Microstructure evolution during reheating of extruded Mg-Gd-Y-Zr alloy into semisolid state
当表面活性剂遇到大环分子
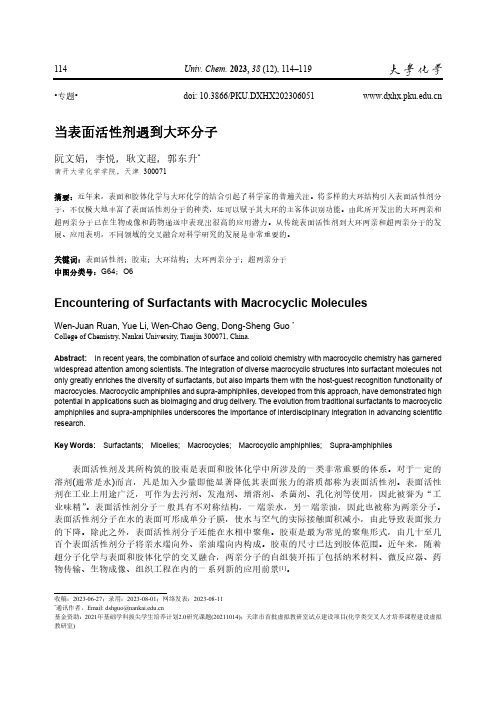
114Univ. Chem. 2023, 38 (12), 114–119收稿:2023-06-27;录用:2023-08-01;网络发表:2023-08-11*通讯作者,Email:*****************.cn基金资助:2021年基础学科拔尖学生培养计划2.0研究课题(20211014);天津市首批虚拟教研室试点建设项目(化学类交叉人才培养课程建设虚拟教研室)•专题• doi: 10.3866/PKU.DXHX202306051 当表面活性剂遇到大环分子阮文娟,李悦,耿文超,郭东升*南开大学化学学院,天津 300071摘要:近年来,表面和胶体化学与大环化学的结合引起了科学家的普遍关注。
将多样的大环结构引入表面活性剂分子,不仅极大地丰富了表面活性剂分子的种类,还可以赋予其大环的主客体识别功能。
由此所开发出的大环两亲和超两亲分子已在生物成像和药物递送中表现出很高的应用潜力。
从传统表面活性剂到大环两亲和超两亲分子的发展、应用表明,不同领域的交叉融合对科学研究的发展是非常重要的。
关键词:表面活性剂;胶束;大环结构;大环两亲分子;超两亲分子中图分类号:G64;O6Encountering of Surfactants with Macrocyclic MoleculesWen-Juan Ruan, Yue Li, Wen-Chao Geng, Dong-Sheng Guo *College of Chemistry, Nankai University, Tianjin 300071, China.Abstract: In recent years, the combination of surface and colloid chemistry with macrocyclic chemistry has garnered widespread attention among scientists. The integration of diverse macrocyclic structures into surfactant molecules not only greatly enriches the diversity of surfactants, but also imparts them with the host-guest recognition functionality of macrocycles. Macrocyclic amphiphiles and supra-amphiphiles, developed from this approach, have demonstrated high potential in applications such as bioimaging and drug delivery. The evolution from traditional surfactants to macrocyclic amphiphiles and supra-amphiphiles underscores the importance of interdisciplinary integration in advancing scientific research.Key Words: Surfactants; Micelles; Macrocycles; Macrocyclic amphiphiles; Supra-amphiphiles表面活性剂及其所构筑的胶束是表面和胶体化学中所涉及的一类非常重要的体系。
干细胞在子宫内膜损伤修复中的应用
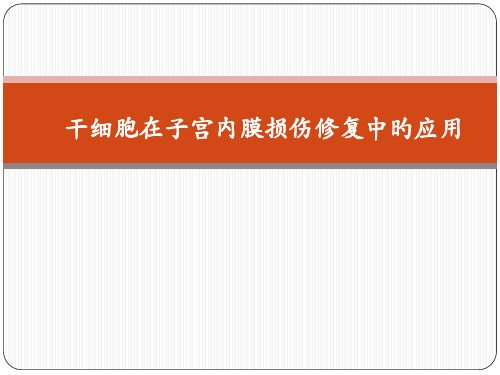
干细胞治疗宫腔粘连旳临床应用
2023年 Nagori 等使用自体BMDSCs治疗了一名33岁旳 重度宫腔粘连患者,该患者在接受干细胞治疗前已尝 试过刮宫、周期性激素治疗等,效果均欠佳。对患者 行刮宫后,在超声引导下用注射器经宫颈向宫底及宫 腔内注入干细胞悬液,术后辅以阿司匹林和周期性激 素治疗。超声检验成果显示患者术后子宫内膜再生很 好,而且,患者经过体外受精成功怀孕,随访至妊娠 第8周胎儿生长良好。
发觉小鼠旳BMSCs 与子宫内膜间质细胞共培养, BMSCs可向子宫内膜上皮细胞方向分化;
将大鼠BMSCs 与子宫内膜间质细胞共培养,发觉 BMSCs能够向子宫内膜间质细胞方向分化。
以上这些研究阐明了干细胞向子宫内膜样细胞方向 分化旳可行性。
2. 干细胞具有分化为血管细胞旳能力
干细胞具有向损伤组织趋化和迁移旳能力。且 能够直接分化为血管细胞。
SINGHN,MOHANTYS,SETHT. Autologous stem cell transplantation inrefractory Asherman’s syndrome: Anovel cell based the rapy. Journal of Human Reproductive Sciences, 2014,7(2):93-98.
2023年,Zhao等针对反复流产造成旳难治型IUA病 人,常规治疗无效后,行宫腔粘连分解术,术后利 用BMDSCs 联合雌激素人工周期治疗,使其成功受 孕。
ZHAO Y,WANG A. Intrauterinetransplantation of autologous bone marrow derived mesenchymal stem cells followed by conception in a patient of severe intrauterine adhesions . Open Journal of Obstetrics and Gynecology, 2013,3(3);377-380.
那神奇的纳米时代英语作文
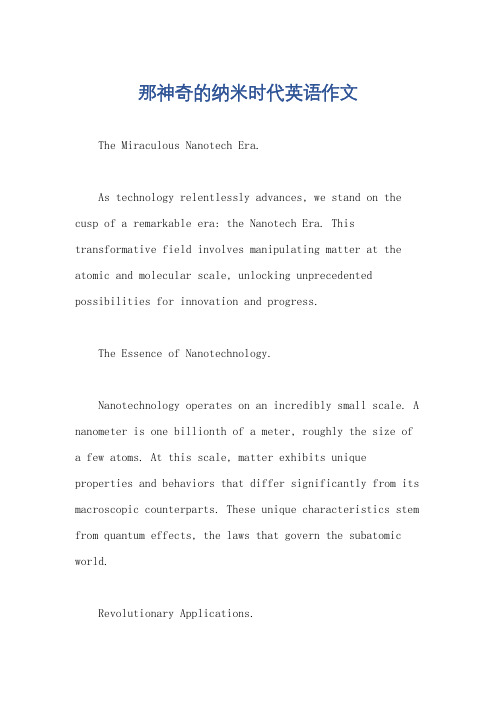
那神奇的纳米时代英语作文The Miraculous Nanotech Era.As technology relentlessly advances, we stand on the cusp of a remarkable era: the Nanotech Era. This transformative field involves manipulating matter at the atomic and molecular scale, unlocking unprecedented possibilities for innovation and progress.The Essence of Nanotechnology.Nanotechnology operates on an incredibly small scale. A nanometer is one billionth of a meter, roughly the size of a few atoms. At this scale, matter exhibits unique properties and behaviors that differ significantly from its macroscopic counterparts. These unique characteristics stem from quantum effects, the laws that govern the subatomic world.Revolutionary Applications.Nanotechnology has far-reaching applications across diverse industries, paving the way for groundbreaking advancements in healthcare, energy, electronics, manufacturing, and more.In Medicine:Targeted Drug Delivery: Nanoparticles can be designed to deliver drugs directly to diseased cells, enhancing efficacy and minimizing side effects.Tissue Engineering: Nanomaterials can be used to grow and repair damaged tissues, offering hope for treating degenerative diseases.Diagnostics: Nanosensors can detect minute amounts of biomarkers, enabling early diagnosis and personalized treatment.In Energy:Solar Energy Harvesting: Nanoengineered materials can improve the efficiency of solar cells, capturing more sunlight and generating more electricity.Fuel Cells: Nanocatalysts can enhance the performance and durability of fuel cells, providing a cleaner and more efficient energy source.Batteries: Nanomaterials can lead to the development of higher-capacity, longer-lasting batteries for portable devices and electric vehicles.In Electronics:Miniaturization: Nanotechnology allows for the creation of smaller, more powerful electronic devices with enhanced capabilities.Advanced Computing: Nanomaterials can enable faster processing speeds and increased memory capacity in computers.Nanophotonics: Nanostructures can manipulate light in novel ways, opening up possibilities for optical computing and ultra-high-speed data transmission.In Manufacturing:Lightweight Materials: Nanomaterials can be engineered to create lightweight, ultra-strong materials for aerospace and automotive applications.Self-Cleaning Surfaces: Nanoparticles can impart self-cleaning properties to surfaces, reducing the need for harsh chemicals and detergents.Antimicrobial Textiles: Nanomaterials can be incorporated into textiles to provide antimicrobial protection, preventing the growth of bacteria and viruses.Challenges and Ethical Considerations.While nanotechnology holds immense promise, it also presents challenges and ethical considerations that need tobe carefully addressed.Environmental Impact: The potential environmental impact of nanomaterials requires thorough assessment and responsible disposal practices.Health and Safety: The health and safety implications of nanomaterials must be fully understood and managed to ensure their safe use.Ethical Responsibility: The rapid advancement of nanotechnology raises ethical concerns about its potential use for malicious purposes or exacerbation of existing inequalities.Conclusion.The Nanotech Era presents both unparalleled opportunities and challenges. By embracing the responsible development and application of nanotechnology, we have the potential to unlock transformative solutions to some of the world's most pressing problems. From revolutionizinghealthcare to addressing the energy crisis, nanotechnology holds the key to shaping a brighter and more sustainable future.。
专业英语词汇_词组(轧制部分)
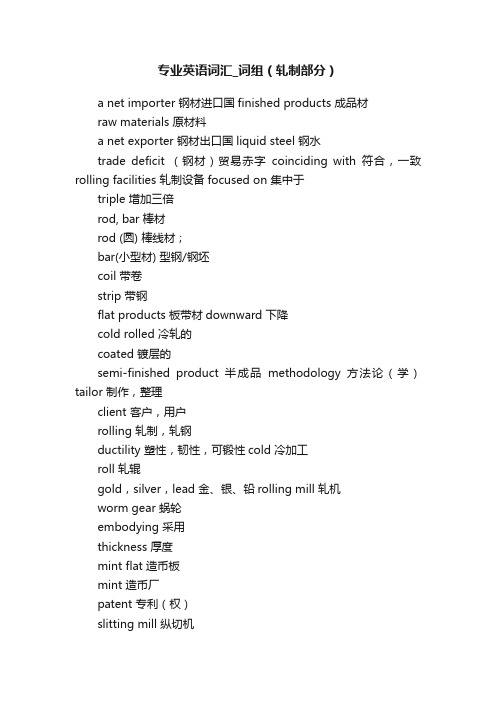
专业英语词汇_词组(轧制部分)a net importer 钢材进口国finished products 成品材raw materials 原材料a net exporter 钢材出口国liquid steel 钢水trade deficit (钢材)贸易赤字coinciding with 符合,一致rolling facilities 轧制设备focused on 集中于triple 增加三倍rod, bar 棒材rod (圆) 棒线材;bar(小型材) 型钢/钢坯coil 带卷strip 带钢flat products 板带材downward 下降cold rolled 冷轧的coated 镀层的semi-finished product 半成品methodology 方法论(学)tailor 制作,整理client 客户,用户rolling 轧制,轧钢ductility 塑性,韧性,可锻性cold 冷加工roll 轧辊gold,silver,lead 金、银、铅rolling mill 轧机worm gear 蜗轮embodying 采用thickness 厚度mint flat 造币板mint 造币厂patent 专利(权)slitting mill 纵切机spindle 轴flat bar 扁平轧件revolving 旋转tin 锡,马口铁pipe 钢管,管道pertain to 适合softer metals 软金属presumably 大概thin flat 薄板slitting 纵切(分)finishing 修整,精整plane-surfaced rolls 平辊hammer 铁锤,锤子large rolling mills 大型轧机hot rolling 热轧ferrous materials 黑色(金属)材料rod 棒(材)ironworks 制铁(钢)厂plate (金属)板tinplate 镀锡板Lauth mill (三辊)劳特轧机backup roll 支持辊equipped with 装备roller table 辊道reversing mill 可逆轧机gear system 齿轮系统plain roll 平辊轧制grooved roll 带槽轧辊steelmaker 钢铁工人cold rolling 冷轧grant 授予rates of revolution 转速wear 磨损guide 导卫(板)elongation 延伸pack rolling 叠轧ply rolling 叠层轧制single-stand:单机架two roll 两辊hot mill 热轧机piece 工件,轧件top roll 上辊cooled down 冷却reheat 再加热owing to 由于conventional sheet hot mill 常规板带热轧机sheet mill 薄板轧机two-high, pull-over mill 两辊往返式轧机rolling unit 轧制机组tandem mill 连轧机successive stand 串列机架wire rod 线棒(材)four-high tandem mill 四辊连轧机mechanical guide 机械导卫rod mill 棒材轧机momentum 动力iron and steel 钢铁rail rolling mill 轨梁轧机wrought iron 锻铁,熟铁I-beam 工字梁three-high mill 三辊轧机heavy section 大型型钢housing (轧机)机架upper roll 上辊lower roll 下辊lifting table 升降辊道middle roll 中间轧辊reversing plate mill 可逆中板轧机universal mill 万能轧机continuous hot mill 连续式热轧机rod rolling mill 棒材轧机billet 小方坯horizontal 水平的vertical 垂直的cluster mill 多辊轧机work roll 工作辊Z-bars Z型轧件beam 钢梁H-beam H型钢梁semi-continuous hot strip mill 半连续热带轧机two-high tandem finishing train 两辊连轧精轧机组width 宽度length 长度roughing train 粗轧机two three-high stands 两架三辊轧机finishing train 精轧机组five-stand 五机架pig iron 生铁hammered bar 锻件forge 铸造pass 道次roll neck 辊颈boiler plate 锅炉板steel corporation 钢铁公司angle iron 角钢inventiveness 独创性mill housing 轧机机架stimulus 刺激,促进因素iron and steel industry 钢铁工业blooming mill 初轧机,方坯初轧机reversing blooming mill 可逆初轧机two-high reversing blooming mill 两辊可逆初轧机three-high roughing mill 三辊粗轧机three-high finishing mill 三辊精轧机horsepower 马力shaft 轴flywheel 飞轮reversal 可逆的electric generator 发电机direct current motor 直流电机main drive 主传动(系统)cold reduction facilities (金属)冷加工设备reduction 压下steel band 钢带high-carbon 高碳Lauth 3-high cold mill 三辊劳特冷轧机cold rolled strip 冷轧带钢2-high mill 两辊轧机roll neck bearing 辊颈轴承reversing cold mill 可逆冷轧机tandem cold rolling 冷连轧机2-high 4-stand tandem mill 两辊四机架连轧机tension 张力tension reel 张力卷取(机)cold strip reel 冷轧带钢卷取机hot strip reel 热轧带钢卷取机high-tension 大张力constant tension 恒张力current control 电流控制concurrent 同时发生的,一致的strip tension control 带钢张力控制interstand tension 机架间张力ingot 钢锭the order of …数量级flat-rolled 扁平轧制的five-stand tandem mill 五机架连轧机stainless sheet 不锈钢板fully continuous 全连续pay-off reel 开卷机welder 焊接机intermediate stand 中间机架Sendzimir mill 森吉米尔轧机shear 剪切机strip accumulator 带钢收集器flying shear 飞剪tension reel 张力卷取机silicon steel 硅钢special alloy 特殊钢single-stand reversing mill 单机架可逆轧机rolling lubricant 轧制润滑roll bite 轧制变形区foil Mill 箔材轧机temper or skin pass mill 平整机annealed strip 退火带钢flatness 平直度(板形)uncontaminated 无污染的tinning 镀锡friction 摩擦corrosion-resistant 抗腐蚀closer dimensional tolerance 更精确的尺寸公差millcomponents 轧机部件instrumentation 仪表control system 控制系统engineering science 工程科学rolling technology 轧制技术shaping 成型metallurgical properties 冶金性能in the case of …..情况下with respect of 关于conventional four-high mill stand 常规四辊轧机planetary mill 行星轧机six-high mill 六辊轧机screw 压下(螺丝)hydraulic roll-positioning system 液压轧辊定位系统(液压APC)automatic-gage-control (AGC) 厚度自动控制系统mathematical model 数学模型stiffness 刚度roll-bending 轧辊弯曲roll-bending jacks 弯辊装置pacing 节奏控制cross-sectional profile 横断面形状shape 板形slab 板坯in-line 在线continuously cast billet 连铸小方坯slab strand (连铸)扁坯billet casting machine 小方坯连铸机bar mill 小型轧机furnace 加热炉scale-breaker 除磷机roughing stand 粗轧机座six-stand finishing train 六机架精轧机组coiler 卷取机run-out table 输出辊道vertical edger 立辊轧机two-stand tandem-roughing mill 两机座粗轧连轧机finishing stand 精轧机座main drive 主传动auxiliary drive 辅助传动charged and discharged 装钢、出钢cooling system 冷却系统cast-iron and steel work roll 铸铁/铸钢工作辊rolling force 轧制压力back-roll-bending system 支持辊弯辊系统laminar-flow 层流冷却coil box 卷取箱microstructure 微观组织yield strength 屈服强度toughness 韧性structure steel 结构钢cooling bed 冷床measuring device 测量装置large reduction 大压下量single pass 单道次seamless tube 无缝钢管mill stand 轧钢机座component 部件deflection 变形,压扁roll gap adjustment mechanism 轧辊调整装置pass 1ine 轧制线housing / mill housing 机架main drive train 主传动机组rolling torque 轧制力矩roll arrangement 轧辊布置two-high mill stand 两辊轧机机座top,bottom and middle roll 上、下、中辊cluster type mill stand 多辊轧机机座intermediate roll 中间辊asymmetrical 非对称的,非均匀的symmetrical 对称的,均匀的roll axes 轧辊轴向horizontal mill stand 水平轧机机座vertical mill stand 垂直轧机机座non-reversing mill stand 不可逆轧机机座reversing mill stand 可逆轧机机座back-pass mill stand 返回式轧机机座direct drive 电机直接传动gear drive 齿轮传动A3 critical temperature A3临界温度austenitic phase 奥氏体相区slabbing mill 板坯轧机p1ate mill 中厚板轧机strip mill 带钢轧机universal rolling mill 万能轧机tandem roiling mill 连轧机reheat furnace 再加热炉roughing mill 粗轧机transfer bar 中间坯transfer table / delay table 中间辊道finishing mill 精轧机tandem finishing train 精轧连轧机组looper 活套interstand strip tension 机架间带钢张力runout table 输出辊道cooling header 冷却喷嘴desealing system 除鳞系统scale breaker 破鳞机roll coolant system 轧辊冷却系统interstand cooling system 机架间冷却系统semi-continuous 半连续twin reversing roughing train 两机架可逆粗轧机组three-quarter continuous 3/4连续式universal roughing mill stand 万能粗轧机座fully continuous. 全连续single-pass stand 单道次机座coilbox 卷取箱Steckel mill 斯泰克尔轧机tandem cold mill 冷连轧机strip tension 带钢张力pickling 酸洗annealing 退火residual stress 残余应力slitting and cutting 纵切rigidity 刚度inspection 表面检查marking 打印quenching 淬火two-high pull-over mills 两辊往复式轧机three-high and reversing mills 三辊轧机和可逆轧机two-high nonreversing mill 两辊不可逆轧机in tandem with 与……连轧multipass 多道次single-pass 单道次edgers 立辊轧机conditioned slab 精整板坯mechanical properties 机械性能walking beam furnaces 步进梁式加热炉scalebreaking stand 除鳞机架primary and secondary scale 初生和二次氧化铁皮modulus 系数,模数specific rolling force 单位轧制压力roll-positioning system 轧辊定位系统high-speed screwdown system 高速压下系统roll gap 辊缝blooming mill 方坯初轧机plate profile and flatness 中厚板断面和板形work-roll and backup-roll bending system 工作辊和支持辊弯辊系统tandem roughing stands 粗轧连轧机组7-stand finifhing train 七机架精轧机组laminar-flow cooling 层流冷却hot-rolling lubricant 热轧润滑zooming 加速轧制profile (带钢)横断面shape and flatness sensing 板形和平直度传感器delay table 中间辊道specialty steel 特殊钢passline 轧制线tunnel-type furnace 隧道式加热炉two-high roughing stand 两辊粗轧机座cooling table 冷却辊道roll wear 轧辊磨损alleviate 缓解,减轻reduction ratio 压下比soaking 均热slab reheat furnaces 板坯再加热炉two-high scalebreaker 两辊破鳞机hydraulic descaling unit 液压除鳞装置reversing roughing stand 可逆粗轧机座finishing train with four or more 4-high stands 由四个或四个以上四辊轧机组成的精轧机组steel grade 钢种hydraulic roll-balance system 液压轧辊平衡系统roll bearing 轧辊轴承crown 凸度screwdown systems 压下系统continuous 5-zone slab-heating furnace 五段连续式板坯再加热炉laminar-spray cooling system 层流冷却系统bite angle 咬入角interstand looper 机架间活套hydraulic cylinder 液压缸work-roll chock 工作辊轴承座screw 压下螺丝ipm(inch per minute)英寸/分钟automatic roll-changing equipment 自动换辊装置。
metal material 金属材料

Materials Science and Engineering A 527 (2009) 52–60Contents lists available at ScienceDirectMaterials Science and EngineeringAj o u r n a l h o m e p a g e :w w w.e l s e v i e r.c o m /l o c a t e /m s eaRecrystallization mechanism of as-cast AZ91magnesium alloy during hot compressive deformationS.W.Xu ∗,S.Kamado,N.Matsumoto,T.Honma,Y.KojimaDepartment of Mechanical Engineering,Nagaoka University of Technology,Nagaoka 940-2188,Japana r t i c l e i n f o Article history:Received 13March 2009Received in revised form 15July 2009Accepted 28August 2009Keywords:Hot compressionContinuous dynamic recrystallization EBSD TwinMg 17Al 12phasea b s t r a c tDynamic recrystallization (DRX)behavior of as-cast AZ91magnesium alloy during hot compression at 300◦C and the strain rate of 0.2s −1was systematically investigated by electron backscattering diffraction (EBSD)analysis.Twin DRX and continuous DRX (CDRX)are observed in grains and near grain boundaries,respectively.Original coarse grains are firstly divided by primary {10¯12}tensile twins and {10¯11}compression twins,and then {10¯11}–{10¯12}double twins are rapidly propagated within these pri-mary compression twins with increasing compressive strain.Some twin-walled grains are formed by themutual crossing of twins or by the formation of the {10¯11}–{10¯12}double twins and furthermore,subgrains divided by low-grain boundaries in the double twins are also formed.Finally,DRXed grains are formed by the in situ evolution of the subgrains with the growth of low-angle boundaries to high-angle grain boundaries in twins.CDRX around the eutectic Mg 17Al 12phases at grain boundaries occurs together with the precipitation of discontinuous Mg 17Al 12phase and the fragmentation of the precipitates during compression.The discontinuous fragmented precipitates distribute at the newly formed CDRXed grain boundaries and have remarkable pinning effect on the CDRXed grain growth,resulting in the average grain size of about 1.5m.© 2009 Elsevier B.V. All rights reserved.1.IntroductionMagnesium alloys show good potential for improving the fuel efficiency of vehicles and reducing CO 2emissions because of their high specific strength and stiffness [1].However,the use of Mg alloys has been limited because of low formability due to their hexagonal close-packed crystal structure with a limited number of operative slip systems at room temperature [2–4]and rel-atively low strengths as comparison with steel and aluminum alloys.Grain refinement by dynamic recrystallization (DRX)is essential for the development of Mg alloys with high strength [5],high toughness [6,7]and good ductility at room temper-ature [8].Recently,grain refinement due to DRX during hot deformation has been demonstrated in pure Mg [9,10],and con-ventional wrought Mg alloys such as Mg–Al–Zn [11–14]and Mg–Zn–Zr alloys [5,15].However,there are limited studies on microstructural evolution of high Al-containing Mg alloys such as Mg–9%Al–1%Zn–0.2%Mn (wt%)alloy (AZ91)during high temperature deformation,resulting in making it difficult to use the high potential of Mg alloys.It is also convenient for hot working such as forging,extrusion,etc.to directly use as-cast∗Corresponding author.Tel.:+81258479760;fax:+81258479770.E-mail address:xushiwei@stn.nagaokaut.ac.jp (S.W.Xu).materials without homogenization in order to save manufacturing cost.It was reported that new grains in Mg alloys were generated by several mechanisms.For example:(1)“Twin DRX”was found occur-ring in coarse-grained Mg during hot compression at 150,300and 450◦C [10,16,17],while due to the limitation of traditional analyz-ing equipments,detail information on the type of twins,an effect of the twins on DRXed grains formation and the DRX sequence inside twins were not so well understood.Recently,in addition toprimary {10¯12}tensile twin,{10¯11}and {10¯13}compression twins,secondary twin was reported to take place within the reori-ented primary twin in Mg alloys,which is known as double twin [18,19].However,effect of the double twins on the DRX behavior is seldom investigated.(2)Deformation-induced continuous reac-tion resulting in grain fragment by kink bands,i.e.continuous DRX (CDRX)was observed in Mg–3%Al–1%Zn (AZ31)[14]during hot compression at 400◦C.CDRX is essentially different from the con-ventional (i.e.discontinuous)DRX (DDRX)including a nucleation of new grains and their larger scale growth taking place under hot deformation.In AZ31alloy,the contents of alloying elements were low and the specimen usually suffered homogenization heat treat-ment before hot working,therefore,the effects of eutectic Mg 17Al 12()phases and precipitates on DRX behavior were neglected.On the other hand,in as-cast AZ91alloy phases exist at grain boundaries and solute atoms enrich near grain boundaries,which has possibil-0921-5093/$–see front matter © 2009 Elsevier B.V. All rights reserved.doi:10.1016/j.msea.2009.08.062S.W.Xu et al./Materials Science and Engineering A527 (2009) 52–6053Fig.1.Typical microstructures and texture of the as-cast AZ91alloy specimen.(a)SEM image,(b)optical microstructure,(c)inverse polefigure map and(d)(0001) basal-plane polefigure.ity to cause discontinuous precipitation ofphase during heating to the compression temperature.Such microstructural factors are expected to influence DRX behavior.In this study,DRX behavior of as-cast Mg–9Al–1Zn(wt%,AZ91) alloy during hot compression was systematically investigated by electron backscattering diffraction(EBSD)analysis.The effects of {10¯11}–{10¯12}double twin andphase on the DRXed grains formation are investigated in detail,and DRX mechanisms of as-cast AZ91alloy are also discussed.2.Experimental proceduresThe direct chill(DC)-cast AZ91ingots used in this study were supplied by Sankyo Tateyama Aluminum Inc.,with chemical com-position of Al9.1,Zn0.88,Mn0.17,Si0.010,Fe0.003,Cu<0.002,and balance Mg(all in wt%).Cylindrical specimens with50mm in height and50mm in diameter werefirstly heated to preset temperature in a resistant furnace and held for5min to allow the temperature to equalize throughout the specimens.Then,the specimens were hot compressed using a hydraulic press machine with a capacity of 100ton at a temperature of300◦C and a strain rate of0.2s−1(ram speed of10mm/s)to the strains of5%,10%,20%and30%.To min-imize the friction,the MoS2lubricant was pasted to the surface of specimens and permanent dies.After the compression,the speci-mens were immediately quenched into water within5s.To check the repeatability of the results,same experiments were conducted three times under each set of condition and the temperature devi-ation from the preset temperature was within±2◦C throughout all the tests.Microstructures of the compressed specimens were examined on sections parallel to the compression direction(CD)by an Olympus Bx60m optical microscope(OM)and a JEOL JSM-7000F scanning electron microscope(FE-SEM).Inverse polefigure maps, twin types and distribution of misorientation angles of the com-pressed specimens were investigated by EBSD mapping analysis which was carried out using a JEOL JSM-7000F scanning electron microscope operating at25kV and equipped with an OIM5.2soft-ware from TSL MSC-2200.3.Results and discussion3.1.Microstructures of the as-cast AZ91alloy specimenThe microstructures and texture of the as-cast AZ91alloy spec-imen used in this study are shown in Fig.1.The as-cast alloy specimen exhibits a typical dendritic microstructure consisting␣-Mg solid solution andphase crystallizing at the grain boundaries as shown in Fig.1(a)and(b),where the Al concentration is higher than that at the central part of␣-Mg solid solution[20].The initial grain orientations are random and no mechanical twins or sub-grains are observed(Fig.1(c)and(d)),therefore,no special effect from initial texture can be shown on the DRX behavior in this study. The initial grain size of the as-cast AZ91alloy specimen is142m.pression deformation behaviorNominal stress–nominal strain curve for the as-cast AZ91alloy specimen during compression test is shown in Fig.2(a).When com-pressed at300◦C and the strain rate of0.2s−1,theflow curve shows a large strain hardening,a single peak,a strain softening,and a stead stateflow as strain increases.Such behavior is a typical DRX type offlow,which is considered to occur in the region of thermally activatedflow[17].54S.W.Xu et al./Materials Science and Engineering A527 (2009) 52–60Fig.2.(a)Nominal stress–nominal strain curve of as-cast AZ91alloy specimen when compressed at 300◦C-0.2s −1(open circles indicate prestrains,where microstructure observation was carried out);(b)SEM images of the specimen just after heating and holding at 300◦C before compression test;and optical microstructures of specimens compressed to (c)ε=5%,(d)ε=10%,(e)ε=20%and (f)ε=30%.3.3.Microstructural evolution during hot compressionTypical microstructures for as-cast specimen just after heating and holding at 300◦C before compression test and the specimens compressed to different strains are shown in Fig.2(b)–(f).From the comparison of Fig.2(b)with Fig.1(a),it can be seen that during heating and holding at 300◦C before hot compression test a lot of compounds have already precipitated in Al-rich regions around the massive eutectic phases,resulting in the contrast around the eutectic phases in Fig.2(c)–(f).During hot compression test microstructures are developed in these regions,but could not be observed in Fig.2only by optical microscope with low resolution and will be shown in the following sections.Furthermore,twins easily occur even at the small strain of ε=5%(Fig.2(c))in the orig-inal grains due to limited slip system and coarse microstructure of the as-cast specimen.The number of twin increases with increasing compression strain (Fig.2(d)and (e)),leading to the early harden-ing response on the stress–strain curve as shown in Fig.2(a)[21,22].DRX is mainly observed inside the twins (Fig.2(e)and (f)).There-fore,in the following sections,“Twin DRX”in the original grains and the microstructural changes around the eutectic phases at orig-inal grain boundaries are investigated in detail by EBSD analysis and SEM observation with high resolution.The formation mecha-nisms are also discussed based on the results of the microstructural analysis.3.4.Twin DRX in the original grainsInverse pole figure maps in the squared areas indicated in Fig.2(c),(d)and (f)are taken in order to investigate the DRX behav-ior in detail.The results are shown in Figs.3and 4.The distribution of misorientation angles in the twinned area is shown in Fig.5.Firstly,the twin types should be confirmed in order to under-stand the twin DRX behavior because there are various types ofS.W.Xu et al./Materials Science and Engineering A527 (2009) 52–6055Fig.3.Inverse polefigure map of the specimen compressed to the strain of5%.(a)The area squared in Fig.2(c).(b)High magnification of the area squared by red line in (a),showing the formation of low-angle boundaries inside double twin.(c)High magnification of the area squared by blue line in(a),showing the formation of twin-walled pression direction is vertical.(For interpretation of the references to color in thisfigure legend,the reader is referred to the web version of the article.)twins in Mg.The type of twin can be deduced from the misorien-tation angle between the twin and the matrix[23–28].Namely, the{10¯12}twin,which is the c axis tensile twin,produces a basal-plane tilt of86.3◦and the{10¯11}twin,which is c axis com-pression twin,produces a basal-plane tilt of56.2◦.Also,there is a special{10¯11}–{10¯12}double twin,which is generated when {10¯12}re-twinning occurs inside the{10¯11}twin.The basal plane of the{10¯11}–{10¯12}double twin is tilted to37.5◦with respect to the basal plane of the matrix.For reference,the schematic illustration for{10¯11}–{10¯12}double twin and the changes in misorientation angles between the twins and the matrix with the formation of{10¯11}–{10¯12}double twin are shown in Fig.6[29]. As shown in Fig.5(a),high frequency peaks appear near38◦,56◦and86◦,indicating{10¯11}–{10¯12}double twin,primary{10¯11} compression twin and{10¯12}tensile twin occurring when com-pressed toε=5%.In particular,the frequency of misorientation angle at38◦is very high.This indicates that most of the bound-aries between the twins and matrix are identified as belonging to{10¯11}–{10¯12}double twin as shown in Fig.3(a).The rem-nant of the{10¯11}compression twin(near56◦)is observed in Fig.3(c)and the{10¯12}tensile twin(near86◦)locates inside the compression twins(Fig.3(c)).This is because double twins involve {10¯12}tensile twins propagating inside with the original com-pression twins.In specimens compressed toε=5%,5EBSD maps including33twins are taken and all the twins are investigated.The results are nearly the same as shown in Figs.3and5(a),showing that the twins have already been formed even atε=5%and most of them are developed to the{10¯11}–{10¯12}double twins.Further-more,though the{10¯11}compression twin,the{10¯12}tensile twin and{10¯11}–{10¯12}double twin are observed,other com-pression twins such as{10¯13}(64◦)are not observed in this study. The main twin types do not change even when further stained to 30%as shown in Fig.5(b).Consequently,based on the results of microstructure evolution revealed by EBSD mapping analyses shown from Figs.3–5,the mechanism of twin DRXed grains formation can be concluded as follows:(1)First,the original coarse grains are divided by primary{10¯12}tensile twins(86◦)and{10¯11}compression twins(56◦),in the meanwhile,double twins involving secondary{10¯12} tensile twins are rapidly propagated inside the primary com-pression twins with increasing compression strain(ε=5%) (Figs.3(a)and5(a)).Some twin-walled grains are formed by the mutual crossing of twins(Fig.3(a))or by the formation of double twins(Fig.3(c)).The geometric relationship between the matrix and the twins around the DRXed grains formed by an occur-rence of{10¯11}–{10¯12}double twins is shown in Fig.6(a) as an area surrounded by the red line.Low-angle boundaries are also observed inside the{10¯11}–{10¯12}double twins (Fig.3(b)).(2)By further straining toε=10%,the number of twins increases(Fig.2(d)).More twin-walled grains are formed,particularly56S.W.Xu et al./Materials Science and Engineering A527 (2009) 52–60Fig.4.Inverse polefigure maps of the specimens compressed to the strains of(a) 10%and(b)30%.(a)The area squared in Fig.2(d);and(b)the area squared in Fig.2(f).at the intersection parts of the twins(Fig.4(a))(of course, some DRXed grains could also be formed by multiple crossing of twins due to an increase in number of twins).The twin-walled grains formed by the occurrence of{10¯11}–{10¯12}double twins could be also observed as indicated in Fig.4(a).Furthermore,more low-angle boundaries are developed in the {10¯11}–{10¯12}double twins,as indicated by white lines in Fig.4(a).(3)With increasing compressive stain toε=20%and30%,the num-ber of twins further increases and DRX occurs inside almost all the twins(Fig.2(e)and(f)).The distribution of misorienta-tion angles in Fig.5(b)shows that when the compressive strain increases from10%to30%,the number fraction of the bound-aries with misorientation angles below10◦in twins decreases, while that above10◦ly the low-angle grain boundaries developed in twins grow to high-angle grain bound-aries with increasing compressive strain,as indicated by black arrows in Fig.4(b).It also should be noted that the average size of the subgrains divided by the low-grain boundaries in twins of Fig.4(a)is roughly the same as that of the DRXed grains in twins of Fig.4(b),indicating that thefinal DRXed grains could be formed by the in situ evolution of subgrains with the growth of low-angle grain boundaries in twins to high-angle grain ly,continuous DRX occurs during the hot compression of the as-cast AZ91alloy specimen.Fur-thermore,SEM images given in Fig.7reveal that no-phase is observed inside or at the grain boundaries of the twin DRX grains in the original grains.It is interesting that most of the twin DRXed grain boundaries are identified as belonging to{10¯11}–{10¯12}double twin.As mentioned above,generally,{10¯11}compression twinning occurs then double twins form by propagating tensile twins in the primary compression twins.Therefore,the enhancement of{10¯11}com-pression twin formation should be discussedfirstly.It is known that the critical resolved shear stress(CRSS)for{10¯11}compression twin is very high at the room temperature,while the CRSS decreases dramatically with increasing deformation temperature[30].Fur-thermore,Meyers et al.[31]and Christian and Mahajan[32]have reported that the grain size dependence of the yield stress for the twinning could also be described by a Hall–Petch relationship as follows:T0.2= T0+k T d−1/2(1) However,the slope k T for twinning was higher than the slope k S for slip.Recently Barnett et al.[33]reported that the Hall–Petch slope for twinning in extruded AZ31magnesium alloy specimen (k T=8.6MN/m3/2at200◦C)was more than10times that for slip (k S=0.73MN/m3/2at200◦C),indicating that twinning stress has larger grain size dependence as compared with the slipstress.Fig.5.Distribution of misorientation angles for compressed specimens.(a)Twinned area in Fig.2(c)ε=5%,(b)twinned area in Fig.2(d)ε=10%and twinned area in Fig.2(f)ε=30%.S.W.Xu et al./Materials Science and Engineering A527 (2009) 52–6057Fig.6.(a)Schematic illustration for{10¯11}–{10¯12}double twin[29]and(b)the change of misorientation angle between the twin and the matrix with the formation of {10¯11}–{10¯12}double twin.Therefore,the T0.2for the{10¯11}twinning at high temperatures could be further decreased in the present as-cast AZ91alloy speci-men with a large initial grain size of142m.Furthermore,massive eutecticphases could cause less deformation at the coarse origi-nal grain boundaries(Fig.1(a)and(b))during hot compression test due to the reduction of dislocation motion between the neighbor grains.The dislocation could be more easily and quickly accumu-lated around the massive eutecticphases and inside the original grains at the beginning of hot compression test compared to Mg alloys with low Al content such as AZ31,resulting in a high dis-location density and high stress concentration inside the original grains.Since the initial texture is random(Fig.1(d)),in some grains with favorable orientations the{10¯11}compression twin and sub-sequent double twin easily occur after the accumulated local stress reaching the CRSS value for{10¯11}compression twin as shown in Fig.3.In addition,{10¯11}twin has the effect of rotating the basal planes(by56◦)towards a more favorable orientation for basal glide.Double twin,which reorients the basal planes by38◦,has the same effect as{10¯11}twin as shown in Fig.6.The{10¯12} twin also reorients the basal planes by86◦,but these reoriented grains are still in the unfavorable orientation for basal slip.There-fore,although the CRSS for{10¯12}tensile twin is much lower than that for{10¯11}compression twin[30],{10¯11}compres-sion twin could also be formed in these regions which is difficult for basal slip.In addition,as shown by the red solid circles in Fig.3(a),in the double-twinned region the matrix has an orientation of c-axis approximately parallel to the compression direction,namely (0002)matrix⊥compression direction(CD),which makes the matrix orientation in the favorable orientation for the{10¯11}compres-sion twin formation.From the results,it also can be expected that at the early stage of compression,due to that the CRSS for the basal slip,tensile twin and non-basal slip is lower than that for the{10¯11}compressive twin at300◦C[30],the former deforma-tion mechanisms and grain boundary sliding arefirstly activated, as a result,the texture of(0002)matrix⊥CD are formed in some regions,then many{10¯11}compression twins are easily formed with further compression.The rapid formation of{10¯11}–{10¯12}double twins could be related to the shear strains induced by different type of twins in hexagonal close-packed(hcp)materials with increasing compres-sive strain[32,34].In Mg,the shear strain is0.129for the{10¯12} tensile twin,0.137for the{10¯11}compression twin and0.004for {10¯11}–{10¯12}double twin[31].Therefore,{10¯11}–{10¯12} double twins are rapidly propagated within the primary compres-sion twins in order to reduce the strain caused by the primary compression twins.It is also interesting in this study that CDRX normally taking place in materials with high stacking fault energy(SFE)occurs in this alloy,although Mg alloy is considered as a material with a low SFE due to the fact that SFE of a dislocation lying on basalplane Fig.7.SEM images of the twin DRX in the original grains.Specimens compressed at(a)ε=10%and(b)ε=30%.58S.W.Xu et al./Materials Science and Engineering A527 (2009) 52–60Fig.8.Typical SEM images (a and b)and inverse pole figure maps (c and d)around the eutectic phases of the specimen compressed to (a and c)ε=10%;(b and d)ε=20%.White lines indicate low-angle boundaries with misorientation angle from 2◦to 15◦.is essentially low.The influence of the twins on the deformation of Mg should be involved in order to explain this fact.It is known that for Mg,the interaction between the basal slip dislocation andthe {10¯12}tensile twin is repulsive [34].In this case,the local stress concentration tends to develop due to a dislocation pileup at the tensile twin boundaries.On the other hand,the interfacesbetween the matrix and the {10¯11}compression twins can absorb dislocations by dissociating them [35].Therefore,it is suggestedthat the basal slip dislocations moving in the {10¯11}compression twins can pass through the twin boundaries without pileup at theinterfaces.However,in the {10¯11}–{10¯12}double twins which is generated when {10¯12}re-twinning occurs in the {10¯11}twin,the basal slip dislocations moving in the {10¯11}twin pileup at the {10¯12}twin boundaries,resulting in the formation of many low-angle boundaries inside or near the double twins as shown in Fig.4.Therefore,with increasing compressive strain the CRSSfor the non-basal slip and cross-slip in {10¯11}–{10¯12}double twins can be easily attained and the dislocations in the interiorof the {10¯11}–{10¯12}double twins can recombine on the basal planes and transform into non-basal dislocation,which can cross-slip in the non-basal planes [16,17,36].In their turn,cross-slipped dislocations are constricted in the non-basal planes and character-ized by high SFE.Due to cross-slip dislocation readily accumulatesin {10¯11}–{10¯12}double twins,further gradual incorporation of dislocations into subgrain boundaries with increasing strain leads to increasing of their misorientation to high-angle bound-aries.Thus,the stress concentration and the operation of cross-slipin {10¯11}–{10¯12}double twins can result in the development of CDRXed grain structure.3.5.Microstructural changes around the eutectic ˇphases at original grain boundariesFig.8shows the typical SEM images and inverse pole figure maps around the eutectic phases at original grain boundaries of the specimens compressed to ε=10%and 20%.From the com-parison of Fig.8(a)with Fig.2(b),it can be seen that,no obvious DRX occurs near the eutectic phases when compressed to ε=10%.However inverse pole figure map (Fig.8(c))reveals that many band-ings with low-angle boundaries indicated by white lines are formed in these regions.They are recognized as kink bands or deformation bands [14,37].Some low-angle boundaries with no specific shape are also observed in these regions,due to accumulation of some misfit dislocation caused by the interaction between moving lat-tice dislocation and the massive eutectic phases.When straining to ε=20%(Figs.8(b)and (d)),the number of kink bands increases.Many new subgrains are formed firstly by the intersection of kink bands and then the low-angle grain boundaries of kink bands grow to high-angle grain boundaries with increasing compressive strain.This new grain formation mechanism is also a kind of continu-ous DRX (CDRX).The phases discontinuously precipitated near the massive eutectic phases (Fig.8(a))are crushed into a large number of small blocks by shear effect of kink bands [14]and dis-tribute at the newly formed CDRXed grain boundaries as shown in Fig.8(b).These precipitates exhibit a pinning effect on the DRXed grain growth,resulting in the remarkable grain refinement.Con-sequently,the average size of the CDRXed grains formed around the eutectic phases of the 20%-compressed specimen is about 1.5m.S.W.Xu et al./Materials Science and Engineering A527 (2009) 52–6059Fig.9.Typical SEM images around the eutecticphases of the specimen compressed toε=30%.(a)Low magnification and(b)high magnification.Fig.9shows the typical SEM images around the eutecticphases of the specimen compressed toε=30%.It can be seen from Fig.9(a) that more DRXed grains are formed around the eutecticphases due to the low-angle grain boundaries of kink bands growing to high-angle grain boundaries,and the DRXed grains in these regions can be divided into two kinds:(1)the DRXed grains withpre-cipitates distributing at the grain boundaries.These DRXed grains mainly occur at the-precipitated regions formed during the heat-ing and holding process as introduced above.The DRXed grain size in these regions is about0.2–1m as shown in Fig.9(b);(2)the DRXed grains without or with fewphases.These DRXed grains mainly occur out of the-precipitated regions and the DRXed grain size in these regions is about2–5m.This indicates that thepre-cipitates are effective in retarding the growth of the DRXed grains, resulting in the refinement of DRXed grains.The above-mentioned analyses also elucidate the important dif-ferences between the high Al-containing Mg alloys such as AZ91 alloy and low Al-containing Mg alloys such as AZ31alloy.That is to say,in the as-cast AZ91alloy specimen,the formation of eutecticphases andprecipitates can impede dislocation motion and cause dislocation pileup near thephases and inside the original grains, thus promote the CDRX process.The crushedphases also can act as the pinning points for the DRXed grain growth,resulting in the refinement of DRXed grains.4.SummaryDynamic recrystallization(DRX)behavior of the as-cast AZ91 magnesium alloy during hot compression at300◦C and the strain rate of0.2s−1was systematically investigated by electron backscat-tering diffraction(EBSD)analysis.Thefindings can be summarized as follows:(1){10¯11}–{10¯12}double twins are rapidly formed even at thecompressive strain ofε=5%by propagating within the{10¯11} compression twins and play a critical role in the continuous DRX(CDRX)behavior in original grains.(2)CDRXed grains in original grains are formedfirstly by formationof twin-walled grains divided by mutual intersection of defor-mation twins or formation of{10¯11}–{10¯12}double twins and then by the in situ evolution of the subgrains with the growth of low-angle boundaries in double twins to high-angle grain boundaries with increasing compressive strain.(3)Continuous DRX occurs near the eutecticphase crystal-lized at grain boundaries together with the precipitation of discontinuousphase and the fragmentation of the discon-tinuous precipitates during compression.The precipitation occurs during the heating process before compression,andduring subsequent compression these discontinuous precipi-tates are fragmented into a large number of small blocks by shear stress of kink bands.Meanwhile,subgrains are formed by the intersection of kink bands.With increasing compres-sive strain,the low-angle boundaries of the kink bands grow to high-angle grain boundaries,leading to the formation of CDRXed grains with discontinuous precipitates distributing at the newly formed CDRXed grain boundaries.The average size of the CDRXed grains at these regions decreases to about1.5m by pinning effect of the precipitates.AcknowledgementThis work was conducted withfinancial aid from the“Forged Magnesium Parts Technological Development Project”which is organized by New Energy and Industrial Technology Development Organization(NEDO),Japan.References[1]M.Hakamada,T.Furuta,Y.Chino,Y.Chen,H.Kusuda,M.Mabuchi,Energy32(2007)1352.[2]R.E.Reed-Hill,W.D.Robertson,Trans.Am.Inst.Min.Metall.Eng.209(1957)496.[3]F.E.Hauser,ndon,J.E.Dorn,Trans.Am.Inst.Min.Metall.Eng.206(1956)589.[4]A.R.Chaudhuri,H.C.Chang,N.J.Grant,Trans.Am.Inst.Min.Metall.Eng.203(1955)682.[5]K.Kubota,M.Mabuchi,K.Higashi,J.Mater.Sci.34(1999)2255.[6]H.Somekawa,T.Mukai,Scr.Mater.53(2005)1059.[7]H.Somekawa,A.Singh,T.Mukai,Phil.Mag.Lett.86(2006)195.[8]T.Mukai,M.Yamanoi,H.Watanabe,K.Higashi,Mater.Trans.42(2001)1177.[9]H.Miura,X.Yang,T.Sakai,H.Nogawa,S.Miura,Y.Watanabe,J.J.Jones,Phil.Mag.85(2005)3553.[10]O.Stidikov,R.Kaibyshev,T.Sakai,Mater.Sci.Forum419–422(2003)521.[11]Y.Chino,M.Kobata,H.Iwasaki,M.Mabuchi,Acta Mater.51(2003)3309.[12]A.Mwembela,E.B.Konopleva,H.J.McQueen,Scr.Mater.37(1997)1798.[13]H.Somekawa,T.Mukai,Scr.Mater.54(2006)633.[14]X.Yang,H.Miura,T.Sakai,Mater.Sci.Forum419–422(2003)515.[15]A.Galiyev,R.Kaibyshev,T.Sakai,Mater.Sci.Forum419–422(2003)509.[16]O.Sitdikov,R.Kaibyshev,Mater.Trans.42(2001)1928.[17]A.Galiyev,R.Kaibyshev,G.Gottstein,Acta Mater.49(2001)1199.[18]M.R.Barnett,Acta Mater.56(2008)5.[19]J.Koike,Metall.Mater.Trans.A36(2005)1689.[20]I.A.Yakubtsov,B.J.Diaka,C.A.Sager,B.Bhattacharya,W.D.MacDonald,M.Niewczas,Mater.Sci.Eng.A496(2008)247.[21]E.W.Kelley,W.F.Hosford,Trans.TMS-AIME242(1968)5.[22]L.Jiang,J.J.Jonas,R.K.Mishra,A.A.Luo,A.K.Sachdev,S.Godet,Acta Mater.55(2007)3899.[23]B.C.Wonciewicz,W.A.Backofen,Trans.Metall.Soc.AIME239(1967)1422.[24]W.H.Hartt,R.E.Reed-Hill,Trans.Metall.Soc.AIME239(1967)1511.[25]W.H.Hartt,R.E.Reed-Hill,Trans.Metall.Soc.AIME242(1968)1127.[26]D.Ando,J.Koike,J.Jpn.Inst.Met.71(2007)684.[27]M.R.Barnett,Mater.Sci.Eng.A464(2007)1.[28]M.D.Nave,M.R.Barnett,Scr.Mater.51(2004)881.[29]M.R.Barnett,Z.Keshavarz,A.G.Beer,X.Ma,Acta Mater.56(2008)5.[30]H.Yoshinaga,R.Horiuchi,Mater.Trans.JIM4(1963)8.。
CALPHAD软件介绍
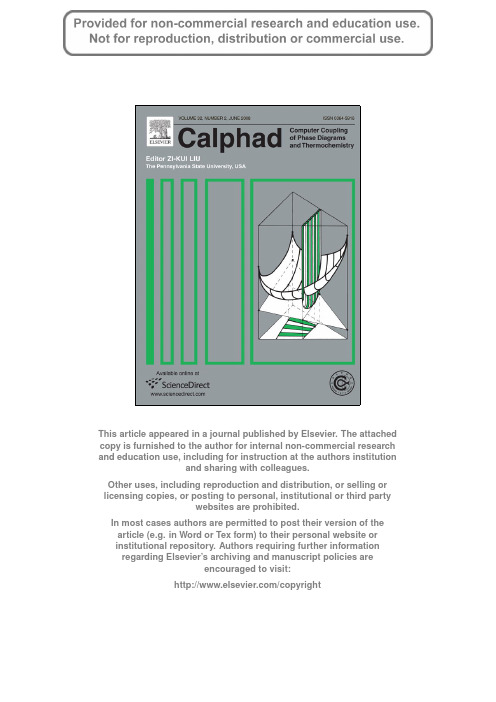
Abstract
The phase-field method has become an important and extremely versatile technique for simulating microstructure evolution at the mesoscale. Thanks to the diffuse-interface approach, it allows us to study the evolution of arbitrary complex grain morphologies without any presumption on their shape or mutual distribution. It is also straightforward to account for different thermodynamic driving forces for microstructure evolution, such as bulk and interfacial energy, elastic energy and electric or magnetic energy, and the effect of different transport processes, such as mass diffusion, heat conduction and convection. The purpose of the paper is to give an introduction to the phase-field modeling technique. The concept of diffuse interfaces, the phase-field variables, the thermodynamic driving force for microstructure evolution and the kinetic phase-field equations are introduced. Furthermore, common techniques for parameter determination and numerical solution of the equations are discussed. To show the variety in phase-field models, different model formulations are exploited, depending on which is most common or most illustrative. c 2007 Elsevier Ltd. All rights reserved.
EBSD Observations of Recrystallisation and Tensile Deformation in Twinning Induced Plasticity Steel
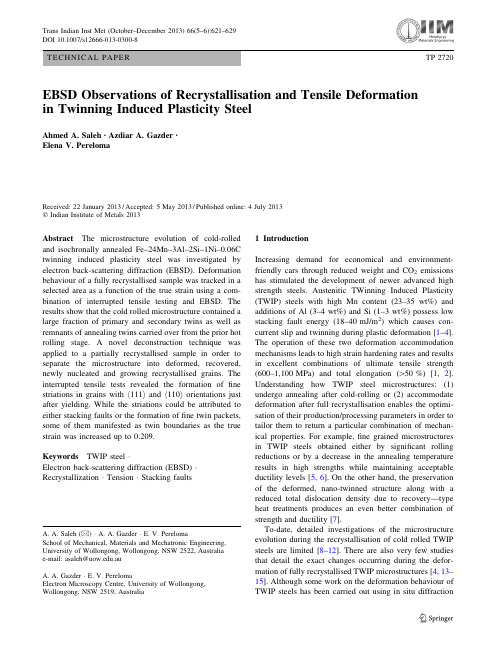
TECHNICAL PAPER TP 2720EBSD Observations of Recrystallisation and Tensile Deformation in Twinning Induced Plasticity SteelAhmed A.Saleh •Azdiar A.Gazder •Elena V.PerelomaReceived:22January 2013/Accepted:5May 2013/Published online:4July 2013ÓIndian Institute of Metals 2013Abstract The microstructure evolution of cold-rolled and isochronally annealed Fe–24Mn–3Al–2Si–1Ni–0.06C twinning induced plasticity steel was investigated by electron back-scattering diffraction (EBSD).Deformation behaviour of a fully recrystallised sample was tracked in a selected area as a function of the true strain using a com-bination of interrupted tensile testing and EBSD.The results show that the cold rolled microstructure contained a large fraction of primary and secondary twins as well as remnants of annealing twins carried over from the prior hot rolling stage.A novel deconstruction technique was applied to a partially recrystallised sample in order to separate the microstructure into deformed,recovered,newly nucleated and growing recrystallised grains.The interrupted tensile tests revealed the formation of fine striations in grains with h 111i and h 110i orientations just after yielding.While the striations could be attributed to either stacking faults or the formation of fine twin packets,some of them manifested as twin boundaries as the true strain was increased up to 0.209.Keywords TWIP steel ÁElectron back-scattering diffraction (EBSD)ÁRecrystallization ÁTension ÁStacking faults1IntroductionIncreasing demand for economical and environment-friendly cars through reduced weight and CO 2emissions has stimulated the development of newer advanced high strength steels.Austenitic TWinning Induced Plasticity (TWIP)steels with high Mn content (23–35wt%)and additions of Al (3–4wt%)and Si (1–3wt%)possess low stacking fault energy (18–40mJ/m 2)which causes con-current slip and twinning during plastic deformation [1–4].The operation of these two deformation accommodation mechanisms leads to high strain hardening rates and results in excellent combinations of ultimate tensile strength (600–1,100MPa)and total elongation ([50%)[1,2].Understanding how TWIP steel microstructures:(1)undergo annealing after cold-rolling or (2)accommodate deformation after full recrystallisation enables the optimi-sation of their production/processing parameters in order to tailor them to return a particular combination of mechan-ical properties.For example,fine grained microstructures in TWIP steels obtained either by significant rolling reductions or by a decrease in the annealing temperature results in high strengths while maintaining acceptable ductility levels [5,6].On the other hand,the preservation of the deformed,nano-twinned structure along with a reduced total dislocation density due to recovery—type heat treatments produces an even better combination of strength and ductility [7].To-date,detailed investigations of the microstructure evolution during the recrystallisation of cold rolled TWIP steels are limited [8–12].There are also very few studies that detail the exact changes occurring during the defor-mation of fully recrystallised TWIP microstructures [4,13–15].Although some work on the deformation behaviour of TWIP steels has been carried out using in situ diffractionA.A.Saleh (&)ÁA.A.Gazder ÁE.V.PerelomaSchool of Mechanical,Materials and Mechatronic Engineering,University of Wollongong,Wollongong,NSW 2522,Australia e-mail:asaleh@.auA.A.Gazder ÁE.V.PerelomaElectron Microscopy Centre,University of Wollongong,Wollongong,NSW 2519,AustraliaTrans Indian Inst Met (October–December 2013)66(5–6):621–629DOI10.1007/s12666-013-0300-8measurements[16,17],the observation of their micro-structure evolution during straining is typically limited to ex-situ examinations of various samples and different areas [4,13–15].To this end,the present work extensively employs the Electron Back-Scattering Diffraction(EBSD)technique to track microstructure evolution in TWIP steel during:(1) isochronal annealing after cold-rolling to42%thickness reduction,and(2)uniaxial tensile loading of a fully re-crystallised sample in a selected area of interest.2Experimental and Analytical ProcedureAn as-cast TWIP steel slab with the nominal composition 24Mn–3Al–2Si–1Ni–0.06C wt%was homogenised at 1,100°C for2h,hot rolled to52%thickness reduction at the same temperature in4passes at*17%reduction per pass then cold rolled to42%thickness reduction(equivalent to a true strain of0.55)in11passes at*4.8%reduction per pass.3091097.3mm3samples were cut from the cold-rolled strip and subjected to isochronal annealing between 600and850°C which included240s of heating to stable temperature and300s of soaking time followed by imme-diate water quenching.Vickers microhardness with a500g load was used to estimate the fraction softened as a function of the isochronal annealing temperature.All EBSD mapping was undertaken on a JEOL–JSM7001Ffield emission gun—scanning electron micro-scopefitted with a Nordlys-II(S)camera and the Oxford Instruments AZtec software suite operating at15kV, *2–5nA and15mm working distance.Microstructure characterisation of the isochronally annealed samples was conducted on the rolling direction(RD)—normal direction (ND)plane of the samples in the middle of the sample cross-sectional thickness.Step sizes of0.05and0.4l m were used for the cold rolled sample in order to acquire selected and large area statistics,respectively.While a step size of 0.125l m was used for the600°C sample,a step size of 0.175l m was manintained constant for all other partially recrystallised conditions.Post-processing of the EBSD maps was carried out using the HKL Channel-5software package.Low-angle grain boundaries(LAGBs)and high-angle boundaries(HAGBs) possess misorientations between2°B h\15°and15°B h B57.5°respectively.The total high angle grain boundary (THAGBs,15°B h B62.5°)population comprises HAGBs and twin boundaries(TBs).The twin boundaries consist of first order(R3=60°h111i)and second order(R9=38.9°h101i)TBs.The partially recrystallised EBSD map for the700°C condition was deconstructed into subsets comprising deformed,recovered,newly nucleated and growing recrystallised grains in accordance with the methodology described in Ref.[18].In brief,the unrecrystallised and recrystallised fractions werefirst separated using a grain orientation spread(GOS)threshold(h C)of1.5°.Then the un-recrystallised fraction was further sub-divided into deformed and recovered subsets by applying an internal misorientation threshold of7°.Lastly,the recrystallised fraction was sub-divided into newly nucleated and growing recrystallised grains by applying a threshold based on the arithmetic mean of the frequency distribution of the recrystallised grain size.The latter accounts for the increasing(sub)grain size with higher isochronal annealing temperature.To study the deformation behaviour,aflat dog-bone shaped tensile sample of25mm gage length and5mm width was wire-cut from the850°C,fully recrystallised material such that its gage length and width were parallel to the rolling(RD)and the transverse(TD)directions, respectively.Uniaxial tensile testing was undertaken on an in-house modified5kN Kammerath&Weiss tensile stage operating in speed control mode at5l m/s.The tension test was interrupted at predetermined load levels and the EBSD mapping was conducted on a defined area of interest in the middle of the gage length at a constant step size of0.1l m. 3Results and Discussion3.1Effect of Isochronal AnnealingThe change in microhardness as a function of the iso-chronal annealing temperature and the area fractions soft-ened and recrystallised estimated from microhardnessand Fig.1The evolution of the microhardness with higher isochronal annealing temperature and the fractions softened and recrystallised estimated by microhardness and EBSD,respectivelyEBSD measurements,respectively are shown in Fig.1.Representative inverse pole figure (IPF)maps of the cold-rolled and partially recrystallised microstructures aligned with the horizontal RD are depicted in Fig.2.The microstructure of the cold-rolled sample comprises elongated grains along the RD (Fig.2a)where the imposed strain was accommodated inhomogeneously via various deformation modes.Some grains are free of twinsandFig.2Representative inverse pole figure (IPF)maps of a 42%cold-rolled,b 600°C recovered,c 700°C,d 750°C,e 775°C,and f 850°C partially recrystallised TWIP GBs (2°B h \15°)=grey ;HAGBs (15°B h B 57.5°)=black ;60°h 111i R 3TBs =red ;38.9°h 101i R 9TBs =white ;RD =horizontal .(Color figure online)deformed via slip only,whereas others contain twins and in some instances,microscopic shear bands[as indicated by the arrows in Fig.2a(inset)].The deformation twins are present either as parallel primary twins occasionally rotated towards RD or as intersecting arrangements of primary and secondary twins.In addition,some coarse annealing twins carried over from prior hot rolling are also detected.The600°C sample(Fig.2b)recorded*16%softening from the microhardness measurements and*3%recrys-tallisation from the EBSD maps.The discrepancy in the above values is due to recovery processes involving the rearrangement of the dislocation substructures(carried over from cold-rolling)resulting in an overall reduction of the total accumulated stored energy[19].Thereafter,the process of recrystallisation proceeds rapidly with an *68%fraction softened obtained at700°C(Fig.2c).The relatively fast recrystallisation kinetics up to this stage of annealing is similar to that encountered in other TWIP steels[9].The start of recrystallisation in the600°C sample is associated with the bulging of annealing twins at grain boundaries(Figs.2b,3a).Similar twin bulging events were seen during the recovery stage in two moderately cold rolled austenitic stainless steels[20].Twin bulges at grain boundaries and the formation of nuclei with orientations either close to or twin related to the cold-rolled matrix are also found in the700°C sample(Figs.2c,3b).In relation to the twin-related nuclei,it was suggested that they ini-tially nucleate with orientations close to that of the deformed matrix and then twinning proliferates in orderto Fig.3Magnified views of a annealing twin boundaries(R3TBs)bulging at the boundaries between two grains at600°C,and b a nucleationevent observed at700°C.c The change in misorientation distribution as a function of the isochronal annealing temperatureTable1The change in the average recrystallised grain size,average misorientation(h AVG°)and grain boundary area fraction with isochronal annealing temperatureSample Recrytallised grain size(l m)Average misorientation(h AVG°)Area fraction(%)w/o TBs with TBs LAGB HAGB R9TB R3TBAs-CR––14.1579.1±1.69.4±0.20.4±0.411.5±2.2 600°C––15.9774.1±0.611.4±1.10.6±0.714.6±2.5 700°C 3.6±2.7 2.1±1.436.7930.3±1.434.9±0.3 5.6±0.134.8±2.4 750°C 4.9±3.7 2.7±1.848.879.4±0.848.1±0.510.7±0.142.5±2.1 775°C 4.9±3.7 2.7±2.048.97 5.3±0.247.0±0.77.4±0.147.7±1.7 850°C7.9±5.5 4.4±3.048.49 4.4±0.650.2±0.67.1±0.245.4±0.9form HAGBs with the matrix[21].While observing similar nucleation events during the recrystallisation of a97% cold rolled bronze(Cu–10Sn),Peters[22]proposed that the first nuclei form by polygonisation with orientations close to the deformed matrix;subsequent to which,first and second order twinning takes place.Following the above,the progress of recrystallisation tends to continue slightly more sluggishly;reaching an *83%fraction recrystallised at750°C and a96% fraction recrystallised at850°C(Fig.2d–f).If TBs are disregarded as grain boundaries,the equivalent circle diameter—based average recrystallised grain size increases from 3.6±2.7l m at700°C to*7.9l m at850°C (Table1).However,the grain refining effect of annealing twins is highlighted by the fact that when TBs are con-sidered as grain boundaries,the average recrystallised grain size reduces by as much as1.7±0.2times.The effect of isochronal annealing temperature on the misorientation distribution is shown in Fig.3c and the average misorientation and the various boundaryarea Fig.4Inverse polefigure maps of the700°C sample deconstructed into a deformed,b recovered,c newly nucleated,and d growing grain fractions.e The misorientation distribution of the various fractions of the700°C sample,and f the misorientation distributions at the interface between newly nucleated and unrecrystallised fractions of the700,750and775°C samples.RD=horizontal.Reprinted with permission from Elsevier,copyright2011[12]fractions are summarised in Table 1.The cold-rolled microstructure is dominated by LAGBs along with minor fractions of HAGBs and TBs.The nucleation events seen in the 600and 700°C samples (Fig.3a,b)and the con-current grain growth seen in Fig.2b–f leads to increases in the R 3and R 9area fractions (first and second order TBs,respectively)up to the 750°C sample.Up to this point,the relatively low fraction of R 9boundaries compared to R 3[11]can be attributed to the limited impingement of R 3boundaries leading to R 9formation via the twinning reaction [23]:R 3?R 3?R 9.Thereafter,the decrease in the R 9boundary area fraction towards the end of recrys-tallisation process (775and 850°C)conforms with the ‘‘R 3regeneration model’’proposed by Randle [23]which pos-tulates the twinning reaction:R 3?R 9?R 3.The unrecrystallised (deformed and recovered)and re-crystallised (newly nucleated and growing grain)fractions of the partially recrystallised 700°C sample are shown in Fig.4a–d.Their corresponding misorientation distributions are given in Fig.4e.While the unrecrystallised fraction is dominated by LAGBs,the recovered grains have an expect-edly lower fraction of LAGBs compared to the deformed grains as the recovered grains possess lower internal misori-entations due to the dislocation annihilation upon annealing.The fraction of first order R 3TBs is the lowest in the deformed grains,is higher in recovered grains,is the highest in the newly nucleated grains and then reduces again in the growing grain fraction.On the other hand,the fraction of second order R 9TBs are more pronounced in the recrystallised fractions than the unrecrystallisedfractions.The lower R 3TB population in the growing grain fractions as opposed to their newly nucleated counterparts follows Gindraux and Form [24]where annealing twins proliferate to reorient the grain boundaries in order to facilitate dislocation absorption and mobility during the initial stages of recrystallisation.Here,twinning contrib-utes significantly to the overall reduction in stored energy during nucleation.Thereafter,during the grain growth stage,the previously formed twins are annihilated and a relatively limited evolution of newer twins occurs.The growth kinetics in TWIP steel can be explained by examining the grain boundary character at the common interface between the newly nucleated and unrecrystallised fractions via subset double-dilation [18]for the 700,750and 775°C samples (Fig.4f).The low-mobility LAGBs and TBs together constitute *59,41and 47%of the total interface boundary population at 700,750and 775°C,respectively.It suggests that orientation-dependent,stored energy consid-erations have a dominant role in dictating the evolution of the microstructure during the recrystallisation process [12].Thus,newly nucleated grains with orientations that inher-ently possess locally higher stored energies will have a growth advantage in order to maximise the release of the stored energy carried over from cold rolling [25].3.2Effect of Uniaxial TensionThe true stress versus strain curve of the 850°C,fully recrystallised sample is given in Fig.5.The red circles in this figure correspond to true strains of 0,0.0014,0.023,0.072,and 0.209and are the points where the tensile test was interrupted for EBSD measurements.The microstruc-ture evolution of the selected area with increasing tensile strain is shown in Fig.6via IPF maps.Similar to Fig.2f and the discussion of its microstructure in Sect.3.1,the initial recrystallised microstructure comprises equiaxed grains with a high fraction of annealing twin R 3boundaries (Fig.6a;Table 2).Expectedly,no change in the microstructure is detected at a true strain of 0.0014(cf.Fig.6a,b)since it corre-sponds to a stress of *210MPa which is lower than the macro-yielding point at *290MPa.At a true strain of 0.0023,striations in the form of single lines or parallel packets evolve preferentially in grains with oreinations close to h 111i and h 110i (Fig.6c).These striations origi-nate mostly at the grain and twin boundaries,while in fewer instances they start and finish within a grain.Inter-secting striations were also detected in a few grains as shown by the white circle in Fig.6c.The number of striations increases progressively upon straining to 0.072and 0.209with some of them being indexed as deformation twin boundaries (indicated by the black arrows in Fig.6d,e).Due to the limitations oftheFig.5The true stress versus true strain curve of the fully recrystal-lised 850°C sample subjected to uniaxial tension.The red circles indicate the true strains at which the tensile test was interrupted for EBSD mapping.(Color figure online)EBSD technique in general and the adopted experimental methodology in particular,there are two possibilities related to the provenance of these striations.As pointed out in previous studies [4],since the thick-ness of deformation twins at low strain levels is in the order of tens of nanometers,they cannot be crystallographically detected due to the limited spatial resolution of the EBSD technique.With increasing strain,the twinning activityincreases such that the twins stack into relatively thick bundles which are eventually detectable by EBSD.Alternatively,TEM investigations of low stacking fault energy austenitic steels during the early stages of defor-mation have frequently reported the formation of stacking faults.Stacking faults were recently observed in the aus-tenite grains of transformation induced plasticity steel at a tensile strain of 0.005[26].Prior to the observation of deformation twinning,stacking faults in the form of widely separated partial dislocations or as long and narrow straight striations have also been detected in a Fe–18Mn–0.6C–1.5Al TWIP steel at a tensile strain of 0.04[15].As opposed to other EBSD studies on TWIP steel deformation behaviour [4],the present work tracks the evolution of the same set of grains up to 0.209true strain.This enables the observation of the change in the nature of the striations;from initial lines of high band contrast at 0.023true strain to their identification as twin boundaries from 0.072true strain onwards.Thus,rather than inter-preting the striations as thin,unindexed twins,it ismoreFig.6Inverse pole figure maps at true strains of a 0,b 0.0014,c 0.023,d 0.072,and e 0.209.f Inverse pole figure showing the orientations of twin-free and twinned grains from e as clear black and solid red squares ,GBs =grey ;HAGBs =black ;60°h 111i R 3TBs =red ;RD =horizontal .(Color figure online)Table 2The change in the average misorientation (h AVG °)and grain boundary area fraction with greater true strain during uniaxial tensile loadingStrain (%)Average misorientation (h AVG °)Area fraction (%)LAGB HAGB R 3TB049.76 2.1848.1949.640.1449.76 2.0648.6149.332.348.02 4.7348.7746.57.241.2118.7243.8537.4420.922.7759.422.2118.39probable that they are stacking faults that form preferen-tially at the grain and twin boundaries(Fig.6c).Conse-quently,and as proposed by Byun[27],the divergence of the dissociated partial dislocations to an infinite separation distance with increasing tensile strain leads to twin formation.The black areas in Fig.6d,e depict unindexed regions in the EBSD maps due to the increase in the surface rough-ness of the sample via the orange-peel effect which is a manifestation of the anisotropic nature of plastic strain within individual grains[28].Additionally,and with increasing tensile strain,grains start popping out of the plane of the tensile sample surface forming peaks and valleys;which indicates that a significant part of the strain is accommodated at the grain boundaries.The change in the grain boundary area fraction with increasing tensile strain is given in Table2.The area fraction of LAGBs continues to increase and is associated with a concurrent decrease in the HAGBs and R3TBs population.Since both annealing and deformation twin boundaries follow the same R3=60°h111i relationship,it is not possible to distinguish between them on the basis of mis-orientation or crystallography.However,the main advan-tage of observing the same area while a sample undergoes uniaxial tension is that it also allows us to track the evo-lution of the annealing twins at different strains.As illus-trated by the white ovals in Fig.6d,e,the annealing twin boundaries at0.023and0.072strain are later identified as regular HAGBs at a tensile strain of0.209(Fig.6e).This decay of the annealing twin boundaries is due to the local lattice rotation at the sides of the TBs leading to a deviation from the exact60°h111i relationship[29].This deviation increases with greater tensile strain until it exceeds the employed tolerance limit of6°(following the Palumbo-Aust criterion).Hence,such boundaries are no longer identified as TBs but are rather recognised as being regular HAGBs.Accordingly,and despite the evolution of defor-mation twins,the area fraction of TBs generally decreases with increasing tensile strain.An additional reason for the diminishing twin boundary fraction is the masking effect associated with the increasing area fraction of LAGBs (Table2).Lastly,an example detailing the effect of deformation twinning is discussed.The orientations of twin-free and twinned grains at a tensile strain of0.209are shown on the IPF in Fig.6f as clear black and solid red squares, respectively.The dashed black line on the IPF(Fig.6f) indicates the area where the Schmid factors for slip and twinning are equal.Thus the area to the left of the dashed line denote orientations with higher Schmid factors that favour slip while the region to the right of the dashed line comprise orientations with higher Schmid factors that favour twinning.In this regard,Fig.6f clearly shows some twinned grains(solid red squares)falling to the left of the dashed black line and within the region that favours slip. This observation is in agreement with previous investiga-tions that correlate twinning activity with the crystallo-graphic orientations of TWIP steels[13,14].Gutierrez-Urrutia et al.[14]suggested that while the orientation dependence of twinning follows Schmid’s law at low strains,it increasingly deviates away from it with greater accumulated strain.They ascribed the deviation to the local stress concentration effect which is induced by the inter-action with neighbouring grains.On the other hand,we postulate that the presumed deviation from Schmid’s law at higher tensile strains is the result of the increased feasi-bility of twin nucleation via extrinsic stacking faults in orientations with low Schmid factors for twinning[30]. 4ConclusionsThe application of EBSD allows for detailed insights into the evolution of the microstructure in TWIP steel during isochronal annealing and uniaxial tensile loading.The strain imposed during cold rolling to42%thickness reduction was accommodated via various deformation mechanisms including slip,twinning and micro-shear banding.From the early stages of recrystallisation, annealing twins contribute to nucleation events as twin bulges and twin-related nuclei.The subsequent growth of the newly nucleated grains is affected by orientation-dependent,stored energy considerations as well as second-order twinning.During the early stages of uniaxial tensile loading,the presumed formation of stacking faults were observed as striations in grains with orientations close to h111i and h110i.With increasing tensile strain,some of these stria-tions were successfully indexed as twin boundaries.The area fraction of annealing twin boundaries decreases with greater tensile strain due to local lattice rotation effects which lead to a deviation from the exact60°h111i rela-tionship.The deviation from Schmid’s law with increasing tensile strain can be ascribed to the increased feasibility of twin nucleation via extrinsic faulting in grains that are nominally regarded as being unfavourably oriented for twinning.Acknowledgments The authors are grateful to Prof.D.B.Santos of the Federal University of Minas Gerais,Brazil for providing the source material.The authors acknowledge the use of the JEOL–JSM7001F FEG-SEM at the UOW Electron Microscopy Centre purchased with thefinancial support from the Australian Research Council(LE0882613).References1.Grassel O,Kruger L,Frommeyer G,Meyer L W,Int J Plast16(2000)1391.2.Frommeyer G,Bru¨x U,Neumann P,ISIJ Int43(2003)438.3.Vercammen S,Blanpain B,De Cooman B C,Wollant P,ActaMater52(2004)2005.4.Barbier D,Gey N,Allain S,Bozzolo N,Humbert M,Mater SciEng A500(2009)196.5.Bouaziz O,Allain S,Scott C,Scr Mater58(2008)484.6.Ueji R,Tsuchida N,Terada D,Tsuji N,Tanaka Y,Takemura A,Kunishige K,Scr Mater59(2008)963.7.Bouaziz O,Scott C P,Petitgand G,Scr Mater60(2009)714.8.Scott C,Allain S,Faral M,Guelton N,Rev Metall6(2006)293.9.Bracke L,Verbeken K,Kestens L,Penning J,Acta Mater57(2009)1512.10.Santos B D,Saleh A A,Gazder A A,Carman A,Duarte D M,Ribeiro E´A S,Gonzalez B M,Pereloma E V,Mat Sci Eng A528 (2011)3545.11.Saleh A A,Gazder A A,Santos B D,Pereloma E V,Adv MaterRes409(2012)719.12.Gazder A A,Saleh A A,Pereloma E V,Scr Mater65(2011)560.13.Yang P,Xie Q,Meng L,Ding H,Tang Z,Scripta Mater55(2006)629.14.Gutierrez-Urrutia I,Zaefferer S,Raabe D,Mat Sci Eng A527(2010)3552.15.Beladi H,Timokhina I B,Estrin Y,Kim J,De Cooman B C,KimS K,Acta Mater59(2011)7787.16.Yan K,Carr D G,Callaghan M D,Liss K-D,Li H,Scr Mater62(2010)246.17.Saleh A A,Pereloma E V,Clausen B,Brown D W,Tome´C N,Gazder A A,Acta Materialia(2013).doi:10.1016/j.actamat.2013.05.017.18.Gazder A A,Sanchez-Araiza M,Jonas J J,Pereloma E V,ActaMater59(2011)4847.19.Humphreys F J,Hatherly M,Recrystallisation and RelatedAnnealing Phenomena,2nd ed.,Elsevier,Oxford(2004).20.Jones A R,J Mater Sci16(1981)1374.21.Field D P,Bradford L T,Nowell M M,Lillo T M,Acta Mater55(2007)4233.22.Peters B F,Met Trans4(1973)757.23.Randle V,Acta Mater47(1999)4187.24.Gindraux G,Form W,J Inst Met101(1973)85.25.Sebald R,Gottstein G,Acta Mater50(2002)1587.26.Rafaja D,Krbetschek C,Borisova D,Schreiber G,Klemm V,Thin Solid Films530(2013)105.27.Byun T S,Acta Mater51(2003)3063.28.Reed-Hill R E,Physical Metallurgy Principles,New York:D.Van Nostrand Company(1973).29.Mishra S K,Tiwari S M,Kumar A M,Hector L G,Met MatTrans A43(2012)1598.30.Gazder A A,Saleh A A,Pereloma E V,Scr Mater68(2013)436.。
Microstructural evolution

(Received 19 August 1997; accepted 22 October 1997)
Abstract Calcium aluminate bonded alumina-spine1 castable refractories have been fabricated with in-situ spine1 formation. Spine1 formation occurs between 1200 and 1400°C with a net-like morphology inter-linked with CaO-MgO-AIIOjrSiOZ phases. Spine1 generated at 1400°C is nearly stoichiometric but at higher temperatures it progessively enriches in AIzO+ The calcium aluminate phases in the cement bond react to form platey CA6 crystals between 1200 and 1400°C which coexist with the spine1 and penetrate and bond to tabular alumina grains. The potential e#ect of these morphologies on properties is discussed. 0 1998 Elsevier Science Limited. All rights reserved
*On secondment from Montanuniversitat tAIso KSR International Ltd., Beauchief,