橡胶粘合与工艺讲稿

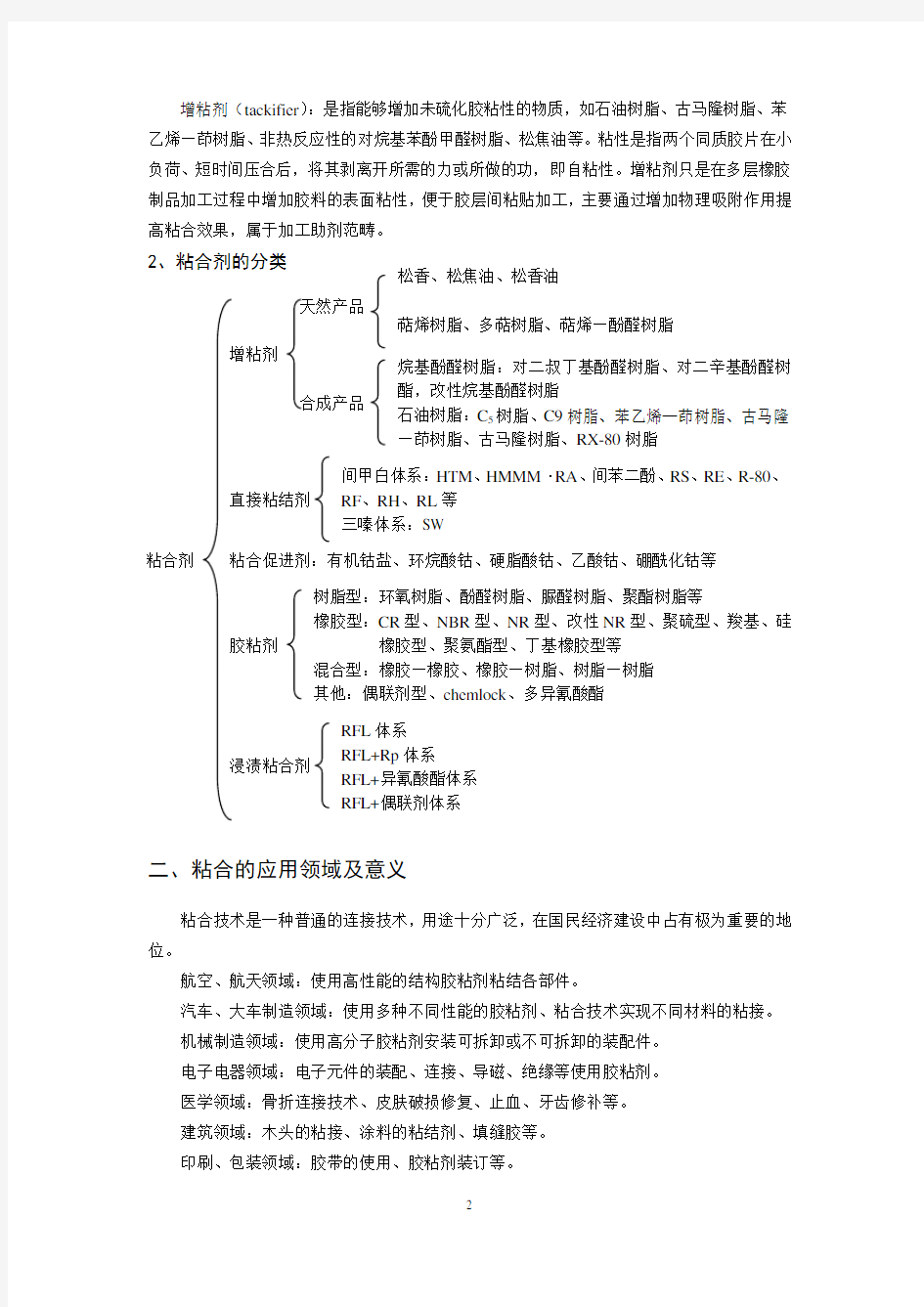
绪论
一、粘合的概念及分类
1、与粘合有关的概念
粘合是指将两个同种或异种材料表面粘附在一起形成一个界面的工艺过程。
橡胶的粘合是指橡胶与同质或异质材料表面相接触,靠范德华力、氢键、化合键合力作用所产生的结合,如橡胶的自粘、互粘,橡胶与骨架材料的粘合等。
能够将材料相邻表面结合成一体的物质称作粘合剂。
有关粘合剂的名词术语很多,如胶粘剂、粘结剂、粘着剂、键合剂、粘合促进剂、增粘剂、直接粘合剂、粘合浸渍剂等。
胶粘剂(adhesive):是指将两种或两种以上的制件(或材料)连接在一起的一类物质,多是胶液或粘带形式,通过喷、涂、贴等工艺达到粘合目的。这种粘合方式是在两种材料表面之间形成以胶粘剂粘料为主成份的中间粘合层,如硫化胶之间的粘合,硫化橡胶与皮革、木材、金属等粘合。胶粘剂自身的性质和性能、粘合工艺决定粘合效果。
粘结剂(粘着剂):是指将不连续的粉体或纤维材料粘附在一起形成连续整体的物质,如造纸用纸浆粘结剂、无纺布粘结剂、石棉粘结剂、粉体湿法造粒所使用的粘结剂等,多为液体或半流体物质,通过高速搅拌等方法实现粘合剂与粉体的均匀混合,靠粘结剂提供粘结力粘合。
键合剂(bonding agent):又称直接粘合剂,在混炼时混入胶料中,在硫化时使被粘表面之间产生化学键合或强烈的物质吸附,形成牢固粘结的物质,如典型的间苯二酚给予体—亚甲基给予体—白炭黑粘合体系(间甲白体系,HRH体系)、三嗪粘合体系。这种类型的粘合剂,在产生结合的两个材料表面上并不存在以粘合剂为主成份的中间层。这种粘合剂多用于橡胶与骨架材料之间形成牢固而持久的粘合。
粘合促进剂(adhesive promoting agent):是指自身不直接产生材料之间的物理吸附作用或化学键合作用,但能够促进粘合作用发生的化学物质,如在橡胶与镀黄铜金属粘合过程中使用的有机钴盐就是一种粘合促进剂。这种粘合促进剂也是作为配合剂直接加入胶料中,并在高温硫化过程中发挥作用。
浸渍粘合剂:又称间接粘合剂,是指将含有粘合成份的浸渍液通过浸渍工艺覆盖在纤维织物的表面或渗透到织物内部缝隙中,在硫化温度下,浸渍液胶膜与橡胶及织物产生化学键合,这种浸渍液就称作浸渍粘合剂,如典型的间苯二酚、甲醛、胶乳三组分的NaOH乳液结合体系,即RFL体系,这是提高橡胶与纤维结合效果的主要途径之一,针对不同的纤维,浸渍液的组成不一样,如其中的胶乳(L组分)可以是NRL,也可以是丁吡胶乳,丁苯吡胶乳,间苯二酚和甲醛的用量也可以发生变化。对聚酯、芳纶、玻璃纤维等难结合的纤维,除了RFL组成外,还要添加其他有利于结合的成份,如Rp树脂、异氰酸酯、硅烷偶联剂等。
增粘剂(tackifier):是指能够增加未硫化胶粘性的物质,如石油树脂、古马隆树脂、苯乙烯—茚树脂、非热反应性的对烷基苯酚甲醛树脂、松焦油等。粘性是指两个同质胶片在小负荷、短时间压合后,将其剥离开所需的力或所做的功,即自粘性。增粘剂只是在多层橡胶制品加工过程中增加胶料的表面粘性,便于胶层间粘贴加工,主要通过增加物理吸附作用提高粘合效果,属于加工助剂范畴。
二、粘合的应用领域及意义
粘合技术是一种普通的连接技术,用途十分广泛,在国民经济建设中占有极为重要的地位。
航空、航天领域:使用高性能的结构胶粘剂粘结各部件。
汽车、大车制造领域:使用多种不同性能的胶粘剂、粘合技术实现不同材料的粘接。
机械制造领域:使用高分子胶粘剂安装可拆卸或不可拆卸的装配件。
电子电器领域:电子元件的装配、连接、导磁、绝缘等使用胶粘剂。
医学领域:骨折连接技术、皮肤破损修复、止血、牙齿修补等。
建筑领域:木头的粘接、涂料的粘结剂、填缝胶等。
印刷、包装领域:胶带的使用、胶粘剂装订等。
造纸领域:纸浆的粘结剂。
皮革领域:皮包的粘接、胶鞋的粘接等。
橡胶制品领域:橡胶的自粘、互粘、与骨架材料的粘合等。
意义:(1)粘合结构牢固、安全、可靠,比铆接、焊接螺栓连接等连接方式性能优越(2)粘合部位耐疲劳性好。
(3)能减轻结构质量,节省材料与费用。
(4)能密封,防腐蚀,可避免高温加工对材料性能上的损害。
(5)粘接方法可用于许多其他连接方法难以胜任的材料的连接,如薄膜材料与高强度、厚度大的固体材料的粘接。
但粘合技术和工艺方法有许多问题至今还没有得到很好地解决,如影响粘合质量的因素太复杂,粘合性能的分散性较大,粘合质量检验比较困难,大多数胶粘剂的耐热性能较差等,限制了粘合技术的应用。
三、橡胶粘合的主要内容
橡胶粘合在橡胶制品或橡胶复合制品制造过程中发挥了十分重要的作用,如在成型加工过程中,混炼胶与混炼胶之间的粘合能保证成型过程的顺利进行,提高半成品及成品的质量。橡胶制品中90%以上的要采用金属或纤维作为骨架或复合增强材料,要求橡胶与骨架材料牢固地结合成一个整体,才能充分发挥其增强作用。另外,许多其他材料如木材、型材、皮革等主要粘合的方法实现连接、复合。因此,橡胶的粘合主要集中在一下内容。
(1)未硫化胶之间的粘合;
(2)硫化橡胶之间的粘合;
(3)橡胶与纤维的粘合;
(4)橡胶与金属的粘合;
(5)橡胶与皮革、塑料的粘合;
(6)橡胶与其他非金属材料的粘合。
其中橡胶与纤维、金属的粘合最重要。
四、橡胶粘合技术的发展概况
粘合技术使用最早的是胶粘剂粘接不同的物体之后长时间的探索和发展,形成了目前较为成熟粘合效果良好的橡胶与纤维的粘合技术HRH、和RFL体系,橡胶与金属粘合的HRH、钴盐、镀黄铜等。
橡胶与金属的粘合,最早采用的是镀黄铜法和硬质胶法,其后发展了胶粘剂法和直接粘合法。黄铜是少数与橡胶直接粘合的金属之一,橡胶中必须含有硫黄,添加钴盐能改善粘合效果。镀黄铜金属与橡胶的粘合效果取决于镀制质量和镀层参数,随着子午线轮胎的快速发展,该粘合技术得到了广泛的应用。
硬质胶法在金属与软质橡胶粘合时被广泛应用,由于模量差异,软质橡胶与金属的粘合界面在剪切力的作用下容易脱层,在软质橡胶与金属之间加一层硬质胶可以解决这一问题,但是硬质胶法不耐冲击,不耐热,只能用于70℃一下使用场合,如实芯轮胎,胶辊的粘接。
橡胶与金属的粘接中,80%以上使用的是胶粘剂粘接,该技术简易有效,用途广泛,对不同的金属材料,可选用不同的胶粘剂实现橡胶与其牢固的结合,如广泛采用的Chemlock 胶粘剂。
直接粘合法工艺操作简便,粘接效果好,并且在和镀黄铜法并用方面已取得了良好的粘合效果。
橡胶与纤维的粘合,最早是采用酚醛树脂—胶乳浸胶法和涂胶液法,其后发展了直接粘合法。到二十世纪60年代,浸胶法工艺以成熟和定型,目前仍大量使用。对棉纤维、人造丝、维尼龙、尼龙等织物与橡胶的粘合有良好效果。但对聚酯、玻璃纤维、芳纶纤维的粘合效果不佳,因此在RFL体系的基础上调价Rp树脂(Pexul树脂)、封端的异氰酸酯、硅烷偶联剂等,粘合效果大大改善。胶料中使用间甲白体系再与浸胶纤维粘合,粘合效果非常好,目前广泛使用。
五、粘合效果的表征
目前普遍采用的方法是静态表征方法,如H抽出、T抽出、剥离、拉伸、剪切力。但许多橡胶制品是在动态下使用的,因此,目前加大了动态测试方法的研究,已开发出多种动态检测法,如屈挠、周期性冲击等。目前也在积极探索动态检测结果与静态检测结果之间的相关性,以及含骨架材料使用寿命的预测等。
第一章粘合的基本原理
第一节粘合的表面性质
一、固体表面的吸附性
由于固体表面层分子受周围的力场不平衡,因而存在表面能。固体
表面没有那样的流动性,因而不能想液体那样依靠收缩表面来降低
系统的表面能,只能从周围介质中捕获气相(或液体、或微小固相)
中的物质的分子平衡表面上不平衡力场,来降低表面能以使系统趋
于稳定,所以固体表面会产生较强的吸附作用。
物理吸附是通过范德华力吸附在表面,吸附过程中放热少,无选择性,吸附速度快,可在较短时间内达到平衡,吸附的分子层可能是单分子层,也可能是多分子层,吸附作用力弱。化学吸附是通过化学键合吸附在固体表面,吸附过程中放热量大,有选择性,吸附速度快慢,不易达到平衡,吸附的分子层为单分子层,由于是通过形成化学键吸附,所以吸附力强。
固体表面的吸附性对粘合既有有利的影响,也有不利的影响,在粘合时要充分考虑固体表面的吸附性。当两个表面在充分靠近时,表面层分子之间相互吸附,此时,两个表面接触越充分,接触面越大,吸附作用力就越大,要将两个表面剥离开所做的功越大,因而粘合效果好,粘合力强。所以在实现粘合时,可以通过给粘合面加压,使两个表面充分接触,提高粘合效果,因此粘合时加压是提高粘合效果的常用方法之一。固体表面吸附性对粘合不利的方面体现在粘合之前,固体表面吸附周围的气体分子、液体分子或小的灰尘颗粒等,是表面污染,粘合时如果不除去这些污染物,会在粘合界面处形成缺陷点或弱界面层,从而削弱粘合效果。所以要提高粘合效果,在粘合之前要对固体表面进行干燥或脱脂处理。
二、液体在固体表面的润湿与铺展
当液体与固体表面接触时,原有的气—固表面自动地被液—固界面所代替的现象叫润湿。润湿是发生在液—固界面上的常见现象,对粘合也有重要影响,如胶粘剂粘接固体时,橡胶与骨架材料粘合时,胶粘剂在固体表面润湿,橡胶在骨架材料表面润湿,就可以使胶粘剂或橡胶在固体表面上充分铺展,有更大的接触面积,吸附作用会增强,因而能提高粘合效果。
液体对固体的润湿程度用接触角来表示。当液体滴在固体表
面上达到平衡时会出现气—液、气—固和液—固三个界面张力呈
平衡的现象。在气、液和固三相交点处,液—固界面与气—液界
面的切线之间的夹角称为接触角或润湿角,用θ表示。由于平衡,
三相交界处的θ点所受的各种界面张力之和为零。所以有σ
g-s =σ
e-s +σg-e 2cos θcos θ=(σg-s -σe-s ) /σg-e (杨方程)。
若σg-s -σe-s <0,即σg-s <σe-s ,cos θ<>90°,此时液体在固体表面收缩,尽量缩小液—固界面,这种现象称为不润湿,接触角θ越大,不润湿的程度越大,当θ=180°时,完全不润湿。
若σ
g-s -σe-s >0,即σg-s >σe-s ,cos θ>0 <90°,此时液体皂固体表面自动地散开,增大液—固界面,这种情况称为润湿,接触角θ越小,润湿的越好。当θ=0°为完全润湿,即铺展。
接触角θ大小取决于两个表面的性质,当同属亲水或亲油物质时,θ一般小于90°,即润湿,当一个亲油一个亲水时,θ往往大于90°,不润湿。
三、表面极性
极性分子之间的相互作用力比非极性分子间的作用大。分子的极性源自于分子中各原子的电负性差异,电负性差异越大,极性越强。极性分子之间由于存在偶极力、诱导力和色散力,因此比非极性分子之间作用力强。当两个粘合表面含有极性基团时,在相互靠近时,分子之间的相互作用力大,因而有利于粘合。所以极性表面相对于非极性表面易粘合。
四、表面活性
表面活性是指固体表面可以反应的官能团或基团的反应能力大小及数量,如果表面具有易于反应的基团或官能团,则表面之间很容易发生化学反应,形成化学键,可以获得牢固而
持久的粘合效果。活性基团如
C C 、α-H 、-OH 、-NH2、-COOH 、C O
Cl 、HC CH
O 、-N=C=O 等,表面含有这些基团的材料比较容易实现牢固的粘合,表面活性基团数量越多,化学反应性越强,越容易实现粘合。许多表面活性很低的表面,可通过改性处理(如等离子体、超声波处理,γ-射线处理等)以及浸渍等方法,使其产生或吸附有高反应活性的基团,从而提高粘合效果,如聚酯纤维、芳纶纤维与橡胶的粘合,橡胶与金属的粘合,橡胶与玻璃纤维之间的粘合等。
五、表面粗糙度
任何一个固体表面都很难达到绝对的平滑,即使是精加工的研磨表面,也不是真正平滑的表面,而是由峰、谷组成的起伏不平的粗糙表面。通常用粗糙度表示表面不平滑的程度,以表面峰高或谷深的平均值来表示。该值越大,表面越粗糙。由于表面的不平滑性总是存在
的,因此,即使两镜面接触也不能在整个平面上达到分子间的接触。两固体表面间的接触通常只是固体表面最高峰的点接触,接触面积行为几何面积的1%左右。因此两固体表面,尤其是坚硬的固体表面之间不能靠分子吸附而粘在一起。
另外,有些固体表面还具有多孔性,如木材、皮革、纸张、织物、
陶瓷等材料,本身是多孔的,所以表面必然具有多孔性。金属、玻璃等
材料,基体是密实的,但金属表面暴露于空气中会生成具有孔隙的薄氧
化层,玻璃表面的碱性氧化物(Na2O和K2O)被凝结的水分侵蚀,原
有的Na2O和K2O所占据的空间会成为充满空气的孔隙,形成由Si-O骨架组成的多孔表面。
固体表面的不平滑性或多孔性,对粘合性既有贡献,又会存在损害。如果多孔表面、材料表面的孔隙中的空气在粘合时未被排除,就减少了量表面的接触面积,削弱了吸附作用,因而粘合效果下降。但当一个表面分子充分扩散扫另一表面的凹陷部分或孔隙中,就会增大两表面的接触面积,增加机械啮合力,从而能提高粘合效果,所以很多固体表面在粘合之前需要打磨,喷砂,蚀刻等操作,增大表面粗糙度,来提高粘合效果。当然,其中的一个表面在另一个表面上要能润湿,才能赶出孔隙中的空气,如果两表面之间不润湿,孔隙中的空气不能被赶出,粘合效果会下降,此时表面孔隙越少越好。由于固体表面的不平滑性和多孔性增大了固体的表面积,增大了表面能,因而吸附性加强,新生的多孔清洁表面在贮存中易被环境污染,影响粘合效果,因此粘合表面常需重新制备,不宜长期存放。
第二节粘合力
两种材料通过界面的相互作用产生粘合力,使其粘接为一体。粘合力越大,粘合越牢固。粘合力的性质决定于粘合剂和被粘材料的化学结构,主要有主价键力和次价键力两大类,主价键力即化学键合力,存在于原子或离子之间,包括离子键、共价键、金属键,次价键力即分子间作用力,包括范德华力(取向力、诱导力、色散力)和氢键。此外,还有界面静电引力,机械啮合力等。
一、化学键合力(主价键力)
主价键具有较高的键能,化学键合力是最强的粘合力,两表面之间形成的化学键越多,粘合力越大
1、离子键
又称电价键,是依靠正、负离子间的静电引力而产生的一种化学键,由原子间通过价电子转移而形成,无方向性和饱和性,其强度与正、负离子电价的乘积成正比,与正、负离子间的距离成反比。离子键的键能为583.8~1042.5KJ/mol。
2、共价键
又称原子键,一般指由两个原子通过共用电子对而产生的一种化学键,每一共用电子对
产生一个共价键。如果电子对是两个原子平均共有的,称非极性共价键;如果电子对不是平均共有的,而是偏属于某一原子的,称极性共价键。极性共价键因其电子对偏属程度不同,而具有不同程度的极性;如果共用电子对由其中一个原子单独供给,这种特殊的共价键称作配位键。共价键的键能:62.5~708.9KJ/mol。
3、金属键
金属原子依靠流动的自由电子相互结合形成金属键。无论金属或合金,在其晶体或熔融体中,金属原子的自由电子(由原子上脱落下来的电子)都可以移动或流动形成金属键。金属键的键能112.6~346.1KJ/mol.
二、分子间作用力
分子间作用力包括范德华力和氢键,这是粘合表面普遍存在的作用力。
1、范德华力(由取向力、诱导力、色散力组成)
(1)取向力:是极性分子永久偶极之间产生的引力,取向力与分子的偶极矩(分子内正、负电荷中心间距离与所带电荷的乘积)的平方成正比,与两分子间距离的六次方成反比,分子的极性越大,分子间距离越小,产生的取向力就越大。取向力与绝对温度成反比,绝对温度越高,分子间取向力越小。
(2)诱导力,是分子固有偶极和诱导偶极之间的静电引力。诱导偶极的产生是由极性分子和非极性分子相互靠近时,极性分子固有偶极的电场作用是非极性分子的电子云吸向偶极的正端,非极性分子的电子云与原子核之间因诱导发生了相对位移,由此产生静电引力。
诱导力与极性分子偶极矩的平方成正比,与被诱导分子的变形度成正比,与两分子间距离的六次方成反比,诱导力与温度无关。
(3)色散力:是分子分散作用产生的引力。色散作用是指分子内电子对原子核的瞬间不对称状态,由于电子处于不断运动之中,正负电荷中心的瞬时不重合状态总是存在的,由这种瞬时的不重合作用产生了瞬时偶极,瞬时偶极又诱导邻近分子瞬时诱导偶极。
色散力与分子间距离的二次方成反比,与环境温度无关。低分子物质的色散力较小,由于色散力具有加和性,因此高分子材料的色散力相当可观。非极性高分子材料中,色散力占全部分子作用力的80%~100%。
取向力、诱导力和色散力均随分子间距离增大而急剧下降,上述力作用的有效距离为1nm。
2、氢键
在化合物中,凡是和电负性较大的原子连接的氢原子都有可能再和同一分子或另一分子中电负性较大的原子相连接,这样形成的键称作氢键。能形成氢键的电负性原子(如N、O、F)都是有较小的原子半径和共用电子对。氢键力大小与电负性原子的电负性有关,电负性越大,氢键力越大。此外,电负性原子的半径越小,邻近氢原子接近它的机会越多,其氢键力也越大。氢键与化学键不同,其键长较长而键能较低,容易遭到破坏,但比范德华力要强。
氢键可以发生在分子内(分子内氢键),也可发生在分子之间(分子间氢键)氢键力有
饱和性和方向性。
分子间作用力广泛存在于粘合体系中,各种次价键力的最大键能:
氢键:50.0KJ/mol ; 色散力:41.7 KJ/mol ;
取向力:20.8 KJ/mol ; 诱导力:2.08 KJ/mol ;
三、界面静电力
当金属与非金属材料(如高分子胶粘剂)紧密接触时,由于金属材料对电子的亲和力低,容易失去电子,而非金属材料对电子的亲和力高,容易得到电子。因此,电子可以从金属材料移向非金属材料,使粘合界面发生接触电势,从而形成双电层,产生了静电引力。一切具有电子给予体和电子接受体性质的两种材料相互接触时都可能产生界面静电引力。
四、机械啮合力
机械啮合力实际上是两表面间的摩擦力,由于一个表面分子渗透到另一表面的凹陷部位或孔隙中,形成嵌合、锚合、钉合、树根状结构,剥离时由于摩擦力增大,因而做的功多,粘合性好。
第三节界面过渡层的结构与性能
一、界面过渡层形成的条件
在相互粘合的两相表面之间都存在着具有一定强度的过渡层,又叫界面层。不仅橡胶与橡胶之间,橡胶与骨架材料之间,甚至橡胶与液体胶粘剂之间都有这种界面层存在。界面层的结构和组成与两表面本体的结构和组成不一样。真正起粘合作用的就是这层界面层,因此界面层的厚度和强度就决定了材料之间粘合的效果。但在实际粘合过程中,由于工艺上无法保证聚合物交联或熔体间流动的均匀性,导致分子结构和微区局部结构的不均匀,而成为缺陷点,从而削弱粘合效果,这种带有缺陷点的界面层称为弱界面层。
1、界面过渡层形成的热力学条件——必要条件
两个表面接触形成一个界面,界面分子间的相互作用首先必须使用两相表面分子之间实现充分接触才能产生,界面分子间的充分接触又必须以两相物质间的相互浸润、吸附、流变和扩散渗透或互溶才能达到,这种变化过程既是热力学的变化过程,又是动力学的变化过程。(1)粘合表面之间的润湿性是形成界面过渡层形成的首要条件
两个表面之间只有润湿才能实现充分接触。通常把胶粘剂或粘合物当作液体,把被粘物当作固体,只有当液体能很好的润湿固体的表面并形成完全的接触,才能实现良好的粘合。
液体表面与固体表面接触时,处于界面区的两种分子在朝向各自内部方向受到同种分子的吸引作用,在朝向界面方向,受到来自不同分子的吸引力作用。此两种吸引力的合力称为
界面张力。如果固体的低能表面固体,其引力作用低于液相分子自身之间的吸引力作用,则界面区的液体分子就有一种向液体内部收缩的张力,这就使液体处于不能自动展开的非润湿状态。如果固体为高能表面固体,则界面区的液体分子就有一种被吸附于固体的压力迫使其在固体表面自动铺展开来,这就是液体处于润湿状态。所以液体在固体表面能润湿,必须满足以下条件:
①固体的表面自由能(表面张力)要大(吸附作用大)。
②液体的表面张力要小,但不能太小(表面收缩性小,有足够的内聚强度)
③界面张力要小。(界面上两分子亲和性好)
所以,为了使液体粘合材料能充分地润湿固体的表面,必须选用表面张力小于固体临界表面张力的液体。临界表面张力不是固体的表面张力,而是能完全润湿固体表面的液体的表面张力最高值。
非极性高聚物固体的临界表面张力γc较小,而一些常用的液体胶粘剂的表面张力要高于非极性高聚物的临界表面张力。因此非极性高聚物固体材料较难粘接,必须进行表面处理,以提高其表面能。
高聚物固体属于低能表面固体,而金属、玻璃等无机固体属于高能表面固体,所以高分子胶粘剂液体的表面张力一般都小于高能表面固体的临界表面张力,因而能完全润湿这些固体的表面。但金属、玻璃表面被油类脂肪烃污染后,表面能会急剧下降,胶粘剂的润湿变得非常困难,所以粘接金属材料时,必须对其表面进行预先处理,才能提高其表面能。
常用胶粘剂的表面张力值(达因/cm220℃)
(2)粘合界面区两相分子的互溶性是界面层形成的重要保证
两个粘合面在接触时,两相表面分子间的相互扩散和溶解作用,尤其是胶粘剂以大分子或其链段穿过界面的扩散,对粘合结构形成和粘合效果十分重要。当液体胶粘剂的大分子扩散到固体被粘物中达到一定深度后,两相分子间的物理作用力总和可以超过化学键能,大分
子的扩散程度越深,其与被粘物之间形成的粘合接触点也越多。所以界面区两相分子之间的相互扩散很重要。但随着润湿过程而发生的分子间相互扩散和溶解作用是保证和扩大界面分子间接触程度的主要条件,导致过渡区的形成。
两个表面分子之间的扩散和互溶性取决于两相的溶解度参数的差异,二者溶解度参数相差越小,扩散和互溶性越好,粘合效果越好。一般,二者溶解度参数之差小于1.7~2.0时,高分子之间易于互溶。当二者溶解度参数之差小于2时,则难以溶混。实践证明,两相分子间的溶解度参数差别越大,相容性越差,相互间的粘合效果也越差,甚至无法粘合。
通过以上分析,为了使两粘合面之间的分子实现充分的接触,从热力学表面能考虑,就必须提高胶粘剂或粘合物液体材料对被粘固体材料表面的润湿能力,条件是γe<γc,这是实现良好润湿的必要条件,尽可能减小两相分子间的溶解度参数的差别。
对表面不润湿的固体,可通过表面改性的技术改变液体对其润湿性,如用偶联剂处理玻璃纤维表面。
2、界面过渡层形成的动力学条件——充分条件
为了达到两相分子在界面上的充分接触,二者之间还必须在界面上进行相互扩散、渗透和互溶,才能使界面分子之间达到足够紧密的程度。液体在固体表面的扩散、渗透和互溶,与液体的流变性能和分子的活动能力直接相关,一切影响液体的流变性能和分子的活动能力的因素,如液体的粘度,分子量大小及其分布,温度,压力,时间等。以及固体表面的粗糙程度,聚合物的交联或固化的速度等,都是界面层形成的动力学条件。
(1)接触区的扩散现象
用胶粘剂来粘接固态时,当胶粘剂的大分子扩散至被粘物中时,在达到一定厚度之后,两相分子之间作用力的总和可以超过化学键;大分子链扩散越深,它与被粘物之间形成的粘合接触点就越多。
高分子的扩散速度可用扩散系数D来表征,与大分子链的柔顺性、分子量大小、分子中超分子结构、填料等有关。一般,分子链越柔顺,越易扩散,分子量越大,扩散系数D 越小;分子中含有超分子结构,扩散系数小,甚至不被扩散。高聚物中加入填料,对大分子有吸附作用,扩散系数小,但能增大内聚力。
(2)温度、压力和时间的影响
提高粘合过程的操作温度、压力和粘合接触受压时间,都有利于胶粘剂或粘合物液体的润湿及粘合界面上两相分子之间相互扩散和渗透作用,有利于过渡层的形成。
二、界面过渡层的结构与性能
1、界面过渡层的尺寸
对于自粘及互溶性很好的粘合两相体系来说,界面过渡层的厚度尺寸可以达到几百纳米,甚至消失。随着界面过渡层厚度尺寸的增大,粘合强度逐渐增大,以至达到完全均一的整体,界面结构消失。
对于性质不同的两相粘合来说,界面过渡层的厚度及其对粘合结构的影响,既与界面过
渡层的性质有关,又与两相的性质有关,还与两相结构单元的厚度尺寸有关。界面过渡层厚度太小,粘合强度低。随着界面分子间的相互扩散、渗透或互溶,界面层的厚度尺寸增大,粘合效果提高。但界面过渡层厚度太大时,会由于弱界层出现的机会增大而导致粘合效果变差。另外,界面过渡层的具体尺寸还要依两相材料的性质而定,原则是界面过渡层要适应应力分布上的要求;在力学性能上有逐渐的过渡或应用。对刚性大的粘合剂,过渡层的厚度尺寸应小些,而对弹性体来说,过渡层的厚度尺寸应适当加大。
2、界面过渡层的结构
界面过渡层是不均匀的多相结构。
3、界面过渡层的形变特性
存在微区局部变形(不均匀性),对提高胶粘剂材料的强度,尤其是抗剥离、耐疲劳性等性能起着非常重要的作用。
三、粘合结构的破坏及影响因素
粘合结构破坏有三种形式:一种是界面破
坏,破坏发生在界面层;二是内聚破坏,在界面
区以外发生破坏,被粘材料或胶粘剂本身发生破
坏,这是界面强度超过内聚强度所致;三是混合
破坏,既有部分界面破坏,又有部分内聚破。
① ② 粘结剂选择不当。
③ 粘合剂粘度过大。
④ 胶粘剂的胶凝固化速度过快,界面区有气孔。
⑤ 粘合剂固化后的收缩性大。
⑥粘合剂与被粘物之间热胀冷缩的差异,导致内应力产生。
⑦固化工艺不合适(温度、压力和时间)。
⑧水分的存在。
第二章橡胶与橡胶的粘合
橡胶是一类具有高弹性的有机高分子材料,模量较低,不同橡胶材料之间模量差异不是很大。但不同橡胶之间粘着性有很大差异。有些橡胶具有良好的粘着性,很容易粘合,如NR、CR、PU等;而有些橡胶的粘着性很差,很难粘合,如EPDM、IIR、Q等。这与橡胶的分子结构有关。
橡胶与橡胶粘合,在橡胶制品生产制造过程中普遍存在,如混炼胶的自粘,不同未硫化胶的互粘,在多层或多部件构成的制品加工过程中,层间或各部件之间需要有良好的粘合,才能保证成型工艺的顺利进行。另外硫化橡胶制品在使用的过程中损坏之后的修补,由硫化橡胶制备复合制品时,均要采用相应的粘合技术。
第一节未硫化橡胶之间的粘合
未硫化橡胶是指还没有交联的橡胶,包括生胶和混炼胶。由于没有交联,未硫化胶中橡胶分子链仍然是线性结构,在橡胶的良溶剂中可以溶解,具有较高的流动性和分子活动能力,因此未硫化胶粘合比较容易实现。但对EPDM、IIR、Q等粘着性差的未硫化胶,需要争取一定的粘合技术提高其粘合效果。对NR、CR、PU等易粘的胶料,不需要经过特殊的处理就能实现良好的粘合。
一、未硫化胶的表面性质
由于未硫化胶具有较好的流动性,容易变形,具有表面张力,但橡胶尤其是非极性橡胶的表面张力较小,表面自由能不高,所以未硫化胶表面的吸附性不是很强。极性橡胶表面有极性,表面张力较大,内聚能密度大,吸附性要比非极性橡胶强。同为非极性或极性的未硫化胶之间,由于表面张力和界面张力较小,两表面之间容易达到润湿状态,可以实现充分的接触,而且由于相容性好,两表面分子之间容易扩散和渗透,形成较厚的过渡层,甚至过渡层消失。因此未硫化胶的表面性质是有利于粘合的。
二、未硫化胶的自粘性及影响因素
未硫化胶的自粘性是指胶料的粘性,是两个同质胶片在小负荷、短时间压合后,将其剥离开所需的力或所做的功,剥离力越大,粘性越大,自粘性好,胶片之间不需增粘就可以很好地粘合。
未硫化胶的自粘性取决于胶种的性质及工艺条件。橡胶品种不同,其分子链的柔顺性不同,活动能力也不一样,自粘性也不同。一般来说,未硫化胶的自粘性受橡胶分子链的柔顺性、饱和性、分子量大小、断链后自由基的活性、结晶性、极性以及胶料中填料的品种和用量等的影响。通常,柔顺性好的橡胶分子链活动能力强,在表面接触后,易扩散和渗透,形成较厚的界面层,自粘性要好。橡胶分子链的饱和性和极性对自粘性影响很大,饱和性橡胶
自粘性较差,尤其是非极性的饱和橡胶如EPDM、EPM、IIR、Q等,自粘性很差。极性不饱和橡胶(如CR)有良好的自粘性。对同一胶种,平均分子量小的,流动性好,更容易扩散、渗透和铺展,所以自粘性好。生胶塑料的目的之一就是提高胶料的自粘性。橡胶分子链的结晶性对自粘性也有重要影响,常温下结晶的橡胶,由于晶体颗粒限制了分子链段的运动,扩散和渗透性变差,因而自粘性较差,如TPI。但橡胶分子链在拉伸过程中由于取向而产生诱导结晶,此时结晶颗粒会限制两表面层分子的脱离,以及提高其格林强度。所以具有自补强性的橡胶自粘性较好,如NR、CR、IR。IIR虽然具有自补强性,但由于IIR分子链两侧含有密集的侧甲基,分子链的活动能力差,在表面接触后难以扩散和渗透,界面层很薄,所以自粘性不好。EPDM、BR、SBR的自粘性不好,与其非自补强有关。
另外胶料中加入填料,由于填料可以与橡胶分子链发生吸附,一方面能提高未硫化胶的格林强度,另一方面也会限制分子链的活动能力。由于不同填料,其粒径大小,结构度高低,表面活性高低不同,与橡胶的吸附作用不同,因而对自粘性有不同的影响。在填料用量较小(不足以严重影响到分子链活动能力)时,粒径小,表面活性高,结构度高的填料与橡胶的相互作用强,胶料的格林强度高,因而自粘性好。但当填料的用量过大时,胶料的粘度太高,流动性差,界面处分子链的扩散和渗透能力变差,自粘性下降。
未硫化橡胶的自粘性还与工艺条件有关,在高温、高压下,两表面可以充分接触,橡胶分子链的扩散和渗透能力增强,自粘性好。
提高未硫化胶粘性的方法
①通过塑炼、混炼工艺提高胶料的可塑度,降低分子量。
②在胶料中添加相容性好的增塑剂。
③在粘合面处刷汽油等良溶剂。
④在粘合面上涂胶浆。
⑤在胶料中使用增粘剂。
⑥升高粘合面的温度。
⑦增加粘合部位的压力。
⑧保持粘合表面清洁,粘合前用塑料薄膜包覆粘合面。
⑨防止胶料喷霜。(配方和工艺上改进)
⑩尽可能少用或不用润滑性的加工助剂,如蜡、凡士林等。
三、未硫化胶的互粘性
如果是两种不同的未硫化胶,其粘合面的粘性成为互粘性。未硫化胶的互粘性比自粘性要复杂一些,如粘合面的润湿性,相容性等,对互粘性也有影响。如果两未硫化胶表面的界面张力小,橡胶分子链之间的相容性好,两表面易润湿,易扩散和渗透,因而粘合效果好,互粘性好。如果两未硫化胶中橡胶分子链相同(仅配合剂品种和用量不同),两胶料之间的互粘性取决于该胶种的自粘性。如果两胶料中胶种不同,互粘性除了鱼各自的自粘性有关外,还与两胶种的相容性有关,相容性好,易扩散和渗透,所以互粘性好。
第二节 硫化橡胶的粘合
一、硫化橡胶的表面性质
硫化橡胶更接近于固体,由于线型大分子被交联成网状结构,分子链及链段的活动能力大大下降,表面不容易弯曲收缩,因而有较高的表面自由能,而且在硫化压力作用下,硫化橡胶表面相对较光滑。所以当两个硫化橡胶表面接触时,由于分子链网络化,扩散和渗透难以进行,两硫化胶之间不能直接产生较强的粘合作用力,粘合相对较难。
二、硫化橡胶的粘合
硫化橡胶之间的粘合,通常采用胶粘剂法,即在两个硫化橡胶表面涂上胶粘剂,再让液体胶粘剂固化。硫化橡胶之间的粘合效果取决于硫化胶的交联密度,胶粘剂的类型及其组成,以及粘合工艺。硫化胶的交联程度越深,分子链的活动能力越差,粘合越难以进行。
1、胶粘剂的配方及制造工艺
橡胶胶粘剂有单组分和双组分之分,有溶剂型和水性型之分两大类。单组分胶粘剂通常是以橡胶(干胶或胶乳)、树脂为主要原料,配合增粘配合剂或偶联剂、固化剂、促进剂、填料或溶剂等加工而成的一种粘稠状液体混合物,其制造过程中经常加极性的树脂以提高粘合效果。双组分胶粘剂中粘料由两种高分子材料组成,如不同橡胶、不同树脂、橡胶和树脂等。
溶剂型胶粘剂的配方组成
水性型胶粘剂的配方组成
① 生胶塑炼(多段塑炼),可塑度要求0.5以上。
② 混炼胶的制备:开炼机或密炼机混炼胶料。
③ 混炼胶造粒:混炼胶切条在造粒。
④ 按比例加入良溶剂,用搅拌器搅拌使其溶解。 2、胶粘剂粘合的工艺
(1)粘合面打磨。(砂轮或砂纸)
(2)粘合面清洁。(毛刷清扫,用溶剂擦洗)
(3)粘合面涂胶粘剂,要求薄而均匀。
(4)干燥除溶剂。(溶剂挥发完全)
(5)粘合,需要加压。
(6)停放一段时间后再使用。
3、硫化橡胶间的粘合方法
(1)胶粘剂室温硫化法:采用室温固化型胶粘剂。
(2)胶粘剂热硫化法:采用热硫化型胶粘剂。
(3)半硫化法:橡胶半硫化,半硫化胶片之间加粘合胶料或涂胶粘剂,再加压热硫化。
(4)混炼胶片贴合再硫化法:将两个同质或异质混炼胶片先贴合,再加压热硫化。
第三章 橡胶与纤维的粘合
第一节 概述
一、橡胶制品中使用的纤维品种及结构特点
纤维材料在橡胶制品中使用非常普遍,是橡胶制品增强的主要骨架材料之一。在橡胶制品中最早使用的纤维是棉纤维,其次是人造丝,尼龙纤维出现后就取缔啊了棉纤维和人造丝在橡胶中的应用,成为橡胶制品中最主要的骨架材料。随着对橡胶制品的性能要求的不断提高,新型合成纤维的开发取得突破性的进展,强度更高的聚酯纤维和芳纶纤维的出现,使得橡胶制品的承重耐高压能力大大提高,在轮胎、胶管、胶带领域得到了广泛的应用。另外,耐热性、阻燃性优异的玻璃纤维也在要求苛刻的橡胶制品中得到广泛应用。
1、纤维的分类
2(1)棉纤维:是纤维素纤维的一种,比较短(10~15mm ),帘线的强度主要靠纤维之间的捻合在一起的摩擦力作用,所以棉帘线的强度只有其纤维强度的55%~58%。由于其化学组成为纤维素,纤维素表面含有大量的-OH ,带有极性,具有比较高的化学反应性,表表面活性高,且表面粗糙,表面有许多绒毛和纤维素末端。在动态疲劳情况下,棉帘线的纤维之间会逐渐松动散开,,不仅降低捻合作用和帘线的强度,而且由于摩擦生热会进一步降低帘线的强度。所以棉帘线的动态疲劳强度比人造丝连线要低7~12倍。
(2)人造丝:纤维长,帘线的强度主要由纤维的强度来决定,器强度为纤维强度的72%。人造丝纤维表面比较光滑,纤维端头少,含有适量的-OH ,化学活性比较低,与橡胶的粘合效果不及棉纤维。
(3)尼龙纤维:聚酰胺纤维,含有C O
H N 基团;表面光滑,端头少,末端含有少量的-OH 、-COOH ,与橡胶之间的粘合比人造丝难。尼龙纤维的强度高,耐疲劳性好,但热收缩
变形大,使用前要进行热伸张处理。
(4)聚酯纤维:纤维表面非常光滑,含C O
O 基团,活性低,表面上是由在分子量末端含有少量的-OH ,表面具有疏水性,与橡胶之间的粘合非常困难,需要对纤维进行特殊处理。聚酯纤维的扯断强度高,定负荷伸长率小,变形小,耐冲击性能和耐热性好,吸水性低,但易胺解、水解,耐光性差,生热高。
(5)芳纶纤维:芳香族聚酰胺纤维,其酰胺键的85%以上与两个芳香族基直接结合。H N C O
,虽然酰胺键有一定的活性,单被苯环屏蔽,所以反应活性很低,表面非常光滑,与橡胶的粘合非常困难。但芳纶纤维的轻度是同直径钢丝的6~7倍,耐疲劳性比钢丝好很多,尺寸稳定性好,滞后小。与橡胶的亲和性优于钢丝,可代替钢丝在轮胎中的应用,其应用效果取决于芳纶纤维与橡胶的粘合效果。
二、橡胶与纤维的粘合原理
1、纤维的表面性质:
①多孔性。由纤维捻成的帘线或织成的布,有许多缝隙; ②极性。各种纤维表面均含有极性基团,具有极性;
③吸附性。和其他固体一样,纤维表面也有一定的吸附性;
④化学吸附性。有些纤维,如棉纤维、人造丝、尼龙纤维表面含有较多的可反应基团,
尤其是棉纤维,如-OH 、-COOH 、
C O H N ;有些纤维,如聚氨酯纤维,芳纶纤维,含有极少数的-OH 或-COOH ,虽然C O O 、C O H N 具有一定的化学反应性,但被苯环屏蔽,
化学反应性很低,是化学惰性表面。玻璃纤维表面由-Si-O-,-Si-OH 等基团,具有一定的化学反应性。
2、橡胶与纤维的粘合原理
橡胶与纤维之间的粘合作用主要表现为以下几种:
(1)机械粘合。橡胶向纤维的缝隙中扩散和渗透,形成钉合、锚合、嵌合。树根固定等机械作用。这是橡胶与纤维的=粘合的主要作用之一。由于固体橡胶的粘合度较高,流动性较差,橡胶向纤维缝隙中国扩散和渗透作用不是很充分,缝隙中还存在有部分空气,形成相界面层,所以直接用橡胶与纤维粘合,效果并不理想。
(2)物理粘合。由于许多纤维表面带有极性,并含有-OH 、-COOH 、-NH-等基团。当橡胶与纤维表面充分接近时,有较强的物理吸附作用,橡胶中含有-OH ,含氧基团,含氮基团等还可与纤维表面的-OH 、-COOH 、-Si-OH 形成氢键,进一步增加哦吸附性。但由于聚酯,芳纶纤维表面的-OH 、-COOH 数量极少,极性基团C O O 、C O
H N 被苯环屏蔽,
橡胶中的极性分子很难与其发挥作用,所以橡胶与聚酯,芳纶纤维粘合时,物理粘合作用较弱。对棉纤维、人造丝、尼龙纤维,玻璃纤维,物理粘合作用较强,成为粘合作用力之一。
(3)化学粘合。对橡胶与棉纤维,人造丝纤维、尼龙来说,由于表面具有一定的化学反应(-OH、-COOH),较容易与橡胶中的配合剂或橡胶分子链发生化学作用,形成化学键,容易突现牢固而持久的粘合。所以橡胶与棉纤维、人造丝、尼龙纤维较容易突现牢固的粘合。玻璃纤维表面的Si-O—Si基团可以被空气中的水蒸气水解成-Si-OH,-Si-OH具有与醇-OH 类似的化学反应性,所以也具有较高的化学反应性,用偶联剂来处理玻璃纤维表面,就可以突现偶联剂分子与玻璃纤维表面的-OH反应。偶联剂分子还与橡胶分子反应。因而可以突现橡胶与玻璃纤维布之间牢固的粘合。举止和芳纶纤维由于表面化学反应性很低,除了末端的-OH可发生极少的化学作用,其他地方均不与橡胶发生化学作用。所以橡胶直接与聚酯、芳纶纤维粘合,几乎没有化学粘合,因此粘合效果很差。为了改善橡胶与聚酯、芳纶纤维之间粘合性,必须对聚酯和芳纶纤维进行表面改性处理,如浸带有多种反应基团的浸胶液,等离子体处理,γ-射线处理,超声波处理等,使其表面带有可反应的基团。然后再与橡胶粘合。因此,橡胶与各种纤维之间要突现牢固粘合,主要还是依靠化学粘合。
为了增强橡胶与纤维之间的机械粘合、物理粘合与化学粘合作用,需要对各种纤维进行浸胶或涂胶处理,并在胶料添加一些可与浸胶纤维表面的基团能反应的物质,提高粘合效果。
三、橡胶与纤维的粘合方法
(一)纤维浸胶法
该方法是将各种纤维在各自对应的浸胶液中浸泡一段时间,然后干燥,使纤维的缝隙、孔洞和表面充满或附着一层浸胶液层,来提高橡胶与纤维粘合效果。该法是提高橡胶与各种纤维材料粘合效果最常用的方法。浸胶液的配方组成、浸胶工艺即胶料配方、硫化工艺是决定粘合效果的关键因素。对不同的纤维材料,浸胶液的配方组成不一样,浸胶工艺也有差别。纤维浸胶法有一步法和两步法两种。一步法,浸胶过程只浸一次,两步法需浸两次,第一次浸激活剂液,干燥后第二次浸RFL浸渍液。
1、提高浸胶纤维材料与橡胶之间粘合强度的方法
为了提高浸胶纤维材料与橡胶之间的粘合强度,一方面要提高浸胶层与纤维之间、浸胶层与橡胶之间在粘合界面上的相互作用力;另一方面还要控制浸胶层的模量或定伸应力,改善纤维-橡胶界面上的应力分布状态,减小界面上的剪切应力作用(即模量过渡)。
(1)增加纤维与浸胶层上分子之间的相互作用力的方法:
①在浸胶液中加入极性物质,如白朊,酪素等含蛋白质物质,同时加入促进剂更能提高界面分子间作用。
②在浸胶液的乳化大分子中引入极性基团,如-COOH,吡啶基(N)等,即使用羧基胶乳和乙烯基吡啶胶乳。
③在帘线表面涂浸皂剂使表面皂化(活化),加大胶层与帘线间的接触面积。
④在胶乳中加入炭黑分散体,胶层与帘线间的紧密程度。
⑤使两相分子间在界面上发生化学结合。如在浸胶液中加入酚醛树脂,封端的异氰酸酯
[橡胶工艺原理]橡胶材料与配方
《橡胶工艺原理》讲稿 绪论 一.橡胶材料的特点 高弹性弹性模量低,伸长变形大,有可恢复的变形,并能在很宽的温度(-50~150℃)范围内 保持弹性。 粘弹性橡胶材料在产生形变和恢复形变时受温度和时间的影响,表现有明显的应力松弛和 蠕变现象,在震动或交变应力作用下,产生滞后损失。 电绝缘性橡胶和塑料一样是电绝缘材料。 4.有老化现象如金属腐蚀、木材腐朽、岩石风化一样,橡胶也会因为环境条件的变化而产生 老化现象,使性能变坏,寿命下降。
必须进行硫化才能使用,热塑性弹性体除外。 必须加入配合剂。 其它如比重小、硬度低、柔软性好、气密性好等特点,都属于橡胶的宝贵性能。 表征橡胶物理机械性能的指标 1.拉伸强度又称扯断强度、抗张强度,指试片拉伸至断裂时单位断面上所承受的负荷,单 位为兆帕(MPa),以往为公斤力/平方厘米(kgf/cm2)。 2.定伸应力旧称定伸强度,指试样被拉伸到一定长度时单位面积所承受的负荷。计量单位 同拉伸强度。常用的有100%、300%和500%定伸应力。它反映的是橡胶抵抗 外力变形能力的高低。
3.撕裂强度将特殊试片(带有割口或直角形)撕裂时单位厚度所承受的负荷,表示材料的 抗撕裂性,单位为kN/m。 4.伸长率试片拉断时,伸长部分与原长度之比叫作伸长率;用百分比表示。 5.永久变形试样拉伸至断裂后,标距伸长变形不可恢复部分占原始长度的百分比。在解除 了外力作用并放置一定时间(一般为3分钟),以%表示。 6.回弹性又称冲击弹性,指橡胶受冲击之后恢复原状的能力,以%表示。 7.硬度表示橡胶抵抗外力压入的能力,常用邵尔硬度计测定。橡胶的硬度范围一般在20~100 之间,单位为邵氏A。 二.关于橡胶的几个概念
橡胶粘接用胶
橡胶粘接用胶 (1]正确判断被粘橡胶的具体品种橡胶分天然橡胶与合成橡胶两大类,合成橡胶又有很多品种,不同品种的橡胶,所用胶粘剂是不同的。因此,对于橡胶的自粘或互粘,必须首先判断被粘橡胶的具体品种.才能选择合适的胶粘剂。判断橡胶制品品种的简单、有效方法,可参考题5-3。 (2)选择合适的胶粘剂橡胶的粘接、橡胶与金属和非金属材料的粘接,一般来讲,均应选用橡胶类胶粘剂为妥。橡胶类胶粘剂的品种较多,有丁苯橡胶胶粘剂、氯丁橡胶胶粘剂、丁基橡胶胶粘剂、丁腈橡胶胶粘剂、改性橡胶胶粘荆、天然橡胶胶粘剂等。不同的胶粘剂,其性能和用途也不同。 橡胶的粘接,应该选择与被粘橡胶同一品种的胶粘剂。例如要粘接丁腈橡胶制品,则选择丁腈橡胶胶粘剂。 橡胶与金属的粘接,应首先考虑被粘橡胶的具体品种来选择相应的橡胶类胶粘剂。为提高粘接强度,也可选用改性橡胶胶粘剂,如氯丁一酚醛胶粘剂、丁腈酚醛胶粘剂等胶粘剂。因为这一类胶粘剂既有橡胶类胶粘剂的特性,又有树脂类胶粘剂的特点因而,粘接效果会大大提高。 (3)粘接工艺方面表面处理十分重要,橡胶的表面处理,一般经表面粗化、脱脂即可,但某些橡胶(如氟橡胶、硅橡胶等)要对表面进行化学处理或预涂一层偶联剂。 橡胶表面处理未能达到粘接的要求,则橡胶的粘接往往会失败。 晾置的时间要掌握适当,长则表面结膜,失去粘性;短则表面残留溶剂,降低粘接强度。橡胶的粘接,一般采用的橡胶类胶粘剂均含有溶剂,含溶剂的胶粘剂涂胶后,必须晾置一定时间,一般均室温晾置。氯丁胶粘剂、丁腈胶粘剂晾置10~l5min;聚氨酯胶粘剂晾置10~20min: 丁腈一酚醛胶粘剂晾置20~30min,待溶剂挥发后合拢。 橡胶类胶粘剂合拖时应一次对准位置,不得错动,不得撕下重贴。否则会使粘接失败。合拢后用圆棍壤压或木锤敲打、压平,排除界面空气,使之紧密接触,提高粘接效果。
橡胶黏合剂PL-600
橡胶黏合剂PL-600也是橡胶抗疲劳剂PL-600,目前在橡胶生产行业得到广泛运用,主要适用轮胎胎体配方及与胎体相邻的部件配方,提高胎体的动态抗疲劳性能,尤其对胶与帘线老化后结合力的提高有着非常优异的效果。下面由橡胶黏合剂PL-600厂家恒力特新材料公司为大家介绍下橡胶黏合剂的相关知识,希望大家对这个行业有新的认识。 橡胶与金属粘合剂是指由普力通生产的一款用于橡胶与金属的粘结胶水。随着橡胶工业的飞速发展,橡胶复合材料得到广泛的应用,而橡胶与金属胶粘剂的质量是复合材料成功的关键,复合制品种类的增多及应用领域的拓展,对粘合技术的要求越来越苛刻。传统的氯化橡胶法、异氰酸酯法等技术已不能满足新的要求。美国LORD公司于1956年专门研发了一种橡胶与金属胶粘剂,它可用于橡胶与金属
的粘结,也可用于橡胶与塑料、纤维织物粘结。随后,民族工业普力通(polyton)也相继研发生产出能和国外产品相媲美的民族胶黏剂。 表面处理:机械处理(喷砂)后脱脂,或化学处理,以除去加工油,锈或其他氧化层。使用钢砂(珠)喷普通钢材,铸铁等铁磁性金属,表面处理后可停放时间应控制在再次出现氧化生锈之前;用石英砂喷不锈钢,铝,黄铜,锌和其他非铁磁性金属,且在表面处理后90分钟内必须完成涂胶。 搅拌:在使用之前必须充分搅拌,达到均匀混合后方可使用。 涂胶方法:浸渍法、喷涂法、刷涂法、辊涂法、转移法。 干燥:涂胶后应在清洁空气中干燥约30~45分钟(室温),使用65-82C鼓风烘箱有利于更快并彻底烘干涂胶件。 停放:若涂胶件被妥善存放,隔绝粉尘、油污和水汽等影响,最长甚至可停放一月。
硫化:当涂胶件被放置于热模中后,应迅速填充橡胶并合模,防止胶粘剂预固化而失效,以确保胶粘剂和橡胶同时硫化,并获得最佳粘接性能。 硫化时间:取决于胶料硫化时间。 恒力特新材料是集科技研发、生产、销售为一体的高新技术企业,是国内和华东地区橡胶助剂骨干企业,恒力特牌橡胶防老剂 8PPD-35、BLE、BLE-W、BLE-C、SP、SP-C、AW、DFC-34等系列,抗疲劳剂PL-600、橡胶耐磨剂SL-A、橡胶助剂EVR、抗热氧剂RW、阻燃剂、橡胶粘合剂HLT-301、HLT-501系列,橡胶促进剂DTDM、DBM系列,橡胶补强剂FH、FHT系列,都得到了轮胎、胶带、胶管及橡胶制品企业的认可。 公司坐落在安徽阜阳颍州经济开发区,生产工艺先进,检测仪器齐全,产品性能稳定,本着“和谐、诚信、奋进”的企业精神,遵循以“过硬的产品、更好的服务”为宗旨,以更好的性价比为橡胶制品行业提供更多、更优的选择。如果您想进一步了解,可以直接点击官网恒力特新材料进行在线咨询。
橡胶及金属的粘合
橡胶与金属的粘合 在汽车工业中,橡胶与金属的粘合是很普遍的,骨架油封、发动机及变速箱支承、摆壁衬套、车身支撑等都是典型的金属——橡胶结构。金属和橡胶的结合强度对产品的性能有着至关重要的影响。金属橡胶件的寿命很大程度上取决于两种材料的粘接质量。粘接技术因此成为许多工厂的研究课题。 众所周知,增大粘接面的表面积及静电吸附力、提高粘接材料之间的化学作用力是获得高粘接强度的关键。本文通过对金属粘合表面不同处理工艺的试验,得出了操作方便、经济性好、粘接性能优异的骨架表面处理方法。 一、实验 1.主要材料 CHEMLOK 252上海洛德公司产品;CHEMLOK 205上海洛德公司产品;10#钢;20目石英砂;天然胶SCR5海南天然胶联合产业集团;丁腈胶N41兰州化学工业公司。 2.设备 普压干喷砂机(空气压力>0.6MPa);磷化处理线;400×400电热平板硫化机;0-200℃老化箱;0-2500N电子拉机。 3.粘接橡胶基本配方 天然胶SCR5 100;硬脂酸1;氧化锌(间接法)5;防老剂3;防护蜡4;软化剂10;炭黑70;硫黄2;促进剂1.5。 丁腈胶N41 10;硬脂酸1;氧化锌(间接法)5;防老剂3;聚酯
增塑剂10;炭黑60;DCP 1.5;硫黄0.5;促进剂1.5。 粘合剂:①单涂氧化锌(间接法);②底涂CHEM-LOK 205,面涂CHEMLOK 252。 4.粘接橡胶的常规机械性能 天然胶邵尔A型硬度65度,拉伸强度22MPa,拉断伸长率450%。 丁腈胶邵尔A型硬度70度,拉伸强度24MPa,拉断伸长率340%。 5.试样制备 ①在K360×160开放式炼胶机上将配方物料混合均匀;②试块表面处理;③在400×400电热平板硫化机上压制试样;④试样制备工艺。 NR硫化工艺条件为155℃×6min。 NBR硫化工艺条件为160℃×6min。 6.测试 按GB/T 13936标准对已硫化的试样进行测试。 二、实验数据 骨架不同表面处理方法下的粘结强度见表1,骨架不同后处理工艺下的粘结强度见表2,双涂层粘合体系下不同骨架表面处理方法的粘结强度见表3,粘合剂涂层厚度对粘结强度的影响见表4。 表1 骨架不同表面处理方法下的粘结强度
最新橡胶工艺原理14
最新橡胶工艺原理(十四) 王作龄 编译 中图分类号:TQ330.1 文献标识码:E 文章编号:167128232(2004)0520047208 第7章 填充剂 7.1 引言 填充剂是混入橡胶中以赋与橡胶补强、增容和特殊功能为目的使用的配合剂。作为填充剂代表的炭黑不仅可以提高橡胶的定伸应力和拉伸强度等力学性能,而且还可赋与橡胶导电等性能,是橡胶材料不可缺少的配合剂 。 一般,填充剂按不同材质、有无补强性和功能性进行分类。按材质分类,有白炭黑、陶土、碳酸钙等无机填充剂和树脂、木粉、软木粉等有机填充剂。按有无补强性分类有炭黑、白炭黑等补强性填充剂和陶土、滑石粉、碳酸钙等非补强性填充剂。 通常将用于提高橡胶物理机械强度的配合剂称为补强剂。补强剂除了上述的补强填充剂外,还有高苯乙烯树脂等补强性树脂和补强性短纤维。 本章节以补强性高的炭黑、白炭黑和短纤维的基本性能、基本性能与橡胶复合体物理性能之间的关系及这些补强剂的补强机理为主进行叙述。 7.2 补强性填充剂 补强性填充剂和非补强性填充剂的区别可用填充剂粒子的大小(粒子表面积)加以说明。此外,粒子的形态和表面特性对橡胶的补强效果也有很大影响。 SBR中配入不同填充剂时的各比表面积与拉伸强的关系如图7-1所示。若仅在白色填充剂范围内考虑,那么拉伸强度与比表面之间有相关性。相同比表面积的炭黑的拉伸强度比白色填充剂的大,这是因为炭黑和橡胶分子的相互作用强。为提高白炭黑等填充剂的补强性,大多还同时使用偶联剂。 图7-1 不同填充剂的比表面积与拉伸 强度的关系(SBR1500) 1—碳酸钙(55vo l%);2—硅酸盐(25vo l%); 3—湿法白炭黑(25vo l%);4—炭黑(27vo l%); 5—陶土(30vo l%) 7.2.1 炭黑 炭黑是由约95%以上无定形的炭组成的毫微米级的微粒,是在燃烧木材和煤时产生的所谓“煤烟子”(含有以多量灰分和焦油为主要成分的溶剂抽出分,炭含量在50%以下)的不同物质。 自1910年发现炭黑对橡胶具有显著的补强效果以来,炭黑成为支持橡胶工业发展的重要材料。炭黑的用途除了用作以汽车轮胎为主的橡胶制品的补强剂外,还可用作印刷油墨、涂料、塑料等的黑色颜料,以及赋与电池活性物质以导电性的填充剂等。但是,从数量上看,炭黑在像胶工业中的需求量占绝对多数,1996年日本橡胶工业的炭黑需求量占日本总需求量约95%,其中约75%用于汽车轮胎。 a.炭黑的种类 炭黑按制造方法的分类如表7-1所示。表7-2为A STM D1765-98的炭黑分类表。现在,橡胶和染料工业使用的炭黑几乎都是用油炉法生产的。
橡胶与金属粘接时金属的表面处理
橡胶与金属粘接时金属表面处理方法 一、橡胶中常用的金属材料 按材质分:铁、钢、不锈钢、铜、铝及铝合金等; 按形态分:线绳、帘布、金属件、金属块等; 如轮胎中胎圈、胎体、带束层所使用的钢丝或钢丝帘线。内胎上的黄铜气门嘴;胶带中的钢丝绳、胶管中的钢丝编织层;胶辊中的金属芯,油封的金属骨架,橡胶的金属减震器,金属的防腐橡胶衬里等。 二、金属的表面性质 1、金属的表面层结构 金属的表面结构,由里向外依次为:金属基体、1000nm厚加工硬化层、10nm厚氧化物质层、0.3nm厚气体吸附层、3nm厚污染物层。 2、金属的表面性质: 由于金属内部的金属原子之间易形成金属键,原子之间的相互作用力强,金属表面层原子受内部原子的相互吸引力较大,力场处于不平衡状态,因此金属表面具有较大的界面张力,表面能很高,因此很容易吸附周围环境中的气体分子、液滴和灰尘,具有很强的吸附性,因此金属表面会有一层气体吸附层和污染物层。在金属与橡胶粘合时,如果气体吸附层和污染物层不除去的话,会严重削弱粘合效果。 由于高能表面对低能表面具有较强的吸附作用,所以低能表面在高能表面上能润湿,能赶走高能表面的气体吸附层,而与金属表面充分接触。由于橡胶材料属于低能材料,因此橡胶在金属表面是湿润的,这给橡胶与金属的粘合提供了热力学条件。由于金属表面层原子受内部分子吸引作用较大,表面层原子排列紧密,很难形变和运动,所以橡胶与金属表面在接触时不能发生互溶、扩散和渗透,再加上金属表面一般都比较光滑,这又给橡胶与金属粘合带来不利的影响。 由于金属表面有一层氧化层,从而使金属表面带有一定的极性,能够增大橡胶与金属表面的吸附作用力,有利于粘合。另外,金属表面较容易失去电子,而橡胶材料易获得电子,所以当橡胶与金属表面靠近时,会发生电子转移,形成双电层,从而产生界面静电引力,这也对粘合有好处。 但是,金属表面的氧化层与橡胶之间不易发生化学作用,形成的化学键键合作用很小(黄铜除外),而且氧化层松脆,与本体结合不很牢固,因此橡胶与金属之间突现牢固的粘合比较难。此外,由于金属材料与橡胶材料的模量差异太大,在粘合界面处易发生应力分布不均匀,易受剪切而破坏。
橡胶工艺原理_复习思考题_ 答案
《橡胶工艺原理》复习思考题 0.1 名词解释 碳链橡胶、硬质橡胶、杂链橡胶、混炼胶、硫化胶、冷冻结晶、拉伸结晶、极性橡胶 杂链橡胶:碳-杂链橡胶: 主链由碳原子和其它原子组成 全杂链橡胶:主链中完全排除了碳原子的存在,又称为“无机橡胶”,硅橡胶的主链由硅、氧原子交替构成。混炼胶:所谓混炼胶是指将配合剂混合于块状、粒状和粉末状生胶中的未交联状态,且具有流动性的胶料 硫化胶 : 配合胶料在一定条件下(如加硫化剂、一定温度和压力、辐射线照射等)经硫化所得网状结构橡胶谓硫化胶,硫化胶是具有弹性而不再具有可塑性的橡胶,这种橡胶具有一系列宝贵使用性能。 硬质橡胶:玻璃化温度在室温以上、简直不能拉伸的橡胶称为硬质橡胶 0.2 一般来说,塑料、橡胶、纤维的分子结构各有什么特点? 0.3 影响橡胶材料性能的主要因素有哪些? 橡胶性能主要取决于它的结构,此外还受到添加剂的种类和用量、外界条件的影响。 (1) 化学组成:单体,具有何种官能团 (2) 分子量及分子量分布 (3) 大分子聚集状况:空间结构和结晶 (4) 添加剂的种类和用量 (5) 外部条件:力学条件、温度条件、介质 0.4简述橡胶分子的组成和分子链结构对橡胶的物理机械性能和加工性能的影响。 答: 各种生胶的MWD曲线的特征不同,如NR一般宽峰所对应的分子量值为30~40万,有较多的低分子部分。低分子部分可以起内润滑的作用,提供较好的流动性、可塑性及加工性,具体表现为混炼速率快、收缩率小、挤出膨胀率小。分子量高部分则有利于机械强度、耐磨、弹性等性能。 0.5 简述橡胶的分类方法。 答:按照来源用途分为天然胶和合成胶,合成胶又分为通用橡胶和特种橡胶; 按照化学结构分为碳链橡胶、杂链橡胶和元素有机橡胶; 按照交联方式分为传统热硫化橡胶和热塑性弹性体。 0.6 简述橡胶的分子量和分子量分布对其物理机械性能和加工性能的影响。 答: 分子量与橡胶的性能(如强度、加工性能、流变性等)密切相关。随着分子量上升,橡胶粘度逐步增大,流动性变小,在溶剂中的溶解度降低,力学性能逐步提高。 橡胶的大部分物理机械性能随着分子量而上升,但是分子量上升达到一定值(一般是600000)后,这种关系不复存在;分子量超过一定值后,由于分子链过长,纠缠明显,对加工性能不利,具体反映为门尼粘度增加,混炼加工困难,功率消耗增大等。 0.7 简述橡胶配方中各种配合体系的作用。
橡胶配方与各性能的关系
橡胶性能与配方的关系 不同的橡胶产品对胶料的物性都有不同的要求,同时对生产这些产品时胶料的工艺性能(加工性能)也需要不同的要求。所谓的工艺性也就是生产这些橡胶产品的过程不能达到理想的状态,做出来的橡胶产品也就很难做到性能理想化、经济效益最大化。一句话,无论你要求橡胶产品有什么样的物性要求,也不管你的要求是高还是低,如果工艺性能无法满足要求(实现要求的过程无法满足),那么你就很难顺利的去生产。 不多赘述,该贴将和大家一起谈论各橡胶工艺性能受配方的影响及关系。 一、混炼性能 1.各种成分对混炼效果的影响 主要分析配方中各种填料、化学药品、操作油等配合成分混入橡胶中的难易性、分散性。它主要由这些配合成分与橡胶之间的互溶性的高低、浸润性的大小来决定。 胶料混炼工艺设计的好坏评价方法之一就是各种成分是否可以在橡胶中能够迅速的分散;混炼效果的好坏,则可以通过各种成分在橡胶中能否均匀分散其中来衡量。这两个指标都主要取决于配合成分与橡胶之间的互溶性、浸润性。 “互溶性”这个词大家可能会认为橡胶那么大的分子怎么可能溶解在各种配合成分里很多配方里,应该是配合成分溶解在橡胶里才对。其实,所谓的溶质、溶剂也是相对的,量少的惯称为溶质,量多的则为溶剂,习惯性的认为溶质溶解在溶剂中,如果“溶质”的量比“溶剂”的量大很多的话,那就是“溶剂”溶解在“溶质”中。所以,也就可以理解为互溶性了。为了能让胶料达到多种综合性能都很优异的效果,很多配方用到的橡胶都不止一种,可能2、3、4、5种橡胶并用,这就涉及到这些橡胶之间的互溶性(也许橡胶之间的互溶性大家更好理解一些)。混炼后的胶料如果电镜图片里显示各相之间没有明显的分离、橡胶之间、橡胶与各配合成分之间分散的非常均匀那就表明互溶性好,否则互溶性就差。互溶性差的配方体系所对应的胶料的各种物性也就不能得到好的体现。 其实,橡胶配合体系是不能像盐溶于水那样做到分子级的互溶性,一是因为橡胶是由不同分子量的高分子复杂体系组成,二是各种配合成分也不是简单的小分子化合物,三它们是固相之间的溶解性。橡胶对配合剂的浸润性也许更能清楚的解释混炼工艺及效果的好坏。 橡胶对配合成分的浸润性高低主要决定于配合成分自身的特性,当然与橡胶的性质也有关系。有机的、非极性的大多数化学样品(塑解剂、分散剂、操作油等软化剂、防老剂、
橡胶制品生产工艺
橡胶制品生产工艺公司内部编号:(GOOD-TMMT-MMUT-UUPTY-UUYY-DTTI-
橡胶制品生产工艺简要介绍 一、基本工艺流程 橡胶制品种类繁多,但生产工艺过程,却基本相同。以一般固体橡胶(生胶)为原料的橡胶制品的基本工艺过程包括:塑炼、混炼、压延、压出、成型、硫化6个基本工序。当然,原材料准备、成品整理、检验包装等基本工序也少不了。 橡胶的加工工艺过程主要是解决塑性和弹性性能这个矛盾的过程,通过各种工艺手段,使得弹性的橡胶变成具有塑性的塑炼胶,再加入各种配合剂制成半成品,然后通过硫化使具有塑性的半成品又变成弹性高、物理机械性能好的橡胶制品。 二、原材料准备: 1.橡胶制品的主要原料是以生胶为基本材料,而生胶就是生长在热带,亚热带的橡胶树上通过人工割开树皮收集而来。 2.各种配合剂:是为了改善橡胶制品的某些性能而加入的辅助材料。 3.纤维材料有(棉、麻、毛及各种人造纤维、合成纤维)和金属材料(钢丝、铜丝)是作为橡胶制品的骨架材料,以增强机械强度、限制制品变型。 在原材料准备过程中,配料必须按照配方称量准确。为了使生胶和配合剂能相互均匀混合,需要对材料进行加工: 生胶要在60--70℃烘房内烘软后,再切胶、破胶成小块; 配合剂有:块状的,如石蜡、硬脂酸、松香等要粉碎; 粉状的若含有机械杂质或粗粒时需要筛选除去;
液态的,如(松焦油、古马隆)需要加热、熔化、蒸发水分、过滤杂质; 配合剂要进行干燥,不然容易结块、混炼时若不能分散均匀,硫化时产生气泡,会影响产品质量; 三、塑炼 生胶富有弹性,缺乏加工时必需的可塑性性能,因此不便于加工。为了提高其可塑性,所以要对生胶进行塑炼;这样,在混炼时配合剂就容易均匀分散在生胶中;同时,在压延、成型过程中也有助于提高胶料的渗透性(渗入纤维织品内)和成型流动性。 将生胶的长链分子降解,形成可塑性的过程叫做塑炼。 生胶塑炼的方法有机械塑炼和热塑炼两种。机械塑炼是在不太高的温度下,通过塑炼机的机械挤压和摩擦力的作用,使长链橡胶分子降解变短,由高弹性状态转变为可塑状态。热塑炼是向生胶中通入灼热的压缩空气,在热和氧的作用下,使长链分子降解变短,从而获得可塑性。 四、混炼 为了适应各种不同的使用条件、获得各种不同的性能,也为了提高橡胶制品的性能和降低成本,必须在生胶中加入不同的配合剂。 混炼就是将塑炼后的生胶与配合剂混合、放在炼胶机中,通过机械拌合作用,使配合剂完全、均匀地分散在生胶中的一种过程。 混炼是橡胶制品生产过程中的一道重要工序,如果混合不均匀,就不能充分发挥橡胶和配合剂的作用,影响产品的使用性能。混炼后得到的胶料,人们称为混炼胶,它是制造各种橡胶制品的半成品材料,俗称胶料,通常均作为商品出
国内常用粘合剂
我国合成胶粘剂生产企业比较分散,有2000多家,并有数百家专门生产通用品种如脲醛树脂胶粘剂、聚醋酸乙烯胶粘剂、聚丙烯酸树脂胶粘剂等。 脲醛树脂、酚醛、三聚氰胺—甲醛胶粘剂:主要用于木材加工行业,使用后的甲醛释放量高于国际标准。 聚丙烯酸树脂:主要用于生产压敏胶粘剂,也用于纺织和建筑领域。近年来,国内企业从国外引进数条压敏胶粘制品生产流水线,推动了国内聚丙烯酸树脂生产技术的发展。 聚氨酯胶粘剂:能粘接多种材料,粘接后在低温或超低温时仍能保持材料理化性质,主要应用于制鞋、包装、汽车、磁性记录材料等领域。近几年,国内聚氨酯胶粘剂年产量以平均30%的速度增长。国内现约有170家工厂在生产100多种不同规格的此类胶粘剂。 热熔胶粘剂:根据原料不同,可分为EVA热熔胶、聚酰胺热熔胶、聚酯热熔胶、聚烯烃热熔胶等。目前国内主要生产和使用的是EVA热熔胶。聚烯烃系列胶粘剂主要原料是乙烯系列、SBS、SIS共聚体。 环氧树脂胶粘剂:可对金属与大多数非金属材料之间进行粘接,广泛用于建筑、汽车、电子、电器及日常家庭用品方面。国内生产环氧树脂胶粘剂工厂有100多家,分布较分散,年产量约为1万吨。 有机硅胶粘剂:是一种密封胶粘剂,具有耐寒、耐热、耐老化、防水、防潮、伸缩疲劳强度高、永久变形小、无毒等特点。近年来,此类胶粘剂在国内发展迅速,但目前我国有机硅胶粘剂的原料部分依靠进口。 合成胶粘剂:主要用于木材加工、建筑、装饰、汽车、制鞋、包装、纺织、电子、印刷装订等领域。目前,我国每年进口合成胶粘剂近20万吨,品种包括热熔胶粘剂、有机硅密封胶粘剂、聚丙烯酸胶粘剂、聚氨酯胶粘剂、汽车用聚氯乙烯可塑胶粘剂等。同时,每年出口合成胶粘剂约2万吨,主要是聚醋酸乙烯、聚乙烯酸缩甲醛及压敏胶粘剂。 木材加工用胶粘剂:用于中密度纤维板、石膏板、胶合板和刨花板等。 建筑用胶粘剂:主要用于建筑工程装饰、密封或结构之间的粘接。随着建筑行业发展,高层建筑、室内装饰的发展需要,建筑用胶粘剂用量急剧增加。2000年我国建筑用胶粘剂消费量约60万吨以上。但专家认为,我国此类胶粘剂的产品结构需调整。在国内,建筑装饰用胶粘剂如聚醋酸乙烯、聚丙烯酸、VAE乳液等基本上可满足需要,但建筑用密封胶粘剂、结构胶粘剂还需部分从国外进口。 密封胶粘剂:主要用于门、窗及装配式房屋预制件的连接处。过去用桐油与石灰拌制后作为密封剂,现在规定两层以上楼房必须用合成胶粘剂。高档密封胶粘剂为有机硅及聚氨酯胶粘剂,中档的为氯丁橡胶类胶粘剂、聚丙烯酸等。在我国,建筑用胶粘剂市场上,有机硅胶粘剂、聚氨酯密封胶粘剂应是今后发展的方向,目前其占据建筑密封胶粘剂的销售量为30%左右。 建筑结构用胶粘剂:主要用于结构单元之间的联接。如钢筋混凝土结构外部修补,金属补强固定以及建筑现场施工,一般考虑采用环氧树脂系列胶粘剂。 汽车用胶粘剂:分为4种,即车体用、车内装饰用、挡风玻璃用以及车体底盘用胶粘剂。目前我国汽车用胶粘剂年消耗量约为4万吨,其中使用量最大的是聚氯乙烯可塑胶粘剂、氯丁橡胶胶粘剂及沥青系列胶粘剂。 制鞋用胶粘剂:年消费量约为12.5万吨,其中氯丁橡胶类胶粘剂需要11 万吨,聚氨酯胶粘剂约1.5万吨。由于氯丁橡胶类胶粘剂需用苯类作溶剂,而苯
橡胶与金属的粘合技术
橡胶与金属的粘合技术 橡胶与金属的粘合技术 粘合剂分类:1.溶剂型:如CH205、CH252、CH220(用酮、苯为溶剂) 2.水性:如E1542 (运输存储较困难、有良好的模具耐脏性,环保型) 3.环保型:CH6100、CH6109、2000TEF(不含重金属、不产生臭氧化合物、不含氯化溶剂) 粘合剂涂层的组成和作用: ?底胶:提供腐蚀环境的耐抗性、提供与金属高强度的附着力和面胶的化学粘结性 ?面胶:用于弹性体与底胶的粘结、提供弹性体与金属的充分附着(经验法则单涂的效果通常不如双涂的效果)、提供对外部环境长期耐久性的屏障、提供必要的抗磨性。 ?单涂:用于特种胶如MVQ、FKM、HNBR等粘合,能提供较薄且坚硬的漆膜、且无色,用于有色弹性体,提供较高的耐热和抗溶剂性、抗腐蚀性。 粘结性能的影响因素: ?弹性体选择 橡胶的硬度? 碳黑用量和类型? 抗氧化物/Antiozonants? ?硫化剂 混合硫化 增塑剂用量和类型 3.粘合剂的组成: 溶剂:78-72%;树脂、聚合物、反应性固体:22-28% 没有溶剂或水的蒸发,固体的含量不会增加; 注意: ?客户不允许任意混合的不同牌号的粘合剂; 粘合剂的溶剂量按以下排列:刷涂= 滚涂<浸涂<喷涂;? ?固体含量是影响黏度的因数之一; 溶剂与固体含量是否充分混合,第一次使用前是否充分搅拌;? ?稀释液必须是和粘合剂中的固体有兼容性的溶剂; 总是将溶剂加入粘合剂而不能相反,加入溶剂时必须搅拌;? ?在通风的地方转移溶剂; 必须能秤重式测量体积;? 酮类和酒精应是高等级水含量少的溶剂;? ?涂了粘合剂的金属工件在热模具中时间应相对多于橡胶; ?预烘的时间越久,模具消耗和积聚的化学活性就越多,这就相应减少用于粘结橡胶化合物的活性; ?如果粘合剂中的交联剂在预烘中遗失和释放,那么橡胶和金属粘结会失败; ?如果粘合剂化学成分活性太高或容易焦化,与橡胶的硫化不匹配,也会造成粘结失败。 粘合剂的使用方法: ?黏度由黏合剂中的固体成分和各成分间的相互作用决定。
橡胶力学性能测试标准
序号标准号:发布年份标准名称(仅供参考) 1 GB 1683-1981 硫化橡胶恒定形变压缩永久变形的测定方法 2 GB 1686-1985 硫化橡胶伸张时的有效弹性和滞后损失试验方法 3 GB 1689-1982 硫化橡胶耐磨性能的测定(用阿克隆磨耗机) 4 GB 532-1989 硫化橡胶与织物粘合强度的测定 5 GB 5602-1985 硫化橡胶多次压缩试验方法 6 GB 6028-1985 硫化橡胶中聚合物的鉴定裂解气相色谱法 7 GB 7535-1987 硫化橡胶分类分类系统的说明 8 GB/T 11206-1989 硫化橡胶老化表面龟裂试验方法 9 GB/T 11208-1989 硫化橡胶滑动磨耗的测定 10 GB/T 11210-1989 硫化橡胶抗静电和导电制品电阻的测定 11 GB/T 11211-1989 硫化橡胶与金属粘合强度测定方法拉伸法 12 GB/T 1232.1-2000 未硫化橡胶用圆盘剪切粘度计进行测定第1部分:门尼粘度的测定 13 GB/T 12585-2001 硫化橡胶或热塑性橡胶橡胶片材和橡胶涂覆织物挥发性液体透过速率的测定(质量法) 14 GB/T 12829-2006 硫化橡胶或热塑性橡胶小试样(德尔夫特试样)撕裂强度的测定 15 GB/T 12830-1991 硫化橡胶与金属粘合剪切强度测定方法四板法 16 GB/T 12831-1991 硫化橡胶人工气候(氙灯)老化试验方法 17 GB/T 12834-2001 硫化橡胶性能优选等级 18 GB/T 13248-1991 硫化橡胶中锰含量的测定高碘酸钠光度法 19 GB/T 13249-1991 硫化橡胶中橡胶含量的测定管式炉热解法 20 GB/T 13250-1991 硫化橡胶中总硫量的测定过氧化钠熔融法 21 GB/T 13642-1992 硫化橡胶耐臭氧老化试验动态拉伸试验法 22 GB/T 13643-1992 硫化橡胶或热塑性橡胶压缩应力松弛的测定环状试样 23 GB/T 13644-1992 硫化橡胶中镁含量的测定CYDTA滴定法 24 GB/T 13645-1992 硫化橡胶中钙含量的测定EGTA滴定法 25 GB/T 13934-2006 硫化橡胶或热塑性橡胶屈挠龟裂和裂口增长的测定(德墨西亚型) 26 GB/T 13935-1992 硫化橡胶裂口增长的测定 27 GB/T 13936-1992 硫化橡胶与金属粘接拉伸剪切强度测定方法 28 GB/T 13937-1992 分级用硫化橡胶动态性能的测定强迫正弦剪切应变法 29 GB/T 13938-1992 硫化橡胶自然贮存老化试验方法 30 GB/T 13939-1992 硫化橡胶热氧老化试验方法管式仪法 31 GB/T 14834-1993 硫化橡胶与金属粘附性及对金属腐蚀作用的测定 32 GB/T 14835-1993 硫化橡胶在玻璃下耐阳光曝露试验方法 33 GB/T 14836-1993 硫化橡胶灰分的定性分析 34 GB/T 15254-1994 硫化橡胶与金属粘接180°剥离试验 35 GB/T 15255-1994 硫化橡胶人工气候老化(碳弧灯)试验方法 36 GB/T 15256-1994 硫化橡胶低温脆性的测定(多试样法) 37 GB/T 15584-1995 硫化橡胶在屈挠试验中温升和耐疲劳性能的测定第一部分:基本原理 38 GB/T 15905-1995 硫化橡胶湿热老化试验方法 39 GB/T 16585-1996 硫化橡胶人工气候老化(荧光紫外灯)试验方法 40 GB/T 16586-1996 硫化橡胶与钢丝帘线粘合强度的测定 41 GB/T 16589-1996 硫化橡胶分类橡胶材料
间甲白橡胶粘合剂
橡胶粘合剂A 产品简介橡胶粘合剂A化学名称为六甲氧基甲基蜜胺,作为橡胶与骨架材料间-甲-白直接粘合体系之亚甲基给予体,能溶于水和一般的有机溶液。 技术指标外观无色透明液体或蜡状体结合甲醛含量%≥40 游离甲醛含量%≤5.0 应用说明1、橡胶粘合剂A在硫化温度下与亚甲基接受体反应,对橡胶和骨架材料起到粘合作用。例如与间苯二酚甲醛树脂GLR-20,粘合剂RE、粘合剂RS等配合发生反应,生成热固性树脂。如果反应在硫化之前发生,则该配合系统的粘合作用将失去。通常先在较高温度下将橡胶、填料和亚甲基接受体组成的胶料制备好;然后,在炼胶后期终炼时,将粘合剂A及其它配合剂加入。 2、建议的比例为1.5-3份橡胶粘合剂A并配合使用2-5份GLR-20树脂或其它亚甲基接受体。 包装贮运1、橡胶粘合剂A外包装为塑料桶,内衬塑料内膜,净重为每包装20Kg。 2、在运输、储存之前应检查产品包装是否无损。在储存过程中应分类堆放在干燥、清洁、阴凉的库房中,严防产品受潮、受热变质。 3、有效存储期为一年。 癸酸钴RCo-1、环烷酸钴RCo-2 癸酸钴RCo-1、环烷酸钴RCo-2是我公司采用全新工艺研制成功的具有自主知识产权的优质橡胶与钢丝(镀铜、镀锌)粘合促进剂。该产品技术起点高,工艺先进,选用原材料品质优良,并可以根据用户的不同要求,灵活调整配方,不断推出新的品牌。经国内轮胎企业在子午线钢丝轮胎中对比应用,产品性能达到国外同类产品水平,完全可以替代进口,并在载重子午线轮胎的生产中获得广泛应用。 该产品2003年通过河南省科学技术厅成果鉴定,并被认定为“河南省高新技术产品”。
橡胶粘合剂 RA 产品简介 橡胶粘合剂RA 的主要成份是六甲氧基甲基蜜胺(粘合剂A )和无机载体组成, 是固体型亚甲基给予体粘合剂。它与亚甲基接受体配合使用,起到使橡胶与钢 丝等骨架材料充分粘合的作用。 技术指标 外 观 白色粉末 灰份% 30-38 水份% ≤4.5 筛余物% ≤0.3 游离甲醛含量% ≤0.1 应用说明 1、橡胶粘合剂RA 通过与亚甲基接受体反应而产生粘合作用。例如与橡胶粘合 剂RE 、间苯二酚甲醛树脂GLR-20等配合发生反应,生成热固性树脂。该反应 在硫化温度下将很快发生,如果反应在硫化之前发生,则该配合系统的粘合作 用将大大降低、甚至失去。通常先在较高温度下将橡胶、填料和亚甲基接受体 组成的混合胶料制备好,然后在炼胶后期终炼时,将橡胶粘合剂RA 同促进剂、 硫磺一起加入。 2、建议比例为每100份胶料用2-5份橡胶粘合剂RA 配合使用2-5份GLR-20树 脂。 包装贮运 1、橡胶粘合剂RA 外包装为编织袋,内衬聚乙烯塑料袋,净重为每包装25Kg 。 2、在运输、贮存之前应检查产品包装是否完好无损。在贮运过程中应分类堆放 在干燥、清洁、阴凉的库房中,严防产品受潮、受热变质。 3、有效存储期为一年。 均匀剂A78
橡胶的粘着性和自粘性
橡胶的粘着性和自粘性 生胶料的胶粘性可表现为自粘性与互粘性(或粘着性)两个方面。自粘性是指粘性物质的自相粘合,如橡胶与橡胶的粘合。粘着性则是 生胶料的胶粘性可表现为“自粘性”与“互粘性”(或粘着性)两个方面。自粘性是指粘性物质的自相粘合,如橡胶与橡胶的粘合。粘着性则是指不同物质之间的粘合,如橡胶与磨料间的粘合。 橡胶的自粘性与粘着性的差异,主要由橡胶的结构来决定,一般来说,天然橡胶的自粘力大于粘结力。丁苯橡胶的粘结力大于自粘力,且天然胶的粘结力小于丁苯胶的粘结力,在用天然橡胶制造橡胶磨具坯体时,由于天然胶的自粘力大,不易被破碎为颗粒状松散料,只能用炼胶辊筒进行压片成型,成型厚度极其有限。高厚度的磨具坯体则需要把多个薄片状坯片装入模具中,用压机合,并需连同模具去加热硫化。当使用丁苯胶时,由于丁苯胶自粘力小,很易把含磨料的丁苯胶料破碎为颗粒状松散料,从而可以装入模具中用压机进行模压成型,并随之可从模具卸出,托在铁板上去加热硫化。 橡胶的自粘性及粘着性除决定于橡胶的结构外,也受外界条件的不同而变化。例如:提高温度,天然胶的粘着力增大而自粘力下降,但丁苯胶的粘着力和自粘力都下降;加入补强剂(如炭黑)后,天然胶自粘力的增长幅度远大于粘着力的增长,而丁苯胶的粘着力仍大于自粘力。加入增粘剂后,丁苯胶的粘着力增长更多。因此在实际工作中,可以通过温度的变化及加入不同的添加剂来调整生胶料的自粘性与粘着性,以获得较好的工艺性能。 橡胶的自粘性与粘着性除在外观表现上有所不同外,它们的产生机理也不尽相同。自粘力实质上是橡胶自身分子间内聚力的反映,是自扩散的结果,因而影响因素较少;而粘着力的大小除与橡胶本身的内聚力及扩散作用有关外,还与被粘物的化学性质、表面状况及施工因素等多种因素有关。 用橡胶结合剂把磨粒粘接起来构成一定形状的固结磨具。而这种橡胶磨具在高速
青岛科技大学橡胶工艺原理讲稿
青岛科技大学橡胶工艺原理讲稿(5) 青岛科技大学, 橡胶, 讲稿, 工艺, 原理 §3-6炭黑对橡胶的补强机理 炭黑补强作用使橡胶的力学性能提高,同时也使橡胶在粘弹变形中由粘性作用而产生的损耗因素提高。例如tanδ、生热、损耗模量、应力软化效应提高。因应力软化效应能够比较形象地说明大分子滑动补强机理,因此将两者结合一起讨论。 一.应力软化效应 (一)应力软化效应的含义 硫化胶试片在一定的试验条件下拉伸至给定的伸长比λ1时,去掉应力,恢复。第二次拉伸至同样的λ1时所需应力比第一次低,如图3-18所示,第二次拉伸的应力-应变曲线在第一次的下面。若将第二次拉伸比增大超过第一次拉伸比λ1时,则第二次拉伸曲线在λ1 处急骤上撇与第一次曲线衔接。若将第二次拉伸应力去掉,恢复。第三次拉伸,则第三次的应力应变曲线又会在第二次曲线下面。随次数增加,下降减少,大约4~5次后达到平衡。上述现象叫应力软化效应,也称为Mullins效应。 应力软化效应用拉伸至给定应变所造成的应变能下降百分率ΔW表示。 (3-10) 式中 W1 —第一次拉伸至给定应变时所需要的应变能; W2 —第一次拉伸恢复后,第二次(或更多次数)再拉伸至同样应变时所需的应变能。 (二)应力软化效应的影响因素 应力软化效应代表一种粘性的损耗因素,所以凡是影响粘弹行为的因素对它均有影响。填料及其性质对应力软化效应有决定性作用。1.填充的影响 2.填料品种对应力软化效应的影响 3.炭黑品种对应力软化效应的影响 总的趋势是补强性高的炭黑应力软化效应比较高,反之亦然。 (三)应力软化的恢复 应力软化有恢复性,但在室温下停放几天,损失的应力恢复很少,而在100℃×24h真空中能恢复大部分损失的应力。因为炭黑的吸附是动态的,在恢复条件下,橡胶大分子会在炭黑表面重新分布,断的分子链可被新链代替。剩下的不能恢复的部分称为永久性应力软化作用。 二.炭黑的补强机理 近半个世纪以来,人们对炭黑补强机理曾进行了广泛的探讨。各个作者提出的机理虽然能说明一定的问题,但有局限性。随着时间进展,橡胶补强机理也在不断地深化和完善。橡胶大分子滑动学说的炭黑补强机理是一个比较完善的理论。现将各种论点简述如下。 (一)容积效应 (二)弱键和强键学说 (三)Bueche的炭黑粒子与橡胶链的有限伸长学说 (四)壳层模型理论 核磁共振研究已证实,在炭黑表面有一层由两种运动状态橡胶大分子构成的吸附层。在紧邻着炭黑表面的大约0.5nm(相当于大分子直径)的内层,呈玻璃态;离开炭黑表面大约0.5~5.0nm范围内的橡胶有点运动性,呈亚玻璃态,这层叫外层。这两层构成了炭黑表面上的双壳层。关于双壳层的厚度Δγc,报道不一,不过基本上是上述范围。这个双壳的界面层内中的结合能必定从里向外连续下降,即炭黑表
间甲白橡胶粘合剂
橡胶粘合剂A 产品简介 橡胶粘合剂A化学名称为六甲氧基甲基蜜胺,作为橡胶与骨架材料间-甲-白直 接粘合体系之亚甲基给予体,能溶于水和一般的有机溶液。 技术指标外观无色透明液体或蜡状体结合甲醛含量% ≥40 游离甲醛含量% ≤5.0 应用说明1、橡胶粘合剂A在硫化温度下与亚甲基接受体反应,对橡胶和骨架材料起到粘合作用。例如与间苯二酚甲醛树脂GLR-20,粘合剂RE、粘合剂RS等配合发生反应,生成热固性树脂。如果反应在硫化之前发生,则该配合系统的粘合作用将失去。通常先在较高温度下将橡胶、填料和亚甲基接受体组成的胶料制备好;然后,在炼胶后期终炼时,将粘合剂A及其它配合剂加入。 2、建议的比例为1.5-3份橡胶粘合剂A并配合使用2-5份GLR-20树脂或其它亚甲基接受体。 包装贮运1、橡胶粘合剂A外包装为塑料桶,内衬塑料内膜,净重为每包装20Kg。 2、在运输、储存之前应检查产品包装是否无损。在储存过程中应分类堆放在干燥、清洁、阴凉的库房中,严防产品受潮、受热变质。 3、有效存储期为一年。 癸酸钴RCo-1、环烷酸钴RCo-2 癸酸钴RCo-1、环烷酸钴RCo-2是我公司采用全新工艺研制成功的具有自主知识产权的优质橡胶与钢丝(镀铜、镀锌)粘合促进剂。该产品技术起点高,工艺先进,选用原材料品质优良,并可以根据用户的不同要求,灵活调整配方,不断推出新的品牌。经国内轮胎企业在子午线钢丝轮胎中对比应用,产品性能达到国外同类产品水平,完全可以替代进口,并在载重子午线轮胎的生产中获得广泛应用。 该产品2003年通过河南省科学技术厅成果鉴定,并被认定为“河南省高新技术产品”。
橡胶粘合剂 RA 产品简介 橡胶粘合剂RA 的主要成份是六甲氧基甲基蜜胺(粘合剂A )和无机载体组成, 是固体型亚甲基给予体粘合剂。它与亚甲基接受体配合使用,起到使橡胶与钢 丝等骨架材料充分粘合的作用。 技术指标 外 观 白色粉末 灰份% 30-38 水份% ≤4.5 筛余物% ≤0.3 游离甲醛含量% ≤0.1 应用说明 1、橡胶粘合剂RA 通过与亚甲基接受体反应而产生粘合作用。例如与橡胶粘合 剂RE 、间苯二酚甲醛树脂GLR-20等配合发生反应,生成热固性树脂。该反 应在硫化温度下将很快发生,如果反应在硫化之前发生,则该配合系统的粘合 作用将大大降低、甚至失去。通常先在较高温度下将橡胶、填料和亚甲基接受 体组成的混合胶料制备好,然后在炼胶后期终炼时,将橡胶粘合剂RA 同促进 剂、硫磺一起加入。 2、建议比例为每100份胶料用2-5份橡胶粘合剂RA 配合使用2-5份GLR-20 树脂。 包装贮运 1、橡胶粘合剂RA 外包装为编织袋,内衬聚乙烯塑料袋,净重为每包装25Kg 。 2、在运输、 贮存之前应检查产品包装是否完好无损。在贮运过程中应分类堆放 在干燥、清洁、阴凉的库房中,严防产品受潮、受热变质。 3、有效存储期为一年。 均匀剂A78
橡胶与金属的粘合是橡胶制品制造过程中的重要环节
橡胶与金属的粘合是橡胶制品制造过程中的重要环节,如果粘合不良或无法粘合,一些橡胶制品如轮胎、钢丝输送带、橡胶软管,橡胶计架油封、汽门油封,橡胶金属组合垫圈、组合胶套等橡胶金属复合制品就无法制作。就橡胶密封制品而言,上世纪80年代初,青岛密封件厂协同青岛化工厂研制成功了 RM-1粘合剂,替代日本TD870成功生产岀与国外同等水平的許架油封,使引进的国外技术得以消化吸收,开辟了卄架汕封制作的新工艺。上世纪 90年代,由于汽车工业的发展,不少厂家要求用氟橡胶制作骨架汕封、汽车汕封,但是粘合问题不好解决,严重的制约了该产品的开发,当时青岛双星集团密封件厂成功的研制了 FG-1氟橡胶与黑色金属的热硫化粘合剂,使氟橡胶与金属计架牢牢的粘合成一体,顺理成章的研发成功斯太尔发动机曲轴前后油封和气门油封替代了进口,满足了配套需要,该粘合剂一直使用至今。因此橡胶与金属粘合是极其重要的应用技术,应引起生产企业的高度重视。 1金属竹架的表面处理)计架表而无油污、无锈蚀,有一左粗糙度的新鲜表而才能有效的与金属粘合,因此竹架必须进行表面处理,处理大体有两种方法:一是机械法处理。如采用履带式的抛丸淸理机326或滚筒式的抛丸淸理机Q3110,将粒径0.5mm的钢砂喷射到计架表面,将表面的锈蚀等有害物料喷掉,使表面新鲜并增大表而积,加大计架与胶粘剂间的接触面:二是化学法。即酸洗处理,磷化钝化处理,其工艺过程是碱液去油,酸液去锈,磷化上磷化膜,然后进行钝化烘干,碱液是有多种材料如苛性钠、硅酸钠(表而湿润剂)、焦磷酸钠(阴离子表而活性剂)、烷基磺酸钠组成的水溶液,淸洗温度80-9CTC,时间视表而的汕污多少而有差异,一般是5min左右。去油污的计架经流动的自来水冲洗后,进行酸洗处理,而不同的金属去锈时对酸的品种是有选择性的。例如,铁件要用盐酸淸洗处理。铜件和不锈钢忖架采用硫酸、硝酸混合液协同去锈。铝件用硫酸、馅酸混合液进行处理。要求对周IM环境不产生或少产生腐蚀时,而金属件架锈蚀较轻的竹架,可采用以草酸为主,掺用少戢硫酸和加入缓钝剂的水溶液进行处理。磷化是黑色金属表而处理的重要方法。磷化液的品种很多, 如常温磷化液,采用的是铁系磷化液,骨架经酸洗后进行表调,放入常温磷化液中(温度30°C 左右)处理5-6min:中温磷化是采用锌系或锌钙系的磷化液,件架在65-75°C下处理6min左右:髙温磷化液是锚系磷化液,骨架在80-90°C下处理3-4min,目前采用中温磷化液较好,因常温磷化表面磷化膜磷化后停放时容易造成再生锈,髙温磷化的竹架表而磷化膜粗糙而且较厚,易造成脱落,中温磷化,磷化膜细致而牢固有利于粘合。磷化后的丹架要进行钝化处理,主要是通过钝化液的表而处理,封闭骨架表而的易氧化离子,防止件架再生锈。钝化液的品种很多,如以辂酸盐类、硝酸盐类,三乙酸胺为代表的有机胺类,其中珞酸盐类钝,化效果好,表而的珞离子有利于与橡胶的粘合,但珞酸盐类环保控制较严格,需进行废液的处理,对于难粘合如不锈钢件架除混合酸淸冼后进行表而钝化后还需进行偶化处理,这有利于提高粘合强度。如无锡威力达公司生产的全电脑控制双勾磷化处理线,温度、浸洗时间、烘干时间、停放滴水时间等全部自动控制,可有效的保证处理质量。其工艺过程是碱液去锈(5°C X3n】in),吊起滴水(常温X lmin)-*自来水冲洗(常温X lminL酸液去锈(常温X3minL吊起滴液(常温XlminL流动自来水冲洗(常温X0.5min)-磷化处理(65-70a C X5-6min)-*吊起滴液(常温X lmin)-*流动自来水冲洗(常温X lmin)-*吊起滴液(常温><11血)-*钝化(90°。X 0.5minL烘干备用。 2粘合胶、胶料配方的设计 要使橡胶与金属件架产生良好的粘合强度,必须要在粘合剂与金属界而上和粘合剂与橡胶界面上,具有良好的扩散、湿润、吸附、渗透能力,大的分子间的引力(即范徳华引力)和密集的化学键及良好的共硫化效应,要达到上述要求,除选择高活性的粘合剂、严格的金属骨架表而处理工艺和正确的配制浸涂、预固化粘合剂之外,橡胶配方是极其重要的因素,若胶料配方不当,苴粘着强度低而且适应性也差。丁腊橡胶勺铁骨架浸涂酚类粘合剂,以进行热硫化为例,通过试验发现丁腊橡胶随着丙烯猜含量的增加,粘合强度随之提髙(见表1)。不同丙烯腊含量丁腊橡胶的粘合强度生胶品种国产丁尉橡胶40日本丁睛橡胶203S国产丁腊橡胶26、27-30日本丁尉橡胶N-41日本丁睛橡胶240S国产丁腊橡胶18