巴尔查斯 金刚石涂层炉BAI730D-0 说明书
HAKO产品说明书

PRODUCTION VISESVisesIntroduction to Design ...........................................66–67VMC/HMC Solutions ............................................68–69Ball Lock® Mounting System ...............................70–71Production Vises4" (100 mm) Production Vises ................................72–736" (150 mm) Production Vises .................................74–75Self Centering Vises .................................................764" (100 mm) ................................................................76–776" (150 mm) ................................................................78–79Accessories ......................................................................79Production Vise Columns 4" (100 mm) Production Vise4 Sided ...........................................................................803 Sided ...........................................................................816" (150 mm) Production Vise4 Sided ...........................................................................823 Sided ...........................................................................8312 Station Hex .................................................................8412 & 16 Station Multi Quads ..................................85–86Hydraulic Production Vises .....................................874" (100 mm) ...............................................................88–896" (150 mm) ...............................................................89–90Hydraulic Vise Columns ...........................................914" (100 mm) 4 sided ........................................................924" (100 mm) 3 sided ........................................................936" (150 mm) 4 sided ........................................................946" (150 mm) 3 sided ........................................................95Column Subplates ..........................................................96Hydraulic Vise Accessories......................................97–98Vise Accessories ...............................................99–104Jaw Selections ..................................................99–101Ball Lock® Shanks/Plates .....................................102–103Sine Fixture Keys/T-Slot Nuts .....................................104Cast Iron Shop Vises ......................................105–106Bock Quick Change FixturingIntroduction ..................................................................107System Overview .................................................108–109Twin Vises ........................................................................110Jaw System .....................................................................111 Twin Vise Data ................................................................112Locator Plates .................................................................113DexLoc™ Locator Pins ...................................................113 Mono-Quad System (114)5-Axis Production VisesIntroduction ...................................................................115Self Centering .................................................................116Jaws /Accessories ................................................117–118Fixed .................................................................................119Jaws/Accessories .......................................................120Quick Clamping Block .................................................121Super Compact Clamp .................................................122Jaws/Accessories ...............................................123–124Vise with Reversible and Interchangeable Inserts ...125Jaws/Accessories .......................................................125Pallet Clamps .. (126)P R O D U C T I O N V I S E SWORKHOLDING SOLUTIONS GROUPPRODUCTION VISESJergens Production Vise SystemFastest Quick Change Jaw SystemMaximum Holding Power• Jaws machined to the contour of your workpiece maximizing holding force.6" (150mm) MonoQuad4" (100mm) MonoQuad• Quick change reverseable soft jaws • Single station adapter plate included• Multiple base designs to meet any requirementDual Station VisesSelf-Centering VisesWORKHOLDING SOLUTIONS GROUPPRODUCTION VISESJergens Production VisesMachine “Pockets” into the vise jaws, in the shape of your workpiece.Benefit: Reduce set-up times and parts change overMultiple mounting base configurations Fully sealed lead screw assemblyBenefit: Lower maintenance Rigid construction with hardened and ground stainless steel railsBenefit: High accuracy and repeatabilityChip and fluid flow through baseBenefit: Easier to keep clean, no more cloggingWORKHOLDING SOLUTIONS GROUPPRODUCTION VISESVertical Machine SolutionsHydraulic Vise Pages 88–90Innovative compact design. Reduced set-up time.Internal Slide Assembly with Hydraulic Clamping Cylinder.Universal Base Production Vises Pages 73 & 75The mounting flange has slotted holes to allow Ball Lock ® Base Production Vises Pages 72 & 74The mounting flange is cut into a jigsaw pattern to allowvises to nest closely together. Designed for use with Jergens Ball Lock ®Mounting System.5-Axis production vises and accessories rigidly clamp parts without obstructing access to multiple part faces.Self Centering Vises (3 Base Styles)Pages 76–79Self-Centering vises provide quick, simple fixturing for concentric machining of different sized workpieces.Narrow Base Production Vises Pages 73 & 75The small footprint allows maximum density of vises on your Bock Brand Quick Change System Pages 107–114Bock Brand vises combine with alpha-numeric locator plates Indexer Systems Page 81Indexer solutions can be customized to yourrequirements. Choose either three or four sided columns.WORKHOLDING SOLUTIONS GROUPPRODUCTION VISES Horizontal Machine Solutions6-Sided Production Vise ColumnsPage 84Increase the number of parts per load, while maintaining a small footprint. Available with bases to fit directly onto 4-Sided Production Vise Multi-Columns Pages 85 & 86Multiple columns mounted on a single base provide 12 or 163-Sided Production Vise ColumnsPages 81 & 83For machining 3 faces of production parts on HMC's. Largespindle noses can access the workpiece.240° workpiece accessibility.Multi-Vise FixturesPages 73, 75, 77, 79 & 89T o maximize productivity, mount multiple narrow body visesonto a single fixture plate. Mount the fixture plate onto thetombstones with the Jergens Ball LockWORKHOLDING SOLUTIONS GROUP PRODUCTION VISESSystem accurately positionsThe Ball Lock System securely holds fixtureplates to subplates with up to 20,000 lbs (88kN)of hold-down force per shank.Ball Lock® Fixture Mounting System forThe Ball Lock® Mounting System provides a method of quickly and accurately locating fixtures onto machine tables. The Ball Lock Commonly Asked QuestionsQ. What is the Ball Lock®Mounting System?It is a means of locating and lockingtwo flat surfaces together, normally afixture plate to a sub-plate.Q. How does it lock?A. Inside the shank are three balls thatexpand into a tapered groove in thereceiver bushing. This action drawsthe plates together. The locking ballsare activated by turning a setscrew inthe head of the shank, which pushesWORKHOLDING SOLUTIONS GROUPPRODUCTION VISESUnmatched Setup Speedand Workholding FlexibilityQ. Is there a preferable location for System repeatability is improvedif the liners are located at opposite corners of a rectangular fixture plate. For consistency, we recommend locating the liner bushings at top left Q. What are the advantages of using with ¾" (18mm) of thread engagementrequires 10 turns to lock. On CNCmachines, the repeatability of fixturelocations makes indicating of thefixture unnecessary.Q. How do I recess the fixtureplatefor a clear surface ?A. Counterbore the fixture plate to adiameter large enough to allow easyQ. What if my plate is thinner thanthe recommended thickness?A. By adjusting the depth of thecounterbore for the receiver bushingin the subplate, you can still use theBall Lockquestions on this type of application,please call 1-877-426-2504.Q. Can I use the shanks in a heated0.38[10]0.96[24]3.438[87.5]1.683.00[73]1.22[30][190]7.50WORKHOLDING SOLUTIONS GROUPPRODUCTION VISESProduction Vises – 4" (100mm)Ball Lock ShankShankPart No.Wt.Part No.SizeMetric17/32" (4) Plcs [13.5]Slotted Mounting Holes:3.13[80]2.50[63.5]6.00[150]Mounting Holes (2) Plcs:17/32"[13.5]WORKHOLDING SOLUTIONS GROUPPRODUCTION VISESProduction Vises – 4" (100mm)traditional strap clamps. The narrow base has 2 locating holes for 12mm -slots shown on page 104. Recessed machine tables, tombstones, or columns. Maximize flexibility by utilizing0.50[12]4.50[114]4.00[100]10.00[248] 1.45[38]0.96[24]WORKHOLDING SOLUTIONS GROUPPRODUCTION VISESProduction Vises – 6" (150mm)MetricBall Lock ShankShank Part No.Wt.Part No.Size1.125[28]2.952[75]4.921[125]7.874[200]6.000[150]Mounting Holes:M10 x 1.5 T ap (6) Plcs2.50[63.5]3.875[100]7.874[200]Locating Holes:.6255 (4) PlcsFor Sine Fixture KeysWORKHOLDING SOLUTIONS GROUPProduction Vises – 6" (150mm)is easily mounted directly to machine tool tables. Slotted mounting holes will match almost any table slot pattern. can be mounted as a stand-alone vise or mounted to a fixture plate. The slim design allows a high density of vises on machine tables, tombstones, or columns. Maximize flexibility by utilizing the Jergens1.22"(31.0)ED MTG. HOLES3.370"(85.60)±0.001"(0.03)WORKHOLDING SOLUTIONS GROUPSelf-Centering Precision Production Vises• Shown in Universal Base, also available in Narrow Bases and Ball Lock Part Number Wt. (lbs)49471SC38WORKHOLDING SOLUTIONS GROUPSelf-Centering Vises – 4" (100mm)12"6"WORKHOLDING SOLUTIONS GROUP Self-Centering Vises – 6" (150mm)12"6"50m m 12" (300mm )WORKHOLDING SOLUTIONS GROUPSelf-Centering Vises – 6" (150mm)Part No.49442SC*Jergens Standard Jaws fully compatible, see complete selection on page o order Jergens Production Vise Jaws with Adjustable Gib Screw, use standard jaw part no. followed by "SC".WORKHOLDING SOLUTIONS GROUP Production Vise Columns – 4" (100mm)QWORKHOLDING SOLUTIONS GROUPcan be mounted onto most any indexer. Columns can be attached directly to an indexer or become Jergens Technical Service for help designing Production Vise Columns – 4" (100mm)Mounting Wt. Ball Lock Shank Pattern 2* (lbs) Part No. Sizen/a 125 49602 20mm x 1"100mm 115 — —Mounting Wt. Ball Lock Shank Tri-column design allows upWORKHOLDING SOLUTIONS GROUP Production Vise Columns – 6" (150mm)QWORKHOLDING SOLUTIONS GROUPProduction Vise Columns – 6" (150mm)Mounting Wt. Ball Lock Shank Pattern 2* (lbs) Part No. Size252 49602 20mm x 1"266 49612 25mm x 1"100mm 240——Tri-column design allows upJBall Lock Mtg. PatternBall Lock Mtg. PatternWORKHOLDING SOLUTIONS GROUPProduction Vise ColumnsQK Ball Lock Mtg. PatternQKBall Lock Mtg. PatternWORKHOLDING SOLUTIONS GROUPPRODUCTION VISESProduction Vise ColumnsMtg. PatternK QQKBall Lock Mtg. PatternWORKHOLDING SOLUTIONS GROUPPRODUCTION VISESProduction Vise ColumnsWORKHOLDING SOLUTIONS GROUPPRODUCTION VISESHydraulic Production Vises• Innovative compact design • Internal hydraulics• 4,700 lbs (2,100 Kg) clamping force • Operates on lower input pressure • Fully machinable jaws• Fastest quick-change jaw system • Hardened stainless steel wear rails •Easy-Flow ™base designJergens hydraulic vises are available in 3 different base configurations. They offer the same unique features as Jergens manual vises.Technical Specifications:Hydraulic Clamping Stroke: 1/4" (6.3mm)Operating Volume: 0.4 Cu In (6.7 cm 3)Maximum Input Pressure: 4000 P .S.I. (275 bar)Minimum Input Pressure: 500 P .S.I. (35 bar)Input Port: #4 SAE (7/16-20 UNF-2B)Clamping Force (lbs) = Input Pressure x 1.19Clamping Force (Kg) = Input Pressure Bars x 7.67Operation:Using the Jergens Hydraulic Vise handle part number 49445, tighten vise jaws so the workpieces touch the fixed jaw. Next, turn the handle back 1/2 turn and activate the hydraulic cylinder. Hydraulic Power Sources AvailableClamping ForceInput PressureClamping ForcePSIBarslbskgf500 35 595 268 1,000 70 1,190 5376.0012.002.50[63.5]3.125[80] 6.00[150]17/32" (4) Plcs [13.5]Slotted Mounting Holes:Mounting Holes :17/32" (2) Plcs [13.5]WORKHOLDING SOLUTIONS GROUPPRODUCTION VISESHydraulic Production Vises – 4" (100mm)Mounting Holes:ap (6) PlcsMOUNTING HOLES (6) Plcs:3.938[100]LOCATING HOLES:.6255 (6) PlcsWORKHOLDING SOLUTIONS GROUPPRODUCTION VISESHydraulic Production Vises – 4" (100mm)Part Wt. N umber lbs/Kg49487 30/14Part Wt. N umber lbs/KgPart Wt.PRODUCTION VISESWORKHOLDING SOLUTIONS GROUP Hydraulic Production Vises – 6" (150mm)12.006.00PRODUCTION VISES WORKHOLDING SOLUTIONS GROUPHydraulic Vise Column(150mm) sizes,Fully Machinable and ReversibleMore workholding flexibility per jaw set.Hydraulic Vise Column Kits Include:Shown with base forSee page 98 for Air PoweredHydraulic PumpPRODUCTION VISESWORKHOLDING SOLUTIONS GROUP Hydraulic Vise Tooling Columns – 4" (100mm)PRODUCTION VISES WORKHOLDING SOLUTIONS GROUPHydraulic Vise Tooling ColumnsPRODUCTION VISESWORKHOLDING SOLUTIONS GROUP Hydraulic Vise Tooling Columns – 6" (150mm)Hydraulic Vise Tooling ColumnsHydraulic Vise Tooling Columns Standard Subplates35°TANK PRESSURE PORT1/4 NPT PORTS3.411.0260.091.0662.750.650.9380.375 AREA FOR TANK LINE LOCATION0.60 AREA FOR PRESSURE LINE LOCATION2.752 3/8"M5 X 0.8 TAP THRU (4) PLACES7/32 DRILL THRU (4) PLACESPTPORTPatent No. 3839866Hydraulic Production Vise AccessoriesPart Number61725HandlePart Number49445Handle for Hydraulic Vises, 4" Rotary Hydraulic UnionDual Passage, Ports 1/4 NPTPressure (psi) Bars Torque (in. lbs) Part Number61755 Performance Curve*(0.655)1000 2000 3000 4000 5000 (69) (138) (207) (276) (345)OUTPUT PRESSURE, PSI (BAR)Part Number61759Hydraulic Production Vise AccessoriesKit Includes61755 36:1 Pump61643 Remote four-way zero-leakageLow Pressure Air HoseHose I.D.1/4" 3/8" 1/2"HosePart Number 61106 61108 61110FittingPart Number 61107 61109 61111Hydraulic HoseHigh pressure hose is supplied assembled and to lengths indicated. Lengths are measured from end of coupling to end of coupling. Hose is 3/8" ID and available in 4000 psi or 7000 psi rating. 3/8" female tubing fittings on each end.N ipple1/8 NPT Male 619501/4 NPT Male 61905 619511/4 NPT Female61954 Air couplers have checks on sleeves only.Adapter for BSP1/4 Male NPT 1/4 NPT x 1/4 T 1/4 Female BSP 60221Adapters & ElbowsJergens Production Vise SystemThe clamping system Completely sealed lead screw Hard coated base made of high-strength, light-weight, aluminum extrusion. Guideway Rails made of hardened stainless steel.Aluminum jaws can be completely milled, therefore Aluminum or steel jaws suitable for milling:Extra Wide Jaws Full Face Vise PlateDual Station with Hard JawSingle Workpiece with Hard JawsProduction Vise JawsQuick Change Fixture PlateProduction Vise Accessoriesinclude two moveable jaws and one fixed jaw.Vise Conversion PlatesVise HandlesHard Jaw Carriers With Steel Inserts*Part No.Vise Size49442 4"/100mm Machinable Soft Jaws(Standard Sets included with Vises)Vise Work StopClearance holes for holddown (2) PlcsClearance holefor holddownStandard ShankJigsaw Fixture PlateMultiple Vise Fixture PlateProduction Vise Ball Lock ®Accessories – InchShank49601 49601-S 49602 49602-S 49611 49611-S49612 49612-SProduction Vise Ball Lock® Accessories – MetricJigsaw Fixture PlateClearance holefor holddownStandardShank Multiple Vise Fixture PlateClearance holes forholddown (2) PlcsProduction Vise Accessories Locate subplates or fixture plates to Tmachine tables. Available in inch sizes for 1/2"to 7/8" slots, and in metric sizes for 12mm to22mm slots.T-Slot NutsWORKHOLDING SOLUTIONS GROUPCast Iron Shop VisesCharacteristicsMade of close grained high tensile cast iron. Jaws ground and Hardened 55±3 HRC. Swivel base provided with positive locking and adjustable through 360°. Adjusts work piece to its center. Opposite threads for quick and accurate centering.CharacteristicsMade of close grained hightensile cast iron. Jaws ground and Hardened 55±3 HRC. Adjusts workpiece to its center. Opposite threads for quick and accurate centering. This is a low profile vise.T echnical DataPart Jaw Width Jaw Opening N umber Inch mm Inch mm Inch mm Inch mm Inch mm Inch mm 110080 2 50 2 50 110081 4 100 4 100 T echnical DataPartJaw Width Jaw OpeningNumber Inch mm Inch mm Inch mm Inch mm Inch mm Inch mm 110085 3 75 5 127 110086 4 100 4 100WORKHOLDING SOLUTIONS GROUPCharacteristicsManufactured from close grained high tensile cast iron. Swivel is full 360°. This is very useful for heavy duty milling jobs. Vise is low height for maximum clearances. Jaws are fully ground and precision with parallelism of 0.0012 (30 microns) the hardness of jaws is 55±33 HRC.T echnical DataPart Jaw Width Jaw Opening Jaw Depth N umber Inch mm Inch mm Inch mm Inch mm Inch mm Inch mm T echnical DataPartJaw Width Jaw Opening Jaw DepthNumber Inch mm Inch mm Inch mm Inch mm Inch mm Inch mm 110250 6 150 7 1/2 188 1 1/2 CharacteristicsManufactured from graded cast iron and precisionground. These vises have a needle bearing thrust collar. Vise jaws are in pairs and replaceable.Cast Iron Shop VisesMilling Machine Vises with Swivel Base (Heavy Duty)Machine VisesWORKHOLDING SOLUTIONS GROUP JERGENS-BOCK QUICK CHANGE S YS TEMFASTPRODUCTIVE by reducing spindle down-time to aminimum. The combination of short setup times, theability to move setups away from the machine andfast loading keeps your spindle cutting, not waiting.WORKHOLDING SOLUTIONS GROUPJERGENS -BOCK QUICK CHANGE S YS TEMwin Vise is the key component of the complete BockWorkholding system. A variety of body styles made from high-strength aluminum, ground steel guides, snap-on quick-change machinable aluminum jaws and a solid clamping screw and third hand mechanism System OverviewBock Locator Plate SystemBock Locator Plates are a great platform to quickly and accurately mount your T win Vises in a number of different positions. Locator/mounting holes with alpha-numeric identifiers and Bock’s DexLoc™ double-expanding locators give you +/- .0005" repeatability.DexLoc ™Locator PinsPatented DexLoc™ double-expanding locator pins allow for fast and accurate location of twin vises on locator plates.WORKHOLDING SOLUTIONS GROUP JERGENS-BOCK QUICK CHANGE S YS TEMHard-coated high-strength aluminum base for lighter WORKHOLDING SOLUTIONS GROUPJERGENS-BOCK QUICK CHANGE S YS TEMStraight basefor use on Bock Locator Plates or with toe clamps Slim-LineStandard interlockingGenerous cut-outs to prevent chip and coolant accumulationBock Twin Vise SystemThree different basestyles for your specificmounting needsWORKHOLDING SOLUTIONS GROUP JERGENS-BOCK QUICK CHANGE S YS TEM Bock Jaw SystemBock Machinable Jaws are made from high-strength aircraft grade anodized aluminum.Once machined to hold a specific part they become quick-change dedicated fixtures ideal for holding even complex shapes.STANDARD JAWS snap on and off in QUICK CHANGEFACE PLATEScan be convertedTALL JAWSto hold larger parts.123WORKHOLDING SOLUTIONS GROUP JERGENS-BOCK QUICK CHANGE S YS TEMBock Twin VisesScrew-on guideways made from hardened steelThird-hand function for fast sequential loading of partsExact positioning of center jaw using locator pins; removing center jaws allows the holding of one single large partAluminum jaws can be milled out to meet each part’s holding and locating requirements.Generous cut-outs to prevent chip and coolant accumulationStandard InterlockingStraight BaseSlim-LineWORKHOLDING SOLUTIONS GROUP JERGENS-BOCK QUICK CHANGE S YS TEM Bock Brand Locator Plate SystemBock Brand Locator PlatesDexLoc™ Locator PinsTo order DexLocWORKHOLDING SOLUTIONS GROUP JERGENS-BOCK QUICK CHANGE S YS TEMBock Mono-Quad System。
重量级铸铁双燃烧炉说明书

2016 06SBCISHDHEAVY DUTY CAST IRON DOUBLE BURNER STOVEINSTRUCTION MANUALREAD ALL INSTRUCTIONS AND WARNINGS BEFORE USING THIS PRODUCT. Every effort has been made to ensure the accuracy of this manual. These instructions are not meant to cover every possible condition and situation that may occur. We reserve the right to change this product at any time without prior notice.IF THERE IS ANY QUESTION ABOUT A CONDITION BEING SAFE OR UNSAFE,DO NOT OPERATE THIS PRODUCT!DO NOT RETURN THIS PRODUCT TO THE RETAILER - CONTACT CUSTOMER SERVICE.If you experience a problem, have questions or need parts for this product, visit our website at or call Customer Service at 1-888-287-6981, Monday-Friday,8 AM - 4 PM Central Time. A copy of the sales receipt is required.FOR CONSUMER USE ONLY – NOT FOR PROFESSIONAL USE.KEEP THIS MANUAL, SALES RECEIPT & APPLICABLE WARRANTY FOR FUTURE REFERENCE.FOR OUTDOOR USE ONLY. USE ONLY IN A WELL-VENTILATED AREA. DO NOT USE INDOORS.LPHK Regulator Hose Kit (Sold Separately) Required To Use Stove Short Gas Valve1) To Connect The Regulator Hose To The Stove …Specifications:Size: 9.2" x 9.2" x 4" Valve: Zinc Low Pressure Burner Output: 8530 BTU/hr BTU's: 2.5 kw/hrAttach the gas valve using the supplied screws.Use Long Screw Double Nut1 Long ScrewWARNINGThis stove is designed to be used and operated on LPLiquid Propane Gas (usually found in a gas tanks likethe type used on gas barbecues. Not for use with 16 or 14 oz canisters.)You must use an LPHK Regulator (sold separately) to properly operate the stove, since the stove will not operate at the gas pressure coming directly from an LP Liquid Propane Gas cylinder.Before each use, always check all gas connections and joints to make sure no leaks are present. Check hoses for cracks and wear, and replace damaged hoses.When the unit is fully assembled, attach the regulator hose to the propane tank. The lit burner should operate with a blue flame, with a small yellow tip. Adjust the air screw if the flame is sputtering or popping. If the flame is not operating normally, check to see if anything is obstructing the gas flow. DO NOT OPERATE the propane stove if you feel that it is not operating normally. WARNINGFOR OUTDOOR USE ONLY. USE ONLY IN A WELL-VENTILATED AREA. DO NOT USE INDOORS.ASSEMBLYTurn the burner upside down. Use caution as the Cast Iron construction does not scratch the surface. Attach the two burners using the supplied screws. 2) Use A Wrench To Tighten This End To Valve.3) Follow The Manufacturers Directions to Hand-Tighten To Propane Tank2 Medium Screws2 Short Screws2 Nuts。
simalube 自动单点液体涂层设备说明书

simalube reduces maintenance costs and downtimes The application of simalube lubricators greatly extends the service life of components such as bearings, chains, gearwheels, conveyors and other mechanical pieces. The reduction of mainte-nance needs and downtimes also leads to a reduction of overall costs.In recycling factories where lots of dust and dirt is present, regular lubrication is important. Badly lubricated components can be quickly damaged and must then be replaced. This leads to interruptions in production and higher costs.Minimize dangers and prevent accidents The simalube lubricator is ideal for use with hard to reach lubrication points. The lubricator also automatically and reliably lubricates exposed lubrication points. Periodic manual lubrication of machines with a grease gun is no longer necessary. When simalube lubricators are installed, workers spend much less time in danger zones. The maintenance personnel have less exposure to noise, dust and the danger of rotating machine parts, which increases workplace safety. The lubrication expert«simalube lubricates continuously, extends the service life of production machines and reduces maintenance costs »«simalube increases employee safety in factories»The externally installed simalube prevents dirt from entering the lubrication point.The FGR ventilator is lubricated by simalube 60ml.A combustion fan lubricated with two 60ml and two 125ml simalube lubricators.Dozens of 30ml simalube lubricators provide the bearings of a conveyor belt with the necessary lubricant.simalube lubricates bearings on a conveyor belt. A vibrating conveyor lubricated by several 125ml simalube lubricators.Applications and advantagessimalube applications in recycling plants:Conveyor belts PressesS orters W ashing machinesC rushers M illsV entilation fans Winnowing machinesShredders Combustion fanSorting machinesAdvantages of the simalube lubrication system:Reliable lubrication system in the recycling industryR eduction of service requirements and maintenance costs: because manual lubrication is no longer necessary, less labour is required and time savings are greatShutting down the machines for maintenance is no longer necessaryLonger service life of machines thanks to continuous and precise lubricationFlexibility: The running time is adjustable from 1–12 monthsO nly one type of lubricator is needed per application. This reduces storage costsO nce the simalube is installed, the lubrication point is reliably lubricated and never forgottenT hanks to the transparent housing, the progress of the lubrication process canbe monitored at all times ( ll level control)Available in 5 sizes: 15, 30, 60, 125, and 250 ml, plus multipointSimple, environmentally-friendly disposal (100% recyclable)The hermetically sealed system prevents contamination by dust and debris (IP68)We will gladly inform you about theapplication of simalube products in therecycling industry.O ur highly-quali ed specialists have anin-depth technical knowledge and willshow you how automatic lubrication canreduce costs and extend the service life ofyour machines.1742/61.9252simatec agStadthof 2CH-3380 Wangen a. AareTel.: +41 (0)32 636 50 00Fax: +41 (0)32 636 50 19*******************。
Fagor Industrial Simba Mini电锅用户和维护手册说明书
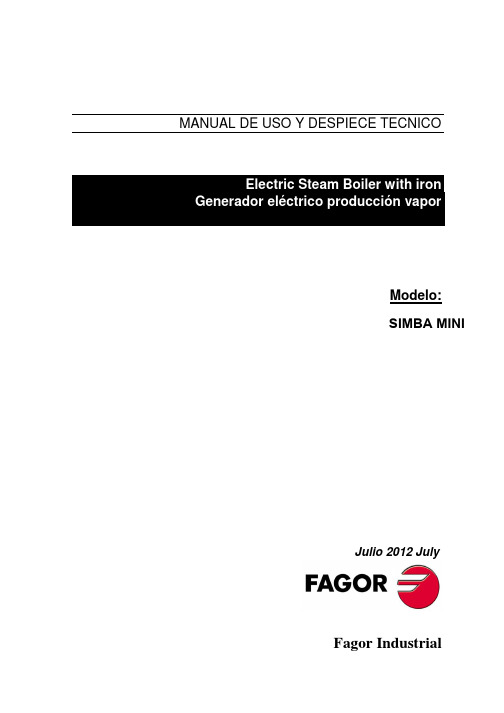
MANUAL DE USO Y DESPIECE TECNICOModelo:SIMBA MINIJulio 2012 JulyFagor IndustrialCONTENTS1 INTRODUCTION2 GENERAL DESCRIPTION3 MACHINEIDENTIFICATION4 TECHNICALFEATURES5 MACHINECOMPONENTS6 MACHINE UNPACKING AND INSTALLATION7 INSTRUCTIONSFORUSE8 TROUBLESHOOTING AND SOLVING9 PRECAUTIONS 10 HAZARDOUS USE11 DIMENSIONS AND TECHNICAL DRAWINGS12 MAINTENANCE PROCEDURES13 DISPOSAL14 HOW TO ORDER SPARE PARTS15 HANDLING AND TRANSPORT16 WARRANTY17 CONFORMITY DECLARATION1 INTRODUCTIONThe present user’s and maintenance manual refers to the electric steam generator “SIMBA mini”.The present user’s and maintenance manual contains important information for the operator’s healthsafeguard and safety.This manual has to be read and kept in a safe place, in order to be always at the operator’s disposal in case of need.FAGOR INDUSTRIAL S.COOP cannot be held liable for any damage to things or injury to persons caused by improperuse of the machine in c ontrast with these instructions.Any possible modifications effected on the components of the machine or its different use without prior written authorization by FAGOR INDUSTRIAL S.COOP relieve the latter of injury to persons and / or damages to things,warranty voiding any b indings, as well.2 GENERAL DESCRIPTIONThe SIMBA MINI boiler produces steam, and must be connected to external electric and water supplies to operate.Its use is simple and efficient thanks to its front control panel.3 MACHINE IDENTIFICATIONOn the left side of the boiler, a metal rating plate quotes the model, serial number, the year of construction and electrical and pressure supply.4 TECHNICAL FEATURESTECHNICAL FEATURESElectrical power supply 230V – 1Ph – 50/60 HzBoiler capacity 5 LMaximum steam pressure 2,8 barBoiler power supply 1450 WIron power supply 800 WSound pressure level < 70 dB(A)Operating temperature + 5 ÷ + 80 COperating humidity 90 % max.Storing temperature -20 ÷ +50 °CNet dimensions 270 x 380 x 110 mm.Net weight 11 KgGross dimensions (with packing) 400 x 300 x 400 mm.Gross weight (with packing) 12 KgNet weight with trolley 18 KgOverall dimensions with trolley (with packing) 460 x 310 x 930 mm.Gross weight with trolley (with packing) 20 KgWARNING: Check that the supplied voltage and pressure correspond to that indicated in the table above.5 MACHINE COMPONENTSThe main parts of the machine are as follows:Pos. CODE DESCRIPTIONPos.CODE DESCRIPTION 1 364253 Iron hose support (antenna) 9 523260 Handle2 39B045 Steam valve 230V 50Hz 10 Z27A07 Complete trolley (optional)3 22K050 Refill and safety cap 11 45G012 Pressure switch4 Z18D00 Iron model K 12 162126 Iron rest tray5 56B010 Swivelling wheels 13 46M028 Boiler casing6 25A001 Silicone iron rest14 201007 Boiler7 43A014 Boiler and iron switch 15 43A061 Boiler thermostat 8 43A016 Double Indicator1643B018Safety thermostat67 18 2 9 10435Iron model K cod. Z18D00COD. DESCRIPTION COD. DESCRIPTION COD. DESCRIPTION 364273 Cable lead for board heater 364278 Screw for back cover 364287 Front handle holder for iron 364256 Electrical cable for iron 364279 Screw for iron microswitch cover 364288 Rear handle holder for iron 364274 Screw for thermostat 364280 Screw for microswitch holder 3.5 x 19 AU 364289 Screw covers for iron 364257 Nickel-plated brass hose holder 364281 Screw for handle fixing M5 x 10 ZNB 364290 Brass washer364258 Complete iron plate 364282 Screw for terminal board fixing 364291 Brass spacers364259 Adjustable thermostat 364283 Handle cover for iron 364267 Complete microswitch for iron 364260 Thermostat with manual reset 364284 Rear cover for iron 364292 Screw for iron handle 364261 Cork grip 364285 Button holder for iron 45H006 Knob made of black bakelite 364275 Handle support for iron 364286 Button holder cover for iron 364293 Washer for screw364270 Casing for iron 364263 Upper button for iron 364294 Washer for knob364262 Cables for iron 364264 Lower button for iron 364268 Cable lead for electrical cable 364276 Insert for iron handle 364265 Plate for handle support 364269 Terminal board with 4 poles 364277 Screw M4 x 22 for thermostat fixing 364266 Cable holder for iron6 MACHINE UNPACKING AND INSTALLATIONWARNING:The unit must be installed, opened and repaired by fully qualified technicians only.6.1 UNPACKINGFind the most suitable place where to put the machine, then remove it from the packaging and check that it is intact. The packing materials do not require special disposal as they are not dangerous or polluting. Refer to the local rules in forceto discard them.6.2 INSTALLATIONThe machine does not need to be anchored to the floor, except for installation on self-moving vehicles, where it is necessary to use the holes on the base for the right attachment.For correct use and operation, as well as for easy maintenance, leave a free space around the machine.Do not put the machine in dangerous or flammable places.6.3 ELECTRICALCONNECTIONConnect the machine to the power line as shown in the diagram, ensuring that the power supply voltage corresponds tothat indicated on the rating plate. To ensure safe connection to the main supply, use a magnetothermal switch or otherwise a switch with fuses.WARNING: At the end of the electrical connection, check that the cables are well fixed, isolated and protected from bumps.7 INSTRUCTIONS FOR USE7.1 OPERATION∙Installation and maintenance must be carried out by qualified technicians only.∙Do not use the machine plunged in fluids, or in dangerous or flammable places.∙Do not ignore the dangers to the operator’s health and follow the hygienic and safety prescriptions.∙Always use piping suitable for operating pressures.∙Make sure that the electrical wiring is carried out correctly according to the current regulations, and that the fuse blocks are closed and complete of fuses.∙Check that the safety and control devices of the boiler (pressure gauge, pressure switch and safety valve) are intact.∙Check that the electrical wiring and the piping of the iron are intact and secure.7.2 USE∙Verify the water level in the tank and add more water if necessary.∙Turn on the boiler and the iron.∙The boiler power supply is fed automatically by turning on the indicator light.∙The boiler reaches the operating pressure of 2.8 bar after a few minutes and the related light turns on automatically.∙The boiler is ready to supply steam.∙Absence of water in the boiler is indicated by the switching off of the two lights (boiler power supply and steam pressure).∙To top up the water it’s necessary to wait 2 or 3 minutes after the lights turn off.∙It’s possible to iron without completely filling the water tank. Using 1 litre of water provides a range of ironing time of 1 to 2 hours. To verify the amount of water added, simply insert the dipstick level into the boiler and cover theupper hole with your finger as you extract it.8 TROUBLESHOOTING AND SOLVINGThe following table shows the main problems and the corresponding causes and solutions. In case of doubts or unresolved problems, do not look for the trouble by removing pieces of the machine, but rather contact the Technical Office or seller of Ghidini products.PROBLEMS AND SOLUTIONSTROUBLES POSSIBLECAUSESSOLUTIONSThe machine does not work. Main power failure Check that the supply terminals are live. Fuses are blown Check fuses.The boiler switch is on but the power supply and steam lamps are turned off. Absence of water in the boiler Refill water tank. Faulty safety thermostat. Replace thermostats.The boiler light and switch are on, but theboiler does not reach the requestedoperating pressure.Heaters are burnt out Check heaters.WARNING: If the safety valve is released, switch the boiler off immediately and contact a qualified technician. Do not block the exhaust and do not underestimate the severity of the problem, as there could be risk of explosion.9 PRECAUTIONSRead carefully the instructions and the risks related to the use of a steam boiler. Operators must know operating system and clearly understand its dangers through the manual.Main electrical supplyPrior to carrying out any inspection or work on the machine, disconnect it from the main electrical supply and make sure that nobody can connect it again during the technical operations. All the electrical or electronic machines or basic structures installed must be connected to the ground line. FlammabilityAdopt all the necessary precautions to avoid any direct contact with hot materials or flames. Put fire extinguishers near the machine for an immediate intervention in the event of fire. Pressure / SteamBefore each intervention switch off the boiler and check that residual pressures are not inside any branch of the hydraulic circuit. They could cause steam sprays in the case of disassembling of pipes or components.NoiseThe noise emission is not excessive, because it remains under 70dB(A).10 HAZARDOUS USEThe verification of conformity to the essential safety rules and to the dispositions enclosed in the machine directive is carried out by filling in the checking lists arranged in advance and included in the technical file. The checking lists are of two kinds:∙ List of dangers (extract from EN 1050 referring to EN 292.∙ Application of the essential safety characteristics (Dir. Machine – encl. 1, part 1)The dangers described in the following items have not been completely eliminated, but they have been considered acceptable:∙ During the maintenance operation there could be some sprays of steam, at low pressure, or of spotting product(maintenance operation must be carried out using suitable protection devices).∙ During use it is possible to accidentally come into contact with surfaces at a temperature of over 80°C. Becareful.∙ Protection against direct and indirect contacts must be adopted by the user.11 DIMENSIONS AND TECHNICAL DRAWINGS12 MAINTENANCE PROCEDURESIn case of troubles, contact the technician for the inspection and, if necessary, for unscheduled maintenance. Periodically it is necessary to carry out the following procedures:OPERATIONS HOURS OF WORK Empty the boiler 150This machine does not require special equipment for check and maintenance operations, but use suitable tools and personal protection in compliance with D.Lgs. 626/94 and in good condition (DPR. 547/55) in order to avoid harm to people and to parts of the machine.Prior to carrying out any inspection or work on the machine, make sure that it is disconnected from the main electrical supply.13 DISPOSALDuring the maintenance operations, or in case of demolition, do not litter the environment with polluting elements. Refer to the local laws in force for appropriate disposal. In case of demolition, it is necessary to destroy the identification rating plate and any other document.14 HOW TO ORDER SPARE PARTSFor the spare parts request it is necessary to quote the model of the machine, the serial number, the quantity of the spare parts requested and their code number. (This data is available on the rating plate, the technical data and on the operating instructions.)If the voltage and frequency of the electrical parts to replace are not V220-380/50Hz (check these particular characteristics on the rating plate of the part to replace), quote the right data.The technical data, the descriptions and pictures included in this manual are not binding. The manufacturer reserves the right to make any necessary modification without notice and without updating these operating instructions.15 HANDLING AND TRANSPORTBefore its transport the machine is carefully packed in a wooden cage. During the transport and the stocking operations, pay attention to warnings printed on the packaging. At the moment of the delivery, check that the packing is intact and put the machine in a dry place.16 WARRANTYAll Ghidini products are supplied with a guarantee for materials and manufacturing failures for a period of maximum 12 months from the date of the delivery.The guarantee is extended as follows:In case of malfunction of the machinery contact Ghidini and quote the trouble, the model, serial number and the operating conditions of the machine. Upon receipt of the machine and after an accurate analysis, Ghidinireserves the right to repair or to replace the product. If the machine is still under guarantee, Ghidini. will repair or replace it free of charge, but if the returned product is not defective, Ghidini reserves the right to charge the freight to the customer (transport, etc.).This warranty must be considered annulled in case of damages caused by incorrect use, negligence, wear and tear, chemical corrosion, or installation contrary to the operating instructions supplied by Ghidini. Any eventual modification or different use of the machine must be previously authorized by Ghidini through a written document, otherwise Ghidini may be considered free even from the guarantee bond.The parts of the machine which are subjected to wear and tear are not included in the guarantee as well as all the items not explicitly cited, or damages and expenses caused by the defects of the product itself. Implicitly the customer accepts the conditions of the present warranty upon purchasing the machine. Eventual modifications to the guarantee must be authorized by Ghidini through a written document.。
双层披萨炉(双门)产品说明书

(double door)WPO750Graphic By Sandra A. Montysko Revised July 21, 2016 Approved 7/21/16 Page 1 of 5Page 2 of 5 Revised July 21, 2016Revised July 21, 2016 Page 3 of 5Illustration #Part #Description1 033753 Temperature Gauge (2 required)2 028626 Temperature Knob with Screws (2 required)3 028626 Timer Knob with Set Screws (2 required)4 034946 Double Power/Light Switch (2 required)4a034947Double On-Off Switch (2 required)5 033755 Foot (4 required)6 029943 Screw (2 required for each timer)7 033764 Timer (2 required)8 029943 Screw (2 required for each thermostat) 9 034948 Thermostat (2 required)10 033766 Temperature Gauge Bracket (2 required)11 033767 Thumb Screw (2 required for each temperature gauge) 12 033768 Oven Light Lens (2 required) 13 035605 Bulb-Rated 230V/25W (2 required)14 034949 Lamp Holder (2 required) 15 034957 Cord (240 volt)16 033756 Thermal Cut-off (2 required) 17 013731 Wire Tie (17 required)18 034979 Thermostat Probe Bracket (2 required)19 034980 Temperature Gauge Probe Bracket (2 required for each oven)20 033760 Screw (4 required for each set of brackets)21 033761 Spring Washer (4 required for each set of brackets) 22 033762 Washer (4 required for each set of brackets) 23 034977 Component Right Side Panel 24 033771 Screw (4 required)25 034984Top Insulation Plate Assembly27 033776 Screw (3 required)27033785 Screw (3 required)WPO750Catalog/ModelPage 4 of 5 Revised July 21, 2016314 Ella T . Grasso Ave.Torrington, CT 06790Tele. 1-800-269-6640Fax 860-496-9017Illustration #Part #DescriptionWPO750Catalog/ModelRevised July 21, 2016 Page 5 of 528 033776 Screw (2 required)29034985 Bottom Inuslation Plate Assembly 30033785 Screw (3 required)31 034962 Angled End Element Bracket (6 required)32 034963 Element Support Bracket Assembly (3 required on each rack) 33 034961 Straight Support Bracket (2 required)34 034981 Element Assembly (4 required each quick-fix rack)35 034964 Top Element Rack Front Panel (2 required) 36 033779 Screw (5 required on each rack) 37 034965 Bottom Element Rack Front Panel (2 required) 38033779 Screw (5 required on each rack)39 033786 Ceramic Sleeve (6 required) 40 034978 Element Left Side Panel41 033771Screw (4 required)42 035346 Door Assembly (2 required)43 035349 Slotted Bolt (4 required one each side of each door assembly) 44 035351 Washer (4 required one each side of each door assembly) 45 035350 Allen Bolt (4 required one each side of each door assembly)314 Ella T . Grasso Ave.Torrington, CT 06790Tele. 1-800-269-6640Fax 860-496-9017。
TANA 648820 8kW 燃木炉说明书

référence 648820Poêle à boisTANARéférence 648820Notice particulière d’utilisation et d’installation Consulter attentivement ce complément notice particulière ainsi que la notice générale également livrée avec l’appareil Caractéristiques et performances en fonctionnement intermittent suivant EN 13240 : ArrayCaractéristiques de construction :INSTRUCTION POUR L’INSTALLATION DE L’APPAREIL.Pour limiter l’échauffement des parois voisines du poêle à 65K (K = degrés Celsius au dessus de la températ ure ambiante), il est nécessaire de respecter les distances minimales indiquées sur le schéma ci-dessous.Si les parois avoisinantes sont en matériaux incombustible et ne se dégradent pas sous l’action de la chaleur (la températur e du mur pouvant atteindre 200 °C), ces dimensions peuvent être réduites à 150 mm.mmTRES IMPORTANTEn complément de ce document, consulter attentivement la «NOTICE D’INSTALLATION ET D’UTILISATION POUR POÊLES A BOIS »fournie avec l’appareil.CONSEILS D’INSTALLATIONLa dépression dans le conduit de fumées doit être comprise entre 6 et 12 Pascals. Cette mesure est vérifiable en chauffe à l’aide d’un manomètre. Un modérateur de tirage est nécessaire dans presque tous les cas pour réguler le tirage aux valeurs préconisées.CONSEILS D’UTILISATIONUtiliser uniquement les combustibles recommandés: Bois sec (Humidité inférieure à 20 %) d’un minim um de 2 ans de coupe (Hêtre, Charme ) , 5 ans pour le Chêne – le sapin et les résineux sont interdit).Le tiroir cendrier doit toujours rester dans l’appareil sauf lors du décendrage. Pour ouvrir et fermer la porte, utiliser le gant anti-chaleur Il peut être nécessaire d’arrêter l’extracteur de la ventilation mécanique pour éviter le refoulement des fumées dans la pièce lors de l’o uverture de la porte.Première mise en service.Pendant les premières utilisations de l’appareil une odeur de peinture va se dégager de l’appareil : aérer la pièce pour limiter ce désagrément ou effectuer, avant l’installation, une première chauffe à l’extérieur de la maison.Il est recommandé, pendant les premières heures de mise en service, de faire un feu modéré afin de permettre une dilatation normale de l’ensemble de l’appareil.Allumage :Placer sur la grille du papier froissé (ou 1 à 2 morceaux d’allume feu) et environs 3 kg de petit bois sec (des petites branches bien sèches ou du bois fendu finement). Enflammer la charg e d’allumage, fermer la porte de l’appareil et ouvrir entièrement l’arrivée d’air. Lorsque le bois est bien enflammé, vous pouvez charger votre appareil et commencer à réduire l’arrivée d’air en s’assurant :∙Que la réduction d’air n’éteigne pas les flammes. Si c’est le cas rouvrir en peu plus longtemps l’arrivée d’air.∙Que l’embrasement de la charge ne devienne pas trop intense (avec des flammes atteignant majoritairement le haut de la chambr e de combustion). Si c’est le cas réduire l’arrivée d’air.Il est possible de laisser la porte entre-ouverte pour faciliter cette phase d’allumage, mais en maintenant toujours l’appareil sous surveillance.Fonctionnement à « Puissance nominale » et « combustion prolongée » :Le fonctionnement à « Puissance nominale » nécessite un rechargement toutes les 30 à 45 minutes avec de petites quantités de bois. Il faut privilégier ce mode de fonctionnement particulièrement performant et respectueux de l’environnement.L’appareil peut également assurer un fonctionnement en « combustion prolongée » quand une puissance réduite et une autonomie importante sont recherchées.▪Puissance nominale :Elle est obtenue :o avec une charge de bois de 1,5 kg, sous forme de 2 demies bûches de bois dur (= une bûche fendue)o avec un tirage de 12Pao c harge renouvelée toutes les 30 à 45 minutes sur un lit de braises d’environ 3 cmo en mettant le réglage d’allure en position « Puissance nominale ».Une baisse d’activité peut se produire à cause d’une évolution défavorable de la combustion, d’une géomét rie inadaptée des bûches, de l’utilisation d’un bois dur ou humide. Ces phénomènes de ralentissement, qui ne sont ni exceptionnels ni totalement prévisibl es, se traduisent par la diminution du rideau de flamme (le combustible forme une voûte et n’est plus en contact avec la braise), la diminution progressive de la réserve de braise et le refroidissement du foyer. Ils s’accompagnent d’une chute de puissance et d’une baisse des performances.Pour l’éviter : ouvrir la porte du foyer avec précaution , réorganiser la charge sur le lit de braise en procédant par piquage et déplacement du combustible avec un tisonnier en prenant garde de ne pas faire chuter de braise hors du foyer , puis refermer la porte. L’activité reprend immédiatement après la fermeture de po rte.▪Combustion prolongéeElle est obtenue :o En triplant la charge de bois à la Puissance nominale, constituée de 1 à 2 bûches de bois dur non fendue de grand diamètre.o avec un tirage de 6 Pa.o en mettant le « réglage d’allure » en position « Combustion prolongée », après avoir assuré et maintenu l’allumage de la charge.o en laissant se poursuivre la combustion jusqu’à obtention d’un lit de braise réduit, destiné à assurer l’allumage d’une charg e de reprise.Ce mode de fonctionnement permet à la fois d’obte nir une puissance réduite et une autonomie de 8 heures sans rechargement.propre »Schéma de principe nonreprésentatif de l'appareilVitre propre Vitre saleAir de postcombustionprimaire▪Registre de réglage d’allure : Situé en façade, ce registre est utilisé pour modu ler l’allure de l’appareil entre « Puissance nominale » et « Combustion prolongée » (voir schémas page 7).▪Registre d’allumage: L’action sur le registre de réglage d’allure, au-delà de la position « Puissance nominale » permet d’obtenir un supplément d’air pour l’allumage. Cette position est réservée aux opérations d’allumage et de reprise et ne doit pas être maintenue plu s de 30 minutes sous peine de dommages sur l’appareil et son environnement. L’appareil doit rester sous surveillance pendant to ute la durée d’utilisation de cette position.▪Registre d’air secondaire : Ce registre doit rester ouvert à moitié pour obtenir un fonctionnement performant et une combustion propre.L’action de réglage de ce registre n’est justifiée que si les tirages sont p lus ou moins élevés que ceux qui sont recommandés (voir ci avant). Dans ce cas, ce registre peut être réglé pour obtenir un fonctionnement satisfaisant. Une fois cette adaptation effectuée, ne plus agir sur ce registre d’air secondaire, et utiliser exclusivement le registre de réglage d’allure pour faire varier la puissance de l’appareil.P OSITIONS DU REGISTRE DE REGLAGE D’ALLURE-Situé en façade du poêle à gauche, ce registre est utilisé pour moduler l’allure de l’appareil :。
巴尔查斯PVD涂层机的起弧保护方式

巴尔查斯PVD涂层机的起弧保护方式近年来,随着中国工业经济的发展,PVD涂层业务也发展很快。
目前在国际市场上知名的PVD设备制造商有瑞士的巴尔查斯、德国的普拉提,荷兰的豪泽等。
其中巴尔查斯的涂层在国际上处于领先地位,市场占有率第一。
在PVD涂层工艺过程中,起弧保护是重要的保护之一,好的起弧保护措施可以有效的避免加工零件灼伤,从而最大限度的保护工件。
一、巴尔查斯PVD涂层机介绍巴尔查斯涂层设备最普遍的型号是BAI1200,在2006年后逐渐推出了新型号-INNOVA无论是BAI1200和INNOVA设备涂层原理都是一样的,都分为抽真空、刻蚀、涂层、冷却、检漏五个阶段。
其中最关键的阶段是刻蚀和涂层:刻蚀:是巴尔查斯涂层机特有的工艺。
由弧电源在阴极和辅助阳极间放电,对工艺气体- 氩气进行电离,从而形成氩气的等离子体。
等离子体中的带正电的氩离子在偏压电源产生的电场中进行加速,高速撞击工件的基体,把附在基体表面的氧化层打掉,从而增加了涂层的结合力。
涂层:金属蒸发源(靶源)作为阴极,在真空的条件下通过它与阳极腔体之间的弧光放电,使靶材蒸发并离化,形成空间等离子体。
等离子体中的金属正离子在偏压电场的牵引下,镀覆到工件基体表面形成涂层。
巴尔查斯涂层机的基本组成包括真空镀膜室、阴极弧源、离子室、辅助阳极、基片、负偏压电源、真空系统、起弧保护装置等。
二、“起弧”定义和判断原理“起弧”定义:在刻蚀和涂层阶段,由涂层电源提供等离子体,在等离子体中包含大量的正离子和电子,如果此时在基体和腔体之间加上负向偏压,则一部分正离子会被吸附到基体上,同时电子会被吸引到腔体,形成偏压电流。
正常情况下,偏压电流均匀分布到基体和腔体之间。
但是特殊情况下,偏压电流突然上升,并且大部分电流都从工件上某个特定位置流过,这种情况我们称之为“起弧”。
起弧现象会引起工件灼伤,严重甚至报废。
判断原理:正常情况下,在刻蚀阶段中的偏压电流为10-20A ,而在涂层阶段的偏压电流为30-50A。
黑石炉(Blackstone)烹饪用氧气炉指南说明书

THERMOSTATIC HEAVY DUTY GAS GRIDDLE OPERATION MANUALThermostatic Heavy Duty Gas Griddle Models: BPHTG-2424i, BPHTG-2436i, BPHTG-2448i, BPHTG-2460i, BPHTG-2472iTHERMOSTATIC HEAVY DUTY GAS GRIDDLE OPERATION MANUALPlease complete this information and retain this manual for the life of the equipment. For Warranty Service and/or Parts, this information is required.Model NumberSerial NumberDate PurchasedBAKERS PRIDE OVEN COMPANY, LLC.1307 N. Watters Rd., Suite 180Allen, TX 75013Phone: 800.527.2100 | Fax: 914.576.0605 | Bakers Pride Oven Company, LLC is a wholly owned subsidiary of Standex International Corporation. All gas operated Bakers Pride ® griddles are intended for use with the type of gas specified on the rating plate and for installation will be in accordance with National FuelGas Code ANSI Z223.1 (latest edition)MANUAL HEAVY DUTY GAS GRIDDLE OPERATION MANUALTABLE OF CONTENTSGAS PRESSUREThe appliance and it’s individual shutoff valve (to be supplied by user) must be disconnected from the gas supply piping system during any pressure testing of that system at test pressures in excess of 1/2 psi (3.45 kPa). The appliance must be isolated from the gas supply piping system by closing it’s individual manual shut-off valve during any pressure testing of the gas supply piping system at test pressures equal to or less than 1/2 psi (3.45 kPa).INTR DUCTI N 1SAFETY PRECAUTIONS2GENERAL INSTALLATION INSTRUCTIONS 3SPECIFICATIONS & DIMENSIONS 4C NVERSI N 7LIGHTING INSTRUCTIONS 8OPERATING INSTRUCTIONS10CLEANING/MAINTENANCE 10SERVICE/REPAIR 11TROUBLESHOOTING GUIDE11REPLACEMENT PARTS LISTS & EXPLODED VIEWS12WARRANTY 17INTRODUCTIONTHERMOSTATIC HEAVY DUTY GAS GRIDDLE OPERATION MANUALCongratulations on your purchase of Bakers Pride®commercial cooking equipment. Bakers Pride takes pride in the design and quality of our products.When used as intended and with proper care and maintenance, you will experience years of reliable operation from this equipment. To ensure best results, it is important that you read and follow the instructions in this manual carefully.Location of Data PlateThe data plate is located on the right side panel. Immediately Inspect For Shipping DamageAll containers should be examined for damagebefore and during unloading. The freight carrier has assumed responsibility for its safe transit and delivery. If equipment is received damaged, either apparent or concealed, a claim must be made with the delivering carrier.A) Apparent damage or loss must be noted on thefreight bill at the time of delivery. It must then be signed by the carrier representative (Driver). If this is not done, the carrier may refuse the claim. The carrier can supply the necessary forms.B) Concealed damage or loss if not apparent untilafter equipment is uncrated, a request forinspection must be made to the carrier within 15 days. The carrier should arrange an inspection. Be certain to hold all contents and packaging material. Installation and start-up should be performed by a qualified installer who thoroughly read, understands and follows these instructions.If you have questions concerning the installation, operation, maintenance or service of this product, write Technical Service Department Bakers Pride Oven Co., LLC, 1307 N. Watters Rd #180, Allen, TX 75013.INTRODUCTION SAFETY PRECAUTIONSMANUAL HEAVY DUTY GAS GRIDDLE OPERATION MANUALSAFETY PRECAUTIONSGENERAL INSTALLATION INSTRUCTIONSEnsure gas supply and gas type, as shown on unit nameplate, agree.Unit installation must conform to the National Fuel Gas Code, ANSI Z223.1/NFPA 54, the National Gas Installation Code, CSA-B149.1, or the Propane Installation Code, CSA-B149.2 as applicable and in accordance with local codes.Screw legs into the permanently fastened nuts on the four corners of the unit and tighten by hand. Level the unit by turning the adjustment screw at the bottom of each leg. Do not slide unit with legs mounted, lift if necessary to move unit. Pipe threading compound must be resistant to the action of liquefied petroleum gases.Adequate clearance for air openings into the combustion chamber is required. Do not place objects between the bottom of the unit and the counter top.There must be adequate clearance for removal of the front panel. All major parts except the burners are removable thru the front if the gas line is disconnected.Unit must have adequate clearances for servicing. (Sides = 0”, Rear = 0”, Floor = 4”).European Community Installation Instructions:“THIS APPLIANCE MUST BE FITTED BY A COMPETENT PERSON. IN THE UK, CORGI REGISTERED INSTALLERS (INCLUDING THE REGIONS OF BRITISH GAS)UNDERTAKE TO WORK TO SAFE AND SATISFACTORY STANDARDS. THIS APPLIANCE MUST BE INSTALLED IN ACCORDANCE WITH THE GAS SAFETY (INSTALLATION AND USE) REGULATIONS AND THE RELEVANT BUILDING REGULATIONS / IEE. REGULATIONS. DETAILED RECOMMENDATIONS ARE CONTAINED IN THE FOLLOWING BRITISH STANDARD CODES OF PRACTICE - BS 6172, BS 5440 PART 2, BS 6891”“THIS APPLIANCE MUST BE INSTALLED IN ACCORDANCE WITH THE RULES IN FORCE”“MUST BE INSTALLED IN A WELL VENTILATED AREA. Ventilation requirements ie. B.S. 5440.”THESE UNITS ARE SUITABLE FOR INSTALLATION ON NON-COMBUSTIBLE SURFACES ONLY.Noncombustible clearances:0” sides (0 mm) 0” rear (0 mm)4” floor (102mm)Do not obstruct the flow of combustion and ventilation air, under the unit by the legs or behind the unit by the flue.THERMOSTATIC HEAVY DUTY GAS GRIDDLE OPERATION MANUALHEAVY DUTY GAS GRIDDLE: BPHTG-2424iSPECIFICATIONS AND DIMENSIONSGriddle Surface DimensionMANUAL HEAVY DUTY GAS GRIDDLE OPERATION MANUALHEAVY DUTY GAS GRIDDLE: BPHTG-2448iHEAVY DUTY GAS GRIDDLE: BPHTG-2436iTHERMOSTATIC HEAVY DUTY GAS GRIDDLE OPERATION MANUAL HEAVY DUTY GAS GRIDDLE: BPHTG-2460iHEAVY DUTY GAS GRIDDLE: BPHTG-2472iMANUAL HEAVY DUTY GAS GRIDDLE OPERATION MANUAL• Connect the regulator to the unit, connect gas and check for leaks.• Instructions are for conversion from Natural Gas to Propane (L.P .) on all models HDTG.• The conversion should be done before connecting the unit to the gas supply.• Units are shipped from the factory equipped for use on natural gas. Orifices necessary for L.P . (propane) are provided in a bag tied to the valve on the front panel.1. R emove the knobs and front panel.2. Remove the orifice fittings from the valve. Change the orifices to the size recommended for propane (L.P .).3. Replace the orifice fittings into the valve.• To change the regulator:CONVERSION• Check the system pressure. With the front panel removed, remove the plug from the manifold.• Place a fitting in the plug opening and connect a manometer.• For Natural gas the pressure in the manifold shouldbe 5” water column or 12.4 millibar. For L.P . the pressure in the manifold should be 10” water column of 24.9 millibar.THERMOSTATIC HEAVY DUTY GAS GRIDDLE OPERATION MANUALCONVERSION• To adjust the pressure remove the brass cap and turn the white plastic part inside the stem of the regulator. See picture regulator 7.• Take a wide straight screw driver and place it in the two notches shown in picture regulator 7 turn clockwise to increase pressure and counter-clockwise to reduce pressure. See picture regulator 7.• Once the pressure has been adjusted replace the brass cap.LIGHTING INSTRUCTIONSRelighting PilotIf the pilot light should go out for any reason:• Promptly shut off all gas at the manual shut off valve.• Turn off all knobs and pilot valves; wait 5 minutes to clear gas.• Relight following steps 4 through 6 under Standing Pilot Lighting Instructions.HDTG Pilot Safety Valve Lighting Instructions1. Turn on main gas supply to unit, on-off valve located behind the unit (not supplied with unit).2. Turn the burner control knobs to “OFF” position. Wait at least 5 minutes to allow any gas which may have accumulated in the firebox compartment to escape.3. Through the hole in the front panel, press red button on the pilot safety valve and light through observation hole in firebox. Keep red button on pilot safety depressed for at least 1 minute after pilot has lit. If pilot does not light, repeat this step.4. To adjust the pilot flame, rotate knob next to the red button. Turning the knob clockwise increases the pilot flame. A properly sized pilot should be 1/2” to 3/4” long (12/19 mm).HDTG Griddles are furnished with either a pilot safety valve or a standing pilot (not available in the European Community). Please follow the instructions for your unit.Standing Pilot Lighting Instructions:(Not Available in the European Community)The pilot lights on the broilers have been set at the factory. A screwdriver may be required for the first lighting to adjust the flame for your elevation.1. Turn off the manual shut off valve and wait 5 minutes to clear the gas.2. Turn all knobs to the “OFF” position.3. The valve can be accessed through an opening in the front panel or remove the cooking grates and light the pilot from above.4. Turn the manual shut off valve on.5. Hold an ignition source (match) to both openings on the pilot tube. When the flames are established, remove the ignition source.6. Turn the burner knobs to “HI”. If the burner does not ignite, promptly open the pilot valve more. If the pilot flame appears larger than necessary, turn it down and reset burner ignition. The pilot flame should be as small as possible but large enough to guarantee reliable ignition of the burners when the knobs are turned to “HI”.MANUAL HEAVY DUTY GAS GRIDDLE OPERATION MANUALLIGHTING INSTRUCTIONSHDTG Lighting The Main Burner:• Turn the thermostat to the desired temperature.Main burner air supply:1. For efficient burner operation, a proper balanceof gas volume and primary air supply mustbe maintained which will result in completecombustion. Insufficient air supply results ina yellow streaming flame. Primary air supply iscontrolled by an air shutter on the front of theburner.2. Loosen the screws on the front of the burner andadjust the air shutter to just eliminate the yellowtips of the burner flame. Lock the air shutter inplace by tightening the screws.European Community:If adjustment becomes necessary in the field, it should bedone by a factory authorized and trained technician whoshould seal the screw after the adjustment to safeguardagainst un-authorized tampering by the end user.All burners are lit from constantly burning pilots. Turningthe valve to the desired flame height is all that is requiredto put the unit in service.Do not permit fans to blow directly at the unit. Whereverpossible, avoid open windows next to the units’ sidesor back. Avoid wall type fans which create air cross-currents within a room.It is also necessary that sufficient air should be allowedto enter the room to compensate for the amount ofair removed by any ventilating system. Otherwise, asubnormal atmospheric pressure will occur, affectingoperation and causing undesirable working conditions.A properly designed and installed hood will act as theheart of the ventilating system for the room or areain which the unit is installed, and will leave the unitindependent of changing draft conditions.All valves must be checked and lubricated periodically.This must be done by an authorized servicerepresentative in your area.THERMOSTATIC HEAVY DUTY GAS GRIDDLE OPERATION MANUAL OPERATING INSTRUCTIONSSeason Griddle:Heat to low temperature (300 - 350 F/150-180C) and pour on a small amount of cooking oil, about one ounce (30cc) per square foot of surface. Spread the oil over the entire griddle surface with a cloth to create a thin film. Wipe off any excess oil with a cloth. Repeat this procedure 2 to 3 times until the griddle has a slick, mirror-like surface. OperationTurn the burners on about 15-20 minutes before cooking for preheating. Set the knobs to the desired flame height (HDTG). Each valve will control the gas flow to the burner to bring that area of the plate up to the set temperature. If different temperature settings are to be used, adjoining areas should be set at progressively higher temperatures using the lowest temperatures on the outside burners. A uniform and systematic approach to the loading of the griddle will produce the most consistent product results.CLEANING / MAINTENANCEInitial Cleaning:Prior to operating your new griddle, thoroughly wash the griddle surface and the exterior with a mild detergent or soap solution. Do not use abrasive cleaners since this might damage the cabinet finish. If the stainless steel surfaces become discolored, scrub by rubbing only in the direction of the finished grain.Cleaning:1. Always turn unit off and allow it to cool completelybefore cleaning. Clean thoroughly before first use.2. After each use, clean the griddle with wire brush orflexible spatula.3. Once a day, thoroughly clean splash back, sides andfront. Remove the grease drawer, empty it and wash it out.4. Once a week, clean the griddle surface thoroughly.If necessary, use a griddle stone, wire brush or steel wool on the surface. Rub with the grain of the metal while the griddle is still warm. A detergent may beused on the plate surface to help clean it; but, care must be taken to be sure the detergent is thoroughly removed. After removal of the detergent, the surfaceof the plate should then be covered with a thin film of oil to prevent rusting. Clean stainless surfaceswith a damp cloth and polish with a soft dry cloth.To remove discoloration, use a nonabrasive cleaner.After each “weekly” cleaning, the griddle must beseasoned again. If the griddle usage is very high, the “weekly” cleaning procedures may be done moreoften than once a week.Extended Shutdown:Turn the manual shutoff valve to “OFF”; (field installedvalve not supplied by the manufacturer); turn all control knobs to the “OFF” position; and shut off the pilot flame by turning the adjustment on the pilot valve.If the griddle is to be shut down for an extended period, put a heavy coat of grease over the griddle plate.MANUAL HEAVY DUTY GAS GRIDDLE OPERATION MANUALSERVICE / REPAIRTROUBLESHOOTING GUIDEIf you have any questions or problems contact your nearest Bakers Pride Service Representative.THERMOSTATIC HEAVY DUTY GAS GRIDDLE OPERATION MANUAL EXPLODED VIEW – BPHTG GRIDDLES (DOMESTIC)PARTS LIST – BPHTG GRIDDLES (DOMESTIC)Description BPHTG-2424i BPHTG-2436i BPHTG-2448i BPHTG-2460i 21831220Weldm't, Griddle Plate121831320Weldm't, Griddle Plate121831520Weldm't, Griddle Plate121832920Weldm't, Griddle Plate121833020Weldm't, Griddle Plate21826433Side, Firebox2222MANUAL HEAVY DUTY GAS GRIDDLE OPERATION MANUAL PARTS LIST – BPHTG GRIDDLES (DOMESTIC)THERMOSTATIC HEAVY DUTY GAS GRIDDLE OPERATION MANUAL EXPLODED VIEW – BPHTG GRIDDLES (CE)PARTS LIST – BPHTG GRIDDLES (CE)MANUAL HEAVY DUTY GAS GRIDDLE OPERATION MANUAL PARTS LIST – BPHTG GRIDDLES (CE)PARTS LIST – BPHTG GRIDDLES (CE)512065885Electrode, Spark12233 522069700Valve, Ball 3/4" 90"11111 532092592Nipple, 3/4 x Close Schd. 40 Black11111 542092626Pipe, Inlet11111 552092702Pilot Safety Valve12233 562092903Orifice, Pilot Natural12233 572092904Orifice Pilot LP12233 582093200Thermocouple, 18" High MV Output12233 5921831213Tube, Pilot Supply CE121830813Tube, Pilot Supply CE121831512Tube, Pilot Supply CE11 6021831317Tube, Pilot Supply CE121831513Tube, Pilot Supply CE121832913Tube, Pilot Supply CE121833017Tube, Pilot Supply CE1 6121833018Tube, Pilot Supply CE1 6221831316Strap, Ignitor12233NOTESBAKERS PRIDE LIMITED WARRANTYWHAT IS COVERED This warranty covers defects in material and workmanship under normal use, and applies only to the original purchaser providing that:• The equipment has not been accidentally or intentionally damaged, altered or misused;• The equipment is properly installed, adjusted, operated and maintained in accordance with Nationaland local codes and in accordance with the installation instruction provided with the product;• The serial number rating plate affixed to the equipment has not been defaced or removed.WHO IS COVERED This warranty is extended to the original purchaser and applies only to equipment purchased for use in the U.S.A.COVERAGE PERIOD Cyclone Convection Ovens: BCO Models: One (1) Year limited parts and labor; (1) Year limited door warranty.GDCO Models: Two (2) Year limited parts and labor; (2) Year limited door warranty.CO11 Models: Two (2) Year limited parts and labor; (5) Year limited door warranty.All Other Products: One (1) Year limited parts and labor. Warranty period begins the date of dealer invoice to customeror ninety (90) days after shipment date from Bakers Pride - whichever comes first.WARRANTY This warranty covers on-site labor, parts and reasonable travel time and travel expenses of the authorized service COVERAGE representative up to (100) miles, round trip, and (2) hours travel time. The purchaser, however, shall be responsible for all expenses related to travel, including time, mileage and shipping expenses on smaller counter models that may becarried into a Factory Authorized Service Center, including the following models: PX-14, PX-16, P18, P22S, P24S, PD-4,PDC, WS Series and BK-18.EXCEPTIONS All removable parts in Bakers Pride® cooking equipment, including but not limited to: Burners, Grates, Radiants, Stones and Valves, are covered for a period of SIX MONTHS. All Ceramic Baking Decks are covered for a period of THREEMONTHS. The installation of these replacement decks is the responsibility of the purchaser. The extended Cyclone doorwarranty years 3 through 5 is a parts only warranty and does not include labor, travel, mileage or any other charges.EXCLUSIONS• Negligence or acts of God,• Failures caused by erratic voltages or gas supplies,• Thermostat calibrations after (30) days fromequipment installation date,• Unauthorized repair by anyone other than a BakersPride Factory Authorized Service Center,• Air and Gas adjustments,• Damage in shipment,• Light bulbs,• Alteration, misuse or improper installation,• Glass doors and door adjustments,• Thermostats and safety valves with broken capillary tubes,• Fuses,• Char-broiler work decks and cutting boards,• Tightening of conveyor chains,• Adjustments to burner flames and cleaning of pilot burners,• Tightening of screws or fasteners,• Accessories — spatulas, forks, steak turners, grate lifters, oven brushes, scrapers, peels. etc.,• Freight — other than normal UPS charges,• Ordinary wear and tear.INSTALLATION Leveling and installation of decks as well as proper installation and check out of all new equipment —per appropriate installation and use materials — is the responsibility of the dealer or installer, not the manufacturer.REPLACEMENT PARTS Bakers Pride genuine Factory OEM parts receive a (90) day materials warranty effective from the date of installation by a Bakers Pride Factory Authorized Service Center.This Warranty is in lieu of all other warranties, expressed or implied, and all other obligations or liabilities on the manufacturer’s part. Bakers Pride shall in no event be liable for any special, indirect or consequential damages, or in any event for damages in excess of the purchase price of the unit. The repair or replacement of proven defective parts shall constitute a fulfillment of all obligations under the terms of this warranty.Form #U4177A 1/07Be sure to keep up with new product announcements and events on social media!。
- 1、下载文档前请自行甄别文档内容的完整性,平台不提供额外的编辑、内容补充、找答案等附加服务。
- 2、"仅部分预览"的文档,不可在线预览部分如存在完整性等问题,可反馈申请退款(可完整预览的文档不适用该条件!)。
- 3、如文档侵犯您的权益,请联系客服反馈,我们会尽快为您处理(人工客服工作时间:9:00-18:30)。
BD 802 633 BE 4th Edition 11/2001B A I 730 D D i a m o n dC o a t i n g S y s t e mP a r t I / O p e r a t i n g M a n u a lS T A N D A R DPart I / Operating ManualBAI 730 D Diamond Coating SystemI m p o r t a n t i n f o r m a t i o n f o r t h e u s e rOnly appropriately qualified personal will have the required technical knowledge to correctly in-terpret and act upon the technical information in this document.We also point out that the content of this document is not part of, nor do they affect, any earlieror existing agreement, commitment or legal relationship. All obligations of Balzers Ltd. will begoverned by the sales contract in question, which also contains complete and exclusively validprovisions regarding warranty. These contractual warranty provisions are neither extended norrestricted by the information contained in this document.The information contained in this document will be regularly updated and checked for correct-ness, and may be subject to amendments at any time without prior notice.Manufacturer's address:Balzers LimitedFL-9496 BalzersPhone+423 388 4111Fax+423 388 5419Ó Balzers Limited. 1997Subject to technical alterations.No part of this document may be stored in a retrieval system, transmitted, or reproduced in anyway, including but not limited to photocopy, photograph, magnetic or other record, without theprior agreement and written permission from BALZERS Ltd. Offenders are liable to pay da-mages. All rights in respect of issuance of a patent or design registration are reserved.The system program, delivered as standard accessory or as updated version, are intended foruse only with the BAI 730 D system installed. It is illegal to use or copy this software for otherpurposes; in particular, it is strictly forbidden to give copies to other persons without the writtenpermission from BALZERS Ltd.2 / 6BD 802 633 BE 4th Edition 11/2001Part I / Operating ManualBAI 730 D Diamond Coating System1.G e n e r a l r e m a r k sThe deposition of wear protective coatings onto tools consists today not only of running thedeposition process. It consists also in the choice of appropriate substrates, pretreatment, toolinspection, documentation and delivery.This is especially true for diamond deposition, because the appropriate choice of the substratesand the pretreatment is the key for achieving good adhesion. Only carbide substrates can becoated and out of the large group of different carbide grades only grades with specificproperties.Depending on the substrates to be coated different efforts for pretreatment are necessary. Ac-cording to these requirements this manual is split into 3 parts:Part I:BAI 730 D Diamond Coating SystemPart II: Pretreatment ManualPart III: Diamond Deposition on ToolsPart I is the Manual for the BAI730 D Diamond Deposition System. It gives you all informationregarding the diamond deposition process, equipment and handling. It allows you to coat spe-cific substrates specially prepared from carbide manufacturers for diamond deposition (1 basicstandard process).Part II describes the pretreatment process and equipment developed by Balzers especially fordiamond deposition. It gives you the technical, chemical and handling information for the pre-treatment of conventionally available carbides for the following successful diamond deposition.Part III is the handbook for the tool coater. It describes all steps from income inspection to de-livery of the diamond coated tools. Here you find different recipes for the deposition process andpretreatment and which process you must choose for which tool application. The recipes youget in part III depend on the package you bought and will be supplemented in future with newrecipes according to progress in development.BD 802 633 BE 4th Edition 11/2001 3 / 6Part I / Operating ManualBAI 730 D Diamond Coating SystemLeerseite4 / 6BD 802 633 BE 4th Edition 11/2001Part I / Operating ManualBAI 730 D Diamond Coating SystemChapter overview The chapter Use, Technical Data and Infrastructure specifies the use of the DiamondCoating System and gives all the necessary technical parameters and specifications.The chapter Safety describes the safety philosophy of the BAI 730 D coating system. It provi-des information on the residual hazards, explains the safety precautions of the manufacturer,and explains safety regulations and warnings.The chapter Design and Function contains detailed information on the design and the func-tion of the BAI 730 D coating system.The chapter Operating Elements provides information on all control elements of the BAI 730D coating system.The chapter Operation describes how to operate the BAI 730 D coating system. This coversall principle operating steps of the deposition process.The chapter Troubleshooting contains a summary of errors and that may appear on theprocess visualization system. It gives also a checklist for possible errors and explainsadvanced trouble shooting.The chapter Maintenance and Service contains a maintenance and service list for the BAI730 D coating system.The chapter Installation, Transport and Disposal provides information on the transport andthe installation of the BAI 730 D coating system. It also explains the rules which are to be ob-served when the system is to be disposed.Consumables / Additional Parts / Accessories / Spare PartsParts lists and Drawings in exploded FormSoftware V04UAdjustmentsBD 802 633 BE 4th Edition 11/2001 5 / 6Part I / Operating ManualBAI 730 D Diamond Coating System6 / 6BD 802 633 BE 4th Edition 11/2001。