道岔加工工艺培训
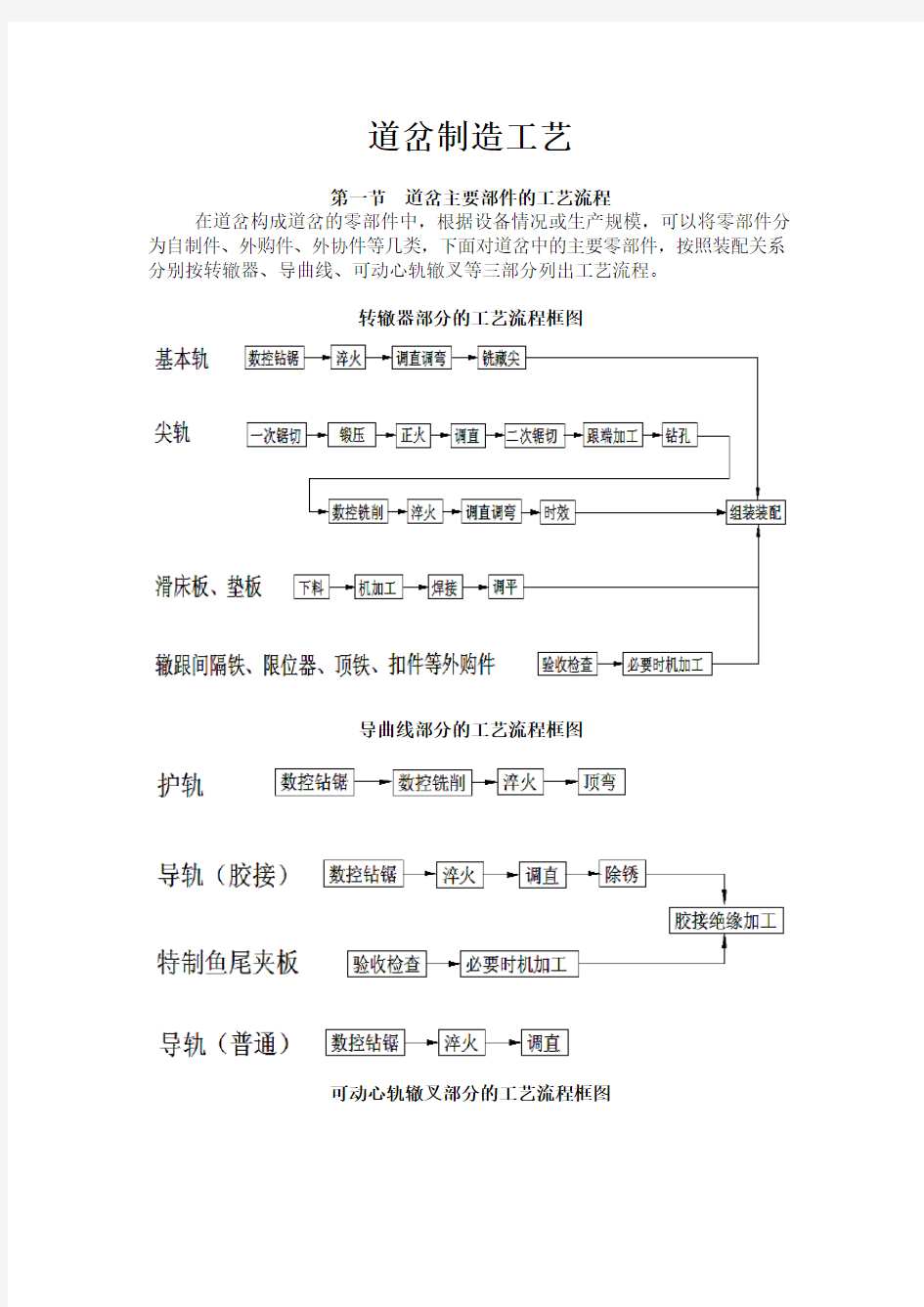
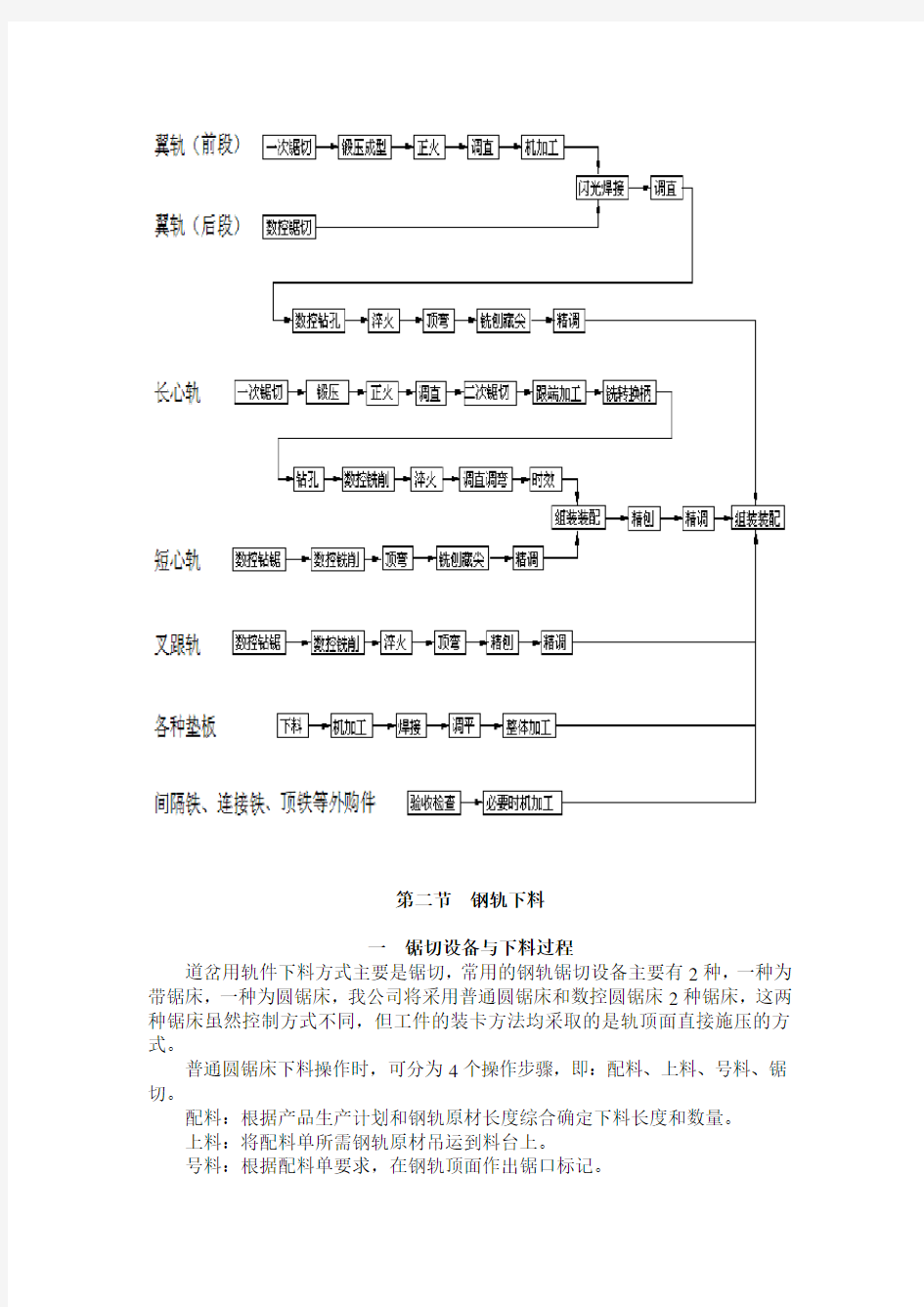
道岔制造工艺
第一节道岔主要部件的工艺流程
在道岔构成道岔的零部件中,根据设备情况或生产规模,可以将零部件分为自制件、外购件、外协件等几类,下面对道岔中的主要零部件,按照装配关系分别按转辙器、导曲线、可动心轨辙叉等三部分列出工艺流程。
转辙器部分的工艺流程框图
导曲线部分的工艺流程框图
可动心轨辙叉部分的工艺流程框图
第二节钢轨下料
一锯切设备与下料过程
道岔用轨件下料方式主要是锯切,常用的钢轨锯切设备主要有2种,一种为带锯床,一种为圆锯床,我公司将采用普通圆锯床和数控圆锯床2种锯床,这两种锯床虽然控制方式不同,但工件的装卡方法均采取的是轨顶面直接施压的方式。
普通圆锯床下料操作时,可分为4个操作步骤,即:配料、上料、号料、锯切。
配料:根据产品生产计划和钢轨原材长度综合确定下料长度和数量。
上料:将配料单所需钢轨原材吊运到料台上。
号料:根据配料单要求,在钢轨顶面作出锯口标记。
锯切:根据锯口标记锯断的过程。
数控锯床下料操作时,可分为3个操作步骤,即:配料、上料、锯切。(号料的步骤已由数控系统取代)
二操作要点
一、配料
1、统计料台上各种长度钢轨的根数,作为配料时的依据。
2、按生产计划数量和产品下料单作出配料施工单。
3、配料时,在保证计划数量的前提下,做到尽量节约原材料的原则,对加工工艺复杂,生产周期长的零件应优先配料,并力求成套供给下工序。
4、配料时要考虑锯床的锯口宽度。
二、上料
1、根据当日的生产配料计划要求,把所需钢轨吊放在下料工作台上,并将钢轨摆放平直,摆放时轨头朝上,相邻轨肢之间要留20mm的间隙。
2、目测检查钢轨表面缺陷,并清除钢轨表面的杂物和浮锈,表面上有缺陷的钢轨不能投料。
三、号料(针对普通锯床)
1、号料时一般采用用钢卷尺度量。测量钢轨长度时应把尺放在钢轨顶面上,不得扭曲,拉尺用力要均匀。对要求比较高的产品工件测量,还应施加合适的张引力(张引力20m以下卷尺为49N;20m以上卷尺为98N),张引力用弹簧秤进行测量。
2、下料时,用手虎钳和锯口卡在钢卷尺上定好所下料件的长度,定尺人和拉尺人应互相高声通报长度尺寸,确认后方可作锯口标记。(锯口标记:根据锯片厚度在两侧划出两条锯口线,在线上各打两个样冲眼,并用白铅油标出锯口的位置)
3、标记:下料时,能在钢轨端面上直接标出长度,应首先标出;无法标出的,写在钢轨顶面上,作为锯切后做标记的依据,锯切后在钢轨端面上补作标记。
四、锯切
1、锯切前,应先检查锯片或刀片磨损状况,装夹有无松动,冷却液是否通畅。
2、对于普通锯床,锯切时,要将钢轨找正,先将锯片边沿和钢轨锯口对正,并检查锯片与钢轨是否垂直,确认无误,然后将钢轨压紧。
3、对于数控锯床,锯切前,要核对输入数据是否和工件对应,各种参数是否合理。
3、锯切后,要对锯口周边进行倒棱1.5×45°处理。
三检验
1、钢轨下料后,要用卷尺对下料长度进行复检。下料标记、等项。
2、用宽座直角尺检查端面竖向及横向垂直度是否符合要求。
3、目测检查端面周边倒角以及下料标记是否符合要求。
第三节钢轨钻孔
一钻孔设备与操作过程
道岔用轨件主要是在轨腰部位打通孔,孔径一般为18mm至31mm,传统的道岔钢轨钻孔方式主要是利用摇臂钻,钻前进行号孔或制作钻模板,钢轨通常为卧放,即轨腰向上摆放。但由于道岔钢轨部件规格较多,采用号孔和制作钻模板的钻孔方式一方面不能满足生产需要,另一方面精度也得不到保证,因此,采用数控钻来进行钢轨钻孔现在越来越多的被采用。
钢轨数控钻床一般都为专机,可以适应各种轨型,能够实现钢轨的自动送料、自动夹紧、自动换装刀具、自动排屑等功能,因此操作较简单。一般分为上料、刀具准备、数据输入、程序执行、倒角、冷膨等几个过程。
上料:将所需钻孔的轨件吊运至料台。
刀具准备:将钻孔时需要的刀具装到刀库中。
数据输入:将系统所需必要数据输入系统。
程序执行:执行具体的钻控循环指令。
倒角:钻孔后的孔边1.5×45°倒角。
冷膨:(必要时)对孔进行冷挤压的操作。
二操作要点
1、联合数控锯钻床主要用来进行普通钢轨的下料和钻孔,下料和钻孔时,为流水线作业,锯断的料由锯切辊道直接进入钻孔辊道。尖轨数控钻床主要用来进行尖轨和或有高差钢轨件的钻孔,钻孔时,钢轨用吊具直接放到台位后,进行钢轨固定装卡。装卡时将钢轨前端头和定位挡靠紧。
2、根据程序所给定的刀号,在刀库相应位置安装对应规格的钻头,并掌握钻头的直径、长度等参数。
3、根据系统要求,输入工件信息、刀具信息、切削用量等数据,也可以直接调入已有的加工程序。
4、运行新的加工程序前最好先进行机床程序的试运转,以确保程序正确。
5、选择要运转的程序,将方式选择开关置于AUTO的位置,按循环起动键,循环起动灯亮,自动运转开始。
6、如果刀具带有倒角刀片,则钻孔的同时可以对孔边进行1.5×45°倒角,如果没有倒角刀片,则钻孔后还需要用电动磨头进行孔边倒角。
三检验
1、用卷尺检查孔距是否和图纸标注一致。
2、用游标卡尺检查检查孔的高度位置偏差及相临孔的孔距偏差,每个孔的孔径偏差。
2、并做好自检标识和自检记录。新产品试制的轨件应进行全数检验,其它轨件的当班首件必须进行自检,其余可进行抽检。
3、钻孔工序的检验采用游标卡尺或钢卷尺等量具。
第三节垫板钻孔
一钻孔设备与操作过程
垫板钻孔主要采用摇臂钻床,钻头一般采用普通麻花钻,板件厚度一般在10mm至40mm之间,长度在300mm至1500mm之间,孔径在22mm至33mm 之间。板件的钻孔操作主要有号孔、装卡、钻孔、倒角等几个步骤。
二操作要点
一、垫板的号孔
1、垫板的号孔一般采用号孔样板,号孔样板一般采用0.5~1.0mm厚的镀锌薄钢板制作。
2、采用号孔样板号孔时,要检查号孔样板上的标记与该产品是否相符,有无标记不清楚或样板有较大变形。
3、垫板号孔时,样板放在工件上面,其大小、方向应和工件保持一致,样板放在工件上要平稳,号孔过程中样板不得窜动。
4、采用画线号孔时,要用划针先画出垫板的基准线,然后用样冲打出约2mm直径、1mm深的样冲眼。
5、垫板号孔出现错误时,应把原样冲孔全部用手锤砸平后,方可重新号孔。
6、垫板号孔后,应按工艺要求书写标记。
二、装卡
1、垫板钻孔采用专用的胎具,用压板压紧。
2、规格相同的垫板钻孔时,可以几块放在一起同钻,但垫板边缘必须平齐,其数量在不影响钻孔质量的前提下由操作者自定。
5、采用钻模板钻孔时,钻模板放在垫板的最上层,模板边和垫板边对齐并与胎具贴靠,压板压住钻模板。对于偏孔垫板,右开时,样(模)板为正面放置;左开时,样(模)板应进行翻面。
三、钻孔
1、开始钻孔和孔将要钻通时,用力不宜过大;用机动进给钻通孔,当接近钻透时,必须停止机动改用手动进给。
2、使用接杆钻头钻深孔时,必须勤排切屑。
3、拆卸钻头、钻套、钻夹头等工具时,须用标准楔铁冲下或用钻卡扳手松开,不准用其他工具随着敲打。
四、倒角和标记
垫板取下后,要清除孔壁周围的毛刺,必要时要用电动磨头进行孔边倒棱。按图纸要求书写垫板标记,对于有左右区别的垫板,要作出区分左右的标记。
三检验
1、垫板件号孔后,应检查孔的位置偏差及相临孔的孔距偏差,并目视检查号孔标记是否清楚。
2、垫板件钻孔后,应首先检查有无漏钻、未钻通孔等现象,还应检查孔径、孔的位置及相邻孔的孔距偏差、倒棱。
2、钻孔工序的检验,首件必须自检,新产品试制时应进行全数检验,常规产品除工艺规程有特殊要求外,全部采用抽样检验
3、钻孔工序的检验采用游标卡尺、钢板尺、或钢卷尺等量具。
第四节钢轨顶弯
一、钢轨弯折的目的:
钢轨弯折是道岔加工中的最重要的工序之一,钢轨通过弯折(调直)来达到加工前所需要的折(曲、直)线型或成品所需要的折(曲、直)线型。
钢轨弯折的加工一般分为如下几类:
1.钢轨的调直;
2.钢轨的加工前的预弯;
3.加工后的精矫;
二、钢轨弯折的内容:
1、钢轨的调直:
钢轨的调直一般包括工件机加工前的调直、AT轨锻压后的调直、工件组装(入库)前的调直等。
钢轨的调直一般涉及导轨、基本轨、尖轨、护轨、长心轨、短心轨等轨件。
钢轨的调直是顶弯工序中最常见的工步,也是顶弯操作工必须达到的基本技能之一。
2、钢轨的顶弯:
钢轨的预弯一般包括机加工前的弯折及因装配(铺设)时所需要的“背弯”等。
我们平常所说的一顶、二顶都属于钢轨的顶弯范畴。其目的是通过弯折(加工)得到一条需要的折(曲)线。
注意:当我们采用刨床加工所需要的曲线而采用工装进行背弯与预弯的目的是一样的。
钢轨的“背弯”是道岔加工中保证相关技术要求的重要手段之一。例如,给尖轨顶出部分“反弯”能保证尖轨与基本轨的密贴间隙达到标准。
3、加工后的精矫:
钢轨的精矫一般包括机加工变形后的调整、装配前的调修等。
钢轨的精矫是顶弯工序中的基本的工步之一,顶弯操作工应熟练掌握。
三、钢轨顶弯常用的工具工装:
1、检测平台及相关检测辅具:
钢轨检测平台是检测钢轨的重要工装,钢轨弯折后的检测密贴、检测台板“空吊”等都在检测平台上完成。
2、顶弯样板:
顶弯样板是检测钢轨弯折支距的最基本量具之一,通过样板可以顶出钢轨所需要的各种弯折支距。(平尺,弯折样板,圆弧样板)
3、塞尺:
塞尺是检测钢轨密贴和台板“空吊”的量具。
4、钢卷尺:(20米、3米)
钢卷尺是测量支距及标记支距位置时所使用的量具。
5、钢板尺:(300mm)
检测支距时使用。
6、粉笔、石笔、细线绳、细钢丝:
辅助检测用。
7、圆撬棍:
翻钢轨及撬钢轨时使用。
8、各种工装:
各类垫块、吊卡及铁勾等。
四、各类常见顶弯加工:
1、钢轨调直:
调直是最常见的加工内容之一,主要涉及原材料的调直、淬火后钢轨的调直及直轨件的调直等。
调直一般包括钢轨长度方向上的调直及高度上的调直等。
调直一般仅依靠平尺及眼睛瞄线完成,必要时可以采用细线绳或细钢丝辅助检测。
2、钢轨的圆顺及弯折:
部分曲基本轨或曲线尖轨需要进行圆顺或弯折。弯折一般靠样板来完成。
3、顶弯时的支距选择:
钢轨顶弯时,有一个顶点和两个反作用力的支点,两支点的距离在生产中一般选择400mm左右。
五、弯折样板的计算:
弯折样板是顶弯操作工操作中最常用的工具,如何计算并选择正确的样板是顶弯操作工必须掌握的技能。
顶弯样板的计算一般有支距法和矢距法两种。支距法一般用于简单的弯折计算,矢距法一般用于圆弧的计算。
我们使用的弯折样板一般以600mm的单边长为标准长度,各样板之间的大小以其单边600mm的支距大小进行区别,如支距为20mm的样板我们就标记为20/600,支距为12.5mm的样板我们就标记为12.5/600。
1、支距法计算:
有了各种不同规格的弯折样板,我们就可以通过计算来选择正确的样板进行弯折操作。
支距法的计算一般是将钢轨弯折的支距通过相似三角形的计算反映到600mm的样板上,这样我们通过选择好的样板进行弯折操作就可以得到我们期望得到的钢轨的支距。
2、矢距法计算:
矢距法计算主要用于进行钢轨圆顺弯折时使用,其原理即通过连续的弯折顶出我们所需要的曲线,具体计算方法不需要操作工掌握。
六、顶弯的操作内容:
1、核对工件样板与产品图纸,确定无误;
2、用卷尺(盘尺)测量出各弯折点的位置,并用粉笔作出标记;
3、应先将钢轨件调平直后再进行钢轨的弯折;(应注意区分钢轨的左右及曲直)
4、用平尺或样板进行检测;
5、平台试密贴并做自检标识。
七、顶弯加工中的安全事项:
1、吊运工件时应注意防止工件突然脱落;
2、使用撬棍时应注意避免撬棍突然脱手伤人;
3、注意钢轨断裂时飞出伤人;
八、钢轨顶弯的质量要求:
1、钢轨不允许加热顶弯,仅在特殊情况时,可允许钢轨局部加热顶弯,加热的
温度不得超过500℃;
2、顶弯产生的压痕深度不得超过1mm;
3、顶弯产生裂纹的钢轨严禁使用。
九、思考题:
1、试简要叙述曲基本轨的顶弯加工过程。
2、上述基本轨弯折完成后如何进行检测?
第五节 钢轨刨切
一、 钢轨刨切的目的:
钢轨刨切的目的是通过刨切得到道岔各零部件所需要的断面或直(曲)线。
二、 钢轨刨切的内容:
钢轨刨切包括尖轨刨切、翼轨的刨切、长短心轨的刨切、叉跟尖轨的刨切、护轨的刨切等等。
三、 刨工常用的刀具及工具及安全注意事项:
刨工常用的工具有:划针、垫铁、顶墩、压板、撬棍等;常用的量具有钢板尺、卷尺、卡尺、样板等;常用的刀具有平板刀、五刨刀、四刨刀、倒圆刀。
1、 吊料时注意防止钢轨突然坠落伤人;
2、 翻料时注意撬棍伤人;
3、 脚踏板的立筋是起保护作用的;
4、 压料时的注意事项;
5、 注意防止刨屑烫伤;
6、 使用砂轮机时注意戴上防护眼镜;
四、 尖轨的刨切
尖轨刨切的原因:
1、为使尖轨尖端呈尖形,能引导车轮从基本轨过渡至尖轨,或从尖轨过渡至基本轨,并保证尖轨与基本轨密贴,尖轨应进行轨头水平刨切和轨底的水平与垂直刨切。
2、为保证尖轨尖端部分不被轧伤和不过多地承受车轮垂直荷载,还要进行尖轨的垂直刨切,使轨顶面较基本轨低一些。
尖轨的刨切工艺流程,依次为一刨、二刨、三刨、四刨和五刨。
一刨:尖轨的轨底水平刨切。
由于刨切面必须垂直,因此使用平板刨刀,刨刀刃部要平直。刨切的允许误差为2
0-+mm 。过渡圆弧采用圆弧刀进行加工。
为使刨切的直线能够通过尖轨弯折点,必须对钢轨进行顶弯。
●二刨:轨头非工作边水平刨切
刨切面要保持垂直或一定的斜度,使用平板刀,底部应有与钢轨颚部相同的坡度。二刨刨切后可采用样板及卡尺检测。
问题:加工二刨时应如何定位,如何进行加工?
●三刨:轨头工作边水平刨切。
刨切面要一定的斜度,使用平板刀,刀底部应磨出相应的圆弧。三刨刨切后可采用样板及卡尺检测。
●五刨:轨顶降低值垂直刨切
尖轨尖端应在基本轨顶面以下有足够的距离,以保证当车轮轮缘有最大垂直磨耗的最不利情况下,车轮也不会轧伤尖轨尖端。但尖轨尖端也不应低于基本轨轨顶面以下25mm,以免尖轨与基本轨偶有不密贴时,发生车轮轮缘爬上尖轨的危险。尖轨轨头宽20mm被设计为车轮转移滚动的开始断面,即
尖轨20mm断面开始与基本轨共同承受车轮的垂直荷载。尖轨顶面自轨头宽20mm至尖轨尖端为一个坡度,自轨头宽50mm至20mm为另一个坡度,对于爬坡式尖轨此坡度顺延至尖轨顶面。尖轨尖端断面和5mm断面高度偏差应为负差,目的是防止车轮撞尖,造成行车事故。
四刨:轨底爬坡垂直刨切
为使尖轨完全紧贴在基本轨轨底上,还要进行轨底的垂直刨切。在尖轨各断面上,轨底垂直刨切的边缘与基本轨轨底边缘之间有一定的空隙。尖轨轨底垂直刨切起点的位置,与轨底水平刨切的起点位置一致,即尖轨轨底的垂直刨切与水平刨切长度相等。
尖轨的轨底垂直刨切一般采用四刨胎型进行刨切。
五、尖轨刨切使用的样板:
问题:上述的样板制作有一个问题,你能发现吗?
问题:尖轨四刨时用什么样的样板检测?
六、操作内容:
1、对照图纸检查工件,确认无误后开始操作;
2、将钢轨放置于机床上,非刨切面应与胎型密贴,尖端与机床定位块靠严;
3、用石(粉)笔标出检测项点的各断面和刨切起点的位置;
4、划针找正并固定工件,固定工件的压板应均匀分布,注意压板不应超过刨切
线并尽量靠近刨切线,压板的位置应不影响断面的测量;
5、刨切并检测,应注意用样板检测刨切面宽度及斜度;
6、刨切接近结束时进刀量要少,不可吃大刀,刀刃要锋利,以保证加工表面的
光洁度及避免掉尖;
七、其它钢轨件的刨切:
1、护轨的刨切;
护轨的刨切较简单,只需注意找正并保证各断面宽度尺寸就可以了。
2、长短心轨组件的刨切;
在保证直线度及断面尺寸的前提下进行刨切,刨切时应注意控制“偏心”及防止短心轨尖端“掉尖”。
八、刨切加工常见质量问题:
1、尖轨掉尖。(掉尖在5×15mm范围内允许焊补);
2、轨顶帽型不合格;
3、刨切时赶刀造成直线度超差;
4、刨切造成的偏心等几何尺寸超差;
5、因刀斜不对或超差造成的不密贴等问题;
九、问题:
当进行一根尖轨二刨刨切时,发现20mm断面及50mm断面找正完成后,35mm 断面不在线上,试分析其原因及处理措施。
第六节钢轨数控铣知识
一、钢轨数控铣:
国外的数控铣床加工钢轨最早可追溯到上世纪八十年代,我国的则最早是九
十年代初期从日本引进的两台数控加工中心,开始了尖轨的数控铣削加工。
十余年来,国内道岔加工行业经过不断的发展,已拥有钢轨专用数控铣床十余台,加工钢轨的品种也由原来的尖轨拓展为基本轨、护轨、长短心轨等近十个品种。
我国已拥有专门用于加工道岔轨件的各类数控铣床10余台。目前我国线路上运行的160km/h以上的道岔轨件基本都是数控铣床加工出来的。
二、轨件数控铣削加工的优点:
1、加工出的工件尺寸精度更好,表面质量更高。可以完成复杂曲线的精确加工。
2、加工的效率更高。一次装夹可以完成多个工序的加工。
3、可以减少轨件的加工工序
三、轨件数控铣加工的内容:
经过多年的摸索及实验,目前可以采用数控铣加工的钢轨包括尖轨、基本轨、护轨、长、短心轨等。
四、操作时的安全注意事项:
●吊料时注意防止钢轨突然坠落伤人;
●翻料时注意撬棍伤人;
●注意防止铣屑烫伤;
●磨刀时的注意戴上防护眼镜;
五、尖轨的铣削加工:
尖轨的数控铣削加工也分为一、二、三、四、五刨进行,其中AT尖轨的二、
三、五刨铣削可在数控铣床上一次装夹完成加工。
1、刀具:
尖轨铣削加工采用的可转位式成型铣刀,刀片采用SC30或YT14硬质合金刀片,由于尖轨加工有比较大的铣削量,所以加工尖轨所用刀具的排屑槽较一般
铣刀大。尖轨加工时的切削量远大于一般的铣削加工,切削断面最大可达到50×50mm。
2、夹具:
目前国内夹具基本为电磁组合夹具或液压夹具,而国外的轨件加工已经有了更先进的电永磁夹具,可以一次装夹将一、二、三、五刨完成。
3、编程:
数控铣削铣削尖轨的编程较一般尖轨铣削加工的编程要简单的多,只需掌握一些常用的G代码和M代码就够了。
下面就是尖轨铣削加工程序中的一部分代码:
N21
M00
G55G90G00X-200.0Y-9.0
M00
Z-23.0
M3S260
G55G90G01X-100.0Y-9.Z-23.0F450.0 X215.00Y-6.0Z-14.0F450.0
X1462.0Y-0.7Z-4.0F500.0
X2226.0Y6.70Z-2.5F500.0
X2594.0Y9.10Z-1.8F500.0
X2894.0Y12.8Z-1.5F500.0
X3194.0Y15.9Z-1.3F500.0
X3561.0Y19.7Z-1.0 X3861.0Y23.8Z-1.0 X4161.0Y27.8Z-1.0 X4461.0Y32.0Z-1.0 X4696.0Y35.5Z-1.0 X4796.0Y36.5Z-1.0 X11000.0Y36.5Z0.00 X11200.0Y40.0Z5.00 G91G28Z0.0
M5
4、坐标系:
为了加工中的方便,一般以尖轨端头轨顶面中心点作为用户坐标系的坐标原点。
5、操作内容:
●对照图纸检查工件与程序,确认无误后开始操作;
●将钢轨放置于机床上,轨腰面应与胎型密贴,尖端与机床定位块靠严;
●电磁吸盘通电,将工件吸于电磁吸盘上表面上,注意观察是否有未吸牢的间
隙存在;
●用石(粉)笔标出检测项点的各断面和刨切起点的位置;
●检查刀具无误后对刀设定用户坐标系;
●执行原点操作后执行程序开始加工;
●观察及倾听铣削过程中的异常现象,以便及时采取措施;
●加工完成后检测工件各项点是否合格并记录;
六、其他钢轨件的数控铣削加工:
1、基本轨
基本轨的铣削加工较尖轨简单,加工时注意控制变形及注意工件的左右区分即可。
2、长、短心轨
长短心轨的铣削与尖轨基本类似,所不同的是其铣削的部位更多一些,且工作边铣削需留精刨余量。
七、数控铣削常见的质量问题:
1、程序、坐标及修改错误造成的质量问题;
2、程序调用错误及刀具使用错误造成的质量问题;
3、因铣削异常(刀片碎裂、突然停电)造成的质量问题;
4、原材料原因造成的质量问题;
5、因设备故障(Y轴突然置负)等原因早成的质量问题;
八、出现质量问题的解决方案:
1、改料
部分道岔中的直线尖轨可以通过继续加工改制成曲线尖轨。
2、修磨
使用砂轮机对工件表面进行修磨。
第七节钢轨胶结
一、胶结绝缘接头简介:
钢轨胶结绝缘接头是由钢轨、全断面夹板、胶层、套管、螺栓、螺母、垫圈、端板等组成的结构。目前已在我国铁路干线上大量使用,有着优良的机械性能和电绝缘性能。
二、绝缘接头的设计原则:
钢轨胶结绝缘接头的结构设计,应综合考虑多方面的因素,一般遵循以下原则:
1、尽量使胶层承受剪切力或正拉力。
2、减少胶层受到剥离力和不均匀撕扯力的作用。
3、在可能和合理的条件下,增大胶粘面积。
4、增强抗冲击、抗疲劳的能力。
5、给扣件安装留有足够的空间,防止扣件与夹板接触,保证可靠绝缘。
三、胶粘工艺流程及参数:
组装与固化是胶粘工艺中最重要的环节,热胶和常温固化胶的胶粘工艺不同。一般来说,热胶钢轨绝缘接头的工艺简单,但只能在固定工厂或基地完成,而常温固化胶钢轨绝缘接头的工艺复杂,但却能在线路上直接完成。
1、钢轨的下料
钢轨尽量采用同一根钢轨锯开胶结,否则两根钢轨胶结端钢轨高度、轨腰厚度相差不得超过0.3mm。
2、喷砂除锈:喷砂打出钢轨本色,要求无锈斑、无油污、无水气。
3、预拼装:钢轨及夹板预拼装
4、加热:拼装接头在烘箱中加热
5、绝缘螺栓紧固:两人对紧完成绝缘螺栓的紧固
6、保温固化:
7、复紧螺栓:
8、检查验收
四、胶结绝缘接头的验收:
1、外观尺寸检验:
1)胶结绝缘钢轨全长范围内不得有硬弯;
2)胶结接头处,用1m直尺检查,轨顶不超过0~0.3mm,严禁低凹。侧面水
平方向偏差不应超过±0.3mm;
3)两胶结轨端垂直错牙不应超过0.3mm,水平错牙不超过0.3mm;
4)胶结绝缘钢轨(20℃)长度允许偏差±6mm;
5)绝缘端板低于胶结轨头不得超过0.5mm,严禁凸出。
2、电绝缘性能:
干燥和潮湿两种状态均达到规定为合格
干燥状态:电阻值大于10MΩ
潮湿状态:电阻值大于1000Ω
五、型式检验:
存在下列情况之一时应进行型式检验:
1、投产时;
2、材料和生产工艺改变;
3、停产1年后再恢复生产;
4、正常生产满3年;
5、累计生产2000件;
6、生产检验结果与上次型式检验结果有较大的差异时;
每次试验时,抽取3根胶结绝缘钢轨,作电绝缘性能试验后,两根锯切进行整体剪切试验。另一根进行疲劳试验,然后再进行电绝缘性能试验。
六、整体剪切检验:
将实物试件沿轨端和距夹板两端越5cm处锯断,即分为2个试件,分别立在5000KN压力试验机上,施加轴向载荷,每次加载100KN逐次加载,测定夹板与钢轨发生错动的最大剪力。
第八节垫板剪、冲、调
一剪、冲、调常用设备与工艺过程
道岔用厚度为20mm至22mm垫板件,所使用的原材一般为宽度一定的扁钢料,因此,针对这种原材,下料时采用了特制的窄板剪板机,扁钢料由剪板机后的辊道送料,经过定长剪切后,从剪板机后前边的辊道出料,另外,对于超出窄板剪板机剪切范围的板料,通常采用斜刃剪板机,操作都比较简单。
垫板制孔方式有两种,一种是钻孔,一种是冲孔。垫板冲孔时,根据孔径、板厚、材料等选择压力机的吨位,但不同规格的孔,需要制作不同的冲孔模具。
垫板下料或焊接后,会产生不同程度的变形,在进入下道工序前,要对垫板进行平面度矫正,平面度矫正也多使用摩擦压力机,吨位一般在160吨以上。矫正时也需要使用专用的矫正胎形。
二操作要点
一、剪切
1、进料时,检查垫板的外观,有严重伤损、锈蚀或周边不平的板件禁止使用。
2、剪切前,应按钢板的厚度调整好剪切间隙,安装剪刃时应保证剪刃与剪切靠板垂直。
3、剪切定尺料时,应把标尺板定准卡牢,防止松动,并应保证标尺板与下剪刃平行。
4、剪切时,首件必须检查合格后方可开始批量剪切,剪切过程中应适时检测零件尺寸,以判断标尺板是否窜动,如有窜动,应急时调整。
5、剪切进料时,料件的前端应紧贴标尺板,推料时用力要均匀,同时料件的侧面也应紧贴剪切靠板。
6、剪切划线的工件时,上剪刃应对准剪切线,剪切线不清时应划清剪切线后方可剪切。
7、原料变形过大时,应调平后再剪切。
二、冲孔
1、冲孔时,首先检查冲头、漏盘是否完好,安装是否牢固,方向是否正确;安装时应保证冲头垂直于冲模,漏盘平稳,间隙均匀。
2、冲孔时,冲模的安装要正确,联结零件要牢固,冲孔时应适时地紧固各联结件,以防松动。
3、冲号孔的垫板时,应保持冲头处在号孔边界线的中央;冲非号孔垫板时,应保证垫板与定位板贴实。
4、单独冲两个大方孔时,应以号孔样板为基准调整冲模定位板,使定位板的方向与号孔样板的方向保持一致。
5、冲孔过程中,应适时检查冲屑的排出情况,并应及时清理。
6、冲裁间隙的确定:
1)间隙合理时,上下剪裂纹会基本重合,获得工件断面较光洁,毛刺最小;2)间隙过小时,上下剪裂纹向外错开,在冲裁件断面上会形成毛刺和迭层;3)间隙过大时,材料中拉应力增大,塑性变形阶段过早结束,裂纹向里错开,不仅光亮带小,毛刺和剪裂带均较大。
7、冲孔后,工件码放时,应保持工件的原有标记,以防混料,并将毛刺清理干
净。
三、调平
1、调平时应把工件在剪切、冲孔工序中出现的飞边、毛刺压平。
2、矫正垫板的焊接变形时应把垫板的背面朝上,垫板中间悬空放置,逐渐加大压力,并保证垫板上的焊接件不至损坏。
3、外形较大的垫板下料后要在压滚机上进行滚平。
4、外形较大、精度要求较高的垫板[如可动心轨辙叉大垫板]焊接后应进行火焰调平。
5、调平过程中应适时用平尺检测工件表面平直度。
6、垫板调平后应保持垫板的原有标记,并正面向上码放。
7、垫板件焊接前予弯时,应首先压平剪切、冲孔工序中出现的飞边毛刺,然后根据焊接变形压出反弯。焊接前予弯适当,不应出现硬弯。予弯后垫板应保持垫板的原标记,并正面向上码放。
8、补强板调平时,应把补强板倾斜适当角度,调平时如补强板内侧出现飞边时,应用砂轮修磨。
9、补强板调平时其两端头及焊缝处要用相应轨形的整形模压平,以保证补强板与钢轨有良好的接触。
10、焊接补强板调平时,严禁在焊缝处施压。
三检验
1、剪切完的工件应用白铅油做出标记,并按要求做出质量跟踪标识。
2、剪切后应用卷尺、直尺和直角尺检查工件的长宽尺寸和和四个边的垂直度;
3、垫板冲孔后用卡尺、卷尺或直尺检查孔径偏差、位置偏差以及孔边裂纹等外观状况。
4、调平工序的检验除检查工件的平面平直度外,还应检查飞边、毛刺,是否压平。
5、经火焰调平的垫板应在检验平台上用钢板尺或塞尺检测垫板的平直度。
6、产品检验合格后,要做好自检标识和自检记录,要求记录准确、清晰、完整。
第九节板件铣削
一铣削常用设备与工艺过程
道岔板件一般指垫板底板、滑床台板、扣板等零部件,该类部件加工一般为平面加工、斜面加工、直槽加工,而且批量比较大。因此,根据其加工特点,选用的铣削设备主要有卧式升降台铣床、立式升降台铣床、龙门铣床或专用铣床等。
由于铣削设备、刀具、方式装卡等方法比较多,因此板件铣削时的工艺过程主要有:工艺准备(包括:工件分析、机床选择、工件装夹方式选择、刀具选择、切削用量选择、测量方法选择等);加工准备(包括:坯件检验、夹具安装或调整、工件装夹和找正、刀具安装、铣削加工);
二操作要点
一、工艺准备(进行工艺准备时应当根据工件、现有条件进行综合考虑)
1、工件分析
根据图样中的信息和相关技术要求,判断工件平面度、粗糙度等精度要求,确定加工基准和毛坯规格,并拟订工序过程。由于对于一般要求的底板,斜面的加工基准一般选择底面,毛坯厚度不预留加工量,对于要求较高的台板和底板,加工时上下面应当互为基准,毛坯一般留较小的加工余量。
2、机床选择
根据工件毛坯规格、加工批量、加工精度、选择铣床类型及型号。如垫板底板在进行批量加工时,一般选用龙门铣床,单件加工时可选用立式铣床。而台板四面加工时,由于要求相对较高,因此,一般选用立式铣床,而台板沟槽加工时,立式和卧式铣床都可以选用。
3、工件装夹方式选择
铣削加工时,工件装卡一般采用机用台虎钳装夹、电磁吸盘吸附、螺栓压板固定等方式。对于形状较规则的工件,通过选择适当的活动钳口进行装卡;对于基准有一定面积的平面,可采用电磁吸盘固定;对于形状不规则或标准夹具难以固定的,一般采用螺栓压板的方法装夹;有时几种方式也可以结合使用。垫板底板在铣削斜面时,一般采用螺栓压板,有条件也可以采用吸盘固定。而台板铣削时,一般采用机用虎钳,也可以采用吸盘固定。
4、刀具选择
道岔板件所用材料主要为主要为碳素结构刚,加工性能良好,选用铣刀的种
是由切削部分材料来决定,高速钢刀具一般结构为整体或镶齿铣刀,而硬质合金刀具一般做成刀片形式,用于可转位铣刀;刀具的形状根据工件的待加工形状选择,平面一般选用平面铣刀,直槽、V形槽、T形槽等选用沟槽铣刀;根据铣刀尺寸确定铣刀安装方式。
5、切削用量选择
在铣削加工中,铣削用量主要是指吃刀量、铣削速度和进给速度。在实际操作中,应先选好合适的铣削速度,然后再根据铣刀直径计算出转速;选择进给量时,应依每齿进给量为依据。
铣削用量选择原则:
1)保证刀具有合理的使用寿命;
2)保证加工质量,主要是指保证加工表面的精度和表面粗糙度;
3)不超过铣床允许的动力和扭矩,不超过工艺系统(刀具、工件、夹具)的刚性,并根据具体情况有所侧重。
6、测量方法选择
工件加工后,最常见的检测项目主要有平面度、平行度、垂直度、粗糙度、斜度、深度、直径、角度、长度等测量,所用到的工具也比较多,常用的测量工
道岔培训资料
矿山窄轨道岔 道岔是矿井窄轨铁道中不可缺少的重要组成部分。它是把两条或两条以上的铁道,在平面上进行相互连接或交叉,从而引导机车车辆由一条铁道进入另一条铁道的设备。道岔的零件较多,结构复杂,养护比较困难,是铁道上部建筑的薄弱环节。 第一节道岔类型和系列 一、煤矿窄轨铁道道岔主要分为两类:一类是标准道岔,另一类是特殊道岔。 1、煤矿窄轨道岔的类型: 原煤矿工业部窄轨道岔标准设计系列有以下几种:煤矿窄轨标准道岔按结构形式主要分为三种:普通单开道岔、对称道岔和渡线道岔。[说明:非标准道岔有特殊道岔和简易道岔(如:棱形道岔、十字交叉道岔,驴尾道岔)]。按轨距划分:有600mm 轨距、762mm轨距和900mm轨距三种。道岔简易图见图1—1。 其中,单开和渡线道岔又有左向(开)和右向(向)之分;道岔的曲线半径有4、6、9、12、15、20、25、30m八种;道岔的辙岔号有2#、3#、4#、5#、6#五种;渡线间距有1.2、1.3、1.6、1.9m四种。 1)普通单开道岔:这种道岔是将一条铁道分为两条铁道的设备。道岔一侧为直股,一侧为曲股,站在尖轨前端向道岔尾部看,曲股向左的为左开道岔,曲股向右的为右开道岔。 2)对称道岔(又称双开道岔):是将铁道向左右对称分开的设备。两侧部是曲股,并对称于直股中心线。
3)渡线道岔:连接两条相邻线路的道岔。由两组相同号数的单开道岔和和一段连接组成的单渡线道岔。 2、道岔简易图 单开道岔(DK 对称道岔(DC 渡线道岔(DX 道岔简易图1—1 3、煤矿使用的特殊道岔: 1)600mm、900mm轨距双用道岔:这种道岔是在为900mm的两条钢轨之间,附设一条钢轨组成一组600mm轨距的铁道,同两用道岔相接,构成可同时行驶轨距为600mm和900mm的电机车和矿车。 2)施工简易道岔(又称驴尾道岔):这是一种简易单开道岔。由于结构简单,制作和使用方便,因此,在煤矿使用较多。 二、普通标准道岔的型号表示方法 1、标准道岔共有615、618、、624、918、924五系列。每一个系列中按辙岔号码和曲线半径又有不同型号。例如:DK615-2-4;DC622-3-9;DX624-4-12……等。 2、道岔的型号函义
油缸加工方法
液压油缸的加工方法 发布时间:2014-8-29 液压油缸的加工方法 它是一种压力光整加工,是利用金属在常温状态的冷塑性特点,利用滚压工具对工件表面施加一定的压力,使工件表层金属产生塑性流动,填入到原始残留的低凹波谷中,而达到工件表面粗糙值降低。 采用滚压方法是:拉削缸体——精镗缸体——滚压缸体,工序是3部分,但时间上对比:磨削缸体1米大概在1-2天的时间,滚压缸体1米大概在10-30分钟的时间。 油缸经过滚压后,它的表面没有锋利的微小刃口,而且与密封材料结合良好,密封效果佳,这点在液压行业特别重要。长时间的运动摩擦也不会损伤密封圈或密封件。 使用磨床或绗磨机、滚压刀滚压后,孔的表面硬度提高约30%,缸筒内表面疲劳强度提高25%。油缸使用寿命若只考虑缸筒影响,提高2~3倍,镗削滚压工艺较磨削工艺效率提高3倍左右。以上数据说明,滚压工艺是高效的,能大大提高缸筒的表面质量。 由于被滚压的表层金属塑性变形,使表层组织冷硬化和晶粒变细,形成致密的纤维状,并形成残余应力层,硬度和强度提高,从而改善了工件表面的耐磨性、耐蚀性和配合性。滚压是一种无切削的塑性加工方法。1.提高表面粗糙度,粗糙度基本能达到Ra≤0.08微米左右。 2.修正圆度,椭圆度可≤0.01mm。 3.提高表面硬度,使受力变形消除,硬度提高HV≥4° 4.加工后有残余应力层,提高疲劳强度提高30%。 5.提高配合质量,减少磨损,延长零件使用寿命,但零件的加工费用反而降低。 液压油缸的组成结构 发布时间:2014-6-6 液压油缸一般由缸筒、活塞杆、缸盖、活塞、密封件等几部分组成。 不锈钢油缸液压油缸最基本5个部件:缸筒和缸盖、活塞和活塞杆、密封装置、缓冲装置、排气装置。 其中缸筒(TUBE)由四部分组成:缸体、法兰、缸底、衬套。活塞杆(ROD)由三部分组成:1. 杆体2. 耳环3. 衬套以上各部分组成;缸体内部由活塞分成两个部分,分别大腔和小腔;大腔指活塞杆完全伸出后,缸体内腔;小腔指起重机轻型起重机空气过滤器旋转门活塞杆完全伸入后,缸体与杆体内腔;由于液压油的黏性比较高,压缩比很小,当缸底油口进油后,活塞将被推动使缸盖油口出油,活塞带动活塞杆做伸出或缩回运动,反之亦然。
道岔培训资料
道岔培训资料 集团标准化工作小组 [Q8QX9QT-X8QQB8Q8-NQ8QJ8-M8QMN]
矿山窄轨道岔 道岔是矿井窄轨铁道中不可缺少的重要组成部分。它是把两条或两条以上的铁道,在平面上进行相互连接或交叉,从而引导机车车辆由一条铁道进入另一条铁道的设备。道岔的零件较多,结构复杂,养护比较困难,是铁道上部建筑的薄弱环节。 第一节道岔类型和系列 一、煤矿窄轨铁道道岔主要分为两类:一类是标准道岔,另一类是特殊道岔。 1、煤矿窄轨道岔的类型: 原煤矿工业部窄轨道岔标准设计系列有以下几种:煤矿窄轨标准道岔按结构形式主要分为三种:普通单开道岔、对称道岔和渡线道岔。[说明:非标准道岔有特殊道岔和简易道岔(如:棱形道岔、十字交叉道岔,驴尾道岔)]。按轨距划分:有600mm轨距、762mm轨距和900mm轨距三种。道岔简易图见图1—1。 其中,单开和渡线道岔又有左向(开)和右向(向)之分;道岔的曲线半径有4、6、9、12、15、20、25、30m八种;道岔的辙岔号有2#、3#、4#、5#、6#五种;渡线间距有、、、1.9m四种。 1)普通单开道岔:这种道岔是将一条铁道分为两条铁道的设备。道岔一侧为直股,一侧为曲股,站在尖轨前端向道岔尾部看,曲股向左的为左开道岔,曲股向右的为右开道岔。 2)对称道岔(又称双开道岔):是将铁道向左右对称分开的设备。两侧部是曲股,并对称于直股中心线。 3)渡线道岔:连接两条相邻线路的道岔。由两组相同号数的单开道岔和和一段连接组成的单渡线道岔。 2、道岔简易图 单开道岔(DK 对称道岔(DC 渡线道岔(DX 道岔简易图1—1 3、煤矿使用的特殊道岔: 1)600mm、900mm轨距双用道岔:这种道岔是在为900mm的两条钢轨之间,附设一条钢轨组成一组600mm轨距的铁道,同两用道岔相接,构成可同时行驶轨距为600mm和900mm的电机车和矿车。 2)施工简易道岔(又称驴尾道岔):这是一种简易单开道岔。由于结构简单,制作和使用方便,因此,在煤矿使用较多。 二、普通标准道岔的型号表示方法 1、标准道岔共有615、618、、624、918、924五系列。每一个系列中按辙岔号码和曲线半径又有不同型号。例如:DK615-2-4;DC622-3-9;DX624-4-12……等。 2、道岔的型号函义 1)DK表示单开道岔,DC表示对称道岔,DX表示渡线道岔。 2)615、618、、624、918、924系列中的“6”和“9”分别表示600mm和900mm 轨距;“15”“18”“24”分别表示轨型。
油缸缸筒加工工艺
攀钢机械制造公司油缸加工项目组 油缸缸筒加工工艺 编写:牟斌 时间:2003年5月
油缸缸筒加工工艺 一、缸筒 1、下料:下料尺寸按工艺图确定。 2、在普通车床上(卧式)上将无缝钢管以外圆找正,一端适当位置处加工中心架口,当缸筒长度尺寸大于1500mm时加工两中心架口,架口位宽应超过80mm,深度车圆为止。 3、上中心架,以中心架位为基准准找正,平中心架侧端面,车出与深孔镗卡盘锥盘和授油器锥盘锥度相符的外锥面,粗造度3.2um。锥度15°。如下图所示: 图中:ΦD为缸筒外径;ΦD1为深孔镗锥盘小端尺寸; ΦD3为缸筒内径;L为缸筒长度 (注:此图为不焊接法兰、耳轴缸筒加工图,如需焊接应 按工艺图加工)
最后平工件卡盘侧端面。如下图所示: 要求:两锥面、中心架位必须保证同轴度。 4、粗镗:更换深孔镗粗镗导向套,将工件装上深孔镗,用对刀规调整粗镗刀尖尺寸,用千分尺调整导向块、支承键尺寸,并核对镗头导向块,支承键是否分布在相应同一圆周上,否则将其加分别加工至同一圆周:镗刀尺寸调整为ΦD ;导向块ΦD 03.001 .0--;支承键调整至比粗镗导向套内径大0.02~0.03mm 。用对刀规检查镗刀、导向块,并确定刀尖应在导向块轴向位置前面2mm 左右(注:ΦD 为导向套公称尺寸)。粗镗走刀量S =0.4~0.5m/r ,转速V =40m/min ,切削液量调整至最大。 5、半精镗:更换深孔镗半精镗导向套,用千分尺调整导向块、支承键尺寸,并核对镗头导向块,支承键是否分布在相应同一圆周上,否则将其分别加工至同一圆周:导向块、支承键尺寸,镗刀尺寸调整为ΦD ;导向块ΦD 03.001 .0--;支承键调整至比半精镗导向套内径大0.02~0.03mm 。用对刀规检查镗刀、导向块,并确定刀尖应在导向块轴向位置前面2mm 左右(注:ΦD 为导向套公称尺寸)。半精镗走刀量S =0.4~0.5m/r ,转速V =40m/min ,切削液量调整至最大。半精镗内孔留余量0.4~0.5mm ,并保证内孔直线度及同轴度度≤0.03mm ,粗造度为6.3um ,为浮动镗提供条件。 6、浮动镗:冲洗干净内孔污渍,更换精镗导向镗,用千分尺调整刀
五金产品加工知识培训
五金产品加工知识培训(针对我司常用)1.五金产品常用材料: 纯铜、青铜/黄铜、硬铝、防锈铝、纯铝、奥氏体不锈钢、马氏体不锈钢、覆铝锌板、电镀锌板、热度锌板、冷轧钢板、热轧钢板。 压铸材料的价格从高至低的排列顺序为:镁合金、铝合金、锌合金。 材料种类图纸标注 牌号 实际可 使用的 材料牌 号 材料状 态 生 产 厂 商 抗拉 强度 Mpa 屈服 强度 Mpa 延伸 率% 硬度HV 拉 延 性 ( 杯 突 mm) 可 焊 性 材 料 耐 蚀 性 与涂 结合 冷轧钢 板Fe,08 Fe,20 CRS SPCC 退火+平 整,麻面 表面 不 限 300-37 200-2 70 39-50 88-106(HRB=45 -60) ≥9 .3 A C 热轧钢 板SPHC 08 SPHC 酸洗表 面 不 限 275-41 ≥25 HB≤108 ≥1 1.0 A C 耐指纹 电镀锌钢板Fe,DX2 SECC-N2 MSE-CC- U 耐指纹 表面 宝 钢、 日 本 300-37 200-2 70 39-50 88-106 (HRB=45-60) ≥9 .3 A B 电镀锌 钢板批 料替代材料SECC-P 不 限 替代材料,价格便宜,但抗腐蚀能力差,只适用于小面积喷涂保护零件, 工程师选材时慎用. 热浸锌 板SGCC St01Z SGCC 小锌花 或无锌 花表面 不 限 360 240 37 104(HRB=58) A B ? 镀锡钢 板(马口铁)SPTE SPTE2.8 2.8T-2. 5 光亮表 面 日 本 300-37 200-2 70 39-50 90-106 (HR30T=48-56) ≥8 .5 A B C
铁路道岔安装、作业培训教材(最新)
道岔安装培训技术资料 第一部分:ZD6型转换装置 一、ZD6型转辙机(如下图): 二、结构 电动机:为转辙机提供动力,采用直流串激电动机 减速器:降低转速以换取足够的转矩,并完成传动。由第一级齿轮、第二级行星传动式减速器组成。 摩擦联结器: 用弹簧和摩擦制动板,组成输出轴与主轴之间的摩擦连接,以防止尖轨受阻时损坏机件。(如下图):
主轴:由输出轴通过起动片带动旋转,主轴上安装锁闭齿轮、由锁闭齿轮和齿条块相互动作,将转动运动变为平动,通过动作杆带动尖轨运动,并完成锁闭作用。 动作杆:与齿条块之间用挤切削相连,正常动作时,齿条块带动动作杆,挤岔时,挤切削折断,动作杆与齿条块分离,避免机件损坏。 表示杆:由前后表示杆以及两个检查块组成。随着尖轨移动,只有当尖轨密贴且锁闭后,自动开闭器的检查柱才能落入表示杆的缺口之中,接通表示电路。挤岔时,表示杆被推动,顶起检查柱,从而断开表示电路。 移位接触器:监督挤切削的受损状态,道岔被挤或挤切削折断时,断开道岔表示电路。 自动开闭器: 由动静接点、速动爪、检查柱组成,用来表示道岔尖轨所在的位置。 安全接点(遮断开关)用来保证维修安全。 外壳:固定各部件,防止内部器件受机械损坏和雨水、尘土等的侵入。 三、ZD6型转辙机各主要部件及作用 1、、电动机 要求具有足够的功率,以获得必要的转矩和转速。电动机要有较大的起动转矩,以克服尖轨与滑床板之间的静摩擦。同时,道岔需要定反位转换,要求电动机能够逆转。通过改变定子绕组中或电枢(转子)中的电流的方向来实现。两个定子绕组通过公共端子分别与转子的绕组串联。额定电压160v;额定电流2.0A,摩擦电流2.3—2.9A;额定转速2400r/m;额定转矩0.8826N,单定子工作电阻(2.85±0.14)×2Ω,刷间总电阻4.9±0.245Ω。(如下图):
五金产品知识培训
什么是五金家具五金家具指的是以金属为主要构成材料的家具,也有叫做金属玻璃家具、钢木家具等名称的,只是称乎不一样。五金家具所用到的材料(材质) 1.A3钢材 2.铝型材3.不锈钢 4.玻璃 5.木材 6.其他 1、A3钢材 A3是钢材的牌号,老国标中的叫法,新的国标中叫Q235。(材质) 比如有圆管、方管、扁方管、蛋管、榄核管、半圆管、圆钢、方钢、钢板、异形管等等(种类) A3钢材是金属家具中最主要的一种材料。它的优点是强度高,结实耐用,工艺性好,容易加工成各种需要的形状。在家具产品中的用途广泛,可以作台架、几架、椅架,沙发架等等 A3钢材的表面处理方式主要有喷塑(塑粉)、油漆、镀铬(电镀)等。铝型材 6063―一种通用型铝材(并非纯铝) 重量轻,表面处理多样且时尚,抗氧化性能好,表面效果更持久。一般被用于家具产品的脚、框架、轨道、小配件等等铝型材的表面处理方式主要有氧化、拉丝、喷砂氧化、拉丝氧化、电泳、拉丝封闭等。不锈钢简单来说,可以分为高铬不锈钢和低铬不锈钢,比如201和304。(成分及作用) 其中,低铬不锈钢需要作额外的保养和防锈处理。也分为圆管、方管、扁方管、蛋管、榄核管、半圆管、异形管等不锈钢并不是永不生锈的,只是抗氧化性能相比其他钢材而言,更加优秀。而不同种类的不锈钢,抗氧化的能力也不尽相同。比方说:201和304。在家具中,主要被用作脚、框架、饰面、扶手等可视部分不锈钢的表面处理方式主要有拉丝、抛光等。不锈钢德胜的优势: 目前家具中使用的不锈钢主要有201、202、301、304等等种类。就如前面讲到的,304在这里面是最好的一种,但304又分国标和非标的两种,国标的又更好一些。一些小厂为图节省成本,都是采用的202材料,少数采用304的也只是采用了非标的材料。使用一段时间后,与大厂生产的国标304材料就会有明显的差别。玻璃家具上用得到的玻璃可分为普通玻璃、钢化玻璃、夹胶玻璃、有机玻璃等。按表面处理又可分为磨砂玻璃、喷油玻璃、丝印玻璃、有色玻璃、彩色夹胶玻璃等。它在金属家具中的重要性越来越高。可以说,金属家具被越来越多的人所接受,与玻璃的作用是分不开的。它主要用于桌面、茶几面、柜子、衣镜等等玻璃产地:秦皇岛,洛阳,上海,蛇口,四大产地。蛇口最好,上海中等,秦皇岛,洛阳次之。检测:a、侧面看无波纹:蛇口,上海 b、
机械加工培训计划
普通机加工培训方案 一,初级钳工培训计划 初级钳工培训计划 1. 培训目标 1.1 总体目标培养具备以下条件的人员:具有机械制图基本知识,具有简单加工工艺编写能 力,掌握钳工基础知识和机修钳工常用设备的操作技能,能运用机修钳工基本技能独立完成常用设备机械部分的安装、调试、维护保养和检验工作。 1.2 理论知识培训目标依据《机修钳工国家职业标准》中对初级机修钳工的理论知识要求, 通过培训,使培训对象掌握职业道德基本知识,机械制图基本知识,公差与配合、常用金属材料与热处理知识;掌握机修钳工基础知识和机修钳工常用设备的操作;掌握常用机械设备的搬迁、安装、调试、维护保养和检验的方法。 1.3 操作技能培训目标依据《机修钳工国家职业标准》对初级机修钳工的操作技能要求,通过 培训,使培训对象掌握钳工的基本操作技能,能够正确使用钳工常用工具、量具和夹具,进行一般的钳加工,能够运用机修钳工基本技能独立完成常用设备的搬迁、安装、调试、维护保养和检验工作,熟悉部分典型机械装置的修理。 二,普通车工培训计划 (一)、培训要求: 通过培训,使学员基本掌握初级车工应具备的应知内容,包括: 1、车床的基本结构、基本操作与保养、安全 2、切削基本知识 3、外圆、台阶、断面的车削 4、切断与车槽 5、孔加工
6车锥度 7、螺蚊加工 8、滚花 9、典型工件的加工 (二)、培训进度与内容和学时 三,初级冷作钣金工培训计划 冷作钣金工 ?职业定义:对金属板材进行冷、热态成形和铆接加工的人员。 初级冷作钣金工培训计划 1?培训目标 1.1总体目标 培养具备以下条件的人员:能够正确掌握冷作钣金基础知识和基本操作技能,能运用冷作钣金工的基本技能独立完成简单构件制作。 1.2 理论知识培训目标 依据《冷作钣金工国家职业标准》中对初级冷作钣金工的理论知识要求,通过培训,使培训 对象掌握职业道德及相关法律法规知识,掌握机械制图基本知识、公差与配合、常用金属材料及热处理知识。掌握冷作钣金工基础知识,能读懂一般零件图和简单装配图,熟悉冷作钣金工常用
油缸缸筒加工工艺标准
* 攀钢机械制造公司油缸加工项目组 油缸缸筒加工工艺 编写: 时间:2003年5月
油缸缸筒加工工艺 一、缸筒 1、下料:下料尺寸按工艺图确定。 2、在普通车床上(卧式)上将无缝钢管以外圆找正,一端适当位置处加工中心架口,当缸筒长度尺寸大于1500mm时加工两中心架口,架口位宽应超过80mm,深度车圆为止。 3、上中心架,以中心架位为基准准找正,平中心架侧端面,车出与 深孔镗卡盘锥盘和授油器锥盘锥度相符的外锥面,粗造度 3.2u m。锥度15°。如下图所示: 图中:①D为缸筒外径;①D1为深孔镗锥盘小端尺寸; ①D3为缸筒内径;L为缸筒长度 (注:此图为不焊接法兰、耳轴缸筒加工图,如需焊接应
按工艺图加工) 最后平工件卡盘侧端面。如下图所示: 要求:两锥面、中心架位必须保证同轴度。 4、粗镗:更换深孔镗粗镗导向套,将工件装上深孔镗,用对刀规调整粗镗刀尖尺寸,用千分尺调整导向块、支承键尺寸,并核对镗头导向块,支承键是否分布在相应同一圆周上,否则将其加分别加工至同 0.01 一圆周:镗刀尺寸调整为①D ;导向块①D 003 ;支承键调整至比粗 镗导向套内径大0.02~0.03mm。用对刀规检查镗刀、导向块,并确定刀尖应在导向块轴向位置前面2mm左右(注:①D为导向套公称尺寸)。粗镗走刀量S= 0.4~0.5m/r,转速V = 40m/min,切削液量调整至最大。 5、半精镗:更换深孔镗半精镗导向套,用千分尺调整导向块、支承键尺寸,并核对镗头导向块,支承键是否分布在相应同一圆周上,否则将其分别加工至同一圆周:导向块、支承键尺寸,镗刀尺寸调整为 0.01 ①D ;导向块①D 0.03;支承键调整至比半精镗导向套内径大 0.02~0.03mm。用对刀规检查镗刀、导向块,并确定刀尖应在导向块轴向位置前面2mm左右(注:①D为导向套公称尺寸)。半精镗走刀量S= 0.4~0.5m/r,转速V = 40m/min,切削液量调整至最大。半精镗内孔留余量0.4~0.5mm,并保证内孔直线度及同轴度度w 0.03mm,粗造度为6.3um,为浮动镗提供条件。 6、浮动镗:冲洗干净内孔污渍,更换精镗导向镗,用千分尺调整刀
油缸装配工艺规范
xxxxx有限公司 工艺规范 编号:xxxxxx 名称:液压油缸装配工艺规范(通用) 受控状态: 有效性: 持有部门: 日期:
一、准备 1、配套:按装配图上的“零件明细表”领取合格的零件成品、密封件标件等。未经检查合格的零配件不得进入装配。 2、清理: 检查并最终清除所有机加工零件、标准件上的飞边、毛刺、锈迹。清除时,零件不能有损伤,同时复查各零件外观是否合格; 3、清洁: A:用压缩空气吹净工作台及待装配零件各部位的异物,并用毛巾擦拭干净。要注意清除缸筒、沟槽、以及油口的铁屑、焊渣等细小异物; B:清洗后要用压缩空气将零件吹干; D:所有待装配的零件清理、清洁后都要放置在装配点的干净工位器具上; E:清理、清洗所有装配工具、工装。 4、零件检验 装配钳工做好自检工作,再向检验员提请检查。装配检验员必须按上述要求进行巡检和完工检查。 二、组装 1、组装活塞杆: A:活塞杆小端为卡键式:将活塞杆小端装上O型圈,然后装配活塞组件,再按图纸要求装轴用卡键、卡键帽、轴用挡圈及其它零件。整体焊接式活塞 杆,须先装导向套组件,再装活塞组件。 B:活塞杆小端为螺纹式:将活塞组件旋入活塞杆上拧紧到位,注意不能损伤O 形圈,然后装锁紧螺母压紧(装配前清除紧定螺钉孔的油脂),装钢球、紧定螺钉(装配前涂紧固胶)。整体焊接式活塞杆,须先装导向套组件,再装活塞组件。C:活塞杆杆端为叉头时,最后装叉头。 2、缸体组装: A:缸体为卡键式:将已组装好的活塞杆装入缸体,再按图纸要求装导向套、孔用卡键、挡环、轴用挡圈及其它零件(注意装配导向套时若O型圈过油口,必须用堵塞堵住油口以免损坏密封件)。 B:缸体为法兰式:将已组装好的活塞杆装入缸体,再按图纸要求装导向套、弹
金产品加工知识培训
五金产品加工知识培训(针对我司常用) 1.五金产品常用材料: 纯铜、青铜/黄铜、硬铝、防锈铝、纯铝、奥氏体不锈钢、马氏体不锈钢、覆铝锌板、电镀锌板、热度锌板、冷轧钢板、热轧钢板。
备注:不锈钢(SUS):韧性好,难折断一般不吃锡但表面镀镍后能吃锡而表面直接镀镍较困难,一般覆盖一层铜后再镀镍。表面光泽度不佳但可分雾面与亮面(不可能象镀镍一样光亮),不锈钢按同型号硬度由大到小可分SUS301 SUS302 SUS 303 SUS304, SUS304具有一定导磁性但比较弱。其余不锈钢一般不导磁; 耐指纹电镀锌钢板:均匀的灰色 热镀铝锌板:小晶花 热镀铝锌板:无晶花 热浸镀锌板:大晶花 左至右的外观为:拉丝、喷砂、光亮表面 喷涂桔纹-所做的百格附着力试验 2.加工工艺流程及注意要点: . 冲压、激光下料、数冲下料、车床下料、还是铸,第一个都防止用料错误; 冲压加工:一般都为批量性加工,下料、冲孔、拉伸、弯形、压死边;针对模具的不同,问题点也不不同,依次类推常见的有: 下料少料、切边毛刺过大;冲孔:多或少孔冲孔未冲通毛刺过大; 拉伸:变形; 弯形:方向、尺寸、角度大小、内外表面压印变形严重擦伤、标准试配;如下图; 压死边:变形、压印、尺寸超差; 激光下料、数冲下料: 下料少料、切边毛刺过大;冲孔:多或少孔冲孔未冲通毛刺过大、工艺缺口大小; 钳工: 沉孔:沉孔的方向、大小、角度、不加大底孔和翻包(㎜之内),钻头使用的种类(挤压、螺旋、切削)和主轴的转速。 攻丝:丝锥使用的种类(挤压、螺旋、切削)和主轴的转速及互配的底孔在的大小,螺纹孔要保证通止(M6以上的要用标准螺钉试配),有效深度、扭力符合要求。 压铆:使用的非标准件是正确、压铆方向、压铆后的性能(螺纹孔要保证通止(M6以上的要用准标螺钉
油缸制造工艺
油缸制造工艺 Document number:NOCG-YUNOO-BUYTT-UU986-1986UT
13、液压油缸和系统制造工艺说明 、液压缸缸体加工工艺 1、目的:控制操作过程,确保加工质量符合图纸要求 2、制造过程中执行的标准: JB4730压力容器无损检测 JB/磨料种类,粒度选择 GB1031表面粗糙度磨参数及其数值 JISB6911钢铁的正火与退火处理 Q/ZB75机械加工通用技术条件 Q/WYG0814-1997过程控制程序 Q/机械加工检验 Q/热处理零件检验 Q/无损检验 Q/工序质量控制点管理 3、深孔加工、深孔光整珩磨及埋弧自动焊接技术重要工艺特色 油缸缸体内孔加工工序被确立为关键工序质量控制点。为保证其全过程受控,专门编制了《工序控制点明细表》、《工序质量分析表》、《作业指导书》、《机械加工工序卡》、《深孔加工质量监控记录》并严格按照要求实施作业,加工全过程在严格受控状态下进行。 (1)、缸体的精镗工序
组合刀具内孔切削加工的稳定性和可靠性,直接影响到加工缸体的母线直线度、孔加工精度及表面粗糙度。缸体内孔加工切削的稳定性主要靠刀具本身结构的合理设计,我公司使用的组合刀具有效支承长度是加工缸体内孔直径的2倍或2倍以上。我公司经过多次技术论证和试验,当刀具支承长度小于内孔直径时,刀具加工时的切削稳定性较差,当刀具支承长度等于缸体直径时,刀具的切削稳定性明显提高。当组合刀具支承长度大于2倍缸体内孔直径时,其切削稳定性就更可靠,整个组合刀具切削加工过程平稳,刀具按导向套的引导进行缸体深孔加工,保证了缸体加工精度、表面粗糙度和母线的直线度。 组合刀具另件加工精度是组合刀具整体性能符合设计要求的关键。我公司组合刀具的制造、检验都选派有经验的、负责的专门人员把关,每个另件都必须满足设计提出的精度、形位公差要求,并且组合刀具总装后每道支承的径向跳动控制在0.01mm以下,多道支承必须一次磨成,道与道之间的直径偏差控制在0.015mm以下,保证刀具母线直线度误差在2倍缸体直径长度上不大于 0.015mm,刀具的直径尺寸与导向套过盈配合,精度为IT6。 (2)、合理的导向长度及组合夹具精度控制 液压启闭机的缸体都比较长,所以我公司采用推镗工艺,要实现推镗就必须有一个高精度的导向套,先把组合刀具放在导向套中,再把缸体接在导向套上,用导向套、组合刀具的精度直线度来保证缸体的加工精度和直线度,当组合刀具进入加工缸体后,已加工好的缸体又成为新的导向套。对导向套的要求是:导向套长度是组合刀具的倍,导向套内孔精度必须达到H7要求,导向套外径支承点跳动不大于0.01mm,端面与缸体结合部位跳动不超过0.02mm。组合刀具与导向套是过盈配合。由于导向套的内孔精度是H7,组合刀具在修磨后支承
机械加工工艺规范
机械加工工艺规范 1.1总则 1.1.1机械加工人员必须是经过专业培训,具有一定机械基础知识和机床操作能力,且能够满足现行产品零件对机械加工提出的各项要求。 1.1.2机械加工设备和工艺装备应能满足现行产品的各项要求。 1.1.3机械加工所使用的计量器具必须是经计量部门检验合格并在规定检定周期内。 1.2加工前的准备 1.2.操作者接到加工任务后,首先要检查加工所需的产品图样、工艺规程和有关技术资料是否齐全。 1.2.2机械加工人员事先必须熟读生产图样和工艺文件,了解零件加工的关键部位,并根据加工的需要准备各种加工工具以及测量器具。 1.2.3机械加工人员加工前应复核毛坯或半成品是否符合图样要求,发现下列情况时不得进行加工: a、被加工件存在明显缺陷; b、被加工件与图样尺寸或形状不相符。 1.2.4按工艺规程要求准备好加工所需的全部工艺装备,发现问题及时处理。对新夹具、模具等,要先熟悉其使用要求和操作方法。 1.3刀具与工件的装夹
1.3.1刀具的装夹 1.3.1.1在装夹各种刀具前,一定要把刀柄、刀杆、导套等擦试干净。 1.3.1.2刀具装后,应用对刀具装置或试切等检查其正确性。 1.3.2工件的装夹 1.3. 2.1在机床工作台上安装夹具时,首先要擦净其定位基面,并要找正其与刀具的相对位置。 1.3. 2.2工件装夹前应将其定位面、装紧面、垫铁和夹具的定位、平紧面擦试干净,并不得有毛刺。 1.3. 2.3按工艺规程中规定的定位基准装夹,若工艺规程中未规定装夹方式,操作者可自行选择定位基准和装夹方法,选择定位基准应按以下原则: a、尽可能使定位基准与设计基准重合; b、尽可能使各加工面采用同一定位基准; 粗加工定位基准应尽量选择不加工或加工余量比较小的平整表面,而且只能使用一次; c、精加工定位基准应是已加工表面; d、选择的定位基准必须使工件定位夹方便,加工时稳定可靠。
道岔培训资料
矿山窄轨道岔道岔是矿井窄轨铁道中不可缺少的重要组成部分。它是把两条或两条以上的铁道,在平面上进行相互连接或交叉,从而引导机车车辆由一条铁道进入另一条铁道的设备。道岔的零件较多,结构复杂,养护比较困难,是铁道上部建筑的薄弱环节。 第一节道岔类型和系列 一、煤矿窄轨铁道道岔主要分为两类:一类是标准道岔,另一类是特殊道岔。 1、煤矿窄轨道岔的类型:原煤矿工业部窄轨道岔标准设计系列有以下几种:煤矿窄轨标准道岔按结构形式主要分为三种:普通单开道岔、对称道岔和渡线道岔。[说明:非标准道岔有特殊道岔和简易道岔(如:棱形道岔、十字交叉道岔,驴尾道岔)]。按轨距划分:有600mn轨距、762mn轨距和900mn轨距三种。道岔简易图见图1—1。 其中,单开和渡线道岔又有左向(开)和右向(向)之分;道岔的曲线半径有4、6、9、12、15、20、25、30m八种;道岔的辙岔号有2#、3#、4#、5#、6#五种;渡线间距有1.2、1.3、1.6、1.9m四种。 1)普通单开道岔:这种道岔是将一条铁道分为两条铁道的设备。道岔一侧为直股,一侧为曲股,站在尖轨前端向道岔尾部看,曲股向左的为左开道岔,曲股向右的为右开道岔。 2)对称道岔(又称双开道岔):是将铁道向左右对称分开的设备。两侧部是曲股,并对称于直股中心线。 3)渡线道岔:连接两条相邻线路的道岔。由两组相同号数的单开道岔和和一段连接组成的单渡线道岔。 2、道岔简易图 单开道岔(DK 对称道岔(DC
渡线道岔(DX 道岔简易图1—1 3、煤矿使用的特殊道岔: 1)600mm 900mn轨距双用道岔:这种道岔是在为900mm t勺两条钢轨之间,附设一条钢轨组成一组600mn轨距的铁道,同两用道岔相接,构成可同时行驶轨距为600mm和900mn的电机车和矿车。 2)施工简易道岔(又称驴尾道岔):这是一种简易单开道岔。由于结构简单,制作和使用方便,因此,在煤矿使用较多。 二、普通标准道岔的型号表示方法 1、标准道岔共有615、618、、624、918、924 五系列。每一个系列中按辙岔号码和曲线半径又有不同型号。例如:DK615-2-4;DC622-3-9;DX624-4-12……等。 2、道岔的型号函义 1)DK表示单开道岔,DC表示对称道岔,DX表示渡线道岔。 2)615、618、、624、918、924系列中的“ 6”和“9”分别表示 600mm 和900mn轨距;“ 15” “ 18” “24”分别表示轨型。 3)名称中第二段数字为辙岔号码(M ),辙岔号码与岔心角的关系 式为M〔ctg a。见《矿井窄轨铁道》一书中的图4-22辙叉角 2 2 b 单开道岔的辙岔号码有2#、3#、4#、5#、6#等几种,其相应的岔心角分别有28420、185530、1415、112516、93138。标准道岔中,对称道岔的辙岔号码有2#、3#两种;渡线道岔只有4#、5#两种。 4)符号的尾数,单开、对称道岔的尾数表示道岔曲轨的曲线半径,单位为米;渡线道岔的尾数中,前两个数字代表曲线半径,单位为米,后两个数字代表双轨中心
五金员工安全培训实施方案
五金员工安全培训实施方案
————————————————————————————————作者:————————————————————————————————日期:
五金制品行业员工安全培训教案 培训目的:了解和掌握五金制品行业安全基本理论知识(机械危害、非机械危害);学习国家有关法律法规和技术标准;了解五金制品行业安全防护的特点(危害点多、防护面广)及基本安全用电常识和消防知识 培训对象:五金制品行业的员工 培训时间:120分钟 培训内容: 1.事故案例回顾(10分钟) 2007年3月15日15时,某五金厂的员工黄某,刚刚从东莞黄江送货回厂,经理便他用冲压机打表底的外字,15时40分左右,黄某可能精神不能集中,一脚踩上冲压机的脚踏开关,同时把手伸进冲压机里面。冲压机的上部移动模块便压下,黄某因抽手不及,被冲压机的移动模块压中姆指和食指的外一指节的一部分。冲压机上顿时血迹斑斑,他痛得蹲在地上不断呻吟。其他员工见状马上报告经理,经理即时把他送到某人民医院救治……,最终的结果导致黄某损失姆指、食指外一指节的一部分 姚君在冲床车间任职品检员,在冲床操作员离岗时,姚君擅自开动冲床机器,他违规操作,在放冲压件的同时,脚踩动了启动开关,导致左手指冲掉。 2.五金行业存在的主要危害因素及个体防护(30分钟) (一)常见的机械伤害事故及防护措施 1.压伤 (1)多发生在冲压加工过程中,主要的机械设备有冲床、平面压痕机、成型机、剪板机等。 (2)致伤原因 第一,设备不安全因素:无安全防护装置(如双手按钮、防护网、罩、机械保护装置、隔栏等)。 第二,人的不安全行为:不按操作规程操作,不使用辅助工具,冒险作业等。第三,管理缺陷:加班时间过长,作业环境恶劣,员工疲劳过度等。 (3)伤害部位:主要是手指、手掌,严重的有头部(平面压痕机伤害)。 防护措施:要设置防护装置(如双手按钮、防护网、罩、机械保护装置、
地铁施工岗前技术培训教材doc
第一章 工程概况、标准
一、工程概况 略 二、采用的主要规范、标准 《城市轨道交通工程测量规范》(GB 50308—2008),《地下铁道工程施工及验收规范》(GB50299-1999)2003版,《地下铁道工程施工及验收规范》(GB50299-1999)2003版,《铁路轨道工程施工质量验收标准》(TB10413-2003),《铁路混凝土与砌体工程施工质量验收标准》(TB10424-2003),车挡设计文件及验收标准,钢弹簧浮置板道床设计文件及验收标准,橡胶隔振垫道床设计文件及验收标准,钢轨涂油器设计文件及验收标准,迷宫式阻尼钢轨设计文件及验收标准 三、主要设计标准 1、轨距:采用标准轨距1435mm。轨距加宽:轨距加宽应在缓和曲线内完成;无缓和曲线时,在直线里进行加宽,变化率不大于1‰。轨距加宽时,保持轨道外轨位置不变,内轨向曲线中心方向移动进行加宽。半径R≤200m 不同半径的轨距加宽值见下表。 不同半径的轨距加宽值表 2、曲线轨道超高:正线地下线按半超高设置,即外轨轨顶标高为中线轨顶标高加超高的一半,内轨轨顶标高为中线轨顶标高减超高的一半。出入段线曲线处于整体道床和碎石道床上,超高按全超高设置,即保持内轨标高不变,外轨轨顶标高为中线轨顶标高加超高。 3、辅助线上的曲线不设超高,为防止反超高,施工时可将外轨抬高4mm至6mm。
4、超高顺坡应在缓和曲线内完成,无缓和曲线时,在直线里进行超高顺坡,顺坡率不大于2‰,困难情况下不大于3‰。 5、轨底坡设置:正线及辅助线设1:40的轨底坡,在道岔及道岔间不足50m地段不设轨底坡。 6、普通线路钢轨接头采用悬空对接式,半径R≤200m曲线地段钢轨接头采用错接式,错接距离应大于3m。50kg/m钢轨和60kg/m钢轨之间采用50-60kg/m异形轨连接。 四、轨道主要技术标准 1、钢轨 正线、辅助线、出入段线和试车线采用长为25m的60kg/m钢轨,钢轨的材质为U75V,车辆段其它库内线和库外线采用长为25m的50kg/m钢轨,钢轨的材质为U71Mn;50kg/m钢轨和60kg/m钢轨之间采用50-60kg/m异形轨连接。 2、扣件及钢轨接头 2.1扣件类型 扣件的类型包括:单趾扣件(铁垫板分为带坡的和不带坡的两种,带坡铁垫板用于钢弹簧浮置板道床地段)、Vanguard先锋扣件、轨道减振器扣件。 2.2辅助线、联络线及道岔前后接头夹板采用相对应的道床地段铺设扣件配套接头夹板。在无缝线路内需要设置绝缘接头的采用胶结绝缘接头,设置位置按设计图纸设置。 3、轨枕 3.1轨枕的类型 正线轨枕分为:A型短轨枕、B型短轨枕、C型短轨枕。 A型短轨枕适用于单趾扣件,B型短轨枕适用于轨道减振器扣件、C型短轨枕适用于Vanguard先锋扣件。 3.2 轨枕铺设数量
钣金加工工艺培训
钣金加工工艺培训 Document serial number【LGGKGB-LGG98YT-LGGT8CB-LGUT-
钣金加工培训资料 编辑于2015年8月31日16:00 1钣金加工简介 定义 钣金至今为止尚未有一个比较完整的定义,根据国外某专业期刊上的一则定义可以将其定义为:钣金是针对金属薄板(通常在6mm以下)一种综合冷加工工艺,包括剪、冲/切/复合、折、焊接、铆接、拼接、成型(如汽车车身)等。其显着的特征就是同一零件厚度一致,对钢板、铝板、铜板等金属板材进行加工。 钣金加工的工艺流程 对于任何一个钣金件来说,它都有一定的加工过程,也就是所谓的工艺流程.不同结构的钣金件,工艺流程可能也各不相同,结合我司的情况,一般按以下流程: (数控编程) 2 机械制图简介: 钣金加工工程图也属于机械制图的范畴,机械制图是用图样确切表示机械的结构形状、尺寸大小、工作原理和技术要求的学科。图样由图形、符号、文字和数字等组成,是表达设计意图和制造要求以及交流经验的技术文件,常被称为工程界的语言。 在机械制图标准中规定的项目有:图纸幅面及格式、比例、字体和图线等。在图纸幅面及格 式中规定了图纸标准幅面的大小和图纸中图框的相应尺寸。比例是指图样中的尺寸长度与机件实 际尺寸的比例,除允许用1:1的比例绘图外,只允许用标准中规定的缩小比例和放大比例绘图。在中国,规定汉字必须按长仿宋体书写,字母和数字按规定的结构书写。图线规定有八种规格,如 用于绘制可见轮廓线的粗实线、用于绘制不可见轮廓线的虚线、用于绘制轴线和对称中心线的细 点划线、用于绘制尺寸线和剖面线的细实线等。 机械图样主要有零件图和装配图,零件图表达零件的形状、大小以及制造和检验零件的技术 要求;装配图表达机械中所属各零件与部件间的装配关系和工作原理;表达零件结构形状的图 形,常用的有视图、剖视图和剖面图等。 视图是按正投影法即零件向投影面投影得到的图形。按投影方向和相应投影面的位置不同, 视图分为主视图、俯视图和左视图等。视图主要用于表达机件的外部形状。图中看不见的轮廓线 用虚线表示。零件向投影面投影时,观察者、机件与投影面三者间有两种相对位置。机件位于投 影面与观察者之间时称为第一角投影法。投影面位于机件与观察者之间时称为第三角投影法。两 种投影法都能同样完善地表达机件的形状。中国国家标准规定采用第一角投影法。 三视图简介 三视图是观测者从三个不同位置观察同一个空间几何体而画出的图形。 将人的视线规定为平行投影线,然后正对着物体看过去,将所见物体的轮廓用正投影法绘制 出来该图形称为视图。一个物体有六个视图:从物体的前面向后面投射所得的视图称主视图—— 能反映物体的前面形状,从物体的上面向下面投射所得的视图称俯视图——能反映物体的上面形状,从物体的左面向右面投射所得的视图称左视图——能反映物体的左面形状,还有其它三个视 图不是很常用。三视图就是主视图、俯视图、左视图的总称。 一个视图只能反映物体的一个方位的形状,不能完整反映物体的结构形状。三视图是从三个 不同方向对同一个物体进行投射的结果,另外还有如剖面图、半剖面图等做为辅助,基本能完整 的表达物体的结构。 三视图的投影规则是: 主视、俯视长对正 主视、左视高平齐 左视、俯视宽相等
油缸制造工艺.
13、液压油缸和系统制造工艺说明 13.1、液压缸缸体加工工艺 1、目的:控制操作过程,确保加工质量符合图纸要求 2、制造过程中执行的标准: JB4730压力容器无损检测 JB/2370.13-88磨料种类,粒度选择 GB1031表面粗糙度磨参数及其数值 JISB6911钢铁的正火与退火处理 Q/ZB75机械加工通用技术条件 Q/WYG0814-1997过程控制程序 Q/WYG0816.1-1997机械加工检验 Q/WYG0816.2-1997热处理零件检验 Q/WYG0816.3-1997无损检验 Q/WYG0814.10-1997工序质量控制点管理 3、深孔加工、深孔光整珩磨及埋弧自动焊接技术重要工艺特色 油缸缸体内孔加工工序被确立为关键工序质量控制点。为保证其全过程受控,专门编制了《工序控制点明细表》、《工序质量分析表》、《作业指导书》、《机械加工工序卡》、《深孔加工质量监控记录》并严格按照要求实施作业,加工全过程在严格受控状态下进行。 (1)、缸体的精镗工序 组合刀具内孔切削加工的稳定性和可靠性,直接影响到加工缸体的母线直线度、孔加工精度及表面粗糙度。缸体内孔加工切削的稳定性主要靠刀具本身结构的合理设计,我公司使用的组合刀具有效支承长度是加工缸体内孔直径的2倍或2倍以上。我公司经过多次技术论证和试验,当刀具支承长度小于内孔直径时,刀具加工时的切削稳定性较差,当刀具支承长度等于缸体直径时,刀具的切削稳定性明显提高。当组合刀具支承长度大于2倍缸体内孔直径时,其切削稳定性就更可靠,整个组合刀具切削加工过程平稳,刀具按导向套的引导进行缸体深孔加工,保证了缸体加工精度、表面粗糙度和母线的直线度。
车站值班员培训教材
中级车站值班员培训教材 第一部分:基础知识 车站、线路 1、什么是车站?车站分类? 车站是设有配线的分界点,通常办理列车到发、通过、会让越行以及客货运业务。(车站的作用:办理列车接到发、会让和运输任务。) 车站按技术作业性质分为编组站、区段站和中间站。 车站按业务性质分为客运站、货运站和客货运站。 2、铁路线路是由哪几部分组成的? 铁路线路是由路基、桥隧建筑物和轨道组成的一个整体工程结构。 3、轨道由哪几部分组成? 轨道由道床、轨枕、钢轨、联结零件、防爬设备和道岔等组成。 4、钢轨分类?结构组成? 钢轨的标准轨长度为 25 米,12.5 米。 钢轨种类按每米质量进行区分,主要有60、50、43、38公斤/米等类型。(60轨表示每米钢轨重60公斤) 钢轨采用抵拉挠曲性能最好的工字型,断面由轨头、轨腰和轨底三部分组成。 5、铁路线路分为哪几种? 铁路线路分为正线、站线、段管线、岔线和特别用途线。 正线是指连接车站并贯穿或直股伸入车站的线路。 站线是指到发线、调车线、牵出线、货物线及站内指定用途的其他线路。 段管线是指机务、车辆、工务、电务等段专用并由其管理的线路。 岔线是指在区间或站内接轨,通向路内外单位的专用线路。 特别用途线是指安全线和避难线。 6、什么是避难线和安全线? 避难线是为了防止在陡长的坡道上失去控制的列车,发生冲突或颠覆而设的线路。 安全线是为了防止列车、机车车辆越过警冲标与邻线上的列车、机车车辆发生冲突、而设的一段不少于50米的线路。 7、车站站线的用途? 到发线:是指供列车到达和出发的线路。 货物线:专为装卸货物使用的线路。 调车线;是指进行列车编组与解体作业使用的线路。 牵出线:是指设在调车场一端,并与到发线连接、专供列车解体、编组及转线等牵处使用的线路。 8、什么是线间距离?站内线路的线间距离规定为多少? 铁路线路无论在区间、站内,平行的两条线路中心线间所必须保持的最小距离称为线间距离。 9、站内股道应怎样编号? 股道编号,单线区段内的车站,从靠近站舍的线路起,向远离站舍方向顺序编号; 双线区段内的车站,从正线起顺序编号,上行为双号,下行为单号; 尽头式车站,向终点方向由左侧开始编号,如站舍位于线路一侧时,从靠近站舍的线路起,向远离站舍方向顺序编号。
液压缸加工工艺流程图
液压缸加工工艺流程图 1、缸筒:a、备料(无缝钢管)→检验(材质证明书等)→调质(外包:部分零件)→车(车外圆、架子口、 镗止口、法兰止口等)→调质硬度检测→焊(焊接管接头座、法兰等附件)→镗孔或珩磨(粗镗、 精镗、滚压)→车(孔卡槽或内外螺纹)→钳工(钻油口)→检验→防锈入库 b、备料(锻件)→检验(材质证明书、探伤等)→焊(毛坯对接焊)→焊接探伤→车(粗车)→调 质(外包:部分零件)→车(车外圆、架子口、镗止口、法兰止口等)→调质硬度检测→焊(焊 接管接头座、法兰等附件)→镗孔或珩磨(粗镗、精镗、滚压)→车(孔卡槽或内外螺纹)→钳 工(钻油口)→检验→防锈入库 2、活塞、导向套: a、备料(铸件、锻件)→检验(材质证明书、锻件探伤等)→粗车→精车→检验→防锈入库 b、备料(圆钢)→检验(材质证明书等)→粗车→精车→检验→防锈入库 3、活塞杆: a、备料(圆钢)→检验(材质证明书等)→车(粗车)→调质(外包:部分零件)→调质硬度检测 →车(粗、精车)→磨(精磨外圆)→电镀(外包:镀硬铬)或表面热处理(外包:部分零件)→抛 光→检验→防锈入库 b、备料(锻件)→检验(材质证明书、探伤等)→材料探伤→车(粗车)→调质(外包:部分零件) →调质硬度检测→车(粗、精车)→磨(精磨外圆)→电镀(外包:镀硬铬)或表面热处理(外包: 部分零件)→抛光→检验→防锈入库 4、缸头、杆头: a、备料(圆钢)→检验(材质证明书等)→车(粗车)→调质(外包:部分零件)→调质硬度检测 →车(粗、精车含球头、内外螺纹)→锯→铣→镗(镗内孔)→钳工(钻油杯孔或油口)→检验→防 锈入库 b、备料(铸钢:正火处理)→检验(材质证明书等)→车(粗车)→调质(外包:部分零件)→调 质硬度检测→车(粗、精车含球头、内外螺纹)→锯→铣→镗(镗内孔)→钳工(钻油杯孔或油口) →检验→防锈入库 c、备料(锻件)→检验(材质证明书、探伤等)→车(粗车)→调质(外包:部分零件)→调质硬 度检测→车(粗、精车含球头、内外螺纹)→锯→铣→镗(镗内孔)→钳工(钻油杯孔或油口)→检 验→防锈入库 5、孔卡、轴卡、丝圈、压帽: a、备料(圆钢)→检验(材质证明书等)→车(粗车)→调质(外包)→调质硬度检测→车(粗、 精车)→钻(孔卡、压帽)→铣→磨(孔卡、轴卡)→检验→防锈入库 b、备料(锻件)→检验(材质证明书、探伤等)→车(粗车)→调质(外包)→调质硬度检测→车 (粗、精车)→钻(孔卡、压帽)→铣→磨(孔卡、轴卡)→检验→防锈入库 6、缸体焊(缸头与缸筒焊接)→焊缝保温去应力→焊接探伤→防锈入库 7、装配 熟悉装配图(含出厂试验大纲等技术文件)→零部件(含密封件、工装)清理→零部件清洗→零部件配 装→零部件精洗→密封件装配→零部件组装→标识标牌→检查试验装置→出厂试验→喷漆→装箱→发 货。 注:因油缸大小不一样,以上零、部件工艺并非统一,根据零、部件图需要,采用合理的加工工艺。 63