粗苯工艺计算(模板)
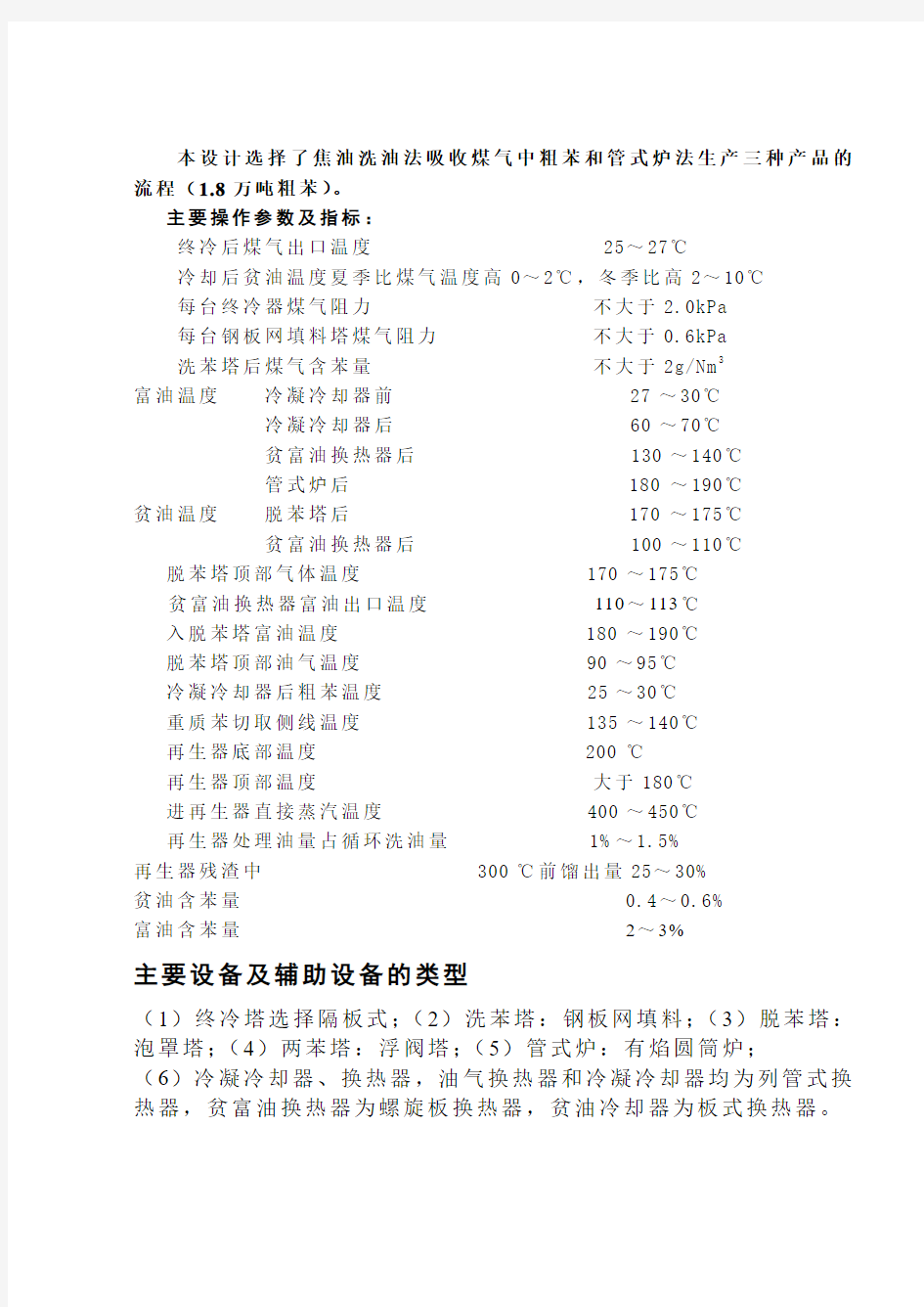

本设计选择了焦油洗油法吸收煤气中粗苯和管式炉法生产三种产品的流程(1.8万吨粗苯)。
主要操作参数及指标:
终冷后煤气出口温度25~27℃
冷却后贫油温度夏季比煤气温度高0~2℃,冬季比高2~10℃
每台终冷器煤气阻力不大于2.0kPa
每台钢板网填料塔煤气阻力不大于0.6kPa
洗苯塔后煤气含苯量不大于2g/Nm3
富油温度冷凝冷却器前 27~30℃
冷凝冷却器后 60~70℃
贫富油换热器后 130~140℃
管式炉后 180~190℃
贫油温度脱苯塔后 170~175℃
贫富油换热器后 100~110℃脱苯塔顶部气体温度 170~175℃
贫富油换热器富油出口温度110~113℃
入脱苯塔富油温度 180~190℃
脱苯塔顶部油气温度 90~95℃
冷凝冷却器后粗苯温度 25~30℃
重质苯切取侧线温度 135~140℃
再生器底部温度 200℃
再生器顶部温度大于180℃
进再生器直接蒸汽温度 400~450℃
再生器处理油量占循环洗油量 1%~1.5%
再生器残渣中 300℃前馏出量25~30%
贫油含苯量0.4~0.6%
富油含苯量2~3%
主要设备及辅助设备的类型
(1)终冷塔选择隔板式;(2)洗苯塔:钢板网填料;(3)脱苯塔:泡罩塔;(4)两苯塔:浮阀塔;(5)管式炉:有焰圆筒炉;
(6)冷凝冷却器、换热器,油气换热器和冷凝冷却器均为列管式换热器,贫富油换热器为螺旋板换热器,贫油冷却器为板式换热器。
工艺计算及设备选型计算
3.1 洗苯部分设计计算
3.1.1 终冷塔的设计计算
入终冷器煤气温度 65℃
入终冷器煤气压力 1100毫米水柱 出终冷器煤气温度 27℃
出终冷器煤气压力 900毫米水柱 根据处理粗苯的量计算此时煤气的组成。 年处理粗苯1.8万吨,即2080千克/时。
干煤量为2080
1.1%
=189吨/时。根据干煤量计算如下:
干煤气的量为1893306270?=标米3/时(28297.9千克/时) 硫化氢的量为1890.2%378?=千克/时(249标米3/时) 苯族烃的量为2080千克/时(561.3标米3/时) 煤气温度为65℃时,露点为50℃,此时水的饱和蒸汽压力为1255毫米水柱。则此时煤气中含水量为
1255
(62370249561.3)1033311001255
++++=7790标米3/时
18
7790626022.4
?=千克/时
则入终冷器煤气组成如下(忽略了微量的氨):
组 成 千克/时 标米3/时 干煤气 28297.9 62370 水蒸汽 6260 7790 硫化氢 378 249 粗苯 2080 561.3 小计 36995.9 70970.3
物料平衡 :
设终冷器出口的煤气温度为27℃,压力为900毫米水柱时,此时水蒸汽的饱和蒸汽压力为363毫米水柱。则终冷段出口水蒸气体积为:
363
(62370249561.3)2121.910333900363
++=+-标米3/时
相当于1705.1千克/时。 故终冷塔的冷凝水总量为 6260-1705.1=4554.9千克/时 则出终冷塔煤气组成为:
组 成 千克/时 标米3/时 干煤气 28297.9 62370 水蒸汽 1705.1 2121.9 硫化氢 378 249 粗苯 2080 561.3 小计 32461 65302.2 终冷塔前后煤气实际流量及煤气含苯量如下: 1、湿煤气实际流量 入塔
V 1=70970.365302.2×27327273+×10333
10333900
+=79414米3 /时
出塔
V 2=65302.264774.6×27327273+×10333
10333600
+=66671米3 /时
塔内煤气平均流量
V=
7941466671
730422
+=米3 /时 取空塔气速为1米/秒
D=
4.98=
=米
取D=5.0米,根据标准选择H=38米。
3.1.2 洗苯塔设计计算
采用三台钢板网填料塔串联操作。由于条件所限,现根据木格填料塔的计算方法换算钢板网填料。
1.原始数据及物料衡算
设出塔煤气含苯量为2克/标米3,则出塔煤气含苯量为: 623702
124.741000
?=千克/时 即33.7标米3/时
煤气进入第一台洗苯塔的温度为27℃,压力为900毫米水柱,经三台洗苯塔后,出塔压力为600毫米水柱。
则出洗苯塔煤气组成为:
组 成 千克/时 标米3/时 干煤气 28297.9 62370 水蒸汽 1705.1 2121.9 硫化氢 378 249 粗苯 124.74 33.7 小计 30505.8 64774.6 洗苯塔前后煤气实际流量及煤气含苯量如下: (1)湿煤气实际流量 入塔
V 1=65302.2×27327273+×10333
10333900
+=66011米3 /时
出塔
V 2=64774.6×27327273+×10333
10333600
+=67274.5米3 /时
(2)洗苯塔前后煤气实际含苯量
120801000
31.5166011a ?=
=克/米3 2124.741000
1.85467274.5
a ?=
=克/米3 (3)粗苯回收率
2080124.74
94%2080
η-=
=
(4)贫油富油实际含苯量及洗油量
当塔顶吸收过程达平衡,所允许的贫油最高含苯量由下式计算:
()CB CB
CB
CB m
1.25x/M .p y.P 0.0224
x 100x M M M =
-+ 式中:y —煤气出塔含苯量,a 2=1.854克/米3
x —贫油含苯量,%(质量) P —煤气压力
P=600
760804.1213.6
+=毫米汞柱 P C B —粗苯饱和蒸汽压力(30℃)
粗苯组成及分子量
% 分子量 苯 76 78 甲苯 15 92 二甲苯 4 106 溶剂油 5 120 则粗苯的平均分子量为:
100
82.27615457892106120
CB M ==+++
则在粗苯中各成分的组成为:
苯
7682.2
0.800878100?=? 甲苯
1582.2
0.134092100?=? 二甲苯
482.2
0.0310106100?=? 溶剂油
582.2
0.0342120100
?=?
P C B =
0.8008119.350.134036.670.0310120.0342 4.2101?+?+?+?=毫米汞柱
式中,119.35,36.67,12,4.2分别是苯、甲苯、二甲苯、溶剂油在30℃时的蒸汽压力,单位为毫米汞柱。 M m —洗油分子量,取为160 代入上式得:
x 1.251011.854804.1282.20.0224x 100x 82.282.2160
??? ????=-+ x=0.16613%
入塔贫油实际含苯量为:1x
C %n
=
n —平衡变动系数,为1.1~1.2。
设n=1.15,则10.16613
C %0.144%1.15
=
= 此时,平衡煤气含苯量为:
0.1441.25101y 804.1282.20.02240.1441000.14482.282.2160
??? ????=
-+ y=1.713克/米3
故塔顶吸收达到平衡时,粗苯的最高回收率为
ηm a x =1-1.713
31.51
=94.564% 最小洗油循环量为 L m i n =
max
22.4cb m P M V p ηη
式中: P C B ─30℃粗苯的蒸气压,P C B =101毫米汞柱;
p ─煤气入塔时压力,p=900
760826.1813.6
+=毫米汞柱
M
m ─洗油分子量,M
m
=160;
V─入塔时煤气流量(粗苯除外),V=10335.81标米3/时;
η─粗苯回收率,η=94%;
ηm a x─粗苯最高回收率,ηm a x =94.564%。
因此,
L
m i n =
118.216061740.994%
22.4826.1894.564%
???
??
=62655千克/时
实际洗油循环量
L=mL
m i n
式中 m─洗油多余系数,取1.5。
L=1.5 ×62655=93982.5千克/时回收的粗苯量
G=2080-124.74=1955.26千克/时富油含苯量
C
2=C
1
+
G
L
×100%=0.144%+
1955.26
93982.5
×100%=2.22%
贫油总含苯量
0.144%×93982.5=135.3千克/时富油总含苯量
1955.26+135.3=2090千克/时
(1)木格填料规格:
木格厚度 a=10毫米
木格缝隙厚 b=20毫米
木格高度 h=120毫米
(2)煤气通过木格缝隙厚度的临界温度
U k =2.32
e d μγ
式中 μ— 煤气粘度,27℃时μ=0.012678厘泊;
d e — 木格填料当量直径,米; γ— 煤气密度,千克/米3。
木格填料当量直径为
d e =2b=2×0.02=0.04米
γ=30505.864774.6×27327327+×1033360010333+=0.4531千克/米3
将已知数据代入得:
U k =2.32×0.012678
0.040.4513
?=1.623米/秒
需木格填料自由截面积
F s =67274.5
3600 1.623
?=11.514米2
塔的横截面积
F= F s a b
b
+=11.514×102020+=17.271米
2
因此,塔直径为
D=
米 选D=5.0米 3.传质面积
F=
G
K P
? 式中:F —吸收面积(米2);
G —吸收粗苯数量,千克/时;
K —总传质系数,千克/米2?时?毫米汞柱; ΔP —吸收推动力,毫米汞柱; (1)吸收推动力ΔP
ΔP=
12
1
2
ln P P P ?-?? 式中:ΔP 1—塔下部吸收推动力,毫米汞柱;
ΔP 2—塔上部吸收推动力,毫米汞柱。 塔下部吸收推动力为
ΔP 1 = P g ' – P e "
式中: P g '—入塔煤气中粗苯分压,毫米汞柱;
P e "—出塔富油面上粗苯的蒸气压,毫米汞柱。 P g '的计算式为 P g '=0.0224
11
CB
a P M 式中: P 1—入塔煤气压力,P 1 =826.18毫米汞柱;
a 1—入塔煤气实际含苯量,a 1=31.51克/米3。
因此,
P g '=0.0224×31.51826.18
82.2?=7.0941毫米汞柱
P e "=0.01
2CB
CB
m c M P M 将已知各值代入得
P e "=0.01×
2.22160101
82.2
??=4.364
由此可得
ΔP 1=7.0941-4.364=2.730毫米汞柱 塔下部吸收推动力为
ΔP 2 = P g " - P e '
式中: P g " —塔出口煤气中粗苯分压,毫米汞柱;
P e '—入塔贫油面上粗苯的蒸气压,毫米汞柱。 P g "的计算式为
P g "=0.0224
22
CB
a p M 将已知各值代入得
P g "=0.0224×
6001.85476013.682.2
??
?+ ?
??=0.4063毫米汞柱 P e '的计算式为
P e '=0.01
1CB
CB
m c M P M P e '=0.01×
0.144160101
82.2
??=0.2831毫米汞柱
由此求得
ΔP 2=0.4063-0.2831=0.1232毫米汞柱
根据以上计算结果,求得吸收推动力为
ΔP=2.7300.1232
2.7300.1232
ln
-=0.842毫米汞柱
(2)总传质系数K
K=
G L
G L
K K K K +
式中: K G —气膜传质系数,千克/米2?时?毫米汞柱;
K L —液膜传质系数,千克/米2?时?毫米汞柱。 ①K G 的计算
0.066
0.752
0.628
360022.47600.0445Re Pr
Re 1000
g CB
g e e e g
D M K Nu d d Nu C ud γμ
=??
???= ???
=
塔内气体平均流量为:
V=
6601167274.5
666432
+=米3/时 空塔速度 '2
66643
0.94330.78553600u ==??米/秒 缝间流速 '
'1.5 1.41a b
u u u b
+===米/秒 塔内煤气平均密度 3246130505.8
0.472266643
g γ+=
=?千克/米3 27℃煤气粘度 0.01233μ=厘泊 1.410.040.472
Re 10002158.50.012333
??=?
=
Pr g
g
D ν=
27℃煤气的运动粘度 60.012333
26.12910100010000.472
g g
μ
νγ-=
=
=??米2/秒
标准状况下,苯族烃在煤气中的扩散系数
'0.113614g D =厘米2/秒
则当煤气的温度为27℃,平均压力为750毫米水柱时,苯族烃在煤气中的扩散系数为:
3
32
2
'
600103332732711.36141010333750273g g P T D D P T -??+??
=?
?=??? ? ?+??
?? =12.26
10-?米2
/秒
则Pr g
g
D ν==
6
626.12910 2.141612.210--?=?
0.066
0.752
0.628
0.0445Re
Pr
e d Nu C ??= ???
=0.066
0.7520.6280.040.4452158.5 2.14160.1??
??? ?
??=22.10
C —木条高度,0.1米 则气膜传质系数为:
360022.4760
g CB g e D M K Nu d =??
?6
12.21022.10.04-?=? 82.23600
0.1171822.4760
??
=?千克/米2?时?毫米汞柱
②K L 的计算
0.503
0.3240.0.1651471Re Pr l L e e D K Nu d H
d Nu C =?
???
= ?
??
Re l
l
q ν=
Pr l
l
D ν=
其中: νl —洗油运动粘度,30℃时,νl =0.0563米2/时
l q —喷洒密度,米3/米.时
q l =
L
L U γ 其中: L —洗油喷淋量,L=93982.5千克/时;
γL —洗油密度,γL =1055千克/米3; U —每层木格填料的润湿周边,米;
U=2()t F F a
-
其中 F — 塔横截面积,塔径5米,F=19.625米2;
F t —木格填料自由截面积,米2。
0.020
19.62513.080.010.020t b F F
a b ==?=++米2 ()
219.62513.081308.40.01U ?-=
=米 93982.5
0.068091308.41055l q =
=?米3/米.时 0.06809
Re 1.2090.0563
l
l
q ν=
=
=
6
0.012410l D -=?
6
60.012410
0.138710--=?=?米2/时
式中:CB γ—粗苯密度,30℃时为0.867千克/米3 Pr l
l
D ν=
6
0.0563
4059120.138710
-=
=? 所以有 0.503
0.324
0.0.165
471Re
Pr
e d Nu C ??= ???
0.503
0.324
0.0.165
0.04471 1.209
405912
26610.1??=??= ???
H —亨利系数,毫米汞柱.米3/千克
H=122
H H +
其中 H 1—塔上部亨利系数,毫米汞柱?米3/千克
H 2—塔下部亨利系数,毫米汞柱?米3/千克
H 1 =P L1/x 1
其中 P L1—入塔贫油面上粗苯蒸气压,0.3008毫米汞柱; x 1 —入塔贫油含苯量,千克/米3。
x 1= c 1γL =0.144%×1055=1.519千克/米3
H 1 =0.3008/1.519=0.198毫米汞柱?米3/千克 H 2=P L2/x 2
其中 P L2—出塔富油面上粗苯蒸气压,为4.408毫米汞柱;
x 2 —出塔富油含苯量,千克/米3。 x 2=c 2γL =2.22%×1055=22.349千克/米 3
H 2=4.408/22.349=0.197毫米汞柱?米3/千克
所以
H=122H H +=0.1980.1972
+=0.198毫米汞柱?米3/千克
将上述数据代入公式 60.1387101
26610.04660.040.198
L K -?=??=千克/米2?时?毫米汞柱
将K G 、K L 代入公式得到总传质系数 K=0.11780.04660.11780.0466?+=0.03334千克/米2?时?毫米汞柱
(3)吸收面积F
F ’=
1954.7
696310.033340.842
G K P ==??米2 每1标米3/时煤气需木格吸收面积为:
69631
1.06665302
=米2 钢板网与木格填料的比值为0.7
钢板网吸收面积F=0.7×F ’=45956米2
每1标米3/时煤气需钢板网吸收面积为:
45965
0.765302
=米2 则洗苯塔所需钢板网填料体积V=
45965
1044.4544
=米3 式中:44—钢板网的比表面积,米2/米3填料
每层填料1.5米,每段3.0米。
每段填料的体积为3.0×0.785×52=58.9米3
所需填料段数为1044.45
58.9
=17.73
每个填料塔的填料为17.73/3=6段
塔的有效高度H=6350.6 6.027
?+?+=米
3.2 脱苯部分设计计算
3.2.1 脱水塔
1.物料衡算
从油油换热器来得富油的数量如下:
其中:苯+二甲苯+甲苯+溶剂油=2090千克/时,即25.046千摩尔/时。
入脱水塔的富油温度为135℃,压力790毫米汞柱,各组分的蒸汽压如下:
表 3-3粗苯个组分的蒸汽压(毫米汞柱)
135℃时,萘的饱和蒸汽压计算如下:
1828.04
lg 7.1268
1.8667
212.5373.57N N P t
P ==+=毫米汞柱
在脱水塔内各组分的蒸发率计算如下:
经脱苯塔后各组分留在液相中的分率,设水分蒸发90%。则
?w =0.1,设留在液相中苯的分率为φB =0.735
?T =
1440
265.03160735.03160
735.0?+??=0.85889
?x
=700
265.03160735.03160
735.0?+??=0.92604 ?s =
350
265.03160735.03160
735.0?+?? =0.96160 ?m =5
.23265.03160735.03160
735.0?+?? =0.997326
?N =
()0.7353160
0.991670.735316010.73573.57
?=?+-
留在液相中的各组分数量如下,千摩尔/时: 水 0.1×53.374=5.3374 苯 0.735×19.098=14.037 甲苯 0.85889×3.467=2.9778 二甲苯 0.92604×1.133=1.0492 溶剂油 0.9616×1.348=1.2962 萘 0.77167×37.5=37.1878
洗油 0.997326×587.39=585.8193 共计 647.7047
A=647.7047
703.31647.7047
-×790=8722.76毫米汞柱 ?
B=
8722.76
8722.763160
+=0.7345
与假设的φB 相近,证明假设正确。留在液相中各组分数量如下:
表3-4 脱水塔液相组成
千摩尔/时 千克/时 水 53.374-5.3374=48.0366 864.659 苯 19.098-14.037=5.061 394.758 甲苯 3.467-2.9778=0.4892 45.0 二甲苯 1.133-1.0492=0.0838 8.883 溶剂油 1.348-1.2962=0.0518 6.216 萘 37.5-37.1878=0.3122 39.96 洗油 587.39-585.8193=1.5707 251.31 共计: 55.60 1610.8 塔顶油气含粗苯量
C B =454.8568
454.8568251.312
+=64.41%
塔顶压力780毫米汞柱,温度为130℃时的油气体积
V=55.29×22.4×273130273+×780
760
=1781.38米3/时
取塔内流速W=0.3米/秒 则塔的直径为:
D=
=1449米
取D=1.6米H=6000毫米,7层弓形折流板板间距350毫米。
2.热量衡算 (1)输入热量
输入热量即为135℃富油带入的热量 洗油带入的热量:
洗油比热C=005
.1135
00081.0403.0?+=0.4988千卡/千克·℃
Q 1=93982.5×0.4988×135=6328593.6千卡/时 粗苯带入的热量:
粗苯比热C=0.383+0.0103×135=0.5238千卡/千克·℃ Q 2=1054.3×0.5238×135=74553千卡/时 水带入的热量:
水的比热C=1.0215千卡/千克·℃
Q 3=960.72×1.0215×135=132486千卡/时 总输入的热量为:
Q 入=Q 1 +Q 2 +Q 3=6608869千卡/时 (2)输出热量
①塔顶气体带走的热量 水蒸气带走的热量
130℃时水蒸气焓I=653.4千卡/千克 q 1=864.659×653.4=564968.2千卡/时 粗苯气体带走的热量 i=130+Ct
C=80.03
130026.07.20?+=0.301千卡/千克·℃
粗苯汽体中各组分的重量组分(%)
[17]
M=120
411
.1106001.292939.978649.86100
+++=80.03
i=130+0.301×130=142013千卡/千克 q 2=454.8568×142.13=64648.8千卡/时 洗油蒸汽带走的热量
i=62.2+0.403×130=114.59千卡/时 q 3=251.312×114.59=28797.8千卡/时
则塔顶汽体带走的热量为: Q 4= q 1+ q 2 +q 3=658415千卡/时 ②热损失
脱水塔保温层厚度100毫米,表面温度60℃,保温后的脱水塔表面积:F=π×1.2×6+0.785×1.62=26.63米2 当风速为3米/秒时对流给热系数
a k =5.3+3.6×3=16.1千卡/米2·时·℃ 辐射给热系数:
a a =4.625
60)10025273()10060273(
4
4-+-+=5.8千卡/米2·时·℃
Q 5=26.63×(16.1+5.8) ×(60-25)=30412千卡/时 ③塔底富油带走的热量 设塔底富油的温度为t ℃ 洗油带走的热量:
洗油比热C=055
.100081
.0403.0t +千卡/千克·℃
q 1=93731(055
.100081.0403.0t
+)t=36775.83t+72.92t 2千卡/时
粗苯带走的热量:
C=0.383+0.001043t 千卡/千克·℃
q 2=1635.6(0.383+0.001.43t )t=626.43t+01.706t 2千卡/时 水带走的热量:
C=1.0174千卡/千克·℃
q 3=96.07×1.0174×t=97.48t 千卡/时 Q 6=q 1+q 2+q 3=37499.7t+75.626t 2千卡/时 则总输出热量为:
Q
出
=658415+37499.7t+75.626t2
令Q
入= Q
出
6608869=658415+37499.7t+75.626t2
得 t=126.46℃
所以可知经过脱水塔后富油温度降低了8.54℃
3.2.2 管式炉
1.物料计算
进入管式炉的富油数量如下:
表3-6 管式炉进料
设分的饱和蒸汽压[19],千帕:
设管式炉出口富油压力为122.66千帕,以?
B、?T、?X、?S、?M、?N、
粗苯工艺流程
1.装置概况及工艺过程 1.1装置概况 粗苯加氢装置由制氢、加氢精制、萃取蒸馏、酸性水处理、酸性气处理、公用工程系统等单元组成。年处理焦化粗苯原料10万吨。其主要工艺过程是将粗苯原料经过脱重组分塔脱除C9以上重组分后经两级加氢处理(预加氢和加氢净化)。原料通过预反应器催化剂床层逆流向上,使双烯烃、苯乙烯、二硫化碳进行加氢脱除和双烯饱和,再通过主反应器催化剂床层进行加氢处理,使烯烃发生饱和反应生成饱和烃。硫、氧、氮等化合物被加氢转化烃类、硫化氢、水及铵盐被脱除,芳烃转化被抑制。处理后的物料经稳定塔除去溶解于物料中的硫化氢后进入萃取蒸馏系统。在环丁砜的作用下将芳烃和非芳烃分离。分离出的混合芳烃经苯塔、甲苯塔、二甲苯塔精馏分离,生产纯度极高的苯、甲苯、混合二甲苯产品及少量的C8—、C8+溶剂油。生产过程中产生的酸性水经酸性水汽提处理后送至污水处理厂,酸性气经酸性气处理装置脱除硫化氢制取硫磺。 1.2工艺流程简述 1.2.1加氢工艺流程 自罐区泵送来的焦化粗苯原料经过滤器FT-1101/A、B,再经主反应产物/脱重组分塔进料换热器E-1101(管程)换热后入脱重组分塔C-1101,在塔内进行轻、重组分分离,塔顶汽相经脱重组分塔顶冷却器E-1102(壳程)冷凝冷却后进入塔顶回流罐V-1101,不凝气经真空机组排放至火炬燃烧。液体经脱重塔回流泵P-1101/A、B加压后部分回流,部分送入加氢进料缓冲罐V-1102。塔底重苯经塔底泵P-1103/A、B 加压后送入脱重组份塔底冷凝器E-1104(管程)冷却后送往罐区。脱重塔底设两台再沸器E-1103/A、B和两台塔底循环泵P-1102/A、B 强制循环。再沸器热源采用导热油。为防止物料聚合结焦在脱重塔进料线注入阻聚剂。 加氢进料缓冲罐V-1102的轻苯经反应进料泵P-1104/A、B 加压后入轻苯预热器E-1105(管程)预热后与K-1101/A、B送来的循环氢气混合后依次进入轻苯蒸发器E-1106/A、B、C(管程),在轻苯蒸发器内被加热蒸发的轻苯和
粗苯加工工艺流程图
第一节粗苯精制苯基本原理 精苯车间加工的原料是外购粗苯和轻苯。其主要组分是苯及同系物、苯、甲苯、二甲苯等占80%—95%,此外还有脂肪烃、环烷烃、不饱合化合物以及少量硫化物、吡啶碱类、酸类如洗油的低沸点馏份。 粗苯的各种主要组份皆在180℃前馏出。 由于粗苯、轻苯是一种比较复杂的混合物,故其本身用途不大、但经加工以后所得的多和纯产品的却是重要的化工原料,具有很高的经济价值。粗苯精制的目的在于获得尽可能多的苯族纯产品,同时对其它组份尽可能加以综合得用。 (一)硫酸洗涤净化法基本原理 粗苯中含有5—12%的不饱合化合物及其它杂质,并主要分布在14℃以后和79℃以前馏出物中。 粗苯经两苯塔是除去140℃以后重苯中的不饱合化合物,以获得轻苯和重苯两种产品。 轻苯初馏的目的是切除79℃以前不饱合化合物及二硫化碳。所得混合馏份还含有与苯族产品沸点相接近不饱合化合物及硫化物杂质,可以采用化学方法加以净化。 1、经常使用的是硫酸洗涤净化法,其主要化学方法如下: (1)不饱合化合物的聚合反应 不饱合化合物在硫酸作用下很容易发生聚合反应,低沸点化合物易生成粘度大,不溶于混合份及硫酸的极深度的聚合物。引起化合物的夹带损失。所以必须先经过初馏除去低沸点不饱合化合物。高沸点不饱合化合物聚合程度较差,一般只生成可溶混合份的二聚物,三聚物。 (2)加成反应 硫酸各不饱合化合物还能生成酸式脂和中式脂,前者溶于硫酸中,后者溶于混合份中。低沸点不饱合化合物与硫酸生成中性脂,在吹苯中,中性脂加热分解,放出腐蚀设备的酸性物质,故初馏时尽可能地把低沸点物质清除。 (3)清除噻吩反应 噻吩在浓硫酸的催化作用下能和高沸点不饱合化合物共聚生成溶于混合物的共聚物,反应迅速完全,噻吩还能直接溶于硫酸中,但溶解速度很慢。 (4)苯族烃和不和化合物共聚反应 苯族烃在浓酸的催化作用下和不饱合化合物发生共聚反应生成能溶解于混合物的共聚物。(5)苯族烃的磺化反应 苯族烃与浓硫酸作用能发生磺化反应而造成苯族烃的损失。 2、影响硫酸洗涤的方要因素 (1)反应温度 最适宜的反应温度为35—45℃,温度过低反应缓慢而达不到净化要求,温度过高苯族烃磺化反应以及不饱合化合物的共聚反应加剧,因而使苯族烃损失增加。 (2)硫酸浓度 硫酸浓度过低达不到净化要求,浓度过高磺化反应加剧,苯族烃损失增加,因此先择较适宜的硫酸浓度为93—95%。 (3)硫酸和混合份的比例 在保证洗涤质量要求的前提下,酸油比例愈小愈好。不仅降低酸耗,而且可以减轻苯族烃的磺化反应。 (4)反应时间 酸洗净化反应所需时间与反应温度、硫酸浓度、酸油化、搅拌合程度等因素有关。一般反应时间为十分左右,时间过短,反应效果差,势必增加酸耗,时间过长,磺化反应加剧,苯族烃损失增加,所以反应器必须立即加水,使浓硫酸反应终止。
钻井工艺流程
钻井工艺流程 以中原油田三开井为例 一.选井位(甲方) 二.定井位:原则:地面服从地下 三.搬迁准备及搬安 井队,材料,技术员资料的(准备)钻井工程设计.井史,本井资料,仪器,工具(∑rA型井架)基础图;校正(要清楚校正的标准) 天车,游车和转盘≤15mm.校正转盘与天车〈2-3mm 泵(不单是皮带轮,还要校正水平尺),不水平度应〈1mm吊测房,地质录井,气测,指重表参数仪(技术员在搬家过程中要经常四处转圈,而不是做一个劳动力) 四.一开准备及一开作业 1.钻具:井口工具,井下工具的准备,配合接头9"钻铤=731 8"=631 7"=521x520 API 411(国内)x410 6 1/4=4A11x410 5" 加厚卡瓦
2.套管与套具的准备(套具由固井队提供) 最主要的是联顶节的长度 联顶节主要考虑:1)转盘面2)封井器四通接出管线离工字钢1.5 cm (3)井架底座 ( 一开的时候要送封井器为啥?就是因为联顶节,封井器,厂家不一样四通等的长度有出入) 封井器送来要问一下,闸板芯子是否是5寸~5-1/2的变径闸板,5寸的封钻杆,5-1/2寸的封油套,所以要问一下.下油套前要封井器试压. 3.测斜与工具的准备(不是拉回来就万事大吉,要做个地面试验) 冲鼠洞钻头用8-1/2的. 4.配浆. 5.一开验收 6.一开钻进 (接一根钻铤提起来,靠住转盘面,看钻铤是否居中,然后卸掉方钻杆,上接钻头,水龙带吊着,只准旋转不准加任何钻压.
200-300米表层要接2柱8寸钻铤,一柱7寸钻铤. 钻进过程中在表层一般用双泵,预防堵水眼,因为沙子很多.用双泵在钻完后,停一个泵,上提,快提完时在停泵.停完泵要抢接单根,根据钻铤的重量确定钻压,第一根不加压,第二根加压10KN-15KN,钻压的多少根据钻铤的多少,(钻压要算好)钻完一开后,循环泥浆,一定要上提下放,不能定点.更不能沉底循环,特别是一开更不能沉底循环,因为一开泥浆不成体系.应打个封闭,尽量不能留下水泥环. 现场灰量要准备好,水量要准备好.下表层套管不好下.斜坡引鞋. 表层固井的水泥质量很差.如果下不到底即使接循环头,方钻杆上提下放,尽量下到底. 7.固井. 固井时替浆量的计算:一开:经验公式:一般是100米8方 留水泥塞是20~30米+2米的口袋=25米检测表层固井水泥浆的比重≥1.85,比重低了凝固时
粗苯加氢精制生产工艺的优化与探究
粗苯加氢精制生产工艺的优化与探究 张文 四川省达州钢铁集团有限责任公司四川达州635002 【摘要】:四川省达钢集团50Kt/a粗苯加氢精制装置生产五年来,随着生产的进行越来越多的工艺情况逐渐显现,很多情况呈规律性发生。这里将装置过去五年生产中所遇工艺、设备、废气排放等情况及相应处理、优化方法做一个归纳总结。 【关键字】:重组分循环气过滤器物料堵塞 【前言】:近年来,公司认真贯彻落实科学发展观,准确把握国家产业政策要求,以创新为抓手,及时调整企业发展战略,努力转变发展方式,抢抓市场成长机遇,走长期可持续发展道路。为进一步落实公司向化工产业转型规划,公司于2009年上马一套50Kt/a粗苯加氢精制装置,装置于2010年3月正式投产。现在年生产量能够达到设计值50Kt/a,其中纯苯精制率达到99.95%以上,甲苯精制率达到98.00%以上,三苯回收率达到98.50%以上。 【装置介绍】:50Kt/a粗苯加氢精制装置工艺采用甲醇驰放气变压吸附提纯氢气和粗苯加氢脱硫精制纯苯等技术,生产控制上采用DCS集散控制系统,由DCS系统进行监视、操作、报警、联锁和控制,尤其对关键电器和运转设备进行远程控制,实现自动化管理。同时本装置三废排放少,对环境影响小,安全消防上采用气防、消防联锁系统,并与DCS系统挂接且互为冗余,措施较完善,抗风险能力较强。 加氢精制生产能力为50Kt/a,三苯回收率≥98%,可以年产精
制纯苯34000t/a,甲苯5000t/a,二甲苯2000t/a,同时还有少量非芳烃及溶剂油。同时由于装置采用了加氢法,替代了高污染的硫酸法处理焦化苯,更产生了巨大的社会效益。 1、原料预处理工序 1、1压力与自动调节 两苯塔作为一个常压精馏塔,在生产过程中属于工艺性能比较稳定的设备。因为它的工艺指标稳定性能较好,在生产过程中整个工序均可以采取自动调节,以减少人工操作强度。值得注意的是两苯塔的稳定性主要基于其塔内压力变化,而塔内压力与蒸发器(T301)底部采出量有直接关系。因此,当蒸发器(T301)底部采出量变化较大以及两苯塔内部压力变化较大时,我们要注意塔内原料、回流以及重组分物料采出的量的变化。做到及时调整,以保证两苯塔的质量平衡和气液平衡。 1、2关于废油的回收 废油的主要构成是水和原料油,并且水的量远远大于原料油的量。因此,在废油回收时,要特别注意两苯塔内的压力变化。通过控制废油量的大小,以避免油水共沸现象的发生。通过控制热源(蒸汽)量的供给大小,以保证塔内的热量平衡。 1、3关于二甲苯塔塔底重组分的回收 本装置设计二甲苯塔采用间歇蒸馏的方式生产,所以在生产一段时间后需要对其塔底重组分物料进行回收。首先,在回收过程中需保证二甲苯塔内压力处于非负压状态下。最好采用打开塔顶放散阀,使
粗苯加氢精制
粗苯加氢精制 粗苯精制的目的是将粗苯加工成苯、甲苯、二甲苯等产品,这些产品都是 宝贵的化工原料。苯是重要的化工原料,广泛用作合成树脂、合成纤维、合成 橡胶、染料、医药、农药的原料,也是重要的有机溶剂。我国纯苯的消费领域 主要在化学工业,以苯为原料的化工产品主要有苯乙烯、苯酚、己内酰胺、尼 龙66盐、氯化苯、硝基苯、烷基苯和顺酐等。在炼油行业中用作提高汽油辛烷值的掺和剂。甲苯是一种无色有芳香味的液体,广泛应用于农药、树脂等与大 众息息相关的行业中,国际上其主要用途是提高汽油辛烷值或用于生产苯以及 二甲苯,而在我国其主要用途是化工合成和溶剂,其下游主要产品是硝基甲苯、苯甲酸、氯化苄、间甲酚、甲苯二异氰酸酯等,还可生产很多农药和医药中间体。另外,甲苯具有优异的有机物溶解性能,是一种有广泛用途的有机溶剂。 二甲苯的主要衍生物为对二甲苯,邻二甲苯等。混合二甲苯主要用作油漆涂料 的溶剂和航空汽油添加剂,此外还用于燃料、农药等生产。对二甲苯主要生产PTA以及聚酯等。邻二甲苯主要用于生产苯酐等。 生产苯、甲苯、二甲苯的主要原料是石油催化重整的重整油、石油裂化的 高温裂解汽油和焦化粗苯。这3种原料占总原料量的比例依次为:70%、27%、3%。以石油为原料生产芳香烃的工艺都采用加氢工艺,以焦化粗苯为原料生产 芳香烃的工艺有酸洗精制法和加氢精制法。 酸洗法仍在发展中国家被大量采用,其工艺落后、产品质量低、无法与 石油苯竞争,而且收率低、污染严重,产生的废液很难处理。在发达国家都已 采用加氢精制法,产品可达到石油苯的质量标准。国内有很多企业已建成投产 或正在建设粗苯加氢装置。20世纪80年代,上海宝钢从日本引进了第一套 Litol法高温加氢工艺,90年代石家庄焦化厂从德国引进了第一套K.K法低温 加氢工艺,1998年宝钢引进了第二套K.K法加氢工艺,还有很多企业正在筹建 加氢装置。随着对产品质量和环保的要求越来越严格,粗苯加氢工艺的应用是 大势所趋。 1、粗苯加氢精制的原理 粗苯加氢根据其催化加氢反应的温度不同可分为高温加氢和低温加氢。 在低温加氢工艺中,由于加氢油中非芳烃与芳烃的分离方法不同,又分为萃取 蒸馏法和溶剂萃取法。 高温催化加氢的典型工艺是Litol法,在温度为600~650℃、压力6.0MPa条 件下进行催化加氢反应。主要加氢脱除不饱和烃,加氢裂解把高分子烷烃和环 烷烃转化为低分子烷烃,并以气态形式分离出去。加氢脱烷基,把苯的同系物 最终转化为苯和低分子烷烃。故高温加氢的产品只有苯,没有甲苯和二甲苯, 另外还要进行脱硫、脱氮、脱氧的反应,脱除原料有机物中的S、N、O,转化 成H2S、NH3、H2O除去,对加氢油的处理可采用一般精馏方法,最终得到产品 纯苯。
产量的计算
关于DCP车间工段关于产量的计算方法为进一步加强车间工段产量物料消耗指标的核算,便于车间考核,提高员工生产积极性、创造性,体现多劳多得、多贡献多分配的原则,本着公开、公正、公平的原则,结合前期生产的实践经验,经讨论分析,制定本计算方法: 1、为便于计算,DCP车间各工段的产量都按折算DCP吨位计。 2、交接班产量,即指交接班时各槽罐、容器的液体(指含磷液体)及未烘干的半成品按照规定的折算办法进行折算成DCP产量,上一个班的交班物料作为下一个班的接班物料。 3、交接班物料折算DCP的方法: ①萃取、脱硫酸计算办法: 首先对脱硫稠厚器、萃取槽的物料进行收方(收方时采用量空高的方法,用容器的总体积减去空高体积即为交接班物料体积数,即脱硫稠厚器【200.96×实际液位m (直段) +100m3(底部椎体】×98%=脱硫稠厚器交班总料浆体积);萃取槽7000×7000×萃取槽实际液位m×6个=萃取槽交班总料浆体积),同时对交班物料抽样送分析室测P2O5、SO3,并按下列方法进行折算。 ②萃取槽物料: 总料浆体积×料浆比重×[液固比/(液固比+1)]÷磷酸液体比重×萃取液P2O5g/l÷180g/l=萃取槽标酸,每1立方米标酸折合DCP0.34吨(液固比,料浆比重以交接班双方交接时数为准。交接班:液固比1.8~2.3;P2O5180~200g/l,液固比浓度超过上限不计)。 脱硫酸(主要指增稠器内的脱硫酸) 脱硫酸:总体积×实测P2O5g/l÷120=脱硫标酸×0.21 (稠厚器总体积×0.98)×实测P2O5g/l÷120=脱硫标酸 上列萃取槽、稠厚器液体标酸折算成DCP总和即为交接班萃取工段DCP产量。 注:在检修、清理时各容器不作特殊考虑,一律按上列办法计算。交接班时,萃取槽抽一个样,稠厚器抽一个综合样。 ③一段液计算办法: 正常情况下,一段中和槽1~9区按一段液体按实际收方计,二段中和槽二段液体1~5区按实际收方计,增稠器以实际收方计,将上列一、二段中和槽液体、增稠器液体合计为一段滤液交接班标方。交接班时,一段中和槽9区抽150ml的样为一段中和槽的样;二段中和槽5区各抽150ml的综合样为二段中和槽的样;增稠器抽一个综合样。一段中和槽4500×4500×实际液位m×9个+一段增稠器【200.96×实际液位m (直段) +100m3 (底部椎体)×2个】=一段中和交班总料
地源热泵钻井工艺设计流程
一、作业工具; 1 无压磅、DN140自由钳两把、DN127自由钳两把、200KG铁铊、DN140套管、大扳手、12吋管子钳、24吋管子钳、钢卡、套筒扳手、梅花扳手、梅花改锥、克丝钳等 2﹒钻进设备 2.1使用合格钻机,回转和给进系统工作必须正常,滑轨和机器之间不能有松旷。 2.2设备安装应符合质量标准。钻机必须正确水平安装在基台上,保证滑轮、立轴和孔的中心在一条直线上。 2.3钻具组配要合理。粗钻具与孔壁的间隙要小,可采用扶正器来加强钻具的稳定性,粗钻具长度要合理,一般为5~8m。钻具要准确、规X;不同岩层改换不同钻具;钻具不弯曲,不偏心。 二、钻孔准备 1了解并确定土壤地质条件。 2确定地下综合管线分布及设置情况,并做好明显的标识记号。 3平整土地,根据地埋管施工图,标示具体钻孔位置及总管管沟位置。 4确认钻孔支架打设位置。 5确认钻孔机械电源容量及供给情况。 6提供水源至钻孔现场。 三、工程钻孔 1根据工程实际情况,随时填写记录表并及时分析土壤实际状况。
2预先挖好泥浆池,利于泥浆收集和清理。 3采用原浆混合黄沙、膨润土进行泥浆护壁,防止产生孔壁坍塌。 4采用地源热泵专用全液压钻井机,以确保钻孔深度和垂直度,钻孔实际深度要大于设计深度。 5 利用岩芯管取出岩芯,观察地质情况,从而选择不同的钻头。 6钻孔完毕后,应及时埋设管道并注浆回填。 7地埋管施工完毕后应及时对现场进行清理,以利于土建单位下一步工作的顺利进行。 四、钻机操作步骤 1下钻联动操作步骤当钻场准备工作完成后,要实现下钻联动操作步骤是: 1)回转手柄处于中位,实现主副泵合流状态; 2)起下钻功能阀手柄处于下钻位置,夹转联动与分离功能阀手柄处于夹转分离位置,副泵溢流加压给进与卡盘增压减压给进功能阀手柄置于副泵溢流加压给进位置; 3)操作起下钻手柄即可实现下钻联动功能。 2起钻操联动操作步骤完成钻进工作或需要起钻时,要实现起钻联动操作步骤是: 1)回转手柄处于中位,实现主副泵合流状态; 2)起下钻功能阀手柄处于起钻位置,夹转联动与分离功能阀手柄处于夹转分离位置,副泵溢流加压给进与卡盘增压减压给进功能阀手柄置于副泵溢流加压给进位置;
主要生产指标的计算公式
主要生产指标的计算公式 一、烧结厂 1、烧结矿产量=皮带速度x料批x作业时间x(100-混合料水分)x残存量 2、反推产量=高返X +落地量-上落地量+高炉入炉烧结矿量 3、台时产量= 产量/作业时间 4、烧结机有效面积利用系数(t /(m ?台时))=烧结矿产出量/ (有效面积X实际作业时间) 5、烧结矿品位=烧结矿含铁量(吨)/烧结矿产出量(吨)X100% 6、日历作业率(%)=实际作业时间/日历时间%(取参数报表中时间) 7、干料量=该原料湿料量X(1 —HO% 8干料单耗=某物料干料量/产量X 1000 (kg) 9、铁料原料消耗(单耗)=1吨消耗多少公斤该物料。 10、烧结矿固体燃料消耗(kg/t )=烧结矿固体燃料耗用量kg/烧结矿产出量t 11、烧结矿煤粉消耗(kg/t )二烧结矿煤粉耗用量kg/烧结矿产出量t 12、烧结矿焦粉消耗(kg/t )=烧结矿焦粉耗用量kg/烧结矿产出量t
13、一次配料:某料下料量=某料的百分比X总下料量/ 100 (t) 14、一次配料某物料配比=某料总配比表中配比/ 一次配料物料在总 配比表配比之和 15、某物料下料量=某物料下料量(吨/小时)X运行时间段 16、成品率=产量(产量+返矿)%(返矿取配料配比变更) 17、出矿率=产量(混合料总量X) 18、返矿率=返矿(产量+返矿) 二、炼铁厂 1、生铁合格率(% =生铁检验合格量(吨)/生铁检验总量(吨)x100% 2、生铁一级品率(% =一级品生铁总量/合格生铁检验总量x100% 3、入炉焦比是反映高炉冶炼每1吨合格生铁所消耗的干焦炭量。入炉 焦比(kg/t )二干焦耗用量kg/合格生铁产量t 4、干焦量=湿焦量x (1-湿焦含水% 5、综合焦比是指高炉冶炼每1吨合格生铁所消耗的综合干焦(将各种燃料均折合成干焦计算)量。综合焦比(kg/t )=综合干焦耗用量kg/ 合格生铁产量t 6、综合干焦量=干焦量+其他各种燃料量x折合干焦系数 7、喷煤比是反映高炉冶炼1吨合格生铁所消耗的煤量。喷煤比(kg/t )
钻井工艺基本流程(教学参考)
钻井工艺基本流程 一、开钻前准备钻头,一二三开接头,测量圆井,导管距地平面高度,大 鼠洞深度,导管埋深等于圆井高度,入地3m,补心高之和,提1根9″钻铤校井口,通知重仪站安装八参数仪器,上二开PDC钻头,钻具,套管头及表层套管,LG36井导管割高以基础平面向下量1400mm,交资料时搞列卷,钻井保障措施,空白资料带上井,分析钻井设计,划出重点,绘制井身结构图,8″随钻一套,171/2″ST127钻头,扣型731,钻头一般不用等级喷嘴。 二、一开 (泵压允许条件下,保证排量尽量大),PDC钻头钻压3~5T,一般4T。套管附件:引鞋,套管头(01),(02)部分,套管循环头,吊卡,接箍长度,最后一根套管外径,垫叉高度,租用5″短钻杆,固井时调节钻具长度。套管插入头(133/8″×5″)插座,B型吊钳。121/4″钻头冲鼠洞,丈量方钻杆有效长度,大鼠洞长度。具备开钻条件后报调度室开钻验收。上录井队,井口,井场深井泵,安全合同。 一开钻进: 钻压0.5~8T,转速50~100N,排量35~60L/S,泵压1~6Mpa,钻35m循环5~10min,起钻加扶正器,前35m钻压0.5T, 转速50~60N,排量35~40L/S,(单泵100冲,转速55N,钻头喷嘴22,18,0),加入扶正器后每接一根钻铤增加1T,每根单根划眼1~2次,禁止定点循环。钻铤加完钻压8T,转速80~100N,排量50~65L/S,泵压8~12Mpa,钻至设计井深循环2~3周起钻,通井一次,起钻前垫高粘,下套管,若为插入式固井,下完套管下插入头循环。表层套管不留口袋,安装井口,按钻井设计要求试压(5″钻杆2根+试压塞+5″钻杆1根),下3柱钻铤后校井口。 三、二开起钻加扶正器时将测斜座装在钻头以上的接头上,若有螺杆应装在离螺杆1~3 柱钻铤上。下钻时安装好防磨套,以后每趟起钻都要松顶丝,第一只钻头121/4″ST127,铣齿,15,12,18;下钻探塞,遇阻不超过5T,探得塞后起1柱,接钻杆套管内试压(按设计要求试压),钻塞不宜太快,钻压0.5~2T, 转速45~50N,钻进地层5~10m 循环1~2周,地破试验,套管鞋以下50m控制钻压2~4T,转速45~55N,排量35~40L/S,每根单根循环10~20min,钻附件时注意扭距。 备注:套管内钻水泥塞一般不带扶正器,钻出管鞋要考虑扶正器不敲打管鞋后起钻加入扶正器。 二开牙轮钻头钻压6~8T,排量50~60L/S,泵压18~20Mpa,转速100~120N, 钻进300~400m循环测斜,1000m后可400~500m测斜一次。第一次短起至管鞋,轮古构造700~800m易遇阻(该井段应考虑测斜短起,若有挂卡应加密测量),起钻每柱灌满泥浆。测斜时将钻具内容积算出来,通过排量算出测斜仪到达井底的时间,超过4500m后若井不斜可不再测斜,但钻压必须控制在4T以下,且不能溜钻,特别是奥陶系灰岩软硬交替地层(即快钻时和慢钻时同存段)。 平时的工作中多注意柴油机转速,扭距,泵压,转盘转速及岩性变化。钻至1300m左右,起钻换121/4″MS1952SS,PDC钻头(钻井参数:钻压0.5~1T塑形
8万吨年粗苯精制工艺设计
毕业设计 题目:8万吨/年粗苯精制工艺设计 系别:化学与化学工程系 专业:化学工程与工艺 姓名: 学号: 指导教师:
设计说明 此设计的任务是处理量为8万吨/年的粗苯精制工艺设计,它采用了粗苯低温加氢工艺流程,选用了连续精馏筛板塔的化工设备。 原料粗苯经过两苯塔实现轻重组分分离,其中塔釜重质苯做为产品回收,塔顶轻苯在加氢反应器中进行加氢反应后进入脱轻塔脱除硫化氢,氨气等低沸物,然后依次进入预精馏塔 萃取精馏塔 纯苯塔和二甲苯塔,最终得到纯净合格苯、甲苯的产品。 为达到设计要求,此设计通过物料衡算、热量衡算、塔的工艺尺寸计算、塔板负荷性能验算及附属设备计算,得到符合要求的一系列工艺流程参数,包括进料量F=106.055Kmol/h,塔顶液体流量D=90.945Kmol/h,塔底釜液流量W=15.11Kmol/h ,塔径D=1.6m,塔高h=24.45m,板间距m 5.40T =H ,精馏段实际塔板数块精17N =,提馏段塔板数块提17N =,设置7个人孔,出塔顶塔底人孔 外其他人孔处的板间距为H=0.7m,进料处板间距H=1m 等。 根据这一系列工艺流程参数绘制工艺流程图、物料衡算图及主设备图。 关键词:低温加氢精制、连续精馏筛板塔、两苯塔、苯、甲苯
Design elucidation This design task is productivity for eight million tons/year cuben refining process design, it adopted cuben cryogenic hydrogenation process, choose the continuous distillation tower chemical equipment sieve. Raw material cuben after two benzene tower, which achieve weight component separation tower kettle heavy benzene as product recycling, tower light benzene in hydrogenation reactor in hydrogenation reaction took off after removal from the light tower into hydrogen ammonia and other low boiling, which in turn into that gets distillation column of pure benzene tower and extract xylene tower, and ultimately the pure qualified benzene, toluene products. To achieve the design requirements, this design through the material calculation, heat calculation, tower craft size calculation, tower plate load performance checking and affiliated equipments calculation, get to meet the requirements of a series of process parameters, including into 106.055 Kmol feed F = liquid flow, being/h D = 90.945 Kmol/h, bottom kettle fluid flow W = 15.11 Kmol/h, tower diameter D = 1.6 m, high tower 24.45 m, board h = distance, rectifying section number and mention actual tower plate, plate number distillated section tower set seven people hole, a tower in the bottom and the other manhole manhole for h = 0.7 board spacing, feeding place board m distance h = 1-m etc. According to this series of process parameters rendering process flow diagram, material calculation chart and main equipment figure. Keywords: low temperature hydrotreating, perforated continuous distillation tower, two benzene tower, benzene, toluene
最新年产0W吨粗苯精制工艺设计设计
年产0W吨粗苯精制工艺设计设计
济源职业技术学院 毕业设计(论文) (冶金化工系) 题目年产10万吨粗苯精制工艺设计专业应用化工技术 班级化工xxx班 完成日期 2011.05.08—2011.10.10
目录 摘 要 (1) 第一章 粗苯精制的综述 (2) 1.1粗苯的性质和用途 (2) 1.2粗苯精制原理 (2) 1.3初步精馏 (3) 1.4设计的依据 (4) 第二章 工艺流程的说明 (6) 2.1化学精制工艺的选择 (6) 2.2粗苯的精制 (6) 2.3生产设备的选择 (7) 2.3.1精馏塔类型的选择 (7) 第三章 粗苯精制的物料衡算 (10) 3.1初步精馏计算 (10) 3.1.1初馏塔全塔的平均温度 (10) 3.2化学精制 (11) 3.3纯苯塔的物料衡算 (12) 663134.97830.492()2430095896.810 m C H ?+?=??=吨.............. 13 第四章 热量衡算 (14) 4.1冷凝器的热量衡算 (14) 第五章 粗苯精制中的危害因素与防护 (16) 5.1防火 (16) 5.2原料、产品、及中间产品的储存 (16) 5.3废气的处理 (17) 第六章 粗苯精制的发展方向 (18) 6.1现状 (18) 6.2展望 (18) 致谢 (19) 参考文献 (20) 附图1 (21) 粗苯精制工艺流程图 (21) 附图2 (22) 精馏塔设备图 (22)
摘要 粗苯中主要成分是苯,是纯苯的主要来源。苯的用途很多,是有机合成的基础原料,可制成苯乙烯、苯酚、丙酮、环己烷、硝基苯、顺丁烯二酸酐等,进一步可制合成纤维、合成橡胶、合成树脂以及染料、洗涤剂、农药、医药等多种产品。 本设计首先是先介绍粗苯的组成、性质以及制得粗笨之后的用途。之后又介绍工艺流程,使得我们更清晰地了解到本设计的原理与目的。经过设备的对比选择最适合本设计的设备,最后经过物料衡算与热量衡算,得出本设计所需要的原料与热量。 本设计的产品有纯苯、甲苯、二甲苯、不饱和化合物及少量含硫、氮、氧的化合物。其中最主要的产品是纯苯、甲苯和二甲苯。 关键词:粗苯精制酸洗精制法粗苯
储量计算方法
油、气储量是油、气油气勘探开发的成果的综合反应,是发展石油工业和国家经济建设决策的基础。油田地质工作这能否准确、及时的提供油、气储量数据,这关系到国民经济计划安排、油田建设投资的重大问题。 油、气储量计算的方法主要有容积法、类比法、概率法、物质平衡法、压降法、产量递减曲线法、水驱特征曲线法、矿场不稳定试井法等,这些方法应用与不同的油、气田勘探和开发阶段以及吧同的地质条件。储量计算分为静态法和动态法两类。静态法用气藏静态地质参数,按气体所占孔隙空间容积算储量的方法,简称容积法;动态法则是利用气压力、产量、累积产量等随时间变化的生产动态料计算储量的方法,如物质平衡法(常称压降法)、弹性二相法(也常称气藏探边测试法)、产量递法、数学模型法等等。 容积法: 在评价勘探中应用最多的容积法,适用于不同勘探开发阶段、不同圈闭类型、储集类型和驱动方式的油、气藏。容积法计算储量的实质是确定油(气)在储层孔隙中所占的体积。按照容积的基本计算公式,一定含气范围内的、地下温压条件下的气体积可表达为含气面积、有效厚度。有效孔隙度和含气饱和度的乘积。对于天然气藏储量计算与油藏不同,天然气体积严重地受压力和温度变化的影响,地下气层温度和眼里比地面高得多,因而,当天然气被采出至地面时,由于温压降低,天然气体积大大的膨胀(一般为数百倍)。如果要将地下天然气体积换算成地面标准温度和压力条件下的体积,也必须考虑天然气体积系数。 容积法是计算油气储量的基本方法,但主要适用与孔隙性气藏(及油藏气顶)。对与裂缝型与裂缝-溶洞型气藏,难于应用容积法计算储量 纯气藏天然气地质储量计算 G = 0.01A ·h ·φ(1-S wi )/ B gi = 0.01A ·h ·φ(1-S wi )T sc ·p i / (T ·P sc ·Z i ) 式中,G----气藏的原始地质储量,108m3; A----含气面积, km2; h----平均有效厚度, m; φ ----平均有效孔隙度,小数; Swi ----平均原始含水饱和度,小数; Bgi ----平均天然气体积系数 Tsc ----地面标准温度,K;(Tsc = 20oC) Psc ----地面标准压力, MPa; (Psc = 0.101 MPa) T ----气层温度,K; pi ----气藏的原始地层压力, MPa; Zi ----原始气体偏差系数,无因次量。 凝析气藏天然气地质储量计算 G c = Gf g f g = n g /(n g + n o ) = GOR / ( GOR + 24056γ o /M o ) 式中,Gc ----天然气的原始地质储量, 108m3; G----凝析气藏的总原始地质储量, 108m3; fg----天然气的摩尔分数;
粗苯加工与精制
第十章粗苯加工与精制 241.什么叫吸收温度?吸收温度过高或过低对吸收苯油什么影响? 吸收温度时至吸苯塔内煤气和洗油接触面的平均温度。它取决于煤气和洗油温度,液受大气温度影响。 当煤气中苯族烃含量一定时,吸收温度愈低,洗油中与其呈平衡的粗苯含量愈高。而提高温度时,洗油中粗苯含量降低。当吸收温度升高时,洗油液面上粗苯的蒸汽压随之增大,吸收推动力减小,因而粗苯回收率л降低和吸苯塔后含苯族烃增高。实践表明,当温度高于30℃时,л和塔后含量均显著恶化。因而吸收温度不宜过高。但也不宜过低。如低于10~15℃,洗油粘度显著增加,这使泵输送困难和塔内均匀分布困难,阻力加大。最适宜的吸收温度为25℃,操纵时波动在20~30℃之间即可。 242.为什么洗油温度应保持比煤气温度略高几度? 洗油温度保持比煤气温度略高一些,主要时防止煤气中水蒸气被冷凝下来进入洗油中,恶化脱苯塔的操作。夏季洗油温度比煤气温度高0~2℃,冬季高5~10℃.差值根据大气温度变化而定。 243.洗油相对分子质量与吸收煤气中粗苯的能力油什么关系? 同类液体吸收剂的吸收能力与其分子质量成反比,吸收剂的相对分子质量与溶质相对分子质量愈接近,则吸收得愈完全。由公式C=2.24Ap/M m P0(式中,P为煤气总压力;P0为在回收温度下苯族烃的蒸气分压;a为煤气中苯族烃的浓度)可知,当其他条件一定时,洗油相对分子质量M m小,洗油中粗苯浓度C增大(吸收能力加强)。但洗油相对分子质量也不能过小,否则在蒸馏脱苯时难与粗苯分离。 244.为什么可以用焦油洗油或石油洗油吸收粗苯? 因为焦油洗油和石油洗油与粗苯属同类物质,分子结构相似(芳香烃结构)。根据物质特性,同类物质互溶性较好。且分子量不一样,而沸点就不同,这样就能利用沸点不同这个特点进行蒸馏分离。 245.石油洗油与焦油洗油有什么区别?那种洗油用来回收煤气中粗苯为好?为什么? 焦油洗油和石油洗油主要区别在于: 1)焦油洗油时焦化厂自产物,石油洗油(轻柴油)则是石油加工产品; 2)石油洗油的相对分子质量比焦油洗油的大,因此吸收苯时所需洗油循环量也比焦油洗油量大30%左右; 3)焦油洗油相对密度为1.04~1.07,比水重,而石油洗油相对密度不大于0.890,比水轻; 4)焦油洗油的沸点比石油洗油的低,一般规定,300℃前焦油洗油馏出量大于90%,230℃前馏出量不大于3%;而石油洗油在350℃前馏出量不小于95%。 由于石油沸点高,因此在回收苯时,其损失量低于焦油洗油,并且用石油洗油回收苯时,180℃前的馏出量比用焦油洗油的多; 5)石油洗油稳定性较高,长期使用后不易变质;焦油洗油稳定性差,在循环使用后,密度、粘度、相对分子质量会增大;
(完整版)城市生活垃圾产量计算及预测方法.doc
城市生活垃圾产量计算及预测方法 2014-04-04 1范围 本标准规定了城市生活垃圾产量的计算方法和预测方法。 本标准适用与不同规模城镇、居民集中居住地区的生活垃圾的计算及预测。 2引用标准 下列标准所包含的条文,通过在本标准中引用而构成为本标准的条文。本版本出版时,所有版本均为有效。所有标准都会被修订,使用本标准的各方应探讨使用下列标准最新版本的可能性。 CJ/T3039—1995城市生活垃圾采样和物理分析方法 CJJ17—1988城市生活垃圾卫生填埋技术标准 3定义 3.1 车载容积 3 垃圾车实际可载容积( m) 3.2 车辆吨位垃圾车额定载质量( t ) 3.3 采样容重垃圾单位体积的质量( t/m 3) 3.4 装载容积垃圾车实际装载质量和装载容积比值(t/m 3) 3.5 垃圾产量垃圾产生量。 4影响城市生活垃圾产量计算及预测的因素 计算和预测垃圾产量应考虑以下主要影响因素:人口、生活水平、燃料结构、人口密度、流动人口、气候 以及收集方式。 5垃圾产量计算方法 5.1垃圾产量计算的要求 取连续几年的实际垃圾产量进行推算,预测未来年度的垃圾产量,使用式(2)计算时,应注意垃圾容重测试方法的正确性和清运量的准确性,在使用式(3)计算时,应注意居住人数的准确性。 5.2垃圾容重的测定,按CJ/T3039 规定执行。 5.3垃圾样品的采集方法,按CJ/T3039 规定执行。 5.4城镇居民生活区划分参照CJJ17 规定执行。 5.5垃圾人均日产量的计算方法: 在日产日清的情况下,计算居民区一天(24h)产出垃圾量与该区域人口数的比值,即人均日产量计算公式如下: R=PW/S×103 式中: R—人均日产量, kg/ 人; P—产出地区垃圾的容重 ,kg/L; W—日产出垃圾容积 ,L;
粗苯精制工艺流程
1粗苯精制 生产芳香烃苯、甲苯、二甲苯的主要原料是石油催化重整的重整油、石油裂化的高温裂解汽油和焦化粗苯。这3种原料占总原料量的比例依次为:70%、27%、3%。以石油为原料生产芳香烃的工艺都采用加氢工艺,以焦化粗苯为原料生产芳香烃的工艺有酸洗精制法和加氢精制法。焦化苯与石油苯生产成本相比约低1500元/t。2007年,我国加氢苯产能约56万t/a,产量约30万t,消耗粗苯约48万t,估计2008年建成投产的苯加氢装置产能为81万t/a,累计产能达到137万t/a。2009年建成投产的苯加氢装置产能为78万t/a,累计产能达到215万t/a。 表1.1 焦化苯与石油苯产品质量对比 20世纪80年代上海宝钢从国外引进了第一套Litol法高温加氢工艺,90年代石家庄焦化厂从德国引进了第一套K.K法低温加氢工艺,1998年宝钢引进了第二套K.K法加氢工艺,还有很多企业正在筹建加氢装置。 1.1加氢原理 焦化苯中芳烃含量一般大于85%(wt),而其中苯、甲苯、二甲苯又占芳烃含量的95%以上。焦化苯精致可分为两大类:酸洗法和加氢精制法。 1.1.1酸洗法 传统的粗苯加工方法,采用硫酸洗涤净化。常温常压、流程简单、操作灵活、设备简单。但由于不饱和化合物及硫化物在硫酸作用下,生成黑褐色的深度聚合物(酸焦油),至今无有效治理方法,另外不能有效分离甲苯、二甲苯,产品质量、产品收率无法和加氢精制相比,正逐步被取代。 1.1.2加氢精制法 粗苯加氢根据其催化加氢反应温度不同可分为高温加氢和低温加氢。在低温加氢中,由于加氢油中非芳烃与芳烃分离方法的不同,又分为萃取蒸馏法和溶剂萃取法。 1.1. 2.1高温法 高温加氢比较有代表性的工艺:由美国胡德利公司开发、日本旭化成改进的高温热裂解法生产纯苯的莱托(Litol)法技术。 在高温(600~630℃)、高压(5.5MPa)、催化剂(Co-Mo和Cr2O3-Al2O3)作用下进行气相催化两段加氢的过程,将轻苯中的烯烃、环烯烃、含硫化合物、含氮化合物转化成相应的饱和烃,同时发生苯的同系物加氢和脱烷基发应,已转化成苯与低分子烷烃,高温加氢的产品只有苯,没有甲苯和二甲苯,另外还要进行脱硫、脱氮、脱氧的反应,脱除原料有机物中的S、N、O,转化成H2S、NH3、H2O的形式除去,对加氢油的处理可采用一般精馏方法,最终得到苯产品。通过精制生产高纯苯,苯回收率可达114%。由于高温催化加氢脱除的烷基制氢作为氢源,不需要外界给其提供氢气。 1.1. 2.2低温法 低温加氢代表性的工艺:美国Axens低温气液两相加氢和德国伍德(Uhde)KK低温气相加氢技术。 在低温(280~350℃)、低压(2.4MPa)、催化剂(Co-Mo和Ni-Mo)作用下进行气相催化或液相两段加氢的过程,将轻苯中的烯烃、环烯烃、含硫化合物、含氮化合物转化成相应的饱和烃。对于加氢油的处理,萃取蒸馏低温加氢工艺采用萃取精馏方法,把非芳烃与芳烃
成本差异的计算公式汇总 计算及分析
成本差异的计算公式汇总计算及分析 成本差异是指一定时期生产一定数量的产品所发生的实际成本与相关的标准成本之间的差额. 总差异=实际产量下实际成本-实际产量下标准成本=实际用量×实际价格-实际产量下标准用量×标准价格=用量差异+价格差异 其中:用量差异=标准价格×(实际用量-实际产量下标准用量)价格差异=(实际价格-标准价格)×实际用量 (一)直接材料成本差异的计算分析 直接材料成本差异=实际产量下实际成本-实际产量下标准成本=实际用量×实际价格-实际产量下标准用量×标准价格=直接材料用量差异+直接材料价格差异 直接材料用量差异=(实际用量-实际产量下标准用量)×标准价格直接材料价格差异=实际用量×(实际价格-标准价格(二)直接人工成本差异的计算分析 直接人工成本差异=实际总成本-实际产量下标准成本=实际工时×实际工资率-实际产量下标准工时×工资率标准=直接人工效率差异+直接人工工资率差异 直接人工效率差异=(实际工时-实际产量下标准工时)×工资率标准直接人工工资率差异=实际工时×(实际工资率-工
资率标准)(三)变动制造费用成本差异的计算和分析变动制造费用成本差异=实际总变动制造费用-实际产量下标准变动制造费用=实际工时×实际变动制造费用分配率-实际产量下标准工时×标准变动制造费用分配率=变动制造费用效率差异+变动制造费用耗费差异变动制造费用效率差异=(实际工时-实际产量下标准工时)×变动制造费用标准分配率变动制造费用耗费差异=实际工时×(变动制造费用实际分配率-变动制造费用标准分配率)?(四)固定制造费用成本差异的计算分析? 固定制造费用成本差异=实际产量下实际固定制造费用-实际产量下标准固定制造费用=实际工时×实际分配率一实际产量下标准工时×标准分配率其中:标准分配率=固定制造费用预算总额÷预算产量下标准总工时1.两差异分析法将总差异分为耗费差异和能量差异两部分.其中,耗费差异是指固定制造费用的实际金额与固定制造费用预算金额之间的差额;而能量差异则是指固定制造费用预算金额与固定制造费用标准成本的差额. 耗费差异=实际固定制造费用一预算产量下标准固定制造费用=实际固定制造费用一标准工时×预算产量×标准分配率=实际固定制造费用一预算产量下标准工时×标准分配率能量差异=预算产量下标准固定制造费用一实际产量下标准固定制造费用=预算产量下标准工时×标准分配率一实际产
粗苯的加氢精制
粗苯的加氢精制 1.粗苯加氢精制的应用历史与现状 所谓“粗苯加氢”实质上是“轻苯加氢”。即:在一定的温度、压力条件下,在专用催化剂、纯氢气的存在下,通过与氢气进行反应,使轻苯中的不饱和化合物得以饱和;使轻苯中的含硫化合物得以去除,转化成硫化氢气体。然后再对“加氢油”进行精馏,最终可以获得高纯度的苯类产品。显然,采用此工艺,没有污染物产生,产品质量好,越来越得到人们的青睐,是今后的发展方向。 对轻苯进行加氢精制工艺早在20世纪50年代就在国外得到了工业应用。目前发达的国家,如美、英、法、德、日等均已广泛采用这个先进的加氢精制工艺。而在国内,直到上世纪70年代,北京燕山石油化工公司从西德引进第一套“Pyrotol制苯”装置,利用裂解汽油为原料,经加氢以获得高纯度石油苯;接着,80年代初,宝钢的一、二期工程从日本引进了一套“高温Litol”加氢装置,对焦化轻苯进行加氢精制;尔后,河南“平顶山帘子布厂”也引进了一套“高温Litol”装置。近年来,石家庄焦化厂、宝钢三期工程引进了德国的“K.K技术”,即:“中温Litol”装置。北京焦化厂也建成了国内自行设计的“中温加氢”装置,并已过关。另外,山西太原等地也正在建设了轻苯加氢装置。可见,粗苯加氢精制是国内今后的发展方向。 轻苯的加氢精制工艺方法很多,其中工业应用的有下列几种: (1)鲁奇法——该法所采用的催化剂为氧化钼、氧化钴和三氧化二铁;反应温度为350~380℃;以焦炉煤气为直接氢气源;操作压力为 2.8Mpa。该法的苯精制率较高,加氢油采用共沸蒸馏法或选择萃取法进行分离,可以制得结晶点为5.5℃的高纯度苯。 (2)考柏斯法——该法也是采用氧化钼、氧化钴和三氧化二铁为催化剂;反应