CRW2040 43K 5% 100PPM;中文规格书,Datasheet资料
PowerWeld Inc. 铝合金焊胶和焊丝安全数据表说明书
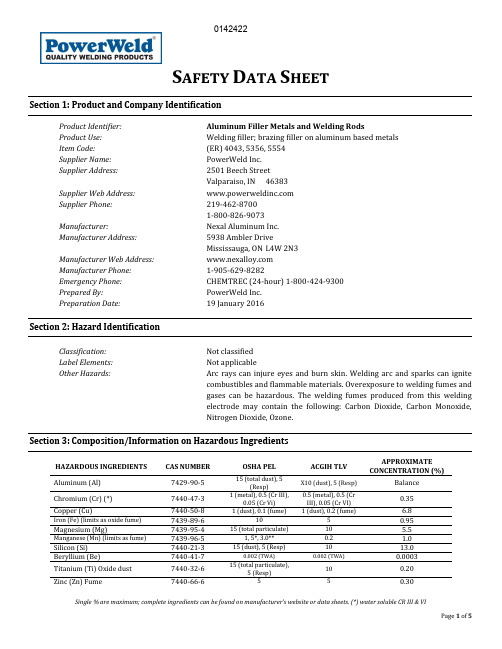
S AFETY D ATA S HEETSection 1: Product and Company IdentificationProduct Identifier:Aluminum Filler Metals and Welding RodsProduct Use: Welding filler; brazing filler on aluminum based metals Item Code: (ER) 4043, 5356, 5554 Supplier Name: PowerWeld Inc. Supplier Address: 2501 Beech StreetValparaiso, IN 46383 Supplier Web Address: Supplier Phone: 219-462-8700 1-800-826-9073 Manufacturer: Nexal Aluminum Inc. Manufacturer Address: 5938 Ambler DriveMississauga, ON L4W 2N3 Manufacturer Web Address: Manufacturer Phone: 1-905-629-8282Emergency Phone: CHEMTREC (24-hour) 1-800-424-9300 Prepared By: PowerWeld Inc. Preparation Date:19 January 2016Section 2: Hazard Identification Classification:Not classifiedLabel Elements:Not applicableOther Hazards:Arc rays can injure eyes and burn skin. Welding arc and sparks can ignite combustibles and flammable materials. Overexposure to welding fumes and gases can be hazardous. The welding fumes produced from this welding electrode may contain the following: Carbon Dioxide, Carbon Monoxide, Nitrogen Dioxide, Ozone.Section 3: Composition/Information on Hazardous IngredientsHAZARDOUS INGREDIENTS CAS NUMBER OSHA PELACGIH TLVAPPROXIMATE CONCENTRATION (%)Aluminum (Al) 7429-90-5 15 (total dust), 5(Resp)X10 (dust), 5 (Resp) Balance Chromium (Cr) (*) 7440-47-3 1 (metal), 0.5 (Cr III),0.05 (Cr Vi) 0.5 (metal), 0.5 (Cr III), 0.05 (Cr VI) 0.35 Copper (Cu)7440-50-8 1 (dust), 0.1 (fume)1 (dust), 0.2 (fume)6.8 Iron (Fe) (limits as oxide fume)7439-89-6 105 0.95 Magnesium (Mg)7439-95-4 15 (total particulate)10 5.5 Manganese (Mn) (limits as fume)7439-96-5 1, 5*, 3.0** 0.2 1.0 Silicon (Si) 7440-21-3 15 (dust), 5 (Resp)1013.0 Beryllium (Be)7440-41-7 0.002 (TWA)0.002 (TWA)0.0003 Titanium (Ti) Oxide dust 7440-32-6 15 (total particulate),5 (Resp)10 0.20 Zinc (Zn) Fume7440-66-6550.30Single % are maximum; complete ingredients can be found on manufacturer’s website or data sheets. (*) water soluble CR III & VI0142422Section 4: First-aid MeasuresInhalation:Inhalation may be the most common cause of overexposure due to thewelding fumes. Large amounts of welding fumes will cause irritation of thenose, eyes and skin. Move from the area that has any fumes to fresh air. Ifbreathing is difficult, give oxygen. If not breathing, give artificial respirationand transport to nearest medical facility for additional treatment.Ingestion:Not an expected route of exposure. Rinse month completely and drink a cupof water if conscious; obtain medical assistance when needed.Eye Contact:If arc flash or burns occur, obtain medical assistance. Large exposure towelding fumes may cause irritation to the eyes. Immediately flush upperand lower eyelids with plenty of water. After initial flushing, remove anycontact lenses and continue flushing for at least 15 minutes. Rest eyes for30 minutes. If redness, burning, blurred vision or swelling persists, visitnearest medical facility for additional treatment.Skin Contact:Large exposure to welding fumes may cause irritation to skin. If burnsoccur, flush with clean cool water for 15 minutes; obtain medical assistancewhen needed.NOTE: In all severe cases, contact physician immediately. Local telephone operators can provide number of regional poison control centre.Section 5: Fire-fighting MeasuresFlammable:NoMeans of Extinction:Not applicableAuto-ignition Temperature:Data not availableHazardous Combustion Products: Data not availableExplosion Data Sensitivity toMechanical Impact:Data not availableExplosion Data Sensitivity toStatic Discharge: Data not availableSpecial Equipment:Not applicablePrecautions for Fire Fighters:This product as shipped is non-flammable; however, fine chips and dustmay increase the explosion rating under certain heat and other ignitionhazards. Hydrogen gas and irritating fumes may form when involved in afire or if decomposing is caused from water, alcohol or sodium hydroxides.Do not use water with any molten metals and use self-contained safetyclothing/equipment in case of fires.Section 6: Accidental Release MeasuresProtection Equipment:Gloves may be worn while handling aluminum.Emergency Procedures:This product is in rod and wire form and has no hazards as shipped.Leak or Spill Procedure:If spilled, the product may be picked up (wearing gloves) and placed backinto the container. If metals become molten, contain with sand and allow toreturn back into a solid for recycle as scrap.Section 7: Handling and StorageHandling Procedures and Equipment:Proper protective gloves can be worn while handling product. During alloperations, do not eat or drink while handling and ensure properventilation while welding, brazing or processing.Storage Requirements:Store in a cool, dry and low humid location.Incompatibilities:None knownSection 8: Exposure Controls/Personal ProtectionExposure Limits:I NGREDIENTSC ANADA TWA V ALUE (MG/M3) E XPOSURE L IMITS (MG/M3) (A) (BC) (M) (O) (Q) OSHA PEL ACGIH TLVAluminum (Al) 5(p), 10(dust) 1(Resp)1(RF)1(RF)10, 5(WF)15(total dust), 5(Resp)10(dust), 1(Resp)Chromium (Cr) 0.5 0.5, 0.01 (Cr VI) 0.5 1(metal), 0.5 (Cr III),0.005 (Cr VI) 0.5(metal), 0.5 (Cr III), 0.05 (Cr VI)Copper (Cu) 1(DM), 0.2(fume) 0.2(fume) 1(DM), 0.2(fume) 1(dust), 0.1(fume) 1(dust), 0.2(fume)Iron (Fe) [oxide fume] 5(Resp)10.0(STEL), 5(FD),3(RF), 10.0(TD)5(FD)5(RF)5(FD), 10.0(TD),10(fume) 10 5Magnesium (Mg) 10(oxidefume) (box) 10.0(STEL), 3,10.0(IU)10.0(IF)10(fume) 15 (total particulate) 10Manganese (Mn) [fume] 0.2 0.1(IF),0.02(RF)0.2 3(fume)(STEL),5(dust), 1(fume) 1, 5(CL), 3.0(STEL)0.2Silicon (Si) 10.0(TD)15(dust), 5(Resp)10Beryllium (Be) 0.002 (TWA) 0.002 (TWA) Titanium (Ti) Oxide Dust 15 (totalparticulate), 5(Resp)10Zirconium 5, 10.0(STEL)5, 10.0(STEL)Zinc (Zn) Fume 2(RESP), 10.0(STEL) (Resp)2(RF), 10.0(STEL)(RF)5, 10.0(STEL),10.0(TD) 5 5Notes: (A)Canada Alberta OLEs –Occupational Health & Safety Code Schedule 1 table 2; (BC)Canada British Columbia OLEs –Occupational Exposure Limits for Chemical Substance, Occupational Health & Safety Regulation 296/97, as amended; (M) Canada Manitoba OLEs – Safety Regulation 217/2006, The workplace Safety and Health Act(MM) Respirable fraction for(M); (O)Canada Ontario OLEs –Control of Exposure to Biological or Chemical Agents; (Q)Canada Alberta OLEs –Ministry of Labor Regulation Respecting the Quality of the Work Environment; (p) Pyrophoric Powder; (CL) Ceiling Limit; (STEL) Short Term Exposure Limit; (IF) Inhalable Fraction; (FD) Fume and Dust; (TD) ;Total Dust; (box) Respirable Dust and/or Fume on Entire Box; (IU) Inhalable Fume; (Resp) Respirable; (RF)Respirable Fraction; (WF) Welding Fume; (DM ) Dust and MistEngineering Controls:Ensure proper ventilation and respiratory protection is used when welding,brazing or processing. Respiratory protection is recommended andinformation may be found regarding the OSHA STANDARDS (29 CRF1910.134), as well as CSA Standards Z94.4, along with many other safetystandards.Personal Protective Equipment:Use proper welding helmet or safety shield, as well as clothing and gloves,as required for job duties. Do not eat or drink while using these productsand wash hands after use.Section 9: Physical and Chemical PropertiesPhysical State:SolidOdour and Appearance:Odourless silver metalOdour Threshold (ppm): Not applicablepH: Not applicableMelting Point:1218°F (658°C)Freezing Point: Not applicableBoiling Point:4521°F (2494°C)Flashpoint:Not applicableUpper Flammable Limit (% by volume):Not applicableLower Flammable Limit (% by volume):Not applicableSection 10: Stability and ReactivityChemical Stability:StablePossible Hazardous Reactions:During welding, brazing and processing: fumes, dust and gas decompositionmay form.Conditions to Avoid:Avoid extreme temperaturesMaterials to Avoid (Incompatibilities):Strong acids; strong bases; strong oxidizers; metal oxides; alcohols;hydrocarbons; halogensConditions of Reactivity:Not applicableHazardous Decomposition By-Products: Not availableHazardous Polymerization:Does not occurSection 11: Toxicological InformationSkin Contact:Arc rays can burn skin; skin cancer has been reported.Skin Absorption: Not applicableEye Contact:Arc rays can injure eyes.Inhalation:Inhalation is the most likely route of exposure; refer to “Effects of AcuteExposure” and “Effects of Chronic Exposure” below.Ingestion:Unlikely due to form of product.Effects of Acute Exposure:Overexposure or inhalation of large amounts of welding fumes may causesymptoms such as metal fume fever, dizziness, nausea, dryness andirritation of your nose, throat or eyes as well as lung disease.Effects of Chronic Exposure:Overexposure or prolonged inhalation of large amounts of welding fumeswith chromium compounds may cause cancer. Other overexposure orprolonged inhalation of large amounts of welding fumes symptoms mayinclude damage to the central nervous system, respiratory system, skin andcould affect organs such as pancreas and liver.Irritancy of Product:Not availableSensitization to Product:Not availableCarcinogenicity:OSHA (29 CFR 1910.1200) lists Nickel and Chromium as possiblecarcinogens, welding fumes as possible carcinogens (2B), and hexavalentchromium as carcinogenic to humans (1) per IARC Monographs. Hexavalentchromium confirmed as human carcinogen (A1) per ACGIH and US NTPReport on CarcinogenReproductive Effects:Not availableRespiratory Sensitization:Not availableToxicological Data:Acute oral (Rat) –Manganese (LD50): 9000 mg/kg; Silicon (LD50): 3160 mg/kg Section 12: Ecological InformationAquatic and Terrestrial Toxicity:Not availablePersistence and Degradability:Not availableBioaccumulative Potential:Not availableSoil Mobility:Not availableSection 13: Disposal ConsiderationsNOTE: Always dispose of waste in accordance with local, provincial and federal regulations.Safe Handling:Gloves can be worn while handling discarded or unwanted product.Methods of Disposal:Recycle when possible. Do not allow to enter drains, sewers orwatercourses. Discard any unwanted product, residues, containers, orliners in a suitable disposal container in an environmentally acceptablemanner, as required by relevant legislation.Section 14: Transportation InformationThis material is not considered as a dangerous good per transportation regulations.Section 15: Regulatory InformationCanadian Controlled ProductsRegulations:This product has been classified according to the hazard criteria of theCanada Controlled Products Regulations, Section 33.California –Permissible ExposureLimits for Chemical Contaminants:Aluminum, Aluminum Oxide, Chromium, Copper, Magnesium, MagnesiumOxide, Manganese, Silicon, Titanium, Vanadium, Iron, Iron Oxide, Zirconium,Zinc, Zinc OxideCalifornia Proposition 65:Hexavalent chromium compounds listed in the following –a Carcinogens &Reproductive Toxic Listed Substance, Carcinogenic Substance 2/27/1987,Developmental Toxin 12/19/2008, Female Reproductive Toxin12/19/2008, Male Reproductive Toxin 12/19/2008Massachusetts – Substance Act: Aluminum, Aluminum Oxide, Chromium, Copper, Magnesium, MagnesiumOxide, Manganese, Silicon, Vanadium, Iron Oxide, Zirconium, Zinc, ZincOxideNew Jersey –Right to Know HazardousSubstance List: Aluminum, Aluminum Oxide, Chromium, Copper, Iron Oxide, HexavalentChromium compounds, Magnesium, Magnesium Oxide, Manganese, Silicon,Titanium, Titanium Oxide, Vanadium, Zinc, Zinc Oxide, Zirconium Pennsylvania – Hazardous SubstanceList: Aluminum, Aluminum oxide, Chromium, Copper, Iron oxide, Hexavalentchromium compounds , Iron oxide, Magnesium, Manganese, Silicon,Welding Fume, Vanadium, Zinc oxide and ZirconiumSection 16: Other InformationDate of Last Revision:19 January 2016Preparation Date:10 July 2015This SDS format is in accordance with GHS. PowerWeld Inc. provides the information contained herein in good faith but makes no representation as to its comprehensiveness or accuracy. This document is intended only as a guide to the appropriate precautionary handling of the material by a properly trained person using this product. Product use and conditions of use are beyond the control of PowerWeld. Warranty of materials is limited to test results of product performance as detailed in certificates of compliance. Interpretation of test results is the responsibility of end-user. No other warranties, expressed or implied, are made.。
Akzo Nobel Coatings Inc. Resicoat R4-ES HJF42R 防腐蚀

Functional Powder CoatingsProduct Datasheet20, Culvert Street T+1 855-294-8934Nashville, TN 37210F+1 615-564-4181USAResicoat ®R4-ESfor Electrostatic Spray Application on Preheated Surfaces Code: HJF42RProduct DescriptionResicoat ® R4 is a high quality thermosetting epoxy powder coating for the corrosion protection of valves and fittings, manufactured from cast iron or steel. The powder coating is available to be applied in one layer on a preheated surface by electrostatic spray application. Typical film thickness achieved is in the range of 250 – 500 µm. The resultant thermoset epoxy has a high mechanical resistance with excellent electrical insulation properties. Drinking water approvals are available to confirm the coatings suitability, as a hygienic and environmental friendly coating. The outstanding adhesion of Resicoat ® R4epoxy powders to the metal substrate provides long term protection of the coated component. It ensures a reliable conservation to the function and value of the parts for the common water and gasdistribution network. The applicator of Resicoat ®R4 benefits from a modern and environmentallyfriendly process. It is possible to overcoat Resicoat ®R4 with polyester powder and liquid coatings to achieve UV protection.Typical valueMethod Powder PropertiesBinder System Epoxy resinDensity1.45 – 1.55 g/cm³ASTM D5965Gel time at 392° F (200° C )25 – 40 sec.ASTM D4217Particle size distribution D10 = 10 – 15 µm D90 = 135 – 160 µm Malvern ISO 8130-1Storage stability 6 months at ≤ 74 °F (23 °C)Safety precautionsSee Material Safety Datasheet (MSDS)Application DataPreheating temperature object 392 – 428 °F (200 – 220 °C) object temperaturePost cure conditions objectThe coating is self curing, if the wall thickness of the steel/cast iron is greater than 8 mm. If the wall thickness of the steel/cast iron is less than 8 mm, additional curing of 3 to 8 minutes at 392 °F (200 °C) object temperature is required.1. Pre-cleaning The surface must be free of oil, grease, salt, and other impurities.2. BlastingMolding sand, rust and sharp edges must be removed with angular steel grit. The graphite from the cast iron must beremoved from the blasting material according NACE No.2/ SSPC-10/Sa 2.5. Recommended anchor profile of ≥60 µm should be stored max. 4 hours before pre-heating (dust-free and dry).3. Pre-heating This form of heating produces a uniform, defined temperature in the component. Any oxidation should be avoided.4. Coating applicationImmediately after preheating, the coating process starts without loosing any object temperature. The coating is done in the shortest possible time in a single pass with no interruptionFunctional Powder Coatings20, Culvert Street T+1 855-294-8934Nashville, TN 37210F+1 615-564-4181USATypical valueMethodCoating Process5. Coating cureCuring is achieved by the heat contained in the object. If the heating capacity of the work piece is sufficient. To confirm fully curing, MIBK is dropped for 30 sec. on the film surface with no visible change.Material PropertiesColorblueRecommended film thickness 10 – 14 mils (250 – 350 µm)Flowsmooth Gloss at 90° angle 70 – 90 units DIN 67530Cross cut test Gt 0DIN EN ISO 2409Impact resistance> 5 Joule > 2.26 Joule > 18 JouleDIN 30677-2ASTM D279420 inchpoundASTM G14 modified1/8 in (3.2 mm) steel plate Abrasion resistance < 40 mg ASTM D4060CS-17, 1000 g, 1000 cycles Dielectric strength≥ 30 kV/mm IEC 60243-1Volume resistivity (DC voltage) 1.1 x 1015ASTM D257Elongation> 5 %DIN 30671Indentation resistance 48 h, 158 °F (70 °C)24 h, 140 °F (60 °C)< 30 %< 10 %DIN 30677-2/DIN EN 14901ASTM G17Compressive strength > 100 MPa ASTM D695Shear adhesion> 35 MPa ASTM D1002Heat aging in air (90 d), water fulfilled DIN EN 14901Thermal stability under heat aging pass AS/NZS 4158:2003Weathering (Xenon test), 100 d pass ASTM D2596-99HardnessF Pencil Strain polarization pass WIS 4-52-01Cathodic disbonding 30 d, 74 °F (23 °C)≤ 10 mm DIN 30677-2, GSK Hot water immersion 90 d, 158 °F (70 °C)pass AWWA C550-05Adhesion> 20 MPa ASTM D4541Adhesion after 7 d,194 °F (90°C)water≥ 16 MPaISO 4624, GSK Tensile strength approx. 500 kg/cm³ASTM D2370Penetration< 5 %ASTM G17Functional Powder Coatings20, Culvert Street T+1 855-294-8934Nashville, TN 37210F+1 615-564-4181USATypical valueMethodMaterial PropertiesDisinfectant resistanceaccording DVGW work sheet W 291(chlorine dioxide, sodium hypochlorite)no change of surface,no chalkingafter 10 test stages à 15 h The following migration test with demineralised water showed no defects of the film. The concentration of the examined parameters in the tested water were below the limits of the epoxy guideline for ancillaries for pipes DN > 300 mm (in main trunks).Water condensation test (Cleveland test), 21 d no changeASTM D4585Salt spray resistance, 2000 h no blistering, no loss of adhesionBS 3900:F4Salt spray test, 4000 hno under-rusting on the cut DIN EN ISO 9227(steel substrate)Water absorption, 100 d, 74 °F (23 °C)pass AS/NZS 3862Chemical resistance (pH 3–13, 23° C)fulfilledEN 598Conformities ·AWWA C116·AWWA C550-05·EN 14901·ISO 12944-2, table 1(standard does not include powder coating systems)It is assumed that Resicoat ® R4 is suitable to meet the high atmospheric corrosivity category C4 (typically in industrial areas and coastal areas with moderate salinity) and the very high atmospheric- corrosivity -categories C5-I (industrial) and C5-M (marine) if applied as a holiday-free coating at a film thickness> 400 µm. A sufficient film thickness is highly required to ensure good edge coverage. For gloss and color stability a UV-resistant polyester topcoat has to be applied.Drinking Water ApprovalsUS: ANSI/NSF 61 Drinking Water System Components – Health Effects, NSF DE: UBA-Coatings Guideline, Approval no.: C-138801-06, Hygiene InstitutDE: DVGW directive work sheet W 270, Approval no. W-211795-11, Hygiene Institut UK: BS 6920, Approval No. 1112500, WRASDate of issue:July 10, 2015Authorized by:GK Revision No.:3Disclaimer: This Product Data Sheet is based on the present state of our knowledge and on current laws. The data referring to Powder Properties, Application Data and Physical Tests is based on lab based samples. Factors such as quality or condition of the substrate may have an effect on the use and application of the product. It remains the responsibility of the user to test thoroughly if the product is applicable for the intended use. The use of the product beyond our recommendation releases us from our responsibility, unless we have recommended the specific use in writing. It is always the responsibility of the user to take all necessary steps to fulfil the demands set out in the local rules and legislation. We are not liable for any application-technological advice. The Product Data Sheet shall be updated from time to time. Please ensure you have the latest version before using the product. All products and Product Data Sheets are subject to our standard terms and conditions of sale (GCS). You can receive the latest copy of GCS via internet or our post address. Brand names mentioned in this Product Data Sheet are trademarks of or are licensed to the AkzoNobel group.Resistance against chemical substances of Resicoat ®R4 at room temperature20, Culvert Street T+1 855-294-8934Nashville, TN 37210F+1 615-564-4181USA Chemical resistanceAugust 01, 2014Page 1 of 3Acetic acid 10 % 2 years no change Ammonia 10 % 2 years no change Ammonia 36 % 1.5 years no change Antifrogen L 50 % 1 year no change Antifrogen N 50 %1 year no change Benzol 1 month no change Bore oil 1 year no change Butanol6 months no change Carbon tetra chloride 1 yearno change Caustic soda solution 10 % 2 years no change Caustic soda solution50 %2 years no change Chlorine cleanser and disinfectant 1.5 years no change Citric acid2 years no change Deicer Safeway KF HOT 1 year no change Deicer Safeway SF (solid) 1 year no change Deicer Safewing MP II 1951 1 yearno change Dichromatic potassium 10 % 1 year no change Diesel2 years no change Engine oil SAE 20 1 year no change Ethanol 1 year no change Ethyleneglycole 1 yearno change Formaldehyde 37 % 6 months no change Formic acid 5 % 2 years no change Formic acid 10 %1.5 years no change Glycerol 1 year no change Glysantin 1 yearno change Hydrochloric acid concentrated1 week no change Hydrochloric acid 10 %2 years no change Hydrochloric acid 25 % 1.5 yearsno change Hydrofluoric acid 1 % 1 day no change Hydrogen peroxide 3 % 1 year no change Hydrogen peroxide10 %1 yearfadedLactic acid10 % 1 week no changeMethanol 1 week no changeMethyl tert-butyl ether (MTBE)100% 6 months softeningNitric acid10 % 1.5 years no changeNitric acid25 % 1 year no changeOxalic acid 5 % 6 months no changePalm oil at 90° C7 days no changePetrol 2 years no changePetroleum 1 year no changePhosphoric acid10 % 2 years no changePhosphoric acid50 % 2 years no changePotassium hydroxide10 % 1 year no changePotassium hydroxide25 % 1 year no changePotassium hydroxide50 % 1 year no changePropanol 1 year no changeSea water 2 years no changeSodium acetate10 % 1 year no changeSodium carbonate20 % 1 year no changeSodium hypochlorite (15 % Cl2)10 weeks no changeSodium chloride 2 % 1 year no changeSodium chloride20 % 1 year no changeSodium formiate10 % 1 year no changeSuds 1 % 1 year no changeSulphuric acid 2 % 2 years no changeSulphuric acid20 % 2 years no changeSulphuric acid50 % 2 years no changeTartaric acid 5 % 1 year no changeToluol 1 year no changeTurpentine oil 1 year no changeUrea10 % 1 year no changeUrine 1 year no changeXylol 1 year no change 20, Culvert Street T+1 855-294-8934Nashville, TN 37210F+1 615-564-4181USA Chemical resistance August 01, 2014Page 2 of 3Our printed literature and technical information Sheets as well as our advisory services are offered to facilitate andsupport decision-making processes. All specifications provided reflect the state of our knowledge at the time of print. Anytechnical data and measured values supplied have been tested for compliance with current applicable standards, ifavailable. The information provided is not legally binding upon the party supplying such information.20, Culvert Street T+1 855-294-8934Nashville, TN 37210F+1 615-564-4181USA Chemical resistance August 01, 2014Page 3 of 3。
SI2302-TP;中文规格书,Datasheet资料

Revision: A
/
3 of 5
2011/01/01
VGS, Gate to Source Voltage (V) ID, Drain Current (A)
VTH, Normalized Gate-Source Threshold Voltage
RDS(ON), Normalized RDS(ON), On-Resistance(Ohms)
IS, Source-drain current (A)
ID, Drain Current (A)
SI2302
10 25 C
Maximum Ratings @ 25OC Unless Otherwise Specified
Symbol VDS ID IDM VGS
PD R©JA
TJ
TSTG
Parameter Drain-source Voltage Drain Current-Continuous Drain Current-Pulsed a Gate-source Voltage
MCC
TM
Micro Commercial Components
5 VDS=10V ID=3.6A
4
3
2
1
0
0
2
4
6
Qg, Total Gate Charge (nC)
Figure 7. Gate Charge
VDD
RL VIN
D
VOUT
VGS
RGEN G
S
Figure 9. Switching Test Circuit
R820T_datasheet

Rafael Micro products are not intended for use in medical, lifesaving or life sustaining applications. Rafael Micro customers using or selling Rafael Micro products for use in such applications do so at their own risk and agree to fully indemnify Rafael Micro for any damages resulting from such improper use or sale. Rafael Micro, logos and R820T are Trademarks of Rafael Microelectronic, Inc. Product names or services listed in this publication are for identification purposes only, and may be trademarks of third parties. Third-party brands and names are the property of their respective owners.
PRELIMINARY VERSION
nly R820T O High Performance Low Power
Advanced Digital TV Silicon Tuner Datasheet
IC datasheet pdf-REF3012,REF3020,REF3025,REF3033,REF3040,REF3030,pdf(50ppm_°C Max, 50μA in SOT23-3

VOLTAGE (V) 1.25 2.048 2.5 3.0 3.3 4.096
DROPOUT VOLTAGE vs LOAD CURRENT 350
IN 1 REF3012 REF3020 REF3025 REF3030 REF3033 REF3040 SOT23-3
300
Dropout Voltage (mV)
REF3012 REF3020 REF3025 REF3030 REF3033 REF3040
SBVS032F – MARCH 2002 – REVISED AUGUST 2008
50ppm/°C Max, 50µA in SOT23-3 CMOS VOLTAGE REFERENCE
"
R30F
"
REF3033
"
SOT23-3
"
DBZ
"
–40°C to +125°C
"
R30D
"
REF3040
"
SOT23-3
"
DBZ
"
–40°C to +125°C
"
R30E
"
"
"
"
"
NOTE: (1) For the most current package and ordering information, see the Package Option Addendum at the end of this document, or see the TI website at .
ELECTRICAL CHARACTERISTICS
Perkadox PF-MT40商品说明书

Product Data SheetPerkadox PF-MT40tert-Butyl monoperoxymaleate, 40% in dibutyl maleatePerkadox® PF-MT40 is a 40% suspension which is used for room temperature curing of acrylic solid surface without yellow discoloration. It is used in combination with Accelerator CTAS for room temperature cure.CAS number1931-62-0EINECS/ELINCS No.217-691-1TSCA statuslisted on inventoryMolecular weight188.2Active oxygen contentperoxide8.5%Concentration3.23-3.57%SpecificationsAppearance PasteAssay38.0 - 42.0 %CharacteristicsDensity, 25 °C0.850 g/cm³Viscosity, 25 °C25000-50000 mPa.sApplicationsPerkadox® PF-MT40 can be used as for the ambient temperature curing of MMA resins. Without the addition of an accelerator, the cure of the acrylate resin starts only above the activation temperature of 90°C. For the cure at ambient temperature, Perkadox® PF-MT40 must be accelerated with a combination of special accelerators. Together with the Accelerators R-913 and Ca(OH)2, a reasonable geltime is obtained with a fast cure at ambient temperatures. The most important advantage of a cure system based on Perkadox® PF-MT 40 is the absence of yellow discoloration and a lower residual monomer content compared to results obtained with a BPO/amine curing system.Thermal stabilityOrganic peroxides are thermally unstable substances, which may undergo self-accelerating decomposition. The lowest temperature at which self-accelerating decomposition of a substance in the original packaging may occur is the Self-Accelerating Decomposition Temperature (SADT). The SADT is determined on the basis of the Heat Accumulation Storage Test.SADT50°C (122°F)Method The Heat Accumulation Storage Test is a recognized test method for thedetermination of the SADT of organic peroxides (see Recommendations on theTransport of Dangerous Goods, Manual of Tests and Criteria - United Nations, NewYork and Geneva).StorageDue to the relatively unstable nature of organic peroxides a loss of quality can be detected over a period of time. To minimize the loss of quality, Nouryon recommends a maximum storage temperature (Ts max. ) for each organic peroxide product.Ts Max.25°C (77°F)Note When stored under the recommended storage conditions, Perkadox® PF-MT40will remain within the Nouryon specifications for a period of at least 3 months afterdelivery.Packaging and transportIn North America Perkadox® PF-MT40 is packed in non-returnable, 5 gallon polyethylene containers of 39.7 lb net weight. In other regions the standard packaging is plastic pails for 14 kg peroxide. Both packaging and transport meet the international regulations. For the availability of other packed quantities contact your Nouryon representative.Perkadox®PF-MT40 is classified as Organic peroxide type E; solid, Division 5.2; UN 3108; PG I.Safety and handlingKeep containers tightly closed. Store and handle Perkadox® PF-MT40 in a dry well-ventilated place away from sources of heat or ignition and direct sunlight. Never weigh out in the storage room.Avoid contact with reducing agents (e.g. amines), acids, alkalis and heavy metal compounds (e.g. accelerators, driers and metal soaps). Please refer to the Safety Data Sheet (SDS) for further information on the safe storage, use and handling of Perkadox® PF-MT40. This information should be thoroughly reviewed prior to acceptance of this product.The SDS is available at /sds-search.All information concerning this product and/or suggestions for handling and use contained herein are offered in good faith and are believed to be reliable.Nouryon, however, makes no warranty as to accuracy and/or sufficiency of such information and/or suggestions, as to the product's merchantability or fitness for any particular purpose, or that any suggested use will not infringe any patent. Nouryon does not accept any liability whatsoever arising out of the use of or reliance on this information, or out of the use or the performance of the product. Nothing contained herein shall be construed as granting or extending any license under any patent. Customer must determine for himself, by preliminary tests or otherwise, the suitability of this product for his purposes.The information contained herein supersedes all previously issued information on the subject matter covered. The customer may forward, distribute, and/or photocopy this document only if unaltered and complete, including all of its headers and footers, and should refrain from any unauthorized use. Don’t copythis document to a website.Perkadox® is a registered trademark of Nouryon Functional Chemicals B.V. or affiliates in one or more territories.Contact UsPolymer Specialties Americas************************Polymer Specialties Europe, Middle East, India and Africa*************************Polymer Specialties Asia Pacific************************2022-6-30© 2022Thermoset composites Perkadox PF-MT40。
CRW2040资料

Power Chip Resistors Type: CRWSizes: 1210, 1216, 2010, 2040, 2512, 4020Features:• Chip Resistors in Thickfilm• Contact areas Nickel-barrier/ tinned• RF – versions with air-abrasive trimming • Improved pulse power rating untrimmedDimensions:L = Length. B = Width. D = Thickness. C = Width of wrap around (in mm)Packaging:Bulk in plastic bags or tubes – minimum quantity 100 pieces per value Blistertape acc. to IEC 60286-3 – minimum 1000 pieces per value Reel diameter 180 mm or 330 mmOrdering Data:Type – value – tolerance – TCR – packagingExample: CRW 1216 100 R ± 1 % TK50 Tape 180 mmIf no requirements for TCR and taping are given, the standard value (highest value in table) will be supplied and packaging is bulkSizes LB DC 1210 3.2 +0.2/-0.052.5 +0.2/-0.05 0.5 +0.2/-0.1 0.8 ±0.2 12163.2 +0.2/-0.054.1 +0.2/-0.05 0.5 +0.2/-0.1 0.8 ±0.2 20105.1+0.2/-0.052.5+0.2/-0.050.6+0.2/-0.11.2±0.22040 5.1 +0.2/-0.05 10.2 +0.2/-0.05 0.6 +0.2/-0.1 1.2 ±0.2 25126.3 +0.2/-0.053.50 +0.2/-0.05 0.6 +0.2/-0.1 0.9 ±0.2 4020 10.2+0.25.1 +0.20.6 +0.2/-0.10.9 ±0.2Willow Technologies Ltd. Shawlands Court, Newchapel Road, Lingfield, Surrey, RH7 6BL, United Kingdom Tel . + 44 (0) 1342 835234 Fax. + 44 (0) 1342 834306 E-Mail.sales@ Web. Power Chip Resistors Type: CRWSizes: 1210, 1216, 2010, 2040, 2512, 4020Technical data – depending on size:Size12101216201020402512 (M) 4020 (M)Power rating P 70 (W)1) (P 155 = 0 W)0.35 0.5 0.5 0.9 0.6 0.9Working voltage U_. U eff (V) trimmeduntrimmed (Tol. > 5%) 200 600200 600250 900250 900300 (1000) 1200 (2000)500 (4000)1500 (6000)Ranges / Tolerances / TCR 2) / VCROR1 – 1R TC250 5/10/20% TC250 5/10/20% TC250 5/10/20% TC250 5/10/20% TC250 5/10/20% TC250 5/10/20% 1R – < 100R TC100/250 1/…/20% TC100/250 1/…/20% TC100/250 1/…/20% TC100/250 1/…/20% TC100/250 1/…/20% TC100/250 1/…/20% 100R – 100MTC50/100 1/ (20)TC50/100 1/ (20)TC50/100 1/ (20)TC50/100 1/ (20)TC50/100 0.5/ (20)TC50/100 0.5/ (20)1)Load acc. To DIN 45921 on PCB. limited by temperature of solder area (competitor data often too high) With suitable heat dissipation higher power rating is possible. Diagrams for over temperatures available on request.2)TC/50: Temperature range + 25°C...+ 125°CZero-Ohm-Jumper: :< 50 mOhm. TCR max. + 4000M at 2512/4020: Meander structure with higher working voltage in bracket.Higher power dissipation, other sizes and specifications on request.Technical data – general:Temperature range-55°C ... +155°C Climatic category acc. to IEC 6006855/155/56 Solderability acc IEC 60068 T2-20. Ta Meth. 1235°C 2 s Max. soldering temperature acc. IEC 60068 T2-20 Tb M. 1A 260°C 10 sLong term stability 10R – 100M <10R Storage 125°C/1000h <0.5% <1% Storage 155°C/1000h <1% <2% Load P 70/70°C/1000h <1% <2%Short term overload <0.25% <0.5% Damp heat (56d/40°C/96%)<0.5%<1%Data not specified according CECC 40401-802Issue 09/04Willow Technologies Ltd. Shawlands Court, Newchapel Road, Lingfield, Surrey, RH7 6BL, United Kingdom Tel . + 44 (0) 1342 835234 Fax. + 44 (0) 1342 834306 E-Mail.sales@ Web. 。
MAKROLON 2405、2407和2456聚碳酸酯机械胶种介绍说明书

MAKROLON® 2405,2407 and 2456Polycarbonate Resins2405 High-Productivity Grade with release2407 High-Productivity, UV-Stabilized Grade with release2456 High-Productivity, FDA-Food Contact Quality Grade with releaseProduct InformationDescriptionMakrolon 2405, 2407, and 2456 polycarbonate resins are linear, low-viscosity, high-performance thermo-plastics produced in pellet form for processing primarily by injection molding. A unique technology enables these polycarbonates to maintain mechanical properties similar to lower-melt-flow grades of polycarbonate, while offering improved flowability for increased design flexibility. Makrolon 2407 resin is UV stabilized.All resins contain an internal mold release additive. They are available in natural, clear tints, select transparent, translucent, opaque colors and special effects.By broadening the processing window, Makrolon 2405, 2407, and 2456 resins are designed to permit faster cycling and higher productivity. Based upon tests conducted at Bayer laboratories, a processing comparison of Makrolon 2405 polycarbonate resin with production runs of standard polycarbonate has demonstrated increases in production rates in excess of 15%. Actual test results may vary, depending on the application and processing conditions. In addition, the increased productivity reduces energy consumption on a unit part basis. These benefits are the result of low melt viscosity and ease of part ejection. The low viscosity is of particular interest in applications where thin walls exist or the flow length-to-wall thickness is high. Ease of processing at lower temperatures translates to faster cycles, as parts may be produced at lower mold-set-point temperatures and ejected after shorter cooling times. Although applicable to existing tools, new tool design can take advantage of the low melt viscosity of these grades. Thinner runners and distribution systems can be employed to minimize regrind and reduce cycle time. Wall sections in the part can be reduced to conserve materials and contribute faster cycling. Although small parts offer some of the more attractive benefits of increased productivity, these grades are also candidates for applications involving large injection molded parts. In both large and small part molding, the same processing allowances exist. Lower melt temperatures and easy release permit demolding with less time necessary for stabilizingthe part.Makrolon 2456 resin complies with FDA food contact regulations 21 CFR 177.1580 (Polycarbonate Resins) and may be used in contact with all food types. Most colors may be used for all thermal food contact applications. However, some colors are limited by conditions of Use B through H, 21 CFR 175.300 and 176.170 and may not be used when the food is sterilized in the food contact article under autoclaving conditions. Please contact your Bayer MaterialScience representative with complete details when food contact is involved.Makrolon 2456 resin, in natural 000000 and clear tints 550042 and 550115, is also listed under NSF standard 51 for use in food equipment. Please consult your Bayer MaterialScience representative for more information about food equipment applications.ApplicationsMakrolon 2405, 2407, and 2456 resins are utilized over a wide range of applications in a variety of market areas. Typical applications include automotive light pipes, clear windows for business machines and instruments, and numerous consumer applications where multicavity tooling is used.As with any product, use of Makrolon 2405, 2407, and 2456 resin in a given application must be tested (including but not limited to field testing) in advance by the user to determine suitability. The suitability of aPage 1 of 4 — Document contains important information and must be read in its entirety.Bayer product in a given end-use environment is dependent upon various conditions including, without limitation, chemical compatibility, temperature, part design, residual stresses, and external loads. It is the responsibility of the Manufacturer to evaluate its final product under actual end-use requirements and to adequately advise and warn purchasers and users thereof. Dr yingAll polycarbonate resins are hygroscopic and must be thoroughly dried prior to processing. A desiccant dehumidifying hopper dryer is recommended. To achieve a moisture content of less than 0.02%, hopper inlet air temperature should be 250°F (121°C) and inlet air dew point should be -20°F (-29°C) or lower. The hopper capacity should be sufficient to provide a minimum residence time of 4 hours. Additional information on drying procedures is available in the Bayer brochure General Drying Guide.Pr ocessingMakrolon 2405, 2407, and 2456 resins may be easily processed on commercially available molding equipment suitable for injection molding of polycarbonate. Barrel temperatures may be reduced by up to 45°F (25°C) below normal processing conditions for standard polycarbonate due to ease of cavity fill. Lower viscosity also means that lower primary and secondary injection pressures may be used and that molded-in stresses should be lower. A lower melt temperature permits the use of shorter hold and cure times. The shorter molding cycle is complemented by ease of part ejection at high part temperatures.Typical processing parameters are noted below. Actual processing conditions will depend on machine size, mold design, material residence time, shot size, etc.Typical Injection Molding ConditionsBarrel Temperatures:Rear .............................................. 445˚–495˚F (229˚–257˚C)Middle ........................................... 510˚–550˚F (266˚–288˚C)Front .............................................. 530˚–570˚F (277˚–299˚C)Nozzle ..............................................510˚–530˚F (266˚–277˚C) Melt T emperature .............................. 535˚–565˚F (279˚–296˚C) Mold T emperature ...............................150˚–220˚F (66˚–104˚C) Injection Pressure ......................................... 10,000–20,000 psi Hold Pressure .................................. 50–70% of Injection Pressure Shot Size .......................................... 25–75% of Barrel Capacity Back Pressure ........................................................... 50–100 psi Screw Speed ............................................................. 50–75 rpm Injection Speed ................................................ Moderate to Fast Cushion ........................................................................ 1/8–1/4 in Clamp ........................................................................... 3–5 ton/in2Additional information on processing may be obtained by consulting the Bayer publication Makrolon Polycarbonate — A Processing Guide for Injection Molding and by contacting a Bayer MaterialScience technical service representative.Regrind Infor mationWhere end-use requirements permit, up to 20% Makrolon resin regrind may be used with virgin material, provided that the material is kept free of contamination and is properly dried (see section on Drying). Any regrind used must be generated from properly molded parts, sprues, and/or runners. All regrind used must be clean, uncontaminated, and thoroughly blended with virgin resin prior to drying and processing. Under no circumstances should degraded, discolored, or contaminated material be used for regrind. Materials of this type should be properly discarded.Improperly mixed and/or dried regrind may diminish the desired properties of Makrolon resin. It is critical that you test finished parts produced with any amount of regrind to ensure that your end-use performance requirements are fully met. Regulatory or testing organizations (e.g., UL) may have specific requirements limiting the allowable amount of regrind. Because third party regrind generally does not have a traceable heat history or offer any assurance that proper temperatures, conditions, and/or materials were used in processing, extreme caution must be exercised in buying and using regrind from third parties. Third party regrind must not be used in end-uses that are to comply with FDA's food-contact regulations.The use of regrind material should be avoided entirely in those applications where resin properties equivalent to virgin material are required, including but not limited to color quality, impact strength, resin purity, and/or load-bearing performance.Page 2 of 4 — Document contains important information and must be read in its entirety.ASTM Makrolon® 2405/2407/2456 Typical Properties* Test Method Resinsfor Natural Resin (Other) U.S. Conventional SI Metric GeneralSpecific Gravity D 792 1.20Density D 792 0.043 lb/in3 1.20 g/cm3 Specific Volume D 792 23.1 in3/lb 0.83 cm3/g Mold Shrinkage D 955 0.005–0.007 in/in 0.005–0.007 mm/mm Water Absorption, Immersion at 73˚F (23˚C): D 57024 Hours 0.12%Equilibrium 0.30%Melt Flow Rate a at 300˚C/1.2-kg Load D 1238 20 g/10 minOpticalT ransmittance at 0.125-in (3.2-mm) Thickness D 1003 88%Haze at 0.125-in (3.2-mm) Thickness D 1003 <0.8%Refractive Index D 542 1.586Mechanical bT ensile Stress at Yield D 638 9,400 lb/in2 65 MPaT ensile Stress at Break D 638 8,700 lb/in2 60 MPaT ensile Elongation at Yield D 638 6%T ensile Elongation at Break D 638 115%T ensile Modulus (1 mm/min) D 638 350,000 lb/in2 2.4 GPa Flexural Stress at 5% Strain D 790 12,000 lb/in2 83 MPa Flexural Modulus D 790 340,000 lb/in2 2.4 GPa Compressive Stress at Yield D 695 11,000 lb/in2 76 MPa Impact Strength, Notched Izod: D 25673˚F (23˚C)0.125-in (3.2-mm) Thickness 14 ft•lb/in 750 J/mT ensile Impact Strength, “S” Specimen: D 18220.125-in (3.2-mm) Thickness 250 ft•lb/in2 525 kJ/m2 Rockwell Hardness: D 785M Scale 75R Scale 120ThermalDeflection T emperature, Unannealed: D 6480.250-in (6.4-mm) Thickness264-psi (1.82-MPa) Load 259˚F 126˚C66-psi (0.46-MPa) Load 273˚F 134˚C Coefficient of Linear Thermal Expansion D 696 3.34 E-05 in/in/˚F 6.0 E-05 mm/mm/˚C Thermal Conductivity C 177 1.39 Btu•in/(h•ft2•˚F) 0.20 W/(m•K) Specific Heat D 2766 0.28 Btu/(lb•˚F) 1,172 J/(kg•K) Relative Temperature Index: (UL746B)0.059-in (1.5-mm) ThicknessElectrical 125˚CMechanical with Impact 115˚CMechanical without Impact 125˚CVicat Softening Temperature, 50N, 50°C/h D 1525 291˚F 144˚CFlammability**Oxygen Index D 2863 28%UL94 Flame Class:(UL94)0.75-mm (0.030-in) Thickness V-2 Rating1.5-mm (0.059-in) Thickness V-2 Rating2.7-mm (0.106-in) Thickness HB Rating3.0-mm (0.118-in) Thickness HB RatingWeatherabilityUV Light Exposure and Hot Water Immersion T ests (UL746C)Makrolon 2407 and 2458 resins f1 ratingElectricalVolume Resistivity (Tinfoil Electrodes) D 257 1.0 E+16 ohm•cmSurface Resistivity D 257 1.0 E+16 ohmDielectric Strength (Short Time Under Oil D 149at 1-mm [0.04-in] and 73˚F [23˚C]) 810 V/mil 32 kV/mm Dielectric Constant (Tinfoil Electrodes): 60 Hz D 150 3.01 MHz 2.9Dissipation Factor (Tinfoil Electrodes): 60 Hz D 150 0.00081 MHz 0.01Arc Resistance: Stainless Steel Electrodes D 495 11 sT ungsten Electrodes 120 s*These items are provided as general information only.T hey are approximate values and are not part of the product specifications. T ype and quantity of pigments or additives used to obtain opaque colors and special effects can affect material properties.**Flammability results are based on small-scale laboratory tests for purposes of relative comparison and are not intended to reflect the hazards presented by this or any other material under actual fire conditions.a For information on using melt flow as a quality control procedure, see the Bayer publication Makrolon Polycarbonate — A Processing Guide for Injection Molding.b T ype and quantity of pigment used in opaque colors can affect mechanical properties, especially toughness.Page 3 of 4 — Document contains important information and must be read in its entirety.General Characteristics of Polycarbonate Hydrolytic Stability. Parts molded from polycarbonate absorb only 0.15 to 0.19% water at room temperature and 50% relative humidity. Dimensional stability and mechanical properties remain virtually unaffected. Even with immersion in water, dimensional changes measure only about 0.5%. Although frequent, intermittent contact with hot water does not harm polycarbonate, continuous exposure to humidity or water at high temperatures(>140°F/60°C) is not recommended due to hydrolytic degradation, which reduces impact strength and tensile properties.Gas Permeability. Steam permeability, measured on 100-µm thick film, is 15 g/m2.24 h (0.97 g/100 in2.24 h). Significant permeability also exists for other gases, such as hydrogen, carbon dioxide, sulfur dioxide, helium, ethylene oxide, and oxygen.Chemical Resistance. Polycarbonate is resistant to mineral acids (even in high concentrations), a large number of organic acids, many oxidizing and reducing agents, neutral and acidic saline solutions, some greases and oils, saturated aliphatic and cycloaliphatic hydrocarbons, and most alcohols. It is important to note that polycarbonate is degraded by alkaline solutions, ammonia gas and its solutions, and amines. Polycarbonate dissolves in a number of organic solvents, such as halogenated hydrocarbons andsome aromatic hydrocarbons. Other organic compounds cause polycarbonate to swell or stress-crack, e.g., acetone and methyl ethyl ketone. Since chemical resistance to various media is dependent on variables, such as concentration, time, temperature, part design, and residual stresses, the above information should serve only as a guideline. It is imperative that production parts be evaluated under actual application conditions prior to commercial use.Regulatory Compliance InformationSome of the end uses of the products described in this bulletin must comply with applicable regulations, such as FDA, NSF, USDA, and CPSC. If you have any questions on the regulatory status of these products, contact your Bayer MaterialScience representative or Bayer’s Regulatory Affairs Manager in Pittsburgh, PA. Health and Safety Information Appropriate literature has been assembled which provides information concerning the health and safety precautions that must be observed when handling the Makrolon resins described in this bulletin. Before working with these products,you must read and become familiar with the available information on their hazards, proper use, and handling. This cannot be overemphasized. Information is available in several forms, e.g., material safety data sheets and product labels. Consult your Bayer MaterialScience representative or contact Bayer’s Product Safety and Regulatory Affairs Department in Pittsburgh, PA.Note: The information contained in this bulletin is current as of September 2007. Please contactBayer MaterialScience to determine whether this publication has been revised.Bayer MaterialScience LLC100 Bayer Road • Pittsburgh, PA 15205-9741 • Phone: 1-800-662-2927 • The manner in which you use and the purpose to which you put and utilize our products, technical assistance and information (whether verbal, written or by way of production evaluations), including any suggested formulations and recommendations are beyond our control. Therefore, it is imperative that you test our products, technical assistance and information to determine to your own satisfaction whether they are suitable for your intended uses and applications. This application-specific analysis must at least include testing to determine suitability from a technical as well as health, safety, and environmental standpoint. Such testing has not necessarily been done by us. Unless we otherwise agree in writing, all products are sold strictly pursuant to the terms of our standard conditions of sale. All information and technical assistance is given without warranty or guarantee and is subject to change without notice. It is expressly understood and agreed that you assume and hereby expressly release us from all liability, in tort, contract or otherwise, incurred in connection with the use of our products, technical assistance, and information. Any statement or recommendation not contained herein is unauthorized and shall not bind us. Nothing herein shall be construed as a recommendation to use any product in conflict with patents covering any material or its use. No license is implied or in fact granted under the claims of any patent.2401 Walton Boulevard, Auburn Hills, MI 48326-1957 • Phone: 1-248-475-7700 • Fax: 1-248-475-770120509 9/07 V3c Page 4 of 4 — Document contains important information and must be read in its entirety.。
- 1、下载文档前请自行甄别文档内容的完整性,平台不提供额外的编辑、内容补充、找答案等附加服务。
- 2、"仅部分预览"的文档,不可在线预览部分如存在完整性等问题,可反馈申请退款(可完整预览的文档不适用该条件!)。
- 3、如文档侵犯您的权益,请联系客服反馈,我们会尽快为您处理(人工客服工作时间:9:00-18:30)。
分销商库存信息:
RIEDON CRW2040 43K 5% 100PPM
Long Term Stability
Storage 125°C / 1000h Storage 155°C / 1000h Load Life / P=70% / 70°C / 1000h Short term overload Humidity / 96%RH / 40°C / 56 days
Max DR <10W
1W - <100 @ 155 °C
( Note: Solder pads must be of sufficient size to dissipate power )
2 3
(M) Meander structure with higher working voltage. 50 PPM : +25°C to +125°C
Riedon Inc. 1.01
/
0
25
50
75
100
125
150
175
Ambient Temperature (°C)
300 Cypress Avenue
Alhambra CA 91801 (626) 284-9901 (626) 284-1704 Page 17
±1% ±2% ±2% ±0.5% ±1%
10W - 100M
±0.5% ±1% ±1% ±0.25% ±0.5%
Type CRW 1210 CRW 1216 CRW 2010 CRW 2040 CRW 2512 CRW 4020
Dimensions L
0.126 +0.008 / -0.002 [ 3.2 +0.2 / -0.05 ] 0.126 +0.008 / -0.002 [ 3.2 +0.2 / -0.05 ] 0.200 +0.008 / -0.002 [ 5.1 +0.2 / -0.05 ] 0.200 +0.008 / -0.002 [ 5.1 +0.2 / -0.05 ] 0.250 +0.006 / -0.002 [ 6.3 +0.15 / -0.05 ] 0.400 +0.006 / -0.002 [ 10.2 +0.15 / -0.05 ]
B
0.098 +0.008 / -0.002 [ 2.5 +0.2 / -0.05 ] 0.160 +0.008 / -0.002 [ 4.1 +0.2 / -0.05 ] 0.098 +0.008 / -0.002 [ 2.5 +0.2 / -0.05 ] 0.400 +0.008 / -0.002 [ 10.2 +0.2 / -0.05 ] 0.138 +0.008 / -0.002 [ 3.5 +0.2 / -0.05 ] 0.200 +0.008 / -0.002 [ 5.1 +0.2 / -0.05 ]
/
300 Cypress Avenue
Alhambra CA 91801 (626) 284-9901 (626) 284-1704 Page 16
CRW Series
Power Chip Resistors
SPECIFICATIONS (continued)
1
0.1W - <1W
5% to 20% 250 1% to 20% 100 / 250 1% to 20% 50 / 100
5% to 20% 250 1% to 20% 100 / 250 0.5% to 20% 50 / 100
5% to 20% 250 1% to 20% 100 / 250 0.5% to 20% 50 / 100
SPECIFICATIONS
Type Power Rating ( W )1 Working Voltage ( VAC )
Trimmed Untrimmed
1210 0.35 200 600
1216 0.5 200 600
2010 0.75 250 900
2040 2.0 250 900
2512 (M) 2 1.5 300 (1000) 1200 (2000)
CRW Series
Power Chip Resistors
• • • • • • •
Resistances from 0.1Ohm to 100MOhms Power Rating 0.35 to 2Watts Resistance Tolerances to ± 0.5% TCR’s to ± 50ppm/K Improved Pulse Rating on Un-trimmed parts Thick Film Resistance Element Sizes: 1210 / 1216 / 2010 / 2040 / 2512 / 4020
Specification
Temperature Range Climactic Cetegory Solderability Max. Soldering Temperature
Value
-55°C to +155°C 55 / 155 / 56 250°C / 3s 260°C / 10s
Riedon Inc. 1.01
D
0.020 +0.008 / -0.004 [ 0.5 +0.2 / -0.1 ] 0.020 +0.008 / -0.004 [ 0.5 +0.2 / -0.1 ] 0.024 +0.008 / -0.004 [ 0.6 +0.2 / -0.1 ] 0.024 +0.008 / -0.004 [ 0.6 +0.2 / -0.1 ] 0.024 +0.006 / -0.002 [ 0.6 +0.15 / -0.05 ] 0.024 +0.006 / -0.002 [ 0.6 +0.15 / -0.05 ]
C
0.032 ±0.008 [ 0.8 ±0.2 ] 0.032 ±0.008 [ 0.8 ±0.2 ] 0.047 ±0.008 [ 1.2 ±0.2 ] 0.047 ±0.008 [ 1.2 ±0.2 ] 0.035 ±0.008 [ 0.9 ±0.2 ] 0.035 ±0.008 [ 0.9 ±0.2 ]
Ordering Information
Part Number - Resistance - Tolerance - TCR - Packaging Example: CRW 2040 50 Ohm 5% 100ppm Tape ( Note: if no TCR is specified, the highest value will be supplied )
Packaging: Bulk or Blistertape to IEC 60286-3
Power ( % )
Power Derating Curve
120 100 80 60 40 20 0
Tape width 8mm / Reel Diameter 180 or 330mm Minimum quantity Bulk / 100 pieces per value Minimum quantity Tape & Reel / 1000 pieces per value
4020 (M) 2 2.0 500 (4000) 1500 (6000)
Resistance Range (W) 5% to 20% 250 1% to 20% 100 / 250 1% to 20% 50 / 100
Tolerances Available ( % ) Temperature Coefficients Available ( ± ppm/K ) 3 5% to 20% 250 1% to 20% 100 / 250 1% to 20% 50 / 100 5% to 20% 250 1% to 20% 100 / 250 1% to 20% 50 / 100