放出,随后经过初步的冷凝操作得到水、一些液相则由特定的位置进行回流,而有机相则将其作为粗酯物,位于釜底的乙酸则可以进一步循环利用。据不完全统计,利用催化精馏技术所得到的乙酸正丁酯,通过科学有效地控制实际乙酸的转化率可以达到97%以上,乙酸的利用率达到8%左右,正丁醇的利用率为5%,乙酸正丁酯的实际回收率也得到明显提高,但整个过程对于能耗的需求则降低至原来的25%,设备成本投入以及操作复杂度等均明显降低。除此之外,该技术还可实现连串的酯化反应,极大降低了对生态环境的污染。 2.2异构化反应 目前烷基异构化是应用较为普遍且技术相对成熟的技术之一,基于科学有效的催化精馏工艺介入可以提高异构烷烃的回收情况。完全异构化技术(TIP)是目前较为典型的技术形式,该技术主要分为分子筛吸附分离以及异构化两个部分。整个技术所需要的原料包括直馏C5/C6馏分、裂解气又加氢拔头油等。基于特殊环境下,通过异构化后可以将研究法辛烷值(RON)从68逐步提升至79左右,随后使用分子筛吸附,从而将正构烷烃进行分离并进行往复异构化处理,此时RON可以得到进一步的提高,并稳定维持在88~89。目前UOP公司的该项技术相对比较成熟,目前已经推出了多个成熟技术方案,在投资成本控制方面、企业效益方面得到了较大提高。 2.3水解/水合反应 基于催化精馏从乙酸甲酯中得到甲醇以及乙酸。在得到聚乙烯醇的过程中往往会附带得到乙酸甲酯。一般每生产1t左右的聚乙烯醇大约可以同时得到1.68t左右的乙酸甲酯。固定床阳离子交换树脂催化水解技术在得到乙酸以及甲醇方面具有较好的效果,但整个实现过程相对复杂、设备投入较大且对于能源需求较高,因此迫切需要更高的技术来克服该问题。经过国内高校与企业的多年合作研究,我国福建纺织化纤集团提出了一种新型催化精馏水解新型技术,并于2000年成功地对10kt的乙酸甲酯工业附加产物进行有效处理。基于该技术催化精馏塔设计直径达200mm,塔上端填充有凝胶型阳离子交换树脂催化反应物。下端则装板波纹填料。整个塔的顶部基于全回流,水与乙酸甲酯就塔的顶部填充,得到的产物即水解液从塔的底部蒸馏釜中慢慢分离。整个水解的环境温度在55℃左右,水与乙酸甲酯的摩尔比控制为(1~6)∶1等。相较于传统技术,该新型技术水解率得提高了约60%,能耗需求降低了约30%。为了进一步提升该技术的生产效率,福建纺织化纤集团与福州大学建立了深度合作,对乙酸甲酯水解与工艺流程进行进一步的研究优化,利用萃取精馏和催化精馏耦合的方式进行测试。如若测试成功则可以进一步提升对乙酸甲酯的水解效率,甚至可以达到95%以上,并减少大量中间环节,有效提升整个生产效率。 3化工精馏高效节能技术的应用 在对化工精馏高效节能技术进行开发时,通过多次实践,最终使能源节约得以实现。在一定程度上使化工产品的质量提升了,又使生产成本降低。然而,在现实应用时,为了最大限度地节约能源,还必须对一些特殊问题进行关注。在引进化工精馏节能开发技术时,企业需要熟悉节能技术,切记盲目地进行工作。并且首先要系统培训员工,从而对工人实操时间进行适当的增加,工人对其能够熟练掌握以后,方可考虑到正式地进入到日常的化工蒸馏工作中去,这样能够最大程度地避免操作失误,降低物料损毁几率;对于化工企业而言,加热器、冷却器和换热器均是构成换热网络的基本单元,也是生产过程中用于热量传递的终于部件。为切实降低精馏作业能耗,在实际工作
催化精馏技术研究进展(DOC)
催化精馏技术应用研究进展 摘要:本文从催化精馏的发展史开始说起,进而介绍了催化精馏塔的内部件及其催化剂的装填方式。综述了国内催化精馏技术在醚化、酯化、加氢、烷基化、酯交换、水解等反应中的新应用与研究进展。指出探索出具有更高活性和选择性、更寿命的催化剂仍是催化精馏技术中的一个重要课题。 1、引言 反应精馏是化学反应与蒸馏技术相耦合的化工过程。最早的反应精馏研究始于1921年,之后,随着对反应精馏研究的不断深入和扩展,到20世纪70年代后期,反应精馏研究突破了均相体系,扩大到非均相体系,即出现了所谓的“催化精馏”工艺。催化精馏的特点是将催化剂引入精馏塔,固体催化剂在催化精馏工艺中既作为催化剂加速化学反应,又作为填料或塔内件提供传质表面。由于催化反应和精馏过程的高度耦合,反应过程中可以连续移出反应产物,使得催化精馏工艺具有高选择性,高生产能力、高收率、低耗能和低投资等优点。最早工业化的催化精馏工艺是甲基叔丁基醚的合成,该工艺由美国Chemical Research & Licensing公司于1978年开发,1981年在美国休斯敦炼厂工业化应用。1985年CR&L公司开始研究将催化精馏用于芳烃的烷基化反应,如用丙烯使苯烷基化制异丙苯。日本旭化成公司也于1984年开发成功了甲醛和甲醇催化精馏合成甲缩醛的技术,建立了工业装置。由于催化精馏技术的诸多优势,国内外学者在该领域已取得了长足发展。
2、催化精馏塔及其填料方式 2.1催化精馏塔 催化精馏塔是催化精馏过程的主要设备,常见的催化精馏塔结构如图2-1 所示。催化精馏塔从上到下分为三个部分,依次为精馏段、反应段和提馏段,原料送入到反应段后先进行反应,反应后的混合物中的轻重组分再分别进入精馏段和提馏段进行精馏和提浓。进料位置根据物料的挥发度不同可设置在反应段的上端或下端,对于原料组成不同的可以从不同位置同时进料。反应段的位置和高度以及操作压力、回流比等操作条件取决于进料的组成、组分的物性和产品的纯度要求等因素[1]。
浅谈纳米材料光催化技术研究现状
龙源期刊网 https://www.360docs.net/doc/c05583227.html, 浅谈纳米材料光催化技术研究现状 作者:林雪牛文成 来源:《神州》2012年第29期 摘要:近年来,人们对半导体纳米光学材料的研究越来越广泛。从1972年Fujishima和Honda利用TiO2电极实验发现光解水现象开始,人们逐步开始对半导体材料进行研究。本文就纳米材料光催化技术研究现状和发展前景进行了简要介绍。 关键词:纳米材料,光催化 一、纳米材料的分类 人类对材料科学的探索与研究已有上千年的历史了,但是纳米材料作为新型材料的一种,其从发展到现在也不过二三十年的时间。1984年,德国著名学者通过现代技术将一个6nm的铁晶体压制成纳米块,并详细的分析了其内部结构的改变而引起的性能差异。发现从强度和硬度上都较普通钢铁强很多倍,并且在低温下失去传导能力,随着自身晶粒尺寸的减小,材料的熔点也会随之降低。1990年,纳米科技大会在美国第一次胜利举办,《纳米技术杂志》的正 式创刊标志着纳米科技从此正式开山立派。而我国的纳米领域的研究基本与国际发展同步,目前已具备开展纳米科技的研究条件,国家重点研究机构对相关高科技的研究步伐不断加快,部分领域已经与国际先进水平持平,这些都为实现跨越式发展提供了可能。近年来,我国通过结合国家战略需求,对纳米技术在能源、环境、资源和污水处理等领域开展深入研究,纳米材料净化机、助燃剂、固硫剂和降解剂等新型产品相继研究成功。 人们对于一门新学科——纳米材料学的研究已经有一定的进展。通常纳米材料以三种方式分类:按结构分类、按化学组分分类和按应用分类: 1、按结构分,我们通常将其分为四类:第一类是具有原子簇与原子束结构的零维纳米材料;第二类是具有纤维结构的一维纳米材料;第三类是具有层状结构的二维纳米材料;第四类是晶粒尺寸至少在一个方向上在纳米量级的单位纳米材料。 2、按化学组分,通常又有两种分类方式,一种是按材料的化学性质分类,另一种是按材料的物理性质分类。按材料化学性质,我们通常将其分为纳米金属材料,纳米晶体材料,纳米陶瓷,纳米玻璃,纳米高分子和纳米复合材料;按材料物理性质,我们可将纳米材料分为纳米半导体材料,纳米磁性材料,纳米非线性光学材料,纳米铁电体材料,纳米超导材料和纳米热电材料等等。 3、按应用,我们可将其分为纳米电子材料、纳米光催化材料、纳米生物医学材料、纳米光敏材料、纳米储能材料等等。 二、纳米光催化技术的研究现状
光催化材料的研究与进展
光催化材料的研究与进展 洛阳理工学院吴华光B08010319 摘要: 光催化降解污染物是近年来发展起来的一种节能、高效的绿色环保新技术.它在去除空气中有害物质,废水中有机污染物的光催化降解,废水中重金属污染物的降解,饮用水的深度的处理,除臭,杀菌防霉等方面都有重要作用,但是作为新功能材料,它也面临着很多局限性:催化效率不高,催化剂产量不高,有些催化剂中含有有害重金属离子可能存在污染现象。但是我们也应当看到他巨大的发展潜力和市场利用价值,作为处理环境污染的一种方式,它以零二次污染,能源消耗为零,自发进行无需监控等优势必将居于污染控制的鳌头。本文介绍了一些关于光催化研究的制备与发展方向的思考,光催化正在以TiO 2 ,ZnO为主导多种非重金属离子掺杂,趋于多样化的制备方法方向发展。 关键字:光催化催化效率 正文: 光催化(Photocatalysis)是一种在催化剂存在下的光化学反应,是光化学与催化剂的有机结合,因此光和催化剂是光催化的必要条件。“光催化”定义为:通过催化剂对光的吸收而进行的催化反应(a catalytic reaction involving light absorption by a catalyst or a substrate)。氧化钛(TiO 2 )具有稳定的结构、优良的光催化性能及无毒等特点,是近年研究最多的光催化剂, 但是,TiO 2 具有大的禁带宽度,其值为3.2 eV,只能吸收波长A≤387 11111的紫外光,不能有效地利用太阳能,光催化或能量转换效率偏低,使它的应用受到限制。因此,研制新型光催化剂、提高光催化剂的催化活性仍是重要的研究课题]1[。复合掺杂不同半导体,利用不同半导体导带和价带能级的差异分离光生载流子,降低复合几率,提高量子效率,成为提高光催化材料性能的有效方法5]-[2。 与一元氧化物如TiO 2 和ZnO等光催化剂相比,复合氧化物光催化剂,如 ZnO- SnO 2TiO 2 -SnO 2 和WO3- TiO 2 等体系具有吸收波长更长和光催化效率更 高等特点因而成为研究热点. 一、常用的光催化剂的制备方法 (一)水热合成法。 热合成反应是在特制的密封容器中(能够产生一定的压力),以水溶液作为反应介质,通过对反应体系加热或接近其临界温度而产生高压,从而进行材料的合成与制备的一种有效方法。 (二)溶剂热合成法 溶剂热合成技术是在水热法的基础上,以有机溶剂代替水作为介质,采用类似水热合成的原理制备纳米材料,极大的扩展水热法的应用范围。 (三)溶胶-凝胶法
催化精馏技术研究及应用进展
催化精馏技术研究及应用进展 摘要:对催化蒸馏发展概况、原理以、工艺流程以及应用状况进行了综述,探讨了催化精馏目前存在的问题与今后的发展方向。 关键词:催化精馏;精馏;催化剂;乙酸乙酯;精馏塔;催化活性 Abstract :The development situation of the catalytic distillation,princiles,technological process and application conditions are briefly summarized . Meanwhile we also disscuss the problems exsisting temporaryly and the development derection in the future . keywords: catalytic distillation ; rectification ; catalyst ; ethyl acetate ; rectification column ; catalytic activity 催化精馏是将固体催化剂以适当形式装填于精馏塔内,使催化反应和精馏分离在同一个塔中连续进行,是借助分离与反应的耦合来强化反应与分离的一种新工艺。由于催化剂固定在精馏塔中,所以它起到了催化和促进气液热质传递的作用。 1 催化精馏发展概况 最早工业化的催化精馏工艺是甲基叔丁基醚(MTBE)的合成,该工艺由美国Chemical Research&Licensing(CR&L)公司于1978年开发,1981年在美国休斯顿炼厂工业化应用。1985年CR&L公司开始研究将催化精馏用于芳烃的烷基化反应,如用丙烯使苯烷基化制异丙苯。日本旭化成公司也于1984年开发成功了甲醛和甲醇催化精馏合成甲缩醛的技术,建立了工业装置。由于催化精馏技术的诸多优势,国内外学者在该领域做了许多研究和创新,如宋少光等己成功地将该技术应用于丙二醇乙醚的合成;高纯度异丁烯的生产过程采用催化精馏技术已获成功。 由于催化精馏技术的诸多优势,催化精馏技术已取得了长足发展。主要研究方向可以分为以下三个方面。 1.1 烷基化过程 目前,工业上另一重要的烷基化过程是异丁烷的烷基化。现有的两种流程(硫酸烷基化流程和氢氟酸烷基化流程),共同的缺点是能耗高,设备腐蚀严重,维修费用大,并且需要投资很高的冷冻设备。采用催化精馏技术基本上可以克服这些缺点。目前这一工艺已取得实验结果,且认为工业上可行,但催化剂活性和选择性尚有较大差距。 1.2 叠合过程 采用催化精馏技术可以使烯烃分子有选择地叠合。因为精密的温度控制将减
光催化材料研究进展概要
光催化材料研究进展 20 世纪以来, 人们在享受迅速发展的科技所带来的舒适和方便的同时, 也品尝着盲目和短视造成的生存环境不断恶化的苦果, 环境污染日趋严重。为了适应可持续发展的需要, 污染的控制和治理已成为一个亟待解决的问题。在各种环境污染中, 最普遍、最重要和影响最大的是化学污染。因而, 有效的控制和治理各种化学污染物是环境综合治理的重点, 开发化学污染物无害化的实用技术是环境保护的关键。目前使用的具有代表性的化学污染物处理方法主要有: 物理吸附法、化学氧化法、微生物处理法和高温焚烧法。这些方法对环境的保护和治理起重大作用, 但是这些技术不同程度的存在着或效率低, 不能彻底将污染物无害化, 产生二次污染, 或使用范围窄, 仅适合特定的污染物而不适合大规模推广应用等方面的缺陷[1]。光催化氧化技术是一门新兴的有广阔应用前景的技术, 特别适用于生化、物化等传统方法无法处理的难降解物质的处理。其中TiO2、ZnO、CdS、WO 3、Fe 2 O 3等半导体光催化技术因其可以直接利用光能而被许多研究者看好[2]。 1.1 TiO 2光催化概述 1.1.1 TiO 2的结构性质 二氧化钛是一种多晶型化合物,常见的n型半导体。由于构成原子排列方式不同,TIO2在自然界主要有三种结晶形态分布:锐钛矿型、
金红石型和板钛矿型。三种晶体结构的TIO2中,锐钛矿和金红石的工业用途较广。和锐钛矿相比,金红石的原子排列要致密得多,其相对密度、折射率以及介电常数也较大,具有很高的分散光射线的能力,同时具有很强的遮盖力和着色力,可用作重要的白色涂料。锐钛矿在可见光短波部分的反射率比金红石型高,普遍拥有良好的光催化活性,在光催化处理环境污染物方面有着极为广阔的应用前景[3]。 1.1.2TiO2光催化反应机理 半导休表面多相光催化的基本原理:用能量高于禁带宽度(Eg)的光照射半导体表面时,价带上的电子被激发,跃迁到异带上,同时在价带产生相应的空穴,这样就半导体内部生成电子(e-)—空穴(h+)随后,.电子-空穴对迁移到粒子表面不同位置、与吸附半导体表面的反应物发生相应的氧化或还原反应,同时激发态的二氧化钛重新回归到基态。与电荷分离相逆的是电子-空穴对的复合过程,这是半导体光催化剂失活的主要原因。电子-空穴对的复合将在半导体体内或表面发生,并释放热量。 1.1.3 TiO2催化剂的局限及改性途径 作为光催化剂,虽然二氧化钛具有其他催化剂难以比拟的无毒、价廉以及稳定等优点。但是目前二氧化钛光催化还存在着一些不足和局限,致使其不能再现实中得到大规模应用。究其原因,主要在于二氧化钛催化剂对太阳光的利用率不高并且其量子产率太低。锐钛矿相和金红石相二氧化铁的带隙分别为3.2eV和3.0 eV,对应的吸收阈值分别为420nm和380nm。它们所吸收的光的波长主要集中在紫外区,
光催化材料研究进展
. 光催化材料研究进展 20 世纪以来, 人们在享受迅速发展的科技所带来的舒适和方便的同时, 也品尝着盲目和短视造成的生存环境不断恶化的苦果, 环境污染日趋严重。为了适应可持续发展的需要, 污染的控制和治理已成为一个亟待解决的问题。在各种环境污染中, 最普遍、最重要和影响最大的是化学污染。因而, 有效的控制和治理各种化学污染物是环境综合治理的重点, 开发化学污染物无害化的实用技术是环境保护的关键。目前使用的具有代表性的化学污染物处理方法主要有: 物理吸附法、化学氧化法、微生物处理法和高温焚烧法。这些方法对环境的保护和治理起重大作用, 但是这些技术不同程度的存在着或效率低, 不能彻底将污染物无害化, 产生二次污染, 或使用范围窄, 仅[1]。光催化适合特定的污染物而不适合大规模推广应用等方面的缺陷氧化技术是一门新兴的有广阔应用前景的技术, 特别适用于生化、物化等传统方法无法处理的难降解物质的处理。其中TiO 、ZnO、CdS、2 WO 、Fe O 等半导体光催化技术因其可以直接利用光能而被许332[2]。多研究者看好1.1 TiO光催化概述 21.1.1 TiO的结构性质 2二氧化钛是一种多晶型化合物,常见的n型半导体。由于构成原子排列方式不同,TIO在自然界主要有三种结晶形态分布:锐钛矿型、2金红石型和板钛矿型。三种晶体结构的TIO中,锐钛矿和金红石的工2业用
途较广。和锐钛矿相比,金红石的原子排列要致密得多,其相对密资料Word . 度、折射率以及介电常数也较大,具有很高的分散光射线的能力,同时具有很强的遮盖力和着色力,可用作重要的白色涂料。锐钛矿在可见 光短波部分的反射率比金红石型高,普遍拥有良好的光催化活性,在[3]。光催化处理环境污染物方面有着极为广阔的应用前景 1.1.2TiO光催化反应机理2半导休表面多相光催化的基本原理:用 能量高于禁带宽度(Eg)的光照射半导体表面时,价带上的电子被激发,跃迁到异带上,同时在价-+)随后h(e,.)—空穴(带产生相应的空穴,这样就半导体内部生成电子电子-空穴对迁移到粒子表面不同位置、 与吸附半导体表面的反应物发生相应的氧化或还原反应,同时激发态 的二氧化钛重新回归到基态。与电荷分离相逆的是电子-空穴对的复 合过程,这是半导体光催化剂失活的主要原因。电子-空穴对的复合将在半导体体内或表面发生,并释放热量。 1.1.3 TiO催化剂的局限及改性途径2作为光催化剂,虽然二氧化钛 具有其他催化剂难以比拟的无毒、价廉以及稳定等优点。但是目前二氧化钛光催化还存在着一些不足和局限,致使其不能再现实中得到大 规模应用。究其原因,主要在于二氧化钛催化剂对太阳光的利用率不 高并且其量子产率太低。锐钛矿相和金红石相二氧化铁的带隙分别为3.2eV和3.0 eV,对应的吸收阈值分别为420nm和380nm。它们所吸 收的光的波长主要集中在紫外区,而在照射到地球表面的太阳光中,
1-费维扬-化工分离过程强化的若干新进展
化工分离过程强化的若干新进展 费维扬,罗淑娟,赵兴雷 (化学工程联合国家重点实验室(清华大学),北京100084)摘要: 介绍了化工分离过程的重要性、复杂性、多样性及面临的机遇和挑战。分析分离过程强化的新特点,并对它在过程工业可持续发展中的意义和作用进行讨论。 关键词:分离过程;过程强化;新分离技术;新特点 Recent advances on separation process intensification FEI Wei-yang, LUO Shu-juan, ZHAO Xing-lei (State Key Laboratory of Chemical Engineering(Tsinghua University), Beijing 100084, China) Abstract: The importance, diversity, complexity of chemical separation process and the challenge it faced are introduced in this paper. The new characteristics of separation process intensification are analyzed. Its significance and impact on sustainable development of process industry are also discussed Key words: separation process; process intensification; new separation technology; new characteristic 1概述 1.1 化工分离过程的重要性 化工分离过程是化学工程的1个重要分支,从原料的精制,中间产物的分离,产品的提纯和废水、废气的处理都有赖于化工分离技术[1-2]。绝大多数反应过程的原料和反应所得到的产物都是混合物,需要利用体系中各组分物性的差别或借助于分离剂使混合物得到分离提纯(见图1)。化工分离过程的应用遍及能源、资源、环保、生物、新材料等领域,无论是石油炼制、塑料化纤、湿法冶金、同位素分离,还是生物制品精制、纳米材料制备、烟道气脱硫和化肥生产等等都离不开化工分离过程。它往往是获得合格产品、充分利用资源和控制环境污染的关键步骤。 图1 化工分离过程的重要性 分离过程是耗能过程,设备数量众多,规模巨大。在1 000万t常、减压和100万t乙烯等特大型石化装置中,塔径10m以上的分离塔比比皆是。随着新产品的不断出现,对分离过程提出了越来越高的要求。例如医用的O18稳定同位素分离需要约2 000个理论级。化工分离过程通常占过程工业设备费和操作费的40%~70%[3],对过程的技术经济指标和产品的成本具有重要的影响。随着节能减排要求的提高
化工生产中精馏技术的原理及应用
化工生产中精馏技术的原理及应用 从我国化工行业发展现状分析,我国化工生产技术并不成熟,在生产中的能耗也相对较高。据有关统计显示,我国化工、石油生产业的能耗是亚太地区的1.5 倍,是欧洲地区的2.2 倍,原因是由于节能技术开发不足,特别是在精馏过程中没有应用高效节能技术。因此,为了能够进一步推动我国化工企业发展,实现绿色生产模式,我们必须要进一步对精馏技术进行研究,分析精馏技术的原理,探究系当代精馏技术在化工生产中的应用。 1、精馏技术原理 精馏技术主要是通过消耗、补偿机械功将精馏塔塔底低温区域转移到塔釜高温区,之后通过塔顶通过低温蒸汽作用塔底再沸器的热源。根据精馏技术的生产工质和工艺进行分化,能够将精馏技术分为直接塔顶式热泵精馏和间接式热泵精馏。 1.1 直接塔顶式热泵精馏系统 该系统主要是由压缩机、精馏塔、驱动器、蒸发器、辅助蒸发器组成。在实际应用中需要现成的载热工质,同时该系统内部只需要设置一个热交换器来实现热量交换即可,压缩机的系数较低,能够有效降低整个精馏塔运行中的功耗问题,并且能够提高压缩效率。再者,直接塔顶式热泵精馏系统结构比较简单,在维护工作中也更加方便。 1.2 间接式热泵精馏系统 该系统主要由压缩机、精馏塔、驱动器、蒸发器、辅助蒸发器、冷凝器、膨胀阀组成。间接式精馏系统能够将有效隔离塔中的材料。也就是直接使用标准精馏系统,从而降低系统控制和设计难度。再者,相比直接式精馏系统来说,间接式精馏系统主要是由于内部多了一个热交换器,这回在一定程度上降低运作效率。在间接式精馏系统中,内精馏工质主要是以水为主,降低了传统制冷剂的依赖性,在实际应用中有着极大的优势。由于水具备更高的化学和热稳定性。在工程设计当中,无新数据也非常丰富,即使内部出现泄漏问题也不会对周围环境造成影响。此外,间接式精馏系统的成本相对较低,再
煤的催化气化技术研究进展
气化反应有较高的催化活性。朱廷钰用氧化铁作催化剂,也取得了很好的实验效果。Yeboah等对熔融盐催化剂进行了大量研究。研究结果显示,熔融盐催化剂的催化活性明显高于单组分催化剂,具体为:三元熔融盐催化剂的催化活性高于二元催化剂的催化活性,二元的催化活性高于单组分的催化活性。笔者认为其原因是三元熔融盐催化剂熔点低,在汽化温度下为液状,而二元混合物催化剂为固态,三元催化剂更容易扩散于反应体系,且活性点更多,因此,其催化活性更好。 上述催化剂虽然表现出很好的催化活性,但都比较昂贵,且其回收和再利用比较麻烦。近来不少学者积极进行更廉价,甚至可弃催化剂的研究。福州大学的洪诗捷等用工业废液碱进行福建无烟煤水蒸气催化气化,研究结果显示,废液碱具有很强的催化活性。谢克昌和Ohtsuka等均报道了用石灰石进行煤水蒸气气化的研究结果。此外,Brown等尝试使用快速裂解柳枝稷所得的生物灰(主要含钾盐)作催化剂,也取得了很好的效果。Zhu等将煤和麦秆通过高温热解制的煤焦进行研究,发现在750℃时制的煤焦有更好的反应活性。生物质作为未来廉价煤气化催化剂的来源,具有良好的应用前景。 凌开成等研究了高灰煤在CO2中的催化气化,认为高灰煤中所含的灰分对煤的气化反应具有一定的自催化作用,故高灰煤适合于用作气化用煤,而且高灰煤中添加适当的催化剂后,其气化活性可以得到进一步的提高。他们将化肥厂炉渣用于平朔气煤,发现其具有与Na2CO3相似的催化活性,还将硫铁矿用于西曲焦煤中,发现其具有比K2CO3还要显著的催化活性,因此,凌开成等人认为它们在一定范围内是一种比较好的可弃型高灰煤气化催化剂。 2 催化机理的研究 作为一种降低汽化温度,提高气化速率,控制煤气成分的有效气化方式——煤炭催化气化,从1867年英国专利首次提出至今,国内曾就不同优质煤种的催化气化进行了广泛的研究,其中对催化气化机理的研究取得了许多重要结果和进展。赵新 煤的催化气化技术研究进展 马涛 吕彦力 周丹 郑州轻工业学院机电工程学院 450002 1 催化剂的研究 煤气化反应的基本原理表明,煤催化气化的目的在于提高C-H2O、C-CO2、C-O2和C-H2等体系的反应速率。适于催化煤气化反应的催化剂不仅要能够明显降低汽化温度,提高气化反应速率,定向调节产品组成,而且要考虑可能带来的环境污染以及生产成本的增加,并且保证其在气化操作条件下不腐蚀设备,保持催化活性。 将碱金属、碱土金属和Fe、Ni、Co等过渡金属作为煤催化气化催化剂的主要来源,研究者们已达成共识。Yeboah等研究表明,碱金属和碱土金属的弱酸盐类(如醋酸盐类和碳酸盐类)及其金属氢氧化物较强酸性盐类(如金属氯化物和硫酸盐)具有更好的催化活性,并对常见单组分碱性金属盐催化剂的催化活性进行了排序:Li2CO3>Cs2CO3>CsNO3>KNO3> K2CO3>K2SO4>N a2CO3>CaSO。张泽凯、庞克亮和张济宇等都通过实验进一步验证了碱金属的催化活性。过渡金属方面,Ohtsuka等证实镍催化剂在较低温下对煤的气化也有特别高的催化活性,Ni催化剂用于褐煤水蒸气气化,在较低温度下(500℃左右)表现出非常高的催化活性,在加压流化床气化炉中可直接生成CH4,利用氨浸提法可回收98%的Ni。但Ni作催化剂代价太高,且在800K~900K时很容易因硫中毒而失活,使用上受到了很大限制。Huttinger的研究表明,单质铁对煤加氢气化和水蒸气 法等人认为不同金属化合物对煤气化反应具有不同的催化作用机理。通常认为,芳香碳氢化合物很难与氧离子或者氢氧离子进行反应,碱金属盐的存在可能会通过与碳原子部分成键而使煤焦表面碳骨架电荷发生迁移,改变了煤焦表面碳原子的电子云分布,削弱了碳-碳键的结合强度,增强了碳-氧键的结合力,使煤焦表面具有更强反应活性点,使气化反应更易于进行。钙和铁化合物的催化作用,更多的学者则趋向于认为钙和铁直接参与了反应,而不像碱金属盐那样通过改变焦样表面的能量分布起到催化作用,它们的催化作用可以用氧化和还原循环反应来表述。谢克昌等]认为,石灰石的催化机理在于Ca2+分布于煤焦表面后增加了煤焦表面的活性位,形成活性中间体。具体过程:(1)CaO细粒均布在煤焦表面,(2)汽化剂H2O与煤焦表面及CaO表面碰撞,(3)H2O在CaO表面吸附时,OH-定位于Ca2+上,H+位于相邻的O2-,因而使表面有两个电子态不同的-OH,(4)相邻-OH压缩脱附H2O并提供一个O2-,(5)在产生CaO?O这样的不稳定活性中间体后按照氧传递机理进行反应,即 CaO?O+C→CaO+C[O] (1)C[O]→CO (2) 氧转移理论还认为,金属催化剂可能形成金属氧化物中间体,该中间体作为氧转移的载体使氧从气相转移到固相,再由固相转移到气相。例如,Wen提出K2CO3催化煤的水蒸气气化和二氧化碳反应机理,催化C-H2O反应机理为: K2CO3+2C→2K+3CO (3)2K+2nC→2CnK (4) 2CnK+2H2O→2nC+2KOH+H2 (5)2KOH+CO→K2CO3+H2 (6)催化C-CO2反应机理为:K2CO3+2C→2K+3CO (7)2K+2nC→2CnK (8) 2CnK+CO2→(2CnK)OCO→(2nC)K2O+CO (9) (2nC)K2O+CO2→(2nC)K2CO3→2nC+K2CO3 (10) 煤催化气化中金属催化剂的催化机理,公认的一点是,在煤催化气化过程中,气化反应速率与反应界面处的活性部位数和活性表面积成正比,催化剂的引入,有效地增加了反应表面的活性部位数和活性表面积,从而明显提高了气化反应速率。许多学者认为,活性表面积的增加是催化剂在固体反应物表面侵蚀开槽作用(包括闭孔的打开和新孔的开凿)的结果。 3 催化反应动力学的研究 煤的催化气化反应实质是一种多相催
催化剂制备方法大全
催 化 剂 的 制 备 方 法 与 成 型 技 术 总 结 应用化学系1202班 王宏颖 2012080201
催化剂的制备方法与成型技术 一、固体催化剂的组成: 固体催化剂主要有活性组分、助剂和载体三部分组成: 1.活性组分:主催化剂,是催化剂中产生活性的部分,没有它催化剂就不能产生催化作用。 2.助剂:本身没有活性或活性很低,少量助剂加到催化剂中,与活性组分产生作用,从而显著改善催化剂的活性和选择性等。 3.载体:载体主要对催化活性组分起机械承载作用,并增加有效催化反应表面、提供适宜的孔结构;提高催化剂的热稳定性和抗毒能力;减少催化剂用量,降低成本。 目前,国内外研究较多的催化剂载体有:SiO2,Al2O3、玻璃纤维网(布)、空心陶瓷球、有机玻璃、光导纤维、天然粘土、泡沫塑料、树脂、活性炭,Y、β、ZSM-5分子筛,SBA-15、MCM-41、LaP04等系列载体。 二、催化剂传统制备方法 1、浸渍法 (1)过量浸渍法 (2)等量浸渍法(多次浸渍以防止竞争吸附) 2、沉淀法(制氧化物或复合氧化物)(注意加料顺序:正加法或倒加法,沉淀剂 加到盐溶液为正,反之为倒加) (1)单组分沉淀法 (2)多组分共沉淀法 (3)均匀沉淀法(沉淀剂:尿素) (4)超均匀沉淀法 (NH4HCO3和NH4OH组成的缓冲溶液pH=9) (5)浸渍沉淀法 浸渍沉淀法是在浸渍法的基础上辅以均匀沉淀法发展起来的,即在浸渍液中预先配入沉淀剂母体,待浸渍单元操作完成后,加热升温使待沉淀组分沉积在载体表面上。此法,可以用来制备比浸渍法分布更加均匀的金属或金属氧化物负载型催化剂。 (6)导晶沉淀法 本法是借晶化导向剂(晶种)引导非晶型沉淀转化为晶型沉淀的快速有效方法。举例:以廉价易得的水玻璃为原料的高硅酸钠型分子筛,包括丝光沸石、Y型、X型分子筛。 3、共混合法 混合法是将一定比例的各组分配成浆料后成型干燥,再经活化处理即可。如合成气制甲醇用的催化剂就是将氧化锌和氧化铬放在一起混合均匀(适当加入铬
精馏在化工生产中的应用
精馏在化工生产中的应用 摘要 精馏是利用混合物中各组分挥发度的差异进行分离的操作单元。它被广泛地应用于工业生产中,并且在所有的分离方法中长期占据着主导地位。在化学工程中,最典型和最重要的多级分离过程是精馏过程,各种节能的、特殊的精馏分离流程得到快速的发展。本文将对精馏技术的原理、发展、应用及前景做出讨论,并浅谈几种新型的精馏工艺,旨在使精馏技术得到更广泛的发展和应用。 Abstract:Distillation is the use of the difference in the volatile components of the mixture were separated in the operation unit,it is widely used in industrial production,and all the long-term separation dominates.In chemical engineering, the most typical and most important multi-stage separation process is distillation process, a variety of energy-saving, special distillation separation processes are rapid development.This article will distillation technology principle, the development, application and prospects to make discussions and on several new distillation process,distillation technology has been designed to enable the development and wider application. 1.蒸馏与精馏的原理 液体具有挥发而成为蒸汽的能力。各种液体的挥发能力不同,因此,液体混合物汽化后所生成的蒸汽组成与原来液体的组成是有差别的。蒸馏是通过加热造成气液两项体系,利用液体混合物各组分挥发性的
添加剂对煤焦催化气化特性的影响
第46卷第11期 当 代 化 工 Vol.46,No.11 2017年11月 Contemporary Chemical Industry November,2017 收稿日期:2017-09-18 作者简介:李珏煊(1986-),女,天津人,高级经济师,硕士研究生,毕业于华北电力大学,研究方向:从事节能方向工作。E-mail:leejx12@https://www.360docs.net/doc/c05583227.html,。 添加剂对煤焦催化气化特性的影响 李珏煊,张晓毅,贺惠民 (国网冀北节能服务有限公司,北京 100045) 摘 要:在自行搭建的热重分析仪上进行恒温下煤焦的催化气化实验。通过添加剂对催化剂进行预处理,可能使得催化剂有着更好的催化效果。研究了氨水和冰乙酸两种添加剂催焦样催化气化的影响,催化剂分别为CaO 和Fe(NO 3)3。分别在780、810、850、900 ℃进行了气化实验。研究结果表明:两种添加剂对原煤焦的气化过程影响很小;对于CaO的催化气化,氨水能起到促进气化过程的作用,冰乙酸使得催化气化反应性降低;对于Fe(NO 3)3的催化气化,冰乙酸能促进催化气化过程,氨水则使得催化气化反应性降低。 关 键 词:煤;添加剂;催化剂;气化温度 中图分类号:TQ 530 文献标识码: A 文章编号: 1671-0460(2017)11-2208-05 Effect of Additives on Catalytic Gasification Characteristics of Coal Char LI Yu-xuan , ZHANG Xiao-yi , HE Hui-min (State Grid Hebei North Energy Conservation Service Corporation, Beijing 100045, China ) Abstract : Experiments on catalytic gasification of coal char under constant temperature were carried out on a thermogravimetric analyzer constructed by ourselves. The catalyst was pretreated by using additives in order to obtain better catalytic effect. Using CaO and Fe(NO 3)3 as the catalyst respectively, the effect of two additives including ammonia water and glacial acetic acid on catalytic gasification of coke was studied. The gasification experiments were carried out at 780, 810, 850 and 900 ℃.The results showed that, the two additives had little effect on the gasification process of the original char. For the catalytic gasification of CaO, ammonia water promoted the gasification process, and glacial acetic acid reduced the catalytic gasification reactivity. For the catalytic gasification of Fe (NO 3)3,glacial acetic acid promoted the catalytic gasification process, while ammonia water reduced the catalytic gasification reactivity. Key words: C oal ;Additive ;Catalyst ;Gasification temperature 近年来温室效应引起的全球变暖现象越来越明显,而CO 2的大量排放是引起温室效应的主要原因之一,通过采用煤炭的高效清洁利用技术可以有效减少CO 2的排放。煤气化技术能够有效的利用煤炭资源,减少CO 2排放,得到了大量研究人员的关注 [1-3] 。 传统的煤气化炉气化温度较高,气化产品难以净化,需要较高的生成条件和成本。[4,5] 而采用催化剂能显著降低气化反应温度,并对气化产品进行调节,加快反应速率,因此煤的催化气化技术在近年来得到了迅速发展。 CaO可由石灰石制得,在自然界分布广泛、成本较低;Fe(NO 3)3是TiO 2、钢铁等制造行业产生的废弃物主要成分之一,研究其对煤气化的催化作用有助于降低工业生成中Fe(NO 3)3的处理成本[6] 。将催化剂放入一些不具有催化作用的添加剂中,可能使催化剂表面结构产生变化,以及使催化剂中碱金属离子活性更高,使得催化效果产生一定提升。本文以锦界煤作为 实验煤样,分别以CaO和Fe(NO 3)3作为催化剂,并向催化剂中加入了氨水和冰乙酸两种添加剂,研究了添加剂对煤焦催化气化的影响。 1 实验部分 1.1 实验系统 图1为自行搭建的热重分析仪,气化实验在该实验装置上进行。该实验系统的测重最小精度为0.1mg,能够达到的最大气化温度为1 200 ℃,经过重复性实验检验,其误差不大于1%。气化实验采用CO 2作为气化剂,N 2作为保护气,其纯度均大于99.9%。实验所采用的原煤为大同原煤,粒径<70 μm,样品的工业分析和元素分析列于表1。 1.2 实验流程 催化剂按照原煤质量和金属原子质量之比进行添加,采用Fe(NO 3)3和CaO 作为催化剂,催化剂的添加方式为浸渍法,具体方法是将催化剂置于去离 万方数据
催化剂的制备方法及成型
催化剂的制备方法及成型 一催化剂的制备方法 1.1浸渍法 将含有活性组分(或连同助催化剂组分)的液态(或气态)物质浸载在固态载体表面上。此法的优点为:可使用外形与尺寸合乎要求的载体,省去催化剂成型工序;可选择合适的载体,为催化剂提供所需的宏观结构特性,包括比表面、孔半径、机械强度、导热系数等;负载组分仅仅分布在载体表面上,利用率高,用量少,成本低。广泛用于负载型催化剂的制备,尤其适用于低含量贵金属催化剂。 影响浸渍效果的因素有浸渍溶液本身的性质、载体的结构、浸渍过程的操作条件等。浸渍方法有:①超孔容浸渍法,浸渍溶液体积超过载体微孔能容纳的体积,常在弱吸附的情况下使用;②等孔容浸渍法,浸渍溶液与载体有效微孔容积相等,无多余废液,可省略过滤,便于控制负载量和连续操作;③多次浸渍法,浸渍、干燥、煅烧反复进行多次,直至负载量足够为止,适用于浸载组分的溶解度不大的情况,也可用来依次浸载若干组分,以回避组分间的竞争吸附;④流化喷洒浸渍法,浸渍溶液直接喷洒到反应器中处在流化状态的载体颗粒上,制备完毕可直接转入使用,无需专用的催化剂制备设备;⑤蒸气相浸渍法,借助浸渍化合物的挥发性,以蒸气相的形式将它负载到载体表面上,但活性组分容易流失,必须在使用过程中随时补充。 1.2沉淀法 用淀剂将可溶性的催化剂组分转化为难溶或不溶化合物,经分离、洗涤、干燥、煅烧、成型或还原等工序,制得成品催化剂。广泛用于高含量的非贵金属、金属氧化物、金属盐催化剂或催化剂载体。沉淀法有: ①共沉淀法,将催化剂所需的两个或两个以上的组分同时沉淀的一种方法。其特点是一次操作可以同时得到几个组分,而且各个组分的分布比较均匀。如果组分之间形成固体溶液,那么分散度更为理想。为了避免各个组分的分步沉淀,各金属盐的浓度、沉淀剂的浓度、介质的pH值及其他条件都须满足各个组分一起沉淀的要求。 ②均匀沉淀法,首先使待沉淀溶液与沉淀剂母体充分混合,造成一个十分均匀的体系,然后调节温度,逐渐提高pH值,或在体系中逐渐生成沉淀剂等,创造形成沉淀的条件,使沉淀缓慢地进行,以制取颗粒十分均匀而比较纯净的固体。例如,在铝盐溶液中加入尿素,混合均匀后加热升温至90~100℃,此时体系中各处的尿素同时水解,放出OH-离子: 于是氢氧化铝沉淀可在整个体系中均匀地形成。 ③超均匀沉淀法,以缓冲剂将两种反应物暂时隔开,然后迅速混合,在瞬间内使整个体系在各处同时形成一个均匀的过饱和溶液,可使沉淀颗粒大小一致,组分分布均匀。苯选择加氢的镍/氧化硅催化剂的制法是:在沉淀槽中,底部装入硅酸钠溶液,中层隔以硝酸钠缓冲剂,上层放置酸化硝酸镍,然后骤然搅拌,静置一段时间,便析出超均匀的沉淀物。 ④浸渍沉淀法,在浸渍法的基础上辅以均匀沉淀法,即在浸渍液中预先配入沉淀剂母体,待浸渍操作完成后加热升温,使待沉淀组分沉积在载体表面上。 混合法多组分催化剂在压片、挤条等成型之前,一般都要经历这一步骤。此法设备简单,操作方便,产品化学组成稳定,可用于制备高含量的多组分催化剂,尤其是混合氧化物催化剂,但此法分散度较低。 混合可在任何两相间进行,可以是液-固混合(湿式混合),也可以是固-固混合(干式混合)。混合的目的:一是促进物料间的均匀分布,提高分散度;二是产生新的物理性质(塑性),便于成型,并提高机械强度。