铝合金薄板缘条类钣金零件冲压工艺分析
冲压件钣金工艺及成本分析
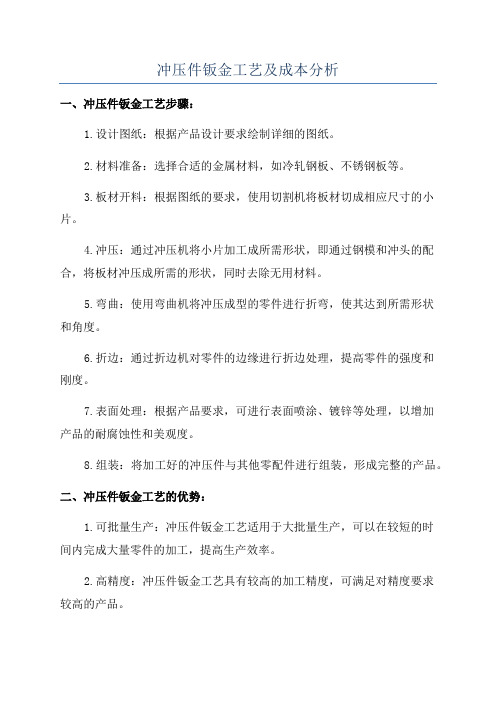
冲压件钣金工艺及成本分析一、冲压件钣金工艺步骤:1.设计图纸:根据产品设计要求绘制详细的图纸。
2.材料准备:选择合适的金属材料,如冷轧钢板、不锈钢板等。
3.板材开料:根据图纸的要求,使用切割机将板材切成相应尺寸的小片。
4.冲压:通过冲压机将小片加工成所需形状,即通过钢模和冲头的配合,将板材冲压成所需的形状,同时去除无用材料。
5.弯曲:使用弯曲机将冲压成型的零件进行折弯,使其达到所需形状和角度。
6.折边:通过折边机对零件的边缘进行折边处理,提高零件的强度和刚度。
7.表面处理:根据产品要求,可进行表面喷涂、镀锌等处理,以增加产品的耐腐蚀性和美观度。
8.组装:将加工好的冲压件与其他零配件进行组装,形成完整的产品。
二、冲压件钣金工艺的优势:1.可批量生产:冲压件钣金工艺适用于大批量生产,可以在较短的时间内完成大量零件的加工,提高生产效率。
2.高精度:冲压件钣金工艺具有较高的加工精度,可满足对精度要求较高的产品。
3.高强度:通过冲压、折边等工艺步骤,可以提高材料的强度和刚度,使产品更加坚固耐用。
4.多种材料可选:冲压件钣金工艺可适用于多种金属材料,如冷轧钢板、不锈钢板、铝板等,具有较大的材料选择余地。
三、冲压件钣金工艺的成本分析:1.材料成本:材料成本是冲压件钣金工艺中较大的成本部分,根据所选材料的种类和规格及材料的采购价格确定。
2.设备成本:冲压件钣金工艺需要使用专用设备,如冲压机、切割机、弯曲机等。
设备的购置、维护和修理等成本需要考虑在内。
3.人工成本:冲压件钣金工艺需要熟练的操作工人进行操作和控制。
人工成本包括工人的工资和福利待遇等。
4.能源成本:冲压件钣金工艺需要消耗电能和压缩空气等能源,因此能源成本是要考虑的因素之一5.后续加工成本:可选的后续加工工序,如表面处理、组装等,也需要考虑在内。
综上所述,冲压件钣金工艺是一项常用的金属加工技术,具有高效、高精度和高强度的优势。
在成本分析中,需要考虑材料成本、设备成本、人工成本、能源成本和后续加工成本等因素。
冲压钣金件加工工艺

冲压钣金件加工工艺冲压钣金件是一种常见的工业零部件,适用于各种机械设备中,具有重要的作用。
钣金件加工工艺是制作这种零部件的关键环节,下面就钣金件加工工艺进行详细介绍。
一、冲压钣金件的特点冲压钣金件是采用冲压工艺制作而成的,具有轻质、高强度、精度高、成本低等特点。
在现代工业生产中得到广泛应用,在制造机械设备、电子产品、汽车零件等方面具有重要作用。
二、钣金件加工工艺1、材料准备:冲压钣金件加工需要准备的材料有:一般钢板、不锈钢、铜、铝等。
这些材料的规格和厚度根据工件要求而定。
2、设计图纸:制作每个冲压零件之前,需要先设计出零件的图纸。
设计图纸中需要包括工件的形状、尺寸、工艺要求、成品要求等。
3、数控冲床:数控冲床是冲压钣金件加工中主要的设备。
数控冲床是一种通过程序控制,根据需要的形状和尺寸对材料进行精确冲裁的机床。
数控冲床的工作原理是将材料放在电动滑台和定位销上,用冲床模具对材料进行冲压成形。
4、模具制作:冲床模具是影响冲压钣金件加工效果的重要因素。
一般情况下,制造一个冲孔模具需要经过CAD设计、加工、试模、校正等多个步骤。
5、表面处理:冲压钣金件加工完成后,需要对零件表面进行处理。
一般采用的表面处理方法有热镀锌、镀铬、抛光、油漆等。
三、钣金件加工工艺的优势冲压钣金件加工工艺具有以下优势:1、高效性:冲压钣金件加工速度快,每分钟可以加工数十个工件,生产效率很高。
2、成本低:冲压钣金件加工比其他钣金件加工方式成本更低,每件零件的制作费用更低。
3、精度高:采用数控冲床加工,精度高达0.1mm左右,能够保证工件的精度。
4、稳定性高:通过严格的工艺流程和检测方法确保工件的质量稳定。
总之,钣金件加工工艺在现代工业生产中具有重要的应用价值,只有掌握了这些技术,才能够更好地生产出优质的冲压钣金件,从而为整个工业生产带来更大的效益。
钣金工艺及模具冲压介绍解析

东莞龙光电业有限公司
钣金产品以及加工工艺介绍
钣金部主要生产机柜、机箱、插框、拉手条、门板类等产品。
我公司主要钣金加工设备有: 1.下料设备:普通剪床、数控剪床、激光切割机、数控冲床 2.成形设备:普通冲床、网孔机、折床和数控折床。 3.焊接设备:氩弧焊机、二氧化碳保护焊机、点焊机、机器人焊机。 4.表面处理设备:拉丝机、喷沙机、抛光机、电镀槽、氧化槽烤漆 线 5.调形设备:校平机
焊接:是对焊件进行 局部或整体加热或使 焊件产生塑性变形, 或加热与塑性变形同 时进行,实现永久连接 的工艺方法.可分为:手 工电弧焊、气体保护 电弧焊、激光焊、气 焊、段焊和接触焊.我 司主工采用气体保护 焊和接触焊.
LASER中TRUMPF L3030的加工精度为±0.1mm,加工范围3000mm*1500mm,加工厚 度为铁板20mm、铝板8mm,不锈钢板12mm,一般不用于加工铝板或铜板,以免损 坏激光头的镜面。通常加工SPCC板用O2作切割气体,加工电解板及不锈钢板用 N2作切割气体。
数控折弯机:折弯上模按其结构形式可分为:直刀、弯刀、尖刀,其中直刀强度最好,
钣金加工一般工艺流程:图面展开、数控编程、下料(剪、冲、 割)、 冲网孔、 校平、拉丝 、 冲凸包、 冲撕裂 、压铆、 折弯 、 焊接、 表处、组装 。
钣金工艺中常遇到的一些问题
❖ 钣金加工时会经常遇到一些问题,需要你去优化它的工艺,使其成为 一个良品或达到一个特定的目的。下面就简单来介绍一下我们在钣金 加工时同,经常要注意到的一些工艺问题。
❖ 折弯成型时一般是利用长边包短边的加工方式,然后在相应角落处开 工艺孔,工艺孔的大小一般由板厚而定,板厚增大时,工艺孔的大小 也要相应增大,否则折弯时会产生棱角。
铝合金型材冲压加工工艺及模具设计

铝合金型材冲压加工工艺及模具设计摘要:铝合金的类型繁多,其中包括非热处理型、热处理型以及热处理型。
这些类型的特点是其强度、加工性能、耐腐蚀性都有所差异,因此在选择合适的铝合金时,必须考虑到它们的特点。
文章讨论了铝合金的不同种类、特性、储存和运输方式,并探讨了其在冲压工艺的应用。
关键词:铝合金型材;冲压加工工艺;模具设计引言:由于铝合金的轻量化、出色的散热特性、容易加工、耐腐蚀和经济实惠,已经成为许多领域的首选材料。
许多铝合金材料都需要经历一系列的精密加工才能达到所需的质量标准,其中包括热处理和二次加工。
而在大规模生产中,这些二次加工常常会使用冲压技术来完成。
一、铝合金型材冲压加工工艺特点随着产品的需求变化,铝合金型材的断面形状也会有所差异,但大多数都是薄壁结构。
散热器是一种高嵴片状(或枝叶状、轮辐状)零件。
当进行大规模生产时,铝合金型材的制造过程包括:首先,将型材进行一次精确的断裂,然后进行剖沟,最后进行冲压。
与普通金属板材不同,铝合金型材的冲压过程需要特别注意以下几点:(一)被加工件采取特别的保护措施由于铝合金的软度比其他金属更高,为了避免型材变形,在冲压加工过程中,必须采取精确、稳定且可靠的定位措施,例如安装定位套。
此外,还需要采用弹性压料装置,以确保被加工的产品能够在受到限制的条件下继续运动。
(二)选择合理的工艺参数在冲裁过程中,为了获得更高的精度,刀具的刃口必须更加锋利,而且与传统的封闭式冲裁相比,其间隙也会更加紧凑。
(三)留有足够的变形区在铝合金冲压加工过程中,由于变形区的存在,会对产品质量造成严重的影响,因此必须在相关工艺中留出足够的空间,以减少变形带来的潜在危害。
二、铝合金型材冲压加工工艺分析(一)铝合金料垛的板料分张由于钢板本身具有磁性,为了更好地将其分离,常常会使用磁性分张器将板料的磁化,使得它们之间的磁性极性保持一致,从而实现对板料的有效分离。
鉴于铝合金板材料的非磁性特征,无法通过磁力来进行分割,在制造铝合金板时,采用磁力分割是一项极具挑战的工艺,而且目前仍然是一个棘手的问题。
浅谈铝合金冲压工艺

Ke y wo r d s : a l u mi n u m a l l o y ; s t a mp i n g p r o c e s s ; c a u t i o n
・
冲
模 技 术
・
浅谈铝 合来自金冲 压 工龙
艺
0 7 1 0 0 0 )
赵金 升 , 苑雪雷 , 谷
长城 汽车股份有 限公 司技术 中心, 河北省汽车 工程技 术研 究 中心 ( 河北保 定
【 摘要 】 介绍 了铝合金的种类, 铝合金 冲压工艺的要 求, 以及模具维修 的注意事项。
性 以及表 面处理性 能等也 比较好 。因此 , 铝材 在航 部分 国家通常按 以下 3 种方法进行分类 。
气、 能源动力 、 冶金化工 、 农业排灌 、 机械制造 、 包装 防 铝合金和不可热处理强化铝合金两大类” 。不可热处 腐、 电器家具 、 E t 用文体等各个领域都获得 了十分广 理强 化铝 合 金 ( 如: 纯铝、 A 1 一 M n 、 A 1 一 M g 、 A 1 一 S i 系合
金、 切削铝 合金 、 耐热铝合金 、 低强度铝合金 、 中强度 铝合金 、 高强度铝合金 ( 硬铝 ) 、 超高强度铝合金 ( 超硬
铝) 、 锻造铝合金及特殊铝合金等 。
( 5 ) 压料 圈着色要优于钢件 。
c . 按合金 中所含主要元素成分可分为 : 工业纯铝
倍, 大大降低 了制件 的生产成本低 , 取得 了较好 的经
济效益和社会效益 。 参
铝合金冲压工艺

铝合金冲压工艺一、引言铝合金冲压工艺是一种常用于制造铝合金零件的加工方法。
铝合金因其优异的性能和轻质特性,在汽车、航空航天、电子等领域得到广泛应用。
冲压工艺是一种通过冲压机械力对铝合金板材进行塑性变形,以达到所需形状和尺寸的加工方法。
本文将介绍铝合金冲压工艺的原理、工艺流程以及工艺参数的选择。
二、铝合金冲压工艺原理铝合金冲压工艺的原理是利用冲压机械对铝合金板材施加压力,使其发生塑性变形,从而得到所需形状和尺寸的零件。
冲压工艺可以分为单工位冲压和连续冲压两种形式。
单工位冲压是指在一次冲压过程中,通过一次冲压动作即可得到所需零件。
而连续冲压是指在一次冲压过程中,通过多次冲压动作,逐步完成零件的加工。
铝合金冲压工艺的原理是通过冲压机械对铝合金板材施加压力,使其在模具的作用下发生塑性变形,从而得到所需形状和尺寸的零件。
三、铝合金冲压工艺流程铝合金冲压工艺的流程包括材料准备、模具设计、冲压工艺参数选择、冲压加工、后处理等步骤。
1. 材料准备:选择适合的铝合金板材,根据零件的要求进行切割和预处理。
2. 模具设计:根据零件的形状和尺寸要求,设计相应的模具。
模具设计要考虑到材料的流动性、变形性以及模具的耐用性和易于加工性。
3. 冲压工艺参数选择:根据零件的形状、尺寸和材料的性能,选择合适的冲压速度、冲压力度、冲压次数等参数。
这些参数的选择需要兼顾产品质量和生产效率。
4. 冲压加工:将铝合金板材放入冲压机械中,根据工艺参数进行冲压加工。
冲压过程中需要保证模具的准确定位和压力的均匀施加,以避免零件的变形或损坏。
5. 后处理:对冲压后的零件进行去毛刺、清洗、抛光等处理,以提高零件的表面质量和功能性。
四、铝合金冲压工艺参数选择在铝合金冲压工艺中,冲压参数的选择对零件的质量和生产效率具有重要影响。
下面介绍几个常用的冲压参数:1. 冲压速度:冲压速度是指冲压机械对材料施加的速度。
过快的冲压速度容易引起材料的撕裂和变形,过慢的冲压速度会延长加工周期。
车用铝合金中铝板冲压的设计及生产的关键技术

车用铝合金中铝板冲压的设计及生产的关键技术随着汽车轻量化的发展趋势,车用铝合金材料在汽车制造中的应用愈发广泛。
而在车身及零部件制造中,铝板冲压技术是一项关键的生产工艺。
本文将重点介绍车用铝合金中铝板冲压的设计及生产的关键技术。
设计阶段在车用铝合金中铝板冲压的设计阶段,需要考虑以下几个关键技术点:1. 材料选择:铝合金材料的选择对于冲压工艺至关重要。
一般而言,汽车中常用的铝合金材料有6系和7系两种。
6系铝合金具有良好的可加工性和韧性,适合用于一般冲压件的制造;而7系铝合金则具有较高的强度和硬度,适合用于制造要求更高的零部件,如车轮等。
2. 零部件设计:在设计车用铝合金中的铝板冲压零部件时,需要考虑其形状复杂度、厚度分布、变形特性等因素。
合理的设计可以降低冲压成本,减小材料浪费,提高产品质量。
3. 模具设计:模具是冲压工艺的关键,直接影响零部件的成型质量。
在设计模具时,需要考虑材料的选择、模具结构、冲压力的传递方式等因素。
生产阶段1. 材料处理:铝合金材料在冲压前需要进行预处理,包括氧化膜清除、表面处理、退火等工艺。
氧化膜的清除对于提高冲压质量至关重要。
2. 冲压工艺:车用铝合金中铝板冲压的工艺包括下料、模具装配、模具调试、冲压成型等环节。
在这个过程中,需要注意工艺参数的设定、模具的调整、冲压速度的控制等关键技术。
3. 质量控制:在冲压过程中,需要通过一系列的质量控制手段来保证产品的质量。
包括对材料的质量把控、对工艺参数的监控、对成品的检测等。
关键技术车用铝合金中铝板冲压的关键技术主要包括材料选择、零部件设计、模具设计、材料处理、冲压工艺、质量控制等方面。
这些技术点的合理运用能够提高产品的质量,降低成本,推动汽车轻量化的发展。
材料选择是车用铝合金中铝板冲压的第一步,选择合适的铝合金材料可以保证产品的成型质量和性能。
合理的零部件设计和模具设计也能够降低生产成本,提高生产效率。
材料处理和冲压工艺则是冲压生产过程中的关键环节,通过合理的处理和控制能够保证产品质量和工艺稳定性。
铝合金冲压工艺

铝合金冲压工艺铝合金冲压工艺是一种常见的金属成形加工方法,广泛应用于汽车、航空航天、电子、家电等领域。
本文将介绍铝合金冲压工艺的基本原理、工艺流程和应用领域。
一、基本原理铝合金冲压工艺是通过应用冲压设备,将铝合金板材置于冲压模具中,施加压力使其发生塑性变形,最后得到所需形状的零部件。
冲压过程分为冲孔、剪切、弯曲、拉伸等步骤,需要根据具体要求选择合适的模具和冲压设备。
二、工艺流程1. 材料准备:选择合适的铝合金板材,根据产品要求进行切割和整形。
2. 模具设计:根据产品的形状和尺寸要求,设计相应的冲压模具。
3. 冲压工艺参数确定:包括冲床的选择、冲头的尺寸、冲程、冲压速度、冲压力等。
4. 冲压加工:将铝合金板材放入冲压机中,根据工艺参数进行冲压加工。
5. 检验与调整:对冲压件进行检验,如尺寸、表面质量等,根据需要进行调整和修正。
6. 表面处理:根据产品要求,对冲压件进行表面处理,如喷涂、电镀等。
7. 组装和检验:将冲压件进行组装,进行最终的产品检验。
三、应用领域1. 汽车工业:铝合金冲压件在汽车制造中应用广泛,如车身外壳、车门板、车顶等。
2. 航空航天工业:铝合金冲压件在航空航天领域中用于制造飞机机身、发动机外壳等。
3. 电子工业:铝合金冲压件在电子设备中的应用也越来越广泛,如电脑外壳、手机壳等。
4. 家电工业:铝合金冲压件在家电制造中用于制造洗衣机外壳、冰箱外壳等。
总结:铝合金冲压工艺是一种重要的金属成形加工方法,具有高效、精确、经济的特点。
通过合理的工艺参数和模具设计,可以实现对铝合金板材的高效加工和成形。
铝合金冲压件在各个领域中有着广泛的应用,为相关行业的发展提供了重要的支持。
- 1、下载文档前请自行甄别文档内容的完整性,平台不提供额外的编辑、内容补充、找答案等附加服务。
- 2、"仅部分预览"的文档,不可在线预览部分如存在完整性等问题,可反馈申请退款(可完整预览的文档不适用该条件!)。
- 3、如文档侵犯您的权益,请联系客服反馈,我们会尽快为您处理(人工客服工作时间:9:00-18:30)。
铝合金薄板缘条类钣金零件冲压工艺分析
零件为一典型的旋转体引伸件。
材料为2024T3,厚度为1.0MM。
其中,整个型面有理论外形,最大法兰边直径是φ472MM,引伸直径是φ424.6MM,高度方向尺寸20.6(含料厚),高度公差为-0.2到+0.2。
本论文主要是对该零件冲压工艺进行分析,对于具有众多的引伸零件的航空产品今后的工业化生产,具有一定的借鉴和指导意义
标签:零件;引伸;冲压
1 零件总体工艺方案的确定
1.1 确定零件的基本加工工序
零件轮廓尺寸较大,材料相对较薄,高度方向尺寸精度要求高,材料塑性尚可。
根据该件的产量,结合以上特点,若实现零件的互换,必须通过下展开料、引伸、压模校形,手工校形等工序加工,方可达到要求。
还有,该零件是一种以引伸成形为主的冲压件。
1.2 引伸过程中基本的规律分析
我们知道,引伸工艺出现质量问题的形式主要是起皱和拉裂。
为了更好地解决起这些问题,必须研究掌握引伸过程中材料各部分的应力与应变状态。
1.2.1 凸缘的平面部分
这是引伸的主要变形区,材料在径向拉应力和切向压应力的共同作用下产生了切向压缩和径向伸长变形而逐渐被拉入凹模。
一般地,在材料产生切向压縮与径向伸长的同时,厚度有所增厚,越接近外缘,材料增厚越多。
当引伸变形程度较大,材料又比较薄时,则在材料的凸缘部分,特别是外缘部分,在切向压应力的作用下可能失稳而拱起,形成所谓的起皱。
1.2.2 凸缘的圆角部分
这是位于凹模圆角部分的材料,切向受压应力而压缩,径向受压应力而伸长,厚度方向受到凹模圆角的压力和弯曲作用。
由于这里切向压应力值不大,而径向拉应力最大,而且凹模圆角越小,则弯曲程度越大,弯曲引起的拉应力越大,所以有可能出现破裂。
该部分也是变形区,但它是变形次于凸缘的平面部分的过渡区。
1.2.3 筒壁部分
这是引伸过程中形成的侧壁部分,是已经结束了塑性变形阶段的已变形区。
这个部分受单向拉应力作用,变形是拉伸变形。
1.2.4 底部圆角部分
这是与凸模圆角接触的部分,它从引伸开始一直承受径向拉应力和切向拉应力的作用,并且受到凸模圆角的压力和弯曲作用,因而这部分材料变薄最严重,尤其是与侧壁相切的部位,所以此处最容易出现拉裂,是引伸的“危险断面”。
1.2.5 筒底部分
这部分材料与凸模底面接触,在引伸开始时即被拉入凹模,并在引伸的整个过程保持其平面形状。
它受双向拉应力作用,变形是双向拉伸变形。
但这部分材料只产生不大的塑性变形。
筒壁、底部圆角、筒底这三部分的作用是传递拉应力,把凸模的作用力传递到变形区凸缘部分上,使之产生足以引起引伸变形的径向拉应力,因而又叫传力区。
值得注意的是:在引伸过程中,材料各部分的应力与应变是很不均匀的,即使在凸缘变形区也是这样,越靠近外缘,变形程度越大,材料增厚越多。
因而,当凸缘部分转变为侧壁时,引伸件的壁厚就不均匀。
引伸件下部壁厚略有变薄,越接近圆角变薄越大,壁部与圆角相切处变薄最严重。
上部却有所增厚,越接近口部增厚越多。
而且,加工硬化程度不同,越接近口部,硬度越大。
2 工艺准备过程
由于此零件是一个比较典型的旋转体引伸件,我们可以直观地确定所需工序的性质和顺序。
接下来,就要根据变形程度,通过一定的计算,确定工序数目。
确切地说,是确定引伸次数。
需要明确的一点是,从尺寸上看,此件是一种有理论外形的旋转体零件,但口部与底部尺寸没有差别,从前面的理论分析来看,这几乎就是带凸缘的圆筒引伸件的最终形状。
因此,完全可以用计算引伸直径φ424.6和带凸缘的圆筒形件的方法,来进行此件的相应计算。
2.1 毛料尺寸的计算
首先计算凸缘的相对直径d/d,其中,d—凸缘直径;d—引伸直径。
则d/d=472/424.6=1.1116
根据体积不变原则,查工具书得公式
D=;D=
D=φ502
为校形方便,留余量后展开料尺寸确定为φ520
其中:D—毛料直径;d—引伸后最大法兰边直径
d—引伸直径;H—引伸高度;r—材料中性层半径
2.2 引伸系数的计算
毛料的相对厚度(t/D)%=1.0/520*100=0.2,查表得,极限引伸系数为0.6,实际引伸系数为
m=d/D=424.6/520=0.816,这表明,材料允许的变形程度还没用足,一次引伸就足够了。
毛料的相对厚度(t/D)%=1.0/520*100*%=0.2%查表得t/D小于1.5%
故这次引伸凸缘处须加压边力。
2.3 工艺方案的选择
该零件属于比较典型的引伸零件,在工艺方法上一般不会引起争议,只要尽可能的减少手工量,减少劳动强度就可以,经研究后,该零件的冲压加工可能有的方案为:
①下方块料—下圆料—引伸模引伸—校形—压模校形—切边
②下方块料—下圆环料—引伸模引伸—校形—压模校形—切边
第一种方案是一种稳妥的办法,但材料利用率不高,增大成形后的切割余量。
出现问题容易查清原因,每一道工序操作都很简便,只是生产效率低,增大劳动强度,不适应大批量生产。
第二种方案跟第一种方案相比,材料利用率增大,效率也有所提高,而且节约内孔中的材料,,减少成型后的手工剪切量,达到了减少手工量的目的,方法也比较简洁有效。
故选用第二种工艺方案
2.4 工艺装备及有关工艺参数的确定
方案确定后,最重要的工作就是保证工艺的稳定性。
在这里,模具和定位因素非常关键。
对此件的加工过程来说,需保证的有两个方面:零件形状的准确和两套模具间的协调性。
围绕这两个方面,下列思路就显得十分必要。
首先,对引伸成形影响最大的是毛料的形状,对旋转体引伸件,最佳的毛料形状是圆形,而我们所下的毛料是圆环料,符合引伸件展开料的需求,但由于金属材料各项异性,引伸时材料各个方向拉应力不同,零件本身有理论外形,高度公差较严,单纯靠引伸还是不能够保证高度公差,如果,引伸后用压模校形,成形后尺寸可以达到图纸要求。
现在来计算加工零件所需的工艺总压力F,
2.4.1 压边力的计算
通过查工具书上的计算公式
F=π[D-(d+2r)]p/4=π[520-(424.6+2) ]/4=69439N=7T
其中:D—毛料直径;d—引伸直径
r—阴模圆角半径;p—单位面积压料力(查表的)
2.4.2 引伸力的计算
F=πdtδk=π424.6*1*40*0.6=32014kg=32T
其中:d—引伸直径;t—材料厚度
δ—拉伸件材料的抗拉强;k—修正系数(查表得,本项目取0.6)
根据上面的计算结果,结合选择设备的其他要素(如闭合高度、工作台面尺寸,因零件小可不与考虑),以及车间的设备能力,加工设备选用550KN复动压力机即可。
3.结束语
在工艺加工过程中,应该注意
(1)由于破裂常常发生在凸模圆角与板料相切的区域,当凸模圆角半径较大时,破裂将会上移到已有加工硬化的区域,即发生破裂的区域扩大,因此,凸模圆角不宜过大。
(2)在生产中有时会出现起皱、掉底、拉裂零件桶壁有硌伤处等现象,此类问题曾一度成为影响交付的主要因素。
究其原因,主要是由于模具制造误差造成的,由于选用压模结构较为简单,只需要两套模具的尺寸协调性,在这里不作展开说明。
所以,必须强调模具制造精度这一影响工艺稳定的因素。