TS16949 FMEA training teaching material
TS16949五大工具---FMEA第四版

FMEA 的时间顺序
DFMEA PFMEA
概念
初始设计
设计完成
样件制造
设计/过程 确认
生产开始
DFMEA 开始早于过程,完成时间在早期的图样完成但任何工具 的制造开始之前 PFMEA 开始于基本的操作方法讨论完成时,完成时间早于生产 计划制定和生产批准之前
小组的开发FMEA转变成个人的行为 FMEA是创造顾客或第三方满意,而不是提高 过程 FMEA在过程开发中运用太迟或没有改进产品/ 过程循环发展 在产品寿命期内FMEA没有被重新评定和更新, 没有像动态工具一样被加工 FMEA被认为太复杂或花费太多的时间
过程流程/ 控制计划 (所有的“”主要“过程)
FMEA 的益处
预防计划 识别改变需求 降低成本 减少浪费 降低保证成本 降低无增值操作
FMEA 的前提条件
选择适当的小组和有效的组织成员 为每个产品/服务、过程/系统选择小组 建立团队体系 定义顾客和顾客需求/期望 涉及/过程需求 开发过程流程图**
过程FMEA 小组成员
过程工程师—通常的小组领导 生产操作者 工艺工程师 设计工程师 可靠性工程师 加工工程师 维修工程师 项目经理 质量工程师 其他,包括:销售、供应商、QA/QC等
定义顾客
DFMEA的顾客 最终使用者:使用产品的人 PFMEA的顾客 后序的操作者 最终使用者:使用产品的人
注意
不要混淆 DFMEA与PFMEA的起因和失效
DFMEA的失效
润滑能力不足 错误的原料说明
PFMEA的失效
润滑油使用不够 错误的原料使用
FMEA2教程
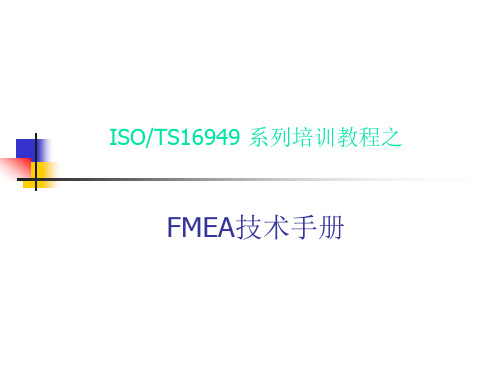
模式 后果 度
起因 O -预防
功能 要求
S
/机
理
-探测
探 R 建议措 测P施 度N D
责任及 目标完 成日期
措施结果
采取 的措 施
S ODR P应从所要分析的系统、子系统或零部件的框图开始;
框图描述了所分析对象的各项目之间的主要关系、逻辑顺序、功能、及其 输入和输出。
FMEA在产品策划中的运用
DMEA
跨功能小组在开展设计FMEA时,应参考以下文件和资料:
保修信息。 顾客抱怨、退货资料。 纠正和预防措施。 类似产品的设计FMEA APQP第一阶段输出,即第二阶段输入和 任何其它相应输入。
DFMEA输出
设计FMEA的输出
潜在设计失效模式。 潜在关键设计要求。 设计问题:曾经受到制造和装配作业挑
原因的方法及採取有效的措施。 5.公司對經驗的累積及技術能制度化的保存。
FMEA实施手法
FMEA过程顺序
子系 潜在 潜在 严 级 潜在 频 现行控制 探 R 建议 责任及
措施结果
统
失效 失效 重 别 失效 度
测 P 措施 目标完
模式 后果 度
功能
S
起因/ O 机理
预 防
探 测
度 D
N
成日期
采取 的措
FMEA的产生
1.1950年格魯曼(Grumman)公司因飛機的推動方式由 螺旋槳進步到噴射引擎;操控系統也由鋼索改為油壓 或電器裝置,為防範飛機飛行時,該等裝置故障而開 發了FMEA。
2.波音與馬丁公司在1957年正式編訂FMEA的作業程序, 列在其工程手冊中。
3.1960年代初期,美國航空暨太空總署(NASA)實施阿 波羅(Apollo)計劃時,將可靠性及安全管理列為合約
TS16949质量体系五大手册培训教材(完整)08681

一、 APQP 产品先期质量策划
1、 产品质量策划循环 ………………………………………………………………2
2、 APQP 推行流程 ………………………………………………………………………3 3、 APQP 阶段区别 ………………………………………………………………………5 4、 第 I 阶段 计划和确定项目 ………………………………………………………5 5、 第 II 阶段 产品设计和开发 ……………………………………………………12 6、 第 III 阶段 过程设计和开发 …………………………………………………16 7、 第 IV 阶段 产品和过程确认 ……………………………………………………19 8、 第 V 阶段 反馈、评定和纠正措施 ……………………………………………22 9、 控 制 计 划 方 法 论 … … … … … … … … … … … … … … … … … … … … … … 2 3
建立同步工程
建立各阶段管制计划
相关结果与问题解决 关结 与 的方法
7
产品质量策划进度图表
------结构化的图示
概念开 发/确认 项目 批准 样件 确认
试生产
生产
1.0 计划 2.0 产品设计和开发 3.0 过程设计与开发 4.0 产品 产品和过程确认 过程确认
新的计划
生 产 5.0 反馈评估和纠正行动
网络工程制造材料采购品管业务供货商与顾客代表定义出顾客的需求组成跨部门小组apqp推动流程定义出顾客的需求鉴定成本时程和必须考虑的限制条件apqp小组顾客apqp小组供应商定义范围小组对小组之沟通与协调定期会议之沟通apqp小组相关人员之教育训练教育训练3145页顾客分包商参与建立同步工程与顾客共同进行品质规划期望供货商有同等之绩效simultaneousengineeringapqp小组专业分工发挥同步工程能力减建立各阶段管制计划少次序性步骤可缩短活动时程满足顾客需求原型量试量产管制计划规划过程所遭遇之产品设计或制程等相关事项应制度书面之相关责任与完成时程相关结果与问题解决的方法事项应制度书面之相关责任与完成时程问题解决的分析技术可运用要因分析图要径法实验计划法易制性与易装性之考量制造流程图品质机能展开qfdfmea结构化的图示项目批准样件确认试生产生产概念开发确认产品质量策划进度图表10计划20产品设计和开发30过程设计与开发40产品和过程确认批准确认发确认新的计划产品过程确认50反馈评估和纠正行动iiiiiiv计划和确定项目产品设计及开发过程设计和开发产品和过程确认反馈评定和纠正措11顾客的声音17设计目标21dfmea31包装标准和规范41一定数量的生产运51减少变异111市场研究18可靠性和质量目标22可制造性和装配设32产品过程质量体系评审42测量系统分析52增进顾客满意apqp阶段区分目标系评审112保修记录和质量信息19初始材料清单23设计验证33过程流程图43ppk研究53增进交付和服务113小组经验110初始过程流程24设计评审34工厂平面布置图44ppap54习得经验最佳实践的有效应用12业务计划营销策略111产品和过程特殊特性的初始清单25样件制造控制计35特性矩阵图45生产确认试验13产品过程标杆数据112产品保证计划26工程图样包括数学数据36pfmea46包装评价14产品过程假设113管理者支持27工程规范37试生产控制计划47生产控制计划15产品可靠度研究28材料规范38过程说明书48质量策划认定和管理者支持16顾客输入29图样及规范的变更39测量系统分析计210新设备工装和设施要求310初始过程能力研究计划211产品过程特殊特311管理者支持212量具试验设备要213小组可行性承诺和管理者支持输入支持第一阶段计划和确定项目顾客的声音业务计划营销策略产品过程标杆数据产品过程假设产品
TS16949培训教材(3)FMEA

FMEA的作用和目标
FMEA的目标是: 1)认可并评价产品/过程中潜在的失效及其后果; 2)确定能够避免或减少这些潜在失效发生的措施; PFMEA的益处是: 1)帮助确认已列出的潜在失效模式及它们的后果; 2)指明相应的起因/机理; 3)降低或消除实效出现的机会的措施; 4)指明潜在的制造或装配过程失效的原因; 5)指明过程变差,如果受控,可降低失效出现的频度 或提高失效的探测度; 6)帮助对纠正措施进行优先排序; 7)对类似制造过程作有用的FMEA分析参考; 8)过程FMEA的实施记录。
失效分析链
水箱支架断裂 水箱后倾
水箱与风扇碰撞
FMEA
水箱冷却水管被风扇刮伤
FMA
水箱冷却液泄漏
冷却系统过热 发动机气缸损坏 汽车停驶
FMEA与控制计划
FMEA和控制计划是帮助产品、过程和服务有关信息 的两个主要工具 DFMEA QFD 控制计划 行动计划
PFMEA
制造与装配过程FMEA
PFMEA的准备工作 ——DFMEA的工作不包含在PFMEA中; ——PFMEA有可能成为DFMEA中对可制造性和装配性 问题的补充,因该反馈到DFMEA中。 PFMEA的准备可以包括: ——建立小组 ——必须的资料(过程流程图,过程特性矩阵图, 动作风险分析,现有类似过程FMEA资料,现有类似 过程FMA,特殊过程特性明细表,过程规范,PFMEA 表格) 填写表头 开始PFMEA 1)过程功能要求(如:装配/注塑/压铸/焊接/攻丝) 2)潜在失效模式
制造与装配过程FMEA
——增加样本容量和抽样频率都有助于改善探测度 ——100%检验办法成本高,而且也不一定是有绝对把握。它 会受到测量系统的变差的影响 ——100%目视检查方法还受到人的判断能力的影响,以及失 效模式性质是否易于目视方法发现 ——不可人为100%检查就具有高的探测度
TS16949FMEA潜在失效模式与后果分析培训教材第

主要功能失效(车辆可操作,但降低操作性)
次要功能损 次要功能失效(车辆可操作,但舒适性/方便性项目不能运行) 失或降低
次要功能失效(车辆可操作,但舒适性/方便性降低)
烦恼
外观、杂音/异响,车辆可操作,75%以上顾客能感觉到缺陷
外观、杂音/异响,车辆可操作, 50%的顾客能感觉到缺陷。
33
大众的评价准则(91年)
缺陷 级别
特别严 重 严重
中等严 重 轻微
人身 事故 伤害
易
运转失灵 必然*
现场难以确 定位置的间 隙故障
必然
次于标 准的运 转故障
增加保养 次数或缩 短寿命
顾客安 外形、涂 装上的 层或工艺 困难 上的困难
必然** 大概会 可能会
不会
必然 必然 可能会 可能会 不会 不会
10
谁编制FMEA?Who shall edit FMEA?
小组
以设计/制造工程师为主的小组 小组成员:可以包括设计、制造、分析/试验、可靠 性、材料、质量、服务、物流、设备制造商、设备 维护、供方,以及更高或更低一级的设计人员。 DFMEA小组: PFMEA小组:
11
第四版对小组成员作用的说明
16
第二部分 设计FMEA(DFMEA)
17
DFMEA过程
——框图、P图 ——DFMEA ——DVP&R
18
DFMEA的关注
DFMEA从产品概念成形前开始,在生产设 计发布前完成。 DFMEA关注: ——设计本身。全力研究后设计风险仍然较高 时,应传递至PFMEA继续关注 ——可制造性/可装配性(如拔模斜度、公差、 装配空间、表面处理、材料硬度限制等) ——服务可行性/回收技术(如工具的可获得 性、诊断能力、材料分类标记等)
TS16949过程FMEA控制程序

TS16949过程FMEA控制程序
1 目的
通过分析过程中的潜在失效,研究失效的原因及其后果,并采取必要的预防措施,避免或者减少这些潜在的失效,从而提高产品、过程的可靠性。
2 适用范围
适用于本公司过程FMEA活动的控制。
3 职责
3.1 技术部负责组织成立过程FMEA小组,负责过程FMEA活动的管理。
3.2 技术部、质量部、生产部、销售部、采购部等部门指定人员参加过程FMEA小组。
必要时,由质量部邀请供应商、客户参加。
3.3 过程FMEA小组负责制定《过程FMEA潜在失效后果严重程度(S)评价标准》、《过程FMEA潜在失效模式发生频度(O)评价标准》、《过程FMEA潜在失效模式发现难度(D)评价标准》。
4 工作程序。
TS16949和顾客特殊要求培训教材

质量管理标准
TS16949要素-产品实现
7.5.2 生产与服务提供过程的确认(定期验证生产过程工艺参数,在作业 准备验证前) 7.5.2.1生产与服务提供过程的确认---补充 7.5.3 标识与可追溯性 7.5.3.1标识与可追溯性---补充 7.5.4 顾客财产 7.5.4.1 顾客所有的工装 7.5.5 产品防护(看PPM值) 7.5.5.1 贮存和库存(整个物流链) 7.6 测量和监控设备的控制(对偏移规范的作风险分析) 7.6.1 测量系统评价 7.6.2 校准/验证记录 7.6.3 实验室要求 7.6.3.1 内部实验室(监定试验,产品监督,型式试验;对相关数据进行 评审) 7.6.3.2 外部实验室
这些过程的识别和相互作用及其管理,称之 为过程方法。
过程方法
• COP过程:以顾客为导向的过程。输入的是 顾客的要求,输出的是顾客的满意;如:产 品设计、市场开发。
• 管理过程:管理者管理的过程。输入的是企 业领导的希望,输出的是管理目标的实现; 如:业务计划的实现。
• 支持过程:支持COP实现的过程。输入的是 内部顾客的要求,输出的是内部顾客的满意。 如:采购过程、PPAP、MSA等过程。
质量管理标准
TS16949要素-产品实现
7.2.3顾客沟通 7.2.3.1顾客沟通---补充 7.3设计和开发(不作介绍/7.3.6.2样件方案) 7.4采购 7.4.1采购过程 7.4.1.1法规的符合性(原产地材料证明) 7.4.1.2供方质量管理体系 7.4.1.3顾客批准的来源 7.4.2采购信息 7.4.3采购产品的验证 7.4.3.1进货产品的质量 7.4.3.2对供方监视(PPM,交付/顾客反馈/退货
质量管理标准
TS16949
TS16949五大工具经典讲解APQPFMEAPPAPSPCMSA课件

Out
In
7
6
5
4
3
2
8
1
In
In
In
In
In
In
In
Out
Out
Out
Out
Out
Out
Out
顾客要求报价
顾客拿到『报价单』
6、章鱼模式(The Octopus Model)
7、乌龟图
寻找可能原因的六大因素
测量Measurement
寻找结果或问题的可能原因。主要归纳为6大类
人力Manpower
过程1
过程2
过程2.1
过程2.2
过程2.3
了解过程方法
过程1
过程2
输出/入
输入
输出
组织内部过程
顾客需求
顾客满意
采购
品保
财务
人力资源
生产管理
设备设施
管制计划
付款
产品保固
询价
投标
售后服务/反馈
产品/流程设计开发
COP
过程方法的特征
一个过程可以通过一连串独立的、相互协调的特性识别出来。对有效实施质量管理,过程有以下六个特征。一个过程所有者存在这个过程被定义这个过程被文件化过程之间的连接被建立这个过程被监控和改进记录并维持
根据关键特性制定Control Plan
确认顾客要求
提出重要过程的评价意见
使用正确的RPN并根据其他的适当信息来决定关键特性
为关键特性制定管理计划
为Control Plan的制订提供恰当的信息
Control Plan/标准的制定
概要设计FMEA简介设计FMEA的开发跟踪措施过程FMEA简介过程FMEA的开发跟踪措施附录A; 附录B; 附录F; 附录I术语
- 1、下载文档前请自行甄别文档内容的完整性,平台不提供额外的编辑、内容补充、找答案等附加服务。
- 2、"仅部分预览"的文档,不可在线预览部分如存在完整性等问题,可反馈申请退款(可完整预览的文档不适用该条件!)。
- 3、如文档侵犯您的权益,请联系客服反馈,我们会尽快为您处理(人工客服工作时间:9:00-18:30)。
潜在失效模式及后果分析Potential Failure Modeand Effect AnalysisFMEAThird EditionTraining Material目录第1章概论1.1 什么是FMEA?1.2FMEA的历史1.3 为什么要进行FMEA?1.4 由谁来做FMEA?1.5 什么时候做FMEA?1.6 失效链1.7 顾客的广义概念1.8 DFMEA与PFMEA的联系1.9 FMEA与ISO/TS16949技术规范的联系1.10 FMEA过程顺序1.11实施FMEA的三种基本情形1.12跟踪第2章产品设计FMEA(DFMEA)2.1 DFMEA的准备工作2.2 系统/子系统/零部件的功能2.3 潜在的失效模式2.4 潜在的失效后果2.5 严重度(S)2.6级别2.7失效的潜在起因/机理2.8 频度(O )2.9 现行设计控制2.10 探测度(D )2.11 风险顺序数(RPN)2.12 建议的措施2.13 建议措施的责任2.14 采取的措施2.15 措施的结果2.16 跟踪措施第3章制造与装配过程FMEA(PFMEA) 3.1PFMEA的准备工作3.2 过程功能/要求3.3 潜在失效模式3.4 潜在失效的后果3.5 严重度(S)3.6 级别3.7失效的潜在原因/机理3.8 频度(O)3.9 现行过程控制3.10 探测度(D)2.11 风险顺序数(RPN)2.12 建议的措施2.13 建议措施的责任2.14 采取的措施2.15 措施的结果2.16 跟踪措施附录第1章概论1.1 什么是FMEA?潜在的失效模式及后果分析(英文: Potential Failure Mode and Effects Analysis,简称FMEA)。
是在产品/过程/服务等的策划设计阶段, 对构成产品的各子系统, 零部件, 对构成过程, 服务的各个程序逐一进行分析, 找出潜在的失效模式, 分析其可能的后果, 评估其风险, 从而预先采取措施, 减少失效模式的严重程度, 降低其可能发生的概率, 以有效地提高质量与可靠性, 确保顾客满意的系统化活动。
FMEA不同于失效模式分析(Failure Mode Analysis, 即FMA), 前者是一种事前行为, 后者是一种事后行为。
FMA是对产品/过程已经发生的失效模式分析其产生的原因, 评估其后果及采取纠正措施的一种活动。
FMA是进行FMEA的重要的资料。
FMEA又不同于失效树分析(Failure Tree Analysis, 即FTA)。
前者是从局部失效入手,分析其对上一级系统、相关部分、下游程序以及总体系统的后果;而后者一般是由系统的失效模式入手,分析造成该失效产生的原因。
形象地说,前者是沿着“由下至上”的分析路径,后者是沿着“由上至下”的分析路径。
FMEA按其应用的领域分成以下多种:SFMEA——系统FMEADFME A——产品FMEAPFMEA——过程FMEAAFMEA——应用FMEASFMEA——服务FMEAPFMEA——采购FMEA1.2 FMEA的历史世界上首次采用FMEA这种概念与方法的是在本世纪60年代中期美国的航天工业。
进入70年代,美国的海军和国防部相继应用推广这项技术,并制订了有关的标准。
70年代后期,FMEA被美国汽车工业界所引用,作为设计评审的一种工具。
1993年2月美国三大公司联合编写了FMEA手册,并正式出版作为QS9000质量体系要求文件的参考手册之一,该手册于1995年2月出版了第2版。
1994年,美国汽车工程师学会SAE发布了SAEJI739-潜在失效模式及后果分析标准。
FMEA还被广泛应用于其他行业,如粮食、卫生、运输、燃气等部门。
1.3 为什么要进行FMEA?工程中大量的事实证明,由于策划设计阶段的疏忽,分析不足,措施不够,以至造成产品/过程/服务等投入运行时严重程度不同的失效,给顾客带来损失,甚至产生诸如“挑战者”号航天飞机爆炸的惨痛事故。
因此,事先花必要的时间对产品/过程进行充分的潜在失效模式与后果的分析,能够大大减少事后产生失效而带来的风险与损失。
FMEA有助于对设计中问题的早期发现,从而避免和减少晚期修改带来的损失,使开发的成本下降。
产品设计的FMEA还有助于可制造性和装配性的早期考虑,利于实施同步工程技术。
FMEA有助于采用更有利的设计控制方法,为制订试验计划,质量控制计划提供正确的、恰当的根据。
由多方面人员组成的小组所进行FMEA能够发挥集体的经验与智慧,使设计表现出组织的最佳水平,提供了一个公开讨论的机会。
FMEA是一个组织的经验积累,为以后的设计开发项目提供了宝贵的参考。
FMEA还是识别特殊特性的重要工具。
FMEA的结果也是用来制订质量控制计划。
FMEA给出的失效模式的风险评估顺序,提供改进设计的优先控制系统,从而引导资源去解决需要优先解决的问题。
FMEA的文件化,使它成为重要设计文件之一,并成为设计评审的重要内容。
因此,FMEA已成为现代质量策划的重要工具,而被广泛应用。
1.4 由谁来做FMEA?FMEA既然是设计工作的一部分,自然应该由负责设计的工程师或工程师小组负责。
但要完成好FMEA工作,非常关键的是要发挥集体的智慧。
因此,FMEA的成功必须依靠小组的共同努力。
必须组成一个包括设计、制造、装配、售后服务、质量及可靠性等方面的专家小组。
与设计有关的上游(如组织、材料、上一个相关系统设计师)和下游(如下一个相关系统的设计师)的部门也将被吸收参加小组的工作。
1.5 什么时候做FMEA?FMEA旨在及早识别出潜在的失效,因此愈早开始愈好。
一般来说,在一个设计概念形成,设计方案初步确定时应该开始FMEA初稿的编制。
随着设计活动的展开,在设计的各个重要阶段,对FMEA的初稿进行评审,不断进行修改。
FMEA作为设计活动的一部分,应该在设计任务完成(如设计图样完成,过程设计文件完成)之时完成FMEA 工作。
FMEA是一个动态文件,在整个产品寿命周期内,根据反馈信息,在进行设计修改时对FMEA进行重新评审和修改。
要注意,任何为改进系统某一问题而进行的设计修改活动,都要谨慎地评审它对系统,对相关的部分的影响。
因引对相关的FMEA(DFMEA,PFMEA等)都要进行重新评审,并做必要的修改。
建议根据FMEA的质量目标(见附录1和附录2)对FMEA进行评审,包括管理评审。
1.6 失效链一个潜在的失效事件的发生,如果没有采取或来不及采取或事实上不可能采取措施,而使之引起下游系统或相关系统产生连锁失效事件,我们称之为“失效链”。
如下图1-1所示的例子。
可以看出:①水箱支架强度不足而造成的支架断裂是这个失效链的根源。
②道路不平引起的车体振动与扭转是引起支架断裂的环境条件,但不能视为失效的内在原因。
因为汽车在不平道路上行驶是正常的输入条件。
③失效链中,上一个失效模式是下一个失效模式的起因,下一个失效模式是上一个失效模式的后果。
④在没有任何措施情况下,失效将发展到最终的模式。
最有效的措施是不让支架断裂这一根源模式发生。
在失效链中任何环节采取“切断”措施,如在水箱与发动机(假设风扇安装在发动机上)之间增加撑杆,保证风扇不与水箱碰撞,可以防止失效链的发展。
但这种措施是否合理要认真评审。
⑤失效链的发展常常会有分支,有时分支的链也会产生更加严重的后果失效模式。
以上这些概念对进行FMEA活动时,将十分有帮助。
图1-1 失效链举例1.7 顾客的广义概念在FMEA中,多处要涉及“顾客”的概念。
广义的“顾客”。
包括:最终顾客:产品/服务的使用者。
直接顾客:下一道工序或用户。
中间顾客:下游工序或用户。
其他凡是产品/服务受益或受损害者均在广义顾客概念之中。
1.8 DFMEA与PFMEA的联系DFMEA与PFMEA既有明确的分工,又有紧密的联系,有以下几点需要注意:①产品设计部门的下一道工序是过程设计,产品设计应充分考虑可制造与可装配性问题,由于产品设计中没有适当考虑制造中技术与操作者体力的限制,可能造成过程失效模式的发生。
②产品设计FMEA不能依靠过程检测作为控制措施。
③PFMEA应将DFMEA作为重要的输入。
对DFMEA中标明的特殊特性也必须在PFMEA中作为重点分析的内容。
1.9 FMEA同ISO/TS16949技术规范的关系①ISO/TS16949技术规范中明确规定FMEA是质量体系和设计控制要素中的要求。
ISO/TS16949指南建议使用APQP手册进行质量策划。
而DFMEA和PFMEA又是APQP规定的输入、输出要素。
同时PPAP手册也明确规定FMEA的要求。
因此,FMEA是必须进行的一项活动。
下表列出ISO/TS16949技术规范、APQP、PPAP中明文规定的与FMEA有关的章节。
文件有关章节7.3.1.1多方论证方法ISO/TS169497.3.2.3特殊特性7.3.3.1产品设计输出7.3.3.2制造过程设计输出7.5.5.1控制计划第二章产品设计和开发 2.1 DFMEAAPQP2.4 设计评审第三章过程设计和开发 3.6 PFMEA第三章PPAP要求之10PPAP第四章提交批准的等级之3②FMEA手册的“前言”中说明:组织在应用FMEA技术时,应采用该手册及报告格式。
但同时指出,本手册提供了FMEA的通用性指南,并没有给出如何完成每一项目的具体说明,也不是综合性的FMEA的参考资料或培训教材。
1.10 FMEA过程顺序图1-2描述了FMEA的顺序,这并不是简单地填写一下表格,而是要理解FMEA的过程,以便消除风险并策划适宜的控制方法以确保顾客满意。
1.11 实施FMEA的三种基本情形每一种情形都有其不同的范围或关注焦点:情形一:新设计、新技术或新过程。
FMEA的范围是全部设计、技术或过程。
情形二:对现有设计或过程的修改(假设对现有设计或过程已有FMEA)。
FMEA的范围应集中于对设计或过程的修改,由于修改可能产生的相互影响以及现场的历史情况。
情形三:将现有的设计或过程用于新的环境、场所或应用(假设对现有的设计或过程已有FMEA)。
FMEA的范围是新环境或场所对现有设计或过程的影响。
1.12跟踪采取有效的预防/纠正措施并对这些措施加以适当的跟踪,对这方面的要求无论怎样强调也不算过分。
措施应传递所有受影响的部门。
一个经过彻底思考、周密开发的FMEA,如果没有积极有效的预防/纠正措施,其价值将是非常有限的。
责任工程师负责确保所有的建议措施都得到实施或充分的强调。
FMEA是动态文件,应始终反映最新水平及最近的相关措施,包括开始生产以后发生的。
责任工程师有几种方法来确保建议的措施得到实施,包括但不限于以下几种:a.对设计、过程及图样进行评审,以确保建议的措施得到事实;b.确认更改已纳入到设计/装配/制造文件中;c.对设计/过程FMEA、FMEA的特殊应用以及控制计划进行评审。