汽车制造企业售后零部件配送中心选址模型与仿真研究
基于Flexsim的某汽车装配车间物流建模与仿真的研究的开题报告

基于Flexsim的某汽车装配车间物流建模与仿真的研究的开题报告一、选题背景汽车装配车间是整个汽车制造流程的重要环节之一,其物流系统的合理性和高效性直接影响到汽车制造的质量和生产效率。
目前,许多汽车厂家已经开始使用仿真技术来优化其物流流程,以达到生产的高效和成本的降低。
Flexsim是一种高度可定制的仿真软件,可广泛应用于各种工业领域。
通过基于Flexsim的物流建模与仿真技术,可以对汽车装配车间的物流系统进行模拟,实现对生产过程的优化和改进。
因此,本文旨在通过基于Flexsim的某汽车装配车间物流建模与仿真,研究和分析其工作流程和瓶颈,进而探索优化物流系统的方法,提高汽车制造的生产效率和质量。
二、研究内容和研究目标研究内容:1. 了解并分析某汽车装配车间的物流系统的工作流程,建立其模型并对其进行仿真。
2. 对模拟结果进行分析和比较,识别出物流系统中的瓶颈问题,并探索优化方案。
研究目标:1. 了解某汽车装配车间物流系统的工作流程及其现存问题,为改善物流系统提供基础。
2. 构建物流仿真模型,准确地反映物流系统的运行状况,找出瓶颈并提出优化方案。
3. 通过仿真结果的验证,证明优化方案的可行性和有效性。
三、研究方法和技术路线1. 研究方法(1)文献调研,了解汽车装配车间物流系统的运行流程及其现存问题。
(2)数据采集,搜集某汽车装配车间的实际数据,并对其进行整理和分析。
(3)建立物流仿真模型,使用Flexsim进行建模和仿真,并对仿真结果进行分析。
(4)提出优化方案,分析传统方法,探索新的优化方案,进行方案的可行性分析。
2. 技术路线(1)数据采集和整理:利用Excel等工具将某汽车装配车间的数据进行整理和分析。
(2)Flexsim建模:针对汽车装配车间的物流系统,进而建立Flexsim仿真模型,并进行详尽的设置和参数配置。
(3)仿真和优化方案:运用模型,模拟汽车装配车间的物流流程,分析模拟仿真的结果,制定优化方案并对其进行有效性验证。
配送中心建模与仿真分析
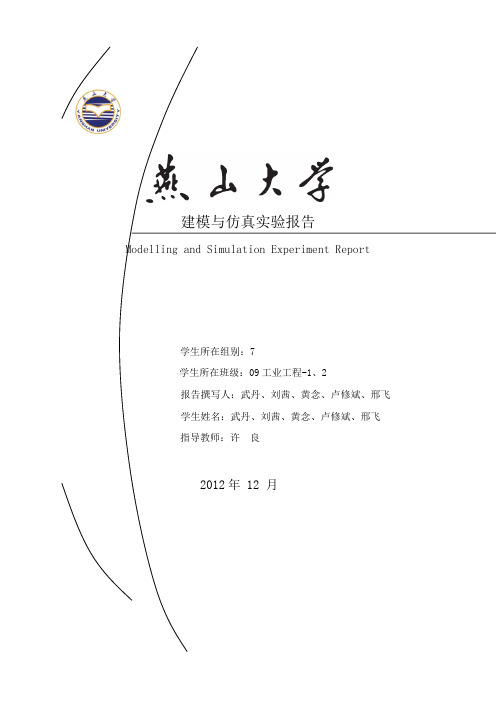
建模与仿真实验报告Modelling and Simulation Experiment Report学生所在组别:7学生所在班级:09工业工程-1、2报告撰写人:武丹、刘茜、黄念、卢修斌、邢飞学生姓名:武丹、刘茜、黄念、卢修斌、邢飞指导教师:许良2012年 12 月实验任务1.完成本组实验内容。
产品测试工艺仿真与分析、配送中心仿真与分析2.按实验指导书及教材要求分析结果。
实验二产品测试工艺实验操作员:武丹、黄念时间:12年12月6日地点:燕大西校区一机房一、实验目的1)了解供应链仿真系统的设计;2)熟悉Flexsim系统元素Flowitem、Processor、Conveyor、Rack、Operator、Dispatcher、Transporter、Queue、Source、Sink3)熟悉产品测试工艺仿真与分析的设计;二、系统描述某工厂车间对三类产品进行检验。
这三种类型的产品按照一定的时间间隔方式到达。
随后,不同类型的产品被分别送往三台不同的检测机进行检测,每台检测机只检测一种特定的产品类型。
其中,类型1的产品到第一台检测机检测,类型2的产品到第二台检测机检测,类型3的产品到第三台检测机检测。
产品检测完毕后,由传送带送往货架区,再由叉车送到相应的货架上存放。
类型1的产品存放在第2个货架上,类型2的产品存放在第3个货架上,类型3的产品存放在第1个货架上。
三、概念模型五、实验步骤第1 步:模型实体设计第2 步:用鼠标左键从库里拖出一个Source放入正投影视图第3 步:把其余的实体拖到正投影视图中第4 步:连接端口第5 步:指定到达速率第6 步:设定临时实体类型和颜色第7 步:设定queue容量第8 步:为queue指定临时实体流选项第9 步:为processor指定操作时间第10 步:向模型中添加一个dispatcher和两个operator第11 步:连接中间和输入/输出端口第12 步:编辑queue临时实体流设置使用operator第13 步:为processor的预置时刻配置operator第14 步:添加transporter第15 步:调整queue的临时实体流参数来使用叉车第16 步:设定用来安排临时实体从queue到rack 的路径的全局表第17 步:调整conveyor后头的queue的“Send To Port”选项第18 步:重新配置conveyor1 和3 的布局第19 步:为叉车添加网络节点来为叉车开发一条路径第20 步:编译第21 步:重置模型第22 步:运行模型第23 步:模型导航六、数据显示与分析1、初始条件下,输出数据如下表产品到达速率:产品到达间隔时间服从均值为20秒、方差为2的正态分布暂存区最大容量:25检测机时间参数:准备时间是10秒,加工时间服从均值为30秒的指数分布传送带参数:传送速度是1 米/秒,传送带上同时最多传送10 个产品Flexsim Summary ReportTime: 593.1079Object Class stats_content stats_staytimeminstats_staytimemaxstats_staytimeavgstate_currentstate_sinceSource1 Source 0.00 0.00 0.00 0.00 5.00 593.11 Queue2 Queue 0.00 2.33 8.54 4.37 6.00 593.11 Queue3 Queue 1.00 0.60 16.11 8.93 10.00 593.11 Processor4 Processor 0.00 20.00 24.63 22.31 1.00 593.11 Processor5 Processor 0.00 20.00 21.58 20.40 1.00 593.11 Processor6 Processor 0.00 20.00 24.63 23.13 1.00 593.11 Conveyor7 Conveyor 0.00 14.71 14.71 14.71 6.00 593.11 Conveyor8 Conveyor 0.00 10.00 10.00 10.00 6.00 593.11 Conveyor9 Conveyor 0.00 2.94 2.94 2.94 6.00 593.11 Rack10 Rack 8.00 0.00 0.00 0.00 2.00 593.11 Rack11 Rack 4.00 0.00 0.00 0.00 2.00 593.11 Rack12 Rack 6.00 0.00 0.00 0.00 2.00 593.11 Dispatcher13 Dispatcher 0.00 0.00 0.00 0.00 2.00 593.11 Operator15 Operator 0.00 2.23 4.11 3.44 1.00 593.11 Operator16 Operator 0.00 0.00 0.00 0.00 1.00 593.11 Transporter17 Transporter 0.00 6.45 14.31 10.10 14.00 593.11Object Class stats_content stats_staytimeminstats_staytimemaxstats_staytimeavgstate_currentstate_sinceSource1 Source 0.00 0.00 0.00 0.00 5.00 593.11 Queue2 Queue 0.00 2.33 8.54 4.37 6.00 593.11 Queue3 Queue 1.00 0.60 16.11 8.93 10.00 593.11 Processor4 Processor 0.00 20.00 24.63 22.31 1.00 593.11 Processor5 Processor 0.00 20.00 21.58 20.40 1.00 593.11 Processor6 Processor 0.00 20.00 24.63 23.13 1.00 593.11 Conveyor7 Conveyor 0.00 14.71 14.71 14.71 6.00 593.11 Conveyor8 Conveyor 0.00 10.00 10.00 10.00 6.00 593.11 Conveyor9 Conveyor 0.00 2.94 2.94 2.94 6.00 593.11 Rack10 Rack 8.00 0.00 0.00 0.00 2.00 593.11 Rack11 Rack 4.00 0.00 0.00 0.00 2.00 593.11 Rack12 Rack 6.00 0.00 0.00 0.00 2.00 593.11 Dispatcher13 Dispatcher 0.00 0.00 0.00 0.00 2.00 593.11 Operator15 Operator 0.00 2.23 4.11 3.44 1.00 593.11 Operator16 Operator 0.00 0.00 0.00 0.00 1.00 593.11 Transporter17 Transporter 0.00 6.45 14.31 10.10 14.00 593.11Object Class idle processing busy blocked generatingemptySource1 Source 0.00% 0.00% 0.00% 0.00% 100.00% 0.00% Queue2 Queue 0.00% 0.00% 0.00% 0.00% 0.00% 86.02% Queue3 Queue 0.00% 0.00% 0.00% 0.00% 0.00% 72.90% Processor4 Processor 69.90% 13.49% 0.00% 0.00% 0.00% 0.00% Processor5 Processor 86.25% 6.74% 0.00% 0.00% 0.00% 0.00% Processor6 Processor 72.71% 11.80% 0.00% 0.00% 0.00% 0.00% Conveyor7 Conveyor 0.00% 0.00% 0.00% 0.00% 0.00% 80.16% Conveyor8 Conveyor 0.00% 0.00% 0.00% 0.00% 0.00% 93.26% Conveyor9 Conveyor 0.00% 0.00% 0.00% 0.00% 0.00% 96.53% Rack10 Rack 0.00% 100.00% 0.00% 0.00% 0.00% 0.00% Rack11 Rack 0.00% 100.00% 0.00% 0.00% 0.00% 0.00% Rack12 Rack 0.00% 100.00% 0.00% 0.00% 0.00% 0.00% Dispatcher13 Dispatcher 0.00% 100.00% 0.00% 0.00% 0.00% 0.00% Operator15 Operator 78.27% 0.00% 0.00% 0.00% 0.00% 0.00% Operator16 Operator 60.89% 0.00% 0.00% 0.00% 0.00% 0.00% Transporter17 Transporter 43.73% 0.00% 0.00% 0.00% 0.00% 0.00%2、改变输入条件,输出数据为:产品到达速率:产品到达间隔时间服从均值为30 秒、方差为4 的正态分布暂存区最大容量:25检测机时间参数:准备时间是10 秒,加工时间服从均值为30 秒的指数分布传送带参数:传送速度是5 米/秒,传送带上同时最多传送100 个产品Flexsim Summary ReportTime: 593.1079Object Class stats_content stats_staytimeminstats_staytimemaxstats_staytimeavgstate_currentstate_sinceSource1 Source 0.00 0.00 0.00 0.00 5.00 593.11 Queue2 Queue 0.00 2.33 8.54 4.37 6.00 593.11 Queue3 Queue 1.00 0.60 16.11 8.93 10.00 593.11 Processor4 Processor 0.00 20.00 24.63 22.31 1.00 593.11 Processor5 Processor 0.00 20.00 21.58 20.40 1.00 593.11 Processor6 Processor 0.00 20.00 24.63 23.13 1.00 593.11 Conveyor7 Conveyor 0.00 14.71 14.71 14.71 6.00 593.11 Conveyor8 Conveyor 0.00 10.00 10.00 10.00 6.00 593.11 Conveyor9 Conveyor 0.00 2.94 2.94 2.94 6.00 593.11 Rack10 Rack 8.00 0.00 0.00 0.00 2.00 593.11 Rack11 Rack 4.00 0.00 0.00 0.00 2.00 593.11 Rack12 Rack 6.00 0.00 0.00 0.00 2.00 593.11 Dispatcher13 Dispatcher 0.00 0.00 0.00 0.00 2.00 593.11 Operator15 Operator 0.00 2.23 4.11 3.44 1.00 593.11 Operator16 Operator 0.00 0.00 0.00 0.00 1.00 593.11 Transporter17 Transporter 0.00 6.45 14.31 10.10 14.00 593.11Object Class idle processing busy blockedgeneratingemptySource1 Source 0.00% 0.00% 0.00% 0.00% 100.00% 0.00% Queue2 Queue 0.00% 0.00% 0.00% 0.00% 0.00% 86.02% Queue3 Queue 0.00% 0.00% 0.00% 0.00% 0.00% 72.90% Processor4 Processor 69.90% 13.49% 0.00% 0.00% 0.00% 0.00% Processor5 Processor 86.25% 6.74% 0.00% 0.00% 0.00% 0.00% Processor6 Processor 72.71% 11.80% 0.00% 0.00% 0.00% 0.00% Conveyor7 Conveyor 0.00% 0.00% 0.00% 0.00% 0.00% 80.16% Conveyor8 Conveyor 0.00% 0.00% 0.00% 0.00% 0.00% 93.26% Conveyor9 Conveyor 0.00% 0.00% 0.00% 0.00% 0.00% 96.53% Rack10 Rack 0.00% 100.00% 0.00% 0.00% 0.00% 0.00% Rack11 Rack 0.00% 100.00% 0.00% 0.00% 0.00% 0.00% Rack12 Rack 0.00% 100.00% 0.00% 0.00% 0.00% 0.00% Dispatcher13 Dispatcher 0.00% 100.00% 0.00% 0.00% 0.00% 0.00% Operator15 Operator 78.27% 0.00% 0.00% 0.00% 0.00% 0.00% Operator16 Operator 60.89% 0.00% 0.00% 0.00% 0.00% 0.00% Transporter17 Transporter 43.73% 0.00% 0.00% 0.00% 0.00% 0.00%Object Class statscontent stats_staytimeminstats_staytimemaxstats_staytimeavgState-currentstate_sinceSource1 Source 0.00 0.00 0.00 0.00 5.00 593.11 Queue2 Queue 0.00 2.33 8.54 4.37 6.00 593.11 Queue3 Queue 1.00 0.60 16.11 8.93 10.00 593.11 Processor4 Processor 0.00 20.00 24.63 22.31 1.00 593.11 Processor5 Processor 0.00 20.00 21.58 20.40 1.00 593.11 Processor6 Processor 0.00 20.00 24.63 23.13 1.00 593.11 Conveyor7 Conveyor 0.00 14.71 14.71 14.71 6.00 593.11 Conveyor8 Conveyor 0.00 10.00 10.00 10.00 6.00 593.11 Conveyor9 Conveyor 0.00 2.94 2.94 2.94 6.00 593.11 Rack10 Rack 8.00 0.00 0.00 0.00 2.00 593.11 Rack11 Rack 4.00 0.00 0.00 0.00 2.00 593.11 Rack12 Rack 6.00 0.00 0.00 0.00 2.00 593.11 Dispatcher13 Dispatcher 0.00 0.00 0.00 0.00 2.00 593.11 Operator15 Operator 0.00 2.23 4.11 3.44 1.00 593.11 Operator16 Operator 0.00 0.00 0.00 0.00 1.00 593.11 Transporter17 Transporter 0.00 6.45 14.31 10.10 14.00 593.11。
物流配送中心选址数学模型的研究和优化
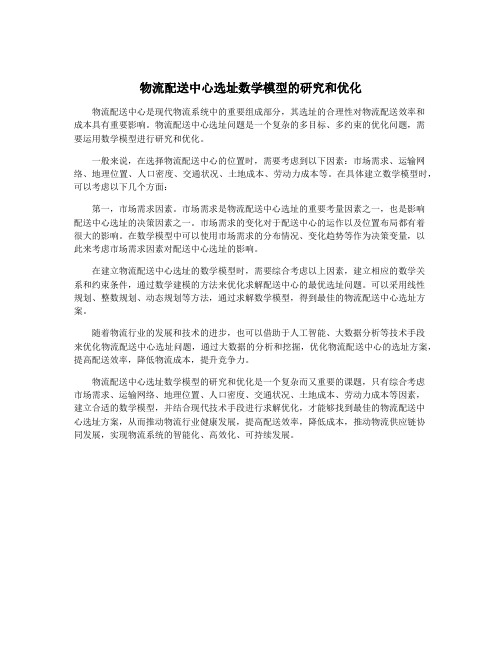
物流配送中心选址数学模型的研究和优化物流配送中心是现代物流系统中的重要组成部分,其选址的合理性对物流配送效率和成本具有重要影响。
物流配送中心选址问题是一个复杂的多目标、多约束的优化问题,需要运用数学模型进行研究和优化。
一般来说,在选择物流配送中心的位置时,需要考虑到以下因素:市场需求、运输网络、地理位置、人口密度、交通状况、土地成本、劳动力成本等。
在具体建立数学模型时,可以考虑以下几个方面:第一,市场需求因素。
市场需求是物流配送中心选址的重要考量因素之一,也是影响配送中心选址的决策因素之一。
市场需求的变化对于配送中心的运作以及位置布局都有着很大的影响。
在数学模型中可以使用市场需求的分布情况、变化趋势等作为决策变量,以此来考虑市场需求因素对配送中心选址的影响。
在建立物流配送中心选址的数学模型时,需要综合考虑以上因素,建立相应的数学关系和约束条件,通过数学建模的方法来优化求解配送中心的最优选址问题。
可以采用线性规划、整数规划、动态规划等方法,通过求解数学模型,得到最佳的物流配送中心选址方案。
随着物流行业的发展和技术的进步,也可以借助于人工智能、大数据分析等技术手段来优化物流配送中心选址问题,通过大数据的分析和挖掘,优化物流配送中心的选址方案,提高配送效率,降低物流成本,提升竞争力。
物流配送中心选址数学模型的研究和优化是一个复杂而又重要的课题,只有综合考虑市场需求、运输网络、地理位置、人口密度、交通状况、土地成本、劳动力成本等因素,建立合适的数学模型,并结合现代技术手段进行求解优化,才能够找到最佳的物流配送中心选址方案,从而推动物流行业健康发展,提高配送效率,降低成本,推动物流供应链协同发展,实现物流系统的智能化、高效化、可持续发展。
物流系统建模与仿真配送中心系统仿真设计实验报告
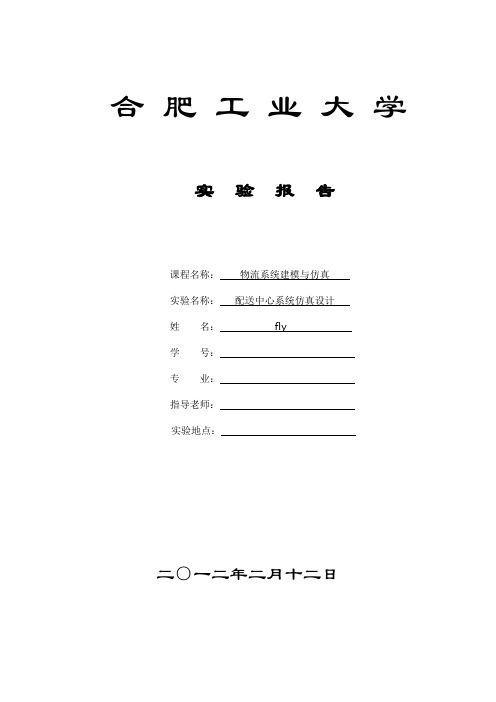
合肥工业大学实验报告课程名称:物流系统建模与仿真实验名称:配送中心系统仿真设计姓名:fly学号:专业:指导老师:实验地点:二○一二年二月十二日一、实验目的:1)了解供应链仿真的设计。
2)熟悉动态表格的设计。
3)了解Conveyor作为生产缓存的方法。
4)了解拉动式系统的设计。
5)研究不同配送策略的利润情况。
二、实验环境电子商务实验室,计算机、Witness 2004 Educational Version 仿真软件三、实验内容与步骤:1、元素定义(Define)本系统的元素定义如表1-1所示。
元素定义后的witness页面截图如图1-1:图1-1 元素定义后的witness页面2、元素可视化(Display)设置各个实体元素的显示特征定义设置如图1-2所示:图1-2 各个实体元素的显示特征1)Part Buffer元素可视化的设置在元素选择窗口选择P1元素,鼠标右键点击Display出现如图3所示对话框,设置它的Text、Icon和Style属性项。
图1-3 Display对话框2)Buffer元素可视化的设置选择Zhongxin元素,设置它们的Text、Icon、Part queue和Rectangle属性项,分别如图1-4、图1-5、图1-6、图1-2所示。
图l-4 Display Text对话框图1-5 Icon对话框图1-6 Display Part Queue对话框图1-7 Text对话框3)Machine元素可视化的设置在元素选择窗口选择Factory1元素,鼠标右键点击Display出现如图11-1所示对话框,设置它的Text、Icon(机器图标)、Icon(可随状态改变颜色的图标),Part Queue。
如图1-7、图1-8、图1-9、图1-2所示。
图1-8 Icon对话框1-9 Icon对话框类似,在元素选择窗门选择Factory2、Factory3、Factory21,Factory22、Factory23元素,鼠标右键点击Display出现如图1-1所示对话框,设置它们的Text、Icon(机器图标)、Icon(可随状态改变颜色的图标)、Part Queue。
物流配送中心选址数学模型的研究和优化
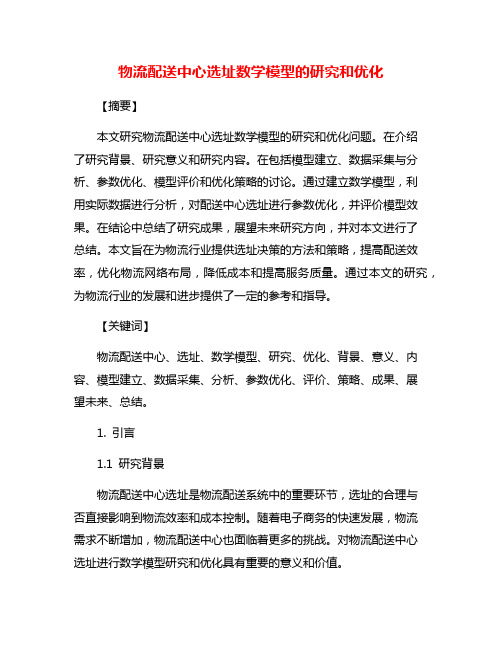
物流配送中心选址数学模型的研究和优化【摘要】本文研究物流配送中心选址数学模型的研究和优化问题。
在介绍了研究背景、研究意义和研究内容。
在包括模型建立、数据采集与分析、参数优化、模型评价和优化策略的讨论。
通过建立数学模型,利用实际数据进行分析,对配送中心选址进行参数优化,并评价模型效果。
在结论中总结了研究成果,展望未来研究方向,并对本文进行了总结。
本文旨在为物流行业提供选址决策的方法和策略,提高配送效率,优化物流网络布局,降低成本和提高服务质量。
通过本文的研究,为物流行业的发展和进步提供了一定的参考和指导。
【关键词】物流配送中心、选址、数学模型、研究、优化、背景、意义、内容、模型建立、数据采集、分析、参数优化、评价、策略、成果、展望未来、总结。
1. 引言1.1 研究背景物流配送中心选址是物流配送系统中的重要环节,选址的合理与否直接影响到物流效率和成本控制。
随着电子商务的快速发展,物流需求不断增加,物流配送中心也面临着更多的挑战。
对物流配送中心选址进行数学模型研究和优化具有重要的意义和价值。
在过去的研究中,物流配送中心选址主要依靠经验和专家判断,缺乏科学的分析和决策支持。
随着数学建模和优化算法的发展,可以通过建立数学模型来辅助决策者进行选址决策。
通过对物流需求、市场结构、交通网络等多方面因素进行综合分析,可以预测不同选址方案的效果,并进行优化选择。
本研究旨在通过建立数学模型,采集和分析相关数据,优化模型参数,评价优化效果,并提出相应的优化策略,以提高物流配送中心选址的效率和准确性。
通过本研究的开展,将为物流配送中心选址提供更科学的决策支持,促进物流行业的发展和进步。
1.2 研究意义物流配送中心选址数学模型的研究和优化具有重要的意义。
物流配送中心的选址决定着整个物流系统的效率和成本。
一个合理的选址能够减少货物的运输距离和时间,降低运输成本,提高配送效率。
选址还关系着配送中心对周边地区的服务覆盖范围,直接影响着客户的满意度和品牌形象。
配送中心规划及仿真研究

配送中心规划及仿真研究作者:高慧芝来源:《商情》2017年第36期【摘要】配送中心的规划与仿真占据着重要的作用,本文研究了配送中心作业区域规划、配送中心作业区域布置,介绍了仿真的概念,分析了仿真的作用。
【关键词】配送中心规划仿真一、配送中心作业区域规划配送中心的作业区域一般包括收货区、发货区、货物存储区、托盘暂存区、拣货区、流通加工区、办公区、计算机管理监控区和设备存放与维护区等,根据规划资料分析确定所需的作业区域。
作业区域确定以后,然后确定各区域的基本运转能力,最后根据各区域的基本运转能力确定各区域的作业面积。
(1)基本运作能力分析。
在确定所需的功能区域后,需要通过对规划资料进行分析,确定各作业区域的基本运作能力,以仓储区的储存能力为例,其估算可采用周转率估算法,其数学模型为:仓储量=年仓储运转量/周转次数×安全系数(2)区域面积规划。
各作业功能区域面积的确定与各区域的物流量、所配备的设施和设备以及作业方式等有关,因此具体每个作业区域的面积应分别进行详细的计算。
以仓储区作业面积的计算为例,仓储区的作业面积与货物的尺寸及数量、托盘尺寸、货架等因素有关,其数学模型为:设托盘的宽度为a米,每托盘平均可以叠放n箱货品,托盘可堆码c层,若配送中心的平均存货量约为q,则存货面积s为:实际仓储需求空间须考虑穿梭车存取作业所需空间,一般通道面积占全部面积的35%-40%,设ε=35%-40%,因此实际仓储面积为:s=s/ε对于有些物流作业区域,其作业面积不能通过像仓储区的作业面积直接求得,但是由于其作业面积主要取决于货物作业量。
可以通过以下的公式估算:式中代表一种货物每日的作业量,代表该区域的面积利用系数,面积利用系数取决于货物的类型、货物的存放方式以及所采用的作业设备等。
二、配送中心作业区域布置作业区域布置包括作业区域位置布置和作业区域面积布置两个步骤。
(1)作业区域位置布置。
配送中心总平面布置并不直接考虑个作业单位的占地面积及几何外形,而是从各作业单位间综合相互关系的密切程度出发,布置个作业单位之间的相对位置,综合相互关系密切程度高的作业单位之间的距离近,反之则距离远,由此得到作业单位位置相关图。
汽车制造业零部件配送中心选址模型建立与Lingo求解
技 术 与 方 法
d i 03 6  ̄is .0 5 1 2 2 1 .80 1 o: .9 9 . n1 0 - 5 X. 20 .9 l s 0
C agh n 3 0 13D pr noOd a cT cn l yJl U iesyC agh n ' 0 2C ia hnc u 10 2 ;.e at tf rn e eh oo ,in nvri ,hn cu 1 0 6 ,hn ) me n g i t 3
Abs r c : nt i p p rwee t b ih dt e iti u i nc s d l o e p r a t iti u i nc n e f e t i g -s aec — k n t a t I s a e , sa l e srb t o t h s hd o mo e r h a ep rs sr to e tr ac r nl e c l a ma i g f t s d b o a a r r e t r rs n h n, mp o i gt e s f r e L n o a d c n i e i gc mp e e sv l o t g c s , x d c s n c l o f c e t c ri d o t n ep iea d t e e ly n ot h wa i g n o sd rn o r h n ie yf a i o t f e o t d s ae c e f i n , a re u l n i a i a sa e h s d ts ft emo e , h e u t f ih h d p i t d o t heo tma e rt e c n tu to flg sisc n o i ai n c n e rt e t g - a e e t d l t er s l o c a on e u p i l a af o sr c in o i t o s ld t e trf o h wh t r oh o c o o h c r ma e . a— k r K e wo d : iti u inc n e :o ai n c s ; d l y r s d srb t 0 e tr lc t ; o tmo e o
关于配送中心重心法选址的研究
关于配送中心重心法选址的研究一、本文概述随着电子商务和物流行业的快速发展,配送中心作为物流网络中的关键节点,其选址问题日益受到业界的关注。
合理的配送中心选址不仅能够降低物流成本,提高物流效率,还能有效地优化供应链的整体性能。
重心法作为一种经典的设施选址方法,在配送中心选址中具有广泛的应用。
本文旨在对重心法在配送中心选址中的应用进行深入的研究和探讨。
本文首先介绍了配送中心选址的重要性,以及重心法的基本原理和计算方法。
在此基础上,通过文献综述的方式,对国内外关于重心法在配送中心选址中的研究进行了梳理和评价。
随后,结合具体案例,详细阐述了重心法在配送中心选址中的实际应用过程,包括数据收集、处理、模型构建和求解等步骤。
本文总结了重心法在配送中心选址中的优势与不足,并提出了相应的改进策略和建议。
本文的研究对于提高配送中心选址的科学性和合理性具有重要的理论意义和实践价值。
通过深入研究重心法在配送中心选址中的应用,不仅可以为企业提供更加科学和有效的选址决策支持,还能为物流行业的健康发展提供有力的理论支撑和实践指导。
二、文献综述配送中心选址问题是物流管理和供应链优化中的核心问题之一。
重心法作为一种经典的选址方法,在理论和实践层面均得到了广泛的研究和应用。
本文旨在对重心法在配送中心选址中的应用进行深入研究,通过对现有文献的梳理和评价,为后续的实证研究提供理论基础。
在文献综述部分,首先回顾了重心法的发展历程和基本原理。
重心法起源于物理学中的重心概念,后被引入到运筹学和物流管理中,用于解决多目标、多约束的选址问题。
该方法通过构建数学模型,将配送中心的选址问题转化为求解成本最小化或效率最大化的问题。
本文梳理了国内外学者在重心法选址研究方面的主要成果。
国内外学者在重心法的基础上进行了大量的改进和创新,如引入不同的成本函数、考虑多层次的约束条件、结合其他优化算法等。
这些研究不仅丰富了重心法的理论体系,也提高了其在实际应用中的效果。
物流配送中心选址数学模型的研究和优化
物流配送中心选址数学模型的研究和优化物流配送中心的选址是一个关键的决策问题,它不仅直接关系到物流效率,也对企业的经济效益产生直接影响。
在新的城市建设或农村地区开发中,物流配送中心的选址更是必不可少的环节。
如何确定物流配送中心的最佳选址,是一个需要深入研究和不断优化的问题。
物流配送中心选址数学模型的研究和优化是解决此问题的有效手段。
数学模型能够通过建立数学方程和条件,将问题转化为可解的数学问题。
在建立数学模型时,需要考虑多个因素,例如周围的交通状况、人流量、商圈、租金、物流成本等。
经过分析和计算,得出最佳方案,能够节省时间和成本,提高效率,并为企业增加更多的经济价值。
常见的物流配送中心选址数学模型包括最小总成本模型、最小覆盖模型、最小距离模型、中心化模型等。
其中,最小总成本模型是最为普遍的,通过分析各种成本因素并评估其影响,寻求最低成本的选址方案。
该模型的关键是确定成本因素的权重和各地区物流成本的数值。
最小覆盖模型则是为了最大化服务范围而设计的,通过要求服务范围包含最多的消费者,找到最佳的配送中心位置。
相比之下,最小距离模型更注重行政层面的管辖,具备较强的政策倾向性。
而中心化模型则是综合考虑多个区域的供货质量和销售需求,寻找最合适的中心点进行服务。
除了考虑表面因素的贡献以外,如今科技的快速发展还提供了新的工具来支持物流配送中心的选址,例如大数据分析和人工智能。
数据分析的方法可以对货物的来源和目的地进行更细致和准确的刻画和描述,用于确定配送的最优路径和方案,优化物流中心的运作。
而人工智能则可以逐步整合并优化各水平上的各种因素,使得物流配送中心的选址更加高效、经济和智能化。
总之,物流配送中心选址数学模型的研究和优化将成为未来物流领域的重要发展方向,帮助企业更好地规划和组织物流仓储,在今后的速递、同城配送、农村配送等领域发挥更加重要的作用。
物流配送中心选址优化模型及算法研究
物流配送中心选址优化模型及算法研究一、概述随着电子商务和全球化的快速发展,物流配送中心在供应链管理中的作用日益凸显。
合理的物流配送中心选址不仅有助于降低运营成本、提高物流效率,还能对整个供应链的顺畅运作产生深远影响。
物流配送中心选址优化问题一直是学术界和工业界研究的热点。
本文旨在深入研究物流配送中心选址优化模型及算法,旨在为实际应用中的物流配送中心选址提供科学、高效的决策支持。
本文首先对物流配送中心选址问题的背景和意义进行介绍,分析现有研究的进展和不足,并指出本研究的必要性和创新性。
在此基础上,本文将构建物流配送中心选址优化模型,综合考虑成本、时间、服务质量等多个因素,以实现选址决策的全面优化。
同时,本文将研究并应用先进的优化算法,如遗传算法、粒子群优化算法等,以提高选址决策的速度和准确性。
本文的研究不仅有助于丰富物流配送中心选址优化理论,还将为实际应用中的物流配送中心选址提供有力支持,对提升我国物流行业的整体竞争力具有重要意义。
1. 物流配送中心选址的重要性物流配送中心选址问题是物流系统规划中的核心问题之一,其重要性不容忽视。
合理的选址决策不仅能够优化物流网络布局,提高物流效率,降低运营成本,还能够促进区域经济发展,增强企业的市场竞争力。
具体来说,物流配送中心选址的重要性体现在以下几个方面:选址决策直接关系到物流网络的运行效率。
物流配送中心作为物流网络中的关键节点,其位置的选择将影响到货物在供应链中的流动速度和成本。
合理的选址能够使货物在运输、仓储、配送等环节中的流动更加顺畅,减少不必要的转运和等待时间,从而降低物流成本,提高物流效率。
选址决策对于企业的运营成本具有重要影响。
物流配送中心的建设和运营成本包括土地购置费用、设施设备投入、人力成本等多个方面。
选址决策的合理与否将直接影响到这些成本的高低。
通过科学的选址优化模型,企业可以在保证物流服务水平的前提下,尽可能降低建设和运营成本,提高企业的盈利能力。
- 1、下载文档前请自行甄别文档内容的完整性,平台不提供额外的编辑、内容补充、找答案等附加服务。
- 2、"仅部分预览"的文档,不可在线预览部分如存在完整性等问题,可反馈申请退款(可完整预览的文档不适用该条件!)。
- 3、如文档侵犯您的权益,请联系客服反馈,我们会尽快为您处理(人工客服工作时间:9:00-18:30)。
务的质量关系着汽车产品的市场销售。在成熟的汽车市场中,
汽车的销售利润约占整个汽车业利润的20%,零部件供应利 润约占20%,而50%-60%的利润是从售后服务中产生的。汽 车制造企业要在整车价格日益压低的情况下获利,就需充分 重视企业的零部件售后服务。汽车售后零部件配送中心作为
商务环境下带软时间窗的配送中心选址模型,并采用遗传算 法和模拟退火算法相结合进行求解嗍。Zhang研究了多级服务 站环境下的设施点选址和容量优化问题,提出了设施点容量 不确定条件下的选址方案[51。郑志成等(2009)提出了将灰色关 联度和层次分析法应用于冷链物流配送中心的选址同。方春明 等(2009)通过采用欧几里得模型确立配送中心地理位置,解 决汽车工业入厂物流的选址问题【7l。马龙飞(2010)对传统模型
配送中心一起实现分区域配送。 由于该公司新建配送中心的主要目的在于提高售后零部 件订单的响应速度,因而配送时间相对于配送成本来说更为
物流技术2013年第32卷第8期(总第287期)
疆、安徽、青海、宁夏、江西、甘肃、陕西、河南、广西、四川、上 海、浙江、福建、广东、江苏、山东。
4.4求解程序的编写
运用lingo软件,编程如下:
model:
sets:
重要。作为供应链上核心企业,该公司更为看重配送中心向4S
店配货的可达性和敏捷性,因而本文将售后零部件运输分为
suppHedl—10,:影 crxt/l。6/:z。b: demand/1..30,:c:
两个阶段,分别赋予两个阶段运输里程不同的权值,初步定为 B:仅=3:1(不同企业可以视具体情况而对其进行变动),即对 配送中心向4S店的配送赋予较高权值,对供应商向配送中心 的批量供货赋予较低权值。
=1。
D:模型构建中引入的一个相当大的正数;
n:供应商到配送中心供货中总吨公里数的权值; B:配送中心到4s店配送中总吨公里数的权值,d+B
瓮
\ /
Mm=a∑::-∑::i ∑::i b≤^
£J:l瓢≥ck
∑}:,K≤Bi
Mij妁zi+p∑;:l∑l:t‰酗
(1)
∑:=。‰=∑l:。龟
(2)
(3) (4)
配送中心选址作为物流网络构建的重要研究内容,引起 1
引言
汽车售后服务是汽车流通领域的一个重要环节,售后服
了国内外学者的广泛关注。主要研究成果集中在选址模型及
相关算法方面。Klose(2005)研究了行程时间、供应与需求模式
都是随机变化的仓库选址分配问题”。秦固(2006)以物流配送
总成本最低为聚类准则,采用蚁群算法求解物流配送中心的 选址121。Allem(2007)研究了在工业服务中不确定因素对于设施 点选址和企业竞争优势的影响131。刘必争等(2008)提出了电子
进行改进,并利用随机规划理论和遗传算法对实例模型进行 求解嘲。汤希峰等(2012)将可靠性作为物流服务水平的一种测 度,提出了配送中心系统可靠度的计算方法,并建立了配送中
汽车售后供应链中不可缺少的关键环节,其将供应商和各地 的4S店衔接起来,对零部件的增值贡献巨大。零部件配送中 心位置的选择与配送网络的规划,不仅对汽车制造企业的售 后服务质量有着巨大的影响,还关系着汽车制造企业能否有 效地压低成本,能否在竞争激烈的环境中获得更大的市场占
(3)供应商的总生产能力已知且固定;
(4)各4S店的零部件需求量已知且基本固定; (5)配送中心建设所需的固定费用和日常管理费用为常 数,且由于定性分析所确立的城市经济发展状况差别不大,认 为其两项费用相同,不在模型中体现。
4.1
4实例仿真
某汽车制造企业配送中心情况概述
目前,某汽车公司拥有一家正在运行的配送中心,位于上 海,负责为全国400多家4S店进行售后零部件的配送。该汽 车公司为应对汽车售后市场需求量的日益增加,需在现有供 应链中增加配送中心的建设,以缓解现有配送中心超负荷运
做进一步的分析,提出配送中心建设地的选址要求。 (1)交通便利,零部件的运输对时间要求很高,配送中心
100.2 218.4 38.4 203
174.9 81
71.4 705.2;
117
182.4 482.8 m=l 008
399 0
322 826
1 269 993
2 223 1 602 1 879 1 885 437 345
example.we built the corresponding model and applied it
to
a
simulation
study.
Keywords:automobile aftersales spsre part;distribution center;,location model;simulation
技术与应用
doi:l
物流技术2013年第32卷第8期(总第287期)
O.39694.issn.1 005-1 52X.201 3.08.050
汽车制造企业售后零部件配送中心 选址模型与仿真研究
王琦。吴群
(江西财经大学,江西南昌330013)
【摘要】结合汽车售后零部件的特点,对两阶段配送的总吨公里数引入不同的权重,将o-l混合整数规划模型进行了改进, 成功建立了汽车售后零部件配送中心选址模型,最后以国内某大型汽车制造企业为例进行建模,通过lingo软件进行了仿真,以 期对企业配送设施选址及零部件配送优化起到一定借鉴作用。 【关键词】汽车售后零部件;配送中心;选址模型;仿真 【中豳分类号]F426;F252.14;1;'224
借助lingo软件进行求解,以期对汽车零部件配送中心选址起
到一定借鉴价值。
3多配送中心选址模型
3.1
目标描述
为满足市场的不断扩张,提高服务的质量,汽车制造企业
பைடு நூலகம்往往需要新建若干家配送中心,与现行的配送中心共同构成
xii:供应商i向备选配送中心j的供货量;
Y。:备选配送中心J向需求地k的送货量;
新的配送网络。建成后的数家配送中心从i个零部件供应商处
3.3模型构建
由于供应商对配送中心的运输为大批量规模运输,而配
送中心对4s店的运输为小批量,且汽车售后零部件的配送对 时间的要求很高,因而配送中心的建立须对4s店有更高的关
作的压力,解决由此带来的订单准时完成率低、订货提前期较 _15争
万方数据
技术与应用
长等问题,全面提高客户的满意度。但考虑到成本投入的有限 性和企业发展的阶段性,其需要新建立一家配送中心,与上海
4.2配送中心位置初选
考虑到汽车售后零部件种类繁多,涉及到的供应商也相
对较多。公司为保证汽车售后服务。对售后零部件配送的准时
性要求很高。因而新的配送中心建设筛选因素中应包括交通 条件、经济发展水平、产业结构与产业布局、城市规划及区域
b=2 000 c=26.4 O.6 27 1.2 10
自然特征、社会环境等。综合考虑,本文将配送中心的选址范 围初步设定在各大省会城市,并结合该汽车公司的具体情况
2 108 1 231 l 308
l 798 1 201 O 1 893
的建立需要四通八达的交通网络作支撑。
(2)经济发达地区,当地的物流产业结构需符合汽车售后 配送中心的要求,且当地对于该公司的售后零部件需求量要 达到全国前列。
-15争
万方数据
王琦,等:汽车制造企业售后零部件配送中心选址模型与仿真研究
心多目标优化模型嘲。 但在现有选址模型研究文献中,普遍缺乏对具体行业发 展特点的关注,尤其针对企业自身发展阶段和已有配送中心 的关注较少,对配送时间的关注程度更少。目前关于汽车企业 配送中心的选址研究也多集中在零部件的人厂物流,鲜有结 合售后零部件特点进行配送中心的选址研究。本文研究汽车 制造企业售后零部件配送中心的选址问题,构建相关模型并
有率和利润。
2相关文献综述
【收稿日期]2013-05-15 【基金项目】教育部人文社科项目(10YJC630285) I作者简介】王琦(1991一),女,河南洛阳人,江西财经大学学生;吴群(1981-),女,山东莱芜人。博士,江西财经大学工商管理学院讲师,在站博 士后,主要研究方向:物流供应链管理。
式(1)表示供应商供应零部件至配送中心与配送中心配
送零部件到各个销售区域的最小吨公里数之和;式(2)表示每
个配送中心的进货量与出货量相等;式(3)表示各供应商的供 货量不超过其生产能力;式(4)表示需求地的收货量不小于其 需求;式(5)表示配送中心的进货量不大于其仓储能力;式(6) 表示供应商只给选中的配送中心供应货物;式(7)表示新建立 n个配送中心;式(8)表示保留原有运行中的配送中心;式(9) 表示zj是0一l变量。
接收货物,经过仓储、拣选、集货等环节后,向全国的k个4s 店提供配送服务,使得零部件的供需和流动形成一个完整的 物流配送网络结构(如图1所示)。供应商和4S店的数量与位 置是固定的,从j个备选配送中心中选出n个(固定数量),并 规划出供应商和配送中心、配送中心与4s店的供应关系,使 得总的运输费用最小。
Location
【文献标识码JA
【文章编号]1005-152X(2013)08-0154-04
Model and Simulation ofAfter-sales Spare Part Distribution Center ofCar-making Enterprises
WangQi,WuQun
0ian鲥University dFinance&Economics,Nanchang 330013,China)
技术与应用
注比例。本文在建立以配送成本最低(由于运输费率相同,计 算时不做考虑)为目标函数的数学模型时,考虑到汽车零部件 的特性,对两阶段的吨公里数进行了赋权,且权数越大表示对 此层级越关注。建立模型如下: I:售后零部件供应商,I={1,2….,i); J:已有配送中心的所在地和预建配送中心的备选地(前e 个为己有配送中心所在地),J={l,2,…,j}; K:需求地,K=(1,2,…,k}; Ai:供应商的零部件生产能力,Ai-(a,,a2,…,ai); Bi:配送中心j的最大容量; c。:需求地k的需求量; Mij:供应商i到配送中心j的距离; NI:备选配送中心j到需求地k的距离; zi:表明备选配送中心j是否建立的O—l变量;