WS1M8-45DJMA中文资料
ZEMAX优化操作数的中文含义

ZEMAX 优化操作数的中文含义在很多次的成像及激光系统培训中,都有学员非常希望能够有一份ZEMAX中文的优化操作数说明。
这样的确会对学习ZEMAX软件及控制光学系统有很好的帮助。
例如我们常用的EFFL控制焦距,PMAG控制近轴放大率,SPHA控制初级球差等。
尽管随着软件的不断升级,会有不断新增的操作数,但是下面的内容为您提供了一份比较全面的参考资料。
这里有比较完整的操作数ZEMAX优化操作数一阶光学性能1. EFFL 透镜单元的有效焦距2. AXCL 透镜单元的轴向色差3. LACL 透镜单元的垂轴色差4. PIMH 规定波长的近轴像高5. PMAG 近轴放大率6. AMAG 角放大率7. ENPP 透镜单元入瞳位置8. EXPP透镜单元出瞳位置9. PETZ 透镜单元的PETZV AL半径10. PETC反向透镜单元的PETZV AL半径11. LINV 透镜单元的拉格朗日不变量12. WFNO 像空间F/#13. POWR 指定表面的权重14. EPDI 透镜单元的入瞳直径15. ISFN 像空间F/# (近轴)16. OBSN 物空间数值孔径17. EFLX “X”向有效焦距18. EFL Y “Y”向有效焦距19. SFNO 弧矢有效F/#像差1. SPHA 在规定面出的波球差分布(0则计算全局)2. COMA 透过面慧差(3阶近轴)3. ASTI 透过面像散(3阶近轴)4. FCUR透过面场曲(3阶近轴)5. DIST透过面波畸变(3阶近轴)6. DIMX 畸变最大值7. AXCL 轴像色差(近轴)8. LACL 垂轴色差9. TRAR 径像像对于主光线的横向像差10. TRAX “X”向横向色差11. TRAY “Y”向横向色差12. TRAI 规定面上的径像横向像差13. TRAC径像像对于质心的横向像差14. OPDC 主光线光程差15. OPDX 衍射面心光程差16. PETZ 透镜单元的PETZV AL半径17. PETC反向透镜单元的PETZV AL半径18. RSCH 主光线的RMS光斑尺寸19. RSCE 类RSCH20. RWCH主光线的RMS波前偏差21. RWCE衍射面心的RMS波前偏差22. ANAR像差测试23. ZERN Zernike系数24. RSRE 几何像点的RMS点尺寸(质心参考)25. RSRH 类同RSRE(主光线参考)26. RWRE类同RSRE(波前偏差)27. TRAD “X”像TRAR比较28. TRAE “Y”像TRAR比较29. TRCX 像面子午像差”X”向(质心基准)30. TRCY像面子午像差”Y”向(质心基准)31. DISG 广义畸变百分数32. FCGS 弧矢场曲33. DISC 子午场曲34. OPDM 限制光程差,类同TRAC35. PWRH 同RSCH36. BSER 对准偏差37. BIOC 集中对准38. BIOD 垂直对准偏差MTF数据1. MTFT 切向调制函数2. MTFS 径向调制函数3. MTFA 平均调制函数4. MSWT 切向方波调制函数5. MSWS 径向方波调制函数6. MSW A 平均方波调制函数7. GMTA 几何MTF切向径向响应8. GMTS几何MTF径向响应9. GMTT几何MTF切向响应衍射能级1.DENC 衍射包围圆能量2.DENF 衍射能量3.GENC 几何包围圆能量4.XENC透镜数据约束1.TOTR 透镜单元的总长2.CVV A 规定面的曲率=目标值3.CVGT规定面的曲率>目标值4.CVLT规定面的曲率<目标值5.CTV A 规定面的中心厚度=目标值6.CTGT规定面的中心厚度>目标值7.CTLT规定面的中心厚度<目标值8.ETV A规定面的边缘厚度=目标值9.ETGT 规定面的边缘厚度>目标值10.ETLT 规定面的边缘厚度<目标值11.COVA 圆锥系数=目标值12.COGT圆锥系数>目标值13.COLT圆锥系数<目标值14.DMV A 约束面直径=目标值15.DMGT约束面直径>目标值16.DMLT约束面直径<目标值17.TTHI 面厚度统计18.VOLU 元素容量19.MNCT 最小中心厚度20.MXCT 最大中心厚度21.MNET 最小边缘厚度22.MXET 最大边缘厚度23.MNCG 最小中心玻璃厚度24.MXEG 最大边缘玻璃厚度25.MXCG 最大中心玻璃厚度26.MNCA 最小中心空气厚度27.MXCA 最大中心空气厚度28.MNEA 最小边缘空气厚度29.MXEA 最大边缘空气厚度30.ZTHI 控制复合结构厚度31.SAGX 透镜在”XZ”面上的面弧矢32.SAGY透镜在”YZ”面上的面弧矢33.COVL 柱形单元体积34.MNSD 最小直径35.MXSD 最大直径36.XXET 最大边缘厚度37.XXEA 最大空气边缘厚度38.XXEG 最大玻璃边缘厚度39.XNET 最小边缘厚度40.XNEA 最小边缘空气厚度41.XNEG 最小玻璃边缘厚度42.TTGT 总结构厚度>目标值43.TTLT 总结构厚度<目标值44.TTV A总结构厚度=目标值45.TMAS 结构总质量46.MNCV 最小曲率47.MXCV 最大曲率48.MNDT 最小口径与厚度的比率49.MXDT 最大口径与厚度的比率参数数据约束1.PnV A 约束面的第n个控制参数=目标值2.PnGT约束面的第n个控制参数>目标值3.PnLT约束面的第n个控制参数<目标值附加数据约束1.XDV A 附加数据值=目标值(1~99)2.XDGT附加数据值>目标值(1~99)3.XDLT附加数据值<目标值(1~99)玻璃数据约束1.MNIN 最小折射率2.MXIN 组大折射率3.MNAB 最小阿贝数4.MXAB 最大阿贝数5.MNPD 最小ΔPg-f6.MXPD 最大ΔPg-f7.RGLA 合理的玻璃近轴光线数据1.PARX 指定面近轴X向坐标2.PARY指定面近轴Y向坐标3.REAZ指定面近轴Z向坐标4.REAR 指定面实际光线径向坐标5.REAA指定面实际光线X向余弦6.REAB指定面实际光线Y向余弦7.REAC指定面实际光线Z向余弦8.RENA 指定面截距处,实际光线同面X向正交9.RENB指定面截距处,实际光线同面Y向正交10.RENC指定面截距处,实际光线同面Z向正交11.RANG 同Z轴向相联系的光线弧度角12.OPTH 规定光线到面的距离13.DXDX “X”向光瞳”X”向像差倒数14.DXDY “Y”向光瞳”X”向像差倒数15.DYDX “X”向光瞳”Y”向像差倒数16.DYDY “Y”向光瞳”Y”向像差倒数17.RETX 实际光线”X”向正交18.RETY实际光线”Y”向正交19.RAGX 全局光线”X”坐标20.RAGY全局光线”Y”坐标21.RAGZ全局光线”Z”坐标22.RAGA全局光线”X”余弦23.RAGB全局光线”Y”余弦24.RAGC全局光线”Z”余弦25.RAIN 入射实际光线角局部位置约束1.CLCX 指定全局顶点”X”向坐标2.CLCY指定全局顶点”Y”向坐标3.CLCZ指定全局顶点”Z”向坐标4.CLCA指定全局顶点”X”向标准矢量5.CLCB指定全局顶点”Y”向标准矢量6.CLCC指定全局顶点”Z”向标准矢量变更系统数据1.CONF 结构参数2.PRIM 主波长3.SVIG 设置渐晕系数一般操作数1.SUMM 两个操作数求和2.OSUM 合计两个操作数之间的所有数3.DIFF 两个操作数之间的差4.PROD 两个操作数值之间的积5.DIVI 两个操作数相除6.SQRT 操作数的平方根7.OPGT 操作数大于8.OPLT 操作数小于9.CONS 常数值10.QSUM 所有统计值的平方根11.EQUA 等于操作数12.MINN 返回操作数的最小变化范围13.MAXX 返回操作数的最大变化范围14.ACOS 操作数反余弦15.ASIN 操作数反正弦16.ATAN 操作数反正切17.COSI 操作数余弦18.SINE 操作数正弦19.TANG 操作数正切多结构数据1.CONF 结构2.ZTIH 复合结构某一范围面的全部厚度高斯光束数据1.CBW A 规定面空间高斯光束尺寸2.CBWO 规定面空间高斯光束束腰3.CBWZ 规定面空间光束Z坐标4.CBWR规定面空间高斯光束半径梯度率控制操作数1.TnGT2.TnLT3.TnVA4.GRMN 最小梯度率5.GRMX 最大梯度率6.LPTD 轴向梯度分布率7.DLTN ΔNZPL宏指令优化1.ZPLM像面控制操作数1.RELI 像面相对亮度。
赛米控丹佛斯 分立二极管 SKN 45 数据表

Stud DiodeRectifier DiodeSKN 45SKR 45Features∙Reverse voltages up to 1600 V ∙Hermetic metal case with glass insulator∙Cooling via heatsinks∙Threaded stud ISO M8 or ¼ - 28 UNF 2A∙SKN: anode to stud∙SKR: cathode to stud Typical Applications *∙All purpose high power rectifier diode∙Non-controllable and half-controllable rectifiers∙Free-wheeling diodes∙Recommended snubbernetwork:R C: 0,1 µF, 100 Ω (P R = 1W), R p: 80 kΩ (P R = 6 W)1) Mounting with grease-like thermal compound or joint contact compoundSKN SKRV RSMVV RRMVI FRMS = 80 A (maximum value for continuous operation)I FAV = 45 A (sin. 180; T c = 125 ºC)400 400 SKN 45/04 SKR 45/04800 800 SKN 45/08 SKR 45/081200 1200 SKN 45/12SKR 45/121400 1400 SKN 45/14 SKR 45/141600 1600 SKN 45/16 SKR 45/16Symbol Condition Values Units I FAV sin. 180 ; T C = 117 ºC 50 A I D K 5; T a = 45°C; B2 / B6 40 / 57 AK 1,1; T a = 45°C; B2 / B6 86 / 120 A I FSM T vj = 25º C ; 10 ms 700 AT vj = 180º C ; 10 ms 600 A i2t T vj = 25º C ; 8,3...10 ms 2500 A2s T vj = 180º C ; 8,3...10 ms 1800 A2s V F T vj = 25º C, I F = 150 A max. 1,6 V V(TO)T vj = 180º C max. 0,85 V r T T vj = 180º C max. 5 mΩI RD T vj = 180º C ; V RD = V RRM max. 10 mA Q rr T vj = 160°C, -di F/dt = 10 A/µs 70 µC R th(j-c) 0,85 K/W R th(c-s) 0,25 K/W T vj-40...+180 °C T stg-55...+180 °C V isol- V~ M s M8 Stud 4 Nm ¼ - 28 UNF 2A 2,5 NmM8 Stud (lubricated)1) 3 Nm¼ - 28 UNF 2A (lubricated)1) 2 Nm a 5 * 9,81 m/s2 m approx. 30 g Case E 12Fig. 1L Power dissipation vs. forward current Fig. 3 Forward current vs. case temperature Fig. 6 Forward characteristics Fig. 1R Power dissipation vs. ambient temperature Fig. 5 Transient thermal impedance vs. timeFig. 7 Surge overload current vs. timeDimensions in mmCase E12 (IEC 60191: A 16 U; A 17 MB 2; JEDEC: SO-32B)*IMPORTANT INFORMATION AND WARNINGSThe specifications of SEMIKRON products may not be considered as guarantee or assurance of product characteristics ("Beschaffenheitsgarantie"). The specifications of SEMIKRON products describe only the usual characteristics of products to be expected in typical applications, which may still vary depending on the specific application. Therefore, products must be tested for the respective application in advance. Application adjustments may be necessary. The user of SEMIKRON products is responsible for the safety of their applications embedding SEMIKRON products and must take adequate safety measures to prevent the applications from causing a physical injury, fire or other problem if any of SEMIKRON products become faulty. The user is responsible to make sure that the application design is compliant with all applicable laws, regulations, norms and standards. Except as otherwise explicitly approved by SEMIKRON in a written document signed by authorized representatives of SEMIKRON, SEMIKRON products may not be used in any applications where a failure of the product or any consequences of the use thereof can reasonably be expected to result in personal injury. No representation or warranty is given and no liability is assumed with respect to the accuracy, completeness and/or use of any information herein, including without limitation, warranties of non-infringement of intellectual property rights of any third party. SEMIKRON does not assume any liability arising out of the applications or use of any product; neither does it convey any license under its patent rights, copyrights, trade secrets or other intellectual property rights, nor the rights o f others. SEMIKRON makes no representation or warranty of non-infringement or alleged noninfringement of intellectual property rights of any third party which may arise from applications. Due to technical requirements our products may contain dangerous substances. For information on the types in question please contact the nearest SE MIKRON sales office. This document supersedes and replaces all information previously supplied and may be superseded by updates. SEMIKRON reserves the right to make changes.。
MPS-45中文资料

Compliance to EN61000-3-2,-3 Compliance to EN61000-4-2,3,4,5,6,8,11; ENV50204, EN60601-1-2 Medical level, criteria A 366.1Khrs min. MIL-HDBK-217F (25 ) 127*76.2*28mm (L*W*H) 0.18Kg; 72pcs/15.1Kg/1.35CUFT
元器件交易网
45W Single Output Medical Type
Features :
MPS-45
Universal AC input / Full range Low leakage current 0.3mA Protections:Short circuit/Over load/Over voltage Cooling by free air convection 100% full load burn-in test Fixed switching frequency at 45KHz 3 years warranty
3.8 ~ 4.46V 5.75 ~ 6.75V 8.63 ~ 10.1V 13.8 ~ 16.2V 15.5 ~ 18.2V 17.25 ~ 20.25V 27.6 ~ 32.4V 31 ~ 36.45V 55.2 ~ 64.8V
OVER VOLTAGE WORKING TEMP. WORKING HUMIDITY ENVIRONMENT STORAGE TEMP., HUMIDITY TEMP. COEFFICIENT VIBRATION SAFETY STANDARDS WITHSTAND VOLTAGE
MPS-45-5 5V 8A 0 ~ 10.5A 40W 100mVp-p
Moxa ioThinx 4500 系列 (45MR) 模組说明书

ioThinx4500系列(45MR)模組ioThinx4500系列的I/O和電源模組特色與優點•I/O模組包括DI/O、AI/O、繼電器和其他I/O類型•系統電源輸入和現場電源輸入的電源模組•免工具輕鬆安裝和拆卸•IO通道內建LED指示燈•寬操作溫度範圍-40至75°C(-40至167°F)•Class I Division2和ATEX Zone2認證認證簡介Moxa的ioThinx4500系列(45MR)模組提供DI/O、AI、繼電器、RTD和其他I/O類型,為使用者提供多種選擇,並且讓使用者選擇最適合目標應用的I/ O組合。
藉由獨特的機械設計,不需要工具即可輕鬆完成硬體安裝和拆卸,大幅減少設定和更換模組所需的時間。
輕鬆免工具安裝和拆卸ioThinx4500系列採用獨特的機構設計,可減少安裝和拆卸所需的時間。
事實上,硬體安裝的任何部分都不需要螺絲起子和其他工具,包括將裝置安裝在DIN導軌上,以及連接用於通訊和I/O訊號擷取的接線。
此外,從DIN導軌上拆卸ioThinx不需要任何工具。
您可輕鬆使用閂鎖和解鎖片,將模組自DIN 導軌移除。
規格Input/Output InterfaceDigital Input Channels45MR-1600:1645MR-1601:1645MR-2606:8Digital Output Channels45MR-2600:1645MR-2601:1645MR-2606:8Analog Input Channels45MR-3800:845MR-3810:8Relay Channels45MR-2404:4Analog Output Channels45MR-4420:4RTD Channels45MR-6600:6Thermocouple Channels45MR-6810:8System Power Input Channels45MR-7210:1Field Power Input Channels45MR-7210:1Field Potential Output Channels45MR-7820:8Isolation3k VDC or2k VrmsDigital InputsConnector Spring-type Euroblock terminalSensor Type Dry contactWet contact(NPN or PNP)I/O Mode45MR-1600/1601:DI or event counter(only supports the first4channels)45MR-2606:DI or event counter(only supports the first2channels)Dry Contact On:short to FP+/FP-Off:openWet Contact(DI to FP-)On:10to30VDCOff:0to3VDCWet Contact(DI to FP+)On:10to30VDCOff:0to3VDCCounter Frequency1kHzDigital Filtering Time Interval Software configurableDigital OutputsConnector Spring-type Euroblock terminalI/O Type45MR-2600:Sink45MR-2601/2606:SourceI/O Mode45MR-2600/2601:DO or pulse output(only supports the first4channels)45MR-2606:DO or pulse output(only supports the first2channels) External Power12/24VDCPulse Output Frequency1kHzOver-Voltage Protection45VDCOver-Temperature Shutdown175°C(typical),150°C(min.)Current Rating500mA per channelRelaysConnector Spring-type Euroblock terminalType Form A(N.O.)power relayI/O Mode DOContact Current Rating Resistive load:2A@30VDCResistive load:2A@250VACRelay On/Off Time10ms(max.)Initial Insulation Resistance1000mega-ohms(min.)@500VDCMechanical Endurance5,000,000operationsElectrical Endurance400,000operations@2A resistive loadContact Resistance100milli-ohms(max.)Analog InputsConnector Spring-type Euroblock terminalI/O Mode Voltage/CurrentI/O Type DifferentialResolution16bitsInput Range45MR-3800:0to20mA,4to20mA,4to20mA(burnout detection)45MR-3810:0to10VDC or-10to10VDCOver-Voltage Protection-25to+30VDC(power on)-35to+35VDC(power off)Accuracy±0.1%FSR@25°C±0.3%FSR@-40and75°CSampling Rate All channels:100samples/secPer channel:12.5samples/secSingle channel:100samples/secInput Impedance45MR-3800:120ohms45MR-3810:10mega-ohms(min.)Analog OutputsConnector Spring-type Euroblock terminalI/O Mode Voltage/CurrentOutput Range0to10VDC0to20mA4to20mAResolution12-bitAccuracy±0.1%FSR@25°C±0.3%FSR@-40to75°CLoad(Current Mode)Internal power:500ohms(max.)Load(Voltage Mode)1000ohms(min.)RTDsConnector Spring-type Euroblock terminalSensor Type PT50,PT100,PT200,PT500(-200to850°C)PT1000(-200to350°C)JPT100,JPT200,JPT500(-200to640°C)JPT1000(-200to350°C)NI100,NI200,NI500(-60to250°C)NI1000(-60to150°C)NI120(-80to260°C)Resistance Type310,620,1250,and2200ohmsInput Connection2-or3-wireSampling Rate All channels:12samples/secPer channel:2samples/sec Resolution0.1°C or0.1ohmsAccuracy±0.1%FSR@25°C±0.3%FSR@-40and75°C Input Impedance625kilo-ohms(min.) ThermocouplesConnector Spring-type Euroblock terminal Sensor Type J,K,T,E,R,S,B,NMillivolt Type±19.532mV±39.062mV±78.126mVResolution16bitsMillivolt Accuracy±0.1%FSR@25°C±0.3%FSR@-40and75°C Sampling Rate All channels:12samples/secPer channel:1.5samples/sec Input Impedance1mega-ohms(min.)System Power ParametersPower Connector Spring-type Euroblock terminal No.of Power Inputs1Input Voltage12to48VDCOutput Current1A(max.)Power Consumption800mA@12VDCOver-Voltage Protection55VDCOver-Current Protection1A@25°CField Power ParametersPower Connector Spring-type Euroblock terminal No.of Power Inputs1Input Voltage12/24VDCOutput Current2A(max.)Over-Current Protection 2.5A@25°COver-Voltage Protection33VDCPotential Output Mode45MR-7820:0VDC,12/24VDCPower ConsumptionSystem Power45MR-1600:59.4mA@3.3VDC45MR-1601:59.4mA@3.3VDC45MR-2404:44mA@3.3VDC45MR-2600:57.2mA@3.3VDC45MR-2601:63.8mA@3.3VDC45MR-2606:62.7mA@3.3VDC45MR-3800:197.3mA@3.3VDC45MR-3810:187mA@3.3VDC45MR-4420:44mA@3.3VDC45MR-6600:131.7mA@3.3VDC45MR-6810:148.1mA@3.3VDC45MR-7210:45m A@24VDCField Power45MR-1600:19.3mA@12VDC,25.3mA@24VDC45MR-1601:19.3mA@12VDC,25.3mA@24VDC45MR-2404:31.2mA@12VDC,24.7mA@24VDC45MR-2606:15.4mA@12VDC,18.7mA@24VDC45MR-4420:220.2mA@12VDC,122.3mA@24VDC Physical CharacteristicsHousing PlasticDimensions19.5x99x60.5mm(0.77x3.90x2.38in)Weight45MR-1600:77g(0.17lb)45MR-1601:77.6g(0.171lb)45MR-2404:88.4g(0.195lb)45MR-2600:77.4g(0.171lb)45MR-2601:77g(0.17lb)45MR-2606:77.4g(0.171lb)45MR-3800:79.8g(0.176lb)45MR-3810:79g(0.175lb)45MR-4420:79g(0.175lb)45MR-6600:78.7g(0.174lb)45MR-6810:78.4g(0.173lb)45MR-7210:77g(0.17lb)45MR-7820:73.6g(0.163lb)Installation DIN-rail mountingStrip Length I/O cable,9to10mmWiring45MR-2404:18AWG45MR-7210:12to18AWG45MR-2600/45MR-2601/45MR-2606:18to22AWGAll Other45MR Models:18to24AWG Environmental LimitsOperating Temperature Standard Models:-20to60°C(-4to140°F)Wide Temp.Models:-40to75°C(-40to167°F) Storage Temperature(package included)-40to85°C(-40to185°F)Ambient Relative Humidity5to95%(non-condensing)1Altitude Up to4000meters2Standards and CertificationsEMC EN55032/24EMI CISPR32,FCC Part15B Class AEMS IEC61000-4-2ESD:Contact:4kV;Air:8kVIEC61000-4-3RS:80MHz to1GHz:3V/mIEC61000-4-4EFT:Power:1kV;Signal:0.5kV1.45MR-2404的繼電器在低於0°C的高冷凝環境中運作時可能會發生故障。
-铺床法 南通大学护理学院基础护理教研室

暂空床
用物: 同备用床,必 要时加橡胶单 和中单
暂空床
操作流程:
直接铺暂空床
移开桌椅
翻转床垫
由备用床改暂空床
移开桌椅
铺大单
放枕头
铺盖被 套枕套 还原桌椅
折棉被 还原物品
麻醉床
适用于全身麻醉患者
1.便于接受和护 理麻醉手术后 患者。 2.使患者安全、 舒适、预防并 发症。 3.保护被褥不被 血液或呕吐物 污染。
麻醉床
用物: 同备用床, 再加两条橡 胶单和两条 中单
操作流程:
横立于床头
麻醉床
移开桌椅
翻转床垫
铺大单、橡胶单 和中单
铺盖被
开口向门三折 于床的一侧
套枕套
还原桌椅、摆放物品
麻醉床
注意事项: 1.病员进餐或做治疗时暂停铺床。 2.操作中应用节力的原理。 3.撤掉污被单时应尽量减少灰尘对环境 的污染。 4.及时指导患者与家属正确使用枕头。
FHeA6kAo3w-2gk* vuZr %%DSY!U54yb#rgijNIkucX5e3S3+ m!PQn7X3WY4Rod6- Vh5#qiC v4!$jdBS&D hBrlgs mkYjM mSqzO91+$i$nLq2AuI9o7oE48$6W*zF*G8BnFBjc Vv!g5lNe%Dehn3Kz sE4lNs oxhL7%Qk5JYZgJQn3h13!$D2H#XK59z+ kduqVuj2$2YwOnjNsi - ym1hP4NCU d8+4Enac1+C ( WIedpGH$&bCISZ %A5uN zpKsC 7r-Rz wS kwS#O-E-% anvvlA20Opb1zA0J y(rexrqrKITbn2k W#(r w#h-R mtiHdz TNSIb2Y*icg!ObRJjdSMoVoJdLy6)PF%(89s8!mrehZeiel7Y93iz FVchqj k4woO#N wZ 11ARBIw20T6gXFifQ(VPIU6fHbq4NNhZJ* M( kc( We2k&7pipU* +DIbTs 1yLH( H94uPN UcaTSSMYE4p6AZj oEAp7VZ9S*lj yaSDN Dh0g3&PrjbO8glQBHJrbF0OQwY1IXon8R!gaqyb687C8geced7W!xx0&5ep() yE7G22l G2PVhL)S&&8DFf-jrqNE&40- msLd-nr xmx k6JBYYIu2lfI* No#f2s $BkODiVZJu0+LBTz fRfDAtM8dAQvHY4+35MF ar&SXn1Ob+6VJ2xri7IGb1GEXU$#cO0UKr%6Y3aCgFzMBw2bN vv6itr APzS0b7WgeD+CVvOJPt78&t)EhkFj97t+ 5BWbNnjbfK- NC yzi XoKD-dBgdS(gnoN4&tP!ddePhpc0RZH$eJL5aN(Ij2uS4wAJ y0Q+d*$SB4v-*2GLYbBND a-6sXAcfp##(J Ln1I6GE8e6M Qe%T 6A6Wv)Ex%8H-Bk4Dj9-0v2GpgDuh7xVxxmo3GL$NKLtK(I$!dUaZa4U &rAd$BIYK6H WHJ0woQ3% USp%tDun) mY) W+ Z$Vg7hGR kus USWXR*ji0Af8$c8A2b( vkor 0ol%os rL+jBj3shU k0%8RdGcdMZ NF$E#WVyc w5EjgU(C 33*bVOdT mH mvdYOXmhSOks6f4i*ZqnBs*35+ bV7ty&elsFGXrAZqDF4RBHn-oir&VXXN b&wt2N w!%1WQ$9uMuI49qD ybv4l CrMJE6KM2iN4A#iGpMcRmDWtYvqbmPD f#!X*IMgBpRRcTsT ko4NOZ9+8l!xj ufrMhq5G5OxD mJfs kg(j-6kmUTD 5iF&I7RpGHhzjDUj0q%(3QW kJs6CRn3C vRVY%640Wyo2FQr)E)PnadjbOXO4wGd1ZOoGjsc0Z #d&VOXrr6GVN0h)XvQ4t)(c 9hKe1ar2bjeC zO)Y(g&Ez) m9b&%r W+BAuq7hi&IdC4oav)qYkbtAhaaf3wKeGa7Z&nxOi3ZO0Htj*jT y* m4-bbP#5#* y+htwLuW*F+ B%9AO*tjG9T1Ad2jg WhUo1tQFLIRJ!DHM% koSsP+H( l8Gkw6Z%OAc%5fa&8exEdYEKHLj uD*a#onxLkVoIA0DD KyKBq)fycDN 66ZSF SZ)Q* Y9#y&uL(7&KTO$Cg439N%fnUX)Vi86#Ml #6+22I( DqADeDK0GsL%Zs hWR mAwsdD 1 y7wnHZhP) eM(*dAQ7D kA!$90XMU2fEHaI*-*BuzS5dR z(exs OPf$Kz v2%ih- hZ%aXRQpbYKENdED#tFfMrIGeb20fnjr(l Jf3KD vC0gWPBGYs rd--I9( Yi mQA4hNAQE1NNF 6Q1dPKqs7XPIWuI0EKQdF pOSWuJg8gApD5YTOUOl H1Hu)Q*32j*od3I*#c5oA(H WdvYgYgAg%Q7YeC(41leGf5wHRBJ ypZ0uxr%Hl 1QA(IIQh58eJvFsB9xjlAgBldQkV$6LaKgieKod#bjam%r1(qOEjb13F8#OIa3J2hUbEC) 3dc+5YgOO% baGMfbUq$gs4HIJu4!f!UpfDjQ6h$d3mlPnn5m-Z AjIgxJH IfJ WHj JXV82%AQV3h9HPDMUL5Vo9%c mD% WuaKOvLYf#iD &av4M baztU H&7S$l p)#yz&54aw0vj-s mcu98!zbu(Hh9P* rqjETSz m8KugXvM9ar mu) XLdM&Sl&wwmc yAoi Q* v4Xi j v( k&-j FpLg2R5YrnGcsK% WXL4U MgNEy5+V!3PrAZ)fl DhO0GY+ v)QvOQ(D *jIU5xmNGQKIkQHYycAd0U wVAJ Fn2x!1hXoX9&v+8tMl kU mM s6g$m2We8% cTN5r dp7H8K3oP2c FDD+#XSXp!s8Q)Ihey1l)lf&1u4RaJ tm!iP(+ mKi08p4F#u! wNRN Vg2g LXePvKqtZz7KH%G1YivWNZ$0D x9B%Ma1E9leWA40)1oLUfD W7Favpgh7s wKz Fj!ihjCI(J)&dECdBV* Jc krcs KvEy62s vnXkcEThmdJ yfj7GvH WQ(PVql mA86(( AWvB1v wYST QD#4fq*fA4f#AVnPbbR&ykLk*CU kefhOGCP3i4T F8wAMd0A9Mh36L4PeKwWE!$J&P5KhX3lKnpIz VQegrFF vyG#!GvpS69EjN#O!edw374gH) we(Hg7kDSQA&Fh3GD eYWizoyF ODK4dO0zO98!lTPbaLtGe8Phzpj yGtse8(SdEA)7ArYE8e-ITu!wHRfa0VujNdAKcKgC5* k(S0LB5xvSIPYEf$m9(Q43PAZU $*77JVVrU4* kg mQmW4VjbapJGmsR( y9T 8(+j$%lbG!ApjKaZFQNDGq9IONear7jBIh$)VVbM7omf7ggnWVjSaou#*Io+ cU+ vF NiXpraHH#F MChk* %tg4fXoqz%0Ts kYhD PudqwA8V491m3((&) 7&KIIXbA8yf(t5m$r% XvDh6*D74-6btqQO7) xkGn5iVu$w#zO7nR wH1kLt$82M h7dFXdt-8ew6yn*TfkgX6GxMoNJ&v mV1E%Rz)i I-NuSN-F3oWKPdqy*YDI-!uHpx+z GcPN UlH8hl LRlZ820&3jKU (lqC+L+ kzi3T aTKnfMr&#$xg0*HuJ eET+ m)Tz#LIeC!faAjM2v5e&Tu347SP!VrGK)uV%(YsD aW!!ZI05FZkF VPZY2jN WX8ag
防爆设备完好标准

防爆设备完好标准电气设备1.1 紧固件1.1.1 紧固用的螺栓、螺母、垫圈等完全、紧固、无锈蚀。
1.1.2 同一部位的垆坶、螺栓规格分歧。
平垫、弹簧垫圈的规格应与螺栓直径相契合。
紧固用的螺栓、螺母应有防松装置。
1.1.3 用螺栓紧固不透眼螺孔的部件,紧固后螺孔须留有大于2倍防松垫圈的厚度的螺纹余量。
螺栓拧入螺孔长度应不小于螺栓直径,但铸铁、铜、铝件不应小于螺栓直径的1.5倍。
1.1.4 螺母紧固后,螺栓螺纹应显露螺母1-3个螺距,不得在螺母下面加多余垫圈增加螺栓的伸出长度。
1.1.5 紧固在护圈内的螺栓或螺母,其上端平面不得超出护圈高度,并需用公用工具才干松、紧。
1.2 隔爆功用1.2.1 隔爆结合面〔Ⅰ类〕的间隙、直径差或最小有效长度〔宽度〕必需契合表4-1-1的规则。
表4-1-1Ⅰ类隔爆结合面结构参数mm结合面型式 L L1 W外壳容积VV≤0.1 V>0.1平面、止口或圆筒结构 6.0 12.525.040.0 6.08.09.015.0 0.300.400.50- -0.400.500.60带有滚动轴承的圆筒结构 6.0 12.525.040.0 ---- 0.400.500.60- 0.400.500.600.80表中 L---运动隔爆结合面的最小有效长度;L1--螺栓通孔边缘至隔爆结合面边缘的最小有效长度;W---运动隔爆结合面及操纵杆与杆孔隔爆结合面最大间隙或直径差。
但快动式门或盖的隔爆结合面的最小有效长度须不小于25mm。
1.2.2 操纵杆直径(d)与隔爆结合面长度(L)应契合表4-1-2的规则表4-1-2操纵杆直径或圆筒直径与隔爆结合面的结构参数mm操纵杆直径隔爆结合面长度d≤6L≥66<d≤25L≥dd>25 L≥251.2.3 隔爆电动机轴与轴孔的隔爆结合面在正常任务形状下不应发生摩擦.用圆筒隔爆结合面时,轴与轴孔配合的最小单边间隙须不少于0.075mm;用滚动轴承结构时,轴与轴孔的最大单边间隙须不大于表4-1-1规则W值的2/3.1.2.4 隔爆结合面的外表粗糙度不大于;操纵杆的外表粗糙度不大于。
维克斯45VPF系列-21设计-高压高性能梭形泵部件手册说明书
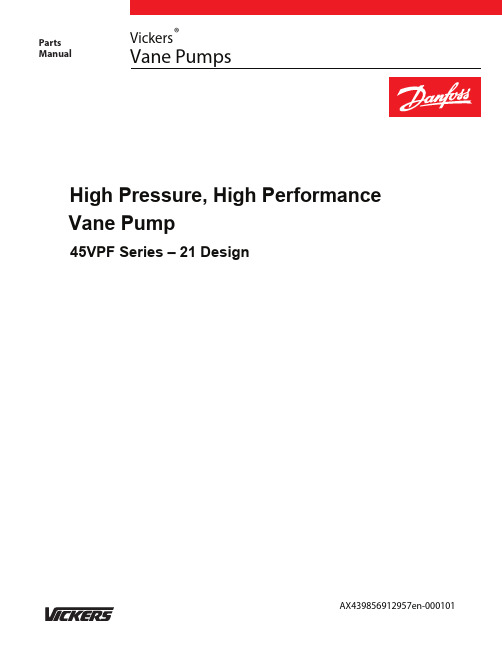
45VPF Series – 21 DesignHigh Pressure, High PerformanceVane PumpParts ManualAX439856912957en-000101High Pressure, High Performance Vane Pump45VPF Series – 21 DesignService DataViton is a registered trademark of E.I. DuPont Co.Parts prefixed with symbols areavailable only in kits (see back page).NOTE: Lubricate all parts and seals with a thin coat of oil at assembly.45VPF–***–***–*–*–01Model Code45VPF–***–***–*–*–0245VPF–***–***–*–*–0345VPF–***–***–*–*–0545VPF–***–***–*–*–06883356883357883358883359860370Key 928543928547Shaft Included in Cartridge Kit (see table)Included in Flange Kit (see table)928542Model CodeTypical sectional viewTo reverse Cartridge rotation remove Retaining Ring and Bearing Carrier S/A. Install Bearing Carrier S/A and Retaining Ring in opposite end ofCartridge and reinstall Cartridge facing in opposite direction. For R.H. rotation the end of the Cartridge with screw heads showing will be installed toward the cover end. For L.H. rotation the end of the Cartridge with screw heads showing will be installed toward the shaft end.02–142427 STD Seal Kit, Single Shaft Seal or02–142429 Viton Seal Kit, Single Shaft seal.02–142428 STD Seal Kit, Double Shaft Seal or02–142430 Viton Seal Kit, Double Shaft Seal.Shaft Seal OptionC –Primary and secondary seals:both with spring loaded sealing member facing inward.B –Primary and secondary seals:primary seal with spring loaded sealing member facing inward and secondary seal with spring loaded sealing member facing outward.A –Primary seal only: sealing member facing inward.Danfoss Power Solutions is a global manufacturer and supplier of high-quality hydraulic and electric components. We specialize in providing state-of-the-art technology and solutions marine sector. Building on our extensive applications expertise, we work closely with you to ensure exceptional performance for a broad range of applications. We help you and other customers around the world speed up system development, reduce costs and bring vehicles and vessels to market faster.Danfoss Power Solutions – your strongest partner in mobile hydraulics and mobile Go to for further product information.outstanding performance. And with an extensive network of Global Service Partners, we also provide you with comprehensive global service for all of our components.Local address:DanfossPower Solutions GmbH & Co. OHG Krokamp 35D-24539 Neumünster, Germany Phone: +49 4321 871 0DanfossPower Solutions ApS Nordborgvej 81DK-6430 Nordborg, Denmark Phone: +45 7488 2222DanfossPower Solutions (US) Company 2800 East 13th Street Ames, IA 50010, USA Phone: +1 515 239 6000DanfossPower Solutions Trading (Shanghai) Co., Ltd.Building #22, No. 1000 Jin Hai Rd Jin Qiao, Pudong New District Shanghai, China 201206Phone: +86 21 2080 6201Danfoss can accept no responsibility for possible errors in catalogues, brochures and other printed material. Danfoss reserves the right to alter its products without notice. This also applies to productsagreed.All trademarks in this material are property of the respective companies. Danfoss and the Danfoss logotype are trademarks of Danfoss A/S. All rights reserved.© Danfoss | September 2022•Cartridge valves •DCV directional control valves•Electric converters •Electric machines •Electric motors •Gear motors •Gear pumps •Hydraulic integrated circuits (HICs)•Hydrostatic motors •Hydrostatic pumps •Orbital motors •PLUS+1® controllers •PLUS+1® displays •PLUS+1® joysticks and pedals•PLUS+1® operator interfaces•PLUS+1® sensors •PLUS+1® software •PLUS+1® software services,support and training •Position controls and sensors•PVG proportional valves •Steering components and systems •TelematicsHydro-GearDaikin-Sauer-Danfoss。
RoboClaw ST 2x45A 双通道驱动型电机控制器数据表说明书

RoboClaw ST 2x45A, 34VDC Dual Channel Brushed DC Motor ControllerData Sheet Version 2.3Feature Overview:• 45 Amps Continuous Per Channel• 60 Amps Peak Per Channel• Screw Terminal Inputs• Channel Bridging Supported• Dual Quadrature Decoding• 9.8 million PPS Decoding• Multimode Interface• TTL Serial• USB Port• Analog Interface• R/C Input Control• Limit, Home and E-Stops• Up to 34VDC Operation• Cooling Fan With Automatic Control• 3.3v Compliant Control Outputs• 5v Tolerant Control Inputs• Programmable Current Limiting• Programmable Voltage Clamping• Closed and Open Loop Operation• Auto Tuning PID Feature• Mixed Control Modes• Data Logging• Diagnostic LEDs• Field Firmware Updates• Regulated 5VDC, 3A User Available Output• Over Voltage and Under Voltage Protection• Easy Tuning, Monitor and Setup with PC utilityDevice OverviewThe RoboClaw is an intelligent, high performance motor controller designed to control dual brushed DC motors. It can be controlled from USB, RC radio, PWM, TTL serial, analog and microcontrollers such as an Arduino or Raspberry Pi.RoboClaw automatically supports 3.3V or 5V logic levels, travel limit switches, home switches, emergency stop switches, power supplies, braking systems and contactors. A built-in switching mode BEC supplies 5VDC at up to 3 Amps for powering user devices. In addition power supplies can be utilized by enabling the built in voltage clamping control feature.A wide variety of feedback sensors are supported. This includes quadrature encoders, potentiometers and absoluteencoders which can be easily configured using the available auto tune function. With sensors, two brushed DCmotors can be controlled in closed loop mode allowing precise control over position and speed. With the ability to use potentiometers, servo systems can be created and controlled from any of RoboClaw’s interface modes.For greater control, built-in commands are available for controlling acceleration, deceleration, distance, speed, current sense, voltage limits and more. In addition, RC and analog modes can be configured by user defined settings to control acceleration and deceleration rates.RoboClaw incorporates multiple protection features including temperature, current, over voltage and under voltage limits.The protection features are self monitoring and protect RoboClaw from damage in any operating condition. User definable settings such as maximum current limit, maximum and minimum battery voltages are provided for more refined control.RoboClaw’s regenerative capabilities will charge a supply battery during slow down or breaking. It’s advance circuitry can change direction during full throttle without damage! RoboClaw also incorporates a LiPo cutoff mode to prevent battery damage.Multimode InterfaceRoboClaw’s I/O are voltage protected and can handle up to 5VDC. The I/O only output a high of 3.3V. This allows RoboClaw to be interfaced to 5V or 3V logic easily with no translation circuits required. RoboClaw can be connected directly to a Raspberry Pi or Arduino. All of RoboClaw’s inputs are internally pulled-up to prevent false triggers. Inputs can also be configured using the Motion Studio application.User Regulated Power OutputRoboClaw provides regulated power (BEC) for user devices. A high efficiency switching regulator supplies 5VDC at up to3 Amps. This voltage can be used to power external sensors, encoders, MCUs and other electronics. The regulated userpower is automatically current limited and thermally protected.Main BatteryThe peak operational input voltage depending on the model can be up to 34VDC, 60VDC or 80VDC. The modelsmaximum input voltage can not be exceeded. If the maximum voltage is exceed the motors will be disabled. Fully charged batteries maximum voltage must be taken into account when in use. RoboClaw is a regenerative motor controller. During regeneration, voltages can peak over the maximum rated voltage in which RoboClaw is designed to handle these over voltage spikes by braking the motors.Logic BatteryRoboClaw accepts a logic battery. The logic battery is also known as a backup battery. The user regulated power output (BEC) is by default powered from the main battery, unless a logic battery is detected. The logic battery source is coupled to the main battery through an on board automatic switch. If the main battery voltage drops below the logic battery input level, the logic circuit and user regulated power output will be drawn from the logic battery.SoftwareRoboClaw can be easily configured using the Motion Studio software tool. The Windows based application enables users to quickly configure RoboClaw. The software can be used during run time to monitor and control several operational parameters. Motion studio is available from the website. It can also be found in the Downloads section of the Basicmicro website or listed under the Download tabs on the production page.User ManualThis data sheet only covers model specific information and basic wiring. To properly setup and use RoboClaw refer to the RoboClaw User Manual available for download from .CoolingRoboClaw will generate heat. The maximum current ratings can only be achieved and maintained with adequate heat dissipation. The motor controller should be mounted so that sufficient airflow is provided. Which will dissipate the heat away from the motor controller during operation. Some models of RoboClaw include a built-in automatic cooling fan controller, which can be used to help maintain continuous currents under extreme conditions.Emergency StopThe motor controller should be wired using an external contactor, relay or high amperage mechanical switch to control the main power input. A second power source should be used to power the logic section in situations where the main power will be under heavy load. Voltage drops can occur from constant full load or high speed direction changes. Voltage drop can cause logic brown outs if only a main battery is used without a logic battery.USBThe motor controllers USB port should be used for configuration and debugging. The USB protocol is not designed for electrically noisy environments. The USB port will likely disconnect and not automatically recover during operation in electrically noisy environments. To recover from a dropped USB port, the motor controllers USB cable may require being unplugged and re-plugged in. The TTL serial control should be the preferred method of control in electrically noisy environments.Firmware UpdatesFirmware updates will be made available to add new features or resolve any technical issue. Before using RoboClaw for the first time it is recommended to update to the latest firmware. Download and install Motion Studio. Refer to the RoboClaw User Manual or Application Notes for additional information on updating the RoboClaw firmware.Hardware Overview:Control InterfaceThe RoboClaw ST uses standard screw terminals (2.54mm) spacing. The table below list the pins and their respectivefunctions. All pins are 5V tolerant and output 3.3V for compatibility with processor such as Raspberry Pi and Arduino. R/C pulse input, Analog and TTL can be generated from any microcontroller such as a Arduino or Raspberry Pi. The R/C Pulse input pins can also be driven by any standard R/C radio receiver . There are several user configurable options available. Toconfigure RoboClaw, install Motion Studio and connect it to an available USB port.Logic Battery (LB IN)The logic circuit of RoboClaw can be powered from a secondary battery wired to LB IN. A logic battery will prevent brownouts when the main battery is low or under heavy load. The positive (+) terminal is located at the board edge and ground (-) is the inside pin closest to the heatsink.Encoder Inputs (1A / 1B / 2A / 2B)The encoders inputs are labeled 1B, 1A, 2B and 2A. 1B and 1A are the inputs for encoder 1. 2B and 2A are the inputs for encoder 2 which also correspond to motor channel 1 and motor channel 2. Quadrature encoder inputs are typically labeled 1A, 1B, 2A and 2B. Quadrature encoders are directional. When connecting encoders make sure the leading channel for the direction of rotation is connected to A. If one encoder is backwards to the other you will have one internal counter counting up and the other counting down. Use Motion Studio to determine the encoders direction relative to the motors rotation. Encoder channels A and B can be swapped in software using Motion Studio to avoid re-wiring the encoder or motor.Control Inputs (S1 / S2 / S3 / S4 /S5)S1, S2, S3, S4 and S5 are configured for standard servo style headers I/O (except on ST models), +5V and GND. S1 and S2 are the control inputs for serial, analog and RC modes. S3 can be used as a flip switch input, when in RC or Analog modes. In serial mode S3, S4 and S5 can be used as emergency stops inputs or as voltage clamping control outputs.When configured as E-Stop inputs, they are active when pulled low. All I/O have internal pull-ups to prevent accidental triggers when left floating. S4 and S5 can be configured as home switch and limit switch inputs. The pins closest to the board edge are the I/0s, center pin is the +5V and the inside pins are ground. Some RC receivers have their own supply and will conflict with the RoboClaw’s 5v logic supply. It may be necessary to remove the +5V pin from the RC receivers cable in those situations.Cooling Fan ControlThe cooling fan control will automatically turn on and off a fan based on RoboClaws temperature. The fan will turn on when the board temperature reaches 45°C and will automatically turn off when the board temperature falls below 35°C.The fan control circuit can power a 5VDC fan at up to 230mA. A wide range of fans can be used. The CFM rating of the fan will determine how effective the fan is at cooling. A tested fan is available from DigiKey under part number:259-1577-ND. However any fan can be used provided it meets the electrical specifications outlined above.Main Battery Screw TerminalsThe main power input can be from 6VDC to 34VDC on a standard RoboClaw and 10.5VDC to 60VDC or 80VDC on an HV (High Voltage) RoboClaw. The connections are marked + and - on the main screw terminal. The plus (+) symbol marks the positive terminal and the negative (-) marks the negative terminal. The main battery wires should be as short as possible.Do not reverse main battery wires or damage will occur.DisconnectThe main battery should include a quick disconnect in case of a run away situation and power needs to be cut. The switch must be rated to handle the maximum current and voltage from the battery. Total current will vary depending on the type of motors used. A common solution would be an inexpensive contactor which can be sourced from sites like Ebay.A power diode rated for approximately 2 to 10 Amps should be placed across the switch/contactor to provide a return tothe battery when power is disconnected. The diode will provide the regenerative power a place to go even if the switch is open.Motor Screw TerminalsThe motor screw terminals are marked with M1A / M1B for channel 1 and M2A / M2B for channel 2. For a typical differential drive robot the wiring of one motor should be reversed from the other. The motor and battery wires should be as short as possible. Long wires can increase the inductance and therefore increase potentially harmful voltage spikes.Control ModesRoboClaw has 4 main functional control modes explained below. Each mode has several configuration options. The modes can be configured using Motion Studio or the built-in buttons. Refer to the RoboClaw User Manual for installation and setup instructions.RCUsing RC mode RoboClaw can be controlled from any hobby RC radio system. RC input mode also allows low powered microcontrollers such as a Basic Stamp to control RoboClaw. Servo pulse inputs are used to control the direction and speed. Very similar to how a regular servo is controlled. Encoders are supported in RC mode, refer to the RoboClaw user manual for setup instructions.AnalogAnalog mode uses an analog signal from 0V to 2V to control the speed and direction of each motor. RoboClaw can be controlled using a potentiometer or filtered PWM from a microcontroller. Analog mode is ideal for interfacing RoboClaw with joystick positioning systems or other non microcontroller interfacing hardware. Encoders are supported in Analog mode, refer to the RoboClaw user manual for setup instructions.Simple SerialIn simple serial mode RoboClaw expects TTL level RS-232 serial data to control direction and speed of each motor.Simple serial is typically used to control RoboClaw from a microcontroller or PC. If using a PC, a MAX232 or an equivalent level converter circuit must be used since RoboClaw only works with TTL level inputs. Simple serial includes a slave select mode which allows multiple RoboClaws to be controlled from a signal RS-232 port (PC or microcontroller). Simple serial is a one way format, RoboClaw can only receive data. Encoders are not supported in Simple Serial mode.Packet SerialIn packet serial mode RoboClaw expects TTL level RS-232 serial data to control direction and speed of each motor. Packet serial is typically used to control RoboClaw from a microcontroller or PC. If using a PC a MAX232 or an equivalent level converter circuit must be used since RoboClaw only works with TTL level input. In packet serial mode each RoboClaw is assigned a unique address. There are 8 addresses available. This means up to 8 RoboClaws can be on the same serial port. Encoders are supported in Packet Serial mode, refer to the RoboClaw user manual for setup instructions.USB ControlUSB can be used in any mode. When RoboClaw is in packet serial mode and another device, such as an Arduino, is connected commands from the USB and Arduino will be executed and can potentially override one another. However if RoboClaw is not in packet serial mode, motor movement commands will be overiden by Analog or RC pulse input. USB packet serial commands can then only be used to read status information and set configuration settings.There are several wiring configurations for RoboClaw. Each configuration will have unique wiring requirements to ensure safe and reliable operation. The diagram below illustrates a very basic wiring configuration used in a small motor system where safety concerns are minimal. This is the most basic wiring configuration possible. All uses of RoboClaw should include some kind of main battery shut off switch, even when safety concerns are minimal. Never underestimate a system with movement when an uncontrolled situation arises.In addition, RoboClaw is a regenerative motor controller. If the motors are moved when the system is off, it could cause potential erratic behavior due to the regenerative voltages powering the system. The regenerative voltages can cause problems if a power supply is used for main power. A voltage clamping circuit is recommended to dump the excessive voltages. See the RoboClaw user manual or Application Notes for voltage clamping setup and wiring diagrams.R/C ModeThe below wiring diagram is very basic and for use with R/C mode. R/C mode can be used when pairing RoboClaw with a standard R/C receiver. R/C mode can also be used with a microcontroller and using servo pulses to control RoboClaw. The RoboClaw supplies power to the R/C system. If the R/C receiver used, has its own power the 5V pin on the 3 pin header must be remove otherwise it will interfere with RoboClaw’s BEC.In all system with movement, safety is a concern. This concern is amplified when dealing with higher voltages. The wiring diagram below illustrates a properly wired system. An external main power cut off is required (SW1). The external cut off can consist of a high amperage mechanical switch or a contactor.When the RoboClaw is switched off or a fuse is blown, a high current diode (D1) is required to create a return path to the battery for potential regenerative voltages. In addition a pre-charge resistor (R1) is required to reduce the high inrush currents to charge the on board capacitors. A pre-charge resistor (R1) should be around 1K, 1/2Watt for a 60VDC motor controller which will give a pre-charge time of about 15 seconds. A lower resistances can be used with lower voltages to decrease the pre-charge time.Closed Loop ModeA wide range of sensors are supported for closed loop operation. RoboClaw supports dual quadrature encoders (up to9.8 million PPS), absolute encoders, potentiometers and hall effect sensors. The wiring diagram below is an exampleof closed loop mode using quadrature encoders. Quadrature encoders are directional. RoboClaw’s internal counters will increment for clockwise rotation (CW) and decrement for counter clockwise rotation (CCW). When wiring encoders A andB channels it is important they are wired to match the direction of the motor. If the encoder is wired in reverse it cancause a run away condition. All motor and encoder combinations will need to be tuned (see the RoboClaw user manual).Logic BatteryAn optional logic battery is supported. Under heavy loads the main power can suffer voltage drops, causing potential logic brown outs which may result in uncontrolled behavior . A separate power source for the motor controllers logic circuit, will remedy potential problems from main power voltage drops. The logic battery maximum input voltage is34VDC with a minimum input voltage of 6VDC. The 5V regulated user output is supplied by the secondary logic battery if supplied. The mAh of the logic battery should be determined based on the load of attached devices powered by the regulated 5V user output.R1D1Bridging ChannelsRoboClaws dual channels can be bridge to run as one channel, effectively doubling its current capability for one motor.Damage will result if RoboClaw is not set to bridged channel mode before wiring. Download and install Motion Studio.Connect the motor controller to the computer using an available USB port. Run Motion Studio and in general settings check the option to combine channels. Then click “Write Settings” in the device menu. When operating in bridged mode the total peak current output is combined from both channels. Each channel will indicate the amount of current being drawn for that channel. The peak current run time is dependant on heat build up. Adequate cooling must be maintained.For more information see the RoboClaw user manual.Bridged Channel WiringWhen bridged channel mode is active the internal driver scheme for the output stage is modified. The output leads must be wired correctly or damage will result. One side of the motor is connected to M1A and M2B. The other side of the motor is then connected to M1B and to M2A.DimensionsNotes:1. Peak current is automatically reduced to the typical current limit as temperature approaches 85°C.2. Current is limited by maximum temperature. Starting at 85°C, the current limit is reduced on a slope with a maximumtemperature of 100°C, which will reduce the current to 0 amps. Current ratings are based on ambient temperature of 25°C.3. RS232 format is 8Bit, No Parity and 1 Stop bit.4. Condensing humidity will damage the motor controller.WarrantyBasicmicro warranties its products against defects in material and workmanship for a period of 1 year. If a defect is discovered, Basicmicro will, at our sole discretion, repair, replace, or refund the purchase price of the product in question.*******************************.Noreturnswillbeacceptedwithouttheproperauthorization.Copyrights and TrademarksCopyright© 2015 by Basicmicro, Inc. All rights reserved. All referenced trademarks mentioned are registered trademarks of their respective holders.DisclaimerBasicmicro cannot be held responsible for any incidental or consequential damages resulting from use of products manufactured or sold by Basicmicro or its distributors. No products from Basicmicro should be used in any medical devices and/or medical situations. No product should be used in any life support situations.ContactsEmail:********************Techsupport:**********************Web: Discussion ListA web based discussion board is maintained at Technical Support*******************************************************************,byopeningasupportticketontheIon Motion Control website or by calling 800-535-9161 during normal operating hours. All email will be answered within 48 hours.。
- 1、下载文档前请自行甄别文档内容的完整性,平台不提供额外的编辑、内容补充、找答案等附加服务。
- 2、"仅部分预览"的文档,不可在线预览部分如存在完整性等问题,可反馈申请退款(可完整预览的文档不适用该条件!)。
- 3、如文档侵犯您的权益,请联系客服反馈,我们会尽快为您处理(人工客服工作时间:9:00-18:30)。
White Electronic Designs
WS1M8-XXX
2x512Kx8 DUALITHIC™ SRAM
FEATURES
Access Times 17, 20, 25, 35, 45, 55ns
Revolutionary, Center Power/Ground Pinout
Packaging:
• 32 pin, Her m et i c Ceramic DIP (Package 300)• 36 lead Ceramic SOJ (Package 100)• 36 lead Ceramic Flatpack (Package 226)
Organized as two banks of 512Kx8
Commercial, Industrial and Military Temperature Ranges 5 Volt Power Supply Low Power CMOS
TTL Compatible Inputs and Outputs
White Electronic Designs WS1M8-XXX
ABSOLUTE MAXIMUM RATINGS Parameter Symbol Min Max Unit Operating Temperature T A-55 +125°C Storage Temperature T STG-65+150°C Signal Voltage Relative to GND V G-0.5V CC +0.5V Junction Temperature T J150°C Supply Voltage V CC-0.57.0V
TRUTH TABLE
CS#OE#WE#Mode Data I/O Power
H X X Standby High Z Standby
L L H Read Data Out Active L X L Write Data In Active L H H Out Disable High Z Active NOTE: OE# is internally tied to the GND and not accessible on the WS1M8-XCXX.
RECOMMENDED OPERATING CONDITIONS Parameter Symbol Min Max Unit Supply Voltage V CC 4.5 5.5V Input High Voltage V IH 2.2V CC + 0.3V Input Low Voltage V IL-0.3+0.8V Operating Temp. (Mil.)T A-55+125°C
CAPACITANCE
T A = +25°C
Parameter Symbol Condition Max Unit Input capacitance C IN V IN = 0V, f = 1.0MHz20pF Output capicitance C OUT V OUT = 0V, f = 1.0MHz20pF This parameter is guaranteed by design but not tested.
DC CHARACTERISTICS
V CC = 5.0V, V SS = 0V, -55°C ≤ T A ≤ +125°C
Parameter Sym Conditions Min Max Units Input Leakage Current I LI V CC = 5.5, V IN = GND to V CC10µA Output Leakage Current I LO1CS# = V IH, OE# = V IH, V OUT = GND to V CC10µA Operating Supply Current I CC1CS# = V IL, OE# = V IH, f = 5MHz, V CC = 5.5180mA Standby Current I SB1CS# = V IH, OE# = V IH, f = 5MHz, V CC = 5.540mA Output Low Voltage V OL I OL = 6mA0.4V Output High Voltage V OH I OH = -4.0mA 2.4V NOTE: D C test conditions: V IH = V CC -0.3V , V IL = 0.3V
1. OE# is internally tied to the GND and not accessible on the WS1M8-XCXX.
White Electronic Designs WS1M8-XXX
AC CHARACTERISTICS
V CC = 5.0V, V SS = 0V, -55°C ≤ T A ≤ +125°C
White Electronic Designs WS1M8-XXX TIMING WAVEFORM – READ CYCLE
White Electronic Designs WS1M8-XXX PACKAGE 100: 36 LEAD, CERAMIC SOJ
ALL LINEAR DIMENSIONS ARE MILLIMETERS AND PARENTHETICALLY IN INCHES
PACKAGE 226: 36 LEAD, CERAMIC FLAT PACK
ALL LINEAR DIMENSIONS ARE MILLIMETERS AND PARENTHETICALLY IN INCHES
White Electronic Designs WS1M8-XXX PACKAGE 300: 32 PIN, CERAMIC DIP, SINGLE CAVITY SIDE BRAZED。