工业型煤燃烧固硫的研究进展
煤炭燃前脱硫方法及其应用现状

二、煤炭脱硫的方法
为了降低煤炭中的硫含量,减少对环境的污染,研究人员已经开发出了多种脱 硫方法。以下是几种目前广泛使用的煤炭脱硫方法。
1、物理洗选脱硫:这种方法是利用煤和硫的物理性质差异,通过水力旋流器 等设备将煤和硫进行分离。虽然这种方法在理论上可行,但实际操作中,由于 煤和硫的物理性质相近,难以实现有效的分离。
2、生物法
生物法是一种利用微生物将煤炭中的硫转化为其他形态的方法。微生物可以将 煤中的有机硫转化为无机硫,并将其从煤炭中分离出来。生物法的优点是操作 简单、成本低,同时对环境友好。但缺点是脱硫速度较慢,需要经过长时间的 反应才能达到较好的脱硫效果。
3、物理法
物理法是一种利用物理手段将煤炭中的硫从其结构中分离出来的方法。其中, 最具代表性的是浮选法和重选法。浮选法是利用不同矿物的密度不同,通过浮 选药剂的作用,使煤和黄铁矿等矿物分离。重选法则利用不同矿物的密度不同, 通过振动等手段将煤和黄铁矿等矿物分离。物理法的优点是可以直接从煤炭中 分离出硫,工艺简单、成本低。但缺点是无法脱除煤中所有的硫,且对含硫量 较高的煤炭效果不佳专家访谈等方法,对国内外煤炭燃前脱硫 工艺的研究现状进行了系统梳理和分析。首先,通过查阅相关文献了解各种脱 硫工艺的研究成果和实际应用情况;其次,结合实地调查,了解现有工艺在实 际运行中的优缺点;最后,通过专家访谈,对各种工艺的未来发展进行了展望。
结果与讨论
应用现状:
目前,化学法和物理法在工业生产和实际应用中较为广泛。化学法虽然可以脱 除大部分的硫,但工艺复杂、成本高,且可能对环境造成一定的影响。物理法 则无法脱除煤中所有的硫,且对含硫量较高的煤炭效果不佳。生物法则处于研 究阶段,尚未在工业生产中得到广泛应用。
在实际应用中,脱硫方法的选用需要考虑煤炭的含硫量、脱硫成本、设备投资 等因素。对于含硫量较低的煤炭,可以采用简单的物理法进行脱硫;对于含硫 量较高的煤炭,可以考虑使用化学法或生物法进行脱硫。此外,还需要考虑脱 硫过程中产生废弃物的处理和再利用问题,以降低对环境的影响。
专家看好生物固硫型煤技术
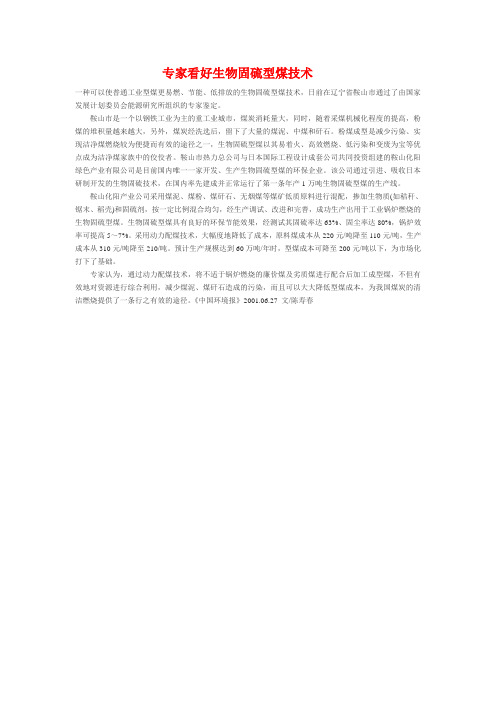
专家看好生物固硫型煤技术一种可以使普通工业型煤更易燃、节能、低排放的生物固硫型煤技术,日前在辽宁省鞍山市通过了由国家发展计划委员会能源研究所组织的专家鉴定。
鞍山市是一个以钢铁工业为主的重工业城市,煤炭消耗量大,同时,随着采煤机械化程度的提高,粉煤的堆积量越来越大,另外,煤炭经洗选后,留下了大量的煤泥、中煤和矸石。
粉煤成型是减少污染、实现洁净煤燃烧较为便捷而有效的途径之一,生物固硫型煤以其易着火、高效燃烧、低污染和变废为宝等优点成为洁净煤家族中的佼佼者。
鞍山市热力总公司与日本国际工程设计成套公司共同投资组建的鞍山化阳绿色产业有限公司是目前国内唯一一家开发、生产生物固硫型煤的环保企业。
该公司通过引进、吸收日本研制开发的生物固硫技术,在国内率先建成并正常运行了第一条年产1万吨生物固硫型煤的生产线。
鞍山化阳产业公司采用煤泥、煤粉、煤矸石、无烟煤等煤矿低质原料进行混配,掺加生物质(如秸秆、锯末、稻壳)和固硫剂,按一定比例混合均匀,经生产调试、改进和完善,成功生产出用于工业锅炉燃烧的生物固硫型煤。
生物固硫型煤具有良好的环保节能效果,经测试其固硫率达63%、固尘率达80%,锅炉效率可提高5~7%。
采用动力配煤技术,大幅度地降低了成本,原料煤成本从220元/吨降至110元/吨,生产成本从310元/吨降至210/吨。
预计生产规模达到60万吨/年时,型煤成本可降至200元/吨以下,为市场化打下了基础。
专家认为,通过动力配煤技术,将不适于锅炉燃烧的廉价煤及劣质煤进行配合后加工成型煤,不但有效地对资源进行综合利用,减少煤泥、煤矸石造成的污染,而且可以大大降低型煤成本,为我国煤炭的清洁燃烧提供了一条行之有效的途径。
《中国环境报》2001.06.27 文/陈寿春。
型煤固硫剂的研究与开发的开题报告

型煤固硫剂的研究与开发的开题报告一、选题的背景及意义随着我国经济的高速发展,能源需求量不断增大,而煤炭一直是我国主要的能源,占据了我国能源消费的很大比例。
但是,煤炭中的硫、氮等有害成分对环境和人类健康有着极大的影响,同时也会影响煤炭的利用,提高煤炭利用效率和降低对环境的影响,是当前我国煤炭行业亟待解决的问题。
目前,利用型煤技术是解决煤炭中有害成分问题的一种有效途径,而型煤固硫剂是制备型煤的关键技术之一。
因此,开发一种高效、绿色型煤固硫剂,对于提高煤炭利用效率、降低对环境的影响具有重要意义。
二、研究的目的和内容本项目的目的是研究开发一种高效、环保的型煤固硫剂,主要包括以下内容:1. 对型煤制备工艺进行优化,确定最佳的制备条件和工艺参数。
2. 筛选和评价不同类型的固硫剂,比较它们的固硫效果、对型煤质量的影响和环境友好性等方面的差异。
3. 对最佳方案进行优化,如增强稳定性、降低成本等,并进行测试和评价。
三、研究的方法和技术路线本研究采用以下方法和技术路线:1. 通过文献资料、煤炭样品分析和实验,确定最佳的型煤制备工艺和工艺参数。
2. 筛选和评价不同类型的固硫剂,采用包括固硫剂浸渍、干燥、煅烧、型煤制备等多个环节的实验流程,比较它们的固硫效果、对型煤质量的影响和环境友好性等方面的差异。
3. 优化方案,如增强稳定性、降低成本等,并进行多次测试和评价以确定最佳的方案。
四、预期研究结果和意义通过本项研究,预计可以实现以下结果:1. 确定最佳的型煤制备工艺和工艺参数。
2. 筛选出具有较好固硫效果、对型煤质量影响小、环境友好等特点的固硫剂,为型煤制备提供重要保障。
3. 优化最佳方案,如增强稳定性、降低成本等,为煤炭行业提供有利的技术支持。
本项研究有望为我国型煤技术的发展和煤炭清洁利用提供新的技术手段和思路,具有重要的理论和应用价值。
应用工业固硫型煤技术控制燃煤工业锅炉

应用工业固硫型煤技术控制燃煤工
业锅炉
工业固硫型煤技术是指在煤的生产和应用过程中,采用掺加固硫剂的方法,使煤中的硫在燃烧过程中与固硫剂发生反应,生成硫酸钙等固体物质,防止污染物的排放。
这种技术已经被广泛应用于各种类型的燃煤工业锅炉中,有效地控制了燃烧产生的污染物的排放,改善了空气质量,减少了对环境的损害。
工业固硫型煤技术控制燃煤工业锅炉的过程中,重点是选择合适的固硫剂和添加量,并通过改变配比的方式调整燃煤的固硫率。
在具体实施过程中,首先需要根据锅炉的规格和工艺要求选择适合的固硫剂,确定最佳添加量和添加方式。
一般来说,沾固剂添加量在0.5%—2%之间,具体数量可根据煤质、
燃烧条件、锅炉结构、排放标准等因素进行调整。
在工业固硫型煤技术控制燃煤工业锅炉的过程中,还需要针对不同的燃烧条件进行精细调整。
例如,在低温条件下燃烧时,应采用温度控制、空气过量和氧气富裕等措施,使硫酸钙等固体物质在燃烧中充分固硫;在高温条件下燃烧时,应采用盐酸喷雾、淋水等措施,降低煤中的挥发性质和气态硫的浓度,使硫在烟囱中得到完成氧化。
为了达到更好的排放效果,除了应用工业固硫型煤技术外,还可以考虑使用其他治理技术,如烟气脱硝、烟气脱臭、烟气
脱烟等。
这些方法的使用可以降低燃煤工业锅炉产生的其他污染物的含量,使空气质量得到进一步提升。
总之,应用工业固硫型煤技术控制燃煤工业锅炉已经成为了现代环保工作中的一项重要措施。
通过合理选择固硫剂、精细调整配比,并与其他治理技术相结合,可以有效地降低锅炉产生的污染物的排放,保护环境,促进经济社会的可持续发展。
不同气氛下煤燃烧固硫化学反应机理研究进展

第28卷第1期煤 炭 学 报Vol.28 No.1 2003年2月J OU RNAL OF CHINA COAL SOCIET Y Feb. 2003 文章编号:0253-9993(2003)01-0074-06不同气氛下煤燃烧固硫化学反应机理研究进展范红宇,曹欣玉,周俊虎,程 军,岑可法(浙江大学热能工程研究所能源清洁利用与环境工程教育部重点实验室,浙江杭州 310027)摘 要:针对煤高温下燃烧脱硫技术的效率较低这一现状,对钙基固硫剂在流化床燃烧条件下还原性气氛和交变气氛下的固硫反应机理以及煤粉炉燃烧过程中氧化性和还原性气氛下固硫化学反应机理的研究现状进行了详细的评述,并在前人研究的基础上提出了不同气氛下流化床和煤粉炉燃烧条件下石灰石固硫化学反应机理研究的若干趋势.关键词:不同气氛;煤燃烧;固硫;化学反应;机理中图分类号:TQ534 文献标识码:A1 煤粉炉和流化床燃烧条件下不同燃烧气氛的形成及其主要反应 石灰石是煤燃烧过程中最常用的钙基固硫剂,在煤粉炉中喷射钙基脱硫剂的温度为827~1223℃,常压流化床的燃烧温度在800~950℃之间[1].在常压流化床和煤粉炉中,脱硫剂首先要经历吸热的煅烧反应,以后的反应历程要取决于炉内的气氛和温度.流化床燃烧条件下的还原性气氛[2]是由于颗粒相氧气的耗尽,而导致流化床锅炉床层的密相,包括氧化钙和硫酸钙,在80%的时间下处在还原性气氛下,氧气分压力较低并且一氧化碳的浓度相对较高(4%~5%).另外还原性气氛还会由于空气分级而加强.在煤粉炉中如果以α代表过量空气系数,就可以界定煤粉炉燃烧条件下氧化还原气氛的出现[3].当α< 110时,应为还原性气氛;当α>110时,炉内大部分为氧化性气氛,但是在燃烧的碳颗粒内部存在局部的还原性气氛.在火焰温度下碳的燃烧在边界层和碳颗粒内部制造了压力梯度,所以碳粒表面被氧化性气体耗尽,从而出现了局部的还原性气氛. 常压流化床和煤粉炉中硫分的脱除包括脱硫剂颗粒连续的煅烧和硫化反应[4]为CaCO3(s)CaO(s)+CO2(g),ΔH298=18211kJ/mol,CaCO3(g)+SO2(g)+015O2(g)CaSO4(s),ΔH298=-50212kJ/mol. 在压力流化床下,当温度低于850℃、运行压力为1~2MPa时,不发生碳酸钙的煅烧反应而会发生直接硫化反应[5]为CaCO3(s)+SO2(g)+015O2(g)CaSO4(g)+CO2(g),ΔH298=-303kJ/mol. Lyngfelt等[6,7]根据实验表明,氧的消耗(Dennis,Jonke)[8,9]和CaSO4的还原性分解[10]都是影响脱硫率的主要原因,在还原性气氛中CaSO4会转化成CaS,反应为CaSO4(s)+4CO CaS(s)+4CO2(g), CaSO4(s)+CO(g)CaO(s)+SO2(g)+CO2(g),CaO(g)+SO2(g)+3CO(g)CaS+3CO2(g).在氧化性气氛中的反应为CaS(s)+2O2(g)CaSO4(s),CaO(s)+SO2(g)+015O2(g)CaSO4(s), CaS(g)+115O2(g)CaO(s)+SO2(g).Chen和Yang等[11]认为在流化床燃烧的温度下,还会发生以下反应,即CaS+3CaSO44CaO+4SO2.2 流化床燃烧条件下交变气氛对石灰石硫化反应机理的影响 近年来,许多研究者对于流化床燃烧条件下交变气氛时石灰石的脱硫反应进行了研究.交变气氛是指收稿日期:2002-04-28 基金项目:国家重点基础研究发展规划项目专项经费资助(G1999022204)在煤的燃烧过程中出现了局部的还原性气氛,这样在燃烧过程中会交替出现氧化性气氛和还原性气氛的情况,在一定时间内这种现象可以假定为以一定周期不断循环下去,因为在流化床燃烧条件下煤粉颗粒的停留时间较长,这种以一定周期循环的交变气氛完全可能出现.影响交变气氛的参数有:循环周期的长短,一个循环周期中还原性气氛的比例,还原性气氛的组成,总的反应时间.对于交变气氛下固硫反应的研究,主要针对不同的脱硫剂种类、尺寸,不同组成的还原性气氛,一个循环周期中还原性气氛所占时间的不同比例,不同长短的循环时间,不同的总反应时间进行分析论证.固硫反应主要应用固定床实验台和石英管燃烧系统进行研究. E 1J 1Anthony 等[12]认为在不同温度、气氛和不同的二氧化硫分压力下,氧化钙和二氧化硫的反应会产生4种不同的物相,它们的摩尔体积分别是碳酸钙为3619cm 3/mol ,氧化钙为1619cm 3/mol ,硫化钙为2819cm 3/mol ,硫酸钙为5212cm 3/mol.硫酸钙的摩尔体积是氧化钙的3109倍.但在高温下二者摩尔体积的比值是2172,因为硫酸钙在高温下的摩尔体积是46cm 3/mol ,而不是常温下的5212cm 3/mol ,这个数值只有在温度低于200℃时才有效.它在不同温度和气氛下的存在形式见表1.表1 不同温度气氛下钙硫化合物的存在形式T able 1 C a -S speciation as a function of temperature 温度范围/℃氧化性气氛下还原性气氛下<450CaSO 3<700CaSO 3,CaSO 4CaSO 3,CaSO 4,CaS >700CaSO 4>830CaS ,CaSO 4 Makarytchev S 1V 1等[13]研究了燃煤鼓泡流化床密相区中氧化和还原性气氛交变条件下的脱硫问题,通过计算煤-蒸汽-添加剂-空气体系中的多相平衡并得出以下结论:(1)在交变的氧化、还原气氛下,在还原区反应生成CaS 能够提高钙基固硫剂的脱硫效率;(2)在脱硫过程中形成了以CaS 为核,以CaSO 4为壳的颗粒结构;(3)加强鼓泡流化床密相的还原性气氛有助于提高其在高温下的脱硫率. 众多学者对交变气氛对固硫剂反应的影响进行了研究,但是对于交变气氛的影响还没有统一的认识,他们认为交变气氛对于石灰石固硫反应既有消极的影响,也有积极的影响.T Mattisson 等[14]在不同气氛下(800和875℃)对3种不同反应活性的石灰石硫化反应进行了研究,并认为交变气氛对于固硫反应具有消极的影响.反应气氛是1500×10-6的SO 2,10%的CO 2和交替变化的氧气及一氧化碳气氛组成.在氧化性气氛下(820和875℃),3种石灰石的脱硫率变化不大.但是在交变气氛下825℃时3种石灰石的脱硫率最高,温度升高到875℃时脱硫率降至最低.脱硫率的迅速降低是由于随着温度升高而引起的硫酸钙的分解和硫化钙的氧化反应而引起的.Anders Lyngfelt 等[15]提出了一个流化床交变性气氛下的固硫反应模型,模型考虑了2个反应速率常数:①固硫反应的速率常数;②CaSO 4还原性分解反应的速率常数.模型表明脱硫剂的利用率会由于还原性气氛的影响而大大降低,特别在高温和固硫率较高的情况下.即使在较低的温度下(小于830℃),还原性气氛的消极影响也比较显著.模型显示即使在其它条件都无法抑制脱硫反应的条件下,还原性气氛还能降低脱硫剂的反应活性.所以对于所有的常压流化床来说,因为其固硫率很大程度上受温度的影响,所以还原性气氛对于固硫率是一个很大的制约因素. 但是,Jonke 等[16]认为,流化床锅炉底部床层出现的交变气氛以及二氧化硫从固硫剂颗粒中不断的析出是导致更多的硫分和固硫剂反应的两个主要原因,所以交变气氛下的固硫剂脱硫率相对于氧化性气氛下会有大幅的提高,从而对固硫反应具有积极的促进作用.对于Jonke 的理论,下列研究者从实验上给予了论证.结果发现交变气氛对于固硫反应的积极促进作用也需要在一定的反应条件下才能实现,不同的反应条件直接决定了交变气氛对固硫反应所发挥的作用.T 1Mattisson 等[17]研究了交变气氛下不同还原性气氛和循环周期对石灰石硫化反应的影响.氧化性气氛由SO 2,CO 2,O 2组成.3种还原性气氛组成:①H 2S ,CO ,CO 2;②SO 2,CO ,CO 2;③H 2S ,H 2,CO 2.研究发现,相对于氧化性气氛而言,在交变气氛下得到的氧化钙固硫率并不总是得到大幅提高,一定条件下还有所降低,这是由循环周期长短和还原性气氛的种类决定的.当循环周期为30~240s 、还原性气氛的比例为20%~50%时,氧化钙的固硫率会出现57第1期范红宇等:不同气氛下煤燃烧固硫化学反应机理研究进展一个最大值.循环周期越长,得到的固硫率最大值也越大.当循环周期为900s 时,氧化钙的固硫率随着还原性气氛比例的增加而增加.当应用H 2/CO 作为还原性组分时,氧化钙的固硫率最大,H 2S/CO 时的氧化钙固硫率次之,最低的是SO 2/CO.Maria Jose Fernandez 等[18]研究了交变气氛下不同的循环周期和一个循环周期中还原性气氛所占时间的不同比例对石灰石固硫反应的影响.为了模拟石灰石在流化床燃烧条件下反应的实际条件,实验中通入氧化和还原性气氛的时间比较短,循环周期从2~24s 不等.还原性气氛在总时间中的比例为50%,33%,25%.当还原性气氛比例为50%、总的循环时间为8s 时,氧化钙固硫率最小为119%,即此时交变气氛对氧化钙固硫反应起消极的抑制作用.当循环时间减小时,转化率会急剧增加,总循环时间为6s 时氧化钙固硫率为1412%.当循环时间在2~6s 时,氧化钙固硫率比同样条件下氧化性气氛时的固硫率要提高50%,此时交变气氛才对固硫反应具有促进作用.当还原性气氛的比例为33%和25%时,相对于氧化性气氛的氧化钙固硫率而言,在任意长短的循环时间下交变气氛对于氧化钙固硫率的提高都具有积极的促进作用. 在交变气氛下,对于不同种类石灰石的脱硫性能的研究[19]表明:在交变气氛下石灰石的固硫性能会有所提高,唯一的例外是氧化铁含量较高的石灰石,它会降低石灰石的脱硫能力,因为在还原性气氛下氧化铁会降低石灰石硫化反应产物的稳定性.另外脱硫剂颗粒尺寸的降低会对硫化钙的氧化反应和硫酸钙的还原性分解有促进作用,增加二氧化硫的析出,结果对于石灰石的脱硫反应活性有消极影响. 通过对流化床燃烧条件下交变气氛对石灰石固硫反应影响的研究,有学者[20]认为由颗粒尺寸决定的停留时间、反应速率、还原性气氛的影响是决定流化床固硫率的主要因素,并且可把前3个因素合并为一个模型来预测固硫率,然而对于还原性气氛对固硫率的作用是积极还是消极却不能把握.对交变气氛下固硫反应的研究很难在实验条件下选择代表性的工况,因为大多数的研究工作都假设固硫反应是对含硫气体的一级反应,然而石灰石在一个循环周期中的反应速率是还原性气氛和氧化性气氛下的反应速率的复杂函数,决不是简单的一级反应,因此交变气氛下石灰石的反应速率系数不是一个常数,而是诸如气体浓度和停留时间等许多因素的复杂函数.因此用模型描述交变气氛下的反应机理也极其困难.另外在交变气氛下的固硫反应是瞬间完成的,而且反应的一些参数也是不断变化的,气相和固相的组成也不断发生变化,因此对交变气氛的数值模拟工作极其困难,至今没有大的进展,其详细的微观反应机理仍是一个研究难题. 由上述研究可以发现,仅通过一些基础的试验工作只能对交变气氛的影响进行定性的描述,其不足之处显而易见.只有在模型建设和数值模拟方面进行深入地研究才能更进一步了解其微观反应机理.图1 煤粉炉分级喷钙脱硫Fig 11 Description of the stageddesulfurization of pulverized boiler 1———一次风燃烧及脱硫区域;2———二次风燃烧区域;3———脱硫区域3 煤粉炉燃烧条件下不同燃烧气氛对氧化钙硫化反应机理的影响 煤粉炉燃烧的典型参数[21]是炉膛内部燃烧温度为1500℃,在炉膛出口处气温降至1100℃,最高燃烧温度可以达到1650℃,炉内大部分处于燃料不足的氧化性气氛.较细的颗粒会在炉膛烟气温度下燃烧,而较粗的颗粒会在更高的温度下燃烧.但是在烟气温度下燃烧的煤颗粒因为在燃烧过程中氧气会渗透到煤粒中,所以固硫产物硫酸钙和硫化钙稳定存在的条件不好,固硫产物硫酸钙在高温下会分解,硫化钙在氧化性条件下又重新被氧化释放出二氧化硫.所以在高温下硫化钙存在的必要条件就是还原性的气氛. Makarytchev S 1V 1等[22]针对煤粉炉内煤-水-石灰石-空气体系建立了数学模型,认为炉内喷钙尾部增湿系统在炉内低温区的脱硫率受反应物的短停留时间所制约.另外,为降低煤粉炉污染物的排放还提出了一种分段脱硫的方法:即首先在炉内高温还原区固硫反应生成CaS ,然后在低温氧化区CaS 进一步转化成CaSO 4.将添加剂分别送入炉内可使脱硫效率达80%~85%.反应历程如图1所示. 研究发现,当过量空气系数小于0185,钙硫比为1~115,炉温67煤 炭 学 报2003年第28卷为1300~1500℃时,煤中的有机硫以硫化氢的形式析出,会在高温还原区发生下列反应:H 2S +CaOCaS +H 2O ,SO 2+CaO CaS +115O 2.在过量空气系数为111~112,钙硫比为2~215,炉温小于1100℃时,才会在低温氧化区域发生固硫反应:CaS +115O 2CaO +SO 2,CaS +2O 2CaSO 4. J 1Torres -Ordonez 等[23]根据热动力学理论得出以下结论:在贫氧燃烧(α<110)情况下,此时炉内主要为还原性气氛,其热动力学预测和其他的一些研究表明,煤中的硫分90%都可以在1227℃以上被固定为硫化钙.对于在富氧燃烧(α>110)情况下,炉内主要为氧化性气氛,但是固硫反应会由于局部的还原性气氛而使硫分以硫化钙的形式固定在燃煤中.研究中表征环境的3个参数为d 0,S 0,α,其中d 0为燃煤颗粒的初始直径;S 0为燃煤颗粒的初始比表面积;α为过量空气系数. 对含有离子交换型钙的Illions 6号煤的分析结果表明,在1100℃的低温下,只有在燃料充足的条件下(α>0191),硫分才有可能固定为硫化钙的形式.在正常燃烧条件下(α=112),d 0S 0低于30m 3/kg.在高温(1500~1900℃)且α=112的条件下,如果能使用比表面积较大并且颗粒较大的煤粉颗粒,90%的硫分也可以固定为硫化钙的形式.这是因为高温下氧气不能完全与煤粉颗粒发生反应是由局部性的还原性气氛造成的.有学者[24]研究认为,含有离子交换型钙的Illions 6号煤在82%的碳燃尽率下有85%的自身固硫率.但是随着碳燃尽率的提高,其自身固硫率下降很快.表明只有在煤中的碳未完全燃烧的情况下硫分才被固定为硫化钙的形式.但是和其他的研究[25,26]对比发现,硫化钙的氧化反应速率比Illions 6号煤中碳的氧化速率要慢,所以一旦氧气进入碳颗粒内部必定先和碳颗粒发生反应,只有在碳完全燃尽时,硫化钙的分解反应才开始进行.这表明较高反应率的煤种的硫分很易于转化为硫化钙. 以上研究表明,煤粉炉的固硫反应有2个途径:①在分段液态排渣炉中还原性气氛下,将硫化钙以熔渣的形式除掉,此时火焰温度至少为1500℃并且需要空气预热和额外通入氧气;②在炉内燃烧的条件下,硫化钙的氧化速率相对碳的燃尽率要慢,这样在较高燃烧效率下才能使硫分固定为硫化钙的形式. Skrifvars 等[27]对炉内喷射石灰石脱硫研究发现,烟气成分对于CaO 颗粒烧结影响显著.在800℃的惰性气氛条件下没有烧结产生;当烟气中存在SO 2,CO 2,O 2或CO 时,就会发生不同程度的烧结,而CO 2存在时烧结最为严重.表明CO 2气氛对CaCO 3的烧结具有促进作用.初期硫化反应对CaO 颗粒烧结的影响有2种方式:当烟气中存在O 2和SO 2时,烟尘中CaSO 4初始含量越高,烟尘烧结越轻微;当烟气中存在CO 和SO 2时,则正好相反. Mattisson 等[28]研究了在交变气氛下石灰石颗粒的硫化反应,发现有更多的硫分和石灰石的内层结构发生反应1这是因为:①在交变气氛下对硫分周期性的吸收和释放使更多的硫分被脱硫剂颗粒吸收;②氧化钙转化为硫化钙,然后硫化钙再反应转化为硫酸钙,比氧化钙和二氧化硫反应直接转化为硫酸钙更容易;③硫化钙氧化为硫酸钙放出热量和温度的升高会影响到通过生成物层的气体的传输,进而影响到脱硫剂的平均粒径;④在生成物层生成硫化钙会使晶体结构产生裂纹和缝隙,从而使气体通过生成物层的扩散系数增大. 以上研究可知,对于煤粉炉还原性气氛下固硫反应机理的研究相对较少,主要是一些工业性试验,这是因为煤粉炉的燃烧温度较高并且脱硫剂在炉内停留时间较短,只有3~5s ,并且还原性气氛只在局部的区域出现.典型的煤粉炉燃烧可以用沉降炉来模拟,但对于如何模拟还原性气氛的组成是一个难题. 如果利用流化床燃烧条件下交变气氛下固硫反应机理研究的思路,假设还原性气氛以一定的周期循环出现,就会发现在煤粉炉条件下,脱硫剂在高温反应区停留时间短,反应时间不足,交变气氛出现的周期不易确定.另外煤粉炉正常情况下是过量空气系数为112的氧化性气氛,只有在一次风喷口附近才会出现局部的还原性气氛,对于整个循环周期中还原性气氛的比例也不易确定,相对于流化床条件下来说,煤粉炉交变气氛下的固硫反应机理研究较难进行.但如果能在煤粉炉固硫反应的模型建设和数值模拟的研究上进行更深入地研究,就可以避开用实验手段无法模拟煤粉炉条件下还原性气氛组成的难题.4 结 语 尽管煤高温燃烧脱硫技术的效率较低,但如果能利用不同气氛对固硫反应机理的影响,设计合理的反77第1期范红宇等:不同气氛下煤燃烧固硫化学反应机理研究进展87煤 炭 学 报2003年第28卷应路径并组织适当的热工环境,如煤粉炉的分级喷钙脱硫技术、链条炉[29]的两段脱硫技术、流化床条件下加强还原性气氛等措施,就可以大幅度提高煤高温燃烧脱硫技术的效率;另外煤粉炉的分级喷钙脱硫技术采用的高温还原性气氛,也能提高炉内脱硝的效率,从而达到炉内同时脱硫、脱硝的效果. 目前国际上对于不同气氛下煤燃烧固硫化学反应机理的研究主要侧重于流化床燃烧条件下的研究,对于1200~1600℃链条炉和煤粉炉条件下的研究屈指可数,特别是1200℃左右链条炉燃烧条件下的研究几乎没有.然而困扰我国环境污染的主要问题在于二氧化硫的排放,而这些二氧化硫则主要是由面广量大的工业锅炉和电站锅炉所排放出来的,所以针对工业链条炉和煤粉炉,研究不同气氛下1200~1600℃中高温区域煤燃烧固硫反应机理对于我国的环保事业具有重要的现实意义.参考文献:[1] Corey R Milne,G eoffrey D Silcox,David W Pershing.Calcination and sintering models for applization to high temperature,short time sulfation of calcium2based sorbents[J].Ind.Eng.Chem.Res.,1990,29:139~149.[2] Ljungstrom E B.In bed oxygen measurement in a commercial size AFBC[A].Proceedin gs of the8th International Confer2ence on Fluidized Bed Combustion[C],ASME,1986.853~864.[3] Neville M,Quann R J,Haynes B S,et al.Vaporization and condensation of mineral matter during pulverized coal combus2tion[J].18th symposium(international)on combustion[C].Pittsburgh:The Combustion Institute,1980,59:1267.[4] Daniels F,Alberty R A.Physical chemistry[M].New Y ork:Wiley,1975.[5] Snow M J H,Longwell J P,Sarofim A F.Direct sulfation of calcium carbonate[J].Ind.En g.Chem.Res.,1988,27:268~273.[6] Lyngfelt A,Leckner B.Sulfur capture in fluidized bed boilers—the effect of reductive decomposition of CaSO4[J].ChemicalEngineering Journal,1989a,40:59~69.[7] Lyngfelt A,Leckner B.SO2capture in fluidized bed boilers:re2emission of SO2due to reduction of CaSO4[J].Chemical En2gineering Journal,1989b,44:207~213.[8] Dennis J S,Hayhurst A N.The effect of tem perature on the kinetics and extent of SO2uptake by calcareous material duringfluidized bed combustion of coal[A].Proceedings of the20th International Symposium on Combustion[C].Ann Arbor Michigan:The Combustion Institute,1984:1347~1355.[9] Jonke A A,Vogel G J,Carls E J,et al.Pollution control ca pabilities of fluidized bed combustion[J]. A.I.Ch. E.Symp.Ser.,1972,126(68):241~251.[10] Dennis J S,Hayhurst A N.Mechanism of the sul phation of calcined limestone particle in combustion gases[J].Chem.Eng.Sci.,1990,45:1175.[11] Chen J M,Y ang R T.Fluidized bed combustion of coal with lime addictives kinetics and mechanism of re generation of thelime sorbent[J].Ind.Engng Chem.Fundam,1979,18:134~138.[12] Anthony E J,Granatstein D L.Sulfation phenomena in fluidized bed combustion systems[J].Progress in Energy and Com2bustion Science,2001,27:215~236.[13] Makarytchev S V,Cen K F,Luo Z Y,et al.High2temperature sulphur removal under fluidized bed combustion conditions─a chemical interpretation[J].Chemical Engineering Science,1995,50(9):1401~1407.[14] Mattisson T,Lyngfelt A.The reaction between limestone and SO2under periodically changing oxidizing and reducing condi2tions-effect of temperature and limestone type[J].Thermochimica Acta,1999,325:59~67.[15] Lyngfelt A,Lechner B.Model of sulfur ca pture in fluidized2bed boilers under conditions changing between oxidizing and re2ducing[J].Chemical Engineering Science,1993,48(6):1131~1141.[16] Jonke A A,Vogel G J,Carls E L,et al.Fluidized2bed regeneration of sulfated dolomite by reductive decomposition withcoal[A].Presentation at the65th Annual AIChE Meethin g,AIChE Microfiche[C].New Y ork:N Y,November,1972.241.[17] Mattisson T,Lyngfelt A.The reaction between sulfur dioxide and limestone underperiodically changing oxidizing and reduc2ing conditions———the effect of reducing conditions[J].Journal of the Institute of Energy,1998,71:190~196.[18] Fernandez M J ,Lyngfelt A ,Britt -Marie Steenari.Reaction between limestone and conditions alternatin g between oxidiz 2ing and reducing :the effect of short cycle times [J ].Energy &Fuels ,2000,14:654~662.[19] Hansen P F B ,Dam -Johnssen K ,Ostergaard K.High temperature reaction between sulfur dioxide and limestone ─Ⅴ:The effect of periodically changing oxidizing and reducing conditions [J ].Chemical Engineering Science ,1993,48(7):1325~1341.[20] Lyngfelt A ,Lechner B.Sulfur capture in circulating fluidized 2bed boilers :can the efficiency be predicted ?[J ].ChemicalEngineering Science ,1999,54:5573~5584.[21] Beer J bustion technology development in power generation in response to environmental challenges [J ].Progress inEnergy and Combustion Science ,2000,26:301~327.[22] Makarytchev S V ,Cen K F ,Luo Z Y.Staged desulfurization by direct sorbent injection in pulverized 2coal boilers [J ].En 2ergy ,1994,19(9):947~956.[23] Torres -Ordonez R J ,Wall T F ,Longwell J P ,et al.Sulfur retention as CaS during coal combustion :a modeling study todefine mechanisms and possible technologies [J ].Fuel ,1993,72(5):633~644.[24] Freund H ,Lyon R bust [J ].Flame ,1982,45:191.[25] Torres -Ordonez R J ,Longwell J P ,Sarofim A F.Intrinsic kinetics of CaS oxidation [J ].Ener gy &Fuels ,1989a ,3:506~515.[26] Torres -Ordonez R J ,Longwell J P ,Sarofim A F.Physical transformations during CaS oxidation [J ].Energy &Fuels ,1989b ,3:595~603.[27] Skrifvars B J ,Hupa M ,Hyoty P.Superheater fouling due to limestone injection in coal 2fired boilers [J ].Journal of the In 2stitute of Energy ,1991,64(461):196~201.[28] Mattisson T.Sulfur capture during combustion of coal in circulating fluidized bed boilers [D ].PhD Thesis ,G oteborg Uni 2versity ,Sweden ,1998.[29] 岑可法,程 军,曹欣玉,等.高温燃烧两段脱硫技术的试验研究[J ].动力工程,2000,20(6):911~915.作者简介: 范红宇(1978-),男,河南镇平人,博士研究生,1999年毕业于石油大学(华东)油气储运工程专业,现从事煤的高温燃烧脱硫化学反应机理的研究工作.E -mail :Albert-van @hotmail 1com.Development of sulf ur capture mechanism during coal combustionprocess in different atmosphereFAN Hong 2yu ,CAO Xin 2yu ,ZHOU J un 2hu ,CHEN G J un ,CEN Ke 2fa(Clean Energy and Envi ronmental Engi neeri ng Key L ab of Mi nist ry of Education ,Zhejiang U niversity ,Hangz hou 310027,Chi na )Abstract :In order to promote the low efficiency of calcium based sorbents during coal combustion.A detailed review of the development of sulfur capture mechanism of calcium based sorbents in reducing atmosphere and al 2ternating atmosphere during combustion process of FBC boilers is given ;in addition ,a review is also given on the development of sulfur capture mechanism in oxidizing atmosphere and reducing atmosphere in PCC boilers.Moreover ,some of the most feasible research program are suggested based on current literature.K ey w ords :different atmosphere ;coal combustion ;sulfur capture ;chemical reaction ;mechanism97第1期范红宇等:不同气氛下煤燃烧固硫化学反应机理研究进展。
赤泥对煤炭燃烧固硫作用的研究

赤泥对煤炭燃烧固硫作用的研究论文
引言
燃烧固硫作用是一种重要的碳氧化反应,用于处理能源生产中产生的含硫废气。
为了解决碳氧化反应中固硫反应的特性,本文应用赤泥对煤炭进行研究,以探讨煤炭燃烧固硫反应的机理和规律。
材料与方法
实验中使用煤炭样品,其中灰分主要为低温灰分(低于200℃)。
经过水分定量测定、粒度分析及相对密度测定,将
煤炭样品放入0.02mol/L NaOH溶液中,搅拌均匀,并在
150℃-400℃之间加热6小时,确定煤炭在高温下固定硫含量。
实验中采用激光粉碎器将赤泥粉碎至粒度小于30μm,并将赤
泥与煤炭搅拌均匀,比例为1:10。
采用X射线衍射测试仪测
定赤泥掺入煤炭后的相组成,并在200℃-400℃之间加热6小时,用相对密度测定仪测定煤炭加入赤泥后的固定硫含量。
结果与讨论
实验结果表明,赤泥掺入煤炭后,煤炭的固定硫含量明显增加。
当煤炭掺入赤泥,且加热温度维持在200℃-400℃时,煤炭的
固定硫含量增加最明显,且固定硫含量随加热温度升高而增加。
同时,赤泥与煤炭混合后,煤炭的碳氧化反应特性也有所改变,如电子传递速率增加,反应速度提高,反应前后CO2及SO2
排放量发生明显变化等。
综上,赤泥掺入煤炭可以有效提高煤炭燃烧固硫反应的效率,大大减少燃烧过程中的污染物的排放,为解决能源生产中的碳氧化废气污染提供了新的方案。
结论
本研究表明,赤泥掺入煤炭可以改变煤炭碳氧化反应特性,具有提高煤炭固定硫含量、增加煤炭燃烧固硫反应效率的作用。
因此,采用赤泥可以大大减少燃烧过程中的污染物的排放,有利于保护环境,是一种潜在的可行性技术。
固硫剂的研究现状(国内)

固硫剂的研究现状(国内)
• 石灰石(主要成分是CaCO3)、电石渣(电石厂废渣,主 要成分有Ca(OH)2、SiO2、Al2O3、Fe2O3等)、白泥(含 Sr 的工业废弃物)、CaO,其中CaO 是用石灰石在 900℃下灼 20 分钟制成的。实验表明,白泥和电石渣在1 000~ 1100 ℃时固硫率较高,其中白泥在1 000 ℃时固硫 率高达84.5%,甚至高于CaO 的固硫率。但当温度升高 到1 200 ~ 1 300 ℃时,白泥和电石渣的固硫率迅速降低, 即白泥和电石渣具有较高的低温固硫效果。石灰石在1 000~1100℃时固硫率只有50%左右,而到1200℃以上, 石灰石的固硫率开始明显高于白泥和电石渣。也就是说, 石灰石的高温固硫效果比白泥和电石渣要好。 • 石灰石和电石渣相配合比单一石灰石或电石渣的固硫效果 好,其最佳配比为 40: 60 ~ 60: 40 之间。这两种固硫剂 相配合,在1300℃时不能形成稳定的高温固硫产物,为 此又添加了一些含金属盐或金属氧化物的工业废料,以促 进钙基固硫剂的固硫效果。
•
固硫剂的研究现状(国内)
• 2.固硫剂的研制现状 • 2.1钙基固硫剂 • 试验表明,CaCO3、CaO、Ca(OH)2 三种固硫剂Ca(OH)2 的固硫效果最好,其次是 CaO 和 CaCO3。这和其发生固 硫反应的温度和其颗粒的结构有关。Ca(OH)2固硫反应开 始的温度低(500℃),在500℃即可发生分解反应生成 CaO,固硫反应和煤大部分硫析出的温度区间相吻合,因 此固硫效果好。而CaCO3分解生成CaO所需的温度高, 即900℃才发生煅烧反应,它不能在低温阶段进行有效的 固硫,低温时会有部分SO2随烟气逸出,固硫效果较差。 从固硫颗粒结构上分析,Ca(OH)2分解释放SO2反应速率 高,所以Ca(OH)2固硫效果好于CaO,其最佳固硫温度是 800 ~1000℃。
燃煤固硫剂研究进展
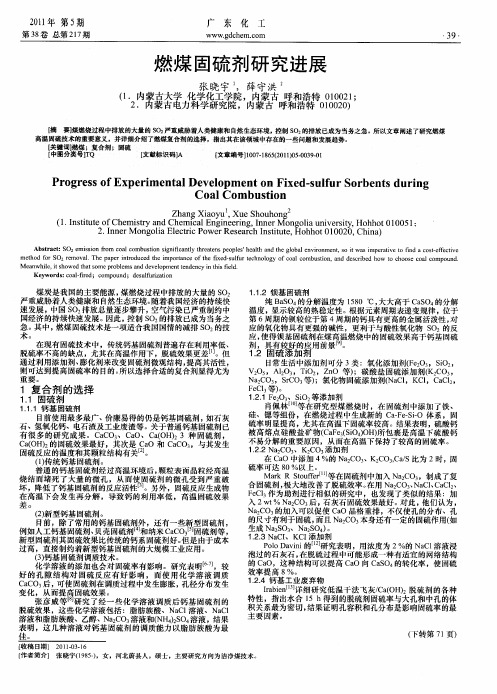
目前 ,除了常 用的钙基 固硫剂外 ,还有一些新型 固硫剂 , 例如人工钙基 固硫 剂、 壳固硫剂 l和纳米 C C 3] 剂等 , 贝 4 a O l固硫 s 新型 固硫剂其 固硫效果 比传统的钙系 固硫剂好 。 但是 由于成本 过高 ,直接制约着新 型钙基 固硫剂的大规模工业应 用。 () 3钙基 固硫剂调质技术 。 化学溶液 的添加也会对 固硫 率有影响 。研究表 明 J ,较 好 的 孔隙结 构对 固硫 反应 有好 影 响 ,而使 用 化 学溶 液调 质 CC 3 , a O 后 可使 固硫剂在 调质 过程 中发生膨胀 , 孔径 分布发生 变化 ,从而提高 固硫效果 。
,
煤炭 是我国的主要能源 , 煤燃烧过程 中排放 的大量 的 S O 严重威胁着 人类健 康和 自然生态环境 。 随着我 国经济 的持 续快 速发展 ,中国 S z O 排放总量逐步攀升 , 空气污染 已严重制约 中 № 国经济 的持 续快速 发展。因此 , 制 S 2 控 O 的排放 已成为 当务之 急 。 中, 其 燃煤 固硫技术是一项适合 我国国情的减排 S O 的技
重要 。
纯 BS 4 a O 的分解温度为 1 8 ℃, 50 大大高于 C S 4 a O 的分解 温度 , 显示 较高的热 稳定性。根据元素 周期表递变规 律 , 位于 第 6周期的钡较位于第 4周期 的钙具有更高 的金属活泼性 , 对 应 的氧化物具有更强 的碱性 ,更利于 与酸性氧 化物 S 的反 Oz 应, 使得钡基 固硫 剂在 煤高温燃烧中的 固硫效果高于钙基 固硫 剂 ,具有较好的应用前景 。 J
Ab t a t 02e si n f m o lc mb si n sg i c n l h e t n e p e ’ e l n h lba e v r n n s t a mp r t e t n o te f ci e s r c :S miso r o c a o u t i n f a t t r ae sp o l s h a t a d te g o l n io me t o i w s i e a i o f d a c s. f t o i y h v i e v
- 1、下载文档前请自行甄别文档内容的完整性,平台不提供额外的编辑、内容补充、找答案等附加服务。
- 2、"仅部分预览"的文档,不可在线预览部分如存在完整性等问题,可反馈申请退款(可完整预览的文档不适用该条件!)。
- 3、如文档侵犯您的权益,请联系客服反馈,我们会尽快为您处理(人工客服工作时间:9:00-18:30)。
・!"・
!%%% 年 & 月
矿业安全与环保
第 !# 卷第 $ 期
和添加剂 /-! 01、230! 组分的型煤样品 4 成型后粉碎 制样 5 在 ’ 1%%6 条件下恒温 1%.37,其固硫率可达 当采用逐渐升温到 ’#% 9 ’ !!%6 , 温度间隔为 ##8 ; ’%6 ,恒温 !:.37,终温为 ’ !%%6 时,固硫率可达 而终温为 ’ !!%6 时, 固硫率仅 1%8 , 另有资 #$8 , 料报道, 采用程序升温时, 230! 、 /-! 01 的协同作用可 大大提高石灰石的固硫效果,而高温恒温条件下反 而降低石灰石的固硫能力。 ’; !; ! 碳酸盐添加剂 碳酸盐类添加剂主要有: <! =01 、 >?! =01、 2@=01 等。在 =?0 固硫剂中添加 $8 的 >?=01 、 <! =01 ( 占 , 固硫率可达 &%8 =?0 的质量百分比) =? A 2 ) ! 时, 以上, 其固硫率提高 ’%8 。在 =?=01 中添加一定量 的 2@=01 , 固硫率也可以提高约 ’%8 。 ’; !; 1 >?=B、 <=B 添加剂 有 >?=C、 <=B 作为 =?=01 或 =?0 的固硫添加剂, 利于提高固硫剂的转化率和转化速率。 在 =?0 中添 加 $8 >?=B( 占 =?0 质量百分比 5 , 加热 =? A 2 ) ! 时, 温度为 ’ %%%6 条件下, 固硫率可达 &%8 以上; 温度 ’ 时, 固硫率约 , 比未加 时提高 ::8 >?=B ’%8 。 %%%6
对以 =?0 为固硫剂, 并加有 =?20$ 和 =?2 或 EG20$ 。 、 添加剂的型煤炉渣进行 —射线衍射分 /-! 01 230! H 析, 证明炉渣中确有 =?20$ 和 =?2 存在。 对加有含 2@ 添加剂的固硫炉渣时行 H—射线衍射分析,发现炉 渣中有 =?20$ 、2@20$ 及 1=?0・1IC! 01 ・=?20$ 晶体 存在。用扫描电镜观察到炉渣中有 /-、 23 成分与 并依附于其表面。 =?20$ 晶体紧密共生, 前述实验及分析结果表明, 型煤固硫机理为: 型 煤燃烧过程中产生的 20! ( 或 201) 在固硫剂内外表 面上发生化学反应,生成 =?20$ 或 =?2 而实现固 硫。但 =?20$ 或 =?2 在高温下易分解而重新释放 在高温燃烧时添加含 /-、 20! 。因此, 23、 2@ 等组分的 添加剂,可使型煤炉渣在高温下形成热稳定性较好 的含硫复盐或生成耐热物相覆盖或包裹含硫物相, 实现高温固硫。 延缓或阻止 =?20$ 的分解, !" $ 型煤固硫模型 或 EG0) 是多孔固体, 其固硫反应 固硫剂 =?0( 是气—固非均相化学反应。 因此, 许多学者将多孔固 体反应模型用于 =?0、 EG0 的固硫研究。 邱宽嵘等建立了 =?0 颗粒的脱硫数学模型。模 型假设 =?0 颗粒尺寸及孔隙率沿颗粒径向为非均 匀分布, =?0 晶粒与 20! 的反应为 “ 未反应核模 ” 型 。整个颗粒的平均反应转化率为: ( "( J. ) ) 1 / ’ % K . ! ・ "( K. , J. ) LK. ") 转化率与孔隙率的关系为: ’ ( !( !. , ". ) ( ’%) ・ "( )’*( $+ ( ’ ) !. , ". ) ’ ( !# 式中 " . —无量纲反应时间; ! . —无量纲颗粒半 径; #—孔隙率; #% —初始孔隙率; $+—固体产物与固 体反应物的摩尔分子体积比。 宋慧英等根据石灰石固硫反应机理及型煤在层 燃炉上燃烧的特点, 建立了层燃型煤固硫模型。 模型 假设固硫剂颗粒与煤均匀混合制成型煤, 煤中硫分 全部以 20! 形态均匀释放, 并被固硫剂颗粒吸收, 空 气恒定从炉底进入并与燃料充分混合后上升, 不考 虑固体颗粒的扬析; 石灰石煅烧瞬间完成等。 经一系列 推导和假设, 最后建立层燃炉烧型煤的数学模型为: ( $ ) "% ) % ) "% ’’) *( ’ ( !) &. ( ’!) &, 式中 $—固硫率; "—转化率; "—平均转化率; %—两相之间混合的度量; %—钙硫摩尔比。
!
型煤固硫剂及添加剂的研究
型 煤 固 硫 剂 的 研 究 主 要 是 围 绕 230 来 进 行 的。常用的固硫剂有石灰石、 白云石、 生石灰、 消石 灰、 电石渣、 白泥等。 固硫添加剂主要有 45! 0)、 6! 0- 、 7!20) 、 83! 20)、 8329、 /:0! 及含 /; 工业废料等。 !" ! 煤燃烧过程中硫的析出规律与固硫剂 煤燃烧过程中硫的析出规律与煤中硫的存在形 态及加热速率等因素有关。我国煤中硫的形态分布 为硫铁矿硫约占 1%. < #%. ,有机硫约占 )%. < $%. ,硫酸盐硫极少。郑瑛等综述了前人的研究成
!
型煤固硫机理及固硫数学模型
煤中硫分在燃烧过程中可能以 D! 2、 =02、 =2! 及 20! 等硫化物形态析出, 但 D! 2 、 =02、 =2! 等气体 在遇到氧气时均氧化成 20! ,同时有少量 20! 进一 步氧化成 201 。因此, 研究型煤燃烧固硫机理基本上 都是以 20! 或 201 为对象,考察其化学反应机理及 固硫物相, 并建立固硫数学模型。 !" # 固硫化学反应 固硫化学反应发生在 20! 或 201 与金属氧化物 之间, 其主要化学反应为: ( E-=01)E-0 * =0! ’) ( ) ( E- 0D ! )E-0 * D! 0 !) ( E-0 * 20! ) E-201 1) ( !E-201 * 0! )!E-20$ $) ( !E-0 * !20! * 0! )!E-20$ :) ( E-0 * 201 ) E-20$ F) ( !E-20$ )!E-0 * !20! * 0! #) — 代表 =? 或 EG 离子。 式中 E-—— 在还原性气氛条件下,气态硫化物几乎在煤粒 表面就与固硫剂结合, 生成 =?2: 〔 〕 ( =?0 * 2 )=?2 * 〔 0〕 &) —— — 煤燃烧产生的气态硫化物; 式中 〔 2〕 〔 —— — 相应含氧产物。 0〕 !" ! 固硫物相及固硫机理 由化学反应知,型煤炉渣中的固硫物相应该是
!%%% 年 " 月
矿业安全与环保
第 !# 卷第 $ 期
工业型煤燃烧固硫的研究进展
! 谌伦建 &, , 赵跃民 &
( 江苏 徐州 !!&%%";!+ 焦作工学院, 河南 焦作 $-$&%%) &+ 中国矿业大学, 摘 要: 对煤中硫分在燃烧过程中的析出规律、 型煤固硫剂、 添加剂及固硫机理的研究进行了综 述, 并分析了影响型煤固硫效果的诸因素, 认为固硫添加剂的主要作用表现在加快固硫反应速率、 提 高固硫剂转化率和形成高温耐热物相、 延缓或阻止硫产物的分解三个方面, 炉温对型煤固硫效果的影 响主要表现在固硫剂表面性质和固硫产物的分解两个方面。 关键词: 型煤; 燃烧; 固硫剂; 添加剂; 固硫机理 中图分类号: 文献标识码: 文章编号: *#%&+ ) , &%%" ( $$’-( !%%%) %$ ( %%!" ( %) 我国 "%. 以上的煤炭用于直接燃烧。 其中电站 工业锅炉及 锅炉燃煤约占全国煤炭产量的 )!+ ). , 窑炉燃煤占全国煤炭产量的三分之一以上。 煤炭的 大量燃烧造成我国大气环境普遍呈煤烟型污染。 目 前, 我国中小型工业锅炉多达-%余万台, 窑炉!%余万 台。 如此众多的工业锅炉及窑炉分散于全国各地, 且 大多燃用灰分、 硫分较高的原煤, 燃烧效率低, 污染 严重。 在 &’’- 年全国排放的 /0! 中, 电站锅炉 /0! 排 放量占))+ $. , 工业锅炉及窑炉占$-+ ". , 民用灶具 其它占’+ !. 。 因此, 控制工业锅炉及窑炉 占&&+ 1. , 的 /0! 排放, 是解决燃煤污染的关键之一。 工业型煤可以有效地降低锅炉燃煤对大气环境 的污染。据资料报道, 固硫型煤固硫率可达 #%. 以 上,可减少烟尘排放量约 1%. ,烟气黑度可降到林 格曼 & 级以下, 并具有一定的固氮作用。因此, 型煤 固硫剂、 固硫机理的研究已引起人们的高度重视, 并 进行了大量的研究工作。 果认为, 在快速加热 ( 条件下, 有机硫析出 & %%%= > ?) 温度为:脂肪族有机硫 #%% < "%%@ ,芳香烃硫约 ’%%@ ,噻吩硫在 ’-%@ 时析出量仍很低。由于试验 条件不同, 黄铁矿硫析出温度无一致结论, 但大多认 为初析温度为 -%% < --%@ , 1%% < "%%@ 时大量析 出。在加热速度较慢( 时, 有机硫析出温度 -@ > A:B) 为 -%% < -1%@ , 黄铁矿硫为 1)% < #%%@ 。 常丽萍等人考察了 45!0) — /:0! 对煤 C / D,E F 其中 /G F "+ &%. , ’+ "). , /? F %+ )&. , /H F &+ $!. ) 燃烧过程中石灰石固硫特性的影响时发现,该煤在 程序升温过程中,硫分解释主要发生在燃烧初期, !%%@ 时开始释放, $%% < -%%@ 时达最大值。 固硫剂种类不同其固硫效果也不一样。 23( 0I) !在 )%% < $%%@ 条件下分解生成 230,当型煤着火燃烧 时就能与 /0! 或 /0) 发生反应生成 23/0$ 。 2320) 在 1%% < ’%%@ 范 围 内 分 解 , 最 大 分 解 率 的 温 度 为 "%’@ 。因此,在 1%%@ 以下石灰石基本上没有固硫 能力, #%%@ 以上固硫率才显著, ’%%@ 以上固硫率增 长缓慢, 超过 & %%%@ 时固硫率下降。 !" # 固硫添加剂 以 230 为型煤的主要固硫成分,生成的 23/0$ 在高温下要发生分解反应,重新生成 230 并释放 /0! 。资料表明,在 & %%%@ 以下, 23/0$ 分解率 在& %%% < & !%%@ , 分解率达!-. ; 而到 & )%%@ &%. ; 时, 分解率超过 -%. 。因此, 高温固硫添加剂及固硫 机理是型煤固硫研究的主要方向。 &+ !+ & 45! 0) 、 /:0! 固硫添加剂 在 230 中添加适量的 45! 0) 、 /:0! 可以提高高温 固硫效果。研究发现, 当加入 %+ 1. 的 45! 0) C 质量含 量 J 时, 固硫率达最高; 当加入 %+ $. 的 45! 0) 时, 23K 同时加入 45、 在 & !%%@ 以 /0$ 分解率最低; /: 组分, 上高温燃烧时, 型煤固硫率仍可达’). , 将含有 230