线切割程序编制与机床操作培训资料
数控机床编程与操作第三版电加工机床分册第二章 数控线切割机床基本操作

第一节 数控线切割机床概述
二、数控线切割机床主要技术参数
数控电火花线切割机床的主要 技术参数包括工作台行程(纵向行 程×横向行程)、最大切割厚度、 加工表面粗糙度值、加工精度、切 割速度、加工锥度和数控系统的控 制方式等。DK77系列数控电火花线 切割机床的主要型号及技术参数见 表。
12 第 二 章 数 控 线 切 割 机 床 基 本 操 作
4.工作液循环系统
在线切割加工中,工作液对 加工工艺指标的影响很大,如对 切割速度、表面粗糙度、加工精 度等都有影响。在线切割加工中 工作液是循环使用的,工作液循 环系统由工作液箱、工作液泵、 流量控制系统、连接导管和上、 下水嘴等组成,如图所示。
10 第 二 章 数 控 线 切 割 机 床 基 本 操 作
开机操作过程
19 第 二 章 数 控 线 切 割 机 床 基 本 操 作
第一节 数控线切割机床概述
1.开机、关机 关机操作过程见表。
关机操作过程
20 第 二 章 数 控 线 切 割 机 床 基 本 操 作
第一节 数控线切割机床概述
2.手控盒操作 手控盒可以控制电极丝的启停、
工作液的开关、工作台的移动等。 线切割机床手控盒如图所示。
(4)正式加工工件前,应确认工件位置正确,以防工件碰撞丝架或 因超载碰坏丝杠、螺母等传动部件。
(5)加工时打开安全开关,将导轮及工作台防护罩安装好后方可进 行放电加工。
(6)禁止用湿手按开关或接触电气部分,防止工作液等导电物进入 电气部分。
27 第 二 章 数 控 线 切 割 机 床 基 本 操 作
二、设备的维护保养方法
(6)机床防尘罩上不要放置重物,不要随意拆卸机床。如果需要拆 卸,应防止灰尘落入。
第6章 数控电火花线切割机床的程序编制
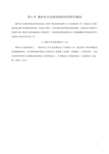
第6章数控电火花线切割机床的程序编制数控电火花线切割机床利用电蚀加工原理,采用金属导线作为工具电极切割工件,以满足加工要求。
机床通过数字控制系统的控制,可按加工要求,自动切割任意角度的直线和圆弧。
这类机床主要适用于切割淬火钢、硬质合金等金属材料,特别适用于一般金属切削机床难以加工的细缝槽或形状复杂的零件,在模具行业的应用尤为广泛。
6.1数控电火花线切割加工工艺数控电火花线切割加工,一般是作为工件尤其是模具加工中的最后工序。
要达到加工零件的精度及表面粗糙度要求,应合理控制线切割加工时的各种工艺参数(电参数、切割速度、工件装夹等),同时应安排好零件的工艺路线及线切割加工前的准备加工。
有关模具加工的线切割加工工艺准备和工艺过程,如图6.1所示。
图6.1线切割加工的工艺准备和工艺过程6.1.1模坯准备1、工件材料及毛坯模具工作零件一般采用锻造毛坯,其线切割加工常在淬火与回火后进行。
由于受材料淬透性的影响,当大面积去除金属和切断加工时,会使材料内部残余应力的相对平衡状态遭到破坏而产生变形,影响加工精度,甚至在切割过程中造成材料突然开裂。
为减少这种影响,除在设计时应选用锻造性能好、淬透性好、热处理变形小的合金工具钢(如Cr12、Cr12MoV、CrWMn)作模具材料外,对模具毛坯锻造及热处理工艺也应正确进行。
2、模坯准备工序模坯的准备工序是指凸模或凹模在线切割加工之前的全部加工工序。
(1)凹模的准备工序1)下料用锯床切断所需材料。
2)锻造改善内部组织,并锻成所需的形状。
3)退火消除锻造内应力,改善加工性能。
4)刨(铣)刨六面,并留磨削余量0.4~0.6mm。
5)磨磨出上下平面及相邻两侧面,对角尺。
6)划线划出刃口轮廓线和孔(螺孔、销孔、穿丝孔等)的位置。
7)加工型孔部分当凹模较大时,为减少线切割加工量,需将型孔漏料部分铣(车)出,只切割刃口高度;对淬透性差的材料,可将型孔的部分材料去除,留3~5mm切割余量.8)孔加工加工螺孔、销孔、穿丝孔等。
数控线切割机床的操作与编程
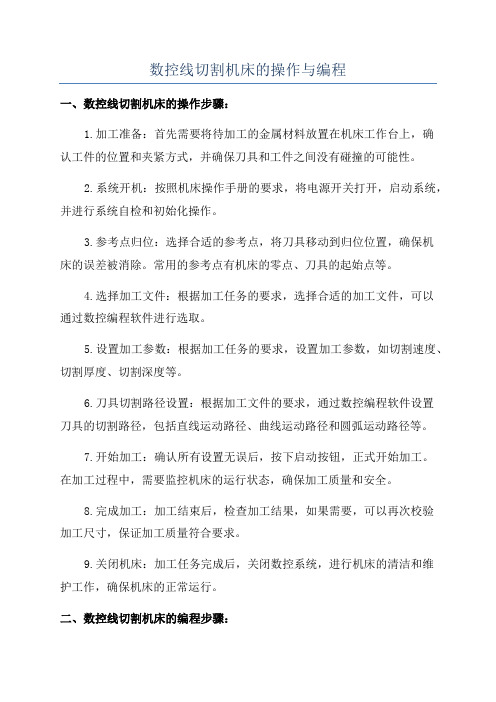
数控线切割机床的操作与编程一、数控线切割机床的操作步骤:1.加工准备:首先需要将待加工的金属材料放置在机床工作台上,确认工件的位置和夹紧方式,并确保刀具和工件之间没有碰撞的可能性。
2.系统开机:按照机床操作手册的要求,将电源开关打开,启动系统,并进行系统自检和初始化操作。
3.参考点归位:选择合适的参考点,将刀具移动到归位位置,确保机床的误差被消除。
常用的参考点有机床的零点、刀具的起始点等。
4.选择加工文件:根据加工任务的要求,选择合适的加工文件,可以通过数控编程软件进行选取。
5.设置加工参数:根据加工任务的要求,设置加工参数,如切割速度、切割厚度、切割深度等。
6.刀具切割路径设置:根据加工文件的要求,通过数控编程软件设置刀具的切割路径,包括直线运动路径、曲线运动路径和圆弧运动路径等。
7.开始加工:确认所有设置无误后,按下启动按钮,正式开始加工。
在加工过程中,需要监控机床的运行状态,确保加工质量和安全。
8.完成加工:加工结束后,检查加工结果,如果需要,可以再次校验加工尺寸,保证加工质量符合要求。
9.关闭机床:加工任务完成后,关闭数控系统,进行机床的清洁和维护工作,确保机床的正常运行。
二、数控线切割机床的编程步骤:1.绘制加工轮廓:在数控编程软件中,通过绘制加工轮廓来描述加工的形状和尺寸。
可以采用CAD软件,也可以直接在数控编程软件中进行绘制。
2.选择切割路径:根据绘制的加工轮廓,选择切割路径,包括直线、曲线和圆弧等不同的运动方式。
3.确定切割参数:根据加工任务的要求,确定切割参数,包括切割速度、切割厚度、切割深度等。
4.编写切割程序:根据选择的切割路径和切割参数,编写切割程序,通过数控编程语言进行描述。
常用的数控编程语言有G代码和M代码。
5.设置初始参数:在切割程序中,需要设置初始参数,包括刀具的起始位置、刀具的切削方向和切削方式等。
6.检查和修改程序:编写完切割程序后,需要进行检查和修改,确保程序的正确性和可靠性。
线切割机床操作基础

BKDC 7740 线切割操作说明于修君一、线切工作原理电火花线切割机床采用电极丝(钼丝、钨钼丝等)作为工具电极,在脉冲电源作用下,工具电极和加工工件之间形成火花放电,火花通道瞬间产生大量的热,使得工件表面熔化甚至汽化。
线切割机床通过X-Y拖板和U-V拖板的运动,使电极丝沿着预定的轨迹运动,从而达到加工工件的目的。
应用:铣削加工无法完成的内外轮廓形状,异型,硬度较高材料1、线切割机床坐标系X-Y:机床上说明正方向U-V:2、机床组成:1)、控制机:2)、机床:丝杠步进电机、导轨、运丝系统装置等。
二、BKDC线切割机床的基本操作BKDC线切割机床的绝大部分操作都是在一副键盘上进行的。
而且所有的操作屏幕都有提示,因此BKDC的操作相对比较简单。
2.1控制机的开启与关闭将位于控制机左侧的电源总开关按下ON按钮,按下控制机面板上的白色灯按钮,控制机进入复位和自动检测,然后控制机屏幕显示版本信息进入欢迎屏幕(图2.1),用户按因意键后进入主菜单(图2.3),按下绿色按钮,按回车键,系统进入正常工作状态。
在系统工作过程中,用户如果按下急停按钮(红色蘑菇头),系统将有提示出现,等待用户操作。
用户需要关闭控制机时,可以首先按下电源关按钮(红色按钮),然后按下电源总开关的OFF按钮。
2.2控制机的屏幕划分在BKDC的工作过程中,各种信息在屏幕上都有自己特定的位置,整个屏幕的显示如图2.2所示:(1)图形显示、数据文件及其它有关信息;(2)显示坐标和其它有关信息;(3)显示当前几何参数和电气参数;(4)显示系统提示信息、指导用户操作;(5)显示操作结果、告诉用户操作成功或出错;(6)显示最近操作的文件名;(7)显示版本信息机菜单目前所处的位置;(8)显示当前时间。
F1-F8键是系统菜单,用户所有操作可根据菜单内容及屏幕提示选择F1-F8键或其它特殊键来实现。
2.3控制机的菜单结构BKDC控制机的菜单采用树状结构,从上往下,最上层是系统主菜单,系统主菜单如图2.3所示在主菜单下按F1-F8键就可以进入相应的菜单,如图F1则进入File菜单。
数控线切割操作工培训第6章电火花切割机床的基本操作

第6章 电火花线切割机床的基本操作
6.1电火花线切割机床的安全操作规程 (1)进入实训区必须穿合身的工作服、戴工作帽,衬衫要系入裤内,
敞开式衣袖要扎紧,女同学必须把长发纳入帽内;禁止穿高跟鞋、拖鞋、 凉鞋、裙子、短裤及戴围巾。
(2)开机前按机床说明书要求对各润滑点加油。 (3)开动机床前,要检查机床电气控制系统是否正常,工作台和传 动丝杆润滑是否充分。检查工作液是否充足,然后开慢车空转3~5min, 检查各传动部件是否正常,确认无故障后,才可正常使用。 (4)按照线切割加工工艺正确选用加工参数,按规定的操作顺序操 作。 (5)用手摇柄转动储丝筒后,应及时取下手摇柄,防止储丝筒转动 时将手摇柄摔出伤人。 (6)装卸电极丝时,注意防止电极丝扎手,卸下的废丝应放在规定 的容器内,防止造成电器 短路等故障。
数控线切割操作工培训教程
2
2020年1月16日
6.2电火花线切割机床的维护与保养 线切割机床维护和保养的目的是为了保持机床能正常可靠地工作,延长其使
用寿命。 6.2.1机床的维护
(1)整机应经常保持清洁,停机8小时以上应擦抹并涂油防锈。 (2)丝架上的导电块、排丝轮、导轮周围以及储丝筒两端应经常用煤油清 洗干净,清洗后的脏油不应流回工作台的回液槽内。 (3)钼丝电极与工件间的绝缘是由工件夹具保证的,应经常将导电块、工 件夹具的绝缘物擦抹干净,保证绝缘要求。
数控线切割操作工培训教程
8
2020年1月16日
6.4工件的装夹与校正 6.4.1工件的装夹
线切割加工,特别是慢走丝线切割加工属于较精密加工,工作的装夹对 加工零件的定位精度有直接影响,特别在模具制造等加工中,需要认真仔细 地装夹工件。
线切割加工的工件在装夹中需要注意如下几点。 (1)工件的定位面要有良好的精度,一般以磨削加工过的面作为定位基 准为好,棱边倒钝,孔口倒角。 (2)切入点要导电,热处理件切入处要去除残物及氧化皮。 (3)热处理件要充分回火去应力,平磨件要充分退磁。 (4)工件装夹的位置应利于工件找正,并应与机床的行程相适应,夹紧 螺钉高度要合适,避免干涉到加工过程,上导丝轮要压得较低。 (5)对工件的夹紧力要均匀,不得使工件变形和翘起。 (6)批量生产时,最好采用专用夹具,以利于提高生产率。 (7)对细小、精密、薄壁等工件要固定在不易变形的辅助夹具上。
培训学习资料-线切割全解
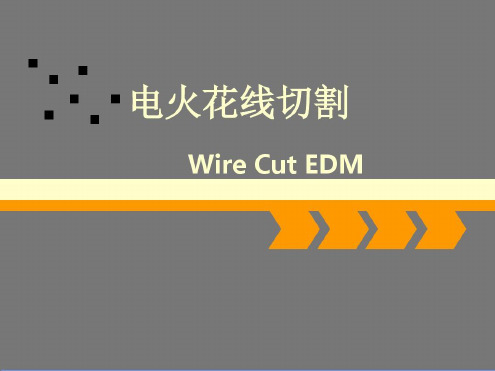
1.3电火花线切割-》-电火花线切割加工Vire Cut EDM-WEDM简称线切割加工,是在电火花加工基 -上发展起来的一种新的工艺形式全称为电火花电-极线切割工艺
1.3.1线切割加工原理-电火花线切割加工的基本原理是利用一根运动的细金-属导线(铜丝或钼丝)作工具电极, 工件与金属丝间通-以脉冲电流,靠电火花对工件进行切割加工-导轮-电源-储丝筒-电极丝-快速往复走丝机床
1.3.4线切割加工的过程
1.3.5线切割的应用-》-1微细结构和复杂型零件-复杂形面-细微结构及窄缝
2》-2高硬度导电材料、-贵重金属成型加工-高速钢车刀-☆王-硬质合金-陶瓷刀片
》-3模具型面及型腔加工-SC-残疾人运动员鞋底模具-无电车爪手模具
4微细、锥体、上下异形等零件加工-00-10-16-14-5
常见的工件电极和工具电极
1.2电火花加工原理-》-优告
电火花加工螺纹孔实例-2 sizhuiwh?cO印-优酷
》-极性效应:工具和工件的正、负极性不同而彼此电蚀量-不一样的现象叫做极性效应。(在生产中,通常把工-件接 冲电源的正极,称“正极性”加工;反之,工-件接脉冲电源的负极称“负极性”加工。-工特-电极工
1.2电火花加工-电火花加工是在一定的液体介质中,利用正负戌极间-脉冲放电时的电腐蚀现象对导电材料进行加工 从而-使零件的尺寸、形状和表面质量达到技术要求的一种-加工方法-工具电极-自动进给调节装置-<①①-工作液 过滤器-工作液泵-脉冲电源-工件-a-被蚀除的材料-T-b-c-电火花加工原理示意图
4加工过程中,工具与工件不直接接触,不存在显著-的切削力。-5由于切缝很细,而且只对工件进行轮廓加工,-实 -金属蚀除量很少,材料利用率高。-6与电火花成形相比,以线电极代替成形电极,省去-了成形工具电极的设计和制 费用,缩短了生产准备时-间。-电火花线切割加工的缺点是不能加工盲孔类零件,
线切割机床操作
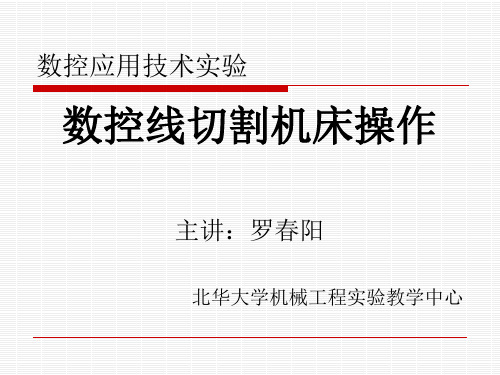
3.9设置电参数
(1)按照4.3.1.7操作过程,打开要加工的 轨迹; (2)再按键盘上的F3(电参数)按键,光 标进入电参数界面,主要有以下几种电参数: (3)通过键盘上F1~F7按键,调整电参数; (4)按键盘上的F8(退出)按后,按键盘上的F8 (退出)按键可以返回上级界面; (2)按键盘上的F7(正向割)按键,开始 切割工件。 (3)切割过程中如需要暂停加工,按键盘 上的F1(暂停)按键,可以暂停,依照提示 可以恢复加工。
3.5对边
(1)在主界面状态,按键盘上的F5(人工) 按键,进入中人工菜单; (2)再按键盘上的F6(对边)按键,进入 对边界面,选择对边方向(+X、-X、+Y、 -Y),电极丝开始向该方向移动,直到遇上 工件,检测到短路电流,拖板停止移动,对 边结束; (3)按键盘上的F8(退出)按键,返回主 界面。
3.2关机 (1)按下控制面板上的红色按钮,系统断 电; (2)断开机床主电源开关,机床断电。 3.3手动移动动作台 (1)按下控制面板上的急停按钮; (2)通过手轮控制工作台移动; (3)手动移动完毕旋出急停按钮,按下控 制面板上绿色按钮,机床恢复自动控制状态。
3.4相对动
(1)在主界面状态,按键盘上的F5(人工) 按键,进入中人工菜单; (2)再按键盘上的F3(相对动)按键,进 入相对动界面,选择移动的坐标轴,输入移 动距离; (3)通过F5/F6调整移动速度,按键盘上 的F7(移动)按键,开始移动; (4)按键盘上的F8(退出)按键,返回主 界面。
4.4生成G代码
(1)完成上一步操作,生成加工轨迹; (2)在屏幕的工具条上用鼠标选择“轨迹 后处理”按钮,再选择“生成G代码”按钮, 弹出对话框; (3)在对话框中修改G代码的保存路径为 C:\BKDC\文件名.iso,按键盘上的回车键, 再点击确定按钮,退出对话框; (4)鼠标左键点选绿色轨迹,右键确认, 出现G代码内容,点击关闭,编程完成。
线切割(快走丝)培训资料
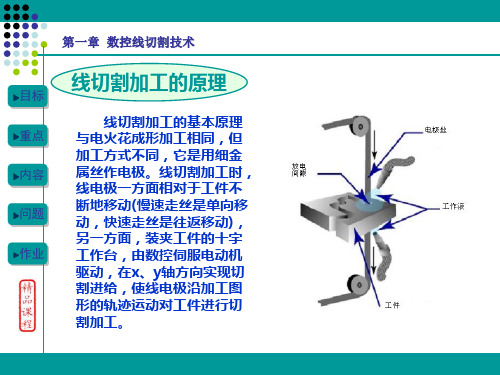
重点 丝的入口处,窄口是电极丝的出口处。
内容
问题
作业
工件
电极丝
电极丝运动引起的斜度
工件 上
下 电极丝
切缝剖面示意图
第一章 数控线切割技术
5.电极丝张力:
目标
重点 内容 问题 作业
vw / (mm2 / min) 36 30 24
5
7
9 10 张 力 / N
电极丝张力与进给速度图
第一章 数控线切割技术
内容
问题
慢速走丝线切割机床(WEDM-LS)
作业
第一章 数控线切割技术
目标 重点 内容 问题 作业
快走丝线切割机床
第一章 数控线切割技术 目标 重点 内容 问题 作业
快走丝线切割机床
第一章 数控线切割技术
目标 重点 内容 问题 作业
快走丝线切割机床
第一章 数控线切割技术 目标 重点 内容 问题 作业
割进给,使线电极沿加工图
形的轨迹运动对工件进行切
割加工。
第一章 数控线切割技术
目标 重点 内容 问题 作业
(a) 加 工 示 意 图
5
4
3
2
1 1—绝 缘 底 板 ; 2—工 件 ; 3—脉 冲 电 源 ; 4—滚 丝 筒 ; 5—电 极 丝
(b) 线 切 割 加 工 原 理 示 意 图
线切割加工
4.极性:
目标
线切割加工因脉宽较窄,所以都用正极性加工, 重点 否则切割速度变低且电极丝损耗增大。
内容 问题 作业
第一章 数控线切割技术
非电参数对工艺指标的影响
目标
1.电极丝的选择:
重点
目前电火花线切割加工使用的电极丝材料有钼丝、
- 1、下载文档前请自行甄别文档内容的完整性,平台不提供额外的编辑、内容补充、找答案等附加服务。
- 2、"仅部分预览"的文档,不可在线预览部分如存在完整性等问题,可反馈申请退款(可完整预览的文档不适用该条件!)。
- 3、如文档侵犯您的权益,请联系客服反馈,我们会尽快为您处理(人工客服工作时间:9:00-18:30)。
线切割程序编制与机床操作培训资料
[培训目标]
1)理解线切割机床程序编制的工艺和方法;
2)掌握线切割机床简单零件的程序编制;
3)掌握凸模类零件的加工方法,能正确设置机床的相关参数。
[培训要求]
在线切割机床上加工如图1-1所示零件轮廓。
已知:材料为45钢,厚度为8mm。
1、零件图形
图1-1 零件图形
2、编程与加工要求:
1)根据电极丝实际直径,正确计算偏移量。
2)根据图形特点,正确选择引入线位置和切割方向。
3)根据材料种类和厚度,正确设置脉冲参数。
4)根据程序的引入位置和切割方向,正确装夹工件和定位电极丝。
[培训要点]
线切割加工工艺(偏移量的计算,引入、引出线位置的确定和切割方向的选取),线切割自动编程、线切割机床操作。
[培训内容]
一、线切割加工工艺
1、线切割加工原理
数控线切割机床加工是利用不断运动的电极丝与工件之间产生火花放电,从而将金属蚀除下来,实现轮廓切割的。
2、偏移量的确定
编程时都是以电极丝中心按照图样的实际轮廓进行编程的。
但在实际加工中,所采用的电极丝有一定的直径,电极丝与被加工材料之间有一定的放电间隙。
因此,要加工出工件的外形轮廓(即凸模类零件),电极丝中心轨迹应向外偏移。
要加工内孔(即凹模类零件),电极丝中心轨迹应向内偏移(如图1-2所示)。
偏移量=实际电极丝半径+单边放电间隙。
图1-2 轨迹偏移方向
正确选取引入、引出线位置和切割方向
3.1 起始切割点(引入线的终点)的确定
加工中,由于电极丝返回到起始点时很容易造成加工痕迹,使工件精度受到影响,所以为了避免这一影响,起始切割点的选择原则如下:
3.1.1首选图样上直线与直线的交点,其次是选择直线与圆弧的交点和圆弧与圆弧的交点。
3.1.2当切割工件各表面粗糙度要求不一致时应在较粗糙的面上选择起始切割点。
3.1.3当工件各面粗糙度相同时,又没有相交面,起始切割点应选择在钳工容易修复的凸出部位。
3.1.4避免将起始切割点选择在应力集中的夹角处,以防止造成断丝、短路。
3.2 引入、引出线位置与切割路线的确定
凸模引入线长度一般取3~5㎜,其切割路线选择与工件的装夹有关。
选择原则是使工件与其夹持部位分离的切割段安排在总的切割程序末端。
例如:切割图1-3所示凸模零件,后图合理。
引出线一般与引入线重合。
图1-3 切割路线选择
凹模穿丝点多取在凹模的对称中心,起始切割点(引入线的终点)的选取除考虑上述原则外,还应考虑选取最短路径切入且钳工容易修复的位置。
二、线切割自动编程
不同厂家生产的自动编程系统有所不同,具体可参见使用说明书。
本处以CAXA线切割V2系统为例,说明自动编程的方法。
CAXA软件中进行自动编程的步骤:绘图——生成加工轨迹——生成3B代码(或G代码)程序——程序传输。
1、绘图
利用CAXA软件的CAD功能能很方便的绘出加工零件图,为作引入线方便,可把图形的左上角移到(0,0)点(如图1-4所示)。
图1-4 绘制零件图
2、生成加工轨迹
2.1点击“线切割”菜单下的“轨迹生成”(如图1-5所示)。
图1-5 选择轨迹生成
2.2系统弹出[线切割轨迹生成参数]对话框。
切割参数项[切入方式]有三种:
[直线]切入:电极丝直接从穿丝点切入到加工起始点。
[垂直]切入:电极丝从穿丝点垂直切入到加工起始段。
[指定切入点]切入:此方式要求在轨迹上选择一个点作为加工的起始点,电极丝直接从穿丝点切入到加工起始点。
其它参数可采用默认值。
已知电极丝直径为0.18mm,单边放电间隙为0.01mm,则电极丝偏移量为0.1mm。
如图示填写切割参数和偏移量参数,单击确定(如图1-6、1-7所示)。
图1-6 切割参数设置
图1-7 偏移量设置
2.3 系统提示[选择轮廓],选取所绘图(如图1-8),被选取的图变为红色虚线,并沿轮廓方向出现一对反向箭头,系统提示[选取链拾取方向],如工件左边装夹,引入点可取在工件左上角点,并选择顺时针方向箭头,使工件装夹面最后切削。
图1-8 加工轮廓选取
2.4 选取链拾取方向后,全部变为红色,且在轮廓法线方向出现一对反向箭头,系统提示[选择切割侧边或补偿方向],因凸模应向外偏移,所以选择指向图形外侧的箭头(如图1-9所示)。
图1-9 补偿方向选取
2.5 系统提示[输入穿丝点的位置](如图1-10所示),键入0,5,即引入线长度取5mm,回车。
图1-10 输入穿丝点
2.6 系统提示[输入退出点(回车与穿丝点重合)] (如图1-11所示),直接回车,穿丝点与回退点重合,系统按偏移量0.1mm自动计算出加工轨迹。
凸模类零件轨迹线在轮廓线外面(如图1-12所示)
图1-11 输入退出点
图1-12 凸模轨迹图
3、生成代码
3.1 选取线切割菜单下的[生成3B加工代码](如图1-13所示)。
图1-13 选择生成3B代码
3.2 系统提示[生成3B加工代码]对话框,要求用户输入文件名,选择存盘路径,单击保存按钮(如图1-14所示)。
图1-14 程序存盘
3.3 系统出现新菜单,并提示[拾取加工轨迹],选绿色的加工轨迹,右击结束轨迹拾取,系统自动生成3B程序,并在本窗口中显示程序内容(如图1-15所示)。
图1-15 程序内容
4、程序传输
程序可通过多种方式传输到机床。
三、线切割机床操作
1、现场了解线切割机床的组成及功能。
2、现场了解机床及控制柜面板上各按钮作用。
3、了解线切割机床的操作方法。
(一)、工作前应作如下检查
1、开控制台电源,让电脑进入工作状态。
2、开机床总电源,检查上下导轮和导电块上是否有污物,检查贮丝筒行程开关位置,开油泵,检查上下水道是否畅通。
3、开机后应按设备润滑要求,对机床有关部位注油润滑。
4、检查电极丝的垂直度。
(二)、加工
1、看清图纸,根据工艺要求确定找正基准,选择工件变形小的切割路线,编制引入程序,按工件厚度,材料种类和技术要求选择高频电源加工参数。
相关工艺参数的调节可参阅相关机床说明书。
2、装夹工件之前,首先消除残余应力(去磁),然后确认工件位置是否在行程范围之内。
3、穿丝,检查电极丝是否在导轮槽内及导电块上,锁住电机,然后开机床运丝开关——开油泵——开断丝保护及自动停机开关——高频打开,开始切割。
4、加工过程中注意观察加工电流,调节变频速度,防止烧丝,断丝及短路现象。
5、工件切完后,先关高频电源——关油泵——关运丝开关——拆下工件洗干净——自验。
[培训小结]
通过本项目的培训,应掌握线切割加工中基准件偏移量的计算,凸模引入、引出线位置的确定和切割方向的选取,CAXA线切割自动编程的步骤和方法,机床操作的方法和步骤。
[思考与练习]
1、按下图所示零件尺寸,编写凸模的加工程序,并在机床上加工出符合图纸尺寸的工件。
已知:材料厚度为8mm ,材料为45钢。
图1-16 零件图形
2、按图1-16所示零件尺寸,编写凹模的加工程序,并在机床上加工出符合图纸尺寸的工件。