基于AMESim的液压AGC系统动态特性仿真与优化研究
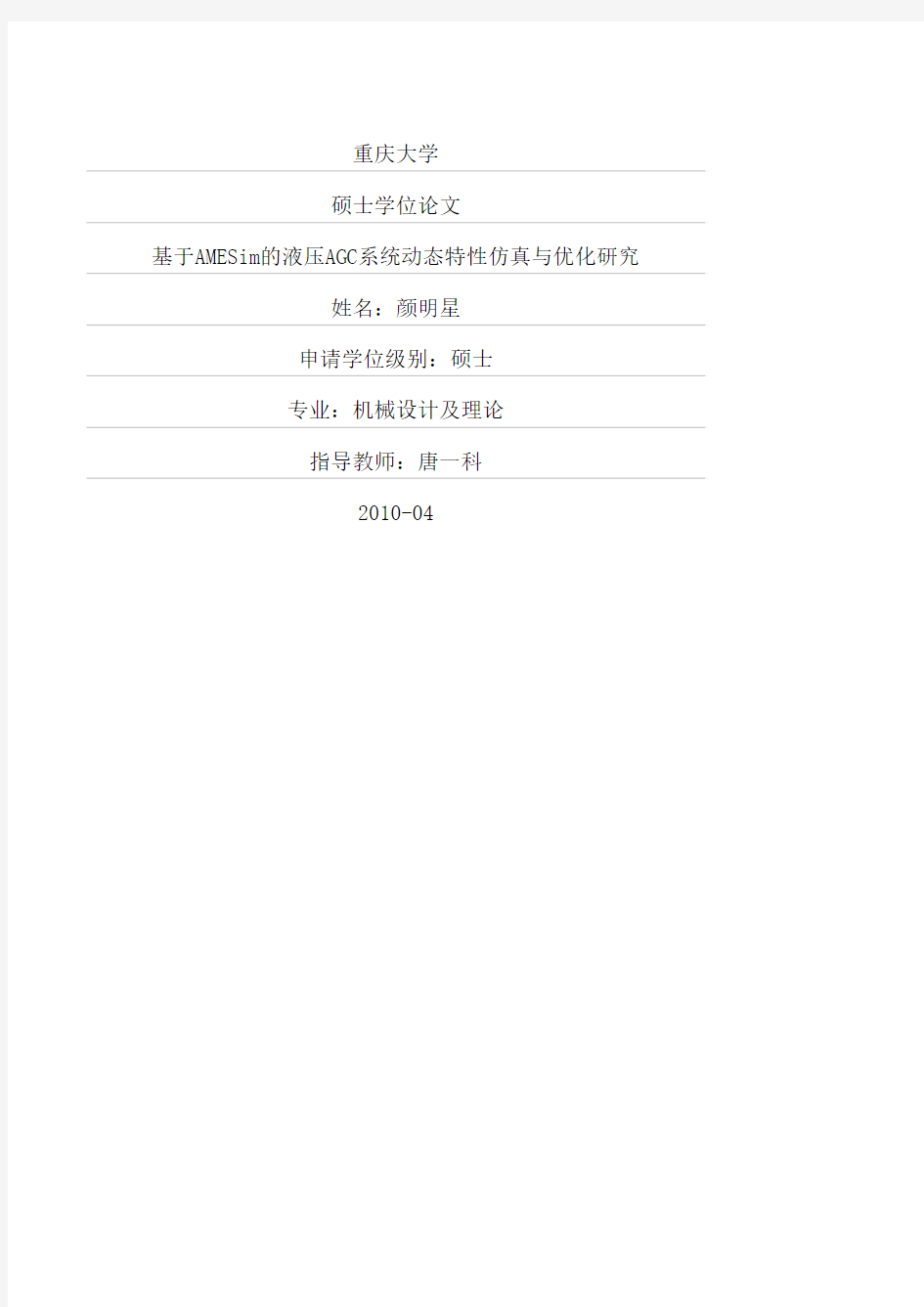

重庆大学
硕士学位论文
基于AMESim的液压AGC系统动态特性仿真与优化研究
姓名:颜明星
申请学位级别:硕士
专业:机械设计及理论
指导教师:唐一科
2010-04
摘要
板厚自动控制(Automatic Gauge Control,简称AGC)是板带轧制领域里的两大关键技术之一。板厚自动控制技术的优劣直接影响到板带材的质量精度,而板带材厚度精度是板带钢材的重要质量指标,不仅关系到生产过程中的节约问题,同时也对下游产业具有不小的影响。
液压AGC系统是板厚自动控制系统中的一个重要分支,典型的液压板厚自动控制系统由液压系统、控制系统、机械系统和电气系统等系统组成。自动板厚控制技术综合了众多学科领域的知识,所以在我国钢铁行业等类似行业中,虽然板厚控制技术已经得到了多年的应用,但是在实际的应用生产上,仍存在着诸多问题。同时,由于板带材厚度精度受到液压伺服系统精度、自动控制系统控制精度、工艺的瞬时条件和来料性质的随机变化等多方面因素的共同影响,使得控制系统的控制精度难以保证。故有必要对轧制过程与液压AGC系统进行研究,了解这些因素影响板厚精度的规律,进而提高液压AGC系统的动态特性及板厚精度。
本文针对液压AGC系统动态特性的仿真优化,主要进行了如下工作:
① 在大量阅读消化相关文献资料的基础上,系统地论述了板带材轧制过程中自动厚度控制的基本理论与控制方法,对板带材轧制过程中影响轧件厚度的主要因素以及实际轧出厚度的变化规律进行了总结。从轧制过程中厚度调节的不同方式出发,着重分析了几种典型的AGC系统构成及其控制原理;
② 在分析了轧机液压AGC系统原理及其运行机理的基础上,推导建立了液压AGC系统中主要动态元件的基本方程,包括电液伺服阀的基本方程、液压缸及辊系负载基本方程、伺服放大器、油路管道以及传感器等动态元件的传递函数,进而建立了液压AGC系统的电液位置闭环控制系统的动态数学模型;
③ 利用AMESim综合建模仿真平台构建了液压AGC系统的仿真模型,采用PID控制器对液压AGC动态模型进行了仿真,分析了影响系统动态特性和控制精度的主要因素。在得到稳定的控制效果之后,利用NLPQL算法、遗传算法等对液压AGC系统进行了优化试验。经仿真试验验证,基于NLPQL算法、遗传算法的液压AGC系统的控制精度得到了提升。
论文的部分研究结果,将应用于重庆钢铁集团股份有限公司热轧薄板厂1780mm生产线的液压AGC系统安装调试过程,为轧机的调试及状态监控提供理论依据。
关键词:板厚自动控制,液压伺服系统,动态特性,遗传算法
ABSTRACT
Automatic Gauge Control(referred as AGC) is one of the two key technologies in strip rolling field.Automatic gauge control technology will directly affect the quality of sheet and strip.The strip thickness accuracy of plate and strip steel is an important quality index, not only to the savings during production process, but also be of great significance on downstream industries.
Hydraulic AGC system is an important branch of the thickness control system.A typical hydraulic automatic control system consists of hydraulic systems, control systems, mechanical systems and electrical system components. Automatic gauge control technology combines the knowledge of many subject areas. Although the gauge control technology has been applied for many years in China's steel industry and similar industries, but there are still many problems in the actual application of production. Because of the thickness of strip be affected by hydraulic servo systems, control systems, process conditions and transient changes of raw materials in the common areas.Such as the impact of the realization of the control system more difficult. Therefore it is necessary to simulate the rolling process and hydraulic AGC system to findout the principles of these factors on thickness accuracy, and thus improve the dynamic characteristics of hydraulic AGC system and the thickness accuracy.
This paper for the simulation and optimization of the dynamic characteristics of hydraulic AGC system, mainly for the following work:
① Conducting hydraulic AGC system before the simulation and optimization. Systematic discussed the process of strip rolling and the basic theory of automatic gauge control and control methods. Made summary of the main factors affecting the thickness of the plate and strip in the rolling process and the discipline of actual variation of the exit thickness.Analyzed several basic AGC system structure and its control principle based on different ways of the thickness of the rolling process;
② Derived and set up the basic equations of electro-hydraulic servo valve,the basic equation of hydraulic cylinder and load of the roll system, the transfer function of servo amplifier, oil pipeline and the sensors and other dynamic components in the hydraulic AGC system based on analyed the theory and operational mechanism of hydraulic AGC system.And then set up a dynamic model of hydraulic AGC system;
③ Constructed hydraulic AGC system simulation model using the integrated
重庆大学硕士学位论文
modeling and simulation platform-AMESim.The simulation of hydraulic AGC system was done using PID controller.Analyed the main factors which impact the system’s dynamics and control accuracy.After the steady control effect of system been achived,the optimization test of hydraulic system was done using NLPQL and genetic algorithm. Verified by simulation test, the control accuracy of hydraulic AGC system based on NLPQL algorithm and genetic algorithm has been improved.
The simulation and optimization results will partly be used in 1780mm sheet production line in hot-rolle factory of Chongqing Iron and Steel Group Co., Ltd. Model data for reference presented to help the installation process and commissioning the diagnosis of the mill's hydraulic AGC system.
Keywords:AGC,Hydraulic Servo System,Dynamic Characteristic,Genetic Algorithm
学位论文独创性声明
本人声明所呈交的___士学位论文《___________________________________ _________》是我个人在导师指导下进行的研究工作及取得的研究成果。尽我所知,除了文中特别加以标注和致谢的地方外,论文中不包含其他人己经发表或撰写过的研究成果。与我一同工作的同志对本研究所做的任何贡献均己在论文中作了明确的说明并表示了谢意。
学位论文作者签名: 签字日期:
导师签名: 签字日期:
学位论文使用授权书
本人完全了解重庆大学有关保留、使用学位论文的规定。本人完全同意《中国博士学位论文全文数据库、中国优秀硕士学位论文全文数据库出版章程》(以下简称“章程”),愿意将本人的___士学位论文《______________________________ _________》提交中国学术期刊(光盘版)电子杂志社(CNKI)在《中国博士学位论文全文数据库》、《中国优秀硕士学位论文全文数据库》以及《重庆大学博硕学位论文全文数据库》中全文发表。《中国博士学位论文全文数据库》、《中国优秀硕士学位论文全文数据库》可以以电子、网络及其他数字媒体形式公开出版,并同意编入CNKI《中国知识资源总库》,在《中国博硕士学位论文评价数据库》中使用和在互联网上传播,同意按“章程”规定享受相关权益和承担相应义务。本人授权重庆大学可以采用影印、缩印或其他复制手段保存论文,可以公开论文的全部或部分内容。
作者签名:_______________ 导师签名:____________________
年月日
备注:审核通过的涉密论文不得签署“授权书”,须填写以下内容:该论文属于涉密论文,其密级是_______,涉密期限至_______年___月___日。
1 绪 论
1绪论
1.1本课题的研究意义
随着社会经济的发展,科技的进步以及市场需求的变化,各类用户对板带钢材的品种、材质、精度提出了更高的要求,尤其在汽车工业、电子工业、高压容器等行业领域对板带材的质量要求越来越高,特别是对其几何尺寸精度的要求越来越严格。板厚精度是板带钢材的重要质量指标,而板厚控制技术是板带轧制领域里的两大关键技术之一[1]。因此,研究钢材的轧制过程,优化板厚自动控制系统控制精度,提高板带材产品的质量精度,不但可以增强国内钢铁生产企业的竞争力,同时对促进制造企业的发展也具有重要意义。
为了提高生产效率和产品质量,获得高精度的板厚控制和板型控制,我国前些年从发达国家引进了一些大型的现代化的板带轧机,这些板带轧机的关键是高精度的板厚自动控制和板形自动控制。板厚精度关系到原材料的节约、下游产品构件的重量以及强度等使用性能。轧机自动化水平要求越来越高,所以为了获得高精度的产品轧出厚度,板厚自动控制(Automatic Gauge Control,简称AGC)系统必须具有高精度的压下调节系统及精确的控制系统的支持[1] [2]。
我国板厚控制技术虽然已经应用多年,但是由于轧机的压下控制技术综合了众多学科领域的知识,在实际的应用生产上,仍存在着诸多的问题[3]。国内在厚控系统的软件开发、检测仪器仪表、液压伺服系统元件的生产水平和精度上存在不足。即使是从国外引进的厚控系统,实际使用中也存在自动控制系统没有完全投入生产的情况。同时,由于板带材厚度受到液压伺服系统、自动控制系统、工艺的瞬时条件和原料的随机变化等几方面的共同影响,控制系统具有不确定性。因此有必要对轧制过程进行仿真研究,以便了解这些因素对板厚精度影响的规律,提出消除或减小该影响的方案。同时,为控制方法的更好实现,对板厚自动控制系统作进一步的仿真研究,将有助于控制参数的优化选取,缩短现场调试周期。另一方面,板厚自动控制系统中的一些非线性环节也影响到板厚精度,传统的控制方法对这些非线性环节的适应是非常有限的,因此有必要引入先进的控制方法,开展智能控制方法在此类对象控制中的实际应用和仿真探讨,不仅具有相当重要的理论意义,而且对促进我国工业自动化技术的发展、提高人工智能领域的研究应用水平,同样具有非常积极的意义[4]。
1.2轧机厚度自动控制技术的研究概况
板厚控制技术及其理论的发展经历了由粗到细、由低到高的发展过程。20世
重庆大学硕士学位论文
纪30年代以前,近代轧制理论处于孕育萌生期。这一阶段的轧机装机水平较低,厚度控制是以手动压下或简单的电动压下移动辊缝方式为主。由于当时各种检测手段尚不完善,轧机的调整和过程的实时调节主要是凭借操作人员的实际经验进行,尚未实现自动控制。
20世纪30年代到60年代,是轧机的常规自动调整阶段。该阶段中SLN理论的发展和完善为板带轧机的厚度控制奠定了基础。同时随着自动调节理论和技术的发展,逐步应用于SLN过程,轧机的控制步入了常规模拟式调节的自动控制阶段。单回路的各种调节系统不断涌现。主要体现在调速调节系统,张力调节系统,位置调节系统等。这些自动调节系统的实现,为完善板带轧机的厚度控制提供了先决条件。
20世纪60年代到80年代,进入计算机控制阶段,以弹跳方程为基础的厚度自动控制理论得到广泛应用。60年代中期计算机首先在热连轧机设定上开始应用。以厚度计式测厚实现厚度控制,以计算机实现各机架设定,很好的解决热连轧机的厚度控制问题,出现了热连轧机发展的鼎盛时期。60年代后期,逐步过渡到以主计算机设定和微机进行DDC(计算机直接数字控制)过程控制的阶段,并将这种控制方式大量应用于冷连轧机,使这一阶段的冷连轧快速发展。70年代起,液压厚控技术的应用使板厚控制技术发生了重大变革。由于液压技术与计算机技术的结合,这一阶段的板厚控制技术大大地向前迈进了一步。这一阶段大部分旧式控制方式的轧机都进行了技术改革。
上世纪80年代到现在,板厚控制向着大型化、高速化、连续化的方向发展,成为板厚技术发展的新阶段。这一阶段已将板厚控制的全过程溶入计算机网络控制的自动化级和基础自动化级。在过程控制级的控制中,采用最优控制、多变量控制、自适应控制、解耦控制等控制理论的最新成果,以追求控制性能的更精确。在监控层的设定计算中,采用人工智能,模糊控制,神经网络等知识工程的手法,以追求系统的灵活性和多样性。把以上两方面的不断追求融合在一起,开发出高精度、无人操作的厚度自动控制系统是这一阶段轧机的目标[5]。
近年来,国内外在板型板厚等控制技术方面取得了许多新的发展,大大提高了板带材的几何尺寸精度。为满足汽车制造、食品包装、家用电器、机械、轻工、仪表、通讯和军事工业等各领域的需要,生产出更高精度的板带材产品,占领国际市场,各国相继投入了大量的人力、物力,开发研制了许多种现代化大型轧机。具有代表性的有日本日立公司研制的工作辊可轴向移动的HC(High Crown)轧机,德国西马克公司研制的连续可变凸度CVC(Coutinuously Variable Crown)轧机,中间辊既可弯曲又可移动的UC轧机,日本三菱公司研制的成对轧辊交叉式的PC (Pair Cross)轧机,德国曼内斯曼-德马科公司的UPC轧机等。这些轧机配以现
1 绪 论
代化控制手段,可实现多功能精密轧制,生产出微米级厚度精度的板带材产品。尤其是近20年来,发达国家工业结构变化和发展中国家国民经济增长对冷轧带钢质量、品种和数量提出了新的要求,为轧制过程的控制进一步增加了难度,用传统的方法已经很难进一步提高控制水平了。因此,一些国家开始全面、有计划的开发智能控制如模糊控制技术、神经网络控制技术等以适应更高精度的要求。日本、美国、德国、法国等,在烧结、炼钢、连铸及轧钢等钢铁生产领域已经获得了成功应用。尤其是日本,在这方面投入很大,并获得了较多成果。例如,日本神户钢铁公司加古川厂五机架冷轧机的神经模糊板型控制系统、日本日立公司森吉米尔轧机的神经模糊板型控制系统等等。
目前,板厚自动控制(AGC)技术己日益成熟,纵向厚差的控制精度已经大为提高。现代控制理论及智能控制理论与技术也被广泛地应用于轧制过程中的厚度控制[6]。如: 刘建昌[7]提出了基于神经网络的自适应厚度自动控制系统,该系统具有良好的自适应跟随和抗干扰性能;方一鸣等[8]提出的基于内模原理的厚度控制系统的自校正控制器,可有效消除系统的静差;潘学军等[9]提出的基于模糊控制技术的模糊前馈厚度控制器,解决了来料厚度和硬度扰动所引起的轧机出口厚度变化的综合补偿问题;王国栋等[10]提出的基于在线辩识自校正控制技术的厚度控制系统,确保了系统的控制精度;方一鸣等[11]提出的应用模糊PID调节解决速度变化带来的厚度波动方案;以及Sharma U等[12]提出的在冷连轧中应用子空间模型辩识和H∞伺服控制理论来提高AGC系统的鲁棒稳定性和跟随性等。AGC技术在国外发展很快,如在日本、美国、法国等国家,各种AGC系统己成功应用于各种轧机。有的发展成高精度AGC系统,有的创立了AGC专利技术。计算机技术的应用深入各个领域。人工智能技术已经广泛应用,包括模糊控制、专家系统和人工神经元网络技术在AGC系统中的应用,己经取得了巨大成果和经济效益[13] [14] [15]。
我国在高精度轧制技术方面也作了大量的研究开发工作。新中国成立后为实现工业化,从外国引进了大型冶金设备和技术,我国的技术人员在多年的学习和消化的基础之上,结合我国的实际情况,自行开发出一些有关提高产品精度的基础理论和实用的先进工艺设备,其中有些技术已经达到或超过国外的先进水平。并且在轧机中也应用了一定的智能控制技术,像鞍钢中板厂2350mm四辊轧机智能控制的开发研究[16]、济钢中板轧机液压APC系统中模糊控制技术的应用等[17]。但总体上来说,我国自行研制的轧机,技术含量不高,生产出的产品竞争力不强,每年尚需进口大量的高精度板带材产品以及高精度轧机。而且许多轧机的生产状况尚不能令人满意,板厚精度急需提高,许多理论问题及所采用的先进技术,尚待进一步消化研究。
重庆大学硕士学位论文
1.3本课题的主要研究内容
轧机的控制非常复杂,其负载力大、扰动因素多、扰动关系复杂,同时对控制精度和响应速度的要求很高,是一个机理复杂的多变量、强耦合非线性过程,各变量之间相互作用和影响密切。随着工业技术的发展,板带材轧制速度逐渐提高,产品尺寸和精度的要求日趋严格,对轧机采用专门的控制技术,以实现对板带材的高精度控制,是目前板厚控制领域研究的热点问题。
本课题以重庆钢铁股份有限公司热轧薄板厂1780mm七机架四辊可逆式带钢轧机生产线为研究对象,对热连轧机厚度自动控制系统进行了深入的研究。在板带材的轧制中,影响轧件出口厚度的因素较多,且都将使工作辊的辊缝发生变化,从而影响了轧件的出口厚度尺寸精度及轧件的板形精度。针对以上的各种情况,本文综合分析各AGC控制方式的特性,通过对液压AGC系统主要元件进行动态特性分析,建立了液压AGC系统的动态模型,再结合重庆钢铁股份有限公司的现有条件,综合得出多机架可逆式热连轧机自动厚度控制策略,为该热轧生产线的运行调试提供可参考的仿真模型和数据。
论文的主要内容有:
① 轧机厚度自动控制系统基本理论
在查阅和消化国内外大量相关文献的基础上,分析总结了板带轧机厚度自动控制系统的基本理论,并对几种较为典型的AGC控制系统的构成方式与控制方法进行了分析。
② 液压AGC系统动态模型的构建
系统学习了轧制过程自动化技术、控制原理、液压控制系统等相关知识,了解掌握轧机板厚自动控制基本原理,熟悉液压AGC系统的运行原理,结合重庆钢铁股份有限公司热轧薄板厂1780mm轧机液压板厚自动控制系统方案,构建影响液压AGC系统控制精度的主要动态元件的基本方程,详细推导建立液压AGC系统的动态模型。
③ 液压AGC系统动态仿真分析
将所建立的轧机AGC模型和液压控制系统模型,利用AMESim系统工程高级建模和仿真平台进行仿真,分析各种情况下得到的仿真结果,提出较为优化的系统模型,为轧机的调试运行提供有一定参考价值的轧机液压AGC系统控制模型。
④ 液压AGC系统控制策略的优化研究
针对液压AGC系统的动态模型,在系统参数与控制策略上进行优化,利用NLPQL算法、遗传算法对系统参数及PID控制器进行改进。利用AMESim软件,对经过优化的系统参数以及PID控制器在液压AGC控制系统上的应用情况进行动态仿真研究。
2 厚度控制基本理论研究
2厚度控制基本理论研究
2.1板厚控制工艺理论基础研究
板厚自动控制是指通过测厚仪或传感器对板带材实际轧出厚度进行连续测量,并根据辊缝、张力、速度等可调参数的实测值与给定值相比较后得到偏差信号,借助控制回路和装置或计算机的功能程序,把厚度控制的波动影响减小甚至消除,使出口厚度接近或达到预设出口厚度。而辊缝、张力等参数的调节又是以机座的弹性曲线和轧件的塑性曲线——弹塑性曲线(P-H)为依据的[17]。
2.1.1轧制基本原理
如图2.1所示为轧制过程基本原理示意图。
其中:P—轧制力;
H—轧机入口板带厚度;
h—板带材轧机出口厚度;
—板带材轧机入口速度;
V
1
V
—板带材轧机出口速度;
2
—辊缝与测厚仪之间的距离。
l
图2.1 轧制基本原理
Figure 2.1 Basic principle of rolling mill
2.1.2 轧机的弹性变形和弹跳方程[1] [17] [18]
根据轧制原理,板带材轧制时在轧制力的作用下,工作机座(轧辊及其轴承、压下装置和机座等)会产生一定量的弹性变形,总变形量可达2~6mm。工作机座的弹性变形将影响轧辊的开口度和辊型,从而对轧制产品厚度精度造成不利影响。
轧件进入轧机前,预调辊缝值为S0;轧件进入辊缝,开始轧制后,在轧制力P
重庆大学硕士学位论文
的作用下,工作机座会产生弹性形变,使辊缝增大,从而使与轧件接触的轧辊形状呈凹形。弹性变形的结果使实际压下量减小,轧件的出口厚度大于空载辊缝值。轧后轧件厚度为:
h=S 0+ΔS (2.1) 式中:h —轧出厚度(mm );
S 0—预调辊缝值(mm );
ΔS —轧机弹跳值(也即机座弹性变形值)(mm )。
图2.2 弹性变形曲线
Figure 2.2 Curve of elastic deformation
图2.2表示了机座弹性变形量ΔS 与轧制力P 之间的关系曲线,称为机座弹性变形曲线或弹跳曲线。将机座弹性变形曲线的直线段的斜率,称为轧机的刚度,用K m 表示,它表征使轧机产生单位弹跳量所需的轧制压力。在轧制力较小的时候,机座弹性变形与轧制力成曲线关系,这是由机座各零件之间的接触面凹凸不平和轧辊的非线性接触变形造成的。当轧制力达到一定数值后,机座弹性变形与轧制力成直线关系。由于通常轧机都不在低负荷区轧制,故一般都把弹性曲线看成线性。
所以由图2.2,轧机的刚度可用下式表示: S
P tg K m Δ==α (2.2) 机座的弹性变形除与轧制力有关外,还与轧机的刚度有关。轧机的刚度越大,由此造成的轧件纵向厚差也就越小,即轧机控制轧件纵向厚差的能力越强。
据此,从图2.2可以得到,轧后轧件厚度h 可以近似表示为:
h
S
2 厚度控制基本理论研究
m
K P S S S h +
=Δ+=00 (2.3) 式中:h —轧件轧出厚度;
S 0—预调辊缝值(mm );
m K —轧机刚度(KN/mm );
P —轧制力(KN )。 式2.3即为弹跳方程,弹跳方程表示了轧件轧出厚度与预调辊缝、轧制力和机座纵向刚度之间的关系,是轧机厚度自动控制系统中的一个基本方程,是精确设定空载辊缝和设计厚度自动控制系统的基本方式,其精确度主要取决于轧制力P ,预压力P 0的精度,机座总刚度K m 以及S 0的精度。
2.1.3轧件的塑性变形及塑性方程[1] [17] [18] [19]
金属材料在外力作用下产生变形,在外力解除后可以恢复的变形方式称为弹性变形。在外力超过一定限值时,即使撤除外力变形也不会恢复,这种变形方式称为塑性变形。轧钢过程就是使轧件产生塑性变形,从而生产出质量得到控制的板带产品。在一定的轧件宽度和轧辊半径条件下,轧制压力与轧后轧件厚度的关系称为轧件的塑性变形曲线。
图2.3 轧件塑性变形曲线
Figure 2.3 Curve of rolling plastic deformation
轧制时的轧制力P 作为其他因素影响结果,是所轧带钢的宽度、轧件入口与出口厚度H 与h 、摩擦系数f 、轧辊半径R 、温度t 、前后张力σh 和σH ,以及变形抗力σS 等的函数。可以表示为:
()S H h t f h H R B F P σσσ,,,,,,,,= (2.4)
h
重庆大学硕士学位论文
此式为轧制的压力方程,当B ,R ,f ,t ,σh ,σH ,σS 及H 等均为一定时,P 将只随轧出厚度h 而改变,这样便可以绘出轧制力与轧出厚度h 的关系曲线即为轧件的塑性曲线。
轧件塑性变形曲线的斜率M 称为轧件的塑性刚度,它表征使轧件产生单位压下量所需的轧制力。
在计算机控制的条件下,可以根据已知的H ,h ,B ,R ,t ,v 和材质等测量出一个轧制力P ,然后再假定在其他条件不变的情况下,增加Δh 的压下量,又可以测量一个轧制力P’,则M 可表示为:
h
P P M Δ?=' (2.5) 式中:M —轧件的塑性刚度(KN/mm )。
轧件塑性在一般轧机使用范围内基本是线性的,轧制力方程可近似表示为:
()H h M P α+Δ= (2.6)
轧件塑性刚度M 反映了轧件的软硬程度,它与一系列因素有关,在塑性曲线的近似直线段范围内,可表示为:
βtg M = (2.7)
式中:β--轧制力近似直线段延长线与横坐标轴的夹角。
M 的变化范围很大,它与轧件宽度有密切关系,一般说来,坯料入口厚度H 和张力T 愈小,摩擦系数μ愈大,变形抗力σs 愈大,塑性系数M 也就愈大。热轧时M 值可从3000~20000KN/mm 。
2.1.4 弹塑性曲线[1] [17] [18]
以轧件厚度h 为横坐标,以轧制力P 为纵坐标,将机座弹性曲线和轧件塑性
曲线(即将图2.2和图2.3中的曲线A 和曲线B )
绘在同一坐标系里就得到P-h 图。 P-h 图是综合分析轧制过程中压力、辊缝、厚度之间相互关系的一种直观简便的方法。它能定量直观地反映出来料厚度、出口厚度、辊缝、弹跳值、轧制力、轧制时压下量等多个参数之间的关系,如图2.4所示。
轧件在轧制压力P 的作用下产生塑性变形,而机座在轧制力P 的反作用下产生弹性变形,其作用力和反作用力相等而达到平衡状态。因此,曲线A , B 的交点O 就是轧机在给定条件下的工作状态,它决定了实际轧制力的大小,从而决定了轧件的出口厚度h ,因此,一切影响曲线A 、B 交点位置的因素,都将影响轧件的出口厚度。因此板带材的厚度控制的基本原理就是无论轧制过程中各参数如何变化,设法维持交点O 的横坐标h 不变,从而得到恒定厚度的板带产品。
2 厚度控制基本理论研究
图2.4 弹塑性曲线
Figure 2.4 Curve of elastic and plastic
2.2 影响轧件厚度的主要因素及实际轧出厚度的变化规律 [18] [19]
在轧制过程中,凡是影响轧制压力、原始辊缝和轴承油膜厚度等的因素都将对实际轧出厚度产生影响,概括起来有如下几个方面:
① 温度变化的影响。温度变化对板带钢厚度波动的影响,实质就是温度差对厚度波动的影响,温度波动主要是通过影响金属变形抗力和摩擦系数的而引起厚度差;
② 张力变化的影响。张力是通过影响压力状态,以改变金属变形抗力,从而引起厚度发生变化。张力的变化除了对带钢头尾部厚度有影响之外,它也会影响其他部分的厚度发生变化。当张力过大时,除了会影响厚度,甚至会引起宽度发生改变,因此在热连轧过程中一般采用微套量的恒定小张力轧制,而冷连轧是在冷态进行轧制,并且随着轧制过程的进行,会产生加工硬化,所以冷轧时采用较大张力进行轧制;
③ 速度变化的影响。它是通过摩擦系数、变形抗力、轴承油膜厚度来改变轧制压力和压下量而起作用;
④ 辊缝变化的影响。当进行带钢轧制时,因轧机部件的热膨胀,轧辊的磨损和轧辊偏心等会使辊缝发生变化。轧辊和轴承的偏心也会使辊缝发生变化,从而直接影响实际轧出厚度变化。轧辊和轴承的偏心所导致的辊缝周期性变化,在高速轧制情况下,会产生高频的周期性厚度的波动。
除上述影响因素之外,来料厚度和机械性能不均匀,也将通过轧制压力的变化而引起带钢厚度发生变化。轧制时由于带钢有焊缝,焊缝处的硬度要比其他部分高,因此会引起厚度的波动。
h S
重庆大学硕士学位论文
2.2.1 实际轧出厚度随辊缝变化的规律[19] [20] [21] [22]
轧辊的偏心、磨损和热膨胀都会使实际的预调辊缝S 0发生变化,从而使轧件的轧出厚度产生波动。如图2.5所示,当空载辊缝由S 0变化到S 01或S 02时,弹跳曲线的位置将由A 平移到A 1或A 2,轧件厚度将由h 变化到h 1或h 2。
如果采取预压紧轧制时,会出现负辊缝,即轧机刚度线会越过零点取负值,如曲线A 3。这时候预调辊缝也为负值——(-S 03),能使轧出的板带刚更薄,此时实际轧出厚度为h 3。
图2.5 轧件出口厚度随辊缝变化的规律
Figure 2.5 Principal of export gauge relative to roll gap thickness changes
2.2.2 实际轧出厚度随轧机刚度而变化的规律[19] [20] [21] [22]
轧机的刚度K m 随轧制速度、轧制力、带钢宽度、轧辊的材质和凸度、工作辊与支撑辊接触部分的状况变化而变化,所以不同轧机的刚度是不同的,而且是由各种条件所决定的略有变化的数值。
当轧机的刚度K m 增加时,实际轧出厚度h 减小。如图2.6所示,当K m 从K m1增大为K m2时,对应的轧件出口厚度从h 1减小为h 2。可见,提高轧机的刚度有利于轧出更薄的带钢。目前板带刚轧机的自然刚度通常大约为3000~14000KN/mm。
在实际的轧制过程中,由于轧辊的凸度大小不同、轧辊轴承的性质以及润滑油的性质不同、轧辊的圆周速度会发生相应的改变,而这种变化将会引起轧机刚度的变化。就使用油膜轴承的轧机而言,当轧辊圆周速度增加时,轴承油膜厚度会增加,油膜的刚性也增大,可以轧出更薄的带材。
h
2 厚度控制基本理论研究
图2.6 轧机刚度对轧件出口厚度的影响
Fig.2.6 Affect of strip export gauge relative to mill rigidity modulus
2.2.3实际轧出厚度随轧制力而变化的规律[19] [20] [21] [22]
如前所述,所有影响轧制力的因素(包括轧件入口厚度、摩擦系数、轧制速度等)都会影响金属塑性曲线的相对位置和斜率,如材料变形抗力等。因此,即使在轧机弹跳曲线的位置(影响预调辊缝值)和斜率(影响轧机刚度系数)不变的情况下,所有影响轧制力的因素都可以通过改变塑性曲线和弹跳曲线的交点位置,进而影响着板带钢的实际轧出厚度。
图2.7 轧件入口厚度对轧件出口厚度的影响
Fig.2.7 Affect of strip export gauge relative to input plate thickness
以轧件入口厚度引起轧制力变化进而影响轧件出口厚度为例。如图2.7所示,轧件入口厚度从H3增大到H1的过程中,轧件塑性曲线位置右移,同时斜率增大,即代表轧件塑性刚度增大。在这种情况下,轧制力增大,轧件出口厚度由h3相应增大到h1,反之亦然。
重庆大学硕士学位论文
在实际的板带材轧制过程中,即使保证辊缝不变,由于入口轧件的性状的变化以及其他因素的变化,也很难得到厚度一致的板带材。而且各种因素对板带材实际轧出厚度的影响不是孤立的,往往是同时对轧出厚度产生作用。所以,在厚度自动控制系统中需要综合考虑各种因素的影响。
2.3 厚度自动控制系统的组成
厚度自动控制系统是一种复杂的控制系统。它由许多直接或间接影响轧件厚度的系统构成,一般认为其中三个主要的控制系统是辊缝控制系统、轧制速度控制系统和张力控制系统。
2.3.1辊缝控制系统
辊缝控制系统在自动厚度控制系统中的作用是根据控制器输出的辊缝调节数据,经过放大器放大之后,传送到伺服阀驱动液压缸运动,进而带动轧辊运动,实现辊缝的控制。
通过对辊缝的控制,可以消除各种变化因素对轧制质量的影响。辊缝控制系统是厚度自动控制系统中最重要的部分。
2.3.2轧制速度控制系统
轧制控制系统主要由轧机变速装置、轧辊、速度传感器等构成。轧制速度是以轧辊与板带材接触处的线速度表征的。操作台控制速度设定值,数据经处理器处理后传输到各个传动系统。通过设定工作辊的直径与减速箱的减速比,从而给出电机的转速给定值。根据控制功能,速度控制有正反向点动功能,用于故障处理;穿带速度设定,用于生产前轧机穿带;轧机线速度设定,用于正常轧制。按照线速度相等的原则以转速的形式分配给各传动系统。
通过调整轧制速度可以起到调整轧制温度、张力和摩擦系数的作用,从而改变塑性曲线的斜率,达到厚度控制的目的。
2.3.3张力控制系统
张力控制系统由厚度计、张力微调控制器、压下微调控制器、顶帽螺丝位置传感器、压下螺丝速度调节器等组件构成。根据轧机出口侧的X-射线测厚仪或其他形式的测厚仪测出的厚度,求得厚度偏差,进而来微调机架之间带钢上的张力,借此减小或消除厚度偏差。
2.4 轧机厚度自动控制系统的主要形式分析[1] [18] [19]
厚度自动控制是通过测厚仪或传感器(如辊缝仪和压头等)对带钢实际轧出厚度连续地进行测量,并根据实测值与给定值相比较后的偏差信号,借助控制回路和装置或计算机的功能程序,改变压下位置、张力或轧制速度,把厚度控制在
2 厚度控制基本理论研究
允许偏差范围内的方法。
根据轧制过程中对厚度调节方式的不同,一般可分为:反馈式、厚度计式、前馈式、张力式、液压式厚度自动控制系统等。下面作简要分析介绍:
2.4.1用测厚仪测厚的反馈式厚度自动控制系统
图2.8为该种厚度控制系统的框图。带钢从轧机中轧出之后,通过侧厚仪
图2.8 反馈式厚度自动控制系统
Fig.2.8 Feedback AGC system
测出实际轧出厚度h
实并与给定厚度值h
给
相比较,得到厚度偏差δh=h
实
-h
给
。当两
者数值相等时,厚度差运算器的输出为零,即δh=0。否则出现厚度偏差δh,这时便将此厚度偏差反馈给厚度自动控制装置,变换为辊缝调节量的控制信号,输出给压下电机带动压下螺钉或液压缸作相应的调节,以消除此厚度偏差。
图2.9 反馈调整的P-H图
Fig.2.9 P-H diagram of feedback adjusting
重庆大学硕士学位论文
为了消除己知的厚度偏差δh ,所必需的辊缝调节量是δS 。为此必须找出δh 与δS 关系的数学模型。根据图2.9所示的几何关系,得到:
M
f f h i
g ==δ fg ef eg S +==δ M K K M P M K K M f M f K f m m m m i i m i ++=???
?????+=+=δ (2.8) 故 M K K M K K M f M
f S h m m m m i i +=????????+=δδ 即 S M
K K h m m δδ+= (2.9) 或 h K M h K M K S m m m δδδ????????+=+=
1 (2.10) 从式2.10可知,为了消除带钢的厚度偏差δh ,则必须将压下螺钉使辊缝移动h K M m δ???????
?+1的距离。也就是说,要移动比厚度差δh 还要大M/K m 倍的距离。因此,
只有当K m 越大,而M 愈小,才能使得δS 与δh 之间的差别愈小。当K m 与M 为一定值时,即(K m +M )/K m 为常数,则δS 与δh 便成正比关系。只要检测到厚度偏差δh ,便可以计算出为消除此厚度偏差应作出的辊缝调节量δS 。
当轧机的空载辊缝S 0改变一个δS 0时,它所引起的带钢的实际轧出厚度的变化量δh 要小于δS 0,如图2.9所示。δh 与δS 0之间的比值C=δh/δS 0称为“压下有效系数”,它表示压下螺丝位置的改变量究竟有多大的一部分能反映到轧出厚度的
变化。当轧机刚度较小或轧件的塑性刚度较大时,
δh/δS 0比值很小,压下效果甚微。换句话说,虽然压下螺丝往下移动了不少,但实际轧出厚度往往未见减薄多少。因而增大δh/δS 0的比值对于实现快速厚度自动控制就有极其重要的意义。所以在实际的生产中,增加轧机整体的刚度是增大δh/δS 0的重要措施。如果能使轧机成为具有超硬性刚度,那么辊缝改变一个δS 0,则实际轧出厚度也就能变化一个δS 0。
反馈式厚度自动控制系统的传递函数框图如图2.10所示。
2 厚度控制基本理论研究
图2.10 测厚仪反馈控制方框图
Fig.2.10 Block diagram of thickness gauge feedback controll
图中:h 0—出口厚度给定值;
h —实测厚度值;
δh —厚度偏差;
G (s )—液压缸位置自动调节传递函数;
S 0—预调空载辊缝值;
S —工作辊缝值;
H —来料厚度;
δH —来料厚度波动干扰;
G 1(s )—轧机轧制环节。
检测点滞后量τ表示为:
v
L =τ 式中:τ—滞后时间,即为图2.10的延时时间;
v —轧制速度;
L —轧辊中心线到测厚仪的距离。
图2.10各环节传递函数可根据具体条件分别确定,G 1(s )可由P-h 图导出。 上述控制系统没有考虑装置动作的滞后,而且由于检测时间滞后,这种按比值进行厚度控制的系统有一定局限性。另外,电动压下和计算也有滞后时间,所以控制不是及时的,如果有任何突发性干扰,反而会出现负调节效果。但只要测厚计误差较小,对来料阶段性波动和仪器漂移最终能够完全加以消除,使出口厚度控制在一定范围内。
2.4.2 厚度计式厚度自动控制系统
在轧制过程中,任何时刻的轧制压力P 和空载辊缝S 0都可以检测到,因此,可用弹跳方程h=S 0+P/K m 计算出任何时刻的实际轧出厚度h 。在此种情况下,就等于把整个机架作为测量厚度的“厚度计”,这种检测厚度的方法称为厚度计方法或