提高熟料强度的质量控制技术探讨
关于提高熟料强度的几点措施(精)

关于提高熟料强度的几点措施2012年全年熟料强度平均仅在56MPa 左右,特别是12月份仅达到54MPa ,而5到10月的高温季节内,熟料强度普遍呈现规律性偏低,很大程度上影响了水泥质量,不利于公司长远发展。
鉴于以上现状,分厂将把提高熟料强度作为2013年重要攻关项目,现就此提出几项建议。
一、稳定原材料我厂原材料受均化条件的限制历来已久,基于这一实际情况,分厂将主要抓好不同品种、不同品位石灰石的分码堆放,做到优劣石灰石位置明确、铲取方便,严格要求铲车司机按要求配石灰石,稳定石灰石破碎粒度,做好矫正原材料的避潮储备。
破碎工段的签收及配料、破碎工作分厂已安排破碎副厂长实行严格把关。
在原材料粉磨稳定方面,主要是加强日常管理,减少原料秤卡料、定期标定电子秤、要求操作员精心精细操作等,以支持化验室在稳定配料上的可控性及大窑的顺利煅烧,原煤方面,由于我厂用煤品种较多,则要对铲车配煤工作严格管控,严格执行化验室下达的配煤方案,派专人不定时监督,以达到最大程度上的均化。
这一工作已安排签收岗位实行管理,并纳入了考核范畴,车间工艺人员亦将每日巡查。
但从根本上讲,还是要继续保障原材料的进厂质量,否则分厂诸多工作都会陷入被动,至于熟料强度等指标则无从谈起,这还需要公司一如既往的支持。
二、合理控制三率值熟料强度主要来自于硅酸盐矿物质,而硅酸盐矿物中的C 3S 对熟料的早期强度起着决定性影响,故需大胆提高熟料的KH 和SM 。
根据以往统计数据,熟料KH 值一般控制在0.89~0.92之间,SM 值一般在2.35~2.45之间,但根据强度统计结果,这两个值还有提高的空间,熟料KH 可以稳定到SM 值可以提高到A+B要超过76%。
至于熟料IM 值,主要受Fe 2O 3和Al 2O 3影响,两者为煅烧提供一定液相量,有利于C 3S 的生成。
按公司现有条件,建议保持或者稍微偏低对两者含量的控制,但Al 2O 3的控制要及时考虑到煤质的变化。
优质水泥熟料生产过程中质量管控及解决方案

优质水泥熟料生产过程中质量管控及解决方案摘要:在各种工程施工过程中,水泥熟料产品的使用量很大,所以直接决定着建筑物的质量。
本文从对水泥熟料制品生产过程中的质量管理和控制进行了分析和探讨,以及提出了一些解决方案。
这样有助于提高水泥熟料产品的质量。
关键词:水泥熟料;生产过程;质量管控;解决方案引言水泥熟料生产过程比较复杂,从石灰石等原料的提取入手,要经过破碎、原料预均化、配料、水泥熟料制备、储存、包装等工序。
另外,根据实际情况,对样品进行取样、分析和试验,并对样品的化学成分和物理性能进行详细分析。
水泥熟料生产过程的控制是整个生产活动的核心。
只有严格检查各工序的质量和质量控制,才能提高水泥熟料产品的整体质量水平。
1 对水泥熟料生产的管控概述水泥熟料产品质量最重要的一点。
只有不断提高产品质量,才能有效提高国家的整体竞争力。
因此,有必要对水泥熟料产品的生产质量进行管理和控制。
水泥熟料制品是我国重要的建筑材料,可直接测定各种材料。
因此,水泥熟料生产企业在生产过程中必须严格管理和控制水泥熟料产品的质量。
此外,水泥熟料生产企业必须具有相应的资质证书,而且,水泥熟料产品的生产还应按照国家有关标准进行。
另外,必须由质量监督部门进行监督。
改革开放以后,随着我国水泥熟料出口和水泥熟料生产技术出口的不断增加。
人们越来越重视产品质量与国际先进水平的差距。
因此,有关部门对水泥熟料执行了具体的质量标准。
此后,随着我国水泥熟料出口量的增加,为了不断提高我国水泥熟料产品的质量,我国有关部门也瞄准了水泥熟料。
质量标准采取了强制性措施,相关标准与过去相比发生了很大变化。
2 对水泥熟料生产过程中的管控2.1原燃料的管控购买原煤时,应保证原煤质量符合有关标准。
选择实力强、服务好的供应商。
原煤进入现场后,海关人员应检查其质量,确保原煤质量符合生产要求和标准。
在水泥熟料制品的生产过程中,要从根本上出发。
从水泥熟料生产中原料质量的管理和控制入手。
关于提高熟料强度的几点措施
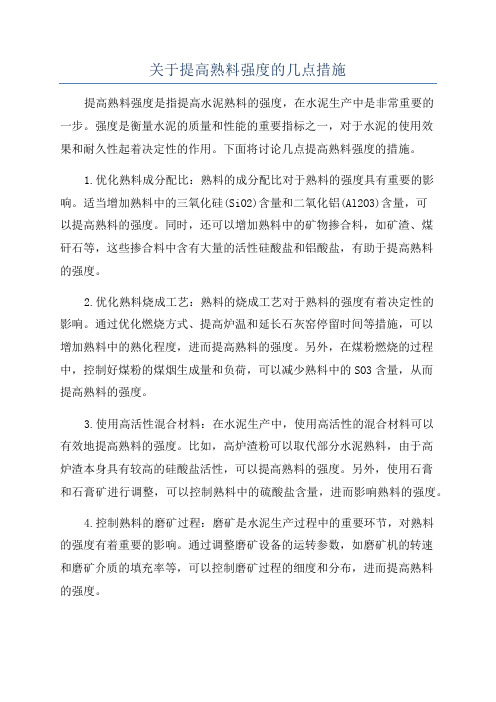
关于提高熟料强度的几点措施提高熟料强度是指提高水泥熟料的强度,在水泥生产中是非常重要的一步。
强度是衡量水泥的质量和性能的重要指标之一,对于水泥的使用效果和耐久性起着决定性的作用。
下面将讨论几点提高熟料强度的措施。
1.优化熟料成分配比:熟料的成分配比对于熟料的强度具有重要的影响。
适当增加熟料中的三氧化硅(SiO2)含量和二氧化铝(Al2O3)含量,可以提高熟料的强度。
同时,还可以增加熟料中的矿物掺合料,如矿渣、煤矸石等,这些掺合料中含有大量的活性硅酸盐和铝酸盐,有助于提高熟料的强度。
2.优化熟料烧成工艺:熟料的烧成工艺对于熟料的强度有着决定性的影响。
通过优化燃烧方式、提高炉温和延长石灰窑停留时间等措施,可以增加熟料中的熟化程度,进而提高熟料的强度。
另外,在煤粉燃烧的过程中,控制好煤粉的煤烟生成量和负荷,可以减少熟料中的SO3含量,从而提高熟料的强度。
3.使用高活性混合材料:在水泥生产中,使用高活性的混合材料可以有效地提高熟料的强度。
比如,高炉渣粉可以取代部分水泥熟料,由于高炉渣本身具有较高的硅酸盐活性,可以提高熟料的强度。
另外,使用石膏和石膏矿进行调整,可以控制熟料中的硫酸盐含量,进而影响熟料的强度。
4.控制熟料的磨矿过程:磨矿是水泥生产过程中的重要环节,对熟料的强度有着重要的影响。
通过调整磨矿设备的运转参数,如磨矿机的转速和磨矿介质的填充率等,可以控制磨矿过程的细度和分布,进而提高熟料的强度。
5.进行合理的熟料混合:在水泥生产中,可以将不同性能的熟料进行合理混合,以提高熟料的强度。
比如,将高硅熟料和高铝熟料进行混合,可以使得熟料中的活性成分更加均匀分布,从而提高熟料的强度。
6.粉磨工艺:通过优化粉磨工艺,可以得到更细腻、更均匀的水泥,从而提高熟料的强度。
术当中常用的有两种方法,一种是较为传统的球磨磨工艺,可以使得水泥粒度更加细腻,另一种是较为先进的辊压台磨工艺,通过辊压和破碎的方式使得水泥颗粒的形状更加完美,从而提高水泥的活性。
控制石灰石有害成分提高熟料强度

前言某公司两条5000t/d新型干法水泥熟料生产线于2010年10月建成投产。
自备的扁担山石灰岩矿山石灰岩矿富含煌斑岩、麻石等低品位岩石,成分波动较大。
生产采用高、低硅砂岩、铁粉等组份配料。
砂岩、铁粉等原材料均需外供,使用的烟煤低位热值在5400×4.18kJ/kg左右。
2015年10月,公司熟料强度持续偏低,28d抗压强度均值在54MPa,个别样品甚至只有48MPa,与公司熟料强度控制目标56MPa相比,强度下降很大。
强度下降,意味着竞争力下降,水泥中熟料配比上升,成本增加。
1 原因分析从原燃材料成分,生产配料,煅烧过程数据来看,均未发生明显变化。
检查化验室压块设备,磨具,养护等设备及环节,没有发现异常情况。
而公司砂岩均为外购,矿点较多,成分波动,碱含量偏高。
2015年12月,公司生产部门把提高熟料强度重点放在加强进厂砂岩的品质控制上,加强辅料堆场均化。
生料中控制w(K₂O+Na₂O)<1.0%,w(Cl)<0.015%~0.020%,熟料强度并没有得到明显改善。
公司两条熟料生产线,当生料磨停机检修或避峰时,烟囱废气中二氧化硫含量明显上升,甚至有超标的情况出现。
硫的化学分析检测耗时长,检验量大,对生产的控制指标不便捷,效果差。
一般水泥企业日常很少对原材料中SO₃的含量进行监测。
为了确保二氧化硫排放达标,2016年3月,公司品质部对原燃材料的硫含量进行全面检验和统计分析。
硅酸盐水泥熟料生产的原料中,一般硫的来源有二,一是黏土或页岩中常含有少量硫,或者硫铁矿、硫酸盐或其他有机硫化合物。
硫的第二个来源是燃料。
通过对公司矿山开采石灰石岩普查得知,石灰石原料中硫含量整体较高。
当生料进入回转窑后,在通常的氧化气氛中,含硫化合物最终都被氧化成为三氧化硫。
由于水泥生料为碱性,当其进入回转窑时就会吸收煤燃烧所产生的气态硫化物,造成生料中含硫化合物逐渐增多,当生料进入高温区时,所有存在的硫酸钙都会部分分解,因而生料中的含硫量是先增至最大值,然后再降低。
提高熟料强度降低熟料煤耗技术革新材料

提高熟料强度降低煤耗技术革新孙玉柱聂保建王麟徐州中联1#窑熟料强度自2011年开始普遍偏低,三天强度平均在29.4mpa 左右,水泥生产台时较低,电耗增加,混合材掺入量降低;直接降低了公司的经济效益;由于周边厂家强度普遍较高,平均在30.5mpa左右,本公司的熟料强度持续偏低,市场销售反应较差,一度对销售量产生影响;系统温度持续偏低,被迫采取增加用煤量来提高系统前温来提高强度,直接影响是增加了系统煤耗,间接影响是增加系统结皮和积料的产生,给预热器安全运行带来威胁。
基于以上理由,迫切需要以提高熟料强度,降低熟料煤耗为目标进行技术革新。
1.目标值的确定为了确定调整的目标值,有效的解决熟料强度低和煤耗高的难题,我们对11年9月到12年1月的强度和煤耗进行了统计:表1:月份3天抗压强度(mpa)28天抗压强度(mpa)标准煤耗(kg/t-cl)2011年9月29.2 57.7 107.252011年10月29.5 57.8 106.042011年11月29.4 57.9 106.642011年12月29.6 57.9 105.732012年1月29.3 58.0 106.25平均值29.4 57.86 106.38从上面表中可以看出,本公司的熟料强度较周边厂家的熟料强度30.5mpa普遍低近1mpa,28天抗压强度平均在57.86mpa,低于公司控制指标58mpa。
熟料的标准煤耗较相同生产线的平均水平105 kg/t-cl普遍高出有1.4 kg/t-cl 为了尽快解决熟料强度偏低的问题,我们对09、10年期间熟料强度数据及运行参数进行了详细的分析。
参照周边厂家熟料强度数据和全国相同生产线数据进行对比,同时根据目前的生产条件及公司制定的指标,确定了熟料强度和煤耗目标:即熟料3天抗压强度在30.5mpa以上,熟料标准煤耗在105 kg/t-cl以下。
2.原因分析针对回转窑生产实际情况,找出对熟料强度起主要影响作用的因素为:2.1.系统前期产能一直偏高,系统设计产量为10000t/d,而在实际运行中,系统产量达到10700t/d。
熟料凝结时间的质量控制方法的课题研究总结报告

熟料凝结时间的质量控制方法的课题研究总结报告序熟料凝结时间的质量控制方法的课题研究一、引言熟料是水泥的主要原料之一,在水泥生产过程中,熟料的凝结时间对最终产品的质量具有重要影响。
研究和控制熟料凝结时间的质量控制方法至关重要。
本文将从深度和广度两个方面对熟料凝结时间的质量控制方法进行探讨,希望能为相关领域的研究提供一定的借鉴。
二、研究背景熟料的凝结时间是指在水泥熟料制备过程中,熟料与水进行反应形成水泥的时间。
凝结时间的长短直接影响到水泥的硬化和强度特性,因此在生产过程中需要进行有效的控制。
三、质量控制方法的分类目前,针对熟料凝结时间的质量控制方法主要包括物理性控制方法和化学性控制方法两大类。
1. 物理性控制方法物理性控制方法主要通过调整熟料的粒度和晶型结构来控制凝结时间。
在实际生产中,通过合理选择原料和适当的工艺参数,可以有效地控制熟料的物理性质,从而影响其凝结时间。
2. 化学性控制方法化学性控制方法主要通过添加助磨剂、控制矿物相组成和晶体结构等手段来控制熟料的凝结时间。
通过精确地控制添加剂的种类和用量,可以在一定程度上影响熟料的凝结时间,从而获得更好的水泥产品。
四、研究现状目前,国内外对熟料凝结时间的质量控制方法进行了大量的研究和实践。
通过实验室研究和工业生产验证,不同的控制方法在一定程度上均取得了一定的成果。
但是,仍然存在一些问题亟待解决。
熟料凝结时间的影响因素复杂多样,不同地区和不同原料的情况也存在差异,因此需要进一步深入研究。
五、个人观点和理解在我看来,熟料凝结时间的质量控制方法是一个复杂而又具有挑战性的课题。
在研究和实践中,我们需要充分理解熟料凝结时间的形成机制,结合物理性和化学性的控制方法,实现对凝结时间的精准控制。
我们也需要不断深入研究,探索新的质量控制方法,以适应水泥生产的不断发展和变化。
六、总结与展望熟料凝结时间的质量控制方法是一个复杂而又重要的课题。
通过对物理性和化学性两大类控制方法的研究和实践,可以有效地控制熟料的凝结时间,在一定程度上提高水泥产品的质量。
提高水泥熟料强度的主要措施
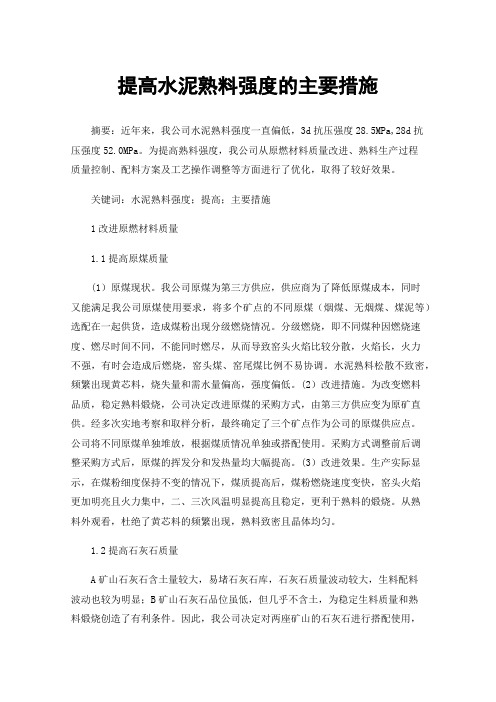
提高水泥熟料强度的主要措施摘要:近年来,我公司水泥熟料强度一直偏低,3d抗压强度28.5MPa,28d抗压强度52.0MPa。
为提高熟料强度,我公司从原燃材料质量改进、熟料生产过程质量控制、配料方案及工艺操作调整等方面进行了优化,取得了较好效果。
关键词:水泥熟料强度;提高;主要措施1改进原燃材料质量1.1提高原煤质量(1)原煤现状。
我公司原煤为第三方供应,供应商为了降低原煤成本,同时又能满足我公司原煤使用要求,将多个矿点的不同原煤(烟煤、无烟煤、煤泥等)选配在一起供货,造成煤粉出现分级燃烧情况。
分级燃烧,即不同煤种因燃烧速度、燃尽时间不同,不能同时燃尽,从而导致窑头火焰比较分散,火焰长,火力不强,有时会造成后燃烧,窑头煤、窑尾煤比例不易协调。
水泥熟料松散不致密,频繁出现黄芯料,烧失量和需水量偏高,强度偏低。
(2)改进措施。
为改变燃料品质,稳定熟料煅烧,公司决定改进原煤的采购方式,由第三方供应变为原矿直供。
经多次实地考察和取样分析,最终确定了三个矿点作为公司的原煤供应点。
公司将不同原煤单独堆放,根据煤质情况单独或搭配使用。
采购方式调整前后调整采购方式后,原煤的挥发分和发热量均大幅提高。
(3)改进效果。
生产实际显示,在煤粉细度保持不变的情况下,煤质提高后,煤粉燃烧速度变快,窑头火焰更加明亮且火力集中,二、三次风温明显提高且稳定,更利于熟料的煅烧。
从熟料外观看,杜绝了黄芯料的频繁出现,熟料致密且晶体均匀。
1.2提高石灰石质量A矿山石灰石含土量较大,易堵石灰石库,石灰石质量波动较大,生料配料波动也较为明显;B矿山石灰石品位虽低,但几乎不含土,为稳定生料质量和熟料煅烧创造了有利条件。
因此,我公司决定对两座矿山的石灰石进行搭配使用,确保石灰石满足CaO≥48%、MgO<2.5%含量的配料要求。
两座矿山的石灰石搭配使用情况见表2。
将两座矿山的石灰石在入仓胶带上混合后,入石灰石预均化场均化。
通过合理搭配石灰石,出磨生料合格率大幅提高。
提高熟料强度的研究

提高熟料强度的研究一、引言熟料强度是水泥生产中的重要指标,直接影响到混凝土的强度和耐久性。
然而,由于原材料质量、生产工艺和环境条件等因素的影响,熟料强度往往存在波动,影响了水泥产品的质量。
因此,提高熟料强度是水泥生产中的重要任务。
本报告旨在探讨提高熟料强度的方法,以期为实际生产提供理论支持。
二、熟料强度的影响因素1.原材料质量:原材料中的杂质、有害物质含量以及烧失量等都会对熟料强度产生影响。
2.生产工艺:生产工艺参数如烧成温度、烧成时间、冷却方式等都会对熟料强度产生影响。
3.环境条件:环境温度、湿度等也会对熟料强度产生影响。
三、提高熟料强度的方法1.优化原材料选择:选择质量稳定的原材料,控制杂质和有害物质含量,降低烧失量。
2.调整生产工艺参数:根据原材料质量和环境条件,合理调整烧成温度、烧成时间和冷却方式,以达到最佳的熟料强度。
3.采用先进技术:采用新型干法水泥生产技术,提高烧成温度和烧成效率,降低能耗和排放。
4.加强质量控制:建立完善的质量检测体系,对每一批次的熟料进行严格的质量检测,确保产品合格率。
四、案例分析某水泥生产企业采用上述方法进行熟料生产,取得了显著的成果。
通过优化原材料选择和调整生产工艺参数,该企业的熟料强度得到了显著提高,同时能耗和排放也得到了有效控制。
采用先进技术和加强质量控制,该企业的产品质量得到了保证,市场竞争力得到了提升。
五、结论通过本文的研究,我们得出以下结论:提高熟料强度需要从原材料选择、生产工艺参数调整、先进技术的应用和质量控制等方面入手。
在实际生产中,应根据具体情况选择合适的方法,以达到提高熟料强度、降低能耗和排放、提高产品质量和市场竞争力等目的。
- 1、下载文档前请自行甄别文档内容的完整性,平台不提供额外的编辑、内容补充、找答案等附加服务。
- 2、"仅部分预览"的文档,不可在线预览部分如存在完整性等问题,可反馈申请退款(可完整预览的文档不适用该条件!)。
- 3、如文档侵犯您的权益,请联系客服反馈,我们会尽快为您处理(人工客服工作时间:9:00-18:30)。
于设备频繁启动而造成的故障,延长 了设备使用寿命 。
参
考
文
献
[ 1 ] 费维 民. 离心式空气压缩机排 气量减 少的故 障分析 与处理 [ I ] . 台
金 动 力 ,2 0 0 2 ,9 2 ( 4 ) :1 4 — 1 7 .
[ 2 ]莫才颂,林荣雄. 离心式压缩机 组振动原 因分析及处理[ 1 ] .轴承 ,
的影 响最大 的参数 为 I M,该参 数影响熟料 2 8 d抗压强度 比较
明显 。在 调 整 过 程 中 ,要 确 保 生料 细度 稳 定 控 制 在 1 2±0 . 2范
游离钙
∞
升重
(
围内。从 2 0 1 3 年 5月开始进行调整 ,经过调整后 ,2 0 1 3 年4 #
L S F S M 咖P a ) R
g / D
窑平均强度 为 5 8 . 1 M P a ,较 2 0 1 2年 9 一l 2月的 5 5 . 9MP a 提 高
9 5 8 2 . 6 2 9 . 4 5 6 . 5
≤1 .2
1 . 1 6
0 6 8
1 2 7 4
了2 . 2 MP a ;2 0 1 3年调整 后 ( 即6 —1 2月) ,4 #窑平 均强度 为
整为 L S F: 9 6±1 . 5 、S M: 2 . 5 ±0 . 1 、I M: 1 . 6 5± 0 . 1 。本 次 调 整
铝氧率 I M与熟料 2 8 d 抗 压强度 的关系图如图 6所示。
表 5 熟料铝氧率 l M与熟料 2 8d抗压强度的关系
I M
统 计 范 围 平均
2 0 1 3 ( 4 ) :3 8 — 4 0 .
[ 责任编辑 :蒙 薇]
5 2
q i y e k e j i y u f a z h a n
1 2 5】
9 5 8
2 4 9
2 9 . 4
5 8 . 6
1 . 6 ~ 1 . 7
l 6 3
0 . 7 6
l 2 5 2
9 5 . 6
2 . 4 9
2 9
5 9 .1
1 . 7 ~ l 8
1 . 7 3
O . 6l
企业科技 与发展
2 0 1 4年第 1 3 期( 总第 3 7 7 期)
5 熟料铝氧率 I N I 与熟料 2 8 d 抗压强度的关 系
熟料铝氧率 I M反映了水泥熟料 中铝 酸三钙与铁铝酸 四钙 的相对含量 。铝氧率过高时 ,则铝酸三钙含量较高 ,煅烧 时液 相黏度较大 ,影响游离氧化钙的吸收,不利于煅烧 ;铝氧率过 低 时,生料烧结范 围变窄 ,不利于煅烧 ,熟料煅烧质量差 ,熟 料 强度 就会受到影响 。我们根据本 生产线 的实际情况 ,统计 了 近3 年 以来熟料铝氧率 I M与熟料强度 的关系 ( 见表 5 ) ,熟料
从表 5 、图 6可知 ,熟料 I M对熟料 2 8 d抗压强度 的影 响 较大 ,随着熟料 I M 的提高 ,熟料 2 8 d 抗 压强度呈现较明显的
上 升趋 势 。
6 调整思路
根据近几年数据分析 ,确定 了配料的调整方 向,由原来熟 料控制 指标 L S F: 9 6±1 . 5 、S M: 2 . 5± 0 . 1 、I M: 1 . 5±O . 1 ,调
[ 1 ] 白宝同. 熟料强度 下降分析一例 [ J ] . 水泥. 石灰 ,1 9 9 4 ( 5 ) .
图 6 熟料 铝 氧 率 l M与熟料 2 8d抗 压 强 度 的 关 系 图
( 上接 第 4 9页 )
5 结论
( 1 )改造 后 ,过滤器每年滤芯更换费用仅为 4 . 2万元 ,检 修费用 降低 ,且不需停机更换滤芯 ,解决 了设备停机率高 、叶 轮易磨损 等问题 。 ( 2 ) 自洁式过滤器滤芯更换周期长 ,减少 了设备维护工作 量 ,降低 了工人劳动强度。 ( 3 )减少压缩机更换滤芯时的停止 、启动次数 ,降低 了由
5 8 . 6MP a ,较 2 0 1 2年 9 一l 2月 的 5 5 . 9M P a 提高 了 2 . 7M P a 。
1 . 2 ~1 3
1 2 6
0 7
1 2 4 8
9 6 4
2 . 5 2
3 0 4
5 6
l 3 ~1 4
1 3 6
0 71
l 2 4 9
9 5 9
2 . 5 2
2 9 4
5 6 8
7 结论
本论文从企业现有数据进行分析和总结 ,查找主要影响 因 素 ,根据企业的实际情况对熟料 铝氧率进行调 整 ,经调整后 , 熟料强度有一定提高 。当然 ,影响熟料强度 的因素很多 ,调整 配料时需要 寻找煤 、料 、煅烧的最佳点 ,使煅烧 的熟料质量达
1 2 6l
9 5 . 2
2 . 4 g
2 9 6
6 0
> 1 . 8
1 8 7
0 7 6
1 2 5 3
9 5 2
2 . 5
2 9 .1
6 0 . 6
特点 ,设计合理 的配料方案 ,生产出理想 的熟料 。
参
考
文
献
[ 责任编辑 :蒙 薇]
到 最佳 状 态 。针 对 不 同的 生 产 线 、不 同 的 窑 ,需 要 分 析 各 自的
1 . 4 ~ 1 . 5
1 4 5
O . 7 5
1 2 5 3
9 5 9
2 . 5l
2 9 5
57 6
1 . 5 ~ 1 . 6
1 5 4
O 7l