转炉区域热试大纲

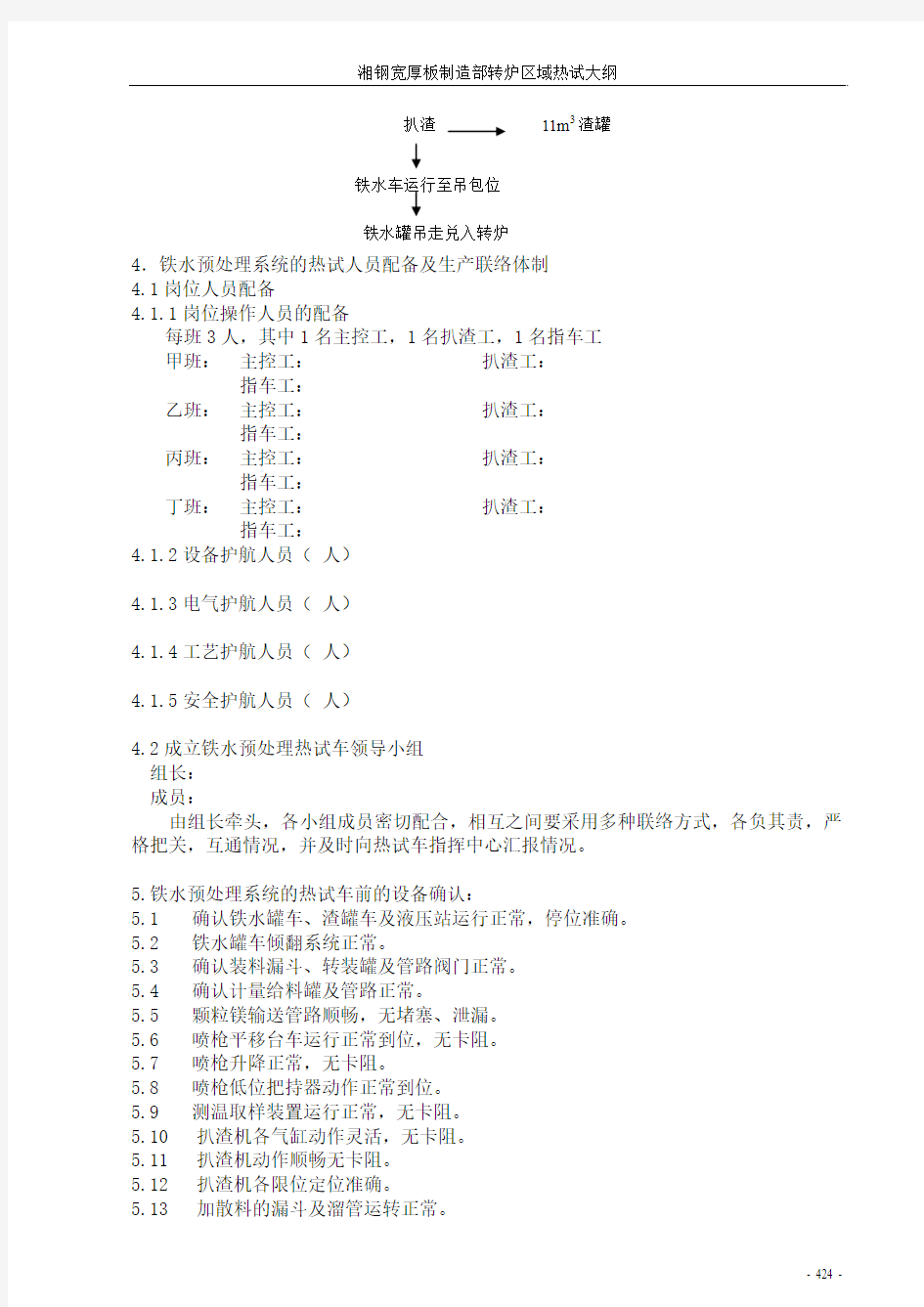
转炉区域热试操作大纲
一、铁水预处理热试大钢
1.目的
为了保证铁水预处理的热试车工作紧张、准确、有序地进行,防止遗漏,确保一次试车成功,制定本方案。
2.适用范围和时间
本方案适用于湘钢宽厚板铁水预处理区域,并仅适用于热试车期间。
3.方案内容
3.1热试条件
3.1.1所有操作人员必须经过培训合格后才能上岗操作,并且全部操作人员到位。
3.1.2操作系统必需的工器具原材料全部到位。
3.1.3通讯系统正常。
3.1.4脱硫铁水罐车、渣罐车、脱硫喷枪、扒渣机、装料漏斗、转装罐、计量给料罐、除
尘器、喷枪平移台车、测温取样装置、加散料系统、液压系统、卷帘门、轨道衡等经单体试车及电气功能试车合格后。
3.1.5整个铁水预处理的自动化系统调试完毕且运行良好、各种联锁正常。
3.1.6各种安全消防设施齐全有效。
3.1.7所有能源介质满足工艺设计要求。
3.1.8环境卫生整洁干净,各种物品摆放合理、有序,符合定置管理要
3.2铁水预处理的热试工艺流程:
高炉铁水罐铁水
在折罐位倒入铁水车上的转炉铁水罐
铁水车运行至脱硫位第一次测温取样
加石灰
下枪喷吹
提枪
第二次测温取样
4.铁水预处理系统的热试人员配备及生产联络体制 4.1岗位人员配备
4.1.1岗位操作人员的配备
每班3人,其中1名主控工,1名扒渣工,1名指车工 甲班: 主控工: 扒渣工: 指车工:
乙班: 主控工: 扒渣工: 指车工:
丙班: 主控工: 扒渣工: 指车工:
丁班: 主控工: 扒渣工: 指车工:
4.1.2设备护航人员( 人)
4.1.3电气护航人员( 人)
4.1.4工艺护航人员( 人)
4.1.5安全护航人员( 人)
4.2成立铁水预处理热试车领导小组 组长: 成员:
由组长牵头,各小组成员密切配合,相互之间要采用多种联络方式,各负其责,严格把关,互通情况,并及时向热试车指挥中心汇报情况。
5.铁水预处理系统的热试车前的设备确认:
5.1 确认铁水罐车、渣罐车及液压站运行正常,停位准确。 5.2 铁水罐车倾翻系统正常。
5.3 确认装料漏斗、转装罐及管路阀门正常。 5.4 确认计量给料罐及管路正常。
5.5 颗粒镁输送管路顺畅,无堵塞、泄漏。 5.6 喷枪平移台车运行正常到位,无卡阻。 5.7 喷枪升降正常,无卡阻。
5.8 喷枪低位把持器动作正常到位。 5.9 测温取样装置运行正常,无卡阻。 5.10 扒渣机各气缸动作灵活,无卡阻。 5.11 扒渣机动作顺畅无卡阻。 5.12 扒渣机各限位定位准确。
5.13 加散料的漏斗及溜管运转正常。
扒渣
铁水车运行至吊包位 铁水罐吊走兑入转炉
11m 3渣罐
5.14卷帘门运行正常到位。
5.15除尘器及烟气排出阀工作正常。
5.16除尘系统运行正常。
5.17各润滑点无缺油现象。
5.18氮气、压缩空气等能源介质满足工艺设计要求。
5.19各种限位、连锁、仪器、仪表正常。
5.20安全消防设施齐全有效。
6. 铁水预处理系统的热试车操作
6.1颗粒镁的输送:
①装料漏斗装料的确认;
②转装罐和计量给料罐及其管路阀门的确认;
③载气氮气压力和流量的确认;
④染尘氮气排出系统的设备确认;
⑤计算机画面功能和自动化系统的确认;
⑥喷枪本体的检查确认;
⑦输送少量颗粒镁,检测喷枪出口的流量和压力;确保管路通畅不堵料。
6.2铁水罐车、渣罐车的操作:
①铁水罐车、渣罐车系统的单体设备试车及冷联动试车的再次确认;
②铁水罐车、渣罐车系统的计算机画面功能和自动化系统的确认;
③铁水罐车上置转炉铁水罐;折罐、行走、倾翻。检查其运行过程的机械电气性能是否
正常;
④铁水罐车上置转炉铁水罐;在折罐位检查其称重轨道衡显示是否正常;
⑤渣罐车上置重渣罐检查其行走过程的机械电气性能是否正常。
6.3喷枪及驱动台车的操作;包括:
①喷枪平移及升降、测温取样机构、低位把持器的单体试车及电气功能试车;
②喷枪平移及升降、测温取样机构、低位把持器的自动化系统测试,包括联锁条件的确
认;
③轨道、链条等附属设备的确认;
④极限位、喷枪及测温取样器的插入深度的确认;
6.4喷吹脱硫的操作:
自动方式要求把“Desulphurization”、“Ladle car”屏幕显示的计量给料罐、喷枪台车、烟气排出阀、铁水车、渣罐车、卷帘门控制阀、测温取样器等设备操作窗口中“Control”一一点开,选择到“MAIN”方式。
1)计量给料罐内压力是否归零;颗粒镁≥50㎏;
2)铁水车是否在脱硫位上;
3)脱硫喷枪是否在A或B位置上;
4)两侧卷帘门关闭,烟气排出阀打开;
5)氮气压力≥0.4Mpa。
6)喷枪低位把持器打开;各极限点信号到位。
按“Data”后弹出“Calculation of desulphurization parameters”窗口,然后手工输入六个参数:“Number of processing”、“Required% of sulfur”、“Initial% of sulfur”、“Weight of pig-iron”、“Temperature”和“μ”。按“Calculate”。待“Data”和“Preparation”两键呈绿色后,按“Start”,此时会弹出一小方框,内有“OK”和“concel”两种选择,点击“OK”,
即可实现自动脱硫过程。
6.5扒渣系统的操作;包括:
①扒渣机及液压系统,电动门的单体试车及电气功能试车;
②扒渣机及液压系统,电动门的自动化系统测试,包括联锁条件的确认;
③扒渣板、润滑的确认;
6.6 除尘系统的操作;包括:
①排烟罩、烟气排出阀的单体试车及电气功能试车;
②各点烟气排出阀的的自动化系统测试,包括联锁条件的确认;
7.铁水预处理系统的常见事故处理
7.1 喷枪上、中、下极限不好使(信号不来)
7.1.1主要原因:横移台画、夹紧油缶,喷枪三处交流电源送上,其辅助点进PLC
24V电源无;保险接触不良。
7.1.2处理方法:检查开关是否合上辅助,接点是否好使;电源是否正常。
7.2扒渣杆变形
7.2.1主要原因:在未收回伸缩杆的情况下就给主控室发出动车信号。
7.2.2处理方法:在扒渣机上增加到位信号极限,使扒渣机必须完全回位以后,才能操作
铁水车。
7.3 铁水车倾翻不好使
7.3.1主要原因:油泵主接触器烧坏;拖缆收线盘变形和双控开关不好使,影响拖缆收放,
致使拖缆拉坏。
7.3.2处理方法:更换油泵主接触器、拖缆收线盘和双控开关;对拖缆弯头内套处定期加
油。
7.4 铁水车不动作
7.4.1主要原因:变频器显示故障;
7.4.2处理方法:更换变频器;
8.铁水预处理系统热试的安全注意事项
8.1凡参加试车的人员必须穿戴好规定的安全劳保用品。
8.2试车期间做好安全防护及危险预知预测工作。
8.3试车期间现场必须备有消防灭火器材。
8.4不得用手触模各转动部件。
8.5试车前专人指挥,电气操作由专人负责,按指挥者的指令进行操作。
8.6若出现异常情况、应立即停车检查。
8.7各种安全消防设施齐全有效
8.8液压站内严禁烟火。
8.9严密监视液压马达,防止漏油着火。
9 9
二、转炉上料系统热试大钢
1.目的
为了保证转炉上料系统的热试车工作紧张、准确、有序地进行,防止遗漏,确保一次试车成功,制定本方案。
2.适用范围和时间
本方案适用于湘钢宽厚板转炉上料系统区域,并仅适用于热试车期间。
3.方案内容
3.1上料系统的热试条件
3.1.1所有操作人员必须经过培训合格后才能上岗操作,并且全部操作人员到位。
3.1.2操作系统必需的工器具、原料到位。
3.1.3通讯系统正常。
3.1.4电振给料机工作正常;皮带秤重量显示正常;托辊齐全,无卡阻现象;各传动电机、减速机、联轴器等正常;皮带完好;卸料小车下料正常,无卡阻现象;各电气元件正常。
3.2.上料系统的热试工艺流程
辅原料高位料仓上料系统(A.I系统)流程:
辅原料地下料仓(FDC01-FDC14)
辅1皮带机(F1BC)
辅2皮带机(F2BC)
辅3皮带机(F3BC)
辅4皮带机(F4BC)
电动卸料车(FXLC1)
辅原料高位料仓(FGC201-FGC210)
铁合金中位料仓上料系统(A.2系统)流程:
铁合金地下料仓(TDC01-TDC16)
地下料仓电振给料机(TDVF01-TDVF16)
铁1皮带机(T1BC)
铁2皮带机(T2BC)
铁3皮带机(T3BC)
铁4皮带机(T4BC)
电动卸料车(TXLC1)
铁合金中位料仓(TZC201-TZC208)
4.转炉上料系统的热试人员配备及生产联络体制
4.1岗位人员配备
4.1.1岗位操作人员的配备
每班2人
甲班:班长:
操作工:
乙班:班长:
操作工:
丙班:班长:
操作工:
丁班:班长:
操作工:
4.1.2设备护航人员(人)
4.1.3电气护航人员(人)
4.1.4工艺护航人员(人)
4.1.5安全护航人员(人)
4.2成立转炉上料系统热试车领导小组
组长:
成员:
由组长牵头,各小组成员密切配合,相互之间要采用多种联络方式,各负其责,严格把关,互通情况,并及时向热试车指挥中心汇报情况。
5.转炉上料系统热试前的准备确认
辅原料及铁合金上料系统热负荷联动试车前的准备确认包括:各单体设备试车前的检查确认和系统设备空负荷联动试车检查确认。首先确认电气室进线柜、各电源柜、各MCC柜、各PLC柜、UPS电源柜,微机室内上位机,上料除尘风机电气柜等送电正常,各现场操作箱正常,通讯系统正常。
5.1 MCC送电准备
5.1.1确认MCC柜的进线电源的三相电压正常。
5.1.2 1#、2#进线的总电源开关,选定其中一路作为电源,并手动合上该路电源断路器。
5.1.3在控制变压器抽屉内,合上“控制变压器开关”断路器。
5.1.4根据MCC柜体上的“零线接地”指示灯和“相线接地”指示灯状态,确认辅助电源处于零线接地。
5.1.5在控制变压器抽屉内合上“电源整流器开关”。
5.1.6在对单体设备进行送电前,先将抽屉内的控制电路开关合闸送电,然后将抽屉推入MCC柜,并确保主电路和控制电路连接端子连接紧密。
5.1.7通过各单体设备抽屉上的旋转手柄将单体设备的主电路断路器合闸送电。
5.2单体设备试车前的检查确认内容有:
5.2.1依次对这8条输送机进行检查。检查输送机各上托辊、下托辊以及改向辊转动是否灵活;皮带粘接是否可靠无撕裂痕迹;各把合螺栓是否紧固;传动减速机及各润滑点是否加油或脂。进行确认或处理。
5.2.2对各卸料小车进行检查。检查传动机构是否完好,传动链条松紧是否合适;减速机、电液推杆和各个润滑点是否加油或脂;小车上的各皮带辊转动是否灵活。进行确认或处理。
5.2.3对振动给料机进行检查。检查各型号的振动给料机是否完好,密封帆布有无撕裂现象;对手动斜闸门、手动平闸门振动给料机依次开启、关闭数次,检查闸门的动作是否顺利灵活;对带有液压缸推动式闸门的振动给料机要检查电液推杆内是否加油。进行确认或处理。
5.2.4对各排料闸门、密封闸门进行检查。检查两种闸门是否完整;闸门上的电液推杆是否加油。进行确认或处理。
5.3系统设备空负荷联动试车检查确认内容有:
5.3.1依次对这8条输送机进行送电试车,启动电动机,使传动辊进行转动,带动皮带进行运动,在这个过程中观察有无异常状况的发生,包括传动辊的转动是否匀速,皮带的运动是否平稳,有无跑偏现象。对各条输送机的上托辊、下托辊以及改向辊转动要仔细听,有无较明显的异音。若有问题则应及时处理。
5.3.2对各卸料小车送电试车,启动电机,带动小车在全行程范围内来回运行数次,运行要平稳,无卡阻、啃轨和异常噪音等现象。小车应在卸料位准确停车,并对小车的布料切换装置进行试车,在电液推杆的带动下,装置应切换灵活、准确。若有问题则应及时处理。
5.3.3依次启动振动给料机,检查该机振动过程中软连接处的绷紧及松弛状况是否超出其
100T转炉物料平衡及热平衡计算
100T顶底复吹转炉炼钢的物料平衡和热平衡计算 5.1 物料平衡计算 5.1.1 计算原始数据 基本原始数据有:冶炼钢种及成分、铁水和废铁的成分、终点钢水成分;造渣用溶剂及炉衬等原材料成分;脱氧和合金化用铁合金的成分及回收率;其他工艺参数。 表5-2 原材料成分 石灰中S自耗的CaO量 表5-3 矿石加入量及成分 矿石中S消耗CaO量=0.001*2/3*56/32=0.001kg
表5-4 其他工艺参数设定值 5.1.2物料平衡的基本项目 收入项有:铁水、废钢、溶剂(石灰、矿石、轻烧白云石)、氧气、炉衬蚀损、铁合金。 支出项有:钢水、炉渣、烟尘、渣中铁珠、炉气、喷溅。 5.1.3 计算步骤 以100㎏铁水为基础进行计算。 第一步:计算脱氧和合金化前的总渣量及其成分。 总渣量包括铁水中元素氧化,炉衬腐蚀和加入溶剂的成渣量。其各项成渣量分别列于表5-5~表5-7。总渣量及成分如表5-8所示:
铁水中元素氧化量 ①由CaO还原出的氧量;计算出铁水中S消耗CaO量=0.009×56/32=0.016㎏。 表5-6 炉衬腐蚀的成渣量
①.石灰加入量:石灰加入量= ()()有效 CaO CaO R SiO %2 ∑∑-? =(1.171*3.2-0.657)/(88.0%-3.2×2.50%) =(3.747-0.657)/0.8 =3.09/0.8 =3.863kg ∑(SiO 2)=铁水[Si]生成(SiO 2)+炉衬、矿石、白云石带入(SiO 2); =1.071+0.009+0.046+0.045=1.171㎏; ∑(CaO )=白云石、矿石、炉衬带入(CaO )-铁水、矿石中S 消耗CaO 量; =0.66+0.01+0.004-0.001-0.016=0.657㎏; 因设定终渣碱度R=3.2: %CaO 有效=石灰中(%CaO )-碱度R ×石灰中(% SiO 2)=88.0%-3.2×2.50% ①.表中除(FeO)和(Fe2O3)以外的总渣量为4.073+1.268+0.835+0.098+0.45+0.645+0.031=7.4㎏,而终渣Σω(FeO)=15%(表5-4), 故总渣量为7.4/86.75%=7.4/86.75%=8.53㎏。 ②.ω(FeO)=8.53×8.25%=0.704㎏ ω(Fe 2O 3)=8.53×5%=0.427㎏。 由于矿石和白云石 第二步:计算氧气消耗量。 氧气的实际消耗量系消耗项目与供入项目之差。见表5-9 第三步:计算炉气量及其成分。
转炉炼钢物料平衡和热平衡计算 模板-
第二章、转炉物料平衡和热平衡计算 1、低磷生铁吹炼(单渣法) 一、原始数据 (一)铁水成分及温度 (二)原材料成分 (三)冶炼钢种及成分 (四)平均比热 (五)冷却剂 用废钢做冷却剂,其成分与冶炼钢种中限相同。 (六)反应热效应
反应热效应通常采用25℃为参考温度,比较常用的反应数据见表2-1-5 (七)根据国内转炉实测数据选取 1、渣中铁珠量为渣量的2.5%; 2、金属中[C]假定85%氧化成CO,15%氧化成CO2; 3、喷溅铁损为铁水量的0.3%; 4、取炉气平均温度1450℃,自由氧含量0.5%,烟尘量为铁水量的1.8%,其中FeO=75%,Fe203=22%; 5、炉衬侵蚀量为铁水量的0.15%; 6、氧气成分为98.9% O2,1.5% N2。 根据铁水成分,渣料质量,采用单渣不留渣操作。先以100公斤铁水为计算基础。 (一)炉渣及其成分的计算 1、铁水中各元素氧化量 表2-1-6 成分,kg C Si Mn P S 合计项目 铁水 4.36 0.57 0.62 0.07 0.05 终点钢水0.13 痕迹0.13 0.008 0.019 氧化量 4.23 0.57 0.49 0.062 0.031 5.308 [C]:取终点钢水含碳量0.15%; [Si]:在碱性氧气转炉炼钢中,铁水中的Si几乎全部被氧化; [Mn]:顶底复吹转炉残锰量取60%; [P]:采用低磷铁水吹炼,铁水中磷90%进入炉渣,10%留在钢中; [S]:氧气转炉去硫率不高,取40%。 2、各元素氧化量,耗氧量及其氧化产物量见表2-1-7 3、造渣剂成分及数量 根据国内同类转炉有关数据选取 1)矿石加入量及成分 矿石加入量为1.00公斤/100公斤铁水,成分及重量见表2-1-8 2)萤石加入量及成分
转炉炼钢物料平衡计算
1.转炉炼钢物料平衡计算 1.1计算原始数据 基本原始数据:冶炼钢种及其成分、铁水和废钢成分、终点钢水成分(表1); 造渣用溶剂及炉衬等原材料的成分(表2);脱氧和合金化用铁合金的成分及其回收率(表3);其他工艺参数(表4)。 表1 钢水、铁水、废钢和终点钢水的成分设定值 成分含量 /% 类别 C Si Mn P S 钢种Q235设定值0.18 0.25 0.55 ≤0.045 ≤0.050 铁水设定值 4.10 0.90 0.55 0.300 0.035 废钢设定值0.18 0.25 0.55 0.030 0.030 终点钢水设定值0.10 痕迹0.18 0.020 0.021 aa[C]和[Si]按实际产生情况选取;[Mn]、[P]和[S]分别按铁水中相应成分含量的30%、10%和60%留在刚水中设定。 表2 原材料成分 成分/% 类别CaO SiO2MnO Al2O3Fe2O3CaF2P2O5S CO2H2O C 灰分 挥发 分 石灰87.00 2.80 2.70 1.80 0.60 0.10 0.06 4.84 0.10 萤石0.30 5.40 0.70 1.60 1.50 88.00 0.90 0.10 1.50 生白云石37.40 0.80 24.60 1.00 36.2 炉衬 1.20 3.00 78.80 1.40 1.60 14.0 焦炭0.58 81.5 12.4 5.52
表3 铁合金成分(分子)及其回收率(分母) 成分含量/回收率/% 类别 C Si Mn Al P S Fe 硅铁—73.00/75 0.50/ 80 2.50/ 0.05/ 100 0.03/ 100 23.92/100 锰铁 6.60/ 900.50/ 75 67.8/ 80 —0.23/ 100 0.13/ 100 24.74/100 10%与氧生成CO2。 表4 其他工艺参数设定值 名称参数名称参数 终渣碱度 萤石加入量 生白云石加入量炉衬蚀损量 终渣∑ω(FeO)含量(按向钢中传氧量ω(Fe2O3) =1.35ω(FeO)折算) 烟尘量 喷吹铁损W(CaO)/W(SiO2)=3. 5 为铁水量得0.5% 为铁水量得2.5% 为铁水量得0.3% 15%,而W(Fe2O3)/ ∑w(FeO)=1/3,即 W(Fe2O3)=5% W(FeO)=8.25% 为铁水量得1.5%(其 中W(FeO)75%, W(Fe2O3)为20%) 为铁水量得1% 渣中铁损(铁珠) 氧气纯度 炉气中自由氧含量 气化去硫量 金属中[C]的氧化产 物 废钢量 为渣量的6% 99%,余者为N2 0.5%(体积比) 占总去硫量得1/3 90%C氧化成CO,10%C氧化成 CO2 由热平衡计算确定,本计算结果 为铁水量的13.64%,即废钢比为 12.00%
区域发展区域研究与区域科学复习大纲
名词解释 1、区域分析:对区域发展的自然条件和社会经济诶经特征及其区域社会经济发展的影响进行分析,探讨区域内部各自然及人文要素间和区域间相互联系的规律。 2、区域自然资源承载力:一个国家或地区的资源承载力是指在可预见的时期内,利用本地资源及其他自然资源和智力、技术等条件,在保证符合其社会文化准则的物质生活水平所持续供养的人口数量。 3、防护费用法影子工程法 所谓防护费用是指用人们为了消除或减少生态环境恶化的影响而愿意承担的费用来替代生态环境价值的方法。 影子工程法是恢复费用法的一种特殊形式,当生态环境价值难以直接估算时,可借助能够提供类似功能的替代工程或所谓的影子工程的价值来替代该生态环境的价值。 4、区域经济:从一定意义上讲,区域经济就是在一国范围内,以客观存在的地域单元为基础,按照劳动地域分工原则建立起来的具有区域特点的地域性国名经济。 5、区域政策:根据区域差异而制定以协调区域间关系和区域宏观运行机制的一系列政策之和,在宏观层次上影响着区域发展。 6、吸收型技术转移:吸收型技术转移是指某项先进技术由甲国转移到乙国并且将会被乙国消化、吸收并复制出来。 7、垂直技术转移:甲国基础科研成果能用于乙国的应用科学中,或将前者的科研成果用于后者的生产中。 8、绿色GDP 绿色GDP=传统GDP-自然环境部分的虚数-人文部分的虚数
9、区域竞争力:一个地区在竞争和发展过程中与其他地区相比较所具有的吸引、争夺、拥有、控制和转化资源,争夺。占领和控制市场以创造价值,为其人民提供福利的能力。 10、比较优势:建立在要素禀赋基础之上,生产某些特定产品所拥有的相对低廉的价格优势,表现为在区外市场占有较大的市场份额。 11、竞争优势:当一个组织实施一种同类组织无法复制或难以模仿的独特的价值创造战略时所形成的优势。 12、垂直分工水平分工 区域垂直分工是指相关区域在同一个生产过程中的不同生产阶段进行专业化生产、彼此联系而产生的区域分工。 区域水平分工是指相关区域发展不同的经济部门、或者生产具有差异的同类产品所形成的分工。 13、空间管治:是区域管治的重要内容和手段,它是通过划定区域内不同功能、不同建设发展特性的类型区,制定各类型区的开发标准和控制引导要求,其中包括城镇建设控制、生态环境保护、乡村建设、土地资源利用等内容,以空间资源合理配置为目标,实施区域的统一规划,以协调区域内各级政府、各团体、企业、居民等不同主体的利益。 14、科技工业园区高新技术加工区 科学工业园区是一种科学研究与工业生产相结合的综合体,是科研成果商品化的区域,其功能表现为以研究开发为主,包括产品试制和开发生产,而不具有大批量制造、销售、管理或其他实业性功能。 高新技术加工区是世界出口加工区由劳动密集型向技术密集型转换过程中出现的
热平衡路试实验大纲
整车热平衡路试实验大纲 1.适用范围 本实验大纲适用于标杆车及样车测定汽车热平衡能力的道路试验方法。 本实验大纲适用于同时装有强制循环液冷式发动机和具有手动挡功能变速器的各类汽车,其他类型的汽车也参照执行 2.实验依据 2.1 GB/T 12542-2009 《汽车热平衡能力道路实验验证方法》 2.2 GB/T 12534 《汽车道路实验方法通则》 2.3 GB/T 18297-2001《汽车发动机性能实验方法》 3. 整车热平衡实验相关术语和定义 a)环境温度:汽车行驶时周围环境阴影下1.5m高处的空气温度。 b)冷却介质:起冷却作用的物质,包括发动机冷却液、发动机润滑油、变速器润滑油、驱动桥润滑油等。本试验中只对发动机冷却液和发动机润滑油的温度进行测量。 c) 热平衡:系统(零部件、总成、汽车)各部分温度与环境温度的差值达到稳 定状态。 d) 汽车热平衡:汽车动力总成(发动机、变速器、驱动桥)热平衡。 e) 冷却常数:汽车热平衡时冷却介质温度与环境温度的差值。 f)冷却介质许用最高温度:汽车动力总成(发动机、变速器、驱动桥)正常工 作所允许的冷却介质最高温度(由生产厂给定)。 g) 极限使用工况:汽车低档位、全油门长时间输出最大扭矩或最大功率的
情况。 h) 常规使用工况:汽车高速行驶、高速爬坡、长时间怠速等汽车常见使用工况。 i) 极限使用许用环境温度:极限使用工况下汽车受冷却介质许用最高温度的 限制而允许使用的最高环境温度。 j) 常规使用许用环境温度:常规使用工况下汽车受冷却介质许用最高温度的 限制而允许使用的最高环境温度。 4. 实验条件及所需工具 4.1 无雨、无雾,环境温度不低于30℃,风速不大于3m/s。如果环境温度低 于30℃,则应详细记录实验时的环境温度、湿度、大气压力等气象参数。 4.2 实验道路按GB/T 12534 的规定,要求路面坚硬、平坦、清洁、干燥,用 混凝土或者沥青铺装,要有足够长的高速跑道,纵坡度小于0.1%。 4.3 轮胎充气压力对实验数据的准确性有较大影响。在进行实验之前应使汽车 轮胎充气压力在冷态的时候符合该车的技术条件规定,误差不得超出±10Kpa。 4.4 在实验过程中被试车辆所用的燃料、机油及冷却液应符合该车技术条件或现行国家标准的规定,采用制造厂规定的牌号。 4.5有挡风效果的“十”字挡风墙,一般长4m、高2.5米,参见附录A。 4.6 实验用主要仪器设备见表1。 表1
转炉炼钢物料平衡和热平衡计算模板-
转炉炼钢物料平衡和热平衡计算模板- 第二章、转炉物料平衡和热平衡计算 1、低磷生铁吹炼(单渣法) 一、原始数据 (一)铁水成分及温度 表2-1-1 成分 C Si Mn P S 温度 ? % 4.36 o.57 0. 62 0.07 0.05 1300 (二)原材料成分 表2-1-2 烧合计成分% CaO SiO MgO AlO S P CaF FeO FeO HO C 2232232减 % 种类100 91(08 1(66 1(54 1(22 0(06 4(44 石灰 100 1(00 5(61 0(52 1(10 0(07 29(4 61(8 0(50 矿石 100 6(00 0(58 1(78 0(09 0(55 89(00 2(00 萤石 10 8 53(04 0(48 34(94 0(74 白云石 100 1(40 2(60 85(00 11(00 炉衬 (三)冶炼钢种及成分 表2-1-3 成分 C Si Mn P S % 0.12—0.20 0.20—0.55 1.20—1.60 ?0.045 ?0.045 (四)平均比热 表2-1-4 项目固态平均比热kcal/kg.? 熔化潜热kcal/kg 液态或气态平均比热 kcal/kg.?
生铁 0.178 52 0.20 钢 0.167 65 0.20 炉渣 50 0.298 烟尘 0.238 50 矿石炉气:CO 0.349 CO 0.558 2 SO 0.555 2 O 0.356 2 N 0.346 2 HO 0.439 2 (五)冷却剂 用废钢做冷却剂,其成分与冶炼钢种中限相同。 (六)反应热效应 1 反应热效应通常采用25?为参考温度,比较常用的反应数据见表2-1-5 (七)根据国内转炉实测数据选取 1、渣中铁珠量为渣量的2.5%; 2、金属中[C]假定85%氧化成CO,15%氧化成CO; 2 3、喷溅铁损为铁水量的0.3%; 4、取炉气平均温度1450?,自由氧含量0.5%,烟尘量为铁水量的1.8%,其中FeO=75%, Fe0=22%; 23 5、炉衬侵蚀量为铁水量的0.15%; 6、氧气成分为98.9% O,1.5% N。 22 表2-1-5 反应放出热 kcal/kg C(FeC)+1/2O=CO 2616.9 32 C(FeC)+1/2O=CO 8250.7 322 Si(FeSi)+O=SiO 6767.2 322
烧结物料平衡计算4
烧结物料平衡计算 关键词:烧结物料平衡 1.1燃烧反应 烧结过程中进行着一系列复杂的物理化学变化,这些变化的依据是一定的温度和热量 需求条件,而创造这种条件的是混合料中碳的燃烧。混合料中的碳在温度达到700℃以上即 着火燃烧,发生以下凹种反应: C+O2=C02△H=-33500kj/mol△Go=-395350-0.54T(1-1)2C+O2=2CO△H=-9800kg/mol△Go=一228800-171.547T(1-2) 2CO+O2=2CO2△H=-23700kJ/mol△Go=-561900十170.46T(1-3) CO2+C=2CO△H=13800N/k8△Go=l66550-171.02T(1-4) 在烧结过程户,反应(2j1)易发生,在高温区有利于(2—2)和(2—4)进行,但由于燃烧层薄,废气经过预热层温度很快下降,所以它们受到限制,但是在混合料中燃料粒度过细,配碳过多而且偏析较大时,此类反应仍有一定程度的发展。反应(2—3)在烧结过程的低温区易于进行。总的来说,烧结废气个以CO:为主,有少量的CO,还有一些自出氧和氮。图1—1显示了烧结过程中废气成分变化 的一般规律。 图(1-1)
1.2分解反应 烧结过程中有三种分解反应发生:结晶水分解,碳酸盐分解,高价氧化物(Fe zo:,Mno2.Mn203)分解。 (1)结晶水分解。一般固溶体内的水容易在120一200℃就分解出来,以OH —根存在的针铁矿(Fe z03·H:O系y—FeO.OH),针铁矿(Fe2O3·H2O系Y —FeO.OH),水锰矿[MnO2·Mn(OH)2系MnO.OH]由于分解过程伴随有品格转变,其开始分解温度要高些约300℃左右。而脉石中的高岭土(A12O3·2SiO2·2H2O),拜来石[(Fe·AL)2O2·3SiO2·3H2O]的早格中进入了OH-,它们均需到500℃才开始分解。分解反应为吸热反应,因而用褐铁矿或强磁选和浮选的褐铁矿精矿粉烧结时,需要更多的燃料,配量一股高达9%一11%。 (2)碳酸盐分解。如果混合料中有菱铁矿,在烧结过程中比较容易分解,在300一350℃就分解了。配入混合料的熔剂白云石和石灰石的分解与废气小的cO 2分压有关。根据烧结废气户CO2含量变化(图1-2)和总压88.3kPa(0.9趾)的条件,可以得出白云石和石灰石开始分解的温度相应为720℃和809℃。沸腾分解温度为910℃。溶剂的分解过程示与图(1-2)。
热平衡计算
热平衡计算 热平衡计算 1.热平衡原理 要使通风房间温度保持不变,必须使室内的总得热量等于总失热量,即。 在通风过程中,室内空气通过与进风、排风、围护结构和室内各种高低温热源进行交换,为了使房间内的空气温度保持不变,必须使房间内的总得热量∑Qd与总失热量∑Qs相等,也就是要保持房间内的热平衡。即热平衡:∑Qd=∑Qs。 通风房间内的得热与热量如图3-2-7所示。随工业厂房的设备、产品及通风方式的不同,车间得热量、失热量差别较大。一般通过高于室温的生产设备、产品、采暖设备及送风系统等取得热量;通过围护结构、低于室温的生产材料及排风系统等损失热量。 图3-2-7 通风房间内的得热与热量模型 在使用机械通风,又使用再循环空气补偿部分车间热损失的车间中,热平衡的等量关系如图3-2-8所示。
图3-2-8 热平衡的等量关系 由图3-2-8的热平衡等量关系,即的通风房间热平衡方程式为: (3-2-16) 式中——围护结构、材料吸热的总失热量,kW; ——生产设备、产品及采暖散热设备的总放热量,kW; Lp——局部和全面排风风量,m3/s; Ljj——机械进风量,m3/s; Lzj——自然进风量,m3/s; Lhx——再循环空气量,m3/s; pu ——室内空气密度,kg/ m3; Pw——室外空气密度,kg/ m3; tu——室内排出空气湿度,℃; tjj——机械进风湿度,℃; to——再循环送风温度,℃; c——空气的质量比热,其值为1.01kj/kg·℃; tw——室外空气计算湿度,℃, tw的确定:在冬季,对于局部排风及稀释有害气体的全面通风,采用冬季采暖室外计算湿度。对于消除余热、余湿及稀释低毒性有害物质的全面通风,采用冬季通风室外计算温度是指历年最冷月平均温度的平均值。 通风房间的风量平衡、热平衡是风流运动与热交换的客观规律要求,设计时应根据通风要求保证满足设计要求的风量平衡与热平衡。如果实际运行时所达到的新平衡状态与设计要求的平
湖南师范大学2018年硕士研究生《区域经济学》复试科目考试大纲
湖南师范大学2018年硕士研究生《区域经济学》复试科目考试大纲 一、考试形式与试卷结构 1)考试时间 本试卷考试时间为180分钟。 2)答题方式 答题方式为闭卷、笔试。 3)试卷内容结构 各部分内容所占分值为: 区域经济学基础知识约80% 区域经济分析方法约20% 4、题型结构 名词解释题:6小题,各计5%,共计30% 简答题:4小题,各计10%,共计40% 分析论述题:2小题,各计15%,共计30% 二、考试目标、考试内容与考试要求 考试目标: 1、掌握基础知识,理解基本概念; 2、掌握区域经济学理论,并能用理论解释区域经济现实问题; 3、掌握区域分析方法,能用定量模型分析区域经济问题 考试内容: 一、区域经济学基础知识 (一)区域经济学概论 区域经济学的基本概念、区域的含义和区域的划分标准、区域经济中的行为主体及其各行为主体之间的关系。 区域经济学的研究对象、区域经济学研究的若干主要问题、区域经济理论的主要内容。 (二)企业区位选择理论 区位分析的基本原理:新古典学派(其基本假设和主要观点、对新古典学派的批评);行为科学学派(其主要分析方法和主要内容、启迪式过程、对行为科学派的批评);结构学派(其主要代表人物和主要内容)。 区位选择因素:潜在的重要区位因素、区位因素的重要性、区位因素的差别、区位因素的历史发展过程。 新古典区位理论:运输费用的作用、运输费用紧小的区位、区域垄断的形成及其稳定性。 (三)区位模式和区位结构理论 分散和集中的区位模式、中心地理论(市场区边界、最佳市场区的形成、中心地体系、中心地结构的变化、廖什的解释、局限性)、勃温特对区位结构理论的整合。 聚集效应的经济学分析:内部效应、外部效应、局部化效应和城市化效应、外部效应与帕累托效率、最佳城市规模。 (四)区域产业结构理论 产业定义的基础(贝恩的观点:需求的可替代性)、产业的分类、产业集中度的测度方法和指标、区域产业结构演变的一般规律、配第—克拉克定理、库兹涅茨关于产业结构变动的观点、霍夫曼的工业化阶段理论、赤松要的“雁行原理”、区域产业结构演变的诱因和机制。 区域主导产业选择的理论、筱原三代平提出的主导产业选择基准、主导产业的选择方法、区位商的计
锅炉热平衡综合实验
锅炉热平衡综合实验 一、实验目的 锅炉热平衡试验的目的是测定锅炉的效率及各种热损失。在新锅炉安装结束后的移交验收鉴定试验中、锅炉使用单位对新投产锅炉按设计负荷试运转结束后的运行试验中、改造后的锅炉进行热工技术性能鉴定试验中、大修后的锅炉进行检修质量鉴定和校正设备运行特性的试验中以及运行锅炉由于燃料种类变化等原因进行的燃烧调整试验中,都必须进行热平衡试验。按热平衡试验进行的方式又可分为正平衡及反平衡试验。通过本实验。 1、了解热平衡实验系统的组成; 2、掌握锅炉给水温度、压力、流量、排烟温度、灰渣质量、灰渣中可燃物含量、烟气成分等的测量方法,通过分析误差原因,学习减小误差的方法; 3、掌握锅炉各项热损失的计算方法; 4、掌握锅炉正、反平衡实验的方法和步骤。 二、实验原理 锅炉热效率测定实验的基本原理就是锅炉在稳定工况下进出热量的平衡。 1、锅炉热平衡 锅炉工作是将燃料释放的热量最大限度的传递给汽水工质,剩余的没有被利用的热量以各种不同的方式损失掉了。在稳定工况下,其进出热量必平衡,可表示如下: 输入锅炉热量=锅炉利用热量+各种热损失 Q(kJ/kg)或100(%)表示。 锅炉输入热量以 r 锅炉热损失包括以下几项:
(1) 排烟热损失2Q (kJ/kg)或2q (%); (2) 机械未完全燃烧热损失4Q (kJ/kg)或4q (%)。链条炉包括:炉渣机械未完全燃烧热损失4lz Q 、4lz q ,飞灰机械未完全燃烧热损失4fh Q 、4fh q 与漏煤机械未完全燃烧热损失4 lm Q 、4lm q 等三项; (3) 化学未完全燃烧热损失3Q (kJ/kg)或3q (%); (4) 锅炉向环境散热热损失5Q (kJ/kg)或5q (%); (5) 灰渣物理热损失等其他热损失6Q (kJ/kg)或6q (%)。 国家标准GB/T -2587-1981规定:热平衡基准温度建议为环境温度;燃料发热量规定用收到基的低位发热量y DW Q 。 根据锅炉热平衡概念,可画出锅炉热平衡图如图1所示。 2、锅炉热效率 锅炉热效率为锅炉利用热量1Q 占输入热量r Q 的百分数,用gl η(%)表示。它可由输入-输出热量法或热损失法通过实验求得。 输入-输出热量法: 1 100gl r Q Q η= ? % (1) 热损失法: gl η=100-(2q +3q +4q +5q +6q ) % (2) 工业锅炉的测量误差是在额定负荷下两次热效率实验之间的偏差,对于输入-输出热量法不得大于4%,而对于热损失法不得大
转炉物料平衡计算
转炉炼钢课程设计 题目转炉物料平衡和热平衡计算及 转炉炉型设计计算 姓名何一依 学号 1076803438 班级 10冶金4班 指导教师王海鸥 学院国际学院
一、转炉物料平衡和热平衡计算 1. 物料平衡计算 1.1 计算原始数据 基本原始数据有:冶炼钢种及成分、铁水和废钢的成分、终点钢水成分(表1-1);造渣用溶剂及炉衬等原材料成分(表1-2);脱氧和合金化用铁合金的成分及回收率(表1-3);其他工艺参数(表1-4)。 表1-2 原材料成分 表1-3 铁合金成分(分子)及其回收率(分母)
表1-4 其他工艺参数设定值 1.2物料平衡的基本项目 收入项有:铁水、废钢、溶剂(石灰、萤石、轻烧白云石)、氧气、炉衬蚀损、铁合金。 支出项有:钢水、炉渣、烟尘、渣中铁珠、炉气、喷溅。 1.3 计算步骤 以100㎏铁水为基础进行计算。 第一步:计算脱氧和合金化前的总渣量及其成分。 总渣量包括铁水中元素氧化,炉衬腐蚀和加入溶剂的成渣量。其各项成渣量分别列于表1-5到表1-7。总渣量及成分如表1-8所示:
表1-5 铁水中元素的氧化产物及其成渣量 ①由CaO还原出的氧量;消耗CaO量=0.009×56/32=0.016㎏。 表1-6 炉衬蚀损的成渣量 表1-7 加入溶剂的成渣量 (SiO2)=1.286+0.006+0.016+0.013=1.321㎏;因设定终渣碱度R=3.5,故石灰加入量为: 3.299/(88.0%-3.5×2.50%)= 4.16㎏ ②.石灰加入量=(石灰中CaO含量)-(石灰中S→CaS自耗的CaO量)
表1-8 总渣量及其成分 第二步:计算氧气消耗量。 氧气的实际消耗量系消耗项目与供入项目之差。见表1-9 表1-9 实际耗氧量 第三步:计算炉气量及其成分。 炉气中含有CO 、CO 2、N 2、SO 2和H 2O.其中CO 、CO 2、SO 2和H 2O 可由表1-5~表1-7查得,O 2和N 2则由炉气总体积来确定。现计算如下: 炉气总体积V ∑ g s x 122.4 =+0.5%++0.5%-) 99.632V V V G V V ∑∑ ∑( ①.表中除(FeO)和(Fe2O3)以外的总渣量为5.11+1.428+1.056+0.123+0.284+0.262+0.123+0.03= 8.416㎏,而终渣Σω(FeO)=15%(表1-4),故总渣量为8.416/86.75%=9.701㎏。 ②.ω(FeO)=9.701×8.25%=0.8㎏ ω(Fe2O3)=9.701×5%-0.002=0.483㎏
干燥过程的物料平衡与热平衡计算
干燥过程的物料与热平衡计算 1、湿物料的含水率 湿物料的含水率通常用两种方法表示。 (1)湿基含水率:水分质量占湿物料质量的百分数,用ω表示。 100%?= 湿物料的总质量 水分质量 ω (2)干基含水率:由于干燥过程中,绝干物料的质量不变,故常取绝干物料为基准定义水分含量。把水分质量与绝干物料的质量之比定义为干基含水率,用χ表示。 100%?= 量 湿物料中绝干物料的质水分质量 χ (3)两种含水率的换算关系: χ χ ω+= 1 ω ω χ-= 1 2、湿物料的比热与焓 (1)湿物料的比热m C 湿物料的比热可用加与法写成如下形式: w s m C C C χ+= 式中:m C —湿物料的比热,()C kg J ?绝干物料/k ; s C —绝干物料的比热,()C kg J ?绝干物料/k ; w C —物料中所含水分的比热,取值4、186()C kg J ?水/k (2)湿物料的焓I ' 湿物料的焓I '包括单位质量绝干物料的焓与物料中所含水分的焓。(都就是以0C 为基准)。 ()θθχθχθm s w s C C C C I =+=+='186.4 式中:θ为湿物料的温度,C 。
3、空气的焓I 空气中的焓值就是指空气中含有的总热量。通常以干空气中的单位质量为基准称作比焓,工程中简称为焓。它就是指1kg 干空气的焓与它相对应的水蒸汽的焓的总与。 空气的焓值计算公式为: ()χ1.88t 24901.01t I ++= 或()χχ2490t 1.881.01I ++= 式中;I —空气(含湿)的焓,绝干空气kg/kg ; χ—空气的干基含湿量,绝干空气kg/kg ; 1、01—干空气的平均定压比热,K ?kJ/kg ; 1、88—水蒸汽的定压比热,K ?kJ/kg ; 2490—0C 水的汽化潜热,kJ/kg 。 由上式可以瞧出,()t 1.881.01χ+就是随温度变化的热量即显热。而χ2490则就是0C 时kg χ水的汽化潜热。它就是随含湿量而变化的,与温度无关,即“潜热”。 4、干燥系统的物料衡算 干燥系统的示意图如下: (1)水分蒸汽量W 按上述示意图作干燥过程中的0水量与物料平衡,假设干燥系统中无物料损失,则: 2211χχG LH G LH +=+ 水量平衡 G 1
发动机热平衡试验方法
编号: 柴油机热平衡试验方法 单位: 发动机部 编制: 李建华 日期: 2005年9月26日 审核: 日期: 批准: 日期: 东风汽车有限公司商用车研发中心
1 发动机热平衡试验的作用 发动机的热平衡试验是分析进入发动机的燃油燃烧产生的总热量的去向。其作用主要有: a. 根据发动机的有效输出功率,评价发动机的热效率。 b. 评价发动机冷却系统设计、制造水平。 c. 评价发动机冷却系统主要参数。如水泵的流量,发动机冷却液进口和出口温度等。 d. 为整车冷却系统主要参数的选定提供依据。如散热器的散热面积,冷却管路的截面积,风扇直径、风量等参数。 2 进入发动机的燃油燃烧产生的热量的去向 2.1 燃烧产生的总热量Q总的去向分布 图1是进入发动机的燃油燃烧产生的总热量Q总的去向分布图。对于增压中冷发动机,Q总的去向有五个部分: l 转化为有效功的热量Qe l 排气排出的热量Q排气 l 冷却液带走的热量Q冷却液 l 进气中冷带走的热量Q中冷 l 残余热量Q残余 2.2 发动机热平衡方程 发动机热平衡方程: Q总=Qe+Q排气+Q冷却液+Q中冷+Q残余 热平衡方程中的各项,用占燃料燃烧产生的总热量Q总的百分比表示,则有: qe+q排气+q冷却液+q中冷+q残余=100% 2.3 热平衡方程中各项的含义 表1 名称、符号、单位及计算公式 QQ残余 图1 燃烧产生的总热量Q总的去向分布图
14 燃油质量流量 G燃油 kg/s G燃油=Gf/3600 计算 15 燃料低热值 Hu kJ/kg 参考值:42780 常数 16 排气流量 G排气 kg/s G排气=G进气+G燃油 计算 17 涡轮出口排气温度 T涡轮出口 ℃ 实测 18 环境温度 T环 ℃ 实测 19 排气的比定压热容 Cp排气 kJ/(kg·℃) 参考值:1.09924 常数 20 冷却液流量 G冷却液 L/min 实测 21 发动机出水温度 T出水 ℃ 实测 22 发动机进水温度 T进水 ℃ 实测 23 冷却液的比定压热容 Cp冷却液 kJ/(L·℃) 参考值:3.670 常数 24 发动机进气质量流量 G进气 kg/s 实测 25 中冷器进口处进气温度 T中冷前 ℃ 实测 26 中冷器出口处进气温度 T中冷后 ℃ 实测 27 进气的比定压热容 Cp进气 kJ/(kg·℃) 参考值:1.000 常数 3 热平衡试验方法 3.1 需要测量的试验参数和对测量精度的要求 表2需要测量的试验参数和对测量精度的要求 序号 参数 符号 单位 测量精度要求 1 燃油消耗量 Gf kg/h ±0.12% 2 发动机进气质量流量 G进气 kg/s 流量>0.1kg/s时,±2.4% 流量≤0.1kg/s时,±5% 3 冷却液流量 G冷却液 L/min ±2.5L/min 4 环境温度 T环 ℃ 5 中冷器进口处进气温度 T中冷前 ℃ 6 中冷器出口处进气温度 T中冷后 ℃ 7 发动机出水温度 T出水 ℃ 8 发动机进水温度 T进水 ℃ 9 涡轮出口排气温度 T涡轮出口 ℃ ±0.13℃ 3.2 对试验一般条件的控制 试验条件的控制和试验时发动机所带的附件,按GB/T 18297-2001 《汽车发动机性能试验方法》中总功率试验执行。 3.3 试验方法 按GB/T 18297-2001 《汽车发动机性能试验方法》进行总功率试验。除了正常测量记录的数据外,必须测量表2中列出的需要实测的值。 在每个试验工况,必须在发动机达到热平衡以后才能测量数据。发动机进、出水温度差值T 出水 -T 进水 的波动不超过 0.1℃/min时,认为发动机达到了热平衡。 在测量发动机冷却液流量时,要考虑除气管(见图2)
转炉物料平衡与热平衡计算
氧气转炉炼钢物料平衡计算与热平衡计算 1物料平衡计算 1.1计算原始数据 基本原始数据铁水和废钢成分、终点钢水成分(表1);造渣用溶剂及炉衬等原材料的成分(表2);脱氧和合金化用铁合金的成分及其回收率(表3);其他工艺参数(表4) 表合金成分及其回收率 2
表 其他工艺参数设定值 1.2物料平衡基本项目: 收入项目:收入量=铁水+废钢+溶剂+氧气+炉衬蚀损+合金 支出项目:支出量=钢水+炉渣+烟尘+渣中铁珠+炉气+喷溅。 1.3计算步骤 以100kg铁水为基础进行计算。 第一步:计算脱氧和合金化前的总渣量及其成分。 总渣量包括铁水中元素氧化,炉衬蚀损和加入溶剂的成渣量。其各项成渣量分别列于表5 表7。总渣量及其成分如表8所示。 第二步:计算氧气消耗量。 氧气实际消耗量系消耗项目与供入项目之差。见表9.
表 铁水中元素的氧化产物及其成渣量 表炉衬蚀损的成渣量 石灰加入量计算如下:由表7-5—表7-7可知,渣中已含(CaO) =-0.014+0.004+0.002+0.910=0.902kg ;渣中已含(SiO2) =1.50+0.009+0.028+0.020=1.557kg。因设定的终渣碱度 R=3.5 ,故石灰加入量为:[R E Q(SiO2)- E Q(CaO)]/[3 (CaO 石灰)-R )]=(3.5X 1.557-0.902)/ (88%-3.5 X 2.5%)=5.73kg。 X3 (SiO 2石灰 由CaO还原岀来的氧量,计算方法同表 5的注
表 总渣量及成分 ① 由表 1-8 知,除 FeO 和 Fe 2O 3 外的渣量 6.799+1.724+1.052+0.137+0.63+0.44+0.63+0.028=11.56kg 而终渣刀 w (FeO) =15% (表 1-4),故渣的总量 11.56-86.75%=13.326kg 。 ② 所以,w (FeO) =13.326 X 8.25%=1.099kg ③ w(Fe 2O 3)= 13.066 X 5%-0.033-0.005-0.008=0.620kg 表9实际耗氧量 2
回转窑系统热平衡计算资料
回转窑系统热平衡计算 1 热平衡计算基准、范围及原始数据 1.1 热平衡计算基准 物料基准:一般以1kg 熟料为基准; 温度基准:一般以0℃为基准; 1.2 热平衡范围 热平衡范围必须根据回转窑系统的设计或热工测定的目的、要求来确定。在回转窑系统设计时,其平衡范围,可以回转窑、回转窑加窑尾预热分解系统、或再加冷却机和煤磨作平衡范围。范围选得大,则进出口物料、气体温度较低,数据易测定或取得,但往往需要的数据较多,计算也烦琐。因此一般选回转窑加窑尾预热分解系统作为平衡范围。 1.3 原始数据 根据确定的计算基准和平衡范围,取得必要的原始数据,这是一项非常重要的工作。计算结果是否符合实际情况,主要取决于所选用的数据是否合理。对新设计窑或改造窑来说,主要是根据同类型窑的生产资料,结合工厂具体条件和我国实际情况、合理地确定各种参数;对于生产窑来说,主要通过热工测定取得实际生产中各种参数。若以窑加窑尾预热系统为平衡范围,一般要取得如下原始数据:生料用量、化学组成、水分、入窑温度;燃料成分、工业分析和入窑温度;一、二次空气的比例和温度;空气过剩系数、漏风系数;废气温度;飞灰量、灰温度及烧失量;收尘器收尘效率;窑体散热损失;熟料形成热等等。熟料形成热可根据熟料形成过程中的各项物理化学热效应求得,也可用经验公式计算或直接选定。 2 物料平衡与热量平衡 计算方法与步骤说明于下: 窑型:预分解窑 基准:1kg 熟料;0℃ 平衡范围:窑+预热器系统 根据确定的平衡范围,绘制物料平衡图和热量平衡图,如图1和图2所示。 图1 物料平衡图 图2 热量平衡图
2.1 物料平衡计算 2.1.1 收入项目 (1)燃料消耗量 m r (kg/kg 熟料) 设计新窑或技术改造时,m r 是未知量,通过热平衡方程求得,已生产的窑,通过热工测定得到。 (2)入预热器物料量 ① 干生料理论消耗量 s ar r gsL 100100L a A m m --= 式中,m gsL —干生料理论消耗量,kg/kg 熟料;A ar —燃料收到基灰分含量,%;a —燃料灰分掺入熟料中的量,%;L s —生料的烧失量,%。 ② 入窑回灰量和飞损量 ηfh yh m m = )1(fh Fh η-=m m 式中,m yh —入窑回灰量,kg/kg 熟料;m fh —出预热器飞灰量,kg/kg 熟料;m Fh —出收尘器飞灰损失量,kg/kg 熟料;η—收尘器、增湿塔综合收尘效率,%。 ③ 考虑飞损后干生料实际消耗量 s fh Fh gsL gs 100100L L m m m --?+= 式中,m gs —考虑飞损后干生料实际消耗量,kg/kg 熟料;L fh —飞灰烧失量,%。 ④ 考虑飞损后生料实际消耗量 s gs s 100100W m m -?= 式中,m s —考虑飞损后生料实际消耗量,kg/kg 熟料;W s —生料中水分含量,%。 ⑤ 入预热器物料量 yh s m m +=入预热器物料量(kg/kg 熟料) (3)入窑系统空气量 ① 燃料燃烧理论空气量 )O 0.033(S 0.267H 0.089C ar ar ar ar LK -++='V LK LK 293.1V m '='
热平衡路试实验大纲知识分享
热平衡路试实验大纲
整车热平衡路试实验大纲 1.适用范围 2.本实验大纲适用于标杆车及样车测定汽车热平衡能力的道路试验方法。 本实验大纲适用于同时装有强制循环液冷式发动机和具有手动挡功能变速器的各类汽车,其他类型的汽车也参照执行 3.实验依据 4. 2.1 GB/T 12542-2009 《汽车热平衡能力道路实验验证方法》 2.2 GB/T 12534 《汽车道路实验方法通则》 2.3 GB/T 18297-2001《汽车发动机性能实验方法》 3. 整车热平衡实验相关术语和定义 a)环境温度:汽车行驶时周围环境阴影下1.5m高处的空气温度。 b)冷却介质:起冷却作用的物质,包括发动机冷却液、发动机润滑油、变速器润滑油、驱动桥润滑油等。本试验中只对发动机冷却液和发动机润滑油的温度进行测量。 c) 热平衡:系统(零部件、总成、汽车)各部分温度与环境温度的差值达到 稳定状态。 d) 汽车热平衡:汽车动力总成(发动机、变速器、驱动桥)热平衡。 e) 冷却常数:汽车热平衡时冷却介质温度与环境温度的差值。 f)冷却介质许用最高温度:汽车动力总成(发动机、变速器、驱动桥)正常工 作所允许的冷却介质最高温度(由生产厂给定)。 g) 极限使用工况:汽车低档位、全油门长时间输出最大扭矩或最大功率的
情况。 h) 常规使用工况:汽车高速行驶、高速爬坡、长时间怠速等汽车常见使用工况。 i) 极限使用许用环境温度:极限使用工况下汽车受冷却介质许用最高温度的限制而允许使用的最高环境温度。 j) 常规使用许用环境温度:常规使用工况下汽车受冷却介质许用最高温度的限制而允许使用的最高环境温度。 4. 实验条件及所需工具 4.1 无雨、无雾,环境温度不低于30℃,风速不大于3m/s。如果环境温度低 于30℃,则应详细记录实验时的环境温度、湿度、大气压力等气象参数。 4.2 实验道路按GB/T 12534 的规定,要求路面坚硬、平坦、清洁、干燥,用 混凝土或者沥青铺装,要有足够长的高速跑道,纵坡度小于0.1%。 4.3 轮胎充气压力对实验数据的准确性有较大影响。在进行实验之前应使汽 车轮胎充气压力在冷态的时候符合该车的技术条件规定,误差不得超出± 10Kpa。 4.4 在实验过程中被试车辆所用的燃料、机油及冷却液应符合该车技术条件或现行国家标准的规定,采用制造厂规定的牌号。 4.5有挡风效果的“十”字挡风墙,一般长4m、高2.5米,参见附录A。 4.6 实验用主要仪器设备见表1。 表1
转炉物料平衡与热平衡计算
钢铁冶金专业设计资料(炼铁、炼钢) 本钢工学院冶化教研室 二00 三年八月
第一章物料平衡与热平衡计算 物料平衡和热平衡计算是氧气顶吹转炉冶炼工艺设计的一项基本的计算,它是建立在物质和能量不灭定律的基础上的。它以转炉作为考察对象,根据装入转炉内或参与炼钢过程的全部物料数据和炼钢过程的全部产物数据,如图1-1-1所示的收入项数据和支出项数据,来进行物料的重量和热平衡计算。通过计算,可以定量地掌握冶炼工重要参数,做到“胸中有数”。对指导生产和分析研究改进冶炼工艺,设计转炉炼钢车间等均有其重要意义。由于转炉炼钢过程是一个十分复杂的物理化学过程,很显然,要求进行精确的计算较为困难,特别是热平衡,只能是近似计算,但它仍然有十分重要的指导意义。 物料平衡和热平衡计算,一般可分为两面种方案。第一种方案是为了设计转炉及其氧枪设备以及相应的转炉炼钢车间而进行的计算,通常侧重于理论计算,特别是新设计转炉而无实际炉型可以参考的情况下;另一种方案是为了校核和改善已投产的转炉冶炼工艺参数及其设备参数或者采用新工艺新技术等,而由实测数据进行的计算,后者侧重于实测。本计算是采用第一种方案。 目前,我国顶吹转炉所采用的生铁基本上为低磷的(0.10?0.40%)和中磷 的(0.40?1.00%)两种,对这两种不同含磷量生铁的冶炼工艺制度也不相同。因此,下面以50吨转炉为例,分别就低磷生铁和高磷生铁两种情况,进行物料平衡和热平衡计算。 1.1原始数据 1.1.1铁水成分及温度
表1-1-2原材料成分 转炉冶炼钢种常为普通碳素钢和低合金钢,在此以要求冶炼3钢考虑,其成分见表
1.1.4平均比热 表1-1-4 冷却剂 用废钢作冷却剂,其成份与冶炼钢种成份的中限相同。(见表1-1-3) 1.1.6反应热效应 虽然炉内化学反应,实际上是在炉料温度和炉内上部气相温度之间的任一温度发生的,但反应热效应通常仍采用25C作为参考温度,值得指出的是,反应热还与组分在铁水中存在形态有关,至今对参与化学反应有关的实际组成物还有不同的看法。但是,比较常用的反应热数据见表1-1-5。