蒸馏过程进料位置优化
蒸馏过程的优化

蒸馏过程的优化杨小波;段文【摘要】介绍了进料位置对蒸馏塔分离能力和能耗的影响,指出进料位置优化是促进分离和节省能耗的有效途径.对进料位置优化主要介绍了计算机模拟软件PROⅡ的分离因子法、Case study分析法和optimizer法.同时还介绍了进料状态对蒸馏过程能耗的影响,通过案例介绍了优化方法并从数值上具体分析了对塔操作费用的影响.指出对于塔顶产品占主要比例的蒸馏工况,进料状态应当以露点或过热为宜;而对塔釜产品占主要比例的蒸馏工况,进料状态以泡点或过冷为佳.【期刊名称】《广州化工》【年(卷),期】2013(041)008【总页数】3页(P185-186,223)【关键词】蒸馏;进料板;进料状态;模拟软件;优化【作者】杨小波;段文【作者单位】中国石油兰州石化公司,甘肃兰州 730060【正文语种】中文【中图分类】TQ021.8蒸馏是分离液体混合物最典型的单元操作。
通过加热液体混合物造成气液两相体系,利用混合物中挥发度的差异实现组分的分离和提纯的操作过程[1]。
广泛运用于石油化工、生物、医药等领域,在石油化工行业中的运用尤其广泛。
蒸馏塔的能量消耗在石油化工生产中占1/3 左右[2]。
蒸馏塔的进料位置和进料状况对蒸馏过程能耗有重要的影响,在保证分离的同时将能耗降至最低。
下面结合计算机模拟计算软件PRO\II 介绍优化进料位置和热状况的方法。
1 优化进料位置1.1 Case study 分析法Case study 是PRO\II 的一个功能模块,可对特定的参数进行优化。
采用Case study 来判断最佳进料板位置是可靠的方法。
下面通过一个典型的教学案例的分析来说明如何确定行最佳进料位置。
设有一泡点物料:F=100 kmol/h;P=1.65 MPa;XEthane=0.01,XPropane=0.79,XN-butane=0.12,XN-pentane=0.08。
利用CW 冷却,143 ℃LS 加热。
石油加工中的蒸馏方法选择与优化
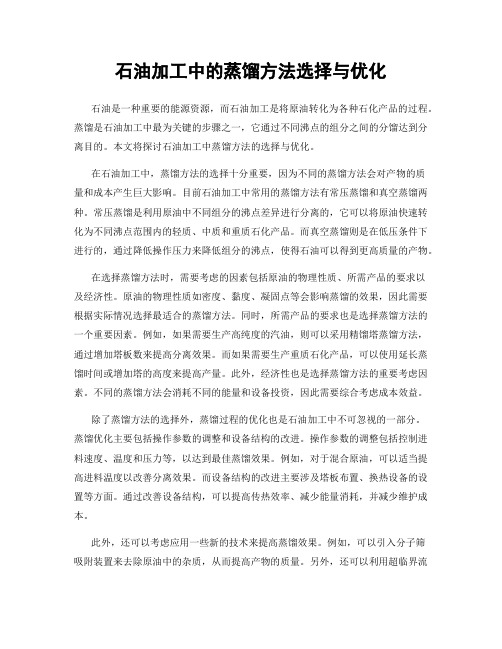
石油加工中的蒸馏方法选择与优化石油是一种重要的能源资源,而石油加工是将原油转化为各种石化产品的过程。
蒸馏是石油加工中最为关键的步骤之一,它通过不同沸点的组分之间的分馏达到分离目的。
本文将探讨石油加工中蒸馏方法的选择与优化。
在石油加工中,蒸馏方法的选择十分重要,因为不同的蒸馏方法会对产物的质量和成本产生巨大影响。
目前石油加工中常用的蒸馏方法有常压蒸馏和真空蒸馏两种。
常压蒸馏是利用原油中不同组分的沸点差异进行分离的,它可以将原油快速转化为不同沸点范围内的轻质、中质和重质石化产品。
而真空蒸馏则是在低压条件下进行的,通过降低操作压力来降低组分的沸点,使得石油可以得到更高质量的产物。
在选择蒸馏方法时,需要考虑的因素包括原油的物理性质、所需产品的要求以及经济性。
原油的物理性质如密度、黏度、凝固点等会影响蒸馏的效果,因此需要根据实际情况选择最适合的蒸馏方法。
同时,所需产品的要求也是选择蒸馏方法的一个重要因素。
例如,如果需要生产高纯度的汽油,则可以采用精馏塔蒸馏方法,通过增加塔板数来提高分离效果。
而如果需要生产重质石化产品,可以使用延长蒸馏时间或增加塔的高度来提高产量。
此外,经济性也是选择蒸馏方法的重要考虑因素。
不同的蒸馏方法会消耗不同的能量和设备投资,因此需要综合考虑成本效益。
除了蒸馏方法的选择外,蒸馏过程的优化也是石油加工中不可忽视的一部分。
蒸馏优化主要包括操作参数的调整和设备结构的改进。
操作参数的调整包括控制进料速度、温度和压力等,以达到最佳蒸馏效果。
例如,对于混合原油,可以适当提高进料温度以改善分离效果。
而设备结构的改进主要涉及塔板布置、换热设备的设置等方面。
通过改善设备结构,可以提高传热效率、减少能量消耗,并减少维护成本。
此外,还可以考虑应用一些新的技术来提高蒸馏效果。
例如,可以引入分子筛吸附装置来去除原油中的杂质,从而提高产物的质量。
另外,还可以利用超临界流体技术和萃取技术等新型分离技术,来替代传统的蒸馏方法,从而提高操作效率和产品质量。
常减压蒸馏的工艺流程
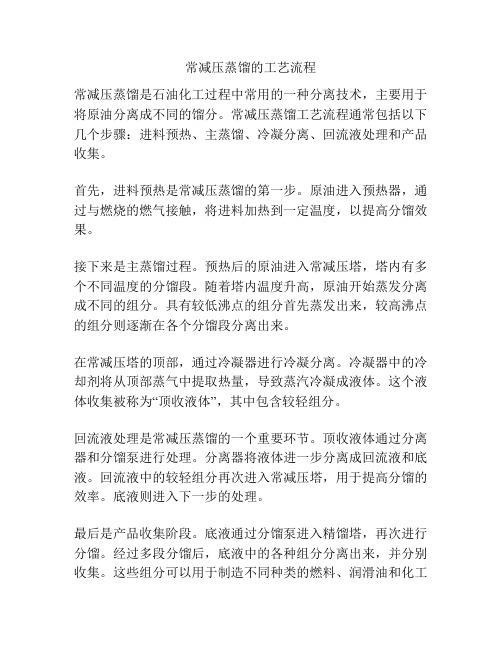
常减压蒸馏的工艺流程
常减压蒸馏是石油化工过程中常用的一种分离技术,主要用于将原油分离成不同的馏分。
常减压蒸馏工艺流程通常包括以下几个步骤:进料预热、主蒸馏、冷凝分离、回流液处理和产品收集。
首先,进料预热是常减压蒸馏的第一步。
原油进入预热器,通过与燃烧的燃气接触,将进料加热到一定温度,以提高分馏效果。
接下来是主蒸馏过程。
预热后的原油进入常减压塔,塔内有多个不同温度的分馏段。
随着塔内温度升高,原油开始蒸发分离成不同的组分。
具有较低沸点的组分首先蒸发出来,较高沸点的组分则逐渐在各个分馏段分离出来。
在常减压塔的顶部,通过冷凝器进行冷凝分离。
冷凝器中的冷却剂将从顶部蒸气中提取热量,导致蒸汽冷凝成液体。
这个液体收集被称为“顶收液体”,其中包含较轻组分。
回流液处理是常减压蒸馏的一个重要环节。
顶收液体通过分离器和分馏泵进行处理。
分离器将液体进一步分离成回流液和底液。
回流液中的较轻组分再次进入常减压塔,用于提高分馏的效率。
底液则进入下一步的处理。
最后是产品收集阶段。
底液通过分馏泵进入精馏塔,再次进行分馏。
经过多段分馏后,底液中的各种组分分离出来,并分别收集。
这些组分可以用于制造不同种类的燃料、润滑油和化工
产品等。
总的来说,常减压蒸馏是一种重要的分离技术,广泛应用于石油化工行业。
通过进料预热、主蒸馏、冷凝分离、回流液处理和产品收集等步骤,可以将原油分离成不同的组分,从而获得具有不同属性的产品。
这种工艺流程能够有效地减压蒸馏原油,提高产品的纯度和品质,满足人们对燃料和化工产品的需求。
高真空蒸馏塔的耐压性能与结构设计优化

高真空蒸馏塔的耐压性能与结构设计优化高真空蒸馏塔是化工领域中常用的分离设备,广泛应用于石油、化工、医药等行业。
其核心功能是通过蒸发和凝华两个过程,将混合物中的组分进行分离和纯化。
在高真空条件下操作,需要考虑蒸馏塔的耐压性能和结构的设计优化,以确保设备的安全运行和高效分离。
首先,高真空蒸馏塔的耐压性能是保证设备运行安全的关键因素之一。
在高真空条件下操作,蒸馏塔需要能够承受外界的压力。
其结构设计应根据设备的工作条件和要求,合理选择材料、厚度和结构。
常用的蒸馏塔材料包括不锈钢、碳钢和合金钢等,这些材料具有良好的耐压性能和耐腐蚀性能。
在选择材料时,需要考虑到被处理混合物的性质,例如温度、压力和化学性质等。
通过正确选择材料,可以确保蒸馏塔在高压环境下工作的稳定性和安全性。
此外,结构设计优化也是提高高真空蒸馏塔性能的重要手段。
通过结构设计的优化,可以提高设备的效率和分离效果,并降低能耗和生产成本。
在结构设计中,可以考虑以下几个方面的优化。
首先,塔床结构的设计是优化的重点之一。
塔床是蒸馏塔的核心部分,直接影响到分离效果和传质性能。
在设计中,可以采用不同的塔床结构,例如平板塔床、波纹板塔床和填料塔床等。
针对不同的应用场景和目标要求,选择适当的塔床结构,以提高传质效率和分离程度。
其次,优化传质与热力学性能也是蒸馏塔结构设计的重点。
传质性能的优化可以通过调整塔板数目、塔板间距、塔板孔径等参数来实现。
在蒸馏塔内部设置合理的洗涤器和分液器,可以提高传质效率和分离效果。
热力学性能的优化可以通过调整进料和冷凝剂的进出口位置,改善温度分布和热量传递,减少能耗。
此外,结构的密封性能和操作的便利性也需要考虑在内。
高真空蒸馏塔需要具备良好的密封性能,以确保在高真空条件下不泄漏。
同时,设计人员还应考虑到操作人员的操作便利性,例如设置合适的进出料口和观察窗,方便操作和维护。
总之,高真空蒸馏塔的耐压性能和结构设计优化是确保设备安全运行和高效分离的关键因素。
aspen 精馏模拟详细过程及探讨疑问

精馏塔设计初步介绍1.设计计算◆输入参数:●利用DSTWU模型,进行设计计算●此时输入参数为:塔板数(或回流比以及最小回流比的倍数)、冷凝器与再沸器的工作压强、轻组分与重组分的回收率(可以从产品组成估计)、冷凝器的形式◆输出参数(得到用于详细计算的数据):●实际回流比●实际塔板数(实际回流比和实际塔板数可以从Reflux Ratio Profile 中做图得到)●加料板位置(当加料浓度和此时塔板上液体浓度相当时的塔板)●蒸馏液(馏分)的流量●其他注:以上数据全部是估计得初值,需要按一定的要求进行优化(包括灵敏度以及设计规定的运用),优化主要在RadFrac模型中进行。
2.详细计算◆输入参数:●输入参数主要来自DSTWU中理论计算的数据◆输出参数:●输出的主要是设计板式塔所需要的水力学数据,尺寸数据等其他数据(主要是通过灵敏度分析以及设计规定来实现)3.疑问●在简捷计算中:回收率有时是估计值,它对得到详细计算所需的数据可靠性的影响是不是很大?●在简捷计算中:有多少个变量,又有多少个约束条件?●在简捷计算中:为什么回流比和塔板数有一定的关系?简捷计算(对塔)1.输入数据:●Reflux ratio :-1.5(估计值,一般实际回流比是最小回流比的1.2—2倍)●冷凝器与再沸器的压强:1.013 ,1.123 (压降为0.11bar)●冷凝器的形式:全冷凝(题目要求)、●轻重组分的回收率(塔顶馏出液):0.997 ,0.002 (如果没有给出,可以根据产品组成估计)●分析时,注意Calculation Option 中的设置,来确定最佳回流比以及加料板位置2.输出数据:●Reflux Ratio Profile中得到最佳的回流比与塔板数为:塔板数在45—50中选择,回流比在:0.547 —0.542●选定塔板数为:48,回流比为:0.544●把所选的塔板数回代计算,得到下列用于RadFrac模型计算的数据(见下图):●●从图中可得:实际回流比为:0.545(摩尔比);实际塔板数为:48;加料板位置:33;Distillate to feed fraction :0.578(自己认为是摩尔比,有疑问??);馏出液的流量:11673.5kg/h疑问:进料的流量是怎么确定的,肯定是大于11574kg/h,通过设计规定得到甲醇产量为:11574kg/h(分离要求),求出流量为:16584.0378kg/h。
逆向蒸馏_陆恩锡
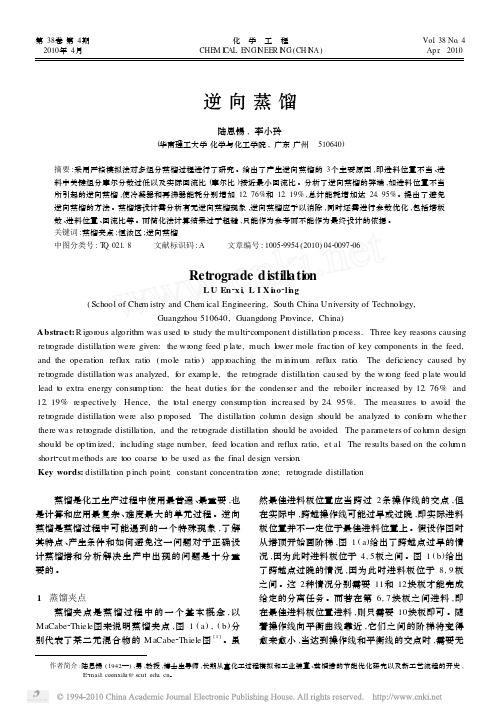
4 逆向蒸馏 4. 1 逆向蒸馏定义
如前面所述 ,蒸馏塔的分离因子曲线在靠近进 料板上方出现极小值 ,在进料板下方出现极大值 ,在 极大值和极小值之间的区间内 ,随着塔板数从下至 上 ,轻 、重关键组分比率非但不增加 ,反而减小的现 象称为逆向蒸馏 [ 1 ] 。 4. 2 逆向蒸馏产生的原因
M aCabe2Thiele图来说明蒸馏夹点 ,图 1 ( a) , ( b)分 别代表了某二元混合物的 M aCabe2Thiele图 [ 1 ] 。虽
然最佳进料板位置应当跨过 2 条操作线的交点 ,但 在实际中 ,跨越操作线可能过早或过晚 ,即实际进料 板位置并不一定位于最佳进料位置上 。假设作图时 从塔顶开始画阶梯 ,图 1 ( a)给出了跨越点过早的情 况 ,因为此时进料板位于 4, 5板之间 。图 1 ( b)给出 了跨越点过晚的情况 ,因为此时进料板位于 8, 9 板 之间 。这 2种情况分别需要 11和 12块板才能完成 给定的分离任务 。而若在第 6, 7 块板之间进料 ,即 在最佳进料板位置进料 ,则只需要 10块板即可 。随 着操作线向平衡曲线靠近 ,它们之间的阶梯将变得 愈来愈小 ,当达到操作线和平衡线的交点时 ,需要无
为考察进料位置不当时引起的逆向蒸馏 ,按照 简化法的计算结果 ,将相关数值输入严格法进行逐 板计算 。即总塔板数为 38,进料位置为第 13块板 , 回流比 1. 293。需注意此时进料位置并非最佳进料 板 ,进料位置过高 。严格计算时 2 个工艺规定分别 是塔顶采出量 80 kmol/ h和回流比 1. 293。该工况 简称为基本工况 。
提高蒸馏效率的方法

提高蒸馏效率的方法蒸馏是一种常用的分离技术,通过利用混合物中不同组分的沸点差异来实现分离纯净物质的目的。
在工业生产和实验室中,蒸馏广泛应用于石油化工、制药、食品加工等领域。
提高蒸馏效率能够提高生产效率、降低能源消耗和减少环境污染。
本文将介绍几种常用的提高蒸馏效率的方法。
1. 提高操作温度和压力提高操作温度和压力是提高蒸馏效率最直接的方法之一。
根据热力学原理,提高温度和压力可以增加混合物中组分的蒸发速率,从而缩短蒸馏时间。
但是需要注意的是,操作温度和压力不能超过混合物中最易挥发组分的临界温度和临界压力,否则会引起副反应或设备失效。
2. 优化馏分塔结构馏分塔是蒸馏的核心设备,其结构的合理优化可以显著提高蒸馏效率。
首先,选择合适的塔板间距和塔板孔径可以增加气液接触面积,促进混合物中组分的传质和传热。
其次,合理设计塔板孔板和塔板布置方式可以减少液体的回流,降低液体在塔板上的滞留时间,提高传质效率。
此外,添加塔板增强剂或填料也可以提高气液分布的均匀性,减少液体的偏流现象。
3. 优化进料和流体分配系统进料和流体分配系统的设计和操作对蒸馏效率有着重要影响。
首先,合理选择进料位置和方式可以使混合物均匀分布在整个塔板上,避免组分的偏析和堆积现象。
其次,优化流体分配系统可以确保塔板上的液体和气体均匀分布,避免液体侧流或气体穿透现象。
这些优化措施可以提高气液传质的效率,加快蒸馏过程。
4. 应用辅助技术在蒸馏过程中,可以应用一些辅助技术来提高蒸馏效率。
例如,应用真空辅助蒸馏可以降低操作温度和压力,提高易挥发组分的蒸发速率。
同时,通过应用溶剂辅助蒸馏或气体增压蒸馏等技术,可以改变混合物的沸点,降低组分之间的沸点差,提高分离效果。
此外,还可以应用蒸汽再循环、热耦合和节能改造等技术,减少能源消耗,提高蒸馏效率。
5. 控制操作参数合理控制操作参数也是提高蒸馏效率的重要方法。
例如,控制液位可以避免液体回流和冲刷现象,保持塔板上的液体和气体的均匀分布。
化工设计实验-进料及最佳位置

实验数据记录:
部分回流数据记录
第一个进料口 第二个进料口 97.3℃ 99.4℃ 2L/h
塔顶温度 塔釜温度 回流量
97℃ 99.7℃ 2L/h
产品量
产品浓度XD 塔釜浓度Xw
1L/h
78% 4%
1L/h
78% 3.2%
结论:
• 因为η1=75%<η2=83.3%,所以第二个进料口效率高,即离塔顶近的进 料口进料塔效率高。
最佳进料位置
• 距塔顶第9块板,距塔釜第2块板
•
பைடு நூலகம்
thankyou!!!
实验步骤:
1.配置约5%酒精水溶液,由供料泵注入蒸馏釜内至液位计上的标记为止。 2.在供料槽内配置15%酒精水溶液。 3.开启电源和冷凝水,待供料槽内的酒精溶液由泵送至蒸馏釜内后,开 始加热,电压控制在220℃,打开回流流量计,进行部分回流操作,待 操作仪器的温度均上升至稳定。 4.记录回流量,检测塔顶产品浓度,塔釜轻组分浓度,最后进行图解法 算全塔效率。 5.换另一个进料位置,重复以上操作,进行全塔效率的比较,从而确定 哪个进料口位置最好。 6.再利用q线,提馏段操作线,精馏段操作线以及平衡线,产品的浓度来 确定最佳进料位置
化工设计实验
不同位置进料对塔效率的影响?怎么确定最佳位置?
2013.11
实验原理
1.总物料平衡:在精馏塔操作时,物料的总进料量等于总出料量,即: F=W+D 当总物料量不平衡时,进料量大于出料量时,会引起淹 塔;相反出料量大于进料量时,会引起塔釜干料,最终都 将破坏精馏 塔的正常操作。 2.全塔效率: Et=Nt/Np 式中,Nt为所需理论板数,Np为塔内实际板数。 3.对于该实验,我们只要测出不同进料口进料塔顶产品的浓度以及塔釜 重组分的浓度,然后用图解法测出不同进料口进料的理论塔板数,算 出塔效率进行比较,就能确定哪个进料口进料塔效率高。然后再利用 q线与精馏段操作线,提馏段操作线的交点,确定进料的最佳位置在 哪一快板,即最佳进料位置。
- 1、下载文档前请自行甄别文档内容的完整性,平台不提供额外的编辑、内容补充、找答案等附加服务。
- 2、"仅部分预览"的文档,不可在线预览部分如存在完整性等问题,可反馈申请退款(可完整预览的文档不适用该条件!)。
- 3、如文档侵犯您的权益,请联系客服反馈,我们会尽快为您处理(人工客服工作时间:9:00-18:30)。
第36卷第7期2008年7月化 学 工 程C HEM IC A L ENG I N EER I NG (C H I NA )V o.l 36N o .7J u.l 2008作者简介:徐忠(1964 ),男,工程硕士,高级主任工程师,E m ai :l xuzhong @gpc m ai.l cn ;陆恩锡,通讯联系人,E m ai:l ceenxil u @scut .edu .cn 。
蒸馏过程进料位置优化徐 忠,陆恩锡(华南理工大学传热强化与过程节能教育部重点实验室,广东广州 510640)摘要:文章介绍了进料位置对蒸馏塔分离能力和能耗的影响,指出进料位置优化是强化分离和节省能耗的一个有效途径。
并介绍了逆向蒸馏、夹点蒸馏等重要概念。
对进料位置优化分别叙述了早期手算的方法和基于计算机模拟的分离因子图法、灵敏度分析法和优化器法。
关键词:蒸馏;进料板;模拟;优化中图分类号:TQ 021.8 文献标识码:A 文章编号:1005 9954(2008)07 0074 05Opti m ization of feed tray location in distillationXU Zhong ,LU En xi(K ey Laboratory o f Enhanced H eat Transfer &Energy Conser vati o n of t h e M inistry o f Education ,South Ch i n a U niversity o fTechno logy ,Guangzhou 510640,Guangdong Province ,Ch i n a)Abst ract :The i n fluence of t h e feed tray location on t h e separati o n and energy consum pti o n w as descri b ed ,and it w as po inted out that the opti m ization of the feed tray l o cation w as an effecti v e m easure m ent for the separation i n tensificati o n and ener gy sav i n g .So m e i m po rtant concepts ,such as retrograde distillation and pinch d istillation w ere also i n troduced .The different feed tray opti m ization m ethods ,such asm anua l calcu lati o n m ethod in the early ti m es ,and separation factor ,sensitiv ity and opti m izer m ethods based on t h e co m puter si m u lation w ere expla i n ed .K ey w ords :d istillation ;feed tray locati o n ;si m u l a ti o n ;opti m ization 蒸馏塔的进料位置对于蒸馏过程节能有着重要的影响,以往的工程设计中往往沿用已有装置的进料位置,而疏于进行详细、严格的进料位置优化。
这是造成分离效果差、能耗居高不下,能量浪费的重要原因之一。
对于任何蒸馏过程均应当进行进料位置的优化,以保证分离能耗降至最小,同时达到最佳的分离效果。
1 最佳进料板位置蒸馏塔的最佳进料板位置可以从以下3个方面进行定义: 相同分离要求及板数下,回流比最小或冷凝器、再沸器热负荷最小;!相同板数及回流比下,塔顶和塔釜产品的分离纯度最高;∀相同分离要求和回流比下,所需塔板数最少。
前2种定义可以使得一定板数的蒸馏塔达到最大的分离能力和最小的能量消耗;而后一种定义可以使达到一定分离要求时塔板数最少。
无论采用哪种定义,其本质都是相同的。
而在进行模拟计算时,必须根据不同的定义,观察不同的参数变化,从而求得正确的最佳进料板位置。
图1 最佳进料位置图解法Fi g .1 Sche m e of opti m um feed tray locati on2 蒸馏塔最佳进料位置早期计算方法从二元蒸馏可知,在采用M cCabe Th iele 图解方法求理论板数时,最佳进料板位置应当在跨过2条操作线交点的位置[1]。
如图1所示,进料板可以在a 和b 之间的任何位置,但是如果进料板不是在最佳位置,则完成相同的分离任务,需要更多的板数。
图中虚线表示在第7块板进料时,所需的理论板数是9块。
而实线表示在第5块最佳位置进料,所需理论板数仅8块即可。
除了图解法求取最佳进料位置之外,也有应用蒸馏塔简化计算法求解计算的。
塔的简化计算法大多采用Fenske 方程求最小理论板数,Under wood 法计算最小回流比,再从G illiland 图中查出实际所需理论板数。
其中最佳进料位置计算较多采用以下2种方法。
对泡点进料,可采用K ir kbride 经验式[2]:log nm =0.206l o g q b q d x ,f h x ,f L x b ,L x d ,h2(1)或直接采用Fenske 方程:nm =log x d ,L x d ,h x ,f h x ,f L /log x ,f L x ,f h x b ,h x b ,L(2)式中:n 为精馏段理论板数;m 为提馏段理论板数;x 为摩尔分数;q d 为塔顶采出量,k m o l/h ;q b 为塔釜采出量,kmo l/h ;下标:f 为进料,d 为塔顶,b 为塔釜,L 为轻关键组分,h 为重关键组分。
随着计算机模拟的发展,手工二元蒸馏作图法已显得较为繁琐,需要花费大量的时间在作图上,且更重要的是实际过程大多是多元混合物的分离,已无法再采用二元作图法,故作图法已基本上不再使用;再者无论二元作图法还是简化计算法都是基于2个基本假设,即全塔处于恒分子流和恒定相对挥发度的理想状况。
其计算结果和实际情况存在一定差别,而对某些蒸馏过程,该差别还相当大,已完全无法适应目前对准确定位最佳进料板位置的要求。
如果说作图法和简化法在20世纪60 70年代还有使用者的话,从80年代开始,随着科技的进步、计算机的发展和过程模拟的普及,最佳进料位置的计算已经逐步为更加准确可靠的一些方法所替代,这些基于手算的方法已经很少使用了。
3 逆向蒸馏蒸馏过程中经常使用的一个参数是塔板上液相中的轻、重关键组分比例,即轻关键组分和重关键组分摩尔分数之比,塔内该比例应当愈向塔顶愈大。
在靠近进料板上方出现轻、重关键组分比率减小或者在进料板下方出现轻、重关键组分比率增大,即在进料板上方出现关键组分比率最小值,而在进料板下方出现关键组分最大值的现象称为逆向蒸馏[3]。
如果以该比值和塔板数作图,称为分离因子图,当出现逆向蒸馏时,该图关键组分比率曲线在进料板上方或下方会出现极小或极大值,如图2所示。
图2 逆向蒸馏图示F i g .2 D i agra m of retrograde d i still ati on图2(a)是进料板位置正常时的图形,可以看出在进料板上、下方,曲线平滑过渡;图2(b)是进料板位置过低,引起进料板上方出现逆向蒸馏,也即经过提馏段的分离,轻组分已经占了较大的比例,但是进入精馏段后,轻组分的比例在一定区间内非但不升,反而呈现下降趋势,直至经过该区间后,轻组分比例才又恢复上升。
无疑,轻组分比例出现反复和波动,浪费了一部分塔板,造成了分离效率的降低。
图2(c)是进料板位置过高,引起进料板下方出现逆向蒸馏。
也即如果从塔顶向塔釜看组成的变化,重组分的比例应当逐渐上升,轻组分应当降低,然而经过精馏段的分离,重组分已经占了较大的比例,但是进入提馏段后,轻组分的比例在一定区间内反而上升,直至经过该区间后,轻组分比例才又恢复下#75#徐 忠等 蒸馏过程进料位置优化降。
同样,这一反复和波动,也引起了分离效率的降低。
逆向蒸馏一方面造成分离效率的降低,另一方面引起能耗的增加,是必须避免的。
4 逆向蒸馏产生的原因逆向蒸馏是多组分蒸馏的特殊现象,对于二元蒸馏不存在该现象。
产生逆向蒸馏主要有以下3种原因:回流比接近最小回流比;!进料中关键组分浓度较小;∀进料位置不是最佳进料板。
实际过程中,前2个因素发生的几率较小,而最后1个原因往往是最常见和最重要的。
进料位置过高,会引起进料板下方有明显的逆向蒸馏;而进料位置过低,会引起进料板上方出现明显的逆向蒸馏;因此在塔设计中一定要注意有无逆向蒸馏问题,也一定要检验进料板位置是否正确。
以往在蒸馏塔的设计中往往存在一些错误概念,如塔顶采出未达分离要求,则增加精馏段板数;塔釜物料未达分离要求,则增加提馏段板数。
实际上,上述措施并不一定奏效,有时还适得其反。
正确的作法是,若未达分离要求,首先须分析进料位置是否为最佳进料板数,若非最佳进料位置,则需要调整进料板,使之达到最佳进料位置;若已达最佳进料位置,则需综合考虑以下因素:回流比和板数的关系;!分析塔顶、塔釜采出量是否合适;∀考虑塔的操作压力有无调整的余地。
回流比的增加可使物料分离得更好,但操作费用也相应增加;板数的增加,也会使分离纯度提高,但须增加设备费用。
两者必须认真加以权衡。
随着能源价格的日益上升,增加塔板数、减小回流比是目前蒸馏过程工业应用的发展趋势。
以丙烯精馏塔为例,由于要制取99.6%纯度的高纯度丙烯,且丙烯和丙烷之间的分离十分困难。
板数多、能耗大成为其主要特点。
其实际塔板数就经历了从早期的100块左右增加到目前的256块左右;回流比从超过20降低到12左右的发展历程。
塔顶、塔釜的采出量需要根据分离要求得到,同时又受到冷凝器和再沸器能力的制约。
对于新设计,可以根据工艺要求,设计出相匹配的冷凝器和再沸器。
而对于已有的装置,经常会遇到分离要求和冷凝器和/或再沸器能力不匹配的情况。
此时为保证产品质量往往不得不牺牲塔顶或塔釜的分离要求,也即牺牲某些组分的回收率来满足产品质量。
塔操作压力对分离有着重要的影响,一般来说,降低压力对蒸馏操作有利,故应在尽可能低的压力下操作。
对于吸收过程压力影响则正好相反,压力升高有利于吸收的进行。
当上述3点均无调整的可能性时,再考虑增加塔板数。
此时精馏段和提馏段板数一定要按照比例增加,而不是单纯增加精馏段或提馏段的板数,以保持进料始终处于最佳进料位置。