模具生产工序
冲压模具的基本工艺

压的基本工序:1.冲裁:包括落料和冲孔两个工序。
1)落料:模具沿封闭线冲切板料,冲下的部分为工件,其余部分为废料,设计时尺寸以模仁为准,间隙取在冲子上;2)冲孔:模具沿封闭线冲切板料,冲下的部分是废料,设计时尺寸以冲子为准,间隙取在模仁上。
2.剪切:用模具切断板材,切段线不封闭.3.切口:在坯料上将板材部分切开,切口部分发生弯曲.4.切边:将拉深或成形后的半成品边缘部分的多余材料切掉。
5.剖切:将半成品切开成两个或几个工件,常用于成双冲压。
切口切边剖切6.弯曲:用模具使材料弯曲成一定形状(V型/U型/Z型弯曲)。
7.卷圆:将板料端部卷圆。
8.扭曲:将平板的一部分相对于一部分扭转一个角度。
弯曲卷圆扭曲9.拉深:将板料压制成空心工件,壁厚基本不变。
10.变薄拉深:用减小直径与壁厚,增加工件高度的方法来改变空心件的尺寸,得到要求的底厚,壁薄的工件。
11.孔的翻边:将板料或工件上有孔的边缘翻成竖立边缘。
拉深变薄拉深孔的翻边12.外缘翻边:将工件的外缘翻起圆弧或曲线状的竖立边缘。
13.缩口:将空心件的口部缩小。
14.扩口:将空心件的口部扩大,常用于管子。
外缘翻边缩口扩口15.起伏:在板料或工件上压出筋条,花纹或文字,在起伏处的整个厚度上都有变薄。
16.卷边:将空心件的边缘卷成一定的形状。
17.胀形:将空心件(或管料)的一部分沿径向扩张,呈凸肚形。
起伏卷边胀形18.旋压:利用赶棒或滚轮将板料毛坯赶压成一定形状(分变薄与不变薄两种)。
19.整形:把形状不太准确的工件校正成形。
20.校平:将毛坯或工件不平的面或弯曲予以压平。
旋压整形校平21.压印:改变工件厚度,在表面上压出文字或花纹。
22.正挤压:凹模腔内的金属毛坯在凸模压力的作用下,处于塑性变形状态,使其由凹模孔挤出,金属流动的方向与凸模运动方向相同。
23.反挤压:金属挤压过程中,沿凸模与凹模的间隙塑流,其流动方向与凸模运动方向相反。
24.复合挤压:正挤与反挤的结合。
生产开模流程详细步骤
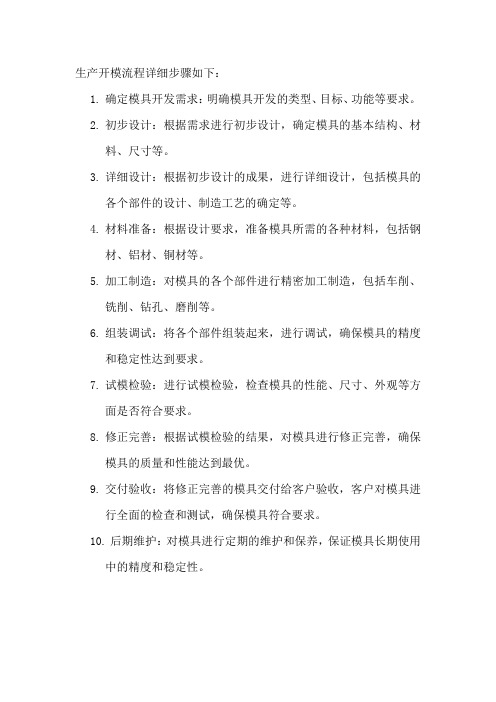
生产开模流程详细步骤如下:
1.确定模具开发需求:明确模具开发的类型、目标、功能等要求。
2.初步设计:根据需求进行初步设计,确定模具的基本结构、材
料、尺寸等。
3.详细设计:根据初步设计的成果,进行详细设计,包括模具的
各个部件的设计、制造工艺的确定等。
4.材料准备:根据设计要求,准备模具所需的各种材料,包括钢
材、铝材、铜材等。
5.加工制造:对模具的各个部件进行精密加工制造,包括车削、
铣削、钻孔、磨削等。
6.组装调试:将各个部件组装起来,进行调试,确保模具的精度
和稳定性达到要求。
7.试模检验:进行试模检验,检查模具的性能、尺寸、外观等方
面是否符合要求。
8.修正完善:根据试模检验的结果,对模具进行修正完善,确保
模具的质量和性能达到最优。
9.交付验收:将修正完善的模具交付给客户验收,客户对模具进
行全面的检查和测试,确保模具符合要求。
10.后期维护:对模具进行定期的维护和保养,保证模具长期使用
中的精度和稳定性。
模具生产加工工艺排程

欢迎阅读• 1.了解产品形状外观面、外观尺寸、组配尺寸、产品拆模大体结构。
• 2. 备料:按备料单尺寸备料 ,根据加工现场加工,情况选择毛••反面,侧壁留余量0.3MM/S,底面留0.3MM (如图二) b.工件完成自检后送质控检测开粗情况。
• 5.热处理:a.工件检测OK 后送钳工攻牙,并确认热处理前加工完后,登记发热处理加工,母模仁一般情况下要求材质:420, 硬度HRC48±1°; b.工件热处理回厂后送质控检测硬度,变形。
• 6.研磨:工件四面分中底面研磨0.3MM,见光加工至图面尺寸,公差±0.01mm(如图一),工件完成后送质控质检。
•C精加工:a. 按图面尺寸四面分中抓底面精加工(如图三)。
b. 型腔部分底部精到字体最高面,抛光后加工下一工序,以便保证字体美观。
四个定位加工时,单边过切0.015mm, 以防公母模仁擦破撑住(如图三),底部定位槽需用定位块实配加工。
C.工件加工完成后自检OK,送质控检测•8.线割:工件四面分中抓底面按图面尺寸加工入子孔进胶孔,入子孔公差为异形孔用入子实配加工完成後送质检检测.•检查模仁口部有无撞坏圆角,电极有无变形等情况•10.抛光:加工人员对照产品外观要求及钳工交接事项,要求顺产品脱模方向抛光加工,保证其工件无圆角无变形• 1.备料 : 按备料单尺寸备料,根据加工现场加工情况选择毛料或精料,毛料余量2-3MM/S,精料余量0.3MM/S .• 2.铣床: a.按备料尺寸加工六面体,留热处理余量0.3MM/S; b. 四面分中抓底抬高0.3MM,加工水孔,螺丝孔,顶针穿一•0.3MM/S,4)•b.HRC±1度,热处理完成回厂後质控检测工件变形度,硬度情况.• 5.研磨:工件四面分中,底面研磨0.3MM,加工至图面尺寸公差±0.01,(如图一), 工件完成後送质控检测.• 6.线割:按图面尺寸四面分中,抓底面加工顶针孔,入子孔,斜销孔公差为顶针孔 ,丝筒孔一般为±0加2. 如有异形入子孔需用入子实配加工,工件完成送质控检测•7. CNC精加工:a. 按图面尺寸四面分中抓底面精加工正反面,(如图三). b. 形腔顶面CNC加工至字体最高面,胶片部分整体预留0.1MM余量,配入子斜销一起加工外观面,PL面CNC尽量做到数或补一精工电极,四个定位台到位,反面定位槽用定位块实配加工,斜销孔;•,•••• 3.放电:先单独放电加工牛角形状尺寸,再配入模仁整体电极放电加工,以便保证外观面美观,一致.注:制作中牛角进胶标准(如图五) • 4.抛光:牛角状流道顺利脱模• 1.按图面尺寸加工斜销最大外形尺寸,顶面留0.05MM,以便配入公仁放电加工,顶面火花纹外观.• 2.按图面尺寸研磨加工直角形状及外形台阶磨线头(如图六) • 3.放电按图面加工胶位部分,加工完成後送质控• 4.抛光:按钳工交接顺脱方向加工作业.••(• C粗:工件四面分中(图一),抓底面抬刀0.3MM(图二),作为工件底面零位置面,按程式粗加工,加工完成後送质控检测.• 4.热处理:工件经钳工攻牙并确认热处理前加工完成後送热处理.材质:420,硬度HRC±1度,热处理完成後送质控检测硬度,变形.• 5.研磨:工件六面分中研磨加工到图面尺寸(图一),公差:±0.01MM,加工完成後送质控检测.• C精:工件四面分中(图一),抓底面为零位对刀(图三),按程•7.线割:工件四面分中(图一),按图加工入子孔,进胶孔,入子孔加工爲,加工完成後送质控检测.(非精密模具入子孔公差可单边0.02mm)•,••定质控检测.• C粗:工件四面分中(图一),抓底面抬刀0.3MM,为工件底面0位,按程式粗加工,粗加工完成後送质控检测.• 4.热处理:工件经钳工攻牙并确认热处理前加工完成後送热处理:材质:SKD61,硬度:HRC48±1度,加工完成後送质控检测硬度,变形. • 5.工件六面分中研磨到图面尺寸(图一),公差:±0.01,加工完成後送质控检测•表•7.线割:工件四面分中(图一),按图加工顶针,入子及斜销孔,入子斜销孔公差为,顶针为±0.01mm,加工完成後送质控检测.••• 1.备料:按备料单备料,毛肧料预留後加工余量2-3MM/S.• 2.铣床:a.按备料单尺寸加工六面体.留热处理余量0.3MM/S; b.工件四面分中(图一),抓底面预留0.3MM热处理後研磨余量(图2),按图加工螺丝孔,水路孔,挂台开粗,加•刀••後送质控检测.• C精:工件四面分中(图一),抓底面(图三)对刀,按程式加工,确以加工完成,表面无弹力痕,台阶後下机,送质控检测•7.放电:工件四面分中(图一),抓底面(图三).按程式单放电坐标加工,工件上机前应检查口部有无撞伤摺角,电极无变形,加工面无刀纹,撞痕後放电加工,确认加工完成後送质控检测•8.抛光:加工人员接到工件後,对照产品外观处理要求彩图,及钳工标示交接,明确加工要求後顺产品脱模方向加工抛顺,保证其工件无摺角,圆角.•面•,,•量• 4.研磨:研磨按图加工挂台到尺寸:加工完成後送质控检测.• 5.放电:检查工件,欢迎阅读电极有无变形,撞伤後,将正弦台调到图面斜度,按程式坐标放电加工确认加工完成後送质控检测.• 6.抛光:按钳工标示,顺脱模方向抛光.• 1.快丝:按视图加工入子外形,一•寸,挂台斜面及直角筋位,公差:,加工完成後送质控检测.•••。
模具生产工艺流程
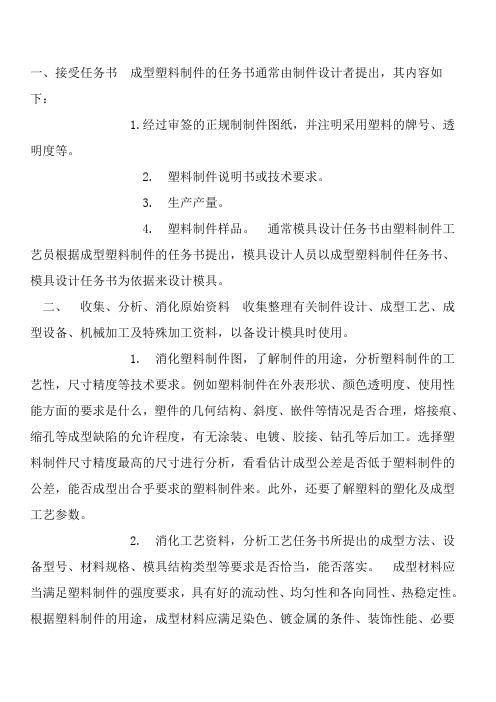
一、接受任务书成型塑料制件的任务书通常由制件设计者提出,其内容如下:1.经过审签的正规制制件图纸,并注明采用塑料的牌号、透明度等。
2. 塑料制件说明书或技术要求。
3. 生产产量。
4. 塑料制件样品。
通常模具设计任务书由塑料制件工艺员根据成型塑料制件的任务书提出,模具设计人员以成型塑料制件任务书、模具设计任务书为依据来设计模具。
二、收集、分析、消化原始资料收集整理有关制件设计、成型工艺、成型设备、机械加工及特殊加工资料,以备设计模具时使用。
1. 消化塑料制件图,了解制件的用途,分析塑料制件的工艺性,尺寸精度等技术要求。
例如塑料制件在外表形状、颜色透明度、使用性能方面的要求是什么,塑件的几何结构、斜度、嵌件等情况是否合理,熔接痕、缩孔等成型缺陷的允许程度,有无涂装、电镀、胶接、钻孔等后加工。
选择塑料制件尺寸精度最高的尺寸进行分析,看看估计成型公差是否低于塑料制件的公差,能否成型出合乎要求的塑料制件来。
此外,还要了解塑料的塑化及成型工艺参数。
2. 消化工艺资料,分析工艺任务书所提出的成型方法、设备型号、材料规格、模具结构类型等要求是否恰当,能否落实。
成型材料应当满足塑料制件的强度要求,具有好的流动性、均匀性和各向同性、热稳定性。
根据塑料制件的用途,成型材料应满足染色、镀金属的条件、装饰性能、必要的弹性和塑性、透明性或者相反的反射性能、胶接性或者焊接性等要求。
3. 确定成型方法采用直压法、铸压法还是注射法。
4、选择成型设备根据成型设备的种类来进行模具,因此必须熟知各种成型设备的性能、规格、特点。
例如对于注射机来说,在规格方面应当了解以下内容:注射容量、锁模压力、注射压力、模具安装尺寸、顶出装置及尺寸、喷嘴孔直径及喷嘴球面半径、浇口套定位圈尺寸、模具最大厚度和最小厚度、模板行程等,具体见相关参数。
要初步估计模具外形尺寸,判断模具能否在所选的注射机上安装和使用。
5. 具体结构方案(一)确定模具类型如压制模(敞开式、半闭合式、闭合式)、铸压模、注射模等。
模具加工

三下模零件 下模刀口成型零件,图形相对比较简单,加工精度要求高。内孔尺寸
一定要按图面尺寸公差加工,内孔超出公差上限或下限都会引起产品毛 边过大。 刀口长度,落斜角度,都要按图面要求加工。 刀口长度过长会引起卡料严重的会导致冲子断裂,刀口崩裂。 落斜尺寸不对,会引起堵料跳料。
有些零件为了避免跳料堵料,会在侧面做吹气孔,吃气孔在加工时不能 破到工件其他表面。
一些冲子看图面,头部尾部形状一样,在加 工挂台时,一定要在电子档中确认方向无误 后再加工!个别尺寸有差别,在电子档中才 能发现!
二 脱料零件
1 脱料入块 易磨损,根据不同要求,材
料多为SKH-9,ASP23/60,钨钢, 上下分体结构时,工件尾部部 分用SKD11,头部部分用SKH9,ASP23/60,钨钢! 编号SXX-XX 工艺流程:(1)线割→磨床 →放电 (2)磨床→线割→光学研磨 →磨床 根据工件修改工艺
结束语
以上是对模具结构及零件的一些简单认识,在加工过程中,最基 本的就是审图,看懂图纸,复杂的零件还要看工艺是怎么安排的, 根据工艺来确定要加工哪里,哪里是最后加工,避免给后道工序带 来麻烦。同时利用闲暇时间来了解整套模具的构造等,来补充自己, 不断学习,不断进步! 最后,再一次祝你:
工作顺利、事业成功、生活美满!
脱料入块直接接触产品,为 冲子提供导向,部分零件会在 头部加管位,强压防止产品移 动,零件头部还要做对导料板 ,产品的让位,比较小的让位 需要精密放电加工,相比其他 零件,脱料入块比较复杂!
脱料入块精确引导冲子,内孔间隙一般为0.003,高精度的要求间隙 0.002,内孔宽度加工时做正公差,方便与冲子实配。
五金模具的基本结构
模具组立图
模板加工整体流程
模具加工工序及细节处理

模具加工工序及细节处理开料:前模料、后模模料、镶件料、行位料、斜顶料;开框:前模模框、后模模框;开粗:前模模腔开粗、后模模腔开粗、分模线开粗;铜公:前模铜公、后模铜公、分模线清角铜公;线切割:镶件分模线、铜公、斜顶枕位;电脑锣:精锣分模线、精锣后模模芯;电火花:前模粗、铜公、公模线清角、后模骨位、枕位;钻孔、针孔、顶针;行位、行位压极;斜顶复顶针、配顶针;其它:①唧咀、码模坑、垃圾钉(限位钉);②飞模;③水口、撑头、弹簧、运水;省模、抛光、前模、后模骨位;细水结构、拉杆螺丝拉钩、弹簧淬火、行位表面氮化;修模刻字。
模具设计知识一、设计依据1:尺寸精度与其相关尺寸的正确性。
2:根据塑胶制品的整个产品上的具体要和功能来确定其外面质量和具体尺寸属于哪一种:A:外观质量要求较高,尺寸精度要求较低的塑胶制品,如玩具;B:功能性塑胶制品,尺寸要求严格;C:外观与尺寸都要求很严的塑胶制品,如照相机。
3:脱模斜度是否合理:脱模斜度直接关系到塑胶制品的脱模和质量,即关系到注射过程中,注射是否能顺利进行:A:脱模斜度是否足够;B:斜度要与塑胶制品在成型的分模或分模面相适应;是否会影响外观和壁厚尺寸的精度;C:是否会影响塑胶制品某部位的强度。
二、设计程序1:对塑料制品图及实体(实样)的分析和消化:A 、制品的几何形状;B 、尺寸、公差及设计基准;C 、技术要求;D 、塑料名称、牌号E 、表面要求2:型腔数量和型腔排列:A 、制品重量与注射机的注射量;B 、制品的投影面积与注射机的锁模力;C 、模具外形尺寸与注射机安装模具的有效面积,(或注射机拉杆内间距)D 、制品精度、颜色;E 、制品有无侧轴芯及其处理方法;F 、制品的生产批量;G 、经济效益(每模的生产值)型腔数量确定之后,便进行型腔的排列,即型腔位置的布置,型腔的排列涉及模具尺寸,浇注系统的设计、浇注系统的平衡、抽芯(滑块)机构的设计、镶件及型芯的设计、热交换系统的设计,以上这些问题又与分型面及浇口位置的选择有关,所以具体设计过程中,要进行必要的调整,以达到比较完美的设计。
模具生产工艺流程
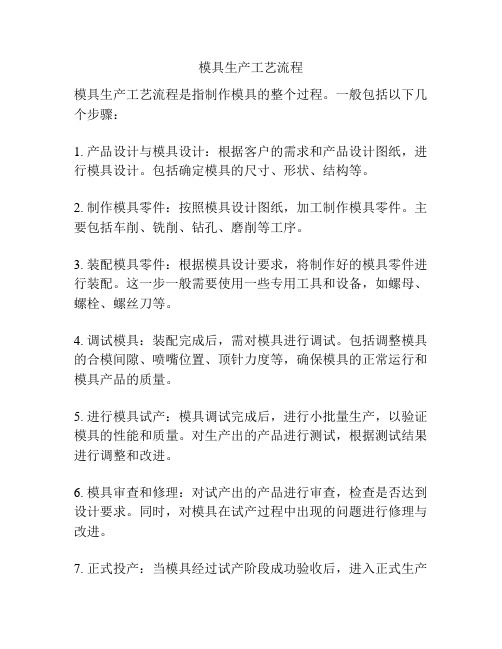
模具生产工艺流程
模具生产工艺流程是指制作模具的整个过程。
一般包括以下几个步骤:
1. 产品设计与模具设计:根据客户的需求和产品设计图纸,进行模具设计。
包括确定模具的尺寸、形状、结构等。
2. 制作模具零件:按照模具设计图纸,加工制作模具零件。
主要包括车削、铣削、钻孔、磨削等工序。
3. 装配模具零件:根据模具设计要求,将制作好的模具零件进行装配。
这一步一般需要使用一些专用工具和设备,如螺母、螺栓、螺丝刀等。
4. 调试模具:装配完成后,需对模具进行调试。
包括调整模具的合模间隙、喷嘴位置、顶针力度等,确保模具的正常运行和模具产品的质量。
5. 进行模具试产:模具调试完成后,进行小批量生产,以验证模具的性能和质量。
对生产出的产品进行测试,根据测试结果进行调整和改进。
6. 模具审查和修理:对试产出的产品进行审查,检查是否达到设计要求。
同时,对模具在试产过程中出现的问题进行修理与改进。
7. 正式投产:当模具经过试产阶段成功验收后,进入正式生产
阶段。
8. 维护与保养:模具生产过程中,需要定期对模具进行维护与保养,保证模具的正常使用寿命和生产效率。
以上是一般模具生产工艺流程的基本步骤,实际生产中还会根据具体情况进行调整和改进。
模具各工序加工操作及质量标准(完整)
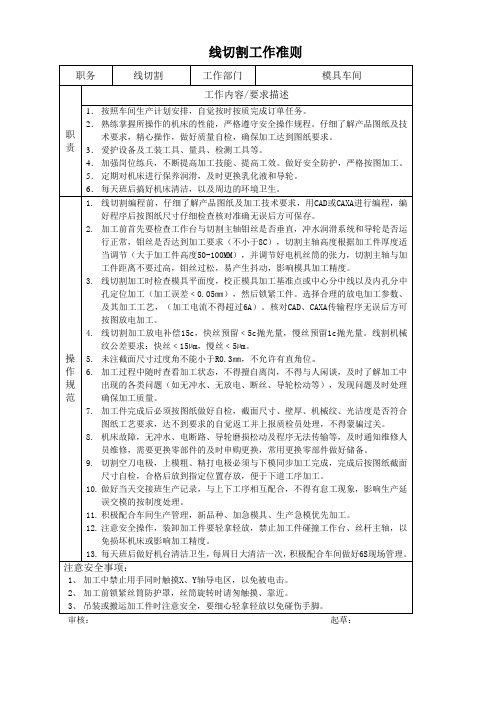
线切割工作准则审核:起草:电火花操作准则划线操作准则审核:起草:铣工/钻工操作准则审核:起草;车工操作准则一、工作内容:1、按照生产图纸先后加工,积极配合加急模具的生产及时完成订单。
2、严格遵守安全操作规程,做好安全防护,按规定穿戴安全防护用品。
3、严格按质量控制标准加工,不断提高加工技能,精心操作,提高工效,做好质量自检,确保加工达到图纸要求。
4、爱护设备及工装工具、量具、检测工具,定期进行保养润滑,定期检修。
5、每天班后搞好机床清洁,以及周边的环境卫生,配合车间做好6S管理。
二、操作规范/技术要求:1、首先仔细了解产品图纸及加工技术工艺要求,熟悉加工操作步骤,选用适合的胚料、刀具、量具提高工作效率。
2、开机前必须仔细检查加工设备运行情况,做好加工前工作准备。
3、模具外型加工尺寸精度表:量(模具成品外圆需精车的要流余量,外圆不需要精车按图加工≤0~–0.5㎜)。
7、粗车下模焊合室按图纸深度留0.5㎜余量精铣,允许公差±0.1㎜,粗车上模公头留拉方余量单边3㎜(以公头截面最长直径为准)。
8、精车上、下模配合贴紧端面(即光面)平整,允许公差﹤0.03㎜,不能有凸凹现象,外形倒角R3,配合止口倒角R1.5,不允许加工直角。
9、平面装配要求:(1)、模具端面平行度应达到GB1184标准规定的6级。
(2)、模具止口对外圆的同轴度达到GB1184标准规定的8级。
(3)、组合上、下模具的同轴度达到GB1184标准规定的13级。
三、注意安全事项:1、加工前必须要做好安全防护措施,佩带好防护罩、眼镜、手套等。
2、开机前检查卡盘、加工件、加工刀具是否锁紧,以免在加工中震动弹出。
审核:起草:工具磨/平面磨操作准则审核:起草:钳工操作准则审核:起草:打磨工操作准则。