SEED-DIM3517 硬件用户指南
“TI杯”研究生嵌入式应用技术创新设计作品竞赛章程

“TI杯”研究生嵌入式应用技术创新设计作品竞赛章程一、竞赛组织“TI杯”研究生嵌入式应用技术创新设计作品竞赛由校研究生院、实验室及设备管理处主办,信息科学与技术学院协办,“西南交通大学-QNX/TI轨道交通嵌入式信息技术联合实验室”承办,美国TI公司赞助。
竞赛成立组委会,下设领导小组及工作小组。
竞赛成立以研究生院牵头,由信息学院,电气学院,机械学院,物理学院,牵引动力中心,工业中心等有关院系推举的专家组成评审组。
评审组负责对初赛题目的评选,竞赛过程的监控,以及最终竞赛作品奖项的评定。
二、竞赛方式及内容本次竞赛不限定题目和范围,不设置竞赛场地,竞赛分初赛和决赛两个阶段。
初赛阶段进行方案设计,将评选出不超过30个设计题目进入决赛阶段。
决赛阶段进行实物设计制作。
成功通过最后作品测试的参赛队可以报销一定额度的低值耗材费。
自行设计加工含嵌入式处理器PCB电路板(板上需刻印参赛队标识)的不超过1500元/组;采用开发板扩充部分硬件电路的不超过800元/组;以标准接口形式扩展部分硬件功能的不超过400元/组。
耗材费说明:耗材费要求参赛队在提交作品初赛设计方案时同时提交,包括耗材用途、规格型号、数量单价等预算。
费用必须如实申报,虚报将被取消资格。
对于价值50元以上的器件由竞赛组统一购买。
零星小额竞赛耗材需学生先行垫支,作品经最后验收后予以报销。
如果学生在制作过程中放弃,所支出费用需自行承担。
竞赛内容应以各类嵌入式系统应用课题为设计目标,倡导面向经济主战场及面向实际应用的创新性设计理念,设计作品的题材和范围没有限制,鼓励原创性作品。
以下情形可以获得加分:(1)针对轨道交通的应用设计作品(2)直接面向企业或社会民生需求具有实用价值的作品(3)针对设计内容获得专利或在核心期刊发表论文的作品最终的设计作品一定是符合设计目标且可演示的实际系统,包括软硬件一体的应用系统或者是运行于某个嵌入式平台下的嵌入式应用软件。
竞赛作品评奖的侧重点是创新性,实用性,同时兼顾性价比。
1014539rev2_AM3517_DevKit_Usr Manual

™Zoom™ AM3517 EVM and eXperimenter Development KitsUser ManualLogic // ProductsPublished: November 2009Last revised: February 2010This document contains valuable proprietary and confidential information and the attached file contains source code, ideas, and techniques that are owned by Logic Product Development Company (collectively “Logic’s Proprietary Information”). Logic’s Proprietary Information may not be used by or disclosed to any third party except under written license from Logic Product Development Company.Logic Product Development Company makes no representation or warranties of any nature or kind regarding Logic’s Proprietary Information or any products offered by Logic Product Development Company. Logic’s Proprietary Information is disclosed herein pursuant and subject to the terms and conditions of a duly executed license or agreement to purchase or lease equipment. The only warranties made by Logic Product Development Company, if any, with respect to any products described in this document are set forth in such license or agreement. Logic Product Development Company shall have no liability of any kind, express or implied, arising out of the use of the Information in this document, including direct, indirect, special or consequential damages.Logic Product Development Company may have patents, patent applications, trademarks, copyrights, trade secrets, or other intellectual property rights pertaining to Logic’s Proprietary Information and products described in this document (collectively “Logic’s Intellectual Property”). Except as expressly provided in any written license or agreement from Logic Product Development Company, this document and the information contained therein does not create any license to Logic’s Intellectual Property.The Information contained herein is subject to change without notice. Revisions may be issued regarding changes and/or additions. © Copyright 2010, Logic Product Development Company. All Rights Reserved.Revision HistoryREV EDITOR DESCRIPTION APPROVAL DATE1 JCA, MB, MT Initial Beta release MB 11/05/092 JCA -Section 2.1: Moved step for connecting USB camera after poweringon the kit RGL 02/12/10Table of Contents1Introduction (1)1.1Scope of Document (1)1.2Requirements (1)2Demo Application (2)2.1Running the Demo Application (2)2.2Exiting the Demo Application (2)3eXperimenter Baseboard (3)3.1eXperimenter Baseboard Features Diagram (3)3.2eXperimenter Baseboard Ethernet Jack (3)3.3DIP Switches (3)4Application Board (5)4.1Application Board Features Diagram (5)4.2Connect the Application Board (6)4.3Application Board Feature Usage (6)4.4Application Board Ethernet Jacks (6)4.5User Interface Buttons (6)5Connect the Wi-Fi Antenna to the SOM-M2 (6)6Using USB/UART Serial Debug Interface (7)6.1VCP Driver Installation (7)6.2Before Using (8)6.3Additional Notes (8)7Install Software (8)7.1Install CodeSourcery (9)7.2Install AM35xx BSL (9)8Board Support Library (BSL) Sample Programs (9)8.1Connect Development Kit to PC (9)8.2Run the Test Menu (9)9Linux Software DVD (10)Appendix A: Additional Documentation (11)1 IntroductionThis User Manual provides example usage instructions for the Zoom AM3517 EVM andeXperimenter Development Kits.1.1 Scope of Document■This User Manual is written for both the Zoom AM3517 EVM Development Kit and the Zoom AM3517 eXperimenter Kit. Where differences exist, a note within the text will explain thedifferences.■This User Manual references specific connectors on the eXperimenter baseboard and application board. However, the discussion is limited to special use instructions; detailedinformation about the connectors should be referenced on the respective schematic and Billof Material (BOM) documents. See Appendix A for links to these documents.■This User Manual does not provide detailed instructions for the software included with the kits. Please refer to the specific User Guides for each respective software product foradditional information. A list of additional documentation is available in Appendix A.1.2 Requirements■It is assumed that the associated QuickStart Guide has been read in its entirety. See Appendix A for links to the QuickStart Guides.■ A development PC with CD drive, USB port, and at least 2 GB of hard drive space.2 Demo ApplicationThe AM3517 Development Kits ship with a demonstration application in flash memory. This demo application displays a spinning OpenGL ES cube on the 4.3” LCD. If a UVC compliant USBwebcam is connected to the Development Kit, the video from the webcam will appear on thecube’s surfaces.2.1 Running the Demo ApplicationTo use a USB webcam with the demo application, please follow these steps.1. Please check http://linux-uvc.berlios.de for a list of UVC compliant USB webcams. TheLogitech webcam Pro 9000 with P/N 860-000109 and another Logitech model withP/N 860-000107 have been tested successfully with the demo. (Please note that the P/N ison the webcam cord, not the one on the webcam box.)2. Connect the 4.3” LCD to the eXperimenter baseboard.3. Connect the power cord to the eXperimenter baseboard.4. Power on the Development Kit.5. If this is the first time the Development Kit has been powered on, please be aware that thekernel may take up to two minutes to boot as the demo application file system is created.This delay only occurs the first time the kit is booted.6. The demo will launch and a spinning, multi-colored OpenGL ES cube will show on the 4.3”display.7. Connect a UVC compliant USB webcam to the USB host port on the eXperimenterbaseboard; the surfaces of the cube should now display the webcam video instead of thescrolling color bar.2.2 Exiting the Demo ApplicationTo quit the demo, do the following:1. Login at the terminal by typing “root” and pressing the Enter key. NOTE: When the demo isrunning, the terminal is updated in real time with the video frame rate and the CPU load. As aresult of this real time updating, text typed at the terminal prompt may appear distorted. Thisis expected as long as the demo is running and does not affect the commands you aresending through the terminal.2. In the terminal window, type “ps” and press the Enter key.3. In the list that is output, identify the process ID (PID) of the “./bccube” process.4. Type “kill ####” where #### is the process ID identified above and press the Enter key.5. Once the demo has stopped, the Linux prompt will be presented.3eXperimenter Baseboard 3.1 eXperimenter Baseboard Features DiagramRS232 serial debug port 60-pin LCD headerUSBOTG port USB host port Power-in jackPower switchGeneral purpose user DIP switches (S2) Boot mode / peripheral DIP switches (S7)USB/UART serial debug port SD/MMC1 card slot (bottom of board) HDMIvideo-out System user button (left) System reset button (right) Above buttons: User LED1 (left) User LED2 (center) Power LED (right) 3.2 eXperimenter Baseboard Ethernet JackThe Ethernet jack located on the eXperimenter baseboard is used with the RMII PHY on the SOM and the Ethernet MAC built in to the AM3517 processor; whereas the Ethernet jacks located on the application board are completely independent. It is possible to use the baseboard Ethernet jack and the application board Ethernet jacks simultaneously if supported in software with multiple Ethernet drivers loaded.3.3 DIP SwitchesThere are two 8-position DIP switches located on the eXperimenter baseboard at reference designators S2 and S7. By default, all of the switches are set to the “OFF” position.The S2 DIP switch is reserved for user application general purpose. The S7 DIP switch controls the processor’s boot mode, IO voltage, and some peripherals on the baseboard. Table 3.1 describes the function of each switch.Table 3.1: S7 DIP Switch FunctionsSwitch OFF Position ON PositionS7:1*BOOT[0]S7:2 BOOT[2]S7:3 ReservedS7:4 BOOT[5]S7:5 ReservedS7:6 ReservedS7:7 AM3517 I/O runs at 3.3V AM3517 I/O runs at 1.8VS7:8 HDMI transmitter disabled HDMI transmitter enabled*Note: S7:1 indicates slide 1 on the S7 DIP switch, S7:2 indicates slide 2 onthe S7 DIP switch, and so on.A default boot mode has been defined by pulling all boot pins (SYS_BOOT[0:5]) to a default state on the SOM. The default boot mode is NAND flash; all available boot modes are described in Table 3.2.Table 3.2: S7 DIP Switch Boot ModesBoot Sequence BOOT[5]BOOT[2]BOOT[0] S7:4 S7:2 S7:1Default NAND, EMAC, USB MMC1 OFF OFF OFFEMAC, USB, MMC1, NAND ON OFF OFFXIP, USB, UART, MMC1 OFF OFF ONUSB, UART, MMC1, XIP ON OFF ONXDOC, EMAC, USB, EMAC OFF ON OFFUSB,XDOC ONONOFF MMC2, EMAC, USB, EMAC OFF ON ONUSB,MMC2 ONONON4 Application BoardThe application board provides connectors to evaluate additional features beyond those built into the baseboard; it is only necessary to connect the application board when these additional features are required.NOTE: This section only applies to the Zoom AM3517 EVM Development Kit.4.1 Application Board Features DiagramCAN headersVideo out headerComponent video input jack SD/MMC2 card slot (bottom of board)Wireless daughterboard connectorWireless daughterboarddebug / test connectors &headphone & line in jacks4.2 Connect the Application Board1. Make sure your AM3517 EVM Development Kit is powered off.2. Align the application board over the three BTB expansion connectors on the eXperimenterbaseboard. Please refer to the diagram in Section 3.1 for the location of the connectors.3. Press straight down on the application board, applying even pressure over the threebaseboard BTB expansion connectors.4. Visually verify that the BTB expansion connectors on the Application board and baseboardhave mated correctly.5. Four screws and nuts are included with the kit to secure the application board to thebaseboard; a Phillips #1 screwdriver is required (not included). Secure the screws throughthe board holes with the nuts on the bottom side of the boards. IMPORTANT NOTE: Onlyfinger tighten the screws. Over-tightening the screws may permanently damage the boards.6. To disconnect the application board: remove the screws holding the boards together and thenpull up on the board above the BTB expansion connectors. Attempt to pull straight up andrefrain from flexing the PCB to avoid damaging the application board.4.3 Application Board Feature UsageSome of the components on the EVM kit run off the same bus, so not every feature can be used at the same time. The following features are mutually exclusive of each other since they shareMMC2:□SD/MMC2 card slot located on the application board□Wireless daughterboard connector located on the application board□Wi-Fi module located on the SOMThe wireless daughterboard interface can be enabled or disabled by switch S11:4 on theapplication board. The other features are controlled through software. This is something to takeinto consideration if intending to use the application board with custom software for the SOM.In addition, the application board supports composite, component, and S-Video analog videoinputs, as well as a camera digital input. All input devices may be connected simultaneously, but only one video input device may be selected at a time. The selection between any analog inputand the camera input is made with switches S11:1 and S11:2 on the application board. Thechoice of analog input is controlled through software.4.4 Application Board Ethernet JacksThe Ethernet jacks located on the application board are connected to the SMSC LAN9311Ethernet chip on the application board. This chip connects to the processor GPMC bus and isindependent of the Ethernet jack located on the baseboard.4.5 User Interface ButtonsTen user interface buttons are available on the application board to interact with software. All of the buttons run through an I/O switch controlled by I2C. Five of the interface buttons are alsoconnected in parallel with a five-way navigation knob.5 Connect the Wi-Fi Antenna to the SOM-M2NOTE: This section only applies to the Zoom AM3517 EVM Development Kit.The antenna included with the AM3517 EVM Development Kit provides reception for 802.11b/gEthernet or Bluetooth signals. Only connect the antenna if 802.11 Ethernet or Bluetooth isrequired for your demo or development efforts.1. Insert the RF cable into the antenna and tighten the screw nut.Figure 5.1: Assemble Antenna2. Connect the antenna to the SOM-M2 reference designator J4 for 802.11 Ethernet andBluetooth reception. See Figure 5.2 for the antenna connector location on the top of theSOM-M2.Figure 5.2: Antenna Connector Location on SOM-M26 Using USB/UART Serial Debug InterfaceIf your computer is not equipped with a COM port, the eXperimenter baseboard allows for theoption of using the USB B device as a virtual COM port (VCP). In order to use this feature, you must first download and install the VCP chip driver on your computer.Please review the FTDI website to make sure your computer meets recommended specifications for the FT232R device (/Products/FT232R.htm).6.1 VCP Driver InstallationThe following are brief instructions for installing the FT232R VCP driver. For more detailedinstructions, please review the documentation on FTDI's site(/Documents/InstallGuides.htm).1. The VCP driver is available for download from FTDI's website. A link is available in theintroduction above or on Logic's product downloads page. (NOTE: There may be multipledrivers available on the FTDI website for this device; only the VCP driver is required.)2. The driver will be downloaded as a ZIP file which must be unzipped before the driver can beinstalled.3. If running Windows XP SP1, please refer to the "Windows XP Installation Guide" located onthe FTDI website for special precautions to observe while installing the driver.4. Plug the USB cable into a USB port on your computer and the USB B device on thedevelopment kit. The Windows XP "Found New Hardware Wizard" will automatically appear.(NOTE: The USB A to B cable is only included with the EVM Development Kit. ForeXperimenter Kit users, a USB A to B cable is commonly available for purchase at a widevariety of retailers.)5. When prompted to allow Windows to search for the driver, select "No not this time."□Install from a list or specific location (advanced)□Browse to the location of the unzipped folder containing driver.□The installation process should complete by itself with a message stating "USB Serial Converter successfully installed."6. A Windows XP Found New Hardware Wizard window will open for a second time. Followsame procedure as Step 5 above. This installation process should complete by itself with amessage stating "USB Serial Port successfully installed."7. Your system should now recognize the new hardware.8. If you encounter any problems during this installation, please refer to FTDI's website fortroubleshooting recommendations.6.2 Before Using■Go to the Device Manager on your computer to determine what COM port is associated with the USB/Serial Port.■Set up the serial configuration as described in the corresponding QuickStart Guide.6.3 Additional Notes■When using this feature, the DB9 Serial Port on the baseboard is disabled whenever the USB cable is connected to the USB B port.■The power supply included with the development kit needs to be plugged into an electrical outlet for the USB device to be recognized by the computer. However, the development kitdoes not need to be powered on for the device to be recognized.7 Install SoftwareThe AM3517 Development Kits include a Board Support Library (BSL) that allows for interaction with the AM3517 EVM or eXperimenter Kit and helps with diagnostics. This BSL is provided on a software CD included with the EVM Development Kit or as a download for the eXperimenter Kit.The BSL works in conjunction with toolchains from CodeSourcery which must be installed on the development PC prior to using the BSL.7.1 Install CodeSourceryThe AM3517 EVM Development Kit includes a DVD with an evaluation version ofCodeSourcery’s Sourcery G++ Professional Edition. The Professional Edition is designed forenterprise software development and includes the GNU Toolchain, the Eclipse IDE, and othertools to build software. More information is available on CodeSourcery’s website/sgpp.For interaction with the BSL and the instructions within this User Manual, all that is required is a command-line tool. CodeSourcery provides a free, command-line only Lite Edition of SourceryG++; we will use the Lite version in these instructions.1. Download the recommended release of “Sourcery G++ Lite for ARM EABI” fromCodeSourcery’s website: /sgpp/lite/arm/portal/subscription3053(NOTE: These instructions were tested using version 2009q3.)2. Double-click on the downloaded executable to launch the installer.3. Follow the on screen instructions. When you arrive at the screen for type of installation, select“Typical.”7.2 Install AM35xx BSL1. Insert the “AM3517 BSL” software CD into your development PC or download the ZIP filecontaining the AM35xx BSL files from Logic’s website2. If using the CD, copy the contents of the CD to a directory of your choice on the developmentPC. Otherwise, unzip the download and place the contents in a directory of your choice onthe development PC.3. Read the BSL_ReadMe.txt file for documentation on the BSL.8 Board Support Library (BSL) Sample ProgramsThe BSL sample programs are included to test the different features of the development kit and diagnose any potential problems. In order to run these tests, you first have to connect yourdevelopment kit to a PC.8.1 Connect Development Kit to PCConnect the development kit to your PC by using the provided serial cable and following theinstructions in the QuickStart Guide or by using a USB A to B cable and following the instructions in Section 6 of this document.8.2 Run the Test MenuAs an example, we will run the test menu that works for both development kit types. In order torun a test program, you will have to select the program, compile (or build) the program, and then load the compiled program. The following steps will walk you through that process.1. Open a command prompt on your development PC and navigate to the .\tests\test_menu\csfolder, located in the directory where you installed the BSL.2. Compile the program by typing “cs-make” at the command prompt.3. This will create a “test_menu.raw” file in that same folder.4. U-Boot is installed in NAND flash on the SOM and will be used to load the program.5. Open Tera Term and select the serial COM port connected to your development kit.6. Power on the development kit.7. When prompted, press any key to stop the autoboot process.8. Load the test menu program by typing “loadb” at the U-Boot prompt.9. If using Tera Term, transfer the file by selecting “File ->Transfer -> Kermit -> Send...” from themenu heading. Locate and then select the “test_menu.raw” file. Click “Open” to send the file.NOTE: This requires Tera Term version 4.63. If you are not using TeraTerm, please read thedocumentation for your terminal emulator about using the Kermit protocol to transfer a file.10. After the program finishes loading, type “go 0x82000000” and press the Enter key.11. Run a test by typing in the test number and pressing the Enter key. For example, type “5” torun the LED, DIP Switch test. This test will flash LEDs in different patterns depending on theS2 switch moved and will output the switch number positions.12. All of the tests listed under “experimenter” can run on both types of development kits; thetests under “evm” can only run on the AM3517 EVM Development Kit.9 Linux Software DVDThe Texas Instruments’ Linux DVD included with the AM3517 EVM Development Kit contains an early release of software for the AM3517. Please refer to the GettingStarted-PSP.pdf file on the DVD for instructions on using the DVD contents and where to go for software updates.Appendix A: Additional DocumentationSoftware Documentation■ U-Boot documentationhttp://www.denx.de/wiki/U-Boot/WebHomeHardware DocumentationAll of the following links are also available on your “My Account” page on the Logic website (/auth/).■ Logic Zoom AM3517 EVM QuickStart Guide/downloads/1255/■ Logic Zoom AM3517 eXperimenter QuickStart Guide/downloads/1256/■Logic AM3517 eXperimenter Baseboard BOM, Schematic, and Layout/downloads/1239/■Logic AM3517 Application Board BOM, Schematic, and Layout/downloads/1240/■Logic AM3517 SOM-M2 BOM, Schematic, and Layout/downloads/1238/■ Logic AM35x SOM-M2 Hardware Specification/downloads/1257/。
Sarix IMP 系列室外迷你球机使用手册说明书

C3956M-CN (10/13)Sarix ®IMP 系列 室外迷你球机 使用手册2目录重要声明 (5)使用须知 (5)广播和电视信号的干扰 (5)法律提示 (5)视频质量警告 (5)选择帧率注意事项 (5)开放源代码软件 (6)关于CCC 电源线的声明 (6)KCC 认证 (6)Korean Class A EMC (6)Korean Class B EMC (6)ESD 警告 (6)网络拓扑结构声明 (6)法律提示(关于音频使用) (6)前言 (7)1.产品概述 (8)1.1 尺寸大小 (8)1.2 外形特征 (9)2.安装和连接摄像机 (10)2.1 标准配备 (10)2.2 可选附件 (10)2.3 安装 (10)2.3.1 检查外观 (10)2.3.2 拆卸摄像机 (11)2.3.3 连接配线 (11)2.3.4 安装摄像机 (11)32.3.5 调整摄像机拍摄位置 (16)2.3.6 调整焦距 (16)2.3.7 网络布局 (17)2.3.8 系统需求 (17)2.4 连接摄像机 (18)2.4.1 默认IP地址 (19)2.4.2 连接电脑&图像查看准备 (19)3. 管理和配置摄像机 (20)3.1 实时显示 (20)3.2 设置 (22)3.2.1 系统 (22)3.2.2 网络 (25)3.2.3 图像 (33)3.2.4 A/V 数据流 (39)3.2.5 用户 (44)3.2.6 事件 (47)技术参数 (57)Pelco故障诊断联系信息 (60)关于产品尺寸图的说明 (60)重要声明使用须知该设备遵照FCC章程第15项条款制造。
操作本设备必须遵循以下两个条件:(1)不对周围环境产生有害干扰。
(2)该设备须接受任何收到的外部干扰,包括可能影响该设备正常工作的干扰。
广播和电视信号的干扰根据FCC章程第15项,本设备经过测试,符合数码设备A级标准。
这些标准为在居民区安装提供了有效的保护,该设备会产生、使用、和发射电磁波,如不按照说明书安装使用,可能会对无线电通信造成干扰。
SEED-DIM3517 Linux BSP 移植及使用指南
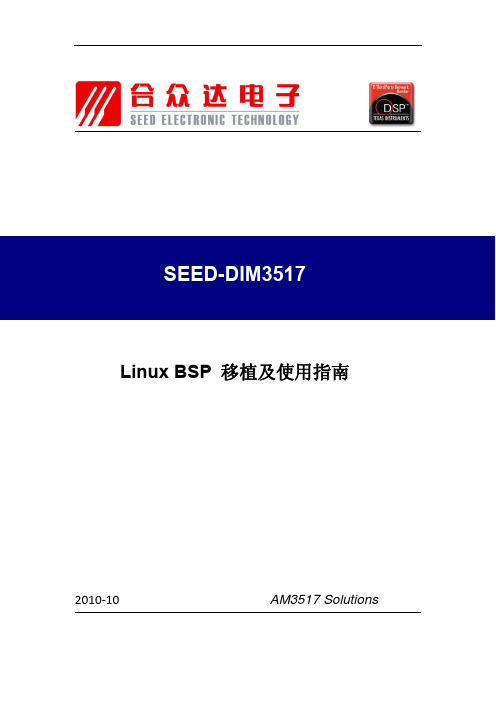
本板卡包含 ESD 敏感器件,请采取适当的预防措施。使用时请不要用手或非 绝缘的物体接触板卡。因使用不当造成的板卡损坏,本公司只提供付费的维 修。 本文中所有类似的警告标识,表明此部分内容有可能损害您的软件、硬件或 其它设备。这个信息谨慎的为您提供保护,请仔细阅读阅读。
商标
SEED 是北京合众达电子技术有限责任公司的注册商标。 TI 是 Texas Instruments 的注册商标。
1-1
SEED-DIM3517 LINUX BSP 移植及使用指南
第2章
Linux 开发环境
2. Linux 开发环境
SEED-DIM3517 Linux 开发环境通常包括 Linux 服务器、Windows 工作台及 SEED-DIM3517 平台三者处于同一个网络中,如下图示:开发工程师在 Linux 服务器上建立交叉编译环境,Windows 工作台通过串口和 JTAG 与 SEED-DIM3517 开发平台连接,开发人员可以在 Windows 工作进行程 序开发或者远程登陆到 Linux 服务器进行开发。
简介
本手册是基于 AM3517 系统解决方案板卡 SEED-DIM3517 的软件使用说明书,详细描述了 源码包软件镜像的编译等内容。
保修
所有由北京合众达电子技术有限责任公司生产制造的硬件和软件产品,保修期为从发货之 日起壹年。在保修期内由于产品质量原因引起的损坏,北京合众达电子技术有限责任公司负责 免费维修或更换。保修期内软件升级,北京合众达电子技术有限责任公司将免费提供。
注:/opt/Tools/arm-2009q1/为用户编译器安装路径
修改完毕如下图所示:
1
SEED-DIM3517 LINUX BSP 移植及使用指南
无人直升机操作手册
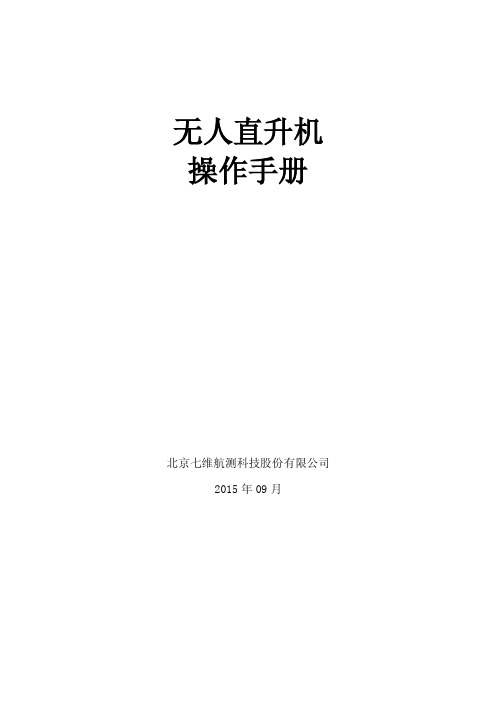
北京七维航测科技股份有限公司 2015 年 09 月
北京七维航测科技股份有限公司
Beijing SDi Science&Technology Co.,Ltd.
目录
第一章 系统使用注意事项 ................................................................................................. 4 一、警告 ............................................................................................................................ 4 二、飞行注意事项 ........................................................................................................... 4 1、空管 ..................................................................................................................... 4 2、飞行区域 ............................................................................................................. 4 3、电磁环境 ................................................................................
乌斯特QUANTUM清纱器设备使用操作说明书
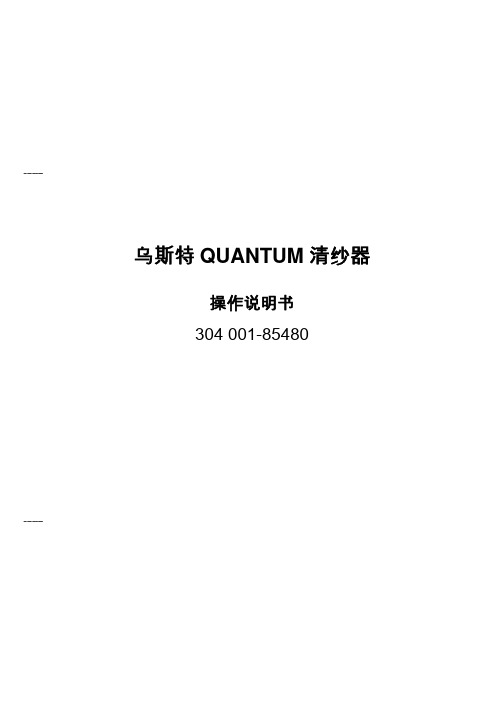
领班级
12
[M] = Polykey inserted
无钥匙插入/无密码输入
- 所有显示都可进入
- 若有钥匙符号显示则意味着只有在进入了领班或客户服务授权后
才能进行更改。
Password
[O] = Password entered
123
可以改变设定。
客户服务级 Password: 6281
[S] = Password entered
异形纤维清除:能清除浅色纱中的深色异纤;深色纱中的浅色异纤.
Q-Data(质量参数): 进行纱疵分级, 测量纱线的不均匀度,测量纱疵的 散点图.
Cone Expert 用于几台 QUANTUM 清纱器的集中设定和评估,可大大减 少完成这些任务所需的时间。
CAY (计算机辅助清纱) 用于自动优化设定清纱曲线.
钮自动跳出 - 打结机在该锭位上不再工作,从其旁边经
过.
消除纺织报警: - 直接按 iMK 按钮或在控制箱上删除报警 - 按红色按钮 - 打结机再次在该锭位上工作.
技术报警 技术报警显示: - iMK 检测头 LED 每秒闪烁一次. - 每次打结后 iMK 检测头切割一次 - 当达到循环的设定次数时,红灯亮且红色按
3
1
A
B
C
D
E
F
G
F1 F2 F3 F4 F5 F6 LF
H
I
J
K
L
M
N
7 8 9 / F Ins Del
O
P
Q
R
S
4 5 6 - Esc
T
U
V
W
123+
Enter
2
X
迪拜狗MINI NDI编码器和解码器用户指南(2018年12月)说明书

USER GUIDE | DECEMBER 2018MINIWELCOME TO THE FUTURE.4. GETTING TO KNOW MINIPhysical connectorsPowering Mini PoE (Power over Ethernet)DC/D-TapThermal management5.POWERING ON SEQUENCEIndication of system boot processOPERATING MINIWeb configuration panelAccess via web browser (URL)BirdDog Finder applicationAccessing Mini via an IP address Accessing Mini on a network without a DHCP server6.PASSWORD MANAGEMENTDefault passwordPassword resetCONFIGURING VIDEO INPUTSAutomatic input7.Semi-automatic inputManual input8.AUDIOEnabling or disabling AudioAudiosetup 8.NDI DECODE OPERATIONChanging modes from NDI Encoder to NDI Decoder Selecting an NDI source to decodeChanging back to NDI Encode operation 10.NETWORK SETTINGS AND DEVICE NAMING Device namingIP configuration methodDHCP IP addressStatic IP address11.TALLY SUPPORTOnboard TallyProgram TallyPreview TallyTally border overlay on loop12.FACTORY RESETSettings resetFIRMWARE UPDATE13.RECEIVING MINI STREAMSNewTek Studio MonitorNewTek TriCaster SeriesMINITHE WORLD’S SMALLEST NDI ENCODER AND DECODER.GETTING TO KNOW MINIThanks for purchasing BirdDog Mini. Please take some time to read this document to allow you to get the most out of your purchase and familiarize yourself with the features available in the unit.Physical connectors1. LED Indicator2. 1Gb Ethernet (Power over Ethernet)3. HDMI Input4. HDMI Output5. Audio Headset connector6. DC Input (5-18v DC)7. Reset SwitchPowering MiniMini is equipped with a sophisticated system allowing power from various sources:PoE (Power over Ethernet)PoE is a convenient way to power Mini as it allows both data and power to be sent through the same standard Ethernet cable. To take advantage of PoE, the network switch that Mini is directly plugged into must support PoE, in either 802.11at or 802.11af standard.Different network switches are capable of providing differing amounts of total power to all connected devices. Mini uses approximately 7 watts in PoE mode.DC/D-TapLocated at the side of Mini is a DC connection port. This power input socket is capable of accepting power in a range of voltages from 5–18 volts DC. Mini can be powered by the included AC adaptor or alternatively via the optional D-Tap cable to power using a D-Tap compatible battery.Thermal managementMini has been engineered to be passively cooled, no fans are required. In order to achieve this the entire enclosure of Mini is designed to dissipate heat. The main processor is capable of operating up to 100º C / 212 degrees Fahrenheit.Some factors affect how much heat BirdDog will produce, and it is normal for it to feel warm to the touch.In extreme circumstances (a hot day/direct hot sun) it is advised to power Mini via DC or D-Tap as this producesless heat than PoE.BirdDog has been tested in extreme environments.BOOTING UP YOUR BIRDDOG MINIIndication of system boot processAs soon as BirdDog Mini detects a power input signal the left hand 'power/fault' light will light up green.1Typically the status will change after 10-20 seconds, at thispoint the middle 'status' light will light up blue to indicate The final stage of booting will show the status light change to white indicating the BirdDog is ready and able to be found on the computer network.3After initial boot up is complete your Mini unit will be visible as a source on any NDI compatible devices on the SAME ethernet subnet.For further networking architecture instructions including OPERATING MINIWeb configuration panelIn this release, the web configuration panel allows you to alter key settings of Mini, specifically video source settings, and video frame rates, restarting the video processing engine, changing networking parameters, and applying firmware updates.Access via web browser (URL)To access the web configuration panel please point your computer web browser to: http://birddog-xxxxx.local/“xxxxx” is the serial number of the Mini, the serial number is printed on the box and on the main unit. Note the web address is case sensitive and should be all lower case. Your computer will need to have ‘Bonjour’ services loaded in order to access the unit via it’s ‘friendly’ name described above.Apple devices come pre-installed with Bonjour, while Windows devices need a small plugin available here:https:///kb/dl999?locale=en_AUBirdDog Finder applicationIn addition to typing this URL in manually there is an applica-tion: BirdDog Finder, which is available from /firmware-updates . This application looks on the local network for any NDI capable Mini and launches the web configuration interface directly from the application.Accessing Mini via an IP addressMini is configured to automatically receive a network (IP) address from the computer network via DHCP (Dynamic Host Configuration Protocol). Most corporate, education and home networks have a DHCP server present on the network to allow this to occur. Usually your Internet Router provides this.If Mini receives an IP address automatically from this server (DHCP) the IP address can be discovered in several ways, including the BirdDog Finder application available from: /firmware-updatesAccessing Mini on a network without a DHCP serverSome standalone or private networks may not have a DHCP server. After 15 seconds of searching for an automatically assigned IP address Mini will fall back to a default address which is:192.168.100.100In order to access the web configuration panel on a network which is configured to a different subnet, change your computers IP address to match the BirdDog unit. Once you gain access to the BirdDog web configuration panel choose your IP address to match the rest of the devices on your network.For instructions on setting your computers IP address please consult your computer operating system manual or IT support resources.Note: only the last 5 digits are required for accessing the web interface.PASSWORD MANAGEMENTOnce you direct your web browser to the web configuration panel you will need to log in to change any settings.Default passwordThe web configuration panel is secured by a user-selectable password. The default password is: birddog (one word, lower case).It is recommended to change this password in a network environment where Mini is shared with other users (e.g. not private). By entering this password, the user is granted full access to the Mini configuration settings and could interrupt a live program.To change the password simply login using the default password, navigate to the network tab in the web interface, and select change password.Password resetIf you lose or forget your password, you must reset the Mini to factory settings, which will allow logging back in using the default birddog password. Please see page 12 for instructions.CONFIGURING VIDEO INPUTSAutomatic inputMini will search for any active video input on startup. It will continue to search until an active input is found.Please note that the source from your camera or video device needs to be in a supported video format.Please check firmware release notes for list of supported video formats.MINICurrent video input:Audiosetup:Mute:Tally:Input selection:DASHBOARD NETWORK CONFIG. SYSTEM LOGOUTMINIManual inputManual input configures Mini to only look at the selected video source for a specific video format and color space.This can be useful if your source is not correctly detected by Mini.BirdDog has taken as much care as possible to ensure any source is automatically detected in the correct format, however some cameras may send nonstandard timing signals or incorrect metadata. In this case please configure Mini with manual input to enable correct operation and report your camera model and video format to BirdDog so it can be added to the list of supported cameras.Current video input: Audiosetup: Mute:Tally:Input selection: Input:Configuration:DASHBOARD NETWORK CONFIG. SYSTEM LOGOUTMINICurrent video input: Audiosetup: Mute:Tally:Input selection: Input:Configuration: Format: Framerate: Colorspace:DASHBOARD NETWORK CONFIG. SYSTEM LOGOUTMINIAUDIOEnabling or disabling AudioMini can be configured to process embedded audio from SDI or HDMI from within the web configuration console. This setting is located in the Video section of the console and operates in the following way:Audio Mute ONAudio is not passed through embedded SDI or HDMI.Audio Mute OFFAudio is passed through the embedded SDI or HDMI input and streamed to the NDI receiver.Current video input:Audiosetup:Mute:Tally:Input selection:DASHBOARD NETWORK CONFIG. SYSTEM LOGOUTMININDI DECODE OPERATIONChanging modes from NDI Encoder to NDI DecoderBirdDog can operate in either NDI Encode (converting from HDMI to NDI) or NDI Decode (receiving an NDI signal from the network and displaying it out the HDMI ports). To change modes from the default NDI Encoder mode into NDI Decode navigate to the CONFIG. section of the web interface.Select DECODE mode from the selection box and press REBOOT DEVICE.N ote that you must reboot the BirdDog unit once a new operating mode is selected, dynamically switching will be added in an upcoming firmware release.CURRENT OPERATION MODE (Change requires reboot)Current Source Available SourcesAPPLYDECODE REBOOT DEVICEDESKTOP-EVS0MMNDESKTOP-EVS0MMDASHBOARD NETWORK VIDEO SYSTEM LOGOUTMINISelecting an NDI source to decodeOnce your BirdDog device has entered NDI decode mode and successfully rebooted, you are able to select the source that you wish to decode via the web interface.All available sources are listed in the drop down menu in the CON FIG. section of the web interface, select the desired source and press APPLY to begin receiving this source.Once your BirdDog unit is in Decode mode you can switch between any available sources on the network by choosing them from the drop down menu and pressing APPLY again.Note. BirdDog can only decode video format and frame rate sources, these formats are the same as what BirdDog capable of encoding. If you are unable to successfully receive a source, please double check that the video format and frame rate are ones that are supported by your unit.Changing back to NDI Encode operationT o change modes from N DI Decode mode back into N DI Encode navigate to the CONFIG. section of the web interface.Select EN CODE mode from the selection box and press REBOOT DEVICE before APPLY .Note. You must reboot the BirdDog unit once a new opera-ting mode is selected, dynamically switching will be added in an upcoming firmware release.CURRENT OPERATION MODE (Change requires reboot)Current Source Available SourcesAPPLYENCODEREBOOT DEVICEDESKTOP-EVS0MMNDESKTOP-EVS0MMDASHBOARD NETWORK VIDEO SYSTEM LOGOUTMINIIP configuration methodYou can configure Mini to operate on the network with a dynamic (DHCP) IP address or a fixed address.For smaller networks DHCP networking is generally suitable, however larger networks with managed opera-tions will often determine each device needs to have a dedicated and static IP address.DHCP IP addressDHCP is set as the network configuration by default for Mini.Static IP addressTo enable a static IP address, change configuration method to static and fill in the details required in Address, Mask and Gateway. Particular attention should be paid to the Address and Mask fields as incorrect information entered will result in Mini not being visible on the network and a factory reset will be required in order to recover the unit.IP address recoveryIn the event that the Mini is not visible on the network, the network has changed, or the static IP address details have been lost, reset the BirdDog back to its default settings by following the factory reset procedure.BirdDog nameYou can name each Mini with a friendly name that makes sense for each production (Camera 1, Camera 2, etc). This name will appear on any N DI receiver when it looks for video coming from Mini over the network. The name must not include any special characters and can be any combina-tion of ‘a-z, 1-0, and –‘.Note: no uppercase characters are valid.On NDI receiving devices, Mini will present as a source as follows:birddog-name [AUTO]when the unit is set to automatic input.birddog-name [HDMI]when set to HDMI in manual mode.Configuration method:Address:Mask:Gateway:DHCP timeout:Static fallback address:Static fallback mask:BirdDog Name:DASHBOARD VIDEO CONFIG. SYSTEM LOGOUTMININETWORK SETTINGS AND DEVICE NAMINGDevice namingWhen Mini is first powered on it defaults to the naming convention as described in the web configuration panel section of this manual.http://birddog-xxxxx.local/It is possible to change the name along with the network settings to better suit your environment.In the web configuration panel, navigate to the network section.TALLY SUPPORTOnboard TallyMini supports Tally within the N DI protocol. Tally is a method of identifying which source is being used ‘on air’ at any particular time.Whenever a Mini source is being used on the program output of an N DI compatible receiver that supports Tally metadata, the screen will light up red on the front of the Mini unit.Program TallyMini also supports preview tally. The onboard screen will light up green when the Mini source is placed in the preview bus of the receiving switcher.In the situation where the BirdDog source is loaded on both the program and preview bus of the receiver the light will be red.Preview TallyTally border overlay on loopMini is capable of enabling Tally borders on the video loop out. This feature is particularly useful for a camera setup that has a video monitor attached.The camera operator is able to quickly see if their camera is being used in a current or preview shot in a live environ-ment. This feature is enabled via the Video settings tab in the web configuration panel.Note the Tally borders now appear on the outside edges of the external monitor and update in real time as you selectsources on your vision switcher.Current video input:Audiosetup:Mute:Tally:Input selection:AUTO/SDI/1080i/25.0/YUVDASHBOARD NETWORK VIDEO CONFIG. SYSTEM LOGOUTMINIThe screen will update the status of the update procedure, once complete it will show the line Please power cycle your device…Remove all power from the Mini and wait for 5 seconds before re-powering the device.UPDATE - PROGRESSWaiting for update service...Connected to updater service...Processing update package: birddog-bdmini01-0_le.tar.gz Extracting...Changing directory...Checking if update script exists in packaging...Running in-packaging updater script...Updating package repositories...Installing required packages...Stopping BirdDog services...Copying new BirdDog data...Setting default systemd target...Rebooting...DASHBOARD NETWORK VIDEO CONFIG. SYSTEM LOGOUTMINIFACTORY RESETSettings resetIf Mini is not found on the network and the web configura-tion console is inaccessible it is possible to perform a factory reset on the network settings. To reset Mini simply press and hold the reset micro switch for 6 seconds at any time after Mini has booted up (approx. 20 seconds after power on).Once the reset process begins, BirdDog Mini will flash the LED screen between red and green repeatedly. Once the screen stops flashing, the reset process has completed and all network settings will return to default (device name and DHCP network address).The reset switch is located on the top of the unit here:FIRMWARE UPDATEMini is updateable via the web interface. Please check the below address regularly to ensure you have the latest firmware available for your device.Having the latest firmware ensures you have all the latest features and performance updates to get the most out of Mini: /firmware-updatesAfter downloading the latest firmware release, navigate to the settings tab on the Mini web configuration console click on Choose file… select the firmware update file and press the update button.SYSTEM UPDATE Update file:CONFIG. UPDATEUpdate file:DASHBOARD NETWORK VIDEO CONFIG. SYSTEM LOGOUTMINIRECEIVING NDI STREAMSThere are many applications that support receiving the NDI signal that Mini produces. Each application will vary slightly on how you choose your source.NewTek Studio MonitorN ewTek provide a free Studio Monitor application that allows you to monitor many N DI sources on a standard Windows computer. Once Studio Monitor is launched on your computer, simply right click anywhere in the interface and select your Mini from the drop-down list.Once connected to the Mini you will notice a configuration cog appears on the bottom right-hand side of the video display, this is a shortcut to access the Mini web configura-tion panel.NewTek TriCaster SeriesNewTek TriCaster series devices allow several NDI sources to be received simultaneously, the amount of simultaneous connections varies by what model TriCaster you have. Consult your TriCaster user manual to determine how many connections are available on your device.To select Mini as a source on your TriCaster, simply click on the configuration cog below your desired source location, this will bring up the Input Setting dialog, select from the drop-down list your Mini source.Once connected to the Mini you will notice a configuration cog appears next to the source drop down window, this is a shortcut to access the Mini web configuration panel. *****************。
EFM8BB51 Busy Bee 8-bit微控制器BB51探索器套件用户指南说明书

UG511: BB51 Explorer Kit User's Guide The BB51 Explorer Kit is an ultra-low cost, small form factor devel-opment and evaluation platform for the EFM8BB51 Busy Bee 8-bit microcontroller.The BB51 Explorer Kit is focused on rapid prototyping and concept creation of multi-pur-pose applications. It is designed around the EFM8BB51 MCU, which is an ideal device family for developing energy-friendly embedded applications.The kit features a USB interface, an on-board SEGGER J-Link debugger, one user-LED and button, and support for hardware add-on boards via a mikroBUS™ socket and a Qwiic® connector. The hardware add-on support allows developers to create and proto-type applications using a virtually endless combination of off-the-shelf boards from mik-roE, sparkfun, AdaFruit, and Seeed Studios.TARGET DEVICE•EFM8BB51 Busy Bee 8-bit microcontroller (EFM8BB51F16I-C-QFN20R)•Pipelined 8-bit C8051 core with 50 MHz maximum operating frequency•16 kB flash and 1280 bytes RAMKIT FEATURES•User LED and push button•2.54 mm breakout pads•mikroBUS™ socket•Qwiic® connector•SEGGER J-Link on-board debugger •Virtual COM port•USB-poweredSOFTWARE SUPPORT•Simplicity Studio™ORDERING INFORMATION•BB51-EK2700ATable of Contents1. Introduction (3)1.1 Kit Contents (3)1.2 Getting Started (3)1.3 Hardware Content (3)1.4 Kit Hardware Layout (4)2. Specifications (5)2.1 Recommended Operating Conditions (5)2.2 Current Consumption (5)3. Hardware (6)3.1 Block Diagram (6)3.2 Power Supply (7)3.3 EFM8BB51 Reset (7)3.4 Push Button and LED (7)3.5 On-board Debugger (8)3.6 Connectors (8)3.6.1 Breakout Pads (8)3.6.2 MikroBUS Socket (9)3.6.3 Qwiic Connector (10)3.6.4 Debug USB Micro-B Connector (10)4. Debugging (11)4.1 On-board Debugger (11)4.2 Virtual COM Port (11)5. Schematics, Assembly Drawings, and BOM (12)6. Kit Revision History (13)7. Board Revision History and Errata (14)7.1 Revision History (14)7.2 Errata (14)1. IntroductionThe BB51 Explorer Kit has been designed to inspire customers to explore the Silicon Labs EFM8BB51 Busy Bee 8-bit microcontroller. The kit includes a mikroBUS™ socket and Qwiic® connector, allowing users to add features to the kit with a large selection of off-the-shelf boards.Programming the BB51 Explorer Kit is easily done using a USB Micro-B cable and the on-board J-Link debugger. A USB virtual COM port provides a serial connection to the target application. The BB51 Explorer Kit is supported in Simplicity Studio™ and a Board Sup-port Package (BSP) is provided to give application developers a flying start.Connecting external hardware to the BB51 Explorer Kit can be done using the breakout pads which present peripherals from the EFM8BB51 Busy Bee such as I2C, SPI, UART and GPIOs. The mikroBUS socket allows inserting mikroBUS add-on boards which in-terface with the EFM8BB51 through SPI, UART or I2C. The Qwiic connector can be used to connect hardware from the Qwiic Connect System through I2C.1.1 Kit ContentsThe following items are included in the box:•1x BB51 Explorer Kit board (BRD2700A)1.2 Getting StartedDetailed instructions for how to get started with your new BB51 Explorer Kit can be found on the Silicon Labs web pages:/dev-tools1.3 Hardware ContentThe following key hardware elements are included on the BB51 Explorer Kit:•EFM8BB51 Busy Bee MCU with 50 MHz operating frequency, 16 kB kB flash, and 1280 bytes RAM•One LED and one push button•On-board SEGGER J-Link debugger for easy programming and debugging, which includes a USB virtual COM port•MikroBUS™ socket for connecting Click boards™ and other mikroBUS add-on boards•Qwiic® connector for connecting Qwiic Connect System hardware•Breakout pads for GPIO access and connection to external hardware•Reset button1.4 Kit Hardware LayoutThe layout of the BB51 Explorer Kit is shown below.Top ViewPush Button35.6 mmBreakout PadsUSB Micro-B Connector - Virtual COM port - Debug access - Packet traceLEDConnectorEFM8BB51On-board USB mikroBUS SocketFigure 1.1. BB51 Explorer Kit Hardware Layout2. Specifications2.1 Recommended Operating Conditions1Not recommended for use with rechargeable Lithium batteries. Most Li-Ion and Li-Po cells exceed 3.6 V when fully charged2When using the provided interfaces with add-on boards or other external hardware, tighter voltage limits might apply2.2 Current ConsumptionThe operating current of the board greatly depends on the application and the amount of external hardware connected. The table below attempts to give some indication of typical current consumptions for the EFM8BB51 and the on-board debugger. Note that the numbers are taken from the data sheets for the devices. For a full overview of the conditions that apply for a specific number from a data sheet, the reader is encouraged to read the specific data sheet.Table 2.1. Current Consumption1From EFM8BB51 data sheet2From EFM32GG12 data sheet3. HardwareThe core of the BB51 Explorer Kit is the EFM8BB51 Busy Bee 8-bit microcontroller. Refer to section 1.4 Kit Hardware Layout for place-ment and layout of the hardware components.3.1 Block DiagramAn overview of the BB51 Explorer Kit is illustrated in the figure below.ExpandabilityDebuggingEFM8BB51Temperature & Humidity Sensor Ambient Light & UV SensorHall Effect Sensor Qwiic Connector mikroBUS SocketFigure 3.1. Kit Block Diagram3.2 Power SupplyThe kit is powered by the debug USB cable as illustrated in the figure below.AutomaticIsolationPeripheralsEFM8BB518-bit MCUPeripheralsFigure 3.2. BB51 Explorer Kit Power TopologyThe 5 volt power net on the USB bus is regulated down to 3.3 V using an LDO (low-dropout regulator). An automatic isolation circuit isolates the LDO when the USB cable is not plugged in.Power can be injected externally on the VMCU net if the USB cable is removed and no other power sources are present on the kit. Failure to follow this guideline can cause power conflicts and damage the LDO.3.3 EFM8BB51 ResetThe EFM8BB51 can be reset by a few different sources:• A user pressing the RESET button.•The on-board debugger pulling the #RESET pin low.3.4 Push Button and LEDThe kit has one user push button, marked BTN0, that is connected to a GPIO on the EFM8BB51. The button is connected to pin P0.2 and it is debounced by an RC filter with a time constant of 1 ms. The logic state of the button is high while the button is not being pressed, and low when the button is pressed.The kit also features one yellow LED, marked LED0, that is controlled by a GPIO pin on the EFM8BB51. The LED is connected to pin P1.4 in an active-high configuration.Button & LEDFigure 3.3. Button and LED3.5 On-board DebuggerThe BB51 Explorer Kit contains a microcontroller separate from the EFM8BB51 Busy Bee that provides the user with an on-board J-Link debugger through the USB Micro-B port. This microcontroller is referred to as the "on-board debugger", and is not programmable by the user. When the USB cable is removed, the on-board debugger goes into a very low power shutoff mode (EM4S).In addition to providing code download and debug features, the on-board debugger also presents a virtual COM port for general pur-pose application serial data transfer.The figure below shows the connections between the target EFM8BB51 device and the on-board debugger. The figure also shows the presence of the Mini Simplicity Connector, and how this is connected to the same I/O pins.Please refer to chapter 4. Debugging for more details on debugging.Mini Simplicity ConnectorP0.5 (UARTx.RX)Figure 3.4. On-Board Debugger Connections3.6 ConnectorsThe BB51 Explorer Kit features a USB Micro-B connector, breakout pads, a mikroBUS connector for connecting mikroBUS add-on boards, and a Qwiic connector for connecting Qwiic Connect System hardware. The connectors are placed on the top side of the board,and their placement and pinout are shown in the figure below. For additional information on the connectors, see the following sub chap-ters.SocketsJ1GND 5VBUTTON0LED0QWIIC I2C SDA QWIIC I2C SCLVCOM TX VCOM RXP0.1P0.2P1.4P1.5P1.6P0.4P0.6P0.5P0.0MikroBUS INT MikroBUS PWMMikroBUS UART RX MikroBUS I2C SCL MikroBUS I2C SDA MikroBUS UART TX SMB0SMB0UARTx UARTxTIMERxFigure 3.5. BB51 Explorer Kit Connectors3.6.1 Breakout PadsTwentyone breakout pads are provided and allow connection of external peripherals. The breakout pads are arranged in two rows and contain a number of I/O pins that can be used with most of the EFM8BB51 Busy Bee's features. Additionally, the VMCU (main board power rail), 3V3 (LDO regulator output), and 5V power rails are also exposed on the pads.The pin-routing on the Busy Bee is flexible, so most peripherals can be routed to any pin on port 1 or 2. However, pins may be shared between the breakout pads and other functions on the BB51 Explorer Kit. The figure in section 3.6 Connectors includes an overview of the breakout pads and functionality that is shared with the kit.3.6.2 MikroBUS SocketThe BB51 Explorer Kit features a mikroBUS™ socket compatible with mikroBUS add-on boards. MikroBUS add-on boards can expand the functionality of the kit with peripherals such as sensors and LCDs. Add-on boards follow the mikroBUS socket pin mapping, and communicates with the on-kit EFM8BB51 through UART, SPI or I2C. Several GPIOs are exposed on the mikroBUS socket. MikroBUS add-on boards can be powered by the 5V or VMCU power rails, which are available on the mikroBUS socket.The pinout of the EFM8BB51 on the kit is made such that all required peripherals are available on the mikroBUS socket. The I2C sig-nals are, however, shared with the Qwiic connector, and all mikroBUS signals are also routed to adjacent breakout pads.When inserting a mikroBUS add-on board, refer to the orientation notch on the BB51 Explorer Kit, shown in the figure below, to ensure correct orientation. Add-on boards have a similar notch that needs to be lined up with the one shown below.socketFigure 3.6. mikroBUS Add-on Board OrientationThe table below gives an overview of the mikroBUS socket pin connections to the EFM8BB51.Table 3.1. mikroBUS Socket Pinout3.6.3 Qwiic ConnectorThe BB51 Explorer Kit features a Qwiic® connector compatible with Qwiic Connect System hardware. The Qwiic connector provides an easy way to expand the functionality of the BB51 Explorer Kit with sensors, LCDs, and other peripherals over the I2C interface. The Qwiic connector is a 4-pin polarized JST connector, which ensures the cable is inserted the right way.Qwiic Connect System hardware is daisy chain-able as long as each I2C device in the chain has a unique I2C address.Note: The Qwiic I2C connections on the BB51 Explorer Kit are shared with the mikroBUS I2C signals.The Qwiic connector and its connections to Qwiic cables and the EFM8BB51 are illustrated in the figure below.Qwiic cableGNDVMCUSDA - P1.5SCL - P1.6Figure 3.7. Qwiic ConnectorThe table below gives an overview of the Qwiic connections to the EFM8BB51.Table 3.2. Qwiic Connector Pinout3.6.4 Debug USB Micro-B ConnectorThe debug USB port can be used for uploading code, debugging, and as a virtual COM port. More information is available in section 4. Debugging.Debugging 4. DebuggingThe BB51 Explorer Kit contains an on-board SEGGER J-Link Debugger that is connected to the C2 debugging interface on the EFM8BB51. The debugger allows the user to download code and debug applications running in the target EFM8BB51. Additionally, it also provides a virtual COM port (VCOM) to the host computer that is connected to the target device's serial port, for general purpose communication between the running application and the host computer. The on-board debugger is accessible through the USB Micro-B connector.4.1 On-board DebuggerThe on-board debugger is a SEGGER J-Link debugger running on an EFM32 Giant Gecko. The debugger is directly connected to the debug and VCOM pins of the target EFM8BB51.When the debug USB cable is inserted, the on-board debugger is automatically active, and takes control of the debug and VCOM inter-faces. This means that debug and communication will not work with an external debugger connected at the same time. The on-board LDO is also activated, providing power to the board.When the USB cable is removed, the board might still be running on external power, as described in section 3.2 Power Supply. In this case, the on-board debugger goes into a very low power shutoff mode (EM4S), consuming about 80 nA.4.2 Virtual COM PortThe virtual COM port is a connection to a UART of the target EFM8BB51 and allows serial data to be sent and received from the de-vice. The on-board debugger presents this as a virtual COM port on the host computer that shows up when the USB cable is inserted.Data is transferred between the host computer and the debugger through the USB connection, which emulates a serial port using the USB Communication Device Class (CDC). From the debugger, the data is passed on to the target device through a physical UART connection.The serial format is 115200 bps, 8 bits, no parity, and 1 stop bit by default.Note: Changing the baud rate for the COM port on the PC side does not influence the UART baud rate between the debugger and the target device.Schematics, Assembly Drawings, and BOM 5. Schematics, Assembly Drawings, and BOMSchematics, assembly drawings, and bill of materials (BOM) are available through Simplicity Studio when the kit documentation pack-age has been installed. They are also available from the kit page on the Silicon Labs website: /.Kit Revision History 6. Kit Revision HistoryThe kit revision can be found printed on the box label of the kit, as outlined in the figure below. The kit revision history is summarized in the table below.EFM8BB51 Explorer KitBB51-EK2700A08-09-2121220001A01Figure 6.1. Revision InfoTable 6.1. Kit Revision HistoryBoard Revision History and Errata 7. Board Revision History and Errata7.1 Revision HistoryThe board revision can be found laser printed on the board, and the board revision history is summarized in the following table.Table 7.1. Board Revision History7.2 ErrataThere are no known errata at present.Silicon Laboratories Inc.400 West Cesar Chavez Austin, TX 78701USAIoT Portfolio/IoTSW/HW/simplicityQuality /qualitySupport & Community/communityDisclaimerSilicon Labs intends to provide customers with the latest, accurate, and in-depth documentation of all peripherals and modules available for system and software imple-menters using or intending to use the Silicon Labs products. Characterization data, available modules and peripherals, memory sizes and memory addresses refer to each specific device, and “Typical” parameters provided can and do vary in different applications. Application examples described herein are for illustrative purposes only. Silicon Labs reserves the right to make changes without further notice to the product information, specifications, and descriptions herein, and does not give warranties as to the accuracy or completeness of the included information. Without prior notification, Silicon Labs may update product firmware during the manufacturing process for security or reliability reasons. Such changes will not alter the specifications or the performance of the product. Silicon Labs shall have no liability for the consequences of use of the infor -mation supplied in this document. This document does not imply or expressly grant any license to design or fabricate any integrated circuits. The products are not designed or authorized to be used within any FDA Class III devices, applications for which FDA premarket approval is required or Life Support Systems without the specific written consent of Silicon Labs. A “Life Support System” is any product or system intended to support or sustain life and/or health, which, if it fails, can be reasonably expected to result in significant personal injury or death. Silicon Labs products are not designed or authorized for military applications. Silicon Labs products shall under no circumstances be used in weapons of mass destruction including (but not limited to) nuclear, biological or chemical weapons, or missiles capable of delivering such weapons. Silicon Labs disclaims all express and implied warranties and shall not be responsible or liable for any injuries or damages related to use of a Silicon Labs product in such unauthorized applications. Note: This content may contain offensive terminology that is now obsolete. Silicon Labs is replacing these terms with inclusive language wherever possible. For more information, visit /about-us/inclusive-lexicon-projectTrademark InformationSilicon Laboratories Inc.®, Silicon Laboratories ®, Silicon Labs ®, SiLabs ® and the Silicon Labs logo ®, Bluegiga ®, Bluegiga Logo ®, Clockbuilder ®, CMEMS ®, DSPLL ®, EFM ®, EFM32®, EFR, Ember ®, Energy Micro, Energy Micro logo and combinations thereof, “the world’s most energy friendly microcontrollers”, Ember ®, EZLink ®, EZRadio ®, EZRadioPRO ®, Gecko ®, Gecko OS, Gecko OS Studio, ISOmodem ®, Precision32®, ProSLIC ®, Simplicity Studio ®, SiPHY ®, Telegesis, the Telegesis Logo ®, USBXpress ® , Zentri, the Zentri logo and Zentri DMS, Z-Wave ®, and others are trademarks or registered trademarks of Silicon Labs. ARM, CORTEX, Cortex-M3 and THUMB are trademarks or registered trademarks of ARM Hold-ings. Keil is a registered trademark of ARM Limited. Wi-Fi is a registered trademark of the Wi-Fi Alliance. All other products or brand names mentioned herein are trademarks of their respective holders.。
- 1、下载文档前请自行甄别文档内容的完整性,平台不提供额外的编辑、内容补充、找答案等附加服务。
- 2、"仅部分预览"的文档,不可在线预览部分如存在完整性等问题,可反馈申请退款(可完整预览的文档不适用该条件!)。
- 3、如文档侵犯您的权益,请联系客服反馈,我们会尽快为您处理(人工客服工作时间:9:00-18:30)。
2.2 SEED-DIM3517 外设及接口模块 ....................................................................2-1
2.3 电源模块......................................................................................................2-4
警告标志
本板卡包含 ESD 敏感器件,请采取适当的预防措施。使用时请不要 用手或非绝缘的物体接触板卡。因使用不当造成的板卡损坏,本公 司只提供付费的维修。 本文中所有类似的警告标识,表明此部分内容有可能损害您的软件、 硬件或其它设备。这个信息谨慎的为您提供保护,请仔细阅读阅读。
商标
SEED 是北京合众达电子技术有限责任公司的注册商标。 TI 是 Texas Instruments 的注册商标。
2.
板上组件 .............................................................................................................2-1
2.1 AM3517 处理器模块 ......................................................................................2-1
作者
更新日期 2010-7-30
更17
硬件用户指南
版本号:A 2011.17
III
声明
北京合众达电子技术有限责任公司保留随时对其产品进行修正、改进和完善的权 利,同时也保留在不作任何通告的情况下,终止其任何一款产品的供应和服务的权利。 用户在下订单前应及时获取相关信息的最新版本,并验证这些信息是当前的和完整的。
3.2 连接器 .........................................................................................................3-2
3.2.1 J4 仿真接口..........................................................................................3-2
1.1 主要特点.....................................................................................................1–1
1.2 功能描述.....................................................................................................1–2
2.1.1 AM3517 主芯片 ......................................................................................2-1
2.1.2 片外存储器...........................................................................................2-1
附录 B
参考资料 ...........................................................................................3-1
VI
图 1. 图 2. 图 3. 图 4. 图 5. 图 6.
图示
SEED-DIM3517 正面实物图 ..........................................................................1–1 SEED-DIM3517 背面实物图 ..........................................................................1–2 SEED-DIM3517 功能框图 ..............................................................................1–2 SEED-DIM3517 正面实物图 ...........................................................................3-1 SEED-DIM3517 背面实物图 ...........................................................................3-2 JTAG 仿真接口..............................................................................................3-2
VIII
SEED-DIM3517 硬件用户手册
第1章
功能描述
1. 功能描述
本章主要介绍 SEED-DIM3517 的主要特性以及系统功能框图。
1.1 主要特点
SEED-DIM3517 是基于德州仪器(TI)AM3517 处理器的评估套件。AM3517 处理器集成 了 600-MHz ARM Cortex-A8 内核,并提供了丰富的外设接口。SEED-DIM3517 采用 DIMM 插 卡式设计,可以灵活方便的融入各种行业应用。板上资源包括:AM3517、NAND FLASH、 DDR2、电源、EMAC PHY、JTAG 等。板卡 DIMM 接口为 1.8V DIMM 连接器。提供的外设接口 包括:USB、VPFE、网口、2D/3D 图形加速器、HDQ\1-Wire、UART、I2C、SPI、MMC\SD\SDIO、 McBSP、HECC、DSS、GPIO 等。
3.
物理描述 .............................................................................................................3-1
3.1 PCB 布局......................................................................................................3-1
版权© 2011,北京合众达电子技术有限责任公司
IV
前言
阅前必读
简介
本手册是基于 AM3517 的嵌入式多媒体系统解决方案板卡 SEED-DIM3517 的硬件使 用说明书,详细描述了 SEED-DIM3517 的硬件构成、原理,以及它的使用方法。
保修
所有由北京合众达电子技术有限责任公司生产制造的硬件和软件产品,保修期为 从发货之日起壹年。在保修期内由于产品质量原因引起的损坏,北京合众达电子技术 有限责任公司负责免费维修或更换。保修期内软件升级,北京合众达电子技术有限责 任公司将免费提供。
图1. SEED-DIM3517 正面实物图
1–1
第一章 功能描述
SEED-DIM3517
硬件用户指南
2011-7
AM3517 Solutions DSP Embedded Controller
版本号 REV A
版本号 SEED-DIM3517
截止印刷时文档名称和编号
SEED-DIM3517 硬件用户指南
文档历史
历史 初始版本
作者 田晓林
软件版本历史
历史 初始版本
VII
表格
表 1. 表 2. 表 3. 表 4. 表 5. 表 6. 表 7. 表 8. 表 9. 表 10. 表 11. 表 12.
DIMM 连接器定义 ..........................................................................................2-4 连接器 .........................................................................................................3-2 JTAG 管脚定义..............................................................................................3-3 USB 管脚定义 ...............................................................................................3-3 EMAC 管脚定义 ..........................................................................................3-4 I2C 管脚定义 ...............................................................................................3-7 SPI 管脚定义 ...............................................................................................3-7 UART 管脚定义 ...........................................................................................3-5 VIDEO IN 管脚定义 .....................................................................................3-5 MMC\SD 管脚定义 ......................................................................................3-6 MCBSP 管脚定义 ........................................................................................3-5 DSS 管脚定义 .............................................................................................3-4