加工中心资料.
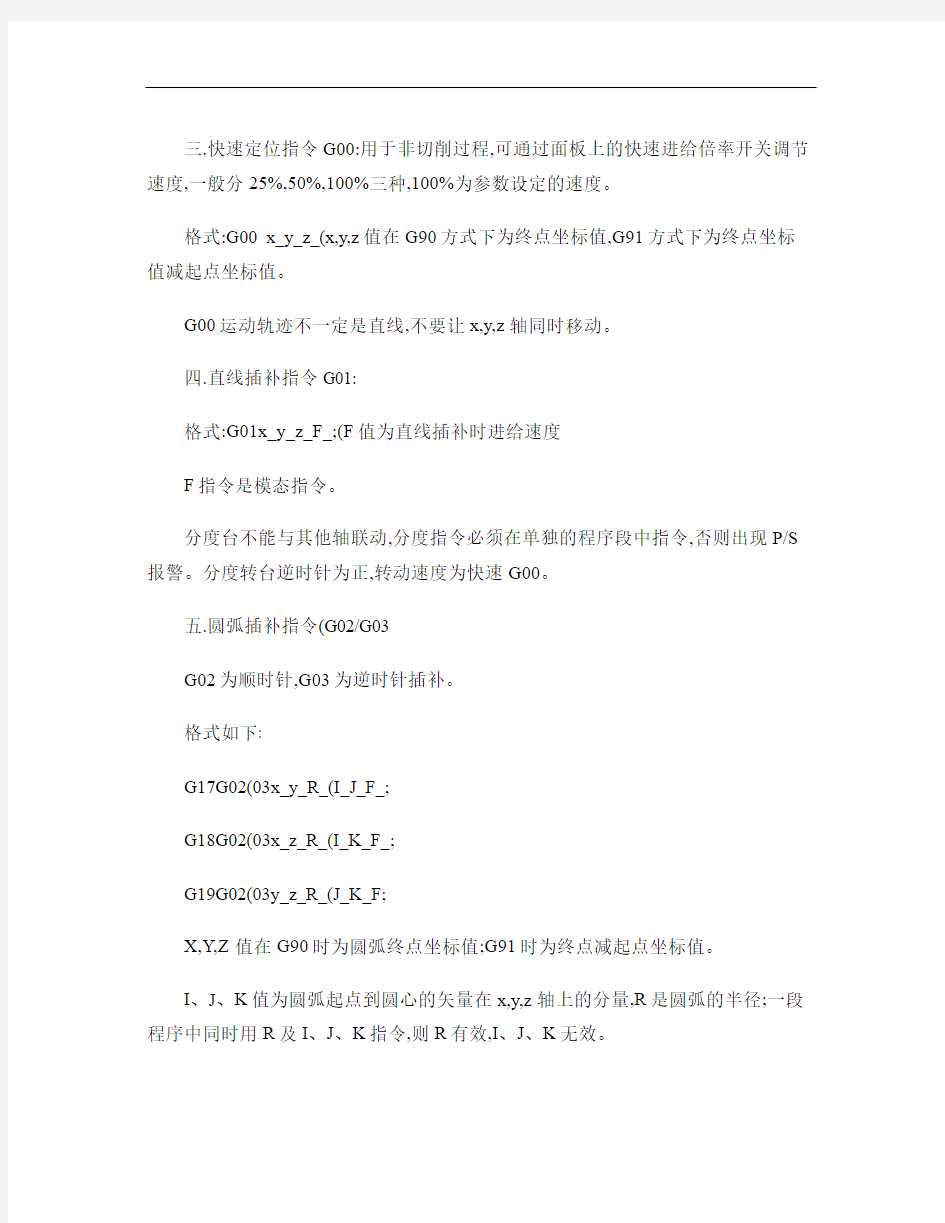

三.快速定位指令G00:用于非切削过程,可通过面板上的快速进给倍率开关调节速度,一般分25%,50%,100%三种,100%为参数设定的速度。
格式:G00 x_y_z_(x,y,z值在G90方式下为终点坐标值,G91方式下为终点坐标值减起点坐标值。
G00运动轨迹不一定是直线,不要让x,y,z轴同时移动。
四.直线插补指令G01:
格式:G01x_y_z_F_;(F值为直线插补时进给速度
F指令是模态指令。
分度台不能与其他轴联动,分度指令必须在单独的程序段中指令,否则出现P/S 报警。分度转台逆时针为正,转动速度为快速G00。
五.圆弧插补指令(G02/G03
G02为顺时针,G03为逆时针插补。
格式如下:
G17G02(03x_y_R_(I_J_F_;
G18G02(03x_z_R_(I_K_F_;
G19G02(03y_z_R_(J_K_F;
X,Y,Z值在G90时为圆弧终点坐标值;G91时为终点减起点坐标值。
I、J、K值为圆弧起点到圆心的矢量在x,y,z轴上的分量,R是圆弧的半径;一段程序中同时用R及I、J、K指令,则R有效,I、J、K无效。
用R编程时,R正值则圆弧所对圆心角小于180°,R负值则圆弧所对圆心角大于180°;指令整圆时不能用R编程。
用I、J、K编程时注意I、J、K是一个从圆弧起点指向圆心的矢量分别在x,y,z 轴上的分量I0,J0,K0可忽略不写.
G02(G03I_(k_F_;之类都是整圆插补指令.G02R_F_;指令零度的圆.
第六节坐标系指令
1.工件坐标系设定指令G92:
指令格式:G92x_y_z_;
用G92设定工件坐标系时,以刀具当前位置为参考点建立坐标系。
2.工件坐标系选取指令G54~G59:都以机床坐标系原点为参考点建立,每个工件坐标系原点在机床坐标系中的坐标值就是该坐标系的偏置值,该偏置值必须在加工前提前输入到机床坐标系中。
3.局部坐标系指令G52:
格式:G52x_y_z_;
G52后X,Y,Z值就是局部坐标系原点在工件坐标系中的坐标值,使用完后用
G52X0Y0Z0将其取消。
4.选择机床坐标系指令G53:
作用:换刀交换工作台过程中可用G53将定位到机床坐标系中一点。
格式:G53G90X_Y_;(非模态指令,仅用于G90绝对方式
第七节平面选择指令G17X_Y_,G18Z_X_,G19Y_Z_
开机时默认有效,可不写出。
第八节暂停指令G04
格式:G04P_;或G04X_.P后不带小数点,单位为毫秒;X后带小数点时单位为秒,不带小数点时单位为毫秒。
用于指令刀具作短时无进给加工。
第九节自动返回机床参考点指令G28
格式:G28X_Y_Z_; 指令结果为各轴经指定中间点(工件坐标系内返回机床参考点。X, Y,Z后的值即为中间点坐标值。
G28G90X0Y0的结果为X,Y轴从刀具当前点到达工件坐标系原点后返回机床参考点;
G28G91X0Y0Z0执行结果为X,Y,Z轴从当前点直接返回机床参考点。
自动返回第二、第三、第四参考点指令G30。有的机床换刀点不在参考点而在第二、第三、第四参考点,这时可用G30。
格式:G30P2(P3、P4X_Y_Z_;(P2、P3、P4为三个参考点,X,Y,Z值为中间点坐标值
第十节常用辅助功能M指令
该指令常由M后接两位数组成,用于控制机床启/停及冷却液开关等动作。
1.程序暂停M00,暂停后按循环启动按钮程序继续执行。
2.程序选择停止M01,只有当面板上选择停止开关为ON时才起作用。
3.主程序结束M02
4.主轴正转M03
5.主轴反转M04
6.主轴停转M05
7.换刀指令M06,一般与T代码配合使用,指令前各轴须移动到换刀点。
8.冷却液开指令M08
9.冷却液关指令M09
10.主轴定向指令M19,用于指令主轴停止在一个固定角度位置,以利于机械手抓刀
或精镗孔时刀具从孔中退出。
11.主程序结束指令M30。(与M02作用相同。
12.调用子程序指令M98
13.子程序结束指令M99
第十一节主轴速度S指令(模态指令
第十二节刀具功能T指令,用于选择刀库中的刀具。
M06T01有两种可能:a.T01装到主轴上。b.T01作准备。建议M06与T代码分为两段。
第十三节进给速度F指令
G94方式时F后数值单位为毫米,开机有效。G95方式时表示刀具每一转的进给量。G94、G95都是模态指令。
第十四节小数点编程
第十五节跳段功能
程序段前加/时,当跳段开关打开时,该程序段不执行。
第十六节公制、英制转换功能
公制G代码G21,最小设定单位0.001mm,英制G代码G20,最小设定单位
0.0001英寸。
G20、G21的设定必须在程序的开头,且工件坐标系设定之前,使用单独的程序段指令,机床断电后再次开机G20、G21状态保持不变。
固定循环相当于子程序指令
固定循环指令格式:G_X_Y_Z_R_Q_P_F_K_;或G99G91G_(孔加工方式
X_Y_(孔位坐标 Z_R_Q_P_F_(孔加工参数K_(重复次数;
当使用G90绝对指令方式时,Z、R后接数值就是两点分别在工件坐标系中的绝对坐标值;当使用G91增量指令方式时,R值就是R点相对于固定循环初始点的相对值;Z值就是Z
点相对于R点的相对距离。
指令中G98、G99指令决定了每孔加工完后Z轴回到的坐标点位置,G98指令加工完后Z 轴回到初始点位置;G99指令加工完后Z轴回到R点位置。
初始点平面就是每次指令固定循环时Z轴所在位置。
R点平面就是刀具快速趋近工件时由快速运动转为切削运动时Z轴所在的位置。
G98、G99都是模态指令,也是同一组的G代码,可以互相取代,每次开机时,默认G98状态。
零件表面未加工时R取5~8毫米,已加工时R取2~3毫米。
固定循环指令列表:
G代码钻削(-Z刀具的孔底动作退刀动作(+Z用途
G73 间歇进给快速进给高速深孔加工循环
G74 切削进给暂停—主轴正转切削进给左旋螺纹攻丝循环
G76 切削进给主轴定向停止快速进给精镗循环
G80 取消固定循环
G81 切削进给快速进给钻孔循环
G82 切前进给暂停快速进给钻镗阶梯孔循环
G83 切前进给快速进给深孔加工循环
G84 切削进给暂停—主轴反转切削进给攻丝循环
G85 切削进给切削进给镗循环
G86 切削进给主轴停止快速进给镗循环
G87 切削进给主轴正转快速进给背镗循环
G88 切削进给暂停—主轴停手动镗循环
G89 切削进给暂停切削进给镗循环
G81X_Y_Z_R_F_K_;(X,Y值为孔坐标值,Z值为目标点孔底坐标;K为重复次数,G90状态下同孔加工K次,G91状态下以相同增量X,Y钻K个孔。
固定指令是模态指令,完成后须用G80取消;
G82X_Y_Z_R_P_F_;
G83X_Y_Z_R_Q_F_;(深孔钻循环,用于长径比大于50或小孔。Q为每次钻削深度,为正值;每次加工完后退回R点平面。
G73X_Y_Z_R_Q_F_;(高速深孔钻循环,每次回退D值,D值由系统决定。
G84X_Y_Z_R_P_F_;(用于右旋螺纹加工,F=螺距S×转速
G74X_Y_Z_R_P_F_;(用于左旋螺纹加工
G84、G74指令时须用攻丝刀柄。
G85X_Y_Z_R_F_;(镗孔循环,孔中以F指令速度退回R点
G86X_Y_Z_R_F_(镗到位后停转,快速退回初始点
G76X_Y_Z_R_P_Q_F_;(精镗循环,镗到位后孔底暂停P秒,向刀尖相反方向移动Q值,然后快速退回到初始点位置,再回到孔中心,主轴正转。
G87X_Y_Z_R_P_Q_F_;(背镗循环,镗小孔下的大孔
刀具快速到X、Y点定向停止,向刀尖相反方向移动Q值,再快速进给到孔底R 点位置,刀具回孔中心位置正转,以F指令速度正方向镗孔到Z点,主轴再次定向停止,向刀尖反方向位移Q值,刀具从孔中退出,回到初始点后,到孔中心,主轴正转。
注意:1.G87指令在G99状态时不能使用;2.G87过程中有四次刀具定向停止.
使用G76、G87循环时,应检验回退方向与刀尖方向是否相反,不对应时可修改2号参数。2号参数是一个八位的二进制数:
7 6 5 4 3 2 1 0
表中第四五位决定刀具回退方向.
第五位第四位退刀方向
0 0 +X
0 1 -X
1 0 +Y
1 1 -Y
G73、G83、G76、G87循环中都有Q指令,但功能不同,须注意Q值是模态指令。
G88X_Y_Z_R_P_F_(镗孔循环,一般用于浮动镗刀手动退刀。
G89X_Y_Z_R_P_F_;(以F速度退到R点后快速退回初始点。
第十八节刀具补偿功能
一.刀具长度补偿。
指令格式:G00(G01G44(G43H_Z_;
取消指令G49
H代码是偏置代码,后接数值是偏置存储器中的地址。
H00~H66(H99,H00中值总为零,用于取消长度补偿值。
指令结果:不论在G90、G91方式,G43结果是将偏置代码中的补偿值与Z轴指令的终点值相加,作为Z轴最终指令值;而G44结果是用Z轴指令的终点值减去偏置代码中的值作为Z轴最终指令值。
G43、G44是模态代码,如:使用G44时输入正的刀具补偿值与用G43输入负补偿值结果一样。
设定有两种方法:1.直接输入刀具长度,有对刀仪时使用较为方便;注意此时工件坐标系Z 向零点偏置值即为它在机床坐标系中的实际值。2.输入几个相关数值的差值。即刀具的补偿值为刀尖到Z向编程零点的距离,此方法中工件坐标系Z轴零点
偏置值为0。
选用哪种方法,与所选工件坐标系相关。直接输入刀具长度方便,但忘记输入刀补值时较危险。
二.刀具半径补偿功能
1.作用:
简化编程,减少计算工作量;
变换刀具后,无须更改程序;
同一程序的粗、精加工可使用同一程序。
2.指令格式:G17G00(G01G41(G42X_Y_D_(F_;
G18G00(G01G41(G42Z_X_D_(F_;
G19G00(G01G41(G42Y_Z_D_F_;
取消指令:G17G00(G01G40X_Y_;(G18G00(G01G40Z_X_;G19G00(G01G40Y_Z_;
G41当补偿值为正时,指定刀具半径左侧补偿。(负值右侧
G42当补偿值为正时,指令刀具半径右侧补偿。(负值左侧
G40取消刀具半径补偿方式。
刀具长度偏置号不能与刀具半径偏置号相同!
3.指令顺序:A.刀具进入零件加工面前设定刀具半径补偿方式;B.在指定平面内给出连续的轴移动指令;C.刀具离开工件加工面后,取消刀具半径补偿方式.
4.注意事项:
指定或取消刀具半径补偿方式时,须在G00或G01状态,而不能在G02或G03方式; 在刀具半径补偿方式下,如有两个或两个以上程序段刀具不移动指令,则会出现过切或
切削不足现象。
当铣削含有圆弧段曲线的内轮廓时,刀具补偿半径偏置值必须小于轮廓圆弧半径值,否则形成圆弧不相交,出现报警。刀具半径过大造成轨迹与编程轨迹相反,也出现报警。
五.刀具半径补偿方向的确定。(当补偿值为正时
沿刀具前进方向看,刀具轨迹在加工曲线左侧时,使用G41左侧偏置指令,否则使用G42
指令。
六.轮廓加工时的刀具路线选择
为保证零件轮廓的平滑过度,刀具切入、切出点一般在零件轮廓延长线上或采用圆弧方式切
入、切出。
一般程序书写格式:
1.程序号O-(后接程序号
2.刀库旋转,第一把刀到达换刀位置作准备;(T代码
3.机床各轴移动到换刀位置;(如G28,G30指令
4.进行换刀动作,第一把刀换到机床主轴上;(用M06指令
5.机床各轴移动到指定的工件坐标系中;(用G00指令
6.主轴按指定速度和方向旋转(如M03,S指令
7.建立刀具长度补偿,Z轴到达加工起始点;(需冷却液时,指定M08功能
8.第一把刀相对于工件运动的轨迹描述指令集合;(轮廓加工时,要使用刀具半径补偿功
能G41/G42时,此段为第一把刀具加工核心部分。
9.第一把刀加工完毕,取消刀具补偿功能和各项辅助功能。(如主轴停转,冷却液关闭等。
10.第二把刀准备;
11.机床各轴移动到换刀位置;
12.进行换刀动作,第二把刀换到机床主轴上;
13.重复5~12的过程,第二把刀相对于工件运动的轨迹描述的指令集合;
14.依此类推进行其他刀具的加工内容描述;
15.最后一把刀还回刀库,不再叫其他刀具作准备;
16.程序结束,使用M02或M30指令。
由上可知,加工中心工序划分一般以一把刀的加工内容为一序,每把刀的加工内容编程都按
2~9的顺序。
第三讲机床的各种操作方式(FANUC OME系统
CRT屏幕下的键为功能软件,它随操作方式及画面的改变而改变;CRT右侧面板为CRT的MDI面板,其上字母、数值为地址数据键,用于输入程序、设置参数。标有CURSOR的两各向上、向下箭头的键为光标键。PAGE键用于前后翻页,SHIFT 为换档键,用于在一个键的两个功能间切换。
INPUT为输入键,用于输入参数或程序。
OUTPTSTART为启动输出键,用于输出参数或程序,也用于MDI方式下执行一段MDI指令。
CAN键为取消键,用于删除输入到缓冲区的字符。
DELET键为删除键,INSRT键为插入键,ALTER键为替换键,它们都是程序编辑键。RESET为复位键,用于使系统复位。
CRT MDI面板上有8个功能键:
1.POS为坐标位置键,用于显示刀具当前坐标位置,有绝对坐标、相对坐标、综合坐
标画面。
2.PRGRM为程序键,用于显示程序内容。
3.OFFSET为偏置设置键,用于输入刀具补偿值和工件坐标系偏置值。
4.MENU为菜单键;
5.DGNOSPARAM为诊断参数,用于显示参数画面。
6.OPRALARM为报警键,机床报警时自动转到改画面,并显示报警提示。
7.AUXGRAPH是辅助绘图键,用于显示刀具轨迹;
8.MACRO为宏程序键。
以上功能键往往显示几页内容,可用PAGE键换页选择。
CRT下是机床操作面板,循环启动、进给暂停键用于自动方式下运行或暂停程序。
第一章机床的开机和关机
第一节机床开机和返回参考点操作
参考点用于确定各轴起始机械位置,机床在此位置进行换刀或设定坐标系。一般加工中心的位置反馈元件有绝对编码器和相对编码器,配绝对编码器的机床开机后不需返回参考点,配相对编码器的机床开机后必须手动返回参考点。
开机及返回参考点操作步骤:
1.开机前检查主轴、导轨润滑油油位是否在允许范围内,使用压缩空气的机床还
应打开气泵或管路开关,确认压力表压力在要求范围内。
2.将空气开关打开,置于ON位置,接通电源。
3.按POWERON按钮,接通数控系统电源,显示器亮。
注意:在未出现位置画面或报警画面之前,不能按动CRT MDI面板上的任何键,以免引起误动作。
4.按机床操作面板上的“准备”按钮;
5.按CRT MDI面板上的功能键POS,查看机床当前位置。
按PAGE键或CRT下的软键可选择综合坐标显示画面。
6.按“返回原点”键,显示器右下角出现ZRN字母。先回零Z轴,还可按快速
进给并选择快速倍率以改变回零速度。
7.按刀库回零按钮,刀库旋转、回零。
8.返回参考点后,建议手动慢速移动各轴及慢速旋转主轴,使机床预热。
第二节机床关机
步骤:
1.检查机床自动、手动运行都已停止。
2.手动移动各轴离开零点位置,以免因离参考点近再次开机时出现超程报警。为避免
床身变形,应停在床身中间位置。
3.按POWER OFF按钮,关操作面板开关,显示器关闭。
4.将电器控制柜上的空气开关置于OFF位置,切断电源,关闭压缩空气气源。
第二章编辑程序
背景编辑:不在编辑方式下编辑程序。按程序键—按CRT下向右软键—CRT下BG-EDIT 进入—输入程序—按CRT下BG-END软键退出。
第一节加工程序的输入
1.先选择操作方式:按编辑键,显示器右下角出现EDIT字样。
2.打开程序保护锁;
3.按PRGRM程序键,再按CRT下LIB功能软键,可查看存储容量、已存程序数量
及程序号。
4.按CRT下“程式”功能软键,转为程序画面。编辑方式下,右上角显示编辑的程
序号和顺序号。非编辑方式下,显示之前最后执行的程序号和顺序号。
5.开始输入程序号。每输入一段后按INSRT存入系统存储器,再按EOB键及INSRT
键,输入分号。
6.继续输入程序段内容。
7.锁上程序保护锁。
第二节加工程序的修改
1.选择编辑方式,打开程序保护锁。
2.用CURSOR光标键将光标移动到要修改的内容下方,键入更改后内容;
3.按ALTER键替换。
4.输入时发现可用CAN键清除最后一个字符。
5.如想删除已输入到存储器的字符,则先将光标移动到该程序字的下面,然后按
DELET键。
6.修改完后,及时锁上程序保护锁。
第三节程序的检索
一、检索:1.将操作方式改为编辑方式;2.按PRGRM程序键,翻到程序画面;3.键入
需查找的程序号,按向下光标键;
二、删除:1.编辑方式下,打开保护锁;2.按程序键;3.键入程序号,按向下光标键;
4.再次键入程序号,按DELET删除键;
5.按CRT屏幕下的LIB软键查看,已删除。
第五节从RS232C接口输入输出程序
优点:占用机器时间少,不容易出错。
步骤:一.根据传输设备设置通讯参数:包括传输通道P/S、数据停止位、程序波特率、传输设备的设置。1.选MDI方式;2.按DGNOSPARAM参数键;3.设置
I/O=0;4.利用翻页键找到第二项PWE,将其设置为1,表明参数可修改;出现100号P/S 报警提示;5.翻页找到2号参数,2号参数是8位2进制数,将其中的3位改变,即从前向后数一位最后一位设为1,第六位不变。将38号参数前两位设为1,552号参数设置为10,将光标移动到PWE将其设为0,再按RESET键;6.将通讯电缆与计算机及机床连接。(应关机操作7.重新开机,改为编辑方式,按程序键,用PAGE翻到程序,输入程序号,按INPUT键;8.操作计算机(程序服务器发射程序;接收完后,CRT转到刚接收到的程序画面。9.输出程序时先将计算机/程序服务器准备好。转到编辑方式下,键入要输出的程序号,按OUTPUT键。
第六节背景编辑
机床具有前台加工,后台编辑功能—背景编辑
可不考虑方式及运行状态。前后台互不影响。步骤:
1.在任何方式下,打开保护锁,按程序键,再按CRT下向右软键,然后按BG-EDIT 软键,
即显示背景编辑画面。
2.输入程序号,按INSET键;
3.继续输入程序;
4.输完后按BG-END软键,存入前台,背景编辑结束,锁上保护锁。
第三章手动运行方式
第一节手动进给:点动移动
1.按手动键,CRT下出现JOG;
2.旋转倍率开关,确定倍率;
3.选择移动轴(正、负向
第二节手轮进给。对刀时经常使用。CRT下出现HNDL
第三节辅助功能的使用。M、S、T代码功能
开机后主轴不转时,须先在MDI方式下输入转速,按OUTPTSTART执行。(ADRS
第四章自动运行方式
第一节 MDI操作方式:
MDI中文解释是手动数据输入,即把一段程序作为指令从键盘输入,机床依其运行。
机床的CRT MDI面板输入一个可执行的程序段:
1.首先设定绝对值增量值参数。MDI方式下,程序的绝对值、增量值不取决于G90、
G91而取决于参数设定;设定参数的步骤:a.按MDI键;b.按DGNOSPARAM键,出现参数画面,按PAGE键及CUTSOR光标键,找到要修改的参数,将其设为“绝
对=1”,按INPUT键;
2.开始输入程序段;a.MDI方式下,按PRGRM程序键并按软键MDI,出现一个画面;
b.键入程序段,按INPUT键;
c.按顺序输入其他程序段;
3.按CRT下循环启动按钮或OUTPTSTART键执行该程序段,此时可按POS位置键
查看程序终点位置运行是否正确。
第二节存储器运行即自动运行
1.存储器运行方式时应先选择要执行的程序号;a.先选择编辑方式b.按PRGRM 程
序键c.键入拟执行的程序号,按向下光标键d.可移动光标查看程序段,按RES
ET键,光标回到程序头
2.按自动键选择自动运行方式,CRT右下角出现AUTO字母。
3.按循环启动按钮,程序自动运行。按检视软键,翻到检视画面可看到正在执行的
程序段和后两段。
4.程序自动运行期间可按进给暂停按钮,也可通过倍率开关改变进给速度。
运行中出现问题时,按暂停按钮,修改后,复位回程序头。再次运行前检查模态指令,如有G43,G44,G41,G42,固定循环等,应将其取消。(适用于程序停止后从头开始加工步骤:
1. 程序键翻到现单节画面,如有模态指令,改为MDI指令,输入G40、G4
9、G80等后按OUTPTSTART输出键。
第二节在线加工
程序长、存储空间不够时使用边传边加工。
1.设置通讯参数;
2.将刀具夹具等准备好;
3.按自动运行方式并按联线键、循环启动键等待程序;
4.发送设备准备好,并发送程序;
5.机床按接受到的程序运行、加工。
第五章程序检查
第一节机床所有轴锁闭运行
可检查程序语法错误。步骤:
自动方式下按轴禁止-MST锁闭-循环启动-按POS位置键,可看到坐标位置变化。如发现错误,可转到编辑方式下修改。
第二节单段方式
如程序需修改,将程序改为编辑状态即可。步骤:编辑方式下调出程序—自动—单段—POS—循环启动
第三节机床试运行
运行速度快,不安装刀、夹具。常与轴禁止、MST闭锁结合使用。
自动方式下按试运行—循环启动
第四节绘图功能
步骤:
1. 设定绘图功能的各种参数。A.轴参数设定可用于设定绘图平面。P=0时为
X、Y平面。输入值后按INPUT键即可。B.旋转角(水平、垂直一般可不设定;C.倍率设定,一般不设定;D.最大值、最小值,用于设定绘图范围。可不
设定。STARTSEQ用于需部分显示程序段时设定起始程序段的程序号。
ENDSEQ终止程序设定。
2. 显示刀具编程轨迹的步骤。A.编辑方式下选择需显示的程序,然后按自动
按钮;B.按CRT MDI面板上的绘图按钮AUXGRAPH,找到绘图参数画面键后按CRT下经络图软键,转到绘图画面,再按CRT下实行软键,再按自动软键,
则绘图开始。
三.输入工件坐标系的设定值
设定工件坐标系的原点偏置值时,任何方式下都可以进行。
步骤:
1. 按OFFSET键;
2. 按CRT下坐标系软键并用PAGE键翻到工件坐标系画面(第一页是NO.00—NO.03,
第四讲加工中心维修的电路基础
维修培训系列资料
第四讲 加工中心维修的电路基础
第一节 电路的基础知识
一、电工原理
1、欧姆定律(Ohm’s Law)E=IR E:(V,伏特)I:电流(A,安培)R:电阻(Ω,欧姆) 2、瓦特定律(Watt’s Law):
P=EI=I2R=E2/R
[电功率(W,瓦特)E:(V,伏特)I:电流(A,安培)R: 电阻(Ω,欧 姆)]
3、交流电功率 单相电功率:P=EIcosθ 三相电功率:P=√3EIcosθ E:(V,伏特)I:电流(A,安培) cosθ :功率因子 4、电阻串联与并联 电阻串联:R=R1+R2+…+Rn 二电阻并联:1/R=1/R1+1/R2 5、变压器 V1/V2=N1/N2=I1/I2 V:端电压 N:绕线匝数 I:电流 R=R1R2/(R1+R2)
二、基本元件原理介绍
凡是自动或手动接通和断开电路,以及能实现对电路或非电对象切换、控制、保护、检测和调 节目的的元件统称电器 1、电阻(Resister) 电阻,用符号R表示。其最基本的作用就是阻碍电流的流动。 衡量电阻器的两个最基本的参数是阻值和功率。阻值用来表示电阻器对电流阻碍作用的大 小,用欧姆表示。除基本单位外,还有千欧和兆欧。功率用来表示电阻器所能承受的最大电流, 用瓦特表示,有1/16W,1/8W,1/4W,1/2W,1W,2W等多种,超过这一最大值,电阻器就会烧坏。 一般電阻器通常是以不同色环标记法來表示電阻值,每種顏色分別代表1至9不同的數字,如 圖1所示;電阻器上第一與 第二條代表十位數與個位數 值,第三條為阻值的倍數值, 而最後一條則表示製造的 電阻值誤差範圍;容許誤 差的色碼是以棕色表示1% 誤差,紅色表示2%誤差等 等;例如一個電阻器如圖, 上面顏色依序為綠、棕、 紅、金,依照色碼對應數 值,可以得到其阻值為 5.1K?±5%。
63
加工中心刀柄规格
加工中心刀柄规格 加工中心的主轴锥孔通常分为两大类,即锥度为7:24 的通用系统和1:10 的HSK 真空系统。 7:24 锥度的通用刀柄 锥度为7:24 的通用刀柄通常有五种标准和规格,即NT(传统型)、DIN 69871(德国标准)、IS0 7388/1 (国际标准)、MAS BT(日本标准)以及ANSI/ASME(美国标准)。 NT 型刀柄德国标准为DIN 2080,是在传统型机床上通过拉杆将刀柄拉紧,国内也称为ST;其它四 种刀柄均是在加工中心上通过刀柄尾部的拉钉将刀柄拉紧。 目前国内使用最多的是DIN 69871 型(即JT)和MAS BT 型两种刀柄。DIN 69871 型的刀柄可以 安装在DIN 69871 型和ANSI/ASME 主轴锥孔的机床上,IS0 7388/1 型的刀柄可以安装在DIN 69871 型、IS0 7388/1 和ANSI/ASME 主轴锥孔的机床上,所以就通用性而言,IS0 7388/1 型的刀 柄是最好的。 (1)DIN 2080 型(简称NT 或ST) DIN 2080 是德国标准,即国际标准ISO 2583 ,是我们通常所说NT 型刀柄,不能用机床的机 械手装刀而用手动装刀。 (2)DIN 69871 型(简称JT、DIN、DAT 或DV) DIN 69871 型分两种,即DIN 69871 A/AD 型和DIN 69871 B 型,前者是中心内冷,后者是 法兰盘内冷,其它尺寸相同。 (3)ISO 7388/1 型(简称IV 或IT) 其刀柄安装尺寸与DIN 69871 型没有区别,但由于ISO 7388/1 型刀柄的D4 值小于DIN 69871 型刀柄的D4 值,所以将ISO 7388/1 型刀柄安装在DIN 69871 型锥孔的机床上是没有问题的,但将 DIN 69871 型刀柄安装在ISO 7388/1 型机床上则有可能会发生干涉。 (4)MAS BT 型(简称BT) BT 型是日本标准,安装尺寸与DIN 69871、IS0 7388/1 及ANSI 完全不同,不能换用。BT 型刀柄的对称性结构使它比其它三种刀柄的高速稳定性要好。 (5)ANSI B5.50 型(简称CAT) ANSI B5.50 型是美国标准,安装尺寸与DIN 69871、IS0 7388/1 类似,但由于少一个楔缺口, 所以ANSI B5.50 型刀柄不能安装在DIN69871 和IS0 7388/1 机床上,但DIN 69871 和IS0 7388/1 刀柄可以安装在ANSI B5.50 型机床上。 二、1:10 的HSK 真空刀柄
加工中心刀柄
加工中心刀柄 集团文件版本号:(M928-T898-M248-WU2669-I2896-DQ586-M1988)
加工中心刀柄介绍 随着加工中心在零件机械加工中的运用越来越普遍,加工中心刀柄的使用也越来越多。但是,刀柄的种类有很多,我们必须选择精度足够的、经济的、使用方便的刀柄用于零件的加工,这就要求我们对刀柄有全面的了解。 刀柄,用于连接加工中心主轴与切削刃具的装备。这就如同人用手拿着笔写字,人是机床,笔是切削刃具,手就是刀柄。 如图1所示,由于刀柄是与主轴连接、与刀具连接,所以刀柄的分类也主要有两种分类。按与加工中心主轴的连接方式分类:分为7:24锥度刀柄和1:10锥度刀柄;按刀柄与刀具的连接方式分类:分为侧固式刀柄、弹簧夹套式刀柄、液压刀柄、热涨刀柄等。 图1 一、刀柄与主轴连接方式 加工中心的主轴和刀柄之间通常采用锥度配合。锥度配合特点是具有定心性好、间隙或过盈可以方便地调整等。 图2 锥度C=(D-d)/L,如图2。 因此刀柄按锥度也分为7:24和1:10两大类。 (一)、7:24锥度刀柄定位原理及特点 1、7:24锥度刀柄定位原理 图3 图4 7:24锥度刀柄通过长锥面限制X、Y方向的移动及转动,Z方向的移动5个自由度,通过拉力F与锥面产生的摩擦力限制Z轴的转动(如图3、图4所示),从
而实现刀柄的完全定位,此定位方式刀柄端面与主轴端面有间隙,如BT系列刀柄。 2、7:24锥度刀柄的特点 优点: 1)、不自锁,可以实现快速装卸刀具; 2)、刀柄的锥体在拉杆轴向拉力的作用下,紧紧地与主轴的内锥面接触。 3)、7:24锥度的刀柄在制造时只要将锥角加工到高精度即可保证连接的精度,所以成本相应比较低,而且使用可靠。 缺点: 1)、单独的锥面定位。7:24锥度刀柄连接锥度较大,锥柄较长,导致a、换刀行程长,换刀时间慢;b、刀柄重量增加,机床损耗功率增加。 2)、在高速旋转时,由于离心力的作用,主轴前端锥孔会发生膨胀,膨胀量的大小随着旋转半径与转速的增大而增大,见图5,但是与之配合的7:24锥度刀柄由于是实心的所以膨胀量较小。(如:在离主轴中心r=0.02m处,一质量为m=100g的质点,在机床主轴转速为n=12000r/min时,所受到的离心力为 F=3158.3N,即为315.83Kg的力。) 图5 则有:a、刀柄旋转时,在拉杆拉力的作用下,刀柄向内位移,轴向精度低;b、刀具总的刚度会降低,导致刀具前端径向跳动大,加工位置的表面质量、位置精度都差;c、每次换刀后刀柄的径向尺寸都可能发生改变,存在着重复定位精度不稳定的问题;d、不适合高速切削
CNC加工中心的刀柄标准是什么
加工中心的主轴锥孔通常分为两大类,即锥度为7:24 的通用系统和1:10 的HSK 真空系统。 7:24 锥度的通用刀柄锥度为7:24 的通用刀柄通常有五种标准和规格,即NT(传统型)、DIN 69871(德国标准)、IS07388/1 (国际标准)、MAS BT(日本标准)以及ANSI/ASME (美国标准)。 NT 型刀柄德国标准为DIN 2080,是在传统型机床上通过拉杆将刀柄拉紧,国内也称为ST;其它四种刀柄均是在加工中心上通过刀柄尾部的拉钉将刀柄拉紧。 目前国内使用最多的是DIN 69871 型(即JT)和MAS BT 型两种刀柄。DIN 69871 型的刀柄可以安装在DIN 69871 型和ANSI/ASME 主轴锥孔的机床上,IS0 7388/1 型的刀柄可以安装在DIN69871 型、IS0 7388/1 和ANSI/ASME 主轴锥孔的机床上,所以就通用性而言,IS0 7388/1 型的刀柄是最好的。 (1)DIN 2080 型(简称NT 或ST) DIN 2080 是德国标准,即国际标准ISO 2583 ,是我们通常所说NT 型刀柄,不能用机床的机械手装刀而用手动装刀。 (2)DIN 69871 型(简称JT、DIN、DAT 或DV) DIN 69871 型分两种,即DIN 69871 A/AD型和DIN 69871 B 型,前者是中心内冷,后者是法兰盘内冷,其它尺寸相同。 (3)ISO 7388/1 型(简称IV 或IT) 其刀柄安装尺寸与DIN 69871 型没有区别,但由于ISO 7388/1 型刀柄的D4 值小于DIN 69871刀柄的D4 值,所以将ISO 7388/1 型刀柄安装在DIN 69871 型锥孔的机床上是没有问题的,但将DIN 69871 型刀柄安装在ISO 7388/1 型机床上则有可能会发生干涉。 (4)MAS BT 型(简称BT) BT 型是日本标准,安装尺寸与DIN 69871、IS0 7388/1 及ANSI 完全不同,不能换用。BT 型刀柄的对称性结构使它比其它三种刀柄的高速稳定性要好。 (5)ANSI B5.50 型(简称CAT) ANSI B5.50 型是美国标准,安装尺寸与DIN 69871、IS0 7388/1 类似,但由于少一个楔缺口,所以ANSI B5.50 型刀柄不能安装在DIN69871 和IS0 7388/1 机床上,但DIN 69871 和IS0 7388/1刀柄可以安装在ANSI B5.50 型机床上。 二、1:10 的HSK 真空刀柄
五轴加工中心培训课程
五轴加工中心培训课程 五轴加工中心培训课程 多轴(四、五轴)加工技术培训课程是三轴数控加工技术课程的补充和提 高,符合国家职业标准对于高级工和技师的要求? 二、培训目标 通过学习数控多轴(四、五轴)加工技术,使学员能够了解多轴加工的基础知识,会操作五轴机床。在专业技能上达到完成零件加工工艺制定、编制多轴加工程序、利用多轴仿真软件实现产品加工的安全保证、能使用多轴(四、五轴)机床加工复杂零件的能力。 三、培训时间:2个月 四、课程内容: (一)软件部分 1、UG NX多轴编程 2、MasterCAM多轴编程 (二)机床部分 1、四、五轴加工介绍,机床结构与运动关系,各种机床的加工特点,运用场合及优势; 2、定轴加工(3+2)在模具及零件加工中的应用; 3、NX软件刀具轴的控制方法; 4、四、五轴实例分析及案例讲解; 5、机床仿真; 6、(可变轴铣、外形轮廓铣);
(1)多种刀轴设置⑵插补刀轴设置⑶ 垂直于部件 17、四、五轴联动工件铣削; 18、四、五轴机床的仿真加工; 19、独立完成加工与编程。 课程特点: (1)同时学习到四轴与五轴加工中心的编程与加工技术,课程更超值,学习效率更高; ⑵采用流行的数控编程软件,Mastercam、UG PM等,方便已有软件基础的学员进行学习; 多轴(五轴)加工培训大纲 一、培训课程性质 多轴(五轴)加工是数控加工技巧中很重要的一个部分,该项技巧在航空航天、汽车、船舶、医疗、模具、轻工、高精密仪器等制作领域得到广泛利用。随着对产品的要求千锤百炼:产品的结构形势日趋复杂,生产效率不断前进,数控机床的更新换代,控制数控多轴加工技巧已经突显出它的重要作用。然由于受到机床硬件前提和师资力量不足的限制,职业院校开设的数控加工课程内容多仅限于三轴加工、理论性比较强,很少涉及数控多轴加工的内容,实战内容比较少,所以使得很多学生不得不在参加工作以后才接触到多轴设备和实战经验。从而影响了他们的工作效率和企业的生产定单。为了满足企业加工需求,在数控教学、培训中开设数控多轴(五轴)加工技巧课程已是迫在眉睫。 多轴(五轴)加工技巧培训课程是三轴数控加工技巧课程的补充和前进,契 合国家职业标准对于高级工和技师的请求。该课程是奥林匹克数控多轴(五轴)加工技巧培训的必修课程,通过考核后,由浙江省机械装备制造技术创新服务平台培训中心颁发数控多轴(五轴)加工技巧培训证书;该培训为全国数控技巧大赛供给技巧支撑和保障。 二、培训目标 通过学习数控多轴(五轴)加工技巧,使学员能够懂得多轴加工的工艺知识,熟练操作四轴、五轴机床。在专业技巧上达到完成零件加工工艺制定、编 制多轴加工程序、利用多轴仿真软件实现产品加工的安全保证、能应用多轴机床加工复杂
数控机床操作实训教学大纲
《数控车床操作实训》教学大纲 一、课程说明 学时数: 75学时 适用专业:数控加工专业、模具设计与制造加工专业 曾用名:《数控车床实训》、《数车实训》 二、实训配套教材: 《数控车床加工工艺与编程操作》 主编:任国兴 出版社:机械工业出版社 三、本实训课的性质、任务与目的 《数控车床操作实训》课是一门为产品加工工艺过程实现现代化的实践课,是模具设计与制造加工专业、数控加工专业学生重要的技能实训课程,是今后学习其他数控加工不可缺少的基础技能课程。其任务与目的是培训学生掌握数车的基本操作技能及设备的调整;正确使用工具、夹具、量具、刃具;具备一定的专业知识;培养遵守操作规程、安全文明生产的良好习惯;结合数控特点培养学生的创新能力及良好的职业道德。 四、本实训课的基本理论 本实训课基于金属切削机床、金属材料学、金属切削刀具与切削原理、机械制造工艺、数控编程等理论,以数控车床的基本操作技能展开实训。 五、实训方式与基本要求 1、实训方式:以实际操作为实训方式。
2.、基本要求:了解数控车床实训教学的任务和特点;了解本工种的工作内容及机械加工的知识;了解安全文明生产知识和设备管理制度;了解数控加工技术的发展前景;掌握数控车床的基本操作技能;能够独立编写加工中等难度零件的程序。 3.、分方向中级考证的专业通过考核达到数车中级的操作技能水平。 六、实训项目的设置与内容提要
七、考核方式与成绩评定 (1)学完本大纲规定的全部(或部分)课题内容,应进行相应水平的实际操作考核(实践考核)。 (2)学期考核,按平时作业成绩占50%,考核成绩占50%进行成绩评定。 (3)职业技能鉴定: 1、本大纲规定考核的职业资格名称:数控车床操作工 2、考核等级:四级/中级工 3、考核标准:按“数控车工国家职业标准”的要求进行考核。
加工中心使用维修须知
数控加工中心是当代高新技术,是机、电、光、气一体化的结晶,电气复杂,管路交叉林立,数控系统五花八门,,故障现象也是千奇百怪,各不相同,特别是大型、重型数控机床,价格昂贵,安装调整时间长。 大型数控机床内有成千上万只元器件,若其中有一个元件有故障,就会引起机床的不正常现象,还有导线的连接、管子的连接,有一点疏忽就会出问题,再加上大型、重型数控机床体积庞大,在无恒温厂房条件下使用,环境的影响很容易引发故障。为此,数控机床“维修难”的问题就摆在我们的眼前。小编特意求助了数控机床领域从业多年的老师傅,让我们一起看看老师傅的意见吧。 当前,国内引进和制造了许多的数控机床,如何迅速查找故障,消除隐患,并及时排除之?怎样才能维修好这些昂贵的设备?首先要有高度的责任心和不怕困难的精神;其次,要努力掌握数控基础知识,根据多年维修数控机床的实践,主要应多看、多问、多记、多思、多练,逐步提高自己的技术水准和维修能力,才能适应各种较复杂的局面,解决困难的问题,要修好数控机床应做到以下几个方面。 (一)要多看 ①要多看数控机床资料要多看,要了解各种数控系统和PLC可编程序控制器的特点和功能;要了解数控系统的报警及排除方法;要了解NC、PLC机床参数设定的含义’要了解PLC的编程语言;要了解数控编程的方法;要了解控制面板的操作和各菜单的内容;要了解主轴和走刀电机的性能和驱动器的特征等,往往数控机床资料一大堆,怎么看?主要应突出重点,搞清来龙去脉,重点是熟悉数控系统的基本组成和结构,掌握方框图。随机资料应通读,但每部分内容要
有重点地了解、掌握。由于数控系统内部线路图比较复杂,而制造商均不提供。因此也不必详细地搞清楚。比如NX-154四轴五联动叶片加工机床上采用A-Bl0系统,要重点了解每部分的作用、各板子的功能、接口的去向及LED灯的含义等。现在数控系统型号多、更新快,不同的制造厂、不同型号往往差别很大。要了解其共性个性和特殊性。一般熟悉维修SIEMENS数控系统的人不见得会熟练排除A-B系统的故障,因此,要多看,不断学习、更新知识。 加工中心修理维护 成海XK7132数控机床 ②要多看电气图、分析电气图 对于每一个电气元件,比如接触器、继电器、时间继电器等以及PLC的I/O 接口,要在电气图上一一标明。举一个简单例子来说,比如1A1为液压泵电机1M启动的接触器,一般在图下注出其常开、常闭触点的去向。因此,可对其对应的某页上的常开或常闭触点1A1,标明内容为液压泵电机开,对于大型的数控机床的电气图有几十页,甚至上百页。要看懂,表明每个元件的功能要花很长时间。有时,一、二次看可能还搞不清楚该元件的作用,要多看等以后消化后再写上。因此,刚才讲到的启动液压泵电机1M,也应清楚标明是PLC的哪一处输出带动接触器1A1动作的,要做到来龙去脉一清二楚。对电气线路图中的某些方框图,比如每个轴的驱动器,只是一个方框图,只要了解某控制条件(通、断情况),对于详细的东西等可等有空再研究、考虑。各个国家的电气符号是不一样的,就首先要清楚了解。对于制造厂所编写的厚厚的几本PLC语句表,也要多看,掌握其编程语言,在看懂的基础上进行中文注译。这样可以大大节省以后
CNC 刀柄标准
CNC 刀柄标准 加工中心的主轴锥孔通常分为两大类,即锥度为7:24 的通用系统和1:10 的HSK 真空系统。 7:24 锥度的通用刀柄 锥度为7:24 的通用刀柄通常有五种标准和规格,即NT(传统型)、DIN 69871(德国标准)、IS0 7388/1 (国际标准)、MAS BT(日本标准)以及ANSI/ASME(美国标准)。NT 型刀柄德国标准为DIN 2080,是在传统型机床上通过拉杆将刀柄拉紧,国内也称为ST;其它四种刀柄均是在加工中心上通过刀柄尾部的拉钉将刀柄拉紧。目前国内使用最多的是DIN 69871 型(即JT)和MAS BT 型两种刀柄。DIN 69871 型的刀柄可以安装在DIN 69871 型和ANSI/ASME 主轴锥孔的机床上,IS0 7388/1 型的刀柄可以安装在DIN69871 型、IS0 7388/1 和ANSI/ASME 主轴锥孔的机床上,所以就通用性而言,IS0 7388/1 型的刀柄是最好的。 (1)DIN 2080 型(简称NT 或ST) DIN 2080 是德国标准,即国际标准ISO 2583 ,是我们通常所说NT 型刀柄,不能用机床的机械手装刀而用手动装刀。 (2)DIN 69871 型(简称JT、DIN、DAT 或DV) DIN 69871 型分两种,即DIN 69871 A/AD 型和DIN 69871 B 型,前者是中心内冷,后者是法兰盘内冷,其它尺寸相同。 (3)ISO 7388/1 型(简称IV 或IT) 其刀柄安装尺寸与DIN 69871 型没有区别,但由于ISO 7388/1 型刀柄的D4 值小于DIN 69871型刀柄的D4 值,所以将ISO 7388/1 型刀柄安装在DIN 69871 型锥孔的机床上是没有问题的,但将DIN 69871 型刀柄安装在ISO 7388/1 型机床上则有可能会发生干涉。 (4)MAS BT 型(简称BT) BT 型是日本标准,安装尺寸与DIN 69871、IS0 7388/1 及ANSI 完全不同,不能换用。BT型刀柄的对称性结构使它比其它三种刀柄的高速稳定性要好。(5)ANSI B5.50 型(简称CAT) ANSI B5.50 型是美国标准,安装尺寸与DIN 69871、IS0 7388/1 类似,但由于少一个楔缺口,所以ANSI B5.50 型刀柄不能安装在DIN69871 和IS0 7388/1 机床上,但DIN 69871 和IS0 7388/1刀柄可以安装在ANSI B5.50 型机床上。 二、1:10 的HSK 真空刀柄 HSK 真空刀柄的德国标准是DIN69873,有六种标准和规格,即HSK-A、 HSK-B、HSK-C、HSK-D、HSK-E 和HSK-F,常用的有三种:HSK-A (带内冷自动换刀) 、HSK-C (带内冷手动换刀)和HSK-E(带内冷自动换刀,高速型)。7:24 的通用刀柄是靠刀柄的7:24 锥面与机床主轴孔的7:24 锥面接触定位连接的,在高速加工、连接刚性和重合精度三方面有局限性。 HSK 真空刀柄靠刀柄的弹性变形,不但刀柄的1:10 锥面与机床主轴孔的1:10 锥面接触,而且使刀柄的法兰盘面与主轴面也紧密接触,这种双面接触系统在高速加工、连接刚性和重合精度上均优于7:24 的刀柄 HSK 刀柄有A 型、B 型、C 型、D 型、E 型、F 型等多种规格,其中常用于加工中心(自动换刀)上的有A 型、E 型和F 型。A 型和E 型的最大区别就在于:1.A 型有传动槽而E 型没有。所以相对来说A 型传递扭矩较大,相对可进行一
加工中心操作培训教材
GDM-650加工中心操作培训内容 第一阶段设备基本情况介绍及机床开关机等初步操作。 第一节数控机床基本情况介绍 一、数控机床的分类 (一)按加工方式和工艺用途分类 1、普通数控机床 普通数控机床一般指在加工工艺过程中的一个工序上实现数字控制的自动化机床,如数控铣床、数控车床、数控钻床、数控磨床与数控齿轮加工机床等。普通数控机床在自动化程度上还不够完善,刀具的更换与零件的装夹仍需人工来完成。 2、加工中心 加工中心是带有刀库和自动换刀装置的数控机床,它将数控铣床、数控镗床、数控钻床的功能组合在一起,零件在一次装夹后,可以将其大部分加工面进行铣、镗、钻、扩、铰及攻螺纹等多工序加工。由于加工中心能有效地避免由于多次安装造成的定位误差,所以它适用于产品更换频繁、零件形状复杂、精度要求高、生产批量不大而生产周期短的产品。 (二)按运动方式分类 1、点位控制数控机床 点位控制是指数控系统只控制刀具或工作台从一点移至另一点的准确定位,然后进行定点加工,而点与点之间的路径不需控制。采用这类控制的有数控钻床、数控镗床和数控坐标镗床等。
2、点位直线控制数控机床 点位直线控制是指数控系统除控制直线轨迹的起点和终点的准确定位外,还要控制在这两点之间以指定的进给速度进行直线切削。采用这类控制的有数控铣床、数控车床和数控磨床等。 3、轮廓控制数控机床 也称连续轨迹控制,能够连续控制两个或两个以上坐标方向的联合运动。为了使刀具按规定的轨迹加工工件的曲线轮廓,数控装置具有插补运算的功能,使刀具的运动轨迹以最小的误差逼近规定的轮廓曲线,并协调各坐标方向的运动速度,以便在切削过程中始终保持规定的进给速度。采用这类控制的有数控铣床、数控车床、数控磨床和加工中心等。 (三)按控制方式分类 1、开环控制系统 开环控制系统,是指不带反馈装置的控制系统,由步进电机驱动线路和步进电机组成。数控装置经过控制运算发出脉冲信号,每一脉冲信号使步进电机转动一定的角度,通过滚珠丝杠推动工作台移动一定的距离。 这种伺服机构比较简单,工作稳定,容易掌握使用,但精度和速度的提高受到限制。 2、半闭环控制系统 半闭环控制系统是在开环控制系统的伺服机构中装有角位移检测装置,通过检测伺服机构的滚珠丝杠转角间接检测移动部件的位
加工中心操作工职业资格培训与鉴定教学大纲
《加工中心操作工职业资格培训与鉴定》教学大纲 (适用于加工中心操作工职业资格培训与鉴定) 一、本职业培训与鉴定的性质和任务 国家《劳动法》和《职业教育法》业已确立了职业资格证书制度的法律地位,规定由国家确定职业分类,对规定的职业制定职业技能标准,实行职业资格证书制度,从事技术工种的劳动者,就业前或上岗前必须接受必要的培训,由经过国家劳动行政部门批准的考核鉴定机构负责对劳动者实施职业技能考核鉴定。 加工中心是机械制造系统中一种重要的高效率、高精度与高柔性特点的自动化加工设备,可有效解决复杂、精密、小批多变零件的加工问题,充分适应现代化生产的需要。随着加工中心的发展与普及,急需大量高素质的能够操作加工中心机床,进行工件多工序组合切削加工的加工中心操作工。基于此,加工中心操作工职业资格培训与鉴定面向全院学生和全社会从事及准备从事本职业的人员,依据《加工中心操作工国家职业标准》的规定,开发加工中心操作技能,提高职业技术素质,增强就业能力和工作能力。 本职业培训与鉴定的主要任务是:通过在培训现场进行的实际操作训练,进一步了解数控机床的组成、性能、结构和特点,掌握加工中心的基本操作、日常维护保养、简单故障和加工中不正常现象的排除方法,熟悉加工中心加工零件的全过程,能较熟练地使用加工中心的全部功能完成中等复杂程度及以上零件的加工,初步具备在现场分析、处理工艺及程序问题的能力,普遍达到中级(国家职业资格四级)加工中心操作工的职业资格水平,相当一部分达到高级(国家职业资格三级)加工中心操作工和少部分达到技师(国家职业资格二级)的职业资格水平,并通过职业资格考核鉴定获取相应的职业资格证书。 二、本职业的知识与技能要求 按照《加工中心操作工国家职业标准》中关于各职业等级的工作要求,提出如下知识和技能方面的基本要求。其中,中级、高级、技师的知识和技能要求依次递进,高级别包括低级别的要求。
加工中心培训教程
加工中心培训教程 Ⅰ安全知识 一、一般的警告和注意 1.我公司机床没有安全防护门,为了安全,在自动和MDI方式下必须合上安全门才能执行程序。机床设有三色报警灯,机床正常并且主轴和驱动轴静止时用绿灯指示,当机床处于运动中时用黄灯指示,而当有报警或程序执行完毕时将点亮红色灯。 2.急停用于危险状况下终止机床轴运动和外围运动设备,系统MDI键盘上的RESET按钮用于CNC复位或者消除系统报警。这两种情况都不会引起坐标位置的丢失,但将使系统终止正在运行 的程序而进入复位状态(坐标系回刀G54、刀具补偿丢失、模态代码回到开机状态)。 3.零件加工前,一定要首先检查程序的坐标系、刀补数据等。执行程序必须从程序开始部分执行。加工前,一定要通过试车保证机床正确工作,例如在机床上不装工件和刀具时利用单程序段、进给倍率检查机床的正确运行。如果未能确认机床动作的正确性,机床有可能发生误动作,从而引起工件或机床本身的损坏,甚至伤及用户。 4.当使用刀具补偿功能时,请仔细检查补偿方向和补偿量。如果指定了不正确的数据操作机床,机床有可能发生误动作,从而引起工件或机床本身的损坏,甚至伤及用户。 5.在机床通电后,CNC单元尚未出现位置显示或报警画面之前,请不要碰MDI 面板上的任何键。BEIJING- FANUC Oi-MB 操作说明书MDI 面板上的有些键专门用于维护和特殊的操作。按下这其中的任何键,可能使CNC 装置处于非正常状态。在这种状态下启动机床,有可能引起机床的误动作。 二、与编程相关的警告和注意 在编程之前,请认真阅读FANUC操作说明书和编程说明书,以确保完全熟悉其内容。 1.坐标系的设定 如果没有设置正确的坐标系,即使指定了正确的指令,机床仍有可能发生误动作。这种误动作有可能损坏刀具、机床、工件甚至伤害用户。 2.非线性插补定位 当使用G0进行非线性插补定位时(在起点和终点之间,利用非线性运动进行定位),在编程之前请仔细确认刀具路径的正确性。这种定位包括快速移动,如果刀具和工件发生了碰撞,有可能损坏刀具、机床、工件甚至伤害用户。 FANUC 系统G0运动是非直线运动,从A 点到B点先沿Y向45°移动到X点的水平线,再 沿X 向直线移动到目标B点。 3.英制/公制转换 输入的英制和公制之间转换并不转换例如工件的原点、参数和当前的位置这些数据的测量单位。因此,在启动机床之前,要确定采用何种测量单位。如果试图采用不正确的数据进行操作会导致刀具、机床、工件的损坏,甚至伤及用户。 4.绝对值/增量值方式 如果用绝对坐标编制的程序在增量方式下运行时,或者反过来,机床有可能发生误动作。 5.平面选择
加工中心操作技能训练培训大纲
《加工中心操作技能》实训大纲 一、此培训的性质、目的和任务 此培训是一门数控技能培训课程。 员工通过本课程的学习能独立操作加工中心,完成中级工复杂程度的零件的程序编制和加工全过程。 二、培训的基本要求 l、熟练操作加工中心。 2、能理解数控机床的故障报警信息,能处理常见的报警信息。 3、根据加工图纸能确定简单工艺路线,根据数控机床的功能,熟练编制初, 中级工复杂程度的工件的数控加工程序。 4、正确装夹工件和刀具,正确设定加工起点,正确处理粗、精加工的工序 关系和切削用量。 5、正确测量加工工件的工序尺寸、余量和工件最终尺寸。 6、能分析加工程序的错误原因,并进行修正。 7、能正确使用下列工具和量具:游标卡尺、千分尺、内径量表、百分表、 杠杆式百分表、塞尺、磁性表架、键槽铣刀和立铣刀、弹簧夹头、、压板、平口钳等。 8、了解加工中心基本操作知识。 三、培训要求与内容 课题1加工中心的操作入门 培训要求:掌握加工中心操作的基本知识。 培训内容:1、熟悉加工中心操作面板和各控制键的功能。 2、熟悉手动操作步骤和速度的控制 课题2加工中心程序编制基础 培训要求:掌握机床坐标系的概念及命名原则;数控加工程序的格式。 培训内容:1、机床坐标系、工件坐标系、绝对坐标系、相对坐标系。 2、加工程序的结构;程序段的格式及编程格式。 课题3工件坐标系的建立 培训要求:1、掌握工件及刀具在加工中心上的正确安装、校正测量。 2、掌握工件坐标系建立方法和数值的输入 培训内容:l、根据被加工零件,正确选择寻边器的形式。 2、掌握工件坐标系建立的方法和数值的输入方法。 课题4单一外形工件加工
培训要求:掌握数控程序的编制、输入和验证的方法及加工中各参数意义和设置方法。 培训内容:1、熟悉数控机床操作面板各字母键的意义,各功能界面的调用及其含义。 2、熟悉数控机床程序与外部的输入、输出方法。 3、根据零件图纸,加工工艺确定工件坐标系。 4、根据所用刀具确定刀具参数。 5、根据尺寸公差及加工工艺确定刀具尺寸参数。 课题5多外形工件加工 培训要求:掌握多外形工件加工的程序编制及试加工的正确方法。 培训内容:1、子程序的调用方法。 2、残料的去除。 课题6 孔加工 培训要求:掌握钻孔、镗孔、攻螺纹的程序编制及试加工的正确方法。 培训内容:1、孔加工各指令的介绍及应用。 2、孔加工程序编制时注意事项。 课题7型腔加工 培训要求:掌握型腔加工程序编制及试加工的正确方法。 培训内容:型腔加工编程及加工。 课题8多工件坐标系应用 培训要求:掌握应用多工件坐标系加工零件程序的编制及试加工的正确方法。培训内容:应用多工件坐标系加工零件的程序的编制及加工。 课题9 综合件练习 培训要求:掌握典型零件的程序编制及试加工的正确方法(零件编程应包括循环指令及子程序)。 培训内容:综合零件编程及加工。 制定: 执笔人: 审定人: 2015-6-12
数控加工中心的日常保养及维护示范文本
数控加工中心的日常保养及维护示范文本 In The Actual Work Production Management, In Order To Ensure The Smooth Progress Of The Process, And Consider The Relationship Between Each Link, The Specific Requirements Of Each Link To Achieve Risk Control And Planning 某某管理中心 XX年XX月
数控加工中心的日常保养及维护示范文 本 使用指引:此操作规程资料应用在实际工作生产管理中为了保障过程顺利推进,同时考虑各个环节之间的关系,每个环节实现的具体要求而进行的风险控制与规划,并将危害降低到最小,文档经过下载可进行自定义修改,请根据实际需求进行调整与使用。 数控加工中心的设备均是高精度自动化的,而且价格 比较昂贵,如何在长期使用中,保证设备的质量与安全, 一直是数控加工中心管理人员关心的问题。本文主要概述 数控加工中心的一些情况以及重点讲述以延长设备使用寿 命为目的的数控加工中心日常的保养和维护工作。 近些年来,科学和经济都得到了飞快地发展,机械制 造随着社会的发展变得越来越精确,人们的生活得到很大 地提高的同时,对于事物提出了越来越高的要求,数控设 备应运而生。数控加工中心及机械加工、计算机、自动控 制、多种类型为一体的综合体,因此讲解数控加工中心的 日常保养维护是十分必要的。
数控加工中心概述 柳州五菱柳机动力有限公司(简称五菱柳机),是我国最大的微车发动机生产基地,具备国内一流的发动机设计、开发、制造、服务水平,为国家大型二类企业,中国机械工业企业500强之一,目前一直致力于成为国际先进、国内一流的发动机生产基地,为推动中国汽车产业的发展做出了巨大贡献。 目前我公司的数控加工中心主要由数控装置、伺服驱动装置、测量反馈装置和机床本体四个部分组成,加工中心主要是采用数字信号来控制零件的加工生产零件或设备。 数控加工中心的核心系统是数控装置,由硬件和软件来组成。工作流程如:首先先是数控装置接受机床输入的控制信号代码,然后装置经过输入、寄存及存储等将指令变为对伺服驱动系统的控制。
加工中心刀柄
加工中心刀柄介绍 随着加工中心在零件机械加工中的运用越来越普遍,加工中心刀柄的使用也越来越多。但是,刀柄的种类有很多,我们必须选择精度足够的、经济的、使用方便的刀柄用于零件的加工,这就要求我们对刀柄有全面的了解。 刀柄,用于连接加工中心主轴与切削刃具的装备。这就如同人用手拿着笔写字,人是机床,笔是切削刃具,手就是刀柄。 如图1所示,由于刀柄是与主轴连接、与刀具连接,所以刀柄的分类也主要有两种分类。按与加工中心主轴的连接方式分类:分为7:24锥度刀柄和1:10锥度刀柄;按刀柄与刀具的连接方式分类:分为侧固式刀柄、弹簧夹套式刀柄、液压刀柄、热涨刀柄等。 图1 一、刀柄与主轴连接方式 加工中心的主轴和刀柄之间通常采用锥度配合。锥度配合特点是具有定心性好、间隙或过盈可以方便地调整等。 图2 锥度C=(D-d)/L,如图2。 因此刀柄按锥度也分为7:24和1:10两大类。 (一)、7:24锥度刀柄定位原理及特点 1、7:24锥度刀柄定位原理
图3 图4 7:24锥度刀柄通过长锥面限制X、Y方向的移动及转动,Z方向的移动5个自由度,通过拉力F与锥面产生的摩擦力限制Z轴的转动(如图3、图4所示),从而实现刀柄的完全定位,此定位方式刀柄端面与主轴端面有间隙,如BT系列刀柄。 2、7:24锥度刀柄的特点 优点: 1)、不自锁,可以实现快速装卸刀具; 2)、刀柄的锥体在拉杆轴向拉力的作用下,紧紧地与主轴的锥面接触。 3)、7:24锥度的刀柄在制造时只要将锥角加工到高精度即可保证连接的精度,所以成本相应比较低,而且使用可靠。 缺点: 1)、单独的锥面定位。7:24锥度刀柄连接锥度较大,锥柄较长,导致a、换刀行程长,换刀时间慢;b、刀柄重量增加,机床损耗功率增加。 2)、在高速旋转时,由于离心力的作用,主轴前端锥孔会发生膨胀,膨胀量的大小随着旋转半径与转速的增大而增大,见图5,但是与之配合的7:24锥度刀柄由于是实心的所以膨胀量较小。(如:在离主轴中心r=0.02m处,一质量为m=100g的质点,在机床主轴转速为n=12000r/min时,所受到的离心力为F=3158.3N,即为315.83Kg的力。)
《数控加工技术》教学大纲
《数控加工技术》(单元教学)教学大纲 一、课程教学目的 本课程是一门以实训教学为主的课程。其教学目的是: 1. 熟悉了解数控车床、数控铣床、数控加工中心的结构组成及工作原理。 2. 熟练掌握待加工零件的装夹、定位、加工路线设置及加工参数调校等实际操作工艺。 3. 熟练掌握阶梯轴、成型面、螺纹等车削零件和平面轮廓、槽形、钻、镗孔等类型铣削零件的手工编程技术以及曲面零件的自动编程技术。能分析判断并解决加工程序中所出现的错误。 4. 熟练操作数控车、数控铣床、并能加工出中等复杂程度的零件。 5. 能初步使用加工中心机床,了解刀库及其设置,了解加工中心的加工过程与特点。 6. 具有对零件加工质量的初步控制和分析、处理能力。 二、课程教学要求 要求学生能在 5周内完成数控车床、数控铣床、数控加工中心的基本编程训练以及典型零件的实际加工训练;掌握自动编程的方法,能熟练操作数控车床、数控铣床;完成指定的实训内容、填写实训报告、加工工艺卡片等工艺文件。三、课程教学适用的专业与年级 适用的专业:高职数控、模具等机械类各专业 适用的年级:二 ~三年级 四、课程的总学时和总学分 课程总学时 140(5周),其中理论讲授34学时,本课程所修学分占 5 学分,其具体安排可参见下表:
五、本课程与其他课程的联系与分工 本课程学习时要求学生已进行过机加工基本实训、制图与 CAD等课程的学习,在具备一定的CAD绘图基础、切削加工的基础后才能进行本课程的学习。本课程以实训教学为主, 但必要的理论讲授是不可缺少的。 六、实训场地、材料及仪器设备的准备工作 本课程实训在现代制造技术中心和CADCAM计算机机房进行。 实训设备: CJK6032数控车床、CK616I数控车床、长城数控车、T6数控车床等 ZJK7532A-1数控铣床、XD-40 数控铣床等 XH713A立式加工中心、TH6350 卧式加工中心 LV-800、V-60立式加工中心、CH6145A车削中心等 计算机(自动编程训练用) 实训材料: 120X100X20 板料、φ40X200圆形棒料若干 实训前必须保证机床状况良好,并检查冷却与润滑液面状况,保证实训能顺利进行 七、课程实训教学的主要内容及方式 教学内容简介 1.实训动员,安技教育,制定计划 1)实训动员:明确实训目的与任务要求,端正实训态度,宣布实训纪律、制度、计划。
数控加工中心检修的方法
数控加工中心检修的方法 摘要: 随着数控加工中心在机械加工中的普及,加工中心的检修成为设备管理重要的一个环节。做好数控加工中心的检修不但可以全面排查设备问题而且还能及时发现并消除设备潜在的隐患。系统完善的检修方法日益成为减少机床故障、提高机床利用率、保证生产的重要部分。本文主要论述了加工中心检修的思路和具体方法。 由于加工中心在长期使用过程中的磨损和老化,如果不注意保养,加工中心会一直处于“亚健康”状态下运行。定期对机床进行检修可使机床保持良好的运行状态,延缓劣化过程,降低机床故障发生率,从而保证机床利用率。加工中心虽然种类繁多结构复杂但其大致可分为机械部分和电气部分。以下就从机械和电气两部分论述其检修的方法。 1 加工中心的概述 数控加工中心是一种自带刀库并且能够自动交换刀具,对加工零件能够在一定范围下进行多工序的加工操作的机床。数控加工中心从结构上划分可分为以下几个主要组成部分。 ( 1) 基础部件。由床身、立柱、工作台等组成。基础部件不仅要承受在切削加工时所产生的动载荷,还要承受机床本身的静载荷,所以这就要求数控加工中心的基础部件要有足够的刚性。 ( 2) 主轴部件。由主轴电动机、主轴、主轴箱、主轴轴承等零部件组成。 ( 3) 数控系统。数控系统的主要部分由可编程控制器、CNC 装置、伺服驱动模块和伺服电机等部件组成。 ( 4)自动换刀系统( ATC) 。自动换刀系统是数控加工中心区别于普通数控机床的特征装置,它可以解决加工零件一次装夹后的多个工序连续进行加工过程中,工序和工序之间的刀具选择、自动储存和交换任务。 ( 5) 其他辅助部件。包括液压单元、润滑单元、冷却单元、气动单元和排屑器等部件。 2 机械部分检修 数控加工中心在长期的使用后其机械部件很容易松动磨损。定期检修发现机床隐藏的问题,并对其进行适当调整,可以恢复其加工精度,延长使用寿命。机械部分检修可以分以下几个部分。 ( 1) 几何精度检查。数控加工中心的几何精度是其加工工件精度的保证,因此需要定期对其进行检查和调整。可按照数控加工中心几何精度表对各轴的几何精度进行检查,并对不合格的事项进行调整。几何精度的校准主要有机械校准和参数补偿两种方式。对于误差不大的情况可以采用参数补偿的方式,如果误差较大就要从机械方面进行调整。
加工中心刀柄的种类和用途
加工中心刀柄的种类和用途 刀柄是机床和刀具的连接体,刀柄是影响同心度和动平衡一个关键环节,千万不能将它当成一般的部件来看待。同心度可以决定刀具在旋转一周的情况下各切刃部分的切削量是否均匀;在主轴旋转时动不平衡将产生周期性的震动。 今天和大家聊一聊关于加工中心刀柄的知识。如今数控机床在工厂里得到了广泛的应用,这些机床和使用的工具来自世界各地,有着不同的型号和标准。你知道加工中心BT 刀柄中的7:24是什么意思吗?你又知道BT、NT、JT、IT、CAT是什么标准吗?往下看↓↓一、根据主轴锥孔分两大类 按加工中心主轴装刀孔的锥度通常分为两大类: ①锥度为7:24的SK通用刀柄; ②锥度为1:10的HSK真空刀柄。 1、锥度为7:24的SK通用刀柄 7:24指的是刀柄锥度为7:24,为单独的锥面定位,锥柄较长。锥体表面同时要起两个重要作用,即刀柄相对于主轴的精确定位以及实现刀柄夹紧。 优点:不自锁,可以实现快速装卸刀具;制造刀柄只要将锥角加工到高精度即可保证连接的精度,所以刀柄成本相对较低。 缺点:在高速旋转时主轴前端锥孔会发生膨胀,膨胀量的大小随着旋转半径与转速的增大而增大,锥度连接刚度会降低,在拉杆拉力的作用下,刀柄的轴向位移也会发生改变。每次换刀后刀柄的径向尺寸都会发生改变,存在着重复定位精度不稳定的问题。 锥度为7:24的通用刀柄通常有五种标准和规格: ①国际标准 IS0 7388/1 (简称IV或IT); ②日本标准 MAS BT(简称BT); ③德国标准 DIN 2080型(简称 NT或ST); ④美国标准 ANSI/ASME(简称CAT); ⑤DIN 69871 型(简称JT、DIN、DAT或者DV); 拉紧方式:NT型刀柄是在传统型机床上通过拉杆将刀柄拉紧,国内也称为ST;其它四种刀柄均是在加工中心上通过刀柄尾部的拉钉将刀柄拉紧。 通用性: ①目前国内使用最多的是DIN 69871型(即JT)和日本MAS BT 型两种刀柄;
加工中心培训大纲
加工中心培训纲要 一、操作需知 1.1 安全需知 (1) 如何操作CNC 立式綜合加工中心機。 (2) 在操作本機器前,請仔細閱讀CNC 控制器之說明書,以確保對CNC 系統進行安全操作。 (3) 在操作本機器前,請仔細閱讀各手冊內容,只有在您完全理解了這 一系統,熟悉了安全操作步驟後才能操作本機器,以避免人員受傷 或機器設備遭受損害。 (4) 本機器提供許多安全設計以避免人員受傷或設備遭受損害。但操作 者不能完全依賴這些安全裝置,而必須詳讀本手冊內容,並充份了 解操作機台前所必備的特殊注意事項,才可以確保安全。 (5) 操作說明書未加說明的操作應當認為是不可能的。 (6) 本機器是一種機電合一的高精密科技產品,故機台周邊的環境,定 期的保養維護及操作者的使用水準,對本產品的使用壽命有相當程 度的影響。 (7) 操作說明是按假定您的機器是配備了全部的操作機能的情形來編 寫的。在操作機器前,請確認您的機器可使用的機能。 1.2 操作注意事項 A. 開機前檢查: (1) 檢查主電源接線是否正確?(參閱電氣線路手冊之電源入力迴路圖) (2) 檢查供電電源電壓是否正確?確認電源電壓無誤後,才能執行開機的 動作。(本機器之使用電壓是AC380V) (3) 檢查機器之安全護罩是否完整? (4) 檢查各操作門及維護門是否已關閉? (5) 檢查電氣箱門是否己關閉? (6) 檢查各部品油量是否足夠? (7) 檢查切削水量是否足夠? (8) 檢查氣壓壓力是否足夠? B. 開機後檢查: (1) 先按原點復歸模式按鈕,執行進給軸機械原點復歸動作(如 非絕對式的馬達)。 (2) 將主軸和進給軸以1/2 或1/3 的極限速度在自動模式下運 轉10~20 分鐘,檢查其動作是否正常? C. 校刀試車前檢查: (1) 檢查工件安裝是否確實、適當? (2) 檢查刀具是否確實鎖緊、夾緊? D. 操作前檢查: (1) 檢查工件座標系設定值是否正確? (2) 檢查刀具補正值是否正確? (3) 檢查程式是否正確?特別注意正負符號及小數點。