分子筛固载钌催化剂的制备及二氧化碳加氢反应的研究
固载Ru基催化剂上二氧化碳加氢合成甲酸
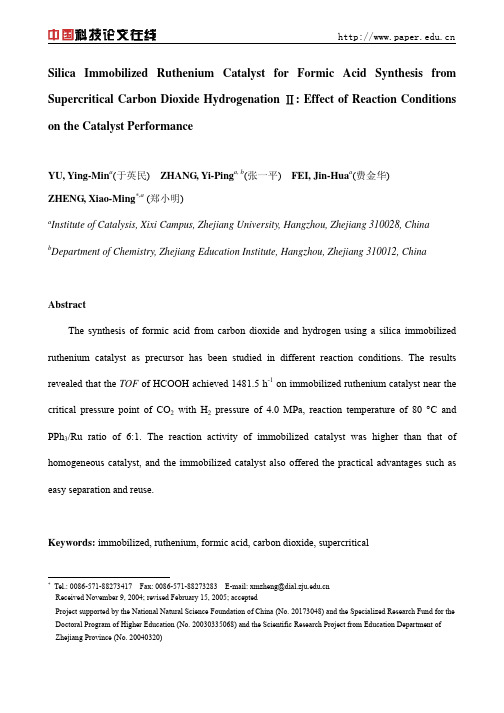
Silica Immobilized Ruthenium Catalyst for Formic Acid Synthesis from Supercritical Carbon Dioxide Hydrogenation Ⅱ: Effect of Reaction Conditions on the Catalyst PerformanceYU, Ying-Min a(于英民) ZHANG, Yi-Ping a, b(张一平) FEI, Jin-Hua a(费金华)ZHENG, Xiao-Ming*,a(郑小明)a Institute of Catalysis, Xixi Campus, Zhejiang University, Hangzhou, Zhejiang 310028, Chinab Department of Chemistry, Zhejiang Education Institute, Hangzhou, Zhejiang 310012, ChinaAbstractThe synthesis of formic acid from carbon dioxide and hydrogen using a silica immobilized ruthenium catalyst as precursor has been studied in different reaction conditions. The results revealed that the TOF of HCOOH achieved 1481.5 h-1 on immobilized ruthenium catalyst near the critical pressure point of CO2 with H2 pressure of 4.0 MPa, reaction temperature of 80 °C and PPh3/Ru ratio of 6:1. The reaction activity of immobilized catalyst was higher than that of homogeneous catalyst, and the immobilized catalyst also offered the practical advantages such as easy separation and reuse.Keywords: immobilized, ruthenium, formic acid, carbon dioxide, supercritical* Tel.: 0086-571-88273417 Fax: 0086-571-88273283 E-mail: xmzheng@Received November 9, 2004; revised February 15, 2005; acceptedProject supported by the National Natural Science Foundation of China (No. 20173048) and the Specialized Research Fund for the Doctoral Program of Higher Education (No. 20030335068) and the Scientific Research Project from Education Department of Zhejiang Province (No. 20040320)IntroductionIn recent years, the efficient conversion and application of carbon dioxide as a chemicalfeedstock has received ongoing attention, because it is a natural and abundant carbon source and hasbeen considered a major atmosphere pollutant, responsible for the greenhouse effect. The catalytichydrogenation of carbon dioxide produces products ranging from alkylanes, alkenes, alcohols,aldehydes and ethers to acids.Among the possible valuable chemical compounds, much attention has been paid to thehydrogenation of carbon dioxide to formic acid,1-6 because it is an atom economic reaction with nowaste produced. But the process is thermodynamically unfavorable. The conversion CO2(g) + H2(g)→HCOOH(l) occurs with ∆G o298= +32.9 kJ·mol-1, the equilibrium conversion of CO2 is 0.72×10-5at 3.0 MPa, 100 °C and 0.14×10-4 at 6.0 MPa, 100 °C, respectively.7 When this reaction was in amixture of scCO2 (supercritical carbon dioxide), H2 and NEt3, a TOF (turnover frequency, mol ofHCOOH/mol of Ru/h ) of 1400 h-1 was obtained using RuH2(PMe3)4 homogeneous catalysts.3However, the separation of the relatively expensive catalysts from the reaction mixture systemis one of the major drawbacks of the homogeneous catalysis. An available solution to this separationproblem is the heterogenisation of homogeneous catalysts. To immobilize homogeneous catalystson solid supports via linkers has become the most often employed method. Herein, we reported thesynthesis of formic acid from CO2 and H2 using ruthenium immobilized on functionalized silica. Itwas found that good performance was achieved when CO2 was in supercritical condition, and thecatalyst could be recovered from the reaction mixture by filtration easily and then, potentially bereused.ExperimentalPreparation of the immobilized ruthenium catalyst precursorIn a typical surface modification process, a mixture of fumed silica (6 g), anhydrous toluene (140 mL) and γ-aminopropyl triethoxysilane (4.65 g) was refluxed for 8 h, then 25 mL of H 2O were added. The mixture was stirred again for 4 h. By reaction of γ-aminopropyl triethoxysilane with the silanol groups, amino ones were grafted onto silica (see Scheme 1). The product was filtered, washed with toluene in order to remove the remaining non-bonding organic amine, and then dried in vacumn at 200 °C for 5 h. The organic amine functionalized silica (Si)-NH 2 was obtained. The amount of amino groups loaded on silica measured by element analysis was 1.76 mmol per gram of catalyst.Scheme 1SiO 2OHOHOH OH +(C 2H 5O)3Si(CH 2)3NH2SiO 2OH O O OSiNH 2Then a mixture of RuCl 3·3H 2O (0.035 g), (Si)-NH 2(1 g) and ethanol (40 mL) was stirred at room temperature for 1 h. The resultant solid, identified as (Si)-NH 2-RuCl 3, was filtered, washed with ethanol and dried in air. The ruthenium content in (Si)-NH 2-RuCl 3 was measured by ICP instrument, to be 3.38×10-2 mmol per gram of catalyst.The active ruthenium complex catalyst responsible for the HCOOH formation was synthesized in situ during the catalytic reaction with (Si)-NH 2-RuCl 3 and triphenylphosphine.Catalytic reactionThe hydrogenation of CO 2 was carried out in a stainless steel 100 ml autoclave. In a typical run, 0.6 g of the immobilized catalyst (Si)-NH 2-RuCl 3 was used. Then solvent (ethanol, 20 mL), ligand(triphenylphosphine, 0.06 g) and base (triethylamine, 5 mL) were added into the autoclave. The vessel was flushed with H2 three times to remove air and pressurized up to 4.0 MPa with H2. Then the liquid CO2 was pumped into the autoclave from a cooled(-5 °C) reservoir using a syringe pump to reach the desired pressure. The vessel was heated to the reaction temperature (80 °C) and the pressure became 16.0 MPa after temperature equilibration, and the reaction was stirred for the desired reaction time. At the end of the reaction period, the reactor was cooled rapidly by being placed in a cold water bath and vented carefully. The reaction solution collected was acidified and the formic acid esterified completely for analysis. Qualitative and quantitative analyses were conduced both by GC-MS equipped with TC-wax column and GC equipped with poropak QS column and FID detector. The two results were consistent with each other.Results and discussionPhase behaviorThe critical point of CO2 is at a T of 33.1 °C and a P of 7.23 MPa. Under the normally applied condition, the reaction proceeded at 80 °C, H2 pressure 4.0 MPa with the total pressure 16.0 MPa and in the supercritical CO2 region.Although the reaction was performed under scCO2 condition, the system contained also other components. The upper phase was predominantly gaseous H2, while the lower phase, which was the reaction phase, included the solvent, the base, the catalyst, also the dissolved CO2 and H2. A large amount of CO2 was present in the lower liquid phase.3 It is likely that the large amount of CO2 in the lower phase increased the solubility of H2 in this phase relative to the solubility of H2 in liquid solvent, thus making scCO2 a good medium for its own hydrogenation.Effect of CO 2 pressureThe effect of CO 2 pressure on the reaction rate is shown in Figure 1. It can be found that at the beginning, the TOF of HCOOH was increased with increasing CO 2 pressure and a maximum value (1197 h -1) appeared at 7.5 MPa. When the CO 2 pressure was further up to 8.5, 9.5 and 12 MPa, the TOF of HCOOH was slightly decreased to 1192, 1180 and 1161 h -1, but those were still higher than that at 6.0 MPa. The 7.5 MPa of CO 2 pressure, which was just the point a little exceeding the critical pressure of CO 2 (7.23 MPa), led to reduce the phase transfer barrier and increase the dissolvability of H 2 in scCO 2, so the high concentration of reactants and the immobilized catalyst were in the same phase to increase the rate of reaction. However, dilution effect might play a role to decrease the reaction rate at a further higher CO 2 pressure. Because at pressure higher than the critical pressure, CO 2 was already in supercritical condition, the addition of more CO 2 did not increase the dissolvability of H 2. On the contrary, the addition of more CO 2 would decrease the probability of contact and impact between catalyst and H 2, therefore the TOF of HCOOH was a bit reduced.4681012600700800900100011001200T O F /h-1CO 2 pressure /MPaFigure 1 The effect of CO 2 pressure on the rate of formic acid production.Reaction conditions: ruthenium content=0.02 mmol, reaction temperature=80 °C, H 2 pressure=4.0 MPa, reaction time=1 h, PPh 3/Ru(mol ratio)=6:1, stirring rate=250 r·min -1.Effect of H 2 pressureWith a CO 2 pressure of 12.0 MPa, the effect of H 2 pressure on the reaction rate is shown in Figure 2. The rate of HCOOH production was nearly first-order dependent on the H 2 pressure, and no formic acid was obtained in the absence of H 2, while TOF of 2019 h -1 was obtained at 8.0 MPa of H 2.T O F /h-1H 2 pressure /MPaFigure 2 The effect of H 2 pressure on the rate of formic acid production under the same reaction conditions as those of Figure 1 except CO 2 pressure=12.0 MPa instead of H 2 pressure=4.0 MPa.Effect of temperatureThe effect of the reaction temperature on the rate of formic acid production under CO 2 pressure of 4.0 MPa and scCO 2 is showed in Figure 3 and Figure 4, respectively. The results displayed that the highest TOF of HCOOH was obtained at 110 and 80 °C under CO 2 pressure of 4.0 MPa and scCO 2, respectively.It was unfavorable to chemical adsorption and activation of reactants when the reaction temperature was too low, hence the reaction activity was also low. With the increase of temperature, the average kinetic energy of reactants was increased, which was favorable to its diffusion, thus thereaction rate quickened. But when the temperature was raised to some extent, the dissolvability of CO 2 in the reaction solution and the dissolvability of H 2 in CO 2 began to decrease. On the other hand, CO 2 hydrogenation to HCOOH was an exothermic reaction, it was unfavorable to the reaction when temperature increased, and hence it was unfavorable to the undergoing of reaction iftemperature was too high.20040060080010005080110140Reaction temperature /℃T O F /h -1Figure 3 The influence of reaction temperature on the rate of formic acid production under high pressure CO 2 condition.Reaction conditions: ruthenium content=0.02 mmol, H 2 pressure=4.0 MPa, total pressure=8.0 MPa, reaction time=3 h, PPh 3/Ru(mol ratio)=6:1, stirring rate=250 r·min -1.400800120016005080110Reaction temperature /℃T O F /h -1Figure 4 The influence of reaction temperature on the rate of formic acid production under scCO 2 condition. Reaction conditions: ruthenium content=0.02 mmol, H 2 pressure=4.0 MPa, total pressure=16.0 MPa, reaction time=1 h, PPh 3/Ru(mol ratio)=6:1, stirring rate=250 r·min -1.From Figure 3 and Figure 4, it can be seen that under scCO 2 condition, the optimum reaction temperature was 80 °C , which was 30°C lower than that of high pressure CO 2 condition. And the TOF of HCOOH was higher than that of high pressure CO 2 condition with the value being 1161 h -1and 826.5 h -1, respectively. It indicated that the use of supercritical fluid as reactant could lower the reaction temperature, and the high dissolvability of H 2 in scCO 2 was responsible for it.Effect of reaction timeFigure 5 and Figure 6 show the effect of reaction time on the HCOOH production under high pressure CO 2 condition (4.0MPa) and scCO 2 (12.0MPa) at 80°C, H 2 pressure of 4.0 MPa, respectively. From Figure 5, the yield of HCOOH reached a constant after 3 h running under high pressure CO 2 condition and the value was 17.50-18.00 mmol.0123454681012141618H C O O H y i e l d /m m o lReaction time /hFigure 5 The influence of reaction time on the HCOOH yield under high pressure CO 2 condition.Reaction conditions: ruthenium content=0.02 mmol, reaction temperature=80 °C, H 2 pressure=4.0 MPa, total pressure=8.0 MPa, PPh 3/Ru(mol ratio)=6:1, stirring rate=250 r·min -1.4812162024H C O O H y i e l d /m m o lReaction time /hFigure 6 The influence of reaction time on the HCOOH yield under scCO 2 condition.Reaction conditions: ruthenium content=0.02 mmol, reaction temperature=80 °C, H 2 pressure=4.0 MPa, total pressure=16.0 MPa, PPh 3/Ru(mol ratio)=6:1, stirring rate=250 r·min -1.From scCO 2 hydrogenation condition, as showed in Figure 6, the yield of HCOOH reached equilibrium only after 1 h running, and the value was enhanced to 23.20-23.70 mmol. While carbon dioxide was in supercritical region, its diffusion coefficient and the dissolvability of hydrogen were both high, therefore CO 2 could react with H 2 rapidly, and the reaction could also reach equilibrium rapidly. That is the reason why the time of reaching equilibrium under scCO 2 condition was much shorter than at high pressure CO 2, and why the yield of HCOOH under scCO 2 condition was increased greatly than at high pressure CO 2.Effect of the ratio of PPh 3/RuFigure 7 exhibits the effect of the ratio of PPh 3/Ru on the performance of the catalyst for formic acid formation. It can be observed that there was no formic acid formed in the absence of PPh 3 ligand. When the PPh 3/Ru ratio was changed from 3:1 to 6:1, TOF of HCOOH increased from 686 to 1161 h -1. The further increase of PPh 3/Ru ratio showed a decrease of the catalytic activity, and at PPh 3/Ru ratio of 10:1, TOF was 656 h -1. Hence, the optimum amount of PPh 3 ligand should obey 6:1 of the PPh 3/Ru ratio.20040060080010001200T O F /h-1PPh 3:RuFigure 7 The influence of PPh 3:Ru ration on the rate of formic acid production under scCO 2 condition.Reaction conditions: ruthenium content=0.02 mmol, reaction temperature=80 °C, H 2 pressure=4.0 MPa, total pressure=16.0 MPa, reaction time=1 h, stirring rate=250 r·min -1.It indicated that the molar ratio of ligand to metal ion effected on the structure of the complex, the formation of active species and its stability. The proposed structure of the catalytic active ruthenium complex formed in situ identified by the method of XPS and IR as Scheme 2 described:8Scheme 2HPPh 3Ph 3The coordination number of PPh 3 in the complex was 3, but the catalytic activity reached the highest value at the PPh 3/Ru ratio of 6:1. The reason why the formation of active ruthenium complex needed more PPh 3 might be that besides some of PPh 3 was used as ligand, the other part was consumed by the oxidation-reduction reaction with RuCl 3.9 The presence of excessive PPh 3 was disadvantageous to the reaction, and this maybe related to the possible mechanism.8 In the mechanism, a PPh 3 ligand in the complex was replaced by the solvent of ROH to generate the catalytic cycle species as Scheme 3 described, and the excess of PPh 3 affected itself dissociation, thus inhibiting the catalytic activity.Scheme 3Ph 3H +PPh 3 Effect of stirring speed Figure 8 depicts the influence of stirring speed on the reaction rate under scCO 2 condition. It can be found that the TOF of HCOOH was increased with the stirring speed, and the value was 1439 h -1 at stirring speed of 500 r·min -1 while that was 1161 h -1 at stirring speed of 250 r·min -1. But when the stirring speed was above 500 r·min -1, this extent of increase was not so obvious, and the TOF of HCOOH was 1481.5 h -1 at stirring speed of 750 r·min -1. According to the analysis of phase behavior, although under scCO 2 condition, the reaction really occurred in the lower phase including the solvent, the base, the catalyst, the dissolved CO 2 and H 2. Hence, the stirring speed had an effect on the reaction activity, but external diffusion became unimportant to the reaction rate when the reaction occurred with high stirring speed state. 0500100015002000250500750Stirring rate /r·min -1T O F /h -1 Figure 8 The influence of stirring speed on the rate of formic acid production under scCO 2 condition. Reaction conditions: ruthenium content=0.02 mmol, reaction temperature=80 °C, H 2 pressure=4.0 MPa, total pressure=16.0 MPa, reaction time=1 h, PPh 3/Ru(mol ratio)=6:1.Effect of immobilizationThe catalytic activity of the ruthenium catalyst before and after immobilization has been compared in Table 1.Comparing the homogeneous system (entry 1) with the immobilized ruthenium system (entry 2), it can be found that the TOF of HCOOH was enhanced from 838 h-1 of the homogeneous system to 1161 h-1 of immobilized ruthenium system. The homogeneous catalyst showed the lower activity due to the aggregation of catalytic sites to multinuclear complexes.10 On the immobilization catalyst, the active sites could be anchored to the support, and it held back the aggregation of catalytic sites with each other. Thus, the fact is that the activity of the catalyst increased after immobilization can be ascribed to so-called site-isolation or well dispersion.Table 1 Catalytic activity of the ruthenium catalyst before and after immobilization under scCO2 condition aHCOOHEntry Catalyst/%TOF /h-1 Selectivity1 RuCl3, PPh3 838 1002 (Si)-NH2-RuCl3, PPh3 1161 100a Reaction conditions: ruthenium content=0.02 mmol, reaction temperature=80 °C, Hpressure=4.0 MPa, total2pressure=16.0 MPa, reaction time=1 h, PPh3/Ru(mol ratio)=6:1, stirring rate=250 r·min-1.The reuse of the catalystOne of the advantages of using immobilized catalysts is recyclability. After reaction, the catalyst was filtered and dried before it was used again, and the recycle occurred in the absence of triphenylphosphine ligand under the same reaction condition as that of fresh catalyst. Table 2 indicates the catalytic results with reused catalysts under scCO2 condition. To the reused catalyst,formic acid could be obtained while the recycle was performed in the absence of triphenylphosphine ligand (Table 2, Entries 2 and 3). A worthy noting detail was that there was no formic acid formed when the catalyst was first used in the absence of triphenylphosphine ligand, as shown in Figure 7. It was attributed to the formation of the catalytic active species from the immobilized ruthenium and triphenylphosphine ligand under reaction conditions in the first run, the structure of which is described in Scheme 2 as above.In addition, 1009 h-1 of TOF was maintained after it was used three times, indicating that the drop of ruthenium from amine modified silica was almost negligible and the recycling of the catalyst was possible. To prove this, after filtering the liquid collected at reaction temperature, the filtrate was used to react further, and it exhibited no activity, indicating there was no leaching of ruthenium in the catalytic run.Table 2 The catalytic results with reused catalysts under scCO2 conditionHCOOHEntry Catalyst PPh3/Ru(mol ratio)/%TOF /h-1 Selectivity1 (Si)-NH2-RuCl3, PPh3 6:1 1161 1002 Recycle-1 0 1054 1003 Recycle-2 0 1009 100 Reaction conditions: ruthenium content=0.02 mmol, reaction temperature=80 °C, H2 pressure=4.0 MPa, total pressure=16.0 MPa, reaction time=1 h, stirring rate=250 r·min-1.ConclusionThe catalyst of amine functionalized silica immobilized ruthenium complexes showed higher activity than homogeneous catalyst for formic acid production from CO2 and H2, and could berecyclable. The reaction could occur at the lower temperature with a shorter reaction time of reaching equilibrium under scCO2 than under high pressure CO2. The optimum CO2 partial pressure was near its critical point, and high H2 partial pressure afforded high reaction rate. The TOF of HCOOH achieved 1481.5 h-1 on immobilized ruthenium catalyst under scCO2 with H2 pressure of 4.0 MPa at reaction 80°C, PPh3/Ru ratio of 6:1 and stirring speed of 750 r·min-1.References1 Inoue,Y.; Izumida, H.; Sasaki,Y.; Hashimoto, H. Chem. Lett.1976, 863.2 Jessop, P. G.; Ikariya, T.; Noyori, R. Chem. Rev.1995, 95, 259.3 Jessop, P. G..; Hsiao,Y.; Ikariya, T.; Noyori, R. J. Am. Chem. Soc. 1996, 118, 344.4 Gassner, F.; Leitner, W. J. Chem. Soc., Chem. Commun.1993, 1465.5 Kröcher, O.; Köppel, R. A.; Baiker, A. J. Chem. Soc., Chem. Commun.1997, 453.6 Zhang, J. Z.; Li, Z.; Wang, H.; Wang, C. Y. J. Mol. Catal.1996, 112, 9.7 Cao, F. H.; Liu, D. H.; Hou, Q. S.; Fang, D. Y. J. Nat. Gas. Chem.2001, 10, 24 (in Chinese).8 Zhang, Y. P. Ph.D. Thesis, Zhejiang university, Hangzhou, 2003 (in Chinese).9 Wang, X. Y. Ph.D. Thesis, Zhejiang university, Hangzhou, 1999 (in Chinese).10 Pugin, B.; Müller, M. Stud. Surf. Sci. Catal. 1993, 78, 107.。
分子筛负载的Cr催化剂在二氧化碳氧化乙烷脱氢制乙烯反应中的研究的开题报告
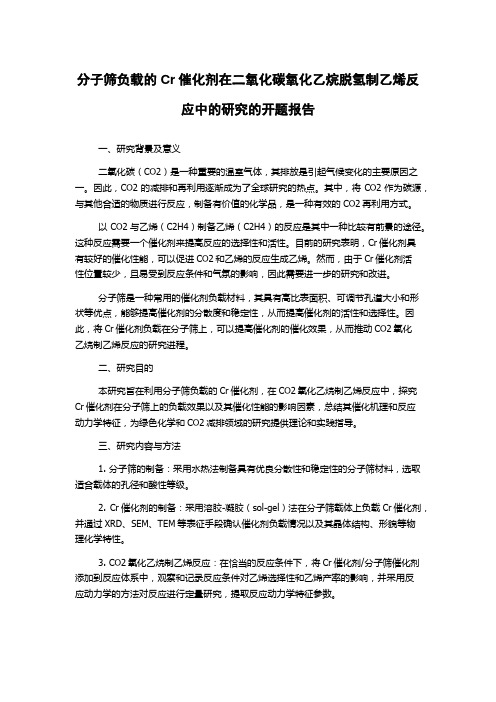
分子筛负载的Cr催化剂在二氧化碳氧化乙烷脱氢制乙烯反应中的研究的开题报告一、研究背景及意义二氧化碳(CO2)是一种重要的温室气体,其排放是引起气候变化的主要原因之一。
因此,CO2的减排和再利用逐渐成为了全球研究的热点。
其中,将CO2作为碳源,与其他合适的物质进行反应,制备有价值的化学品,是一种有效的CO2再利用方式。
以CO2与乙烯(C2H4)制备乙烯(C2H4)的反应是其中一种比较有前景的途径。
这种反应需要一个催化剂来提高反应的选择性和活性。
目前的研究表明,Cr催化剂具有较好的催化性能,可以促进CO2和乙烯的反应生成乙烯。
然而,由于Cr催化剂活性位置较少,且易受到反应条件和气氛的影响,因此需要进一步的研究和改进。
分子筛是一种常用的催化剂负载材料,其具有高比表面积、可调节孔道大小和形状等优点,能够提高催化剂的分散度和稳定性,从而提高催化剂的活性和选择性。
因此,将Cr催化剂负载在分子筛上,可以提高催化剂的催化效果,从而推动CO2氧化乙烷制乙烯反应的研究进程。
二、研究目的本研究旨在利用分子筛负载的Cr催化剂,在CO2氧化乙烷制乙烯反应中,探究Cr催化剂在分子筛上的负载效果以及其催化性能的影响因素,总结其催化机理和反应动力学特征,为绿色化学和CO2减排领域的研究提供理论和实践指导。
三、研究内容与方法1. 分子筛的制备:采用水热法制备具有优良分散性和稳定性的分子筛材料,选取适合载体的孔径和酸性等级。
2. Cr催化剂的制备:采用溶胶-凝胶(sol-gel)法在分子筛载体上负载Cr催化剂,并通过XRD、SEM、TEM等表征手段确认催化剂负载情况以及其晶体结构、形貌等物理化学特性。
3. CO2氧化乙烷制乙烯反应:在恰当的反应条件下,将Cr催化剂/分子筛催化剂添加到反应体系中,观察和记录反应条件对乙烯选择性和乙烯产率的影响,并采用反应动力学的方法对反应进行定量研究,提取反应动力学特征参数。
4. 催化剂表征和反应机理研究:通过表征技术和计算机模拟的方法,研究分子筛负载的Cr催化剂在CO2氧化乙烷制乙烯反应中的催化机理和反应机制,分析活性物种的生成和转化路径,总结反应动力学行为的规律。
催化剂在CO2催化加氢中应用的研究进展
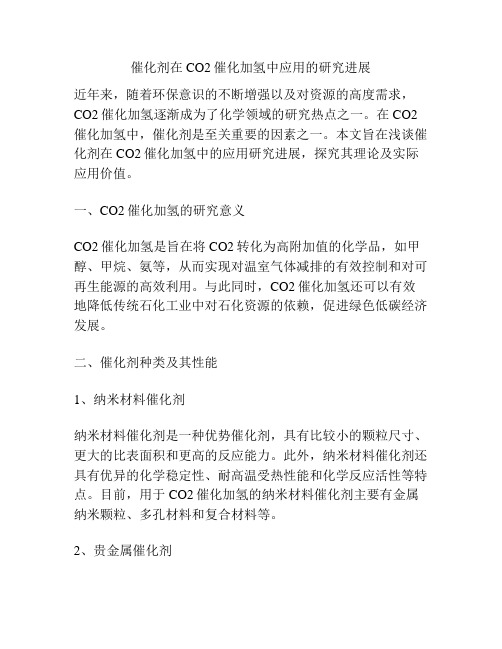
催化剂在CO2催化加氢中应用的研究进展近年来,随着环保意识的不断增强以及对资源的高度需求,CO2催化加氢逐渐成为了化学领域的研究热点之一。
在CO2催化加氢中,催化剂是至关重要的因素之一。
本文旨在浅谈催化剂在CO2催化加氢中的应用研究进展,探究其理论及实际应用价值。
一、CO2催化加氢的研究意义CO2催化加氢是旨在将CO2转化为高附加值的化学品,如甲醇、甲烷、氨等,从而实现对温室气体减排的有效控制和对可再生能源的高效利用。
与此同时,CO2催化加氢还可以有效地降低传统石化工业中对石化资源的依赖,促进绿色低碳经济发展。
二、催化剂种类及其性能1、纳米材料催化剂纳米材料催化剂是一种优势催化剂,具有比较小的颗粒尺寸、更大的比表面积和更高的反应能力。
此外,纳米材料催化剂还具有优异的化学稳定性、耐高温受热性能和化学反应活性等特点。
目前,用于CO2催化加氢的纳米材料催化剂主要有金属纳米颗粒、多孔材料和复合材料等。
2、贵金属催化剂贵金属催化剂是目前被广泛研究和应用的催化剂之一,主要由钯、铜、银等元素组成。
贵金属催化剂通过调整活性中心和表面反应活性位点,可以有效地提高CO2催化加氢的反应效率。
同时,贵金属催化剂还具有优异的化学稳定性和耐高温性能。
3、非贵金属催化剂与贵金属催化剂相比,非贵金属催化剂具有无贵金属成分、更高的原子经济性和成本效益等优点。
预计在未来的CO2催化加氢研究中,非贵金属催化剂将成为重要的研究方向。
三、催化剂的修饰方式催化剂的修饰方式是影响催化剂活性和选择性的重要因素之一,主要包括催化剂载体的调整、催化剂表面修饰和催化剂的添加等。
1、催化剂载体的调整催化剂载体的调整是一种常用的催化剂修饰方法。
通过改变催化剂的载体类型和形貌等,并以氧化铝、活性炭、MgO等材料作为载体,可以有效地提高催化剂的比表面积、提高催化剂的稳定性和化学反应活性等性能。
2、催化剂表面修饰催化剂表面修饰是一种常规的催化剂修饰方式。
通过在催化剂表面引入氧化物、酸/碱性中心、金属修饰等活性位点,可以提高催化剂反应活性和降低催化剂的毒化作用,从而实现CO2催化加氢反应的高效进行。
分子筛固载钌催化剂制备及二氧化碳加氢反应研究报告
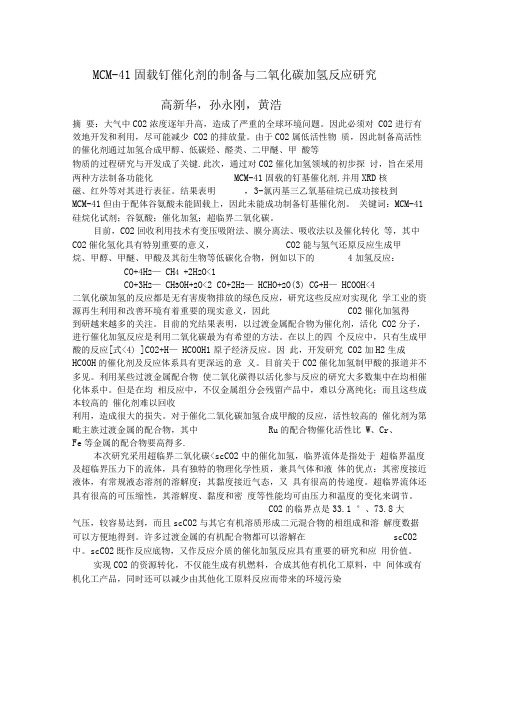
MCM-41固载钉催化剂的制备与二氧化碳加氢反应研究高新华,孙永刚,黄浩摘要:大气中CO2浓度逐年升高,造成了严重的全球环境问题。
因此必须对C02进行有效地开发和利用,尽可能减少CO2的排放量。
由于CO2属低活性物质,因此制备高活性的催化剂通过加氢合成甲醇、低碳烃、醛类、二甲醚、甲酸等物质的过程研究与开发成了关键.此次,通过对CO2催化加氢领域的初步探讨,旨在采用两种方法制备功能化MCM-41固载的钉基催化剂,并用XRD核磁、红外等对其进行表征。
结果表明,3-氯丙基三乙氧基硅烷已成功接枝到MCM-41但由于配体谷氨酸未能固载上,因此未能成功制备钉基催化剂。
关键词:MCM-41硅烷化试剂;谷氨酸;催化加氢;超临界二氧化碳。
目前,CO2回收利用技术有变压吸附法、膜分离法、吸收法以及催化转化等,其中CO2催化氢化具有特别重要的意义,CO2能与氢气还原反应生成甲烷、甲醇、甲醚、甲酸及其衍生物等低碳化合物,例如以下的4加氢反应:CO+4H2—CH4 +2H2O<1CO+3H2—CH3OH+2O<2 CO+2H2—HCHO+2O(3) CG+H—HCOOH<4二氧化碳加氢的反应都是无有害废物排放的绿色反应,研究这些反应对实现化学工业的资源再生利用和改善环境有着重要的现实意义,因此CO2催化加氢得到研越来越多的关注。
目前的究结果表明,以过渡金属配合物为催化剂,活化CO2分子,进行催化加氢反应是利用二氧化碳最为有希望的方法。
在以上的四个反应中,只有生成甲酸的反应[式<4) ]CO2+H—HCOOH1原子经济反应。
因此,开发研究CO2加H2生成HCOOH的催化剂及反应体系具有更深远的意义。
目前关于CO2催化加氢制甲酸的报道并不多见。
利用某些过渡金属配合物使二氧化碳得以活化参与反应的研究大多数集中在均相催化体系中。
但是在均相反应中,不仅金属组分会残留产品中,难以分离纯化;而且这些成本较高的催化剂难以回收利用,造成很大的损失。
二氧化碳催化加氢及其研究进展

二氧化碳催化加氢及其研究进展一、本文概述二氧化碳(CO₂)作为一种常见的温室气体,对全球气候变化产生了深远的影响。
然而,除了其对环境的负面影响外,CO₂也是一种丰富的碳源,具有潜在的化学利用价值。
近年来,通过催化加氢技术将CO₂转化为有用的化学品和燃料,已成为化学和能源领域的研究热点。
本文旨在全面概述二氧化碳催化加氢技术的研究现状、发展动态以及面临的挑战,以期为该领域的进一步研究和工业应用提供参考。
我们将首先介绍CO₂催化加氢的基本原理和催化剂类型,包括金属催化剂、非金属催化剂以及双金属催化剂等。
随后,我们将综述不同催化剂在CO₂加氢反应中的性能表现,包括活性、选择性和稳定性等方面。
我们还将探讨反应条件(如温度、压力、溶剂等)对催化加氢过程的影响,以及催化剂的再生和循环利用问题。
在总结现有研究成果的基础上,我们将分析当前CO₂催化加氢技术所面临的挑战,如催化剂活性不足、选择性差、稳定性差以及能耗高等问题。
我们还将展望未来的研究方向,包括新型催化剂的设计与开发、反应机理的深入研究以及反应过程的优化与控制等。
通过本文的阐述,我们期望能够为读者提供一个全面而深入的了解CO₂催化加氢技术的研究进展和前景,为推动该领域的可持续发展贡献力量。
二、二氧化碳催化加氢的基本原理二氧化碳催化加氢是一种将二氧化碳转化为有价值化学品的重要方法。
其基本原理在于利用催化剂将二氧化碳与氢气在适当的温度和压力下进行反应,生成一氧化碳或甲醇等化学品。
催化剂在反应中起到了关键作用。
常见的催化剂包括金属催化剂、金属氧化物催化剂和金属有机框架催化剂等。
这些催化剂能够降低反应的活化能,使反应在较低的温度和压力下进行。
二氧化碳催化加氢的反应过程涉及多个步骤。
在金属催化剂的作用下,氢气首先被吸附在催化剂表面,形成活性氢物种。
然后,二氧化碳分子与活性氢物种发生反应,生成中间产物,如甲酸或甲醇等。
这些中间产物进一步加氢或分解,最终生成目标产物。
新型分子筛催化剂的研究进展
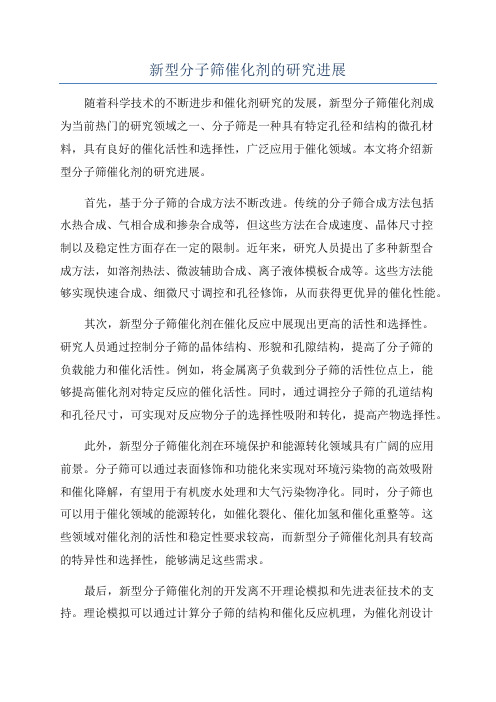
新型分子筛催化剂的研究进展随着科学技术的不断进步和催化剂研究的发展,新型分子筛催化剂成为当前热门的研究领域之一、分子筛是一种具有特定孔径和结构的微孔材料,具有良好的催化活性和选择性,广泛应用于催化领域。
本文将介绍新型分子筛催化剂的研究进展。
首先,基于分子筛的合成方法不断改进。
传统的分子筛合成方法包括水热合成、气相合成和掺杂合成等,但这些方法在合成速度、晶体尺寸控制以及稳定性方面存在一定的限制。
近年来,研究人员提出了多种新型合成方法,如溶剂热法、微波辅助合成、离子液体模板合成等。
这些方法能够实现快速合成、细微尺寸调控和孔径修饰,从而获得更优异的催化性能。
其次,新型分子筛催化剂在催化反应中展现出更高的活性和选择性。
研究人员通过控制分子筛的晶体结构、形貌和孔隙结构,提高了分子筛的负载能力和催化活性。
例如,将金属离子负载到分子筛的活性位点上,能够提高催化剂对特定反应的催化活性。
同时,通过调控分子筛的孔道结构和孔径尺寸,可实现对反应物分子的选择性吸附和转化,提高产物选择性。
此外,新型分子筛催化剂在环境保护和能源转化领域具有广阔的应用前景。
分子筛可以通过表面修饰和功能化来实现对环境污染物的高效吸附和催化降解,有望用于有机废水处理和大气污染物净化。
同时,分子筛也可以用于催化领域的能源转化,如催化裂化、催化加氢和催化重整等。
这些领域对催化剂的活性和稳定性要求较高,而新型分子筛催化剂具有较高的特异性和选择性,能够满足这些需求。
最后,新型分子筛催化剂的开发离不开理论模拟和先进表征技术的支持。
理论模拟可以通过计算分子筛的结构和催化反应机理,为催化剂设计和性能优化提供指导。
先进表征技术如傅里叶变换红外光谱、X射线衍射和傅里叶变换核磁共振等,可以对分子筛催化剂的晶体结构、孔隙结构和催化活性进行详细分析,揭示分子筛催化剂的结构性能关系。
综上所述,新型分子筛催化剂的研究已取得了重要进展。
基于新型合成方法和先进的表征技术,研究人员能够合成具有优异性能的分子筛催化剂,并实现对催化反应的高效控制。
分子筛催化剂的研究与应用

分子筛催化剂的研究与应用分子筛催化剂是当今化学领域中的一个重要的研究方向,它是指具有精细空间网络结构的固体材料,通过其特殊的空间结构和化学功能,可以在化学反应中起到催化作用。
分子筛催化剂广泛应用于石油加工、化学制品、环境保护等领域,是一个非常有前途的研究领域。
一、分子筛催化剂的基本原理分子筛催化剂的催化原理基于它特殊的孔道结构,孔道尺寸与特定反应分子的尺寸相匹配。
当反应分子通过孔道时,会与分子筛中的活性位点发生相互作用,实现催化反应。
因此,作为催化剂,分子筛材料的最重要的性质是大孔度和优秀的比表面积,以及催化位置和反应选择性。
二、分子筛材料的制备分子筛材料的制备需要引入模板分子,它尺寸与孔道相一致,可以帮助形成分子筛结构。
通常使用有机碱或某些有机分子作为模板剂。
分子筛材料的制备方法一般分为两大类:溶胶-凝胶法和晶种法。
其中,溶胶-凝胶法是将硅酸酯、铝酸酯等合成原料与模板分子在水和乙醇中混合,在高温条件下转化为固态材料。
而晶种法则是将已经合成好的分子筛加入合成反应体系中,主要应用于制备特定形式的分子筛。
三、分子筛催化剂的应用与研究分子筛催化剂广泛应用于石油加工、化学制品、环境保护等领域。
在石油化工生产中,分子筛催化剂被广泛用于汽油和柴油加氢、裂化和异构化等过程中;在化学制品生产中,分子筛催化剂被用于合成各种有机分子,如医药、染料和催化剂等;在环境保护方面,分子筛催化剂也有广泛的应用。
例如,NOx催化还原、VOC催化氧化等领域。
在研究方面,分子筛材料不仅被广泛应用于催化反应,而且还成为研究具有新型性质和应用的材料的热点之一。
例如,有人研究了纳米分子筛材料和分子筛/金属有机骨架材料,具有较高的比表面积和催化活性,可以用于制备更高效的催化剂。
另外,还有一些关于分子筛催化剂的新型材料的研究。
研究人员使用不同的合成方法制备了具有不同空间结构、孔径和成分的新型分子筛材料,带来了更多的研究方向。
总之,分子筛催化剂作为一种高效而广泛应用于各种反应的催化剂,在化学领域中发挥着重要的作用。
分子筛载体钌催化剂用于制备山梨醇
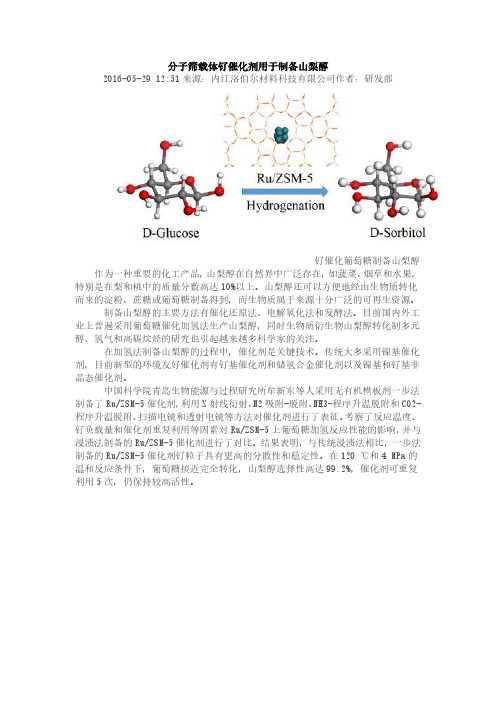
分子筛载体钌催化剂用于制备山梨醇
2016-05-29 12:51来源:内江洛伯尔材料科技有限公司作者:研发部
钌催化葡萄糖制备山梨醇作为一种重要的化工产品,山梨醇在自然界中广泛存在,如蔬菜、烟草和水果,特别是在梨和桃中的质量分数高达10%以上。
山梨醇还可以方便地经由生物质转化而来的淀粉、蔗糖或葡萄糖制备得到,而生物质属于来源十分广泛的可再生资源。
制备山梨醇的主要方法有催化还原法、电解氧化法和发酵法。
目前国内外工业上普遍采用葡萄糖催化加氢法生产山梨醇,同时生物质衍生物山梨醇转化制多元醇、氢气和高碳烷烃的研究也引起越来越多科学家的关注。
在加氢法制备山梨醇的过程中,催化剂是关键技术。
传统大多采用镍基催化剂,目前新型的环境友好催化剂有钌基催化剂和储氢合金催化剂以及镍基和钌基非晶态催化剂。
中国科学院青岛生物能源与过程研究所牟新东等人采用无有机模板剂一步法制备了Ru/ZSM-5催化剂,利用X射线衍射、N2吸附-脱附、NH3-程序升温脱附和CO2-程序升温脱附、扫描电镜和透射电镜等方法对催化剂进行了表征。
考察了反应温度、钌负载量和催化剂重复利用等因素对Ru/ZSM-5上葡萄糖加氢反应性能的影响,并与浸渍法制备的Ru/ZSM-5催化剂进行了对比。
结果表明,与传统浸渍法相比,一步法制备的Ru/ZSM-5催化剂钌粒子具有更高的分散性和稳定性。
在120 ℃和4 MPa的温和反应条件下,葡萄糖接近完全转化,山梨醇选择性高达99.2%,催化剂可重复利用5次,仍保持较高活性。
- 1、下载文档前请自行甄别文档内容的完整性,平台不提供额外的编辑、内容补充、找答案等附加服务。
- 2、"仅部分预览"的文档,不可在线预览部分如存在完整性等问题,可反馈申请退款(可完整预览的文档不适用该条件!)。
- 3、如文档侵犯您的权益,请联系客服反馈,我们会尽快为您处理(人工客服工作时间:9:00-18:30)。
MCM-41固载钌催化剂的制备与二氧化碳加氢反应研究高新华,孙永刚,黄浩摘要:大气中 CO2 浓度逐年升高,造成了严重的全球环境问题。
因此必须对 CO2进行有效地开发和利用,尽可能减少 CO2的排放量。
由于CO2属低活性物质,因此制备高活性的催化剂通过加氢合成甲醇、低碳烃、醛类、二甲醚、甲酸等物质的过程研究与开发成了关键.此次,通过对 CO2催化加氢领域的初步探讨,旨在采用两种方法制备功能化MCM-41固载的钌基催化剂,并用XRD、核磁、红外等对其进行表征。
结果表明,3-氯丙基三乙氧基硅烷已成功接枝到MCM-41,但由于配体谷氨酸未能固载上,因此未能成功制备钌基催化剂。
关键词:MCM-41;硅烷化试剂;谷氨酸;催化加氢;超临界二氧化碳;目前,CO2回收利用技术有变压吸附法、膜分离法、吸收法以及催化转化等,其中 CO2催化氢化具有特别重要的意义,CO2 能与氢气还原反应生成甲烷、甲醇、甲醚、甲酸及其衍生物等低碳化合物,例如以下的4加氢反应:CO2 +4H2→ CH4+2H2O(1)CO2 +3H2→ CH3OH+H2O(2)CO2 +2H2→ HCHO+H2O(3)CO2 + H2→ HCOOH(4)二氧化碳加氢的反应都是无有害废物排放的绿色反应,研究这些反应对实现化学工业的资源再生利用和改善环境有着重要的现实意义,因此 CO2催化加氢得到研越来越多的关注。
目前的究结果表明,以过渡金属配合物为催化剂,活化 CO2分子,进行催化加氢反应是利用二氧化碳最为有希望的方法。
在以上的四个反应中,只有生成甲酸的反应[式(4)]CO2+H2→HCOOH 是原子经济反应。
因此,开发研究 CO2 加 H2 生成 HCOOH的催化剂及反应体系具有更深远的意义。
目前关于CO2 催化加氢制甲酸的报道并不多见。
利用某些过渡金属配合物使二氧化碳得以活化参与反应的研究大多数集中在均相催化体系中。
但是在均相反应中,不仅金属组分会残留产品中,难以分离纯化;而且这些成本较高的催化剂难以回收利用,造成很大的损失。
对于催化二氧化碳加氢合成甲酸的反应,活性较高的催化剂为第Ⅷ主族过渡金属的配合物,其中 Ru 的配合物催化活性比 W、Cr、Fe 等金属的配合物要高得多.本次研究采用超临界二氧化碳(scCO2)中的催化加氢,临界流体是指处于超临界温度及超临界压力下的流体,具有独特的物理化学性质,兼具气体和液体的优点:其密度接近液体,有常规液态溶剂的溶解度;其黏度接近气态,又具有很高的传递度。
超临界流体还具有很高的可压缩性,其溶解度、黏度和密度等性能均可由压力和温度的变化来调节。
CO2 的临界点是 33.1°、73.8 大气压,较容易达到,而且 scCO2与其它有机溶质形成二元混合物的相组成和溶解度数据可以方便地得到。
许多过渡金属的有机配合物都可以溶解在 scCO2中。
scCO2 既作反应底物,又作反应介质的催化加氢反应具有重要的研究和应用价值。
实现 CO2的资源转化,不仅能生成有机燃料,合成其他有机化工原料,中间体或有机化工产品,同时还可以减少由其他化工原料反应而带来的环境污染问题。
虽然目前的 CO2催化加氢研究都还不成熟,但前景是良好的,因此,加强这方面的研究,钻研 CO2的活化规律,开发合适的多相催化体系,将高活性和高选择性的均相催化剂固载化,并结合scCO2 流体的优势,能够克服均相催化的诸多缺点,改善多相催化反应体系中传质和传热,促进反应的产业化转化,使CO2有效地成为有用的化工资源,对解决环境问题、能源问题和化工原料问题都具有重大的意义。
1 实验部分反应路线:+Cl Si(OC2H5)3OOSi ClNH2OOSi NH CO2HCO2Hcatalyst1.1将3-氯丙基三乙氧基硅烷接枝到MCM-41反应方程式:+Cl Si(OC2H5)3O Si Cl反应步骤:称取1.2催化剂的合成方法一:将钌配合物固载于载体上直接将三氯化钌固载于功能化载体上。
具体过程为:用分析天平称取0.0256g水合三氯化钌和谷氨酸0.1470g,在氮气保护下,加入无水乙醇30ml搅拌回流2.5h。
控制回流温度为78摄氏度左右,待反应2.5小时后,加入1.0gMCM-Si-(CH2)3Cl继续搅拌2小时,反应结束后,冷却至室温,固体产物经抽滤,乙醇洗涤,干燥,得目标产物0.1210g。
方法二:将三氯化钌固载于功能化的载体上1.分子筛的功能化将配体谷氨酸接枝于MCM-Si-(CH2)3Cl上。
模拟反应:将谷氨酸先合成谷氨酸二甲酯,再与3-氯丙基三乙氧基硅烷反应。
(1)谷氨酸先合成谷氨酸二甲酯反应方程式:HO 2CCO 2HNH2+CH 3OHCO 2CH 3NH 2CO CH 3实验步骤:将1.0g 谷氨酸加入盛有100ml 甲醇的反应瓶中,再加入SOCl 20.7ml,在室温下搅拌2h,然后将反应体系放入75℃水浴中回流45 min,旋蒸出甲醇,再加入40 mL 无水乙醚,有白色沉淀产生,体系在冷却后过滤出沉淀,干燥后得到谷氨酸二甲酯盐酸盐1.2g,取0.4g 氨酸二甲酯盐酸盐与0.4g 碳酸氢钠在水中反应30min 后,用氯仿萃取三次,得到淡黄色油状物谷氨酸二甲酯0.22g 。
(2)谷氨酸二甲酯与3-氯丙基三乙氧基硅烷的反应方程式:CO 2CH 3NH 2CO CH 3+ClSi(OC 2H 5)Si(OC 2H 5)3CO 2CH 3HNCO 2CH 3实验步骤:将0.1g 谷氨酸二甲酯溶解在氯仿中,加入50ml 圆底烧瓶中,再加入3-氯丙基三乙氧基硅烷1mmol 和适量NaHCO 3,加入少量KI 作为催化剂,最后得0.2610g 产物。
2 结果与讨论2.1傅里叶变换红外光谱表征将3-氯丙基三乙氧基硅烷接枝到MCM-41以及方法一直接合成催化剂通过红外检测,发现前者实验成功,而后者即催化剂并未合成。
如图1:图1:1—MCM-41;2—MCM-Si-(CH 2)3Cl ;3—catalyst上图中,1、2、3分别代表MCM-41、MCM-Si-(CH 2)3Cl 与catalyst ,通过分析可知,3000-3600之间的宽大吸收峰为分子筛表面大量Si-OH,由于其表面羟基密度大,并成氢键,在接枝硅烷偶联剂后,其有所减弱。
2930与2850处分别为-CH2-的对称伸缩与反对称伸缩。
1000处出现的为Si-O特征峰,在接枝硅烷试剂后,形成Si-O-Si键,其吸收峰明显加强。
据此可证明3-氯丙基三乙氧基硅烷已成功接枝到分子筛上。
而经直接法合成的催化剂通过对比发现,与接枝后的分子筛为同一物质。
2.2 XRD表征图2:︱—MCM-41;‖—MCM-Si-(CH2)3ClMCM-41分子筛是一类硅铝分子筛材料,介于微孔材料和大孔材料之间,具有六方有序排列的孔道结构。
从图2可看出,两个样品都在2θ=2.1°左右显示强而尖锐的(100)晶面衍射峰,另外在2θ=3.8°,4.5°和6°左右分别为二级(110)、三级(200)和(210)晶面衍射峰。
这四个峰为典型的MCM-41的标志峰,在接枝硅烷试剂后,其任然保持了这种六方有序孔道结构,但强度逐渐减弱。
这表明处理对分子筛的有序孔道有一定的破坏作用,各种组分可能覆盖在孔道内壁,引起晶格缺陷增多,从而导致衍射峰强度的降低。
2.3核磁表征2.3.1图3:谷氨酸二甲酯图3所示为谷氨酸二甲酯的核磁谱图NH 2CHCH 2COOC H 2OOCH 3H 3C12345其在3.67附件出现的两个峰为1、5号C 上的振动峰,2.25和2.29附近的两组峰出现在2、3号位,4号位的为3.45左右,N 上的H 出现在2.0附近。
其余为杂质峰。
通过图3,我们可以证明已成功合成谷氨酸二甲酯。
2.3.2图4:谷氨酸二甲酯与3-氯丙基三乙氧基硅烷的反应产物经过与3-氯丙基三乙氧基硅烷标准图谱的对比,图4所谓的反应产物仍为3-氯丙基三乙氧基硅烷。
SiOCH 2OCH 22Cl123CH 3CH 3CH 3451号出现在3.38附近,2号1.6附近,3号0.58附近,4号在3.83附近,5号在1.2附近。
即通过分析,我们认为反应产物认为3-氯丙基三乙氧基硅烷。
3 结语与展望通过以上研究,我们认为3-氯丙基三乙氧基硅烷与谷氨酸配体的反应较难进行。
为此,我们目前又从另外一个路线研究分子筛固载钌。
合成路线如下:OO OSiNH2O O OSiNH catalystNH2Si(OC 2H 5)3+HOOOBr Br HOOOBr目前,我们所研究的反应为粘溴酸与3-氨丙基三乙氧基硅烷的反应,初步取得成果。
我们希望能通过所学知识,继续对分子筛固载钌进行研究。
参 考 文 献:。