标准作业流程图(SOP)——集合管
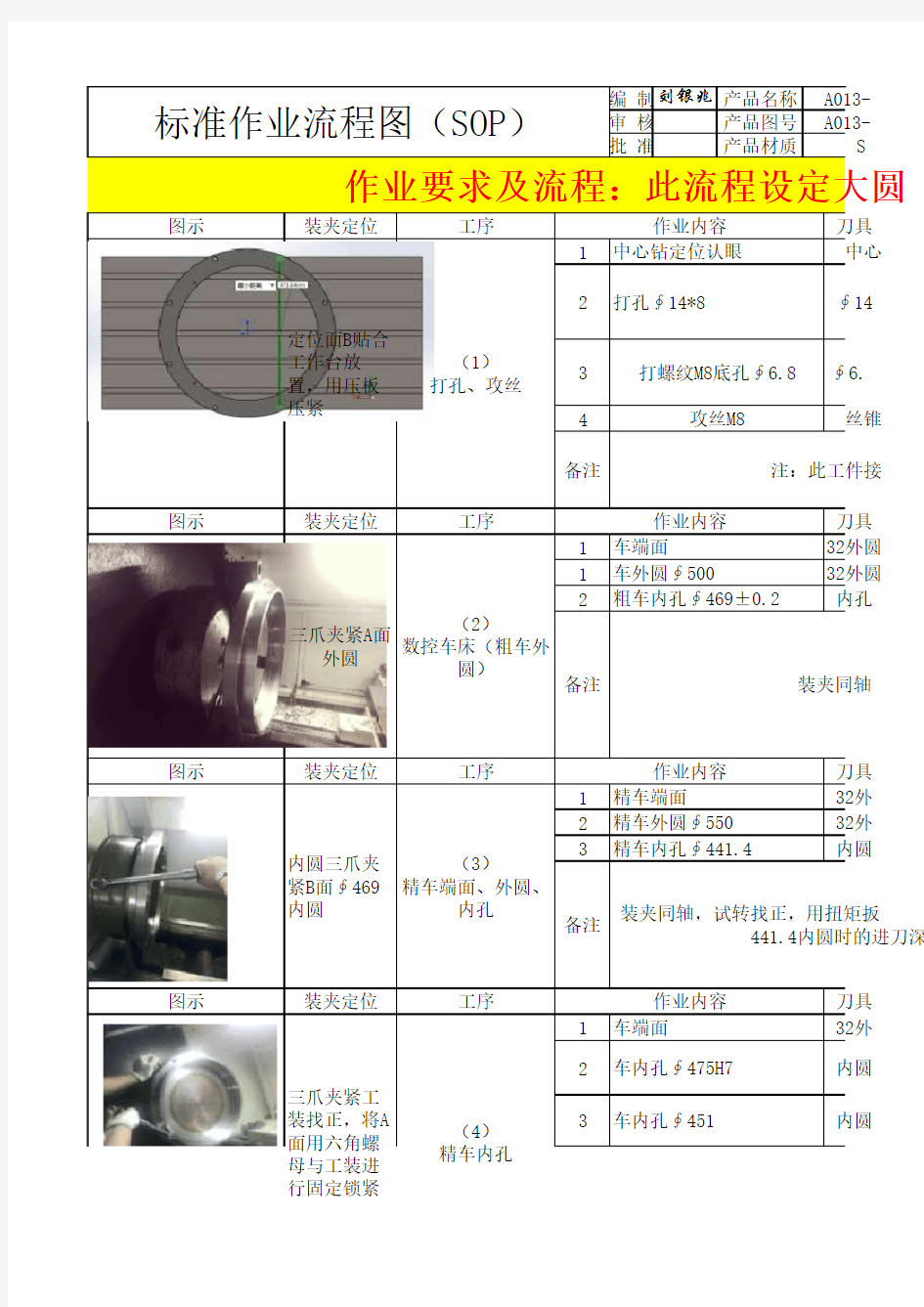

124112
1
2
32审 核产品图号A013-标准作业流程图(SOP)
编 制刘银兆产品名称A013-批 准产品材质S 作业要求及流程:此流程设定大圆图示装夹定位工序
作业内容刀具定位面B贴合
工作台放
置,用压板
压紧(1)打孔、攻丝中心钻定位认眼中心3打螺纹M8底孔∮6.8∮6.打孔∮14*8∮14攻丝M8丝锥备注注:此工件接
图示装夹定位工序作业内容
刀具车外圆∮500
32外圆三爪夹紧A面外圆(2)数控车床(粗车外圆)车端面
32外圆粗车内孔∮469±0.2内孔备注装夹同轴
图示装夹定位工序
作业内容刀具内圆三爪夹
紧B面∮469
内圆(3)精车端面、外圆、内孔精车端面32外精车内孔∮441.4内圆精车外圆∮55032外图示装夹定位工序
作业内容刀具备注装夹同轴,试转找正,用扭矩扳
441.4内圆时的进刀深度
三爪夹紧工装找正,将A
面用六角螺
母与工装进
行固定锁紧(4)精车内孔1
车端面32外车内孔∮475H7
内圆3
车内孔∮451内圆
备注装找正,将A 面用六角螺母与工装进行固定锁紧(4)精车内孔
装夹要求:装夹同轴,试转找正形。此工序加工完成后,三坐标测量平面
加工技巧为:
1.工装车一个∮441.4的小圆台定位装夹
2.在精车时更换新刀片,螺钉稍松再紧;
过程尺寸检验及
标准作业流程图(SOP)
编 制刘银兆产品名称A013-审 核图示工序测量位置
作业要点产品图号A013-批 准产品材质S 粗车内孔∮469 1.测量内圆直径内圆∮469,保证测量的为最大内圆尺寸即加工直径 2.多
点测量,确保测量准确
数显图示工序测量位置
作业要点(2)
数控车床
(粗车外
圆)外圆∮500
1.测量外圆直径外圆∮500,保证测量的为最大外圆尺寸即加工直径
2.多点测量,确保测量准确数显1.测量外圆直径外圆∮550,保证测量的为最大外圆尺寸即加工直径 2.多
点测量,确保测量准确
0-精车内孔∮441.4 1.测量内圆直径∮441.4,
保证测量的为最大内圆尺寸即加工直径
2.多点测量,确保测量准确
0-(3)
精车端面、
外圆、内孔精车车端面 1.测量图示厚度34
2.多点测量,确保测量准确0-1
精车外圆∮550图示工序测量位置作业要点2.多点测量,确保测量准确
(4)精车内孔
精车车端面
1.全长61
2.多点测量,确保测量准确
0-精车内圆∮475
三坐标测量
1.平面度、圆度∮451 ∮475
2.多点测量,确保测量准确
思
1.测量内圆直径∮475,保证测
量的为最大内圆尺寸即加工直径
2.深度45
3.多点测量,确保测量准确
内精车内孔∮451
1.测量内圆直径内圆∮451,保
证测量的为最大内圆尺寸即加工
直径
2.深度9.4
3.多点测量,确保测量准确
0-2
尺寸要求尺寸要求尺寸要求转找正,用扭矩扳手锁紧,锁紧力4N·M,用以保证不变
成后,三坐标测量平面度,圆度及相应尺寸
1.4的小圆台定位装夹;
刀片,螺钉稍松再紧;用以便保证平面度
检验及工装
A013-046-2000
文件编号GDZY-C4-P8-3077检测工具
2工装
A013-046-2000
修改版次第1版SCS14A 页 码第3页/共4页数显卡尺 0-600∮469±0.2
检测工具数显卡尺 0-600∮500±0.20-600数显550( 0,-2)
0-600数显∮441.4+0.2
3工装
0-150游标卡尺34±0.1
检测工具4工装
0-200深度尺61±0.3
思瑞三坐标
475
(+0.063,0)∮451±0.2平行度±0.02圆度±0.02
内径百分表
475
(+0.063,0)45(+0.1,0)
0-200深度尺
9.4±0.1
内圆451卡尺无法测量需下活后
测量