印制板DFM规范(1)(1)
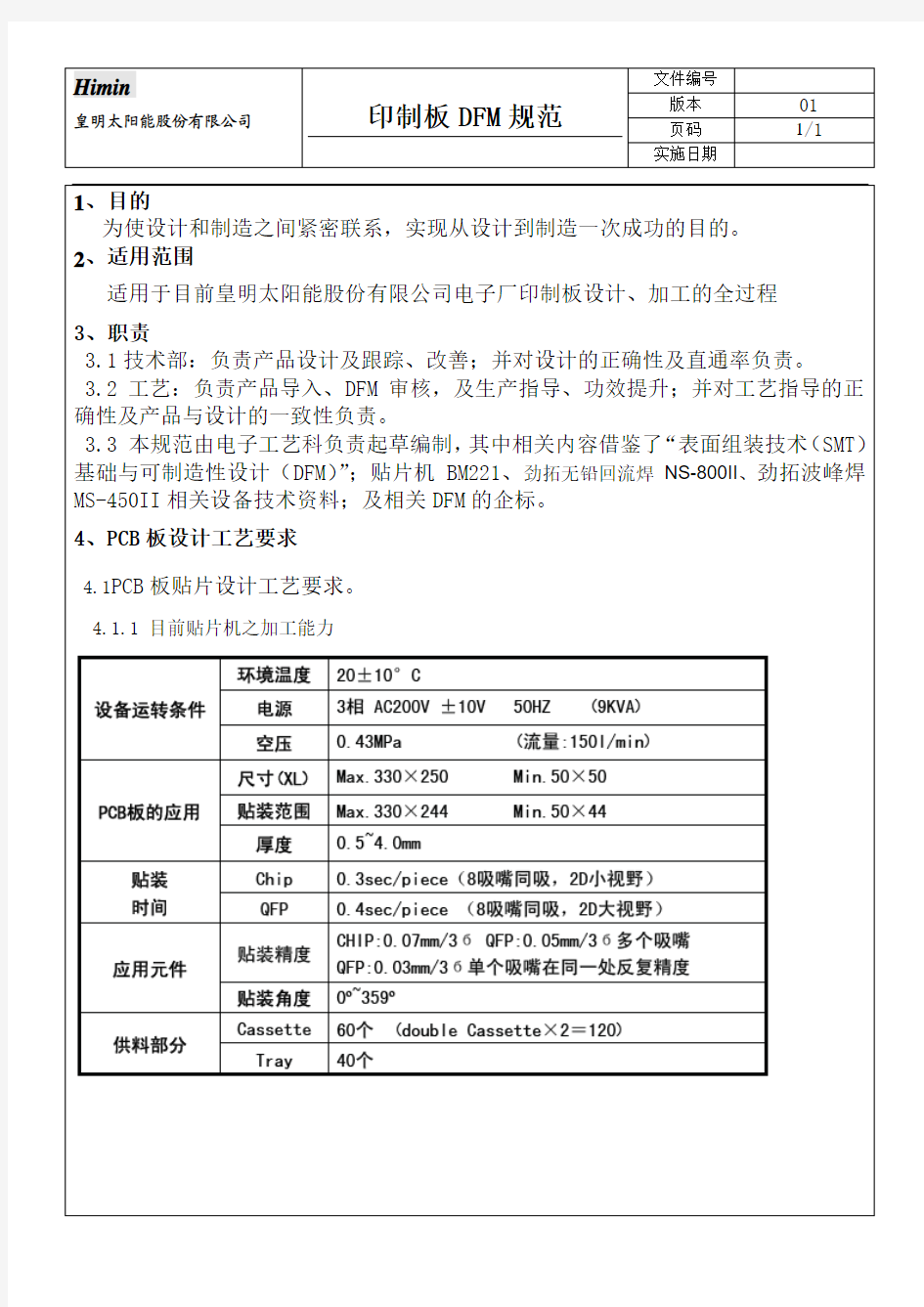
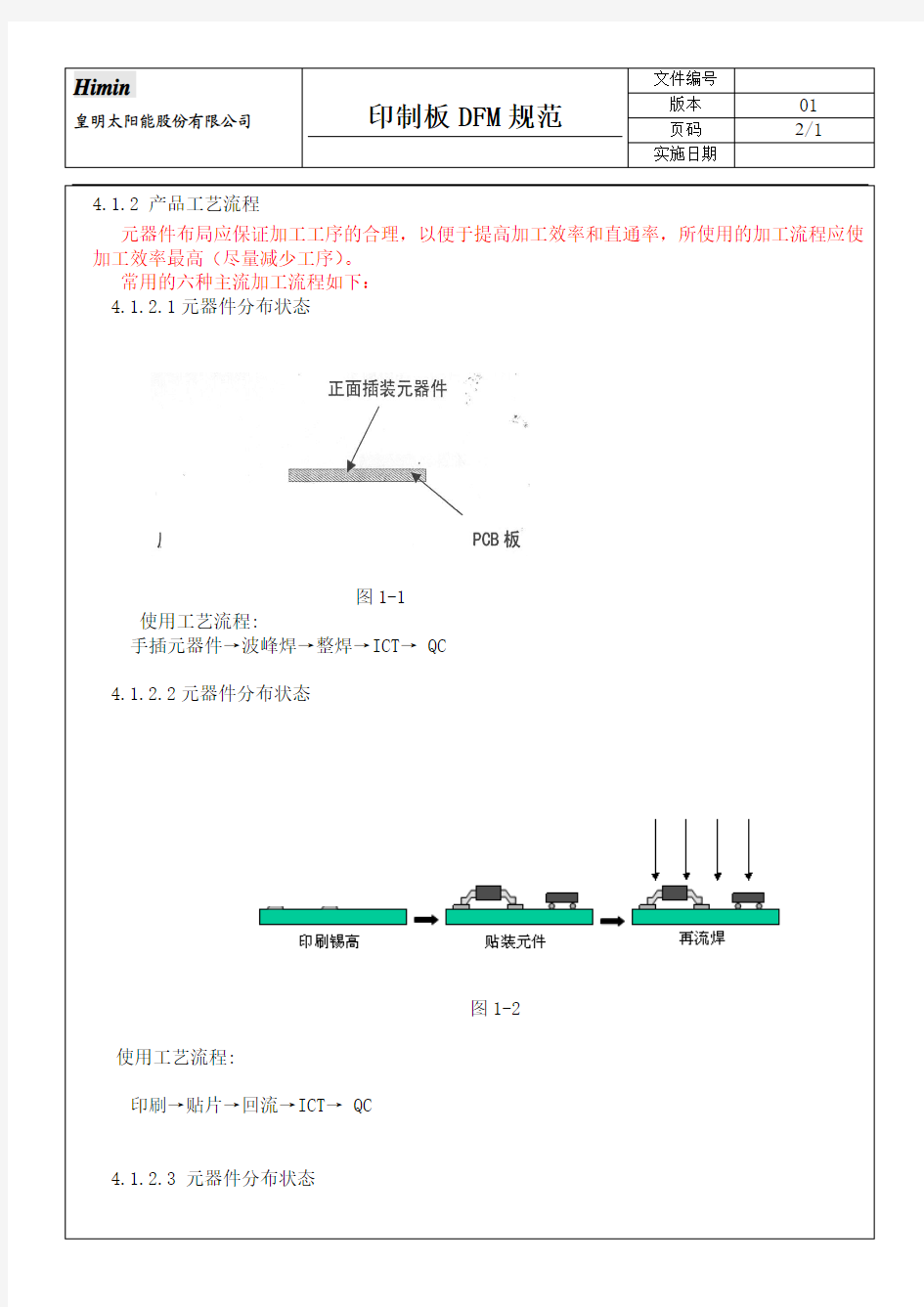
实施日期
1、目的
为使设计和制造之间紧密联系,实现从设计到制造一次成功的目的。
2、适用范围
适用于目前皇明太阳能股份有限公司电子厂印制板设计、加工的全过程
3、职责
3.1技术部:负责产品设计及跟踪、改善;并对设计的正确性及直通率负责。
3.2工艺:负责产品导入、DFM审核,及生产指导、功效提升;并对工艺指导的正确性及产品与设计的一致性负责。
3.3 本规范由电子工艺科负责起草编制,其中相关内容借鉴了“表面组装技术(SMT)基础与可制造性设计(DFM)”;贴片机BM221、劲拓无铅回流焊NS-800II、劲拓波峰焊MS-450II相关设备技术资料;及相关DFM的企标。
4、PCB板设计工艺要求
4.1PCB板贴片设计工艺要求。
4.1.1 目前贴片机之加工能力
实施日期
4.1.2 产品工艺流程
元器件布局应保证加工工序的合理,以便于提高加工效率和直通率,所使用的加工流程应使加工效率最高(尽量减少工序)。
常用的六种主流加工流程如下:
4.1.2.1元器件分布状态
图1-1
使用工艺流程:
手插元器件→波峰焊→整焊→ICT→ QC
4.1.2.2元器件分布状态
图1-2
使用工艺流程:
印刷→贴片→回流→ICT→ QC
4.1.2.3 元器件分布状态
实施日期
图1-3
使用工艺流程:
点红胶→贴片→回流焊→手插元器件→波峰焊→整焊→ICT→ QC
4.1.2.4元器件分布状态(正面贴片元器件/反面贴片元器件)
图1-4
使用工艺流程:
丝网印刷(贴片较少的一面或无集成块等大元件)→贴片→回流→丝网印刷(贴片另一面)→贴片→回流→ (转序)
4.1.2.5 元器件分布状态(正面插装,贴片元器件/反面贴片元器件)
实施日期
图1-5
使用工艺流程
丝网印刷→贴片(正面)→回流焊→点红胶→贴片(反面)→回流焊→手插→波峰焊→整焊→ICT→ QC
4.1.2.6元器件分布状态(正面插装,贴片元器件/反面插装,贴片元器件)
图1-6
使用工艺流程
丝网印刷→贴片(正面)→回流焊→点红胶→贴片(反面)→回流焊→手插→波峰焊→整焊→反面插装器件手焊→ICT→ QC →检测→包装,入库
实施日期
优选的工艺流程顺序为:1→2→3→4→5→6
随着贴片技术的发展,我们也可按照以下流程进行设计。
实施日期
4.1.3 MARK 设计要求
4.1.3.1需贴片的线路板的MARK 点要放在线路板的对角线上,并且MARK 点设计要求为直径是¢1.0的圆焊盘-无孔无绿油,再加一个¢3.0同心圆-无铜皮(如下图)线路板上的贴片元器件要在MARK 点边的里面,贴片元器件太靠边的线路板要在线路板边加一条5mm 的工艺边.如下图:图1-7
2
4
图1-7
4.1.3.2对于IC (QFP,PLCC,BGA )等器件,要求在零件的单位对角加两个MAKE 点,作为该零件校正标记,位置可选在元器件内或附进. MARK 点设计要求为直径是¢1.0的圆焊盘-无孔无绿油,再加一个¢2.0同心圆-无铜皮(如下图图1-8)。
图1-8
4.1.4定位孔:孔壁要求光滑,不应有涂覆层,定位孔周围1.5mm 处无铜箔,且不得贴装元件。
4.1.5工艺边: 印制板两侧3-5mm 以上不贴装元器件,不允许放置插件、和走线。
直径为¢1.0±0.1
两MAKE 点位置:距非传输边15mm 以上;距传输边4mm 以上,如图
MARK 点
直径为¢3.0±0.1 15
实施日期
4.1.6对于吸热大的器件,在整板布局时要考虑焊接时热均衡原则,不要把吸热多的器件集中放在一处,以免造成局部供热不足,面另一处过热现象。
4.1.7 SMD 器件的引脚与大面积铜箔连接时,要进行热隔离处理。
4.1.7.1采取热隔处理,如下图:图1-9
图1-9
其中A 表示铜箔最小间隙:单面板:0.3MM,双面板:0.2MM ;B 表示铜箔最小线宽:单面板
0.3MM,双面板:0.2MM ,最大不超过焊盘宽度的三分之一。
4.1.7.2对于需过5A 以上大电流的焊盘不能采用隔热焊盘,可采用如下方法。
图1-10
4.1.8在采用贴片一波峰工艺时,片式元件,SOIC 的引脚焊盘应垂直于印制板波峰焊运动方
向,QFP(引脚间距≥ 0.8mm 以上), 则应转角45°,引脚之间加阻焊层,SOIC,QFP 除注意方向外,还应增加辅助焊盘,引脚之间增加阻焊层,如图:
图1-11
4.1.9 在采用贴片一波峰工艺(即工艺流程中4.1.2.3所采用的流程)时,应确定贴片阻容件与
SOP 的布局方向正确,贴片电阻、电容、二极管、三极管在线路板上的放置方向要与过波峰焊方向垂直SOP 器件轴向需与波峰方向一致,并在左边的第一个引脚上加宽焊盘,宽为2倍的其它焊盘,如下图:
导锡角图形如图,大
小为同引脚宽度。
实施日期
方向正确
图1-12
4.1.10 在采用贴片--波峰工艺(即工艺流程中4.1.2.3所采用的流程)时,某些片式元件如SOT-23
需在元器件的引脚附近增加收锡孔。
图1-13
类似贴片三极管封装的元器件在图示处增加通孔,大小为¢0.6mm。
4.1.11贴片元件焊盘设计
4.1.11.1常用贴片阻容和三极管的焊盘设计,当采用锡膏焊接时的焊盘设计可根据标准库里现有的文件设计,采用波峰焊工艺时:
实施日期
公制尺寸英制尺寸 A B c
1608 0603 0.7 0.8 0.8
2125 0805 1.0 1.5 1.5
3216 1206 2.0 1.2 1.6
封装形式 a b c d e f
Smt3 1.8 0.8 1.3 1.4 0.3 1.2
图1-14
4.1.11.2两面引脚芯片(P≥0.5MM)焊盘设计:
图1-15
4.1.11.3波峰焊接面上不能安放QFP/PLCC等器件(单面板特殊情况应满足45度布局、设计椭圆焊盘、L值增加或延长0.4-0.6mm即焊盘延长、波峰尾部增加窃锡焊盘P≥0.8MM即引脚间距≥0.8MM)焊盘设计:
实施日期
图1-16
4.1.12在采用贴片波峰工艺(即工艺流程中1.3所采用的流程)时,背面器件不形成阴影效应的
安全距离已考虑波峰焊工艺的SMT器件距离要求如下:
4.1.12.1呈平行排列的贴片电阻,贴片电容焊盘间距保持在0.5mm以上。
图1-17
4.1.12.2呈垂直排列的贴片电阻,贴片电容焊盘间距保持在0.4mm以上。
图1-18
4.1.12.3呈直线排列的贴片电阻,贴片电容焊盘间距保持在0.4mm以上。
图1-19
4.1.12.4芯片和贴片电阻,贴片电容之间的距离关系。
图1-20
4.1.12.5其它异种器件之间的距离关系。
实施日期
图1-21
4.1.13贴片器件焊盘上不能有过孔,要求过孔离焊盘距离在0.4mm以上。如下图:
图1-22
4.1.14瓷片电容、三极管等径向元件应尽量设计成贴片,以提高生产效率;若该产品已含有贴
片工序,则瓷片电容、三极管径向元件则一定设计成贴片。
4.2.PCB板波峰焊设计工艺要求:
4.2.1波峰焊设备加工能力
4.2.2 线路板上的元器件本体距线路板至少有两平行边缘不得小于5mm。有芯片的线路板,平行芯
实施日期
片的两条边的元器件距离线路板不得小于5mm,若达不到要求,由PCB应加工艺边,器件与V-CUT 的距离≧1mm。距离PCB边缘3mm处不能放置走线;示意图如下:
140~180mm
DIP(波峰焊流)
图1-23
4.2.3波峰焊拼板最佳尺寸:拼板最佳宽度为140mm~180mm。
4.2.4波峰焊进板的方向:为防止过波峰焊时元器件的各引脚之间的连焊,通常把主要集成块
的焊接方向作为PCB板的焊接方向,同时较重的一端作为尾部。
4.2.5波峰焊进板的方向标识:应在PCB板工艺边上注明,如无拼板工艺边,直接在板上注明并使
进板方向合理。
标识尺寸
图1-24
4.2.6拼板设计:拼板形式,PCB板的外形以长方形为准,单板的长作为拼板后的宽,保证拼板的
美观及成本的控制。对于特殊形状的线路板要采用特定的连接方式。
图1-25 物殊形状线路板的拼板形式
4.2.7 V型槽:
4.2.7.1 V型槽设计:
实施日期
图1-26
图1-27
4.2.7.2 V型槽拼板数量:当拼板需要做V-CUT时,拼板的PCB板厚应小于3.5mm;最佳:
平行传送方向的V-CUT数量≤3(对于细长的单板可以例外)。
实施日期
图1-28
4.2.8若PCB上有大面积开孔的地方,在设计时要先将孔补全(在0~15mm范围内必须有拼板),以
避免焊接时造成漫锡和板变形,补全部分和原有的PCB部分要以单边几点连接,在波峰焊后将之去掉。
图1-29
4.2.9传送方向:要求L>W。(L:线路板拼板总长度,W:线路板拼板总宽度)
图1-30
4.2.10板材纹路方向:即线路板中加强纤维的走向。覆铜箔板的纤维为线状。板材方向为纤维的走向。覆箔板的纤维为网状,则无方向性,如玻璃布板都无方向性。沿着板材方向,线路板的机械性能能增加。如下图:
图1-31
4.2.11在线路板的螺丝孔周围1.5mm之内不得布线,避免在打螺丝时打断线路板.定位孔,安装孔铜
箔面边缘应无铜箔,否则过波峰焊后焊锡会将孔堵住.
4.2.12为提高波峰焊接质量轴向/径向元件应垂直与过波峰焊的方向。
实施日期
图1-32
4.2.13超高的元器件在线路板设计时,不能将该元器件放置到PCB边缘造成运输损坏(WLT-MII 主板电解电容1000UF/25V)
4.2.14为防止轴向器件过波峰焊短路,焊盘与焊盘之间的距离必须大于0.5mm;
4.3手插件设计工艺要求
4.3.1手插器件开孔原则:
4.3.2重量大部品摆放(维持PCB板整体的重量均衡)
图1-33
4.3.3 IC下面以不设跨线为最佳.如果设计时,注意跨线的对称及IC放置后的平衡
性。
错误
图1-34
4.3.4重加焊设计:
实施日期
4. 3.4.1线路板设计时,如计算不能承受负载电流,可裸露线路铜箔或加宽线路,
要求过波峰焊后满足负载电流标准要求,确因两种方式不能达标,应改用
多根跳线或导线连接方式,线束规格的选择要保证与实际电路需求一致,
原则上不允许手工重加焊。
4.3.4.2对大电流元件脚用铆钉加固时,该焊点作特别加锡要求。需要加焊的焊点或走线,用三角形进行标识。如下图:
图1-35
4.3.4.3较重的元器件(如变压器),其焊盘应设计为菊花状(发散状)。
4.3.5为尽可能地避免连焊,对于连续排列的多个(两个或两个以上)焊盘,设计时应以类似椭圆形为主,焊盘相邻部分要标准的许可下窄化,以增大焊盘相对间距,同时在(焊接外围加阻焊层以防连焊。
4.4. PCB板可测试性(DFT)设计工艺要求
为提高产品质量,降低测试成本和缩短产品的制造周期;要求所有贴片元件的板子必须加测试点,有关测试点的工艺性要求及可测试性要求如下:
4.4.1 精确的定位孔:PCB板(单板)上必须有两个非金属化的定位孔,定位孔的大小为φ3~4mm(一
般要求为φ4),定位孔精度为0.05mm如图1。
4.4.2测试点为圆形焊盘,要求不小于0.4mm,但为确保测试的经济性及可靠性一般焊盘直径设定
φ1.2~1.5mm(一般为φ1.5mm.元器件分布密集,焊盘直径设定成φ1.2mm),相邻测试点的间距最好在2.54mm以上。
4.4.3最好将测试点放在元器件1.0mm以外避免探针损伤元器件;定位孔环附近3.2mm以内不可
有元器件和测试点;测试点不可设置在PCB夹持边4mm范围内;测试点不可被阻焊剂或文字油墨覆盖。
实施日期
4.4.4测试点要求加在插件元器件的引脚面。
要求尽量将元件面的SMC,SMD测试点通过过孔引到焊接面,过孔直径应大于1.0mm,避免两面用针床测试减低测试成本。
4.4.5测试点添加规则:每个电器接点都必须有一个测试点,每个IC必须有蒂电源(POWER)及地
(GROND)的测试点,测试点尽量接近器件;每一条走线选一个点作为测试点,若该走线的两端为贴片元件,则必须在走线上添加测试点;若走线的两端,有一端为插件元件则该走线可以不加测试点,但须满足与其它线路测试点的间距≥2.0mm,具体如下图。
4.4.6两测试点之间的间距要求大于2.0mm,否则需要重新选择测试点位置。
4.4.7直插式IC引脚脚距<2.0mm,其引脚不能作为测试点。
两测试点的最小间距必须大于2.0mm,否则必须加测试点。
图1-36
4.4.8测试点应均衡的分布在印制板上,如果探针几种在某区域较高的压力会使带侧板或针床变形。
4.5 PCB板灌胶设计工艺要求
实施日期
电控盒
图1-37
4.5.1要求线路板中央至少有一个以上Ф4的透气孔(漏胶孔),同时线路板四角分布四个Ф4的透
气孔;线路板四边不能与电控盒完全贴紧,应有1.0mm 以上的空隙;线路板与电控盒底部的距离必须在3.5mm 以上。
4.5.2电控盒的设计方式,采取如图1-37:
4.5.3灌胶的高度一般为1.5~2.0mm ,灌胶的产品一定要考虑到元件底部及电控盒的密封性,特
别是插座、开关、可调电位器应采用防水设计。 4.5.4灌胶产品的集成块不能采用IC 座形式。
5.焊盘设计工艺要求
5.1手插器件焊盘根据器件引脚的形状设计,普通器件焊盘为孔径的两倍(D=2d),大电流的器件为
了便于堆锡,可设计成菱形或适当加大焊盘。
图1-38
5.2其他元器件的孔径根据元器件的引脚粗细来确定,如继电器等手插元器件的孔径比元器件引脚
大0.3mm,引脚数少于3个的元器件的孔径比元器件引脚大0.2mm.要求元器件的安装紧配合.
5.3焊盘相对独立,焊盘不要与加导电层铜箔相连,电加热例外.否则过波峰焊后,使元器件焊点变
薄,需加锡.
5.4在三极管,三端稳压块,芯片,插座(XH,PH,EH)及元器件密集引脚处加阻焊层,防止元器件 引脚之间搭焊短路(如图1-39)。
线路板
1.0mm 以上
线路板
电控盒
3.5mm 以上
实施日期
图1-39
5.5 PH ,EH 插座及芯片布板设计时需增加偷锡焊盘(间距在2.54mm 以下),方向与过锡方向相同
(如图1-40),或水平方向成一定角度(如75°,焊盘设计成菱形,最后面的一个焊盘设计成长形如图1-41)或垂直(如图1-42),焊盘与焊盘之间加阻焊层。 1、间距为2.5mm 的也可采用涂覆阻焊层方式(整个焊盘周围涂阻焊层,XH 可以不加偷锡焊盘)。
图1-40
图1-41 图1-42
2.芯片引脚间距为1.78、PH/EH 插座以及类似的偷锡焊盘规定尺寸如下图:
5.6对于单面板中过波峰焊后插的插焊元器件,元件插孔增加开锡槽设计,开开锡槽沿水平方向,
与PCB 移动方向一致,宽度视孔的大小为0.4 mm 到1.0mm 。
SOL
DIP
偷锡焊盘
实施日期
图1-43
5.7当电路中走线需要流过大电流时,需设置条形焊锡层(不允许将走线设置为大面积的焊锡层)如下图:
图1-44
6.元器件设计工艺要求
6.1.元器件设计跨距要求(为提高预成型效率避免设备的反复调整,操作的标准化)
6.1.1 设计时应尽量采用系统内已有的通用规格元器件.
各元器件推荐跨距要求如下:
名称 规格型号 跨距(mm) 备注 电阻 1/8w 10
1/6w 10 1/4w , 1/2W 短小型 10 1/2w 12.5 1w 15 2w 20 电解电容 220uF 、470uF 、1000UF 5
手插件
22UF/450 7.5 1uf 、10uF 、100uF 2.5
瓷片电容 104 5 涤纶电容 103J/630V 9.2 消磁电容 0.1U/275V 15 风机电容 实际尺寸
二极管 1N4148 10
1N4007 12.5
HER107 12.5
压敏电阻 7.5
0.4~1.0mm
DIP
PCB设计规范
PCB设计规范 _2s-Z_. 冃U言 木规范参考国.家标准卬毓卜也路板设计和使用等标准编制而成。 、布局 元件在二维、三维空间上不能产生冲突。 先放置与结构关系密切的元件,如接插件、开关、电源插座等。对于按键,连接器等与结构相关 的元器件放置好后应锁定,以免在无意之中移动。 如果有相同结构电路部分,尽可能采用“对称式”标准布局。 元器件的排列要便于调试和维修,小元件周围尽量不放置大元件、需调试的元、器件周围要有足够的空间。 按照“先大后小,先难后易”的布置原则,重要的单元电路、核心元器件应当优先布局。 布局应尽量满足以下要求:总的连线尽可能短,关键信号线最短;高电压、大电流信号与小电流, 低电压的弱信号完全分开;模拟信号与数字信号分开;高频信号与低频信号分开;高频元器件的间 隔要充分; 发热元件要一般应均匀分布(如果有散热片还需考虑其所占的位置),且置于下风位置以利于单板和整机的散热,电解电容离发热元件最少400mil;除温度检测元件以外的温度敏感器件应远离发 热量大的元器件。 元器件离板边尽量不小于5mm,特殊情况下也应大于板厚。 如果PCB用排线连接,控制排线对应的插头插座必须成直线,不交叉、不扭曲。 连续的40PIN排针、排插必须隔开2mm以上。 考虑信号流向,合理安排布局,使信号流向尽可能保持一致。输入、输出元件尽量远离。 电压的元器件应尽量放在调试时手不易触及的地方。 驱动芯片应靠近连接器。 有高频连线的元件尽可能靠近,以减少高频信号的分布参数和电磁干扰。 对于同一功能或模组电路,分立元件靠近芯片放置。连接器根据实际情况必须尽量靠边放置。 开关电源尽量靠近输入电源座。 BGA等封装的元器件不应放于PCB板正中间等易变形区 BGA等阵列器件不能放在底面,PLCC、QFP等器件不宜放在底层。 多个电感近距离放置时应相互垂直以消除互感。 元件的放置尽量做到模块化并连线最短。 在保证电气性能的前提下,尽量按照均匀分布、重心平衡、版面美观的标准优化布局。 按电路模块进行布局,实现同一功能的相关电路称为一个模块,电路模块中的元件应采用就近集中原则,同时数字电路和模拟电路分开; 定位孔、标准孔等非安装孔周围 1.27mm内不得贴装元、器件,螺钉等安装孔周围 3.5mm (对于M2.5 )、4mm(对于M3内不得贴装元器件; 卧装电阻、电感(插件)、电解电容等元件的下方避免布过孔,以免波峰焊后过孔与元件壳体短 路; 元器件的外侧距板边的距离为5mm 贴装元件焊盘的外侧与相邻插装元件的外侧距离大于2mm 金属壳体元器件和金属件(屏蔽盒等)不能与其它元器件相碰,不能紧贴印制线、焊盘,其间距应大于2mm定位孔、紧固件安装孔、椭圆孔及板中其它方孔外侧距板边的尺寸大于3mm 发热元件不能紧邻导线和热敏元件;高热器件要均衡分布; 电源插座要尽量布置在印制板的四周,电源插座与其相连的汇流条接线端应布置在同侧。特别应注意不要把电源插座及其它焊接连接器布置在连接器之间,以利于这些插座、连接器的焊接及电源线缆设计和扎线。电源插座及焊接连接器的布置间距应考虑方便电源插头的插拔;其它元器件的布置:
SMT印制板设计规范
S M T印制板设计规范 Document serial number【KKGB-LBS98YT-BS8CB-BSUT-BST108】
SMT印制板设计规范 锡膏印刷缺陷分析SMT印制板设计规范 缺陷类型 可能原因 改正行动 锡膏对铜箔位移 印刷钢板未对准,钢板或电路板不良调整印刷机,测量钢板或电路板 短路 锡膏过多,孔损坏 检查钢板 锡膏模糊 钢板底面有锡膏、与电路板面间隙太多清洁钢板底面 锡膏面积缩小 钢孔有乾锡膏、刮刀速度太快 清洗钢孔、调节机器 锡膏面积太大
刮刀压力太大、钢孔损坏 调节机器、检查钢板 锡膏量多、高度太高 钢板变形、与电路板之间污浊 检查钢板、清洁钢板底面 锡膏下塌 刮刀速度太快、锡膏温度太高、吸入水份及水气 调节机器、更换锡膏 锡膏高度变化大 钢板变形、刮刀速度太快、分开控制速度太快 调节机器、检查钢板 锡膏量少 刮刀速度太快、塑胶刮刀刮出锡膏 调节机器 回流焊缺陷分析: *锡珠:原因: *1、印刷孔与铜箔不对位,印刷不精确,使锡膏弄脏PCB。*2、锡膏在氧化环境中暴露过多、吸空气中水份太多。
*3、加热不精确,太慢并不均匀。 *4、加热速率太快并预热区间太长。 *5、锡膏乾得太快。 *6、助焊剂活性不够。 *7、太多颗粒小的锡粉。 *8、回流过程中助焊剂挥发性不适当。 ※:锡球的工程认可标准是:当铜箔或印制导綫的之间距离爲 0.13mm时,锡珠直径不能超过0.13mm,或者在600mm平方范围内不能出现超过五个锡珠。 ※:短路:一般来说,造成短路的因素就是由於锡膏太稀,包括锡膏内金属或固体含量低、摇溶性低、锡膏容易榨开,锡膏颗粒太大、助焊剂表面张力太小。焊盘上太多锡膏,回流温度峰值太高等。 *空悍:原因: *1、锡膏量不够。 *2、零件接脚的共面性不够。 *3、锡湿不够(不够熔化、流动性不好),锡膏太稀引起锡流失。 *4、接脚吸锡或附近有连线孔。接脚的共面性对密间距和超密间距接脚零件特别重要,一个解决方法是在铜箔上预先上锡。接脚吸锡可以通过放慢加热速度和底面加热多、上面加热少来防止。也可以
SMT印制板设计规范
SMT印制板设计规范 錫膏印刷缺陷分析SMT印制板设计规范 缺陷類型 可能原因 改正行動 錫膏對銅箔位移 印刷鋼板未對準,鋼板或電路板不良調整印刷機,測量鋼板或電路板 短路 錫膏過多,孔損壞 檢查鋼板 錫膏模糊 鋼板底面有錫膏、與電路板面間隙太多清潔鋼板底面 錫膏面積縮小 鋼孔有乾錫膏、刮刀速度太快 清洗鋼孔、調節機器 錫膏面積太大 刮刀壓力太大、鋼孔損壞 調節機器、檢查鋼板 錫膏量多、高度太高 鋼板變形、與電路板之間汙濁
檢查鋼板、清潔鋼板底面 錫膏下塌 刮刀速度太快、錫膏溫度太高、吸入水份及水氣 調節機器、更換錫膏 錫膏高度變化大 鋼板變形、刮刀速度太快、分開控制速度太快 調節機器、檢查鋼板 錫膏量少 刮刀速度太快、塑膠刮刀刮出錫膏 調節機器 回流焊缺陷分析: * 錫珠:原因: * 1、印刷孔與銅箔不對位,印刷不精確,使錫膏弄髒PCB。* 2、錫膏在氧化環境中暴露過多、吸空氣中水份太多。 * 3、加熱不精確,太慢並不均勻。 * 4、加熱速率太快並預熱區間太長。 * 5、錫膏乾得太快。 * 6、助焊劑活性不夠。 * 7、太多顆粒小的錫粉。 * 8、回流過程中助焊劑揮發性不適當。
※: 錫球的工程認可標準是:當銅箔或印製導綫的之間距離爲0.13mm時,錫珠直徑不能超過0.13mm,或者在600mm平方範圍內不能出現超過五個錫珠。 ※: 短路:一般來說,造成短路的因素就是由於錫膏太稀,包括錫膏內金屬或固體含量低、搖溶性低、錫膏容易榨開,錫膏顆粒太大、助焊劑表面張力太小。焊盤上太多錫膏,回流溫度峰值太高等。 * 空悍:原因: * 1、錫膏量不夠。 * 2、零件接腳的共面性不夠。 * 3、錫濕不夠(不夠熔化、流動性不好),錫膏太稀引起錫流失。 * 4、接腳吸錫或附近有連線孔。接腳的共面性對密間距和超密間距接腳零件特別重要,一個解決方法是在銅箔上預先上錫。接腳吸錫可以通過放慢加熱速度和底面加熱多、上面加熱少來防止。也可以用一種浸濕速度較慢、活性溫度高的助焊劑或者用一種Sn/Pb不同比例的阻滯熔化的錫膏來減少接腳吸錫。 焊錫球 許多細小的焊錫球鑲陷在回流後助焊劑殘留的周邊上。在RTS曲綫上,這個通常是升溫速率太慢的結果,由於助焊劑載體在回流之前燒完,發生金屬氧化。這個問題一般可通過曲綫溫升速率略微提高達到解決。焊錫球也可能是溫升速率太快的結果,但是,這對RTS曲綫不大可能,因爲其相對較慢、較平穩的溫升。 焊錫珠
pcb印制板设计规范
竭诚为您提供优质文档/双击可除pcb印制板设计规范 篇一:pcb工艺设计规范 规范产品的pcb工艺设计,规定pcb工艺设计的相关参数,使得pcb的设计满足可生产性、可测试性、安规、e(pcb 印制板设计规范)mc、emi等的技术规范要求,在产品设计过程中构建产品的工艺、技术、质量、成本优势。 本规范适用于所有电了产品的pcb工艺设计,运用于但不限于pcb的设计、pcb投板工艺审查、单板工艺审查等活动。 本规范之前的相关标准、规范的内容如与本规范的规定相抵触的,以本规范为准。 导通孔(via):一种用于内层连接的金属化孔,但其中并不用于插入元件引线或其它增强材料。 盲孔(blindvia):从印制板内仅延展到一个表层的导通孔。埋孔(buriedvia):未延伸到印制板表面的一种导通孔。 过孔(throughvia):从印制板的一个表层延展到另一个表层的导通孔。
元件孔(componenthole):用于元件端子固定于印制板及导电图形电气联接的孔。standoff:表面贴器件的本体底部到引脚底部的垂直距离。 板材,应在文件中注明厚度公差。 机密 20xx-7-9页1页 5.2热设计要求 5.2.1高热器件应考虑放于出风口或利于对流的位置 5.2.4温度敏感器械件应考虑远离热源 对于自身温升高于30℃的热源,一般要求: 若因为空间的原因不能达到要求距离,则应通过温度测试保证温度敏感器件的温升在降额范围内。 为了保证透锡良好,在大面积铜箔上的元件的焊盘要求用隔热带与焊盘相连,对于需过5a以上大电流的焊盘不能采用隔热焊盘,如图所示: 焊盘两端走线均匀 或热容量相当 焊盘与铜箔间以”米”字或”十”字形连接 5.2.6过回流焊的0805以及0805以下片式元件两端焊盘的散热对称性 为了避免器件过回流焊后出现偏位、立碑现象,地回流焊的0805以及0805以下片式元件两端焊盘应保证散热对称
华为PCB设计规范
~~ Q/DKBA 深圳市华为技术有限公司企业标准 Q/DKBA-Y004-1999 印制电路板(PCB)设计规范 VER 1.0 0707
1999-07-30发布 1999-08-30实施 深圳市华为技术有限公司发布 前言 本标准根据国家标准印制电路板设计和使用等标准编制而成。 本标准于1998年07 月30日首次发布。 本标准起草单位:CAD研究部、硬件工程室本标准主要起草人:吴多明韩朝伦胡庆虎龚良忠张珂梅泽良本标准批准人:周代琪 0707
Q/DKBA-Y004-1999 目录 目录 1. 1 适用范围 4 2. 2 引用标准 4 3. 3 术语 4 4. 4 目的 2 .1 4.1 提供必须遵循的规则和约定 2 .2 4.2 提高PCB设计质量和设计效率 2 5. 5 设计任务受理 2 .3 5.1 PCB设计申请流程 2 .4 5.2 理解设计要求并制定设计计划 2 6. 6 设计过程 2 .5 6.1 创建网络表 2 .6 6.2 布局 3 .7 6.3 设置布线约束条件 4 .8 6.4 布线前仿真(布局评估,待扩充)8 .9 6.5 布线8 .10 6.6 后仿真及设计优化(待补充)15 .11 6.7 工艺设计要求15 7. 7 设计评审15 .12 7.1 评审流程15 .13 7.2 自检项目15 附录1:传输线特性阻抗 附录2:PCB设计作业流程 3
深圳市华为技术有限公司1999-07-30批准 1999-08-30实施 深圳市华为技术有限公司企业标准 Q/DKBA-Y004-1999 印制电路板(PCB )设计规范 1. 适用范围 本《规范》适用于华为公司CAD 设计的所有印制电路板(简称PCB )。 2. 引用标准 下列标准包含的条文,通过在本标准中引用而构成本标准的条文。在标准出版时,所示 版本均为有效。所有标准都会被修订,使用本标准的各方应探讨,使用下列标准最新版本的 可能性。 [s1] GB 4588.3—88 印制电路板设计和使用 Q/DKBA-Y001-19 99 印制电路板CAD 工艺设计规范 1. 术语 1..1 PCB (Print circuit Board):印刷电路板。 1..2 原理图:电路原理图,用原理图设计工具绘制的、表达硬件电路中各种器件之间的连接 关系的图。 1..3 网络表:由原理图设计工具自动生成的、表达元器件电气连接关系的文本文件,一般包 含元器件封装、网络列表和属性定义等组成部分。 1..4 布局:PCB 设计过程中,按照设计要求,把元器件放置到板上的过程。
印制PCB板通用设计规范(拼板)
印制板通用设计规范(草稿) 1职责与流程 1.1 新设计的PCB板 根据产品要求新设计的PCB板的制作、入厂验收按以下流程进行。 1.2原有的PCB板 对已经设计好的PCB板应按SMT的要求进行夹持边、Mark点或拼板的补充设计,其制作、入厂验收按以下流程进行。
2 SMT 设备对PCB 的要求 2.1 PCB 板在SMT 中的放置 PCB 板流向由左至右 ≥ ≥ 2.2 SMT 对PCBA 的要求 2.3 夹持边的设置 为保证SMT 设备正常运行,在PCB 板的两侧沿PCB 板流向设置3~5mm 的夹持边,在受
到安装尺寸限制时,夹持边的宽度应≥3mm。在夹持边的范围内,不允许存在元器件。 2.4 PCB的尺寸要求 2.4.1 SMT设备允许的PCB板最大尺寸为330mm×250mm,大于此尺寸贴片机不能贴装。2.4.2 PCB板允许的最小尺寸50mm×50mm,建议PCB板尺寸≤80mm×80mm时做拼版处理。 2.4.3 PCB板外形有铣边要求,或有元器件(如接插件)超出PCB板边缘,加工前应说明。 2.4.4 有缺口类异型PCB板需做拼版或补板处理。 2.4.5 不需要拼版的PCB板如允许时,可将四个角设计成R2圆角,方便SMT设备间传送。做拼版处理的PCB板应按照拼版要求,将夹持边的四个角设计成R2圆角。 2.5 PCB板设计应考虑工艺流向,必要时在PCB板上或下边缘画出流向标识。我公司SMT 流程为由左→右。 3 PCB板设计坐标原点的选取 根据我公司SMT设备要求,规定PCB板统一以PCB板的右下角为坐标原点(0,0)。 4 基准标志(Mark)设计 基准标志(Mark) :是为了纠正PCB加工误差,用于光学定位的一组图形。由于SMT 设备的识别相机的视野范围为4.0mm×4.0mm,所以MARK点必须在其范围内。 3.1 Mark点的种类: 3.2 Mark点的形状与设计要求
PCB设计规范37839
______________________________________________________________________________________________________________ 1 目的 为了PCB 设计标准规范化,PCB 设计符合客户、生产、品质要求特制定本文件。 2 范围 发 行 及 修 正 栏 版 本 修 正 内 容 生 效 日 期 备 注 A0 新 发 行 2010-05-01 A1 A2 A3 A4 A5 B0 B1 B2 B3 B4 B5 分 发 栏 总经理 管理者代表 业务部 工程部 采购部 物控部 计划部 生产部 品质部 仓务部 文控中心 人事行政部 制 定 及 审 批 编 写: 审 核: 批 准:
适用于PCB开发设计、修改的整个过程。 3职责 PCBA工程组负责本规范的制定/修订与实施,PE主管负责监督本程序正确实施。 4内容 4.1PCB设计步骤(以下“L”表示所设置层,如“L7”表示设置在第7层) 4.1.1画Board线(LO),开孔线(L24)。 4.1.2画Key位置线、导电胶碳Key面形状(L7) 4.1.3画导电胶外形及偷空位轮廓线(L8)。 4.1.4画底面壳柱位、骨位线(防撞线)(L9)。 4.1.5设置布线层。 4.1.6建Key,放置Key。 4.1.7确定元件形状建元件,放置元件。 4.1.8为各元件加鼠线,并为各网络命名。 4.1.9检查鼠线连接,调整并确定元件位置。 4.1.10布线,布线优化,整理。 4.1.11加元件位铜皮。 4.1.12添加阻焊膜(绿油窗)。 4.1.13添加文字标识(正面白油放在L5,背面白油放在L6,绿油文字放在L4)。 4.1.14添加SMT元件面基准点。 4.1.15确定拼板图和出板数。 4.1.16全面检查,菲林输出。 4.2PCB设计标准 4.2.1 线径及安全间距对照表 ITEM 双面镀金板尺寸标准(mm)单面板、双面贯碳板尺寸标准(mm)1.电源/地线0.6以上(尽可能加大) 0.6以上(尽可能加大) 2.IR灯连线0.5以上0.5以上 3.I/O铜皮连线0.2以上0.25以上 4.相邻两铜皮连线间距0.2以上(尽可能加大) 0.25以上(尽可能加大) 5.相邻不相连两焊盘间距0.5以上(但PITCH≤2mm最小间 距可取0.4mm) 0.5以上(但PITCH≤2mm最小间 距可取0.4mm) 6.金手指宽/间距0.25至0.5 \ 7.碳手指宽/间距\ 0.5至0.6
PCB电路板PCB设计规范
PCB电路板PCB设计规 范
PCB设计规范 二O一O年八月 目录 一.PCB设计的布局规范---------------------------3 ■布局设计原则-----------------------------------3 ■对布局设计的工艺要求------------------------------4 二.PCB设计的布线规范--------------------------15 ■布线设计原则----------------------------------15 ■对布线设计的工艺要求-----------------------------16 三.PCB设计的后处理规范-------------------------25 ■测试点的添加----------------------------------25 ■PCB板的标注---------------------------------27 ■加工数据文件的生成------------------------------31 四.名词解释----------------------------------33 ■金属孔、非金属孔、导通孔、异形孔、装配孔--------------33 ■定位孔和光学定位点------------------------------33 ■负片(Negative)和正片(Positive)------------------33 ■回流焊(ReflowSoldering)和波峰焊(WaveSolder)-------34
■PCB和PBA-----------------------------------34 一.PCB设计的布局规范 (一)布局设计原则 1.距板边距离应大于5mm。 2.先放置与结构关系密切的元件,如接插件、开关、电源插座等。 3.优先摆放电路功能块的核心元件及体积较大的元器件,再以核心元件为中心摆放周围电路元器件。 4.功率大的元件摆放在利于散热的位置上,如采用风扇散热,放在空气的主流通道上;若采用传导散热,应放在靠近机箱导槽的位置。 5.质量较大的元器件应避免放在板的中心,应靠近板在机箱中的固定边放置。 6.有高频连线的元件尽可能靠近,以减少高频信号的分布参数和电磁干扰。7.输入、输出元件尽量远离。 8.带高电压的元器件应尽量放在调试时手不易触及的地方。 9.热敏元件应远离发热元件。 10.可调元件的布局应便于调节。如跳线、可变电容、电位器等。 11.考虑信号流向,合理安排布局,使信号流向尽可能保持一致。 12.布局应均匀、整齐、紧凑。 13.表贴元件布局时应注意焊盘方向尽量取一致,以利于装焊,减少桥连的可能。
PCB板设计规范
PCB板设计基本规范 适用范围:适用于电子产品设计。 1、单面板要求: 1:线径、线距不小于0.3mm,建议为0.35mm以上。(半玻纤板及玻纤板不小于0.18mm)。 2:焊盘和焊盘之间的间距不小于0.5mm。 3:走线至板边距离板不小于0.8mm。 4:过孔至板边距离不小于1.6mm。 5:元件焊盘孔径不小于0.7mm。 6:丝印文字线宽不小于0.18mm,SMT不小于0.13mm。 7:板边宽的部分离焊盘必须大于3mm以上,SMT板大于5mm。 8:固定螺丝的孔位直径5mm以内不能有元件实体;与非地线的铜皮直径距离为5mm。 9、板厚≤1.0mm,公差±0.10mm;板厚≥1.0mm,公差为±10% 2、双面板要求: 1:线径、线距(金板)不小于0.15mm。(锡板不小于0.18mm) 2:线边距板边不小于0.8mm。 3:孔边距板边不小于1.6mm。 4:孔径不小于0.35mm。 5:丝印文字线宽不小于0.18mm,SMT不小于0.13mm。 6:板边宽的部分离焊盘必须大于3mm以上,SMT板大于5mm。 7:焊盘和焊盘之间的间距不小于0.5mm 8:固定螺丝的孔位直径5mm以内不能有元件实体;与非地线的铜皮直径距离为5mm。 9、板厚≤1.0mm,公差±0.10mm;板厚≥1.0mm,公差为±10% 3、PCB设计布局及走线等基本要求: 1、所有元件放置要有规律,同一工作部分电路尽量靠在一起,避免走长线;电阻要平 插元件尽量排成行,如无特殊要求尽量减少直立元件插件。 2、外线进线部分(包括压敏电阻)必须靠在一起,因开关电路以前的电路属于高压部 分,此走线不要太长越短越好,铜皮走线线径不能小于0.45mm;,不要靠近其它信号线和CPU的IO口,避免对它的干扰。 3、走线转角需走圆角或者45度角,避免走90度角;所有焊盘及地线尽量加粗。 4、所有的元件间距与实体间距需相适应。 5、所有元件要有正确标识,有卧倒的元件要有方向箭头表示。 6、卧倒的元件尽量要有空间卧倒,避免元件压在元件上。 7、如有IC或者其它元件焊盘过密时(即0.4—0.5mm),焊盘间需加白油线,以防止 连锡。 8、需过锡炉的贴片IC与PCB过炉方向要形成45度角。
PCB电路板PCB布线设计规范
PCB电路板PCB布线 设计规范
印制电路板设计规范 一、适用范围 该设计规范适用于常用的各种数字和模拟电路设计。对于特殊要求的,尤其射频和特殊模拟电路设计的需量行考虑。 应用设计软件为Protel99SE。也适用于DXPDesign软件或其他设计软件。 二、参考标准 GB4588.3—88印制电路板设计和使用 Q/DKBA—Y004—1999华为公司内部印制电路板CAD工艺设计规范 三、专业术语 1.PCB(PrintcircuitBoard):印制电路板 2.原理图(SCH图):电路原理图,用来设计绘制,表达硬件电路之间各种 器件之间的连接关系图。 3.网络表(NetList表):由原理图自动生成的,用来表达器件电气连接的关 系文件。 四、规范目的 1.规范规定了公司PCB的设计流程和设计原则,为后续PCB设计提供了设 计参考依据。 2.提高PCB设计质量和设计效率,减小调试中出现的各种问题,增加电路设 计的稳定性。 3.提高了PCB设计的管理系统性,增加了设计的可读性,以及后续维护的便 捷性。 4.公司正在整体系统设计变革中,后续需要自主研发大量电路板,合理的PCB
设计流程和规范对于后续工作的开展具有十分重要的意义。 五、SCH图设计 5.1命名工作 命名工作按照下表进行统一命名,以方便后续设计文档构成和网络表的生成。有些特殊器件,没有归类的,可以根据需求选择其英文首字母作为统一命名。 表1元器件命名表 对于元器件的功能具体描述,可以在LibRef中进行描述。例如:元器件为按键,命名为U100,在LibRef中描述为KEY。这样使得整个原理图更加清晰,功能明确。 5.2封装确定 元器件封装选择的宗旨是 1.常用性。选择常用封装类型,不要选择同一款不常用封装类型,方便元器件
普通印制板设计规范(总结)
低频印制板设计经验 一、PCB板 1.板材与板厚 印制线路板一般用覆箔层压板制成,常用的是覆铜箔层压板。板材选用时要从电气性能、可靠性、加工工艺要求、经济指标等方而考虑。常用的覆铜箔层压板有覆铜箔酚醛纸质层压板、覆铜箔环氧纸质层压板、覆铜箔环氧玻璃布层压板、覆铜箔环氧酚醛玻璃布层压板、覆铜箔聚四氟乙烯玻璃布层压板和多层印制线路板用环氧玻璃布等。由于环氧树脂与铜箔有极好的粘合力,因此铜箔的附着强度和工作温度较髙,可以在260-C的熔锡中浸焊而不起泡。环氧树脂浸渍的玻璃布层压板受潮湿的影响较小。超髙频印制线路最优良的板材是覆铜箔聚四氟乙烯玻璃布层压板。在有阻燃要求的电子设备上,还要使用阻燃性覆铜箔层压板,其原理是由绝缘纸或玻璃布浸渍了不燃或难燃性的树脂, 使制得的覆铜箔酚醛纸质层压板、覆铜箔环氧纸质层压板、覆铜箔环氧玻璃布层压板、覆铜箔环氧酚醛玻璃布层压板,除了具有同类覆铜箔层压板的相拟性能以外,还有阻燃性。 印制线路板的厚度应根据印制板的功能及所装元件的重量、印制板插座规格、印制板的外形尺寸和所承受的机械负荷来决左。多层印制板总厚度及各层间厚度的分配应根据电气和结构性能的需要以及覆箔板的标准规格来选取。常见的印制线路板厚度有0. 5mm. 1mm、1.6mm、2mm等。 2.尺寸 本公司贴片机能加工的PCB最大尺寸不超过330mmX250mmo (钢网板最大不超过(450~550) mmX (570-670) mm) 3.外形 由机壳、支架、支撑位等决圧,为PCB板的最终形状,由结构设计工程师提供,不得更改。如需变动,须征得结构工程师同意。 4.固定孔 孔位麗:由支撑柱位置决定,由结构设计工程师提供,不得更改。 孔大小:由固泄螺钉大小决定,由结构设计工程师提供参数。为便于安装,孔的直径一般比螺钉直径大0.2mm~0.5mm。实际尺寸根据PCB在安装时的泄位精确度要求决建。 孔间隙:固泄孔周围要给固泄支架和螺钉头留一左空间用于固左印制板,在这个空间内不允许布线和放置任何元件。固左支架端面参数由结构设讣工程师提供,螺钉头所需的空间尺寸为螺钉头的实际直径加上孔的放大尺寸再加上2mm(例如:用3的螺钉,螺钉头的直径为5mm,固左孔的直径为《3.2,那么为螺钉头留的安装空间尺寸为7.2mm),这样il?算间隙大小使得安装比较安全。 孔类型:当支撑柱为金属,固左孔不要求接保护地时或用于与其它电路板的地相连时,将固定孔设计为非金属化孔,而且在“孔间隙”内不得铺铜。当支撑柱为非金属时,固泄孔可以设计为非金属化孔,也可以设计为金属化孔。如果固龙孔为金属化孔,为避免波峰焊后孔被堵住,固左孔应开走锡位或采用梅花形,如图1、图2所示。梅花形固左孔中的小过孔不加阻焊,中间的大孔为非金属化孔。 图Z梅花形固定孔 图1:开有上锡位的固定孔
印制电路板设计规范标准
印制电路板(PCB)设计规 版本(V1.0) 编制: 审核: 会签: 批准: 生效日期:
印制电路板(PCB)设计规(V1.0) 1围 本设计规规定了印制电路板设计中的基本原则和技术要求。 本设计规适用于盈科电子的印刷电路板的设计。 2引用文件 (本设计规参考了美的空调事业部的电子设备用印刷电路板的设计。) 下列标准所包含的条文,通过在本标准中引用而构成为本标准的条文。本标准出版时,所示版本均为有效。所有标准都会被修订,使用本标准的各方应探讨使用下列标准最新版本的可能性。 GB4706.1-1998 家用和类似用途电器的安全 QJ/MK03.025-2003 空调器防火规 参考文件: GB 4588.3-1988 印刷电路板设计和使用 QJ 3103-1999 印刷电路板设计规(中国航天工业总公司) 3定义 无。 4基本原则 在进行印制板设计时,应考虑本规所述的四个基本原则。 4.1电气连接的准确性 印制板设计时,应使用电原理图所规定的元器件,印制导线的连接关系应与电原理图导线连接关系相一致,印制板和电原理图上元件序号应一一对应。 注:如因结构、电气性能或其它物理性能要求不宜在印制板上布设的导线,应在相应文件(如电原理图上)上做相应修改。 4.2可靠性和安全性 印制板电路设计应符合电磁兼容和电器安规的要求。 4.3工艺性 印制板电路设计时,应考虑印制板制造工艺和电控装配工艺的要求,尽可能有利于制造、装配和维修,降低焊接不良率。 4.4经济性 印制板电路设计在满足使用的安全性和可靠性要求的前提下,应充分考虑其设计方法、选择的基材、制造工艺等,力求经济实用,成本最低。 5技术要求 5.1印制板的选用 5.1.1印制电路板的层的选择 一般情况下,应该选择单面板。在结构受到限制或其他特殊情况下,经过研发经理的批准, 可以选择用双面板设计。 5.1.2 印制电路板的材料和品牌的选择
印制板设计简要规范
金兰电子印制板设计简要规范 一、印制板构成 A、基板:酚醛树脂,环氧树脂或聚四氟乙烯等 B、增强材料:纸质或玻璃布 二、铜箔 A、不能有划痕、沙眼或皱板 B、铜纯度≥99.8% C、厚度误差≤±5μm D、标准有:18、25、35、70、105μm,平常一般用35μm E、设计时,建议铜箔设计的宽度0.5mm以上,特殊情况可少量使用0.4mm 三、印制板分类 A、酚醛纸板,其工作频率≤30MHz,耐湿耐热差 B、环氧玻璃布板,其工作频率≤100MHz,耐湿、耐热、耐药、机械强度好 四、印制板设计及基本要求 A、抗剥离强度:纸板≥0.12kg/mm2;玻璃布板≥0.15kg/mm2 B、焊盘拉脱强度:非金属化孔单面板焊盘拉脱强度,及重焊两次后的拉脱强度不小于以下数据: 焊盘直径 拉脱强度(kg/mm2) 玻璃布纸 2 1 0.2 4 7 5 C、耐热性能: 玻璃布板在260℃±2℃的铅锡熔剂中保持15秒以上后,抗剥离强度≥0.12kg/mm2 纸板在240℃±2℃的铅锡熔剂中保持10秒以上后,抗剥离强度≥0.1kg/mm2 D、耐压性能KV/mm 玻璃布板纸板 正常 1.2 1.2 潮热处理后0.9 0.9 E、一般情况下,位于边沿的元件离边沿不少于2mm F、一般印制板导线的电流密度可设计为20A/mm2,在这个要求下,在温升不大的情况 下,设计导线宽度按以下数据考虑 导线宽度mm 0.5 1.0 1.5 2.0 允许通过的电流A 0.8 1.0 1.3 1.9 G、导线间的间距一般情况下不小于1mm,最好在1.5mm以上。最小的导线间距不得 小于0.5mm H、在-60℃下,击穿电压如下 导线间距mm 0.5 1.0 1.5 击穿电压V 50 200 300 I、焊盘要求 1、焊盘孔大于元件引线直径0.2~0.4mm,一般选0.4mm 2、焊盘直径和安装孔直径的关系按以下参数考虑,特别说明TO-220封装的孔和焊 盘的关系推荐按这个参数:孔1mm,焊盘1.8mm×3mm 焊盘直径mm 2 2.5 3.0 3.5 4.0
PCB印刷电路板设计规范
PCB印刷电路板设 计规范 1
印刷电路板(PCB)设计规范 1范围 本设计规范规定了印制电路板设计中的基本原则、技术要求。 本设计规范适用于电子科技有限公司的电子设备用印刷电路板的设计。 2引用文件 下列文件中的条款经过在本规范中的引用成为本规范的条款。凡是注日期引用的文件,其随后所有的修改单(不包括勘误的内容)或修订版均不适用本规范。 GB 4588.3~88中华人民共和国国家标准:<印刷电路板设计和使用> QJ 3103-99 中国航天工业总公司<印刷电路板设计规范> 3定义 本标准采用GB2036的术语定义 4一般要求
根据结构,印制板分为单面印制电路板、双面印制电路板、多层印制电路板,板材主要分为纸质板(FR-1),半玻璃纤维板(CEM-1),环氧树脂玻璃纤维板(FR-4)。有防火要求的器具用的印制板应有阻燃性和符合相应的UL标准。 4.2印制板设计的基本原则 在进行印制板设计时,应考虑本规范所述的基本原则。 4.2.1电气连接的准确性 印制板上印制导线的连接关系应与电原理图导线连接关系相一致,电原理图设计应符合原理图设计规范,并尽量调用原理图库中的功能单元原理图,印制板和原理图上元件序号应一一对应;如因结构、电气性能或其它物理性能要求不宜在印制板上布设的导线,应在相应文件(如电原理图上)上做相应修改。 4.2.2可靠性 印制板应符合其产品要求的相应EMC规范和安规要求,并留有余量,以减小日益严重的电磁环境的影响。影响印制板可靠性的因素很多,印制板的结构、基材的选用、印制板的制造和装配工艺以及印制板的布线、导线宽度和间距等都会影响到印制板的可靠性。设计时必须综合考虑以上的因素,按照规范的要求,并尽可能的保留余量,以提高可靠性。 4.2.3工艺性 设计电路板时应考虑印制板的制造工艺和装配工艺要求,尽可能有利于制造、装配和维修,各具体要求请严格遵守QG/MK03.04- V的工艺规范。 4.2.4经济性 印制板设计应充分考虑其设计方法、选择的基材、制造工艺等成本最低的原则,满足使用的安全性和可靠性要求的前提下,力求经济实用。 4.2.5 布局
大公司PCB设计规范
XXXXXXX 电器股份有限公司 电子分公司 文件:印制PCB板工艺设计规范 版本: B 制定: 校核: 审核: 审批: 日期: 2008-1-30 1、目的 规范我司产品的PCB工艺设计,规定PCB设计的相关工艺参数,使得PCB的设计满足可生产性、可测试性、安规、EMC、EMI等的技术规范要求,在产品的设计过程中构建产品的工艺、技术、质量、成本的优势。
2、适用范围 适用于本司所有的PCB工艺设计,运用于但不限于PCB的工艺设计、PCB投板工艺审查,单板工艺审查等活动。 考虑到我司的实际情况,本设计规范的内容重点放在了低频、插件工艺的单面PCB上,对于高频、双面(包括多层)、SMT工艺的PCB方面的内容没有做具体的要求,以后随着发展的需要再考虑增加。3.职责 客户:负责 PCB板外形尺寸、主要元件的安装等要求的提供; 技术单位:负责PCB板的设计及样板确认; 品管单位:负责PCB板的试验和来料检验; 3、定义 1、电气间隙:两相邻导体或一个导体与相邻电机壳表面的沿空气测量的最短距离。 2、爬电距离:两相邻导体或一个导体与相邻电机壳表面的沿绝绝缘表面测量的最短距离 4、引用/参考标准或资料 1、《电子分公司标准元件库》 2、IEC60194 《印制板设计、制造与组装术语与定义》 3、TS—S0902010001 《信息技术设备PCB安规设计规范》 5、规范内容 5.1 PCB板材要求: 5.1.1确定PCB使用板材 5.1.1.1 根据设计的产品的实际需要,确定使用PCB板的板材,例如:KB-3151、KB-3150、ZD-90F、 FR-4等; 5.1.1.2 优先采用单面板,除非设计必须或客户要求尽量不采用双面板; 5.1.1.3 对于所选择的板材的阻燃等级要求:除非特别规定,否则本司所有设计的PCB板的板材的 阻燃等级全部按94-V0级标准执行; 5.1.2确定PCB板的表面处理工艺 根据设计产品的需要,确定PCB板铜箔表面的处理工艺,例如:光铜板、镀锡、镀镍、镀金等,应在打样及评估时注明; 5.1.2.1 对于PCB设计过程中涉及带金手指的产品,统一采用镀金工艺; 5.1.2.2 对于PCB设计过程中涉及IC邦定的产品(一般不推荐),优先采用镀金工艺; 5.2 热设计要求: 5.2.1 高热器件应考虑放在出风口或利于对流的位置 PCB在布局中应考虑将高热器件放在整机出风口或利于对流的位置。 5.2.2 较高的元件应考虑放于出风口,且不阻挡风路; 5.2.3 散热器的放置应考虑利于对流 5.2.4 温度敏感器件应考虑远离热源 对于自身温升高于30K的热源,一般要求: 在风冷条件下,电解电容等温度敏感元件离热源距离要求≥2.5mm; 在自然冷条件下,电解电容等温度敏感元件离热源距离要求≥4mm; 若因为空间的原因不能达到要求的距离,则应通过温度测试保证温度敏感元件的温升在将额 范围内。 5.2.5 大面积铜箔要求用隔热带与焊盘相连 为了保证透锡良好,在大面积铜箔上的元件的焊盘要求用隔热带与焊盘相连,对于需通过5A以上大电流的焊盘不能采用隔热焊盘,如图2-1所示:
PCB设计规范模板
P C B 设计规范 目的 A.本规范归定了我司PCB设计的流程和设计原则,主要目的是为PCB设计者提供必须遵循的规则和约定。 B.提高PCB设计质量和设计效率。 C.提高PCB的可生产性、可测试、可维护性 一.PCB 设计的布局规范 (一)布局设计原则 1.距板边距离应大于5mm。 2.先放置与结构关系密切的元件,如接插件、开关、电源插座等。 3.优先摆放电路功能块的核心元件及体积较大的元器件,再以核心元件为中心摆放周围电路元器件。4.功率大的元件摆放在利于散热的位置上,如采用风扇散热,放在空气的主流通道上;若采用传导散热,应放在靠近机箱导槽的位置。 5.质量较大的元器件应避免放在板的中心,应靠近板在机箱中的固定边放置。 6.有高频连线的元件尽可能靠近,以减少高频信号的分布参数和电磁干扰。 7.输入、输出元件尽量远离。 8.带高电压的元器件应尽量放在调试时手不易触及的地方。 9.热敏元件应远离发热元件。 10.可调元件的布局应便于调节。如跳线、可变电容、电位器等。 11.考虑信号流向,合理安排布局,使信号流向尽可能保持一致。 12.布局应均匀、整齐、紧凑。 13.表贴元件布局时应注意焊盘方向尽量取一致,以利于装焊,减少桥连的可能。 14.去耦电容应在电源输入端就近放置。 (二)对布局设计的工艺要求 当开始一个新的PCB 设计时,按照设计的流程我们必须考虑以下的规则: 1.建立一个基本的PCB 的绘制要求与规则(示意如图)
建立基本的PCB 应包含以下信息: 1)PCB 的尺寸、边框和布线区 A.PCB 的尺寸应严格遵守结构的要求。 B.PCB 的板边框(Board Outline)通常用0.15 的线绘制。 C.布线区距离板边缘应大于5mm。 2)PCB 的机械定位孔和用于SMC 的光学定位点。 A.对于PCB 的机械定位孔应遵循以下规则:要求 ■机械定位孔的尺寸要求 PCB 板机械定位孔的尺寸必须是标准的(见下表和图),如有特殊必须通知生产经理,以下单位为mm。 B.机械定位孔的定位 机械定位孔的定位在PCB 对角线位置如图: ■对于普通的PCB,推荐:机械定位孔直径为3mm,机械定位孔圆心与板边缘距离为5mm。 ■对于边缘有元件(物体、连接器等),机械定位孔将在X 方向做移动,机械定位孔的直径推荐3mm。■机械定位孔为非孔化孔。 C.对于PCB 板的SMC 的光学定位点应遵循以下规则: ■ PCB 板的光学定位点 为了满足SMT 的自动化生产处理的需要,必须在PCB 的表层和底层上添 加光学定位点,见下图:
PCB设计规范
PCB设计规范 前言 本规范参考国家标准印制电路板设计和使用等标准编制而成。 一、布局 ●元件在二维、三维空间上不能产生冲突。 ●先放置与结构关系密切的元件,如接插件、开关、电源插座等。对于按键,连接器等与结构相关 的元器件放置好后应锁定,以免在无意之中移动。 ●如果有相同结构电路部分,尽可能采用“对称式”标准布局。 ●元器件的排列要便于调试和维修,小元件周围尽量不放置大元件、需调试的元、器件周围要有足 够的空间。 ●按照“先大后小,先难后易”的布置原则,重要的单元电路、核心元器件应当优先布局。 ●布局应尽量满足以下要求:总的连线尽可能短,关键信号线最短;高电压、大电流信号与小电流, 低电压的弱信号完全分开;模拟信号与数字信号分开;高频信号与低频信号分开;高频元器件的间隔要充分; ●发热元件要一般应均匀分布(如果有散热片还需考虑其所占的位置),且置于下风位置以利于单板 和整机的散热,电解电容离发热元件最少400mil;除温度检测元件以外的温度敏感器件应远离发热量大的元器件。 ●元器件离板边尽量不小于5mm,特殊情况下也应大于板厚。 ●如果PCB用排线连接,控制排线对应的插头插座必须成直线,不交叉、不扭曲。 ●连续的40PIN排针、排插必须隔开2mm以上。 ●考虑信号流向,合理安排布局,使信号流向尽可能保持一致。 ●输入、输出元件尽量远离。 ●电压的元器件应尽量放在调试时手不易触及的地方。 ●驱动芯片应靠近连接器。 ●有高频连线的元件尽可能靠近,以减少高频信号的分布参数和电磁干扰。 ●对于同一功能或模组电路,分立元件靠近芯片放置。 ●连接器根据实际情况必须尽量靠边放置。 ●开关电源尽量靠近输入电源座。 ●BGA等封装的元器件不应放于PCB板正中间等易变形区 ●BGA等阵列器件不能放在底面,PLCC、QFP等器件不宜放在底层。 ●多个电感近距离放置时应相互垂直以消除互感。 ●元件的放置尽量做到模块化并连线最短。 ●在保证电气性能的前提下,尽量按照均匀分布、重心平衡、版面美观的标准优化布局。 ●按电路模块进行布局,实现同一功能的相关电路称为一个模块,电路模块中的元件应采用就近集 中原则,同时数字电路和模拟电路分开; ●定位孔、标准孔等非安装孔周围1.27mm 内不得贴装元、器件,螺钉等安装孔周围3.5mm(对于 M2.5)、4mm(对于M3)内不得贴装元器件; ●卧装电阻、电感(插件)、电解电容等元件的下方避免布过孔,以免波峰焊后过孔与元件壳体短 路; ●元器件的外侧距板边的距离为5mm; ●贴装元件焊盘的外侧与相邻插装元件的外侧距离大于2mm; ●金属壳体元器件和金属件(屏蔽盒等)不能与其它元器件相碰,不能紧贴印制线、焊盘,其间距 应大于2mm。定位孔、紧固件安装孔、椭圆孔及板中其它方孔外侧距板边的尺寸大于3mm; ●发热元件不能紧邻导线和热敏元件;高热器件要均衡分布;
pcb印制板设计规范
pcb印制板设计规范 篇一:PCB 工艺设计规范 规范产品的PCB工艺设计,规定PCB工艺设计的相关参数,使得PCB的设计满足可生产性、可测试性、安规、E(转载于: 小龙文档网:pcb印制板设计规范)MC、EMI 等的技术规范要求,在产品设计过程中构建产品的工艺、技术、质量、成本优势。 本规范适用于所有电了产品的PCB工艺设计,运用于但不限于PCB的设计、PCB投板工艺审查、单板工艺审查等活动。 本规范之前的相关标准、规范的内容如与本规范的规定相抵触的,以本规范为准。 导通孔(via):一种用于内层连接的金属化孔,但其中并不用于插入元件引线或其它增强材料。 盲孔(Blind via):从印制板内仅延展到一个表层的导通孔。埋孔(Buried via):未延伸到印制板表面的一种导通孔。 过孔(Through via):从印制板的一个表层延展到另一个表层的导通孔。
元件孔(Component hole):用于元件端子固定于印制板及导电图形电气联接的孔。 Stand off:表面贴器件的本体底部到引脚底部的垂直距离。 板材,应在文件中注明厚度公差。 机密 XX-7-9 页 1 页 热设计要求 高热器件应考虑放于出风口或利于对流的位置 温度敏感器械件应考虑远离热源 对于自身温升高于30℃的热源,一般要求: 若因为空间的原因不能达到要求距离,则应通过温度测试保证温度敏感器件的温升在降额范围内。 为了保证透锡良好,在大面积铜箔上的元件的焊盘要求用隔热带与焊盘相连,对于需过5A 以上大电流的焊盘不能采用隔热焊盘,如图所示: 焊盘两端走线均匀 或热容量相当 焊盘与铜箔间以”米”字或”十”字形连接