生产性向上改善学习手册共36页
合集下载
生产性向上学习手册

1人*8H
14人*8H*21天
生产性
×100 =↓0.29%
作业优化、 年休假 加班管理 标准化、 管理 电子化
管理部
20
21
共性问题:
①考核目标设定依据?
②考核目标一刀切合理吗?
22
对应专项工作, 相关部门都有工 时增加,影响生 产性↓,如何解 决考核问题?
23
2月(春节) 基准能率 实际能率 生产性向上 3.34 3.10 -7%
1.二者计算方法和计算要素不同, 则计算结果不是同一个概念下的 含义 2.财务给的11年努力目标是在依 据生产能率的计算方法和要素计 算出该部门10年实际完成值的 基础上追加公司事业体努力目标 5%作成 3.下一步还要与相关部门一起研 讨“台数变化与生产能率的关系 以及标准能率如何制定” 30
困惑点3
★实际计算采用10年基准工时(固定不变值)
各工序加工完成 的并转下一工序 的合格品数量
生 产 = 能 率
制品时间(=基准时间*合格品数)
总作业时间
包含生产、磨试、改 善运搬、检查、辅产、改 善、专项、培训、调刀、 生产服务、5S、创意等实 际出勤工时
7
生产性向上的评价公式:
生产性 = 评价
实际生产能率 1 ×100% 上年生产能率
我们用大量的人 力、物力来生产 性向上,牵扯现 场很多精力,在 那种情况下做这 种考核管理?做 到那种状况会停 下来呢?
改善是无止境的,生 产性向上考评也是公 司发展必需要推进的。 当然,这种评价是有 周期性的,那要看达 到什么样的水平上才 可以结束。这也是我 们下一步要共同研讨 的课题。
31
改善和保全是为生产性向上 进行的投入,在以后的产出 会体现效果,理论上讲年度 内是不影响生产性向上的!
14人*8H*21天
生产性
×100 =↓0.29%
作业优化、 年休假 加班管理 标准化、 管理 电子化
管理部
20
21
共性问题:
①考核目标设定依据?
②考核目标一刀切合理吗?
22
对应专项工作, 相关部门都有工 时增加,影响生 产性↓,如何解 决考核问题?
23
2月(春节) 基准能率 实际能率 生产性向上 3.34 3.10 -7%
1.二者计算方法和计算要素不同, 则计算结果不是同一个概念下的 含义 2.财务给的11年努力目标是在依 据生产能率的计算方法和要素计 算出该部门10年实际完成值的 基础上追加公司事业体努力目标 5%作成 3.下一步还要与相关部门一起研 讨“台数变化与生产能率的关系 以及标准能率如何制定” 30
困惑点3
★实际计算采用10年基准工时(固定不变值)
各工序加工完成 的并转下一工序 的合格品数量
生 产 = 能 率
制品时间(=基准时间*合格品数)
总作业时间
包含生产、磨试、改 善运搬、检查、辅产、改 善、专项、培训、调刀、 生产服务、5S、创意等实 际出勤工时
7
生产性向上的评价公式:
生产性 = 评价
实际生产能率 1 ×100% 上年生产能率
我们用大量的人 力、物力来生产 性向上,牵扯现 场很多精力,在 那种情况下做这 种考核管理?做 到那种状况会停 下来呢?
改善是无止境的,生 产性向上考评也是公 司发展必需要推进的。 当然,这种评价是有 周期性的,那要看达 到什么样的水平上才 可以结束。这也是我 们下一步要共同研讨 的课题。
31
改善和保全是为生产性向上 进行的投入,在以后的产出 会体现效果,理论上讲年度 内是不影响生产性向上的!
韩国LG 革新领导教材 1 生产性向上与合理化教材
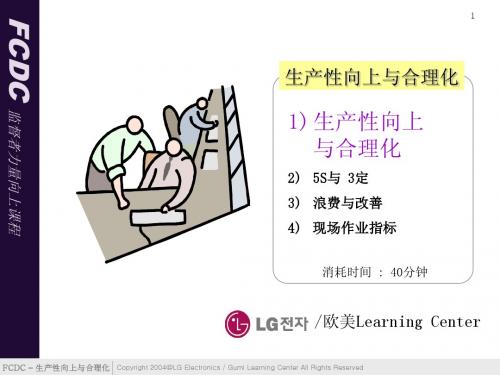
先入先出管理 Line 综合现况板 生产目标管理 异常 有,无管理
Ⅱ 阶段
用眼管理 稳定设置
Line 直线化 去除隔断 改善班运营 3定运动 Clean up 3 Step
Line Stop Lamp 设置 : Stop, 预警, 正常 异常警报灯运营 Line Pitch 设定 Pace Maker 设定 设备 Cover交换 : 硬塑,网 Control Box Cover交换 : 硬塑,玻璃 I.E 教育 改善班运营 定位置,定量,定容器 5 S 3 定 用眼管理
不良 发生工程 F/Proof化 F/Proof 竞进大会 – 本部,OBU 主管 : Boom Up
条件管理 管理点检项目 3次元 改善
F/Proof 履历管理 设备别 Spec 整备 各种仪器范围设定 : 用眼管理 为了条件(Spec) 维持的点检项目设定 Check Sheet化 - 周期性的点检Check 推进Process 1次元 对策 - 改善 + 标准化 遵守对策 F/Proof 化 3次元 对策 - 检查方案树立: 结果管理 Line别 3次元 改善活动展开 现场展示 现场发表会,内容共享,传播 3次元 竞进大会 2次元 对策
FCDC – 生产性向上与合理化 Copyright 2004@LG Electronics / Gumi Learning Center All Rights Reserved
学习
3. 3不驱逐
P.Q 改善班运营
优秀班.组长中心 组成 周间单位活动报告,评价,奖励 6个月 Rotation 自律改善 – 改善的成功体验 TPC 改善大学 –管理监督者对象
Time Check
周间 改善会议 - 周间 工程不良 现况 及 改善现况(制造Audit) 月评价会 - 品质 革新会议 顺次检查 项目 设定 Tag 粘贴 - 顺次检查王, 奖励 顺次检查 结果 F/Back, 现场展示 全数检查 实施 Check 周期,项目 设定 – 初,中,终物 管理 测量仪器 Jig化 - Check Die, 试料 保管 异常处理 4M 变更要因解决 所属 Lot 全数检查 Line别 对象 Item 设定 - 评价管理 品质 契约制 实施 RTN 不良率 管理 Q-Manager 活动 目标未达成 : 夜市场 对策发表 Consulting 指导
Ⅱ 阶段
用眼管理 稳定设置
Line 直线化 去除隔断 改善班运营 3定运动 Clean up 3 Step
Line Stop Lamp 设置 : Stop, 预警, 正常 异常警报灯运营 Line Pitch 设定 Pace Maker 设定 设备 Cover交换 : 硬塑,网 Control Box Cover交换 : 硬塑,玻璃 I.E 教育 改善班运营 定位置,定量,定容器 5 S 3 定 用眼管理
不良 发生工程 F/Proof化 F/Proof 竞进大会 – 本部,OBU 主管 : Boom Up
条件管理 管理点检项目 3次元 改善
F/Proof 履历管理 设备别 Spec 整备 各种仪器范围设定 : 用眼管理 为了条件(Spec) 维持的点检项目设定 Check Sheet化 - 周期性的点检Check 推进Process 1次元 对策 - 改善 + 标准化 遵守对策 F/Proof 化 3次元 对策 - 检查方案树立: 结果管理 Line别 3次元 改善活动展开 现场展示 现场发表会,内容共享,传播 3次元 竞进大会 2次元 对策
FCDC – 生产性向上与合理化 Copyright 2004@LG Electronics / Gumi Learning Center All Rights Reserved
学习
3. 3不驱逐
P.Q 改善班运营
优秀班.组长中心 组成 周间单位活动报告,评价,奖励 6个月 Rotation 自律改善 – 改善的成功体验 TPC 改善大学 –管理监督者对象
Time Check
周间 改善会议 - 周间 工程不良 现况 及 改善现况(制造Audit) 月评价会 - 品质 革新会议 顺次检查 项目 设定 Tag 粘贴 - 顺次检查王, 奖励 顺次检查 结果 F/Back, 现场展示 全数检查 实施 Check 周期,项目 设定 – 初,中,终物 管理 测量仪器 Jig化 - Check Die, 试料 保管 异常处理 4M 变更要因解决 所属 Lot 全数检查 Line别 对象 Item 设定 - 评价管理 品质 契约制 实施 RTN 不良率 管理 Q-Manager 活动 目标未达成 : 夜市场 对策发表 Consulting 指导
精益生产现场管理和改善培训教材
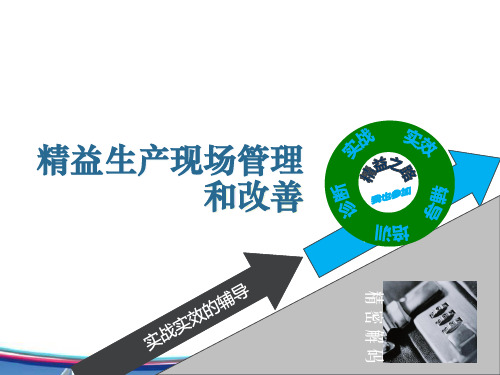
– 张贴操作规范,以便全 体人员都能看到
•快速换线
– 色标系统和模子以解决 标识问题
– 确定换线小组,提高 “紧迫意识”
•全员生产维护
– 采用标识展示设备检查 点
– 在量具上做标记,方便 显示不合格情况
目视管理评价 目视管理要符合以下要求: ---无论谁都能判明异常和好坏; ---能迅速判断,且判断的准确程度高; ---判断结果不会因人而异。
管理看板的作用
1、展示改善成绩,让参与者有成就感、自豪感 ; 2、营造竞争的氛围; 3、营造现场活力的强有力手段; 4、明确管理状况,营造有形及无形的压力,有利于 工作的推进; 5、树立良好的企业形象(让客户或其他人员由衷地 赞叹公司的管理水平); 6、展示改善的过程,让大家都能学到好的方法及技 巧。
快速换线、预防性维护)
•对员工的影响
– 提高员工的工作效率、安全性和士气
目视管理的5个基本要求
•5S
– 采用颜色和标牌,明确 标示操作部位
– 运用图表公布5S 检查结 果
•解决问题
– 利用问题板追踪项目进 程
– 张贴帕累托图来展示存 在的最大问题
目视 管理
•标准操作流程
– 采用示意图明确标准流 程
目视工作现场的建立
在实施前得到相关方面的认同 要坚持用同一个标准 要从流程和人/机/料/法/环方面综合考虑 必须取得高层领导的支持
5S 基本 → TPM IE TQM JIT 6σ → LP 精益之路
1
实
战 内
2
容
3
看板是如何提升管理的精度? 看板有哪些,如何确定? 围绕看板,构建目标管理运作平台
目视化工作现场的建立
建立目视化控制持续改进计划 检验和修正目视控制 创建和实施目视控制 协调和标准化目视控制 制订目视化控制计划
•快速换线
– 色标系统和模子以解决 标识问题
– 确定换线小组,提高 “紧迫意识”
•全员生产维护
– 采用标识展示设备检查 点
– 在量具上做标记,方便 显示不合格情况
目视管理评价 目视管理要符合以下要求: ---无论谁都能判明异常和好坏; ---能迅速判断,且判断的准确程度高; ---判断结果不会因人而异。
管理看板的作用
1、展示改善成绩,让参与者有成就感、自豪感 ; 2、营造竞争的氛围; 3、营造现场活力的强有力手段; 4、明确管理状况,营造有形及无形的压力,有利于 工作的推进; 5、树立良好的企业形象(让客户或其他人员由衷地 赞叹公司的管理水平); 6、展示改善的过程,让大家都能学到好的方法及技 巧。
快速换线、预防性维护)
•对员工的影响
– 提高员工的工作效率、安全性和士气
目视管理的5个基本要求
•5S
– 采用颜色和标牌,明确 标示操作部位
– 运用图表公布5S 检查结 果
•解决问题
– 利用问题板追踪项目进 程
– 张贴帕累托图来展示存 在的最大问题
目视 管理
•标准操作流程
– 采用示意图明确标准流 程
目视工作现场的建立
在实施前得到相关方面的认同 要坚持用同一个标准 要从流程和人/机/料/法/环方面综合考虑 必须取得高层领导的支持
5S 基本 → TPM IE TQM JIT 6σ → LP 精益之路
1
实
战 内
2
容
3
看板是如何提升管理的精度? 看板有哪些,如何确定? 围绕看板,构建目标管理运作平台
目视化工作现场的建立
建立目视化控制持续改进计划 检验和修正目视控制 创建和实施目视控制 协调和标准化目视控制 制订目视化控制计划
生产性向上培训
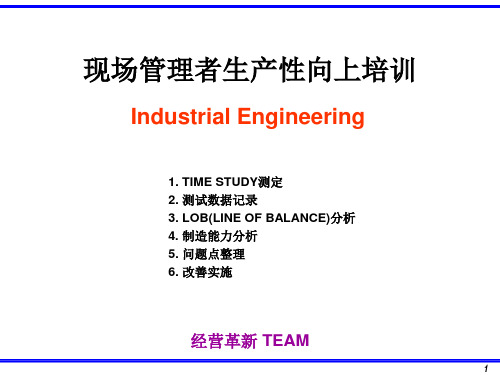
实际T/T : 12.1秒
100%
非运转 LOSS ( 13% )
非驱动时间(流失, 瞬间停止) 60分可以做出的能力
LINE
E 37名 460
能力T/T : 10.5秒
能力运转 LOSS ( 13% )
(400分) ※ 能力 LOSS 损失时间 -> 460分 × 13% = 59.8%
活
N/T : 8.96秒
◆ 改恶 – 劳动强化:
没有进行浪费消除, 为了达成目标, 要制造主体追加努力, 熟练度, 速度等导致作业疲劳(设备压力). 从而品质下降, 作业散布, 设备故障, 达成的成果缺乏持久性.
◆ 制造能力提升的改善(删除, 公用, 分配, 自动化)
非正规作业改善 作业散布改善 作业条件, 环境, 方法, 动作改善 道具, 工具, JIG改善 简易自动化推进 作业量再分配
对制造现场产生的运转LOSS进行分析.
5. 问题点整理 分析现场的不足, 提出最佳的改善提案.
6. 改善实施
通过现场问题点, 列出改善课题进行改善. (并通过照片反应改善前和改善后的区别)
2
词汇解释
种 类 定 义 计算方法
工作时间(460分) 生产数 TIME STUDY实测
TACK TIME T/T CYCLE TIME C/T NECK TIME
0.00
0.00
0.00
0.00
0.00
0.00 0.00 0.00 0.00 0.00 0.00 0.00 0.00 0.00 0.00
0.00
0.00
0.00
0.00
0.00
0.00
8
改善实施STEP
STEP
1 STEP
100%
非运转 LOSS ( 13% )
非驱动时间(流失, 瞬间停止) 60分可以做出的能力
LINE
E 37名 460
能力T/T : 10.5秒
能力运转 LOSS ( 13% )
(400分) ※ 能力 LOSS 损失时间 -> 460分 × 13% = 59.8%
活
N/T : 8.96秒
◆ 改恶 – 劳动强化:
没有进行浪费消除, 为了达成目标, 要制造主体追加努力, 熟练度, 速度等导致作业疲劳(设备压力). 从而品质下降, 作业散布, 设备故障, 达成的成果缺乏持久性.
◆ 制造能力提升的改善(删除, 公用, 分配, 自动化)
非正规作业改善 作业散布改善 作业条件, 环境, 方法, 动作改善 道具, 工具, JIG改善 简易自动化推进 作业量再分配
对制造现场产生的运转LOSS进行分析.
5. 问题点整理 分析现场的不足, 提出最佳的改善提案.
6. 改善实施
通过现场问题点, 列出改善课题进行改善. (并通过照片反应改善前和改善后的区别)
2
词汇解释
种 类 定 义 计算方法
工作时间(460分) 生产数 TIME STUDY实测
TACK TIME T/T CYCLE TIME C/T NECK TIME
0.00
0.00
0.00
0.00
0.00
0.00 0.00 0.00 0.00 0.00 0.00 0.00 0.00 0.00 0.00
0.00
0.00
0.00
0.00
0.00
0.00
8
改善实施STEP
STEP
1 STEP
清益管理课程生产性能向上
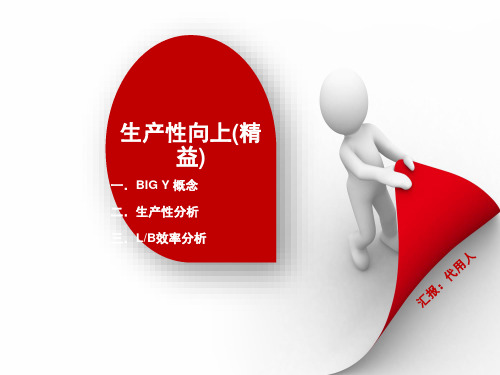
生产性向上(精 益)
一.BIG Y 概念
二.生产性分析
三.L/B效率分析
1.BIG Y 概念
问题的类型
问题的类型
①发生型:已经发生的问题(脱离,未达到目标) ②探索型:做的更好的问题(改善,强化目前) ③设定型:以后要怎么做的问题(研发,避免缺陷,质量飞跃)
③ ②
目标
①
过去
现在
未来
原因
目标
发生型 探索型 设定型
间接工时 *(100%)
总出勤工时
无作业工时 *(100%)
直接工时
再作业损失率 =
再作业工时 *(100%)
实动工时
生产线损失率 =
生产线损失工时 *(100%)
直接工时
总和损失率 = 总和损失工时 *(100%)
总出勤工时
2.生产性分析
设备效率LOSS的结构
作业时间
负荷时间
计划
稼动时间
停止
精密稼动时间
• 检讨 RTY(生产性)革新重要度/自己解决的可能性
树立改善计划
• 现象/目标,活动方法,完成日程及责任人
实施内容
• 关联部门的改善课题 • 发行改善邀请书
2.生产性分析
质量层面
从质量层面来找出生产现场能力低下的工序
工程 工程不良Data 直行率
RTY IT 输入
• 工程自检,互检数据 --LQC,OQC 数据
*(100%)
平衡损失率 = 1 - L/B 效率
操作内容
精密作业时间的测定 记录T.T,人员数,生产量/Hr 计算L/B效率 制作管理工程图
使用E.C.R.S T.T上升,L/B上升,人员减少 改善后时间记录 2周
一.BIG Y 概念
二.生产性分析
三.L/B效率分析
1.BIG Y 概念
问题的类型
问题的类型
①发生型:已经发生的问题(脱离,未达到目标) ②探索型:做的更好的问题(改善,强化目前) ③设定型:以后要怎么做的问题(研发,避免缺陷,质量飞跃)
③ ②
目标
①
过去
现在
未来
原因
目标
发生型 探索型 设定型
间接工时 *(100%)
总出勤工时
无作业工时 *(100%)
直接工时
再作业损失率 =
再作业工时 *(100%)
实动工时
生产线损失率 =
生产线损失工时 *(100%)
直接工时
总和损失率 = 总和损失工时 *(100%)
总出勤工时
2.生产性分析
设备效率LOSS的结构
作业时间
负荷时间
计划
稼动时间
停止
精密稼动时间
• 检讨 RTY(生产性)革新重要度/自己解决的可能性
树立改善计划
• 现象/目标,活动方法,完成日程及责任人
实施内容
• 关联部门的改善课题 • 发行改善邀请书
2.生产性分析
质量层面
从质量层面来找出生产现场能力低下的工序
工程 工程不良Data 直行率
RTY IT 输入
• 工程自检,互检数据 --LQC,OQC 数据
*(100%)
平衡损失率 = 1 - L/B 效率
操作内容
精密作业时间的测定 记录T.T,人员数,生产量/Hr 计算L/B效率 制作管理工程图
使用E.C.R.S T.T上升,L/B上升,人员减少 改善后时间记录 2周
现场生产力提升与工作效率改善
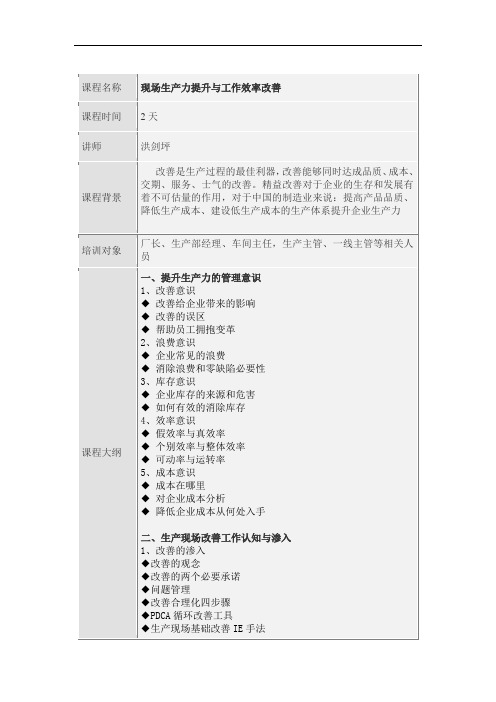
1、精益化生产流程优化与改善
◆流程优化的内容
◆流程优化的步骤
◆流程改善四个原则
◆向工艺流程要效益
◆向平面流程要效益
◆向移动方式要效益
◆向均衡生产要效益
2、精益化柔性生产单元与U型布局
◆单件流动
◆按工艺流程布置设备
◆生产速度同步化
◆设备小型化
◆生产线U形化
◆多工序操作
◆走动作业
◆员工多能化
◆一个流生产的推行步骤
◆生产线平衡分析与改善
◆生产线平衡改善方法要领
◆平衡线对降低成本和减少浪费的作用
※案例研讨分析
5、精益均衡化生产
◆准时化的前提条件——均衡化
◆均衡化的生产工序
◆消除了不平均现象的均衡化
◆批量生产和均衡化生产
◆产品总量均衡化
◆种类的均衡化
◆生产均衡化之混合生产
◆如何实现混合生产
◆品种及生产数的排列
※案例研讨分析
3、准时化拉动生产与看板管理
◆快速响应客户的拉动系统
◆拉动系统图示
◆拉动式生产之信息传递工具---看板
◆生产看板管理--符合JIT ,压缩库存量
◆看板运行的种类和工作原理
◆看板方式的六个原则
◆决定看板的数目
◆领取看板的运行过程
※精益企业看板案例分析
4、实现生产线平衡效率最大化
◆何为生产线平衡
◆平衡线计算
◆降低企业成本从何处入手
二、生产现场改善工作认知与渗入
1、改善的渗入
◆改善的观念
◆改善的两个必要承诺
◆问题管理
◆改善合理化四步骤
◆PDCA循环改善工具
◆生产现场基础改善IE手法
◆识别并改善企业瓶颈
◆流程优化的内容
◆流程优化的步骤
◆流程改善四个原则
◆向工艺流程要效益
◆向平面流程要效益
◆向移动方式要效益
◆向均衡生产要效益
2、精益化柔性生产单元与U型布局
◆单件流动
◆按工艺流程布置设备
◆生产速度同步化
◆设备小型化
◆生产线U形化
◆多工序操作
◆走动作业
◆员工多能化
◆一个流生产的推行步骤
◆生产线平衡分析与改善
◆生产线平衡改善方法要领
◆平衡线对降低成本和减少浪费的作用
※案例研讨分析
5、精益均衡化生产
◆准时化的前提条件——均衡化
◆均衡化的生产工序
◆消除了不平均现象的均衡化
◆批量生产和均衡化生产
◆产品总量均衡化
◆种类的均衡化
◆生产均衡化之混合生产
◆如何实现混合生产
◆品种及生产数的排列
※案例研讨分析
3、准时化拉动生产与看板管理
◆快速响应客户的拉动系统
◆拉动系统图示
◆拉动式生产之信息传递工具---看板
◆生产看板管理--符合JIT ,压缩库存量
◆看板运行的种类和工作原理
◆看板方式的六个原则
◆决定看板的数目
◆领取看板的运行过程
※精益企业看板案例分析
4、实现生产线平衡效率最大化
◆何为生产线平衡
◆平衡线计算
◆降低企业成本从何处入手
二、生产现场改善工作认知与渗入
1、改善的渗入
◆改善的观念
◆改善的两个必要承诺
◆问题管理
◆改善合理化四步骤
◆PDCA循环改善工具
◆生产现场基础改善IE手法
◆识别并改善企业瓶颈
生产性向上改善

1次
级
部门
威海星地电子有限公司
级
最终
A4(297×210)
级
F031-003 REV.02
员工技能培训不足
事例名 改善部门 员工技能资格认定改善 日程 J线 2010.9.13 2010.9.13 完成人
肖丽英
开始日
完成日
提案人
肖丽英
改善前
改善后
返修人员及一些特殊工种操作人员没有技能资格认证,只有 “返修品投入口”及某某工位的标识字样,不能保证工作效率 和产品品质,产品无追溯性和明确责任人。
原材料存放乱。 检查其他线产品识别 原材料速度慢。 制作不良样品困难。 3901-000493产品沾 锡困难。
7.22 7.26 7.28 7.30
7.29 8.02 7.28 7.30
苑胜
原因分析
设备故障 1、设备使用点检、保养不规范
非 生 产 时 间
1、计划不能预知 LOT 更换 2、图纸、材料等准备不足 3、检查JIG准备不到位、使用不方便 1、原材料不足、不良
使用技巧
生产一部J线计划
计划: 项目 掌握现象 设定目标 实绩:
活动时间
( 5-6)月 (7-8 )月 ( 9-11)月 ( 12 )月
担当
使用技巧
肖丽英 肖丽英 肖丽英 纪庆云
肖丽英 肖丽英
找出不合理清单 原因分析 建立对策和实施 掌握效果 标准化及事后管理 反省及向后计划
肖丽英 肖丽英 肖丽英
威海星地电子有限公司
员工技能培训不足
事例名 改善部门 员工培训资料改善 日程 生产一部J线 2010.10.05 2010.10.13 完成人 王蕾 开始日 完成日 提案人 肖丽英
精选提案改善生产车间培训教材

留意日常工作
10.在大小尺寸,长度方面是否有浪費的情況?11.在重量宽度方面是否出現浪費?12.有关不良品废弃物等是否有浪費的行为?13.在工作的作业流程上,是否发生了停留于手中現象?14.有沒有浪費的工程或作业之事发生?15.是否有过于費事的情形发生?16.提高作业速度后,是否有浪費于裝置或手中的事情发生?17.是否有无谓的分割.统一之事发生?18.是否有无谓的方式,制度持续在运转?19.是否在工作上有太过不合理的负担?
8.5
66.8
8.3
66.8
0.0
68.5
1.7
76.6
8.1
80.2
3.6
80.2
0.0
82.0
1.8
89.9
7.9
93.8
3.9
95.8
2.0
97.8
2.0
106.0
8.2
109.6
3.6
109.6
0.0
111.4
1.8
121.3
9.9
4.0
4.0
4.0
0.0
6.4
2.4
15.2
8.8
19.0
3.8
制程防呆
制程防呆
制程防呆
制程防呆
制程防呆
制程防呆
手法名称 防止错误法 (防错法)
(Fool-Proof)
目的 认识“防呆法”的意义及学习如何应用“防呆法”的原理于我们的工作上,以避免工作错误的发生,进而达到“第一次就把工作做对”之境界.
含义
制程防呆
意 义 防呆法,其义即是防止人做错事.亦即,连
作业内容
测量点
作业时间(连续测量10次﹐取平均值)
时间价值
10.在大小尺寸,长度方面是否有浪費的情況?11.在重量宽度方面是否出現浪費?12.有关不良品废弃物等是否有浪費的行为?13.在工作的作业流程上,是否发生了停留于手中現象?14.有沒有浪費的工程或作业之事发生?15.是否有过于費事的情形发生?16.提高作业速度后,是否有浪費于裝置或手中的事情发生?17.是否有无谓的分割.统一之事发生?18.是否有无谓的方式,制度持续在运转?19.是否在工作上有太过不合理的负担?
8.5
66.8
8.3
66.8
0.0
68.5
1.7
76.6
8.1
80.2
3.6
80.2
0.0
82.0
1.8
89.9
7.9
93.8
3.9
95.8
2.0
97.8
2.0
106.0
8.2
109.6
3.6
109.6
0.0
111.4
1.8
121.3
9.9
4.0
4.0
4.0
0.0
6.4
2.4
15.2
8.8
19.0
3.8
制程防呆
制程防呆
制程防呆
制程防呆
制程防呆
制程防呆
手法名称 防止错误法 (防错法)
(Fool-Proof)
目的 认识“防呆法”的意义及学习如何应用“防呆法”的原理于我们的工作上,以避免工作错误的发生,进而达到“第一次就把工作做对”之境界.
含义
制程防呆
意 义 防呆法,其义即是防止人做错事.亦即,连
作业内容
测量点
作业时间(连续测量10次﹐取平均值)
时间价值
- 1、下载文档前请自行甄别文档内容的完整性,平台不提供额外的编辑、内容补充、找答案等附加服务。
- 2、"仅部分预览"的文档,不可在线预览部分如存在完整性等问题,可反馈申请退款(可完整预览的文档不适用该条件!)。
- 3、如文档侵犯您的权益,请联系客服反馈,我们会尽快为您处理(人工客服工作时间:9:00-18:30)。
END
16、业余生活要有意义,不要越轨。——华盛顿 17、一个人即使已登上顶峰,也仍要自强不息。——罗素·贝克 18、最大的挑战和突破在于用人,而用人最大的突破在于信任人。——马云 19、自己活着,就是为了使别人过得更美好。——雷锋 20、要掌握书,莫被书掌握;要为生而读,莫为读而生。——布尔沃
生产性向上,就像为 了城墙 而战斗 一样。 ——赫 拉克利 特 17、人类对于不公正的行为加以指责 ,并非 因为他 们愿意 做出这 种行为 ,而是 惟恐自 己会成 为这种 行为的 牺牲者 。—— 柏拉图 18、制定法律法令,就是为了不让强 者做什 么事都 横行霸 道。— —奥维 德 19、法律是社会的习惯和思想的结晶 。—— 托·伍·威尔逊 20、人们嘴上挂着的法律,其真实含 义是财 富。— —爱献 生