船舶技术规格书常用条款描述汇总
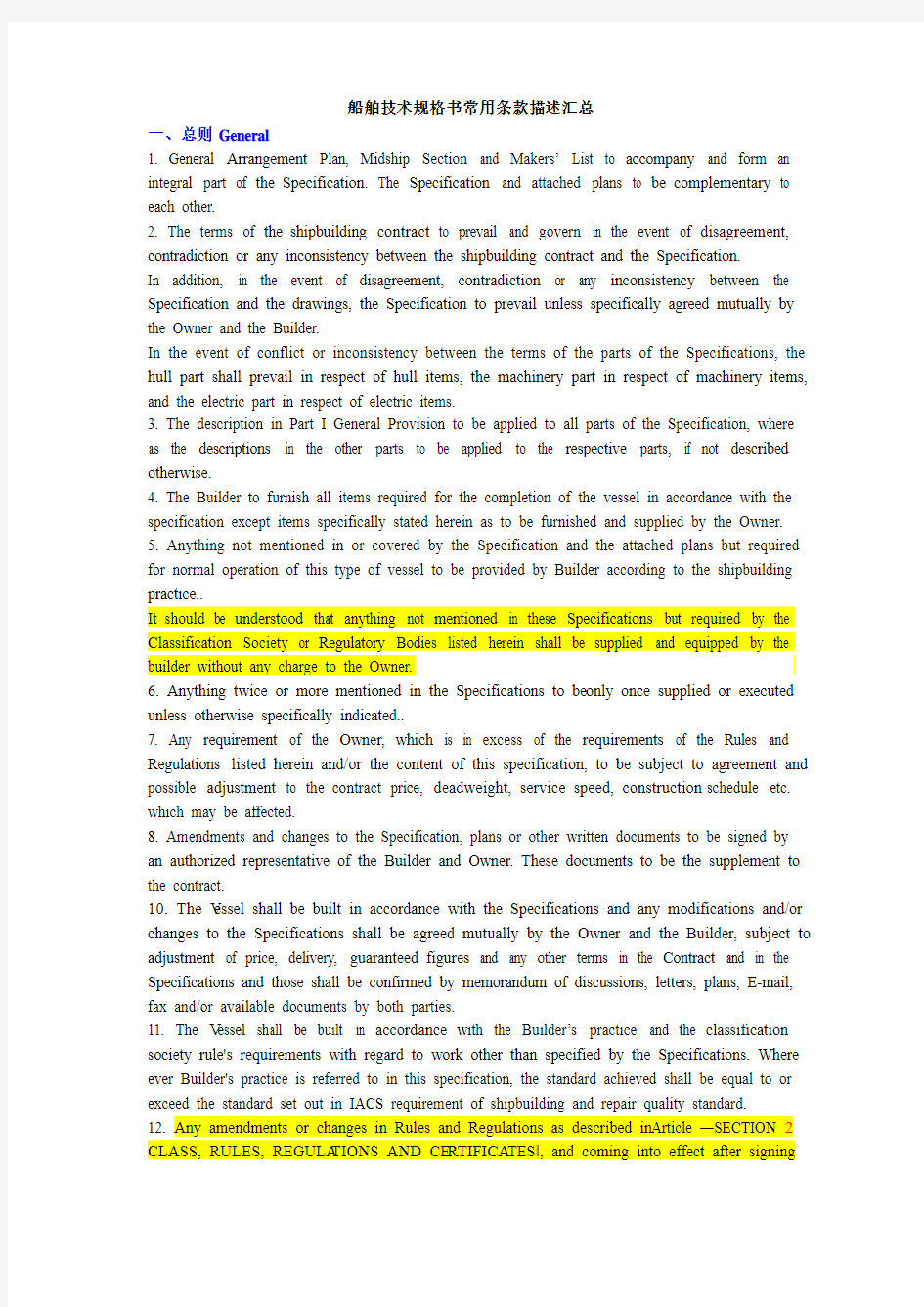
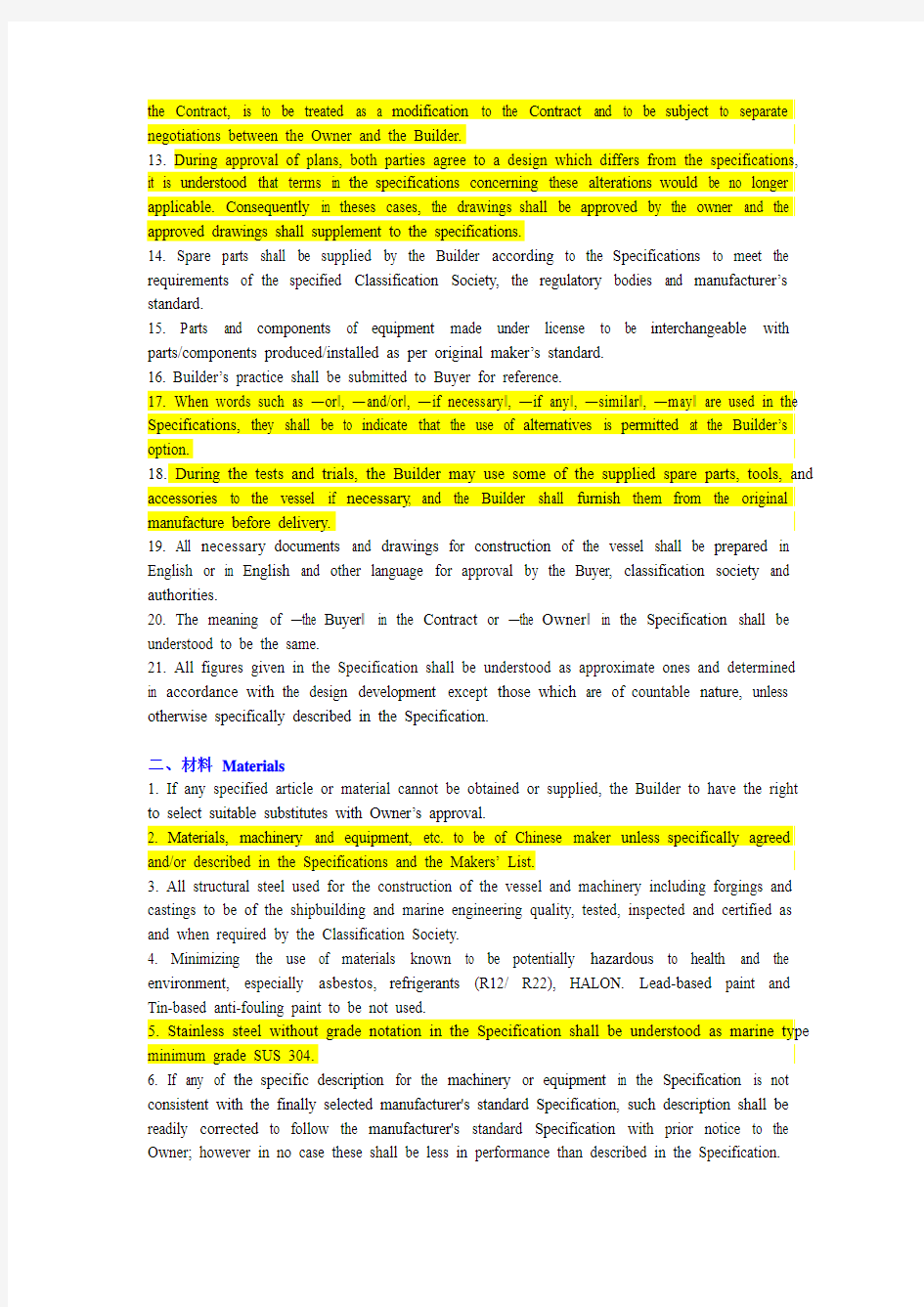
船舶技术规格书常用条款描述汇总
一、总则General
1. General Arrangement Plan, Midship Section and Makers’ List to accompany and form an integral part of the Specification. The Specification and attached plans to be complementary to each other.
2. The terms of the shipbuilding contract to prevail and govern in the event of disagreement, contradiction or any inconsistency between the shipbuilding contract and the Specification.
In addition, in the event of disagreement, contradiction or any inconsistency between the Specification and the drawings, the Specification to prevail unless specifically agreed mutually by the Owner and the Builder.
In the event of conflict or inconsistency between the terms of the parts of the Specifications, the hull part shall prevail in respect of hull items, the machinery part in respect of machinery items, and the electric part in respect of electric items.
3. The description in Part I General Provision to be applied to all parts of the Specification, where as the descriptions in the other parts to be applied to the respective parts, if not described otherwise.
4. The Builder to furnish all items required for the completion of the vessel in accordance with the specification except items specifically stated herein as to be furnished and supplied by the Owner.
5. Anything not mentioned in or covered by the Specification and the attached plans but required for normal operation of this type of vessel to be provided by Builder according to the shipbuilding practice..
It should be understood that anything not mentioned in these Specifications but required by the Classification Society or Regulatory Bodies listed herein shall be supplied and equipped by the builder without any charge to the Owner.
6. Anything twice or more mentioned in the Specifications to be only once supplied or executed unless otherwise specifically indicated..
7. Any requirement of the Owner, which is in excess of the requirements of the Rules and Regulations listed herein and/or the content of this specification, to be subject to agreement and possible adjustment to the contract price, deadweight, service speed, construction schedule etc. which may be affected.
8. Amendments and changes to the Specification, plans or other written documents to be signed by an authorized representative of the Builder and Owner. These documents to be the supplement to the contract.
10. The V essel shall be built in accordance with the Specifications and any modifications and/or changes to the Specifications shall be agreed mutually by the Owner and the Builder, subject to adjustment of price, delivery, guaranteed figures and any other terms in the Contract and in the Specifications and those shall be confirmed by memorandum of discussions, letters, plans, E-mail, fax and/or available documents by both parties.
11. The V essel shall be built in accordance with the Builder’s practice and the classification society rule's requirements with regard to work other than specified by the Specifications. Where ever Builder's practice is referred to in this specification, the standard achieved shall be equal to or exceed the standard set out in IACS requirement of shipbuilding and repair quality standard.
12. Any amendments or changes in Rules and Regulations as described in Article ―SECTION 2 CLASS, RULES, REGULA TIONS AND CE RTIFICA TES‖, and coming into effect after signing
the Contract, is to be treated as a modification to the Contract and to be subject to separate negotiations between the Owner and the Builder.
13. During approval of plans, both parties agree to a design which differs from the specifications, it is understood that terms in the specifications concerning these alterations would be no longer applicable. Consequently in theses cases, the drawings shall be approved by the owner and the approved drawings shall supplement to the specifications.
14. Spare parts shall be supplied by the Builder according to the Specifications to meet the requirements of the specified Classification Society, the regulatory bodies and manufacturer’s standard.
15. Parts and components of equipment made under license to be interchangeable with parts/components produced/installed as per original maker’s standard.
16. Builder’s practice shall be submitted to Buyer for reference.
17. When words such as ―or‖, ―and/or‖, ―if necessary‖, ―if any‖, ―similar‖, ―may‖ are used in the Specifications, they shall be to indicate that the use of alternatives is permitted at the Builder’s option.
18. During the tests and trials, the Builder may use some of the supplied spare parts, tools, and accessories to the vessel if necessary, and the Builder shall furnish them from the original manufacture before delivery.
19. All necessary documents and drawings for construction of the vessel shall be prepared in English or in English and other language for approval by the Buyer, classification society and authorities.
20. The meaning of ―the Buyer‖ in the Contract or ―the Owner‖ in the Specification shall be understood to be the same.
21. All figures given in the Specification shall be understood as approximate ones and determined in accordance with the design development except those which are of countable nature, unless otherwise specifically described in the Specification.
二、材料Materials
1. If any specified article or material cannot be obtained or supplied, the Builder to have the right to select suitable substitutes with Owner’s approval.
2. Materials, machinery and equipment, etc. to be of Chinese maker unless specifically agreed and/or described in the Specifications and the Makers’ List.
3. All structural steel used for the construction of the vessel and machinery including forgings and castings to be of the shipbuilding and marine engineering quality, tested, inspected and certified as and when required by the Classification Society.
4. Minimizing the use of materials known to be potentially hazardous to health and the environment, especially asbestos, refrigerants (R12/ R22), HALON. Lead-based paint and Tin-based anti-fouling paint to be not used.
5. Stainless steel without grade notation in the Specification shall be understood as marine type minimum grade SUS 304.
6. If any of the specific description for the machinery or equipment in the Specification is not consistent with the finally selected manufacturer's standard Specification, such description shall be readily corrected to follow the manufacturer's standard Specification with prior notice to the Owner; however in no case these shall be less in performance than described in the Specification.
7. New, first class materials etc. shall be used, with a quality suitable for this type and size of V essel, adapted to world-wide operation.
三、工艺及标准Workmanship & Standards
1. All workmanship entering into the construction of the vessel to be in accordance with the Chinese ship building standards and/or Builder's standard practice, applicable to this kind of vessel, subject to the approval of the Classification Society where necessary. The standards of Builder's practice to be submitted to the Owner for reference.
2. The following standards to be applied to the construction of the vessel, as far as practicable except the fittings specially described hereinafter.
a) ISO standard
b) Chinese industrial standards (GB, CSQS, CB, YB, etc.)
c) Builder's standards, and Builder's standard practice
d) IEC
e) IACS 47, part A: shipbuilding and repair quality standard for new construciton
3. International System of Units (SI) to be adopted for designing and constructing of hull, machinery and equipment unless specifically stated in this Specification.
四、船东供品(Owner’s supply)
1. Following items to be furnished and supplied by the Owner at their own expense, and installed on the vessel by the Builder. The Builder to provide sheltered and secure storage, handling in storage and handling on-board.
- Mooring ropes in excess of the Specification
- All air tools, hoses, steel wires, etc. other than those mentioned in the Specification
- All charts, nautical and radio station books, house flag and national flag
- All consumable stores
- All medicine , medical equipment and oxygen bottle for hospital except those for life boat
- Recreation equipment such as Stereophony, V ideo tape recorder and TV etc and stationery other than mentioned in the Specification
- Painting and pictures
- Boatswain's and carpente r's tools over and above the Builder’s standard
- All bedding and linen (blankets, sheets, covers, etc.) but excluding mattress.
- All napery (serviettes, table clothes, etc.)
- All cook's and steward's utensils (crockery, cutlery, silverware, earthenware, glasses, pots, pans, etc.
- Typewriters, copy machine
- Loose lashing/securing fittings for cargoes
- Suez Canal searchlight, but socket and davit to be supplied by builder
- Navigation equipment in excess of those required by the authorities and/or those specified in this Specification
- Cargo handling equipment such as grabs (including the control devices) etc.
- Personal computer
- All bunkers, lubricants, grease/hydraulic oil, working oil and other consumable liquid except those consumed during construction and test/trials before delivery. The Owner to supply lub. oil
for sea trials and the Builder to pay the cost for the quantities of lub. oil consumed during the trials.
- All other spare, store and equipment in excess of Rule and Specification requirements and maker's standard, unless maker agrees to supply additional spares free of charge after agreement with Owner/Builder.
- Gas sampling device and temperature measuring device for cargo hold
- Gymnastic and Sport apparatus/equipment, except specified in other parts of this specification
- Chemistry deposit
- The hazardous gas detection equipment and personal protection for carriage of dangerous cargo. - Portable wash cleaning machine for cargo hold
- Garbage cans
- Necessary number of operating tools for helicopter winching if required
- Cable for shore connection
- Fire ropes for Suez Canal
- Articles specified as "Owner's supply" in other parts of this specification
- Lifting Beams 对多用途船
2. The Owner shall furnish the Builder with necessary specifications, plans, drawings, instruction books, manuals, test reports, certificates, the manufacturer's service engineer(s), etc. as required by the Builder, which shall form an integral part of the Owner?s supplies.
3. Commissioning for good working order of the Owner?s supplied equipment during and after installation on board shall be carried out by the Owner or person(s) designated by the Owner in accordance with the construction schedule of the V essel.
The expenses related with commissioning shall be the Owner?s account.
4. All Owner's supplies to be sent to the Builder?s shipyard by Owner at Owner?s costs at the time designated by the Builder in a condition ready for installation costs such as transportation, customs inspection fees, etc. shall be borne by the Owner.
五、规范及规则Rules and Regulations
1. The latest Rules with amendments and Regulations listed as following including any circular, amendments which are in force before and at the date of the signing of the ship’s contract shall be applied.
2. The rules and requirements shall be understood to include all amendments, supplements and changes thereto which shall have been published by the date of contract for construction of the vessel and which shall have become compulsorily applicable to the vessel by reason of the date of contract.
1) Rules and Regulations of Classification Society
2) Maritime laws and regulations of flag authority
3) International rules and regulations
- International Convention on Load Lines (1966) including all and latest amendments
- International Convention for the Safety of Life at Sea (SOLAS 1974) including all and latest amendments
- International Convention for the Prevention of Pollution from Ships 1973 (MARPOL 1973) with protocol 1978 and all amendments, including Annexes I, IV, V, VI,and including IMO
Resolution MEPC.203(62) regulation on EEDI and SEEMP.
- International Regulations for Preventing Collisions at Sea (London 1972) including latest revision
- International Tele-communication convention with amendments including watch keeping receiver (Geneva 1976) and radio regulation
- International Regulation on Tonnage Measurement of ships, 1969
- MLC Maritime Labour Convention, 2006 , Regulation 3.1 mandatory requirements
- 2008 IS Code – International Code on Intact Stability, 2008
- IMO Resolution MSC. 23 (59) (International Grain Code)
- IMO Resolution MSC. 137 (76) ―Standards for Ship Maneuverability ―
- IMO Resolution MSC. 215 (82) (PSPC)
- IMO Resolution A. 868 (20) ―Guidelines for the control and management of ships’ ballast wa ter to minimize the transfer of harmful aquatic organisms and pathogens ―
- IMSBC Code – International Maritime Solid Bulk Cargoes Code 散货船
- All IACS Unified Requirements for strength applicable to New Building of Bulk Carrier which has been formal published at the date of signing contract including UR S1A, S21, S24, S25, S26, S27, S28, etc. (散货船)
- SOLAS resolution II-1/3-6 regarding PMA. (散货船)
- International marine pilots association requirements for pilot ladder
- Guidelines for Construction, Installation, Maintenance and Inspection/ Survey of Means of Embarkation and Disembarkation, MSC.1/ Circ.1331.
- IMO resolution A468 (XII) code of noise level on board ships
- ISO 6954 guidelines for vibrations on board ships
- AFS - International Convention on the Control of Harmful Anti-Fouling Systems on Ships, 2001
- ISPS code only fixed equipment
- Hong Kong International Convention for the Safe and Environmentally Sound Recycling of Ships, 2009.(未生效)
4) Special rules and regulations
- Rules and Regulations governing navigation of Suez Canal, including tonnage measurement - Rules and Regulation governing navigation of the Panama Canal including tonnage measurement
- U.S. Coast Guard Regulations applying to foreign flag vessel trading in U.S. waters concerning pollution prevention (CFR Title 33-Part 155, 159 for pollution and 164 for safety of navigation without certificate)
- Australian Maritime Safety Authority MARINE ORDERS Part 32 ―Cargo Handl ing Equipment‖ prepared on 29 November 2011 (for ladders in cargo hold/deck)
- European Union Council directive 2005/33/EC amending 1999/32/EC of 26 April 1999 and, in relating to introduce 0.1% sulfur limit for marine fuel.
- U.S. Department of Labor Occupational Safety and Health Administration (OSHA) rules, Safety and Health Regulations for Longshoring (espec. CFR, Title 29) (集装箱船)
- Kiel Canal Regulations
- Great Lakes & St. Lawrence Seaway Regulations
- Marine Equipment Directive (MED) 2011/75/EU of 2 September 2011, amending Council
Directive 96/98/EC on marine equipment
六、证书Cerfificates
1. The Builder to obtain following certificates and deliver to the Owner at the time of V essel's delivery. Each certificate to be delivered in triplicate, one (1) as original and two (2) as counterparts at delivery of the V essel.
2. However if formal certificate(s) cannot be obtained at the ship’s delivery, Builder to furnish provisional certificate(s) to the Owner which substitutes the formal certificate(s). In such case, Builder to deliver formal c ertificate(s) to Owner as soon as practicable after the ship’s delivery, but in any case prior to the expiration of the validity of the provisional certificate(s).
七、监造、检验、试验及试航Supervision,Inspections, T ests and T rials
1. Tests and trials to be carried out in accordance with the requirement of the classification society and according to the Builder's usual standard practice in the presence of the surveyor of the Classification Society and the Owner's and the Builder's representatives.
The Owner has the right to appoint one or more Supervisors for the supervision during construction and execution of works in accordance with the Shipbuilding Contract. During the building period, the Builder shall allow Owner's Supervisor to enter the yard during working hours for the purpose of supervision and the Builder also shall negotiate with his sub-Contractors that the Supervisor may attend during construction and testing of major equipment at subContractors' sites.
The supervisor to have access to all places and offices which are related to the design and construction of the V essel.
The Builder shall give necessary information such as schedule of building, tests and working drawings as well as assistance including two suitably furnished offices with writing desks, chairs, refrigerators, heaters and air conditioning, lamps, cupboards, shelves and including internal telephone and a direct international telephone line with fax- and e-mail connection to enable Owner's representatives to effect the supervision. The costs for telecommunication will be to Owner?s account.
2. The Builder will inform the supervision about the building schedules, test and working drawings. Schedules for daily inspections will be handed over to the supervision one day in advance except the inspection for painting work in emergency condition. Information about tests of equipment (date and program) will be handed over to the supervision three days before tests will take place. If the Owner can not attend inspections for reasons of their own after being given reasonable notice, the inspection and test would be entrusted to surveyor of the Classification Society and/ or the Builder’s inspector or the paint manufacturer or the equipment maker’s representative, and the results to be accepted by the Owner.
3. Inspection of hull structure
All steel structures to be inspected and tightness to be tested for tanks, bulkheads, superstructures, decks and other wet spaces as required by the Rules.
Tanks to be tested hydrostatically or by air as required by the Rules.
X-ray photographs or ultrasonic to be taken mainly from cross-points of seams and butts of block assemblies of bottom shell, bilge strake, main deck and sheer strake as required by the Rule. Additional 10% X-ray photographs to be appointed and checked by the Owner’s supervisor. Castings of stern frame and rudder to be tested by magnaflux or equivalent.
Temporary pieces such as staging pieces, lifting lugs and their reinforcements located in the fatigue sensitive area, high stressed area or passage way shall be treated without leaving notches according to the Builder?s practice. However those pieces considered not inconvenient for the future service may remain as the Builder?s practice.
4. Block inspection
The block inspection to be carried out after completion of hull block steel works. Even if fittings are fitted wholly or partially to the hull blocks, the inspection for the hull blocks to be carried out without dismantling such fittings unless the block inspection is obstructed by such fittings.
The internal inspection for hull construction works of tanks, engine room, etc. to be carried out even if outfitting works in such spaces have not been finished yet but any works in connection with strength and tightness of the hull construction to be completed before the said inspection, in which case, after completion of the outfitting works, final inspection of such parts to be made in accordance with the ―Item of inspection and testing― mutually agreed between the Owner and the Builder.
5. Shop tests
Shop tests for main engine, auxiliary machinery, deck machinery, motors etc. to be performed in accordance with the Rule requirements and/or the standard of the makers by the manufacturers at their shops.
Test results of major machinery and equipment shall be furnished to the Owner in triplicate.
The Owner shall be informed of the shop test schedule at least fourteen(14) days for foreign Maker (outside China) and seven(7) days for domestic Maker in advance of the expected date of the shop tests and the Owner's attendance shall be confirmed to the Builder four(4) days in advance of the expected date of the shop test.
The Owner’s representatives will join the shop tests of main equipment. The travel cost and hotel cost outside China for Owner’s representatives will be born by Owner.
6. Installation and equipment
Installation and equipment to be tested on board the vessel in accordance with the requirements of the Classification Society and/or Regulatory Bodies and the standard protocol of the Builder. Test protocol to be approved by the Owner.
The structure, fittings, machinery and electrical installations to be tested after installation on board to demonstrate satisfactory workmanship, proper working, alignment of moving parts, suitability for the purpose intended and in compliance with rules and regulations.
7. Piping tests
Working tests to be carried out after completion of the piping system. Pressure tests of piping systems to be conducted as per requirement of the Classification Society and normal shipbuilding practice.
8. Light Ship weight measurement and Inclining test
When the vessel is substantially completed except minor items of work, inclining test or deadweight measurement of the vessel to be carried out by the Builder near the pier. The inclining
test scheme to be submitted to the Owner for approval. The inclining test to be conducted in calm water without strong current and strong winds.
The light ship weight measurement to be carried out by reading the draught of the vessel, by measuring specific gravity of water and by an investigation of weights to be added or to be deducted in the presence of the Owner’s representatives or the person authorized by the Owner. The draught of the vessel to be measured at both sides of stem, stern and midship draught marks. Displacement of the vessel to be measured from the hydrostatic curves. All measurements and correction to be made as per international standard.
If any superfluous weight is on board the vessel or any item belonging to the light ship weight is not on board the vessel at the time of the light ship weight measurement, such a weight to be adjusted later.
The calculation of the light ship weight and deadweight to be made by the Builder and verified by the Owner’s and Classification representatives in order to determine ―light ship weight― and ―deadweight―.
The incl ining test to be carried out in the presence of the Owner’s representatives or the person authorized by the Owner and the Classification Society’s surveyor, and then the position of the centre of gravity of the vessel in lightship condition to be determined by the calculation based on the results of the inclining experiment.
The results of the experiment shall be submitted to the Classification Society or other assigned Authority for approval.
The inclining test to be done for first ship of the series only.
For subsequent V essels of a series, the inclining experiment may be deleted in agreement with the Classification Society. In this case, the results of the first V essel shall be referred to.
9. Mooring trials
Mooring tests to be conducted after vessel is substantially complete and prior to the sea trial. Procedure for mooring test of the vessel to be as per Builder’s standard.
After the mooring trial of main engine the crankcase shall be inspected and crankshaft deflection measured. All main bearing top/bottom clearance shall be checked and all records to be submitted to Owner’s representative.
10. Sea T rials
When the vessel is substantially completed, i.e. major mooring trials finished except minor items which can be carried out on or after sea trial, defects remedied, all equipment and outfitting in sailing condition and painting work almost completed, sea trial to be performed by the Builder.
Only HFO and MDO will be used during sea trial.
Main engine to use heavy fuel oil abt. 380 cSt/50℃during sea trial except otherwise specified. All H.F.O., D.O., L.O. for commissioning and testing and L.O. in system to be paid by yard.
Detailed scheme for sea trials to be submitted to the Owner for approval at least two weeks prior to sea trials.
Reports of sea trial to be submitted to the Owner.
Sea trial to be carried out under calm and deep water with ship’s normal sea going ballast condition as that in model test.
1)The trial speed to be measured by DGPS. Each speed trial to consist of two c onsecutive runs,
along and against the tide over the same course and the speed to be obtained as the mean speed of the consecutive runs at each condition.
The wind shall not exceed Beaufort 4.
The water depth shall be at least 40m.
Result of speed trial shall be corrected to the calm water condition ( no wind, no wave ) and deep sea according to Builder’s standard.( international standards.)
2)Noise levels to be measured by the Builder at suitable points in the above spaces agreed with
the Owner when the ship is running ahead at normal output on the calm and deep open sea trial condition.
Where the measured noise levels exceed by more than 3dB(A) above the specified maximum limits, the Builder shall make necessary improvements to reduce the noise to the specified level as mutually agree between Owner and Builder.
3)After sea trial, working parts of main engine to be opened for the Owner's inspection in
accordance with the standard of the Builder and approved by Owner and refitted to working condition.
A/E also to be opened for visual overhaul if necessary.
4)In case of the series V essels, the following trials and measurements shall not be conducted on
the 2nd and following V essels, subject to Owner and Classification Society agreement:
-Progressive speed trial except for assessment of guarantee speed point
-Manoeuvring trials.
-Shaft torsional and axial vibration measurement.
-Hull vibration measurement.
-Noise measurement.
-Electrical load measurement.
八、进坞及交船Dry docking , Delivery
1. Before the delivery, If the period between launching and delivery is more than 6 months, the vessel to be subjected to the dry docking. Hull bottom cleaning and final painting to be carried out.
2. At the delivery, the vessel to be complete in every respect, ready for service as specified, with the exception of the fuel oil, lubricating oil, water, store, provisions, crew and their effects, and such items of outfit and equipment as are herein exempted in this Specification.
The Builder shall guarantee the V essel other than those supplied by the Buyer for a period of twelve(12) calendar months from delivery.
九、图纸及文件Plans and documents
1. The lists of the drawings for the Owner's approval and the final drawings to be submitted to the Owner for approval after the contract of the vessel.
2. The Builder to submit four (4) copies of the plans to the Owner for approval, and two (2) copies
to be returned to the Builder with the Owner's signature of approval.
3. If the Builder does not receive the Owner's reply to the plans within twelve (12) working days excluding mailing time, they to be regarded as approved by the Owner without any comments.
When the Owner finds it impossible to return the plans within the specified period, the Owner shall inform the Builder / Designer without delay and they shall discuss on the matter. In any event, any extension shall not delay the construction schedule of the vessel.
The Owner can send his comments to Builder by Email prior to dispatching the hard copies.
4. The Builder to give answer for Owner's comments within 14 days from the date of receiving. If the Builder fails to answer, the Owner to deem that the comments have been automatically accepted.
5. In the event that any of the already approved plans for the first vessel are same as those for the subsequent sister vessels, the Builder may leave out the submission of such plans for the subsequent vessels. In which case the plan to clearly state the name/yard number of vessels.
6. The Builder to furnish four (4) copies of the final drawings and the instruction books of the major machinery and equipment to the Owner at the delivery of the vessel. One (1) CD-ROM with all available finished plans and documents to be provided to the Owner.
7. The plans which have to be approved by the Classification Society to be submitted to the Society directly by the Builder or the Subcontractors.
8. Basically, the major drawings shall be submitted to the Owner?s head office according to the ―List of the Plans for Owner?s Approval‖. However, for the effective produc tion progress during the construction of the V essel, the Builder may submit to the Owner?s representative resident in the shipyard for the minor changed items.
9. All the approval plans shall be written in English or English and other languages.
10. One copy of the approval drawings and comments by classification society will be submitted to the Owner.
11. The Fax or E-mail may be used for technical communication between the Buyer and the Builder (including the builder’s subcontractors), in any case the rec eiver should reply the sender within fourteen (14) calendar days from the date of receiving. Any future communications concern to the same item should be replied within three (3) calendar days after receipt the other side’s comments. If the receiver fails to answer, the sender will deem that the sender’s latest comments have been automatically accepted.
十、油漆及阴极保护Painting and cathodic protection
1. The surface preparation grades to be as per ISO or Swedish standards SIS.
2. The detail inspection procedure including surface preparation and coating processes for dedicated seawater ballast tanks according to IACS PSPC shall be agreed upon between the Owner, Builder and paint maker (hereinafter referred to as ―the three paties’ agreement‖) at the signing of contract.
3. Painting scheme to be submitted to Owner for approval, colors of finish paint to be as per Owner’s color scheme.
4. Copper, copper alloy, aluminum alloy and stainless steel or other non-corrosive materials shall
not to be painted in general unless otherwise specified.
5. Hot galvanized pipes shall not to be painted in general unless otherwise specified. During sand blasting and painting work the gal. pipes shall be properly protected.
6. The surface in contact with doubling plates and internal surfaces of tightly enclosed spaces shall not be painted unless otherwise specified subject to paint maker’s recommendation.
7. Steel outfitting manufactured by sub-contractors to be coated as per specification or with equivalent type of paint compatible with the adjacent structure's coating system for ease of subsequent maintenance.
8. Time schedule for painting of each coat to be decided according to the Builders construction schedule but to be governed by re-coating intervals recommended by the paint maker.
9. Painting for the parts or spaces not specially specified to be similar to the surrounding space or comparable space.
10. Coating of machinery, electrical equipment, outfitting, valves, navigation equipment, deck machinery, furniture etc. to be done acc ording to makers’ standard unless otherwise specified. When paint damage occurs before or after installation on board the damaged parts to be repaired with equivalent paint to original and in case of extensive damage a full coat to be applied after repairs.
11. All sharp edges, edge of small holes, such as slots, scallops, drain holes etc. and flame cut free edges of structural steel to be grounded smooth. R2 or three pass grinding for PSPC area.
12. Generally the hull structural and sections of 6 mm thickness and above to be shot blast cleaned on both sides to ISO or SIS SA 2.5. Grit or sand blasting to ISO or SIS SA 2.5 or pickling may be applied instead of shot blasting when shot blasting is considered impractical. The hull structural steel below 6 mm, if any, to be treated by pickling or power tool cleaning in according to paint maker’s recommendation.
13. Just after primary surface preparation one coat of 15 microns zinc silicate or epoxy zinc type shop primer to be applied. The shop primer to have good compatibility with the succeeding coats. Different color shop primer to be used for mild and high tensile steel plates and sections.
14. Before the first coat is applied, the damages on shop primer by welding, burning, rubbing, etc., and the rusted steel surface to be prepared in accordance with the following table.
Before the first coat is applied, wire-brush to be used for non-damages on the shop primed area. The secondary surface preparation for F.O., D.O. tanks etc. to be cleaned and oil wiped as per the Builder’s practice.
After erection, the damaged areas and re-rust welding seams etc will be power tooling to ST3 for
epoxy paint and ST2 for other areas.
15. The painting to be carried out by airless spray, in general. Where the spraying is impractical, the brush or roller to be used.
16. The painting scheme specified hereunder may have alteration in number of coats and the dry film thickness in accordance with standard specification of the selected paint maker.
17. In the edges of small holes such as slots, scallops, drain holes, etc. and corners of flame burnt free edge of structural members, the dry film thickness may not always be specified. Stripe coats shall be applied according to the maker’s recommendation and the Builder’s practice.
18. After the specified coating is applied, the damages in paint film to be repaired at proper time. When the damage reaches the steel surface and rust occurs, the surface to be cleaned by the wire brush and/or disc sander and to be coated as originally specified.
When the damage does not reach the steel surface, the surface to be touched up to the specified film thickness.
19. The steel structure surfaces including all welded beads to be painted before the leak test, in general. However, fillet welding joint and erection butt joint forming tank boundary to be painted after joint has been examined either by compressed air test, vacuum test or tank air test as appropriate, but the shop primer can be applied to the fillet welding joint and erection butt joint before the leak test.
20. Pre-erection joint of hull block which is erected at any location, to be painted before leak test and not to be considered as block erection joint.
21. The adhesive tape may be used to protect the fillet joint and erection butt joint waiting for leak test from contamination by surrounding painting.
22. The dry film thickness to be measured after each coat to confirm adequate thickness. Under water hull paint thickness to be checked before and after application of anti-fouling paint and recorded. The number of points of thickness measurement to be adequate to get a fair idea of the paint thickness on covered areas.
23. The dry film thickness specified in the painting schedule to be attained on at least 90% of the measuring points and may nor be achieved on the remaining 10% measuring points, but at least 90% thickness of the specified one to be attained on remaining 10% measuring points.
24. No measurement of dry film thickness shall be made for machinery, equipment, outfittings, pipes, pipe supports, machinery seats, small fittings, area within 30mm from free edges, slots, scallops, drain holes, air holes and manual welding beads.
25. Self-polishing paint under waterline and paint of ballast tanks to have five (5) years guarantee.
26. Painting works shall not performed in the open air during the periods of rain, snow, fog or mist and also shall not be carried out when the weather conditions may cause condensation i.e., when the relative humidity exceeds 85%, or steel temperature is not higher than the dew point by 3℃. 27. When blasting in proximity of galvanized items, the damaged parts of galvanized surface shall be touched up with zinc rich primer.
28. No mixing and stirring of paint by hand. Only power mixer shall be used.
29. Prior to installation of pipes, equipment, the foundation and pipes/ equipment in way of contact surface shall be painted with complete paint system.
30. The measured DFT shall not exceed the maximum dry film thickness defined by the paint manufacturer.
31. Application at low temperature only upon recommendation of paint manufacture.
32. For the inside surface of the diesel oil tanks, fuel oil tanks, and other oil tanks, the shop primer not to be removed.
十一、临时开孔及临时构件T emporary openings & temporary pieces
1. Temporary openings for the convenience of access, communication or ventilation for workers during the construction shall be provided on the shell, bulkheads or other necessary places in accordance with the Builder?s practices, and the holes shall be closed by insert plates after completion of the work. Non-destructive examinations shall be carried out to the weld joints of the insert plates. Preparation and painting of the inserts shall be according Builder?s practice but shall meet the coatings specification for that area.
2. Lifting lugs, staging pieces or other temporary pieces fitted to the hull structures for construction shall be removed to about 10mm from the base plate and grinded smooth.
In critical and highly stressed areas, lifting lugs shall be removed and ground smooth in accordance with the Builder?s standards.