镍冶炼工艺摘抄
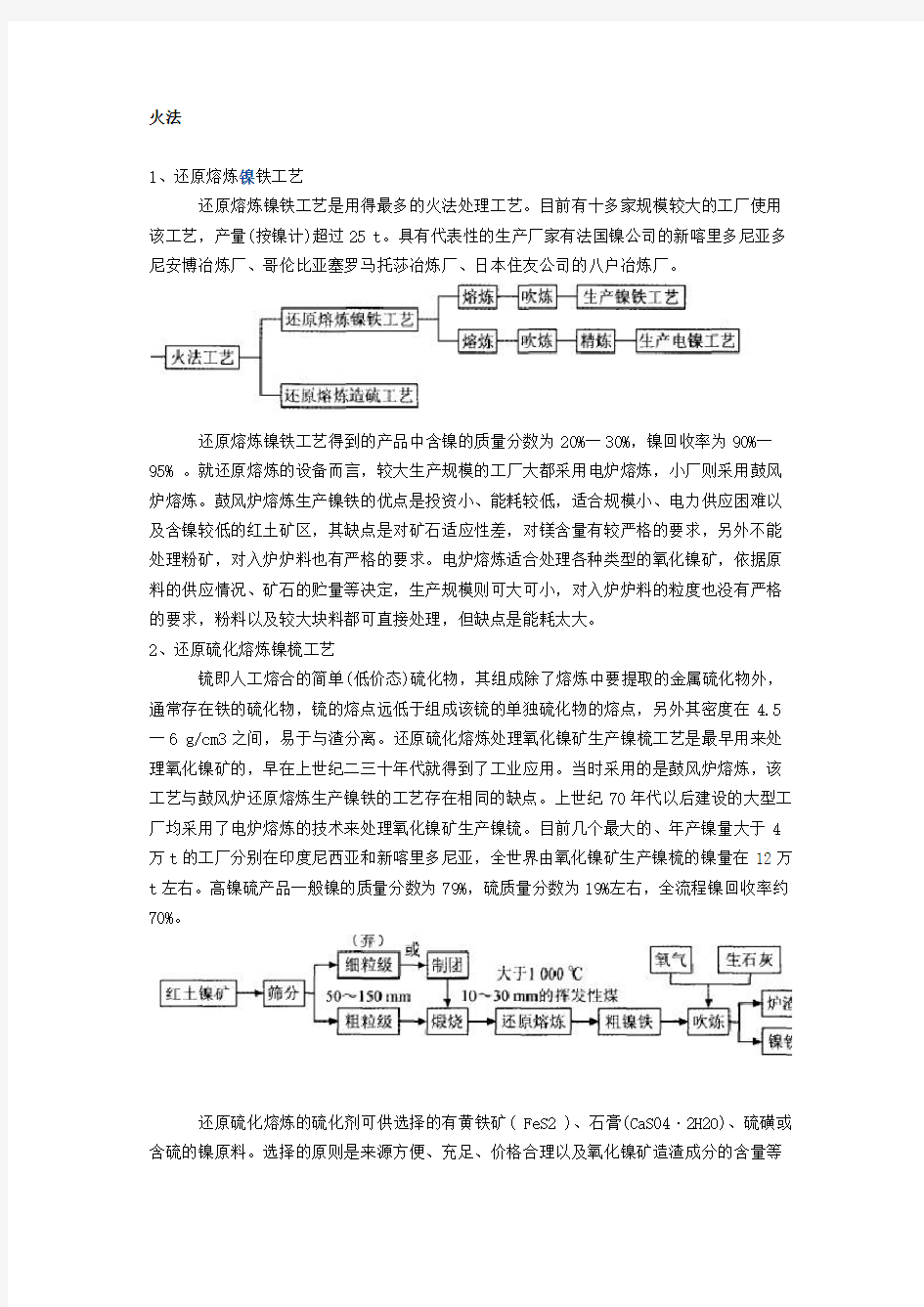

火法
1、还原熔炼镍铁工艺
还原熔炼镍铁工艺是用得最多的火法处理工艺。目前有十多家规模较大的工厂使用该工艺,产量(按镍计)超过25 t。具有代表性的生产厂家有法国镍公司的新喀里多尼亚多尼安博冶炼厂、哥伦比亚塞罗马托莎冶炼厂、日本住友公司的八户冶炼厂。
还原熔炼镍铁工艺得到的产品中含镍的质量分数为20%一30%,镍回收率为90%一95% 。就还原熔炼的设备而言,较大生产规模的工厂大都采用电炉熔炼,小厂则采用鼓风炉熔炼。鼓风炉熔炼生产镍铁的优点是投资小、能耗较低,适合规模小、电力供应困难以及含镍较低的红土矿区,其缺点是对矿石适应性差,对镁含量有较严格的要求,另外不能处理粉矿,对入炉炉料也有严格的要求。电炉熔炼适合处理各种类型的氧化镍矿,依据原料的供应情况、矿石的贮量等决定,生产规模则可大可小,对入炉炉料的粒度也没有严格的要求,粉料以及较大块料都可直接处理,但缺点是能耗太大。
2、还原硫化熔炼镍梳工艺
锍即人工熔合的简单(低价态)硫化物,其组成除了熔炼中要提取的金属硫化物外,通常存在铁的硫化物,锍的熔点远低于组成该锍的单独硫化物的熔点,另外其密度在4.5一6 g/cm3之间,易于与渣分离。还原硫化熔炼处理氧化镍矿生产镍梳工艺是最早用来处理氧化镍矿的,早在上世纪二三十年代就得到了工业应用。当时采用的是鼓风炉熔炼,该工艺与鼓风炉还原熔炼生产镍铁的工艺存在相同的缺点。上世纪70年代以后建设的大型工厂均采用了电炉熔炼的技术来处理氧化镍矿生产镍锍。目前几个最大的、年产镍量大于4万t的工厂分别在印度尼西亚和新喀里多尼亚,全世界由氧化镍矿生产镍梳的镍量在12万t左右。高镍硫产品一般镍的质量分数为79%,硫质量分数为19%左右,全流程镍回收率约70%。
还原硫化熔炼的硫化剂可供选择的有黄铁矿( FeS2 )、石膏(CaS04·2H2O)、硫磺或含硫的镍原料。选择的原则是来源方便、充足、价格合理以及氧化镍矿造渣成分的含量等因素。采用硫磺作硫化剂的优点是简单易行,而且对熔炼过程不产生负面影响(即不影响渣成
分、处理能力,不增加电耗),但价格较贵,硫的有效利用率不高,而且还需要有一套硫磺熔化和输送喷洒的设施。国际镍公司(INCO)所属的印度尼西亚、新喀里多尼亚的工厂均采用硫磺作硫化剂。将硫磺熔化后,有控制地喷洒在回转窑焙烧的处于一定温度下的焙砂上,使铁、镍转化为硫化物,而后送人电炉熔炼生产高镍锍。
还原硫化熔炼镍锍工艺的产品—高镍锍,具有很大的灵活性:经焙烧脱硫后的氧化镍可直接还原熔炼生产用于不锈钢的通用镍;也可以作为常压拨基法精炼镍的原料生产镍丸和镍粉;由于高镍锍中不含铜,还可以直接铸成阳极板送硫化镍电解精炼的工厂生产阴极镍。
火法工艺能耗高,金属综合回收效果差,为保证矿石处理的经济性,通常要求矿石达到一定品位;所以,在开始熔炼前,首先需对风化程度低、品位较低的矿石筛除;但是,火法工艺适合处理硅镁镍类型矿(即矿床下部硅、镁的含量比较高、铁含量较低、钻含量也较低的矿石)。
湿法
1、氨浸工艺
湿法工艺处理氧化镍矿的工业始于20世纪40年代,最早采用的就是氨浸工艺,又称为Canon工艺,其代表性的工厂是美国建设的古巴尼加罗镍厂。氧化镍矿经干燥、还原焙烧后得到的焙砂进行多段常压氨浸,还原焙烧的目的是使硅酸镍和氧化镍最大限度地被还原成金属,镍、钴及部分铁被浸出进人液相,与氨不溶性脉石分离。
金属铁呈铁氨络合物进人溶液后再氧化成Fe3+,水解生成氢氧化铁沉淀,氢氧化铁沉淀时会造成较大的钴损失。
氨浸液通过蒸氨得到碱式碳酸镍,然后煅烧得到NiO。 NiO可以作为产品出售,也可以加氢还原得到金属Ni。钴从蒸氨尾液中用H2S沉淀得到硫化钴。尹飞等人采用选择性还原焙烧-氨浸工艺,从低品位红土镍矿中综合提取镍、钴、铁,得到了最佳的氨浸工艺条件为:NH3/CO2为90:60,焙砂粒度为0.074 mm,占80%,液固比L/S为2,浸出温度为25℃,浸出终点电位大于-100 mV,镍、钴浸出率分别为89.9%和62.2%,浸出剂可以循环使用。
20世纪80年代末年澳大利亚昆士兰镍公司(QNI)的雅布鲁厂(Yabula)对传统的还原焙烧-氨浸工艺作了很大的改进,主要是氨浸液采用了Lix84-1萃取,反萃得到的硫酸镍溶液电积即可以得到高质量的阴极镍,而钴存在于萃余液中,用硫化物沉淀可得到硫化钴。1997
年以前该厂出售硫化钻,现在已经建了钴精炼厂,生产能力为5.5万t/a镍和2000t/a钴。
还原焙烧-氨浸工艺处理氧化镍矿,其产品可以是镍盐、烧结镍、镍粉、镍块等。氨浸法处理工艺不适合处理含铜和含钴高的氧化镍矿以及硅镁镍型的氧化镍矿,只适合于处理表层的红土矿,极大地限制了氨浸工艺的发展。此外,氨浸工艺镍、钴回收率偏低,全流程镍回收率仅为75%-80%,钴约40%-50%。到目前为止,世界上只有4家工厂采用氨浸法处理氧化镍矿,而且都是在上世纪70年代以前建设的,三十多年来没有一家新建工厂采用氨浸工艺。
2、高压酸浸工艺
高压酸浸工艺(High pressure acid leaching,又称HPAL工艺)适合于处理低镁(铝)高铁类型的红土镍矿,于上世纪的50年代得到了工业应用,代表性的工厂是古巴毛阿(Moa)镍冶炼厂。在250~270℃、4~5 MPa的高温高压条件下,用硫酸将镍、钴等有价金属和铁、铝矿物一起溶解,在随后的反应中,控制一定的pH值等条件,使铁、铝和硅等杂质元素水解进人渣中,镍、钴选择性进人溶液,达到与大部份脉石分离的目的,然后通过净化、除杂、分离等工序,即可得到镍、钴产品。
加拿大鹰桥公司(Falconbridge)用高压酸浸工艺生产镍钴混合硫化物,作为该公司在挪威的精炼厂处理的原料。
上世纪末澳大利亚建立了3个采用HPAL工艺处理镍红土矿的工厂(Cawse, Bulong, Murrin Mur-rin ),近年来已开始盈利。尽管它们前面均采用高压酸浸,但后半部流程有所不同。考斯镍厂生产氢氧化镍中间产品,然后再电解得到金属阴极镍和硫化钴。布隆厂的流程则不经过氢氧化镍中间产品的过程,直接电解生产金属镍和钴。莫林莫林则与古巴Moy Bay镍厂现场流程相近,并沿用加拿大Sherritt技术,先生产混合的硫化镍/钴中间产品,而后电解精炼生产出金属镍和钴。
由于约70%的红土矿资源是褐铁矿型的,高压酸浸技术受到了极大关注,其发展趋势大于火法工艺。从1998年以来,几家大公司,包括BHPBilliton公司(BHPB )、巴西国有矿业公司(CVRD)、加拿大的鹰桥公司(Falconbridge)和国际镍公司(INCO ),都已进行该方面的技术开发工作。HPAL工艺均经过高压釜浸出工序,主要的区别在于矿浆是直接加热还是间接加热、体系中是用新水还是用含盐水、高压釜浸出液采用何种方法处理以及得到何种镍和钴的产品。该工艺适合于处理低镁含量的氧化镍矿,矿石中镁含量过高会增加酸的消
耗,提高操作成本,对工艺过程也会带来影响。如果矿石中的钴含量高,则更适合采用酸浸工艺,不仅钴的浸出率比氨浸工艺高,而且由于钴的价值比镍高,使酸浸工艺的单位生产成本大幅度降低。红土镍矿不同处理工艺的综合比较见下表所示。
3、还原焙烧-酸浸工艺
还原焙烧-酸浸或亚硫酸浸出工艺,可在常压下进行。将矿粉在710~730℃下还原焙烧,得到的焙砂球磨后,采用1% H2SO4浸出,Ni浸出率为80%~85% , Fe浸出率为10%。如果用5% H2SO4浸出,Ni浸出率可达95% ,Fe浸出率为15%~20% 。矿石还原焙烧后,用亚硫酸或吹人SO2的水浸出,也可取得较好的效果。
4、硫酸化焙烧-水浸工艺
该工艺的原理是将矿石加入硫化剂,在大于700℃的高温下硫酸化焙烧,使氧化镍转化成为硫酸盐,球磨后采用水浸出,使镍转入溶液相,而焙烧过程中铁生成Fe2(SO4)3,高温下再分解成氧化铁,浸出时留在渣相。
—————————————
声明:本文由simao100发布、并对此行为可能带来的后果承担全部责任.