铝合金铸件热处理
铝合金铸件的热处理

铝合金铸件的热处理铝合金铸件的热处理是指按某一热处理规范,控制加热温度、保温时间和冷却速度,改变合金的组织,其主要目的是:提高力学性能,增强耐腐蚀性能,改善加工性能,获得尺寸的稳定性。
铝合金铸件的热处理工艺可以分为如下四类:1 退火处理将铝合金铸件加热到较高的温度,一般约为300 ℃左右,保温一定的时间后,随炉冷却到室温的工艺称为退火。
在退火过程中固溶体发生分解,第二相质点发生聚集,可以消除铸件的内应力,稳定铸件尺寸,减少变形,增大铸件的塑性。
2 固溶处理固溶处理把铸件加热到尽可能高的温度,接近于共晶体的熔点,在该温度下保持足够长的时间,并随后快速冷却,使强化组元最大限度的溶解,这种高温状态被固定保存到室温,该过程称为固溶处理。
固溶处理可以提高铸件的强度和塑性,改善合金的耐腐蚀性能。
固溶处理的效果主要取决于下列三个因素:(1)固溶处理温度。
温度越高,强化元素溶解速度越快,强化效果越好。
一般加热温度的上限低于合金开始过烧温度,而加热温度的下限应使强化组元尽可能多地溶入固溶体中。
为了获得最好的固溶强化效果,而又不便合金过烧,有时采用分级加热的办法,即在低熔点共晶温度下保温,使组元扩散溶解后,低熔点共晶不存在,再升到更高的温度进行保温和淬火。
固溶处理时,还应当注意加热的升温速度不宜过快,以免铸件发生变形和局部聚集的低熔点组织熔化而产生过烧。
固溶热处理的悴火转移时间应尽可能地短,一般应不大于15s,以免合金元素的扩散析出而降低合金的性能。
(2)保温时间。
保温时间是由强化元素的溶解速度来决定的,这取决于合金的种类、成分、组织、铸造方法和铸件的形状及壁厚。
铸造铝合金的保温时间比变形铝合金要长得多,通常由试验确定,一般的砂型铸件比同类型的金属型铸件要延长20%-25% 。
(3)冷却速度。
淬火时给予铸件的冷却速度越大,使固溶体自高温状态保存下来的过饱和度也越高,从而使铸件获得高的力学性能,但同时所形成的内应力也越大,使铸件变形的可能性也越大。
铝合金热处理方法汇总
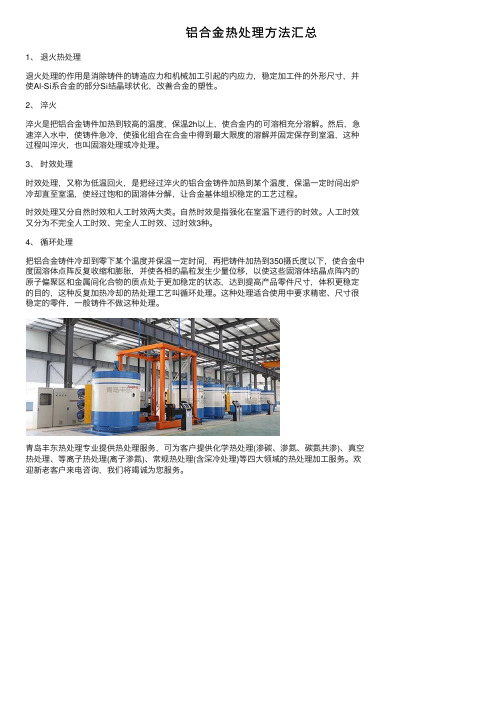
铝合⾦热处理⽅法汇总
1、退⽕热处理
退⽕处理的作⽤是消除铸件的铸造应⼒和机械加⼯引起的内应⼒,稳定加⼯件的外形尺⼨,并使Al-Si系合⾦的部分Si结晶球状化,改善合⾦的塑性。
2、淬⽕
淬⽕是把铝合⾦铸件加热到较⾼的温度,保温2h以上,使合⾦内的可溶相充分溶解。
然后,急速淬⼊⽔中,使铸件急冷,使强化组合在合⾦中得到最⼤限度的溶解并固定保存到室温,这种过程叫淬⽕,也叫固溶处理或冷处理。
3、时效处理
时效处理,⼜称为低温回⽕,是把经过淬⽕的铝合⾦铸件加热到某个温度,保温⼀定时间出炉冷却直⾄室温,使经过饱和的固溶体分解,让合⾦基体组织稳定的⼯艺过程。
时效处理⼜分⾃然时效和⼈⼯时效两⼤类。
⾃然时效是指强化在室温下进⾏的时效。
⼈⼯时效⼜分为不完全⼈⼯时效、完全⼈⼯时效、过时效3种。
4、循环处理
把铝合⾦铸件冷却到零下某个温度并保温⼀定时间,再把铸件加热到350摄⽒度以下,使合⾦中度固溶体点阵反复收缩和膨胀,并使各相的晶粒发⽣少量位移,以使这些固溶体结晶点阵内的原⼦偏聚区和⾦属间化合物的质点处于更加稳定的状态,达到提⾼产品零件尺⼨,体积更稳定的⽬的,这种反复加热冷却的热处理⼯艺叫循环处理。
这种处理适合使⽤中要求精密、尺⼨很稳定的零件,⼀般铸件不做这种处理。
青岛丰东热处理专业提供热处理服务,可为客户提供化学热处理(渗碳、渗氮、碳氮共渗)、真空热处理、等离⼦热处理(离⼦渗氮)、常规热处理(含深冷处理)等四⼤领域的热处理加⼯服务。
欢迎新⽼客户来电咨询,我们将竭诚为您服务。
铝合金铸件热处理工艺参数

------
------
-------
180±5
3~5
空冷
轻载荷的零件
T2
------
------
-------
290±5
2~4
空冷
要求尺寸稳定并消除应力的零件
T5
515±5
3~6
60~100℃
175±5
3~5
空冷
在低于175℃下下重载荷的零件
T7
515±5
3~6
60~100℃
230±5
3~5
空冷
10~14
空冷
要求高强度高硬度的零件
175±5(J)
7~14
T7
510±5
3~5
80~100℃
200±250
3
空冷
高温下工作的零件如活塞
ZL203
T4
515±5
10~15
60~100℃
------
------
-------
要求高强度高塑性的零件
T5
515±5
10~15
60~100℃
150±5
2~4
空冷
__
680~750
1.2~1.4
铝合金铸件热处理工艺参数(一)
代号
热处理状态
淬火
时效
用途举例
加热温度℃
保温时间h
冷却(水中)
加热温度℃
保温时间h
冷却
ZL101
T1
------
------
-------
230±5
7~9
空冷
改善被切削性能
T4
535±5
2~6
60~100℃
铝合金热处理基本形式
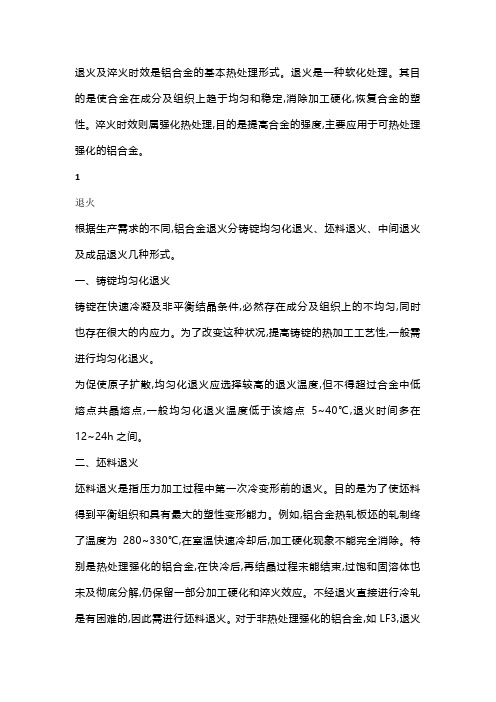
退火及淬火时效是铝合金的基本热处理形式。
退火是一种软化处理。
其目的是使合金在成分及组织上趋于均匀和稳定,消除加工硬化,恢复合金的塑性。
淬火时效则属强化热处理,目的是提高合金的强度,主要应用于可热处理强化的铝合金。
1退火根据生产需求的不同,铝合金退火分铸锭均匀化退火、坯料退火、中间退火及成品退火几种形式。
一、铸锭均匀化退火铸锭在快速冷凝及非平衡结晶条件,必然存在成分及组织上的不均匀,同时也存在很大的内应力。
为了改变这种状况,提高铸锭的热加工工艺性,一般需进行均匀化退火。
为促使原子扩散,均匀化退火应选择较高的退火温度,但不得超过合金中低熔点共晶熔点,一般均匀化退火温度低于该熔点5~40℃,退火时间多在12~24h之间。
二、坯料退火坯料退火是指压力加工过程中第一次冷变形前的退火。
目的是为了使坯料得到平衡组织和具有最大的塑性变形能力。
例如,铝合金热轧板坯的轧制终了温度为280~330℃,在室温快速冷却后,加工硬化现象不能完全消除。
特别是热处理强化的铝合金,在快冷后,再结晶过程未能结束,过饱和固溶体也未及彻底分解,仍保留一部分加工硬化和淬火效应。
不经退火直接进行冷轧是有困难的,因此需进行坯料退火。
对于非热处理强化的铝合金,如LF3,退火温度为370~470℃,保温1.5~2.5H后空冷,用于冷拉伸管加工的坯料、退火温度应适当高一些,可选上限温度。
对于可热处理强化的铝合金,如LY11及LY12,坯料退火温度为390~450℃,保温1~3H,随后在炉中以不大于30℃/h的速度冷却到270℃以下再出炉空冷。
三、中间退火中间退火是指冷变形工序之间的退火,其目的是为了消除加工硬化,以利于继续冷加工变形。
一般来说,经过坯料退火后的材料,在承受45~85%的冷变形后,如不进行中间退火而继续冷加工将会发生困难。
中间退火的工艺制度基本上与坯料退火相同。
根据对冷变形程度的要求,中间退火可分为完全退火(总变形量ε≈60~70%),简单退火(ε≤50%)和轻微退火(ε≈30~40%)三种。
铝合金热处理工艺

铝合金热处理工艺作者:中国铝板带箔信息中心日期:2006-12-16 点击数:2843.1铝合金热处理原理铝合金铸件的热处理就是选用某一热处理规范,控制加热速度升到某一相应温度下保温一定时间并以一定得速度冷却,改变其合金的组织,其主要目的是提高合金的力学性能,增强耐腐蚀性能,改善加工型能,获得尺寸的稳定性。
3.1.1铝合金热处理特点众所周知,对于含碳量较高的钢,经淬火后立即获得很高的硬度,而塑性则很低。
然而对铝合金并不然,铝合金刚淬火后,强度与硬度并不立即升高,至于塑性非但没有下降,反而有所上升。
但这种淬火后的合金,放置一段时间(如4~6昼夜后),强度和硬度会显著提高,而塑性则明显降低。
淬火后铝合金的强度、硬度随时间增长而显著提高的现象,称为时效。
时效可以在常温下发生,称自然时效,也可以在高于室温的某一温度范围(如100~200℃)内发生,称人工时效。
3.1.2铝合金时效强化原理铝合金的时效硬化是一个相当复杂的过程,它不仅决定于合金的组成、时效工艺,还取决于合金在生产过程中缩造成的缺陷,特别是空位、位错的数量和分布等。
目前普遍认为时效硬化是溶质原子偏聚形成硬化区的结果。
铝合金在淬火加热时,合金中形成了空位,在淬火时,由于冷却快,这些空位来不及移出,便被“固定”在晶体内。
这些在过饱和固溶体内的空位大多与溶质原子结合在一起。
由于过饱和固溶体处于不稳定状态,必然向平衡状态转变,空位的存在,加速了溶质原子的扩散速度,因而加速了溶质原子的偏聚。
硬化区的大小和数量取决于淬火温度与淬火冷却速度。
淬火温度越高,空位浓度越大,硬化区的数量也就越多,硬化区的尺寸减小。
淬火冷却速度越大,固溶体内所固定的空位越多,有利于增加硬化区的数量,减小硬化区的尺寸。
沉淀硬化合金系的一个基本特征是随温度而变化的平衡固溶度,即随温度增加固溶度增加,大多数可热处理强化的的铝合金都符合这一条件。
沉淀硬化所要求的溶解度-温度关系,可用铝铜系的Al-4Cu合金说明合金时效的组成和结构的变化。
铝的热处理

铝的热处理铝合金铸件的热处理是指按某一热处理规范,控制加热温度、保温时间和冷却速度,改变合金的组织,其主要目的是:提高力学性能,增强耐腐蚀性能,改善加工性能,获得尺寸的稳定性。
铝合金铸件的热处理工艺可以分为如下四类:1。
退火处理将铝合金铸件加热到较高的温度,一般约为300 ℃左右,保温一定的时间后,随炉冷却到室温的工艺称为退火。
在退火过程中固溶体发生分解,第二相质点发生聚集,可以消除铸件的内应力,稳定铸件尺寸,减少变形,增大铸件的塑性。
2。
固溶处理把铸件加热到尽可能高的温度,接近于共晶体的熔点,在该温度下保持足够长的时间,并随后快速冷却,使强化组元最大限度的溶解,这种高温状态被固定保存到室温,该过程称为固溶处理。
固溶处理可以提高铸件的强度和塑性,改善合金的耐腐蚀性能。
固溶处理的效果主要取决于下列三个因素:(1)固溶处理温度。
温度越高,强化元素溶解速度越快,强化效果越好。
一般加热温度的上限低于合金开始过烧温度,而加热温度的下限应使强化组元尽可能多地溶入固溶体中。
为了获得最好的固溶强化效果,而又不便合金过烧,有时采用分级加热的办法,即在低熔点共晶温度下保温,使组元扩散溶解后,低熔点共晶不存在,再升到更高的温度进行保温和淬火。
固溶处理时,还应当注意加热的升温速度不宜过快,以免铸件发生变形和局部聚集的低熔点组织熔化而产生过烧。
固溶热处理的悴火转移时间应尽可能地短,一般应不大于15s,以免合金元素的扩散析出而降低合金的性能。
(2)保温时间。
保温时间是由强化元素的溶解速度来决定的,这取决于合金的种类、成分、组织、铸造方法和铸件的形状及壁厚。
铸造铝合金的保温时间比变形铝合金要长得多,通常由试验确定,一般的砂型铸件比同类型的金属型铸件要延长20%-25% 。
(3)冷却速度。
淬火时给予铸件的冷却速度越大,使固溶体自高温状态保存下来的过饱和度也越高,从而使铸件获得高的力学性能,但同时所形成的内应力也越大,使铸件变形的可能性也越大。
铝合金压铸件 热处理

铝合金压铸件热处理
热处理是指通过对铝合金压铸件进行加热和冷却处理,改变其组织结构和性能的工艺。
热处理主要包括固溶处理、时效处理和应力退火处理。
固溶处理是将铝合金压铸件加热至固溶温度,并保持一段时间,使溶解在晶粒中的合金元素均匀分布,形成固溶体。
然后通过快速冷却,使合金元素固溶体保持在固溶状态,以提高硬度和强度。
时效处理是在固溶处理后,将铝合金压铸件再次加热至一定温度,然后保持一段时间,使合金元素析出形成细小的抗拉强度相,提高材料的硬度和强度。
应力退火处理是在完成固溶和时效处理后,将铝合金压铸件加热至一定温度,然后通过缓慢冷却,以消除合金在加工过程中产生的残余应力,提高材料的韧性和耐腐蚀性。
热处理可以改善铝合金压铸件的机械性能和物理性能,提高其强度、硬度和耐磨性等特性,使其更适合特定的工程应用。
铸造铝合金热处理质量缺陷及其消除与预防
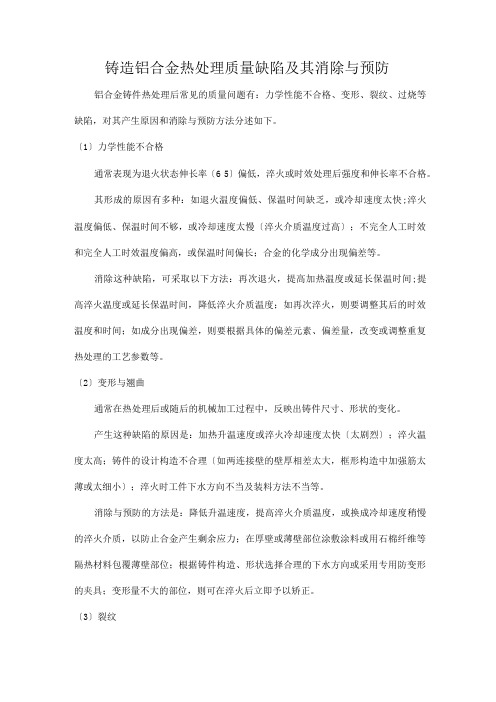
铸造铝合金热处理质量缺陷及其消除与预防铝合金铸件热处理后常见的质量问题有:力学性能不合格、变形、裂纹、过烧等缺陷,对其产生原因和消除与预防方法分述如下。
〔1〕力学性能不合格通常表现为退火状态伸长率〔6 5〕偏低,淬火或时效处理后强度和伸长率不合格。
其形成的原因有多种:如退火温度偏低、保温时间缺乏,或冷却速度太快;淬火温度偏低、保温时间不够,或冷却速度太慢〔淬火介质温度过高〕;不完全人工时效和完全人工时效温度偏高,或保温时间偏长;合金的化学成分出现偏差等。
消除这种缺陷,可采取以下方法:再次退火,提高加热温度或延长保温时间;提高淬火温度或延长保温时间,降低淬火介质温度;如再次淬火,则要调整其后的时效温度和时间;如成分出现偏差,则要根据具体的偏差元素、偏差量,改变或调整重复热处理的工艺参数等。
〔2〕变形与翘曲通常在热处理后或随后的机械加工过程中,反映出铸件尺寸、形状的变化。
产生这种缺陷的原因是:加热升温速度或淬火冷却速度太快〔太剧烈〕;淬火温度太高;铸件的设计构造不合理〔如两连接壁的壁厚相差太大,框形构造中加强筋太薄或太细小〕;淬火时工件下水方向不当及装料方法不当等。
消除与预防的方法是:降低升温速度,提高淬火介质温度,或换成冷却速度稍慢的淬火介质,以防止合金产生剩余应力;在厚壁或薄壁部位涂敷涂料或用石棉纤维等隔热材料包覆薄壁部位;根据铸件构造、形状选择合理的下水方向或采用专用防变形的夹具;变形量不大的部位,则可在淬火后立即予以矫正。
〔3〕裂纹表现为淬火后的铸件外表用肉眼可以看到明显的裂纹,或通过荧光检查肉眼看不见的微细裂纹。
裂纹多曲折不直并呈暗灰色。
产生裂纹的原因是:加热速度太快,淬火时冷却太快〔淬火温度过高或淬火介质温度过低,或淬火介质冷却速度太快〕;铸件构造设计不合理〔两连接壁壁厚差太大,框形件中间的加强筋太薄或太细小〕;装炉方法不当或下水方向不对;炉温不均匀,使铸件温度不均匀等。
消除与预防的方法是:减慢升温速度或采取等温淬火工艺;提高淬火介质温度或换成冷却速度慢的淬火介质;在壁厚或薄壁部位涂敷涂料或在薄壁部位包覆石棉等隔热材料;采用专用防开裂的淬火夹具,并选择正确的下水方向。
- 1、下载文档前请自行甄别文档内容的完整性,平台不提供额外的编辑、内容补充、找答案等附加服务。
- 2、"仅部分预览"的文档,不可在线预览部分如存在完整性等问题,可反馈申请退款(可完整预览的文档不适用该条件!)。
- 3、如文档侵犯您的权益,请联系客服反馈,我们会尽快为您处理(人工客服工作时间:9:00-18:30)。
2011-11-4
热处理工艺
铝合金的热处理
2011-11-4
热处理工艺一般包括加热 保温 冷却 加热、保温 冷却三个过程。 加热 保温、冷却 加热:一般都是加热到相变温度以上,以获得高温
组织。 保温:使内外温度一致,保证显微组织转变完全。 冷却:随炉冷、空冷、水冷。
温度(℃)
α L+α
铝合金的热处理
罗伯占 2011年8月12日
何谓热处理?
2011-11-4
图1:热处理曲线示意图
热处理的作用
2011-11-4
去除铸件的内应力 稳定尺寸 改善机械性能
2011-11-4
图2:二元合金相图
2011-11-4
2011-11-4
固溶体示意图
铝合金的一般相图
2011-11-4
660
10 0.5 3
2011-11-4
2011-11-4
Al-Cu二元合金相图
铸造铝合金
铸 造 铝合金
2011-11-4
铝硅系 合 金
铝铜系 合 金
铝镁系 合 金
铝锌系 合 金
铸造、 铸造、机械 性能良好
强度、 强度、塑性高 耐腐蚀, ,耐腐蚀,铸 造时易氧化 高温强度高( 高温强度高(耐 ),易腐蚀 热),易腐蚀 强度高,易 强度高, 腐蚀, 腐蚀,价格 低
L
Al 水冷
α+β
时间(t) 空冷 随炉冷
铝合金的主要热处理形式
2011-11-4
铝合金的主要热处理形式是退火与淬火时效。 前者是一种软化处理,消除材料中的内应力
及加工硬化,使组织趋于平衡。 后者属于强化热处理,目的是提高合金的机 械强度。
淬火(固溶处理)
2011-11-4
将铝合金加热到固溶线以上保温一 段时间,使铝合金中的强化相溶入基体, 随后快冷,以抑制强化相在冷却过程中 重新析出,从而获得一种过饱和的以铝 为基的固溶体。淬火后铝合金的强度和 硬度不高,具有很好的塑性。
常见的热处理缺陷
2011-11-4
过烧 淬火变形与开裂 机械性能不合格 腐蚀氧化
常见的热处理缺陷——过烧
2011-11-4
正常淬火组织×400
严重过烧组织×400
避免过烧的措施
2011-11-4
1.掌握不同合金的实际过烧温度 2.严格执行淬火加热工艺规程和准确控制炉温 3.定期检查实际炉温的均匀性和控温仪表的 可靠性
常见的热处理缺陷——淬火开裂
2011-11-4
水温过低
铸件开裂
水温过高
强度不够
常见的热处理缺陷——机械性能不合格
2011-11-4
退 火 产 品
退火温度偏低
塑性不够 保温时间不足
冷却速度过快
常见的热处理缺陷——机械性能不合格
2011-11-4
淬 火 产 品
淬火温度偏低 硬度不够 保温时间不足
转移和冷却过慢
常见的热处理缺陷——腐蚀氧化
2011-11-4
在空气炉内进行高温加热,如炉膛内湿度
较大或含有其他有害物质,如硫化物,将 加剧铝制品的高温氧化。 特征:在金属表面形成气泡或在金属内形 成空洞。
2011-11-4
谢谢!
3 10 20 30 40 60
533 525 517 460 427 404
503 485 461 385 354 316
11.2 10.7 10.3 12.0 11.6 11.0
淬火
2011-11-4
铸铝的淬火冷却介质一般选用热变形和裂纹的铸件,以及 要求尺寸稳定性好的铸件,应当在沸水中或热油中 淬火。 铸件形状比较复杂、壁厚相差较大,加热及冷却时 容易发生变形且较难校正,因此加热和淬火速度需 适当减缓。
时效 将淬火后的铝合金,在室温
2011-11-4
或低温加热下保温一段时间, 随时间延长其强度、硬度显著 升高而塑性降低的现象,称为 时效。室温下进行的时效称为 自然时效;低温加热下进行的 时效称为人工时效。
3、影响时效强化的主要因素
2011-11-4
规律:淬火 越高 淬火冷却V越快 转移t越 越高, 越快, 规律:淬火T越高,淬火冷却 越快,转移 越 过饱和程度越高, 短,过饱和程度越高,时效强化效果也越大
淬火工艺参数
加热温度:在避免发生过烧的情况下,尽可能提高
2011-11-4
加热温度,促使更多的强化相溶入基体。 保温时间:对于含铜及含镁量高的合金,以及砂型 铸造的厚大铸件,应选取较长的淬火加热保温时间。 转移时间:越短越好。
淬火转移时间/s 淬火转移时间/s 抗拉强度σh/MPa 屈服强度σ0.2/MPa 伸长率δ/% 伸长率δ/%
固溶 处理
要点:在不过热过烧条件下, 淬高些 淬高些, 要点:在不过热过烧条件下,T淬高些,保温t 长些。淬火冷却要保证不析出第二相。 长些。淬火冷却要保证不析出第二相。为了防止 淬火变形开裂,一般采用20~ ℃ 淬火变形开裂,一般采用 ~80℃水冷却
时效 工艺
温度:对一定合金,有最佳时效温度 温度:对一定合金,有最佳时效温度. 时间:在一定时效温度下,有最佳时效时间。 时间:在一定时效温度下,有最佳时效时间。 方式:单级和多级时效。 方式:单级和多级时效。高强合金常用分级时效